减阻剂
页岩储层压裂减阻剂减阻机理研究
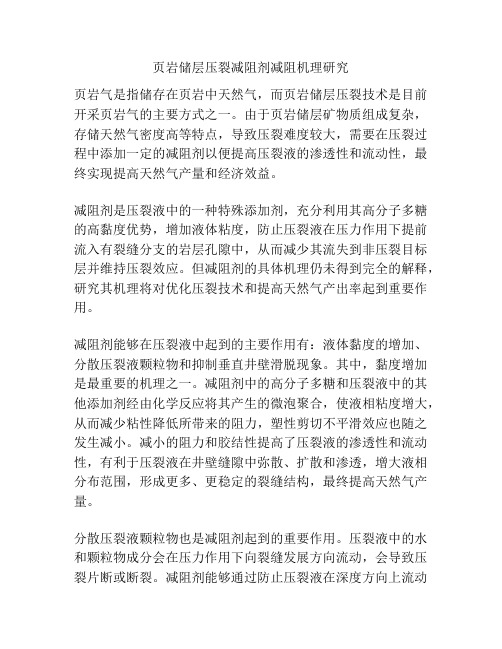
页岩储层压裂减阻剂减阻机理研究页岩气是指储存在页岩中天然气,而页岩储层压裂技术是目前开采页岩气的主要方式之一。
由于页岩储层矿物质组成复杂,存储天然气密度高等特点,导致压裂难度较大,需要在压裂过程中添加一定的减阻剂以便提高压裂液的渗透性和流动性,最终实现提高天然气产量和经济效益。
减阻剂是压裂液中的一种特殊添加剂,充分利用其高分子多糖的高黏度优势,增加液体粘度,防止压裂液在压力作用下提前流入有裂缝分支的岩层孔隙中,从而减少其流失到非压裂目标层并维持压裂效应。
但减阻剂的具体机理仍未得到完全的解释,研究其机理将对优化压裂技术和提高天然气产出率起到重要作用。
减阻剂能够在压裂液中起到的主要作用有:液体黏度的增加、分散压裂液颗粒物和抑制垂直井壁滑脱现象。
其中,黏度增加是最重要的机理之一。
减阻剂中的高分子多糖和压裂液中的其他添加剂经由化学反应将其产生的微泡聚合,使液相粘度增大,从而减少粘性降低所带来的阻力,塑性剪切不平滑效应也随之发生减小。
减小的阻力和胶结性提高了压裂液的渗透性和流动性,有利于压裂液在井壁缝隙中弥散、扩散和渗透,增大液相分布范围,形成更多、更稳定的裂缝结构,最终提高天然气产量。
分散压裂液颗粒物也是减阻剂起到的重要作用。
压裂液中的水和颗粒物成分会在压力作用下向裂缝发展方向流动,会导致压裂片断或断裂。
减阻剂能够通过防止压裂液在深度方向上流动而减少悬挂的颗粒物,从而避免不同层位上物质的界面引起的剪切应力,减轻液流速度对裂缝的破坏作用,从而减少因颗粒物悬浮而形成的流体阻力,最终提高压裂液在岩石中渗透的动态性,增加页岩储层的效率。
抑制井壁滑脱现象是减阻剂起到的另一个机理。
压裂液在井壁接触处的落差和方向变化会产生切割作用和摩擦作用,导致井壁和裂缝的摩擦系数较高,从而影响压裂液渗透的效果,造成压裂效果不佳。
减阻剂通过增加液体粘度,降低入井速率,减少井壁上的切割作用和摩擦作用,从而防止井壁滑落,减小井壁与岩石之间的相对速度,最终减少在井壁和没有被加压的天然气层中的切割、摩擦和其他机械应力的效应。
减阻剂质量标准的详细描述
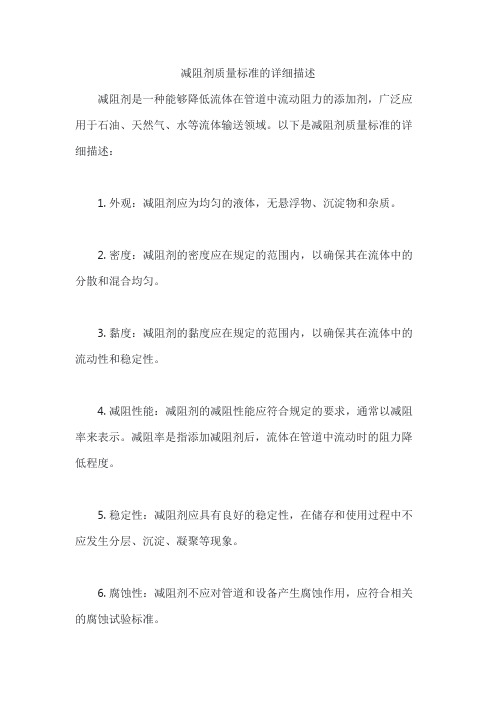
减阻剂质量标准的详细描述
减阻剂是一种能够降低流体在管道中流动阻力的添加剂,广泛应用于石油、天然气、水等流体输送领域。
以下是减阻剂质量标准的详细描述:
1. 外观:减阻剂应为均匀的液体,无悬浮物、沉淀物和杂质。
2. 密度:减阻剂的密度应在规定的范围内,以确保其在流体中的分散和混合均匀。
3. 黏度:减阻剂的黏度应在规定的范围内,以确保其在流体中的流动性和稳定性。
4. 减阻性能:减阻剂的减阻性能应符合规定的要求,通常以减阻率来表示。
减阻率是指添加减阻剂后,流体在管道中流动时的阻力降低程度。
5. 稳定性:减阻剂应具有良好的稳定性,在储存和使用过程中不应发生分层、沉淀、凝聚等现象。
6. 腐蚀性:减阻剂不应对管道和设备产生腐蚀作用,应符合相关的腐蚀试验标准。
7. 毒性:减阻剂不应对人体和环境产生危害,应符合相关的毒性
试验标准。
8. 兼容性:减阻剂应与流体和管道材料兼容,不应发生化学反应
或影响流体的性质。
9. 标识和包装:减阻剂应具有明确的标识,包括产品名称、生产
厂家、批号、生产日期、有效期等信息。
包装应密封、防潮、防泄漏。
以上是减阻剂质量标准的一般要求,具体的标准可能因应用领域和相关法规的不同而有所差异。
在选择和使用减阻剂时,应根据实际需求参考相应的产品标准和规范。
利用减阻剂提高原油管线的输量

利用减阻剂提高原油管线的输量摘要:减阻剂是用于管输流体的一种化学添加剂,可减少流体在管道中的流动阻力,起到增输节能的作用。
文章介绍了原油减阻剂原理、性能、减阻效果的影响因素,在实际生产中运用,产生了增输降耗效果,是一项较有前途的生产技术。
关键词:减阻剂;减阻机理;聚合物;增输率1 减阻剂介绍在液体流动时加入某些特定物质,能大大降低流体在湍流状态下的摩擦阻力,增加输量。
这些特定的物质称为减阻剂,根据使用对象的不同,分为水溶性减阻剂和有油溶性减阻剂。
这里所说的hg 减阻剂是一种应用于原油和成品油管道输送的油溶性化学添加剂,他能降低管路系统的摩阻,提高输送量,降低能耗,提高管线运行的效率及安全性。
该减阻剂是几种α-烯烃的聚合物,聚合单体为c5至c18的α-烯烃,外观为白色的液体,具有可泵性,可溶解于有机溶剂中。
它是纯粹的碳氢化合物,对于炼油工艺无任何影响,其基本特点是添加量小、减阻效果明显、在管输原油和成品油中有良好的溶解性、对下游用户无不良影响。
使用时注入方便、不需要特殊的设备、产品本身无毒副作用等。
不过,减阻剂对流态有严格的要求,管道中的流体必须是湍流。
如果是层流,则减阻剂不起作用,并且只有管道中的直管段产生的摩阻损失才能通过减阻剂来降低,减阻剂不能对管道中弯头、法兰、阀等产生的这部分摩阻损失起作用。
2 hg减阻剂的减阻机理减阻作用是一种特殊的湍流现象,减阻效应是减阻影响湍流场的宏观表现。
它是一个纯物理作用。
减阻剂分子与油品的分子不发生作用,也不影响油品的化学性质,而只与其流动特性密切相关。
减阻剂加入到管道以后,靠本身的粘弹性,分子长链顺流向自然拉伸,其微元直接影响流体微元的运动。
来自流体微元的径向作用力作用在减阻剂微元上,使其发生扭曲,旋转变形。
减阻剂分子间引力抵抗上述作用力反作用于流体微元,改变了流体微元作用力的大小和方向,使一部分径向力转变为顺流向的轴向力,从而减少无用功的消耗,宏观上起到减少摩阻损失的作用。
压裂液减阻剂的类型

压裂液减阻剂(油包水乳液):在油田增产方法操作中,许多的压裂液通过泵在高压力及高流速条件下被运送到深度约500米至6000米或许更深的钻孔处,致使井眼周围的岩层开裂。
油层中的油气在地层压力作用下渗透到井眼分裂处,通过泵又被运送到地上。
压裂液在管道中被运送的过程中,因为来自泵的压力会发生湍流,湍流致使阻力的发生。
阻力会消耗更多的能量。
通常高分子量的线性聚合物可以用于改善流体的流变性质,然后使湍流最小化,然后尽可能的减少在运送过程中丢掉的不必要能量。
压裂液减阻剂(油包水型)在用量很小的情况下减少摩擦阻力,成本低,而且会有高剪切、及抗高温抗高压等出色的功用。
尽管,传统的乳液聚合物具有适合的分子量,但是,体系中因为富含碳氢化合物及表面活性剂,会对环境发生危害,表面活性剂及有机溶剂可能在陆地泄露或许在海上途径发生火灾。
此外,运用前,需要破乳,所以,传统的乳液聚合物的运用遭到约束。
固体聚合物通常在这种运用中被广泛运用,因为固体聚合物的有用浓度比液体聚合物溶液的浓度高许多。
但是,固体聚合物难以溶解,需要格外的设备以及许多的动力和水来稀释产品。
在悠远的钻井现场,动力和水常常供应不上,需要许多的经费投入确保。
压裂液减阻剂
产品形状:乳白色流动性液体
产品特征:溶解快,能耗小,抗剪切性好,无毒无污染,无粉尘,无损健康,流动性好易于操作,格外适宜自动加药,完结出产的自动化。
1、与粉体产品对比,溶解快,药效高,无粉尘无污染,可自动连续加药;
2、与胶体产品对比,溶解快,含量高,粘度低,流动性好,易操作,可自动连续加药;
运用范畴:首要用于页岩气压裂液减阻剂,石油工业用于钻井乳液包被抑制剂,水处理领域等!。
国内压裂用减阻剂的研究及应用进展

国内压裂用减阻剂的研究及应用进展I. 引言- 压裂技术的背景和意义- 减阻剂的作用和研究意义II. 国内压裂用减阻剂研究现状- 减阻剂分类及其特点- 国内压裂减阻剂研究现状概括III. 中国页岩气压裂用减阻剂研究进展- 页岩气压裂工艺特点及影响减阻剂选择的因素- 国内研究现状及进展情况IV. 减阻剂的应用案例- 减阻剂应用案例概括- 减阻剂在实际生产中的效果与问题V. 减阻剂未来发展方向- 未来减阻剂研究需求与趋势- 减阻剂在压裂工艺中的应用前景VI. 结论- 国内减阻剂研究与应用现状综述- 减阻剂在压裂工艺中的影响与前景展望第一章引言随着全球能源消费需求的不断增长,非常规天然气(包括页岩气、煤层气等)的开发越来越引起人们的重视,其中,页岩气是非常规气藏中开发最为活跃、储量最为丰富的一种。
页岩气勘探开发是一种复杂而多变的过程,在生产过程中需要使用许多技术手段来保障高效、经济的生产。
其中,压裂技术被广泛应用于页岩气的开发之中。
压裂技术是利用高压液体将岩石层破碎,从而增加天然气从岩石层中流出的渗透性。
在压裂过程中,需要将高压液体注入到岩石层中,大大增加了注入液体对管道、设备、井壁等系统的腐蚀和磨损。
为了解决这个问题,压裂技术中常常添加减阻剂来减少注入液体对系统的腐蚀和磨损。
本文将介绍国内减阻剂在压裂技术中的研究和应用进展。
本文将从国内压裂用减阻剂研究现状、中国页岩气压裂用减阻剂研究进展、减阻剂的应用案例、减阻剂未来发展方向等方面对其进行探讨。
在大规模应用中,减阻剂的使用既有利于生产效益,同时也提高了生产健康与安全。
因此,减阻剂研究及其应用具有重要的现实意义和广阔的应用前景。
希望本文能够对减阻剂领域感兴趣的专业人员或学者们提供一定的参考价值。
第二章国内压裂用减阻剂研究现状2.1 减阻剂分类及其特点减阻剂是指添加在压裂液中,用来降低液体与管道或岩石壁面摩擦阻力的化学添加剂。
根据其来源和化学特性,减阻剂可以分为有机和无机两类。
减阻、降粘、防蜡

油溶性减阻剂的研究与应用概述
此后几十年,世界上许多国家都进行了对减阻剂的 科研与应用实践,处于领先地位的有美国CONOCO
公司、Baker Hunghes公司,这些公司使得减阻剂
研发技术得到迅速发展,开发出了性能好、成本低 的减阻剂产品。
油溶性减阻剂的研究与应用概述
尤其是CONOCO公司,该公司的减阻剂产品从
油溶性减阻剂的特点
总之,油溶性高分子聚合物减阻剂在很小的用量 下就可以达到和好的效果,例如, CONOCO公司
的CDR102油相减阻剂在添加0.00005(wt)%时,
就可有9%的减阻率(平均流速2.5m/s,管内径 25mm,介质:0号柴油)。添加0.0001(wt)% 即能达到50%的减阻效率,因此在管道运输行业 中被普遍应用。
3、油溶性减阻剂的研究与应用概述
减阻剂的产生:降低摩阻,提高输量,快速缓 解产量与管线输油能力不足之间的矛盾,加速 原油的开发与利用 。 1972年诞生了第一个减阻剂的专利。1979年是 一个转折点,美国CONOCO公司生产的CDR减 阻剂在进行了大量的试验后,正式工业化生产 并应用于横贯阿拉斯加的原油管道上,揭开了 管道运输应用减阻剂的序幕。
称之为原油本体分散减阻,所用的活性剂称之
原油分散剂(dispersant)。
降粘
还有一类减阻剂称之为降摩阻剂(frictional reducer)。 降摩阻剂与降粘剂不同之处在于: 降摩阻剂一般不掺水或掺少量水(5%~10%), 它通过改变原油和介质表面的作用力,进而减 小原油的流动阻力。而乳化降粘一般掺水为 30%左右,通过改变原油乳状液的类型,使其 转变为以水为连续相,油为分散相的水包油的 乳状液,进而降低在原油在流动过程中的阻力。 如果条件允许,可以掺稀油(轻油)输送稠油。
减阻剂研究概述
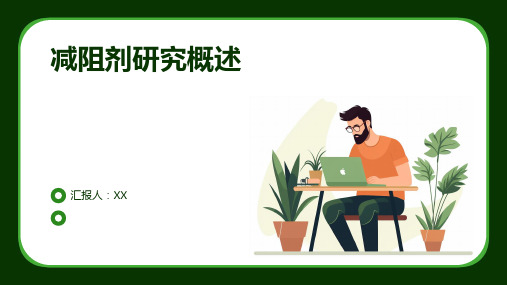
人工智能、大数据等智能化技术有望在减阻剂性 能预测、优化设计等方面发挥重要作用,提高研 究效率和应用水平。
06
结论与建议
研究成果总结
01
减阻剂能有效降低流体在管道中的摩擦阻力,提高流体的输送效率。
02
不同类型的减阻剂在不同流体和管道条件下具有不同的减阻效果,需 要根据实际情况进行选择。
复合型减阻剂
将不同类型减阻剂进行复合,发挥各自优势,提高综 合减阻效果。
03
减阻机理与方法
边界层控制理论
边界层概念
在流体与固体壁面之间形成的薄层,其中流体速度从零逐渐增加 到主流速度。
边界层分离
当边界层内的流体受到逆压梯度作用时,流体会从壁面分离,形成 涡旋和阻力。
减阻方法
通过改变边界层内的流动状态,如增加壁面粗糙度、引入吹气或吸 气等方式,可以延缓边界层分离,从而降低阻力。
数值模拟精度有待提高
数值模拟方法虽然具有成本低、周期短等优点,但目前数值模拟精度仍有待提高,特别 是对于复杂流动和新型减阻剂的模拟预测。
未来发展趋势预测
1 2 3
新型减阻剂研发
随着材料科学和纳米技术的发展,未来有望研发 出性能更优、环境友好的新型减阻剂。
多学科交叉融合
减阻剂研究涉及流体力学、化学、材料科学等多 个学科领域,未来多学科交叉融合将成为推动减 阻剂研究发展的重要趋势。
表面活性剂减阻剂
界面活性
01
表面活性剂能降低流体与固体壁面间的界面张力,减少流动阻
力,提高流体的流动性。
吸附作用
02
表面活性剂在固体壁面上形成吸附层,改变壁面润湿性,降低
摩擦阻力。
泡沫与乳状液
03
部分表面活性剂可形成泡沫或乳状液,进一步降低流动阻力。
高抗盐减阻剂的合成及性能评价

第52卷第12期 辽 宁 化 工 Vol.52,No.12 2023年12月 Liaoning Chemical Industry December,2023收稿日期: 2023-11-08 作者简介: 孙建波(1988-),男,山东省潍坊市人,工程师,硕士,2015年毕业于西南石油大学石油与天然气工程专业,研究方向:聚丙烯酰高抗盐减阻剂的合成及性能评价孙建波,任凯*,于朋朋,赵桃桃,景晓雅(山东诺尔生物科技有限公司, 山东 东营 257000)摘 要:以丙烯酰胺、2-丙烯酰胺-2-甲基丙磺酸、十六烷基丙烯酰胺为单体,自制低聚物为分散剂,氧化还原体系为引发剂合成了高抗盐减阻剂。
通过测定聚合物的溶解速度以及不同浓度、不同矿化度条件下的减阻率,来评价合成减阻剂的减阻性能,通过实验可知,高抗盐减阻剂在10%氯化钙条件下具有76%以上的减阻率;通过测定聚合物的交联悬砂性能以及流变性能,来表征压裂液增稠剂的应用效果,通过实验可知,压裂液增稠剂具有优异的悬砂性能,且具有良好的流变性能。
关 键 词:减阻剂; 聚丙烯酰胺; 水包水; 抗盐性能中图分类号:TE357.1 文献标识码: A 文章编号: 1004-0935(2023)12-1807-04水包水PAM 是一种新型的聚丙烯酰胺产品形态。
阴离子水包水PAM 作为滑溜水减阻剂,具有溶解速度快、能耗低、环保安全、固含量高等特点,特别适用于不具备安装大型溶解装置的施工现场。
本文以丙烯酰胺、2-丙烯酰胺-2-甲基丙磺酸和十六烷基丙烯酰胺为单体,自制低聚物为分散剂,氧化还原体系为引发剂合成了高抗盐减阻剂。
1 实验部分1.1 实验试剂丙烯酰胺、丙烯酸,工业级,山东诺尔生物科技有限公司;2-丙烯酰胺基-2-甲基丙磺酸,工业级,山东联盟化工集团有限公司;N-十六烷基丙烯酰胺,工业级,广东翁江化学试剂有限公司;十二烷基硫酸钠,工业级,山东旺通化工有限公司;交联剂,自制;氢氧化钠、无水氯化钙、六水氯化镁、氯化钠、甲酸钠、过硫酸钾、亚硫酸氢钠,分析纯,国药集团化学试剂有限公司。
减阻剂

(1)大幅度节省新建管线建设投资。新 管线设计中一个重要的依据就是管道的 年 输量,但对管道年输量影响因素有许 多是 不确定的。如对油田储量的估测不 可能做 到十分精确,市场条件要求管道 输量的变 化及油品种类的改变等等。这 一些不确定 的因素,可根据相对经济的 数据作为设计 依据,留下一部分设计余 量,用减阻剂来平 衡这部分余量。减小 管径、压缩泵站建设规 模可大大节省新 管线的建设投资。
2 输油管道应用减阻剂后的减阻与 增输
2 .1 减阻剂减阻与增输的含义 在管道输油过 程中加入减阻剂,可以 有两个方面的作用: (1)在原定输量不变的条件下,降低油 流摩阻, 减少管道沿程压头损失,从而降低了泵的动力消 耗,节约了能量,可以改换成 扬程较低的泵输油。 (2)在原定压力不变的条件下,由于油 流摩阻降 低,而输量增加;在多数情况下, 使用减阻剂 是为了增加管道的输量,增输 是由于减阻的作 用而实现的。
2.3 减阻剂的应用和减阻增输效果 2.3.1 输油管道适于应用减阻剂的 情况 减阻剂发展到目前阶段,多在下列情 况下, 作为一种短期的、权宜性的或特殊处 理手段 而采用: ①季节性输油任务的波动; ②暂时性的输油任务的高峰; ③根据市场需求时增加输量(这种情况 在国外 尤为多见); ④管道超过额定输油能力,暂时来不 及扩建, 或在一定的超额范围内不准备扩 建;
1 减阻剂的减阻机理
减阻作用是—种特殊的湍流现象,减 阻 效应是减阻影响湍流场的宏观表现。它 是 一个纯物理作用。减阻剂分子与油品的 分 子不发生作用,也不影响油品的化学性 质, 而只与其流动特性密切相关。减阻剂加入到 管道以后,靠本身的粘 弹性,分子长链顺 流向自然拉伸,其微元直 接影响流体微元 的运动。来自流体微元的 径向作用力作用 在减阻剂微元上,使其发 生扭曲,旋转变 形。减阻剂分子间引力抵抗 上述作用力反 作用于流体微元,改变了流体微元作用力的 大小和方向, 使一部分径向力转变为顺流 向的轴向力, 从而减少无用功的消耗,宏 观上起到减少 摩阻损失的作用。
减阻剂的原理及应用
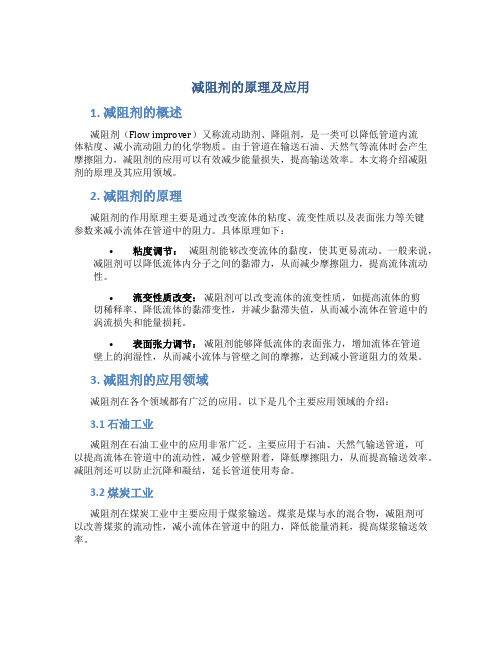
减阻剂的原理及应用1. 减阻剂的概述减阻剂(Flow improver)又称流动助剂、降阻剂,是一类可以降低管道内流体粘度、减小流动阻力的化学物质。
由于管道在输送石油、天然气等流体时会产生摩擦阻力,减阻剂的应用可以有效减少能量损失,提高输送效率。
本文将介绍减阻剂的原理及其应用领域。
2. 减阻剂的原理减阻剂的作用原理主要是通过改变流体的粘度、流变性质以及表面张力等关键参数来减小流体在管道中的阻力。
具体原理如下:•粘度调节:减阻剂能够改变流体的黏度,使其更易流动。
一般来说,减阻剂可以降低流体内分子之间的黏滞力,从而减少摩擦阻力,提高流体流动性。
•流变性质改变:减阻剂可以改变流体的流变性质,如提高流体的剪切稀释率、降低流体的黏滞变性,并减少黏滞失值,从而减小流体在管道中的涡流损失和能量损耗。
•表面张力调节:减阻剂能够降低流体的表面张力,增加流体在管道壁上的润湿性,从而减小流体与管壁之间的摩擦,达到减小管道阻力的效果。
3. 减阻剂的应用领域减阻剂在各个领域都有广泛的应用。
以下是几个主要应用领域的介绍:3.1 石油工业减阻剂在石油工业中的应用非常广泛。
主要应用于石油、天然气输送管道,可以提高流体在管道中的流动性,减少管壁附着,降低摩擦阻力,从而提高输送效率。
减阻剂还可以防止沉降和凝结,延长管道使用寿命。
3.2 煤炭工业减阻剂在煤炭工业中主要应用于煤浆输送。
煤浆是煤与水的混合物,减阻剂可以改善煤浆的流动性,减小流体在管道中的阻力,降低能量消耗,提高煤浆输送效率。
3.3 化工工业减阻剂在化工工业中的应用也比较常见。
化工行业中常涉及到输送各种液体和气体,减阻剂可以提高流体在管道中的流动性,降低阻力,节省能源。
同时,减阻剂还可以减少管道堵塞和冲蚀的发生,减少设备维护和停机时间。
3.4 其他领域除了上述主要应用领域外,减阻剂还广泛应用于水处理、污水处理、食品工业、造纸工业等领域。
在这些领域中,减阻剂可以改善流体在管道中的流动特性,提高输送效率,减少能源消耗。
减阻剂在输油管道中的应用

减阻剂在输油管道中的应用发布时间:2021-07-26T10:15:57.043Z 来源:《科学与技术》2021年9期作者:朱晓东[导读] 液体在管道中流动时有两种流动状态,一种是层流,朱晓东华东管道设计研究院有限公司江苏徐州 221008摘要:液体在管道中流动时有两种流动状态,一种是层流,另一种是紊流,通常采用雷诺数(Re)来确定流动状态。
流体在管道中流动时受管道沿程阻力和局部阻力的影响,导致系统能量消耗,降低管道输送能力和输送效率。
减阻剂是一种长链、高分子量聚合物,可降低摩擦压力损失,提高烃类产品在管道中的流量,是油品管道输送系统中的重要组成部分,可降低输油管道运行的总能耗费用,提高管道输送效率。
关键词:减阻剂;输油管道;应用引言减阻剂是一种广泛用于原油管道运输的化学添加剂。
它可以有效地减少原油和精炼石油管道运输的摩擦和能源消耗,抑制流量中的石油波动程度,降低流量阻力。
它可以有效提高管道输送能力,减少管道压力,节约能源,提高管道运行的安全系数而不增加设备。
1减阻剂的减阻机理减阻剂通过改变管道中流体的流动状态,具体通过影响湍流场的宏观表现来实现减阻作用。
减阻作用只是单纯的物理作用,减阻剂不与油品物质发生化学反应,所以不影响油品的化学性质,只对其流动特性产生影响。
减阻剂进入流体中后,由于其具有粘弹性,分子链沿流体流向方向自然伸展,从而对流体分子的运动产生影响。
减阻剂分子受到流体分子径向作用力,发生扭曲变形的同时,因其分子间引力而对流体分子产生反作用力。
受到该反作用力的影响,流体分子作用力方向和大小发生改变,一部分径向作用力转变为顺流向的轴向作用力,无用功的消耗降低,宏观上起到减少摩阻损失的作用。
2减阻剂的减阻作用减阻剂注入油品后,能限制油品分子径向运动,使其沿减阻剂长链分子方向运动(即沿管道方向运动),有效减小油品的紊流程度。
根据流体力学原理,层流趋势越高,摩阻系数越小,减阻剂便是通过这种方式实现减阻、增输的目的。
减阻剂
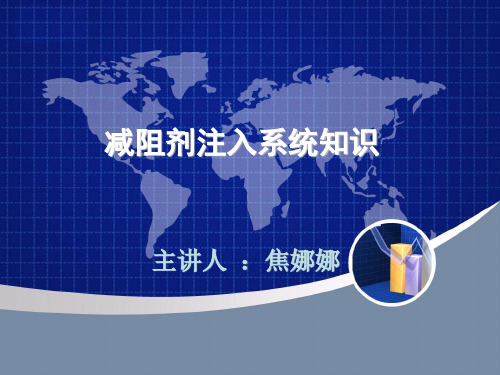
1.根据抄表底数计算本日注入量操作
本日注入量(m3)=(本日底数 – 昨日底数)× 3.785 / 1000
2.根据中控调度室下达的注入浓度值(ppm)通过浓度与加仑量换算公式 算出每小时需要的注入量(美制加仑/小时)
• 常用单位换算关系 1立方米=1000升 1升=0.2642美制加仑 1美制加仑=3.785升
储存温度
EP系列减阻剂的储存温度不应超过35℃,应避免因直接暴露于太阳光和其它高热热 源里引起的过热。搅拌罐液位应保持在最少1/3。醇基产品的储存环境温度必须保
持在-35℃以上。
谢 谢!
出题
选择题: EP系列减阻剂的储存温度不应超过( ) a.45℃ b.40℃ c.35℃ d.30℃ • 搅拌罐液位应保持在最少1/3 • 1立方米=1000升 • 循环泵压力表范围在0.1MAP—0.2MAP 减阻剂启动操作
操作柱总电源控制旋钮
(5)按下电源控 制柱搅拌泵 “启 动”电源开关, 搅拌罐启动,对 减阻剂溶剂进行 搅拌。
搅拌泵启停按钮
提料泵启停按钮
(6)将减阻剂撬座电 源控制面总开关旋钮 向至“ON”,给减阻 剂系统送电,循环泵 BYASS至“ON”,两台 计量泵(ECC1、ECC2) 在“ON”上。
减阻剂撬座电源控制面板
目
测
7
目
测
风险提示及风险削减、预控措施
序号
风险提示
风险削减、预控措施
1
中
毒
检查搅拌罐液位时,佩戴防毒面具。
2
触
电
电源侧安装漏电保护器,设备外壳接地良好。
五.桶装减阻剂向搅拌罐加剂操作
(1)连接桶装减阻剂下出料口与提料泵之间的软管并上紧卡箍。 (2)搅拌桶装减阻剂内溶剂,消除分层现象,使其均匀分布。 (3)导通桶装减阻剂至搅拌罐之间的流程。 (4)按下提料泵“启动”电源开关,提料泵向搅拌罐内加剂。 (5)加剂操作完毕后,按下提料泵“停止”电源开关,提料泵停止工作。 (6)拆卸桶装减阻剂下出料口与提料泵之间的软管。 (7)清理现场,将空桶在减阻剂区摆放整齐。 (8)汇报站值班干部、站长、兰州调度,并做好记录。
原油减阻剂的研究概况

原油减阻剂的研究概况宋昭峥 张雪君 葛际江(石油大学 山东省东营市 257062) 摘要 减阻剂是一种高分子聚合物的化学制品,能减少液体在管道内流动的摩阻。
减阻剂的使用,对输油管道的增输、节能降耗、提高经济效益和社会效益起到重要的作用。
减阻剂的研究热点仍是开发新产品及新合成方法。
通过改变单体种类、结构单元连接方式、序列分布和单体组分组成,可以合成品种众多的聚合物,为制备具有指定结构和预期性能的高分子聚合物减阻剂提供了可能性和可行性。
主题词 原油 降阻剂 聚合物长输管道 化学处理剂 合成 分子量 减阻剂是一种减少管道摩阻损失的化学制品,是高分子聚合物,属于碳氢化合物。
40年代后期,催化剂与添加剂的研究取得了巨大的进展,为石油炼制工业提供了有利条件,使炼制成品收率大大提高,产品质量也有了极大的改进。
接着添加剂又进入了油田,为油田开发做出了巨大的贡献。
到70年代,减阻剂才开始逐渐进入管道工业。
输油管道对铁路、公路、水路要有竞争力,采用的化学剂要求高效、低价,但减阻剂要在经济上可行,还需要做许多工作。
1979年横贯阿拉斯加的原油管道成功地应用了高分子聚合物减阻剂,为减阻剂在输油工业上的应用打开了局面,使输油工艺出现了一个飞跃。
1.减阻剂的发展概况20世纪30年代初,人们肯定了在液体中加入某些可溶添加物,有可能减少表面摩阻。
1945~1946年,国外才正式开展减阻剂的研究。
1948年, B1A1T oms首次发现高分子聚合物在紊流时的减阻现象,引起了化学界、物理学界、流体力学界和高分子学界的广泛注意。
1949年,注册了第一个减阻剂专利。
50年代发展了油田压裂技术,井场上使用某些高分子聚合物,如G uar胶稳定钻井泥浆,发现这些添加物质能使压裂过程中泵的功率有明显下降。
Savins捕捉到这些现象的实际意义,命名此种现象为“减阻”。
他定义“减阻”为“在流体中添加少量添加剂,流体可输性的增加”。
大量的实验研究表明,不溶的固体纤维、可溶性的长链聚合物和缔合胶体均有一定的减阻效应。
管道减阻剂在原油管道运输中的应用

管道减阻剂在原油管道运输中的应用关键词:减阻剂延长石油减阻增输原油在进行管道运输时,管道中的原油由于摩擦阻力的存在而限制了其在管道中的流动,造成了管道运输效率的降低,增加了能量消耗。
减阻剂的注入可以在不改变管道运行方式的条件下,有效的降低管道中流体的摩擦阻力,提高管道的输送能力。
管道减阻剂是一种可以降低流体流动摩阻,增加输送量的高分子添加剂,对输送管道的增输、节能、提高经济效益有非常重要的作用。
一、管道减阻剂减阻机理原油在管道运输过程中,随着管道摩阻的增加,原油的层流部分将会逐渐减少,紊流部分将会增加。
处于紊流状态的原油中有很多漩涡,而这些旋涡是逐级变小的,旋涡的尺度越小,能量的粘滞损耗越大,旋涡的能量最终将被流体的粘滞力损耗掉,变成热能,因此处于紊流状态的原油需要消耗大量的管输能量[1]。
管道的中心区是紊流核心区,管内大部分流体处于这一区,只有靠近管壁的很少部分的液体运动为层流,这两者之间有一过渡区。
减阻剂就是通过改变管壁附近(过渡区)油分子的运动状态,使其向同一方向运动,以扩大已有的层流区,减少能量消耗,降低摩阻损失,以达到减阻增输的目的[2]。
同时,处于紊流状态下的原油中各级旋涡将能量传递给减阻剂分子,使其发生弹性变形,将能量储存起来,之后,减阻剂分子又将获得的能量还给油分子,以维持原油正常运输所必需的能量,达到减阻的目的[3]。
值得注意的是只有当原油处于紊流状态时,减阻剂才起减阻作用。
二、原油管道应用阻剂后的减阻增输效果减阻剂的减阻与增输即为:减阻:在原定输量不变的情况下,降低原油流动摩阻,减少管道沿程压力损失,从而减低泵的动力消耗,节约了能量,可以改换成扬程较低的泵输油。
增输:在原定压力不变的条件下,由于原油流动摩阻降低,而输量增加;在多数情况下,使用减阻剂是为了增加管道的输量,增输是由于减阻的作用而实现的。
使用减阻剂减阻或增输,不需要扩展原有管道工程规模,不需增设泵站或建管道复线,也不需要更换输油设备即可达到提高管道输送能力的目的。
减阻剂

减阻机理减阻的机理说法很多,尚无定论。
如伪塑说、湍流脉动抑制说、粘弹说、有效滑移说、湍流抑制说等等。
油相减阻剂从其结构看,多数是流状链或长直链少侧链的高分子聚合物,如CDR102是高分子聚-σ烯烃,分子量为10~10。
这种高分子聚合物纯剂为橡胶状固体,作为商品,一般是溶在烃类(煤油)的溶液中。
10%的减阻剂溶液呈非常粘稠的粘弹性体,较难流动,可拔成很长的丝。
高聚物减阻剂能溶于原油或油品中,但不溶于水,遇水发生分子长链卷曲。
减阻剂溶液呈强牛顿特性,低剪切率下粘度高达3000Pa·S,120℃以下不会分解,比较稳定。
减阻作用是一种特殊的湍流现象,减阻效应是减阻影响湍流场的宏观表现,它是一个纯物理作用。
减阻剂分子与油品的分子不发生作用,也不影响油品的化学性质,只是与其流动特性密切相关。
在湍流中,流体质点的运动速度随机变化着,形成大大小小的旋涡,大尺度旋涡从流体中吸收能量发生变形、破碎,向小尺度旋涡转化。
小尺度旋涡又称耗散性旋涡,在粘滞力作用下被减弱、平息。
它所携带的部分能量转化为热能而耗散。
在近管壁边层内,由于管壁剪切应力和粘滞力的作用,这种转化更为严重。
在减阻剂加入到管道以后,减阻剂呈连续相分散在流体中,靠本身特有的粘弹性,分子长链顺流向自然伸呈流状,其微元直接影响流体微元的运动。
来自流体微元的径向作用力作用在减阻剂微元上,使其发生扭曲,旋转变形。
减阻剂分子间的引力抵抗上述作用力反作用于流体微元,改变流体微元的作用方向和大小,使一部分径向力被转化为顺流向的轴向力,从而减少了无用功的消耗,宏观上得到了减少摩擦阻力损失的效果。
在层流中,流体受粘滞力作用,没有像湍流那样的旋涡耗散,因此,加入减阻剂也是徒劳的。
随着雷诺数增大进入湍流,减阻剂就显露出减阻作用。
雷诺数越大减阻效果越明显。
当雷诺数相当大,流体剪切应力足以破坏减阻剂分子链结构时,减阻剂降解,减阻效果反而下降,甚至完全失去减阻作用。
减阻剂的添加浓度影响它在管道内形成弹性底层的厚度,浓度越大,弹性底层越厚,减阻效果越好。
减阻剂成分
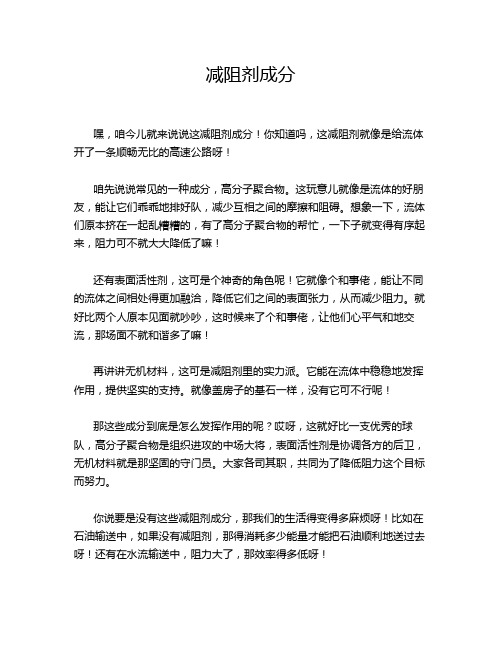
减阻剂成分
嘿,咱今儿就来说说这减阻剂成分!你知道吗,这减阻剂就像是给流体开了一条顺畅无比的高速公路呀!
咱先说说常见的一种成分,高分子聚合物。
这玩意儿就像是流体的好朋友,能让它们乖乖地排好队,减少互相之间的摩擦和阻碍。
想象一下,流体们原本挤在一起乱糟糟的,有了高分子聚合物的帮忙,一下子就变得有序起来,阻力可不就大大降低了嘛!
还有表面活性剂,这可是个神奇的角色呢!它就像个和事佬,能让不同的流体之间相处得更加融洽,降低它们之间的表面张力,从而减少阻力。
就好比两个人原本见面就吵吵,这时候来了个和事佬,让他们心平气和地交流,那场面不就和谐多了嘛!
再讲讲无机材料,这可是减阻剂里的实力派。
它能在流体中稳稳地发挥作用,提供坚实的支持。
就像盖房子的基石一样,没有它可不行呢!
那这些成分到底是怎么发挥作用的呢?哎呀,这就好比一支优秀的球队,高分子聚合物是组织进攻的中场大将,表面活性剂是协调各方的后卫,无机材料就是那坚固的守门员。
大家各司其职,共同为了降低阻力这个目标而努力。
你说要是没有这些减阻剂成分,那我们的生活得变得多麻烦呀!比如在石油输送中,如果没有减阻剂,那得消耗多少能量才能把石油顺利地送过去呀!还有在水流输送中,阻力大了,那效率得多低呀!
咱再想想,要是汽车的发动机里能有更好的减阻剂成分,那汽车跑起来不就更省油、更顺畅了嘛!这可不是我在这儿瞎吹,这是实实在在有可能实现的呀!
所以说呀,这减阻剂成分可真是太重要啦!它们就像是幕后的英雄,默默地为我们的生活带来便利和高效。
咱可得好好感谢这些小小的成分呢,它们虽然不起眼,但是作用可大着呢!它们让我们的生活变得更加美好,更加顺畅,难道不是吗?。
- 1、下载文档前请自行甄别文档内容的完整性,平台不提供额外的编辑、内容补充、找答案等附加服务。
- 2、"仅部分预览"的文档,不可在线预览部分如存在完整性等问题,可反馈申请退款(可完整预览的文档不适用该条件!)。
- 3、如文档侵犯您的权益,请联系客服反馈,我们会尽快为您处理(人工客服工作时间:9:00-18:30)。
减阻剂(兰州输油气公司张家川维抢修队甘肃天水 745000)摘要:用于降低流体流动阻力的化学剂称为减阻剂(drag reducing agent),简称DRA。
减阻剂广泛应用于原­油和成品油管道输送,它是在特定地段提高管道流通能力和降低能耗的重要手段。
作者在《浅谈减阻剂》一文中介绍了减阻剂的发展历史、减阻机理、生产工艺、新动向及在国内外输油管道应用的实例;分析了在输油管道中应用减阻剂的优势。
关键词:流体减阻剂降耗聚合物前言流体的摩擦阻力限制了流体在管道中的流动,造成管道输量降低和能量消耗增加,而高聚物减阻法是在流体中注入少量的高分子聚合物,使之在紊流(速度、压强等流动要素随时间和空间作随机变化,质点轨迹曲折杂乱、互相混掺的流体运动。
)状态下降低流动的阻力。
主体一、减阻及减阻剂的发展历史减阻的概念早在20世纪40年代就已经提出。
20世纪初美国纽约的消防队员曾使用水溶性聚合物增加排水系统的流量。
1948年Toms(汤姆斯)在第一届国际流变学会议上发表了第一篇有关减阻的论文,文章指出,以少量的聚甲基丙烯酸甲酯(PMMA)溶于氯苯中,摩阻可降低约50%,因此,高聚物减阻又称为Toms(汤姆斯)效应。
20世纪60年代末,美国Conoco(康诺克)公司研制成CDR-101型减阻剂,1972年取得专利,1977~1979年间首次商业化应用于横贯阿啦斯加的原油管道的越站输送及提高输量方面,并取得巨大成功。
1981年又研制成功CDR-102型减阻剂,比CDR-101型的性能成数倍地提高。
20世纪80年代初,开展了成品油管道的减阻试验,用于汽油、煤油、柴油和NGL(液化天然气)、LPG(液化石油气)的减阻,到1984年正式在成品油管道上应用。
70年代中期,美国Shellco(壳牌)公司和加拿大Shell Inc(壳牌)公司提出申请减阻剂专利。
1983年,美国Atlantic Richfield co(大西洋富田)公司研制出Arcoflo(艾少芬)减阻剂产品,加入5ppm(百万分之)即可达到20%的减阻效果。
减阻聚合物的生产条件很难控制,国际上只有极少数公司垄断了这项技术,其代表是美国的Conoco(康诺克)公司和Baker Hughes(贝克休斯)公司,他们的产品基本上代表了目前世界上减阻剂生产工艺的最高水平和发展方向。
1982年,我国浙江大学开始国产减阻剂的开发和试验工作,1985年进行了EDR型减阻剂的试生产,并在国内原油管道上进行了中型试验,产品性能已达到国外70年代初期水平。
1984年,成都科技大学也发表了PDR型减阻剂的研制成果,以上两校的试验,都曾采用过柴油和煤油等成品油。
近年来,中国石油管道公司管道科技研究中心开展了减阻剂的研究工作,并取得了成功,其EP系列减阻剂产品的性能已经达到国际同类产品的水平。
二、减阻剂的减阻机理减阻的机理说法很多,尚无定论。
如伪塑说、湍流脉动抑制说、粘弹说、有效滑移说、湍流抑制说等等。
油相减阻剂从其结构看,多数是流状链或长直链少侧链的高分子聚合物,如CDR102是高分子聚-σ(德尔塔)(密度)烯烃(细听),分子量为106~107。
这种高分子聚合物纯剂为橡胶状固体,作为商品,一般是溶在烃(听)类(煤油)的溶液中。
10%的减阻剂溶液呈非常粘稠的粘弹性体,较难流动,可拔成很长的丝。
高聚物减阻剂能溶于原­油或油品中,但不溶于水,遇水发生分子长链卷曲。
减阻剂溶液呈强牛顿特性,低剪切率下粘度高达3000Pa·S(帕秒),120℃以下不会分解,比较稳定。
减阻作用是一种特殊的湍流现象,减阻效应是减阻影响湍流场的宏观表现,它是一个纯物理作用。
减阻剂分子与油品的分子不发生作用,也不影响油品的化学性质,只是与其流动特性密切相关。
在湍流中,流体质点的运动速度随机变化着,形成大大小小的旋涡,大尺度旋涡从流体中吸收能量发生变形、破碎,向小尺度旋涡转化。
小尺度旋涡又称耗散性旋涡,在粘滞力作用下被减弱、平息。
它所携带的部分能量转化为热能而耗散。
在近管壁边层内,由于管壁剪切应力和粘滞力的作用,这种转化更为严重。
在减阻剂加入到管道以后,减阻剂呈连续相分散在流体中,靠本身特有的粘弹性,分子长链顺流向自然延伸呈流状,其微元直接影响流体微元的运动。
来自流体微元的径向作用力作用在减阻剂微元上,使其发生扭曲,旋转变形。
减阻剂分子间的引力抵抗上述作用力反作用于流体微元,改变流体微元的作用方向和大小,使一部分径向力被转化为顺流向的轴向力,从而减少了无用功的消耗,宏观上得到了减少摩擦阻力损失的效果。
在层流中,流体受粘滞力作用,没有像湍流那样的旋涡耗散,因此,加入减阻剂也是徒劳的。
随着雷诺数增大进入湍流,减阻剂就显露出减阻作用。
雷诺数越大减阻效果越明显。
当雷诺数相当大,流体剪切应力足以破坏减阻剂分子链结构时,减阻剂降解,减阻效果反而下降,甚至完全失去减阻作用。
减阻剂的添加浓度影响它在管道内形成弹性底层的厚度,浓度越大,弹性底层越厚,减阻效果越好。
理论上,当弹性底层达到管轴心时,减阻达到极限,即最大减阻。
减阻效果还与油品粘度、管道直径、含水、清管等因素有关。
三、减阻剂的生产工艺减阻剂生产的技术关键主要包括两个方面,一是超高分子量、非结晶性、烃类溶剂可溶的减阻聚合物的合成;二是减阻聚合物的后处理。
1.聚合物的合成大量文献资料表明,目前最有效的减阻聚合物是聚α(阿尔法)-烯烃。
早期聚α(阿尔法)-烯烃的生产采用溶液聚合的方法进行,并将聚合产物直接用于输油管道,由于溶液聚合产物本身粘度大,聚合物含量低,因此给运输和使用带来极大的困难。
直到20世纪90年代中期,才发展了本体聚合的方法,从而大大提高了单体转化率和减阻剂性能。
实施本体聚合需要解决的关键技术是及时带走聚合过程中产生的大量反应热,方法之一是使用一种由高分子材料制成的反应容器,并将其设计成能将反应热迅速释放出来的形状。
实施聚合时,先用氮气吹扫反应容器,然后按比例加入单体和催化剂,密封后放入低温介质中,使其在低温下反应3~6天的时间。
一般情况下,本体聚合产物纯度高,分子量也比溶液聚合产物高得多。
另外,采取溶液聚合α(阿尔法)-烯烃减阻聚合物也有了新突破,通过在α(阿尔法)-烯烃聚合过程中加入粘度降低剂,可以改进成品的总体流动性能和处理特性,同时可以获得更高的聚合物分子量和更均匀的分子量分布,改进聚α(阿尔法)-烯烃类减阻剂的溶解性。
2.聚合物的后处理实际应用表明,直接将溶液聚合产物作为减阻剂使用,会给输油生产带来诸多不便,因而该方法现已被淘汰;。
为了改善减阻剂的使用性能,通常将聚合物和分散剂一起在低于其玻璃化温度的环境中磨成粉末,并加入适当的添加剂以制成不同外观形态的减阻剂产品。
目前,在原油管道上广泛使用的是水基乳胶状减阻剂,它是利用稳定剂、表面活性剂等添加剂,将聚合物粉末悬浮在水或水与醇的混合物中。
这种产品具有聚合物浓度高、注入方便、在原油中溶解性好等优点,但也存在储存时间短、稳定性较差等缺点。
在成品油管道中主要使用低粘度胶状减阻剂,它是将聚合物粉末溶解在成品油或成品油和某些溶剂的混合物中。
这种产品具有粘度低、注入方便等优点,但存在聚合物浓度低、运输工作量大等缺陷。
为了克服上述两种产品的缺陷,最近研制开发了一种非水基悬浮减阻剂,它是借助悬浮剂将聚合物粉末悬浮在醇类流体中。
这种减阻剂的生产无需使用表面活性剂、杀菌剂和复杂的稳定剂体系,简化了生产过程,具有防冻性好、聚合物浓度高、稳定性好、能防止水等杂质进入输油管道等优点,并可同时用于原油和成品油的输送。
本体聚合产物可以直接置于低温环境中磨碎,溶液聚合产物则需要先将聚合物从溶剂中沉淀出来,然后粉碎。
美国Conoco(康诺克)公司和Baker Hughes(贝克休斯)公司分别采用了将聚合物从溶液中沉淀出来的方法,用能够沉淀聚合物而与烃类溶剂不互溶的醇类作为沉淀剂,并通过特殊的装置使沉淀出来的聚合物形成小颗粒。
值得一提的是,Baker Hughes(贝克休斯)公司通过控制向溶液聚合产物中加入沉淀剂的速度,以及适当的搅拌将沉淀出来的聚合物颗粒直径控制在0.25cm以下,这种粒度的聚合物可直接与悬浮剂、液体醇一起制成非水基悬浮减阻剂。
这种方法省去了聚合物的低温粉碎工序,简化了生产过程。
综上所述,通过不同的后处理工序,可以获得不同外观形态和不同性能的减阻剂产品四、减阻剂发展的新动向将高浓度减阻聚合物微粒封装在由某些惰性物质组成的外壳内,便制成了微囊减阻剂(microencapsulated drag reducing agent),又称MDRA。
微囊减阻剂的研制成功是减阻剂发展的一个新动向。
生产微囊减阻剂的方法有很多种,主要包括静态挤压法、离心挤压法、振动喷嘴法、旋转盘法、界面聚合、多元凝聚、悬浮聚合等。
使用这种装置生产微囊减阻剂,是将聚合反应单体、催化剂和外壳材料分别从中心孔和外环套中加入,并以一定的速度从装置下端挤出,形成微囊减阻剂颗粒。
挤出速度非常重要,当挤出速度慢时,形成的微囊颗粒外观规整、尺寸均匀;相反,如果挤出速度较快,将会使微囊颗粒发生粘连,造成微囊颗粒形状异常、大小不一。
在生产过程中保持一定频率的振动,将有利于控制微囊颗粒的粒度。
由于单体是在封闭的小微囊内进行本体聚合反应,对于单个微囊,反应规模极小,因此,反应条件可以得到很好地控制,特别是反应热能够被及时散发掉。
如果单体是σ(德尔塔)-烯烃,通常使用齐格勒-纳塔体系催化剂,并在微囊形成之前加入。
由于齐格勒-纳塔体系催化剂遇到氧气会迅速失效,因此反应体系内不能有氧气存在。
某些单体可以使用紫外线引发聚合,但紫外线必须能够穿透微囊外壳。
微囊外壳是微囊减阻剂的重要组成部分,外壳材料与微囊内芯的反应物不能相互反应或混溶。
如果微囊内芯是σ(德尔塔)-烯烃聚合反应体系,为避免催化剂失效,微囊外壳中就不能有氧气存在,但少量的羟基和羧基对聚合反应影响不大。
比较合适的外壳材料有聚丁烯、聚甲基丙烯酸酯、聚乙二醇、蜡、硬脂酸等。
若微囊外壳本身是聚合物,其聚合反应可以在生产微囊减阻剂的过程中进行,但是不能制约形成微囊系统的其它技术需求。
另外要求微囊外壳在运输和储存过程中性能稳定,其破碎或溶解残渣对原­油或石油产品的物化性质以及油品加工过程没有影响。
微囊外壳可以通过溶解在注入介质或管输流体中、机械破碎、融化、光化学破碎、生物降解、化合等方法去除。
由于微囊减阻剂以固体颗粒的形式储存和运输,因此节省了运输溶剂、浆料或其它载体的费用。
注入输油管道时,如果需要使用溶剂或其它载体(即注入介质),则可以在当地低价采购,现场配液,而不再需要复杂的后处理工序。
五、减阻剂在国内外输油管道上的应用实例先看看国外在输油管道上使用减阻剂的实例。