氧化反应事故案例分析
氧化铝事故案例及措施
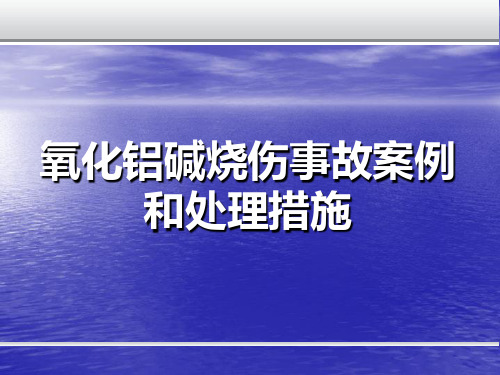
4、检修过程中发生碱烧伤事 故
(1)2009年某月某日,沉降片区倒稀释后槽, (1)2009年某月某日,沉降片区倒稀释后槽,控制过 年某月某日 滤区域上午9:00停车放料 9:07分联系电工将滤饼 停车放料, 滤区域上午9:00停车放料,9:07分联系电工将滤饼 235B断电 10:40分左右 断电。 分左右, 泵235B断电。10:40分左右,检修人员回装滤饼管 三通时用撬棍固定法兰两端螺栓孔, 三通时用撬棍固定法兰两端螺栓孔,用捶敲打管道校 位,突然有料浆从三通和管道对位后的法兰缝隙中溅 料浆溅到现场作业的两名检修人员1 出,料浆溅到现场作业的两名检修人员1名运行人员 面部。片区立即组织人员用应急水源和硼酸水对3 面部。片区立即组织人员用应急水源和硼酸水对3人 进行反复冲洗。经原平市人民医院医生诊断, 进行反复冲洗。经原平市人民医院医生诊断,3人为 脸部和脖颈轻微碱灼伤,用药一周后康复。 脸部和脖颈轻微碱灼伤,用药一周后康复。
(3)2009年某月某日上午 时 因管道堵塞, (3)2009年某月某日上午10时,因管道堵塞,操作人员对 年某月某日上午10 Pc404母液泵进行放料 当阀门清通时, Pc404母液泵进行放料,当阀门清通时,铝酸钠溶液瞬 母液泵进行放料, 间流出,经地沟二次飞溅, 间流出,经地沟二次飞溅,站在放料管阀门旁边的指挥 人员被料浆溅至眼部、面部及衣服上。 人员被料浆溅至眼部、面部及衣服上。其他人员立即使 用大量硼酸水和清水进行了反复清洗约半小时。 用大量硼酸水和清水进行了反复清洗约半小时。并迅速 去医院进行治疗,医生打针并做了简单处理, 去医院进行治疗,医生打针并做了简单处理,1周后完全 康复。 康复。
2、处理冒料事故中发生的碱烧伤事故 、
(1)2007年某月某日下午,因蒸发和溶出设备跳停,Ⅰ、 年某月某日下午,因蒸发和溶出设备跳停, 年某月某日下午 Ⅱ组磨机紧急停车导致冒料。15:50点左右,接班人员杨 组磨机紧急停车导致冒料。 : 点左右, 点左右 某查完2#中间泵池是否放完料后 观察2#棒磨机流槽是 中间泵池是否放完料后, 某查完 中间泵池是否放完料后,观察 棒磨机流槽是 否清理干净,流槽内料浆不慎飞入眼内。 否清理干净,流槽内料浆不慎飞入眼内。现场其它工作人 员和维护人员立刻用硼酸水和清水对其进行冲洗, 员和维护人员立刻用硼酸水和清水对其进行冲洗,同时将 其送往医院进行诊治。经医生检查,认为伤者现场处理及 其送往医院进行诊治。经医生检查, 时,简单处理后用药1周后完全康复。 简单处理后用药 周后完全康复。 周后完全康复
停车不当氧升高装置爆炸损失重化工事故案例
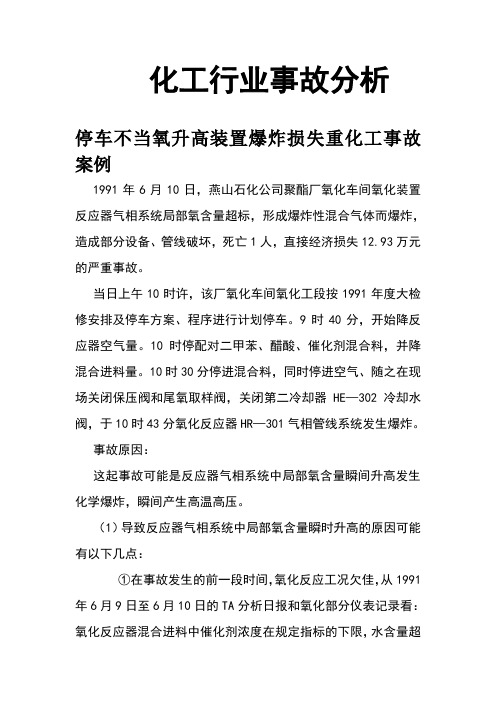
化工行业事故分析
停车不当氧升高装置爆炸损失重化工事故案例
1991年6月10日,燕山石化公司聚酯厂氧化车间氧化装置反应器气相系统局部氧含量超标,形成爆炸性混合气体而爆炸,造成部分设备、管线破坏,死亡1人,直接经济损失12.93万元的严重事故。
当日上午10时许,该厂氧化车间氧化工段按1991年度大检修安排及停车方案、程序进行计划停车。
9时40分,开始降反应器空气量。
10时停配对二甲苯、醋酸、催化剂混合料,并降混合进料量。
10时30分停进混合料,同时停进空气、随之在现场关闭保压阀和尾氧取样阀,关闭第二冷却器HE—302冷却水阀,于10时43分氧化反应器HR—301气相管线系统发生爆炸。
事故原因:
这起事故可能是反应器气相系统中局部氧含量瞬间升高发生化学爆炸,瞬间产生高温高压。
(1)导致反应器气相系统中局部氧含量瞬时升高的原因可能有以下几点:
①在事故发生的前一段时间,氧化反应工况欠佳,从1991年6月9日至6月10日的TA分析日报和氧化部分仪表记录看:氧化反应器混合进料中催化剂浓度在规定指标的下限,水含量超。
典型气瓶相关事故案例展示

重庆潼南氧气瓶爆炸事故
事故概况:2006年8月6日上午,位于重 庆潼南县城的一家临街气体经营部发生 氧气瓶爆炸事故,致5人死亡、1人重伤 。氧气钢瓶爆炸碎片震飞近20米,存放 气瓶的库房中间隔墙被炸开一个大洞。
事故原因:在对氧气瓶进行测压时使用 了含有油脂的测压表,高压氧气接触油 脂发生剧烈氧化反应导致形成瞬间高温, 进而造成气瓶闪爆事故。氧气瓶已过报 废年限是事故的第二原因。
气瓶事故案例:
福建南安五金厂氮气瓶爆炸事故
事故概况:2007年7月6日,福建省南安 市水头镇一五金厂发生氮气气瓶爆炸事 故,至2人死亡、2人重伤。当时该厂锌 合金压铸机需检修和补氮,在维修工检 查设备时,氮气瓶突然发生爆炸。
事故原因:氮气瓶曾受到过局部猛烈撞 击已至瓶身存在内应力缺陷,在事故当 日氮气瓶经长时间太阳,又受压铸机周 围局部高温环境影响,最终引发气瓶超 压爆炸。
安全提示:1、氩气属惰性气体,虽不燃烧不爆炸也无毒,但吸入过量会导致缺氧窒 息。氩气密度比空气重,氩气一旦发生泄漏会集聚于低洼处,在坑道地形使用氩气应 作好通风工作,并严格遵守有限空间作业流程,作好必要安全措施。2、液氩储罐不 得设立于坑、井、池当中或者附近,液氩泄漏易造成低洼处氧浓度过低,构成窒息危 险。
气瓶事故案例:
西安六村堡黑作坊氩气泄漏事故
事故概况:2016年5月8日,西安市未央 区曹家堡村一黑化工厂发生氩气泄漏事 故,至2人死亡。现场一处5m³液氩储罐 设置于坑道内,2名工人在坑道内作业因 窒息死亡。
事故原因:直接原因为氩气泄漏导致有 限空间形成缺氧环境,而操作人员在未 进行任何安全防护的条件下违规进入有 限空间作业导致窒息死亡。黑化工厂违 法违规经营也是导致事故的重要诱因。
简易事故案例分析报告 - 未加溶媒导致反应失控

简易事故案例分析报告未加溶媒导致反应失控事故描述:某工厂使用毗咤氧化物与二乙氨基甲酰氯反应,生成的中间体与氟化钠(NaCN)进一步反应生成最终产品。
体系溶媒为丙酮。
事故发生当天,由于反应失控引起中间体和毗咤氧化物发生分解,导致反应釜发生爆炸,反应釜人孔、固体投料口损坏,高温的反应物释放至车间内。
事故最终导致1人死亡、1人受伤,并导致建筑物严重损坏。
事故原因:通过事故调查,有以下几个原因导致此次事故的发生:1 .毗咤氧化物和中间体不稳定,容易发生剧烈分解。
2 .在二乙氨基甲酰氯之前应将丙酮加入至反应釜,但是操作人员未加入丙酮。
操作规程中并未将加入丙酮识别为关键操作步骤。
3 .反应体系内无丙酮加入造成中间体起始分解温度降低。
4 .反应体系内无丙酮加入同时造成反应釜内物料粘度增大,影响了搅拌及换热效果。
5 .反应釜安装的安全阀和爆破片泄压能力不足,从而使用固体加料口作为辅助的泄压口。
事故教训:1 .在进行危害与可操作性(HAZOP)分析时应选用有经验和能力的HAZoP小组成员,小组成员需要熟悉反应机理、生产和工程要求。
2 .在HAZOP分析时需要考虑物料加入量(包括溶媒)对于反应体系的影响,从而更好地识别反应失控的原因。
3 .在HAZOP分析时需要考虑操作人员失误造成操作步骤遗漏(如本案例中未加入溶媒)或者顺序错误对于反应体系的影响,基于工厂的管理要求合理地评估风险。
4 .如果某一操作步骤错误可能导致严重的安全后果,建议在操作规程中识别为关键操作步骤,从而让操作人员更好地理解此操作步骤的重要性。
反应釜的泄压设施需要针对识别的事故情形进行合理的选型、设计、计算和安装以起到泄压作用。
典型危险化学反应分析

1氧化如氨氧化制硝酸、甲苯氧化制苯甲酸、乙烯氧化制环氧乙烷等。
(1)氧化的火灾危急性①氧化反响需要加热,但反响过程又是放热反响,特别是催化气相反响,一般都是在 250~600℃的高温下进展,这些反响热如不准时移去,将会使温度快速上升甚至发生爆炸。
②有的氧化,如氨、乙烯和甲醇蒸气在空中的氧化,其物料配比接近于爆炸下限,如果配比失调,温度掌握不当,极易爆炸起火。
③被氧化的物质大局部是易燃易爆物质。
如乙烯氧化制取环氧乙烷中,乙烯是易燃气体,爆炸极限为2.7%~34%,自燃点为450℃;甲苯氧化制取苯甲酸中,甲苯是易燃液体,其蒸气易与空气形成爆炸性混合物,爆炸极限为 1.2%~7%;甲醇氧化制取甲醛中,甲醇是易燃液体,其蒸气与空气的爆炸极限是 6%~36.5%。
④氧化剂具有很大的火灾危急性。
如氯酸钾,高锰酸钾、铬酸酐等都属于氧化剂,如遇高温或受撞击、摩擦以及与有机物、酸类接触,皆能引起着火爆炸;有机过氧化物不仅具有很强的氧化性,而且大局部是易燃物质,有的对温度特别敏感,遇高温则爆炸。
⑤氧化产品有些也具有火灾危急性。
如环氧乙烷是可燃气体;硝酸虽是腐蚀性物品,但也是强氧化剂;含 36.7%的甲醛水溶液是易燃液体,其蒸气的爆炸极限为 7.7%~73%。
另外,某些氧化过程中还可能生成危急性较大的过氧化物,如乙醛氧化生产醋酸的过程中有过醋酸生成,过醋酸是有机过氧化物,性质极度不稳定,受高温、摩擦或撞击便会分解或燃烧。
(2)氧化过程的防火措施①氧化过程中如以空气或氧气作氧化剂时,反响物料的配比(可燃气体和空气的混合比例)应严格掌握在爆炸范围之外。
空气进入反响器之前,应经过气体净扮装置,消退空气中的灰尘、水汽、油污以及可使催化剂活性降低或中毒的杂质,以保持催化剂的活性,削减着火和爆炸的危急。
②氧化反响接触器有卧式和立式两种,内部填装有催化剂。
一般多承受立式,由于这种形式催化剂装卸便利,而且安全。
在催化氧化过程中,对于放热反响,应掌握适宜的温度、流量,防止超温、超压和混合气处于爆炸范围之内。
氧化反应事故案例分析

氧化反应事故案例分析
2、原因分析 由于工厂管理的不良、人员操作的失误及设备安置的错误,都直接或间接地
导致了这次灾难的发生。该起事故原因归纳如下: (1)维修过程无详细的规划;(2)工厂的人事管理及生产工艺修改管理不良; (3)值班人员交代不清; (4)测漏时压力设定不足 (5)不锈钢管产生锌脆化现象; (6)硝酸盐腐蚀反应槽 (7)厂区建筑物、设备的配置不良; (8)该厂储存过多的危险性可燃物质 (9)氮气的供应不足 (10)缺乏紧急应变能力
氧化反应事故案例分析
1.事故经过
到6月1日下午,开始有可燃性气体外泄,但并无人员警觉或注意到。 将近16时,空气中弥漫着大量的可燃性气体,并向外扩散。2分钟后,可能 在氢气2车间遇点火源着火,随即发生了爆炸。环己烷蒸气云的爆炸造成2 个替代的伸缩接头受不当的外力引起破裂挫曲,而连接4号和6号氧化反应 槽的三曲管因爆炸而扭曲成“<”形掉落在地面。由此可以推断出2个替代 的伸缩接头受不了当时的外力引起破裂弯曲,造成容器内环己烷大量外泄。
氧化反应事故案例分析
1.事故经过
在拆下5号氧化反应槽后,即进行修复工作。在装4号和6号氧化反应槽间连接管线时,施 工人员仅在现场地面上以粉笔画一简单的修复工程图样,并没有预先规划并绘制正规的设计 工程图及必要的工程应力详细核算。现场以鹰架支撑管子。两氧化反应槽间因有高度差(约相 差35.5cm),故以三曲旁通管作为两氧化反应槽间的连接管,而原来氧化反应槽出口处的伸缩 接头管径为72cm,但当时厂内只有管径为51cm的管线可用。施工人员经大概的计算后,认为 51cM管线尚可提供反应时所需的流量,并以直管计算压力后得知其反应亦可承受操作时的压 力,决定以此管取代之。三曲旁通管仅以分成四点的鹰架支撑着,结构上并不坚固。于3月30 日2时完成全部修复作业。
石化行业典型事故案例分析报告

石化行业典型事故案例分析报告石化行业是一个高危行业,由于其生产环节中存在着易燃、易爆、有毒和高温的物质,所以常常发生各种事故。
本文将以一起典型的石化行业事故为例进行分析。
1. 事故概述2018年5月,某石油化工公司的生产车间发生了一起重大事故。
事故发生在该公司的乙炔生产车间,造成了4人死亡、10人受伤。
事故原因是由于车间管理不善和操作不规范导致的。
2. 事故经过事故当天,车间内正在进行乙炔氧化反应的生产工作。
由于当时车间管理不善,一位工人在进行反应装置的检修时没有按照规定进行操作。
他在检修完毕后没有关闭相关设备,而是直接离开岗位。
由于疏忽大意,设备并未被关闭,乙炔氧化反应仍在继续进行。
之后,由于车间操作人员对设备的监控不到位,无法及时发现问题。
乙炔氧化反应持续进行,导致温度和压力升高,最终达到了危险的程度。
在温度和压力超过设定值后,反应装置发生了爆炸,导致车间内多个设备损坏,造成人员伤亡。
3. 事故原因分析a. 车间管理不善:公司在管理方面存在严重问题,对车间人员的培训和安全意识教育不到位,对设备和操作的监控不到位。
b. 操作不规范:由于工人在检修后没有按照规定关闭设备,导致乙炔氧化反应持续进行,最终引发事故。
c. 设备监控不到位:车间操作人员对设备的监控不到位,无法及时发现温度和压力升高的异常情况。
4. 事故教训和改进措施a. 加强车间管理:公司应加强对车间人员的培训和安全意识教育,提高员工的安全意识和操作规范性。
b. 建立严格的操作程序:确保每一项操作都按照规定进行,特别是在检修完成后,必须验证设备是否正常关闭。
c. 完善设备监控系统:引入先进的监控系统,对设备的温度、压力、液位等参数进行实时监测,及时发现异常情况并采取相应的措施。
d. 加强安全检查:公司应定期对设备进行安全检查和维护,确保设备的正常运行。
5. 结论本次事故的发生给石化行业敲响了警钟,也给我们带来了深刻的教训。
只有加强车间管理、规范操作、完善设备监控,才能最大程度地减少事故的发生,保障生产安全。
双氧水装置事故分析案例

鲁西双氧水“7.27”火灾事故
2.鲁西双氧水“7.27”火灾事故简介(续) ----事故发生经过: 该双氧水装置于7月23日工作液进系统循环,7月25日引氢气进系统,正式投料试生产;27日12时05分,萃取塔开始分出双氧水,浓度为27%。 27日16时45分左右,中控室操作人员通过远程视频监控发现萃取塔、萃余分离器位置有浓烟冒出。随后操作人员离开中控室前往现场,发现萃余分离器部位起火,火势随萃余液(油质可燃物)的泄露增大,并伴有爆鸣声;立即通知中控室其他操作人员进行一键安全停车,同时启动装置切断氢气并充氮保护。 企业和当地政府迅速启动应急预案扑救火灾,27日20时左右火势得到有效控制,28日3时36分火灾被全部扑灭。“清净下水”全部封堵在厂区内并导入环境安全应急池,经环保部门对大气和周边水体检测,未发现有毒有害物质和水体污染。
*
博汇及鲁西双氧水装置事故原因评析
2.操作层面的事故原因分析(续) (3)对双氧水装置静电危害的重视程度不够。 1)防静电设施和措施不够全面。萃取塔至萃余液分离器、高位集液槽、工作液计量槽的气液相管路法兰既未做静电跨接,也没有测量接触电阻,存在静电积聚的安全隐患。 2)系统设计缺陷导致多个易产生静电的环节。 萃取塔与萃余液分离罐高达6.8米的位差,造成工作液的流速在岀液管道内大大加快,易产生静电; 萃取塔溢流管设计不合理造成萃取塔塔顶液位不稳定,特别是在双氧水分解较活跃的状况下,萃取塔萃余液出口管内介质为气液非均相混合物,管内介质流速快而紊乱,易产生静电。
15时50分乙班人员接班后,因氮气中氧含量一直不合格无法再次开车。
博汇 “8.25”双氧水爆炸事故
博汇 “8.25”双氧水爆炸事故简介----事故发生经过 (续) :
*
在装置停车时段内,DCS主操发现氧化塔压力由17时25 分的0.08MPa升至 18时24分的 0.2MPa,通过远程控制打开氧化塔尾气调节阀泄压,由于阀的开度过小,塔内压力升高速度短暂减缓后仍继续升高;
铁黄颜料生产线氧化反应工序事故原因分析及安全整改建议

2015年5月,某氧化铁颜料生产企业铁黄生产线氧化反应工序处于停产技改状况时,4#生产线氧化反应釜顶部的水封盖突然弹出,碰撞到反应釜旁边的尾气管线。
事故造成该玻璃钢材质的尾气管线(管径为200mm )局部开裂损坏,幸好当时现场无人,未造成人员伤亡。
该氧化反应釜直径为5m ,高度约为9.3m ,容积约为124m 3。
水封盖为玻璃钢材质,外形近似倒扣盆状(带顶盖圆筒短节),外径为1.85m ,高度为0.45m ,厚度为10mm ,质量约为40kg 。
该氧化反应釜为间隙操作,每批次反应周期为84~110h 。
为了便于原料铁皮投料,在反应釜顶部封头处设有铁皮原料投料口,投料口处设有一环形水封槽。
正常操作时,水封盖倒扣在环形水封槽中形成水封,环形水封槽内充满水时的最大水封高度约为300mm 。
当需要进行投料操作时,临时将水封盖吊移至釜顶投料口旁边的平台。
反应釜简图如图1所示。
在查阅相关项目资料和公开发表的文献资料的基础上,从该氧化反应工序的工艺原理着手,对过程的工艺本质安全等问题进行分析和探讨,并分析发生该事故的主要原因。
从改进和优化工艺操作规程与工艺操作条件、增设必要的氢气浓度在线检测手段等安全措施的角度出发,提出改善该反应工序过程本质安全的若干建议和措施,供铁黄车间实施安全整改时参考。
1铁黄生产过程中氧化反应工序的配料及主要操作条件1.1氧化反应工序每批次配料情况(1)初始晶种料液:来自前一工序即铁黄晶种制备工序的料液约90000kg ,是含有羟基氧化铁(琢-FeOOH )铁黄晶种并溶解有FeSO 4·7H 2O 及少量Na 2SO 4的悬浮水溶液。
其组成见表1(FeSO 4·7H 2O 折合成无水FeSO 4计)。
铁黄颜料生产线氧化反应工序事故原因分析及安全整改建议王勤获上海华谊工程有限公司(上海200241)作者简介:王勤获男1961年硕士研究生教授级高级工程师主要从事石化和化工工程设计及技术管理工作摘要针对某氧化铁颜料生产企业铁黄生产线氧化反应工序反应釜水封盖弹出事故,通过查阅相关资料,对该氧化反应过程的工艺本质安全等问题进行了分析和探讨,并初步分析了发生该事故的主要原因。
某石化公司CO中毒事故分析
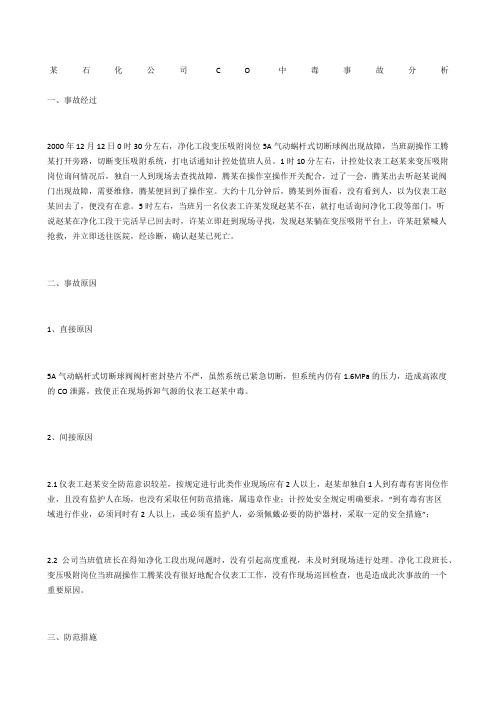
某石化公司C O中毒事故分析一、事故经过2000年12月12日0时30分左右,净化工段变压吸附岗位5A气动蜗杆式切断球阀出现故障,当班副操作工腾某打开旁路,切断变压吸附系统,打电话通知计控处值班人员。
1时10分左右,计控处仪表工赵某来变压吸附岗位询问情况后,独自一人到现场去查找故障,腾某在操作室操作开关配合,过了一会,腾某出去听赵某说阀门出现故障,需要维修,腾某便回到了操作室。
大约十几分钟后,腾某到外面看,没有看到人,以为仪表工赵某回去了,便没有在意。
5时左右,当班另一名仪表工许某发现赵某不在,就打电话询问净化工段等部门,听说赵某在净化工段干完活早已回去时,许某立即赶到现场寻找,发现赵某躺在变压吸附平台上,许某赶紧喊人抢救,并立即送往医院,经诊断,确认赵某已死亡。
二、事故原因1、直接原因5A气动蜗杆式切断球阀阀杆密封垫片不严,虽然系统已紧急切断,但系统内仍有1.6MPa的压力,造成高浓度的CO泄露,致使正在现场拆卸气源的仪表工赵某中毒。
2、间接原因2.1仪表工赵某安全防范意识较差,按规定进行此类作业现场应有2人以上,赵某却独自1人到有毒有害岗位作业,且没有监护人在场,也没有采取任何防范措施,属违章作业;计控处安全规定明确要求,“到有毒有害区域进行作业,必须同时有2人以上,或必须有监护人,必须佩戴必要的防护器材,采取一定的安全措施”;2.2公司当班值班长在得知净化工段出现问题时,没有引起高度重视,未及时到现场进行处理。
净化工段班长、变压吸附岗位当班副操作工腾某没有很好地配合仪表工工作,没有作现场巡回检查,也是造成此次事故的一个重要原因。
三、防范措施1、实行工作票制度。
认真办理工作票,凡无工作票作业,一律视为违章作业。
2、强化调度工作。
明确调度长职责,中夜班由调度长组织各装置值班长及公司岗检人员,安排布置其中夜班的安全生产工作。
3、完善安全设施。
在重要生产岗位安装监控器,使调度中心能够随时掌握各岗位的状况。
空分制氧典型事故案例资料

空分制氧典型事故案例资料第一部分:行业事故案例1、液氧槽车事故事故经过:2011 年4 月24 日下午2 点35 分左右,扬溧高速上,一辆槽罐车正从镇江开往扬州,眼看就要到瓜州收费站,谁知就在还有一公里时,让人意想不到的事故发生了。
“砰!”一声巨响,槽罐车撞上了前面一辆小型吊车,在惯性作用下,槽罐车侧翻,尾部重重地撞上了高速右侧的护栏,护栏严重变形。
由于惯性巨大,槽罐车并没有因此停下来,横着向前滑行了好长一段距离。
滑行过程中,车里燃油发生泄漏,引燃了车后轮胎,并烧到了驾驶室。
事故发生后,槽罐车的驾驶员李师傅很快就从驾驶室里跑了出来,当他惊恐地拍打自己腿上的火时,突然想到押运员还被困在里面,李师傅又冲回现场,用尽全力将同伴从副驾驶位置上拉了出来,并帮他把身上的火扑灭。
之后两人被紧急送往扬州市苏北人民医院救治。
押运员烧伤面积达60%,幸好驾驶员无大碍。
不过,由于受到撞击,罐体上出现两个漏洞,液氧大量泄漏,为了排除险情,扬州各部门现场排氧,26吨液氧全部放空。
事故处理:下午4 点左右,记者在现场看到,槽罐车罐体前后部位都发生了泄漏,白色的“烟”不断冒出。
据介绍,经过20 分钟左右的扑救,明火被基本控制,不过由于油箱温度过高,还是发生了爆炸,所幸有惊无险。
火控制住了,但液体一直在泄漏。
为了排除险情,消防员分别对前后两个漏洞进行强制堵漏,并将随身携带的衣服一并用上,覆盖在漏洞处。
该槽罐车厂家派出的工程师赶到了现场,大家现场研究决定,先现场将罐体的液氧放掉,然后再对罐体实施转移。
但排放液氧是有条件的,就是方圆500米范围内的车辆发动机必须熄火,否则会造成液氧爆炸等危险事件发生。
情况紧急,在交警部门的配合下,现场方圆500 米范围内的所有车辆发动机全部熄火。
厂方工程师见安全措施到位后,立即戴着面罩来到罐体尾部,把阀门打开,只见一股白色液体笔直从尾部冒了出来,喷到高速下面的绿化带中。
在排液的过程中,消防员同时出动水枪,从各个角度对液体进行稀释,防止出现意外。
案例分析试题一

《事故案例分析》试题一案例1、某危险化学品生产企业,有北区、中区和南区等三个生产厂区,北区有库房等,在南区通过氧化反应生产脂溶性剧毒危险化学品A,中区为办公区。
为扩大生产,计划在北区新建工程项目。
2007年7月2日,北区库房发生爆炸事故,造成作业人员9人死亡、5人受伤。
事故损失包括:医药费12万元,丧葬费5万元,抚恤赔偿金180万元,罚款45万元,补充新员工培训费3万元,现场抢险费200万元,停工损失800万元。
根据以上场景,回答下列问题(共7题,每题2分,其中1~3题为单选题,4~7题为多选题):1.该企业要取得安全生产许可证应进行的安全评价为( )。
A.安全预评价B.安全验收评价C.安全现状评价D.安全技术评价E.安全管理评价2.按照上述事故损失明细,此次事故的直接经济损失为( )。
A.197万元 B.397万元 C.442万元 D.1197万元 E.1200万元3.建立、健全本企业的安全生产责任制是( )的责任。
A.该单位主要负责人 B.该单位安全管理人员C.该单位安全技术人员D.政府安全监管部门E.该单位主管部门4.按照《安全生产许可证条例》的规定,该企业要取得安全生产许可证,应该具备的安全生产条件包括( )。
A.建立健全安全生产责任制 B.安全投入符合安全生产要求C.每半年进行一次安全评价D.设置安全生产管理机构,配置专职安全生产管理人员E.企业技术负责人取得注册安全工程师执业资格5.根据产品A的性质,下列关于产品A的危害和监管的说法,正确的有( )。
A.产品A不可以经皮肤吸收引起接触人员中毒B.因产品A为脂溶性的,所以进入人体消化道不能被吸收C.生产产品A的反应过程失控,有发生爆炸的可能性D.产品A必须存储在经安监部门批准设置的专门危险化学品仓库中E.运输产品A时,应指派专人押运,押运人员不得少于2人6.为了防止危险化学品爆炸事故再次发生,该企业可以采取的措施有( )。
A.安装安全监控系统B.进行危险源辨识C.开展风险评价D.准备充足的医疗救护设备E.疏散企业周围的居民7.此次事故发生后,安全生产监督管理部门和负有安全生产监管职责的有关部门应逐级上报事故情况。
氧化反应的火灾危险性分析与评价

氧化反应的火灾危险性分析与评价黄郑华李建华赵建分析了氧化反应生产工艺过程的火灾危险性,并运用美国道化学公司的火灾、爆炸危险指数评价方法对氧化反应装置的火灾、爆炸危险性进行了评价,探讨了针对性的防火防爆技术措施。
氧化反应在化工生产中得到广泛的应用。
通过氧化反应,可以生产大宗有机中间体和聚合物单体。
然而,氧化反应生产过程中潜在较大的火灾危险性,国内外曾有过多次氧化反应器爆炸的案例。
2004年7月26日,厦门翔鹭石化企业有限公司90万t/a精对苯二甲酸装置的氧化反应器,因长年高压、高温工作,罐体内物料搅拌装置产生振动,使进料管道法兰松动,管道法兰连接处突然产生裂缝,大量物料喷出,因其本身的高温起物料着火燃烧,3名工人被物料灼伤。
加强对氧化反应防火、防爆的研究,十分重要。
1 氧化反应火灾爆炸危险性分析1.1原料和产品易燃易爆有毒被氧化和物质大都具有火灾爆炸危险性,例如乙稀、丙烯、萘、乙醛、氨等。
某些氧化中间产物不稳定,甚至还有火灾爆炸危险,例如液相氧化反应系统往往存在一定尝试的烃类过氧化氢和过氧酸类中间产物,当其浓度积累到一定程度后会发生分解而导致爆炸。
非均相丙烯氨氧化反应副产的氢氰酸、乙腈和丙烯醛是可燃有毒的物质。
部分氧化产品也具有火灾爆炸危险性,例如乙烯氧化生成的环氰化生成的环氧乙烷是可燃气体;甲醇氧化生成的甲醛(含36.7%甲醛)是易燃液体;丙烯氨氧化生成的丙烯腈是易燃液体。
1.2反应温度高,放热量大氧化反应强烈放热,反应温度高,传热情况复杂。
非均相氧化系统中存在催化剂颗粒内及其与气体间的传热,以及床层与管壁间传热。
催化剂的载体往往是导热欠佳的物质,因此,如采用固定床反应器,床层温度分布受到传热效率的限制,可能产生较大温差,甚至引起飞温,导致火灾爆炸事故;如采用流化床反应器,反应热若不能及时移出,反应器内稀相段上就极易发生燃烧,因为原料在浓相段尚有一部分未转化,进入稀相段后会进一步反应放热,当温度达到物料的自燃点就可能发生燃烧。
双氧水装置事故分析案例
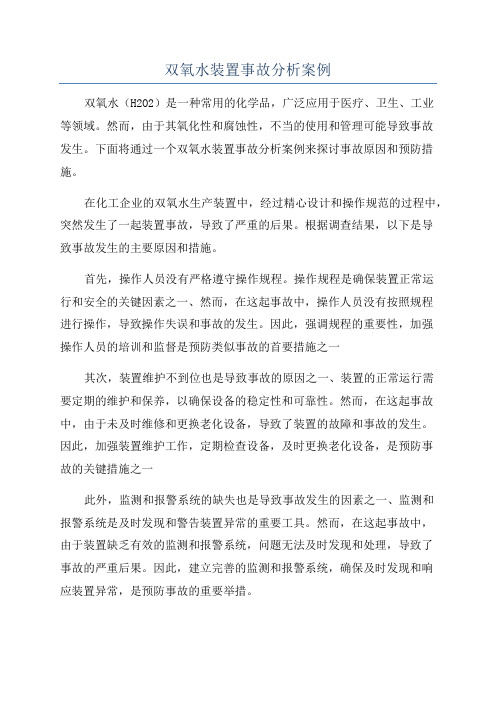
双氧水装置事故分析案例双氧水(H2O2)是一种常用的化学品,广泛应用于医疗、卫生、工业等领域。
然而,由于其氧化性和腐蚀性,不当的使用和管理可能导致事故发生。
下面将通过一个双氧水装置事故分析案例来探讨事故原因和预防措施。
在化工企业的双氧水生产装置中,经过精心设计和操作规范的过程中,突然发生了一起装置事故,导致了严重的后果。
根据调查结果,以下是导致事故发生的主要原因和措施。
首先,操作人员没有严格遵守操作规程。
操作规程是确保装置正常运行和安全的关键因素之一、然而,在这起事故中,操作人员没有按照规程进行操作,导致操作失误和事故的发生。
因此,强调规程的重要性,加强操作人员的培训和监督是预防类似事故的首要措施之一其次,装置维护不到位也是导致事故的原因之一、装置的正常运行需要定期的维护和保养,以确保设备的稳定性和可靠性。
然而,在这起事故中,由于未及时维修和更换老化设备,导致了装置的故障和事故的发生。
因此,加强装置维护工作,定期检查设备,及时更换老化设备,是预防事故的关键措施之一此外,监测和报警系统的缺失也是导致事故发生的因素之一、监测和报警系统是及时发现和警告装置异常的重要工具。
然而,在这起事故中,由于装置缺乏有效的监测和报警系统,问题无法及时发现和处理,导致了事故的严重后果。
因此,建立完善的监测和报警系统,确保及时发现和响应装置异常,是预防事故的重要举措。
最后,紧急救援准备不到位也是导致事故后果严重化的原因之一、当事故发生时,救援措施的及时性和有效性对于减少事故的损失至关重要。
然而,在这起事故中,由于缺乏紧急救援准备和培训,导致事故后果严重化。
因此,建立紧急救援预案,加强事故应急演练和培训,是预防和应对事故的重要手段。
综上所述,双氧水装置事故的发生往往与操作不规范、维护不到位、监测和报警系统的缺失以及紧急救援准备不足等因素密切相关。
为了预防类似事故的发生,必须加强操作人员的培训和监督,定期检查设备并及时更换老化设备,建立完善的监测和报警系统,以及制定紧急救援预案并加强培训。
关于氧化剂事故的案例

关于氧化剂事故的案例一、事故概况1993年8月,深圳市某危险物品储运公司,由于4号仓内过硫酸铵(强氧化剂)和硫化碱(还原剂)混存,而过硫酸铵不稳定,极易放出臭氧,扩散接触硫化碱,引发了激烈的氧化还原反应,形成大量热积累,导致起火燃烧。
4号仓的燃烧,引燃了库区多种可燃物质,库区空气温度升高,使多种化学危险品处于被持续加热状态。
6号仓内存放的约30吨有机易燃液体被加热到沸点以上,快速挥发,冲破包装和空气、烟气形成爆炸性混合物,继而引发了燃爆。
出现闪光和火球,引发该仓内存放的硝酸铵第二次剧烈爆炸。
形成蘑菇状云团(爆炸核心高温气流急速上升,周围气体向这里补充)。
这起事故共造成15人死亡,200多人受伤,其中重伤25人,直接经济损失超过2.5亿元。
二、事故原因1、干杂仓库被违章改作化学危险品仓库及仓内化学危险品存入严重违章是事故的主要原因。
4号仓内混存的氧化剂与还原剂接触是事故的直接原因。
属严重的责任事故。
2、深圳市政府没有认真贯彻“安全第一,预防为主”的方针,城市规划忽视安全要求,安全意识淡薄。
深圳市缺水长期未得到解决,这次事故由于消防无水,失去了火灾初期的灭火良机。
3、深圳市公安局执法不严,监督不力。
未按规定严格审查,就给安贸危险品公司发放《广东省爆炸物品储存许可证》、《剧毒物品储存许可证》、《深圳市爆炸品、危险品接卸中转许可证》,使该公司在不具备国家规定的安全条件下,经营民用爆炸物品合法化。
致使重大隐患未能消除而发生事故。
4、储运公司安全管理混乱,冒险蛮干。
货物到达才临时指定仓库堆放的现象时有发生,仓管员和搬运工仅根据仓库剩余空间大小决定存放地点和存放方式,混存混装习以为常。
危险品接卸过程,不按规范化程序执行,违章指挥、违章作业、有令不行、有禁不止,决定了发生事故的必然性。
三、防范措施1.要搞好城市规划和市政建设。
各级政府在城市规划中,要有全局观念,统筹规划,合理布局,始终坚持经济建设与市政建设同步发展的原则,确保人民生命和国家财产的安全,对严重影响城市安全的重大隐患要彻底解决。
甲硫醚氧化塔事故案例

甲硫醚氧化塔事故案例1. 2019年某化工厂发生甲硫醚氧化塔爆炸事故,导致多人死亡和重伤。
事故原因初步认定为操作不当和设备失效。
2. 该化工厂生产甲硫醚的过程中,使用甲硫醚氧化塔进行氧化反应。
事故发生时,氧化塔内部的反应温度和压力异常升高,最终导致爆炸。
3. 事故调查显示,事故的直接原因是操作人员在操作过程中未能及时发现和处理氧化塔内部温度和压力的异常变化。
操作人员对氧化塔的运行状态了解不足,未能正确判断和处理危险信号。
4. 另外,事故还暴露出甲硫醚氧化塔的设计和设备维护存在问题。
氧化塔的温度和压力监测装置未能及时报警或故障,导致操作人员无法得知内部异常情况。
5. 事故发生后,化工厂对甲硫醚氧化塔的安全管理进行了全面检查和整改。
对操作人员进行了培训和考核,加强了安全意识和应急处置能力。
6. 此外,化工厂还对甲硫醚氧化塔的设备进行了升级改造,增加了温度和压力监测装置,并加强了设备维护和检修工作,提高了设备的安全性和可靠性。
7. 事故发生后,相关部门对该化工厂的安全生产管理进行了调查和处罚。
化工厂被责令停产整顿,并处以巨额罚款。
8. 该事故引起了社会各界的广泛关注,促使相关部门对化工行业的安全监管进行了加强,出台了更为严格的安全生产标准和规范。
9. 事故的教训是,化工企业在生产过程中必须高度重视设备安全和操作人员的安全培训,加强设备的监测和维护,确保生产过程的安全性和可控性。
10. 各级政府和相关部门应加大对化工企业的安全监管力度,加强对危险化学品生产企业的巡查和监督,确保企业严格遵守安全生产法规和标准。
同时,还应提供相关技术支持和培训,提高化工企业的安全管理水平。
- 1、下载文档前请自行甄别文档内容的完整性,平台不提供额外的编辑、内容补充、找答案等附加服务。
- 2、"仅部分预览"的文档,不可在线预览部分如存在完整性等问题,可反馈申请退款(可完整预览的文档不适用该条件!)。
- 3、如文档侵犯您的权益,请联系客服反馈,我们会尽快为您处理(人工客服工作时间:9:00-18:30)。
1、事故经过英国傅立克斯镇(Flixborough)Nypro公司环己烷车间包含了一串联式的6座氧化反应槽,以环己烷为原料制成己内酰胺。
其制造过程中,首先将环己烷在6个串联的氧化反应槽中,以辛酸盐(caprylic acid)为触媒,经空气氧化成环己酮和环己醇,再转变成己内酰胺。
1974年3月27日傍晚,反应系统中的5号氧化反应槽的碳钢外壳发现150cm长的裂纹,造成环己烷外泄,其原因为硝酸类物质产生的应力腐蚀。
值班人员向主管报告经同意后,开始降低反应系统的压力和温度,准备停车检验泄漏点。
经检验为氧化反应槽的内衬、外壳皆产生相当程度的破裂,不适合再参与反应过程,因此决定拆下5号氧化反应槽,以便检修。
翌日早上,经厂务会讨论后,厂长与相关技术人员认为停车检修需要3—6个月,而当时英国国内对于己内酰胺的需求甚急,不适合停工降低工厂产能,为了让该车间继续运行,决定将第5号氧化反应槽搬离,并在4号和6号氧化反应槽间连接一管线暂时以5座氧化反应槽维持生产。
在拆下5号氧化反应槽后,即进行修复工作。
在装4号和6号氧化反应槽间连接管线时,施工人员仅在现场地面上以粉笔画一简单的修复工程图样,并没有预先规划并绘制正规的设计工程图及必要的工程应力详细核算。
现场以鹰架支撑管子。
两氧化反应槽间因有高度差(约相差35.5cm),故以三曲旁通管作为两氧化反应槽间的连接管,而原来氧化反应槽出口处的伸缩接头管径为72cm,但当时厂内只有管径为51cm的管线可用。
施工人员经大概的计算后,认为51cM管线尚可提供反应时所需的流量,并以直管计算压力后得知其反应亦可承受操作时的压力,决定以此管取代之。
三曲旁通管仅以分成四点的鹰架支撑着,结构上并不坚固。
于3月30日2时完成全部修复作业。
修复后经试漏检测即恢复生产。
但到5月29日又发现泄漏。
其位置为下部液面计处。
于是将整个反应系统的压力降低至0.15MPa,并降低温度使之冷却,停工2天执行部分修复工作。
于6月1日4时再度开工。
不久环己烷的循环部分又发生泄漏,因此停止加热,再度进行修补,至早上5时才开工。
在6月1日7时换班时,值班主管对压力情况未对下一班值班人员交代清楚,因此值班人员并未注意压力变化情况。
到6月1日下午,开始有可燃性气体外泄,但并无人员警觉或注意到。
将近16时,空气中弥漫着大量的可燃性气体,并向外扩散。
2分钟后,可能在氢气2车间遇点火源着火,随即发生了爆炸。
环己烷蒸气云的爆炸造成2个替代的伸缩接头受不当的外力引起破裂挫曲,而连接4号和6号氧化反应槽的三曲管因爆炸而扭曲成“<”形掉落在地面。
由此可以推断出2个替代的伸缩接头受不了当时的外力引起破裂弯曲,造成容器内环己烷大量外泄。
2、原因分析由于工厂管理的不良、人员操作的失误及设备安置的错误,都直接或间接地导致了这次灾难的发生。
该起事故原因归纳如下:(1)维修过程无详细的规划查出5号氧化反应槽破裂需维修后,连接4号和6号氧化反应槽的管线的设计,并不是经由有经验的工程师负责,整个设计图是用粉笔简略地画在现场的地上。
氧化反应槽出口部分的法兰原应配装72cm管线,却以51cm管线代替,且对于此旁通管既未作强度计算,也未实施耐压检验。
由事故发生后旁通管弯曲成“<”状掉落,究其原因是旁通管的安装不够完好。
依英国国家标准规定,为了使伸缩管能在管轴方向伸缩,应安装饰缩接头;为防止因内部流体压力所产生的轴向移动,应在伸缩管附近对伸缩接头加以固定。
但是该厂并没有按照标准正确地作业。
(2)工厂的人事管理及生产工艺修改管理不良根据调查,事故发生前公司内有一位总工程师离职,职务空缺后并没有人员填补这一职位。
在移除5号氧化反应槽后进行4号、6号氧化反应槽暂时性连接工程时,这一职位空缺情况已经影响工艺修改。
在执行改善工程前,应先进行必要的风险评估,以确保基本过程整体设计没有被改变或破坏。
缺乏有经验的资深专业技术人员的指导,这是事故发生的祸因之一。
如果该厂没有工艺修改管理制度的话,修改前专家评估小组必会先查看有关法规、标准、操作规程等相关资料,然后才会订立安全的具体方案,不至于因总工程师的离职而有考虑不周之憾,以免重大事故的发生。
工艺修改管理制度的欠缺是此起事故的关键因素。
(3)值班人员交代不清爆炸前,6月1日上午曾有—次换班,但上班值班主管并没对下一值班人员交代凌晨泄漏修补情况,以至于值班人员不了解情况,而造成疏于查巡修补后的设备。
(4)测漏时压力设定不足在修复后使用0.39MPa的氮气进行试漏时发现有泄漏,进行部分焊接修补,再以0.88MPa 的氮气压力试漏确定无泄漏,于4月1日再度运转。
但是,依据英国标准规定,泄漏试验应以设计压力的1.3倍以上的压力进行水压试验。
如果该厂当时使用1.18MPa以上的压力试验,必然会立即发现缺陷处,这场事故或许能防患于末然。
再者,如果现场不能做水压试验时,亦可用气压试验代替,但是对于可能发生的危险应有妥善的防范措施。
(5)不锈钢管产生锌脆化现象化工厂锌的来源一般为镀锌钢料(如栏杆、阶梯、通道等),或是广泛用于保温材料的镀锌铁丝。
当不锈钢管受到应力(0.57MPa)和高温时,不用直接接触,只要附近有含锌物质就会导致锌的脆化现象,使不锈钢突然失效。
因此,当不锈钢材料受到相当高温时,不锈钢表面应仔细检查或酸洗。
该起事故发生后,在事故现场收集到不锈钢管发现有锌脆化表面龟裂现象,经研究,判断为与分离器连接的21cm不锈钢管线因锌产生脆化而发生龟裂。
(6)硝酸盐腐蚀反应槽对碳钢最具侵蚀性的物质为硝酸盐与碱性化合物。
当碳钢与上述可溶性盐类接触时,其硝酸根离子应当保持在100ppm以下,否则当金属表面温度超过50℃,可溶性盐类会被结晶析出而导致应力腐蚀。
经专家鉴定,5号氧化反应槽外壳的裂纹是由硝酸盐产生的应力腐蚀所致。
当发现5号氧化反应槽有裂纹时,未对其它氧化反应槽进行检查,同时也未探究其裂纹原因并采取措施。
(7)厂区建筑物、设备的配置不良死亡28人中有18人死于控制室内,因为该厂控制室、实验室、办公室等皆位于爆炸中心点的附近,且控制室是小木屋构造,而并非耐爆结构,造成爆炸区附近被完全摧毁,人员死伤严重。
(8)该厂储存过多的危险性可燃物质该厂事故当时储存着1500m3环己烷、300m3石脑油、50m3甲苯、120m3苯、2046m3汽油。
该厂经过许可的危险物质储存量仅有32m3石脑油、6.8m3汽油,但该厂却储存着大量未获批准储存的危险物质,这些物质也是爆炸后造成连续10天大火的主要原因。
(9)氮气的供应不足该厂某些生产过程安全的保障有赖于供给足够的氮气。
但事故后调查资料显示,环己烷氧化系统再次开车操作常受氮气供应不足而停顿,其原因是该厂本身氮气的产能不足,又无足够的氮气储存设备,需要厂外的供应补充。
因此,工厂本身具有足够的氮气生产设备,或有足够的安全可靠的氮气储存设备,才可能维持厂区的安全。
(10)缺乏紧急应变能力事故发生时,厂内员工未马上执行紧急应变处理程序,他们只能做一些简单的修复工作,各相关人员缺乏紧急应变能力的训练。
3预防措施由英国博立克斯镇爆炸事件,可明确地看出此灾难的发生原因不外乎人为的操作失误、厂区的配置不良、工艺设备故障及人事管理及工艺修改管理的缺失。
如何由此事件学习对作业现场实施检查,掌握作业现场潜在危害并加以改善,进而维护工厂的安全,以降低灾难发生的概率,确保人民及生态环境的安全。
由此事件提出下面几点建议:(1)落实危险物及有害物的周知制度存在于工厂中的危险物及有害物有多种,如爆炸性、可燃性、腐蚀性、毒性、放射性等物质。
为了确保这些危害物质能够被工人正确地使用而不至于产生危害,必须建立工厂危险物及有害物周知制度,一方面有效地管理工厂中的各种危害物质,另一方面使工人能够清楚地认识工厂中的各种危害物质的特性及正确的使用方法,以避免工人因不正确的使用这些危害物质而发生意外。
危险物及有害物的周知制度内容包括:1)危害物质周知计划书;2)危害物质清单;3)危害物质的标示;4)化学品安全技术说明书(MSDS);5)工人的安全卫生与训练。
(2)使用防爆型的电器设备在整个化工生产过程中会使用到大量的电器设备,这些电器设备如果没有经过特殊的设计,很容易产生火花,成为点火源,再加上化工厂内爆炸性及可燃性的物质相当的多,因此引起火灾爆炸的危险性相当的高,所以应尽可能在此类作业环境中采用特定等级防爆型的电器设备,降低爆炸发生概率。
一般防爆型的电器设备可分为五大类:1)耐压型的防爆设备;2)内压型的防爆设备;3)安全防爆设备;4)绝缘油防爆设备;5)本质安全化防爆设备。
(3)建立健全安全管理制度在此追求可持续发展的时代,只重视生产而忽视安全环保管理的经营理念是落伍的。
由此事故可以看出Nypro公司经营理念的不正确性,赶时生产固然重要,但是亦不能忽略工业安全而降低工程标准,省去必要的安全步骤往往欲速则不达。
如果企业在经营时,能够不累积小问题,不忽略小隐患的存在,往往能降低其生产过程中重大意外事故的风险。
(4)安装防漏和测漏装置在化学物质的工艺设备上,应装有防漏与测漏装置,以防泄漏的发生或在泄漏发生后发出警报,告知工作人员事先预防爆炸的发生。
(5)设置自动火灾监测警报装置自动火灾监测警报装置可及早发现火灾的发生,以及火灾初期的灭火,但需定期维修警报装置。
(6)实施量化风险评估生产过程安全风险评估的目的在于分析工艺过程中潜在危险发生原因及应有的保护措施,并评估潜在危险发生后的后果严重性,及危害发生频率,并评估其风险值是否可接受或需有改善措施以降低风险,保障工厂及社区的安全。
生产过程量化风险评估时需要考虑的事项及单元:化工生产过程风险评估定义、系统描述(生产工艺说明)、危害辩识、事故案例、选择分析程度、建立化工生产过程量化风险分析模式、潜在危害后果估计、潜在危害频率估计、风险评估及应用。
(7)建立周密的紧急应变体系对于工厂而言,建立一套完整的紧急应变体系是不可或缺的,其应变程序主要包括:紧急状况的通报、疏散计划、救灾、应变工作、灾后复原、灾后检讨。
通过有系统的规划,使得紧急应变程序在各类化学灾害中发挥其功能,其主要目的在于工厂发生化学灾害时,利用邻近的资源,在最短的时间内,有效地遏制灾害范围的扩大,以降低灾害对人类及环境的冲击,最终的目的就是保持一个安全无害的环境。