3.2材料受迫成形工艺技术
先进制造技术总结[修改版]
![先进制造技术总结[修改版]](https://img.taocdn.com/s3/m/c9c96dc631126edb6e1a10b0.png)
第一篇:先进制造技术总结先进制造技术考试答案1、零件的无损检测无损检测:是在不破坏或基本不破坏零件、构件和材料,即不破坏零件、构件的形状、尺寸精度,表面质量和不改变材料的成分、性能及零件使用性能的前提下,采用物理、化学等方法探测零件材料内部和表面的缺陷及其某些物理性能。
无损检测技术主要应用在以下三方面:监督和控制生产过程中的质量问题产品出厂前的成品检测和用户验收检测产品的使用过程中的维护检测。
无损检测方法:渗透探伤磁粉探伤涡流探伤超声波探伤射线探伤声发射探伤综合探伤法。
2、超声波探伤原理超声波探伤:是利用超声波通过两种介质的界面时发生反射和折射的特性来探测零件内部的缺陷。
3)超声波探伤的特点厚度: 探测5~3000mm厚的金属或非金属材料的构件。
粗糙度: 对零件表面粗糙度有一定要求。
一般要求粗糙度等级高于Ra6.3,表面清洁光滑,与探头接触良好。
盲区: 零件表面一段距离内的缺陷波与初始波难于分辨,难以探测缺陷。
盲区的大小因超声波探伤仪不同而异,一般为5~7mm。
超声波探伤中对缺陷种类和性质的识别较为困难,需借助一定的方法和技术。
3、无损检测:是在不破坏或基本不破坏零件、构件和材料,即不破坏零件、构件的形状、尺寸精度,表面质量和不改变材料的成分、性能及零件使用性能的前提下,采用物理、化学等方法探测零件材料内部和表面的缺陷及其某些物理性能。
机器视觉的技术趋势:高速化、高分辨率、彩色低功耗、智能化、模块化、傻瓜化先进数字网络特殊应用。
4、21世纪制造业面临的六大挑战:快速响应市场能力的挑战-全部制造环节并行实现打破组织、地域和时间壁垒的挑战-技术资源的集成信息时代的挑战-信息向知识的转变(信息的收集、储存、分析、发布和应用)有限的资源和日益增长的环保压力的挑战-可持续发展(减少污染、合理资源利用)制造全球化和贸易自由化的挑战-可重组工程技术创新的挑战-全新制造工艺和产品的开发5、先进制造技术的内涵和特点传统制造技术先进制造技术系统性能驾驭生产过程物质流、信息流和能量流广泛性贯穿从产品设计、加工制造到产品销售的整个过程集成性专业和学科不断渗透、交叉融合,其界限逐渐淡化甚至消失动态性不同时期、不同国家,其特点、重点、目标和内容不同实用性注重实践效果,促进经济增长,提高综合竞争力先进制造技术的分类:现代设计技术先进制造工艺加工自动化技术现代生产管理技术先进制造生产模式先进制造技术与传统制造技术比较具有系统性、广泛性、集成性、动态性、实用性特征。
高速加工与超高速加工

轴承润滑:油脂润滑、油雾 润滑、油气润滑等。
1.2 超高速切削加工关键技术
2.超高速切削的主轴系统
主轴轴承: 气浮轴承--高回转精度、高转速、低温升,承载能力低。
1.2 超高速切削加工关键技术
2.超高速切削的主轴系统
主轴轴承: 液体静压轴承--运动精度高,动态刚度大,有油升影响。
1.3 超高速磨削技术
超高速磨削砂轮 砂轮基体--必须考虑高速离心力作用; 砂轮磨粒--立方氮化硼、金刚石。
高速砂轮典型结构 变截面等力矩腹板结构,无中心法兰孔, 通过多个小螺孔与主轴安装固定,以降低法兰孔应力。
1.3 超高速磨削技术
超高速磨床结构 具有高动态精度、
高阻尼、高抗振性和 热稳定性。
时,刀具的主要失效形式为刀尖破损,设计时应 着重考虑提高刀尖的抗冲击强度。 超高速铣削刀具材料:有整体硬质合金、涂层硬 质合金、陶瓷、硬质合金和立方氮化硼等。
思考与练习
1. 在怎样的速度范围下加工属于高速加工?分析 高速切削加工所要解决的关键技术。 2. 超高速切削包含哪些相关技术? 3. 简述超高速磨削特点及关键技术。 4. 简述超高速铣削特点及关键技术。
1. 高速与超高速加工技术
1.1 高速与超高速切削技术概述 1.2 超高速切削加工关键技术 1.3 超高速磨削技术 1.4 超高速铣削技术
1.1 高速与超高速切削技术概述
“高速加工”的起源
Salomon切削理论: 工件材料均有一个
临界切削速度,在该速 度下有最高切削温度。
为什么要进行高速加工?
萨洛蒙曲线
常用结构有龙门式、并联式机床结构。
1.2 超高速切削加工关键技术
材料成型工艺技术

材料成型工艺技术材料成型工艺技术是指将材料通过一定的工艺方法,经过加工、成形、塑造等过程,使其达到特定的形状和性能要求的一种技术。
这种技术可以广泛应用于各个行业,如汽车、航空、电子、家电等领域。
材料成型工艺技术的发展,为各个行业提供了更多的可能性和选择。
材料成型工艺技术主要包括压力成型、热成型、造型、粉末冶金等多种方法。
其中,压力成型是一种将材料放入模具中,在给定的条件下施加一定的压力,使材料在模具内成型的方法。
这种方法适用于加工金属、塑料、陶瓷等材料。
压力成型工艺技术具有成形精度高、表面光洁度好等特点,被广泛应用于制造各种零部件。
热成型是一种通过加热材料使其变软,然后通过外界力的作用使其变形的方法。
这种方法适用于加工塑料、橡胶等材料。
热成型工艺技术能够使材料保持一定的形状稳定性,并且在加工过程中能够消除材料内部的应力,提高产品的性能。
造型是一种通过模板、模具等工具对材料进行塑造的方法。
这种方法适用于加工陶瓷、玻璃等材料。
造型工艺技术能够使材料呈现出各种复杂的形状,满足设计师的要求,并且能够提高生产效率。
粉末冶金是一种通过将金属粉末进行成型、烧结等处理,制造出具有特定形状和性能的材料的方法。
这种方法适用于生产精密零部件、高温合金等材料。
粉末冶金工艺技术能够扩大材料的应用范围,提高产品的性能。
在材料成型工艺技术中,工艺参数的控制是非常重要的。
工艺参数包括温度、压力、速度等多个方面。
通过合理控制这些参数,可以使成型产品具有更好的性能。
材料成型工艺技术的发展,对于提高产品质量、降低产品成本、增加产品种类等方面具有重要作用。
随着科技的不断进步,材料成型工艺技术也在不断创新和发展,为各行各业的发展提供更多的机会和挑战。
材料成形工艺学
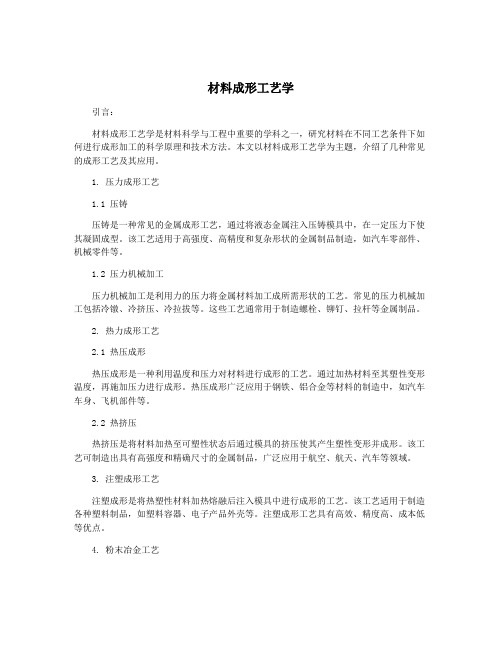
材料成形工艺学引言:材料成形工艺学是材料科学与工程中重要的学科之一,研究材料在不同工艺条件下如何进行成形加工的科学原理和技术方法。
本文以材料成形工艺学为主题,介绍了几种常见的成形工艺及其应用。
1. 压力成形工艺1.1 压铸压铸是一种常见的金属成形工艺,通过将液态金属注入压铸模具中,在一定压力下使其凝固成型。
该工艺适用于高强度、高精度和复杂形状的金属制品制造,如汽车零部件、机械零件等。
1.2 压力机械加工压力机械加工是利用力的压力将金属材料加工成所需形状的工艺。
常见的压力机械加工包括冷镦、冷挤压、冷拉拔等。
这些工艺通常用于制造螺栓、铆钉、拉杆等金属制品。
2. 热力成形工艺2.1 热压成形热压成形是一种利用温度和压力对材料进行成形的工艺。
通过加热材料至其塑性变形温度,再施加压力进行成形。
热压成形广泛应用于钢铁、铝合金等材料的制造中,如汽车车身、飞机部件等。
2.2 热挤压热挤压是将材料加热至可塑性状态后通过模具的挤压使其产生塑性变形并成形。
该工艺可制造出具有高强度和精确尺寸的金属制品,广泛应用于航空、航天、汽车等领域。
3. 注塑成形工艺注塑成形是将热塑性材料加热熔融后注入模具中进行成形的工艺。
该工艺适用于制造各种塑料制品,如塑料容器、电子产品外壳等。
注塑成形工艺具有高效、精度高、成本低等优点。
4. 粉末冶金工艺粉末冶金是一种将金属或非金属粉末通过成形和烧结等工艺制成制品的技术。
该工艺可制造出具有特殊性能和形状的制品,广泛应用于汽车、航空航天、机械等领域。
结论:材料成形工艺学是研究材料在不同工艺条件下进行成形加工的学科,对于材料制造和工程应用具有重要意义。
通过不同的成形工艺,可以获得多种形状和性能的制品,满足不同需求,并推动了现代工业的发展。
金属工艺及材料成形技术
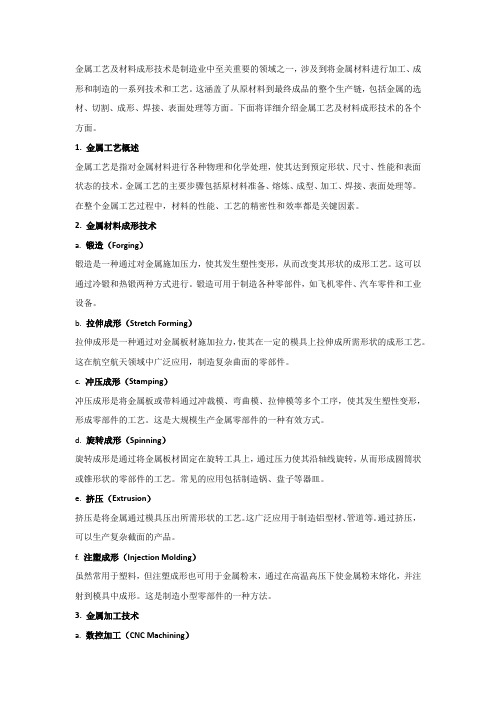
形和制造的一系列技术和工艺。
这涵盖了从原材料到最终成品的整个生产链,包括金属的选材、切割、成形、焊接、表面处理等方面。
下面将详细介绍金属工艺及材料成形技术的各个方面。
1. 金属工艺概述金属工艺是指对金属材料进行各种物理和化学处理,使其达到预定形状、尺寸、性能和表面状态的技术。
金属工艺的主要步骤包括原材料准备、熔炼、成型、加工、焊接、表面处理等。
在整个金属工艺过程中,材料的性能、工艺的精密性和效率都是关键因素。
2. 金属材料成形技术a. 锻造(Forging)锻造是一种通过对金属施加压力,使其发生塑性变形,从而改变其形状的成形工艺。
这可以通过冷锻和热锻两种方式进行。
锻造可用于制造各种零部件,如飞机零件、汽车零件和工业设备。
b. 拉伸成形(Stretch Forming)拉伸成形是一种通过对金属板材施加拉力,使其在一定的模具上拉伸成所需形状的成形工艺。
这在航空航天领域中广泛应用,制造复杂曲面的零部件。
c. 冲压成形(Stamping)冲压成形是将金属板或带料通过冲裁模、弯曲模、拉伸模等多个工序,使其发生塑性变形,形成零部件的工艺。
这是大规模生产金属零部件的一种有效方式。
d. 旋转成形(Spinning)旋转成形是通过将金属板材固定在旋转工具上,通过压力使其沿轴线旋转,从而形成圆筒状或锥形状的零部件的工艺。
常见的应用包括制造锅、盘子等器皿。
e. 挤压(Extrusion)挤压是将金属通过模具压出所需形状的工艺。
这广泛应用于制造铝型材、管道等。
通过挤压,可以生产复杂截面的产品。
f. 注塑成形(Injection Molding)虽然常用于塑料,但注塑成形也可用于金属粉末,通过在高温高压下使金属粉末熔化,并注射到模具中成形。
这是制造小型零部件的一种方法。
3. 金属加工技术a. 数控加工(CNC Machining)加工具有高精度、高效率和灵活性的优势,广泛应用于定制零部件制造。
b. 电火花加工(EDM)电火花加工是通过电脉冲放电的方式在金属工件上形成微小的放电坑,从而实现零部件的精密加工。
材料受迫成形工艺技术

材料受迫成形工艺技术引言材料受迫成形工艺技术是一种常见的加工方法,通过对材料施加外力使其产生形变,从而实现零件的加工和制造。
本文将介绍材料受迫成形工艺技术的基本概念、应用领域、工艺流程以及未来的发展趋势。
基本概念材料受迫成形材料受迫成形是指通过施加外力使材料发生塑性变形的制造方法。
它包括了挤压、拉伸、压力和弯曲等多种成形方式。
在材料受迫成形过程中,外力会使材料发生形变,从而改变其形状和尺寸。
工艺参数在材料受迫成形工艺技术中,工艺参数是指影响成形过程和成形结果的各种参数。
包括施加的外力大小和方向、温度、成形速度等。
恰当的选择和控制工艺参数可以确保材料受迫成形工艺的质量和效果。
材料选择在材料受迫成形工艺技术中,材料的选择非常重要。
不同的材料在受力过程中会有不同的塑性变形行为和特性。
因此,根据需要选择适合的材料可以提高成形质量和效率。
应用领域材料受迫成形工艺技术在多个领域都有应用。
以下是一些常见的应用领域。
汽车制造材料受迫成形工艺技术在汽车制造中扮演着重要角色。
例如,通过挤压成形工艺可以生产汽车零件,如车身和发动机零件。
材料受迫成形工艺可以提高零件的质量和性能,并提高生产效率。
电子设备制造在电子设备制造中,材料受迫成形工艺技术可以用于制造电子设备的外壳和封装材料。
这些材料需要具备高强度、导热性能和电绝缘性能,通过合适的受迫成形工艺可以得到满足要求的产品。
材料受迫成形工艺技术在金属加工中应用广泛。
通过拉伸、压力和弯曲等工艺,可以将金属材料加工成各种形状和尺寸的零件。
例如,金属管的制造、金属板的拉伸成形等。
其他领域除了上述几个领域,材料受迫成形工艺技术在航空航天、船舶制造、建筑和机械工程等领域也有广泛的应用。
工艺流程材料受迫成形工艺技术的具体工艺流程可以根据不同的材料和成形方式而有所不同。
以下是一个通用的工艺流程。
1.材料准备:选择合适的材料,并按要求切割、预处理。
2.模具设计:根据零件的形状和尺寸设计或选择合适的模具。
材料成形技术基础知识点总结
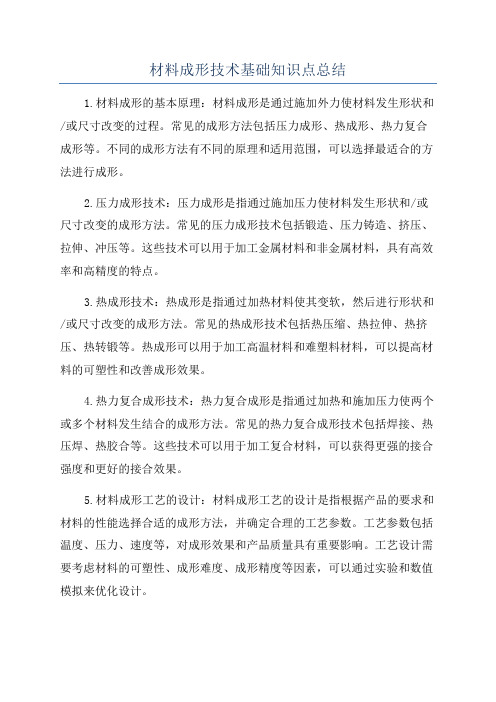
材料成形技术基础知识点总结1.材料成形的基本原理:材料成形是通过施加外力使材料发生形状和/或尺寸改变的过程。
常见的成形方法包括压力成形、热成形、热力复合成形等。
不同的成形方法有不同的原理和适用范围,可以选择最适合的方法进行成形。
2.压力成形技术:压力成形是指通过施加压力使材料发生形状和/或尺寸改变的成形方法。
常见的压力成形技术包括锻造、压力铸造、挤压、拉伸、冲压等。
这些技术可以用于加工金属材料和非金属材料,具有高效率和高精度的特点。
3.热成形技术:热成形是指通过加热材料使其变软,然后进行形状和/或尺寸改变的成形方法。
常见的热成形技术包括热压缩、热拉伸、热挤压、热转锻等。
热成形可以用于加工高温材料和难塑料材料,可以提高材料的可塑性和改善成形效果。
4.热力复合成形技术:热力复合成形是指通过加热和施加压力使两个或多个材料发生结合的成形方法。
常见的热力复合成形技术包括焊接、热压焊、热胶合等。
这些技术可以用于加工复合材料,可以获得更强的接合强度和更好的接合效果。
5.材料成形工艺的设计:材料成形工艺的设计是指根据产品的要求和材料的性能选择合适的成形方法,并确定合理的工艺参数。
工艺参数包括温度、压力、速度等,对成形效果和产品质量具有重要影响。
工艺设计需要考虑材料的可塑性、成形难度、成形精度等因素,可以通过实验和数值模拟来优化设计。
6.材料成形工具的设计与制造:材料成形工具是实现成形过程的重要设备,需要根据产品的形状和尺寸设计相应的工具。
工具设计包括毛坯设计、凸模设计、模具结构设计等。
材料成形工具的制造需要精密的加工工艺和高质量的材料,可以采用数控加工、电火花等先进技术来提高工具的精度和寿命。
7.材料成形过程的监测与控制:材料成形过程需要对温度、压力、力量、速度等进行监测和控制,以确保成形效果和产品质量的稳定。
常用的监测和控制技术包括传感器、自动控制系统等。
这些技术可以实时监测成形过程的参数,并根据需求调整工艺参数,以达到最佳的成形效果。
成形工艺技术

成形工艺技术成形工艺技术是一门工程技术学科,通过对工件的成型过程及其技术性能的研究,设计出成型方法和工艺流程,实现对原材料的加工和转化。
成形工艺技术广泛应用于制造业各个领域,包括金属加工、塑料加工、陶瓷加工等。
成形工艺技术的基本理论是原材料形变和流变性能的研究。
通过研究材料的流动行为,可以设计出合适的成型设备和工艺参数,实现对原材料的精确控制。
成形工艺技术还研究了原材料的热力学性质、机械性能、物理性能等,为工艺设计提供了基础。
成形工艺技术的一大特点是可以大规模生产相同的零部件。
通过模具制造和成型设备的使用,可以在短时间内批量生产大量的相同产品。
与传统的手工制造相比,成形工艺技术大大提高了生产效率,降低了人力成本。
成形工艺技术的应用非常广泛,其中最常见的就是金属成形技术。
金属成形技术包括锻造、压力成型、铸造等。
锻造是将金属材料加热至一定温度后,利用力使其发生塑性变形,从而得到所需形状的工艺。
压力成型是通过施加压力使金属原材料变形,从而得到所需形状的工艺。
铸造是将金属熔化后,倒入模具中进行冷却凝固,最终得到所需形状的工艺。
除了金属成形技术,塑料成形技术也是成形工艺技术的重要组成部分。
塑料成形技术包括注塑成型、挤出成型、吹塑成型等。
注塑成型是将塑料原料加热熔融后,通过注射装置将其注入模具中,在模具中冷却硬化,最终得到所需形状的工艺。
挤出成型是将塑料原料加热熔融后,通过挤出机将其从模具中挤出,最终得到所需形状的工艺。
吹塑成型是将塑料原料加热熔融后,通过吹塑机在模具中进行吹塑,最终得到所需形状的工艺。
另外,成形工艺技术还涉及到陶瓷成形技术、橡胶成形技术等。
陶瓷成形技术包括注浆成型、挤出成型、压制成型等。
橡胶成形技术包括压制成型、挤出成型、注射成型等。
这些成形技术在陶瓷制造和橡胶制造领域得到了广泛应用。
总之,成形工艺技术在制造业中发挥了重要作用。
通过成形工艺技术,可以实现对原材料的精确控制,大规模生产相同的零部件,提高生产效率和降低成本。
01材料锻造冲压及特种成形工艺技术

01材料锻造冲压及特种成形工艺技术材料锻造、冲压及特种成形工艺技术是现代工业生产中不可或缺的重要工艺技术之一、在材料加工过程中,通过锻造、冲压和特种成形工艺技术,可以将金属材料加工成所需形状和尺寸的零件或产品,提高材料的性能和使用价值。
本文将详细介绍材料锻造、冲压及特种成形工艺技术。
一、材料锻造技术材料锻造是指利用压力对金属材料进行塑性变形的一种加工方法。
在锻造过程中,通过施加压力和温度来改变材料的形状和性能,使其满足产品的要求。
锻造工艺一般分为自由锻造、模锻和闭式锻造三种。
1.自由锻造自由锻造是指材料在没有任何限制条件下进行锻造的一种方法。
在自由锻造中,锻件的形状和尺寸主要由锻造前的锻坯决定。
自由锻造常用于锻制体积较大的零件,例如轴类零件、铸造坯件的整形等。
2.模锻模锻是指利用模具对金属材料进行锻造的一种方法。
在模锻过程中,材料在模具的限制下,被迫塑性变形成所需的形状和尺寸。
模锻可以生产高精度、高质量的锻件,广泛应用于航空、汽车、机械等领域。
3.闭式锻造闭式锻造是指利用模具对金属材料进行锻造的一种方法,与模锻不同的是,闭式锻造在锻造过程中,模具会完全封闭锻件的形状和尺寸。
闭式锻造可以生产复杂形状的零件,如齿轮、曲轴等。
二、冲压技术冲压技术是指利用模具对金属材料进行冲击或扭转的一种加工方法。
在冲压过程中,通过冲击或扭转,将金属材料加工成所需的形状和尺寸。
冲压技术广泛应用于汽车、电子、家电等行业。
冲压技术主要分为冲切、冲孔和冲凸等几种方法。
1.冲切冲切是指利用模具对金属材料进行剪切的一种方法。
通过冲切,可以将金属材料切割成所需形状和尺寸的零件。
冲切广泛应用于金属板材的切割、下料等工序。
2.冲孔冲孔是指利用模具对金属材料进行冲击的一种方法。
通过冲击,可以在金属材料上形成孔洞。
冲孔广泛应用于金属零件的孔加工、标牌制作等。
3.冲凸冲凸是指利用模具对金属材料进行扭转的一种方法。
通过扭转,可以在金属材料上形成凸起或凹陷的形状。
先进制造技术课程自主学习教学模式探索

先进制造技术课程自主学习教学模式探索作者:董雁来源:《中国科教创新导刊》2013年第13期摘要:针对先进制造技术课程内容广、更新快、知识交叉等特点以及影响学生建立应用先进制造技术意识的教学目的,提出以自主学习为主要教学方式,通过课程网站学习教学基本内容,通过自主讲座培养学生获取制造技术最新发展的意识和能力,锻炼学生资料查阅与整理,语言与文字表达等多方面的综合素质。
关键词:先进制造技术教学内容自主学习中图分类号:G712 文献标识码:A 文章编号:1673-9795(2013)05(a)-0037-02先进制造技术是制造业为了适应现代生产环境以及市场动态变化,在传统制造技术基础上通过不断吸收科学技术最新成果而逐渐发展起来的一个新兴技术群,包括现代设计技术、先进制造工艺技术、制造系统综合自动化技术和现代管理技术。
机械类本科专业开设先进制造技术课程,可以大大拓宽学生专业视野,掌握制造技术最新发展,以适应现代制造企业对人才的需求,其重要性日趋显著。
然而,由于全球高新技术的高速发展以及先进技术的庞大信息量,决定了本课程教学实施的难度。
传统的以教师为主、学生为客的教学模式,教师要全面了解先进制造技术的最新动态,往往心有余而力不足,学生被动接受教学内容,学习积极性往往不高。
而且,先进制造技术发展日新月异,培养学生获取制造技术最新发展的能力显得更为重要。
自主学习是与传统的接受性学习相对应的一种现代学习模式,通过课程网站学习先进制造技术课程的教学基本内容,通过自主讲座,培养学生获取制造技术最新发展的能力,为日后推广先进制造技术,提高我国机械制造技术水平奠定基础。
1 先进制造技术课程的特点(1)内容综合性。
先进制造技术是一门交叉学科,涉及众多学科的知识内容,授课教师不可能对所有领域都进行过深入研究,采用多位教师授课的教学模式效果会好一点,但一般普通本科院校均不具备这样的条件。
对于不是自己研究方向的内容,往往通过资料查阅和整理再灌输给学生,这样教学效果很难提高。
第三章 先进制造工艺技术 第二节 材料受迫成形工艺技术

卧式离心铸造
挤压铸造
2、清洁铸造技术
1、采用洁净能源。以铸造焦代替冶金焦,以少粉尘、少熔渣的感应电炉 熔化代替冲天炉熔化,以减轻熔炼过程中对空气的污染。 2、采用无砂或少砂的特种铸造工艺,如压力铸造、金属型铸造等,改善 操作者工作环境。 3、研究并推广使用清洁无毒的工艺材料。 4、采用高溃散性型砂工艺,如树脂砂、改性脂硬化水玻璃砂工艺 5、研究开发多种废弃物的再生和综合利用技术,如铸造旧砂的再生回收 技术、熔炼炉渣的处理和综合利用技术。 6、研制开发铸造机器人或机械手,以代替工人在恶劣条件下工作。
超塑性拉伸的Zn-Al合金试样
经典的超塑性气 压阴模成形工艺 示意图
超塑性气压成形过程中施加“背压”的作 用—在材料中形成静水压,防止产生“空 洞”。
超塑性成形的火箭发动机涡轮盘(材料Ti-6Al-4V合金)
超塑性成形的飞机发动机压气 机盘(材料:TC11钛合金)
3、精密冲裁工艺
精密冲裁是使冲裁件呈纯剪切分离的冲裁工艺,在普通冲 裁工艺基础上通过改进模具来提高制件的精度,使冲裁件 尺寸精度可达IT6~IT9级,断面粗糙度Ra值为1.6~0.4μm 。 精密冲裁通常通过光洁冲裁、负间隙冲裁、带齿圈压板冲 裁等工艺手段来实现。
金属的超塑性主要有两种类型:
(1)细晶超塑性,又称组织超塑性或恒温超塑性,其超塑性产生的内
在条件是具有均匀、稳定的等轴晶组织,晶粒尺寸通常小于10微米; 外在条件是应变速率要比普通金属应变速率至少低一个数量级; (2)相变超塑性,又称为环境超塑性,是指在材料相变点上下进行温度 变化循环的同时对试样加载,经多次循环试样得到积累的大变形。
热固性材料
在受热或其它条件下能固化成不熔不溶性物质的塑 料 ,其分子结构最终为体型结构。(变化过程不 可逆) (酚醛塑料、氨基塑料、环氧塑料、聚邻苯二甲酸 、二烯丙酯、有机硅塑料、硅酮塑料
《材料成形工艺》课件

在建筑领域中,焊接工艺被用 于钢结构、钢筋混凝土结构的
连接和加固。
05
热处理工艺
热处理工艺的原理
热处理是通过加热、保温和冷却的方式改变金属材料的内部组织结构,以达到改善其力学性能、提高 耐腐蚀性和加工性的目的。
热处理过程中,金属材料内部的原子或分子的运动速度会随着温度的升高而加快,当温度达到一定的临 界点时,原子或分子的排列会发生改变,形成新的晶体结构。
焊接工艺的原理基于金属的热传导和热对流,以及液态金属的流动和结晶。
焊接工艺的种类
01
熔焊
将待焊接的金属加热至熔化状态,然后通过液态金属将两块金属连接在
ห้องสมุดไป่ตู้
一起。常见的熔焊方法有电弧焊、气焊等。
02
压焊
通过施加压力将两块金属连接在一起,常见的压焊方法有电阻焊、摩擦
焊等。
03
钎焊
利用熔点低于母材的钎料,将其加热至熔化状态,润湿并填满母材接头
模锻
将金属坯料放入模具中,在压力 作用下进行塑性变形,以获得所 需形状和尺寸的加工方法。
特种锻造
针对特殊要求或特殊材料,采用 特殊的工艺和工具进行塑性变形 的加工方法。
锻造工艺的应用
航空航天领域
由于对材料性能要求极高,锻造工艺广泛应用于航空航天领域的 各种零件制造,如发动机叶片、涡轮盘等。
汽车工业
热处理工艺的原理就是通过控制加热、保温和冷却三个阶段的时间和温度,使金属材料内部组织结构发 生变化,从而达到所需的性能要求。
热处理工艺的种类
第一季度
第二季度
第三季度
第四季度
退火
将金属材料加热到一定 温度后保温一段时间, 然后缓慢冷却至室温。 退火可以消除金属内部 的应力,提高其塑性和 韧性。
材料受迫成形工艺技术教学讲义共26页

21、要知道对好事的称颂过于夸大,也会招来人们的反感轻蔑和嫉妒。——培根 22、业精于勤,荒于嬉;行成于思,毁于随。——韩愈
23、一切节省,归根到底都归结为时间的节省。——马克思 24、意志命运往往背道而驰,决心到最后会全部推倒。——莎士比亚
25、学习是劳动,是充满思想的劳动。——乌申斯基
谢谢!
ቤተ መጻሕፍቲ ባይዱ
材料受迫成形工艺技术 教学讲义
6、纪律是自由的第一条件。——黑格 尔 7、纪律是集体的面貌,集体的声音, 集体的 动作, 集体的 表情, 集体的 信念。 ——马 卡连柯
8、我们现在必须完全保持党的纪律, 否则一 切都会 陷入污 泥中。 ——马 克思 9、学校没有纪律便如磨坊没有水。— —夸美 纽斯
10、一个人应该:活泼而守纪律,天 真而不 幼稚, 勇敢而 鲁莽, 倔强而 有原则 ,热情 而不冲 动,乐 观而不 盲目。 ——马 克思
3.2材料受迫成形工艺技术

3.精密冲裁工艺 精密冲裁是使冲裁件呈纯剪切分离的冲裁工艺,它是在 普通冲裁工艺基础上通过模具改进来提高制件精度,使冲 裁件尺寸精度可达IT6-IT9级,断面粗糙度Ra值为1.60.4μm。 (1)光洁冲裁 光洁冲裁又称小间隙小圆角冲裁。与普通 冲裁相比,其特点是采用了小圆角刃口和很小的冲模间隙。 (2)负间隙冲裁 负间隙冲裁的特点是凸模尺寸大于凹模 型腔尺寸,产生负的冲裁间隙负间隙冲裁实质上为冲裁与 整修两者的复合工序。
目前,较为流行一种冷温模锻成形技术。所谓冷温模锻, 是指金属材料在室损或再结晶温度以下的塑性成形工艺,又 称冷挤压成形。
2.超塑性成形 超塑性是指材料在一定的内部组织条件(如晶粒形状及尺寸、 相变等)和外部环境条件(如温度、应变速率等)下,呈现出异 常低的流变抗力、异常高的伸长率现象。有人将伸长率超过 100%的材料称之为超塑性材料。 金属的超塑性主要有两种类型:①细晶超塑性;②相变超 塑性;目前研究和应用较多的是细晶超塑性。 超塑性成形工艺包括超塑性等温模锻、挤压、气压成形、 真空成形、模压成形等;对于薄板的超塑性成形加工,气压 成形应用最多。 超塑性成形需要较高恒定的温度条件,较低的成形政变速 率,生产率较低.模具需耐高温,这些不足因素致使该工艺 没有得到较大推广的原因。
2.粉末锻造成形工艺过程 粉末锻造成形的工艺过程可归纳为:粉末制取-模压成形 -型坯烧结-锻前加热-锻造-后续处理。 3.粉末锻造模具
粉末锻造一般都是在闭式模腔内进行,因此对模具精度 要求较高。
四、高分子材料注射成形
高分子材料是以高分子化合物为主要组分的材料。高分 子化合物是指相对分子质量(分子量)很大的化合物,其分子 量一般在5000以上 。 高分子化合物包括有机高分子化合物和无机高分子化合物 两类。有机高分子化合物又分为天然的和合成的。 机械工程中使用的高分子材料主要是人工合成的有机高分 子聚合物(简称高聚物),例如塑料、合成橡胶、合成纤维、 涂料和胶接剂等。 在21世纪的今天,高分子材料已与钢材、水泥、木材并 列为四大基本工程材料,已经成为支持人类文明、社会发展 和科学进步的重要物质基础。高分子材料成形加工技术主要 有注射成形、挤出成形、吹塑成形、模
材料成形工艺学

材料成形工艺学
摘要:
一、材料成形工艺学的概念
1.材料成形工艺学的定义
2.材料成形工艺学的研究对象
二、材料成形工艺学的发展历程
1.古代材料成形工艺
2.现代材料成形工艺的发展
3.我国材料成形工艺学的进展
三、材料成形工艺的分类
1.金属材料成形工艺
2.非金属材料成形工艺
3.复合材料成形工艺
四、材料成形工艺的应用领域
1.制造业
2.航空航天
3.汽车工业
4.医疗器械
5.其他领域
五、材料成形工艺的发展趋势
1.智能制造与数字化
2.绿色制造与可持续发展
3.新材料的研究与应用
4.跨学科整合与创新
正文:
材料成形工艺学是一门研究材料在力的作用下发生形状变化、尺寸变化或内部组织结构变化的学科。
它涉及到各种材料,如金属、非金属和复合材料等,并广泛应用于制造业、航空航天、汽车工业、医疗器械等领域。
自古以来,人类就已经开始研究材料成形工艺。
从最初的陶器、青铜器到后来的钢铁器具,都是材料成形工艺发展的见证。
进入现代社会,随着科技的发展,材料成形工艺得到了迅猛发展,出现了许多新的工艺方法,如锻造、铸造、挤压、塑性加工等。
在我国,材料成形工艺学的研究和应用也取得了显著的成就。
不仅在传统领域如钢铁、有色金属等方面取得了突破,还在新材料、绿色制造等方面取得了重要进展。
随着社会的进步和科技的发展,材料成形工艺学将继续发挥重要作用。
- 1、下载文档前请自行甄别文档内容的完整性,平台不提供额外的编辑、内容补充、找答案等附加服务。
- 2、"仅部分预览"的文档,不可在线预览部分如存在完整性等问题,可反馈申请退款(可完整预览的文档不适用该条件!)。
- 3、如文档侵犯您的权益,请联系客服反馈,我们会尽快为您处理(人工客服工作时间:9:00-18:30)。
2.粉末锻造成形工艺过程 粉末锻造成形的工艺过程可归纳为:粉末制取-模压成形 -型坯烧结-锻前加热-锻造-后续处理。 3.粉末锻造模具
粉末锻造一般都是在闭式模腔内进行,因此对模具精度 要求较高。
四、高分子材料注射成形
高分子材料是以高分子化合物为主要组分的材料。高分 子化合物是指相对分子质量(分子量)很大的化合物,其分子 量一般在5000以上 。 高分子化合物包括有机高分子化合物和无机高分子化合物 两类。有机高分子化合物又分为天然的和合成的。 机械工程中使用的高分子材料主要是人工合成的有机高分 子聚合物(简称高聚物),例如塑料、合成橡胶、合成纤维、 涂料和胶接剂等。 在21世纪的今天,高分子材料已与钢材、水泥、木材并 列为四大基本工程材料,已经成为支持人类文明、社会发展 和科学进步的重要物质基础。高分子材料成形加工技术主要 有注射成形、挤出成形、吹塑成形、压延成形、压制成形等。
第三章 先进制造工艺技术
第二节 材料受迫成形工艺技术
制造加工工艺实质上就是一种材料成 形工艺。
依据材料成形学观点,从物质组成方式上可把机械零件 成形方法分为如下三种类型: ①受迫成形 ②去除成形
③堆积成形
轻量化、精确化、高效化是未来材料成形加工技术的重 要发展方向。
一、精密洁净铸造成形
1.精确铸造成形技术
三、粉末锻造成形工艺
1.粉末锻造成形工艺特点 粉末锻造成形是将传统的粉末冶金和精密锻造结合起 来的一种新工艺。 粉末锻造成形兼有粉末冶金和精密锻造两者的优点。 与普通银造相比较,其优越性表现为;①能源消耗低, 材料利用率高,如粉末锻造连杆是普通锻造能耗的49%, 材料利用率达90%以上,而普通锻造只有40%—60%; ②锻件精度高,力学性能好,内部组织无偏析,无各向 异性;③疲劳寿命高,例如粉末锻造连杆的疲劳寿命比 普通锻造提高了20%,高速钢工具寿命可提高两倍以上。
(4)特种铸造技术 包括压力铸造、低压铸造、熔模铸造、 真空铸造、挤压铸造等。以金属模取代砂型模,以非重力浇 注取代重力挠注,可使铸件尺寸精确,表面光洁,内部致密, 铸件可实现少切削或无切削加工。但每一种特种铸造方法都 有其自身的特点,应用场合都有一定的局限性。
2.清洁(绿色)铸造技术
日趋严格的环境与资源的约束,清洁铸造已成为21世 纪铸造生产的重要特征。清洁铸造技术的主要内容有:
3.模具滑合成形法
由日本制钢所开发,可用于中空制品和不同树脂的复合 体制造。与吹塑模相比,该法制品具有表面精度好、尺寸精 度高、壁厚均匀日设计自由度高的优点。
4.剪切场控制取向成形法
该法通常用于玻纤或碳纤维增强塑料制品的成形。该 技术不仅可提高熔接痕强度,也可消除制品内部的缩孔或 表面的缩痕。 5.直接注射成形法 主要用于高浓度玻璃纤维、碳纤维或有机、无机粉体等 复合材料制品的注射成形。直接注射成形法不需经挤出机 混炼造粒过程,可以将掺棍物直接注射成制品,简化了工 艺过程,有较大的经济性。
注射成型压机
熔融成型
注射原理
注射成型产品
压注成型压机
压注原理
压注成型产品
原理
吹塑成型产品
1.气体辅助成形
气体辅助成形是在熔融塑料充填(不完全充填)完成后, 利用型腔内熔融体冷却前的时间差,将具有一定压力的 惰性气体迅速地注入成形体内部,此时气体可在成品壁 较厚的部分形成空腔,这样即能使成品壁厚变得均匀, 防止产生表面缩痕或收缩翘曲,使制品表面平整光滑, 提高表面质量。
(3)带齿圈压板精冲 带齿圈压板的冲裁工艺可由原 材料直接获得精度高、剪切面光洁的高质量冲压件,并 可与其他冲压工序复合进行如沉孔、半冲孔、压印、弯 曲、内孔翻边等精密冲压成形。
4.辊轧工艺 辊轧工艺是用轧辊对坯料进行连续变形的压力加工方法, 具有生产率高、质量好、低和材料消耗少的优点。 (1)辊锻轧制 辊锻是将轧制工艺应用于锻造生产的一种 新工艺。辊锻既可作为模锻的制坯工序,也可直接生产锻件, 主要用于:①扁断面的长杆件,如扳手、链环等;②带有不 变形头部而沿长度方向横截面面积递减的锻件。 (2)辗环轧制 辗环轧制是用来扩大环形坯料的外径和 内径,从而获得各种零件的轧制方法。
(3)消失模铸造 消失模铸造工艺是利用泡沫塑料作为铸 造模样,直接在模样四周填充型砂,不分上下模。由于泡沫 塑料模样在浇注过程中被熔融的浇注液气化,因而可避免在 做砂型时由于起模以及刷涂料时所引起的砂型馈散所造成铸 件精度及表面质量的下降,使其完全等同于模样的水平。模 造型可消除起模斜度,可减少铸件壁厚,能够获得表面光洁、 尺寸精确、无飞边的少无余量的精密铸件。这种铸造工艺已 在国内外得到广泛应用,并被称为“明天的铸造新技术”。
1)采用洁净的能源
2)采用无砂和少砂的特种铸造工艺
3)研究并推广使用清洁无毒的工艺材料 4)采用高溃散性型砂工艺 5)研究开发多种废弃物的再生和综合利用技术 6)研制开发铸造机器人或机械手,以代替工人在恶劣 条件下工作。
3.铸造过程计算机模拟 铸造过程计算机仿真可在计算机上实现试浇,预测显示充 型及凝固过程随时间流动及温度的变化,预测显示因工艺不 合理而产生的铸造缺陷,可对各种不同铸造工艺方案做出最 优的选择。
反光镜玻璃模
绝缘陶瓷模
大型覆盖件模
密封圈挤出模
轮胎橡胶模
保险杠注射模
轮毂压铸模
本节结束
气辅成型塑件
模具配置气针装 置,由气体产生器 (惰性气体)向气 针装置供气,以实 现气辅。 气辅模具
2.注射压缩成形法
注射压缩成形法有整体压缩法和部分压缩法之分。注射 压缩成形法的优点是可以采用较低的注射压力成形簿壁制品 或需较大成形压力的制品,一般适用于流动性较差且薄壁的 制品,如高分子PC或纤维填充工程塑料等。
二、精确高效金属塑性成形工艺
1.精密模锻工艺
精密模锻是在模锻设备上锻造出锻件形状复杂、精度高 的模锻工艺。
为了最大限度地减少氧化,提高精锻件的质量,精锻时 采用较低的加热温度。对于碳素钢,精锻一般在900450℃之间,又称低温模锻。精密模锻的锻件精度在很大程 度上取决于锻模的加工精度,锻模精度要求比锻件精度高 1—2级。模具型腔需开排气孔,以减小金属流动阻力。
目前,较为流行一种冷温模锻成形技术。所谓冷温模锻, 是指金属材料在室损或再结晶温度以下的塑性成形工艺,又 称冷挤压成形。
2.超塑性成形 超塑性是指材料在一定的内部组织条件(如晶粒形状及尺寸、 相变等)和外部环境条件(如温度、应变速率等)下,呈现出异 常低的流变抗力、异常高的伸长率现象。有人将伸长率超过 100%的材料称之为超塑性材料。 金属的超塑性主要有两种类型:①细晶超塑性;②相变超 塑性;目前研究和应用较多的是细晶超塑性。 超塑性成形工艺包括超塑性等温模锻、挤压、气压成形、 真空成形、模压成形等;对于薄板的超塑性成形加工,气压 成形应用最多。 超塑性成形需要较高恒定的温度条件,较低的成形政变速 率,生产率较低.模具需耐高温,这些不足因素致使该工艺 没有得到较大推广的原因。
3.精密冲裁工艺 精密冲裁是使冲裁件呈纯剪切分离的冲裁工艺,它是在 普通冲裁工艺基础上通过模具改进来提高制件精度,使冲 裁件尺寸精度可达IT6-IT9级,断面粗糙度Ra值为1.60.4μm。 (1)光洁冲裁 光洁冲裁又称小间隙小圆角冲裁。与普通 冲裁相比,其特点是采用了小圆角刃口和很小的冲模间隙。 (2)负间隙冲裁 负间隙冲裁的特点是凸模尺寸大于凹模 型腔尺寸,产生负的冲裁间隙负间隙冲裁实质上为冲裁与 整修两者的复合工序。
(1)自硬砂精确砂型铸造 自硬树脂砂具有高强度、高精度、 高溃散性和低的造型造芯劳动强度,是一种适合各种复杂 中、小型铸件型芯制作的高效工艺。近年来采用冷芯露盒 树脂砂芯发展起来的“精确砂芯造型”技术,可以生产壁 厚仅有2.5mm的缸体、缸盖、排气歧管等复杂铸件。
(2)高紧实砂型铸造 铸型的高紧实率是当代造型机的发展 方向,高紧实率及其均匀性可提高铸型强度、刚度、硬度 和精度,可减少金属液浇注和凝固时型壁的移动,提高工 艺的出品率,降低金属消耗,减少缺陷和废品。高紧实率 铸型的获得,可通过真空吸砂、气流吹砂、气动压实、液 动挤压和气冲等工艺手段。 由于紧实度提高,铸件的精度、表面粗糙度可提高2—3 级、适用于大批量铸件的生产。