齿轮疲劳寿命与传动性能测试技术与装备
齿轮弯曲疲劳强度试验方法

齿轮弯曲疲劳强度试验方法全文共四篇示例,供读者参考第一篇示例:齿轮在机械设备中起着至关重要的作用,它们通过齿轮传动来实现机械运动,比如汽车的变速箱、风力发电机和其他机械设备都离不开齿轮。
齿轮在长时间运作中会受到各种力的作用,容易发生疲劳断裂,因此对齿轮的疲劳强度进行测试是非常重要的。
本文将介绍一种关于齿轮弯曲疲劳强度试验方法,以帮助读者了解如何对齿轮进行有效的疲劳强度测试。
一、试验原理齿轮在实际工作中常常处于扭转状态,因此齿轮齿面上会受到交替弯曲负载,导致齿轮的疲劳断裂。
齿轮弯曲疲劳强度试验就是通过加载一定应力的齿轮样品,进行一定次数的循环载荷,观察齿轮在经过一定循环次数后是否发生疲劳断裂,从而得到齿轮的弯曲疲劳强度数据。
二、试验步骤1. 制备齿轮样品:根据要测试的齿轮种类和规格,选择合适的齿轮样品进行测试。
确保齿轮样品的质量和尺寸符合要求。
2. 振动应力加载:将齿轮样品安装在试验设备上,施加振动应力加载进行弯曲疲劳试验。
根据所需的循环次数和载荷大小,设定试验参数。
3. 观察齿轮状态:在试验过程中,定期观察齿轮的状态,包括表面裂纹、变形等情况。
一旦发现齿轮有异常情况,立即停止试验,并对齿轮进行检查和修复。
4. 记录数据:记录齿轮样品在每个循环周期后的疲劳情况,包括疲劳寿命、发生裂纹的次数等数据。
5. 分析结果:根据试验数据分析齿轮的疲劳断裂情况,计算出齿轮的弯曲疲劳强度指标,评估齿轮的使用寿命和安全性。
三、试验注意事项1. 选用合适的试验设备和工具,确保试验过程中的准确性和可靠性。
2. 控制试验参数,包括载荷大小、循环次数等,确保试验结果具有可靠性。
3. 在试验过程中定期检查齿轮的状态,及时发现问题并采取措施修复。
4. 根据试验结果对齿轮进行评估和改进,提高其疲劳强度和使用寿命。
通过以上介绍,相信读者已经对齿轮弯曲疲劳强度试验方法有了一定的了解。
要保证齿轮的安全可靠运行,进行疲劳强度测试是非常关键的。
齿轮传动效率及齿轮疲劳实验
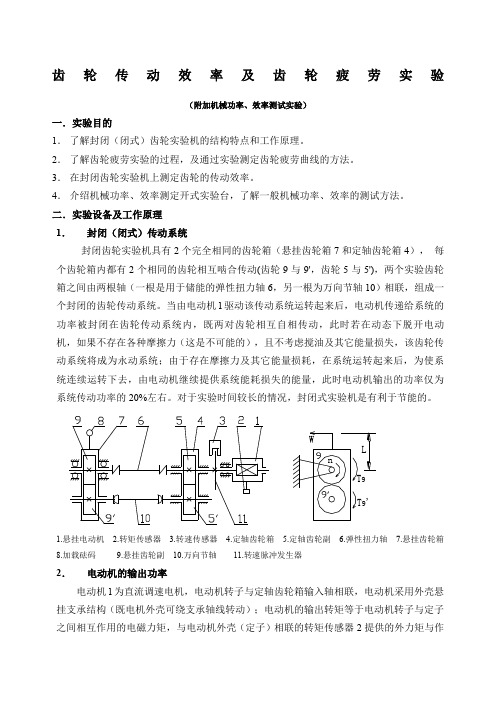
齿轮传动效率及齿轮疲劳实验(附加机械功率、效率测试实验)一.实验目的1.了解封闭(闭式)齿轮实验机的结构特点和工作原理。
2.了解齿轮疲劳实验的过程,及通过实验测定齿轮疲劳曲线的方法。
3.在封闭齿轮实验机上测定齿轮的传动效率。
4.介绍机械功率、效率测定开式实验台,了解一般机械功率、效率的测试方法。
二.实验设备及工作原理用于定子的电磁力矩相平衡,故转矩传感器测得的力矩即为电动机的输出转矩T 0;电动机转速为n ,电动机输出功率为 P0=n ·T 0 / 9550 (KW)。
3. 封闭系统的加载当实验台空载时,悬挂齿轮箱的杠杆通常处于水平位置,当加上载荷W 后,对悬挂齿轮箱作用一外加力矩WL ,使悬挂齿轮箱产生一定角度的翻转,使两个齿轮箱内的两对齿轮的啮合齿面靠紧,这时在弹性扭力轴内存在一扭矩T 9(方向与外加负载力矩WL 相反),在万向节轴内同样存在一扭矩T 9'(方向同样与外加力矩WL 相反);若断开扭力轴和万向节轴,取悬挂齿轮箱为隔离体,可以看出两根轴内的扭矩之和(T 9+T 9')与外加负载力矩WL 平衡(即T 9+T 9'=WL );又因两轴内的两个扭矩(T 9和T 9')为同一个封闭环形传动链内的扭矩,故这两个扭矩相等(T 9=T 9'),即2T 9=WL , T 9=WL/2(Nm );由此可以算出该封闭系统内传递的功率为:P 9=T 9 n / 9550=WLn /19100 (KW)其中:n--电动机及封闭系统的转速(rpm );W--所加砝码的重力(N );L--加载杠杆(力臂)的长度,L= 0.3 m 。
4. 单对齿轮传动效率设封闭齿轮传动系统的总传动效率为η;封闭齿轮传动系统内传递的有用功率为P 9;封闭齿轮传动系统内的功率损耗(无用功率)等于电动机输出功率P 0,即:P 0=(P 9 /η)-P 9η=P 9 /(P 0+P 9)=T 9 /(T 0+T 9 )若忽略轴承的效率,系统总效率η包含两级齿轮的传动效率,故单级齿轮的传动效率为:9091T T T +==ηη 5. 封闭功率流方向封闭系统内功率流的方向取决于由外加力矩决定的齿轮啮合齿面间作用力的方向和由电动机转向决定的各齿轮的转向;当一个齿轮所受到的齿面作用力与其转向相反时,该齿轮为主动齿轮,而当齿轮所受到的齿面作用力与其转向相同时,则该齿轮为从动齿轮;功率流的方向从主动齿轮流向从动齿轮,并封闭成环。
齿轮弯曲疲劳寿命系数

齿轮弯曲疲劳寿命系数齿轮是机械传动中常见的零件,广泛应用于机械装置和设备中。
作为常规的机械部件,齿轮需要具备极高的稳定性和耐久性,才能够保证其正常运行和服务寿命。
而齿轮弯曲疲劳寿命系数是刻画齿轮性能的一个指标,本文将详细探讨齿轮弯曲疲劳寿命系数的相关内容。
1. 齿轮弯曲疲劳寿命系数的定义齿轮弯曲疲劳寿命系数是指在齿轮传动装置的设计寿命内,齿轮齿根处应力的分布与疲劳寿命之间的关系。
齿轮弯曲疲劳寿命系数越大,即表示齿轮具备更高的耐久性和可靠性,能够承受更大的工作负荷和更长时间的使用寿命。
2. 影响齿轮弯曲疲劳寿命系数的因素齿轮弯曲疲劳寿命系数的大小受到多种因素的影响,主要包括以下几个方面:(1)齿轮材料齿轮材料的物理性能和力学性能对齿轮弯曲疲劳寿命系数的影响非常明显。
一般来说,强度高、韧性好、疲劳寿命长、组织均匀的材料更适合作为齿轮材料,能够提高齿轮弯曲疲劳寿命系数。
(2)齿轮的设计几何参数齿轮的设计几何参数也会对齿轮弯曲疲劳寿命系数产生较大的影响。
齿轮参数的合理设计可以减小齿轮齿根处的应力集中程度,从而提高齿轮弯曲疲劳寿命系数。
(3)负荷条件负荷条件是齿轮弯曲疲劳寿命系数的另一个重要影响因素。
在负荷条件相同的情况下,齿轮弯曲疲劳寿命系数越大,表示齿轮具备更好的承载能力和耐久性。
(4)轴承和润滑条件轴承和润滑条件是影响齿轮弯曲疲劳寿命系数的另一因素。
良好的轴承和润滑条件有助于减少齿轮的磨损和摩擦,降低应力水平,提高齿轮弯曲疲劳寿命系数。
3. 齿轮弯曲疲劳寿命系数的测试方法齿轮弯曲疲劳寿命系数的测试是对齿轮性能进行评估和确认的重要手段。
一般采用模拟试验或数值模拟两种方法进行测试,具体方法如下:(1)模拟试验模拟试验是指利用齿轮模拟器或齿轮试验台等设备进行实物测试的方法。
通过不断重复负荷的作用,观察齿轮的磨损程度和变形情况,推算齿轮弯曲疲劳寿命系数和寿命预测模型。
(2)数值模拟数值模拟是通过建立齿轮弯曲疲劳寿命的有限元模型,采用ANSYS、ABAQUS等有限元软件进行计算、模拟和预测的方法。
齿轮疲劳测试实验报告(3篇)

第1篇一、实验目的本次实验旨在研究齿轮在循环载荷作用下的疲劳性能,通过对齿轮进行疲劳测试,获取其疲劳寿命、疲劳极限和疲劳特性曲线,为齿轮的设计和选材提供理论依据。
二、实验原理齿轮疲劳测试是利用实验方法模拟齿轮在实际工作条件下的疲劳失效过程,通过测量齿轮在循环载荷作用下的应力、应变、裂纹扩展等参数,分析齿轮的疲劳性能。
实验通常采用以下原理:1. 应力控制法:通过控制加载装置,使齿轮承受恒定的应力水平,观察齿轮的疲劳寿命。
2. 应变控制法:通过控制应变,使齿轮承受恒定的应变水平,观察齿轮的疲劳寿命。
3. 频谱控制法:通过控制载荷的频率和幅度,模拟齿轮在实际工作条件下的载荷特性,观察齿轮的疲劳性能。
三、实验设备1. 齿轮疲劳试验机:用于施加循环载荷,模拟齿轮在实际工作条件下的载荷特性。
2. 数据采集系统:用于采集齿轮在疲劳测试过程中的应力、应变、裂纹扩展等参数。
3. 光学显微镜:用于观察齿轮表面裂纹的形态和扩展情况。
4. 硬度计:用于测量齿轮表面的硬度。
四、实验材料本次实验选用材料为45号钢,经过调质处理,硬度为HRC35-40。
五、实验步骤1. 实验前准备:将齿轮加工成标准试样,并进行表面处理,如喷丸处理等。
2. 加载:将齿轮试样安装在疲劳试验机上,按照预定程序施加循环载荷。
3. 数据采集:在实验过程中,实时采集齿轮的应力、应变、裂纹扩展等参数。
4. 裂纹观察:在实验结束后,利用光学显微镜观察齿轮表面裂纹的形态和扩展情况。
5. 硬度测试:在实验结束后,利用硬度计测量齿轮表面的硬度。
六、实验结果与分析1. 疲劳寿命:通过实验数据,计算出齿轮的疲劳寿命,即齿轮在循环载荷作用下发生疲劳失效所需的时间。
2. 疲劳极限:通过实验数据,确定齿轮的疲劳极限,即齿轮在循环载荷作用下能够承受的最大应力水平。
3. 疲劳特性曲线:通过实验数据,绘制齿轮的疲劳特性曲线,分析齿轮的疲劳性能。
实验结果表明,齿轮在循环载荷作用下具有良好的疲劳性能。
塑料齿轮疲劳寿命分析报告

1 齿轮的疲劳破坏疲劳是一种十分有趣的现象,当材料或结构受到多次重复变化的载荷作用后,应力值虽然始终没有超过材料的强度极限,甚至比屈服极限还低的情况下就可能发生破坏,这种在交变载荷重复作用下材料或结构的破坏现象就叫做疲劳破坏。
如图1所示,F表示齿轮啮合时作用于齿轮上的力。
齿轮每旋转一周,轮齿啮合一次。
啮合时,F由零迅速增加到最大值,然后又减小为零。
因此,齿根处的弯曲应力or也由零迅速增加到某一最大值再减小为零。
此过程随着齿轮的转动也不停的重复。
应力or随时间t的变化曲线如图2所示。
图1 齿轮啮合时受力情况图2 齿根应力随时间变化曲线在现代工业中,很多零件和构件都是承受着交变载荷作用,工程塑料齿轮就是其中的典型零件。
工程塑料齿轮因其质量小、自润滑、吸振好、噪声低等优点在纺织、印染、造纸和食品等传动载荷适中的轻工机械中应用很广。
疲劳破坏与传统的静力破坏有着许多明显的本质差别:1)静力破坏是一次最大载荷作用下的破坏;疲劳被坏是多次反复载荷作用下产生的破坏,它不是短期内发生的,而是要经历一定的时间。
2)当静应力小于屈服极限或强度极限时,不会发生静力破坏;而交变应力在远小于静强度极限,甚至小于屈服极限的情况下,疲劳破坏就可能发生。
3)静力破坏通常有明显的塑性变形产生;疲劳破坏通常没有外在宏观的显著塑性变形迹象,事先不易觉察出来,这就表明疲劳破坏具有更大的危险性。
工程塑料齿轮的疲劳寿命,是设计人员十分关注的课题,也是与实际生产紧密相关的问题。
然而,在疲劳载荷作用下的疲劳寿命计算十分复杂。
因为要计算疲劳寿命,必须有精确的载荷谱,材料特性或构件的S-N曲线,合适的累积损伤理论,合适的裂纹扩展理论等。
本文对工程塑料齿轮疲劳分析的最终目的,就是要确定其在各种质量情况下的疲劳寿命。
通过利用有限元方法和CAE软件对工程塑料齿轮的疲劳寿命进行分析研究有一定工程价值。
2 工程塑料齿轮材料的确定超高分子量聚乙烯(UHMWPE)是一种综合性能优异的新型热塑性工程塑料,它的分子结构与普通聚乙烯(PE)完全相同,但相对分子质量可达(1~4)×106。
齿轮齿面接触疲劳特性与寿命预测
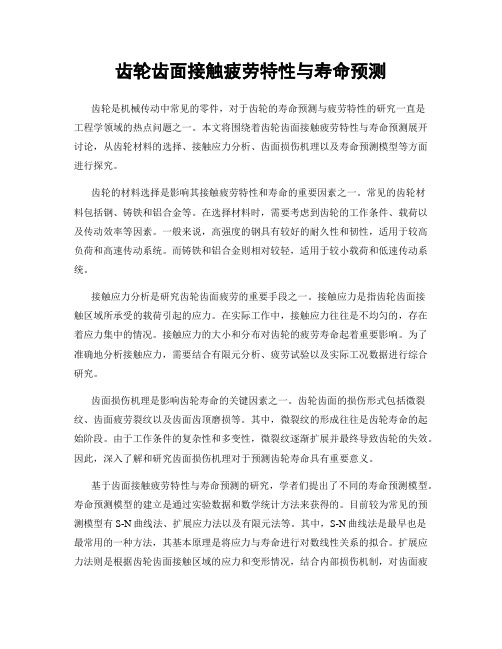
齿轮齿面接触疲劳特性与寿命预测齿轮是机械传动中常见的零件,对于齿轮的寿命预测与疲劳特性的研究一直是工程学领域的热点问题之一。
本文将围绕着齿轮齿面接触疲劳特性与寿命预测展开讨论,从齿轮材料的选择、接触应力分析、齿面损伤机理以及寿命预测模型等方面进行探究。
齿轮的材料选择是影响其接触疲劳特性和寿命的重要因素之一。
常见的齿轮材料包括钢、铸铁和铝合金等。
在选择材料时,需要考虑到齿轮的工作条件、载荷以及传动效率等因素。
一般来说,高强度的钢具有较好的耐久性和韧性,适用于较高负荷和高速传动系统。
而铸铁和铝合金则相对较轻,适用于较小载荷和低速传动系统。
接触应力分析是研究齿轮齿面疲劳的重要手段之一。
接触应力是指齿轮齿面接触区域所承受的载荷引起的应力。
在实际工作中,接触应力往往是不均匀的,存在着应力集中的情况。
接触应力的大小和分布对齿轮的疲劳寿命起着重要影响。
为了准确地分析接触应力,需要结合有限元分析、疲劳试验以及实际工况数据进行综合研究。
齿面损伤机理是影响齿轮寿命的关键因素之一。
齿轮齿面的损伤形式包括微裂纹、齿面疲劳裂纹以及齿面齿顶磨损等。
其中,微裂纹的形成往往是齿轮寿命的起始阶段。
由于工作条件的复杂性和多变性,微裂纹逐渐扩展并最终导致齿轮的失效。
因此,深入了解和研究齿面损伤机理对于预测齿轮寿命具有重要意义。
基于齿面接触疲劳特性与寿命预测的研究,学者们提出了不同的寿命预测模型。
寿命预测模型的建立是通过实验数据和数学统计方法来获得的。
目前较为常见的预测模型有S-N曲线法、扩展应力法以及有限元法等。
其中,S-N曲线法是最早也是最常用的一种方法,其基本原理是将应力与寿命进行对数线性关系的拟合。
扩展应力法则是根据齿轮齿面接触区域的应力和变形情况,结合内部损伤机制,对齿面疲劳寿命进行预测。
有限元法则通过建立齿轮的数值模型,对接触应力进行详细分析,从而得到齿面疲劳寿命的预测结果。
总之,齿轮齿面接触疲劳特性与寿命预测是机械工程领域中的重要研究方向。
机械工程中变速箱齿轮材料的疲劳寿命预测

机械工程中变速箱齿轮材料的疲劳寿命预测随着工业技术的不断发展,机械工程的应用越来越广泛。
其中,变速箱作为机械设备的关键部件,其可靠性与寿命问题一直是工程师们关注的焦点。
而在变速箱中,齿轮作为传递动力和承受负载的主要部件,材料的疲劳寿命预测则成为研究的重要内容。
1. 简介变速箱是用于改变动力传递比例以实现车辆行驶、工业机械传动等的装置。
它具有传递扭矩和功率的能力,同时也承受着巨大的负载。
在变速箱中,齿轮是主要的承载元件之一,其直接影响整个变速箱的性能和寿命。
2. 变速箱齿轮材料特性分析齿轮材料在工程实践中的选择需要满足一系列要求。
首先,齿轮材料需要具备高强度和硬度,以承受大的载荷和磨损。
其次,齿轮需要具备良好的耐疲劳性能,以防止由于高负荷频繁变动而导致材料疲劳破坏。
最后,齿轮材料还需要具备良好的热处理适应性,以提高其综合性能。
3. 齿轮疲劳寿命预测方法为准确预测齿轮材料的疲劳寿命,工程师们通常采用一系列预测方法。
其中,最常见的方法是基于疲劳强度与应力循环次数关系的S-N曲线法。
该方法通过实验测试,构建材料的S-N曲线,即应力与循环次数的对应关系。
根据S-N曲线,可以预测出齿轮材料在不同应力下的疲劳寿命。
4. 影响齿轮疲劳寿命的因素预测齿轮材料的疲劳寿命需要考虑多种因素。
首先,应力水平对于疲劳寿命的影响是至关重要的。
高应力下,齿轮材料容易发生疲劳破坏,寿命较短。
其次,载荷类型也会对材料的疲劳寿命产生影响。
例如,动态载荷会导致疲劳寿命减少。
同时,齿轮的设计和制造质量也对疲劳寿命有重要影响。
5. 改进齿轮材料的方法为提高变速箱齿轮的疲劳寿命,工程师们通过多种方式进行改进。
一种常见的方式是选用高强度和高硬度的材料,以提高齿轮的承载能力和耐磨性。
同时,合理的热处理工艺也能够提高材料的性能,延长齿轮的使用寿命。
此外,优化齿轮的设计和制造工艺也能够减少材料的疲劳损伤。
6. 结论变速箱齿轮材料的疲劳寿命预测是机械工程领域的一个重要研究方向。
斜齿轮传动过程的力学性能及疲劳寿命预测
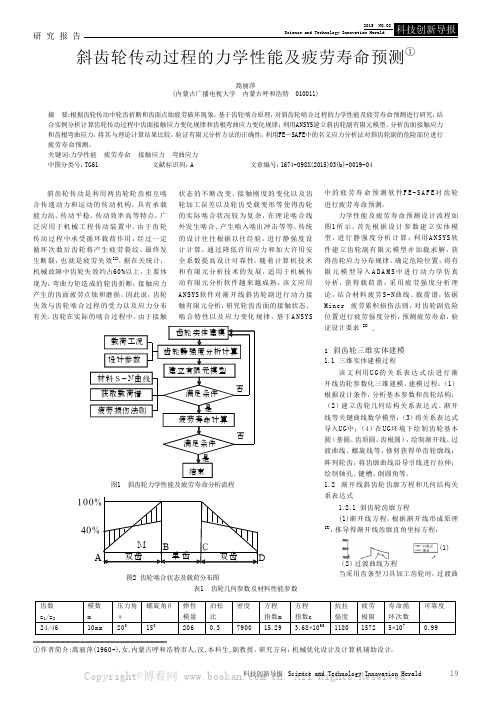
斜齿轮传动是利用两齿轮轮齿相互啮合传递动力和运动的传动机构,具有承载能力高、传动平稳、传动效率高等特点,广泛应用于机械工程传动装置中。
由于齿轮传动过程中承受循环载荷作用,经过一定循环次数后齿轮将产生疲劳裂纹,最终发生断裂,也就是疲劳失效[1]。
据在关统计,机械故障中齿轮失效约占60%以上,主要体现为:弯曲力矩造成的轮齿折断,接触应力产生的齿面疲劳点烛和磨损,因此说,齿轮失效与齿轮啮合过程的受力以及应力分布有关。
齿轮在实际的啮合过程中,由于接触状态的不断改变、接触刚度的变化以及齿轮加工误差以及轮齿受载变形等使得齿轮的实际啮合状况较为复杂,在理论啮合线外发生啮合、产生啮入啮出冲击等等。
传统的设计往往根据以往经验,进行静强度设计计算,通过降低许用应力和加大许用安全系数提高设计可靠性。
随着计算机技术和有限元分析技术的发展,适用于机械传动有限元分析软件越来越成熟,该文应用A N SYS 软件对渐开线斜齿轮副进行动力接触有限元分析,研究轮齿齿面的接触状态、啮合特性以及应力变化规律,基于A N S YS中的疲劳寿命预测软件F E -S A F E 对齿轮进行疲劳寿命预测。
力学性能及疲劳寿命预测设计流程如图1所示。
首先根据设计参数建立实体模型,进行静强度分析计算;利用A N S Y S 软件建立齿轮副有限元模型并加载求解,获得齿轮应力分布规律、确定危险位置;将有限元模型导入A D A M S 中进行动力学仿真分析,获得载荷谱;采用疲劳强度分析理论,结合材料疲劳S-N曲线、载荷谱,依据Miner 疲劳累积损伤法则,对齿轮副危险位置进行疲劳强度分析,预测疲劳寿命,验证设计要求 [2] 。
1 斜齿轮三维实体建模1.1 三维实体建模过程该文利用U G 的关系表达式法进行渐开线齿轮参数化三维建模,建模过程:(1)根据设计条件,分析基本参数和齿轮结构;(2)建立齿轮几何结构关系表达式、渐开线等关键曲线数学模型;(3)将关系表达式导入U G中;(4)在U G环境下绘制齿轮基本圆(基圆、齿顶圆、齿根圆),绘制渐开线、过渡曲线、螺旋线等,修剪获得单齿轮廓线;阵列轮齿,将齿廓曲线沿导引线进行拉伸;绘制轴孔、键槽、倒圆角等。
齿轮疲劳寿命开题报告
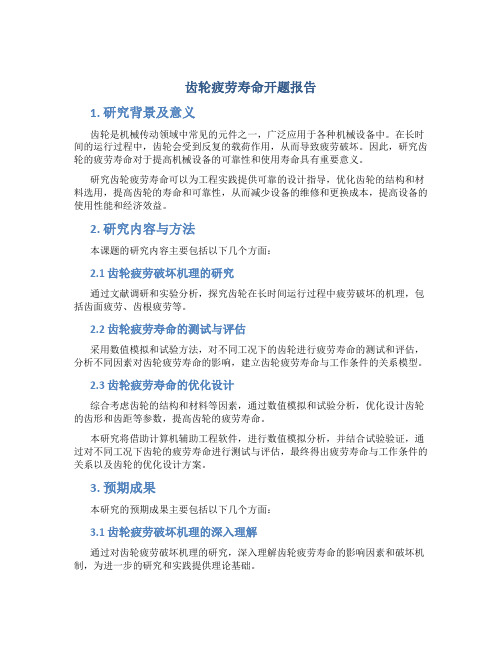
齿轮疲劳寿命开题报告1. 研究背景及意义齿轮是机械传动领域中常见的元件之一,广泛应用于各种机械设备中。
在长时间的运行过程中,齿轮会受到反复的载荷作用,从而导致疲劳破坏。
因此,研究齿轮的疲劳寿命对于提高机械设备的可靠性和使用寿命具有重要意义。
研究齿轮疲劳寿命可以为工程实践提供可靠的设计指导,优化齿轮的结构和材料选用,提高齿轮的寿命和可靠性,从而减少设备的维修和更换成本,提高设备的使用性能和经济效益。
2. 研究内容与方法本课题的研究内容主要包括以下几个方面:2.1 齿轮疲劳破坏机理的研究通过文献调研和实验分析,探究齿轮在长时间运行过程中疲劳破坏的机理,包括齿面疲劳、齿根疲劳等。
2.2 齿轮疲劳寿命的测试与评估采用数值模拟和试验方法,对不同工况下的齿轮进行疲劳寿命的测试和评估,分析不同因素对齿轮疲劳寿命的影响,建立齿轮疲劳寿命与工作条件的关系模型。
2.3 齿轮疲劳寿命的优化设计综合考虑齿轮的结构和材料等因素,通过数值模拟和试验分析,优化设计齿轮的齿形和齿距等参数,提高齿轮的疲劳寿命。
本研究将借助计算机辅助工程软件,进行数值模拟分析,并结合试验验证,通过对不同工况下齿轮的疲劳寿命进行测试与评估,最终得出疲劳寿命与工作条件的关系以及齿轮的优化设计方案。
3. 预期成果本研究的预期成果主要包括以下几个方面:3.1 齿轮疲劳破坏机理的深入理解通过对齿轮疲劳破坏机理的研究,深入理解齿轮疲劳寿命的影响因素和破坏机制,为进一步的研究和实践提供理论基础。
3.2 齿轮疲劳寿命评估模型的建立通过试验数据的分析与数值模拟,建立齿轮疲劳寿命与工作条件的关系模型,为齿轮的寿命评估与优化设计提供参考依据。
3.3 齿轮疲劳寿命的优化设计方案通过研究齿轮的结构和材料等因素,提出齿轮的优化设计方案,以提高齿轮的疲劳寿命和可靠性。
4. 工作计划为了完成以上的研究内容和达到预期的成果,我们制定了以下工作计划:•第一年:完成齿轮疲劳破坏机理的文献调研和试验分析,深入探究齿轮疲劳破坏的机理和影响因素。
基于实际载荷谱的电动汽车减速器齿轮疲劳寿命分析

基于实际载荷谱的电动汽车减速器齿轮疲劳寿命分析摘要:现阶段,新能源电动车推动普遍使用电动机-减速器计划方案。
减速器可以赔偿电动机本身转距不够的不足,合适的传动比可让电动机长期性运行在最好工况,减少资源消耗,因而,减速器已经成为电动式汽车传动系统中不可缺少的关键核心部件之一。
用以减速器的载荷谱根据新车型总体目标位置布局高精度传感器,即时获得总体目标区域的动态性能,可以真实反映待测件所受到的载荷鼓励。
时下模拟仿真可以创建较准确的分析方法,但初始条件和键入标准层面仍存在一些缺乏。
将载荷谱用于虚似试验中,可促使仿真结果更符合实际。
减速器的疲惫稳定性对新能源电动车动力传动系统乃至车身的疲惫稳定性具备关键性的危害,而齿轮则是最主要的零件之一,其真正疲惫寿命事关减速器的疲惫稳定性。
关键词:实际载荷谱;电动汽车;减速器齿轮疲劳寿命1载荷谱的获取1.1齿轮接触应力谱文中所收集载荷谱的新能源电动车减速器齿轮为斜齿轮,材料为20CrMnTi。
根据经验,当齿轮原材料相同的情况下,齿轮副最开始产生疲劳破坏的一般为转动轴,因此减速器齿轮接触疲劳寿命实则转动轴接触疲劳寿命。
要测算齿轮的接触疲劳寿命,需要得到接触压力—时间曲线,所以该曲线图能够适合于循环系统记数,之前已经根据收集技术性赢得了永磁电机的输出转矩载荷,要获得适合于疲惫计算出来的齿轮接触压力载荷谱,应该做一些转换,将要收集所得到的推动电机扭矩载荷转化为齿轮上轴颈的接触压力。
1.2采集方案新能源电动车减速器关键承担来源于电动机变动的转速比载荷及其地面行车负载转矩载荷,因此,对新能源电动车具体行车时的减速器转距转速比载荷开展收集。
为了便于全车及其它零部件的开发,此次收集除减速器转距转速比载荷以外,还采集了车轱辘六分力及车体应变力等。
采用CAN总线获得减速器转速比数据信号,运用六分力量的横着转距获得减速器转距数据信号,全部数据信号根据性能卓越数采系统进行同歩收集。
收集工况根据某公司的实验场耐久性试验标准,包含加强工况驱动力工况。
齿轮传动系统设计中的疲劳强度分析

齿轮传动系统设计中的疲劳强度分析齿轮传动系统是机械运动控制系统中的重要组成部分,广泛应用于汽车、航空、船舶、军工等领域。
在设计齿轮传动系统时,疲劳强度分析是至关重要的一步,因为齿轮在长期使用过程中会承受不同程度的疲劳损伤,从而导致传动系统失效。
本文将从齿轮材料选用、载荷分析、疲劳寿命预估等多个方面探讨齿轮传动系统设计中的疲劳强度分析。
一、齿轮材料选用在齿轮传动系统设计中,首先要确定齿轮的材料。
尤其对于高负荷、高速传动的齿轮来说,材料的选用更显得至关重要。
传统齿轮材料包括低碳钢、中碳钢、铸铁等,但这些材料在高负载、高速传动的情况下容易产生疲劳裂纹,进而导致齿轮失效。
针对这一问题,现代齿轮传动系统常采用效应材料,如合金钢、超高强钢等。
这类材料不仅具有高拉伸强度和高硬度,而且还能够增加齿轮的韧性和耐久性,从而提高齿轮的疲劳强度。
此外,在选用材料时,也需要结合实际应用场景和经济成本综合考虑。
二、载荷分析在考虑齿轮的疲劳强度时,载荷分析是一个关键的环节。
不同的载荷会对齿轮的疲劳强度造成不同影响,因此需要根据具体应用情况设计不同的载荷条件。
一般而言,载荷分为静载荷和动载荷两种,其中静载荷是指传动系统在静止状态下的承载能力,而动载荷则是指传动系统在运动状态下受到的载荷。
在实际应用中,载荷往往是非常复杂的。
对于齿轮传动系统来说,载荷来源多种多样,如机器本身的振动、不同部件之间的相互作用、外部环境的影响等。
因此,需要对多种载荷进行分析,确保齿轮的设计满足最糟糕的载荷情况下的强度要求。
三、疲劳寿命预估齿轮的疲劳寿命是指在一定载荷条件下,齿轮出现第一个裂纹的时间。
疲劳寿命的长短直接影响齿轮传动系统的可靠性和安全性。
因此,在齿轮传动系统设计中,预估疲劳寿命非常重要。
常用的疲劳寿命预估方法包括双应力范围法、极限载荷法、等效应力法等。
这些方法分别通过不同的方式计算疲劳寿命,具有各自的优缺点。
其中,等效应力法是目前应用最广泛的方法,它将不同载荷情况下的应力转化为等效应力,进而推导出疲劳寿命。
减速器(齿轮)综合性能测试方法方案
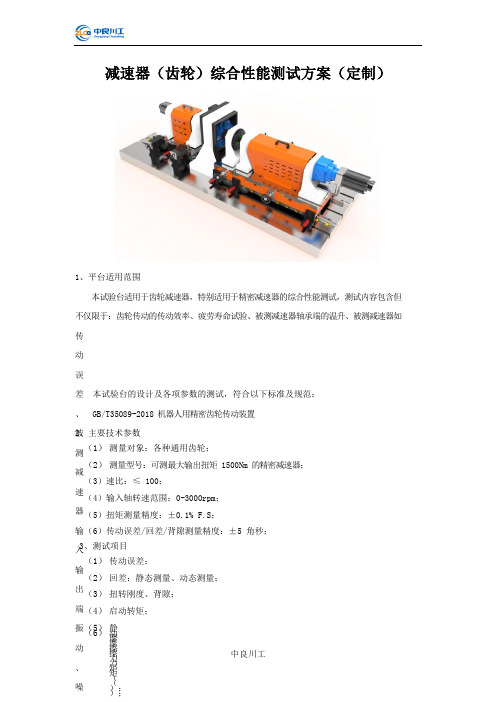
减速器(齿轮)综合性能测试方案(定制)1、平台适用范围本试验台适用于齿轮减速器,特别适用于精密减速器的综合性能测试,测试内容包含但不仅限于:齿轮传动的传动效率、疲劳寿命试验、被测减速器轴承端的温升、被测减速器如传动误差、被测减速器输入输出端振本试验台的设计及各项参数的测试,符合以下标准及规范: GB/T35089-2018 机器人用精密齿轮传动装置 2、主要技术参数 (1) 测量对象:各种通用齿轮;(2) 测量型号:可测最大输出扭矩 1500Nm 的精密减速器;(3)速比:≤ 100;(4)输入轴转速范围:0-3000rpm ;(5)扭矩测量精度:±0.1% F.S;(6)传动误差/回差/背隙测量精度:±5 角秒; 3、测试项目 (1) 传动误差; (2) 回差:静态测量、动态测量;(3) 扭转刚度、背隙; (4) 启动转矩;(5) 静摩(6) 动摩(7)传动效率,包括在不同转速、不同载荷、不同温度工况下的效率;(8)负载;(9)振动、噪音、温升。
4、主机结构试验台采用卧式机构,由精密机械系统、测控系统、测量软件等部分组成。
其中主机结构如图 1 所示:图 1 平台主机结构示意图主机相关各组件安装在约 3 米长的带T 型槽铸铁平台基座上。
主机主要由驱动装置、加载装置、安装支架、基座等部分组成。
输入端由交流伺服电机驱动,可分别工作在速度模式和力矩模式。
输出端阻尼电机采用交流伺服电机,作为加载装置,并在回差静态测量时,作为驱动装置。
为了实现不同型号的精密减速器安装,设计精密安装支架,精密减速器通过连接圆盘固定在精密安装支架上,提高装夹的通用性。
被测精密减速器通过专用安装过渡工装安装在减速器支架上,其输入、输出端分别与角度编码器(高精度圆光栅)相连接。
为了消除装偏心引起的测量误差,圆光栅采用双读数头的结构。
各伺服电机、扭矩传感器、被测减速器、陪测减速器均安装在支架上,并且沿同一轴线方向安装到平台基座上。
齿轮接触疲劳试验
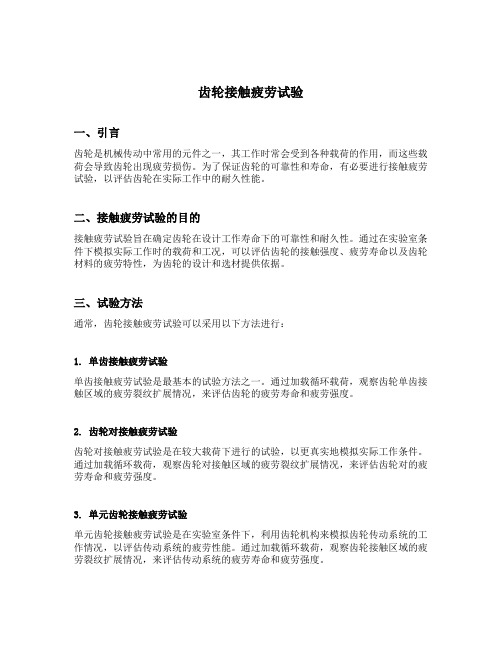
齿轮接触疲劳试验一、引言齿轮是机械传动中常用的元件之一,其工作时常会受到各种载荷的作用,而这些载荷会导致齿轮出现疲劳损伤。
为了保证齿轮的可靠性和寿命,有必要进行接触疲劳试验,以评估齿轮在实际工作中的耐久性能。
二、接触疲劳试验的目的接触疲劳试验旨在确定齿轮在设计工作寿命下的可靠性和耐久性。
通过在实验室条件下模拟实际工作时的载荷和工况,可以评估齿轮的接触强度、疲劳寿命以及齿轮材料的疲劳特性,为齿轮的设计和选材提供依据。
三、试验方法通常,齿轮接触疲劳试验可以采用以下方法进行:1. 单齿接触疲劳试验单齿接触疲劳试验是最基本的试验方法之一。
通过加载循环载荷,观察齿轮单齿接触区域的疲劳裂纹扩展情况,来评估齿轮的疲劳寿命和疲劳强度。
2. 齿轮对接触疲劳试验齿轮对接触疲劳试验是在较大载荷下进行的试验,以更真实地模拟实际工作条件。
通过加载循环载荷,观察齿轮对接触区域的疲劳裂纹扩展情况,来评估齿轮对的疲劳寿命和疲劳强度。
3. 单元齿轮接触疲劳试验单元齿轮接触疲劳试验是在实验室条件下,利用齿轮机构来模拟齿轮传动系统的工作情况,以评估传动系统的疲劳性能。
通过加载循环载荷,观察齿轮接触区域的疲劳裂纹扩展情况,来评估传动系统的疲劳寿命和疲劳强度。
4. 实际工况下的齿轮接触疲劳试验实际工况下的齿轮接触疲劳试验是在实际使用条件下进行的试验。
通过在现场实测齿轮传动系统的负载和工况,并采集相关数据,来评估齿轮的实际疲劳寿命和疲劳强度。
四、试验评估指标在齿轮接触疲劳试验中,通常会评估以下指标:1. 疲劳寿命疲劳寿命指的是齿轮传动系统在特定工作条件下,能够承受多少个循环载荷,而不发生疲劳裂纹和失效。
通过试验数据的统计和分析,可以获得齿轮的疲劳寿命。
2. 疲劳强度疲劳强度是指齿轮传动系统在疲劳载荷下能够承受的最大应力水平。
通过试验中观察到的齿轮裂纹扩展情况,可以评估齿轮的疲劳强度。
3. 裂纹扩展速率裂纹扩展速率是评估齿轮疲劳性能的重要指标之一。
高分子齿轮寿命预测及其疲劳磨损试验装置设计

高分子齿轮寿命预测及其疲劳磨损试验装置设计高分子齿轮是一种新型的传动元件,具有轻质、高强度、低噪音、低摩擦损失等优点,因此在航空、汽车、机械等领域得到了广泛应用。
然而,由于材料的柔软性和易变形性,高分子齿轮在使用过程中容易产生疲劳磨损,进而影响其寿命。
因此,对高分子齿轮的寿命预测以及疲劳磨损试验装置的设计具有重要意义。
针对高分子齿轮的寿命预测,目前已有一些研究成果。
其中,基于有限元模拟的寿命预测方法是目前较为常用的一种方法。
该方法通过建立高分子齿轮的有限元模型,并考虑材料的非线性、疲劳损伤等因素,预测其在不同工况下的使用寿命。
此外,还可以通过试验方法获取高分子齿轮的材料性能参数,进而对其寿命进行预测。
为了研究高分子齿轮的疲劳磨损特性,需要设计一套适用于高分子材料的疲劳磨损试验装置。
该装置应该具有以下特点:1、能够模拟高分子齿轮在不同负载、转速和工作温度下的使用情况;2、能够实现疲劳磨损试验的自动化;3、能够对试验过程进行实时监测和数据采集。
为实现这些要求,可以设计一套基于电机驱动的疲劳磨损试验装置。
该装置主要由电机、传动系统、工作台、负载系统、温度控制系统等组成。
其中,传动系统采用带有高分子齿轮的传动装置,可进行不同负载和转速的试验。
工作台采用冷却式的结构,可以保证试验过程中的工作温度。
负载系统采用电子称重传感器,可实现试验过程中的自动化负载控制。
温度控制系统则采用PID调节器,可对试验过程进行实时的温度监测和控制。
通过上述装置的设计和搭建,可以对高分子齿轮的疲劳磨损特性进行研究。
根据试验数据,可以分析高分子齿轮的疲劳磨损机制,并提出相应的改进方案,从而提高其使用寿命和可靠性。
机械齿轮传动系统的寿命预测与改进

机械齿轮传动系统的寿命预测与改进在现代机械制造中,齿轮传动系统是一种常见且重要的动力传递方式。
不论是工业生产中的机械设备还是家用电器中的齿轮装置,都要求其寿命长、运行稳定。
然而,由于齿轮传动系统复杂的工作环境和承受的压力,其寿命难以预测和延长。
本文将从寿命预测和改进两个方面探讨机械齿轮传动系统的优化。
首先,我们来讨论齿轮传动系统的寿命预测。
齿轮传动系统的寿命预测是指通过分析系统中各个部分的磨损和损坏情况,通过一些计算模型来估计系统的使用寿命。
一个常用的方法是采用传统力学理论中的材料疲劳模型。
通过对材料性能和工作条件的分析,我们可以预测齿轮的剩余寿命。
此外,还可以利用实验手段对齿轮进行压力、转速等各方面的测试,通过统计学方法得出寿命预测结果。
然而,单纯的寿命预测并不能解决齿轮传动系统持续高效运转的问题。
进一步的,我们需要思考如何改进齿轮传动系统,延长其使用寿命。
第一,我们可以优化齿轮的设计和材料选择。
采用更高强度、更耐磨损的材料可以有效提升齿轮的寿命。
此外,合理设计齿轮的齿形和齿距,减少摩擦和失效,也是一个重要的改进方向。
第二,我们可以优化齿轮传动系统的润滑方式。
润滑对于减少齿轮传动系统的磨损和摩擦非常重要。
传统的润滑方式包括液体润滑、脂类润滑和干润滑。
然而,在一些特殊工况下,如高温环境或者高速高负载工作时,常规润滑方式的效果有限。
因此,研究新型润滑剂的使用和应用能够有效提高齿轮传动系统的工作效率和寿命。
第三,我们可以进行齿轮传动系统的故障预警和检测。
通过监测齿轮的振动、温度和噪声等特征,我们可以提前发现潜在的故障点,并采取相应的措施进行修复和维护。
现代技术的发展,如传感器和数据分析算法的应用,使得这项工作变得更加容易和准确。
总结来说,机械齿轮传动系统的寿命预测与改进对于提高机械设备的运行效率和稳定性非常重要。
通过寿命预测,我们可以合理安排设备的维护和更换周期,并提前进行物料准备,减少因突发故障带来的生产损失。
精密齿轮传动装置疲劳寿命试验方法

精密齿轮传动装置疲劳寿命试验方法
对于精密齿轮传动装置的疲劳寿命试验,以下是一种常见的方法:
1. 设计试验样品:根据具体的精密齿轮传动装置设计试验样品,并确保其符合设计规范和要求。
2. 载荷设置:根据实际使用条件和设计要求,确定适当的载荷水平。
这包括确定齿轮传动的扭矩、速度和工作周期等参数。
3. 试验台架搭建:搭建试验台架,确保其稳定和可靠。
试验台架应具备适当的支撑和固定装置,以保持试验样品的准确运行和载荷施加。
4. 开展试验:将试验样品安装到试验台架上,并根据预定的载荷条件进行试验。
试验时间应足够长,以使试验样品经历充分的循环载荷。
5. 监测和记录:在试验过程中,监测并记录关键参数,如载荷、转速、温度等。
这有助于评估试验样品的工作状态和疲劳寿命。
6. 终止试验:当试验样品出现破坏、失效或达到预定寿命时,终止试验。
7. 结果分析:根据试验数据和监测记录,分析试验样品的疲劳性能和寿命。
这包括疲劳强度、疲劳寿命曲线、疲劳损伤特征等。
需要注意的是,精密齿轮传动装置的疲劳寿命试验方法可能因不同的应用和设备要求而有所差异。
因此,在实际应用中,具体的试验方法可能会根据不同的场景和要求进行调
整和优化。
详细了解特定装置的疲劳寿命试验方法,建议参考相关的标准、规范或与专业测试机构进行咨询。
- 1、下载文档前请自行甄别文档内容的完整性,平台不提供额外的编辑、内容补充、找答案等附加服务。
- 2、"仅部分预览"的文档,不可在线预览部分如存在完整性等问题,可反馈申请退款(可完整预览的文档不适用该条件!)。
- 3、如文档侵犯您的权益,请联系客服反馈,我们会尽快为您处理(人工客服工作时间:9:00-18:30)。
2.传递误差/综合质量试验台
(3)主减综合质量试验台
接触斑点,识别分析 振动、噪声,频谱分析 传递误差、综合分析 加载试验
进口:加载,自动检测 综合分析
国产:空载,看斑点、听噪声
3.变速器换挡性能试验台
AMT自动变速器换挡性能试验台
反向驱动 整车惯量 TCU模拟 快速上下料 自动测试
23
4. 倾斜润滑试验台
变速器倾斜润滑试验台
两轴倾斜 正/反驱动 各轴承润滑 空载功率
24
七、总 结
齿轮及齿轮传动系统测试关键:
测试技术 测试装备 测试人才
机械科学研究总院
中机生产力促进中心 制造工程研究所
贴近de技术服务 高端de试验装备 深入de合作研究
地址:北京市 海淀区 首体南路2号,100044 电话:010-88301762/1718/1732 传真:010-68321835
试验要求:载荷大小精确、加载点准确、齿长载 荷分布均匀,装卡方便可靠。
加载工装:技巧,特别是斜齿轮试验。
试验机为通用高频试验机
三、齿轮试验装备
国产高频试验机
德国高频试验机
6
三、齿轮疲劳寿命测试装备
工装夹具是关 键,需要在专 业公司定制 工装要求
1.齿轮装夹方便可靠 2.齿宽方向载荷均布 3.齿顶加载点准确
四、齿轮传动性能测试技术
齿轮传动性能测试包括: 1. 齿轮接触斑点测试 2. 齿轮传递误差测试
12
四、齿轮传动性能测试技术
1. 接触斑点、传递误差、振动噪音的关系
四、齿轮传动性能测试技术
2、传递误差是齿轮啸叫的激励源
扭转振动:φ(t)= φ{ [i (t)-i 0] φ 1(t)}(动态) (1)稳态情况下, φ(t)反映传递误差TE =φ(t) ; (2) 动态情况下,齿轮受迫振动, φ(t)反映
齿轮疲劳寿命测试方法
1. 模拟齿轮啮合过程
用途:主要用于测试接触疲劳和胶合失效测试 特点:接近实际运行情况,效率低
2. 单齿高频加载
用途:用于弯曲疲劳测试 特点:效率高,与实际啮合情况有区别,需标定
二、齿轮疲劳寿命测试技术
影响齿轮疲劳寿命的因素
宏观几何参数 微观几何参数
齿轮材料 热处理及制造工艺
润滑油及温度 表面处理工程等
ω1
ω2
(1) 齿距累积总偏差:Fp
(2) 齿距偏差:fpt
(3) 齿形偏差:Fα,ffα ,fHα (4) 安装偏心:e (5) 轮齿受载变形:δ (6) 轮齿修形:f,等……
偏差特征:
1. 随机性 2. 规律性-不同周期正弦曲线
变形特征:随载荷变化,形状确定
齿距累积总偏差Fp:呈正弦规律+随机性 齿距偏差fpt:呈随机性
4
二、齿轮疲劳寿命测试技术
测试齿轮疲劳寿命的关键
1. 测试目的
S-N曲线?对比测量?其它目的?
2. 试验齿轮设计、制造与检测 3. 试验方案确定
三、齿轮疲劳寿命测试装备
1. 齿轮弯曲疲劳强度试验机及加载夹具 2.齿轮接触疲劳强度试验机
5
三、齿轮疲劳寿命测试装备
1. 弯曲疲劳强度试验机及加载夹具
试验机:高频电磁谐振式试验机,加载频率高: 80~250 Hz,106—1.5h,效率很高。一般不用电 液伺服型试验机频率低,<50Hz。
性能测试:振动、效率、接触斑点 S-N曲线测试:测试齿轮材料S-N曲线,为齿轮正向设
计计算提供可靠的基础依据
8
中机中心引进DU齿轮接触疲劳试验台
三、齿轮疲劳寿命测试装备
160mm、91.5中心距背靠背齿轮疲劳试验机技术参数
序
项目
1 试验齿轮中心距
2 齿轮最大齿宽
3 试验齿轮模数 4 最大试验功率 5 工作转速 6 最大测试扭矩 7 电机功率 8 油温 9 试验齿轮螺旋角 1 主机尺寸 0 控制柜尺寸
单位 mm mm mm
kW rpm Nm kW ℃
mm mm
参数 160
60 2~10
2000 0~4500 6000,±1.5%FS 75
~100 0~30 2800×1230 2000×600
参数 91.5
35 2-5
880 0-6000 2100 30
~130 0~30 1850×800 2000×600
7
三、齿轮疲劳寿命测试装备
背靠背齿轮疲劳试验台原理
试验 齿轮
液压加载器
试验 齿轮
传感器
变频电机
三、齿轮疲劳寿命测试装备
背靠背齿轮疲劳试验机功能:
对比测试:验证齿轮设计、齿轮材料、加工工艺、热 处理参数改进等对齿轮寿命的影响 ,寻找规律
强度测试:用于测试齿轮接触疲劳、弯曲疲劳寿命及 胶合特性 ,质量验证
处
-20 -30
2 2
理
-40 -50
-60
-70
Time, s
Raw Data Timer Filtered Measurement
1
1
0
0
50
100
150
200
250
300
350
400
450
Frequency, Hz
六、齿轮传动系统其它测试装备
常见试验台的类别: 1. 综合性能/疲劳寿命试验台 2. 振动与噪声试验台 3. 传递误差试验台 4. 换挡性能试验台 5. 接触斑点/密封性试验台 6. 倾斜(润滑)试验台 7. 环境试验台……
2.传递误差/综合质量试验台
圆柱齿轮及系统传 递误差试验台
19
2.传递误差/综合质量试验台
传
递
齿轮1
误 齿轮2
差
数
光栅2
1/Z1
计 数 器
数据 采集 卡
据
1/Z2
采
4
集
30 20
4
10
3
与
0
0.0
0.1
0.2
0.3
0.4
0.5
0.6
0.7
0.8
0.9
1.0
3
-10
M icron s M icrons, p-p
加载启动、载荷稳定 转角设定、低速稳定
在疲劳寿命试验 台上无法准确获 得齿轮接触斑点
17
1. 齿轮接触斑点试验台
1. 齿轮接触斑点试验台
接触斑点检测与对比
18
2.传递误差/综合质量试验台
1. 圆柱齿轮传递误差试验台
齿轮副传递误差测试 齿轮轴系传递误差测试
关键技术: •转角精密测量技术 •传递误差信号处理技术 •测试误差修正、补偿技术
9
三、齿轮疲劳寿命测试装备
试验台液压加载器
叶片式:隔振。间隙密封(泄露),加工精度高 扭力杆式:简单,传递扭振,易泄载
齿轮安装结构
锥面轴颈,液压装拆方便,不磨损。 圆柱轴颈,装拆困难,易磨损。
端盖活动支撑
减振弹性支撑 装拆高压油口
10
三、齿轮疲劳寿命测试装备
机械科学研究总院中机生产力促进中心与英国纽卡斯 尔大学齿轮技术研究中心全方位技术合作,为中国企业 提供齿轮疲劳寿命试验设备、合作研究和技术咨询服务。 DU在齿轮试验检测技术世界领先。 贴身服务、快速响应—齿轮试验
(2) 减少振动噪声的途径: 减小传递误差 减小齿轮的振动响应 减小系统的振动响应 隔振、隔噪,减少传播
源头减小
TE激励
响应减小
动态 响应
轮齿: 振动、噪声
传播、响应减少
传播 响应
系统: 振动、噪声
四、齿轮传动性能测试技术
5. 优化齿轮啮合,减小和优化传递误差,降低振动噪音
软件建模 加载分析:不同扭矩下错位分析
齿形偏差Fα,ffα ,fHα:呈正弦规律+随机性
14
h
h
双齿进入啮合 点,产生冲击
齿形变形曲线
K型修形曲线
δ
f
典型的传递误差
不同载荷下的传递误差 (要考虑加载载荷)
不同速度下的传递误差 (要考虑测量方法)
15
四、齿轮传动性能测试技术
4.拟制啸叫的途径:减少传递误差、控制相应传播
(1) 减少传递误差途径: 减少制造误差 进行合理的齿廓修形 减小轮齿刚度变化 减小安装误差
25
26
齿轮修形设计 接触斑点、传递误差模拟分析
样箱制造 接触斑点试验测试
影响系统变形要素调整
不一致
模 拟
传递误差测试
与
测 试
一 致
齿轮
结
修形
果 对
设计 定型
比
综合 分析 确定 解决 方案
分
析
振动噪音测试
16
五、齿轮传动性能测试装备
1. 齿轮接触斑点试验台 2. 齿轮传递误差测试台
1. 齿轮接触斑点试验台
1
一、概述
1. 齿轮疲劳寿命和振动噪音性能是评价齿 轮传动系统优劣的重要指标
2. 测试以提高寿命与噪音性能为目的 3. 科学的测试方法是基础 4. 可靠的测试设备是关键
二、齿轮疲劳寿命测试技术
2
二、齿轮疲劳寿命测试技术
齿轮失效方式
2. 弯曲疲劳
二、齿轮疲劳寿命测试技术
2. 胶合
齿轮失效方式
3
二、齿轮疲劳寿命测试技术
20
1. 综合性能/疲劳寿命试验台
(1)风电齿轮箱电功率封闭试验台
1.综合性能/疲劳寿命试验台
(2)汽车驱动桥电功率封闭试验台
21
1. 综合性能/疲劳寿命试验台
(3)液力封闭试验台
旋挖钻机动力头 动态性能试验台