纱线色差的产生和预防
中长纱线色差问题的控制

4O 6 O 0 5 4 3 .8 5 19
编 号
1 6 . 1 5 . 5 3 8 7 3 1 9 5 9 2 8 34 .0 562 3 8 0 954 2 6 9 6 1 4 1 9 3 8 3 3 08 . 3
.
3 5 7 82 4 3 .8 0 3 3
3 6 .6 6 5 4 5 .9 4 4 3 2 15 0 4 6 . 6 6 . 2 417 9 4 5 7 3 6 .9
5 6 7 6 1 4 7 2 5 41 5 5 9 1 6 6 . 8 6 . 4 4 2 .0 4 9 4 0 22 4 7 6 . O 6 3 4 3 .l 5 1 80 2 80 8 6 .O 6 .8 4 5 .4 5 2 5 7 2 10 9 6 2 6 . 0 4 5 . 6 5 4 9 6 2 6 2 l 6 5 6 1 0 5 2 4 7 4 5 .6 2 75 1 6 . 3 6 2 4 8 . 8 1 5 4 6. 9 2 10 l 6 . 7 6 . 4 42 6 3 2 54 88 8 .2 l 6 . 5 6 6 4 2 . 6 3 5 7 9 9 3 30 1 6 9 6 5 4 2 2 4 5 7 34 3 8 3 1 6 9 6 4 4 2 2 5 5 7 7. 0 3 83 1 6 9 6 8 4 6 8 6 6 0 7. 0 37 9 1 6 .0 6 4 4 4 . 6 7 7 4 7. 0 5 2 7
易 产生 混和不 匀 。因为 涤纶纤 维相 对粘胶 纤维 蓬 松, 在抓 棉机 抓取纤 维 的过程 中, 涤纶纤维 相对 容 易 抓取 , 而粘胶 纤 维 由于 回潮 率高 打包 较紧 , 不够 蓬松, 不易抓 取 , 尤其 在 棉包 到达 箱底时 此现 象更 为突 出。有一 些企 业采 用预 开松 粘胶 的方法来 解 决这 一 问题 , 我 厂 根据 企 业 的实 际情 况 采 用小 而 量混 棉 的办法 , 每一 箱输 人原料 的过程 中 , 在 严格 按 照 二者 的 比例 喂^ , 同时 注 意 涤纶 与 粘 胶 多层 铺设 , 以确保混 和均 匀 。
纱线色差产生的原因及预防措施

纱线色差产生的原因及预防措施纱线色差是评定纱线品质的重要指标,也是棉纺企业在生产过程中把关产品质量的重点之一,色差又叫黄白纱,可以分为本色色差和染色色差。
本色色差就是产品在着色前显现的色差。
染色色差就是产品只有在着色后才能显现的色差。
一般来讲,纯化纤纱由于化纤原料颜色单一,故化纤纱线色差较小:涤棉、粘棉纱等化纤与棉混纺纱线色差也较小,而棉型纱线极易产生色差。
色差仅对同一批号的纱线而言,不同批号的纱线没有可比性。
色差仅凭肉眼就能看出来,不明显的需借助荧光灯来观察。
色差纱线对印染布和色织布等色布影响很大,会产生上色不匀、染色条花、染色色差等有损织物外观质量问题。
因此,控制纱线色差是纺纱生产中的一个重点。
纱线色差产生的原因本色色差:本色色差产生的原因是多方面的,如配棉工艺不合理,清棉工序混棉不均匀,各工序没有保证先纺先用,锭速级差引起的长片段和条干引起的短片段的捻度差异等,都是造成本色色差的主要因素。
染色色差:由于产品中掺有异性纤维或原棉成熟度差异过大,致使纤维着色能力不同而产生染色色差。
纱线产生色差的根本原因是原棉颜色的差异和在加工过程中对原料没有进行很好地利用、搭配,以及没有采取必要的把关和预防措施。
控制和预防纱线色差的措施(1)加强棉花检验和逐包检验工作。
取样一定要全面,要确实有代表性,各项指标试验要准确,真突地反映原棉实际质量情况;对正常使用中的棉花进行逐包检验工作,发现个别品级、色泽等质量指标有差异的棉包,要合理使用。
(2)配棉时要保持原棉色泽上有主体。
使一种颜色原棉占70%以上,并且有一定量库存保持相对稳定。
配棉还要满足相似原则。
所谓相似原则,就是某批原棉色泽和主体色泽差距大时,它的各项物理性能指标必须和主体性能相似。
反之,如果原棉性能指标和主体性能差距大时,原棉的色泽就必须和主体色泽相似。
同时,在色泽转变时,要稳定的进行调整,每批调整幅度不大于5%,调整周期可根据细纱车间生产能力确定。
(3)色差的程度随棉纤维成熟情况而变化,成熟度差异越大的纤维,其色差越大,而成熟度接近的棉花,其色差较小。
筒子染色时内外色差原因及预防措施

筒子染色时内外色差原因及预防措施1 简纱染色色差色花的形成原因1.1 筒纱质量络筒时要保证筒纱卷绕密度一致,卷绕硬度一般为27±2(肖氏硬度)。
若卷绕硬度过小,染色过程中受气流的冲击会损伤纱,导致成形不良,也会造成染液局部短路,使筒纱染色深浅不一,产生染花;若卷绕硬度过大,染液不易渗透造成内外色差。
1.2 设备运行状况在设备方面,主泵泵力不足,换向装置不到位,电脑指示灯失灵,染缸法兰盘漏液,都会降低流速,严重时就会造成色花。
1.2.1 泵力不足及换向装置不到位操作时盐未被溶化就投入染缸,进泵后泵叶与盐摩擦,与泵体之间的间隙增大,而造成泵力不足;鹅颈管式换向装置活塞运行不良,行程不到位,致使染色压力达不到。
1.2.2 染缸部件漏液因装纱后,纱架重量很重,起吊过程中与染缸底部发生碰撞,使染缸底部盘管的焊接点开裂、螺丝松动,纱杆与底盘密封不好,导致漏流。
1.2.3 控温系统由于缸内液体淋渗到感温针上,使感温针运作失灵,造成控温系统所显示的`温度与实际温度不符,导致染色温度不准确,使色相发生偏差。
1.3 工艺1.3.1 前处理前处理的除杂、毛效、白度、洗后pH值和双氧水的去除情况都会影响染色的均匀性。
1.3.2 染色选择合适的染料与助剂,设计合理的染色工艺可以保证染色质量。
工艺设计不好,选择三原色的配伍性差,也会造成色花。
2 防止色差色花的措施2.1 筒纱质量筒纱成形要严格把关,杜绝哑铃纱、喇叭纱、重叠纱、漏眼纱及硬边纱,卷绕密度要控制在要求范围之内,过硬过松的要挑出,筒纱大小一致。
2.2 设备维修为保证设备正常运行,对上述所存在的问题要定期检查,这样才能保证设备运转良好和染色质量稳定。
定期对水、汽阀门进行检查,看有无开启不灵活和关闭不严现象,加强设备维护。
2.3 前处理工艺选择前处理工艺要煮透、煮匀,以便于染色。
为缩短时间,采用煮练漂白同浴法。
工艺处方(g/L)3O%氢氧化钠 4精练剂 2渗透剂 2双氧水 6稳定剂 3前处理工艺曲线(见图1)。
筒子纱染色如何避免染色上色不匀、白节白点、色渍色斑
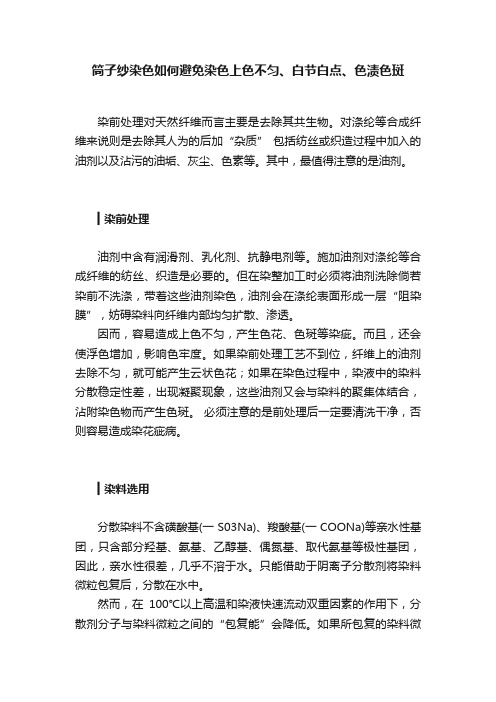
筒子纱染色如何避免染色上色不匀、白节白点、色渍色斑染前处理对天然纤维而言主要是去除其共生物。
对涤纶等合成纤维来说则是去除其人为的后加“杂质” 包括纺丝或织造过程中加入的油剂以及沾污的油垢、灰尘、色素等。
其中,最值得注意的是油剂。
▎染前处理油剂中含有润滑剂、乳化剂、抗静电剂等。
施加油剂对涤纶等合成纤维的纺丝、织造是必要的。
但在染整加工时必须将油剂洗除倘若染前不洗涤,带着这些油剂染色,油剂会在涤纶表面形成一层“阻染膜”,妨碍染料向纤维内部均匀扩散、渗透。
因而,容易造成上色不匀,产生色花、色斑等染疵。
而且,还会使浮色增加,影响色牢度。
如果染前处理工艺不到位,纤维上的油剂去除不匀,就可能产生云状色花;如果在染色过程中,染液中的染料分散稳定性差,出现凝聚现象,这些油剂又会与染料的聚集体结合,沾附染色物而产生色斑。
必须注意的是前处理后一定要清洗干净,否则容易造成染花疵病。
▎染料选用分散染料不含磺酸基(一S03Na)、羧酸基(一COONa)等亲水性基团,只含部分羟基、氨基、乙醇基、偶氮基、取代氨基等极性基团,因此,亲水性很差,几乎不溶于水。
只能借助于阴离子分散剂将染料微粒包复后,分散在水中。
然而,在100℃以上高温和染液快速流动双重因素的作用下,分散剂分子与染料微粒之间的“包复能”会降低。
如果所包复的染料微粒游离出来,就会重新聚集成更大的染料颗粒。
这种现象即为分散染料的“高温凝聚性”不同结构的分散染料,其热凝聚现象不同。
大体可分三种:一为不易发生热凝聚。
这类染料不会因升温、降温或相互碰撞而凝聚。
使用这样的染料染色一般不会造成染色不匀或色斑色渍。
二为容易发生热凝聚但随着染料分子向纤维内部扩散,染料的聚集体会再度解聚,只要染料在纤维表面吸附均匀,一般就不会造成色花、色渍。
三为容易发生热凝聚,而且在染色过程中,又难以解聚。
使用这类染料染色时,特别是当使用的分散剂或匀染剂高温分散能力较差时,就很容易由于染料的热凝聚而造成色泽不匀。
纱线色差的产生和预防措施

纱线色差的产生和预防措施现代纺织品制造技术的发展为纱线色差的发生提供了更多的机会。
纱线色差是指纱线色调和所需(订单)色调之间的偏差,它可能会破坏最终产品的外观,影响客户的满意度,甚至严重影响纺织品企业的声誉。
因此,研究纱线色差的产生原因,以及采取的相应的预防措施,以确保色彩质量,显得格外重要。
一般来说,纱线色差的产生是由于原料、染色工艺和织造工艺等多种因素引起的。
其中较为重要的原因是原料质量和染色过程中缺乏精确的操作技术。
首先,原料的质量要求会影响纱线色差的发生,如果原料质量低劣,在染色过程中会造成大量残余,这样会影响最终色彩的一致性,从而导致纱线色差的发生。
此外,原料的颜色和光泽也会影响染色的成功程度,如果原料本身的色彩过淡,那么在染色后的色彩效果就会比预期的差。
除原料质量外,纱线色差也可能是由于染色工艺不足而产生的。
现代染色工艺要求对染料的控制,以保证每一批纱线的工艺一致,消除纱线色差的发生。
然而,大多数纺织企业在实际染色过程中都有日常管理的漏洞,以及缺乏操作技术,这些都会导致染色结果的不可预知性。
另外,织造工艺的不当也会导致纱线色差的发生。
机织布由纱线和纬线组成,它们的编织位置会影响布料的外观,而编织不均匀,布料色差也会出现。
此外,机织布也会出现变形,如果这种变形影响布料色调,也会出现色差现象。
上述原因都可能导致纱线色差,但是,可以采取一些措施来预防色差的发生。
首先,在投入生产前,要对原料进行全面检测,严格控制原料的质量。
此外,染色工艺也需要加以完善,包括机器维护、染料和水质的检测,以及精确控制每一步的操作过程,使染色质量达到理想状态。
此外,还需要加强对编织工艺的管理,防止布料变形,以保障机织布的色彩一致性。
以上是纱线色差的产生及其预防措施。
纱线色差的发生将会影响纺织品企业的声誉,因此必须重视,从原料、染色工艺、织造工艺等多方面入手,制定有效的预防措施,以保障纱线色彩的一致性。
仅有一致的控制才能保障纱线色彩的一致性,才能满足市场对纱线色彩的需求。
筒子纱染色内外层色差产生的原因及防止

维普资讯
染
整
技
术
V 12 o2 o 4N . .
A t2 0 p. 02
筒子纱在染色过程中正反循环时间比, 则应根
据 泵 的扬 程流量 、 纱线类 别 而定 一般 筒纱采 用 反
襄 1 筒 纱的卷绕 密度
循环 ( 外一 内) 时间大于正循环 ( 内一外) 时间。 筒子
注: 筒子 纱 支数 越 南 , 相应 筒 子 纱 卷 绕 密度 应越 小 。
3 43 筒 子纱 染 色工艺 .. () 涤工 艺 ; 1染
分散染料染涤 , 一般采用高温高压染色法 。在 高温高压条件下 , 染料分子产生强烈运动, 从纤维 表面向内部扩散 , 而纤维表面又不断被染料饱和溶
纱颜 色 内层 浅 , 外层深 , 增加染 液 的正 循环 ; 筒子纱
颜色内层深 , 外层浅 , 则增加反循环时间。
3 3 染料 的选 择 .
在染涤棉混纺纱 、 全棉纱时, 染料选择的好与 坏是影响筒纱 内外色差的最重要因素 , 由于筒子纱
染 色 的特殊性 ,要求 所用 染料 有较好 的渗 透性 、优 良的移 染性 、 和染 色牢 度 。 在染 色 中 , 染物 的色 泽往 往不 是来 自一 个 染料 ,而 是 由几个 染 料拼 色所 得 , 染料 拼色 时应考 虑掌 握 以下 几条 原 则 ._ a 染料 对纤 维 的适应性 ;.染料 一般 采用 同类 型 ;.染 料 的性 b c 能 , 接性 , 散性 , 色牢 度 等尽 可能一致 。 直 扩 染 若所选 用 的染料 它们 的相溶 性 ,同步性 ,重演
对铁 的含 量也应控 制好 ,如 f — F 含 量过
其一织机中产生 , 其二是筒子色纱有 内外层色差。 针对筒子纱 内外层色差问题 , 将从以下各个环节进
纱线色差的产生和预防措施

纱线色差的产生和预防措施
纱线色差是指纱线在不同色泽的原因,是纱线在颜色调色不同而产生异色的情况,是
所有纱线制造和应用过程中,最重要也是最常见的缺陷。
主要由原材料、人工操作、操作
设备等多重因素造成,在后期加工中会产生较大的影响,严重影响产品的整体外观,影响
产品质量。
产生纱线色差的原因很多,通常由以下几个方面造成:
一是由于原料的质量异质造成的色差。
纱线的原料是棉花,它含有一些品质的不同,
比如纤维的紧密程度、丝光度、棉头的多少等,这也会影响到最终产品的颜色;
二是涂料的不同造成的色差。
涂料和助剂的配比非常重要,偏差越大,纱线色差就越大;
三是纱线染色技术的不同出现的色差。
包括温度、蒸汽压力、pH值、时间等,任何一项出现偏差,都会导致色差;
四是纱线混纺技术的不精确造成的色差。
在纱线混纺的过程中,各种棉纤维的量有一
定的量关系,在细节处理上容易出现误差,会产生色差。
要预防纱线色差,需从原材料、涂料、设备、技术等多方面入手。
首先,在涂料上应制定标准化比例,严格控制调色配比;
其次,采用先进的纱线染色技术,开发出色彩稳定、耐用和抗污染性能高的染料,使
产品色彩显示精确;
再次,结合使用纱线混纺和染色机,定制合理的技术参数,更为精确的控制混纺质量;
最后,有效的质量安全管理措施,使每一道工序走的更加严密,也使纱线质量更加稳定。
综上所述,要想降低纱线色差的可能性,需要在原材料调配,设备技术升级,质量监
测和安全管理等多个方面进行精细化管理,从而提高纱线色差的预防能力。
染整问题总结

染整问题总结引言染整是纺织行业中重要的一个环节,主要负责将纱线、面料等进行染色、整理和处理,使其达到预期的色彩、质地和外观效果。
然而,在染整过程中经常会出现一些问题,影响产品质量和生产效率。
本文将对染整问题进行总结和分析,希望能够帮助相关从业人员尽快解决问题。
问题一:色差问题在染整过程中,色差是一个常见的问题。
染色后的纱线或面料与预期色彩存在一定的偏差,造成产品的色彩不稳定或不一致。
产生色差的原因可以归结为以下几点:1.配方不准确:染色配方中的染料浓度、PH值、时间等参数可能存在误差,导致染色结果与预期不符。
2.染色条件不合适:温度、湿度、搅拌速度等条件对染色结果有重要影响,不合适的条件可能导致色差问题。
3.染料质量问题:染料的质量差异也会导致染色结果不稳定,有些染料可能存在色牢度不高的问题,容易褪色或变色。
4.染色工艺控制不当:染色过程中搅拌、上浆、漂洗等环节的控制不当也会产生色差。
解决色差问题的方法包括加强配方管理,严格控制染色条件,选择高质量的染料和改进染色工艺等。
问题二:退色问题退色是指染色后的纱线或面料出现褪色现象,使得产品的颜色失去原有的鲜艳度。
退色的原因主要有以下几点:1.染料固定不牢:染料在染色后未完全固定在纤维上,容易在后续的使用或洗涤过程中褪色。
2.染色不均匀:染色过程中染料的分散均匀程度不够,导致染色结果不稳定,在使用或洗涤后容易出现部分褪色的情况。
3.织物质量问题:如果面料质地不均匀或存在质量问题,染色后容易出现褪色。
解决退色问题的方法包括加强染料固定性能的测试和控制,改进染色工艺,选择质地均匀的面料等。
问题三:尺寸变化问题在染整过程中,纱线和面料的尺寸变化是一个常见的问题。
尺寸变化指的是纱线或面料在染整过程中发生的收缩或伸展现象,导致最终产品的尺寸与预期不符。
尺寸变化的原因主要有以下几点:1.温度影响:纱线或面料在高温下会发生收缩,而在低温下会发生伸展,染色过程中的温度变化可能导致尺寸变化。
一色色织布左中右色差解决方法
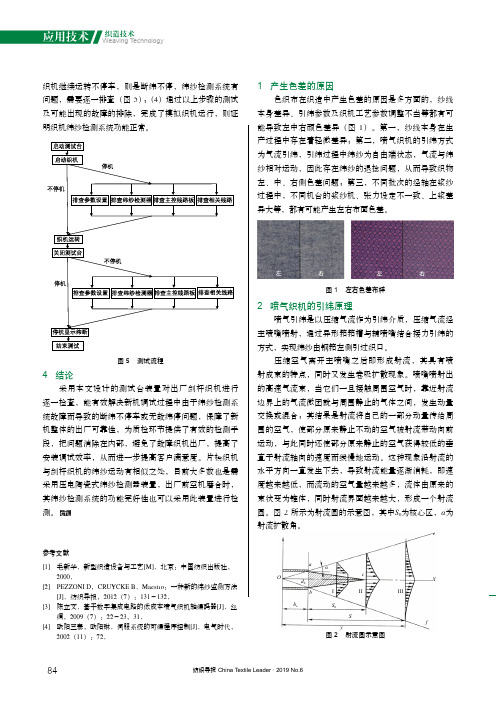
因是织缩率分布不匀造成的。当织物左右两边纬向织缩率大,则纬纱的弯曲程度较大,织物表面则呈现纬向颜
色;织物中部纬向织缩率小,则纬纱的弯曲程度较小,织物表面呈现经向颜色。文章通过引纬工艺参数和上机
工艺的调整,解决了织物左中右差异的问题,保证了织物颜色一致。
关键词:色织布;色差;气压
中图分类号:TS115.4
图 5 测试流程
4 结论
采用本文设计的测试台装置对出厂剑杆织机进行 逐一检查,能有效解决新机调试过程中由于纬纱检测系 统故障而导致的断纬不停车或无故纬停问题,保障了新 机整体的出厂可靠性,为质检环节提供了有效的检测手 段,把问题消除在内部,避免了故障织机出厂,提高了 安装调试效率,从而进一步提高客户满意度。片梭织机 与剑杆织机的纬纱运动有相似之处,目前大多数也是需 采用压电陶瓷式纬纱检测器装置,出厂前空机磨合时, 其纬纱检测系统的功能完好性也可以采用此装置进行检 测。
在条件相同时,摩擦系数愈大的纱线,气流对纱线 的摩擦牵引力愈大。实际引纬时,纬纱除了受到气流的 摩擦牵引力外,还受到阻力的作用,阻力主要由纬纱进 喷嘴之前与导纱器的摩擦引起。
2002(11):72.
图 1 左右色差布样
2 喷气织机的引纬原理
喷气引纬是以压缩气流作为引纬介质,压缩气流经 主喷嘴喷射,通过异形筘筘槽与辅喷嘴结合接力引纬的 方式,实现纬纱由钢筘左侧引过织口。
压缩空气离开主喷嘴之后即形成射流,其具有喷 射成束的特点,同时又发生卷吸扩散现象。喷嘴喷射出 的高速气流束,当它们一旦接触周围空气时,靠近射流 边界上的气流微团就与周围静止的气体之间,发生动量 交换或混合;其结果是射流将自己的一部分动量传给周 围的空气,使部分原来静止不动的空气被射流带动向前 运动,与此同时还使部分原来静止的空气获得较低的垂 直于射流轴向的速度而缓慢地运动。这种现象沿射流的 水平方向一直发生下去,导致射流能量逐渐消耗,即速 度越来越低,而流动的空气量越来越多,流体由原来的 束状变为锥体,同时射流界面越来越大,形成一个射流 圆。图 2 所示为射流圆的示意图,其中S0为核心区,α为 射流扩散角。
低级棉纺纱色差产生的原因与防治
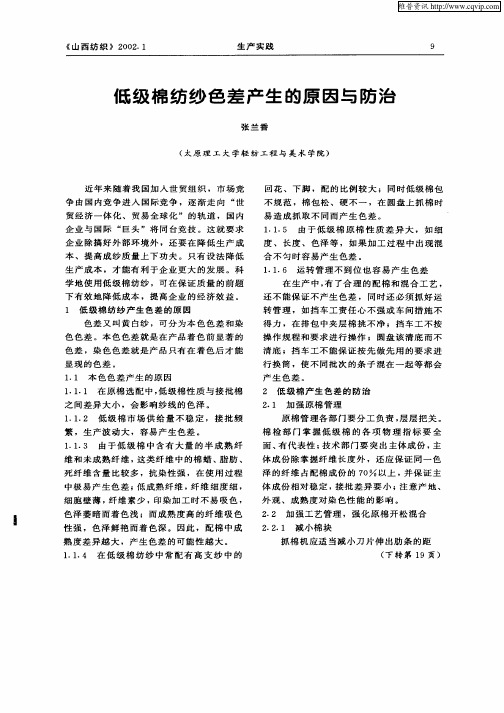
第 2路 上 针 成 圈 下 针 浮 线 ,两 路 一循 环 。 纱 线 排 列 : 1路 喂 人 1 . tx天 丝 , 第 4 8e 第
繁 ,生 产 波 动 大 ,容 易 产 生 色 差 。
1 1 3 由 于 低 级 棉 中 含 有 大 量 的 半 成 熟 纤 . . 维 和 未 成 熟 纤 维 , 类 纤 维 中 的棉 蜡 、 肪 、 这 脂
死 纤 维 含 量 比较 多 ,抗 染 性 强 ,在 使 用 过 程
面 、 代表性 ; 术 部门要 突出主体成份 , 有 技 主 体 成 份 除 掌 握纤 维 长 度 外 ,还 应 保 证 同一 色
回花 、下 脚 ,配 的 比例 较 大 ; 同 时低 级 棉 包 不 规 范 ,棉 包 松 、 硬 不 一 ,在 圆 盘 上 抓 经 济 一 体 化 、 贸 易 全球 化 ” 的 轨 道 , 国 内
企业 与国际 “ 巨头 ”将 同 台竞 技 。这 就 要 求 企 业 除 搞好 外 部 环 境 外 ,还 要 在 降 低 生 产 成 本 、 提 高成 纱 质 量 上 下 功 夫 。 只 有 设 法 降 低 生 产 成 本 ,才 能 有 利 于 企 业 更 大 的 发 展 。科 学 地 使 用 低 级 棉 纺 纱 ,可 在 保 证 质 量 的 前 题 下 有 效 地 降低 成 本 ,提 高 企 业 的 经 济 效 益 。
色 差 ,染 色 色 差 就 是 产 品 只 有 在 着 色 后 才 能
显 现的色差 。 1 1 本 色 色 差 产 生 的 原 因 .
行 换 筒 ,使 不 同批 次 的 条 子 混 在 一 起 等 都 会
产 生色差 。 2 低 级 棉 产 生 色 差 的 防 治 2 1 加 强 原 棉 管理 .
大师说印染83篇棉织物轧染色差的原因及预防措施

大师说印染83篇棉织物轧染色差的原因及预防措施1前言与间歇式卷染和绳状染色相比,连续轧染冈生产效率较高、适应品种较广、工艺控制相对简单而被众多染厂采用。
无论是棉织物还是涤棉织物,连续轧染时的色差问题,一直是困扰印染企业不断稳定和提高产品质量的难题。
特别是左中右色差和前后色差,严重影响产品质量且很难修复。
分析其原因,主要包括前处理、染色、后处理等多个加工工序,同时还包括加工设备等原因。
其中关键因素有:坯布、半制品、前处理、轧车、轧槽、预烘、预缩设备等。
在生产过程中对上述关键因素进行有效地控制,对降低连续轧染产品的色差具有重要意义。
2色差产生原因及预防措旌2.1坯布以全棉织物为例,新上机的坯布在规格上与后续生产出来的坯布总会有些区别。
如果再加上织机调试的原因,就会对坯布织造产生更大的影响。
即使是长期生产的常规品种,在织造过程中织物布边密度相对于织物中部密度也会有所区别。
上述这些情况在坯布状态下不易察觉,染成成品后就会对织物的组织密度产生直接影响,因组织密度的疏密形成布面阴影差异,容易在人们的视觉上产生浅或深的带状色差。
在轧染加工中织物回潮率对左中右色差的产生不容忽视。
实际上,把一块半漂棉织物放在烘箱中烘干一段时间,再把织物迅速取出,用电子天平称量其质量后会发现,读数无法固定。
主要原因就是因为干燥的棉织物会不断吸收空气中的水分。
而在染色过程中,织物单位面积含水量越多,浸轧过程中吸附染料量就越少,织物得色就浅。
如果织物含水量越少,浸轧过程中吸附染料量就越多,织物得色就深。
退浆和煮练不匀,棉织物的吸水性也会不均匀。
丝光不均匀也会产生吸色不均匀。
染色前烘干不均匀,也会造成棉织物含水不均匀。
凡此种种都会对染色均匀性产生不良影响,造成棉织物连续轧染加工的产品容易产生左右色差。
烘干后的半成品需要落布或打卷。
以落布为例,织物经过前处理,以甩布方式堆积到布车,布与布之间空隙较大,布与空气接触面积较多,水分渗入布堆的速度较快,且成不规则状态。
色纺纱色差的预防与控制

第48卷第3期2020年3月【52】Co社on Textile Technology色纺纱色差的预防与控制龙永生(汶上如意技术纺织有限公司,山东济宁,272500)摘要:探讨色纺纱色差产生的原因和预控措施。
分析了纱线色差的产生原因,结合实际生产实践,从原料领料、合料到生产流程各工序,针对性地采取色差控制措施。
认为:熟记各工序控制色差的产生原因及其控制措施,在各工序展示半制品色差异常实物图,加强对员工质量意识、操作水平培训提升,做好色纺纱色差预控工作,完善色纺纱色差质量管控体系,可以稳定提高色纺纱产品质量。
关键词:色纺纱;色差;横档;花式纱;质量管控体系;条混工艺;成本中图分类号:TS101.9文献标志码:B文章编号:1000-7415(2020)03-0052-03Color Difference Prevention and Control of Colored Spun YarnLONG Yongsheng(Wenshang Ruyi Technology Textile Co.,Ltd.,Shandong Jining,272500)Abstract Color difference causes and pre-control measures of colored spun yam color difference were discussed.Causes of yam color difference were analyzed.According to actual production practice,from raw material picking,compounding material to production processes,targeted color difference control measures were taken.lt is considered that causes and control measures of color difference in each process should be memorized in heart.A bnormal physical color difference pictures of semi-finished products in each process are displayed.Training of employees7 quality awareness and operation level are strengthed.Pre-control work of colored spun yam color difference should be done well.Colored spun yam color difference quality control system is consummated.Quality of color spun products can be stably improved.Key Words Colored Spun Yam,Color Differrence,Cross Bar,Fancy Yam,Quality Control System,Sliver Blending Process,Cost在国家环保政策宣导下,色纺纱在纺织行业中逐步成为一道美丽的风景。
【纺织技术】纱线原因横档、黄白纱的解决办法

【纺织技术】纱线原因横档、黄白纱的解决办法1、原料原因由于纱线的原因造成布面横档疵点,大约70%左右比例是由原料问题造成的。
关于原料注意控制以下几点:(1) 保持适量的原料库存,能够顺利完成原料的接批过渡工作,是解决色差问题的基础。
一般长绒棉品种两个月以上的库存、细绒棉品种40天以上的库存是必要的。
当原棉库存在一个月以下,并且货源不稳定的情况下,容易出现色差问题。
(2) 严格按照配棉原则来执行配棉工艺,突出配棉主体的概念,接批过渡保持颜色和内在质量指标的稳定。
(3) 坚持做好棉花逐包检验工作。
对正常使用中的棉花进行逐包检验工作,发现个别颜色差异大、异纤含量多等质量问题的棉包,要合理使用。
(4) 严格执行配棉工艺,按照排包图排好棉包,力求纤维的混合均匀,重点做好清梳工序的纤维混合效果。
(5) 配棉排包时不要将同样马克隆值的棉包放在一起。
(6) 每次配棉变动后的平均马克隆值的变化数值争取控制在±0.1以内;一次配棉中的马克隆值CV值小于10%。
(7) MIC值正常但成熟度指数不正常的棉包要慎重使用。
(8) 回花均衡使用,棉台摆放符合要求。
(9) 原料中的异性纤维也会造成布面色差,要做好控制。
2、运转操作管理(1) 纺纱各工序认真落实好半成品“先纺先用”的原则。
(2) 禁止半成品、成品带进附房,存放一段时间后回用。
(3) 关注细纱的生产状态,出现煤灰纱现象时,空调停止使用外风或及早落纱。
(4) 控制油污纱的产生。
3、设备管理减小细纱锭间的捻度差异。
纱线的捻度不匀过大,也会造成色差。
(1) 细纱锭子使用规格要一致。
(2) 细纱锭带规格、张力一致。
(3) 锭带轮运转灵活。
4、纱线的毛羽不匀率大,也会造成横档疵点(1) 同一品种钢领型号、使用周期尽量一致。
(2) 选择好适宜的钢丝圈型号、重量,控制好气圈形态,避免小纱毛羽过重的问题。
(3) 消灭过大的歪气圈、歪锭子,做好锭子、钢领、导纱钩的对中基础工作。
色纺纱色差产生的原因及防治措施

色纺纱色差产生的原因及防治措施毛保文(仪征金鹰纺织有限公司)色纺纱容易产生色差,是色纺企业需要重点控制的质量问题之一。
因此必须对各工序产生色差的原因进行细致分析,并采取相应的技术措施来进行控制。
1 混棉工序(1)原料染色不匀、缸差太大,混和时没有进行预处理而产生色差,可采取预混处理来消除或预防。
(2)染色原料前后批的颜色差异较大而产生色差,可重新调节有色部分比例,无法调整的可采用分批处理的办法来防治。
(3)称重问题引起的色差,可采取规范操作、认真核对“混料比例通知单和要求”并复重的办法来防治。
(4)原料回潮问题引起的色差。
回潮率大小不一致的原料,没有按照公定重量折算,新染原料回潮率通常都很大,此时还是按照实际重量称重,有色部分的成份的实际比例降低,纱线颜色变浅;有色原料放置时间较长,因放湿回潮率降低,按照实际重量称重有色部分的实际比例增加,纱线颜色变深。
这种色差应严格按照公定重量折算各成份的标准重量来防治。
(5)排盘不匀产生的色差。
在清花排盘时,如果没有将各种成份的原料按对称点或规定要求放置,也容易造成色差。
防治措施:如果配棉中的原料成份较多,排盘时每种原料要取二个对称点;如果配棉中的原料成份较少,排盘时每种原料要取三个及以上的对称点。
(6)纺浅色纱线时,有色原料含量较少,排盘时如果有色原料放置不够均匀,也容易出现色差问题。
防治措施:将有色部分的原料填在其他原料的狭缝中;或采取先预混再排盘的方法。
(7)对排盘后没有做好削高嵌缝、低包松高等工作,也容易产生色差。
可采取规范排盘工作,排盘后由质量主管或当班班长复检合格在开车的措施来防治。
(8)因异纤混入而产生的色差,可采取严格和规范原料和半制品定位和标识管理的办法来防治。
(9)回花管理不当也会产生色差,应加强回花管理工作,如打包过称、标明成分和重量、分类排放等。
2 清花工序(1)排盘错误产生的色差。
如排盘时整盘排错;或有几包排错。
可采取规范制度和操作,要求排盘工必须认真看清标识牌,校对标识牌内容,排盘后由主管或当班班长检查合格才能开车的办法来防治。
色差产生的原因及克服办法
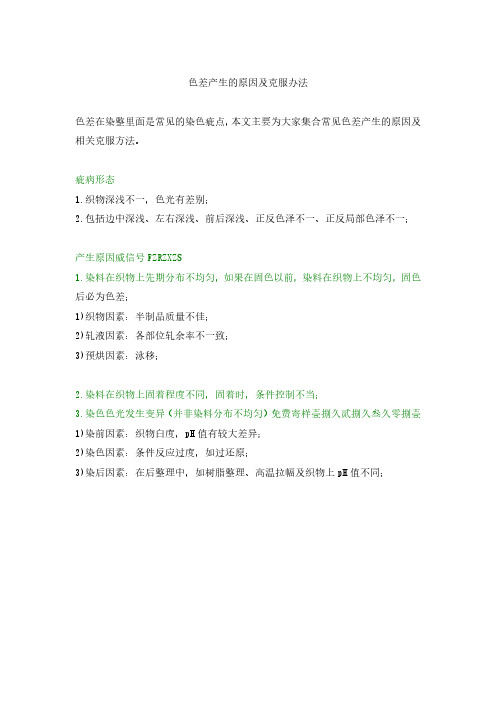
色差产生的原因及克服办法
色差在染整里面是常见的染色疵点,本文主要为大家集合常见色差产生的原因及相关克服方法。
疵病形态
1.织物深浅不一,色光有差别;
2.包括边中深浅、左右深浅、前后深浅、正反色泽不一、正反局部色泽不一;
产生原因威信号FZRZXZS
1.染料在织物上先期分布不均匀,如果在固色以前,染料在织物上不均匀,固色后必为色差;
1)织物因素:半制品质量不佳;
2)轧液因素:各部位轧余率不一致;
3)预烘因素:泳移;
2.染料在织物上固着程度不同,固着时,条件控制不当;
3.染色色光发生变异(并非染料分布不均匀)免费寄样壹捌久贰捌久叁久零捌壹
1)染前因素:织物白度,pH值有较大差异;
2)染色因素:条件反应过度,如过还原;
3)染后因素:在后整理中,如树脂整理、高温拉幅及织物上pH值不同;。
面料色差成因及预防措施办法

面料色差成因及预防措施办法所谓色差是指两种颜色的差异,即色调、饱和度和亮度三种综合因素之间的差异。
从广义上讲,任何两种颜色之间的差异就称之为色差。
在纺织品加工过程中,由于纺纱织造以及印染加工工艺的实施与质量控制不当,纺织品的不同部位或者各匹之间会存在色泽差异。
常见面料色差分类染色制品所得色泽深浅不一,色光有差别。
1. 同批色差:同批产品中,一个色号的产品箱与箱之间、件与件之间、包与包之间、匹与匹之间、缸与缸之间有色差。
2. 同匹色差:同匹产品中的左、中、右色差(包括深浅边)最常见到的色差,按照色差排料可稍微调整色差的效果,但不能彻底根除色差;一卷面料前后色差,排料一般经向在2米内调整;正反面色差;3. 不合色样:包括样本与产品的色差, 成交小样与产品的色差。
色差是染整厂常见疵病和多发性疵病之一,严重影响染色成品的质量。
面料色差原因各类织物的纤维组成不同,染色时采用的染料种类及工艺设备不同、加上染色加工中有不同的要求和特点,产生疵病的原因及表现就不一样。
色差在外观表现上多种多样,但究其原因,主要有以下几种。
- 1 -染料在织物上先期分布不均匀染料在固着之前,如果在织物各部位上分布不匀,固色后必然形成色差。
造成这种现象的主要原因为:•织物因素:由于纤维性能不同或前处理退、煮、漂、丝不够匀透,使染前半制品渗透性不匀而引起对染料吸收程度的差异。
•吸液因素:由于机械结构上的原因或操作不当,使织物各部位的带液率不一致,因而造成色差。
轧辊压力不匀、加入染化料不匀等都会使织物吸收染料不匀。
•预烘因素:在浸轧染液后预烘时,由于烘燥的速率和程度不一致,引起染料发生不同程度的泳移,使染料在织物上分布不匀。
- 2 -染料在织物上固着程度不同尽管染料在织物上先期分布是均匀的,但在固着过程中,如果条件控制不当(如温度、时间、染化料浓度等),使织物上某些部位的染料没有得到充分固色,在后处理皂洗时即被去除,从而产生色差。
- 3 -染料色光发生变异这种差异不是由于织物上染料分布不均匀造成的,而是由于某些原因引起织物上的部分染料的色光发生变化,一般有以下几种原因:•染前因素:半制品的白度不匀或pH值有较大差异,在染色后往往造成色光差异。
预防与控制色纺纱色差的措施
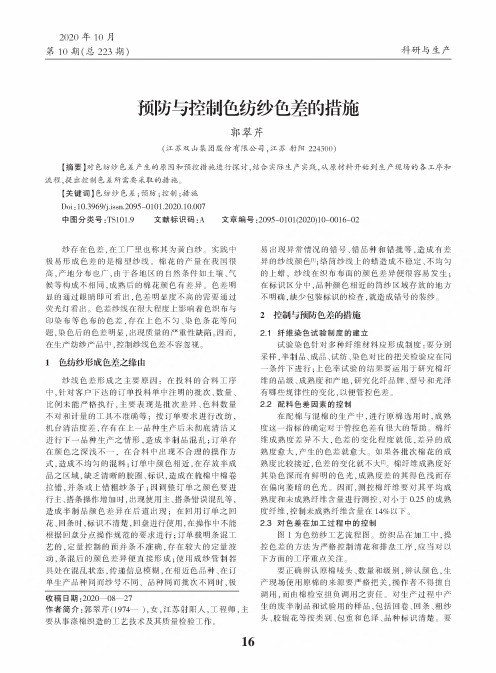
2020年10月第10期(总223期)科研与生产预防与控制色纺纱色差的措施郭翠芹(江苏双山集团股份有限公司,江苏射阳224300)【摘要】对色纺纱色差产生的原因和预控措施进行探讨,结合实际生产实践,从原材料开始到生产现场的各工序和流程,提出控制色差所需要采取的措施。
【关键词】色纺纱色差;预防;控制%措施Doi:10.3969/j.issn.2095-0101.2020.10.007中图分类号:TS101.9文献标识码:A文章编号:2095-0101(2020)10-0016-02纱存在色差,在工厂里也称其为黄白纱。
实践中极易形成色差的是棉型纱线。
棉花的产量在我国很高,产地分布也广,由于各地区的自然条件如土壤、气候等构成不相同,成熟后的棉花颜色有差异。
色差明显的通过眼睛即可看岀,色差明显度不高的需要通过荧光灯看岀。
色差纱线在很大程度上影响着色织布与印染布等色布的色差,存在上色不匀、染色条花等问题,染色后的色差明显,岀现质量的。
,在产纱产中,纱线色差。
1色纺纱形成色差之缘由纱线色差形成主要原:在投料的合料工序中,对的投料中明的、量、,主要现是差异、色料量不对量的工等;要,度差,存有在上后形,成;存在颜色,在合料中岀现合的,成匀的料;中颜色相,在存成区,的、,成在棉中棉,条上纱条;颜色要主、条,岀现主、条等,成颜色差异在后岀现;在花、条,,,在中分的要;明条混工的,定量的条,存在大的量,条后的颜色差异形成;成纱在,信息模糊,在相色、在产品种同而纱号同、同而批次不同,极收稿日期:2020—08—27作者简介:(1974—),,,工程师,主要从事涤棉织的工其质量检验工。
易岀现异常况的号、等,成有差异的纱线颜色叫络筒纱线上的蜡造成不稳、匀的上蜡,纱线在织布布面的颜色差异很易发;在区分中,颜色相的筒纱区存的地不明,少包装的检查,就成错号的装纱。
2控制与预防色差的措施2.1纤维染色试验制度的建立试验染色对多纤维材料应形成度:要分别采样,半、成、试纺、染色对的把关检验应在同一条件;上色率试验的结果要运于研究棉纤维的级、成熟度产地,研究化纤品牌、型号光泽有哪些规律性的变化,以色差。
防止涤丙纱色差的措施

我 厂 原 料 来 自辽 阳 、 连 、 大 山东 、 海 等 地 , 从 韩 上 也
国进 口。各 产 地原 料 色泽 差异 很 大 , 内在 质 量 不 一 , 供
本 上避 免 了色差 纱 的产 生 。本 文 作如 下 探讨 。
给 量 不稳 定 , 接 批 频 繁 , 产 波 动 大 , 纱 易 产 生 色 使 生 成
外, 清花 工 序放 包 不平 , 棉 设 备 作 用 不 良 , 混 回花 质 量 及 回花 回用 不 当 , 也是 造 成 成 差 的几 个 主 要 因 素 , 取 了相 应 的 措 施 , 根 采 从
3 1 调 整涤 丙 比例 的接 批 方 法 .
接 批方 法 , 原 料 能 正 常 配 用 , 纱 白度 保 持 稳 定 。 使 成
3 1 1 对 比 接批 小样 , 颜 色 没 有 差 异 , 直 接 接 用 , .. 若 可
混 比不 变 。
2 2 调 入 储 棉 室 中 的原 料 , 进 行 逐 包 检 验 。 在 同 一 . 先
纺性一般。
要求 纱 线 的 自度 及 自度 稳 定 性 保 持 长 期 不 变 。在 实 际
生 产 中 , 厂 所 进 的 原 料 产 地 多 , 维 形 态 及 其 物 理 性 我 纤 能 存 在很 大差 异 , 给原 料 配 用 带 来 很 大 的 困难 。特 别 这 是 原 料 色 泽 差 异 , 果 接 批 不 当 , 纱 会 产 生 色 差 。此 如 成
一
油率 偏 低 。配 棉 时 小 量 配 用 , 需 补 喷 油 剂 。 在 喷 油 并
处 理 时 , 调 整 好 油 剂 和水 的 比例 , 油 处 理 后 的 原 料 应 喷 需 放 置 1 2h后 使 用 , 以使 油 剂 和 水 分 充 分 渗 透 , 于 便 在 生 产 中能 被 正 常 抓 取 、 送 混 合 。 输
- 1、下载文档前请自行甄别文档内容的完整性,平台不提供额外的编辑、内容补充、找答案等附加服务。
- 2、"仅部分预览"的文档,不可在线预览部分如存在完整性等问题,可反馈申请退款(可完整预览的文档不适用该条件!)。
- 3、如文档侵犯您的权益,请联系客服反馈,我们会尽快为您处理(人工客服工作时间:9:00-18:30)。
捻度松紧、 纱线粗细、 上蜡差异等造成的假性黄白纱。 2 . 1 . 2 建立纤维染色试验制度 对各种纤维原料建立染色试验; 对快速试纺与日 常生产的半制品、 成品分别采样, 在同一条件下做染色 对比把关检验; 对棉纤维的生产地区、 品级、 成熟度以 及化学纤维的牌号、 型号、 光泽做上色率试验, 研究其 变化规律, 以控制色差。 2 . 1 . 3 控制配料色差因素 配料工作应贯彻“ 分类排队, 逐步接替, 多包混合, 交叉抵补” 的原则。使用黄棉、 低级棉、 回料、 再用料以 及国外棉等, 由于差异过大, 混合困难, 应控制接替比 例。对化学纤维应控制产地、 牌号、 型号、 有光、 半光、 无光、 有色、 增白等因素, 在使用时要因地制宜, 多啧多 包, 合理接批。 在混配棉选用原棉时, 把成熟度作为控制原棉染 色质量的指标, 将有助于对染色品色差的控制。色差 的程度随棉纤维成熟情况而变化, 成熟度差异越大的 纤维, 其色差越大, 而成熟度接近的棉花, 其色差较小。 成熟度好的棉纤维得色深, 且色光鲜明, 而成熟度差的 不仅得色浅, 且色光偏向萎暗。因此, 棉纺厂不仅要测 试和控制棉纤维的平均成熟度, 而且还要测试和控制 未成熟纤维含量, 对纤维细胞充实度小于0 . 2 5 ( 成熟
回角的不同而产生差异。
表 1 对黄白纱的捻度测试数据
纱色泽
( 6 ) 配棉时要保持原棉色泽上有主体, 使一种原棉 占7 0 %以 上, 并且要有一定量库存以保持相对稳定。 ( 7 ) 配棉要突出性能主峰, 比如纤维长度为 2 5 m m 的原棉占7 0 %以上, 则长度为性能主峰。 ( 8 ) 配棉要满足相似原则, 就是某批原棉色泽和主 体色泽差距大时, 它的各项物理性能指标必须和主峰 性能相似; 反之, 如果原棉性能指标和主峰性能差距大
S H A N G H A I T E X T I L E S C I E N C E&T E C H N O L O G Y 上海纺织科技
专题 论 坛
度系数 0 . 5 ) 的这部分未成熟纤维含量应控制在 1 4% 以内。根据纺织产品最终用途的需要而选用原棉时, 一般漂白坯可用成熟度低一档的原棉, 而染色坯需要 用成熟度较好的原棉。科学地使用低级棉, 可以在保 证质量的前提下, 有效地降低成本。但是低级棉有特 殊的物理性能, 使用过程中极易产生色差质量事故, 因 而须加强防范。 国产棉的颜色差异通常比 进口 棉大些, 如澳棉、 印 度棉色差较小; 细绒棉比长绒棉色差大些; 国内新疆棉 的色差小于其他地区的棉花。选择色差较小的原棉进 行配棉, 从源头上对色差进行控制, 是预防色差的有效
C r e a t i o n a n d p r e v e n t i o n o f c o l o u r d i f f e r e n c e o n y a n r F A N G Y i n g 一 i e , WA N G A i - p i n g
Байду номын сангаас
2 色差的控制和预防
2 . 1 对原棉颜色差异的分析与控制
收稿日期: 2 0 0 5 - 1 1 - 1 0 作者简介: 房英杰( 1 9 6 8 - ) , 男, 生产技术经理, 从事纺织企业管理和新
产品开发工作。
第 2期 2 0 0 6 年2 月・ 第3 4卷 ・
V o l . 3 4 N o . 2 , 2 0 0 6
上海纺织科技
S H ANGH AI T E T I X L E S C I E NC E &T E C H NOL OGY
2 0 0 6年2月 ・ 第3 4卷 ・ 第2期
V o l . 3 4 N o . 2 . 2 0 0 6
专题 论 坛
纱线色差的产生和预防
房英杰, 王爱萍
( 山东泰丰纺织集团, 山东 莱芜 2 7 1 1 0 0 )
1 色差产生的原因
1 . 1 本色色差产生的原因
配棉工艺不合理; 清棉工序混棉不均匀; 各工序没 有保证先纺先用; 锭速级差引起的长片段和条干引起
的短片段的捻度差异。 1 . 2 染色色差产生的原因 由于产品中掺有异性纤维或原棉成熟度差异过 大, 致使纤维着色能力不同而产生染色色差。
摘 要: 系统分析了纱线色差的产生原因、 预防措施以及对产品质量的影响。分别阐述了原棉的选配、 混合效果、 纱线捻度等 的因素对色纺纱线和彩棉纱线色差影响和预防措施。
关键词: 纱线; 纱疵; 配棉; 纺纱
中图分类号: T S 1 0 4 . 2 文献标识码 : B 文章编号: 1 0 0 1 - 2 0 4 4 ( 2 0 0 6 ) 0 2 - 0 0 3 0 - 0 3
际情况。
时, 原棉的色泽就必须和主体色泽相似。 ( 9 ) 稳定地转变配棉主体, 科学地调度配棉主峰。 根据库存情况, 配棉主体色泽常常要由一种色泽向另 一种色泽转变, 这种转变必须稳定地、 逐步地变化调 整, 每批调整幅度不可大于 5%。性能主峰过渡幅度 偏小掌握, 一般在0 . 5%以下, 调整周期可根据细纱车 间生产能力确定。 ( 1 0 ) 认真分析原棉成熟度, 不同时使用成熟度差 异大的原棉, 并且优化纺纱工艺以排除未成熟纤维。 ( 1 1 ) 加强清棉工序操作管理, 认真做好排包、 平 包、 清包工作, 使棉包放置和排包方案严格一致, 适度 掀包松包, 使棉包松紧程度一致。 ( 1 2 ) 棉纱存放太久或受到污染也会造成色差, 因 此棉纱库应通风、 防潮, 已人库棉纱应及时出售或织布 用, 避免存放太久。 2 . 3 减少因捻度级差造成的色差 2 . 3 . 1 捻度级差造成色差的实例分析 减少锭速级差引起的长片段和条干不匀引起的短 片段捻度差异。消除细纱接头和胶辊回转失常造成的 紧捻纱; 消除捻线罗拉部分回转失常或纱线通道不符 操作要求造成的紧捻纱。 某棉纺织厂生产 2 7 . 8 t e x 的纱供出口灯芯绒坯布 纬纱用, 用户反映, 主要是布面出现黄白色差, 其长短 不一, 长的有十几厘米, 短的几毫米, 严重的色差造成 坯布降等, 影响出口率。一开始, 只在原棉试验, 原棉 混配、 原棉上车管理以及前后道对 口供应等方面找原 因下措施, 但没有效果或效果不明显。从灯芯绒黄白 疵布上拆下同 样长度的黄白纱, 分别进行称重, 做捻度 试验, 发现同样长度的黄白纱称重差异很小, 但捻度差 异很大, 正常的呈黄色的纱捻度一般在 6 4捻/ 1 0 c m左 右, 呈次白 色的纱捻度要比黄色的的减少 5%左右, 而 呈白 色的纱捻度要比黄色的减少 1 2 . 5%左右。具体 测试数据见表 1 , 经分析这是 由于纱线的色泽与纤维 对光线的反射有关 , 而纤维对光线的反射又因纱线捻
措施。
2 . 2 加工过程中对色差的控制 在加工过程中, 应认真执行操作法, 尤其在清花工 序, 要严格按配棉工艺图排盘, 切实做好以下几点。 ( 1 ) 正确识别原棉唆头、 级别、 颜色、 数量, 不得私 自 乱用乱调棉花, 如遇特殊情况应由棉检室负责调配。 ( 2 ) 正确使用落物。包括数量、 颜色、 类别, 回花间 严格把关回花质量, 分清类别 、 色泽, 标明包重及品种。 ( 3 ) 加强排盘工责任心, 避免用错棉花, 遇到标识 不清的, 不能随便乱用。排盘后认真检查, 排盘工在开 包时, 应及时把关色差包 , 各种回花落物的颜色也应注 意把关。看盘工认真把关削高填平是否合格, 底上成 分是否一致, 各种落物、 回花等使用是否合理 , 同时控 制抓棉机的运转效率, 保证抓棉混棉的均匀性。 ( 4 ) 极易产生色差的棉花是黄棉, 因此黄棉上包时 应加强把关力度, 避免黄白纱的产生。采用直线往复 式抓棉机黄棉应尽量分布在中间位置, 以利于混棉的 均匀性; 采用圆盘式抓棉机时, 应把黄棉放在内层, 以 利于抓棉机对黄棉的有效控制, 从而减少黄白纱的产 生, 防止出现大面积色差。前值车工开车前必须与标 准条子相对照, 发现色差及时查找原因立即整改, 梳棉 值车工把关棉卷色差; 并条值车工把关生条色差, 下工 序给上工序把关, 层层设防, 以杜绝色差的产生。 ( 5 ) 加强棉花检验, 低级棉取样一定要全面, 要确 实有代表性 , 各项指标试验要准确, 真实地反映原棉实
Ke y w o r d s ; y a m; y a r n f a u l t s ; c o t t o n i n s t r u c t i o n ; s p i n n i n g