车削加工操作中切削用量的选择
切削用量及选择
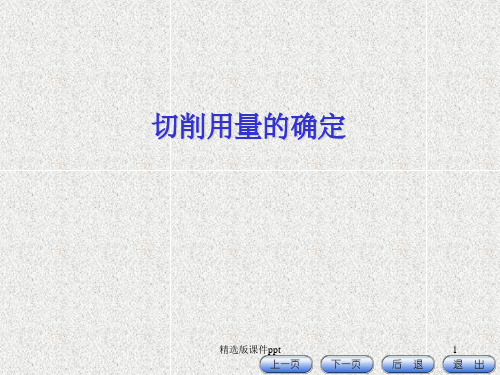
精选版课件ppt
14
3、切削用量对刀具耐用度的影响
(3) 进给量f与刀具耐用度的关系
当增大进给量后,切屑厚度增大,由切屑带着走的热量增 多,同时切屑与前刀面的接触长度增加,散热面积增大。 通过测试得知,切削温度随进给量的增加而升高,但温度 的升高幅度不及切削速度显著。
(4 )背吃刀量ap与刀具耐用度的关系
下课件ppt
33
4.分段切削背吃刀量
如果牙型较深,螺距较大,可分几次进给。每次进给 背吃刀量用螺纹深度减精加工背吃刀量所得的差按递减规 律分配。
螺纹分段切削示意图
常用螺纹切削进给次数与背吃刀量可参考表3-7~表3-9
精选版课件ppt
34
总结
1. 切削用量确定的步骤
背吃刀量的选择 →进给量的选择→切削速度的确定→校验 2. 提高切削用量的途径
13
3、 切削用量对刀具耐用度的影响 (1)刀具耐用度 所谓刀具耐用度,是指一把新刀从开始切削直到磨损量 达到磨损标准为止,在这期间所使用的总的切削时间, 用T表示。
(2) 切削速度vc与刀具耐用度的关系
切削速度是影响刀具耐用度的主要因素,其原因是当提高 切削速度时,单位时间的金属去除率会成正比例增加,刀 具与工件间的摩擦加剧,消耗于金属变形和摩擦的无用功 增加,因而产生过多的热量。因此,提高切削速度的结果 是:摩擦热大量的积聚在切屑底层而来不及传导出去,从 而使切削温度急剧升高,使刀具的耐用度大大降低。
精选版课件ppt
16
切削用量的选择:基本原则
选择切削用量的基本原则是首先选取尽可能大的背吃刀量; 其次要在机床动力和刚度允许的范围内,同时又满足已加 工表面粗糙度的要求的情况下,选取尽可能大的进给量, 最后利用《切削用量手册》选取或用公式计算确定最佳切 削速度。
车削加工的基本知识

项目一 车削加工的基本知识(1.3)
1.3 切削用量的选择
二、选择切削用量的原则 2.半精车、精车时切削用量的选择
半精车、精车时,主要以保证工件加工精度为主,但也要注意提高生产率及保证 车刀寿命。
半精车、精车的切削余量是根据技术要求由粗车留下的,原则上半精车和精车都 是一次进给完成。当工件表面粗糙度值要求较小,一次进给无法保证表面质量时才 可分两次或三次进给,但最后一次进给的背吃刀量不得小于0.1 mm。
表面粗糙度的评 定参数有轮廓算术平 均偏差Ra 及轮廓最 大高度 。通常选用 的最基本参数是Ra 。
项目一 车削加工的基本知识(1.5)
1. 表面粗糙度参数
一、影响表面粗糙度的因 素 影响表面粗糙度值大小的 因素主要有残留面积(图 1-34)、积屑瘤和振动 等,车削时,车刀主、副 切削刃在工件已加工表面 上留有痕迹,这些未被切 去部分的截面积就称为残 留面积。
实验证明:当背吃刀量增大一倍时,主切削力也增大一倍;进给量增大一倍时, 主切削力只增大0.7~0.8倍;低速切削塑性材料时,切削力随切削速度的提高而减小; 切削脆性材料的金属时,切削速度的变化对切削力的影响并不明显。
项目一 车削加工的基本知识(1.4)
1.4 金属切削过 程(3)车刀几何角度 车刀几何角度中对切削力影响最大的是前角、主偏角和刃倾角。
方法来减小残留面积中的残留高度。 (2)增大刀尖圆弧半径 刀尖圆弧也不宜过大,太大时易引起振动,所以刀
尖圆弧半径要大小适当。 (3)减小进给量。
项目一 车削加工的基本知识(1.5)
1.5 表面粗糙度参数
二、表面粗糙度值大的现象、原因及解决措施 2.工件表面有硬点或毛刺
工件表面有硬点和毛刺是由于积屑瘤脱落嵌入 工件而造成的。要想避免硬点或毛刺,必须防止 积屑瘤的产生,即使用高速钢车刀时,要选择较 低的切削速度( <5 m/min);使用硬质合金 车刀时,一定要选取高速( >70 m/min)。
车削加工操作中切削用量的选择
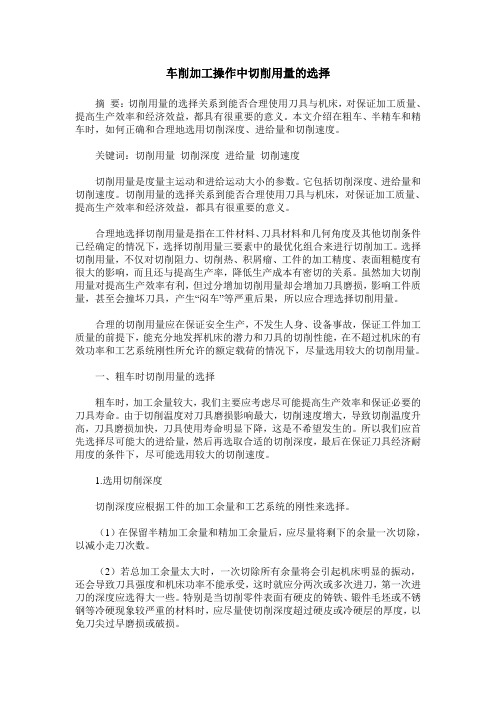
车削加工操作中切削用量的选择摘要:切削用量的选择关系到能否合理使用刀具与机床,对保证加工质量、提高生产效率和经济效益,都具有很重要的意义。
本文介绍在粗车、半精车和精车时,如何正确和合理地选用切削深度、进给量和切削速度。
关键词:切削用量切削深度进给量切削速度切削用量是度量主运动和进给运动大小的参数。
它包括切削深度、进给量和切削速度。
切削用量的选择关系到能否合理使用刀具与机床,对保证加工质量、提高生产效率和经济效益,都具有很重要的意义。
合理地选择切削用量是指在工件材料、刀具材料和几何角度及其他切削条件已经确定的情况下,选择切削用量三要素中的最优化组合来进行切削加工。
选择切削用量,不仅对切削阻力、切削热、积屑瘤、工件的加工精度、表面粗糙度有很大的影响,而且还与提高生产率,降低生产成本有密切的关系。
虽然加大切削用量对提高生产效率有利,但过分增加切削用量却会增加刀具磨损,影响工件质量,甚至会撞坏刀具,产生“闷车”等严重后果,所以应合理选择切削用量。
合理的切削用量应在保证安全生产,不发生人身、设备事故,保证工件加工质量的前提下,能充分地发挥机床的潜力和刀具的切削性能,在不超过机床的有效功率和工艺系统刚性所允许的额定载荷的情况下,尽量选用较大的切削用量。
一、粗车时切削用量的选择粗车时,加工余量较大,我们主要应考虑尽可能提高生产效率和保证必要的刀具寿命。
由于切削温度对刀具磨损影响最大,切削速度增大,导致切削温度升高,刀具磨损加快,刀具使用寿命明显下降,这是不希望发生的。
所以我们应首先选择尽可能大的进给量,然后再选取合适的切削深度,最后在保证刀具经济耐用度的条件下,尽可能选用较大的切削速度。
1.选用切削深度切削深度应根据工件的加工余量和工艺系统的刚性来选择。
(1)在保留半精加工余量和精加工余量后,应尽量将剩下的余量一次切除,以减小走刀次数。
(2)若总加工余量太大时,一次切除所有余量将会引起机床明显的振动,还会导致刀具强度和机床功率不能承受,这时就应分两次或多次进刀,第一次进刀的深度应选得大一些。
车削加工切削用量选择分析

车削加工切削用量选择分析在长期车削加工实践中,有经验的车工老师会在开车切削前,对照着零件图样先考虑开几转车速,吃刀多少深,选择多少走刀量。
这不仅体现了切削用量的重要性,更直接关系到如何充分发挥车刀、机床的潜力来提高实际的生产效率。
因此在车削加工前一定要合理的选择切削用量。
一、切削用量对切削的影响在车削加工中,始终存在着切削速度、吃刀深度和走刀量这三个切削要素,在有条件增大切削用量时,增加切削速度、吃刀深度和走刀量,都能达到提高生产效率的目的,但它们对切削的影响却各有不同。
1. 切削速度对切削的影响所谓切削速度,实质上是指切屑变形的速度,其高低决定着切削温度的高低,影响着切削变形的大小,而且直接决定着切削热的多少。
当车削碳钢、不锈钢以及铝和铝合金等塑性金属材料达到一定的切削温度时,切削底层金属将粘附在车刀的刀刃上面形成积屑瘤。
由于积屑瘤的存在,将会增大车刀的实际前角,对切削力、车刀的磨损以及工件加工质量会产生较大影响。
(1)切削速度对切削力的影响。
一般来说,提高切削速度,切屑变形小,切削力也就相应降低。
对于碳钢等塑性金属材料,在用硬质合金车刀车削碳钢工件时(前角γ=0°),开始切削速度小,切削力大,但随着切削速度的提高,形成积屑瘤后会增大车刀的实际前角,使切屑变形减小,导致切削力下降。
积屑瘤在刀刃上的堆积高度越高,即车刀实际前角增加得越多,切削变形与切削力也就越小。
但当切削速度超过一定范围时(≥20m/min),随着切削速度的提高,积屑瘤高度将会逐渐减小,直至完全消失,车刀的实际前角也随之逐渐减小,直至回复原来大小,这时切削变形与切削力又将逐渐增大。
当切削速度再继续提高时(≥50m/min),由于切削温度甚高,切屑与车刀前面接触的一层表皮开始微熔,起了一种特殊的润滑作用,减少了摩擦,而且因被切层变形不够充分,使切屑变形减小,切削力得到了再次降低。
此后切削力的变化逐渐趋于稳定。
对于不同的工件材料以及不同的车刀前角值,切削速度与切削力之间的变化规律大致如此,但各个变化阶段的速度范围则会不尽相同。
切削 用量的合理选择
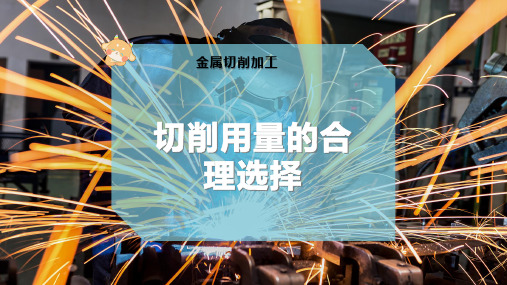
2)根据机床说明书,取机床实际进给量 =0.51mm/r。 3)检验机床进给机构允许的进给量。参考CA6140车床说 明书,查出机床进给机构允许的最大进给抗力为:FMfmax= 3528N。 计算切削时进给力为:
统、工件刚度以及精加工时表面粗糙度要求,确定进给量。
3)根据刀具寿命,确定切削速度。 4)所选定的切削用量应该是机床功率所允许的。
1.2切削用量的合理选择方法
1.背吃刀量的合理选择
背吃刀量一般是根据加工余量来确定。 粗加工(表面粗糙度Ra=50~12.5μm)时,尽可能一 次走刀即切除全部余量,在中等功率的机床上加工,取 ap=8~10mm;加工余量太大或余量不均匀、工艺系统刚性 不足或者断续切削时,可分几次走刀。 半精加工(Ra=6.3~3.2μm)时,取ap=0.5~2mm。 精加工(Ra=1.6~0.8μm)时,取ap=0.1~0.4mm。
1.5切削用量的优化概念
切削用量的优化是指在一定的预定目标及约束条件下, 选择最佳的切削用量。
在实际生产中,由于各种条件(加工零件、机床、刀 具、夹具等)都在变化,很难确定出一组最合理的切削用 量数值。
利用切削用量优化的方法,在确定加工条件下,综合 考虑各个因素,通过计算机辅助设计,能找出满足高效、 低成本、高利润和达到表面质量要求的一组最佳的切削用 量参数。实际切削用量的优化过程就是建立优化目标的数 学模型,用计算机求极值。主要目标函数有三个。
床功率是否允许。 在实际生产中,切削用量的合理选择,既可参照有关 手册的推荐数据,也可凭经验根据选择原则确定。
1.3车削用量的合理选择例题
浅谈车削切削用量的选择

浅谈车削切削用量的选择作者:舒安来源:《读与写·教育教学版》2015年第07期摘要:确定进给量,首先看是粗加工还是精加工或半精加工,然后考虑工件的表面粗糙度,还和刀尖参数有关。
在保证刚度等条件的前提下,粗加工背吃刀量尽量大,切削速度取小值,精加工反之。
关键词:刀具耐用度表面粗糙度切削速度背吃刀量进给量中图分类号:G642 文献标识码:A 文章编号:1672-1578(2015)07-0260-01选用合理的切削用量不仅是在车削加工前必须确定的主要参数,而且其数值合理程度对加工质量和精度、加工效率、产品的生产成本等有着非常重要的影响。
所谓“合理的”切削用量是指充分利用刀具各种切削性能和机床功率、扭矩等动力性能,在保证加工质量的前提下,获得高的生产效率和低的加工成本的切削用量。
1 工件信息编制加工工序卡、制定工艺方案以及调装设计都需要在对以下资料作了充分的了解的基础上,做为刀具选择、夹具设计以及切削用量的选择依据。
工件图:包括形状特征、尺寸大小、公差带、形位公差和粗糙度以及其他技术要求。
特别强调的是每个序加工的部位、程度必须明确,装夹部位要表示清楚。
毛坯图:毛坯形状特征、尺寸大小、加工余量的预留、材料、毛坯表面硬度等。
生产批量:年产量、每批取货时间、单件时间等,这对制定工艺方案、工具、夹具、量具的设计以及招标项目尤为重要。
验收要求:机床验收时对工件考核什麽项目,有无其它特殊要求。
用户是否对工件定位基准、夹紧面、辅助支承等有特别的要求,或指定参考的夹具样式。
对刀具选择要求:是否指定用国内或国外厂家的刀具,是否有自备特殊刀具等。
用户单位:工件名称、工件编号等也应标明,以便管理。
2 选择切削用量的原则2.1总要求保证人身和财物安全,不致发生人身伤亡事故或设备损坏事故;保证加工质量,复合客户要求。
在保证两项要求的前提下可以充分发挥机床的潜力、技术工人的技术水平和刀具的切削性能,选用尽可能大的切削用量以提高生产率;不能超负荷工作,不能导致产生过大的变形和震动。
车削切削用量选取参考表

三、按表面粗糙度选择进给量的参考值
工件材料
粗糙度等级(Ra)
切削速度(m/min)
刀尖圆弧半径
0.5
1
2
进给量f mm/r
碳钢及合金碳钢
10~5
≤50
0.3~0.5
0.45~0.6
1
0.3
1.1
0.3
—
—
—
—
>18~30
1
0.3
1
0.3
1.1
0.3
1.3
0.4
1.4
0.4
—
—
>30~50
1.1
0.3
1
0.3
1.1
0.4
1.3
0.5
1.5
0.6
1.7
0.6
>50~80
1.1
0.3
1.1
0.4
1.2
0.4
1.4
0.5
1.6
0.6
1.8
0.7
>80~120
1.1
0.4
1.2
0.4
1.2
铸铁及铜合金
16×25
40
0.4~0.5
—
—
—
—
60
0.6~0.8
0.5~0.8
0.4~0.6
—
—
100
0.8~1.2
0.7~1
0.6~0.8
0.5~0.7
—
400
1~1.4
1~1.2
0.8~1
0.6~0.8
车削时切削用量的选择原则

三要素获得最佳组合,此时的高生产率才是合理的。
◆ 2. 刀具寿命 切削用量三要素对刀具寿命影响的大小,按顺 序为v、f、ap。因此,从保证合理的刀具寿命出发,在确定切
削用量时,首先应采用尽可能大的背吃刀量;然后再选用大的
接近要求的形状和尺寸。
◆ 粗车以提高生产率为主,在生产中加大切削深度,对提
高生产率最有利,其次适当加大进给量,而采用中等或中
等偏低的切削速度。
5
◆
粗车铸、锻件毛坯时,因工件表面有硬皮,为保护
刀尖,应先车端面或倒角,第一次切深应大于硬皮厚
度。若工件夹持的长度较短或表面凸凹不平,切削用 量则不宜过大。 粗车应留有精车余量。粗车后的精度
6
二、 刀具寿命的选择原则
◆切削用量与刀具寿命有密切关系。在制定 切削用量时,应首先选择合理的刀具寿命, 而合理的刀具寿命则应根据优化的目标而 定。一般分最高生产率刀具寿命和最低成 本刀具寿命两种,前者根据单件工时最少 的目标确定,后者根据工序成本最低的目 标确定。
7
◆1. 根据刀具复杂程度、制造和磨刀成本来 选择。复杂和精度高的刀具寿命应选得比 单刃刀具高些。 ◆2. 对于机夹可转位刀具,由于换刀时间短, 为了充分发挥其切削性能,提高生产效率, 刀具寿命可选得低些。
(1)几何因素 (2)物理因素 (3)工艺因素
从切削过程的物理实质考虑,刀具的刃口圆角及后面 的挤压与摩擦使金属材料发生塑性变形,严重恶化了表 从几何的角度考虑,刀具的形状和几何角度,特 面粗糙度。在加工塑性材料而形成带状切屑时,在前刀 从工艺的角度考虑其对工件表面粗糙度的影响,主要 别是刀尖圆弧半径、主偏角、副偏角和切削用量中的 面上容易形成硬度很高的积屑瘤。它可以代替前刀面和 有与切削刀具有关的因素、与工件材质有关的因素和与加 进给量等对表面粗糙度有较大的影响。 切削刃进行切削,使刀具的几何角度、背吃刀量发生变 工条件有关因素等。 化。积屑瘤的轮廓很不规则,因而使工件表面上出现深 浅和宽窄都不断变化的刀痕。有些积屑瘤嵌入工件表面, 更增加了表面粗糙度。切削加工时的振动,使工件表面 粗糙度参数值增大。
浅谈车削加工中切削用量的选择

一
度。
!
( m/ s 、
1 0 0 0x6 0
式中 :0 £ 一 工件 待加工表面 的直径 ,或 刀 具、砂 轮的直径 ( 咖): 工件 或刀具的转速 ( r / m i n ) 。 如果主运动为直线运 动 ( 如拉 、插 、刨 等) , 则切削速度 为直线运 动的平均速度 ,可用下 式计算 :
v :
刀具切削性能,使切削效率最高 ,加工成本 最低。在切削用量三要素中切削速度对刀具 耐用度影响最大,进给量 ,背吃刀量影响较 小。刀具耐用度值不变 ,只要提高切削用量 三要素中任何一要素。另外两个要素就必须 有相 应 的改变 。合理 选择切 削用 量 的原则 是 :粗加工时 ,以提高生产效率为主 ,同时 考虑经济性和加工成本 ,应尽量保证金属切 除率和刀具耐用度 。半精加工和精加工 时, 应 在保 证加工 品质 的前 提下 ,兼顾 切削效 率 ,经济性和加工成本 。 三 、切 削 用量 的选取 方法 切削用量的总体选择方法: ①根据零件加工余量和粗、精加工的要 求,选择背吃刀量 印 。 国根据加工工艺系统允许的切削力。其 中包括机床进给系统、工件刚度 以及精加工 时表面粗造度要求 ,确定进给量 f 。 @根据刀具寿命 ,确定切削速度 @所选 定 的切削 用量应 该 是机床 功率 允许 的。
1 . 粗 加 工
, r— 隶 示进给量影响程度的指数
七 P —一切肖 0 条件与实验条件不同时的修
正系数 : 日 背吃刀量 ( m Ⅲ ) ; 卜— 一进给蠢 ( 姗/ r ) : 切肯 Ⅱ 速度 ( m / m i n ) 。 上述指数 或系数可从相关手册 中查取 . 粗 车时 的切 削用量 一般为 印= 2 - 5 硼, f = 0 . 3 - 0 . 7 m m / r ,在确 定 印 、f之后,可根 据刀具材料和机床 功率确 定切削速 度 2 . 精加工 在精加工时,加工精度和表面粗糙度的 要求都较高 ,加工余量小而均匀 。因此 ,确 定精加工切削用量时 , 应在保证质量 的前提 下 ,提高生产率 。 ①背吃刀量 a p的选择 印 由粗加工后 留下 的余量 决定 ,一般 印 不能太大 , 否则会影响加工质量 。 精加 工 般采用逐渐减 小 印 的方法来 保证加 工精
数控车削切削用量的选择原则
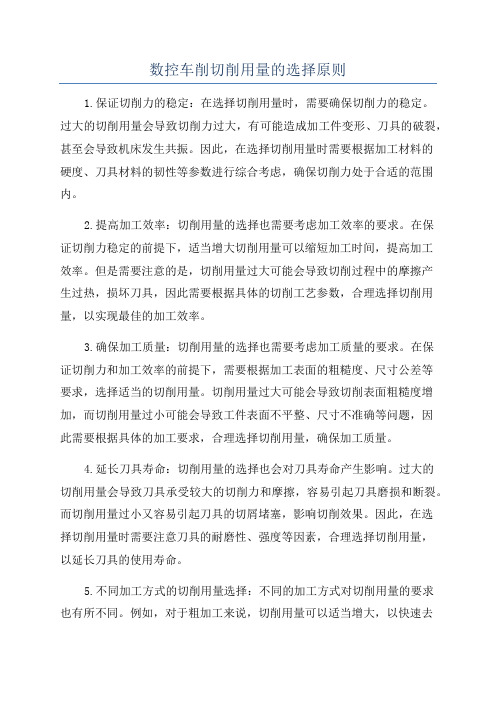
数控车削切削用量的选择原则1.保证切削力的稳定:在选择切削用量时,需要确保切削力的稳定。
过大的切削用量会导致切削力过大,有可能造成加工件变形、刀具的破裂,甚至会导致机床发生共振。
因此,在选择切削用量时需要根据加工材料的硬度、刀具材料的韧性等参数进行综合考虑,确保切削力处于合适的范围内。
2.提高加工效率:切削用量的选择也需要考虑加工效率的要求。
在保证切削力稳定的前提下,适当增大切削用量可以缩短加工时间,提高加工效率。
但是需要注意的是,切削用量过大可能会导致切削过程中的摩擦产生过热,损坏刀具,因此需要根据具体的切削工艺参数,合理选择切削用量,以实现最佳的加工效率。
3.确保加工质量:切削用量的选择也需要考虑加工质量的要求。
在保证切削力和加工效率的前提下,需要根据加工表面的粗糙度、尺寸公差等要求,选择适当的切削用量。
切削用量过大可能会导致切削表面粗糙度增加,而切削用量过小可能会导致工件表面不平整、尺寸不准确等问题,因此需要根据具体的加工要求,合理选择切削用量,确保加工质量。
4.延长刀具寿命:切削用量的选择也会对刀具寿命产生影响。
过大的切削用量会导致刀具承受较大的切削力和摩擦,容易引起刀具磨损和断裂。
而切削用量过小又容易引起刀具的切屑堵塞,影响切削效果。
因此,在选择切削用量时需要注意刀具的耐磨性、强度等因素,合理选择切削用量,以延长刀具的使用寿命。
5.不同加工方式的切削用量选择:不同的加工方式对切削用量的要求也有所不同。
例如,对于粗加工来说,切削用量可以适当增大,以快速去除材料。
而对于精加工来说,切削用量需要较小,以保证加工表面的质量。
对于深孔加工来说,由于切削油液的润滑不足,切削用量需要较小,以减小切削过程中的磨损和发热。
总之,数控车削切削用量的选择需要综合考虑切削力、加工效率、加工质量、刀具寿命等因素,根据具体加工要求和材料特性,合理选择切削用量,以实现高效、高质量的加工。
车削切削用量选取参考表

190-215
0。4
不锈钢
奥氏体
135~275
1
18-34
0。18
58—105
67-120
0。18
YG3X,YW1
84-60
0.18
275—425
0.13
>225HBS时宜用W12Cr4V5Co5及W2Mo9Cr4VCo8
4
15-27
0.4
49—100
58-105
0.4
YG6,YW1
76—135
275—335
0.25
8
17-21
0。5
66-72
82-90
0。75
YT5
105-120
0.5
215-245
0。4
高强度钢
225~350
1
20-26
0.18
90-105
115—135
0。18
YT15
150-185
0。18
380-440
0.13
>300HBS时宜用W12Cr4V5Co5及W2Mo9Cr4VCo8
0.7~1
0。6~0.8
0。5~0。6
—
20×3025×25
20
0。3~0.4
-
—
—
—
40
0。4~0。5
0.3~0.4
-
—
—
60
0。6~0.7
0。5~0.7
0。4~0。6
—
-
100
0.8~1
0.7~0。9
0.5~0。7
0.4~0。7
—
400
1。2~1。4
1~1.2
0。8~1
车削薄壁工件时车刀的几何参数与切削用量的选择(精)
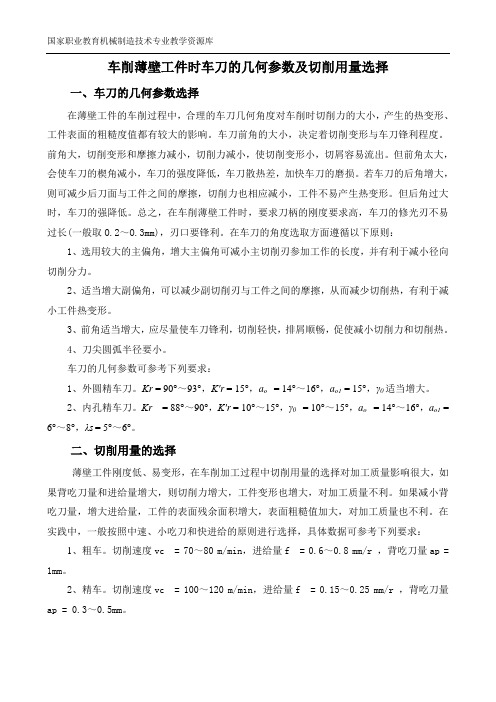
国家职业教育机械制造技术专业教学资源库车削薄壁工件时车刀的几何参数及切削用量选择一、车刀的几何参数选择在薄壁工件的车削过程中,合理的车刀几何角度对车削时切削力的大小,产生的热变形、工件表面的粗糙度值都有较大的影响。
车刀前角的大小,决定着切削变形与车刀锋利程度。
前角大,切削变形和摩擦力减小,切削力减小,使切削变形小,切屑容易流出。
但前角太大,会使车刀的楔角减小,车刀的强度降低,车刀散热差,加快车刀的磨损。
若车刀的后角增大,则可减少后刀面与工件之间的摩擦,切削力也相应减小,工件不易产生热变形。
但后角过大时,车刀的强降低。
总之,在车削薄壁工件时,要求刀柄的刚度要求高,车刀的修光刃不易过长(一般取O.2~O.3mm),刃口要锋利。
在车刀的角度选取方面遵循以下原则:1、选用较大的主偏角,增大主偏角可减小主切削刃参加工作的长度,并有利于减小径向切削分力。
2、适当增大副偏角,可以减少副切削刃与工件之间的摩擦,从而减少切削热,有利于减小工件热变形。
3、前角适当增大,应尽量使车刀锋利,切削轻快,排屑顺畅,促使减小切削力和切削热。
4、刀尖圆弧半径要小。
车刀的几何参数可参考下列要求:1、外圆精车刀。
Κr = 90°~93°,Κ′r = 15°,a o = 14°~16°,a o1= 15°,γ0适当增大。
2、内孔精车刀。
Κr = 88°~90°,Κ′r = 10°~15°,γ0 = 10°~15°,a o = 14°~16°,a o1= 6°~8°,λs= 5°~6°。
二、切削用量的选择薄壁工件刚度低、易变形,在车削加工过程中切削用量的选择对加工质量影响很大,如果背吃刀量和进给量增大,则切削力增大,工件变形也增大,对加工质量不利。
如果减小背吃刀量,增大进给量,工件的表面残余面积增大,表面粗糙值加大,对加工质量也不利。
数控车削中切削用量的选择
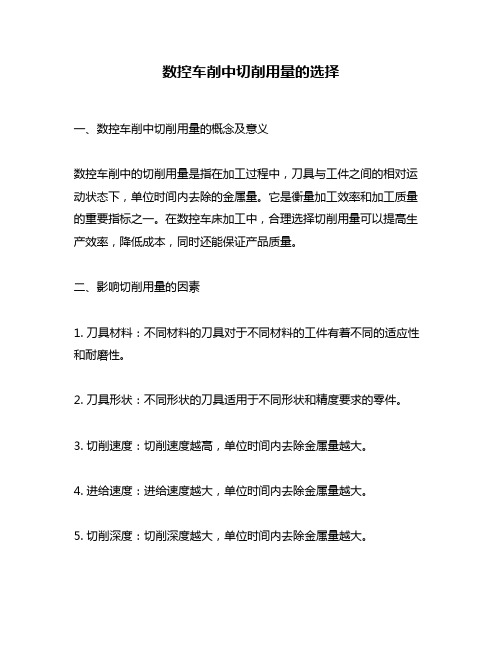
数控车削中切削用量的选择一、数控车削中切削用量的概念及意义数控车削中的切削用量是指在加工过程中,刀具与工件之间的相对运动状态下,单位时间内去除的金属量。
它是衡量加工效率和加工质量的重要指标之一。
在数控车床加工中,合理选择切削用量可以提高生产效率,降低成本,同时还能保证产品质量。
二、影响切削用量的因素1. 刀具材料:不同材料的刀具对于不同材料的工件有着不同的适应性和耐磨性。
2. 刀具形状:不同形状的刀具适用于不同形状和精度要求的零件。
3. 切削速度:切削速度越高,单位时间内去除金属量越大。
4. 进给速度:进给速度越大,单位时间内去除金属量越大。
5. 切削深度:切削深度越大,单位时间内去除金属量越大。
6. 工件硬度:硬度较高的工件需要使用更耐磨损的刀具以及更小而深入地进行切割以提高切削用量。
三、如何选择合适的切削用量1. 根据工件材料和形状选择刀具:不同材料和形状的工件需要使用不同的刀具,以达到最佳加工效果。
2. 根据加工要求选择切削速度和进给速度:根据加工要求确定切削速度和进给速度,以达到最佳的加工效率和质量。
3. 根据机床性能选择最佳切削深度:根据机床性能选择最佳的切削深度,以达到最佳的加工效率和质量。
4. 根据刀具磨损情况及时更换:定期检查并更换磨损严重的刀具,以保证加工质量。
5. 选择合适的冷却液:根据不同材料和形状的工件,选择合适的冷却液以降低温度、减少摩擦、延长刀具寿命等。
四、常见问题及解决方法1. 切屑太长或太细怎么办?答:调整进给速度或者增大/减小齿数可以改变每个齿面上去除金属量,从而改变切屑形状。
2. 切削力过大怎么办?答:减小切削深度或者降低切削速度可以减小切削力,同时也可以延长刀具寿命。
3. 刀具磨损过快怎么办?答:增加冷却液的流量或者更换更耐磨的刀具可以延长刀具寿命。
4. 加工表面粗糙度过大怎么办?答:调整进给速度或者增大/减小齿数可以改变每个齿面上去除金属量,从而改善表面质量。
车削外圆切削用量的选择
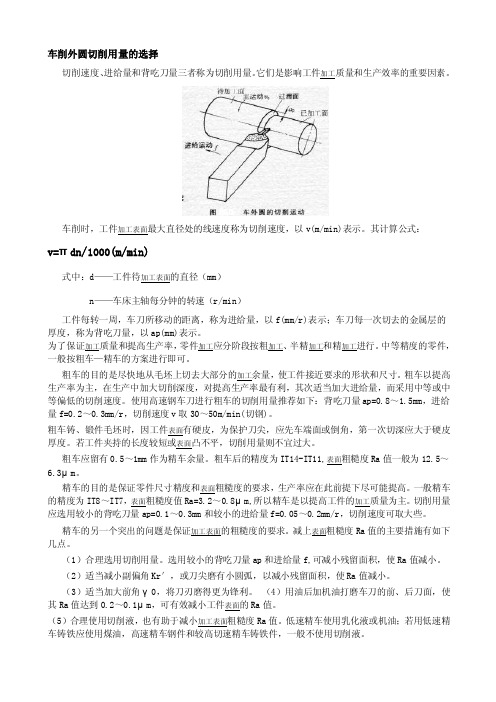
车削外圆切削用量的选择切削速度、进给量和背吃刀量三者称为切削用量。
它们是影响工件加工质量和生产效率的重要因素。
车削时,工件加工表面最大直径处的线速度称为切削速度,以v(m/min)表示。
其计算公式:v=πdn/1000(m/min)式中:d——工件待加工表面的直径(mm)n——车床主轴每分钟的转速(r/min)工件每转一周,车刀所移动的距离,称为进给量,以f(mm/r)表示;车刀每一次切去的金属层的厚度,称为背吃刀量,以ap(mm)表示。
为了保证加工质量和提高生产率,零件加工应分阶段按粗加工、半精加工和精加工进行。
中等精度的零件,一般按粗车—精车的方案进行即可。
粗车的目的是尽快地从毛坯上切去大部分的加工余量,使工件接近要求的形状和尺寸。
粗车以提高生产率为主,在生产中加大切削深度,对提高生产率最有利,其次适当加大进给量,而采用中等或中等偏低的切削速度。
使用高速钢车刀进行粗车的切削用量推荐如下:背吃刀量ap=0.8~1.5mm,进给量f=0.2~0.3mm/r,切削速度v取30~50m/min(切钢)。
粗车铸、锻件毛坯时,因工件表面有硬皮,为保护刀尖,应先车端面或倒角,第一次切深应大于硬皮厚度。
若工件夹持的长度较短或表面凸不平,切削用量则不宜过大。
粗车应留有0.5~1mm作为精车余量。
粗车后的精度为IT14-IT11,表面粗糙度Ra值一般为12.5~6.3μm。
精车的目的是保证零件尺寸精度和表面粗糙度的要求,生产率应在此前提下尽可能提高。
一般精车的精度为IT8~IT7,表面粗糙度值Ra=3.2~0.8μm,所以精车是以提高工件的加工质量为主。
切削用量应选用较小的背吃刀量ap=0.1~0.3mm和较小的进给量f=0.05~0.2mm/r,切削速度可取大些。
精车的另一个突出的问题是保证加工表面的粗糙度的要求。
减上表面粗糙度Ra值的主要措施有如下几点。
(1)合理选用切削用量。
选用较小的背吃刀量ap和进给量f,可减小残留面积,使Ra值减小。
切削用量的选择原则、方法
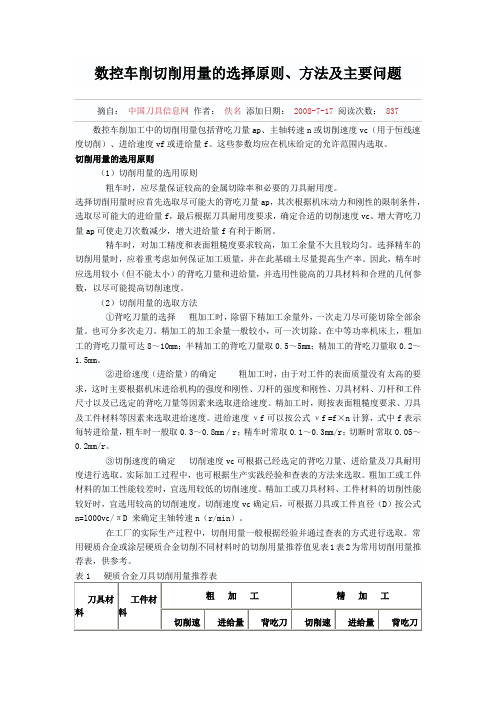
●螺纹加工程序段中指令的螺距值,相当于以进给量f(mm/r)表示的进给速度vf。如果将机床的主轴转速选择过高,其换算后的进给速度vf (mm/min)则必定大大超过正常值。
●刀具在其位移过程的始终,都将受到伺服驱动系统升降频率和数控装置插补运算速度的约束,由于升降频率特性满足不了加工需要等原因,则可能因主进给运动产生出的“超前”和“滞后”而导致部分螺牙的螺距不符合要求。
进给量(mm/r)
背吃刀量mm
硬质合金或涂层硬质合金
碳钢
220
0.2
3
260
0.l
0.4
低合金刚
1800.23来自2200.l0.4
高合金钢
120
0.2
3
160
0.l
0.4
铸铁
80
0.2
3
120
0.l
0.4
不锈钢
80
0.2
2
60
0.l
0.4
钛合金
40
0.2
1.5
150
0.l
0.4
灰铸铁
120
0.2
2
120
粗车时,应尽量保证较高的金属切除率和必要的刀具耐用度。
选择切削用量时应首先选取尽可能大的背吃刀量ap,其次根据机床动力和刚性的限制条件,选取尽可能大的进给量f,最后根据刀具耐用度要求,确定合适的切削速度vc。增大背吃刀量ap可使走刀次数减少,增大进给量f有利于断屑。
精车时,对加工精度和表面粗糙度要求较高,加工余量不大且较均匀。选择精车的切削用量时,应着重考虑如何保证加工质量,并在此基础土尽量提高生产率。因此,精车时应选用较小(但不能太小)的背吃刀量和进给量,并选用性能高的刀具材料和合理的几何参数,以尽可能提高切削速度。
车削切削用量选取参考表

0.75
YT5
170-220
0.5
335-490
0.4
中碳
175~225
1
52
0.2
165
200
0.18
YT15
305
0.18
520
0.13
4
40
0.4
125
150
0.5
YT14
200
0.4
395
0.25
8
30
0.5
100
120
0.75
YT5
160
0.5
305
0.4
碳 钢
低碳
100~200
4、加工淬硬钢时,进给量应减小。硬度为HRC45-56时,乘以修正系数:0.8, 硬度为HRC57-62,乘以修正系数:k=0.5。
三、按表面粗糙度选择进给量的参考值
工件材料
粗糙度等级(Ra)
切削速度(m/min)
刀尖圆弧半径
0.5
1
2
进给量fmm/r
碳钢及合金碳钢
10~5
≤50
0.3~0.5
0.45~0.6
1
0.3
1.1
0.3
—
—
—
—
>18~30
1
0.3
1
0.3
1.1
0.3
1.3
0.4
1.4
0.4
—
—
>30~50
1.1
0.3
1
0.3
1.1
0.4
1.3
0.5
1.5
0.6
1.7
0.6
>50~80
1.1
切削用量的合理选择
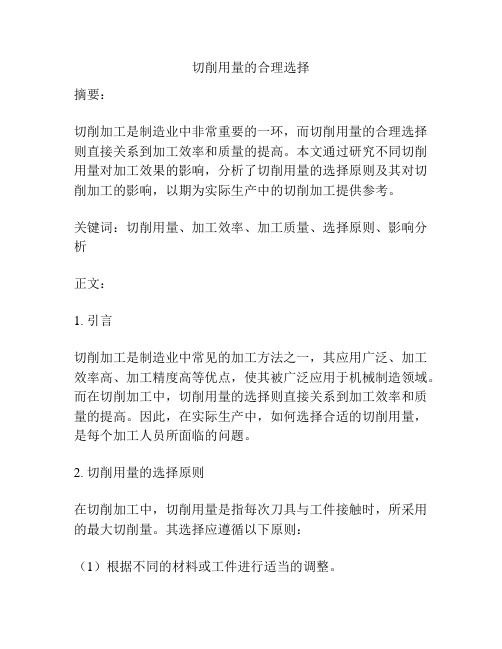
切削用量的合理选择摘要:切削加工是制造业中非常重要的一环,而切削用量的合理选择则直接关系到加工效率和质量的提高。
本文通过研究不同切削用量对加工效果的影响,分析了切削用量的选择原则及其对切削加工的影响,以期为实际生产中的切削加工提供参考。
关键词:切削用量、加工效率、加工质量、选择原则、影响分析正文:1. 引言切削加工是制造业中常见的加工方法之一,其应用广泛、加工效率高、加工精度高等优点,使其被广泛应用于机械制造领域。
而在切削加工中,切削用量的选择则直接关系到加工效率和质量的提高。
因此,在实际生产中,如何选择合适的切削用量,是每个加工人员所面临的问题。
2. 切削用量的选择原则在切削加工中,切削用量是指每次刀具与工件接触时,所采用的最大切削量。
其选择应遵循以下原则:(1)根据不同的材料或工件进行适当的调整。
不同材料或工件应根据其硬度、刚性等特性进行不同的切削用量选择,以确保刀具寿命长、加工效率高。
(2)保证切削力合理。
切削用量过大会导致切削力增大,进而使切削加工过程中产生振动、噪音等不良现象,因此应保证切削力在合理范围内。
(3)控制切削温度。
切削温度过高不仅会影响刀具寿命,还会对工件表面产生烧伤等影响,因此需要选择合适的切削用量,控制切削温度在可控范围内。
3. 切削用量对加工效果的影响(1)切削用量对加工速度的影响切削用量的选择对加工速度具有一定的影响。
切削用量越大,所需要的切削次数就越少,加工效率也就越高。
(2)切削用量对质量的影响切削用量过大会使工件表面粗糙度增加,从而降低工件加工精度。
但若切削用量过小,则会导致加工时间较长,无法提高加工效率。
4. 切削用量的合理选择对加工质量的提高在实际生产中,选择合理的切削用量能够提高加工效率和质量。
正确选择切削用量,不仅可以保证刀具寿命长,还能有效控制切削温度、切削力等,从而避免切削加工过程中产生振动、噪音等现象,提高加工质量。
5. 结论通过对切削用量选择的原则及其对加工效果的影响分析,本文认为在切削加工中,选择合适的切削用量是确保加工效率和质量的保障。
数控车削切削用量的选择原则
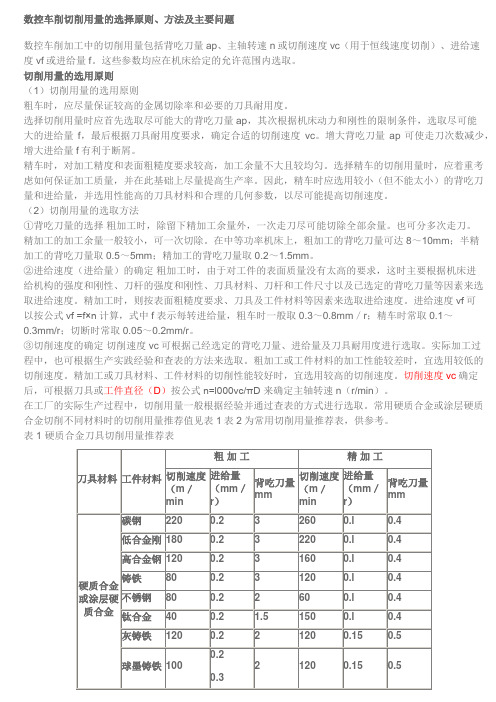
数控车削切削用量的选择原则、方法及主要问题数控车削加工中的切削用量包括背吃刀量ap、主轴转速n或切削速度vc(用于恒线速度切削)、进给速度vf或进给量f。
这些参数均应在机床给定的允许范围内选取。
切削用量的选用原则(1)切削用量的选用原则粗车时,应尽量保证较高的金属切除率和必要的刀具耐用度。
选择切削用量时应首先选取尽可能大的背吃刀量ap,其次根据机床动力和刚性的限制条件,选取尽可能大的进给量f,最后根据刀具耐用度要求,确定合适的切削速度vc。
增大背吃刀量ap可使走刀次数减少,增大进给量f有利于断屑。
精车时,对加工精度和表面粗糙度要求较高,加工余量不大且较均匀。
选择精车的切削用量时,应着重考虑如何保证加工质量,并在此基础上尽量提高生产率。
因此,精车时应选用较小(但不能太小)的背吃刀量和进给量,并选用性能高的刀具材料和合理的几何参数,以尽可能提高切削速度。
(2)切削用量的选取方法①背吃刀量的选择粗加工时,除留下精加工余量外,一次走刀尽可能切除全部余量。
也可分多次走刀。
精加工的加工余量一般较小,可一次切除。
在中等功率机床上,粗加工的背吃刀量可达8~10mm;半精加工的背吃刀量取0.5~5mm;精加工的背吃刀量取0.2~1.5mm。
②进给速度(进给量)的确定粗加工时,由于对工件的表面质量没有太高的要求,这时主要根据机床进给机构的强度和刚性、刀杆的强度和刚性、刀具材料、刀杆和工件尺寸以及已选定的背吃刀量等因素来选取进给速度。
精加工时,则按表面粗糙度要求、刀具及工件材料等因素来选取进给速度。
进给速度νf可以按公式νf =f×n计算,式中f表示每转进给量,粗车时一般取0.3~0.8mm/r;精车时常取0.1~0.3mm/r;切断时常取0.05~0.2mm/r。
③切削速度的确定切削速度vc可根据己经选定的背吃刀量、进给量及刀具耐用度进行选取。
实际加工过程中,也可根据生产实践经验和查表的方法来选取。
粗加工或工件材料的加工性能较差时,宜选用较低的切削速度。
- 1、下载文档前请自行甄别文档内容的完整性,平台不提供额外的编辑、内容补充、找答案等附加服务。
- 2、"仅部分预览"的文档,不可在线预览部分如存在完整性等问题,可反馈申请退款(可完整预览的文档不适用该条件!)。
- 3、如文档侵犯您的权益,请联系客服反馈,我们会尽快为您处理(人工客服工作时间:9:00-18:30)。
车削加工操作中切削用量的选择
摘要:切削用量的选择关系到能否合理使用刀具与机床,对保证加工质量、提高生产效率和经济效益,都具有很重要的意义。
本文介绍在粗车、半精车和精车时,如何正确和合理地选用切削深度、进给量和切削速度。
关键词:切削用量切削深度进给量切削速度
切削用量是度量主运动和进给运动大小的参数。
它包括切削深度、进给量和切削速度。
切削用量的选择关系到能否合理使用刀具与机床,对保证加工质量、提高生产效率和经济效益,都具有很重要的意义。
合理地选择切削用量是指在工件材料、刀具材料和几何角度及其他切削条件已经确定的情况下,选择切削用量三要素中的最优化组合来进行切削加工。
选择切削用量,不仅对切削阻力、切削热、积屑瘤、工件的加工精度、表面粗糙度有很大的影响,而且还与提高生产率,降低生产成本有密切的关系。
虽然加大切削用量对提高生产效率有利,但过分增加切削用量却会增加刀具磨损,影响工件质量,甚至会撞坏刀具,产生“闷车”等严重后果,所以应合理选择切削用量。
合理的切削用量应在保证安全生产,不发生人身、设备事故,保证工件加工质量的前提下,能充分地发挥机床的潜力和刀具的切削性能,在不超过机床的有效功率和工艺系统刚性所允许的额定载荷的情况下,尽量选用较大的切削用量。
一、粗车时切削用量的选择
粗车时,加工余量较大,我们主要应考虑尽可能提高生产效率和保证必要的刀具寿命。
由于切削温度对刀具磨损影响最大,切削速度增大,导致切削温度升高,刀具磨损加快,刀具使用寿命明显下降,这是不希望发生的。
所以我们应首先选择尽可能大的进给量,然后再选取合适的切削深度,最后在保证刀具经济耐用度的条件下,尽可能选用较大的切削速度。
1.选用切削深度
切削深度应根据工件的加工余量和工艺系统的刚性来选择。
(1)在保留半精加工余量和精加工余量后,应尽量将剩下的余量一次切除,以减小走刀次数。
(2)若总加工余量太大时,一次切除所有余量将会引起机床明显的振动,还会导致刀具强度和机床功率不能承受,这时就应分两次或多次进刀,第一次进刀的深度应选得大一些。
特别是当切削零件表面有硬皮的铸铁、锻件毛坯或不锈钢等冷硬现象较严重的材料时,应尽量使切削深度超过硬皮或冷硬层的厚度,以免刀尖过早磨损或破损。
2.选用进给量
一般制约进给量的主要因素是切削阻力和表面粗糙度。
粗车时,我们对加工表面粗糙度要求不高,只要工艺系统的刚性和刀具强度允许,可以选用较大的进给量。
一般粗车铸铁件比粗车钢件切削深度大,而进给量小。
3.选用切削速度
粗车时切削速度的选择,我们主要考虑切削的经济性,既要保证刀具的经济耐用度,又要保证切削载荷不超过机床的额定功率。
具体可作如下考虑。
(1)刀具材料耐热性好,切削速度可选得高一些。
用硬质合金车刀切削比用高速钢车刀切削时可选的切削速度高。
(2)工件材料的强度大、硬度高或塑性太大、太小,切削速度应选得低一些。
(3)断续切削即加工不连续表面时,切削速度应选得较低一些。
(4)工艺系统刚性较差时,切削速度应适当减小。
二、半精车和精车时切削用量的选择
半精车、精车时加工余量较小,此时主要考虑要保证加工精度和表面质量,若提高生产率只有适当提高切削速度。
而此时,由于被切削层较薄,切削阻力较小,刀具磨损也不突出,这就具备了适当提高切削速度的条件。
此时应尽可能选择较高的切削速度,再选取较大的进给量。
1.选用切削速度
为了抑制积屑瘤的产生,提高表面质量,当选用硬质合金车刀切削时,一般可选用较高的切削速度,这样既可提高生产效率,又可以提高工件表面质量。
而对高速钢车刀,则宜采用较低的切削速度,以降低切削温度。
2.选用进给量
半精车和精车时,制约增大进给量的主要因素是表面粗糙度。
半精车尤其是精车时通常选用较小的进给量。
3.选用切削深度
半精车和精车的切削深度,是根据加工精度和表面粗糙度要求并由粗加工后留下的余量决定的。
若精车时选用硬质合金车刀,由于其刃口在砂轮上不易磨得
很锋利,最后一刀的切削深度不易选得过小,否则很难满足工件表面粗糙度要求。
若选用高速钢车刀,则可选择较小的切削深度。