海底油气管道防腐层的选择
油气田井下油管的防腐技术

油气田井下油管的防腐技术在石油工业中起着至关重要的作用,可以延长油管的使用寿命、提高生产效率,并保证油气的安全输送。
以下是一些常见的油气田井下油管防腐技术:
1. 油管涂层防腐技术
-环氧涂层:环氧涂层是最常用的油管防腐材料之一,具有良好的耐腐蚀性能和粘附性,可以有效防止金属表面受到腐蚀。
-聚乙烯涂层:聚乙烯涂层具有良好的机械性能和耐腐蚀性能,广泛应用于海底油气管道等环境中。
-聚胺脂涂层:聚胺脂涂层具有优异的耐化学腐蚀性能和耐磨损性能,适用于高腐蚀环境下的油管防腐。
2. 阴极保护技术
-镀锌:将油管表面镀上一层锌,利用锌的阳极保护作用保护油管不受腐蚀。
-牺牲阳极保护:在油管系统中加入一些更容易氧化的金属,如锌、铝等,使其成为“牺牲阳极”,保护油管不受腐蚀。
3. 管道涂层检测技术
-非破坏检测:采用超声波、X射线、磁粉探伤等非破坏检测技术对油管涂层进行定期检测,及时发现问题并进行修复。
-电化学阻抗谱分析:通过电化学阻抗谱分析技术,监测涂层的电化
学性能变化,评估防腐涂层的状况和耐腐蚀性能。
4. 管道防腐维护管理
-定期检查维护:定期对油管涂层进行检查和维护,及时修复涂层损坏或腐蚀部位。
-建立档案记录:建立完善的管道防腐维护档案,记录每次维护和检测的结果,制定科学的预防性维护计划。
通过以上技术手段和管理措施,可以有效延长油气田井下油管的使用寿命,确保油气输送系统的安全稳定运行。
同时,保障油气资源的开发利用,促进石油工业的持续发展。
海底油气管线现场节点内部防腐施工及质量控制要点

海底油气管线现场节点内部防腐施工及质量控制要点1. 引言1.1 背景介绍海底油气管线是海洋油田开发的重要基础设施之一,其安全运行与否直接影响到海洋油气资源的开发利用和生产运营的顺利进行。
海底油气管线现场节点内部防腐施工是保障海底管线运行安全和延长使用寿命的关键环节之一。
节点内部防腐施工质量的高低直接影响到管线的耐蚀性能和安全性能,关系到整个海底油气开发生产系统的稳定运行。
随着海洋石油开发的不断扩大和深化,海底油气管线的数量和长度也在不断增加,而海底环境的复杂多变性给海底管线的运行带来了更大的挑战,因此对海底油气管线现场节点内部防腐施工的重视程度也越来越高。
随着我国海洋石油勘探开发技术的不断进步和完善,海底油气管线现场节点内部防腐施工技术也得到了长足的发展,但仍然面临着一些挑战和问题,如施工质量控制不严格、验收标准不清晰等。
开展海底油气管线现场节点内部防腐施工及质量控制研究和实践具有重要意义,对提高海底油气管线施工质量、保障管线运行安全、推动海洋石油开发技术水平的提高具有积极意义。
【背景介绍】1.2 研究意义海底油气管线是连接陆上油气生产设施与海底油气田的主要通道,其安全可靠运行对于油气勘探开采具有重要意义。
节点内部防腐施工是保障海底油气管线长期稳定运行的关键环节,其质量直接影响管线的使用寿命和安全性。
研究节点内部防腐施工及质量控制要点的意义在于加强对海底油气管线施工质量的监督和管理,提高防腐施工技术水平,减少因施工质量问题导致的安全事故发生的可能性,保障海底油气管线的安全运行。
通过深入研究节点内部防腐施工的工程前期准备工作、施工工艺流程、质量控制要点和常见质量问题及处理方法等方面的内容,能够为相关领域的工程技术人员提供实用指导和参考,提高他们在节点内部防腐施工方面的技术水平和管理水平,从而更好地保障海底油气管线的安全运行,促进油气资源的开发利用。
2. 正文2.1 工程前期准备工作海底油气管线现场节点内部防腐施工的工程前期准备工作至关重要,直接影响着施工后的质量和效率。
海底管道防腐施工方案
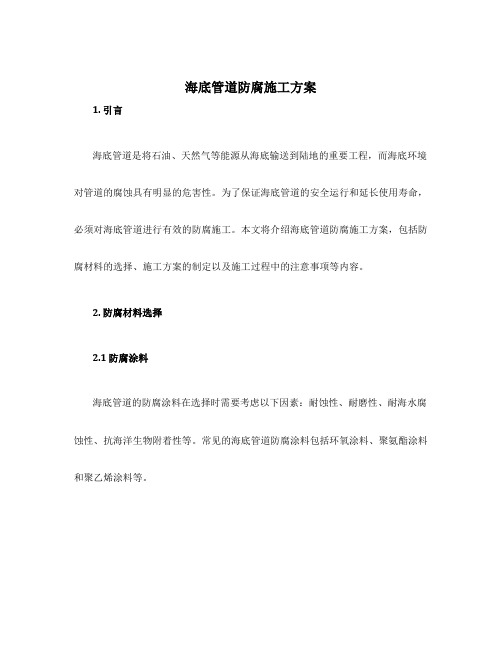
海底管道防腐施工方案1. 引言海底管道是将石油、天然气等能源从海底输送到陆地的重要工程,而海底环境对管道的腐蚀具有明显的危害性。
为了保证海底管道的安全运行和延长使用寿命,必须对海底管道进行有效的防腐施工。
本文将介绍海底管道防腐施工方案,包括防腐材料的选择、施工方案的制定以及施工过程中的注意事项等内容。
2. 防腐材料选择2.1 防腐涂料海底管道的防腐涂料在选择时需要考虑以下因素:耐蚀性、耐磨性、耐海水腐蚀性、抗海洋生物附着性等。
常见的海底管道防腐涂料包括环氧涂料、聚氨酯涂料和聚乙烯涂料等。
在选择防腐涂料时,应综合考虑管道材质、运输介质以及海底环境等因素,选择具有良好耐腐蚀性能和长期稳定性的涂料。
同时,需要确保涂料的施工性能良好,能够满足施工现场的要求。
2.2 防腐包裹材料海底管道防腐包裹材料主要用于保护管道的外表面,防止海水中的腐蚀物质侵蚀管道。
常见的海底管道防腐包裹材料包括聚乙烯包裹材料、玻璃纤维包裹材料和聚丙烯包裹材料等。
在选择防腐包裹材料时,应考虑材料的耐腐蚀性、耐压性以及尺寸稳定性等因素。
此外,还需要对包裹材料进行合适的加工和安装,确保其与管道表面完全贴合,形成均匀的保护层。
3. 施工方案制定3.1 施工前准备工作在进行海底管道防腐施工前,需要进行充分的准备工作。
首先,应对管道进行清洁和除锈处理,确保管道表面光洁。
其次,需要对防腐材料进行检查和测试,确保材料质量合格。
最后,进行施工现场的环境评估和安全评估,制定安全施工措施。
3.2 施工过程海底管道防腐施工的主要过程包括涂刷防腐涂料和包裹防腐材料。
3.2.1 防腐涂料施工首先,使用刷子或喷枪等工具将防腐涂料均匀地涂刷在管道表面。
涂刷时应确保涂料的厚度符合设计要求,且涂层均匀光滑。
对于较大直径的管道,可以采用机械涂刷设备进行施工。
3.2.2 防腐包裹材料施工首先,将防腐包裹材料剪成合适尺寸,包裹在管道表面上。
然后,使用热风枪等设备对包裹材料进行加热,使其与管道表面粘结牢固。
海底油气管线现场节点内部防腐施工及质量控制要点
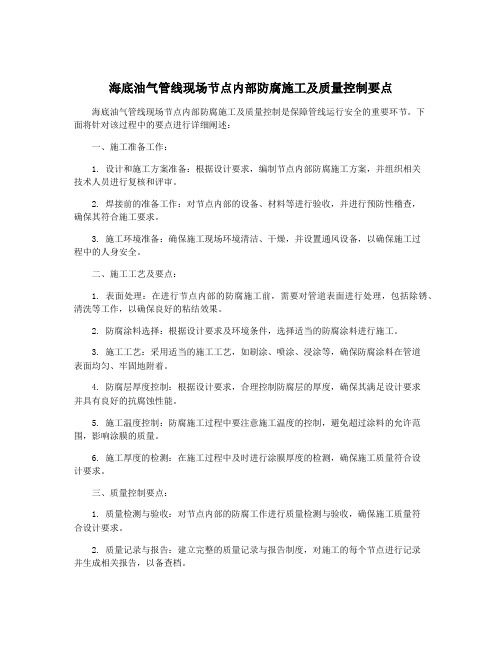
海底油气管线现场节点内部防腐施工及质量控制要点海底油气管线现场节点内部防腐施工及质量控制是保障管线运行安全的重要环节。
下面将针对该过程中的要点进行详细阐述:一、施工准备工作:1. 设计和施工方案准备:根据设计要求,编制节点内部防腐施工方案,并组织相关技术人员进行复核和评审。
2. 焊接前的准备工作:对节点内部的设备、材料等进行验收,并进行预防性稽查,确保其符合施工要求。
3. 施工环境准备:确保施工现场环境清洁、干燥,并设置通风设备,以确保施工过程中的人身安全。
二、施工工艺及要点:1. 表面处理:在进行节点内部的防腐施工前,需要对管道表面进行处理,包括除锈、清洗等工作,以确保良好的粘结效果。
2. 防腐涂料选择:根据设计要求及环境条件,选择适当的防腐涂料进行施工。
3. 施工工艺:采用适当的施工工艺,如刷涂、喷涂、浸涂等,确保防腐涂料在管道表面均匀、牢固地附着。
4. 防腐层厚度控制:根据设计要求,合理控制防腐层的厚度,确保其满足设计要求并具有良好的抗腐蚀性能。
5. 施工温度控制:防腐施工过程中要注意施工温度的控制,避免超过涂料的允许范围,影响涂膜的质量。
6. 施工厚度的检测:在施工过程中及时进行涂膜厚度的检测,确保施工质量符合设计要求。
三、质量控制要点:1. 质量检测与验收:对节点内部的防腐工作进行质量检测与验收,确保施工质量符合设计要求。
2. 质量记录与报告:建立完整的质量记录与报告制度,对施工的每个节点进行记录并生成相关报告,以备查档。
3. 资材管理:加强对防腐材料的质量管理,组织检测机构对材料进行抽样检验,确保材料符合标准要求。
4. 管道质量检验:在施工结束后,进行管道的质量检验,对防腐层的厚度、附着力、韧性等指标进行检测,以确保管道的质量。
5. 质量监督与整改:建立质量监督与整改制度,及时发现问题并采取相应整改措施,确保施工质量。
海底油气管线现场节点内部防腐施工及质量控制要点
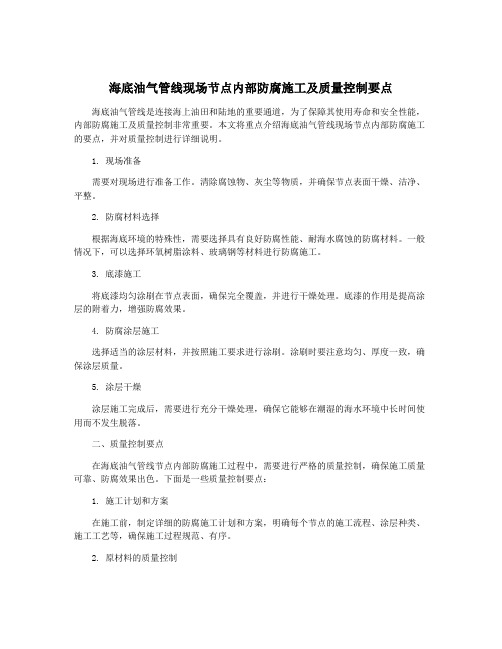
海底油气管线现场节点内部防腐施工及质量控制要点海底油气管线是连接海上油田和陆地的重要通道,为了保障其使用寿命和安全性能,内部防腐施工及质量控制非常重要。
本文将重点介绍海底油气管线现场节点内部防腐施工的要点,并对质量控制进行详细说明。
1. 现场准备需要对现场进行准备工作。
清除腐蚀物、灰尘等物质,并确保节点表面干燥、洁净、平整。
2. 防腐材料选择根据海底环境的特殊性,需要选择具有良好防腐性能、耐海水腐蚀的防腐材料。
一般情况下,可以选择环氧树脂涂料、玻璃钢等材料进行防腐施工。
3. 底漆施工将底漆均匀涂刷在节点表面,确保完全覆盖,并进行干燥处理。
底漆的作用是提高涂层的附着力,增强防腐效果。
4. 防腐涂层施工选择适当的涂层材料,并按照施工要求进行涂刷。
涂刷时要注意均匀、厚度一致,确保涂层质量。
5. 涂层干燥涂层施工完成后,需要进行充分干燥处理,确保它能够在潮湿的海水环境中长时间使用而不发生脱落。
二、质量控制要点在海底油气管线节点内部防腐施工过程中,需要进行严格的质量控制,确保施工质量可靠、防腐效果出色。
下面是一些质量控制要点:1. 施工计划和方案在施工前,制定详细的防腐施工计划和方案,明确每个节点的施工流程、涂层种类、施工工艺等,确保施工过程规范、有序。
2. 原材料的质量控制对防腐涂料和防腐材料进行验收,要求其符合国家相关标准,并进行质量记录。
原材料的质量直接影响施工后的防腐效果,所以需保证原材料质量可靠。
3.施工人员的培训和管理防腐施工过程中,要确保施工人员具备防腐施工的相关技能,并严格落实岗位责任。
进行班前教育和技术培训,提高施工人员的施工水平,保证施工质量。
加强对施工节点现场的监督和管理,确保施工过程中的质量问题能够及时发现和解决。
对疑似质量问题的节点,进行取样检测,确保施工质量符合要求。
5. 质量记录和报告施工完成后,对各个节点的防腐施工进行记录和报告,包括施工过程的记录、验收记录和施工质量分析报告等。
海底油气管线现场节点内部防腐施工及质量控制要点

海底油气管线现场节点内部防腐施工及质量控制要点海底油气管线的节点处是管线系统的重要组成部分。
节点处连接着海底管线的两端,起着承压和转移石油天然气的作用。
因此,节点的防腐施工和质量控制关系到整个管线系统的运行安全和寿命。
本文将介绍海底油气管线现场节点内部防腐施工及质量控制要点。
一、防腐施工要点1. 工序控制:防腐施工需要按照规范的工序进行。
首先需要清理节点内部的杂物和油污,然后进行钢材表面处理,涂刷底漆和面漆。
每道工序之间需要严格控制干燥时间和厚度。
2. 选材:节点内部的钢材需要选用耐腐蚀的材料。
底漆和面漆需要选用质量稳定、具有一定的耐化学性和耐海水腐蚀性能的防腐涂料。
3. 加热控制:海底油气管线节点防腐施工需要在一定的温度范围内进行,一般为15℃至35℃。
在施工过程中,应根据当时海底温度和海水温度,采取加热或降温控制,确保防腐涂料完全固化和贴合性好。
4. 局部防护:在节点较易腐蚀的部位,需要加强局部涂刷厚度或加固材料。
例如,管道接头处应当将涂层涂刷至无缺陷和有足够的厚度。
二、质量控制要点1. 管线内部清理:在进行节点内部防腐施工前,需要对管线内部进行清理和疏通,确保防腐涂料能够完整地附着在管壁上。
2. 涂层质量检查:防腐涂料在施工过程中需要进行现场检查,包括表面干燥时间、涂层厚度、均匀性、颜色、附着力、硬度、光泽度等各项指标。
同时也需要对涂层进行水分检测和酸碱度检测,确保涂层质量合格。
3. 涂层检验:在涂料施工完毕之后,需要进行涂层检验,检查涂层厚度、均匀性和附着力等各项指标。
对于不合格的涂层需要进行修补或整改,直至合格为止。
4. 技术资料备案:海底油气管线节点的防腐施工需要完整的技术资料资料备案,包括防腐施工规范、涂料质量证明、施工现场记录等,以备后续的检查和维护。
以上就是海底油气管线现场节点内部防腐施工和质量控制要点的介绍。
在防腐施工过程中,需要科学规范地进行管道清洗、表面处理、涂层施工和涂层质量检查,对于不合格的涂层要及时进行修补。
海上油气开采设备的防水防腐技术与材料选择
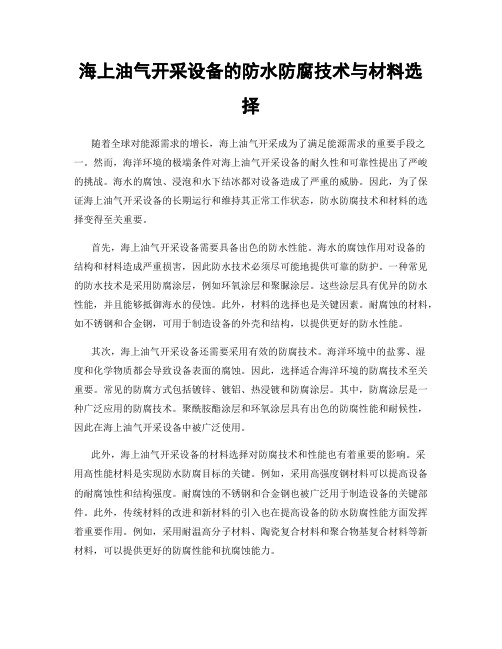
海上油气开采设备的防水防腐技术与材料选择随着全球对能源需求的增长,海上油气开采成为了满足能源需求的重要手段之一。
然而,海洋环境的极端条件对海上油气开采设备的耐久性和可靠性提出了严峻的挑战。
海水的腐蚀、浸泡和水下结冰都对设备造成了严重的威胁。
因此,为了保证海上油气开采设备的长期运行和维持其正常工作状态,防水防腐技术和材料的选择变得至关重要。
首先,海上油气开采设备需要具备出色的防水性能。
海水的腐蚀作用对设备的结构和材料造成严重损害,因此防水技术必须尽可能地提供可靠的防护。
一种常见的防水技术是采用防腐涂层,例如环氧涂层和聚脲涂层。
这些涂层具有优异的防水性能,并且能够抵御海水的侵蚀。
此外,材料的选择也是关键因素。
耐腐蚀的材料,如不锈钢和合金钢,可用于制造设备的外壳和结构,以提供更好的防水性能。
其次,海上油气开采设备还需要采用有效的防腐技术。
海洋环境中的盐雾、湿度和化学物质都会导致设备表面的腐蚀。
因此,选择适合海洋环境的防腐技术至关重要。
常见的防腐方式包括镀锌、镀铝、热浸镀和防腐涂层。
其中,防腐涂层是一种广泛应用的防腐技术。
聚酰胺酯涂层和环氧涂层具有出色的防腐性能和耐候性,因此在海上油气开采设备中被广泛使用。
此外,海上油气开采设备的材料选择对防腐技术和性能也有着重要的影响。
采用高性能材料是实现防水防腐目标的关键。
例如,采用高强度钢材料可以提高设备的耐腐蚀性和结构强度。
耐腐蚀的不锈钢和合金钢也被广泛用于制造设备的关键部件。
此外,传统材料的改进和新材料的引入也在提高设备的防水防腐性能方面发挥着重要作用。
例如,采用耐温高分子材料、陶瓷复合材料和聚合物基复合材料等新材料,可以提供更好的防腐性能和抗腐蚀能力。
最后,应综合考虑设备的运行环境,以选择最合适的防水防腐技术和材料。
不同的海域和水深环境对设备的防水防腐要求不同。
例如,对于浅海湿地,对海上油气开采设备的防腐性能要求更高,因为该地区更容易受到海水的侵蚀和损害。
因此,在设备设计和制造过程中,必须考虑到不同环境条件下的防水防腐需求,并确保所选择的技术和材料能够在任何条件下保持设备的完整和性能。
海底油气管线现场节点内部防腐施工及质量控制要点

海底油气管线现场节点内部防腐施工及质量控制要点海底油气管线是海洋能源开发的重要设施,其长期处于高度腐蚀环境中,必须进行有效的防腐施工以保障管线的安全可靠运营。
下面将从内部防腐施工和质量控制两个方面介绍海底油气管线现场节点的防腐要点。
一、内部防腐施工要点1. 材料选择:选择适合海底环境的防腐材料,如环氧树脂、聚酰胺、氟碳漆等。
材料应具有良好的耐腐蚀性能和附着力,能够有效防止海水、盐雾和沉积物的侵蚀。
2. 表面处理:在施工前,要对管线的内壁进行彻底的清洁和处理,确保表面无污垢、油脂和锈蚀物,以保证防腐层能够牢固地附着在管线上。
3. 涂层施工:根据管线的材质和操作条件,选择适当的涂覆方法,如刷涂、喷涂、喷涂等。
施工时要注意涂层的均匀性和厚度,确保涂层的质量和防腐效果。
4. 预热和固化:涂层施工后,要及时进行预热和固化处理,以提高涂层的附着力和耐腐蚀性能。
预热温度和时间应根据涂层材料的要求进行控制。
5. 层间连接:不同涂层层间的连接处是防腐施工的重要部分,要确保涂层之间的质量和连续性,防止涂层的局部剥离和腐蚀。
二、质量控制要点1. 施工记录:在施工过程中要做好详细的记录,包括施工材料、施工方法、施工工艺参数等。
并对施工过程中的质量问题进行记录和整改,以便后期的追溯和评估。
2. 检验检测:要对管线内部的防腐层进行必要的检验和检测。
可采用现场测厚仪、附着力测试仪等检测工具,对防腐层的厚度和附着力进行定量测量。
3. 质量评估:对防腐施工的质量进行评估,包括涂层的均匀性、厚度、硬度和耐腐蚀性能等。
评估结果应与相关标准和要求进行比对,以确保防腐施工的质量符合规范要求。
4. 整改措施:如果发现防腐施工存在质量问题,要及时采取相应的整改措施,修复涂层的缺陷和损伤,以保证管线的防腐效果。
5. 质量保证:防腐施工完成后,要进行质量保证工作。
对防腐层进行长期的监测和维护,定期检验涂层的状况,并采取相应的维修和更换措施,确保管线防腐性能的持久有效。
海底石油管道的防腐与保温技术

第一章绪论1.1目的与意义腐蚀到处存在于生活当中,所造成的后果是非常严重的,尤其是在海洋石油工业中,海洋环境中防止腐蚀造成的经济损失占其生产本的10%左右。
在腐蚀严重的海水、海泥环境中,管道的外部腐蚀比陆上管线严重的多,且大幅度降低的海底管道的服役期限,同时由腐蚀造成海底输油管线泄露时有发生,产生严重的石油污染和环境污染。
可以看出腐蚀是影响海洋管道系统的可靠性和其使用寿命的关键因素,这使得腐蚀防治成为海洋管道系统的重中之重。
海洋石油管道大多处于温度较低的环境当中,热力环境恶劣,结蜡趋势远远高于陆上管道,由结蜡造成的后果也比陆上管道严重,所以为了控制海洋石油管道输送工况,优化石油流动行为,对管道的保温显得尤为重要。
管道的防腐和保温,不但延长了管道的使用寿命,减少了资源浪费,而且是保障节能,降低生产成本的的重要措施。
近年来,深海开发中的油气勘探和生产活动大大增加,如墨西哥湾(GoM),西非(WoA),巴西和北海,与几年前相比深水增加了一倍。
海洋工业正在更深的海域中建造生产系统,更多地采用新技术并较大程度地发展现有技术。
作为油气生产中不可或缺的管道系统,保障其安全使用尤为重要。
对于1000m以上超深水管道,防腐保温体系的技术水平决定了其能否安全高效经济运行。
国外通过实践与研究相结合的模式,使海洋管道的防腐保温技术不断得到发展,开发出了许多新技术,以满足生产要求。
国内对南中国海的联合勘探和生产,开始在水深100-400m的范围内进行,最近的勘探活动显示,在南中国海水深约600处发现了油气资源。
但是对于深水管道防腐保温体系的设计及相关材料的研究,国内处于刚起步阶段,与国外存在着很大的差距,需要加大科研力度,为海洋油气开发提供技术支持和保障。
1.2.国内外研究现状1.2.1国外研究现状1.2.1.1海洋管道防腐技术目前海洋管道的防腐层主要采用熔结环氧粉末(FBE)、双层熔结环氧粉末(双层FBE)、三层聚乙烯(3PE)、三层聚丙烯(3PP)以及高性能复合涂层(HPCC),早期有采用煤焦油瓷漆、聚烯烃缠带、石油沥青等防腐手段。
海底油气管线现场节点内部防腐施工及质量控制要点
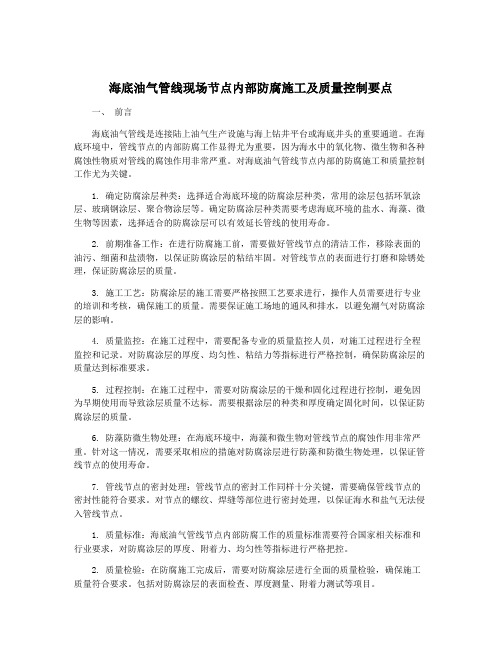
海底油气管线现场节点内部防腐施工及质量控制要点一、前言海底油气管线是连接陆上油气生产设施与海上钻井平台或海底井头的重要通道。
在海底环境中,管线节点的内部防腐工作显得尤为重要,因为海水中的氧化物、微生物和各种腐蚀性物质对管线的腐蚀作用非常严重。
对海底油气管线节点内部的防腐施工和质量控制工作尤为关键。
1. 确定防腐涂层种类:选择适合海底环境的防腐涂层种类,常用的涂层包括环氧涂层、玻璃钢涂层、聚合物涂层等。
确定防腐涂层种类需要考虑海底环境的盐水、海藻、微生物等因素,选择适合的防腐涂层可以有效延长管线的使用寿命。
2. 前期准备工作:在进行防腐施工前,需要做好管线节点的清洁工作,移除表面的油污、细菌和盐渍物,以保证防腐涂层的粘结牢固。
对管线节点的表面进行打磨和除锈处理,保证防腐涂层的质量。
3. 施工工艺:防腐涂层的施工需要严格按照工艺要求进行,操作人员需要进行专业的培训和考核,确保施工的质量。
需要保证施工场地的通风和排水,以避免潮气对防腐涂层的影响。
4. 质量监控:在施工过程中,需要配备专业的质量监控人员,对施工过程进行全程监控和记录。
对防腐涂层的厚度、均匀性、粘结力等指标进行严格控制,确保防腐涂层的质量达到标准要求。
5. 过程控制:在施工过程中,需要对防腐涂层的干燥和固化过程进行控制,避免因为早期使用而导致涂层质量不达标。
需要根据涂层的种类和厚度确定固化时间,以保证防腐涂层的质量。
6. 防藻防微生物处理:在海底环境中,海藻和微生物对管线节点的腐蚀作用非常严重。
针对这一情况,需要采取相应的措施对防腐涂层进行防藻和防微生物处理,以保证管线节点的使用寿命。
7. 管线节点的密封处理:管线节点的密封工作同样十分关键,需要确保管线节点的密封性能符合要求。
对节点的螺纹、焊缝等部位进行密封处理,以保证海水和盐气无法侵入管线节点。
1. 质量标准:海底油气管线节点内部防腐工作的质量标准需要符合国家相关标准和行业要求,对防腐涂层的厚度、附着力、均匀性等指标进行严格把控。
海底油气管线现场节点内部防腐施工及质量控制要点

海底油气管线现场节点内部防腐施工及质量控制要点海底油气管线是输送海底油气资源的重要设施,为确保管线的安全运行和延长使用寿命,节点内部防腐施工及质量控制十分关键。
以下是海底油气管线现场节点内部防腐施工及质量控制的要点:1. 施工材料选择选择符合国家标准的防腐材料,如环氧涂料、绝缘胶带等,要求其具有优异的耐腐蚀性能和粘附性能,能够长时间保持稳定的防腐效果。
2. 表面处理在进行防腐施工前,必须对管线节点进行彻底清洁,并进行表面处理。
表面处理工艺包括除锈、除油、除尘等,确保管线表面光洁,无油污和杂质。
3. 防腐施工工艺根据设计要求和工程环境,采用适合的防腐施工工艺。
一般情况下,可以采用涂刷、喷涂和涂覆等工艺方法进行防腐层的施工,确保防腐层的均匀性和整体性。
4. 施工环境要求防腐施工需要在适宜的环境条件下进行,避免在大风、高温或湿度较大的情况下施工。
施工环境温度、湿度等要符合防腐材料的施工要求。
5. 施工人员要求防腐施工需要具备一定的经验和技能的施工人员进行施工。
施工人员应接受相关培训,了解施工工艺和操作规程,并具备相应的操作技巧。
6. 质量控制要点在防腐施工过程中,需要对施工质量进行严格控制。
包括防腐材料的质量检查、工艺的符合性检验、施工过程的监控等。
还需要对施工完成后的防腐层进行质量检测,确保防腐层的厚度、粘附力等指标符合设计要求。
7. 施工记录和档案管理防腐施工需要做好施工记录和档案管理工作,包括施工过程的记录、质量检测报告、施工问题的处理等。
这些记录和档案是对施工质量的重要证明和依据,也便于日后的维护和管理。
海底油气管线现场节点内部防腐施工及质量控制要点包括施工材料选择、表面处理、防腐施工工艺、施工环境要求、施工人员要求、质量控制要点、施工记录和档案管理等方面,通过科学规范的施工措施,可以保证海底油气管线的安全运行和延长使用寿命。
浅论海洋油气管道的防腐及维护措施
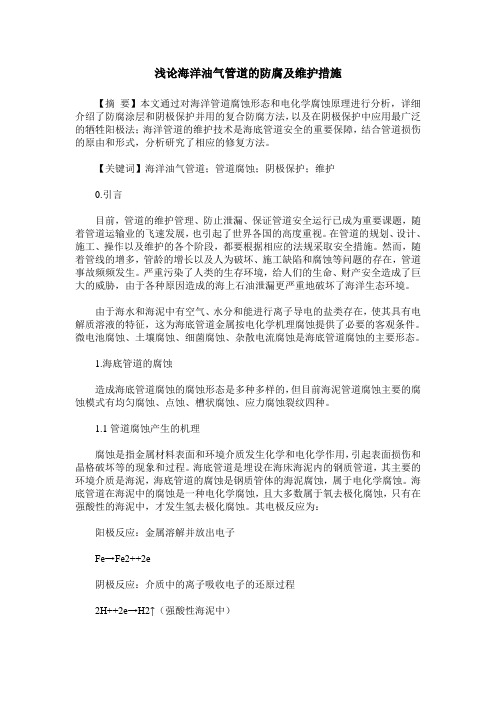
浅论海洋油气管道的防腐及维护措施【摘要】本文通过对海洋管道腐蚀形态和电化学腐蚀原理进行分析,详细介绍了防腐涂层和阴极保护并用的复合防腐方法,以及在阴极保护中应用最广泛的牺牲阳极法;海洋管道的维护技术是海底管道安全的重要保障,结合管道损伤的原由和形式,分析研究了相应的修复方法。
【关键词】海洋油气管道;管道腐蚀;阴极保护;维护0.引言目前,管道的维护管理、防止泄漏、保证管道安全运行已成为重要课题,随着管道运输业的飞速发展,也引起了世界各国的高度重视。
在管道的规划、设计、施工、操作以及维护的各个阶段,都要根据相应的法规采取安全措施。
然而,随着管线的增多,管龄的增长以及人为破坏、施工缺陷和腐蚀等问题的存在,管道事故频频发生。
严重污染了人类的生存环境,给人们的生命、财产安全造成了巨大的威胁,由于各种原因造成的海上石油泄漏更严重地破坏了海洋生态环境。
由于海水和海泥中有空气、水分和能进行离子导电的盐类存在,使其具有电解质溶液的特征,这为海底管道金属按电化学机理腐蚀提供了必要的客观条件。
微电池腐蚀、土壤腐蚀、细菌腐蚀、杂散电流腐蚀是海底管道腐蚀的主要形态。
1.海底管道的腐蚀造成海底管道腐蚀的腐蚀形态是多种多样的,但目前海泥管道腐蚀主要的腐蚀模式有均匀腐蚀、点蚀、槽状腐蚀、应力腐蚀裂纹四种。
1.1管道腐蚀产生的机理腐蚀是指金属材料表面和环境介质发生化学和电化学作用,引起表面损伤和晶格破坏等的现象和过程。
海底管道是埋设在海床海泥内的钢质管道,其主要的环境介质是海泥,海底管道的腐蚀是钢质管体的海泥腐蚀,属于电化学腐蚀。
海底管道在海泥中的腐蚀是一种电化学腐蚀,且大多数属于氧去极化腐蚀,只有在强酸性的海泥中,才发生氢去极化腐蚀。
其电极反应为:阳极反应:金属溶解并放出电子Fe→Fe2++2e阴极反应:介质中的离子吸收电子的还原过程2H++2e→H2↑(强酸性海泥中)O2+2H2O+4e→4OH-(中、碱性海泥中)1.2海底管道的腐蚀防护及防腐涂层的选择现今,全世界数百条海底管线均采用涂层和阴极保护联合应用的方法进行防护。
海底油气管线现场节点内部防腐施工及质量控制要点

海底油气管线现场节点内部防腐施工及质量控制要点海底油气管线是连接海上油气生产平台与陆地油气加工设施的重要通道。
为了保证管线的安全运行和寿命,节点内部的防腐施工非常重要。
本文将从施工材料、施工工艺和质量控制三个方面介绍海底油气管线节点内部防腐施工的要点。
一、施工材料1. 防腐涂料:选择防腐效果好、附着力强、耐高温、耐腐蚀、耐磨损的防腐涂料。
常用的防腐涂料有环氧树脂涂料、聚氨酯涂料等。
2. 防腐刷毛:选择耐腐蚀、抗磨损的刷毛。
刷毛的长度应适中,不得过长或过短,保证刷涂均匀。
3. 防腐胶带:选择耐腐蚀、耐高温、具有橡胶弹性的防腐胶带。
胶带应具有良好的粘结力,能够牢固地粘附在管道表面。
4. 防腐补强材料:在节点处需要进行防腐补强,选择具有耐高温、耐腐蚀、强度高的材料,如玻璃钢、碳纤维等。
二、施工工艺1. 表面处理:节点部位的表面处理非常重要。
首先要对管道表面进行除锈,彻底清除污垢和氧化物,保证涂料的附着力。
然后进行打磨,使管道表面光滑。
2. 预涂处理:在进行施工前,需对节点部位进行预涂处理。
首先在节点部位涂上一层防腐底漆,增加底漆与钢材的粘结力,提高防腐效果。
3. 防腐涂料施工:防腐涂料应根据施工要求进行搅拌,以保证涂料的均匀性。
对于节点部位,应分层涂刷,确保涂膜厚度符合要求。
每一层涂刷后,需进行干燥,保证涂膜强度。
4. 防腐胶带施工:在节点部位需要进行防腐补强时,首先将管道表面涂上一层防腐底漆。
然后将防腐胶带缠绕在管道上,要求胶带搭接严密,无空隙,确保密封性能。
5. 防腐补强:节点部位的防腐补强是为了增加节点的强度和耐腐蚀性能。
补强材料应选择与管道材料相配的材料,并按照工艺要求进行施工。
三、质量控制1. 面料检测:施工前要对防腐涂料进行检测,确保涂料的质量符合要求。
2. 施工现场检验:施工过程中要进行现场检验,检查表面处理是否彻底、涂膜厚度是否符合要求、涂层干燥是否充分等。
3. 防腐补强检验:对于防腐补强部位,要进行力学性能测试和耐腐蚀性能测试,确保补强材料的质量。
海底管道铺设工程施工中的管道防腐与维护技术研究

海底管道铺设工程施工中的管道防腐与维护技术研究随着海洋石油开发的不断深入,海底管道的需求也随之增加。
海底管道作为海洋石油开发的重要组成部分,承载着输送石油和天然气等能源资源的重要任务。
然而,由于长期暴露在海洋环境中,海底管道容易受到腐蚀和损坏,因此管道的防腐与维护技术显得至关重要。
一、海底管道的防腐技术1. 防腐涂层技术在海底管道施工中,使用防腐涂层技术是常见的防护措施之一。
防腐涂层可以有效地保护管道免受海水中的腐蚀,延长管道的使用寿命。
目前,常用的防腐涂层包括环氧涂层、聚乙烯涂层和三层共聚物涂层等。
2. 阳极保护技术阳极保护是一种常用的海底管道防腐技术。
通过在海底管道表面连接阳极体,使阳极体和管道构成电化学电池,阳极体被腐蚀,从而保护管道不被腐蚀。
这种技术可以有效地降低海水中的电位,减少管道的腐蚀速度。
二、海底管道的维护技术1. 监测与检修技术海底管道的定期监测与检修是维护管道的重要环节。
通过使用无人潜航器、遥感技术等现代技术手段,可以对海底管道进行全面的巡检和检修,及时发现管道的腐蚀、破损等问题,并采取相应的维护措施。
2. 清洗与防结垢技术海水中的沉积物和结垢物质容易在管道内形成沉积物,对管道的正常运行产生不利影响。
因此,定期的清洗与防结垢工作是必要的。
常用的清洗和防结垢技术包括高压水射流清洗、化学药剂清洗和超声波清洗等。
3. 修复与更换技术当海底管道受到严重损坏时,修复与更换便成为必要的维护手段。
修复常采用的方法有局部疏通、外套管修复和撇灌技术等,而更换则是将受损的管道进行全面更换。
三、海底管道施工中的技术研究1. 管道防腐技术的改进研究目前,海底管道的防腐技术已取得了一定的进展,但仍存在一些问题。
例如,防腐涂层的附着力和耐腐蚀性有待提高,阳极保护技术仍面临着较高的成本和技术难题。
因此,需要进一步的研究和改进,提高防腐技术的效果和可靠性。
2. 海底管道维护技术的创新研究随着海洋工程技术的发展,海底管道维护技术也需要不断创新。
油气储运中的管道防腐措施分析

油气储运中的管道防腐措施分析油气储运中的管道防腐措施是非常重要的,它能够保护管道不受腐蚀的影响,确保油气的安全储运。
下面将就油气储运中的管道防腐措施进行分析。
管道内壁涂层是一种常见的防腐措施。
在油气储运中,由于液态和气体的特性,容易在管道内壁形成湿度,从而加速腐蚀的产生。
在管道内壁涂层上添加特殊化学物质,能够形成防腐层,有效抵御腐蚀的发生。
管道内壁涂层还能够减少摩擦阻力,提高油气的流通效率。
对管道进行阴极保护也是一种常见的防腐措施。
阴极保护是指在管道表面加上一层具有电化学活性的物质,通过外加电流的方式,使得管道表面成为阴极,从而抑制腐蚀的产生。
阴极保护方法主要包括防腐电流和防腐阳极两种方式。
防腐电流是通过外加电流,使得管道表面形成一层保护膜,从而起到防腐的效果。
防腐阳极是在管道内部或外部安装阳极,使得阳极被腐蚀,而管道则不受腐蚀的侵害。
管道的材质选择也是一个重要的防腐措施。
在油气储运中,常见的管道材质有钢管、塑料管等。
钢管是一种常用的管道材质,但是由于其易于腐蚀,需要加强防腐措施。
塑料管则相对于钢管来说,具有较强的抗腐蚀性能,可以减少防腐工作的难度和成本。
定期进行管道的检测和维护也是一项重要的防腐措施。
定期检测可以发现管道中的腐蚀和损伤情况,及时采取措施进行修复和维护。
还可以通过对管道进行清洗和除锈等操作,保持管道的整洁和良好的工作状态。
油气储运中的管道防腐措施包括管道内壁涂层、阴极保护、材质选择和定期检测等方面,这些措施能够有效保护管道不受腐蚀的侵害,确保油气的安全储运。
科学合理的防腐措施也有助于延长管道的使用寿命,提高经济效益和社会效益。
海底油气管线现场节点内部防腐施工及质量控制要点

海底油气管线现场节点内部防腐施工及质量控制要点海底油气管线的防腐施工是保障管线运行安全的重要环节,也是管线的生命周期管理中的关键部分。
本文将从施工要点和质量控制两个方面详细介绍海底油气管线现场节点内部防腐施工。
2000字。
一、施工要点1. 施工前准备工作在进行海底油气管线节点内部防腐施工之前,必须进行充分的准备工作,包括制定详细的施工方案和操作规程,明确施工的任务和目标;进行现场勘察,了解节点内部的具体情况,确定施工所需的工艺和材料;安排专业技术人员进行施工前培训,确保施工人员具备相关的技能和知识。
2. 表面处理在进行节点内部防腐施工前,必须对待施工表面进行充分的准备工作,确保施工效果。
对待施工表面进行清洁处理,包括去除油污、锈蚀和杂物等;然后,对待施工表面进行打磨,提高其粗糙度,增加与涂料的附着力。
3. 防腐涂料的选择和涂装在海底油气管线节点内部防腐施工中,防腐涂料的选择非常关键。
要选择具有良好的耐腐蚀性能和附着力的防腐涂料;要根据节点内部的具体情况确定防腐涂料的种类和涂装方法。
在涂装过程中,要确保每一道涂料层的厚度均匀一致,避免涂料流挂和漏涂的情况。
4. 涂膜养护防腐涂膜施工完成后,必须进行养护工作,以保证其性能和寿命。
养护工作包括室温下涂装层干燥时间的控制,避免涂膜过早受水、受压和受污染;避免潮湿环境和高温环境对涂膜的影响;定期检查涂膜的质量和性能,及时进行修补和维护。
二、质量控制要点1. 施工质量检查在节点内部防腐施工过程中,应定期对施工质量进行检查和评估。
检查的重点包括防腐涂料的种类和规格是否符合要求,涂装层的厚度是否符合要求,涂膜的附着力和耐腐蚀性是否满足设计要求等。
对于发现的质量问题,要及时进行整改和修复,并记录相关的处理过程和结果。
2. 检测手段和方法为了保证海底油气管线节点内部防腐施工的质量可行性和有效性,需要采用一些专业的检测技术和方法。
常用的检测手段包括涂膜厚度测试、附着力测试、耐腐蚀性测试等。
海底管线管的防腐涂层处理

海底管线管的防腐涂层处理
来源:文章发表时间:2009-11-24
由于是在海底复杂的环境下使用,考虑到海水腐蚀、温度损失、浮力影响等多种因素制约,海底管线钢额外必须经过涂层、保温、配重、阴极保护等处理才可使用,
具体为:
1、防腐涂层
目前海洋管道的防腐层主要采用熔结环氧粉末(FBE)、双层熔结环氧粉末(双层FBE)、三层聚乙烯(3PE)、三层聚丙烯(3PP)以及高性能复合涂层(HPCC)。
其中最先进的是HPCC,由FBE层、粘结层和聚乙烯层组成,结构与常用的3PE相同,不同的是HPCC各层均采用静电粉末喷涂工艺涂敷,中间的粘结剂层是粘结剂和一定浓度FBE的混合物,外层是中密度的聚乙烯,该工艺使各涂层之间能紧密相连。
通过工厂施工的具有防腐功能的涂层系统涂敷后,HPCC涂层与管道表面的强力粘结,从而具有优良的剪切阻力特性,低温韧性,非常低的渗透性,优良的抗冲击性,
抗阴极剥离性。
应用环境-40-85℃。
2、保温层
目前常用的保温系统有聚乙烯复合保温体系、不发泡聚氨酯复合保温体系、钢套钢保温体系、单层管保温体系等4种保温技术。
施工时在涂层外增加一种保温材料,以防止所输送的油气因温度损失降低流动性
或凝固造成的输送困难。
3、配重层
是施工时在经过涂层和保温层处理后的管道外表面增加一道处理措施,以增加管道的重量,克服海水浮力并使其固定的安装位置上,通常以钢筋焊接笼或钢丝网固定
混凝土的方法加以实施。
4、阴极保护措施
指利用电解腐蚀理论,附加阳极金属块防止可能渗透到管道表面的海水对管道的
腐蚀。
海底油气管线现场节点内部防腐施工及质量控制要点

海底油气管线现场节点内部防腐施工及质量控制要点
海底油气管线是连接海上油气生产设施和陆地石油炼厂的重要通道,为确保管线的安
全运行,防腐施工及质量控制是非常重要的环节。
1. 防腐施工材料的选择:应选择耐腐蚀、耐高温、耐压的合适材料,并且需满足相
关国家标准和规范的要求。
2. 表面处理:在进行防腐施工前,需要对管线节点进行表面处理,以去除油脂、污
垢等杂质,确保施工效果。
3. 底漆施工:在表面处理后,需要进行底漆的施工。
底漆应使用符合要求的防腐底漆,涂刷均匀、稳定,覆盖工件表面。
4. 防腐涂层施工:底漆施工后,需进行防腐涂层的施工。
防腐涂层应符合相关规范
要求,涂刷均匀、无气泡,并达到预定的厚度。
5. 检查与修复:防腐涂层施工完成后,需要对施工质量进行检查,如发现涂层不均匀、有剥落等情况,需及时进行修复。
1. 管线节点检测:在进行节点防腐施工前,需要对管线节点进行检测,如管道连接口、管接头等,并记录下检测结果。
2. 施工计划与方案:施工前需制定详细的施工计划与方案,明确施工的步骤和要求,并制定相应的质量控制措施。
3. 施工人员培训:施工人员应接受相关的培训,熟悉施工要求和操作规程,并持有
相关的证书。
4. 施工现场管理:施工现场应进行划定,采取相应的安全措施,确保施工人员的安全,并严格控制施工材料的使用。
5. 施工质量检验:在施工过程中,需要进行质量检验,如涂层厚度检测、粘结强度
检测等。
检测结果需进行记录,以备后续的质量评估。
6. 管线节点验收:施工完成后,需要对管线节点进行验收,并进行相应的质量检测,确保施工质量符合相关要求。
用于海洋工程的防腐蚀管材型号

用于海洋工程的防腐蚀管材型号
海洋工程中广泛应用的防腐蚀管材型号有很多种。
下面我将介绍几种常见的防腐蚀管材型号及其特点。
1. HDPE管材
HDPE管材是一种高密度聚乙烯管材,具有优异的耐腐蚀性能。
它能够有效抵抗海水中的氯离子、硫化物等腐蚀介质,同时具有良好的耐磨性和抗冲击性。
HDPE管材重量轻、安装方便,广泛用于海洋工程中的给水、排水、输油、输气等管道系统。
2. FRP管材
FRP管材是一种由玻璃纤维增强塑料制成的管材,具有优异的耐腐蚀性和机械强度。
它能够抵抗海水中的酸碱、盐类等腐蚀介质,同时具有较长的使用寿命和较低的维护成本。
FRP管材适用于海洋工程中的污水处理、海水淡化、化学品输送等领域。
3. PPR管材
PPR管材是一种聚丙烯随机共聚物管材,具有良好的耐腐蚀性和热稳定性。
它能够抵抗海水中的氯离子、硫化物等腐蚀介质,同时具有优异的耐高温性能。
PPR管材广泛应用于海洋工程中的供暖、供冷、空调等系统。
4. 镀锌钢管
镀锌钢管是一种将碳素钢管表面镀上锌层的管材,具有良好的耐腐
蚀性和机械强度。
它能够抵抗海水中的氯离子、硫化物等腐蚀介质,同时具有较长的使用寿命。
镀锌钢管广泛应用于海洋工程中的供水、排水、输油、输气等系统。
以上是海洋工程中常见的几种防腐蚀管材型号。
它们在抵抗海水腐蚀、提供可靠的管道系统方面发挥着重要作用。
在选择管材时,需要根据具体情况考虑海水成分、工作环境、使用要求等因素,以确保管道系统的安全可靠运行。
海底油气管道腐蚀与防护技术现状

04
3
技术挑战
深海环境
压力:深海环境压力高,对管道材料和结构产生影响
温度:深海环境温度低,对管道材料和结构产生影响
腐蚀:深海环境腐蚀性强,对管道材料和结构产生影响
生物:深海环境生物种类繁多,对管道材料和结构产生影响
地形:深海环境地形复杂,对管道铺设和维护产生影响
02
方法:牺牲阳极法、外加电流法、强制电流法等
03
应用:广泛应用于海底油气管道、船舶、海洋工程等领域
04
优缺点:优点是防护效果好,缺点是成本较高,需要定期维护
外加电流保护
原理:利用外加电流,使金属表面形成致密氧化膜,防止腐蚀
01
优点:保护效果好,适用于各种金属材料
02
缺点:需要消耗大量能源,成本较高
演讲人
01.
02.
03.
04.
目录
腐蚀原因
防护技术
技术挑战
发展趋势
1
腐蚀原因
海水环境
海水中含有大量氯离子,对金属材料产生腐蚀
海水中含有微生物,对金属材料产生生物腐蚀
海水中含有氧气,对金属材料产生电化学腐蚀
海水中含有盐分,对金属材料产生渗透压腐蚀
微生物作用
B
D
A
C
微生物附着在管道表面,形成生物膜
智能防护技术:采用智能防护技术,提高防护效果和效率
地震:深海环境地震活动频繁,对管道安全产生影响
3
2
1
4
5
6
复杂地形
海底地形复杂多样,管道铺设困难
01
海底地质条件多变,管道稳定性受影响
02
海底环境恶劣,管道腐蚀加剧
- 1、下载文档前请自行甄别文档内容的完整性,平台不提供额外的编辑、内容补充、找答案等附加服务。
- 2、"仅部分预览"的文档,不可在线预览部分如存在完整性等问题,可反馈申请退款(可完整预览的文档不适用该条件!)。
- 3、如文档侵犯您的权益,请联系客服反馈,我们会尽快为您处理(人工客服工作时间:9:00-18:30)。
4 结
语
3 环氧粉末涂层的防护措施
当海底管道采用环氧粉末涂层并加混凝土配 重层时, 要注意防止混凝土层的滑移。由于环氧
迄今为止我国海底管道仍大量采用以煤沥青 涂层加混凝土配重层的作法。因此, 在今后的海底
管道防腐层选用方面, 应该大力推广新型防腐层。
作者简介: 朱一林, 工程师, 男, 现任中石化管道储运公司
了性能评价, 见表t o 从表 1 熔结环氧粉末涂层除与水泥粘 看出,
结性较差外, 其它各项性能均优于沥青类涂层 ( 煤焦油瓷漆) 。沥青类涂层的综合评分仅为 4 6 分, 而环氧粉末涂层可达到 8 分。上述评估已 3 得到国内外一些试验研究单位测试结果的证实。
第 2 卷第 4 8 期
朱一林等: 海底油气管道防腐层的选择
表 1 沥青类与熔结环氧粉末涂层性能评价
评估 内容
抗弯曲
抗 阴极剥离
与金属表面的粘结力 冲击强度
抗渗透性
修复与焊接性
耐磨性 水泥粘结性 土壤应力 阻燃性 抗候性 总计
评估权重 沥青类 加 』、 〕 内j 巧 12 4 ll ro  ̄ l0 10 6 6 4 4 3
1 0 0 4 6
环氧粉末
目前海底管道的一个发展趋势是 , 直径小于
在每根管子的 末端。 其优点是: ①只需要一小块面 积来阻止滑移, 并具有抗挠性; ②固化条件对剪切 强度影响较小; ③应用简单方便, 不需要特殊设备。 以上三种方法在国外管道上均有应用, 但粗
糙带较受欢迎。
陆地管道的 B F E涂层的厚度一般为 30 0-
对喷涂工艺做些改进。其缺点是螺纹尺寸难于控 制, 且附加环氧粉末涂层可能引起固化问题。 () 是将一层厚约25 m 2 屏蔽层 .4 m的玻璃 纤维增强的聚合物改性水泥直接喷徐到 F E涂 B 层上。这种混合物中的聚合物组分能与 F E涂 B 层牢固粘结, 并与混凝土层有较好的附着力。屏 蔽层还可以防止涂装混凝土层时( 无论是采用冲击 法, 或挤压结作业) FE涂层。但屏蔽层对涂 损伤 B 装工艺、 湿度、 固化等要求较为严格, 不易控制。 () 3 粗糙带 在 F E涂层上刷一层厚 04 B . m 、 10 m宽 0 m m的双组分液态环氧, 并手工在液 态环氧中加人筛 目在 4一 0 1m m的坚硬碎片, 用 标准参考板判断碎片的分布状况。粗糙带一般设
1 对海底油气管道涂层的要求
11 抗拉伸和抗弯曲 . 海底管道一般多采用铺管船铺设, 当涂装好 的钢管一节节焊起来 , 连接好, 并通过滑道和托架 下放到海底时, 管道会出现较大的弯曲和轴向应
力。通常是将这两项应力之和限定在钢材最低屈
服极限的8%以内, 5 相应的应变约为 02 .%。管 道在水下安装的深度越深, 这种应变也越大, 因 此, 涂层应具有较高的抗弯、 抗拉伸形变的能力, 同时要在受力的情况下, 保持与钢管的粘结力, 不 得产生断裂和剥离。
3 3 3
8 3
此外, 透水性和电绝缘强度对海底管道的阴 极保护具有非常重要的意义。国外一家公司曾对 沥青涂层和环氧粉末涂层进行过对比测试。试验 根据 AT G 管道涂层透水性试验方法进行, SM J 涂 层绝缘电阻值的增加使保护电流以2 一 0 0 3 倍的 量级减少, 在海底管道涂层应用方面必须重视。 18 年英国首先在北海成功地安装了3 91 条 熔结环氧粉末加混凝土配重的管道, 管径为72 6 m , m 9 0年代海底管道已广泛采用环氧粉末作防 腐层, 其管径范围从 5. 944 并研制了 08 1. m, - m 多种防滑移材料。1% 年墨西哥湾一条管径为 9 58 、 0 m 长为 27 m 4k m的天然气管道, 采用三层 P E涂层加混凝土配重层。配重层用冲击法直接施 加到经特殊处理的P E层上, 节省投资2 万美元。 0
编辑 : 黄 勇
朱一林, 航 尹
氢气形成, 随着海水深度的增加, 氢气泡内的压力 增大, 增大的泡压可能具有爆发性, 并形成较小的 气泡, 使其出现在界面上, 造成涂层承受较大的剥 离力。因此, 海底管道应选用抗阴极剥离的涂层。
14 良好的粘附性 . 涂层必须与钢管表面有 良好的粘结力, 以抵 抗管道安装时承受的牵引力 ( 底拖法安装) 。牵 引力可从混凝土外套通过涂层传递到管道本身, 使管道移动就位, 因此要求涂层有足够的粘结剪 切强度。除此之外, 涂层与加重混凝土层之间, 必须要有足够的粘结阻力, 以防止混凝土在安装 或运行时滑移。 除以上几点外, 海底管道防腐层还要求耐冲 击、 耐细菌和海生物、 电阻抗及耐温等。
1 8 1 4 1 0 s
引起的涂层损坏。防止环氧粉末与混凝土涂层之 间的滑移有以下三种方法: () 1环氧螺纹 这是最简单、 最便宜的一种
98 52源自方法, FE 环氧粉末层) 即在 B 层( 上喷一个大约高 05 、 . m 、 . m 宽50 螺距23 m m 0m m的连续螺纹, 并
2 海底油气管道涂层的选择
过去的3 海底管道多采用煤焦油瓷漆作 年, 0
防腐层, 现在这种状况已发生了变化。一些新的 防腐性能更好的涂层, 如熔结环氧粉末、 挤出聚乙 烯不仅在陆地管线上被广泛应用, 而且也在海底 管线得到大力推广。 0 2 世纪 9 年代新制定的海 0 洋工程计划, 对沥青类涂层与环氧粉末涂层做出
料的粘径尺寸和喷涂速度, 以减少对 FE涂层的 B
损坏, 如果生产和业主允许 , 以采用混凝土挤压法
涂装为宜。
铺设的3 条气管线, 35 , 1 k , 直径 2 m 长度 6 就 m m 采用了加大壁厚的作法。对于这种不加混凝土配
重的钢管可以采用三层聚乙烯涂层, 这种涂层已 在中国渤海水域得到广泛采用。
鲁宁输油处安全科长, 长期从事安全管理工作, 电话) (
0 3 5 7 19 5 7一 2 3 0 0
粉末涂层很硬, 且表面光滑, 与传统的煤焦油瓷漆 相比较, 其与混凝土层粘结能力差。此外, 环氧粉 末层厚度较薄, 在涂装混凝土层时, 要防止因冲击
收稿 日 : 0 - 4 0 期 2 5 0 -6 0
焊管 ・ 2 卷第 4 ・05 7 第 8 期 20 年 月
海底油气管道防腐层的选择
( 邹城 230) 中石化管道储运公司 鲁宁输油处,山东 750
摘 要: 针对海底油气管道防腐层的特殊要求, 结合国内外海底油气管道防腐层使用情况, 提 出了海底油气管道防腐层的选择技术条件; 并介绍了新型环氧粉末防腐涂层的几种防护措施。 关键词:海底;油气管道;防腐层;选择 中图分类号: G7. 文献标识码 :B 文章编号:1 1 3 ( 0) - 02 T1 4 46 0 -98 5 0 03 -2 0 3 2 0 4 0 海底油气管道与陆地管道的防腐层要求既有 相通, 又有不同, 其不同在于海底管道的施工作业 及运行环境条件不同。因此, 针对海底油气管道 的特点, 应对其防腐层进行很好地选择。
40 , 0 } 而海底管道的 FE涂层的厚度应采用 L m B 60 , 4 R 以防止涂装混凝土涂层引起的损坏。如 , m
果混凝土采用冲击法涂装, 应尽量优选混凝土骨
58 0m m的管道采用增大管壁厚度而不加混凝土 配重层。这主要是由于小直径管受到的浮力较 小, 负浮力易于控制。1 年前在加里福尼亚海岸 0
12 抗水渗透 . 海底管道涂层的老化变质主要由潮湿渗透引 起, 渗透包括电位梯度下的电渗透、 毛细现象引起 的扩散和渗透。渗透主要是由于涂层内部的可溶 性物质和管道表面处理后沉积在基底表面上的可 溶性盐引起。海水作为溶剂, 可通过涂层渗人溶 解。沥青类软层在水渗透的情况下, 会导致体积 膨胀, 其结果是涂层与基面剥离或分层。海水深 度增加, 剥离的压力也会增大。因此, 海底管道应 避免使用对潮湿和水渗透敏感的涂层。 13 抗阴极剥离 . 在管道附加阴极保护时, 涂层与钢管界面有