汽车产品设计开发流程的术语
汽车开发流程及术语

25
GVDP
Operations
26
ICD
Interface Control Document
27
IDR
Initial Data Release
Information Manager (data management
28
iMAN
system)
29
Init.
Initial (powertrain mule calibration)
40
MRD
Material Required Date
41
MVB
Manufacturing Validation Build
42
MVNS
Manufacturing Validation Non-Salable
43
MVS
Manufacturing Validation Salable
44
N/A
Not Applicable
65
PPM
Program Purchasing Manager
66
PQRR
Program Quality Readiness Review
67
PR
Performance Review
68
Prod
Readiness for Production/Acceleration
69
PSS
Program Status System
5
AVLE
Assistant Vehicle Line Executive
6
BOM
Bill of Material
7
BOP
Bill of Process
汽车研发常用专业术语详细汇总与解释!

汽车研发常⽤专业术语详细汇总与解释!汽车研发过程中,有⼤量的专业术语,每个术语都有其特殊的含义,且不同的主机⼚还有不同的叫法!今天漫谈君全⾯总结了⼀版汽车研发常⽤专业术语和⼤家⼀起交流学习⼀、研发阶段1、商品计划阶段1)完成项⽬前期研究,管理层评审预研阶段定义的所有初期⽬标、评审并批准市场分析、技术⽅案、造型⽅向、资源获得⽅案、项⽬综合可⾏性分析、正式启动项⽬。
2)批准初步项⽬⽅案,包括所有的产品⽬标和商业计划⽬标的最初符合性,⼯程/制造/物流/采购等项⽬⽅案。
为项⽬批准做准备。
3)综合评审产品开发状态,包括造型冻结,对产品、制造、物流和销售计划进⾏评审和批准,所有的⽬标在项⽬的经济架构中都必须是可⾏的,正式批准项⽬。
2、产品开发阶段1)通过对数模的⼯程可⾏性确认和pertest试验,通过CAE和制造可⾏性分析,完成整车数据发放。
2)对设计样车进⾏相关验证试验,检查评估产品设计及⼯艺的正确性。
完成试⽣产准备。
3、量产准备阶段1)使⽤⼯装零件按⼯艺要求在总装线上制造样车,验证⼯装模具和供应商的制造能⼒,完成⼯程的最终验证和制造的早期⼯艺调试。
2)调试整车⼚的⽣产设备,验证⽣产⼯艺,验证全⼯装和⼯艺条下件批量提供的零部件质量,完成样车数据更改,冻结变更数据。
3)验证整车⼚在⼀定节拍下的⽣产能⼒。
4)按整车⽣产节拍的提升计划,投⼊批量⽣产。
4、量产维持阶段1)新产品预研⽴项GATE#0(KO)项⽬⽴项研究。
成⽴项⽬团队,开始对项⽬进⾏研究分析。
2)预可研评审(SI)完成产品初步可⾏性分析后,通过预可研评审确定开发平台。
3)产品开发决策(SC)进⼀步细化产品⽅案,通过评审后,初步确定项⽬开发⽬标。
4)新产品开发项⽬认可GATE#1(OD)完成各项性能指标的细化,形成产品的最终设计⽅案和⽬标并获得批准。
5)设计数据发布(DR)⾸轮设计数据经过评审确认后,进⾏发布⽤于相关部门的设计样车制作。
6)设计样车验证完成(CP)对设计样车进⾏相关试验验证,检查及评审产品设计和⼯艺的正确性。
汽车行业常见术语汇总

MSA:Measurement System Analysis 测量系统分析
测量系统:借用某种工具(量具、检具、设备、软件等)通过某种方法对 特定半成品或成品赋值的全过程。
测量系统分析:使用数理统计和图表的方法对测量系统进行分析,以评估 测量系统的分辨率和误差对于被测量的参数来说是否合适,并确定测量系 统误差的主要成分。
CP:Control Plan 控制计划
定义:控制计划是对控制产品所要求的系统和过程的文件化的描述。 通俗来讲就是对一个产品从进料到发货的全过程的特性进行定性定量的 规定,以确保成品或服务的质量稳定。 分类:样件控制计划、试生产控制计划、生产控制计划
示例
BOM:Bill of Material 物料清单
Repeatability重复性
G R&R
误差
Producibility再现性
偏倚
1.Bias偏倚;2.Linearity线性;3.Stability稳定性
常见输出:计量型、计数型2种报告 常用软件:MiniTab
测量系统类型 基本计量型
MSA方法 级差,均值和极差,方差分析(ANOVA),偏倚,线性,控制图
PPAP文件包含:
1.PSW;2.BOM;3.检测报告(4种类型);4.产品特殊特性清单;5.Process flow diagram过程 流程图;6.PFMEA-过程潜在失效模式及后果分析;7.工艺设备调查表;8.工装模具一览表;9. 检验设备一览表;10.MSA测量系统分析;11.Cpk & Ppk-初始过程能力研究;12.Control plan生 产控制计划;13.包装认可报告;14.其他客户特殊要求的,IMDS、包装指导书,产能分析表、 具有资格的实验室文件(可以由实验室人员上岗资格证书代替)等。
汽车开发流程术语

汽车开发流程术语一、概述汽车开发流程是指从汽车概念设计到量产交付的全过程,涵盖了从需求分析、设计开发、验证测试到生产制造等多个环节。
本文将介绍汽车开发流程中常用的术语和相关内容。
二、需求分析阶段1. 市场调研:通过对潜在用户群体的需求、市场趋势和竞争对手的产品进行研究,以确定目标市场和产品定位。
2. 用户需求分析:通过与用户进行沟通和调研,了解用户对汽车的功能、性能、安全等方面的需求,以制定产品开发的目标和要求。
3. 功能规划:根据用户需求和市场调研结果,制定汽车的功能规划,明确车型的配置、选装项目和标配功能等。
三、设计开发阶段4. 概念设计:基于用户需求和市场调研结果,进行创新性的设计,形成初始的产品概念,并进行初步评估和论证。
5. 详细设计:在概念设计的基础上,进行细化设计,包括外观设计、结构设计、动力系统设计、电子系统设计等。
6. 集成设计:将各个子系统的设计进行整合,确保其相互协调和兼容,以满足整车的功能和性能要求。
7. 验证测试计划:制定验证测试的目标、方法和流程,明确测试项目和测试标准,以验证汽车的各项性能指标。
8. 试制样车制造:根据设计要求和生产工艺,制造少量试制样车,用于验证测试和产品改进。
四、验证测试阶段9. 功能性测试:对汽车的各项功能进行测试,包括动力性能、悬挂系统、制动系统、转向系统等。
10. 安全性测试:测试汽车在碰撞、侧翻、刹车距离等各方面的安全性能,确保车辆在各种情况下的安全性。
11. 可靠性测试:通过长时间的耐久性测试,评估汽车的可靠性和使用寿命,以确保产品的质量和可靠性。
12. 环保性测试:测试汽车的排放性能和燃油经济性,以满足环保法规和用户对节能环保的需求。
五、生产制造阶段13. 生产计划:根据市场需求和销售预测,制定生产计划,包括产量、交付时间、零部件供应等。
14. 零部件采购:根据生产计划和供应商能力,进行零部件的采购和供应链管理,确保生产的顺利进行。
15. 生产调试:将各个零部件组装成整车,并进行功能调试和性能测试,确保整车的质量和功能正常。
汽车设计专业术语

1) PP Produc tionProveo ut 生产验证2) TTO Tool Try-Out 工装设备试运行3) (J1) Job 1 整车投产4) DFMEADesign Failur e Mode Effect s Analys is 故障模式影响分析设计5) DVP Design Verifi catio n Plan 设计验证计划6) DVP&R Design Verifi catio n Plan & Report设计验证计划和结果7) FMEA Failur e Mode Effect s Analys is 故障模式影响分析8) FPDS Ford Produc t Develo pment System福特产品开发系统9) GYR Green-Yellow-Red 绿-黄-红10) MRD Materi al Requir ed Date 物料要求到厂日11) OTT OK-TO-TOOL 可以开模12) TKO Toolin g-Kick-Off 工装启动13) OEM origin al Equipm ent Manufa cture r 设备最初制造厂14) FtF/F2F Face To Face 面对面会议15) PV Produc tionValida tion产品验证16) OTS Off-Toolin g-Sample完全工装样件17) QOS Qualit y Operat ing System质量运作体系18) TS-16949Techni cal Specif icati on – 16949技术规范-1694919) APQP Advanc ed Produc t Qualit y Planni ng 先期产品质量计划20) IPD In PlantDate 进厂日21) PPM Partsper Millio n (applie d to defect ive Suppli er parts)零件的百万分比率(适用于供应商不合格零件)22) PPAP Produc tionPart Approv al Proces s 生产件批准程序23) Pre-PV Pre -Produc tionValida tion产品预先验证24) 1PP- FirstPhaseof Produc tionProve-Out 第一次试生产25) 3C Custom er(顾客导向)、Compet ition(竞争导向)、Compet ence(专长导向)26) 4S Sale, Sparep art零配件, Servic e, Survey信息反馈27) 5S 整理,整顿,清理,清洁,素养28) 8D- 8 Discip line29) ABS Anti-lock Brakin g System30) AIAG 美国汽车联合会31) ANPQPAllian ce New Produc t Qualit y Proced ure32) Apport ionme nt 分配33) APQP Advanc ed Produc t Qualit y Plan34) Backli te Windsh ield后窗玻璃35) Benchm ark Data 样件资料36) bloods hot adj.充血的, 有血丝的37) BMW Bavari an MotorWorks38) C.P.M Certif ied Purcha singmanger认证采购经理人制度39) CB- Confir matio n Build确认样车制造40) CC- Change CutOff设计变更冻结41) CC\SC- critic al/signif icant charac teris tic42) CCR Concer n & Counte rmeas ure Reques t43) CCT CrossCompan y Team44) Charac teris ticsMatrix特性矩阵图45) COD Cash on Delive ry 货到付现预付货款(T/T in advanc e)46) CP1- Confir matio n Protot ype 1st 第一次确认样车47) CP2- Confir matio n Protot ype 2nd 第二次确认样车48) Cpk 过程能力指数Cpk=Zmin/349) CPO Comple menta ry Partsorder50) Crafts mansh ip 精致工艺51) Cross-functi onalteams跨功能小组52) CUV Car-BasedUltili ty Vehicl e53) D1:信息收集;8D54) D2:建立8D小组;55) D3:制定临时的围堵行动措施,避免不良品流出;56) D4:定义和证实根本原因,避免再发;57) D5:根据基本原因制定永久措施;58) D6:执行和确认永久措施;59) D7:预防再发,实施永久措施;60) D8:认可团队和个人的贡献。
tampa 大众开发流程术语

tampa 大众开发流程术语Tampa 大众开发流程术语引言:在Tampa大众开发流程中,有许多术语被广泛使用。
这些术语有助于开发团队之间的沟通和协作,确保项目按计划顺利进行。
在本文中,我们将介绍一些常见的Tampa大众开发流程术语,以帮助您更好地理解和应用这些概念。
一、需求分析和规划阶段:1. 用户故事(User Stories):用户故事是描述系统功能或需求的简短描述。
它们通常由用户或利益相关者提出,用于明确开发团队需要实现的功能和期望的结果。
2. 产品路线图(Product Roadmap):产品路线图是一种高层次的计划,用于指导产品的发展方向。
它描述了产品的愿景、主要功能和计划的发布时间表,帮助团队了解项目的整体目标和优先级。
3. 需求调研(Requirement Elicitation):需求调研是通过与利益相关者交流、访谈和调查等方式,收集和明确项目需求的过程。
它有助于团队了解用户的期望和需求,并为后续开发工作提供指导。
二、设计和开发阶段:1. 原型(Prototype):原型是一种用于展示系统功能和界面的模型。
它可以是简单的草图或交互式的模拟,用于验证设计和收集反馈,以便在开发之前进行修改和改进。
2. 数据库模型(Database Model):数据库模型是描述系统数据结构和关系的图表或文档。
它定义了数据表、字段和关联关系,为开发人员提供了设计数据库的指导。
3. 代码审查(Code Review):代码审查是一种团队成员之间相互检查和评估代码质量的过程。
它有助于发现潜在的问题和错误,并提供改进建议,以确保代码的可读性、可维护性和安全性。
4. 单元测试(Unit Testing):单元测试是对软件系统中最小可测试单元(如函数或方法)进行测试的过程。
它旨在验证每个单元的功能和正确性,以提高代码质量和可靠性。
三、测试和部署阶段:1. 集成测试(Integration Testing):集成测试是对系统不同组件之间的集成进行测试的过程。
汽车研发与制造专业术语汇总(中英文对照)

PP Production Proveout 生产验证TTO Tool Try-Out 工装设备试运行(J1) Job 1 整车投产DFMEA Design Failure Mode Effects Analysis 故障模式影响分析设计DVP Design Verification Plan 设计验证计划DVP&R Design Verification Plan & Report 设计验证计划和结果FMEA Failure Mode Effects Analysis 故障模式影响分析FPDS Ford Product Development System 福特产品开发系统GYR Green-Yellow-Red 绿-黄-红MRD Material Required Date 物料要求到厂日OTT OK-TO-TOOL 可以开模TKO Tooling-Kick-Off 工装启动OEM original Equipment Manufacturer 设备最初制造厂FtF/F2F Face To Face 面对面会议PV Production Validation 产品验证OTS Off-Tooling-Sample 完全工装样件QOS Quality Operating System 质量运作体系TS-16949 Technical Specification –16949 技术规范-16949APQP Advanced Product Quality Planning 先期产品质量计划IPD In Plant Date 进厂日PPM Parts per Million (applied to defective Supplier parts) 零件的百万分比率(适用于供应商不合格零件)PPAP Production Part Approval Process 生产件批准程序Pre-PV Pre -Production Validation 产品预先验证1PP- First Phase of Production Prove-Out 第一次试生产3C Customer(顾客导向)、Competition(竞争导向)、Competence(专长导向)4S Sale, Sparepart零配件, Service, Survey信息反馈5S 整理,整顿,清理,清洁,素养8D- 8 DisciplineABS Anti-lock Braking SystemAIAG 美国汽车联合会ANPQP Alliance New Product Quality ProcedureApportionment 分配APQP Advanced Product Quality PlanBacklite Windshield 后窗玻璃Benchmark Data 样件资料bloodshot adj.充血的, 有血丝的BMW Bavarian Motor WorksC.P.M Certified Purchasing manger 认证采购经理人制度CB- Confirmation Build 确认样车制造CC- Change CutOff 设计变更冻结CC\SC- critical/significant characteristicCCR Concern & Countermeasure RequestCCT Cross Company TeamCharacteristics Matrix 特性矩阵图COD Cash on Delivery 货到付现预付货款(T/T in advance) CP1- Confirmation Prototype 1st 第一次确认样车CP2- Confirmation Prototype 2nd 第二次确认样车Cpk 过程能力指数Cpk=Zmin/3CPO Complementary Parts orderCraftsmanship 精致工艺Cross-functional teams 跨功能小组CUV Car-Based Ultility VehicleD1:信息收集;8DD2:建立8D小组;D3:制定临时的围堵行动措施,避免不良品流出;D4:定义和证实根本原因,避免再发;D5:根据基本原因制定永久措施;D6:执行和确认永久措施;D7:预防再发,实施永久措施;D8:认可团队和个人的贡献。
汽车专业术语 (2)
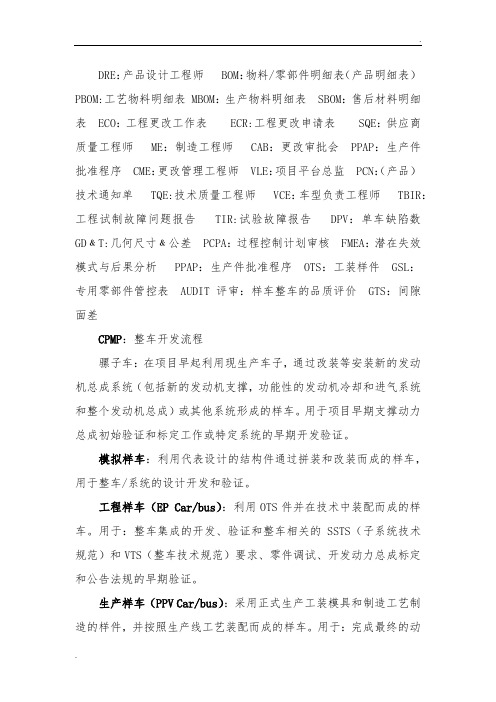
DRE:产品设计工程师 BOM:物料/零部件明细表(产品明细表)PBOM:工艺物料明细表 MBOM:生产物料明细表 SBOM:售后材料明细表 ECO:工程更改工作表 ECR:工程更改申请表 SQE:供应商质量工程师 ME:制造工程师 CAB:更改审批会 PPAP:生产件批准程序 CME:更改管理工程师 VLE:项目平台总监 PCN:(产品)技术通知单 TQE:技术质量工程师 VCE:车型负责工程师 TBIR:工程试制故障问题报告 TIR:试验故障报告 DPV:单车缺陷数GD﹠T:几何尺寸﹠公差 PCPA:过程控制计划审核 FMEA:潜在失效模式与后果分析 PPAP:生产件批准程序 OTS:工装样件 GSL:专用零部件管控表 AUDIT评审:样车整车的品质评价 GTS:间隙面差CPMP:整车开发流程骡子车:在项目早起利用现生产车子,通过改装等安装新的发动机总成系统(包括新的发动机支撑,功能性的发动机冷却和进气系统和整个发动机总成)或其他系统形成的样车。
用于项目早期支撑动力总成初始验证和标定工作或特定系统的早期开发验证。
模拟样车:利用代表设计的结构件通过拼装和改装而成的样车,用于整车/系统的设计开发和验证。
工程样车(EP Car/bus):利用OTS件并在技术中装配而成的样车。
用于:整车集成的开发、验证和整车相关的SSTS(子系统技术规范)和VTS(整车技术规范)要求、零件调试、开发动力总成标定和公告法规的早期验证。
生产样车(PPV Car/bus):采用正式生产工装模具和制造工艺制造的样件,并按照生产线工艺装配而成的样车。
用于:完成最终的动力总成、底盘、空调系统的标定;最终的VTS验证(整车技术标准)和整认证试验,用于装配线人员培训;开始生产线的早期工艺验证和产品的最终验证,确保产品的可制造性,符合业务部门对后续过程的产品上市计划所必须的零件可使用性和质量要求。
预试生产PP:在试生产(P)前,完成产品或过程的最终验证和认可,使用工装零件按照工艺要求在生产线上装配产品的生产活动。
有关IATF16949质量管理体系中汽车行业术语大全

有关IATF16949质量管理体系中汽车行业术语大全1、Accessory Part 配件在交付给最终顾客之前(或之后),与车辆或动力总成以机械或电子方式相连的顾客指定的附加部件(例如:定制的地毯、车箱衬垫、轮罩、音响系统加强件、天窗、尾翼、增压器等)。
2、Advanced Product Quality Planning(APQP)产品质量先期策划对开发某一满足顾客要求的产品或服务提供支持的产品质量策划过程。
APQP 对开发过程具有指导意义,并且是组织与其顾客之间共享结果的标准方式。
APQP 涵盖的项目包括:设计稳健性设计试验和规范符合性生产过程设计质量检验标准过程能力生产能力产品包装产品试验操作员培训计划3、Aftermarket Part 售后市场零件并非由OEM 为服务件应用而采购或放行的替换零件,可能按照或不按照原始设备规范进行生产。
4、Authorization 授权对某(些)人的形成文件的许可,规定了其在组织内部授予或拒绝权限或制裁有关的权利和责任。
5、Challenge(master)Part 挑战(标准)件具有己知规范、经校准并且可追溯到标准的零件,其预期结果(通过或不通过)用于确认防错设备或检具(如通止规)的功能性。
6、Control Plan 控制计划对控制产品所要求的系统和过程的形成文件的描述。
7、Customer Requirements 顾客要求顾客规定的所有要求(例如:技术、商业、产品和制造过程的相关要求、一般条款和条件、客户特殊要求等)。
8、Customer-Specific Requirements(CSRs)顾客特殊要求对本汽车行业质量管理体系标准特定条款的解释或补充要求。
9、Design for Assembly(DFA)可装配性设计出于易于装配的考虑设计产品的过程。
(例如,如果产品包含较少的零件,产品的装配时间则较短,从而降低装配成本)。
10、Design for Manufacturing(DFM)可制造性设计产品设计和过程设计的结合,用于设计可简单且经济地制造的产品。
APQP术语
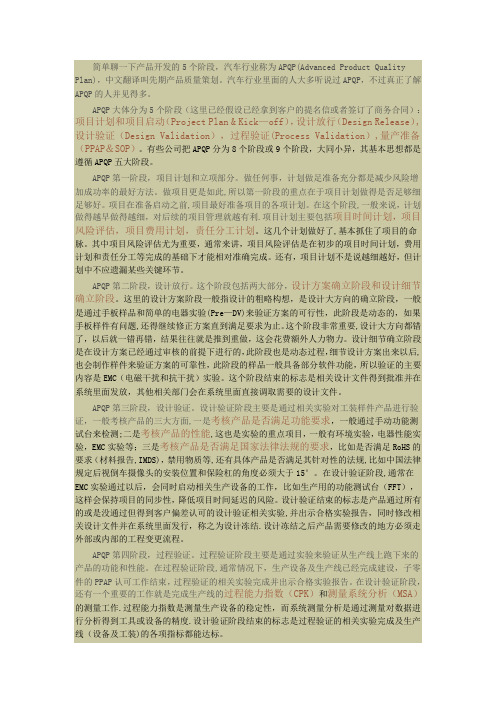
简单聊一下产品开发的5个阶段,汽车行业称为APQP(Advanced Product Quality Plan),中文翻译叫先期产品质量策划。
汽车行业里面的人大多听说过APQP,不过真正了解APQP的人并见得多。
APQP大体分为5个阶段(这里已经假设已经拿到客户的提名信或者签订了商务合同):项目计划和项目启动(Project Plan & Kick—off),设计放行(Design Release),设计验证(Design Validation),过程验证(Process Validation),量产准备(PPAP&SOP)。
有些公司把APQP分为8个阶段或9个阶段,大同小异,其基本思想都是遵循APQP五大阶段。
APQP第一阶段,项目计划和立项部分。
做任何事,计划做足准备充分都是减少风险增加成功率的最好方法。
做项目更是如此,所以第一阶段的重点在于项目计划做得是否足够细足够好。
项目在准备启动之前,项目最好准备项目的各项计划。
在这个阶段,一般来说,计划做得越早做得越细,对后续的项目管理就越有利.项目计划主要包括项目时间计划,项目风险评估,项目费用计划,责任分工计划。
这几个计划做好了,基本抓住了项目的命脉。
其中项目风险评估尤为重要,通常来讲,项目风险评估是在初步的项目时间计划,费用计划和责任分工等完成的基础下才能相对准确完成。
还有,项目计划不是说越细越好,但计划中不应遗漏某些关键环节。
APQP第二阶段,设计放行。
这个阶段包括两大部分,设计方案确立阶段和设计细节确立阶段。
这里的设计方案阶段一般指设计的粗略构想,是设计大方向的确立阶段,一般是通过手板样品和简单的电器实验(Pre—DV)来验证方案的可行性,此阶段是动态的,如果手板样件有问题,还得继续修正方案直到满足要求为止。
这个阶段非常重要,设计大方向都错了,以后就一错再错,结果往往就是推到重做,这会花费额外人力物力。
设计细节确立阶段是在设计方案已经通过审核的前提下进行的,此阶段也是动态过程,细节设计方案出来以后,也会制作样件来验证方案的可靠性,此阶段的样品一般具备部分软件功能,所以验证的主要内容是EMC(电磁干扰和抗干扰)实验。
bmw汽车零部件开发流程术语

bmw汽车零部件开发流程术语
BMW汽车零部件的开发流程涉及许多术语和步骤,让我们来详
细了解一下。
1. 概念阶段,在这个阶段,团队会进行市场调研和需求分析,
以确定新零部件的设计方向和目标市场。
这可能涉及到概念验证和
初步设计。
2. 设计阶段,在这个阶段,工程师和设计师将进行详细的设计
工作,包括CAD建模、工程分析、原型制作等。
涉及的术语可能包
括CAD(计算机辅助设计)、CAE(计算机辅助工程)、原型验证等。
3. 测试阶段,新零部件需要经过严格的测试,包括性能测试、
可靠性测试、安全测试等。
术语可能包括DVP(设计验证计划)、FMEA(故障模式和影响分析)、试验验证等。
4. 供应商选择和采购,BMW汽车通常会与供应商合作生产零部件,因此在这个阶段涉及到供应商选择、谈判和采购合同签订等流程。
5. 生产阶段,一旦零部件设计完成并且供应链准备就绪,就会
进入生产阶段。
这可能涉及到工艺优化、生产设备采购、质量控制
等术语。
6. 质量控制,在整个开发流程中,质量控制是至关重要的一环,包括SPC(统计过程控制)、PPAP(生产零部件批准程序)等术语。
7. 上市和售后服务,最后,新零部件将面临上市和售后服务阶段,这可能涉及到市场推广、技术支持、保修政策等。
以上是BMW汽车零部件开发流程中可能涉及的一些术语和步骤,涵盖了从概念到生产的整个过程。
希望这些信息能够帮助你更全面
地了解这一过程。
APQP产品开发流程与管理(汽车行业)你懂得!

实施FMEA的意义 的意义 实施
国内
• 一汽、二汽、上汽、北汽福 一汽、二汽、上汽、 田等公司在积极探寻FMEA 田等公司在积极探寻FMEA 的实施策略和实施办法, 的实施策略和实施办法,并 且开始了初步的实施; 且开始了初步的实施; • 国外汽车公司的国内配件厂 被要求实施FMEA。 被要求实施FMEA。
调试
产品设计阶段 Detail Design
工艺同步工程 进入二维设计的同时 进入二维设计的同时,汽车制造的四大工艺设计 二维设计的同时, 就得介入, 三维设计油泥模型评审后 评审后, 就得介入, 三维设计油泥模型评审后, 四大工艺设 计也应有相应的方案。 计也应有相应的方案。 工艺可行性分析 工装准备阶段 四大工艺( 总装) 四大工艺(冲压成形 涂装 焊装 总装)
产品设计阶段 Detail Design
工艺同步工程 PSE(Process Simultaneous Engineering)
车身结构 校核、 校核、分析 同步工程 介入 内、外饰模 型数据採集
软模开发
试制焊装 试制 设备 检具、 检具、夹具
公装模开发
SOP
样车组装 试制 工程开发 开发 检具、 检具、夹具 开发焊装 设备
产品设计阶段 Detail Design
在发动机上的应用: 在发动机上的应用: 1.电子控制喷油装置 . 2.电子点火装置(ESA) .电子点火装置( ) 电子技术在底盘上的应用: 电子技术在底盘上的应用: 1. 电控自动变速器(ECAT) 电控自动变速器( ) 2. 防抱死制动系统(ABS) . 防抱死制动系统( ) 3.电子转向助力系统 . 4.适时调节的自适应悬挂系统 . 5.常速巡行自动控制系统(CCS) .常速巡行自动控制系统( ) 6 . 倒车雷达
tampa 大众开发流程术语
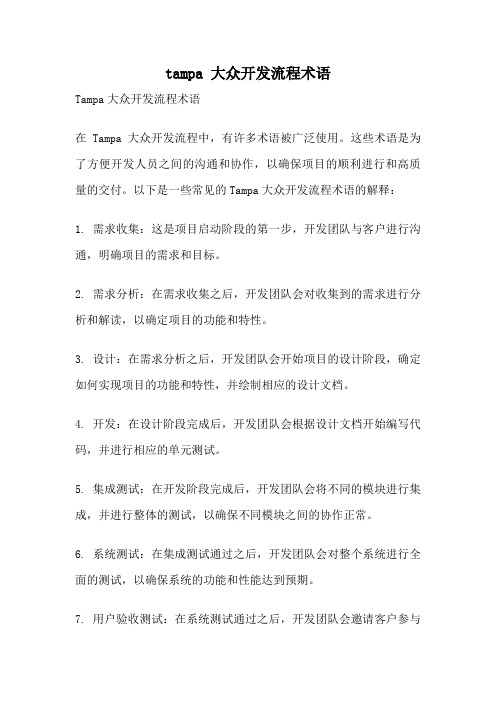
tampa 大众开发流程术语Tampa大众开发流程术语在Tampa大众开发流程中,有许多术语被广泛使用。
这些术语是为了方便开发人员之间的沟通和协作,以确保项目的顺利进行和高质量的交付。
以下是一些常见的Tampa大众开发流程术语的解释:1. 需求收集:这是项目启动阶段的第一步,开发团队与客户进行沟通,明确项目的需求和目标。
2. 需求分析:在需求收集之后,开发团队会对收集到的需求进行分析和解读,以确定项目的功能和特性。
3. 设计:在需求分析之后,开发团队会开始项目的设计阶段,确定如何实现项目的功能和特性,并绘制相应的设计文档。
4. 开发:在设计阶段完成后,开发团队会根据设计文档开始编写代码,并进行相应的单元测试。
5. 集成测试:在开发阶段完成后,开发团队会将不同的模块进行集成,并进行整体的测试,以确保不同模块之间的协作正常。
6. 系统测试:在集成测试通过之后,开发团队会对整个系统进行全面的测试,以确保系统的功能和性能达到预期。
7. 用户验收测试:在系统测试通过之后,开发团队会邀请客户参与用户验收测试,以确保系统满足客户的需求和期望。
8. 部署:在用户验收测试通过之后,开发团队会将系统部署到生产环境中,以供客户正式使用。
9. 维护:在系统部署之后,开发团队会继续对系统进行维护和修复,以确保系统的稳定性和可靠性。
10. 反馈和改进:在系统维护阶段,开发团队会收集用户的反馈和建议,并进行相应的改进和优化。
11. 项目管理:在整个开发过程中,项目经理会负责项目的计划、组织和控制,以确保项目按时、高质量地完成。
12. 代码审查:在开发过程中,开发团队会进行代码审查,以确保代码的质量和规范,减少潜在的bug。
13. 风险管理:在项目开发过程中,项目团队会识别和评估项目的潜在风险,并采取相应的措施进行管理和控制。
14. 迭代开发:Tampa大众开发流程中通常采用迭代开发的方式,将整个开发过程划分为多个迭代,每个迭代都有明确的目标和交付物。
汽车行业项目阶段术语

汽车行业项目阶段术语在汽车行业项目管理中,不同的阶段通常有特定的术语来描述。
以下是一些常见的项目阶段和相关术语:1. 概念阶段(Concept Phase):在这个阶段,主要是确定产品的初步设计概念、市场定位、功能需求以及初步的成本评估等。
2. 预研阶段(Preliminary Research Stage/Phase):进行市场需求分析、竞品研究、技术可行性研究和技术路线规划。
3. 产品定义阶段(Product Definition Phase):完成详细的产品设计参数设定、整车架构设计、关键零部件选择及初步的工程设计。
4. 工程开发阶段(Engineering Development Phase):包括设计冻结(Design Freeze)、样车制造(Prototype Build)、验证测试(Validation Testing),如耐久性测试、NVH测试、性能测试等。
5. 试生产阶段(Trial Production/PPAP Phase):1)生产件批准程序(Production Part Approval Process, PPAP),此阶段需要制作试制产品,并提交给客户或主机厂进行批准。
2)两轮试验车(Two Trial Production, 2TP),指的是试生产过程中的第二次小批量生产以进一步验证工艺和产品质量。
6. OTS(Off Tool Sample):工装样件阶段,即按照最终生产工艺流程生产的首批样品,用于验证工装设备的精度和生产能力。
7. SOP(Start of Production):开始量产阶段,意味着生产线上的所有准备工作已完成,可以开始正式的大规模生产。
8. 持续改进阶段(Continuous Improvement Phase):在量产之后,通过对生产和用户反馈的数据分析,不断优化产品和生产流程。
每个阶段都有明确的目标和交付物,并且会通过一系列的质量控制工具和技术评审来确保项目的顺利推进,例如使用先期产品质量策划(Advanced Product Quality Planning, APQP)和潜在失效模式与后果分析(Failure Mode and Effects Analysis, FMEA)等方法。
汽车产品设计开发流程的术语

汽车产品设计开发流程的术语1. 概念设计 (Concept Design)概念设计是汽车产品设计开发流程的起点,它包括通过市场调研和用户需求分析来确定产品的目标群体和定位。
概念设计阶段的主要目标是确定产品的整体外观和风格,以及初步确定产品的功能和特点。
2. 草图设计 (Sketch Design)在概念设计完成后,设计师将开始进行草图设计。
这一阶段是通过手绘或计算机辅助设计软件来创建车辆的初步外观设计。
设计师会进行多次修改和优化,直到获得满意的设计概念。
3. 三维建模 (3D Modelling)在草图设计完成后,设计师将使用三维建模软件将设计概念转化为真实的三维模型。
这个阶段的设计师需要考虑产品的内部结构和比例,并与工程师合作以确保设计的可行性和制造性。
4. 造型设计 (Clay Modelling)造型设计是将三维模型转化为物理模型的过程。
设计师将使用黏土和其他材料,在一个模型车间里手工塑造出车身外形的模型。
这个过程充分展示了设计师的艺术家的手法,因为它要求工匠级别的技巧和经验。
5. 工程设计 (Engineering Design)工程设计是将造型设计转化为可生产之车型的过程。
在这个阶段,设计师和工程师合作,解决工程问题,例如引擎配置、底盘设计、安全性能等。
目标是使设计在可生产的前提下尽可能保持概念设计的外观和风格。
6. 样车制造 (Prototype Manufacturing)样车制造是制造车辆的雏形以用于测试和评估的过程。
这个阶段的主要方法是使用专业的工具和工程技术人员来完成车辆的生产。
样车通常是按照设计和工程规格制造的,但可能不是最终的生产质量。
7. 车辆测试 (Vehicle Testing)车辆测试是评估车辆性能和安全性的过程。
这包括相关的测试,如制动测试、加速测试、悬挂系统测试以及碰撞测试等。
通过这些测试,设计师和工程师可以确认产品是否符合设计要求,并对需要改进的方面提出建议。
汽车制造业开发阶段生产准备的英文术语
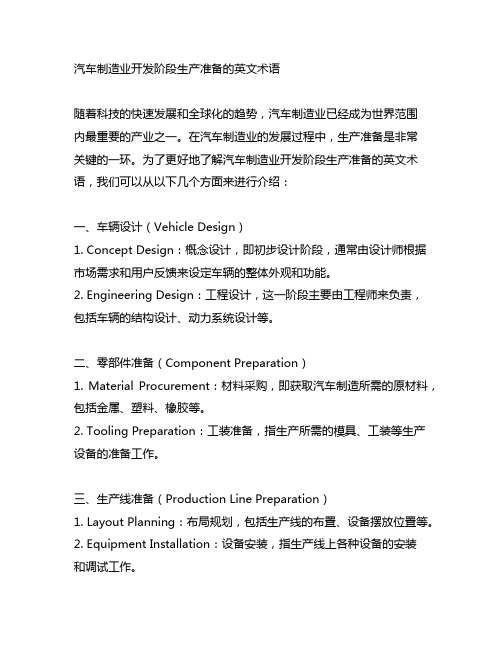
汽车制造业开发阶段生产准备的英文术语随着科技的快速发展和全球化的趋势,汽车制造业已经成为世界范围内最重要的产业之一。
在汽车制造业的发展过程中,生产准备是非常关键的一环。
为了更好地了解汽车制造业开发阶段生产准备的英文术语,我们可以从以下几个方面来进行介绍:一、车辆设计(Vehicle Design)1. Concept Design:概念设计,即初步设计阶段,通常由设计师根据市场需求和用户反馈来设定车辆的整体外观和功能。
2. Engineering Design:工程设计,这一阶段主要由工程师来负责,包括车辆的结构设计、动力系统设计等。
二、零部件准备(Component Preparation)1. Material Procurement:材料采购,即获取汽车制造所需的原材料,包括金属、塑料、橡胶等。
2. Tooling Preparation:工装准备,指生产所需的模具、工装等生产设备的准备工作。
三、生产线准备(Production Line Preparation)1. Layout Planning:布局规划,包括生产线的布置、设备摆放位置等。
2. Equipment Installation:设备安装,指生产线上各种设备的安装和调试工作。
四、生产试制(Prototype Production)1. Prototype Build:试制车辆生产,即根据设计图纸制作出最初的样车。
2. Testing and Validation:测试和验证,对样车进行各种测试,验证其性能和安全性。
五、量产准备(Mass Production Preparation)1. Process Optimization:工艺优化,即对生产工艺进行优化,提高效率和降低成本。
2. Supplier Development:供应商开发,确保零部件供应商能够按时按质供货。
六、生产调试(Production Debugging)1. Line Validation:生产线验证,对整条生产线进行试运行,确保生产设备正常运行。
APQP-和PPAP过程专业术语
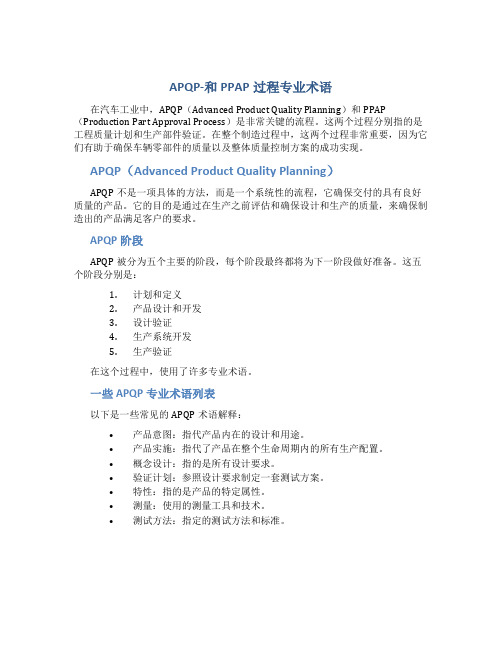
APQP-和PPAP过程专业术语在汽车工业中,APQP(Advanced Product Quality Planning)和PPAP (Production Part Approval Process)是非常关键的流程。
这两个过程分别指的是工程质量计划和生产部件验证。
在整个制造过程中,这两个过程非常重要,因为它们有助于确保车辆零部件的质量以及整体质量控制方案的成功实现。
APQP(Advanced Product Quality Planning)APQP不是一项具体的方法,而是一个系统性的流程,它确保交付的具有良好质量的产品。
它的目的是通过在生产之前评估和确保设计和生产的质量,来确保制造出的产品满足客户的要求。
APQP阶段APQP被分为五个主要的阶段,每个阶段最终都将为下一阶段做好准备。
这五个阶段分别是:1.计划和定义2.产品设计和开发3.设计验证4.生产系统开发5.生产验证在这个过程中,使用了许多专业术语。
一些APQP专业术语列表以下是一些常见的APQP术语解释:•产品意图:指代产品内在的设计和用途。
•产品实施:指代了产品在整个生命周期内的所有生产配置。
•概念设计:指的是所有设计要求。
•验证计划:参照设计要求制定一套测试方案。
•特性:指的是产品的特定属性。
•测量:使用的测量工具和技术。
•测试方法:指定的测试方法和标准。
PPAP(Production Part Approval Process)PPAP是一系列的评估过程,确保所涉及的部件在开始生产前是合格的。
这个过程的主要目的是确保在量产阶段,所生产的零件满足要求的质量标准。
这是实现全面质量控制方案的一部分。
PPAP阶段PPAP也分为五个主要的阶段,可以与APQP的五个阶段相对应。
这五个阶段分别是:1.部件计划2.材料评估3.制造过程评估4.部件评估5.PPAP批准一些PPAP专业术语列表以下是一些常见的PPAP术语解释:•过程登记:是指过程的过程记录和统计分析。
汽车行业常用缩写

Glossary of Terms术语Glossary of Terms术语AAR: Appearance Approval Report 外观批准报告A/D/V: Analysis/Development/Validation 分析/开发/验证A/D/V–DV:ADV Design Validation ADV设计验证A/D/V P&R: Analysis/Development/Validation Plan and Report。
This form is used to summarize the plan and results for validation testing. Additional information can be found in the GP—11 procedure。
分析/开发/验证计划和报告A/D/V–PV:ADV Product Validation ADV产品验证AIAG:Automotive Industries Action Group, an organization formed by General Motors, Ford and Daimler—Chrysler to develop common standards and expectations for automotive suppliers。
汽车工业行动集团AP: Advance Purchasing 先期采购APQP: Advanced Product Quality Planning 产品质量先期策划APQP Project Plan:A one—page summary of the SGM APQP process that describes the tasks and the timeframe in which they occur。
APQP项目策划AQC:Attribute Quality Characteristic 属性质量特性ASQE: Advanced Supplier Quality Engineer 先期供应商质量工程师BIW:Body in White。
汽车行业术语大全
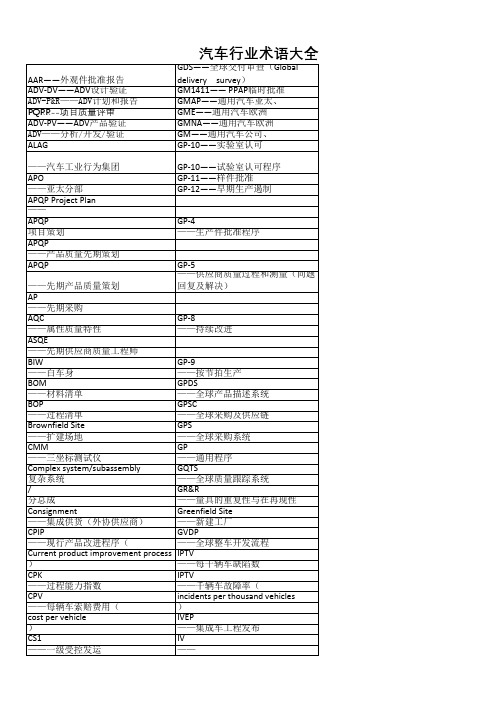
DFM/DFA ——可制造
/ 可装配性涉及
DFM/EA ——设计失效模式分析
DPV ——每辆车缺陷数
DR ——
DR 特性 DRE ——设计释放工程师
DRL ——一次生产通过率损失
DR ——生产质量综合指数( Direct Run ) DV ——设计验证 E&APSP ——工程 & 先期采购定点程序 EP ——电子采购流程 Error Occurrence Prevention
CMM ——三坐标测试仪
GP ——通用程序
Complex system/subassembly 复杂系统
GQTS ——全球质量跟踪系统
/ 分总成
GR&R ——量具的重复性与在再现性
Consignment ——集成供货(外协供应商)
Greenfield Site ——新建工厂
CPIP ——现行产品改进程序(
GVDP ——全球整车开发流程
Current product improvement process IPTV
)
——每千辆车缺陷数
CPK ——过程能力指数
IPTV ——千辆车故障率(
CPV ——每辆车索赔费用(
incidents per thousand vehicles )
cost per vehicle )
IVEP ——集成车工程发布
CS1 ——一级受控发运
IV ——
CS2 ——二级受控发运
CTC ——零部件时间表(
DRE )文件
CTS ——零件技术规范
CVER ——概念车工程发布
CVIS ——整车检验标准(
汽车产品设计开发流程的术语
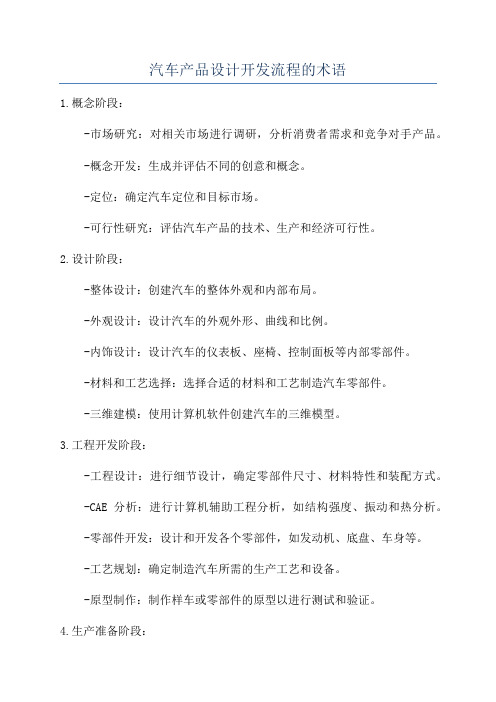
汽车产品设计开发流程的术语1.概念阶段:-市场研究:对相关市场进行调研,分析消费者需求和竞争对手产品。
-概念开发:生成并评估不同的创意和概念。
-定位:确定汽车定位和目标市场。
-可行性研究:评估汽车产品的技术、生产和经济可行性。
2.设计阶段:-整体设计:创建汽车的整体外观和内部布局。
-外观设计:设计汽车的外观外形、曲线和比例。
-内饰设计:设计汽车的仪表板、座椅、控制面板等内部零部件。
-材料和工艺选择:选择合适的材料和工艺制造汽车零部件。
-三维建模:使用计算机软件创建汽车的三维模型。
3.工程开发阶段:-工程设计:进行细节设计,确定零部件尺寸、材料特性和装配方式。
-CAE分析:进行计算机辅助工程分析,如结构强度、振动和热分析。
-零部件开发:设计和开发各个零部件,如发动机、底盘、车身等。
-工艺规划:确定制造汽车所需的生产工艺和设备。
-原型制作:制作样车或零部件的原型以进行测试和验证。
4.生产准备阶段:-工艺验证:验证生产工艺是否满足设计要求。
-工装制造:制造用于生产的专门工具和设备。
-零部件采购:采购生产所需的零部件和材料。
-供应商管理:管理和协调外部供应商。
5.试生产和测试阶段:-试生产:进行小规模生产以验证生产工艺和零部件可用性。
-功能测试:检验汽车的正常运行和性能。
-安全测试:评估汽车的安全性能和碰撞保护能力。
-排放测试:检测汽车的废气排放是否符合法规要求。
-可靠性测试:测试汽车在不同环境条件下的可靠性和耐久性。
6.量产阶段:-生产计划:制定汽车的生产计划和排产安排。
-质量控制:监控和控制汽车生产过程中的质量问题。
-供应链管理:管理和协调供应商、分销商和零部件供应等。
-营销和销售:市场推广和销售汽车产品。
以上是汽车产品设计开发流程中的一些术语。
根据实际项目和公司的要求,还可能涉及其他特定的术语和步骤。
不同的汽车制造公司和项目可能会有不同的流程和术语,但总体上,这些术语提供了车辆开发过程中的关键步骤和活动。
- 1、下载文档前请自行甄别文档内容的完整性,平台不提供额外的编辑、内容补充、找答案等附加服务。
- 2、"仅部分预览"的文档,不可在线预览部分如存在完整性等问题,可反馈申请退款(可完整预览的文档不适用该条件!)。
- 3、如文档侵犯您的权益,请联系客服反馈,我们会尽快为您处理(人工客服工作时间:9:00-18:30)。
汽车产品设计开发管理流程的术语(一)产品型谱是产品发展规划的核心内容,用最少数目的不同规格产品构成的,列出企业已有的和将来要发展的全部系列产品,能满足可预见到的全部使用要求的产品系列。
(备注:1、产品型谱按平台及相关指标系列化;2、产品型谱包含成熟产品、正在开发产品和预期产品,产品体系既保持相对稳定,又处于动态变化之中。
)用批量工装生产的零件(OTS)在批量生产用的工装/设备/模具/检具条件下,按B状态的图纸/技术规范等设计资料生产的件。
2TP两日生产(供应商)是供应商批量生产前的“总演习”,也是批量生产启动前对供应商的状况进行检查,即在正式批量生产条件下按事先商定的生产产品的数量或时间进行“生产演练”以验证所有设备、工装、工具、装配过程、传输系统、包装及质量检验是否符合批量生产条件,来考核供应商是否能确保其能在随后的批量生产下保持良好的稳定的生产一致性。
生产试制批量PVS(整车厂)是一种批量生产练习,所有的单件和总成件都到位,并都是用批量生产的设备及工装模具、试生产控制计划制造出来的件;对一般作业人员进行理论、线下和线上培训。
整个生产过程可在不连续的条件下按B阶段的图纸进行生产,从而对各工序加工能力、生产设备、试生产控制计划是否适当以及生产线的制造可行性、装配可行性、通过性、批量生产的适宜性进行实际验证,获得哪些设备和过程能确保所有要求的批量节拍和质量要求。
发现的薄弱环节必须在零批量生产启动前得到消除,其主要目的是通过生产的试运行来对其批量生产和确保产品质量进行验证。
PVS的车主要用来提供特定评价用车和培训用车以及进一步的分析和质保路试。
零批量0S(整车厂)是在批量生产条件(正式生产控制计划、正式生产工装和设施、已经过资质认定操作人员)下,按规划的批量生产节拍进行批量生产前的“总演习”。
其前提条件是外购、外协件和动力总成件都成功地通过了批量条件的两日生产验收;生产线、装配线、物流和各验收区域都已经达到了批量生产状态,整个工作的组织达到了批量生产的要求((如:工艺规程、检验规程、操作规程等处于最新状态),整个系统(生产、物流、质量保证和人员培训)都按批量的要求接受检查。
0S的车继续进行质量保证路试和试车评价。
批量生产总签发(SF)零批量生产获得成功,生产试制批量的车或发动机已通过规定里程的路试,没有发现任何大技术问题,且路试报告已经提供;零批量生产的或发动机已成功的完成相应里程的路试,路试报告已经提供;所有在质保路试中发现的缺陷获得分析,所采取的改进措施有效性在路试中获得验证;型式认证获得通过;新产品上市项目组已经成立,上市策略与上市方案已制定并下发,所有产品质量目标能达到和保持,进行批量生产启动前的总签发。
生产计划认可(EPF)批量生产总签发已经签发并颁布,导致推迟批量生产启动的特定风险已不存在,通过制定和下发批量计划来确认批量启动日期,所有供应商和物流部门都为此进行准备,以使批量启动和产量爬坡能有充足的批量生产启动(SOP)所有要求的各种认可都已获得;车型检验和型式认证已经成功完成并获得政府部门的使用批准;所有PVS、0S、SF和EPF的问题都已经得到了解决;整个生产线都具有批量能力,所有零部件都已经供应到位,且动力总成已SOP;整个生产线能按设计节拍、正式控制计划等正常生产条件下连续(10台/天)生产可销售状态的整车,接着按计划的产量爬坡曲线进行生产。
市场导入(ME)网络发展计划已按计划完成,销售人员及售后服务人员培训已按计划完成,备件已经开始强制销售,各类上市文件已经审批,营销策略已经确定,试销产品问题已改进或落实改进方案,产品正式上市已经获得批准,按既定的销售策略和方案开始全面导入市场。
标准白车身具备代表批量生产条件(模具、工装、夹具、场地等)和批量生产工艺、工艺路线等制造水平制作的白车身,其测量点符合率达到项目规定的要求。
标准白车身按对象分:内饰匹配标准白车身、外饰匹配标准白车身、底盘与动力总成匹配标准白车身和整车标准白车身四种。
PP认可—规划认可。
BB认可—采购认可。
DD认可—零件和材料订货认可。
M0初始数模,用于空间布置及概念设计、初步工艺评审,此阶段考虑供应商介入。
M1工艺数模,为拉伸模模型,主要为定位点讨论,需进行检、夹、模具的启动,方便供应商介入,开始模具概念设计。
M2P阶段数模/正式数模,为详细模型,用于模具正式设计,制造手工模具和Prototype模具。
M3B阶段数模/归档数模,用于正式模具制造。
生产件批准程序PPAP用来了解供应商是否已经正确掌握OEM工程设计记录的内容和规范要求,过程是否有能力生产出顾客要求的产品,过程节拍是否满足最佳经营方式。
项目由一组有启动时间的、相互协调的受控活动所组成的特定过程,该过程要达到符合规定要求的目标,包括时间、成本和资源的约束条件。
注2:在一些项目中,随着项目的进展,其目标需要修订或重新界定,产品特性需要逐步确定;注3:项目的结果可以是一种或几种产品;注4:项目组织机构是临时性组织,在项目寿命周期中存在;注5:项目活动之间的相互影响可能是复杂的。
项目产品项目范围中规定的交付给顾客的产品。
注意:项目范围可以随项目进展而修订。
项目管理项目管理是对项目及其资源进行计划、组织、协调和控制,以实现项目目的,包括项目各方面的策划、组织、监测和控制等过程的活动。
项目计划满足项目目标所需要活动的文件。
注1:项目计划应包括或引用项目的质量计划;注2:项目计划还应该包括诸如组织结构、资源、进度和预算等其他计划。
项目整体计划以项目各单项计划为基础,从项目全局出发把项目的各单项计划作为一个子系统进行整体管理,从而形成指导项目各单项管理的整体文件。
项目组织项目组织是指实施项目的组织。
项目周期项目实现过程中先后衔接的各个阶段的结合。
项目风险指由于项目所处环境和条件的不确定性,项目的最终结果与项目相关方的期望产生背离,并给项目相关方带来损失的可能性。
项目风险管理指通过风险识别、风险评估去认识风险,并以此为基础合理地使用各种管理方法、技术和手段对项目风险实行有效的控制,妥善处理风险事件所造成的不利后果,以最少的成本保证项目总体目标实现的过程。
项目质量指项目的交付物能够满足客户需求的程度。
项目质量管理是为了保证项目的交付物成果能够满足客户的需求,围绕项目的质量而进行的计划、协调、控制等活动。
项目成本在完成项目过程中,必然要发生的各种活动的消耗,这种消耗的货币表现形式就是项目成本。
项目成本管理指为了保证项目实际发生的成本不超过项目预算成本所进行的项目资源计划编制、项目成本估算、项目成本预算和项目成本控制等方面的管理过程和活动。
项目进度计划是在工作分解结构的基础上,对项目活动进行一系列的时间安排,它要对项目活动进行排序,明确项目活动必须何时开始以及完成项目活动所需要的时间。
其主要目的是控制和节约项目的时间,保证项目在规定的时间内能够完成。
项目进度管理在项目进展过程中,为了确保项目能够在规定的时间内实现项目的目标,对项目活动进度及日程安排所进行的管理活动。
项目门项目门是产品开发项目管理过程中设置的一系列控制点,用来确保产品开发项目在每阶段所有活动的标准已经得到满足,产品和过程已达到适宜的成熟、稳定的条件,可以进入产品开发的下一个阶段。
即项目门用来驱动产品开发过程,以依次确保所有的目标都能达到。
质量目标是对各级部门在产品、过程、流程和服务方面的规定。
这些目标根据顾客的要求、竞争情况、法规要求、内部规定以及遵循零缺陷战略而制订。
质量策划指一种确定生产某具体产品或系列产品(如:零件、材料等)所用方法如:测量和试验等)的结构化的过程,是质量管理的一部分,致力于设定质量目标并规定必要的作业过程和相关资源以实现其质量目标;与缺陷探测大不相同,质量策划包括防错和持续改进的思想。
产品质量先期策划APQP用来确定和制定确保某产品使顾客满意所需步骤的一种结构化、系统化的方法。
质量计划指质量管理体系要素被应用于一个特定情况的规范,是描述特殊产品或合同相关的具体质量规程、资源和系列活动的文件。
当控制计划作为质量计划时,质量计划便成为一种广义的概念。
同步工程同步工程又称并行工程,是一种用来综合、协调产品的设计及其相关过程——包括制造过程和保障过程的系统方法。
这种方法是用来使产品及过程开发人员从一开始就考虑从方案设计直到废弃的产品寿命周期的所有要素,包括质量、费用、进度和用户要求。
特殊特性由顾客指定的产品和过程特性,包括政府法规和安全特性,和/或由供应商通过产品和过程的了解选出的特性。
子系统系统的一个主要部分,本身具有系统的特性,通常包含几个部件。
系统由几个部件或部分设备组合起来以执行某一特定功能组合体。
设计开发将要求转换为产品规定的特性或规范的一组过程。
基准数据确定竞争者和/或最佳公司怎样达到其性能水平的调查结果。
材料清单制造产品所需的所有零件/材料的总清单。
失效模式及后果分析指一组系统化的活动。
在产品设计和制造过程设计阶段,对构成产品的系统、子系统和零件,以及制造过程的各个工序逐一进行分析,找出所有潜在的失效模式,并分析其可能的后果,从而预先采取必要的措施,以提高产品的质量和可靠性的一种系统化的活动,并将全部过程形成书面文件。
设计失效模式及后果分析是负责设计的工程师/小组用来尽最大可能确保潜在的失效模式和相关的原因/机理已被考虑并记录的分析技术,其目的在于降低失效风险,对设计过程提供支持。
过程失效模式及后果分析由负责制造的工程师/小组为确保尽最大可能考虑并记录潜在的失效模式和相关的原因/机理而使用的分析技术,其目的在于降低制造风险,对制造过程提供支持。
DVP&R设计验证计划和报告是包含试验计划和试验报告的单一文件,要求列出全部的试验(试验项目、程序或标准、试验描述、接收标准、目标要求、试验职责、试验场所、样件数目及类型、进度),以保证满足功能和可靠性标准及设计目标要求;试验报告提供了试验结果,以及试验计划规定设计目标的进展。
可制造性和装配设计用来优化设计功能、可制造性和装配方便性之间关系的同步工程过程。
可靠性某项产品在某一观测点上,在规定的环境和工作负荷条件下,在顾客期望的水平上继续发挥功能的概率。
设计输入指所要设计的产品在计划和确定项目、制造过程设计阶段所确定的顾客的需求和期望以及对制造过程的要求。
且应尽可能将所有要求定量化,并在产品和制造过程设计开发与生产准备任务书等文件中予以明确规定。
设计输出指相关部门根据设计输入要求在产品设计和开发过程中为实现过程的后续活动(如:用于采购、生产、安装、检验和试验以及服务的最终技术文件)提供产品或服务的规范和所进行各种活动的结果,这种规范设计记录是零件图样、规范、和/或电子(CAD)数据,用来传达生产一个产品必需的信息。