热冲压发展历史和现状
冲压工艺发展(3篇)

第1篇一、引言冲压工艺是一种重要的金属成形工艺,广泛应用于汽车、家电、航空、航天、电子等领域。
随着科技的不断进步和工业生产的发展,冲压工艺在材料、设备、工艺等方面都取得了显著的成果。
本文将从冲压工艺的发展历程、材料、设备、工艺等方面进行探讨。
二、冲压工艺的发展历程1. 早期冲压工艺在人类历史上,冲压工艺起源于古代。
最初,人们使用简单的手工工具进行金属成形,如锤子、钳子等。
到了19世纪,随着工业革命的兴起,冲压工艺得到了快速发展。
当时,冲压设备主要以手工操作为主,如锤子、冲床等。
2. 机械化冲压工艺20世纪初,随着电力、石油等能源的广泛应用,冲压设备开始实现机械化。
这一时期,冲压设备主要包括冲床、折弯机、剪切机等。
机械化冲压工艺大大提高了生产效率,降低了生产成本。
3. 自动化冲压工艺20世纪中叶,随着电子技术的快速发展,自动化冲压工艺应运而生。
自动化冲压设备主要包括数控冲床、自动化折弯机、自动化剪切机等。
自动化冲压工艺可以实现生产过程的连续化、自动化,进一步提高生产效率。
4. 智能化冲压工艺21世纪以来,随着物联网、大数据、人工智能等技术的不断突破,智能化冲压工艺逐渐成为发展趋势。
智能化冲压工艺可以实现生产过程的实时监控、数据分析和优化,提高生产效率和产品质量。
三、冲压工艺的材料1. 金属材料冲压工艺的主要材料是金属材料,如钢铁、铝、铜、钛等。
不同金属材料的性能差异较大,适用于不同的冲压工艺。
2. 复合材料随着科技的进步,复合材料在冲压工艺中的应用越来越广泛。
复合材料具有轻质、高强度、耐腐蚀等特点,适用于航空航天、汽车等领域。
3. 非金属材料非金属材料在冲压工艺中的应用逐渐增多,如塑料、橡胶等。
这些材料具有优良的耐腐蚀、绝缘等性能,适用于电子、家电等领域。
四、冲压工艺的设备1. 冲床冲床是冲压工艺的核心设备,用于实现金属材料的成形。
冲床按结构形式可分为开式冲床、闭式冲床、数控冲床等。
2. 折弯机折弯机用于将金属材料弯曲成所需形状。
热冲压的发展史

热冲压的发展史
热冲压技术,也称为热成形或冲压淬火,是一种新型的制造技术,它将传统的冷冲压技术及热处理工艺相结合。
该技术起源于欧洲,由瑞典的Plannja公司开发并于1977年申请专利,主要用于生产割草机的刀片和锯条。
随后,瑞典的Saab汽车公司于1984年首先采用热冲压技术生产汽车零部件,并将生产的热冲压零部件用在车型Saab9000上。
法国Renault汽车公司在1999年的Laguna车型上首次采用了热冲压技术生产的防撞梁。
随着全球气候变暖问题日益严重,各国政府积极应对,制定各种法规促进节能减排。
汽车作为重要的排放源,对节能减排有重大影响。
例如,1975年美国国会通过了能源整车和保护议案,要求汽车制造商生产和销售符合油经济性指标的车辆。
1997年的京都议定书限制二氧化碳排放,再次促进轻量化。
热冲压技术正是为了解决汽车工业发展面临的三大问题——安全、节能和环保而产生的。
在节能方面,汽车必须降低排放和更好的气经济性,需要降低汽车自重,汽车每减重10%,油耗减少8%,排放降低5-6%。
而热冲压技术能够使成形之后
的零件具有超高的强度及硬度,满足安全碰撞法规,同时实现轻量化,符合节能和环保的要求。
以上内容仅供参考,如需更多信息,建议查阅相关文献或咨询材料学专家。
桥壳热冲压工艺

桥壳热冲压工艺【桥壳热冲压工艺】一、桥壳热冲压工艺的历史1.1 起源与早期发展其实啊,桥壳热冲压工艺并不是凭空出现的,它的起源可以追溯到几十年前。
在汽车工业刚刚兴起的时候,对于桥壳的制造要求还没有那么高,但是随着汽车性能的不断提升,传统的制造工艺逐渐无法满足需求了。
1.2 逐渐成熟的过程说白了就是,经过科研人员和工程师们不断地尝试和改进,桥壳热冲压工艺才慢慢成熟起来。
从最初的简单试验,到小规模应用,再到如今成为汽车制造领域中不可或缺的一部分,这一路走来可不容易。
举个例子,就像我们学习骑自行车,一开始总是摇摇晃晃,不断摔倒,但通过一次次的练习和调整,最终能够熟练地骑行。
桥壳热冲压工艺也是这样,在不断的实践和摸索中逐渐完善。
二、桥壳热冲压工艺的制作过程2.1 材料准备首先呢,要准备好合适的材料。
这就好比做饭要先选好食材一样,材料的质量和性能直接影响到最终桥壳的品质。
一般会选用高强度的钢板,这些钢板要有良好的可塑性和强度。
2.2 加热环节接下来就是加热啦。
把选好的钢板放入高温炉中进行加热,让钢板变得像面团一样柔软,容易塑形。
这个温度和时间的控制可非常关键,就像烤蛋糕,温度太高或者时间太长,蛋糕就会烤焦;温度太低或者时间太短,蛋糕又没熟。
2.3 冲压成型加热好的钢板迅速转移到冲压模具中,通过巨大的压力将其冲压成桥壳的形状。
这一步就像是用模具做饼干,一压就成型。
2.4 冷却处理冲压成型后,要快速进行冷却,让桥壳的组织结构发生变化,从而获得更高的强度。
这有点像把刚出炉的铁块放到冷水中淬火,让它变得更加坚硬。
三、桥壳热冲压工艺的特点3.1 高强度桥壳热冲压工艺制造出来的桥壳强度非常高。
打个比方,就像是一个超级强壮的大力士,能够承受巨大的压力和负荷,保证汽车在各种复杂路况下都能稳定行驶。
3.2 轻量化它还有轻量化的特点。
这意味着在不降低桥壳性能的前提下,减轻了汽车的整体重量,就像运动员减轻了身上的负担,能够跑得更快、更省油。
先进高强钢——热冲压综述

热冲压综述H. Karbasian, A.E. Tekkaya轻型结构与成型工艺研究所,多特蒙德理工大学,Baroper Str. 301, D-44227,多特蒙德,德国摘要:具有需求性能的热冲压(也被称之为硬压加工)高强钢板零件的生产需要渊博的知识和成形规程的控制。
通过这种方式,在不同工艺参数和相互作用下,零件最后的性能具有可预见性和可调节性。
除了常见的冷成形参数,热参数和微观结构参数使得热冲压过程中的力学现象的描述变得复杂,而这正是这种成形方式所有物理现象所必须得到的阐述。
在这篇文章中,热冲压中的热、力学、微观结构和工艺领域的艺术状态得到了综述。
所有工艺流程的研究,从毛坯加热到热冲压和后续的进一步工艺均得到了描述。
现有著作的一项调查显示了一些差距,这些差距是在形成相依相改造,整个过程中不断的塑性流动行为,力学和几何的一部分属性之间的相关性,和一些先进工艺的工业应用领域中。
回顾分析目的在于提供对成形规程背景的深入了解和显示了在热金属板料成形领域进一步研究及创新的巨大潜力。
关键词:热冲压高强钢板 22MnB51.引言出于对减轻整车重量,提高安全性和防碰撞性能的需要,采用高强钢板制造的汽车零部件的需求量是显然的。
热冲压是由瑞士一家公司(Plannja)开发用来加工锯片和割草机刀刃的,并获得了专利(GB1490535, 1977)。
在1984年,萨博汽车公司是第一个采用硬化的硼钢作为萨博9000汽车组件的汽车制造商。
生产的零部件的产量从1987年的3亿件/年增加到1997年的8亿件/年。
自2000年以来,更多的热冲压件被应用在汽车上,每年的零部件的生产量已经达到了约1.07亿件/年。
热冲压件在汽车工业中的应用主要是底盘部件,如左右车柱,保险杠,车顶纵梁,摆臂横杆和隧道(图1)。
热加工目前存在着两种不同的主要的变种:直接和间接热冲压方法。
在直接热冲压加工中,毛坯在炉子里被加热后被转移到压床上,随后成形并在封闭的工具中进行淬火(图2a)。
热冲压产业发展趋势

热冲压产业发展趋势热冲压是一种在高温下对金属材料进行变形的工艺,是金属加工行业中常用的一种方法。
随着工业技术和市场需求的发展,热冲压产业也逐渐壮大起来,并呈现出许多新的发展趋势。
本文将从技术、市场和政策等方面,探讨热冲压产业未来的发展趋势。
一、技术发展趋势1. 高速化:随着生产效率的提高和金属材料的需求增长,热冲压机的速度将越来越快。
研发高速热冲压机将成为产业发展的重点。
高速热冲压机具有生产效率高、成本低、品质稳定等优势,能够满足市场对大批量、高品质产品的需求。
2. 自动化:热冲压机的自动化程度将越来越高。
随着机器人技术的发展,热冲压机可以实现自动送料、自动冲压和自动卸载,大大提高了生产效率和生产品质。
自动化热冲压生产线的应用将越来越广泛。
3. 多工位:多工位热冲压机具有一次加工多个工序的能力,能够同时完成多个产品的加工,提高了生产效率和产能。
在家电、汽车等领域,多工位热冲压机将成为主流。
4. 智能化:热冲压机将越来越智能化。
通过传感器和控制系统,可以实现对热冲压过程的实时监测和控制,提高了生产品质和稳定性。
智能化热冲压机的应用将进一步推动产业的发展。
二、市场发展趋势1. 产业转型升级:目前,热冲压产业主要集中在汽车、家电和电子等领域,但随着新兴产业的兴起,如新能源汽车、智能手机和物联网等,热冲压产业将迎来新的市场机遇。
热冲压机企业需要加大研发投入,开发适应新需求的产品和技术,实现产业转型升级。
2. 个性定制化:随着消费者需求的多样化,热冲压产品将越来越向个性化和定制化的方向发展。
热冲压机企业需要进行产品组合优化,提供灵活的生产方案,满足不同用户的需求。
3. 国际化竞争:热冲压机产业将面临来自国内外企业的激烈竞争。
国内热冲压机企业需要加大技术研发和市场开拓力度,提高产品品质和竞争力。
同时,还应积极拓展海外市场,实现国际化发展。
4. 环保可持续发展:环保问题在全球范围内受到越来越多的关注,热冲压机企业需要积极应对环保要求,研发和采用更环保的工艺和材料,降低对环境的影响,实现可持续发展。
我国冲压设备的现状与发展

我国冲压设备的现状与发展引言冲压技术是一种通过模具将金属板材加工成所需形状的方法。
在制造业中,冲压设备被广泛应用于汽车、电子、家电等行业。
随着我国制造业的快速发展,冲压设备也得到了迅猛的发展。
本文将对我国冲压设备的现状与发展进行全面详细的介绍。
现状分析1. 市场规模我国冲压设备市场规模庞大,逐年增长。
根据相关数据统计,2019年我国冲压设备市场规模已超过500亿元人民币,并且呈现稳步增长的趋势。
2. 技术水平我国冲压设备的技术水平不断提高。
目前,我国已经具备了一定的自主研发能力,在关键技术上取得了很大突破。
例如,高速、高精度、多功能等方面均有所提升。
3. 品牌竞争我国冲压设备市场存在着众多品牌竞争。
其中,一些知名企业在技术实力、市场份额等方面具备一定的优势。
同时,一些新兴企业也在不断涌现,通过技术创新和市场拓展,取得了一定的成绩。
4. 国际竞争我国冲压设备在国际市场上也具备竞争力。
一些中国冲压设备品牌已经走出国门,进入国际市场,并在一些发达国家取得了良好的口碑和销售业绩。
发展趋势1. 自动化与智能化随着制造业的转型升级,冲压设备将朝着自动化与智能化方向发展。
自动化生产线可以提高生产效率、降低劳动力成本,并且减少人为操作带来的错误。
智能化技术则可以通过数据分析和预测,实现设备状态监测、故障诊断等功能。
2. 绿色环保环保意识的提高使得绿色环保成为冲压设备发展的重要趋势。
未来,冲压设备将更加注重节能减排、废料回收利用等方面。
同时,采用新材料和新工艺也将有助于减少对环境的影响。
3. 多功能一体化为了适应市场需求的多样化,冲压设备将朝着多功能一体化方向发展。
未来的冲压设备将具备更多的功能,能够完成不同形状、材料的加工,提高生产效率和灵活性。
4. 智能制造智能制造是冲压设备发展的重要方向之一。
通过与其他智能设备和系统的连接,冲压设备可以实现信息共享、协同作业等功能,提高生产效率和质量。
支持政策为了促进我国冲压设备产业的发展,政府出台了一系列支持政策。
热冲压成型钢的现状和市场前景

热冲压成型钢的现状和市场前景1热成型钢基本概念热成型钢是指将常温下抗拉强度级别500-600MPa 钢板,经过加热到950°C 左右高温一次加工成型后迅速冷却所获得的特殊高强度钢材,见下示图1:2热成型钢生产流程热成型钢生产工艺有直接工艺和间接工艺,其两种工艺主要区别是直接工艺在加热前比间接工艺减少了一道“冷冲压预加工成型”。
目前,行业选择直接工艺较多,其生产流程主要有7个工序,分别是垛板料上料、加热炉高温加热、热压机快速闭合成型、合模保温冷却、激光切割、抛丸涂油去氧化铁皮、零部件装框,具体见示图2:常温下,抗拉强度500-600MPa 硼钢(如:22MnB5)。
加热到880-950℃,使钢奥氏体化。
热冲压后冷却到100-200℃,使钢马氏体化即硬化热成型。
热成型钢概念示图1热成型(直接)工艺流程示图23热成型钢产品介绍目前,热成型钢产品按成型前基板表面镀层状况进行分类,主要有无镀层(裸板)和镀层热成型钢,其中无镀层(裸板)热成型钢一般是指冷轧板;镀层热成型钢按镀层成份体系可分为铝硅(Al-Si)镀层、电镀锌镍(Zn-Ni)镀层、热镀锌纯锌(GI)镀层和合金化锌铁(GA)镀层。
但目前受专利技术保护、技术能力制约以及综合成本等考虑,行业应用铝硅(Al-Si)镀层和无镀层(裸板)热成型产品较多。
(1)铝硅(Al-Si)镀层产品经热冲压成型后,具有耐高温氧化、防脱碳和耐腐蚀等优越性能,并且成型零件不用抛丸处理,目前普遍应用于热成型零件的制备。
(2)无镀层(裸板)产品经热冲压成型加工后,抗拉强度可达1500MPa以上,可大大提高汽车部件的强度,为车身轻量化做出了很大贡献。
相对镀层零件其存在高温加热时容易氧化和机件需抛丸处理等不足,但其具有成本优势,目前在汽车车身部件仍广泛使用。
此外,热成型钢使用原料主要参考其淬透性,目前行业一般采用含B合金钢,常用钢板厚度为1.0-2.0mm。
4热成型钢工装及市场现状据不完全统计,全球已有400余条热成型产线,其中国内120余条,主要分布在华东和上海地区,尤其是屹丰集团把握热成型钢广阔前景,抢抓市场机遇,已在国内投资建设了30余条产线。
热冲压综述
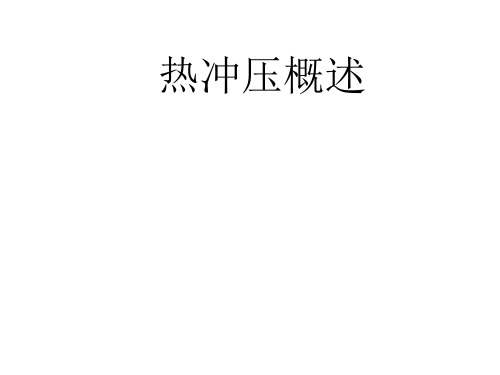
在热冲压后,喷丸处理,同时去除氧化层、涂层的附着。
最新的防止氧化的方法是采用防护油
3、加热
Lechler and Merklein (2008) 对22MnB5的研究。在不同的奥氏体化温 度和不同厚度的钢板下,要获得最大的硬度(为470HV)所需的最 短奥氏体化时间如图4所示。
根据 Stopp 等人 (2007年)实验,涂层厚度不超过40um最有利于奥氏体化。
热冲压概述
文章信息
• 原名:A review on hot stamping • 2010年收录于Journal of Materials Processing Technology
• 作者:H. Karbasian, A.E. Tekkaya • 单位:Institute of Forming Technology and Lightweight Construction, Dortmund University of Technology;Germany
内容
1、热冲压技术的背景 2、热冲压材料和涂层 3、加热 4、热冲压的成形与淬火 5、FE模拟 6、最终性能及热冲压的后续加工 7、具有特殊性能的热冲压件 8、应用 9、结论 10、读后感
Naderi(2007)对于高强度钢的研究显示,仅使用22MnB5, 27MnCrB5,37MnB4钢级才能在热冲压后再经过水淬的工艺 中得到完全马氏体组织。 22MnB5是热冲压中最为常用的钢级 。经过热冲压工序后零 部件获得马氏体组织并且其强度可高达1500MPa。 在淬火后钢的机械性能变化将取决于碳含量,最终获得 的强度可以通过适当调整碳含量来控制。硼是对淬透性 影响最大的元素,鉴于硼延缓了软组织转变而导致马氏 体组织的产生。
9、结论
新时期热冲压成形技术的构建探究

新时期热冲压成形技术的构建探究一、热冲压成形技术的发展历程热冲压成形技术是一种在高温条件下进行金属成形的新型技术,其发展历程可以追溯至20世纪60年代。
最初,热压成形技术主要用于高温合金、钢铁等金属材料的成形加工,其主要目的是提高材料的塑性变形能力和成形质量。
随着材料科学和加工技术的不断进步,热冲压成形技术逐渐应用于航空航天、汽车制造、机械制造等领域,成为一种重要的金属成形加工技术。
1. 高温条件下的成形加工:热冲压成形技术的最大特点就是在高温条件下进行成形加工。
高温条件下,金属材料的塑性变形能力大大提高,可以实现更复杂、更精密的金属成形加工。
2. 提高产品质量和精度:热冲压成形技术能够有效改善产品的表面光洁度和成形精度,减少材料的内部缺陷和裂纹,提高产品的强度和耐磨性。
3. 节能环保:热冲压成形技术可以减少金属材料的消耗,减少能源消耗,降低生产成本,减少对环境的污染,是一种高效节能、环保的加工工艺。
4. 多工序一体化:热冲压成形技术可以实现多工序一体化成形加工,简化生产工艺,提高生产效率,降低生产成本。
1. 材料和工艺的相容性:热冲压成形技术要求金属材料在高温条件下具有良好的塑性变形能力和抗热疲劳性能,这对材料的研发和工艺的设计提出了挑战。
2. 设备和工艺的集成化:热冲压成形技术需要结合高温加热设备、成形模具和润滑冷却系统,实现设备和工艺的高效集成化,提高生产效率和产品质量。
3. 数据化智能化:随着智能制造的发展,热冲压成形技术需要实现数据化采集和监控,建立智能化控制系统,提高生产过程的稳定性和可控性。
1. 多材料复合成形:随着新材料的不断涌现,热冲压成形技术将会发展成为一种多材料复合成形技术,实现金属与非金属材料的复合成形。
2. 精密微成形:随着微电子、光电子等领域的发展,热冲压成形技术将会发展成为一种精密微成形技术,实现微米级甚至纳米级的成形加工。
3. 智能制造:随着智能制造的发展,热冲压成形技术将会实现智能化生产,利用大数据、人工智能等技术实现设备和工艺的自适应控制。
热冲压发展历史和现状

2、热冲压技术应用现状
热冲压零件主要供应商(制造商): ① Bentler; ② Gestamp (Hard Tech); ③ Cosma; ④ 宝钢 ⑤ 浦项 ⑥ 新日铁
2、热冲压技术应用现状
国内热冲压产线分布
q q q q q 长春BENTLER 昆山GESTAMP 上海BENTLER 上海COSMA 上海宝钢热冲压零部件有限公司
Better Steel, Better Life.
热冲压发展历史和现状
宝钢研究院 徐伟力
2010-4-22
内容
1. 热冲压技术发展历史 2. 热冲压技术应用现状
1、热冲压技术发展历史
1、热冲压技术发展历史
全球经济活动加速,大气中二氧化碳含量增长,温室气体 排放和全球变暖成为人类共同面对的问题。
2、热冲压技术应用现状
上海宝钢热冲压零部件有限公司优势所在:
q q q q q 隶属宝钢集团,原材料价格、资源优势; 在技术封锁非常严重的热冲压领域,技术上相对开放; 秉承宝钢“提供一揽子解决方案”企业精神; 技术沟通方便,无语言和时差问题。 产品性价比高。
2、热冲压技术应用现状
热冲压产线主要供应商:
2010-4-22
Confidential
25
2、热冲压技术应用现状
2、热冲压技术应用现状
2、热冲压技术应用现状
2、热冲压技术应用现状
Volkswagen PASSAT B6大众帕萨特B6 - 重量减轻25千克 -E-NCAP碰撞测试5星 -B柱比传统方案成本更低
2、热冲压技术应用现状
菲亚特500是意大利三、四十年代以来最流行的车型,设计师吉阿科萨也因此成为名留青史的传奇 人物。热冲压技术使这个小车型重新焕发了新的生命力,在同类车型中其碰撞性能最好。
2024年冲压市场环境分析

2024年冲压市场环境分析引言冲压技术是一种常见的金属成形加工方法,广泛应用于各个行业。
冲压零部件具有质量高、成本低、生产效率高等优点,因此在市场上享有很大的市场需求。
本文将进行冲压市场环境的分析,旨在了解当前冲压市场的发展状况、竞争态势以及未来发展趋势。
冲压市场发展状况冲压市场发展状况对于了解冲压行业的整体情况至关重要。
根据相关统计数据,冲压市场在过去几年保持了较为稳定的增长态势。
其中,汽车行业是冲压市场的主要需求来源,占据了冲压市场的大部分份额。
此外,电子行业和家电行业也是冲压市场的重要需求方。
随着国内汽车市场的快速发展和技术进步,汽车冲压零部件市场持续增长。
然而,冲压行业也面临一些挑战,例如原材料价格的波动、环保法规的升级以及技术升级带来的市场竞争。
因此,冲压企业需要不断创新,提高产品质量和技术水平,以适应市场需求。
冲压市场竞争态势冲压市场竞争激烈,主要表现在以下几个方面:1.品牌竞争:冲压企业之间的品牌竞争很激烈。
一些知名品牌具有较高的知名度和市场份额,在市场上具有一定的竞争优势。
同时,一些新兴品牌通过创新技术和差异化产品竞争,逐渐蚕食市场份额。
2.价格竞争:价格是影响冲压市场竞争的重要因素之一。
由于冲压行业的产品同质化程度较高,价格对于企业来说是一个重要的竞争策略。
然而,过度降低价格可能会对企业的盈利能力产生负面影响。
3.技术竞争:冲压技术的不断更新迭代,对企业的技术水平提出了更高的要求。
一些具有先进冲压技术的企业能够生产出更高质量的产品,提高市场竞争力。
冲压市场发展趋势未来冲压市场的发展将呈现以下几个趋势:1.汽车工业的发展将继续推动冲压市场的增长。
随着新能源汽车的普及和汽车智能化的发展,对冲压零部件的需求将进一步增加。
2.绿色环保将成为冲压行业发展的重要方向。
随着环保法规的加强,冲压企业需要采用更环保的生产工艺和材料,以满足市场需求。
3.技术创新将推动冲压行业的发展。
随着科技的不断进步,冲压技术将不断更新迭代,企业需要加大对技术研发的投入,提高技术水平和产品质量。
新时期热冲压成形技术的构建探究
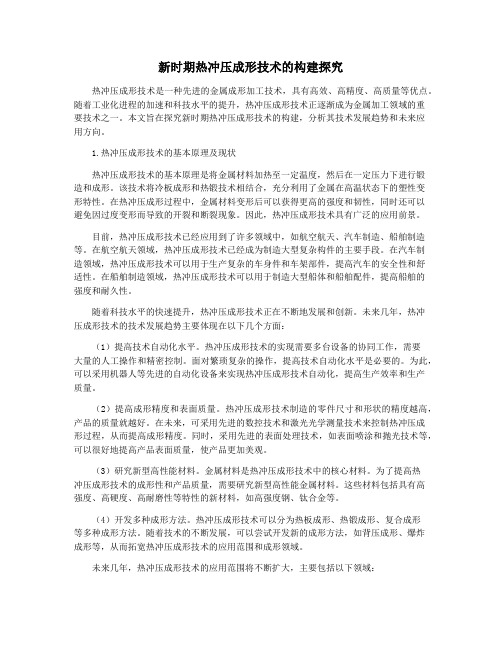
新时期热冲压成形技术的构建探究热冲压成形技术是一种先进的金属成形加工技术,具有高效、高精度、高质量等优点。
随着工业化进程的加速和科技水平的提升,热冲压成形技术正逐渐成为金属加工领域的重要技术之一。
本文旨在探究新时期热冲压成形技术的构建,分析其技术发展趋势和未来应用方向。
1.热冲压成形技术的基本原理及现状热冲压成形技术的基本原理是将金属材料加热至一定温度,然后在一定压力下进行锻造和成形。
该技术将冷板成形和热锻技术相结合,充分利用了金属在高温状态下的塑性变形特性。
在热冲压成形过程中,金属材料变形后可以获得更高的强度和韧性,同时还可以避免因过度变形而导致的开裂和断裂现象。
因此,热冲压成形技术具有广泛的应用前景。
目前,热冲压成形技术已经应用到了许多领域中,如航空航天、汽车制造、船舶制造等。
在航空航天领域,热冲压成形技术已经成为制造大型复杂构件的主要手段。
在汽车制造领域,热冲压成形技术可以用于生产复杂的车身件和车架部件,提高汽车的安全性和舒适性。
在船舶制造领域,热冲压成形技术可以用于制造大型船体和船舶配件,提高船舶的强度和耐久性。
随着科技水平的快速提升,热冲压成形技术正在不断地发展和创新。
未来几年,热冲压成形技术的技术发展趋势主要体现在以下几个方面:(1)提高技术自动化水平。
热冲压成形技术的实现需要多台设备的协同工作,需要大量的人工操作和精密控制。
面对繁琐复杂的操作,提高技术自动化水平是必要的。
为此,可以采用机器人等先进的自动化设备来实现热冲压成形技术自动化,提高生产效率和生产质量。
(2)提高成形精度和表面质量。
热冲压成形技术制造的零件尺寸和形状的精度越高,产品的质量就越好。
在未来,可采用先进的数控技术和激光光学测量技术来控制热冲压成形过程,从而提高成形精度。
同时,采用先进的表面处理技术,如表面喷涂和抛光技术等,可以很好地提高产品表面质量,使产品更加美观。
(3)研究新型高性能材料。
金属材料是热冲压成形技术中的核心材料。
热冲压的 现状和趋势
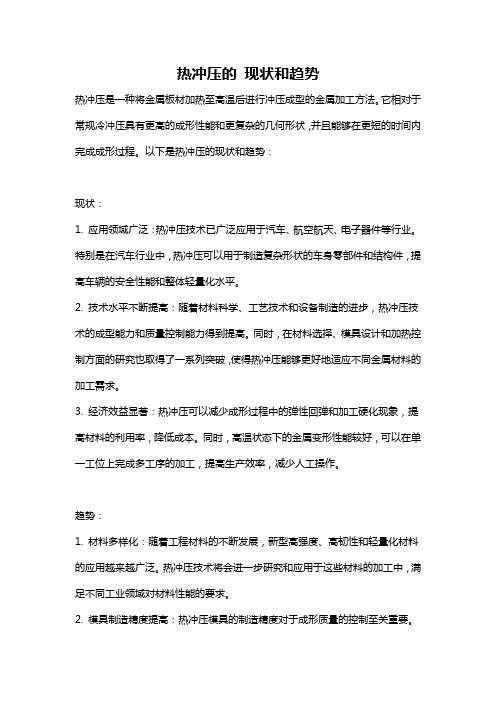
热冲压的现状和趋势热冲压是一种将金属板材加热至高温后进行冲压成型的金属加工方法。
它相对于常规冷冲压具有更高的成形性能和更复杂的几何形状,并且能够在更短的时间内完成成形过程。
以下是热冲压的现状和趋势:现状:1. 应用领域广泛:热冲压技术已广泛应用于汽车、航空航天、电子器件等行业。
特别是在汽车行业中,热冲压可以用于制造复杂形状的车身零部件和结构件,提高车辆的安全性能和整体轻量化水平。
2. 技术水平不断提高:随着材料科学、工艺技术和设备制造的进步,热冲压技术的成型能力和质量控制能力得到提高。
同时,在材料选择、模具设计和加热控制方面的研究也取得了一系列突破,使得热冲压能够更好地适应不同金属材料的加工需求。
3. 经济效益显著:热冲压可以减少成形过程中的弹性回弹和加工硬化现象,提高材料的利用率,降低成本。
同时,高温状态下的金属变形性能较好,可以在单一工位上完成多工序的加工,提高生产效率,减少人工操作。
趋势:1. 材料多样化:随着工程材料的不断发展,新型高强度、高韧性和轻量化材料的应用越来越广泛。
热冲压技术将会进一步研究和应用于这些材料的加工中,满足不同工业领域对材料性能的要求。
2. 模具制造精度提高:热冲压模具的制造精度对于成形质量的控制至关重要。
模具制造工艺和加工设备将进一步改进,以提高模具的加工精度和表面质量,提高成形产品的几何形状和尺寸一致性。
3. 数字化和自动化生产:热冲压过程中的温度、压力、成形力等参数对于产品质量具有重要影响。
通过引入数字化和自动化控制技术,可以实时监测和控制这些加工参数,提高生产过程的稳定性和一致性。
总的来说,热冲压技术在金属板材成形领域具有广阔的发展前景,将会继续在工业生产中得到广泛应用,并不断推动行业的发展和进步。
热冲压的发展史

热冲压的发展史全文共四篇示例,供读者参考第一篇示例:热冲压技术是一种利用热力对金属进行塑性变形加工的方法,广泛应用于金属制造、汽车制造、航空航天等领域。
热冲压技术的发展历程可以追溯到上世纪50年代,随着科技的不断进步和工艺的不断完善,热冲压技术已经取得了长足的发展。
热冲压技术最初是在冷冲压工艺的基础上发展起来的。
冷冲压技术虽然具有高效、高精度、低成本的优势,但在处理高强度、高硬度的金属时往往会遇到困难。
热冲压技术的出现填补了这一空白,为金属加工技术的发展注入了新的活力。
上世纪50年代,美国、德国等发达国家开始推广热冲压技术。
热冲压技术通过提高金属的温度,使其易于塑性变形,并能够降低工件的强度和硬度,从而实现更高效、更精确的加工。
在这一时期,热冲压技术主要应用于军工、航空航天等领域,为国防建设和科技发展做出了重要贡献。
随着全球工业化的快速发展,热冲压技术逐渐走向了民用领域。
特别是在汽车制造领域,热冲压技术得到了广泛应用。
汽车零部件通常需要具有一定的强度和硬度,同时又要求精度高、成本低,热冲压技术正好满足了这些需求。
采用热冲压技术可以大幅提高汽车零部件的生产效率,降低生产成本,同时还能提高产品的质量和性能。
随着科技的不断进步,热冲压技术也在不断创新和完善。
近年来,一些新兴的热冲压技术逐渐兴起,如热成形、热冲熔复合成形等。
这些新技术在提高加工效率、降低能耗、改善工件质量等方面具有独特的优势,为热冲压技术的发展带来了新的契机。
未来,随着智能制造、数字化技术等的不断发展,热冲压技术将会迎来新的发展机遇。
热冲压技术将更加智能化、自动化,加工精度、效率将会大幅提高,同时还会实现对多品种、小批量生产的适应。
热冲压技术的应用领域也将不断拓展,涵盖更多的金属材料和产品类型。
第二篇示例:热冲压技术最早可以追溯到19世纪末。
当时,工业革命的推动下,人们开始寻求更有效率的金属加工方式。
在试图解决冲压过程中金属脆化和延展性下降的难题时,科学家们开始研究采用加热的方法来提高金属的变形性能。
热冲压发展现状及未来趋势分析

热冲压发展现状及未来趋势分析热冲压技术是一种利用高温和高压将金属材料加热变软后形成所需形状的成形方法。
在制造业中,热冲压技术被广泛应用于汽车制造、家电制造、航空航天等领域。
本文将对热冲压的发展现状和未来趋势进行分析。
首先,热冲压技术的发展现状。
随着现代制造业的进步和发展,热冲压技术在各个行业中得到了广泛应用。
特别是在汽车制造领域,热冲压技术被认为是一种可以提高零部件质量、降低成本并提高生产效率的高效成形技术。
例如,利用热冲压技术可以制造出更轻、更坚固和更安全的汽车车身部件,如车门、车顶等。
此外,在家电制造行业,利用热冲压技术可以制造出更加精密和高效的家电零部件,如冰箱铝合金门壳、洗衣机水箱等。
其次,热冲压技术的未来趋势。
从技术发展角度来看,热冲压技术将继续朝着更高的成形速度、更精密的成形质量和更低的能源消耗方向发展。
一方面,随着高温和高压控制技术的不断改进,热冲压设备的成形速度将不断提高,从而进一步增加生产效率。
另一方面,随着材料科学的发展,新型高强度、高耐热金属材料的出现将使得热冲压技术能够应用于更严苛的工况。
此外,热冲压技术也将与其他先进制造技术结合,如先进模具制造技术、智能控制技术等,进一步提高成形质量和生产效率。
在市场需求方面,热冲压技术也面临着新的机遇和挑战。
随着国家对于节能环保的重视和汽车工业的发展,对于轻量化和高强度汽车零部件的需求不断增加。
而热冲压技术正可以满足这一需求,通过减少材料厚度和提高材料的强度,可以制造更轻、更强的汽车车身零部件。
此外,随着家电行业的快速发展,对于高效和精密制造的需求也在不断提高,热冲压技术可以满足家电制造行业对于高质量零部件的需求。
然而,热冲压技术也面临一些挑战。
首先,热冲压设备的投资成本相对较高,对于一些中小规模企业来说可能难以承受。
其次,热冲压技术在操作过程中需要严格控制温度和压力等参数,操作难度较大,对技术人员的要求较高。
此外,热冲压设备在长时间高温高压环境下工作,对设备的性能和稳定性要求较高。
冲压工艺的现状及其发展

《冲压工艺的现状及其发展》冲压工艺介绍:冲压是靠压力机与模具对板材、带材、管材与型材等施加外力,使之产生塑性变形或者分离,从而获得所需形状与尺寸的工件(冲压件)的成形加工方法。
冲压与锻造同属塑性加工(或者称压力加工),合称锻压。
冲压的坯料主要是热轧与冷轧的钢板与钢带。
全世界的钢材中,有 60~70%是板材,其中大部份是经过冲压制成成品。
汽车的车身、底盘、油箱、散热器片,锅炉的汽包、容器的壳体、机电、电器的铁芯硅钢片等都是冲压加工的。
仪器仪表、家用电器、自行车、办公机械、生活器皿等产品中,也有大量冲压件。
冲压件与铸件、锻件相比,具有薄、匀、轻、强的特点。
冲压可制出其他方法难于创造的带有加强筋、肋、起伏或者翻边的工件,以提高其刚性。
由于采用精密模具,工件精度可达微米级,且重复精度高、规格一致,可以冲压出孔窝、凸台等。
冷冲压件普通再也不经切削加工,或者仅需要少量的切削加工。
热冲压件精度与表面状态低于冷冲压件,但仍优于铸件、锻件,切削加工量少。
冲压是高效的生产方法,采用复合模,特别是多工位级进模,可在一台压力机上完成多道冲压工序,实现由带料开卷、矫平、冲裁到成形、精整的全自动生产。
生产效率高,劳动条件好,生产成本低,普通每分钟可生产数百件。
冲压工艺的种类:冲压主要是按工艺分类,可分为分离工序与成形工序两大类。
分离工序也称冲裁,其目的是使冲压件沿一定轮廓线从板料上分离,同时保证分离断面的质量要求。
成形工序的目的是使板料在不破坯的条件下发生塑性变形,制成所需形状与尺寸的工件。
在实际生产中,往往是多种工序综合应用于一个工件。
冲裁、弯曲、剪切、拉深、胀形、旋压、矫正是几种主要的冲压工艺。
冲压用板料的表面与内在性能对冲压成品的质量影响很大,要求冲压材料厚度精确、均匀;表面光洁,无斑、无疤、无擦伤、无表面裂纹等;屈服强度均匀,无明显方向性;均匀延伸率高;屈强比低;加工硬化性低。
在实际生产中,常用与冲压过程近似的工艺性试验,如拉深性能试验、胀形性能试验等检验材料的冲压性能,以保证成品质量与高的合格率。
国内外高强度汽车板热冲压技术研究现状
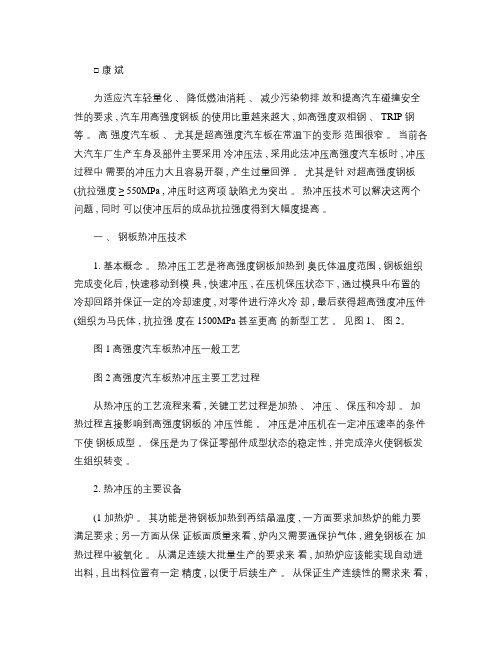
□ 康斌为适应汽车轻量化、降低燃油消耗、减少污染物排放和提高汽车碰撞安全性的要求 , 汽车用高强度钢板的使用比重越来越大 , 如高强度双相钢、 TRIP 钢等。
高强度汽车板、尤其是超高强度汽车板在常温下的变形范围很窄。
当前各大汽车厂生产车身及部件主要采用冷冲压法 , 采用此法冲压高强度汽车板时 , 冲压过程中需要的冲压力大且容易开裂 , 产生过量回弹。
尤其是针对超高强度钢板(抗拉强度≥ 550MPa , 冲压时这两项缺陷尤为突出。
热冲压技术可以解决这两个问题 , 同时可以使冲压后的成品抗拉强度得到大幅度提高。
一、钢板热冲压技术1. 基本概念。
热冲压工艺是将高强度钢板加热到奥氏体温度范围 , 钢板组织完成变化后 , 快速移动到模具 , 快速冲压 , 在压机保压状态下 , 通过模具中布置的冷却回路并保证一定的冷却速度 , 对零件进行淬火冷却 , 最后获得超高强度冲压件(组织为马氏体 , 抗拉强度在 1500MPa 甚至更高的新型工艺。
见图 1、图 2。
图 1高强度汽车板热冲压一般工艺图 2高强度汽车板热冲压主要工艺过程从热冲压的工艺流程来看 , 关键工艺过程是加热、冲压、保压和冷却。
加热过程直接影响到高强度钢板的冲压性能。
冲压是冲压机在一定冲压速率的条件下使钢板成型。
保压是为了保证零部件成型状态的稳定性 , 并完成淬火使钢板发生组织转变。
2. 热冲压的主要设备(1 加热炉。
其功能是将钢板加热到再结晶温度 , 一方面要求加热炉的能力要满足要求 ; 另一方面从保证板面质量来看 , 炉内又需要通保护气体 , 避免钢板在加热过程中被氧化。
从满足连续大批量生产的要求来看 , 加热炉应该能实现自动进出料 , 且出料位置有一定精度 , 以便于后续生产。
从保证生产连续性的需求来看 ,加热炉与其他连续性生产一样 , 配备了 2套动力装置 , 而且在意外发生后能保证加热炉自动启动 , 以确保炉况正常和炉内设备使用寿命。
- 1、下载文档前请自行甄别文档内容的完整性,平台不提供额外的编辑、内容补充、找答案等附加服务。
- 2、"仅部分预览"的文档,不可在线预览部分如存在完整性等问题,可反馈申请退款(可完整预览的文档不适用该条件!)。
- 3、如文档侵犯您的权益,请联系客服反馈,我们会尽快为您处理(人工客服工作时间:9:00-18:30)。
热冲压发展历史和现状
宝钢研究院 徐伟力
2010-4-22
内容
1. 热冲压技术发展历史 2. 热冲压技术应用现状
1、热冲压技术发展历史
1、热冲压技术发展历史
全球经济活动加速,大气中二氧化碳含量增长,温室气体 排放和全球变暖成为人类共同面对的问题。
2010-4-22
Confidential
25
2、热冲压技术应用现状
2、热冲压技术应用现状
2、热冲压技术应用现状
2、热冲压技术应用现状
Volkswagen PASSAT B6大众帕萨特B6 - 重量减轻25千克 -E-NCAP碰撞测试5星 -B柱比传统方案成本更低
2、热冲压技术应用现状
菲亚特500是意大利三、四十年代以来最流行的车型,设计师吉阿科萨也因此成为名留青史的传奇 人物。热冲压技术使这个小车型重新焕发了新的生命力,在同类车型中其碰撞性能最好。
① 德国SCHULER; ② 瑞典AP&T ③ 德国NEFF-Cartec、Hyundai Hysco ④ 西班牙公司
2、热冲压技术应用现状
应用场合向着能量吸收和平台零件扩展
在AMTB Gent生产的中国奥迪A4后边梁
2、热冲压技术应用现状
2、热冲压技术应用现状
抗拉强度2081MPa,50标距延伸率6%
1、热冲压技术发展历史
现代汽车工业的发展要求:
汽车轻量化
--采用减薄高强零件
1、热冲压技术发展历史
零件高强化传统途径: 采用高强钢(HSS、AHSS、UHSS),进行冷冲压。
1、热冲压技术发展历史
高强度钢板冷冲压的瓶颈问题: ① 成形性差,容易开裂; ② 成形精度差,回弹大,容易产生各种表面缺陷; ③ 所需设备吨位大; ④ 超高强度钢板制造困难; ⑤ 超高强度钢板冲压及其困难,甚至根本无法冲压。
1、热冲压技术发展历史 CAFE和欧洲的二氧化碳排放标准
1、热冲压技术发展历史 减少二氧化碳及改善燃油经济性指标
1、热冲压技术发展历史 政府对汽车节约燃料和减少排放方面制定了法规
1、热冲压技术发展历史
汽车节能减排的办法
改善发动机性能,提高燃烧效率; 改进汽车的动力学设计,降低运行阻力; 改进传动系设计,减小功或动力传递的损失; 寻求新的替代能源,开发新能源汽车(IISI的FSV) 减轻汽车自重,进行轻量化汽车的设计制造。
1、热冲压技术发展历史
在温室气体排放中,汽车是重要的排放源。
1、热冲压技术发展历史 各国政府积极应对制定各种法规促进节能减排
20世纪70年代两次石油危机促进发展节能汽车,美国国会1975年通 过能源整车和保护议案,要求汽车制造商生产和销售符合燃油经济 性指标的车辆。1978年CAFE标准生效。 1990年以后,提高了燃油经济性,规定轿车不低于11.69Km/L,轻型 载货车不低于8.80Km/L。 为应对全球气候变暖,1997年京都议定书,限制二氧化碳排放,再 次促进轻量化。
1、热冲压技术发展历史 车重减少100Kg,每升油多行驶1Km
1、热冲压技术发展历史
汽车工业发展面临的三大问题 ——安全 节能 环保
安全:必须满足各种安全碰撞法规,正碰和侧碰法规 节能:汽车必须降低排放和更好的燃气经济性,需要降低汽车自 重,汽车每减重10%,油耗减少8%,排放降低5-6%。 环保-降低油耗,强化汽车工业的竞争力,汽车性能更完善,用户 更满意(操作和噪音等) 成本:降低汽车的制造和使用成本 这些综合要求,就是汽车轻量化强大的驱动力
2、热冲压技术应用现状
热冲压技术在欧美,特别是欧洲得到非常广泛的应用,被 普遍认为是有效减轻车重、提高碰撞性能和降低车身制造 成本的有效手段。 • 德国大众建立了6条热冲压产线,在改进车型和新车型中大量 采用热冲压零件; • FIAT从瑞典AP&T公司采购了5条热冲压产线,在改进车型和新 车型中大量采用热冲压零件,后续新车型中热冲压零件的使 用比例在16%以上; • VoVle规定后续新车型中热冲压零件的使用比例在35%以上;
• 20世纪中叶, Norrbottens Jernverk, Luleå ( SSAB)首先 开发出热轧和冷轧热冲压钢板; • 1973年Norrbottens Jernverk率先开发出热冲压工艺; • 1975年在Volvo车型上开展热冲压零件适用性研发; • 1984年SAAB成为率先使用热冲压零件的汽车厂; • 1991年率先使用热冲压的前保险杠; • Arcelor于20世纪90年代开展热冲压技术研究,攻克相关核心 技术,开发了全球闻名的镀层热冲压用钢Usibor1500; • 热冲压技术在全球普遍应用,目前已有100多条产线。
谢谢!
2、热冲压技术应用现状
典型热冲压产线
880 – 930 °C
2、热冲压技术应用现状
迈腾车型中热冲压零件的使用
2、热冲压技术应用现状
Anti intrusion parts防侵入零件 Lightening potential 30 % 轻量化潜力30% Increase in vehicle safety 提高车体安全性
1、热冲压技术发展历史
如何来解决高强度钢板冷冲压的瓶颈问题?? 策略一: 主机厂:通过优化车身结构设计,限制车身零件的强度级别; 钢板供应商、零件制造商:进行高强钢成形技术攻关。 问题:需要长时间攻关,积累大量经验,难度大; 策略二: 部分放弃高强度钢板冷冲压,另辟蹊径!
1、热冲压技术发展历史
零件高强化基本机理:
① 变形强化; ② 热处理强化。 直接、朴素的想法:使钢板含有热处理强化元素(条件),冲 压出零件以后,再对零件进行热处理,就像模具制造领域广泛 采用的热处理; 问题:零件尺寸精度将发生变化!! 新的设想:保压状态下进行热处理,即保证零件尺寸精度条件 下的热处理。 热冲压技术应运而生!!!
1、热冲压技术发展历史
2、热冲压技术应用现状来自上海宝钢热冲压零部件有限公司优势所在:
q q q q q 隶属宝钢集团,原材料价格、资源优势; 在技术封锁非常严重的热冲压领域,技术上相对开放; 秉承宝钢“提供一揽子解决方案”企业精神; 技术沟通方便,无语言和时差问题。 产品性价比高。
2、热冲压技术应用现状
热冲压产线主要供应商:
1、热冲压技术发展历史
1、热冲压技术发展历史
1、热冲压技术发展历史
热冲压类似术语: ① 热冲压、热压制、热成形、热成型; ② hot forming 、hot stamping 、hot pressing 、die quenching、 press hardening Heat forming不是目前常规的热冲压! 国内热成形、热成型概念很早就有,目的是提高成形性,不具 备淬火强化功能,和目前所说的热成形有天壤之别。 建议统一称为热冲压为宜,以和以前概念加以区别。
2、热冲压技术应用现状
热冲压零件主要供应商(制造商): ① Bentler; ② Gestamp (Hard Tech); ③ Cosma; ④ 宝钢 ⑤ 浦项 ⑥ 新日铁
2、热冲压技术应用现状
国内热冲压产线分布
q q q q q 长春BENTLER 昆山GESTAMP 上海BENTLER 上海COSMA 上海宝钢热冲压零部件有限公司