半导体工艺2
半导体湿法工艺

半导体湿法工艺
半导体湿法工艺是半导体制造过程中的一种重要工艺,也被称为湿法腐蚀或湿法刻蚀。
该工艺通过使用化学腐蚀剂(如酸、碱等)来将材料表面的一层或多层材料去除,以达到改变该物质表面性质的目的。
半导体湿法工艺主要用于制备氮化硅、氧化铝、氧化硅等材料的薄膜,以及制造导电铜、金属码盘等电子元器件。
半导体湿法工艺具有操作简便、加工效率高、成本低等优点,但同时也存在环境污染、产生腐蚀废液等问题,需要加强环保措施和处理方法。
45nm,半导体工艺的里程碑:Intel Core 2 Extreme QX9650

一
上 所 集 成 的 晶体 管 数 量 大 约 每 两 年 增 长 倍 ,这 便 是 我 们 所 熟 知 的 摩 尔 定 律 。
4 纳 米 制 造 工艺 的 应 用 ,使 英 特 尔 新 一 5
是 目 前 英 特 尔 最 高 端 的 一 款 桌 面 级 处 代 处 理 器 再 次 享 受 了 晶 体 管 数 量 的 大 幅 e rn 理 器 产 品 , 用 于 取 代 之 前 的 旗 舰 产 品 度 提 升 :P n y 双 核 处 理 器 的 核 心面 积 I t l o e E te QX6 5 。作 n e C r 2 x r me 80 为一颗面 向骨灰级 用户的 四核处理器 ,
台式机& 笔记本 电脑
2 H P vI n DX 2 P a ii H o 2 D L X S 2 8 E L P 4 0
4 7九州风神笔记本散热套件
4 AS S MW 2 I 8 U 2 C
服务器
3 AS S R 61 E 4 U S1 - 5 4 It l t a ly 0 ne S o k e
3 8艾维特G 68 D 0 4 6金士顿存储卡
5 AP -M G U B1 6 C E P O 5 W a o B mb o F N 9 c m a o U
配件
1 1 t{ C r 2 xr me n e o e E te QX 6 0 0 9 5 4 AS S M a i s F r l E 1 U xmu o mu a S 4 G F re 8 0 GT 9 e oc 8 0
Y r Id ofl k e 四核处理器 。
并 没 有 像 大 多 数 人 所 期 待 的那 样 实 现 二
半导体器件原理和工艺2

半导体器件
晶体管的频率特性---小信号模型
▪ 小信号工作条件:
➢ 输入信号电压以及输出信号电压都远小于热电压 (kT/q)
vBE VBE vbe iC IC ic
半导体器件
小信号模型-1
i1
i2
v1
T
v2
短路输入导纳 短路反向跨导纳
短路正向跨导纳 短路输出导纳
半导体器件
h参数 短路输入阻抗
小信号模型-2
短路正向电流传输系 数、即电流增益
开路反向电压传输系 数,即电压反馈系致
半导体器件
开路输出导纳
小信号模型-3
共发射极h参数等效电路
b vbe
c vce e
半导体器件
小信号等效电路
▪ 混合模型
g
-g
gm
go
由E-M方程:
正向有源区
半导体器件
混合模型-1
▪ 跨导gm
1. gm正比于Ic,反比于T。 2. gm只决定于工作电流及工作温度,与器件所用材
半导体器件
Bardeen, Brattain, and Schockley 获1956年诺贝尔物理奖
晶体管的特性
半导体器件
半导体器件
理想NPN掺杂分布
▪ 集电结外延, 发射结离子 注入
eb
半导体器件
c
晶体管的静电特性
▪ 两个独立的PN结构成
N+
P
N
半导体器件
背靠背二极管
半导体器件
工作原理
半导体器件
特征频率和截止频率
▪ 特征频率fT和截止频率f 是根据hFE随频率的变化 关系定义的
半导体器件
特征频率和截止频率-1
半导体八大工艺名称

半导体八大工艺名称1. 硅晶圆制备工艺硅晶圆制备是半导体制造过程的第一步,也是最为关键的一步。
它是指将高纯度的硅材料通过一系列的工艺步骤转化为薄而平整的硅晶圆。
硅晶圆制备工艺主要包括以下几个步骤:(1) 单晶生长单晶生长是将高纯度的硅材料通过熔融和凝固的过程,使其在特定的条件下形成单晶结构。
常用的单晶生长方法包括Czochralski法和区熔法。
(2) 切割切割是将生长好的硅单晶材料切割成薄片的过程。
常用的切割方法是采用金刚石刀片进行切割。
(3) 研磨和抛光研磨和抛光是将切割好的硅片进行表面处理,使其变得平整光滑的过程。
研磨通常使用研磨机进行,而抛光则使用化学机械抛光(CMP)工艺。
(4) 清洗清洗是将研磨和抛光后的硅片进行清洁处理,去除表面的污染物和杂质。
清洗过程通常采用酸洗和溶剂清洗的方法。
2. 光刻工艺光刻工艺是半导体制造中的一项关键工艺,用于将设计好的电路图案转移到硅晶圆上。
光刻工艺主要包括以下几个步骤:(1) 涂覆光刻胶涂覆光刻胶是将光刻胶涂覆在硅晶圆表面的过程。
光刻胶是一种敏感于紫外光的物质,可以通过紫外光的照射来改变其化学性质。
(2) 曝光曝光是将硅晶圆上的光刻胶通过光刻机上的光源进行照射,使其在特定区域发生化学反应。
曝光过程需要使用掩模板来控制光刻胶的曝光区域。
(3) 显影显影是将曝光后的光刻胶进行处理,使其在曝光区域发生溶解或固化的过程。
显影过程通常使用显影液进行。
(4) 清洗清洗是将显影后的硅晶圆进行清洁处理,去除残留的光刻胶和显影液。
3. 离子注入工艺离子注入工艺是将特定的离子注入到硅晶圆中,以改变其电学性质的过程。
离子注入工艺主要包括以下几个步骤:(1) 选择离子种类和能量选择合适的离子种类和能量是离子注入工艺的第一步。
不同的离子种类和能量可以改变硅晶圆的导电性质。
(2) 离子注入离子注入是将选择好的离子通过离子注入机进行注入的过程。
离子注入机通过加速器将离子加速到一定的能量,并将其注入到硅晶圆中。
半导体工艺等离子体技术

半导体工艺等离子体技术1. 嘿,你知道半导体工艺里的等离子体技术吗?那可真是个超酷的玩意儿!就像一群隐形的小工匠,在微观世界里大显身手。
比如说在芯片制造的时候,等离子体就像一群超级微小的雕刻师,精准地把那些复杂的电路图案刻在硅片上。
这要是没有等离子体技术,就像盖房子没有工人一样,芯片哪能那么精致又好用呢?2. 半导体工艺中的等离子体技术啊,简直是魔法一样的存在!我给你说,这等离子体就像是一群微观世界的精灵,在半导体的材料里穿梭、工作。
你看啊,在蚀刻工艺中,它就像一把把无形的小刷子,把不需要的部分刷掉。
要是没有它,那些半导体器件就会像没整理过的杂乱房间,功能乱七八糟的,多糟心啊!3. 哇塞,半导体工艺的等离子体技术,你可不能小瞧!这就好比是一场微观世界的战斗,等离子体就是那英勇的战士。
比如说在清洗半导体表面的时候,等离子体就像一群清洁小卫士,把脏东西都给赶跑。
如果没有等离子体技术,半导体表面就像沾满灰尘的镜子,什么都看不清楚,还怎么发挥作用呢?4. 你了解半导体工艺里的等离子体技术不?这技术就像一把神奇的钥匙,打开了半导体制造的新世界。
在沉积工艺中,等离子体就像一个个勤劳的小搬运工,把需要的材料一层一层地堆积起来。
要是少了它,这就好比盖楼没有砖头,半导体器件根本就没法成型,这可太可怕了吧!5. 半导体工艺中的等离子体技术哟,那可不得了!它就像一个微观的厨师,精心烹饪着半导体材料。
像掺杂工艺中,等离子体就像调味料一样,精确地给半导体材料添加需要的元素。
要是没了这个技术,半导体就像没放盐的菜,淡而无味,根本没法达到我们想要的性能呢。
6. 嗨,我跟你讲半导体工艺的等离子体技术哈。
这就像是一场微观的音乐会,等离子体是那演奏的音乐家。
在光刻胶去除工艺里,等离子体就像灵动的音符,把光刻胶这个障碍物轻松消除。
要是没有等离子体技术,光刻胶就像卡在齿轮里的小石子,半导体的生产进程就会被卡住,那可太麻烦了!7. 哎呀,半导体工艺中的等离子体技术简直太神奇了!你可以把它想象成一群微观的画家,在半导体的画布上尽情创作。
半导体材料制备技术(二)
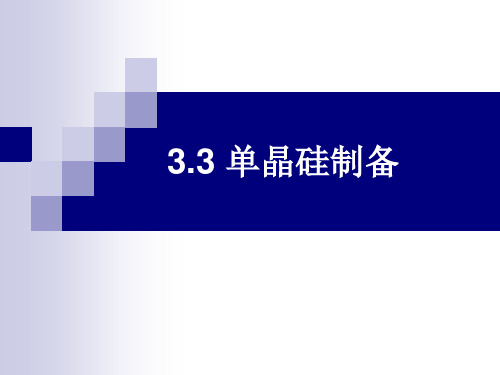
CL ≈ 5 × 1016 cm −3
m ≈ 0.057 mg
例题2 若要求拉出x= 处 ρ 例题 若要求拉出 =1/2处, = 1Ω ⋅ cm 的n-型硅单晶 型硅单晶 50g,问需要掺入砷杂质多少? ,问需要掺入砷杂质多少? 解:经计算得到
C0 ≈ 4 × 1015 cm −3
m=0.01mg
坩埚
主要要求: 主要要求: 坩埚材料在熔体中不溶或微溶; 坩埚材料在熔体中不溶或微溶; 不能从坩埚中引入有害杂质到熔体中; 不能从坩埚中引入有害杂质到熔体中; 坩埚要便于清洁处理; 坩埚要便于清洁处理; 气孔率低; 气孔率低; 容易机械加工或成型 拉制硅常用石英坩埚:纯度高; 拉制硅常用石英坩埚:纯度高;沾污小子半径与Si原子半 杂质元素的原子半径与 原子半 径之差是影响晶体完整性的重要因 素之一! 素之一!
2、 掺杂方式 、
(1)元素掺杂 ) 直接将纯杂质元素加入硅中。 直接将纯杂质元素加入硅中。这种方式适于制备 电阻率10 电阻率 -2~ 10-3Ωcm重掺单晶 重掺单晶 (2)母合金掺杂 ) 将杂质与Si制成合金 适于制备电阻率 制成合金。 制备电阻率10 将杂质与 制成合金。适于制备电阻率 -1Ω·cm 以上的单晶 (3)中子嬗变 )
中子在硅中的射程为90~100cm,杂质可以掺 , 中子在硅中的射程为 杂得很均匀很准确。 杂得很均匀很准确。
3 、掺杂的计算
计算掺杂量考虑因素: 计算掺杂量考虑因素:
1)原材料中杂质的含量 ) 2)杂质的分凝效应 ) 3) 杂质在真空中的蒸发效应 ) 4)坩锅和系统的玷污 )
(1)掺纯杂质元素重量的计算 ) 电阻率ρ与杂质浓度 电阻率ρ与杂质浓度CS关系如下
3.3.3 直拉法制备单晶硅工艺简介
半导体工艺(第1章2)衬底材料制备PPT课件

本征吸除:
在晶片内引入一些缺陷,以此吸除在表 面附近的杂质和缺陷;
写在最后
经常不断地学习,你就什么都知道。你知道得越多,你就越有力量 Study Constantly, And You Will Know Everything. The More
国内自造单晶炉设备图如下
直拉法制备单晶硅生长原理
点击视屏
单晶材料中的原生缺陷与有害杂质
硅单晶中存在多种原生缺陷和有害杂质。
宏观缺陷:
孪晶、裂纹、夹杂、位错等
原生缺陷:晶体生长过程中形成的缺陷
微缺陷 :微沉积
➢ 有害杂质是指会影响晶体性质的杂质或杂 质团:施主、受主、重金属、碱金属等。
➢ 孪晶:晶体中有两个或以上生长晶核
(2)晶片平整度:晶片微细加工中,晶片的 翘曲将对图形加工质量产生严重影响。欲 减少翘曲,必须增加晶片厚度、减小晶片 所受的加工应力。
2、器件浅结化对硅材料的要求
➢ 随着器件图形特征尺寸的缩小,器件结深也 越来越浅。
➢ 因此器件特性对硅材料表面质量和界面性质 更为敏感。
➢ 任何表面缺陷都可能引起器件失效或可靠性 降低。
➢ 材料中的缺陷和有害杂质是工艺诱生缺陷 的主要核化中心,因此必须通过单晶生长 过程中的质量控制和后续处理来提高单晶 的质量,使单晶材料趋于完美。
➢ 减少单晶材料缺陷和有害杂质的后续处理 方法通常采用吸除技术。 本征吸除 背面损伤 物理吸除 应力吸除 扩散吸除 吸除技术 溶解度增强吸除 化学吸除
物理吸除过程:
硅单晶体制备
➢多晶硅是制备单晶硅的原始材料 (一)多晶硅制备 多晶硅制备方式主要有三种: ✓ 四氯化硅氢还原法 ✓ 三氯氢硅氢还原法 ✓ 硅烷热分解法
2、半导体工艺原理-扩散

薄层电阻Rs(方块电阻) 表面浓度:扩散层表面的杂质浓度。
扩散层质量参数
方块电阻
方块电阻是标志扩散层质量的另一个重要参数, 一般用R□或Rs表示,单位是Ω/□ 。
2、恒定杂质总量扩散
扩散开始时,表面放入一定量的杂质源,而在以后的扩散
过程中不再有杂质加入。假定扩散开始时硅片表面极薄一层内
单位面积的杂质总量为 QT ,杂质的扩散长度远大于该层厚度,
则杂质的初始分布可取为 函数,扩散方程的初始条件和边界
条件为
0 N (x, t)dx QT
N (,t) 0
2 NS1
D1t1 D2t2
exp
x
2 j
4 D2t2
NB
即可解得
xj 2
D2t2
ln
2 NS1
NB
1
D1t1 D2t2
2
A
D2t2
掺杂分布控制:
3.3 简单理论的修正
前面得出的扩散后的杂质分布是采用理想化假设的结果, 而实际分布与理论分布之间存在着一定的差异,主要有:
1、二维扩散(横向扩散) 实际扩散中,杂质在通过窗口垂直向硅中扩散的同时,也 将在窗口边缘沿表面进行横向扩散。考虑到横向扩散后,要得 到实际的杂质分布,必须求解二维或三维扩散方程。横向扩散 的距离约为纵向扩散距离的 75% ~ 80% 。由于横向扩散的存在, 实际扩散区域大于由掩模版决定的尺寸,此效应将直接影响到 VLSI 的集成度。
2、杂质浓度对扩散系数的影响
前面的讨论假定扩散系数与杂质浓度无关。实际上只有当 杂质浓度比扩散温度下的本征载流子浓度 ni(T) 低时,才可认 为扩散系数与掺杂浓度无关。在高掺杂浓度下各种空位增多, 扩散系数应为各种电荷态空位的扩散系数的总和。
复旦半导体工艺教材Chapter-2
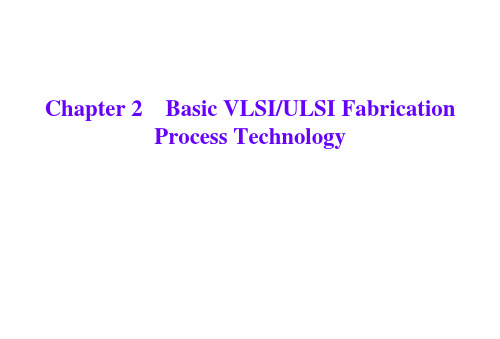
3. Selective Doping Technology
Si transistor — product of doping engineering
*Device type and performance--determined by impurity doping profile ( element, concentration, distribution)
➢ Lowest power consumption than all others ➢ Noise resistance and higher reliability ➢ Main stream of VLSI/ ULSI process since late 80’s
BiCMOS
➢ Combination of high speed and low power ➢ High process complexity
Low energy ion implant and shallow junction formation — of vital importance for nano-meter CMOS fabrication
High energy ion implant for n/p wells
Rapid thermal process (RTP) and dopant atom diffusion control
*Double diffused mesa transistor process
*Transistor by planar process
➢Transistor and other circuit elements formed by planar technology
✓On-chip resistor: by diffusion; poly-Si by deposition
半导体公司be2全流程的工作内容
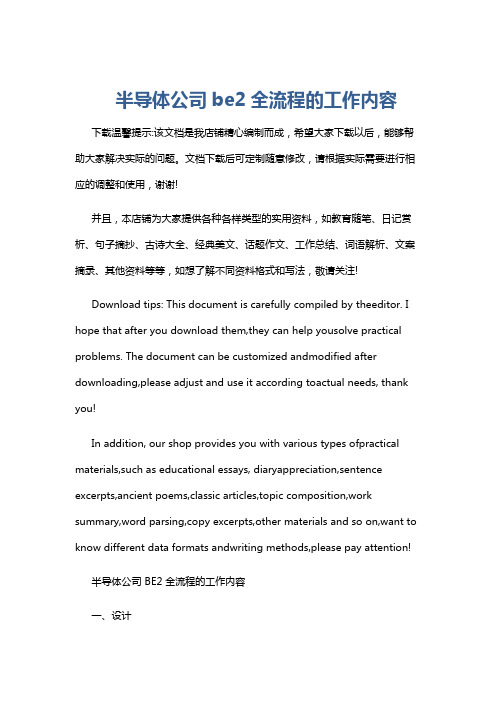
半导体公司be2全流程的工作内容下载温馨提示:该文档是我店铺精心编制而成,希望大家下载以后,能够帮助大家解决实际的问题。
文档下载后可定制随意修改,请根据实际需要进行相应的调整和使用,谢谢!并且,本店铺为大家提供各种各样类型的实用资料,如教育随笔、日记赏析、句子摘抄、古诗大全、经典美文、话题作文、工作总结、词语解析、文案摘录、其他资料等等,如想了解不同资料格式和写法,敬请关注!Download tips: This document is carefully compiled by theeditor. I hope that after you download them,they can help yousolve practical problems. The document can be customized andmodified after downloading,please adjust and use it according toactual needs, thank you!In addition, our shop provides you with various types ofpractical materials,such as educational essays, diaryappreciation,sentence excerpts,ancient poems,classic articles,topic composition,work summary,word parsing,copy excerpts,other materials and so on,want to know different data formats andwriting methods,please pay attention!半导体公司 BE2 全流程的工作内容一、设计1. 需求分析与客户沟通,了解产品需求和规格。
半导体制造工艺流程(钽电篇)
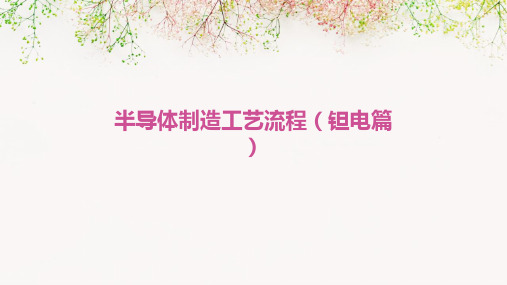
对未来发展的展望
01
02
03
04
随着科技的不断发展,半导体 制造工艺流程也在不断进步和 完善。未来,钽电制造工艺流 程将继续向着更高效、更可靠 、更环保的方向发展。
随着科技的不断发展,半导体 制造工艺流程也在不断进步和 完善。未来,钽电制造工艺流 程将继续向着更高效、更可靠 、更环保的方向发展。
随着科技的不断发展,半导体 制造工艺流程也在不断进步和 完善。未来,钽电制造工艺流 程将继续向着更高效、更可靠 、更环保的方向发展。
制造工艺流程的未来发展趋势
随着新材料和新技术的不断涌 现,制造工艺流程将朝着更高 效、更灵活、更环保的方向发 展。
未来制造工艺流程将更加注重 智能化和自动化技术的应用, 以提高生产效率和降低成本。
可持续发展将成为未来制造工 艺流程的重要考虑因素,以减 少对环境的影响并实现绿色生 产。
03
钽电制造工艺流程
制造工艺流程需要高度的技术和管理能力,以确保 生产过程中的一致性和可靠性。
制造工艺流程的重要性
02
01
03
制造工艺流程决定了半导体产品的性能和可靠性,是 实现产品差异化的关键因素。
随着技术的不断进步,制造工艺流程也需要不断更新 和改进,以适应市场需求和竞争环境。
制造工艺流程的优化和创新对于降低成本、提高生产 效率和产品质量具有重要意义。
由于其高熔点、高导电性和高强 度等特性,钽电在制造光电器件 中的电极、窗口材料等方面具有
优势。
在光电器件制造过程中,钽电的 应用能够提高器件的稳定性和可
靠性,延长器件的使用寿命。
钽电在其他领域的应用
除了在集成电路和光电器件制造中应 用外,钽电还广泛应用于其他领域。
这些应用都得益于钽电的高熔点、高 导电性和高强度等特性,使得它在各 种极端条件下都能保持稳定的性能。
平坦化工艺2

(5)磨粒尺寸、浓度及硬度
CMP的磨粒一般有SiO2,和Al2O 3其尺寸在 20~200nm 之间。一般情况下, 当磨粒尺寸增加, 抛光速率增加,但磨粒尺寸过小则易凝聚成团, 使硅 片表面划痕增加; 磨粒硬度增加, 抛光速率增加, 但划痕增加, 表面质量下降。磨粒的浓度增加时,材 料去除率也随之增加,但当磨粒浓度超过某一值时, 材料去除率将停止增加,维持一个常数值,这种现象 可称为材料去除饱和,但磨粒浓度增加, 硅片表面缺 陷(划痕)增加, 表面质量降低。
一 传统的平坦化技术
反刻
玻璃回流
旋涂膜层
1.1反 刻
概念:由表面图形形成的表面起伏可以用一层 厚的介质或其它材料作为平坦化的牺牲层来进 行平坦化,这一层牺牲材料填充空洞和表面的 低处,然后用干法刻蚀技术来刻蚀这一层牺牲 层,通过用比低处图形快的刻蚀速率刻蚀掉高 处的图形来使表面平坦化。 反刻不能实现全局的平坦化。
一般的化学机械抛光系统构造整个系统是由三 大部分组成。 1一个旋转的硅片夹持器 2承载抛光垫的工作台 3抛光浆料供给装置
Hale Waihona Puke 化学机械平坦化的原理图平坦化的4个术语
CMP设备
CMP是采用把一个抛光垫粘在转盘的表面来进行平坦化,在抛光的时 候一个磨头装有一个硅片,大多数的生产性抛光机都是有多个转盘合 抛光垫,以适应抛光不同材料的需要。
平坦化工艺
李传第 陈建
周天亮 邓应达
概要:
简单的说就是在晶片的表面保持平整平坦的工艺 随着半导体工业飞速发展,电子器件尺寸缩小, 要求晶片表面可接受的分辨率的平整度达到纳米级 。 传统的平面化技术,如选择淀积、旋转玻璃法等,仅 仅能够局部平面化技术,但是对于微小尺寸特征的电 子器件,必须进行全局平面化以满足上述要求。90年 代兴起的新型化学机械抛光技术则从加工性能和速度 上同时满足了硅片图形加工的要求,是目前几乎唯一 的可以提供全局平面化的技术。
半导体制造工艺 第2版

学习情景三
难以淀积合金材料
由于合金是两种金属材料组成,而两种金 属就会有两种不同的熔点,这使得利用蒸 发使合金材料按原合金比例淀积到硅片上 是不可能的;
常州信息职业技术学院
学习情景三
溅射
概念:
利用等离子体中的离子,对被溅镀物体 (粒子靶)进行轰击,使气相等离子体内 具有被溅镀物体的粒子,这些粒子淀积到 硅晶片上形成溅射薄膜;
常州信息职业技术学院
学习情景三
真空设备
机械泵 又称真空旋转泵,用来获得低真空的一种 抽气设备; 能从一个大气压开始抽气,真空度可达103Torr;
常州信息职业技术学院
机械泵结构示意图
学习情景三
常州信息职业技术学院
油泵扩散
学习情景三
原理:当机械泵抽气达到10-2Torr以后,再要 抽气,就要用到油扩散泵了(它的起始点必 须在10-2Torr); 工作时用电炉加热扩散泵油,使之沸腾, 产生大量油蒸汽; 油蒸汽通过各级喷嘴以较高的速率喷射出 来。系统中的气体分子不断作扩散运动, 一旦与油蒸汽分子相撞,就被油蒸汽分子 带走。因为油蒸汽分子的质量大,并且作 定向运动,所以气体分子就会被油蒸汽分 子带到前方;
常州信息职业技术学院
溅射示意图
学习情景三
常州信息职业技术学院
学习情景三
辉光放电
轰击靶材料的高能粒子是辉光放电产生的; 气,两个电极之间的距离为15cm,电压为 1.5kv,在玻璃管中引入一个电子,这个电 子在两个电极间的电场中加速,这个自由 电子有可能碰撞氩原子,把氩原子中的电 子激发出来,激发出来的电子就是轰击源 材料的轰击源;
常州信息职业技术学院
学习情景三
半导体工艺基础氧化

半导体工艺的重要性
半导体工艺是实现电子器件小型化、高性能化的 关键技术,对于推动电子工业的发展具有重要意 义。
随着科技的不断发展,半导体工艺在信息技术、 通信技术、人工智能等领域的应用越来越广泛, 已经成为现代社会不可或缺的重要技术之一。
半导体工艺的历史与发展
半导体工艺的发展经历了从晶体管到集成电路、再到微电子器件的过程,其发展历程与电子工 业的发展密切相关。
01 湿氧
湿氧气作为氧化剂,具有较高的氧化能力,适用 于大多数硅基材料的氧化。
02 高压氧气
高压氧气可以提高硅片的氧化速率,但设备成本 和维护成本较高。
03 其他氧化剂
如臭氧、二氧化氮等,适用于特定条件下的氧化 工艺。
其他辅助材料选择
01
02
03
添加剂
添加剂可以调节氧化速率 、改善二氧化硅层质量, 如掺氯硅片、掺硼硅片等 。
随着新材料、新技术的不断涌现,半导体工艺也在不断进步和完善,未来将朝着更小尺寸、更 高性能、更低成本的方向发展。
02
氧化工艺原理
氧化工艺定义
01
氧化工艺定义
氧化是半导体制造过程中的一种重要工艺,通过与氧气的反应,在半导
体表面形成一层氧化物薄膜。这层氧化物薄膜具有保护和钝化半导体的
作用,同时也可以作为掺杂的掩蔽膜。
氧化炉的安全操作规范
01 操作前检查
确保炉体、热电偶、温度 传感器等设备正常,无安 全隐患。
03 严格控制温度
避免超温导致设备损坏或
产品质量问题。
02 防止气体泄漏
确保炉膛密封良好,防止
有毒气体泄漏。
04 操作人员培训
操作人员应经过专业培训
,熟悉设备操作和安全规
wafersight 2+原理
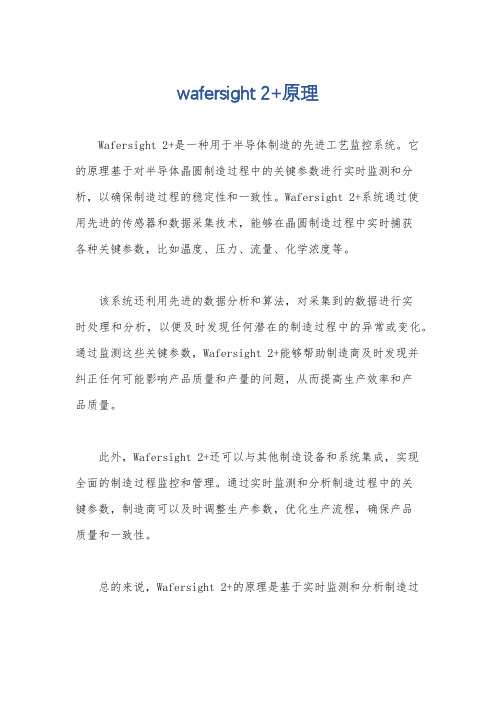
wafersight 2+原理
Wafersight 2+是一种用于半导体制造的先进工艺监控系统。
它
的原理基于对半导体晶圆制造过程中的关键参数进行实时监测和分析,以确保制造过程的稳定性和一致性。
Wafersight 2+系统通过使
用先进的传感器和数据采集技术,能够在晶圆制造过程中实时捕获
各种关键参数,比如温度、压力、流量、化学浓度等。
该系统还利用先进的数据分析和算法,对采集到的数据进行实
时处理和分析,以便及时发现任何潜在的制造过程中的异常或变化。
通过监测这些关键参数,Wafersight 2+能够帮助制造商及时发现并
纠正任何可能影响产品质量和产量的问题,从而提高生产效率和产
品质量。
此外,Wafersight 2+还可以与其他制造设备和系统集成,实现
全面的制造过程监控和管理。
通过实时监测和分析制造过程中的关
键参数,制造商可以及时调整生产参数,优化生产流程,确保产品
质量和一致性。
总的来说,Wafersight 2+的原理是基于实时监测和分析制造过
程中的关键参数,以实现对半导体晶圆制造过程的全面监控和管理,从而确保产品质量和生产效率。
半导体制造工艺流程简介 (2)

半导体NPN高频小功率晶体管制造的工艺流程为:外延片——编批——清洗——水汽氧化——一次光刻——检查——清洗——干氧氧化——硼注入——清洗——UDO淀积——清洗——硼再扩散——二次光刻——检查——单结测试——清洗——干氧氧化——磷注入——清洗——铝下CVD——清洗——发射区再扩散——三次光刻——检查——双结测试——清洗——铝蒸发——四次光刻——检查——氢气合金——正向测试——清洗——铝上CVD——检查——五次光刻——检查——氮气烘焙——检查——中测——中测检查——粘片——减薄——减薄后处理——检查——清洗——背面蒸发——贴膜——划片——检查——裂片——外观检查——综合检查——入中间库。
PNP小功率晶体管制造的工艺流程为:外延片——编批——擦片——前处理——一次氧化——QC检查(tox)——一次光刻—□□—QC检查——单结测试——磷注入——前处理——发射区氧化——前处理——发射区再扩散——前处理——POCl3预淀积(R□)——后处理——前处理——HCl退火、N2退火——三次光刻——QC检查——双结测试——前处理——铝蒸发——QC检查(t Al)——四次光刻——QC检查——前处理——氮氢合金——氮气烘焙——正向测试(ts)——外协作(ts)——前处理——五次光刻——QC检查——大片测试——测试ts——中测编批——中测——中测检查——入中间库。
变容管制造的工艺流程为:外延片——编批——擦片——前处理——一次氧化——QC检查——N+光刻——QC检查——前处理——干氧氧化——QC检查——P+注入——前处理——N+扩散——P+光刻——QC检查——硼注入1——前处理——CVD(LTO)——QC检查——硼注入2——前处理——LPCVD ——QC检查——前处理——P+扩散——特性光刻——电容测试——是否再加扩——电容测试——......(直到达到电容测试要求)——三次光刻——QC检查——前处理——铝蒸发——QC检查(t Al)——铝反刻——QC检查——前处理——氢气合金——氮气烘焙——大片测试——中测——电容测试——粘片——减薄——QC检查——前处理——背面蒸发——综合检查——入中间库。
半导体工艺讲解
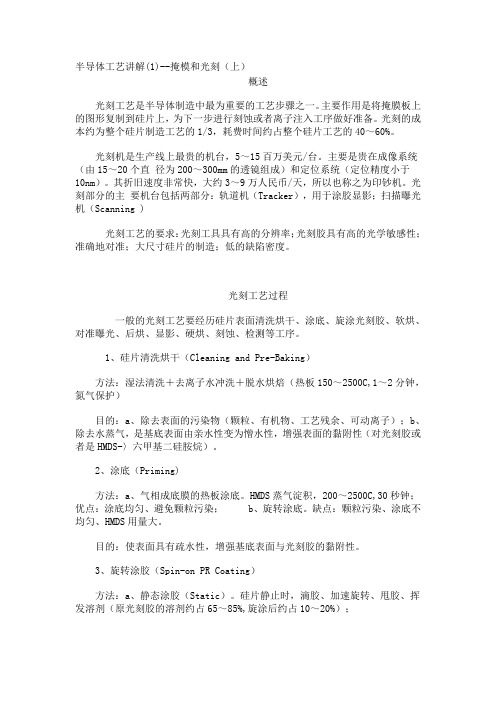
半导体工艺讲解(1)--掩模和光刻(上)概述光刻工艺是半导体制造中最为重要的工艺步骤之一。
主要作用是将掩膜板上的图形复制到硅片上,为下一步进行刻蚀或者离子注入工序做好准备。
光刻的成本约为整个硅片制造工艺的1/3,耗费时间约占整个硅片工艺的40~60%。
光刻机是生产线上最贵的机台,5~15百万美元/台。
主要是贵在成像系统(由15~20个直径为200~300mm的透镜组成)和定位系统(定位精度小于10nm)。
其折旧速度非常快,大约3~9万人民币/天,所以也称之为印钞机。
光刻部分的主要机台包括两部分:轨道机(Tracker),用于涂胶显影;扫描曝光机(Scanning )光刻工艺的要求:光刻工具具有高的分辨率;光刻胶具有高的光学敏感性;准确地对准;大尺寸硅片的制造;低的缺陷密度。
光刻工艺过程一般的光刻工艺要经历硅片表面清洗烘干、涂底、旋涂光刻胶、软烘、对准曝光、后烘、显影、硬烘、刻蚀、检测等工序。
1、硅片清洗烘干(Cleaning and Pre-Baking)方法:湿法清洗+去离子水冲洗+脱水烘焙(热板150~2500C,1~2分钟,氮气保护)目的:a、除去表面的污染物(颗粒、有机物、工艺残余、可动离子);b、除去水蒸气,是基底表面由亲水性变为憎水性,增强表面的黏附性(对光刻胶或者是HMDS-〉六甲基二硅胺烷)。
2、涂底(Priming)方法:a、气相成底膜的热板涂底。
HMDS蒸气淀积,200~2500C,30秒钟;优点:涂底均匀、避免颗粒污染;b、旋转涂底。
缺点:颗粒污染、涂底不均匀、HMDS用量大。
目的:使表面具有疏水性,增强基底表面与光刻胶的黏附性。
3、旋转涂胶(Spin-on PR Coating)方法:a、静态涂胶(Static)。
硅片静止时,滴胶、加速旋转、甩胶、挥发溶剂(原光刻胶的溶剂约占65~85%,旋涂后约占10~20%);b、动态(Dynamic)。
低速旋转(500rpm_rotation per minute)、滴胶、加速旋转(3000rpm)、甩胶、挥发溶剂。
- 1、下载文档前请自行甄别文档内容的完整性,平台不提供额外的编辑、内容补充、找答案等附加服务。
- 2、"仅部分预览"的文档,不可在线预览部分如存在完整性等问题,可反馈申请退款(可完整预览的文档不适用该条件!)。
- 3、如文档侵犯您的权益,请联系客服反馈,我们会尽快为您处理(人工客服工作时间:9:00-18:30)。
Chapter 2 Basic VLSI/ULSI FabricationProcess TechnologyI. Evolution of IC Process TechnologyII. Main LSI/VLSI processes developed in historyIII. CMOS core based ULSI technology---basis of presentMicroelectronicsIV. Main elemental devices and process flow of IC fabrication V. Major chip fabrication material and technologyVI. Ultra clean technologies-of vital importance for VLSI/ULSI manufacturingI. Evolution of IC Process Technologyz IC circuitry evolution determined by process progress ---Bipolar process: RTL, DTL, TTL, STTL, LSTTL, ECL, I 2L…..---MOS Process: PMOS, NMOS, CMOS---JFET, MESFETz Process technology---Most active factor in IC progress ---PN junction formed by growth doping or metal/Ge(Si) alloy doping in 1950s---PN junction formed by blanket diffusion doping in 1950s ---Transistor formed by planar process based on diffusion, oxidation and lithograph in late 1950s*Double diffused mesa transistor process*Transistor by planar processz Transistor and other circuit elements formed by planar technology---On-chip resistor: by diffusion;poly-Si by deposition--- On-chip capacitor: metal/I/Si;M/I/M; Poly-Si/I/Poly-Si (I-SiO2or other dielectric film)--- On-chip inductor: spiral metal linewith ground shieldII. Main LSI/VLSI processes developed in historyz Main LSI/VLSI/ULSI requirements:---High integration density---High speed---High reliability---Low powerz PMOS:---Early LSI/VLSI products: calculators, electronic game,...---Low speedz NMOS:---Higher speed than PMOS---Main VLSI process in 80’s for DRAM, microprocessorsz Standard bipolar (LSTTL, ECL…)---High driving capability---Applied for high-speed devices: Early high-speed computer, communication system, …---Lower integration density and higher power consumptionz I2L bipolar---Lower power & higher integration than standard bipolar ---Lower speedz CMOS---Lowest power consumption than all others---Noise resistance and higher reliability---Main stream of VLSI/ ULSI process since late 80’sz BiCMOS---Combination of high speed and low power---High process complexityz GaAs MESFET IC---High-speed devices for communication, etc.---Possibility of integration with photonic devicesIII. CMOS core based ULSI technology---basis of present Microelectronicsz Low power consumption---essential requirement for ULSI/SoC chipz CMOS based Si process---dominant ULSI technologyz Combination of CMOS core process and special process modules→Various ULSI chip technologies---DRAM,SRAM, Flash EPROM, Logic, BiCMOSCommunication ICs,…→System on Chip (SoC) technologyIV. Main elemental devices and process flow of IC fabrication z All IC are based on few main device effects---pn junction: transistor, diode, JFET---Field effect: PMOS, NMOS---Schottky barrier effect: SBD, MESFET*Their fundamental physics---Interface effectsz Schematic crosssection and processtechnology for0.18μm CMOS ofBell Labz Main Si chipfabrication processflow diagramEtchingz Wafer fabrication process module—Process module—a group of process steps to form a part structure of IC—The entire IC wafer manufacturing process consists of 14-20 process modules—A typical process module consists of 10-20 process steps —Process integration—of vital importance for success of a certain fabrication technologyV. Major chip fabrication material and technology(1) Si material— Large-diameter and defect-free Si crystal growth Φ100ÆΦ125ÆΦ150ÆΦ200ÆΦ300ÆΦ450(mm) — Thin Si layer epitaxial growthn-Si layer/p-Si substrate, n/n+, p/p+— SiGe/Si hetero-epitaxy; strained SiGe or strained Si— SOI(Si on Insulator) materialBy SIMOX (O+-implant), bonding/smart-cut— Gettering technology(2) Fine pattern microstructure formation technology— Reticle/mask pattern generation by e-beam— Optical lithographyUV Lamp g-line=436nm Æ 0.5μmi-line=365nm Æ 0.35μmDUV Eximer Laser*KrF 248nm Æ 250, 180 nm …*ArF 193nm Æ 130, 110, 90, 65nm,45nm*ArF 193nm (Immersion) Æ32nm, 22nmF2 157nm(?); Ar2 126nm(?)*EUV Laser plasma source: 13nmPhase shift mask and other wave-front technologyÆPattern feature < λStep-and-Scan exposure system— E-beam lithography (for mass production tool still in R&D) Direct writing on wafer and other methods— Mix-and-Match lithography— High resolution resist material and process— High resolution etching technology (Ex. HDP-RIE)— Self-aligned microstructure formationBy selective etching, reaction, epitaxy and other methods(3) Selective Doping Technology— Si transistor--product of doping engineering*Device type and performance--determined by impurity doping profile ( element, concentration, distribution)— Low energy ion implant and shallow junction formation---Of vital importance for nano-meter CMOS fabrication— High energy ion implant for n/p wells— Rapid thermal process (RTP) and dopant atom diffusion control(4) Dielectric Thin Film Material and Process— Ultra thin gate oxide growth---Of key important for advanced CMOS: 30nm Æ 0.8nmBy using nitrided oxide— High-K dielectrics for gate application*Intensive investigation on a series of materials with k~10-100HfO2, Al2O3, ZrO2, ZrSi x O y, TaO x N y, HfSi x O y, TiO2, La2O3, SrTiO3 …— Low-K dielectrics for inter-metal isolationInorganic/Organic K<3.9*High-density plasma (HDP) CVD deposition*SOG (Spin-On-Glass), SOP (Spin-On-Polymer)(5) Device Isolation Technology: from pn junction isolation tonew dielectric isolation— Modified LOCOS (Local Oxidation of Si)Poly-Si buffered LOCOS (PBL)— Shallow trench isolation (STI)(6) Contact and Interconnection— Polycide (silicide/poly-Si) gate electrode & interconnect (WSi2)— Salicide process – Self-aligned silicide formation on S/G/D TiSi2Æ CoSi2, NiSi— New type of metal gate technology— Diffusion barrier (TiN, TaN…)— High conductive and reliable interconnect material & process: Al-Si-Cu alloy, W-plug, Cu-damascene— Multilevel interconnection4-5 levels Æ >10 levels— CMP planarization(7) Si based hetero-structure material and device process (A field expecting more invention and creation in the years ahead) — Si/SiGe/Si hetero-junction bipolar transistor (HBT) process— Strained Si/SiGe or SiC channel PMOS/NMOS devices— GaAs on Si and other semiconductors on SiExample: --GaAs-MESFET on GaAs/STO(Strontium Titanium Oxide) /SiO2/Si(A work of Motorola: SST, July/2002)VI. Ultra clean technologies-of vital importance forVLSI/ULSI manufacturingz Wafer environment cleanliness and utility purity (wafer, gas, chemicals…)*Minimum defect density requirement for different DRAM generationsDRAM process technology 4M 16M 64M 256M 1GDesign rule(μm) 0.8 0.5 0.35 0.25 0.13Critical layer 9 10 11 13Critical particle size (nm) 120 90 50 30Killing defect size (μm) 0.27 0.18 0.1 0.06Defect density measured at thekilling defect size (D/cm2)0.50 0.40 0.32 0.22Defect density measured at 0.12μm particle size (D/cm2)2.53 0.90 0.22 0.055Defect density/critical levelmeasured at 0.12μm particlesize (D/cm2)0.28 0.09 0.02 0.004Defect improvement factor 1 3 14 65(source :KLA)Clean room class 1 0.1 0.1 0.1/mini-environment)0.1/mini-environment)DI water required specificationsResistivity (MΩ·cm)>18.0 >18.1 >18.2>0.085μm <10 <2 <0.5 Particle(pieces/cc) >0.05μm<5<1 Bacteria (Unit/L) <10 <1 <1TOC (ppb) <20 <5 <1 Oxygen (ppb) <50 <10 <5Silica (ppb) <3 <1 <0.2Na, Cl (ppb) <0.1 <0.05 <0.01 Metal ion (ppb) <0.1 <0.05 <0.01 Required chemicals specifications0.2μm <50<10<1 Particles0.1μm <100<10 Anion (ppb) <500 <100 <50Metal (ppb) <10 <1 <0.2 Required bulk gas specificationsParticle level: size(μm)-pcs/cc 0.1-<5 0.1-<50.05-<5Impuritylevel(O2,CO,CO2,CH4)(ppb)<10 <5 <1H20 level (ppb) <100 <10 <0.13Metal level (μg/m3) 10.10.01z Control of the wafer environment is of crucial importance for wafer manufacturing process*Cleanroom fab by carefully designed filtration and laminar- flow circulation for the air to create a clean environment; higher and higher cleanliness required for ULSI*Pure/clean and dust-free materials for all utilities and equipments*Ultra-clean mini-environment required for update ULSI; Transport of wafers between minienviroments by means of SMIF (standard mechanical interfaces) podsExample of cleanroom layout and its cleanlinessz Wafer-cleaning process—critical step in IC manufacturing to obtain an ultraclean wafer surface--free from particles, organic contamination, metal contamination, surfacemicro-roughness andnative oxide*Various contaminants to beremoved by cleaning process*Wafer cleanliness hascrucial effect on thequality of ultra thingate oxide and otherthin film/thin layer;many process factorsmay cause surfacecontaminationz RCA cleaningprocess and itsmodified recipe arecommonly used in Si-IC process*RCA cleaningprocess—first developed by Kern and Puotinen in 1960 at RCA and published in 1970*Two sequential RCA Standard Cleaning solutions based onH2O2, NH4OH, and HCl: SC-1 & SC-2SC-1: NH4OH/H2O2/H2O (1:1:5 to 0.5:1:5); 70-80°C, 10-15 min To remove organic films by oxidation and certain metals (Au, Ag, Cu, Ni, Zn, Cd, Co, Cr and IB/IIB group metals) by complexing; Native oxide etching & re-oxidation→ to dislodge particles; Microroughness from Si-etching by NH4OH--∴less NH4OH is preferred and H2O2 depletion should be avoidedSC-2: HCl/H2O2/H2O (1:1:6 to 1:1:8); 70-80°C, 10-15 minTo remove alkali ions and cations like Al+3, Fe+3 and Mg+2 (they form NH4OH insoluble hydroxides in SC-1) and other metal residue/contamination by forming a soluble complex*Effort to modify recipe of RCA cleaning process: IMEC cleaning process with more diluted solutions for better cleaning effect and with better enviromental protectionz Other important solutions for wafer cleaningSPM (Sulfuric-Peroxide Mixture) solution: H2SO4/H2O2 (1:1 to 4:1); 120-150°C, 10 min; To remove organics and stripe photoresistDHF (Diluted HF) solution: HF/H2O (1:10 to 1:50); room temperature, 1 min; to remove chemical oxide grown by SC-1, SC-2, SC-3 cleaning processz Standard wafer cleaning processing*SPM clean→ DI H2O rinse→ HF/H2O etching→ DI H2O rinse→ SC-1 clean →DI H2O rinse→ SC-2 clean→ DI H2O rinse → HF/H2O etching → DI H2O rinse → Dry*Depletion of H2O2 in SC-1 solution should be avoided to protect Si surface from NH4OH etching*Ultrasonic agitation is used to dislodge particles。