某电器开关外壳体塑料注射模设计开题报告
注塑模设计 开题报告

注塑模设计开题报告注塑模设计开题报告一、选题背景和意义注塑模是注塑成型工艺中的核心设备,其设计的好坏直接影响到产品的质量和生产效率。
随着现代工业的发展,注塑模设计也面临着越来越多的挑战和需求,因此,对注塑模设计进行深入研究和优化是十分必要和重要的。
二、研究目标和内容本次研究的目标是通过对注塑模设计的分析和优化,提高注塑成型工艺的效率和产品的质量。
具体研究内容包括注塑模的结构设计、材料选择、热流分析、模具流道设计等方面。
三、研究方法和步骤1. 文献调研:通过查阅相关文献,了解注塑模设计的基本原理和现有研究成果,为后续研究提供理论基础。
2. 注塑模结构设计:根据注塑成型工艺的要求和产品的特点,设计合理的注塑模结构,包括模腔、模芯、顶出机构等。
3. 材料选择:根据注塑模的使用环境和工艺要求,选择合适的材料,以保证模具的强度、硬度和耐磨性。
4. 热流分析:通过热流分析软件对注塑模进行模拟,分析注塑过程中的温度分布和热应力,以优化模具的冷却系统和加热系统。
5. 模具流道设计:根据产品的形状和尺寸,设计合理的模具流道,以保证塑料材料在注塑过程中的均匀流动和充填。
四、预期成果和创新点通过本次研究,预期可以得到以下成果:1. 注塑模设计的优化方案,提高注塑成型工艺的效率和产品的质量。
2. 注塑模的结构设计和材料选择的理论指导,为注塑模设计提供科学依据。
3. 注塑模的热流分析结果和模具流道设计的优化方案,提高注塑模的冷却效果和塑料材料的充填性。
本次研究的创新点主要有:1. 结合现代工业的需求,对注塑模设计进行深入研究,提出切实可行的优化方案。
2. 运用热流分析软件进行模拟,对注塑模的热流分布进行分析和优化。
3. 结合产品的形状和尺寸,设计合理的模具流道,提高注塑成型工艺的稳定性和一致性。
五、研究的局限性和挑战在进行注塑模设计的研究过程中,可能会面临以下局限性和挑战:1. 数据采集的困难:注塑模设计需要大量的实验数据和现场观察,而这些数据的采集可能会受到一些限制和困难。
注塑模开题报告

注塑模开题报告注塑模开题报告一、研究背景注塑模是一种常用于制造塑料制品的工具。
它通过将熔融的塑料注入模具中,然后冷却固化,最终得到所需的塑料制品。
注塑模的设计和制造对于塑料制品的质量和生产效率起着至关重要的作用。
因此,研究注塑模的开题报告具有重要的理论和实践意义。
二、研究目的本次研究的目的是探讨注塑模的设计和制造过程中的关键技术和问题,并提出相应的解决方案。
具体目标包括:1. 分析注塑模的结构和工作原理,了解注塑模的基本知识;2. 研究注塑模的设计原则和方法,提高注塑模的设计效率和制造质量;3. 探讨注塑模的材料选择和热处理工艺,改善注塑模的使用寿命和稳定性;4. 分析注塑模的冷却系统设计,提高注塑模的冷却效果和生产效率;5. 研究注塑模的模具流道设计,优化注塑模的注射过程和塑料制品的质量。
三、研究方法本次研究将采用文献调研和实验研究相结合的方法,以理论研究为基础,通过实验验证和数值模拟分析,探讨注塑模的设计和制造过程中的关键技术和问题。
四、研究内容1. 注塑模的结构和工作原理注塑模是由模具基座、模具芯、模具腔等组成的。
模具基座是注塑模的基础,承载着整个模具的重量和注射压力。
模具芯和模具腔则是塑料制品的形状和尺寸的决定因素。
本次研究将详细探讨注塑模的结构和工作原理,为后续的研究打下基础。
2. 注塑模的设计原则和方法注塑模的设计需要考虑到塑料制品的形状、尺寸、材料等因素,并结合注塑机的工作特点进行设计。
本次研究将分析注塑模的设计原则和方法,包括模具结构设计、模具尺寸设计、模腔分离设计等方面,以提高注塑模的设计效率和制造质量。
3. 注塑模的材料选择和热处理工艺注塑模的材料选择和热处理工艺对注塑模的使用寿命和稳定性有着重要影响。
本次研究将对注塑模的材料选择和热处理工艺进行探讨,包括材料的力学性能、耐磨性、耐腐蚀性等方面的要求,以及热处理工艺的优化和控制。
4. 注塑模的冷却系统设计注塑模的冷却系统设计对于塑料制品的质量和生产效率有着重要的影响。
注塑模具的开题报告

注塑模具的开题报告一、选题背景与意义注塑模具是一种用于塑料制品生产的重要工具,广泛应用于各个行业,如汽车、家电、电子、日用品等。
随着社会经济的不断发展和人们对生活品质的追求,对注塑模具的要求也越来越高。
因此,深入研究注塑模具的开发与应用,提高其精度和效率,具有重要的实践意义和应用价值。
二、研究目的和内容本开题报告旨在通过对注塑模具的开发与应用进行研究,探索提高注塑模具精度和效率的方法和途径。
具体研究内容包括:注塑模具的设计原理与要求、注塑模具制造工艺流程、注塑模具加工技术和质量控制方法等。
三、研究方法和步骤1.文献资料收集与综述:通过查阅相关书籍、期刊论文以及互联网上的相关信息,了解注塑模具的研究现状和发展动态。
2.原理分析与设计要求:对注塑模具的结构和工作原理进行分析,总结注塑模具的设计要求,为后续的研究提供基础和指导。
3.注塑模具制造工艺流程研究:对注塑模具的制造工艺流程进行研究,包括模具材料选择、模具结构设计、数控加工、热处理等环节。
4.注塑模具加工技术研究:研究注塑模具的加工技术,包括数控机床的操作技巧、加工参数的设定以及表面处理等,以提高注塑模具的制造精度和效率。
5.质量控制方法研究:研究注塑模具的质量控制方法,包括检测设备的选用、检测方法的确定以及质量评估与管理等。
四、预期成果和创新点1.通过对注塑模具的开发与应用进行研究,总结注塑模具的设计原理和要求,为注塑模具的设计和制造提供参考依据。
2.研究注塑模具的制造工艺流程,优化模具制造工艺,提高制造精度和效率。
3.深入研究注塑模具加工技术,探索提高加工精度和效率的新方法和途径。
4.研究注塑模具的质量控制方法,确保模具制造的质量和可靠性。
五、研究计划和进度安排1.第一阶段:文献资料收集与综述,调查注塑模具的发展状况和应用领域(1个月)。
2.第二阶段:原理分析与设计要求,总结注塑模具的设计原理和要求(2个月)。
3.第三阶段:注塑模具制造工艺流程研究,探索优化模具制造工艺的方法和途径(3个月)。
一模二腔开关面板注射模具设计开题报告

[16]李秦蕊主编.塑料模具设计[M].西安:西北工业大学出版社,1991.
教研室意见
教研室主任签字:年月日
第四周~第五周:查阅资料,与指导老师讨论建立设计思路;
第六周~第七周:相关数据计算;绘制草图;
第八周~第九周:电子绘图;
第十周~第十三周:手工绘图;
第十四周~第十五周:编制设计说明书;
第十六周:毕业设计修改、打印、装订,送指导教师审阅;
5.主要参考文献
[1]付宏生,刘京华编著.注塑制品与注塑模具设计.北京:化学工业出版社,2003
德国是世界上主要的制造大国之一,在模具制造方面具有领先的技术。德国拥有世界领先的汽车、船舶等制造技术,受上游行业需求影响,德国模具在世界上具有较为重要的地位。由于德国将将技术含量较高的制造业作为其立国之本,预计未来德国会继续加强技术含量较高的模具的研究和开发。
本设计题目涉及目标均为工程实际零件,通过对塑件的实体测绘,完成基本参数的采集,然后运用《塑料模具设计》《塑料成型工艺》知识,利用Pro/E或CAD软件完成模具结构的设计,并进行相关的校核计算。注射模具设计能够锻炼在专业技术应用能力,以及在塑料成型工艺与塑料模具设计技术方面得到全面提高。
[2]蒋继宏,王效岳编绘.注塑模具典型结构100例.北京:化学工业出版社,2000
[3]贾润礼,程志远主编.实用注塑模设计手册.北京:中国轻工业出版社,2000
[4]潘叶表,吴崇峰.塑料模具标准模架的数据库管理[J ].天津轻工业学院学报,2000,(4):2 - 3.
[5]王鹏驹.塑料模具技术手册[ M].北京:机械工业出版社,1997.
(5)是模具技术含量将不断提高,中、高档模具比例将不断增大,这也是产品结构调整所导致模具市场走势的变化。
电器后盖注塑模设计开题报告

2、注塑模具从依靠钳工技艺转变为依靠现代技术。 随着模具企业设计和加工水平的提高,注塑模具的
制造正在从过去主要依靠钳工的技艺转变为主要依靠技 术。这不仅是生产手段的转变,也是生产方式的转变和 观念的上升。这一趋势使得模具的标准化程度不断提高, 模具精度越来越高,生产周期越来越短,钳工比例越来 越低,最终促进了模具工业整体水平不断提高。 3、模具生产正在向信息化迅速发展。
领域和更高水平发展。现在,能把握机遇、开拓市场, 不断发现新的增长点的模具企业和能生产高技术含量模 具企业的业务很是红火,利润水平和职工收入都很好。 因此,模具企业应把握这个趋向,不断提高综合素质和 国际竞争力。
随着市场的发展,塑料新材料及多样化成型方式今 后必然会不断发展,因此对模具的要求也越来越高。为 了满足市场需要,未来的塑料模具无论是品种、结构、 性能还是加工都必将有较快发展。超大型、超精密、长 寿命、高效模具;多种材质、多种颜色、多层多腔、多 种成型方法一体化的模具将得到发展。更高性能及满足 特殊用途的模具新材料将会不断发展,随之将产生一些 特殊的、更为先进的加工方法。
在信息社会中,作为一个高水平的现代模具企业, 单单只是CAD/CAM的应用已远远不够。目前许多企业已 经采用了CAE、CAT、PDM、CAPP、KBE、KBS、RE、 CIMS、ERP等技术及其它先进制造技术和虚拟网络技术 等,这些都是信息化的表现。向信息化方向发展这一趋 向已成为行业共识。
4、注塑模向更广的范围发展。 随着人类社会的不断进步,模具必然会向更广泛的
三、研究方案及工作计划
1、结构尺寸设计 (1)塑料的工艺分析 (2)注塑设备的选择 (3)塑料件工艺尺寸的计算 (4)分型面的选择和浇注系统的设计 (5)排气系统的设计 (6)侧向分型与抽芯机构的设计 (7)合模导向机构及脱模机构的设计 (8)温度调节系统的设计 (9)模具的装配
注塑模设计的开题报告

注塑模设计的开题报告塑料模具是塑料制品的基础,是影响塑件质量及生产效率的最重点要素,约占 80%。
所以掌握好塑料模具的安装与调试至关重要。
下边是整理的注塑模设计的开题报告,欢迎来参照!1塑料注射模具在生产前调试的重要性试模是模具制造过程中的重要环节,是技术、生产和经营管理的基础,它为生产的全过程供给原始数据。
模具制成后,都应在交托行进行试模。
试模主假如查验模具的可生产性、塑料成品能否切合质量要求及合格率,并依据试验结果改正模具,同时探索模具投入正常生产运转的最正确工艺参数。
2模具调试前的准备工作2.1检查图纸模具调试一定审查图纸,依据图纸认识产品要求的几何尺寸、功能、资料、外观要求、调试采纳的设施及工具和附件能否齐备、工艺参数能否切合要求等。
2.2检查设施试模前应查验所使用设施的油路、水道、电路和机械运动部分等,还应检查设施喷嘴球体R的大小、定位圈的直径、最小模具厚度、最大模具厚度、开模行程和顶出方法等技术参数能否知足试模要求,做好试模前的准备工作。
2.3准备试模的原料因为模具是依据原料的物理力学性能设计的,所以原则上我们应采纳图纸上要求的原料。
检查原料的牌号、规格、型号、增添剂、色母料等并对配料进行烘干。
2.4检查模具在模具安装到注塑机前,应依据模具装置图检查模具的外形尺寸、主流道进口尺寸、定位圈尺寸、压垫块高度和宽度及冷却水的进口与出口等,以便实时发现问题,进行修复。
模具的成型部件、浇注系统表面应光洁,无塌坑及显然伤痕。
各滑动部件配合空隙要适合,无卡住及紧涩现象。
各嵌镶件、紧固件要坚固,无松动。
2.5模具的空载检查①活动型芯、顶出及导向部位运动及滑动要安稳,要动作自如、定位正确靠谱。
②合模后各承压面(分型面)之间不得有空隙,接合要严实。
③锁紧部件要安全靠谱,紧固件无松动,开模时,顶出部位要保证顺利脱模,以方便拿出塑件及浇注时产生的系统废料。
3调试的详细步骤3.1试模操作方式注射机操作方式一般有手动、半自动、全自动。
电机接线插头的塑料注射模具设计开题报告 (80)

毕业设计(论文)开题报告题目:电机接线插头的塑料注射模具设计1.设计(论文)进展状况本设计已经完成以下内容;(1)对于在开题报告答辩中,老师对我所画塑件的三维和二维图提出了一些问题,我进行修改和完善,并通过了指导老师的检查;完善了开题报告的内容和格式。
(2)根据我的塑件的外观和用途,我确定了塑件的类型是ABS:ABS树脂是一种共混物,是丙烯腈-丁二烯-苯乙烯共聚物,它为浅黄色粒状或珠状不透明树脂,无毒、无味、吸水率低,具有良好的综合物理机械性能,如优良的电性能、耐磨性,尺寸稳定性、耐化学性和表面光泽等,且易于加工成型。
缺点是耐候性,耐热性差,且易燃。
在用途方面ABS主要应用在汽车贺电子电器方面,而在电器方面则广泛应用与电冰箱、电视机、洗衣机、计算机等电子电器中。
此外,ABS还广泛应用于包装、家具、体育和娱乐用品、机械和仪表中。
(3)根据的所加工的难以程度和塑件的结构特征,我确定加工塑件的型腔数目是一模两腔。
(4)通过对模具的结构分析,大致的画出总装配草图。
(5)完成了3000字的外文翻译。
2.存在的问题及解决措施存在的问题:在画总装配图时,对型腔的布局、分型面的选择和浇口位置等一系1列问题,虽然之前在书本上有些接触,但是在综合考虑装配图的结构和经济等方面还有许多要改进的。
还有用软件画复杂的装配图时,画的不够精准和完善。
解决的措施:在继续学习和巩固画图软件,使装配图更加完善精准。
继续看书,在书本中了解更多关于模具装配的布局和装配所用到的浇注的选择。
3.后期工作安排在剩余的时间里,要进行装配图的完善、计算和编写说明书。
具体安排如下:第4周:在中期答辩中存在的问题,进行修改和完善,还有外文翻译中的一些错误进行改正;第5—6周:完善二维装配图和三维图(包括各个小部件)并准备进行计算;第7—10周:计算塑件的体积和重量(包含初选注塑机的型号)、塑件注射工艺参数的确定、注塑机有关参数的校核等;第11—12周:整理装配图及零件图;并编写毕业设计论文,准备毕业答辩。
注塑模设计开题报告
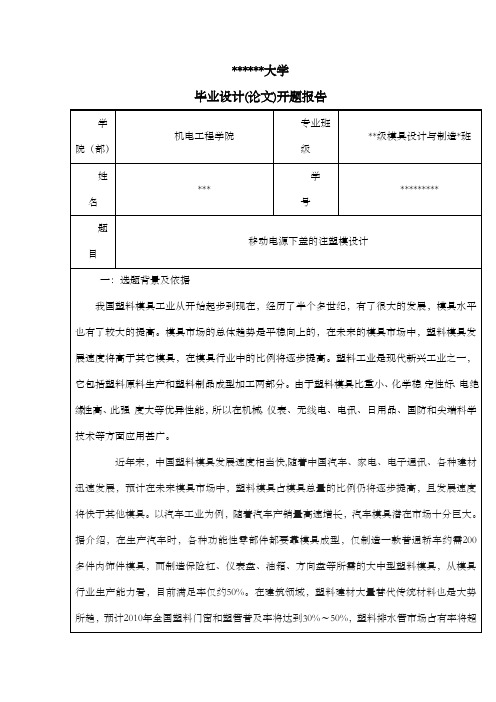
******大学毕业设计(论文)开题报告过50%,都会大大增加对模具的需求量。
应该说,塑料模具的应用潜力是不可低估的。
专家预测,大型、精密、设计合理的注塑模具将受到市场普遍欢迎。
在欧美,CAD/CAE/CAM已成为模具企业普遍应用的技术。
在CAD的应用方面,已经超越了甩掉图板、二维绘图的初级阶段,目前3D设计已达到了70%~89%。
PRO/E、UG、CIMATRON等软件的应用很普遍。
应用这些软件不仅可完成2D设计,同时可获得3D模型,为NC 编CAD/CAM的集成提供了保证。
应用3D设计,还可以在设计时进行装配干涉的检查,保证设计和工艺理性。
数控机床的普遍应用,保证了模具零件的加工精度和质量。
30~50人的模具企业,一般拥有数控机床十多台。
经过数控机床加工的零件可直接进行装配,使装配钳工的人数大大减少。
CAE技术在欧美已经逐渐成熟。
在注射模设计中应用CAE分析软件,模拟塑料的冲模程,分析冷却过程,预测成型过程中可能发生的缺陷。
在冲模设计中应用CAE软件,模拟金属变形过程,分析应力应变的分布,预测破裂、起皱和回弹等缺陷。
CAE技术在模具设计中的作用越来越大,意大利COMAU公司应用CAE技术后,试模时间减少了50%以上。
参考文献[1]孙铃.塑料成型工艺与模具设计[M].北京清华社,2008:1–5100–254328–333.[2]李军.精通Pro/ENGINEER中文野火版模具设计篇[M].中国青年出版社,2004:26–80.[3]韩玉龙.Pro/E 零件设计基础教程[M].科学出版社,2009:54–166.[4]屈华昌.塑料成型工艺及模具设计(第二版)[M].北京教育出版社,2007:180–260.[5]谭雪松.新编塑料模具设计手册[S].人民邮电出版社,2007:47–286.[6]刘朝儒.吴志军,高政一许纪旻.机械制图[M].北京高等教育出版社,2006:449–507.[7]罗河胜.塑料材料手册[M].广州广东科技出版社,–166.。
外壳注射模设计 毕业设计开题报告
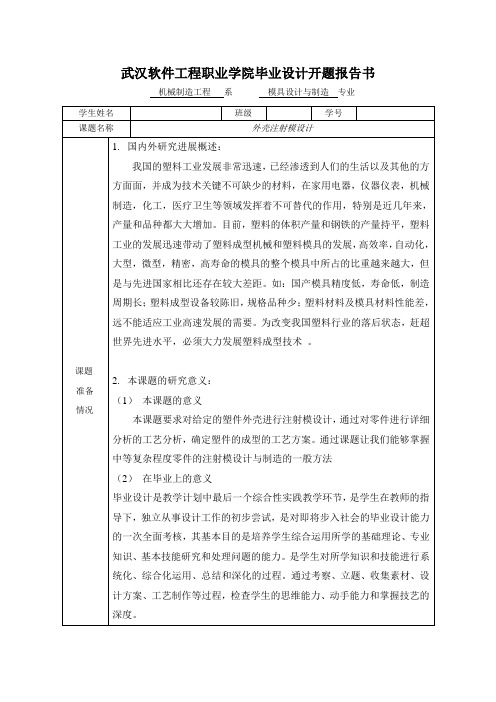
机械制造工程系模具设计与制造专业
学生姓名
班级
学号
课题名称
外壳注射模设计
课题
准备
情况
1.国内外研究进展概述:
我国的塑料工业发展非常迅速,已经渗透到人们的生活以及其他的方方面面,并成为技术关键不可缺少的材料,在家用电器,仪器仪表,机械制造,化工,医疗卫生等领域发挥着不可替代的作用,特别是近几年来,产量和品种都大大增加。目前,塑料的体积产量和钢铁的产量持平,塑料工业的发展迅速带动了塑料成型机械和塑料模具的发展,高效率,自动化,大型,微型,精密,高寿命的模具的整个模具中所占的比重越来越大,但是与先进国家相比还存在较大差距。如:国产模具精度低,寿命低,制造周期长;塑料成型设备较陈旧,规格品种少;塑料材料及模具材料性能差,远不能适应工业高速发展的需要。为改变我国塑料行业的落后状态,赶超世界先进气系统和冷却系统的设计;
5.模架的选择;
6.公差配合,形位公差和表面粗糙度的确定;
7.工作零件的材料选择和制造工艺路线。
计
划
进
度
2011.10.13,选定毕业设计题目并报与指导老师。
2011.10.14~2011.10.19,撰写毕业设计开题报告,交给指导老师。
2011.10.20~2012.4.20 ,搜集相关资料,开始设计,撰写毕业设计说明书。在设计过程中若遇到自己解决不了的问题,就去请教指导老师。基本完成后交给老师并请指导老师审查,听取指导老师意见进行修改和改进。
【5】刘力.机械制图(第二版).北京:高等教育出版社.2004.
【6】李有才.模具材料.北京:化学工业出版社.2009.
【7】李云程.模具制造工艺学(第二版).北京:机械工业出版社.2008.
注射模设计开题报告

注射模设计开题报告注射模设计开题报告一、研究背景与意义近年来,随着工业技术的不断发展,注射模在制造业中扮演着重要的角色。
注射模设计的优劣直接影响着产品的质量和生产效率。
因此,注射模设计的研究和改进具有重要的理论和实践意义。
二、研究目标本研究旨在通过对注射模设计的深入研究,探索优化注射模设计的方法和技术,提高注射模的制造质量和生产效率,为相关行业的发展做出贡献。
三、研究内容1. 注射模设计的基本原理和流程通过对注射模设计的基本原理和流程进行分析和总结,建立起注射模设计的理论基础。
2. 注射模设计中的关键技术研究注射模设计中的关键技术,包括模具结构设计、材料选择、模具加工工艺等,探索如何在设计过程中合理应用这些技术,提高注射模的性能和效率。
3. 注射模设计的优化方法探索注射模设计的优化方法,如基于仿真的优化设计、基于人工智能的优化设计等,通过优化设计方法,提高注射模的设计效果和生产效率。
4. 注射模设计的案例分析通过对实际注射模设计案例的分析,总结经验和教训,为注射模设计提供实践指导。
四、研究方法1. 文献调研通过查阅相关文献和资料,了解注射模设计的研究现状和发展趋势,为研究提供理论依据。
2. 实验研究设计并进行一系列实验,验证注射模设计的理论和方法的可行性和有效性。
3. 数值模拟运用计算机辅助设计软件,进行注射模设计的数值模拟,评估设计方案的性能。
五、预期成果1. 注射模设计的理论基础和流程建立注射模设计的理论基础和流程,为注射模设计提供指导。
2. 注射模设计的关键技术和优化方法研究注射模设计的关键技术和优化方法,提出具体的设计方案和改进措施。
3. 注射模设计的案例分析分析实际注射模设计案例,总结经验和教训,为注射模设计提供实践指导。
六、研究进度安排1. 第一年:进行文献调研,了解注射模设计的研究现状和发展趋势。
2. 第二年:开展实验研究,验证注射模设计的理论和方法的可行性和有效性。
3. 第三年:进行数值模拟,评估设计方案的性能,并总结研究成果。
连接器壳体注塑模具设计开题报告(53)

连接器壳体注塑模具设计开题报告(53)毕业设计(论文)开题报告题目:连接器壳体注塑模具设计1 毕业设计(论文)综述1.1 研究意义模具作为工业之母,其重要性无需多言,包括我国在内的众多国家都将其单列出来作为一个大的行业,而随着塑料制品的大规模应用,塑料注射模具更在这一行中占了很大的比例。
但很可惜的是,由于历史的原因,我国在这一行业,与西方发达国家之间有着很大的差距,但这种差距并非不可弥补的,作为21世纪国家青年,我应当为此而努力,所以现在我理所当然的选择了注射模具毕业设计这一课题。
通过这一课题使我能运用已学的知识,独立进行科学研究活动,学会分析和解决学术问题的方法,锻炼解决某一学术问题的能力。
a塑料件制品涉及及成型工艺的选择b一般塑料件制品成型模具的设计能力c塑料制品质量分析及工艺改进、塑料模具结构改进设计的能力d 掌握模具设计常用的软件(如AutoCAD、Pro/E等)及同实际设计的结合的能力e使自己在文档组织与检索方面的能力得到提高f掌握写论文的一般步骤及格式方法,同时提高自己的学习、思考、解决问题的能力,为以后的工作奠定良好的基础。
1.2 国内外研究现状及发展趋势近年来我国的模具技术有了很大的发展,在大型模具方面,已能生产大屏彩电注塑模具、大容量洗衣机全套塑料模具以及汽车保险杠和整体仪表板等塑料模具。
机密塑料模具方面,已能生产照相机塑料件模具、多型腔小模数齿轮模具及塑封模具。
在成型工艺方面,多材质塑料成行模、高效多色注塑模、镶件互换结构和抽芯脱模机构的创新业取得了较大进展。
气体辅助注射成形技术的使用更趋成熟。
热流道模具开始推广,有些单位还采用具有世界先进水平的高难度针阀式热流道模具。
当前国内外用于注塑模具方面的先进技术主要有以下几种:a热流道技术它是通过加热的办法来保证流道和浇口的塑料保持熔融状态。
由于在流道附近或中心设有加热棒和加热圈,从注塑机喷出口到浇口的整个流道都处于高温状态,使流道中的塑料成型可在保证产品质量的前提下,大幅度降低成本。
壁式电源开关面板注塑模设计-开题报告

江苏财经职业技术学院毕业设计(论文)开题报告题 目壁式电源开关面板注塑模毕业设计 学 院江苏财经职业技术学院专 业模具设计与制造学生姓名季程 学号 0911103212 指导老师何玉林 职称讲师顾问老师陆斗坤 职称模具工程师2011年12月12 日1、结合毕业设计(论文)课题情况,根据所查阅的文献资料,撰写 1500字左右的文献综述(包括目前该课题在国内外的研究状况、发展趋势以及对本人研究课题的启发):一.塑料模具的国内外研究情况塑料制品在人们的日常生活中及现代化工业生产领域中得到日益广泛的应用。
随着塑料工业的 发展,社会对塑料制品的需求愈来愈大。
据统计,在现代化工业生产中,60%~90%的工业产品 需要使用模具加工,模具工业已经成为工业发展的基础[2]。
而塑料注射模在模具中所占的分量 越来越大,其发展也非常迅速,大有凌驾其它模具之上的趋势。
专家预测,在未来的模具市场 中,塑料模具在模具总量中的比例将逐步提高,且发展速度将高于其他模具。
国内相塑料模具相对国外来说比较落后,目前大多用的是单型腔,简单型腔的模具达 70%以上, 仍占主导地位,一模多腔精密复杂的塑料注射模,多色塑料注射模已经能初步设计和制造,但 是有很多精密的模具都要靠进口。
不过,我国模具从开始起步到现在有经历了半个世纪的发展, 模具工业有了很大的发展,1999 年我国模具工业产值为 245 亿,至 2002年我国模具总产值约为 360 亿元,其中塑料模约 30%左右,年均增速均为 13%。
模具制造水平也有了很大的提高,成 型工艺方面,多材质塑料成型模、高效多色注射模、镶件互换结构和抽芯脱模机构的创新方面 也取得较大进展。
气体辅助注射成型技术的使用更趋成熟,如青岛海信模具有限公司、天津通 信广播公司模具厂等厂家成功地在29~34英寸电视机外壳以及一些厚壁零件的模具上运用气辅 技术,一些厂家还使用了 CMOLD 气辅软件,取得较好的效果。
注塑模具设计开题报告

注塑模具设计开题报告注塑模具设计开题报告一、引言注塑模具是一种用于制造塑料制品的工具,它在现代工业中起着至关重要的作用。
随着塑料制品市场的快速发展,注塑模具设计的需求也日益增加。
本文将对注塑模具设计进行研究和探讨,旨在提高注塑模具的设计质量和生产效率。
二、背景注塑模具是将熔化的塑料材料注入到模具腔中,并在一定的温度和压力下冷却和固化,最终得到所需的塑料制品。
注塑模具的设计需要考虑多个因素,如模具结构、材料选择、冷却系统设计等。
合理的注塑模具设计可以提高产品的质量,降低生产成本,并且能够满足不同客户的需求。
三、目标本研究的主要目标是设计出一种高效、高质量的注塑模具,以满足市场需求。
具体目标包括:1. 分析和评估不同注塑模具设计的优缺点;2. 优化模具结构,提高产品的成型精度和表面质量;3. 设计合理的冷却系统,加快产品的冷却速度;4. 提高模具的寿命和稳定性。
四、方法为了达到上述目标,我们将采取以下研究方法:1. 收集和分析现有的注塑模具设计案例,了解各种设计方案的特点和应用范围;2. 运用CAD软件进行模具的三维设计和模拟仿真,评估不同设计方案的性能;3. 利用有限元分析方法,对模具结构进行强度和刚度分析,确保其在生产过程中不会发生变形和破裂;4. 设计合理的冷却系统,通过流体力学模拟和实验验证,优化冷却效果;5. 制造和测试样品模具,评估设计的可行性和实用性。
五、预期结果通过本次研究,我们预计能够设计出一种高效、高质量的注塑模具,具有以下特点:1. 模具结构合理,能够满足不同产品的成型要求;2. 冷却系统设计合理,能够提高产品的冷却速度和表面质量;3. 模具寿命长,能够满足大批量生产的需求;4. 模具稳定性高,能够降低生产过程中的故障率。
六、意义和应用注塑模具设计的优化将对塑料制品行业产生积极的影响。
首先,优化的模具设计可以提高产品的质量和外观,增加产品的竞争力。
其次,优化的模具设计可以减少生产过程中的废品率,降低生产成本。
继电器外壳注塑模设计开题报告

毕业设计(论文)开题报告题目继电器外壳注塑模一、选题的依据及意义:模具生产水平的高低已成为衡量一个国家产品水平高低的重要标志,因为模具在很大程度上决定着产品的质量、效益、和新产品的开发能力。
随着我国加入WTO,我国模具工业的发展将面临新的机遇和挑战。
我国的模具工业的发展,日益受到人们的重视和关注。
“模具式工业生产的基础工艺装备”也已经取得了共识。
在电子、汽车、电机、电器、仪器、仪表、家电和通信等产品中,60%~80%的部件都要依靠模具成型。
用模具生产制件所具备的高精度、高复杂程度、高一致性、高生产效率和低消耗,是其它加工制造方法所不能比拟的。
模具又是“效率放大器”,用模具生产的最终产品价值,往往是模具自身价值的几十倍、上百倍。
目前全世界模具年产值约为1000亿美元,日、美等工业发达国家的模具工业产值已超过机床工业。
近几年,我国模具工业一直以每年15%左右的增长速度发展,2009年,我国模具总产值超过800亿元人民币。
二、国内外研究概况及发展趋势(含文献综述):1. 国内外研究概况1)塑料模今年来,我国塑料模有很大的进步。
在大型塑料模方面,已能生产34英寸大屏幕彩电塑壳模具,6kg大容量洗衣机全套塑料模具及汽车保险杆和整体仪表板等塑料模具。
在精密塑料模具方面,已能生产多型腔小模数齿轮模具和600腔塑封模具,还能生产厚度仅为0.08mm的1模2腔的航空杯模具和难度较高的塑料门窗挤出模等。
内热式或外热式热流道装置得以采用,少数单位采用了具有世界先进水平的高难度针阀式热流道模具,完全消除了制件的浇口痕迹。
气体辅助注射技术已成功得到应用。
在精度方面,塑料模具制造精度可达0.02~0.05mm(国外可达0.005~0.01mm),分型面接触间隙为0.02mm,模板的弹性变形为0.05mm,型面的表面粗糙度值为Ra0.2~0.25μg,塑料模具寿命已达100万次(国外可达300万次),模具制造周期仍比国外长2~4倍。
塑料盖注射模具设计开题报告

[1]占尧.白柳主编.塑料模具典型结构设计实例.化学工业.2008
[2]濮良贵.纪名刚主编.机械设计.高等教育.2006
[3]于永泗.齐编.机械工程材料.理工大学.2010
[4]美芸.凌佳.磊主编.公差配合与测量.理工大学.2010
[5]屈华昌主编.塑料成型工艺与模具设计.高等教育.2001
加入WTO,给塑料模具产业带来了巨大的挑战,同时带来更多的机会。由于中国塑料模具以中低档产品为主,产品价格优势明显,有些甚至只有国外产品价格的1/5~1/3,加入WTO后,国外同类产品对国冲击不大,而中国中低档模具的出口量则加大;在高精模具方面,加入WTO前本来就主要依靠进口,加入WTO后,不仅为高精尖产品的进口带来了更多的便利,同时还促使更多外资来中国建厂,带来国外先进的模具技术和管理经验,对培养中国的专业模具人才起到了推动作用。
技术方案路线根据参数确定设计方案根据参数确定设计方案根据参数确定设计方案塑件工艺性分析塑件工艺性分析塑件工艺性分析模具结构设计模具结构设计模具结构设计查阅国内外相关资料查阅国内外相关资料查阅国内外相关资料分型面的选择分型面的选择分型面的选择造型及绘图造型及绘图造型及绘图浇注系统设计浇注系统设计浇注系统设计绘制模具的结构草图绘制模具的结构草图绘制模具的结构草图成型零件机构设计和固定成型零件机构设计和固定成型零件机构设计和固定绘制非标准零件绘制非标准零件绘制非标准零件侧抽芯机构设计侧抽芯机构设计侧抽芯机构设计绘制模具的总装图绘制模具的总装图绘制模具的总装图推出和回程机构设计细化推出和回程机构设计细化推出和回程机构设计细化图纸审核图纸审核图纸审核冷却系统的设计冷却系统的设计冷却系统的设计三设计论文的研究重点及难点
↓ ↓
侧抽芯机构设计
绘制模具的总装图
注塑模开题报告

注塑模开题报告注塑模开题报告一、研究背景和意义注塑模是一种常见的制造工具,广泛应用于各个行业的产品生产中。
随着科技的不断进步和市场需求的变化,注塑模的设计和制造也面临着新的挑战和机遇。
因此,对注塑模进行深入研究和开发具有重要的现实意义和经济价值。
二、研究目的和内容本研究旨在通过对注塑模的开发和优化,提高产品的质量和生产效率。
具体包括以下几个方面的内容:1. 注塑模设计:通过对注塑模的结构和材料的选择进行优化,提高模具的使用寿命和稳定性,减少产品缺陷和废品率。
2. 注塑模制造:采用先进的制造技术和设备,提高注塑模的制造精度和效率,降低生产成本。
3. 注塑模调试:通过对注塑机和模具的调试,实现注塑过程的自动化和智能化,提高生产效率和产品质量。
4. 注塑模维护:建立完善的注塑模维护体系,定期检修和保养注塑模,延长模具的使用寿命,减少生产停机时间。
三、研究方法和步骤本研究将采用实验研究和理论分析相结合的方法,具体步骤如下:1. 收集相关文献和资料,了解注塑模的基本原理和现有研究成果。
2. 设计和制造注塑模样品,包括模具结构设计、材料选择和加工工艺等。
3. 进行模具试验,测试模具的使用寿命、稳定性和产品质量等指标。
4. 分析试验结果,找出模具存在的问题和改进的方向。
5. 优化注塑模设计和制造工艺,改进模具的结构和材料,提高模具的性能和寿命。
6. 进行注塑模调试和生产实验,测试改进后的模具的生产效果。
7. 总结研究成果,撰写研究报告,并进行相关技术推广和应用。
四、预期结果和影响通过本研究,预期可以取得以下几个方面的成果和影响:1. 提高产品质量:通过优化注塑模的设计和制造,减少产品缺陷和废品率,提高产品的质量和可靠性。
2. 提高生产效率:通过改进注塑模的结构和材料,提高模具的使用寿命和稳定性,减少生产停机时间,提高生产效率。
3. 降低生产成本:通过优化注塑模的制造工艺,降低模具的制造成本,减少生产过程中的能耗和废品率,降低生产成本。
注塑模模具设计开题报告
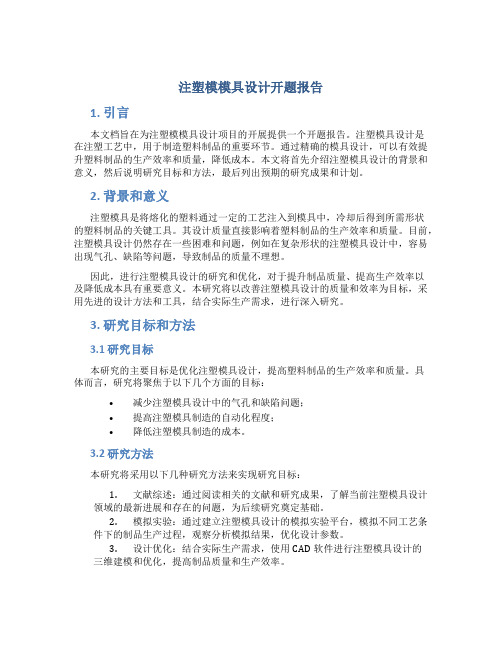
注塑模模具设计开题报告1. 引言本文档旨在为注塑模模具设计项目的开展提供一个开题报告。
注塑模具设计是在注塑工艺中,用于制造塑料制品的重要环节。
通过精确的模具设计,可以有效提升塑料制品的生产效率和质量,降低成本。
本文将首先介绍注塑模具设计的背景和意义,然后说明研究目标和方法,最后列出预期的研究成果和计划。
2. 背景和意义注塑模具是将熔化的塑料通过一定的工艺注入到模具中,冷却后得到所需形状的塑料制品的关键工具。
其设计质量直接影响着塑料制品的生产效率和质量。
目前,注塑模具设计仍然存在一些困难和问题,例如在复杂形状的注塑模具设计中,容易出现气孔、缺陷等问题,导致制品的质量不理想。
因此,进行注塑模具设计的研究和优化,对于提升制品质量、提高生产效率以及降低成本具有重要意义。
本研究将以改善注塑模具设计的质量和效率为目标,采用先进的设计方法和工具,结合实际生产需求,进行深入研究。
3. 研究目标和方法3.1 研究目标本研究的主要目标是优化注塑模具设计,提高塑料制品的生产效率和质量。
具体而言,研究将聚焦于以下几个方面的目标:•减少注塑模具设计中的气孔和缺陷问题;•提高注塑模具制造的自动化程度;•降低注塑模具制造的成本。
3.2 研究方法本研究将采用以下几种研究方法来实现研究目标:1.文献综述:通过阅读相关的文献和研究成果,了解当前注塑模具设计领域的最新进展和存在的问题,为后续研究奠定基础。
2.模拟实验:通过建立注塑模具设计的模拟实验平台,模拟不同工艺条件下的制品生产过程,观察分析模拟结果,优化设计参数。
3.设计优化:结合实际生产需求,使用CAD软件进行注塑模具设计的三维建模和优化,提高制品质量和生产效率。
4.实际生产验证:将优化后的注塑模具设计方案进行实际生产验证,评估其在实际生产环境中的性能和效果。
4. 预期的研究成果和计划4.1 预期成果本研究预期将取得以下几个方面的研究成果:1.建立注塑模具设计的模拟实验平台,可用于模拟不同工艺条件下的制品生产过程和优化设计参数。
注塑模设计开题报告

注塑模设计开题报告注塑模设计开题报告一、研究背景与意义注塑模是一种常见的工业模具,广泛应用于塑料制品的生产过程中。
随着塑料制品需求的增加,注塑模的设计和制造变得越来越重要。
注塑模设计的质量和效率直接影响到塑料制品的生产效果和成本控制。
因此,深入研究注塑模设计的方法和技术,对于提高生产效率、降低成本具有重要意义。
二、研究目标本研究的目标是通过对注塑模设计的深入研究,探索一种高效、精确的注塑模设计方法,以提高注塑模的设计质量和制造效率。
三、研究内容1. 注塑模设计的基本原理和流程注塑模设计是一个复杂的过程,涉及到材料力学、热力学、流体力学等多个学科的知识。
本研究将深入探讨注塑模设计的基本原理和流程,包括模具结构设计、注塑工艺参数的确定等内容。
2. 注塑模设计中的材料选择与优化材料的选择对注塑模的设计和制造具有重要影响。
本研究将研究不同材料在注塑模设计中的应用,探索材料的选择与优化方法,以提高注塑模的使用寿命和性能。
3. 注塑模设计中的模具结构优化模具结构的合理性对注塑模的性能和生产效率有着重要影响。
本研究将通过模拟和实验研究,探索模具结构的优化方法,以提高注塑模的生产效率和产品质量。
4. 注塑模设计中的工艺参数优化工艺参数的合理选择对注塑模的生产效果和成本控制具有重要影响。
本研究将研究不同工艺参数对注塑模的影响,探索工艺参数的优化方法,以提高注塑模的生产效率和成本控制能力。
四、研究方法与计划1. 研究方法本研究将采用实验研究和模拟仿真相结合的方法,通过实验验证和模拟分析,探索注塑模设计的最佳方法和技术。
2. 研究计划第一年:收集相关文献资料,深入了解注塑模设计的基本原理和流程。
第二年:开展实验研究,验证注塑模设计的方法和技术。
第三年:进行模拟仿真分析,优化注塑模设计的方法和技术。
第四年:总结研究成果,撰写论文并进行学术交流。
五、预期成果与创新点1. 预期成果本研究预期将提出一种高效、精确的注塑模设计方法,以提高注塑模的设计质量和制造效率。
充电器外壳的注塑注射模具设计开题报告
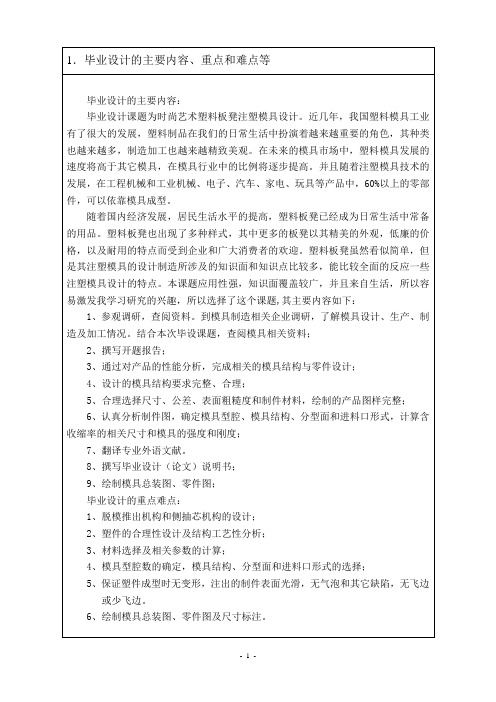
1、模具技术的现状模具是汽车、电子、电器、航空、仪表、轻工、塑料、日用品等工业部门极其重要的工艺装备。
没有模具、就没有高质量的产品。
模具不是一般的工艺装备,而是技术密集型的产品,工业发达国家把模具作为机械制造方面的高科技产品来对待。
他们认为:“模具是发展工业的一把钥匙;模具是一个企业的心脏;模具是富裕社会的一种动力”。
近年来,我国塑料模具业发展相当快,目前,塑料模具在整个模具行业中约占30%左右,而在整个塑料模具市场以注塑模具需求量最大。
随着模具制造行业的发展,许多企业开始追求提高产品质量及生产效率,缩短设计周期及制造周期,降低生产成本,最大限度地提高模具制造业的应变能力等目标。
新兴的模具CAD技术很大程度上实现了企业的愿望。
近年来,CAD技术的应用越来越普遍和深入, 大大缩短了模具设计周期, 提高了制模质量和复杂模具的制造能力。
目前,美国、日本、德国等工业发达国家模具工业的产值均已超过机床工业总产值。
美国模具年产值已超过100亿美元;日本从1957年到1984年二十七年间,模具工业增长100倍;1987年台湾地区模具出口达一亿二千万美元。
香港的模具年产值为30亿港币,我国的模具年产值为人民币30亿元。
从整体来看,中国塑料模具无论是在数量上,还是在质量、技术和能力等方面都有了很多进步,但与国民经济发展的需求、世界先进水平相比,差距仍然很大。
主要缺陷明显的表现在精度不高,技术含量低、复杂程度低等缺点。
严重的阻碍着国内模具业的发展。
一些大型、精密、复杂、长寿命的中高档塑料模具每年仍需大量进口。
在总量供不应求的同时,一些低档塑料模具却供过于求,市场竞争激烈,还有一些技术含量不太高的中档塑料模具也有供过于求的趋势。
因此中国塑料模具行业和国外先进水平相比,主要存在一下问题:发展不平衡,产品总体水平较低;工艺装备落后,组织协调能力差;大多数企业开发能力弱,创新能力明显不足;供需矛盾短期难以缓解;体制和人才问题的解决尚需时日。
- 1、下载文档前请自行甄别文档内容的完整性,平台不提供额外的编辑、内容补充、找答案等附加服务。
- 2、"仅部分预览"的文档,不可在线预览部分如存在完整性等问题,可反馈申请退款(可完整预览的文档不适用该条件!)。
- 3、如文档侵犯您的权益,请联系客服反馈,我们会尽快为您处理(人工客服工作时间:9:00-18:30)。
毕业设计(论文)开题报告题目:某电器开关外壳体塑料注射模设计1.毕业设计(论文)综述(题目背景、研究意义及国内外相关研究情况)1.1 题目背景模具是工业生产的基础设备,被称为“工业之母”。
是高新技术产业的一个组成部分。
作为国民经济的基础工业,模具涉及机械、汽车、轻工、电子、化工、冶金、建材等各个行业,应用范围十分广泛。
塑料模具在整个模具行业中所占比重约为30%,在模具进出口中的比重高达50%~70%。
近年来我国塑料模具发展迅速。
塑料制品的应用日渐广泛,为塑料模具提供了非常广阔的市场。
预计在未来的模具市场中, 塑料模具的发展速度将高于其它模具, 在模具行业中的比例将逐步提高[3]。
1.2 研究意义模具工业是国民经济的基础工业,受到政府和企业界的高度重视, 发达国家“模具工业是进入富裕社会的源动力“之说,可见其受重视之程度, 当今“模具就是经济效益”的观念已被越来越多的人所接受。
所以目前对于模具设计研究的创新及改革对国家的经济与政治及军事的发展具有极其重要的意义。
现在工业生产中需要大批量的生产塑料模具,通过模拟实际的模具设计过程,可以使学生加深基本技能的应用和创新思维的磨练[5]。
1.3 国内模具行业现状和趋势发展现状:我国模具行业近年来发展很快,据不完全统计,目前模具生产厂点共有2万多家,从业人员约50万人,全年模具产值约360 亿元,总量供不应求,出口约2亿美元,进口约10亿美元.。
当前,我国模具行业的发展具有如下特征:大型、精密、复杂、长寿命中高档模具及模具标准件发展速度快于行业总体发展水平;塑料模和压铸模成比例增长;专业模具厂家数量及其生产能力增加较快;“三资”企业及私营企业发展迅速;股份制改造步伐加快等。
从地区分布来看:以珠江三角洲和长江三角洲为中心的东南沿海地区发展快于中西部地区,南方的发展快于北方。
我国模具总量虽然已位居世界第三,,但设计制造水平总体上落后于德、美、日、法、意等发达国家,模具商品化和标准化程度也低于国际水平。
趋势:近年来,全球制造业正以垂直整合的模式向中国及亚太地区转移,中国正成为世界制造业的重要基地。
制造业模式的变化,必将产生对新技术的需求,也必将导致CAD技术的发展。
目前,模具制造厂已经较广泛地采用了数控加工。
为了保证加工质量、提高加工效率、改进制造流程,有较多的模具制造厂开始使用多坐标数控加工、高速铣削加工及基于快速原型的模具制造等方法。
主要表现为:(1)激光技术的应用日益受到重视;(2)模具CAD技术应用的ASP模式,将成为发展方向[5]。
1.4 国外的发展情况目前国外发达国家的模具制造发展水平都已趋近智能化、批量化、数字化生产,厂家大多都已采用数控加工,具有先进的制造技术及管理技术,使得模具向着高速、精密、长寿命方向发展,计算机、激光、电子、新材料、新技术的发展,使得快速经济制模技术应用范围不断扩大,类型不断增多,创造的经济效益和社会效益越显著[6]。
2.本课题研究的主要内容和拟采用的研究方案、研究方法或措施:2.1塑件分析图2.1 塑件二维图图2.2 塑件三维图该零件二维图,如图2.1,该零件为某电器开关外壳体塑料注射模设计,三维如上图2.2所示材料为ABS,对塑件进行分析,从模型图和制件三视图上分析,该制品是一个长和宽为85mm,高为23mm的正方形盒盖类制件,内部分布少量筋,盒盖内部一个侧凹及多处内扣,所以需要注塑模具带有侧抽芯机构。
该制件的尺寸精度为MT5,精度中等。
设计注塑模具时,既要考虑良好的塑料成型,冷却等问题,又要考虑模具的制造、装配、加工等方面。
设计主要内容有以下几个方面:(1)决定塑件的分型面。
(2)侧凹的成型方法。
(3)根据塑料件的结构,分析确定浇口位置和注塑方式。
(4)决定型腔的模块组合。
模具的总体结构和零件形状不单要满足注塑充模和冷却工艺及设计方面的要求,同时成型零件还要具有适当的精度,粗糙度,刚度和强度,易于装配和制造,尽量降低制造成本。
2.2. 拟采用的方案方案1:选择开关外壳体下表面为分型面,浇口形式采用潜伏式浇口,侧抽芯机构采用斜导柱加滑块,型腔布局一模两腔,顶出机构采用顶杆顶出机构脱模。
方案2:选择开关外壳体上表面为分型面,浇口形式采用潜伏式浇口,侧抽芯机构采用斜导柱加滑块,型腔布局一模一腔,顶出机构采用推板顶出机构脱模。
方案3:选择开关外壳体下表面为分型面,浇口形式采用侧浇口,侧抽芯机构采用斜顶杆机构,型腔布局一模两腔,顶出机构采用顶杆顶出机构脱模。
2.3 方案的初步设计2.3.1型腔数的确定根据塑件计算重量,选择设备型号规格,确定型腔数。
为了是模具与注射机的生产能力相匹配,提高生产效率和经济性,并保证塑件精度,模具设计时应确定型腔数目。
常用的方法有四种:(1)根据经济性确定型腔数目。
(2)根据注射机的额定锁模力确定型腔数目。
(3)根据注射机的最大注射量确定型腔数目。
(4)根据制品精度确定型腔数目。
由于塑件尺寸较大,内部结构不很简单,而且要用到多处斜顶侧抽芯,生产批量为中小批量,模具结构拟采用一模两腔结构。
2.3.2 抽芯机构图2.3侧凹与内扣的位置该塑件盒盖内部一个侧凹及多处内扣,其中四周封闭的,且均垂直于脱模方向,阻碍成型后的塑件从模具脱出,因此成型时必须设计有侧向分型机构,经分析本模具采用斜顶侧向抽芯机构。
2.3.3 浇口所采用形式根据型腔数为一模两腔,所做塑件初选择的是侧浇口:原因:侧浇口是最常用的浇口形式常用于一模多腔,可根据塑件的形状特点和充模需要,灵活地选择浇口位置,如框形或环形塑件,其浇口可设在外侧,也可设在内侧。
潜伏浇口经常用于精度较高的塑件,对此精度的塑件用不经济。
2.3.4 顶出机构在所给塑件内部可以明显看到顶杆痕迹,在注射成型的每一个循环中,塑件必须由模具型腔中或凸模/型芯上松动分离(即脱出),脱出机构的机构就叫塑件脱出机构,脱出机构的设计基本考虑:(1)保证塑件质量(2)脱出机构结构(3)所需顶出行程、开模行程计算;根据以上原则,选择顶杆脱模机构。
2.3.5 分型面的位置分型面的选取原则尽可能选择在不影响外观的部位,并使其产生的溢料边易于消除或修整;保证塑件尺寸精度;有利于排气;脱模是塑件留在动模上:塑件在分型面上的投影面积最大化:所以采用塑件的下表面做为模具分型面。
综合以上原因,所以此次模具设计拟采用方案32.4可能遇到的问题及解决措施(1)模具表面出现气泡根据气泡的产生原因,解决的对策有以下几个方面:1.在制品壁厚较大时a.根据壁厚,确定合理的浇口,浇道尺寸.一般浇口高度应为制品壁厚的50%~60%b.至浇口封合为止,留有一定的补充注射料。
c.注射时间应较浇口封合时间略长。
2.由于挥发性气体的产生而造成的气泡,解决的方法主要有:a.充分进行预干燥。
b.降低树脂温度,避免产生分解气体。
3.本课题研究的重点及难点,前期已开展工作3.1重点及难点:(1)型腔数的确定。
(2)测抽芯机构的设计。
(3)根据塑料件的结构,分析确定浇口位置和注塑方式。
(4)决定型腔的模块组合。
3.2前期已开展工作:(1)学习相关课程。
(2)查阅相关资料及文献。
(3)绘制二维、三维零件图。
(4)拟定设计方案。
4.完成本课题的工作方案及进度计划(按周次填写)(1)接受设计任务,查阅相关资料,了解课题的背景和发展状况,1-2周;(2)了解学习常用注射模设计的基础知识,初步原理方案的提出,3-4周;(3)某电器开关外壳体的注塑件的工艺分析,5周;(4)成型设备的计算和选择,6周;(5)简单模塑工艺规程的编制,7周;(6)某电器开关外壳体注塑模的结构设计,8周;(7)盒盖注塑模冷却系统的分析设计,9周;(8)绘制相关设计的零件图和装配图,10-12周;(9)撰写毕业论文,13-14周;(10)准备答辩,15周。
5 指导教师意见(对课题的深度、广度及工作量的意见)指导教师:年月日6 所在系审查意见:系主管领导:年月日参考文献[1]张洪峰.塑料模具设计与制造[M].北京:高等教育出版社.2008.[2]翁其金.塑料模塑成型技术[M].北京:机械工业出社. 2001.[3] 蒋桂芝.王丽.我国模具技术的发展现状及其发展趋势[J].2000.[4]孙安垣,闫烨,杨超谈等.我国改性塑料行业的发展前景[M].《工程塑料应用》杂志社.2010,11(2):83-87.[5]伍先明,王群.塑料模具设计指导[M].北京:国防工业出版社. 2006.[6]朱光力,万金保.塑料模具设计[M].北京:清华大学出版社.2003.[7]王匀.Pro/e Wildfire 模具设计[M].机械工业出版社.2005.[8]张维合.注塑模具设计实用教程 [M].化学工业出版社 2007.[9]屈华昌.塑料成型工艺与模具设计[M].机械工业出版社.2005.[10]赵蓓蓓.初探塑料模具材料现状及发展方向[J].科技资讯. 2009, (34).[11]金秀莲.浅谈注塑工艺的影响因素[J].商品与质量·前沿观察. 2010, (2).[12]王永平.注塑模具设计经验点评[J].机械工业出版社.2009, (2).[13]杨占尧自柳. 《塑料模具典型结构设计实例》[M] 化工公业出版社.2008.[14]几种新型注塑设备的简单介绍[J].中国液压机械网. 2009.[15]许发樾.实用模具设计与制造手册[M].机械工业出版社. 2005.[16]CHIN, KWAI-SANG and T. N. WONG, Knowledge-based evaluation for the conceptual[J]. C omputer-Aided Design, 2003, 6(7): 12-22.[17]MOK, C. K, K. S. CHIN and JOHN K. L. HO, An interactive knowledge-based CAD system f or mould design in injection molding processes[J]. The International Journal of Advanced Manufa cturing Technology, 2001, 8(1): 27-38.[18]Autodesk Co Ltd. Moldflow insight 2010 help System [G]. MA: Autodesk Co Ltd, 2009.。