超声振动辅助磨削技术的现状与新进展
超声辅助加工的研究与实践

超声辅助加工的研究与实践近年来,随着科技的不断进步和发展,超声辅助加工技术逐渐成为了新型高效加工生产技术的热点研究方向。
不仅如此,越来越多的实践证明,采用超声辅助加工技术可以大幅度提升加工效率,并且可实现对加工材料加强热和冷加工过程的控制,从而使材料的性能得以进一步优化。
超声辅助加工技术是一种创新性的加工技术。
其主要特点在于通过超声波的能量作用下,能够改变材料的物化性质,从而实现对材料进行更加精准的加工。
因此,超声辅助加工技术不仅适用于单纯的热加工,还适用于冷加工、疲劳、塑性和腐蚀等方面。
超声辅助加工技术的优势在于其加工效率高、效果好、材料损伤小,具有生产节约、资源节约等诸多优点。
这些特点意味着它在工业生产以及研究领域中都具有广泛的应用前景。
但是,超声辅助加工技术也存在一定的挑战和问题。
要想实现超声辅助加工技术的应用,关键是要深入研究超声波作用下材料的变化规律及机理。
另外,还需要针对不同的加工方案,进行适当的技术和应用上的优化,以来提高超声辅助加工技术的效率和可操作性。
目前,相关研究和开发工作正在逐步推进中。
超声辅助加工技术的具体应用包括了很多领域。
在航空领域,超声辅助加工技术被用于翼板、螺旋桨的制造中。
利用这种技术,不仅保证了加工精度和质量,而且还有效地提高了生产效率。
另外,在电子行业中,超声辅助加工技术可以被用于半导体、电子元件包装等的生产中,也被广泛应用到了制备二维材料、金属材料表面的精细处理等方面。
尽管目前超声辅助加工技术应用的范围还不是很广泛,但是在未来的发展中,它必将在工业制造领域中发挥更为突出和重要的作用。
同时,相关的学者和研究人员也应该积极地进行技术和应用的创新,来为这项技术的发展和推广提供更为有力的支持。
超声波技术国内外技术现状和发展趋势
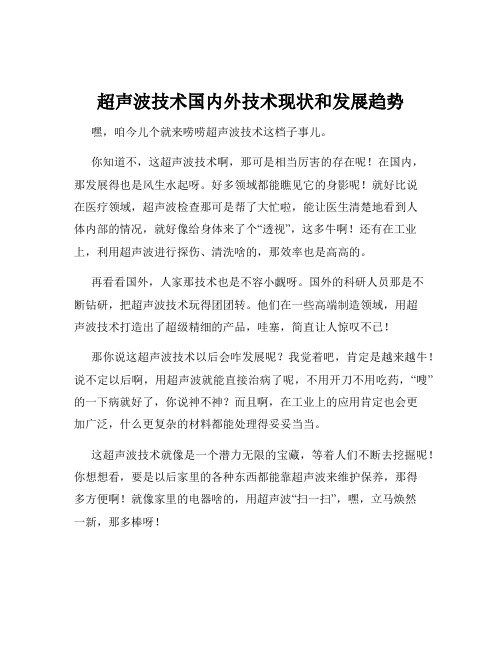
超声波技术国内外技术现状和发展趋势嘿,咱今儿个就来唠唠超声波技术这档子事儿。
你知道不,这超声波技术啊,那可是相当厉害的存在呢!在国内,那发展得也是风生水起呀。
好多领域都能瞧见它的身影呢!就好比说在医疗领域,超声波检查那可是帮了大忙啦,能让医生清楚地看到人体内部的情况,就好像给身体来了个“透视”,这多牛啊!还有在工业上,利用超声波进行探伤、清洗啥的,那效率也是高高的。
再看看国外,人家那技术也是不容小觑呀。
国外的科研人员那是不断钻研,把超声波技术玩得团团转。
他们在一些高端制造领域,用超声波技术打造出了超级精细的产品,哇塞,简直让人惊叹不已!那你说这超声波技术以后会咋发展呢?我觉着吧,肯定是越来越牛!说不定以后啊,用超声波就能直接治病了呢,不用开刀不用吃药,“嗖”的一下病就好了,你说神不神?而且啊,在工业上的应用肯定也会更加广泛,什么更复杂的材料都能处理得妥妥当当。
这超声波技术就像是一个潜力无限的宝藏,等着人们不断去挖掘呢!你想想看,要是以后家里的各种东西都能靠超声波来维护保养,那得多方便啊!就像家里的电器啥的,用超声波“扫一扫”,嘿,立马焕然一新,那多棒呀!还有啊,随着科技的不断进步,超声波技术和其他技术的结合肯定也会越来越多。
比如说和人工智能结合,那可就厉害了,能自动检测、自动处理,哇,那简直就是科幻电影里的场景呀!咱可不能小瞧了这超声波技术,它现在已经给我们的生活带来了很多便利,以后肯定还会有更多的惊喜等着我们呢!它就像一个无声的英雄,默默地在各个领域发挥着重要的作用。
咱得好好关注这超声波技术的发展呀,说不定哪天它就会给我们带来意想不到的大惊喜呢!你说是不是?咱可得跟上时代的步伐,别被这快速发展的科技给落下咯!。
超声加工技术的应用及发展趋势
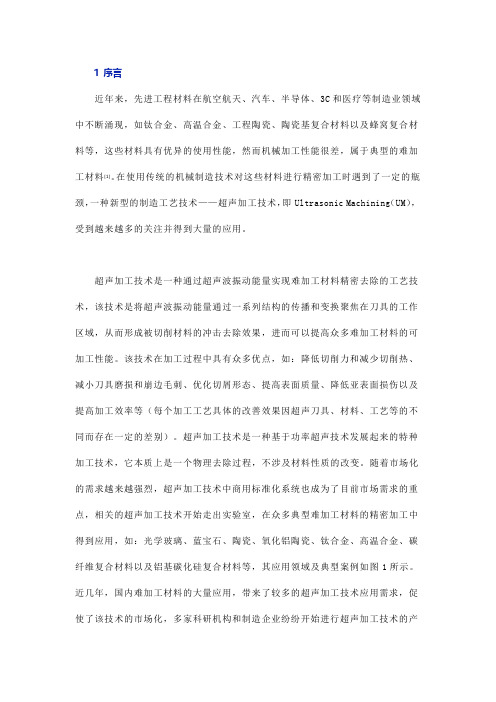
1 序言近年来,先进工程材料在航空航天、汽车、半导体、3C和医疗等制造业领域中不断涌现,如钛合金、高温合金、工程陶瓷、陶瓷基复合材料以及蜂窝复合材料等,这些材料具有优异的使用性能,然而机械加工性能很差,属于典型的难加工材料[1]。
在使用传统的机械制造技术对这些材料进行精密加工时遇到了一定的瓶颈,一种新型的制造工艺技术——超声加工技术,即Ultrasonic Machining(UM),受到越来越多的关注并得到大量的应用。
超声加工技术是一种通过超声波振动能量实现难加工材料精密去除的工艺技术,该技术是将超声波振动能量通过一系列结构的传播和变换聚焦在刀具的工作区域,从而形成被切削材料的冲击去除效果,进而可以提高众多难加工材料的可加工性能。
该技术在加工过程中具有众多优点,如:降低切削力和减少切削热、减小刀具磨损和崩边毛刺、优化切屑形态、提高表面质量、降低亚表面损伤以及提高加工效率等(每个加工工艺具体的改善效果因超声刀具、材料、工艺等的不同而存在一定的差别)。
超声加工技术是一种基于功率超声技术发展起来的特种加工技术,它本质上是一个物理去除过程,不涉及材料性质的改变。
随着市场化的需求越来越强烈,超声加工技术中商用标准化系统也成为了目前市场需求的重点,相关的超声加工技术开始走出实验室,在众多典型难加工材料的精密加工中得到应用,如:光学玻璃、蓝宝石、陶瓷、氧化铝陶瓷、钛合金、高温合金、碳纤维复合材料以及铝基碳化硅复合材料等,其应用领域及典型案例如图1所示。
近几年,国内难加工材料的大量应用,带来了较多的超声加工技术应用需求,促使了该技术的市场化,多家科研机构和制造企业纷纷开始进行超声加工技术的产业化应用。
图1超声加工应用领域及典型案例2 超声加工技术发展现状“工欲善其事,必先利其器”,超声加工技术是针对难加工材料精密加工的利器。
在大多数切削加工领域,超声加工更确切的名称应该为“超声辅助精密加工”,即在传统切削加工技术上辅助超声振动,从而实现特殊的材料去除效果。
超声辅助技术在果蔬加工中的应用与研究

超声辅助技术在果蔬加工中的应用与研究近年来,随着科技的不断进步,超声辅助技术逐渐在各个领域展示出巨大的潜力。
在食品加工行业中,特别是在果蔬加工领域,超声辅助技术也开始崭露头角。
通过超声波的作用,果蔬的加工过程极大地得到改善。
本文将探讨超声辅助技术在果蔬加工中的应用与研究。
首先,超声辅助技术在果蔬清洁过程中的应用已经得到广泛研究和应用。
传统的果蔬清洗方法往往存在一些问题,比如无法彻底去除表面的污垢和微生物,同时还会造成果蔬受损。
而超声波的微强声波震动作用可以产生空化效应,从而增强水对果蔬表面的力量,进一步清洁果蔬,并有效减少对果蔬的物理损伤。
研究表明,超声辅助清洗方法可以显著降低果蔬表面的菌落总数和污垢含量,提高果蔬的质量和安全性。
其次,超声辅助技术在果蔬干燥领域也有着广泛的应用。
传统的果蔬干燥方法往往需要较长时间,并且会导致营养物质的流失。
而超声波的作用可以加速果蔬中水分的蒸发,提高干燥速度,同时可以在一定程度上保留果蔬中的营养成分。
研究发现,利用超声辅助技术进行果蔬干燥可以显著降低果蔬的干燥时间,同时能够保持果蔬的色泽、味道和营养价值。
除了清洁和干燥,超声辅助技术在果蔬提取过程中也有着独特的应用。
很多果蔬中含有一些有益的活性成分,如维生素、多酚类物质等,这些成分对人体健康有着积极的作用。
然而,传统的提取方法往往存在一些问题,如提取效率低、操作繁琐等。
超声辅助技术利用声波的能量可以促进果蔬中活性成分的迁移和释放,提高提取效率。
研究发现,超声辅助提取方法可以提高果蔬中活性成分的提取率,并且对果蔬的物理和化学性质几乎没有影响。
此外,超声辅助技术还被应用于果蔬加工过程中的其他方面。
例如,超声波的振荡作用可以改变果蔬的细胞结构,提高果蔬的渗透性和可溶性,从而利于果蔬的腌制和浸泡。
超声辅助技术还可以用于果蔬中潜在的品质检测,如检测果蔬中的含水量、硬度等。
研究表明,超声辅助技术在果蔬加工领域的应用还有很大的发展潜力,可以进一步改善果蔬加工的过程和质量。
超声加工技术的应用现状及其发展趋势
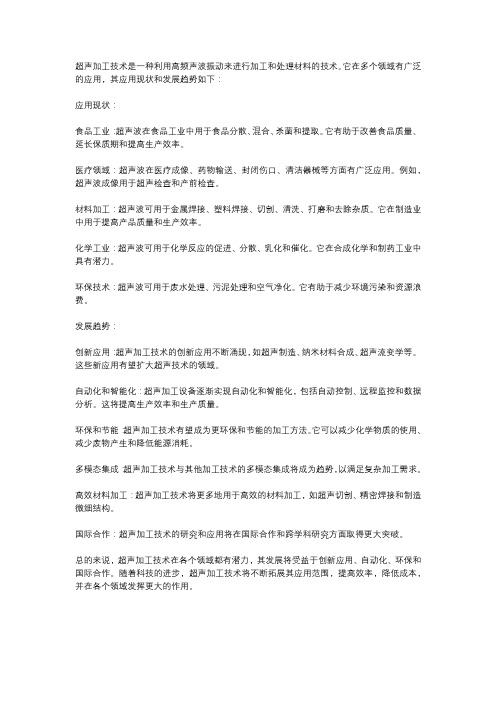
超声加工技术是一种利用高频声波振动来进行加工和处理材料的技术。
它在多个领域有广泛的应用,其应用现状和发展趋势如下:应用现状:食品工业:超声波在食品工业中用于食品分散、混合、杀菌和提取。
它有助于改善食品质量、延长保质期和提高生产效率。
医疗领域:超声波在医疗成像、药物输送、封闭伤口、清洁器械等方面有广泛应用。
例如,超声波成像用于超声检查和产前检查。
材料加工:超声波可用于金属焊接、塑料焊接、切割、清洗、打磨和去除杂质。
它在制造业中用于提高产品质量和生产效率。
化学工业:超声波可用于化学反应的促进、分散、乳化和催化。
它在合成化学和制药工业中具有潜力。
环保技术:超声波可用于废水处理、污泥处理和空气净化。
它有助于减少环境污染和资源浪费。
发展趋势:创新应用:超声加工技术的创新应用不断涌现,如超声制造、纳米材料合成、超声流变学等。
这些新应用有望扩大超声技术的领域。
自动化和智能化:超声加工设备逐渐实现自动化和智能化,包括自动控制、远程监控和数据分析。
这将提高生产效率和生产质量。
环保和节能:超声加工技术有望成为更环保和节能的加工方法。
它可以减少化学物质的使用、减少废物产生和降低能源消耗。
多模态集成:超声加工技术与其他加工技术的多模态集成将成为趋势,以满足复杂加工需求。
高效材料加工:超声加工技术将更多地用于高效的材料加工,如超声切割、精密焊接和制造微细结构。
国际合作:超声加工技术的研究和应用将在国际合作和跨学科研究方面取得更大突破。
总的来说,超声加工技术在各个领域都有潜力,其发展将受益于创新应用、自动化、环保和国际合作。
随着科技的进步,超声加工技术将不断拓展其应用范围,提高效率,降低成本,并在各个领域发挥更大的作用。
超声减摩发展现状
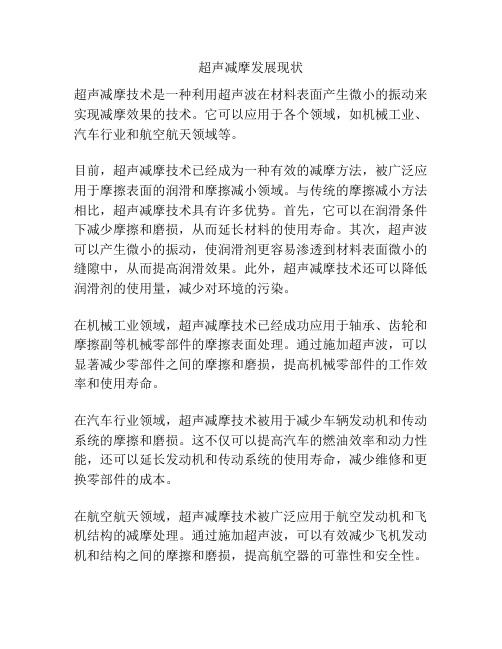
超声减摩发展现状
超声减摩技术是一种利用超声波在材料表面产生微小的振动来实现减摩效果的技术。
它可以应用于各个领域,如机械工业、汽车行业和航空航天领域等。
目前,超声减摩技术已经成为一种有效的减摩方法,被广泛应用于摩擦表面的润滑和摩擦减小领域。
与传统的摩擦减小方法相比,超声减摩技术具有许多优势。
首先,它可以在润滑条件下减少摩擦和磨损,从而延长材料的使用寿命。
其次,超声波可以产生微小的振动,使润滑剂更容易渗透到材料表面微小的缝隙中,从而提高润滑效果。
此外,超声减摩技术还可以降低润滑剂的使用量,减少对环境的污染。
在机械工业领域,超声减摩技术已经成功应用于轴承、齿轮和摩擦副等机械零部件的摩擦表面处理。
通过施加超声波,可以显著减少零部件之间的摩擦和磨损,提高机械零部件的工作效率和使用寿命。
在汽车行业领域,超声减摩技术被用于减少车辆发动机和传动系统的摩擦和磨损。
这不仅可以提高汽车的燃油效率和动力性能,还可以延长发动机和传动系统的使用寿命,减少维修和更换零部件的成本。
在航空航天领域,超声减摩技术被广泛应用于航空发动机和飞机结构的减摩处理。
通过施加超声波,可以有效减少飞机发动机和结构之间的摩擦和磨损,提高航空器的可靠性和安全性。
总之,在各个领域中,超声减摩技术都显示出极大的应用潜力。
随着科技的发展和研究的深入,相信超声减摩技术将会在未来得到更广泛的应用,并为相关领域带来更大的发展机遇。
超声加工技术的现状及发展趋势
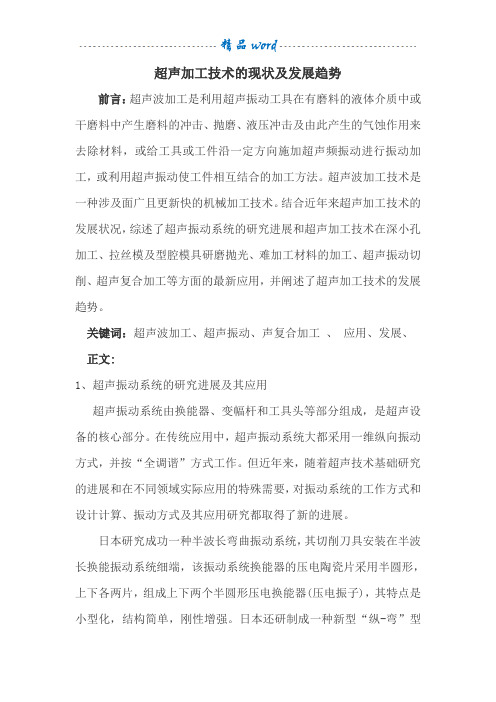
超声加工技术的现状及发展趋势前言:超声波加工是利用超声振动工具在有磨料的液体介质中或干磨料中产生磨料的冲击、抛磨、液压冲击及由此产生的气蚀作用来去除材料,或给工具或工件沿一定方向施加超声频振动进行振动加工,或利用超声振动使工件相互结合的加工方法。
超声波加工技术是一种涉及面广且更新快的机械加工技术。
结合近年来超声加工技术的发展状况,综述了超声振动系统的研究进展和超声加工技术在深小孔加工、拉丝模及型腔模具研磨抛光、难加工材料的加工、超声振动切削、超声复合加工等方面的最新应用,并阐述了超声加工技术的发展趋势。
关键词:超声波加工、超声振动、声复合加工、应用、发展、正文:1、超声振动系统的研究进展及其应用超声振动系统由换能器、变幅杆和工具头等部分组成,是超声设备的核心部分。
在传统应用中,超声振动系统大都采用一维纵向振动方式,并按“全调谐”方式工作。
但近年来,随着超声技术基础研究的进展和在不同领域实际应用的特殊需要,对振动系统的工作方式和设计计算、振动方式及其应用研究都取得了新的进展。
日本研究成功一种半波长弯曲振动系统,其切削刀具安装在半波长换能振动系统细端,该振动系统换能器的压电陶瓷片采用半圆形,上下各两片,组成上下两个半圆形压电换能器(压电振子),其特点是小型化,结构简单,刚性增强。
日本还研制成一种新型“纵-弯”型振动系统,并已在手持式超声复合振动研磨机上成功应用。
该系统压电换能器也采用半圆形压电陶瓷片产生“纵-弯”型复合振动。
日本金泽工业学院的研究人员研制了加工硬脆材料的超声低频振动组合钻孔系统。
将金刚石中心钻的超声振动与工件的低频振动相结合,制造了一台组合振动钻孔设备,该设备能检测钻孔力的变化以及钻孔精度和孔的表面质量,并用该组合设备在不同的振动条件下进行了一系列实验。
实验结果表明,将金刚石中心钻的超声振动与工件的低频振动相结合是加工硬脆材料的一种有效方法。
另一种超声扭转振动系统已在“加工中心”用超声扭转振动装置上应用。
超声加工及振动切削
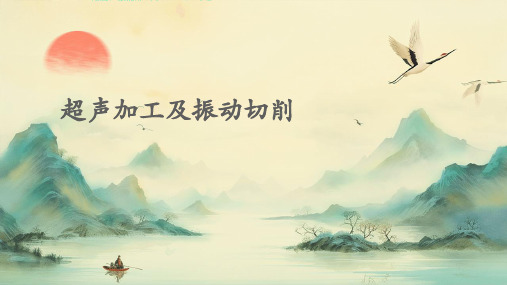
精密零件的加工
如微小型零件、复杂曲面 零件等需要高精度加工的 零件。
难加工环境的加工
如高温、高压、真空等极 端环境下的加工。
04
超声加工与振动切削的比较
工作原理的比较
超声加工
利用超声波的振动能量对工件进行加工,通过工具的快速振动,使工件表面材 料在工具的作用下产生局部高温、高压,使材料发生变形、破碎或去除。
应用领域的比较
超声加工
广泛应用于玻璃、陶瓷、石英等 硬脆材料的加工;在珠宝、钟表 制造等领域也有广泛应用。
振动切削
广泛应用于各种金属材料的加工 ,如汽车、航空、机械制造等领 域;在难加工材料的加工方面也 有一定应用。
05
超声加工与振动切削的发展趋势和未
来展望
超声加工的发展趋势和未来展望
高效化
随着工业生产对加工效率 的要求不断提高,超声加 工技术将不断优化,实现 更高效、更快速的生产。
振动切削的基本原理是利用振动系统产生的周期性弹性力,使刀具在切削过程中产生快速的 往复运动,从而实现对工件的加工。
振动切削过程中,刀具的振动频率和振幅对加工效果具有重要影响,需要根据不同的加工要 求进行合理选择。
振动切削的主要技术
超声振动切削
利用超声波的振动能量对工件进行加工,具有加工精度高、表面 质量好、适用于各种难加工材料等特点。
智能振动切削
结合人工智能和振动切削技术,实 现智能控制和自适应调整,提高加 工精度和效率。
多轴振动切削
研究多轴振动切削技术,实现复杂 形状和高精度零件的加工。
交叉学科的研究和应用前景
超声加工与振动切削的结合
01
研究超声加工与振动切削的结合技术,发挥各自的优势,提高
加工效率和精度。
超声辅助加工发展现状及未来趋势分析
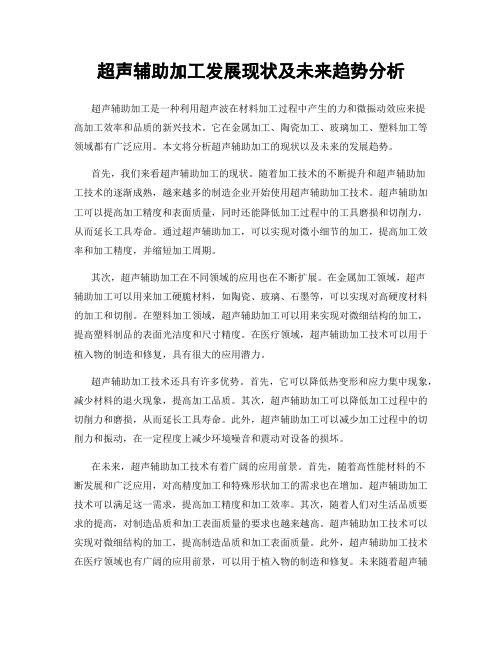
超声辅助加工发展现状及未来趋势分析超声辅助加工是一种利用超声波在材料加工过程中产生的力和微振动效应来提高加工效率和品质的新兴技术。
它在金属加工、陶瓷加工、玻璃加工、塑料加工等领域都有广泛应用。
本文将分析超声辅助加工的现状以及未来的发展趋势。
首先,我们来看超声辅助加工的现状。
随着加工技术的不断提升和超声辅助加工技术的逐渐成熟,越来越多的制造企业开始使用超声辅助加工技术。
超声辅助加工可以提高加工精度和表面质量,同时还能降低加工过程中的工具磨损和切削力,从而延长工具寿命。
通过超声辅助加工,可以实现对微小细节的加工,提高加工效率和加工精度,并缩短加工周期。
其次,超声辅助加工在不同领域的应用也在不断扩展。
在金属加工领域,超声辅助加工可以用来加工硬脆材料,如陶瓷、玻璃、石墨等,可以实现对高硬度材料的加工和切削。
在塑料加工领域,超声辅助加工可以用来实现对微细结构的加工,提高塑料制品的表面光洁度和尺寸精度。
在医疗领域,超声辅助加工技术可以用于植入物的制造和修复,具有很大的应用潜力。
超声辅助加工技术还具有许多优势。
首先,它可以降低热变形和应力集中现象,减少材料的退火现象,提高加工品质。
其次,超声辅助加工可以降低加工过程中的切削力和磨损,从而延长工具寿命。
此外,超声辅助加工可以减少加工过程中的切削力和振动,在一定程度上减少环境噪音和震动对设备的损坏。
在未来,超声辅助加工技术有着广阔的应用前景。
首先,随着高性能材料的不断发展和广泛应用,对高精度加工和特殊形状加工的需求也在增加。
超声辅助加工技术可以满足这一需求,提高加工精度和加工效率。
其次,随着人们对生活品质要求的提高,对制造品质和加工表面质量的要求也越来越高。
超声辅助加工技术可以实现对微细结构的加工,提高制造品质和加工表面质量。
此外,超声辅助加工技术在医疗领域也有广阔的应用前景,可以用于植入物的制造和修复。
未来随着超声辅助加工技术的不断发展和创新,它将能够适应各种复杂、高精度和高材料性能要求的加工需求。
超声振动磨削技术、

超声振动精密磨削技术的发展1、引言随着科学技术的进步,金属间化合物、工程陶瓷、石英、光学玻璃等硬脆材料以及各种增韧、增强的新型复合材料因其高硬度、耐磨损、耐高温、化学稳定性好、耐腐蚀等优点在航空航天、国防科技、生物工程、计算机工程等尖端领域中的应用日益广泛;但由于这些材料的脆硬特性,传统加工方法已不能满足对这些材料零件的精密加工要求,,因此有关其精密超精密磨削加工技术便成为世界各国研究的热点。
超声振动精密磨削技术便是顺应这一需要而发展起来的技术之一。
超声振动磨削技术的基本原理为:由超声波发生器产生的高频电振荡信号(一般为16~25KHz)经超声换能器转换成超声频机械振动,超声振动振幅由变幅杆放大后驱动工具砂轮产生相应频率的振动,使刀具与工件之间形成周期性的切削。
即工具砂轮在旋转磨削的同时做高频振动。
超声加工技术的经历了从传统超声波加工到旋转超声波加工的发展阶段,旋转式超声加工是在传统超声加工的工具上叠加了一个旋转运动。
这种加工用水带走被去除的材料并冷却工具,不需要传统超声加工中的磨料悬浮液,因此,这种方法被广泛的运用于超声振动磨削加工中[6]。
2、超声振动磨削技术发展回顾1927 年,R.W.Wood 和 A.L.Loomis 就发表了有关超声波加工的论文,超声加工首次提出。
1945 年L.Balamuth 就申请了关于超声加工的专利。
20 世纪 50~60 年代日本学者隈部淳一郎发表了许多对振动切削进行系统研究的论文,提出了振动切削理论,并成功实现了振动磨削等加工 [8] 。
1960 年左右,英国 Hawell 原子能研究中心的科学家发明了新的超声磨削复合加工方法。
超声振动磨削加工在难加工材料和高精度零件的加工方面显示了很大的优越性。
1986 年日本学者石川健一受超声电机椭圆振动特性启发,首次提出了“椭圆振动切削方法”(elliptical vibration cutting)。
20 世纪 90 年代初,日本神户大学社本英二等人对超声椭圆振动切削技术进行了深入研究,其最具代表性的研究成果是利用金刚石刀具采用双激励双弯曲合成椭圆振动的方式对黑色金属淬火不锈钢进行精密车削,最小表面粗糙度可以达到 Ra0.0106um,不但解决了金刚石不能加工黑色金属的难题,而且使这项技术达到了实用化阶段。
【原创】石英半球谐振子超精密加工技术现状及发展建议
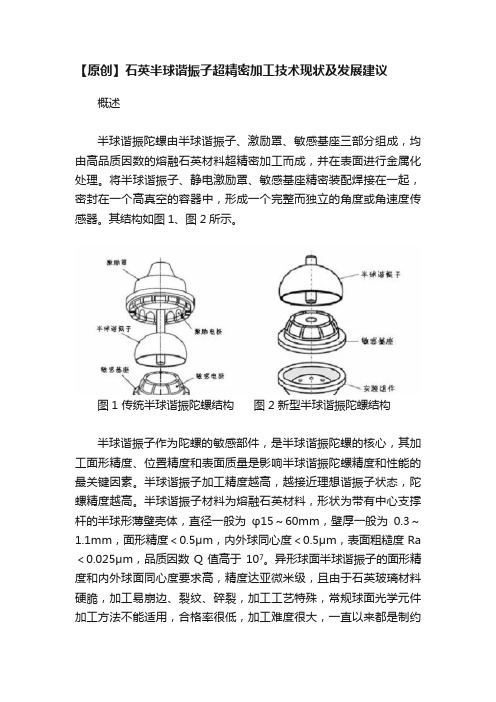
【原创】石英半球谐振子超精密加工技术现状及发展建议概述半球谐振陀螺由半球谐振子、激励罩、敏感基座三部分组成,均由高品质因数的熔融石英材料超精密加工而成,并在表面进行金属化处理。
将半球谐振子、静电激励罩、敏感基座精密装配焊接在一起,密封在一个高真空的容器中,形成一个完整而独立的角度或角速度传感器。
其结构如图1、图2所示。
图1 传统半球谐振陀螺结构图2 新型半球谐振陀螺结构半球谐振子作为陀螺的敏感部件,是半球谐振陀螺的核心,其加工面形精度、位置精度和表面质量是影响半球谐振陀螺精度和性能的最关键因素。
半球谐振子加工精度越高,越接近理想谐振子状态,陀螺精度越高。
半球谐振子材料为熔融石英材料,形状为带有中心支撑杆的半球形薄壁壳体,直径一般为φ15~60mm,壁厚一般为0.3~1.1mm,面形精度<0.5μm,内外球同心度<0.5μm,表面粗糙度Ra <0.025μm,品质因数Q值高于107。
异形球面半球谐振子的面形精度和内外球面同心度要求高,精度达亚微米级,且由于石英玻璃材料硬脆,加工易崩边、裂纹、碎裂,加工工艺特殊,常规球面光学元件加工方法不能适用,合格率很低,加工难度很大,一直以来都是制约半球谐振陀螺发展的瓶颈。
图3为石英半球谐振子零件。
图3 石英半球谐振子(镀膜前后)2.国内外研究现状2.1国外现状国外从事半球谐振陀螺研究主要集中在美国、俄罗斯和法国。
美国是最早研制半球谐振陀螺的国家,经历了较长历程,技术成熟,并在空间和导弹等高精度制导系统中得到成功应用,代表着半球谐振陀螺的世界先进水平。
俄罗斯、法国、英国、日本等国家也先后投入力量开展研究,俄罗斯、法国已取得明显效果,其他国家基本处于探索阶段。
目前,半球谐振陀螺正朝着高精度、系统型号多样化、系统应用多样化、小体积与微型化、抗辐射等方向发展。
半球谐振陀螺发展历程参见图4。
图4 半球谐振陀螺发展历程半球谐振陀螺的基本理论由英国物理学家布莱恩于1890年提出。
钛铝合金制备技术现状及新进展

钛铝合金制备技术现状及新进展钛铝合金作为一种具有高强度、轻质和优良耐腐蚀性能的合金材料,在航空航天、汽车、机械制造等领域得到了广泛应用。
为了满足不同领域的应用需求,钛铝合金制备技术的发展一直受到人们的。
本文将概述钛铝合金制备技术的现状及新进展。
目前,钛铝合金的制备主要采用熔炼和铸造等方法。
熔炼法是将钛和铝按照一定比例混合,在高温下熔化,然后进行浇铸、冷却和加工处理。
铸造法则是通过铸造设备将熔融的钛铝合金倒入模具中,冷却后得到所需形状和尺寸的铸件。
这些方法在生产实践中得到了广泛应用,但也存在一些不足之处,如成分控制不够精确、生产周期长、成本高等。
近年来,钛铝合金制备技术取得了许多新的进展。
随着材料性能的提升,钛铝合金的强度、硬度、耐腐蚀性能等得到了显著改善。
制备工艺方面也得到了很大的改进。
例如,真空熔炼技术可以有效地降低杂质含量,提高合金纯度;喷射沉积技术则可以实现快速凝固,提高生产效率。
一些新的生产设备和方法,如3D打印技术、离子注入技术等也在钛铝合金制备中得到了应用,进一步提高了生产效率和降低了成本。
随着钛铝合金制备技术的不断发展,其应用前景也越来越广阔。
在航空航天领域,钛铝合金可用于制造飞机和火箭等高速飞行器的结构件和发动机部件;在汽车领域,钛铝合金可用于制造轻量化、高强度的汽车零部件,提高汽车燃油效率和安全性;在机械制造领域,钛铝合金可用于制造高精度、高稳定性的机械设备和工具。
钛铝合金制备技术的发展对于提高合金材料性能、降低生产成本、推动相关领域的技术进步具有重要意义。
未来随着科学技术不断创新,钛铝合金制备技术有望在材料性能、制备工艺和生产效率等方面取得更多突破,为各领域的发展提供更强大的支撑。
粉末冶金是一种制备材料和零件的先进技术,具有近净成形、高密度、高性能等优点。
钛铝合金作为一种具有优异性能的新型材料,具有广阔的应用前景。
本文将综述粉末冶金制备钛铝合金技术的现状和展望。
在粉末冶金制备钛铝合金技术方面,相关文献和资料表明,目前主要有以下几种制备方法:机械合金化法:通过强力的机械搅拌将钛和铝粉末混合,然后进行热压烧结或热等静压处理得到钛铝合金。
超声振动辅助车削SiCp

表面技术第53卷第6期超声振动辅助车削SiCp/Al切屑形成机理及表面粗糙度研究林洁琼1,于行1,周岩1,谷岩1*,周晓勤2(1.长春工业大学 机电工程学院,长春 130000;2.吉林大学 机械与航空航天工程学院,长春 130000)摘要:目的研究切屑形成机理对加工过程的影响。
方法超声振动辅助车削技术通过刀具振动的拟间歇切削特征控制切屑尺寸和切屑形态,从而提高了加工表面质量。
针对SiCp/Al复合材料的切屑形成机理,探究常规车削和超声振动辅助车削的切屑形成过程。
研究了颗粒分布对第一变形区变形阶段的影响,以及不同加工方式下切削参数对切屑形态的影响。
最后,描述了切屑自由表面和刀-屑接触界面的颗粒损伤形式,以直观地描述常规车削与超声振动辅助车削SiCp/Al复合材料加工中切屑的形成过程。
结果通过测试加工后工件表面形貌发现超声振动辅助车削的切屑更加连续、切屑尺寸较小的加工表面粗糙度更小,常规车削的表面粗糙度为0.805 μm,超声振动辅助车削的表面粗糙度为0.404 μm,超声振动辅助车削比常规车削的表面粗糙度降低了49.8%。
结论与常规车削相比,超声振动辅助车削有利于减小切屑厚度。
超声振动辅助车削得到的切屑更加连续,避免了切屑碎裂,促进了切屑的顺利排出。
通过对切屑形态进行研究,选择最优切削参数可以有效提高工件表面质量。
关键词:超声振动辅助车削;SiCp/Al;切屑形成机理;颗粒损伤;表面完整性;粗糙度中图分类号:TG663 文献标志码:A 文章编号:1001-3660(2024)06-0144-13DOI:10.16490/ki.issn.1001-3660.2024.06.013Chip Formation Mechanism and Surface Roughness of SiCp/AlComposites by Ultrasonic Vibration-assisted TurningLIN Jieqiong1, YU Hang1, ZHOU Yan1, GU Yan1*, ZHOU Xiaoqin2(1. College of Electrical Mechanical Engineering, Changchun University of Technology, Changchun 130000, China;2. School of Mechanical and Aerospace Engineering, Jilin University, Changchun 130000, China)ABSTRACT: SiCp/Al is a metal matrix composite. It has excellent properties such as wear resistance, high temperature resistance, and fatigue resistance, and is widely used in fields such as aerospace, automobiles, electronics. The excellent physical and chemical properties of SiCp/Al composite materials have attracted widespread attention from the industry.With the application of SiCp/Al composite materials in these fields, there is an urgent demand for their precision收稿日期:2023-04-06;修订日期:2023-07-03Received:2023-04-06;Revised:2023-07-03基金项目:国家自然科学基金(U19A20104);吉林省高性能制造及检测国际科技合作重点实验室(20220502003GH)Fund:National Natural Science Foundation of China (U19A20104); Jilin Province Key Laboratory of International Science and Technology Cooperation for High Performance Manufacturing and Testing (20220502003GH)引文格式:林洁琼, 于行, 周岩, 等. 超声振动辅助车削SiCp/Al切屑形成机理及表面粗糙度研究[J]. 表面技术, 2024, 53(6): 144-156.LIN Jieqiong, YU Hang, ZHOU Yan, et al. Chip Formation Mechanism and Surface Roughness of SiCp/Al Composites by Ultrasonic Vibration- assisted Turning[J]. Surface Technology, 2024, 53(6): 144-156.*通信作者(Corresponding author)第53卷第6期林洁琼,等:超声振动辅助车削SiCp/Al切屑形成机理及表面粗糙度研究·145·machining technology, as well as research on machining methods and cutting mechanisms to improve surface quality.In the processing of SiCp/Al composite materials, the smooth discharge of chips and the prevention of chip fragmentation and adhesion on the processed surface can effectively improve the surface quality of the work piece. The effect of chip formation mechanism on the machining process was explored. Ultrasonic vibration assisted cutting technology improved the chip size and shape through the quasi-intermittent cutting characteristics of tool vibration, thereby improving the surface quality of machining. The chip morphology of SiCp/Al composite materials was analyzed through comparative experiments of conventional cutting and ultrasonic vibration assisted cutting. The particle distribution in the shear deformation zone stage and the effect of cutting parameters on chip morphology were studied.The chip morphology of conventional and ultrasonic vibration assisted cutting was compared from three aspects: feed rate, cutting depth and rotational speed. Due to the presence of SiC particles in SiCp/Al composite materials, the material began to deform along the boundaries of the particles, and the effective stress reached the material yield strength for the first time. During the deformation process, the increase of stress might cause particle movement and fracture. Therefore, during the cutting process, due to the continuous changes in the position of the particles cut by the tool, the angle of the boundary line at the beginning of deformation changed, leading to fluctuations in the shear angle within a certain range.And the chip segmentation degree Gs was introduced for quantitative comparison between conventional cutting and ultrasonic vibration assisted cutting experiments. It was found by comparison that the sawtooth degree of conventional cutting was 0.264-0.685, and the sawtooth degree of ultrasonic vibration assisted cutting was 0.085-0.364. The sawtooth shaped chips formed by ultrasonic vibration assisted cutting were not obvious, which avoided the fracture of the free surface of the chip at the crack. Finally, the particle damage forms of the chip free surface and the tool chip contact interface were described to visually describe the chip formation process in conventional cutting and ultrasonic vibration assisted cutting of SiCp/Al composites. Ultrasonic vibration assisted turning with more obvious elastic recovery was beneficial for reducing chip thickness.The chips obtained by ultrasonic vibration assisted cutting are more continuous, avoiding chip fragmentation and promoting the smooth discharge of chips. By observing the surface morphology of the work piece after processing, it is concluded that the smaller and more continuous the chip size, the smaller the surface roughness of the machined surface, while the surface roughness for conventional cutting is 0.805 μm. The surface roughness of ultrasonic vibration assisted turning is0.404 μm. Compared with traditional turning, ultrasonic vibration assisted turning can reduce surface roughness by 49.8%. Byobserving the morphology of chips and selecting the optimal cutting parameters, the surface quality of work piece processing can be effectively improved.KEY WORDS: ultrasonic vibration assisted turning; SiCp/Al; chip formation mechanism; particle damage; surface integrity;roughness近年来,以SiC、TiB等硬质颗粒为主增强的新型金属基复合材料因性能优异而在汽车等领域表现出良好的市场应用价值,然而SiC等增强颗粒的加入,导致加工过程变得困难,例如切削力急剧增大、刀具使用寿命减少以及表面质量下降等,切屑形成过程反映了SiCp/Al复合材料的加工过程,研究SiCp/Al 复合材料的切屑形成,有助于掌握SiCp/Al复合材料的加工状态,对优化SiCp/Al复合材料加工参数有重要意义[1-2]。
超声振动切削的发展现状

超声振动切削的发展现状作者:李征李辉殷振来源:《中小企业管理与科技·下旬刊》2011年第07期摘要:超声振动切削技术具有独特的切削原理和优越的工艺效果,广泛应用于难加工材料。
本文主要介绍了超声振动切削的原理、优点和应用,概述了超声振动切削的国内外发展现状。
关键词:超声振动切削发展现状0 引言随着科学技术的发展,各种难加工的新材料和复合材料在工业中的应用日益广泛,特别是光学玻璃、人工晶体、工程陶瓷等硬脆性材料也得到了极为广泛地应用。
由于材料的高硬度、高脆性和零件结构的复杂性给加工带来了极大的困难,从而限制了新材料和新结构应用范围的进一步扩展。
超声振动切削技术具有独特的切削原理和优越的工艺效果。
它可以明显地提高加工表面质量、加工精度和加工效率,特别是对工程陶瓷等硬脆难加工材料、有色金属的精密加工具有独特的优越性,因而引起了国内外学者的广泛重视。
1 超声振动切削技术超声振动切削是一种脉冲切削。
振动切削过程中,由于刀具有规律的振动,刀具和工件产生周期性的接触与分离,使刀具在振动的一个周期中的极短时间内完成了切削,从而形成了脉冲切削的方式。
超声振动切削的脉冲切削力的平均值要远小于普通切削,一般可减小到普通切削的1/3~1/10。
振动切削中,刀具在振动源驱动下周期性接触、离开工件,切削液可充分进入切削区,切削液使用效果得到提高,刀具的耐用度也得到了提高。
同时,切屑容易顺利排出,加工表面的耐磨性和耐腐蚀性得到提高。
2 国内外研究现状振动切削是一种新型的非传统的特种切削加工方法,它是给刀具(或工件)以适当的方向、一定的频率和振幅的振动,以改善其切削功效的脉冲切削方法。
与普通切削相比,振动切削具有切削力小、切削热降低、工件表面质量高、切屑处理容易、刀具耐用度提高、加工稳定、生产效率高等优点。
我国超声加工技术的研究始于50年代末,60年代初,哈尔滨工业大学应用超声车削,加工了一批飞机上的铝制细长轴,取得了良好的切削效果。
超声技术在材料加工中的新进展
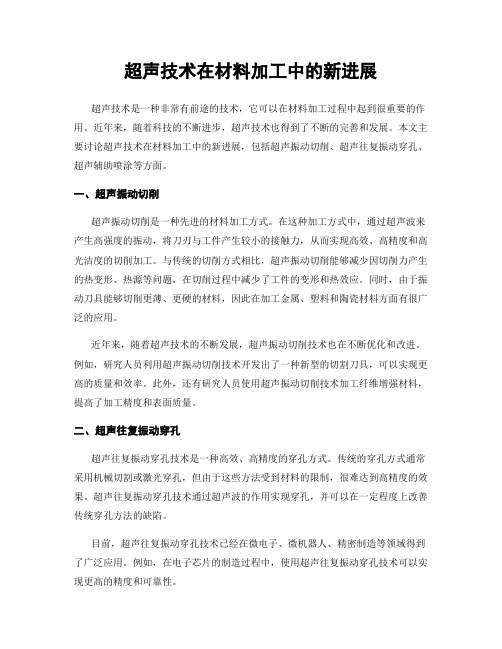
超声技术在材料加工中的新进展超声技术是一种非常有前途的技术,它可以在材料加工过程中起到很重要的作用。
近年来,随着科技的不断进步,超声技术也得到了不断的完善和发展。
本文主要讨论超声技术在材料加工中的新进展,包括超声振动切削、超声往复振动穿孔、超声辅助喷涂等方面。
一、超声振动切削超声振动切削是一种先进的材料加工方式。
在这种加工方式中,通过超声波来产生高强度的振动,将刀刃与工件产生较小的接触力,从而实现高效、高精度和高光洁度的切削加工。
与传统的切削方式相比,超声振动切削能够减少因切削力产生的热变形、热源等问题,在切削过程中减少了工件的变形和热效应。
同时,由于振动刀具能够切削更薄、更硬的材料,因此在加工金属、塑料和陶瓷材料方面有很广泛的应用。
近年来,随着超声技术的不断发展,超声振动切削技术也在不断优化和改进。
例如,研究人员利用超声振动切削技术开发出了一种新型的切割刀具,可以实现更高的质量和效率。
此外,还有研究人员使用超声振动切削技术加工纤维增强材料,提高了加工精度和表面质量。
二、超声往复振动穿孔超声往复振动穿孔技术是一种高效、高精度的穿孔方式。
传统的穿孔方式通常采用机械切割或激光穿孔,但由于这些方法受到材料的限制,很难达到高精度的效果。
超声往复振动穿孔技术通过超声波的作用实现穿孔,并可以在一定程度上改善传统穿孔方法的缺陷。
目前,超声往复振动穿孔技术已经在微电子、微机器人、精密制造等领域得到了广泛应用。
例如,在电子芯片的制造过程中,使用超声往复振动穿孔技术可以实现更高的精度和可靠性。
三、超声辅助喷涂超声辅助喷涂技术是一种新兴的涂层技术。
该技术通过超声波的高频振动使涂料微粒受到激励,形成颗粒的聚合体,从而形成更加均匀和致密的涂膜。
与传统的涂层方式相比,超声辅助喷涂技术可以提高涂层的质量和成形率,并且节省材料成本。
近年来,该技术已经在汽车制造、建筑物防水材料、涂料喷涂等领域得到了广泛的应用。
总体来看,超声技术在材料加工中的新进展主要集中在超声振动切削、超声往复振动穿孔和超声辅助喷涂等方面。
《2024年超声波技术应用现状》范文

《超声波技术应用现状》篇一一、引言随着现代科技的发展,超声波技术已成为多个领域不可或缺的工具。
超声波是指振动频率超过人耳可听范围的高频振动波,其在物理学、化学、医学、工程学等多个领域都得到了广泛的应用。
本文将就超声波技术的定义、特点及其在各领域的应用现状进行详细阐述。
二、超声波技术概述超声波技术以其非接触式检测和高效的特性被广泛运用。
通过传播速度快和衰减小等特性,该技术可有效地获取数据,分析结构特性以及提供相关物性参数。
该技术的关键优势在于其高度的非接触性和灵活性,使它在多个领域都能发挥作用。
三、超声波技术在医学领域的应用医学领域是超声波技术应用最为广泛的领域之一。
首先,在诊断方面,超声波技术已被广泛应用于各类医学影像检查,如超声心动图和腹部B超等,其对于人体内脏器的形态、大小以及病理改变有着极其准确的检测效果。
其次,在医学治疗方面,超声波技术也发挥了重要作用,如高强度聚焦超声治疗肿瘤等。
此外,超声波技术还用于外科手术中的辅助治疗和手术导航等。
四、超声波技术在工程领域的应用在工程领域,超声波技术的应用主要集中于材料无损检测和非金属材料探伤。
超声波可以用于检测金属和非金属材料内部的裂纹、气泡和杂质等缺陷,是产品质量控制和工艺优化的重要手段。
同时,超声波也在水利工程中用于检测大坝、水库等设施的裂缝和安全隐患。
此外,在石油工程中,超声波技术也用于地层结构的探测和油藏评估等。
五、超声波技术在其他领域的应用除了医学和工程领域,超声波技术在其他领域也得到了广泛的应用。
如在商业领域的表面涂层检查,它能确保产品符合特定的质量标准;在科学研究方面,超声的相互作用也经常用于测量和分析物理化学特性等;在工业上,还可以用于物料控制与生产流程监测等方面。
六、未来展望随着科技的不断进步和研发的深入进行,未来超声波技术的应用将会更加广泛和深入。
其精准度将不断提高,适用范围将进一步扩大,将会更好地服务于各领域的应用需求。
另外,新型材料、微电子技术的发展也将在很大程度上促进超声波技术的革新和发展。
磨削技术的发展现状及未来趋势分析

磨削技术的发展现状及未来趋势分析磨削技术是一种高精度、高效率的加工方法,广泛应用于机械制造、航空航天、汽车制造、电子设备等领域。
磨削技术的发展对制造业的提升和产品质量的改善起着重要作用。
本文将对磨削技术的发展现状及未来趋势进行分析。
近年来,磨削技术在国内外得到了快速发展。
一方面,随着高品质工件的需求不断增长,磨削技术逐渐成为高精度加工的主要方法之一。
在传统磨削技术的基础上,出现了多种新型磨削技术,如超声磨削、电化学磨削、电解腐蚀磨削等。
这些新技术不仅提高了工件的表面质量,还降低了加工成本和能耗。
另一方面,随着材料科学和机械制造技术的不断进步,磨削技术也在不断提高。
磨削刀具材料的研发使得切削效率得到了显著提升,磨粒性能的改善使得磨削加工得到了更好的控制,磨削液的优化使得磨削过程更加稳定和可靠。
这些技术进展让磨削技术在加工精度、表面质量和加工效率方面取得了巨大的进步。
未来,随着工业4.0和智能制造的快速发展,磨削技术将继续向着高精度、高效率和智能化方向发展。
首先,利用传感器和数据分析技术,实现磨削过程的监控和优化。
通过收集磨削过程中的各种数据,如刀具磨损情况、温度、振动等,可以实现对加工过程的实时监测和调整,提高加工效率和产品质量。
其次,磨削过程中的自动化和机器人技术将进一步推动磨削技术的发展。
自动化的磨削生产线可以实现对复杂形状工件的连续磨削加工,提高生产效率和稳定性。
机器人磨削系统可以实现对工件的全自动加工,减少人工干预,提高加工精度和一致性。
另外,磨削技术与其他加工技术的融合也将是未来的发展方向。
例如,磨削加工和3D打印技术结合,可以实现对复杂形状工件的加工;磨削加工和激光技术结合,可以实现对高硬度材料的加工。
这些新的磨削技术将进一步推动制造业的升级和创新。
此外,环保和节能也是磨削技术未来发展的重要方向。
随着能源和环境问题的日益突出,磨削工艺中的磨削液和废气处理将成为关注的焦点。
研发环保型磨削液和减少磨削过程中废气排放的技术不仅可以保护环境,还可以提高生产效率和降低成本。
超声波辅助研磨技术探究

超声波辅助研磨技术探究超声波辅助研磨技术探究近年来,随着科技的不断进步,超声波辅助研磨技术成为了研磨领域中的一项重要技术。
它通过利用超声波的特殊效应,提高了研磨过程中的效率和质量。
本文将对超声波辅助研磨技术进行探究。
超声波辅助研磨技术是将超声波与研磨过程相结合的一种研磨方式。
超声波是指频率超过20kHz的声波,其振动频率高达数十万次每秒。
相比传统的研磨方式,超声波辅助研磨技术具有独特的优势。
首先,超声波能够产生强大的声波振动。
在超声波的作用下,研磨工具与工件之间会产生高频振动,这种振动能够有效地破坏材料表面的氧化膜和附着层,提高研磨的效率。
同时,超声波振动还可以促使研磨液中的颗粒快速流动,增加研磨面与工具之间的接触频次,从而提高研磨的质量。
其次,超声波辅助研磨技术还具有材料表面修复的作用。
在研磨过程中,由于材料表面的缺陷和磨削引起的微观伤痕,会导致材料的力学性能下降。
而超声波的振动能够促进材料分子的重新排列和结晶,修复表面的缺陷和伤痕,提高材料的表面质量和力学性能。
此外,超声波辅助研磨技术还可以减少研磨过程中的磨损。
在传统的研磨过程中,由于磨料与工件之间的摩擦,会产生大量的热量,导致磨料和工件的磨损加剧。
而超声波的振动能够减少摩擦热的产生,降低磨料和工件的摩擦系数,从而减少磨损。
然而,超声波辅助研磨技术也存在一些挑战。
首先,超声波振动的能量较大,容易对材料造成损伤。
在应用超声波辅助研磨技术时需要控制超声波的能量和频率,以避免对材料的损伤。
其次,超声波辅助研磨技术的设备成本较高,需要专门的设备进行研磨。
因此,超声波辅助研磨技术的推广和应用还需要进一步的研究和开发。
总之,超声波辅助研磨技术作为一种创新的研磨方式,具有提高研磨效率和质量的潜力。
通过合理控制超声波的能量和频率,可以有效地应用超声波辅助研磨技术进行材料表面的加工和修复。
随着科技的进步,相信超声波辅助研磨技术将在各个领域得到更广泛的应用。
超声振动辅助电弧加工技术及机理

超声振动辅助电弧加工技术及机理电弧加工技术是一种常见的金属加工方法,其通过产生高温电弧,使金属工件表面熔化、喷溅,从而实现切削、焊接等操作。
然而,传统电弧加工存在效率低、加工精度有限等问题。
为了克服这些问题,超声振动辅助电弧加工技术应运而生。
超声振动辅助电弧加工技术是将超声振动与电弧加工相结合的一种新型加工方法。
超声振动通过高频振动作用于电弧,使其在振动频率下产生剧烈的振动。
这种振动能够改变电弧的形态和运动状态,从而达到优化电弧加工效果的目的。
超声振动辅助电弧加工技术具有以下几个主要特点:首先,该技术能够显著提高电弧加工的效率。
超声振动作用于电弧,能够增加电弧的能量密度和热量传递效率,使加工速度和效率得到明显提升。
其次,超声振动辅助电弧加工技术能够提高加工精度。
超声振动的作用下,电弧会发生剧烈的振动和扩散,使材料的熔池更加均匀,减小了加工过程中的温度梯度,从而提高了加工精度。
此外,超声振动辅助电弧加工技术还能够改善材料的性能。
振动作用下,电弧加工过程中的金属结晶结构得到了优化,晶粒尺寸变小,晶界清晰度提高,从而使材料的强度和硬度等性能得到了提升。
超声振动辅助电弧加工技术的机理主要包括以下几个方面:首先,超声振动作用下,电弧的振幅加大,使电弧产生扩散效应,提高了熔池的流动性。
这种流动性能够使熔池更加均匀,减小了焊接缺陷的产生。
其次,超声振动还能够改变电弧的形态,使其呈现球形或半球形。
这种形态的电弧具有较大的能量密度和热量传递效率,从而提高了加工效率和精度。
此外,超声振动作用下,电弧的振动频率与金属表面的共振频率相匹配,产生了共振效应。
这种共振效应能够使电弧与金属表面之间产生更大的摩擦力,进一步提高了加工效果。
综上所述,超声振动辅助电弧加工技术通过振动作用改善了电弧加工的效率、精度和材料性能。
该技术在航空航天、汽车制造等领域具有广泛应用前景,将为金属加工领域带来新的发展机遇。
- 1、下载文档前请自行甄别文档内容的完整性,平台不提供额外的编辑、内容补充、找答案等附加服务。
- 2、"仅部分预览"的文档,不可在线预览部分如存在完整性等问题,可反馈申请退款(可完整预览的文档不适用该条件!)。
- 3、如文档侵犯您的权益,请联系客服反馈,我们会尽快为您处理(人工客服工作时间:9:00-18:30)。
( .Ke a oaoy o u d me tl ce c o d a cd Ma hnn 1 yL b rtr fF n a na S in efrA vn e c iig,B in n tueo eh ooy,B in 0 ,C ia ej gIsi t fT cn lg i t ej g1 0 8 i 0 1 hn ;
关键词 : 械制造工 艺与设备 ;超声 辅助磨 削; 圆振 动;硬脆 材料 ;磨 削力 ;粗 糙度 机 椭
中图分类 号 : G 5 T 16 文 献标志码 : A 文 章 编 号 : 0 0 19 (0 0 l.5 00 10 0 3 2 1 ) 】13 .6
S a u n o r s f Ulr s ni ss e i di c ni u t t s a d Pr g e s o t a o c As it d Gr n ng Te h q e
第 3 卷第 1 期 1 1
2 0 10年 1 1月
兵
工
学
报
V0 . NO. I 1 3l 1
ACTA ARM AM ENTARI I
NO . 2Ol V O
超 声振 动辅 助 磨 削技 术 的现 状 与新 进 展
梁 志 强 ,王 西彬 ,吴 勇波 ,栗 勇 ,赵 文祥 ,庞Байду номын сангаас思 勤
( 北 京 理 工 大学 先进 加 工 技 术 国 防重 点 学 科 实验 室 , 京 1 0 8 ; 1 北 0 0 1
2 .秋 田 槊立 大 学 系 统 科学 技 术 学 部 , 田 20 1 ,日本 ) 秋 904
摘要 : 何实现硬脆 性材 料 的高效 率 、 如 高质 量 、 高精度 加 工是 现 代精 密制造 领域 的技 术难 题 , 为解决这 一难题超 声波振 动磨 削技术被 引入 到硬脆 性材料 的加工 中。综述 了超声振 动磨 削技 术 的 现状 , 于现有 的一维振 动磨 削与 二维 振动 磨 削技 术 , 重分 析 了不 同超 声 振 动施 加方 式 对磨 削 基 着 力、 加工表 面完整 性 、 砂轮磨 损等加 工特性 的影响 。作为 二 维振 动磨 削技 术 的最 新进展 , 垂直 型 对 椭 圆振 动磨 削技术 的加工原 理 以及加 工特 性进 行初 步介绍 。
2 a ut fS se ce c n eh oo y .F c l o ytmsS inea dT c n lg ,Akt rfcu a Unvri ,A i 9 0 4,Jp n y i Pee trl iest a y kt 2 0 1 a aa )
Ab tac :I u r n r cso a hii g fed, te e s c i c lp o lm o a hiv g fiin y, s r t n c re t p e iin m c n n il h r i a rt a r b e t c e e hih efce c i
i g me h d a e i to u e n t o r n r d c d.
Ke y wor ds: m a hn fcu ig t c n q e a d q i me t u ta o i sitd rn i g; el tc lv b a c ioa t rn e h i u n e u p n ; lr s n c a sse g id n li ia ir — p
o oh o e dm e so a n wo d me so a lr s n c a sse rn i g t c n q e r n lz d. As a fb t n — i n in la d t — i n in lu ta o i sitd g i d n e h i u sa e a ay e n w p o r s ,t e p icp e a d f n me tlc a a t rsi so e tc lel tc lu ta o i s it d g i d e r ge s h rn il n u da n a h r ce it fv ria li i a lr s n c a sse rn — c p
h g — u lt n ih— r cso c i i g frh r rtl t ra . Ba e n t i a k r u d,t e uta ih q ai a d h g p e iin ma h n n o a d b i e mae i1 y t s d o h sb c g o n h l - r s n c a sse rn i g ma h n n swi ey ito u e s a p o sn rc si g t c n lg . I h sp — o i s it d g i d n c i i g i d l n r d c d a r mii g p o e sn e h oo y n t i a pe ,t e ma h n n h r ce it s s e ily g id n oc s,go n u f c ne r l y a d wh e a , r h c i i gc a a trsi ,e p cal rn i g fr e c r u d s ra e it g ai n e lwe r t