煤制油天然气制氢烃类蒸汽转化炉设备操作规程
天然气制氢装置操作规程

天然气制氢装置操作规程一、目的和适用范围本操作规程是为了规范天然气制氢装置操作过程,确保操作的安全性和高效性。
适用于天然气制氢装置的日常操作。
二、安全注意事项1.操作人员必须熟悉操作规程,掌握天然气制氢装置的操作技能,并具备一定的安全意识。
2.操作前,应检查设备工作状态,确保设备无异常。
如有异常需及时报修。
3.操作人员需穿戴好防护装备,包括安全鞋、防护眼镜、安全帽等。
4.操作过程中严禁吸烟、使用明火或其他可能产生火花的物品。
5.操作人员需密切注意设备工作状态,如有异常情况应立即停止操作并报告相关负责人。
三、操作步骤1.开机准备(1)操作人员按照要求穿戴好防护装备,并经过安全培训后方可进行操作。
(2)检查天然气供应管道是否正常,如发现问题应及时修复。
(3)检查天然气制氢装置是否正常,确保各种仪表设备工作正常。
(4)检查制氢反应器的催化剂和催化剂床是否饱满。
(5)确认制氢装置内部没有任何残留物或杂质。
2.开启天然气供应(1)打开天然气供应阀门,并观察压力表。
(2)确认天然气供应压力稳定后,逐步调整至所需压力。
(3)确认天然气供应无异常后,进入下一步操作。
3.升温(1)启动加热系统,升温至设定温度。
(2)检查加热系统工作状态,确保其正常运行。
(3)观察温度表,确认温度达到要求后方可进行下一步操作。
4.制氢(1)确认制氢反应器的催化剂床温度稳定后,打开制氢反应器进料阀门。
(2)观察制氢反应器压力表,确认压力稳定。
(3)根据制氢需求,调整进料阀门和出料阀门的开度。
(4)根据制氢反应器做好的制氢记录表,持续监控制氢效果。
5.停机(1)停止天然气供应,关闭天然气供应阀门。
(2)关闭加热系统,待温度降至安全范围后方可停机。
(3)关闭制氢反应器进料阀门和出料阀门。
(4)检查设备状态,确保设备处于安全状态后方可结束操作。
四、工作记录1.操作人员需按照规定记录好每次操作的时间、天然气的压力、温度、制氢量等重要参数。
2.出现异常情况和处理措施也需记录,以备日后分析和改进。
天然气转化制氢装置正常操作规程

天然气转化制氢装置正常操作规程第一节装置主要动设备操作法一原料气压缩机1、压缩机的工作原理压缩机由增安型防爆一步电机通过刚性联轴节驱动,电机转子直接带动压缩机的曲轴旋转,然后由连杆和十字头将曲线的旋转运动转变为活塞的往复支线运动,压缩机气缸为双作用,即盖侧和轴侧都有相应的工作腔,以盖侧为例,当活塞由盖侧始点位置向轴侧开始运动时,盖侧容积增大,腔内残留气体膨胀,压力下降,与进气腔内气体产生压差,当压力差大于吸气阀弹簧力时,吸气阀打开,随着活塞继续向轴侧运动,将气体吸入缸内。
活塞达到内止点时,吸气完毕。
随着活塞又从轴侧位置向盖侧方向放回移动,此时吸气阀关闭,随着活塞的继续移动,缸内体积不断变小,已吸入的气体受到压缩,压力逐步升高,当缸内气体压力高于背压和配气阀弹簧力之和时,排气阀打开,缸内被压缩气体开始排除,当活塞返回外止点时,排气完毕;至此完成一个工作循环,轴侧工作腔与此相同,由于活塞不断地作往复运动,使气缸内交替发生气体的膨胀、吸入、压缩和排出的过程,从而获得连续脉冲的压缩气源。
主机气缸采用无油润滑结构,除各密封件、活塞环、支撑环采用填充四氟PTFE制成外,缸内凡与气体接触的零件均采用耐腐蚀材料并经防腐处理。
机组气体管路系统由气体过滤器、进排气缓冲器、中间冷却器、气液分离器、止回阀、安全阀等结构,为了消除进排气管内的气流脉冲机管路振动,使气阀工作稳定和输气平稳。
每个气缸的进排气口均设有缓冲器,系统进气应首先经过过滤器,气体进入系统前应先通过止回阀。
机组冷却水由水管引入并分成若干支路进入需要冷却的部位,冷却部位包括缸体、油冷却器、级间冷却器、返回冷却器、水站冷却水、填料、电机等,其中填料采用软化水冷却,各支路的回水管上装有视水镜,以便检查水流情况。
机组润滑系统包括由曲轴驱动的主轴泵(轴头泵)和电机驱动的能自启动的辅助油泵,油冷却器为列管板式换热器,油过滤器采用带四通换向阀的双联过滤器,其过滤精度为25um。
煤制油天然气制氢装置炉子的燃烧操作规程
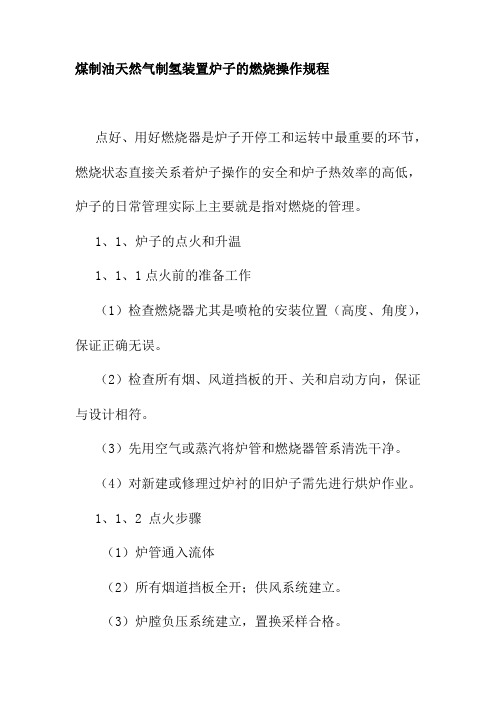
煤制油天然气制氢装置炉子的燃烧操作规程点好、用好燃烧器是炉子开停工和运转中最重要的环节,燃烧状态直接关系着炉子操作的安全和炉子热效率的高低,炉子的日常管理实际上主要就是指对燃烧的管理。
1、1、炉子的点火和升温1、1、1点火前的准备工作(1)检查燃烧器尤其是喷枪的安装位置(高度、角度),保证正确无误。
(2)检查所有烟、风道挡板的开、关和启动方向,保证与设计相符。
(3)先用空气或蒸汽将炉管和燃烧器管系清洗干净。
(4)对新建或修理过炉衬的旧炉子需先进行烘炉作业。
1、1、2 点火步骤(1)炉管通入流体(2)所有烟道挡板全开;供风系统建立。
(3)炉膛负压系统建立,置换采样合格。
(4)燃料系统吹扫合格。
(5) 准备好燃烧供给系统。
对气体燃烧完全切除水分和液相组分,并保持压力一定;(6)对有一次、二次风门的自然送风燃烧器,暂时完全关闭一次风门。
(7) 稍稍开启燃料主管上控制总量的主阀,点燃燃烧器。
如未点燃而使燃料喷入炉膛内,立即关闭阀门并炉膛置换采样合格。
(8)如点火完成,逐渐开打主阀至全开。
按相同方法点其他燃烧器。
(9)调节一次和二次风门,并调节烟道挡板。
1、1、3 升温升温速度400°C前,控制20°C,以后一般控制在每小时50°C左右(指炉管内介质的出口温度)。
1、2、天然气制氢装置燃烧器主要技术参数与性能指标:型号: WYNQ-DQ125型燃气燃烧器WYNQ-DQ60型燃气燃烧器WYNQ-DQ80型燃气燃烧器燃料气进燃烧器的正常压力:开工工况(天然气:0.15MPa);正常操作工况(天然气和PSA尾气:0.05MPa)热负荷调节比: 5:1空气过剩系数:~1.15燃烧器运行噪音: <80dB@1m(距设备1m以外处)通风形式:自然通风、强制通风1)燃烧器结构组成:本燃气燃烧器由辅助气枪、中心气枪、筒体、调风机构、火盆砖等组成。
燃烧器的安装2)安装前的检查:对燃烧器各组件、配件应作如下检查:a.各组件应无损坏、无严重变形,调风机构应调节灵活;b.软管接头或密封面应无碰撞损坏;c.火盆转各棱角应无大于6mm损伤;d.燃气抢喷头应无松动或堵塞;3)清理待炉侧砖、火盆砖全部砌筑完后,应将掉入火盆砖型腔内及燃烧器筒体内所有杂物清理干净;其它均按常规进行安装(注:燃气枪的安装以枪上刻线为准);4)连接金属软管:a.先在进燃烧器燃料气管线上的适当位置分别焊接M45X1.5接头(应保证焊接处不漏气,且要求接上金属软管后,金属软管能保证正确的弯曲状态。
制氢工艺转化炉操作法

制氢工艺转化炉操作法2.5.1 燃料系统操作法2.5.1.1 燃料系统概述制氢装置正常生产时只有转化炉为燃料消耗设备。
正常生产状态下,转化炉的燃料来源主要为中变气PSA提浓尾气,不足部分补充炼厂瓦斯。
2.5.1.2 燃料系统的气密与置换1)气密流程F-2101顶中心火嘴各小阀GN-2109→GF-2101 GF-2103→ GF-2201→气密至炉顶各火嘴小阀→GF-2205→PSA解吸气缓冲罐出口→ RV-2210→火炬线本部分气密最终压力为0.4 MPa,采用工业风气密,对炉顶的每一个入火嘴的小阀都要详细检查,防止出现瓦斯泄露。
进行气密前要仔细检查以下项目:(1)燃料系统各管线连接是否正确,有无漏接、多接;(2)各仪表是否好用;2)置换气密检查合格后,直接用氮气进行置换。
开F-2101炉顶燃料气放空,吹扫2分钟左右,采样分析含氧量小于0.5%为合格,停止吹扫,保压气密。
2.5.1.3开工1)装置开工期间,联系调度,引进管网高压瓦斯;2)关闭F-2101的燃料气总阀及放空阀,关闭与其它容器、管线相连接的阀门,防止跑串。
引瓦斯入D-1305,充压至0.4MPa后,关进装置瓦斯总阀。
开F-2101上的燃料气放空阀,如此置换2~3次后可认为置换合格。
确认E-1301已正确投用。
开工初期燃料气消耗全部为瓦斯,注意控制好D-1305的液面,TV-2117(炉出口温度调节器)改手动控制,根据需要适当调节FIC-2205,确保中心火嘴燃烧良好。
4)正常运行后,逐步投用PSA解吸气,注意操作的平稳,避免造成炉温大幅度波动,并及时调整火嘴的燃烧状态。
2.5.2 转化炉操作法2.5.2.1 点火前的准备工作1)检查炉体结构是否完好,衬里有无脱落,其它附件完好,确认关闭各瓦斯火嘴和长明灯的炉前手阀。
2)检查炉膛及对流室,应无施工杂物,各火嘴已安装好并已吹扫干净。
3)燃料气管线已吹扫干净,置换完毕,火嘴畅通,压力表完好,准备好点火枪及点火用具4)各火嘴阀关好,防爆门、看火口关好,炉膛扫干净,人孔全部封好。
煤制油天然气制氢装置设备控制阀与副线切换操作规程

煤制油天然气制氢装置设备控制阀与副线切换操作规程1、.1. 控制阀改副线操作1) 接到内操指令控制阀改副线。
2) 现场与室内联系好准备改副线。
3) 缓慢关小控制阀的上游阀,直至室内流量指示有下降趋势。
4) 缓慢开控制阀的副线阀,同时按内操指令缓慢关控制阀的上游阀,直至控制阀上游阀全关。
5) 按内操指令微调控制阀副线阀,稳定流量。
6) 联系仪表维修工处理。
4.2调节阀需要解体则:7) 关闭调节阀的下游阀。
8) 打开调节阀的排凝阀,排净管线内的介质,同时做好防护工作。
9) 如果是有毒有害介质,应佩戴好气防用具进行操作,并做好监护工作。
4.3副线改控制阀操作10) 接到内操指令副线改控制阀。
11) 现场与室内联系对照控制阀的开度,确认行程正常后内操全关控制阀。
12) 外操缓慢将控制阀的上游阀全开,室内确认流量无变化。
13) 现场与室内联系好准备改副线。
14) 外操缓慢关控制阀的副线阀,同时内操根据流量的变化缓慢打开控制阀,保持流量的稳定,直至副线阀全关。
15) 内操调整流量正常后控制阀投自动。
4.4 如果控制阀解体后改回:16) 先确认控制阀排凝阀关闭。
17) 现场与室内联系对照控制阀的开度,确认行程正常,内操将控制阀保留少许开度。
18) 外操稍开控制阀的上游阀,对控制阀各密封部位进行气密,确认无漏点后内操关闭控制阀。
19) 外操缓慢将控制阀的上游阀全开,室内确认流量无变化。
20) 现场与室内联系好准备改副线。
21) 外操缓慢关控制阀的副线阀,同时内操根据流量的变化缓慢打开控制阀,保持流量的稳定,直至副线阀全关。
22) 内操调整流量正常后控制阀投自动。
一段转化炉炉型设备操作规程
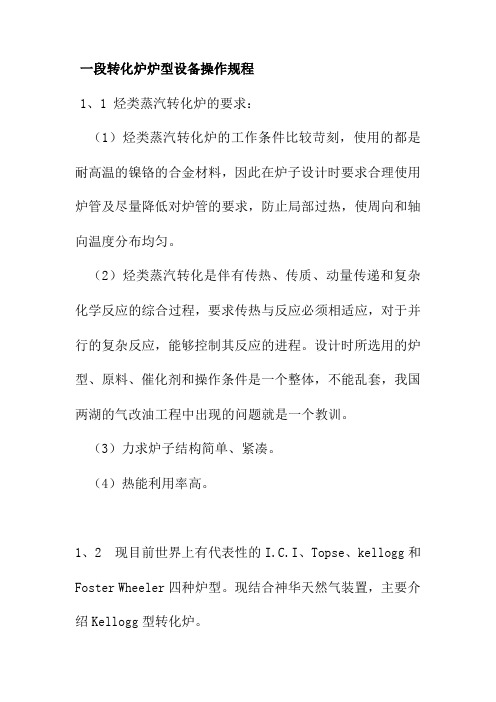
一段转化炉炉型设备操作规程1、1 烃类蒸汽转化炉的要求:(1)烃类蒸汽转化炉的工作条件比较苛刻,使用的都是耐高温的镍铬的合金材料,因此在炉子设计时要求合理使用炉管及尽量降低对炉管的要求,防止局部过热,使周向和轴向温度分布均匀。
(2)烃类蒸汽转化是伴有传热、传质、动量传递和复杂化学反应的综合过程,要求传热与反应必须相适应,对于并行的复杂反应,能够控制其反应的进程。
设计时所选用的炉型、原料、催化剂和操作条件是一个整体,不能乱套,我国两湖的气改油工程中出现的问题就是一个教训。
(3)力求炉子结构简单、紧凑。
(4)热能利用率高。
1、2 现目前世界上有代表性的I.C.I、Topse、kellogg和Foster Wheeler四种炉型。
现结合神华天然气装置,主要介绍Kellogg型转化炉。
1、2、1、 Kellogg型转化炉引进的年产30*104t合成氨装置中的转化炉,如图:1)转化炉结构尺寸为13m(长)*17m(宽)*10m(高)。
炉内装有378根炉管、分为9排、每排42根。
每排炉管下端与一个下集气管焊接,下集气管外面有轻质绝热材料保温,集气管的中间又焊上一根上升管,九个上升管伸出炉顶与集气总管连接,集气总管内衬耐火材料。
这种炉管排列又称竖琴式,增加产量,只需增加排数即可。
2)催化剂管及下集气管的重量是由固定在炉顶钢架上的189个弹簧支架承担,上升管和输气总管的重量由几个输气管弹簧承担,因此,九排炉管及输气总管均处在弹簧支架的弹性吊挂状态。
这种全部采用钢性焊接的管排在操作时因热膨胀差而产生热应力就可以大部分被这种弹簧吊挂系统所吸收。
、3)辐射室顶部共装有200个自吸式烧嘴,炉底下烟道内都设置一个辅助烧嘴,以供给对流段热量不足。
4)脱硫后的工艺混合气预热至510℃由上集气管经上猪尾管通入转化炉内,气流从上向下流动,边加热边反应,转化炉管出口处温度达823℃,进入下集气管经上升管再加热至868℃,进炉顶的集气总管后再进入二段炉。
天然气制氢(静设备)操作规程一

天然⽓制氢(静设备)操作规程⼀第⼀章概述⼀、简介神华煤制油天然⽓制氢装置为搬迁项⽬,主要利⽤巴陵⽯化洞庭氮肥⼚⽇产1100吨合成氨装置中的脱硫造⽓、中低变和脱碳⼯序的设备、管道以及钢结构等,新增PSA制氢⼯序。
巴陵⽯化洞庭氮肥⼚合成氨装置是七⼗年代初从美国凯洛格公司引进的、以⽯脑油为原料⽇产850吨合成氨的“⽓改油”装置。
为了扩⼤⽣产能⼒与降低能耗,先后在1988年、1996年对合成氨装置进⾏了两次改造,最终达到⽇产1100吨合成氨的⽣产能⼒。
2004年装置停车。
原巴陵⽯化洞庭氮肥⼚天然⽓制氢,绝⼤部分设备为从国外引进的设备。
本次神华煤制油天然⽓制氢装置为巴陵⽯化洞庭氮肥⼚天然⽓制氢整体搬迁。
设备型式包括:转化炉、塔、换热器、反应器、废热锅炉、罐、分离器、储槽、过滤器、离⼼式压缩机、往复式压缩机、螺杆式压缩机、离⼼泵、隔膜泵、天车等。
机泵驱动⽅式主要以蒸汽透平、⽔⼒透平为主,辅以电机。
⼆、⼯艺流程简述来⾃界区的天然⽓经天然⽓过滤器(0101-LM)除尘后,进⼊原料⽓压缩吸⼊罐(116-F)分离掉其中的液体,分为两股,⼀股作为燃料⽓与来⾃PSA制氢⼯序的尾⽓在燃料⽓混合器(0103-FM)混合后去对流段预热;⼀股作为原料天然⽓,配⼊来⾃脱碳⼯序的返氢⽓后,进⼊原料⽓压缩机(0102-J)压缩⾄4.2MPaA,在对流段预热⾄400℃,依次进⼊加氢转化器(101-D)、氧化锌脱硫槽(108-DA/B)脱硫,使天然⽓中的硫含量降低⾄0.1ppm以下。
脱硫后的天然⽓按3.5的⽔碳⽐配⼊⼯艺蒸汽,混合⽓经⼀段转化炉对流段的混合⽓盘管预热到510℃后进⼊⼀段转化炉辐射段转化管,在镍触媒的作⽤下进⾏蒸汽转化反应⽣成氢⽓和⼀氧化碳。
转化反应需要的热量靠⼀段转化炉辐射段燃烧燃料天然⽓提供。
⼀段炉出⼝的转化⽓温度约813℃,甲烷含量约9.7%(⼲基),经输⽓管(107-D)进⼊⼆段转化炉(103-D),⼆段转化炉仅作为通道使⽤,在⼆段炉⽔夹套的作⽤下,⼀段转化⽓的温度降低到约789℃,在第⼀废热锅炉(101-CA/B)和第⼆废热锅炉(102-C)中回收热量后,温度降低⾄约370℃去变换⼯序。
转化炉操作规程

转化炉操作规程本页仅作为文档页封面,使用时可以删除This document is for reference only-rar21year.March转化炉操作规程转化炉因氧气纯度达%,正常生产时出口温度≤880℃,触媒床层温度为980℃,因此操作的好坏直接影响到设备本体及各组换热设备的使用寿命,以及整个车间的平稳连续运行;因此确保转化炉平稳运行是本岗位的重要工作职责之一。
⑴转化炉出口温度的控制①控制指标:转化炉出口温度≤880℃②控制方式:DSC手动调节③相关参数:氧气焦炉气比值、转化炉入口工艺气温度④正常调节:A.通过空分调节氧气压力或调节TIC60611阀门开度控制转化炉温度;氧气流量与转化炉温度成正比。
B.通过调节预热炉温度,提高转化炉入口各工艺气温度间接控制转化炉温度;预热炉温度与转化炉温度成正比。
⑤异常处理:A.原料焦炉气中断:(a)立即打开氧气放空阀,关闭氧气入转化炉调节阀组。
(b)引入开工蒸汽,继续向烧嘴通入吹扫蒸汽及保护蒸汽,适当加大入炉蒸汽流量防止设备超温爆炸及触媒烧结。
(c)打开煤气放散阀卸除系统压力。
B.氧气中断处理:(a)立即打开氧气放空阀,关闭氧气入转化炉调节阀组。
(b)引入开工蒸汽,继续向烧嘴通入吹扫蒸汽及保护蒸汽,适当加大入炉蒸汽流量防止爆炸及触媒结碳。
(c)打开煤气放散阀卸除系统压力。
(d)切除系统原料焦炉气。
(2)转化炉烧嘴冷却系统的控制氧气烧嘴冷却系统是转化炉氧气烧嘴的配套设备,使用优质脱盐水做冷却介质,采用对氧气烧嘴进行强制加压循环降温的方式,事故状态下,事故水槽储存脱盐水或消防水短时间内作为应急冷却水保证烧嘴安全运行。
A、控制指标:氧气烧嘴冷却水回水流量12NM3/HB、控制方式:现场手动调节C、相关参数:运行过程中中控人员通过DCS监视PIA60619(脱盐水回水压力)、PI60621/PI60622(烧嘴保护泵出口压力)、FI60614(烧嘴保护水流量)判断烧嘴保护泵运行情况及脱盐水系统运行情况。
煤制油天然气制氢装置101-CA、101-CB第一废热锅炉操作规程

煤制油天然气制氢装置101-CA、101-CB第一废热锅炉操作规程
1、废热锅炉的型式和结构特点
工艺流程中的废热锅炉,实际上是一个高温高压换热器,是为了冷却工艺气体同时产生高压蒸汽,它与设置在烟气中的废热锅炉是有所不同的。
此类锅炉,由于热负荷大,传热面积大,大多数采用管壳式,其中又可分成火管式和水管式两类:凡是高温气体走管程,水和蒸汽走壳程的是火管式锅炉,反之就是水管式锅炉。
具有以下的特点:
(1)工艺气体是不允许泄露,设备密封性要求高。
(2)工艺上的要求,必须要有稳定的出口温度,因此都设有温度调节装置。
(3)工艺气体干净,流速大,传热系数大。
101-CA、101-CB废热锅炉的型式:刺刀式锅炉
换热管由内管、外管组成,内管与小管板相连接,外管
与大管板相连接,水从顶部进入内管,至换热管端折回,从外管向上流动,同时汽化,汽水混合物自大、小管板间引出。
转化气从炉底进入,通过气体分配气进入炉内,在壳体上部出口,锅炉壳体内部有绝热层保护,外部有水夹套。
特点是避免了管子与壳体由于温差产生的膨胀差所引起的应力,有效地解决了热补偿问题,同时水循环较好,操作可靠。
2、废热锅炉主要故障分析。
管子与管板连接处开裂的原因:
(1)连接接头因高温应力松弛而失效,
(2)接头因受高温高压气体腐蚀而破坏;
(3)管束在高压气流冲击下产生振动,使接头疲劳破坏;
(4)制造工艺不合理,接头中焊接残余应力过大,在操作中引起疲劳破坏;
(5)操作不当,水循环不正常或给水温度波动,使管板温度产生周期性的变化或忽冷忽热,引起管子疲劳破坏;
(6)热补偿不好,使接头承受过大的温度应力而破坏。
燃气蒸汽锅炉设备安全操作规程范本(2篇)

燃气蒸汽锅炉设备安全操作规程范本一、设备准备1. 在操作前,必须确保设备所使用的燃气、水和电源正常供应,并进行必要的检查。
2. 检查设备周围是否有易燃和易爆物品,确保操作环境安全。
3. 检查设备的阀门、管路、仪表等是否完好无损,如有发现问题及时进行修理或更换。
二、启动操作1. 操作前必须熟悉设备的启动流程和操作规程,并依次进行操作。
2. 在启动前,先打开进气阀,将燃气引入燃烧室,然后打开点火装置,进行点火操作。
3. 点火成功后,观察火焰的状况,确保火焰稳定并符合标准。
4. 启动主泵,开始循环供水,确保设备正常运行。
三、设备调整1. 在设备启动后,按照规定的参数进行调整,确保设备运行在正常的工作状态下。
2. 根据实际需要,调整燃气和空气的比例,以达到最佳的燃烧效果。
3. 观察燃烧室的压力、温度和氧含量等指标,并进行必要的调整。
四、运行操作1. 在设备正常运行后,及时观察设备的运行指标,并与设定参数进行对比,如有异常立即停机检修。
2. 定期对设备进行清洗和维护,保持设备的清洁和正常运行。
3. 密切关注设备的温度和压力变化,确保设备运行在安全范围内。
五、停机操作1. 在停机前,先关闭燃气进气阀和点火装置,确保燃气不会继续流入燃烧室。
2. 关闭主泵,停止循环供水,排除系统中的水和压力。
3. 关闭设备的电源和水源,并进行必要的标识和警示。
六、安全措施1. 操作人员必须穿戴合适的防护装备,如安全帽、防护眼镜和防护手套等。
2. 在操作过程中,严禁吸烟、使用明火和产生火花的设备。
3. 如发现设备有燃气泄漏、异常噪音或其他异常情况,应立即停机报修。
七、应急处理1. 在发生火灾或其他紧急情况时,立即关闭燃气进气阀和电源,并立即报警。
2. 在进行紧急救援时,必须按照应急预案进行操作,确保人员安全和设备的正常运行。
八、操作记录1. 在每次操作前,应在操作记录表格上填写相关信息,包括操作人员、操作时间和操作内容。
2. 在操作过程中,如有异常情况或重要的调整变化,应在操作记录表格上做好相应的记录。
天燃气制氢操作规程
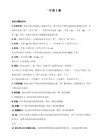
天然气制氢第一章天然气制氢岗位基本任务以天燃气为原料的烃类和蒸汽转化,经脱硫、催化转化、中温变化,制得丰富含氢气的转化气,再送入变压吸附装置精制,最后制得纯度≥99.9%的氢气送至盐酸。
1.1工艺流程说明由界区来的天然气压力为1.8~2.4MPa,经过稳压阀调节到1.8Mpa,进入原料分离器F0101后,经流量调节器调量后入蒸汽转化炉B0101对流段的原料气预热盘管预热至400℃左右,进入脱硫槽D0102,使原料气中的硫脱至0.2PPm以下,脱硫后的原料气与工艺蒸汽按水碳比约为3.5进行自动比值调节后进入混合气预热盘管,进一步预热到~590℃左右,经上集气总管及上猪尾管,均匀地进入转化管中,在催化剂层中,甲烷与水蒸汽反应生产CO和H2。
甲烷转化所需热量由底部烧咀燃烧燃料混合气提供。
转化气出转化炉的温度约650--850℃,残余甲烷含量约3.0%(干基),进入废热锅炉C0101的管程,C0101产生2.4MPa(A)的饱和蒸汽。
出废热锅炉的转化气温度降至450℃左右,再进入转化冷却器C0102,进一步降至360℃左右,进入中温变换炉。
转化气中含13.3%左右的CO,在催化剂的作用下与水蒸气反应生成CO2和H2,出中变炉的转化气再进入废热锅炉C0101的管程换热后,再经锅炉给水预热器C0103和水冷器C0104被冷至≤40℃,进入变换气分离器F0102分离出工艺冷凝液,工艺气体压力约为1.4MPa(G)。
燃料天然气和变压吸附装置来的尾气分别进入转化炉的分离烧嘴燃烧,向转化炉提供热量≤1100℃。
为回收烟气热量,在转化炉对流段内设有五组换热盘管:(由高温段至低温段)蒸汽-A原料混合气预热器, B 原料气预热器,C烟气废锅,D燃料气预热器,E尾气预热器压力约为1.4的转化工艺气进入变化气缓冲罐,再进入PSA装置。
采用5-1-3P,即(5个吸附塔,1个塔吸附同时3次均降)。
常温中压下吸附,常温常压下解吸的工作方式。
制氢转化炉操作指南

版本号:00转化炉操作指南第5页
5.4原料质量控制
制氢转化催化剂中毒或积碳大多是由原料不合格引起的,因此,严格控制制氢原料指标
是非常必要的。
制氢原料控制指标
名称
项目
单位
指标
制氢原料油
含硫
ppm(w)
≯100
含氯
ppm(w)
<0.5
砷
ppb(w)
<5
铅
ppb(w)
<20
芳烃
V%
<10
烯烃
V%
<1
干点
℃
<180
干气富氢
含硫
ppm(w)
≯150
脱硫后原料
含硫
ppm(w)
<0.5
含氯
ppm(w)
<0.5
自产蒸汽
CI-
ppm(w)
<0.5
注:当上述指标违反工艺卡片要求时,以工艺卡片为准!
日期:2003/6/14制氢装置
版本号:00转化炉操作指南第6页
6.常见故障处理
6.1催化剂中毒
WEPEC操作指南共8页
制氢装置
转化炉操作指南
生效
签字
日期
执笔:于承祖
装置主任
年月日
编制人:
于承祖
生产部
年月日
机动部
年月日
质量部
年月日
公司主管领导
年月日
打字排版:李冰
版本
No.00
年月日
校对:于承祖
文件编号:QJ/SYXT-17-8700-2003
日期:2003/6/14制氢装置
版本号:00转化炉操作指南第2页
版本号:00转化炉操作指南第7页
制氢转化炉操作指南

制氢转化炉操作指南制氢转化炉操作指南一、前言本操作指南旨在提供制氢转化炉的详细操作方法,以确保操作人员能够正确、安全地使用该设备。
请在使用前仔细阅读本指南,并按照指南的要求进行操作。
二、设备概述1.制氢转化炉是一种用于将化学原料转化为氢气的设备,具有高效、节能的特点。
2.转化炉由炉体、燃烧器、进料口、出料口、废气排放口等组成。
三、安全注意事项1.操作人员必须熟悉转化炉的使用方法,并遵守相关安全规定。
2.在操作转化炉前,请确保设备正常运行,无损坏或泄漏等情况。
3.确保操作人员都佩戴适当的个人防护装备,如手套、防护眼镜等。
4.在操作过程中,严禁离开操作岗位,如有特殊情况需离开,请事先关闭炉体和燃烧器,并通知相关人员。
5.操作结束后,应及时清理转化炉周围的杂物,保持设备清洁。
四、操作步骤1.开机准备a.检查炉体和燃烧器是否正常,如有异常情况,请及时通知维修人员。
b.打开进料口,根据需要加入适量的化学原料。
c.打开燃烧器,调节火焰大小,使其能够提供足够的热量。
2.开始操作a.将化学原料缓慢地加入转化炉,避免产生冲击和溢出。
b.观察炉内温度和压力的变化,并及时调整燃烧器的火焰强度。
c.根据工艺要求,控制转化炉的温度和时间。
3.操作结束a.停止加料,并将燃烧器调至最小火焰。
b.关闭炉体和燃烧器,并等待转化炉冷却后进行下一步操作。
五、附件本文档附带以下附件:1.转化炉操作记录表:用于记录每次操作的详细信息。
2.转化炉维护检查表:用于定期检查维护转化炉设备的情况。
六、法律名词及注释1.安全规定:指根据国家相关法律法规和行业标准制定的安全操作规范。
2.防护眼镜:用于保护操作人员的眼睛免受化学物质或碎片的伤害。
3.化学原料:指用于制氢转化炉的化学反应的起始物质。
4.工艺要求:指制氢转化炉在操作过程中需要遵循的工艺要求,包括温度、压力等。
制氢转化炉操作指南
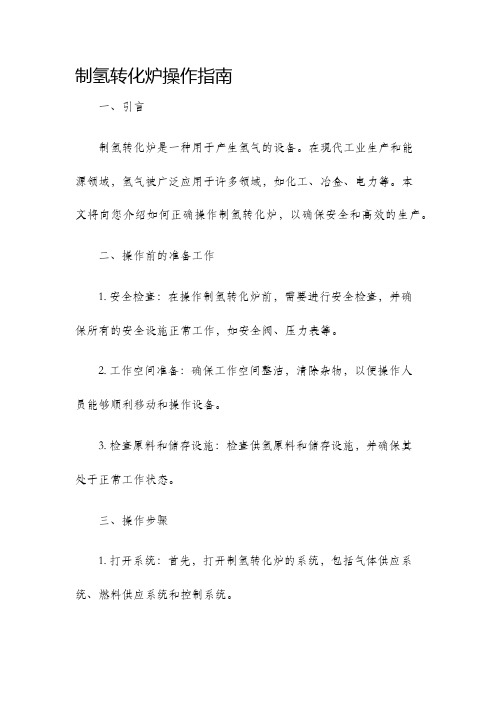
制氢转化炉操作指南一、引言制氢转化炉是一种用于产生氢气的设备。
在现代工业生产和能源领域,氢气被广泛应用于许多领域,如化工、冶金、电力等。
本文将向您介绍如何正确操作制氢转化炉,以确保安全和高效的生产。
二、操作前的准备工作1. 安全检查:在操作制氢转化炉前,需要进行安全检查,并确保所有的安全设施正常工作,如安全阀、压力表等。
2. 工作空间准备:确保工作空间整洁,清除杂物,以便操作人员能够顺利移动和操作设备。
3. 检查原料和储存设施:检查供氢原料和储存设施,并确保其处于正常工作状态。
三、操作步骤1. 打开系统:首先,打开制氢转化炉的系统,包括气体供应系统、燃料供应系统和控制系统。
2. 检查工艺参数:确认工艺参数是否符合要求,如温度、压力等,并根据需要进行调整。
3. 加热转化炉:根据操作手册的要求,加热制氢转化炉,使其达到适宜的工作温度。
4. 控制氧气流量:调整控制系统,控制氧气的流量,以维持适宜的氧气含量,确保转化过程稳定。
5. 监测氢气产量:通过监测系统中的传感器,实时监测氢气的产量,并根据需要进行调整。
6. 样品采集和分析:定期采集氢气样品,并使用适当的分析仪器进行分析,以确保氢气质量符合要求。
7. 安全措施:确保操作人员严格遵守相关安全规定,如戴防护眼镜、戴手套等,并定期进行安全培训。
四、操作注意事项1. 注意气体泄漏:定期检查制氢转化炉的管路和接口,确保气体不会泄漏,如发现泄漏要及时停止操作,并采取相应的补救措施。
2. 防止氢气积聚:制氢转化炉产生的氢气具有易燃和爆炸风险,因此必须确保氢气未积聚在工作区域中,维持良好的通风。
3. 防止过热:在操作制氢转化炉时,必须密切关注炉体的温度,防止过热导致设备损坏或发生事故。
4. 遵守操作手册:严格遵守制氢转化炉的操作手册中的要求,不得随意更改工艺参数或操作方式。
5. 及时维护保养:定期对制氢转化炉进行维护保养,清洁设备,更换损坏的部件,以确保设备的正常运行。
煤制油天然气制氢装置101-F汽包设备操作规程
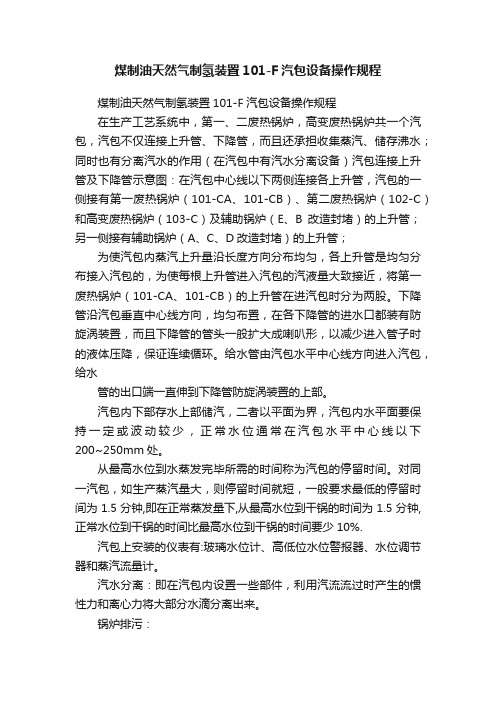
煤制油天然气制氢装置101-F汽包设备操作规程煤制油天然气制氢装置101-F汽包设备操作规程在生产工艺系统中,第一、二废热锅炉,高变废热锅炉共一个汽包,汽包不仅连接上升管、下降管,而且还承担收集蒸汽、储存沸水;同时也有分离汽水的作用(在汽包中有汽水分离设备)汽包连接上升管及下降管示意图:在汽包中心线以下两侧连接各上升管,汽包的一侧接有第一废热锅炉(101-CA、101-CB)、第二废热锅炉(102-C)和高变废热锅炉(103-C)及辅助锅炉(E、B改造封堵)的上升管;另一侧接有辅助锅炉(A、C、D改造封堵)的上升管;为使汽包内蒸汽上升量沿长度方向分布均匀,各上升管是均匀分布接入汽包的,为使每根上升管进入汽包的汽液量大致接近,将第一废热锅炉(101-CA、101-CB)的上升管在进汽包时分为两股。
下降管沿汽包垂直中心线方向,均匀布置,在各下降管的进水口都装有防旋涡装置,而且下降管的管头一般扩大成喇叭形,以减少进入管子时的液体压降,保证连续循环。
给水管由汽包水平中心线方向进入汽包,给水管的出口端一直伸到下降管防旋涡装置的上部。
汽包内下部存水上部储汽,二者以平面为界,汽包内水平面要保持一定或波动较少,正常水位通常在汽包水平中心线以下200~250mm处。
从最高水位到水蒸发完毕所需的时间称为汽包的停留时间。
对同一汽包,如生产蒸汽量大,则停留时间就短,一般要求最低的停留时间为1.5分钟,即在正常蒸发量下,从最高水位到干锅的时间为1.5分钟,正常水位到干锅的时间比最高水位到干锅的时间要少10%.汽包上安装的仪表有:玻璃水位计、高低位水位警报器、水位调节器和蒸汽流量计。
汽水分离:即在汽包内设置一些部件,利用汽流流过时产生的惯性力和离心力将大部分水滴分离出来。
锅炉排污:锅炉运行时,蒸汽带走的盐份比给水带入的要少得多。
因而锅炉水的含盐量比给水的要大,而且愈来愈大。
当锅炉水含盐量达到一定程度时蒸汽水质变坏。
因此要排污,将锅炉水的含量控制在一定范围内。
煤制油天然气制氢装置一段转化炉设备操作规程
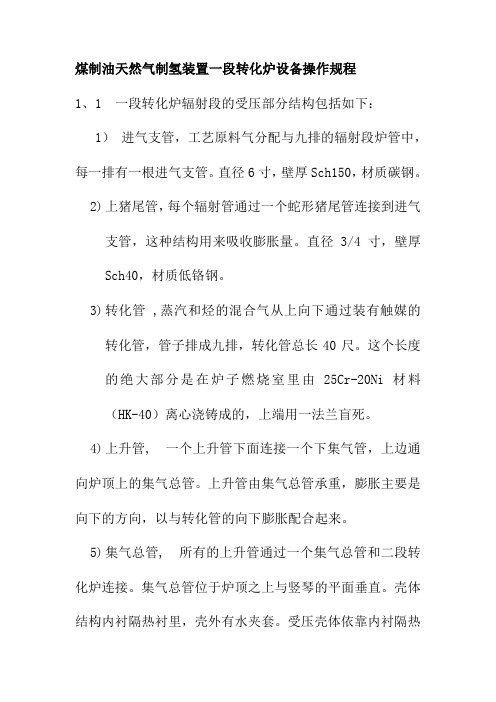
煤制油天然气制氢装置一段转化炉设备操作规程1、1 一段转化炉辐射段的受压部分结构包括如下:1)进气支管,工艺原料气分配与九排的辐射段炉管中,每一排有一根进气支管。
直径6寸,壁厚Sch150,材质碳钢。
2)上猪尾管,每个辐射管通过一个蛇形猪尾管连接到进气支管,这种结构用来吸收膨胀量。
直径3/4寸,壁厚Sch40,材质低铬钢。
3)转化管 ,蒸汽和烃的混合气从上向下通过装有触媒的转化管,管子排成九排,转化管总长40尺。
这个长度的绝大部分是在炉子燃烧室里由25Cr-20Ni材料(HK-40)离心浇铸成的,上端用一法兰盲死。
4)上升管, 一个上升管下面连接一个下集气管,上边通向炉顶上的集气总管。
上升管由集气总管承重,膨胀主要是向下的方向,以与转化管的向下膨胀配合起来。
5)集气总管, 所有的上升管通过一个集气总管和二段转化炉连接。
集气总管位于炉顶之上与竖琴的平面垂直。
壳体结构内衬隔热衬里,壳外有水夹套。
受压壳体依靠内衬隔热衬里和水夹套保持在约212°F。
1、2 整个系统的全部重量是由两种弹簧支撑:1、2、1 转化管的弹簧所有炉管都用弹簧吊在炉子上空的钢架上,一个弹簧吊一对炉管,但在两端一根弹簧只吊一根炉管。
吊两根炉管的弹簧用轭板托住这两根炉管的管耳,此外下集气管和上猪尾管的重量也分担在各弹簧上。
1、2、2 集气总管弹簧集气总管也是依靠弹簧支撑在炉子的钢结构上,但在自由膨胀端是一固定的支点。
弹簧位于每两个上升管之间,而在两端也有弹簧。
每个弹簧所支撑的重量是集气总管的一部分加上上升管的重量。
4、 3 操作要点:1、3、1 顶喷烧嘴的燃烧基本要求是保持火焰和热的分配均匀,在正常和开车时都是如此。
如燃烧不均匀,就会使上升管内产生弯曲力矩,另外对下集气管也会产生一个较小的弯矩。
1、3、2 触媒如果一个转化管由于触媒出现问题而使流量减少,导致温度的变化,将减少炉管寿命。
如果上升管的一边有多个热管子,就会引起附加的热应力。
煤制油天然气制氢装置设备关键设备的操作规程

煤制油天然气制氢装置设备关键设备的操作规程1、1 水夹套把水加入输气管(107-D)、二段转化炉(103-D)以及第一废热锅炉(101-CA/CB)的水夹套中。
水来自脱盐水或101-JCM的冷凝液。
将水夹套其它附属设备投入运行,水夹套低液位报警系统投用,这样,水夹套系统从此处于运转状况。
在操作中,应始终保持水夹套中充满水。
当冷凝液不够时可使用事故冷却水,如果任何时候水夹套的液面消失,不管是什么原因,必须立即停车。
同时应切记在水夹套因失水过热后不能马上加水,否则会造成严重的设备事故。
1、2、表面冷凝器101-JCM表面冷凝器必须在它所服务的任何一个设备开车以前就投入使用。
这些设备所产生的冷凝液来自于下述驱动透平排出的乏汽的冷凝液:102-JT 原料气压缩机透平101-BJT 引风机透平101-BJAT强制风机透平1107-JBT 半贫液循环泵透平1110-JAT 贫液循环泵透平在运行中,会有表面冷真空度下降的情况,原因可能如下:1)循环水流量减少甚至中断,降低甚至失去了冷却效力2)循环水温度较高,降低了蒸汽与水之间的温度差,冷却效力减弱。
3)循环水质不好,使冷凝器内管束结垢甚至堵塞,热阻增大,降低了冷却效力。
4)冷凝器内液位过高,淹没了管束,减少了蒸汽与冷却水的换热面积。
5)抽气器喷射入口蒸汽压力低,抽气器效力低。
6)抽气器因喷嘴结垢、堵塞或磨损,效力降低。
7)真空系统不严密,空气漏入系统。
8)各机组负荷增加,排汽量增加,增加了冷凝器负荷。
9)因为冷凝器真空降低,引起各机组的排汽量增加,反过来进一步降低真空度。
1、3、半贫液闪蒸槽喷射器(1107-LA/LB/LC/LD)的投用在半贫液闪蒸槽半贫液入口管线上的阀门LV4013全开,工艺气已经进入(1104-C),(1105-C),(1160-C),热量已经输入系统。
监测(1104-C)的液位,用产生的蒸汽投运半贫液闪蒸槽喷射器(1107-LA/LB/LC/LD),如果蒸汽不足,可以使用外来的低压蒸汽补充,以便使闪蒸槽的各级压力达到设计值。
制氢装置炉子管理和操作规程

制氢装置炉子管理和操作规程1.1加热炉投用前的检查准备工作(1)检查炉膛内衬里无脱落,其他附件完好。
(2)炉膛内和炉区周围环境清扫干净,人孔、防爆门、看火窗封好。
(3)加热炉零部件,如烟道挡板、看火孔、防爆门、火嘴一、二次风门灵活好用。
(4)加热炉的自保系统、压力表、热电偶,各有关控制阀、手阀灵活好用。
(5)瓦斯系统气密转置换合格,处于可开工状态,火嘴、长明灯清洗搞通,并安装好,瓦斯软管脱开。
(6)消防器具齐全好用。
(7)检查确认瓦斯系统流程,将引瓦斯至调节阀前,用瓦斯置换残存在管线的氮气并注意防止瓦斯漏入加热炉炉膛,投用V2025伴热蒸汽,并将液体排净。
(8)确认所有炉管有均匀介质流动。
(9)全开风门和烟道挡板,保持炉膛通风良好,然后炉膛采样做动火分析合格。
(10)准备好点火工具。
1.2 引燃料气的操作(1)改通瓦斯系统流程瓦斯PCA7502 KV7102 TC7101 F2001FV7502 F2002(2)瓦斯系统置换调通装置界区平台低压氮至瓦斯的8字盲板,向瓦斯充入氮气至0.1MPa后,打开安全阀SV2007跨线,对瓦斯系统置换。
氧含量小于0.5%合格。
(3)瓦斯系统气密从界区低压氮充氮线向瓦斯系统充入低压氮至0.5MPa后,利用肥皂水对瓦斯系统进行气密。
(4)联系生产调度,准备引燃料气进装置。
(5)确认加热炉火咀、长明灯手阀已全关、管线高低点放空手阀已关。
(6)微开瓦斯界区阀,将瓦斯引至F2001、F2002火嘴手阀前,当瓦斯压力达到0.1MPa时,关闭瓦斯界区阀,打开安全阀SV2007跨线,对瓦斯系统置换。
置换两遍后,重新打开瓦斯界区阀,将瓦斯引至F2001、F2002火嘴手阀前。
(7)联系分析站采瓦斯样作气体组成分析。
1.3 点火操作1.3.1 加热炉的点火操作⑴关闭各瓦斯火嘴和长明灯的炉前手阀等有关手阀。
⑵将瓦斯引至长明灯及火嘴各手阀前。
⑶关闭一次风门,稍开二次风门,将烟道挡板的开度调至最小,尽量降低炉膛负压。
- 1、下载文档前请自行甄别文档内容的完整性,平台不提供额外的编辑、内容补充、找答案等附加服务。
- 2、"仅部分预览"的文档,不可在线预览部分如存在完整性等问题,可反馈申请退款(可完整预览的文档不适用该条件!)。
- 3、如文档侵犯您的权益,请联系客服反馈,我们会尽快为您处理(人工客服工作时间:9:00-18:30)。
煤制油天然气制氢烃类蒸汽转化炉设备操作规程一、简介以烃类为原料,用蒸汽转化法生产合成氨原料气和氢气,在合成氨、炼油、石油化工、冶金等工业部门具有特定的地位。
炼油厂的制氢炉、甲醇厂的制氢转化炉合成氨厂的一段转化炉等都属于烃类蒸汽转化炉。
其工作原理、操作参数和结构设计等都大致相同。
所不同的是合成氨厂因有二段转化炉,因此其一段转化炉的转化率要低一些,残余甲烷比制氢炉高一倍左右,一段转化炉的残余甲烷一般是12%-15%,而制氢炉的仅5%-7%。
就合成氨工业而言,目前世界上应有该法生产的原料气占其总产量的80%以上。
天然气蒸汽转化最早由德国法本公司,英国I.C.I公司和美国美孚公司进行研究,1936年英国建立了第一套生产装置,1959年英国又建立了第一套石脑油蒸汽转化装置,该技术得到了进一步的发展并日趋完善。
烃类蒸汽转化制氢的路线具有工艺流程短、投资省、能量利用合理、自控程度高、环境污染少等优点,因此,应用极为普遍。
为多生产化肥支持农业,我国在上世纪70年代引进薄8套以天然气为原料的大型合成氨装置,建于大庆、辽河、沧州、齐鲁二化、泸天化、赤天化、云天化;80年代迄今又引进8套以天然气为原料的大型合成氨装置,建于濮阳、锦西、涪陵、合江、海南、乌石化。
二、烃类蒸汽转化概述1.烃类蒸汽转化热力学1.1化学反应主要反应:CH4+H2O→CO+3H2-206288kj∕kg·molCH4+2H2O→CO+4H2-185098kj∕kg·molCH4+CO2→2CO+2H2-247478 kj∕kg·molCO+H2O→CO2+H2-41190kj∕kg·mol析碳反应:CH4→C+2H2-74898 kj∕kg·mol2CO→C+CO2+172580 kj∕kg·molCO+H2→C+H2O+131390 kj∕kg·mol对于烃类混合物(包括轻油)转化时,通过换算,用下列统式表示:CHm+(a+b)H2O→Aco+bCO2+(1-a-b)CH4+(3a+4b-4-m ∕2)H21.2 影响平衡甲烷含量的因素根据反应式,用平衡转移的原理进行分析。
温度:因为是吸热反应,温度升高,则平衡甲烷含量降低,反之则升高。
压力:因为是增分子反应,压力升高,则平衡甲烷含量升高,反之,则降低。
水碳比:水碳比增加,相当于向系统中加入水蒸气。
平衡向生成一氧化碳的方向移动,甲烷含量减少,反之,则升高。
氢碳比:原料的氢碳比增加,相当于向系统加入氢气,则平衡向生成甲烷饿方向移动,平衡甲烷含量省锆,反之,则降低。
三、烃类蒸汽转化流程1、凯洛格流程天然气首先被压缩至3.6MPa,通过对流段预热至350℃左右进入钴钼反应器和氧化脱硫槽,将硫脱至小于后与中压蒸汽混合(水碳比为2.7-3.5),再入对流段预热至520℃左右,通过上集气管,猪尾管从辐射段顶部进入转化炉管,在转化炉管内边反应边吸热,当离开炉管底部时温度达820℃,甲烷含量为10%左右,压力3.1MPa,经炉底分集气管和上升管,0.5ppm温度升至850℃左右,出炉顶汇集子集气总管再入二段炉。
工艺空气压缩至3.3-3.5MPa并混入少量蒸汽经对流段预热至450℃后进入二段炉,与一段炉转化气混合、燃烧、进一步转化、出二段炉的温度达1000℃左右,甲烷含量小于0.4%,二段炉出来的工艺气经第一,第二废热锅炉温度降至370℃以后进入变换炉。
辐射段出来的烟气温度为1000℃左右,经对流段预热工艺混合气,工艺空气,动力蒸汽,原料气锅炉给水等使温度降至240℃左右后由引风机排入大气。
流程设置中的关键设备为一段转化炉,烃类蒸汽转化反应主要在此进行,为了维持正常操作,必须使转化反应和传热相适应,在满足工艺要求的前提下,力求降低对转化炉管的要求和节约高温合金钢的使用。
就合成氨生产而言,它要求转化后的甲烷含量越低越好,一般不大于0.5%,如果这任务全由一段炉来承担,则出口温度为1000℃左右,这无疑对炉管材料的要求太苛刻了。
由于制合成氨原料气时需要氮。
因而又引出了二段炉流程,一段炉反应所需的热量是通过管壁从高温烟气中传入的,因此对炉管要求较高,因二段炉是绝热反应,高温的或得是靠工艺气中的氢、一氧化碳和甲烷与空气中的氧燃烧,不需传热的高合金材料,只需耐火衬里就行了。
对于制氢,就不能没二段炉,它的操作条件也不一样,所得气体中甲烷含量也远大于0.5%,对流段的设置,一方面是充分利用废热,另一方面也是减少辐射段的热负荷,以就可节省高温材料。
脱硫设备的设置是由于转化催化剂的要求。
二段炉气废热锅炉的设置也是充分回收能量。
四、一段转化炉炉型4、1 烃类蒸汽转化炉的要求:(1)烃类蒸汽转化炉的工作条件比较苛刻,使用的都是耐高温的镍铬的合金材料,因此在炉子设计时要求合理使用炉管及尽量降低对炉管的要求,防止局部过热,使周向和轴向温度分布均匀。
(2)烃类蒸汽转化是伴有传热、传质、动量传递和复杂化学反应的综合过程,要求传热与反应必须相适应,对于并行的复杂反应,能够控制其反应的进程。
设计时所选用的炉型、原料、催化剂和操作条件是一个整体,不能乱套,我国两湖的气改油工程中出现的问题就是一个教训。
(3)力求炉子结构简单、紧凑。
(4)热能利用率高。
4、2 现目前世界上有代表性的I.C.I、Topse、kellogg和Foster Wheeler四种炉型。
现结合神华天然气装置,主要介绍Kellogg型转化炉。
4、2、1、 Kellogg型转化炉引进的年产30*104t合成氨装置中的转化炉,如图:1)转化炉结构尺寸为13m(长)*17m(宽)*10m(高)。
炉内装有378根炉管、分为9排、每排42根。
每排炉管下端与一个下集气管焊接,下集气管外面有轻质绝热材料保温,集气管的中间又焊上一根上升管,九个上升管伸出炉顶与集气总管连接,集气总管内衬耐火材料。
这种炉管排列又称竖琴式,增加产量,只需增加排数即可。
2)催化剂管及下集气管的重量是由固定在炉顶钢架上的189个弹簧支架承担,上升管和输气总管的重量由几个输气管弹簧承担,因此,九排炉管及输气总管均处在弹簧支架的弹性吊挂状态。
这种全部采用钢性焊接的管排在操作时因热膨胀差而产生热应力就可以大部分被这种弹簧吊挂系统所吸收。
、3)辐射室顶部共装有200个自吸式烧嘴,炉底下烟道内都设置一个辅助烧嘴,以供给对流段热量不足。
4)脱硫后的工艺混合气预热至510℃由上集气管经上猪尾管通入转化炉内,气流从上向下流动,边加热边反应,转化炉管出口处温度达823℃,进入下集气管经上升管再加热至868℃,进炉顶的集气总管后再进入二段炉。
燃料天然气经烧嘴燃烧后垂直向下,出辐射段温度为1025℃左右,经对流段,最后由引风机引出,其温度为252℃.5)炉管规格为∮112mm(外径)*∮71 mm(内径)*9582mm(总长)材质为HK-40,设计温度为932℃,设计压力为3.4MPa,操作时,管外壁最高温度为899℃,进口压力为3.6MPa,进出口压差为0.5MPa.传热面为1286.7㎡,炉管热负荷为73。
5MW,传热强度为55700W∕㎡催化剂装载量为15.3m3,催化剂型号为C-119.规格为:上层∮15.9(外圆)*∮6.4(内圆)*6.4(高);下层∮15.9 *∮6.4*9.5或∮15.9)*∮6.4*15.9。
下集气管材质为Incoloy-800;上升管材质为Superthem(超热合金钢),规格为∮123*∮91*9536,传热面为32.5㎡.4、2 、2 Kellogg型转化炉的特点:1) Kellogg型转化炉的特点之一:是采用了竖琴式炉管结构,取消下猪尾管,一排垂直地焊接在下集气管上,而由上升管经工艺气引出炉外,炉管和上升管都置于炉内,都处于高温下工作,虽然上升管的温度稍高于转化炉管,但材料的线膨胀系数前者略小于后者,因此热膨胀相差不大所产生的热应力全由炉顶的弹簧支架承担。
这一结构可节约炉管材料,提高管材料利用率,避免了炉底空气的漏入,降低了烟气含氧量,由于炉管和集气管都置于炉内,减少了热损失,对前面两种炉型讲,一段炉出来进入二段炉,温降达20~30℃,而该炉通过上升管,反而温升30℃,和Tops∮e一样,卸催化剂不方便,必须从炉顶抽出。
一旦损失,必须停车,将整排炉管吊出更换,为了维持正常操作,要求更苛刻,设计时必须留有更大的安全系数。
2) Kellogg转化炉的特点之二:是采用小直径的转化炉管,其径内只有71mm,是目前使用的各种炉型中最小的。
在此,我们讨论一下最佳化管径的选取问题,最佳化的标准是在同样的生产能力下,生产氨的成本最低。
对转化炉这一局部问题来讲,应该是同样生产能力下,使生产能力下,生产氨的成本最低。
对转化管这一布局问题来讲,应该是同样生产能力下,使用的转化管材最少,影响的因素较多,烃类蒸汽转化是强吸热过程。
Kellogg转化炉也是顶烧炉,像I.C.I炉一样,保留了顶烧炉的一切优点。
Kellogg转化炉的操作空速为1800h,接近I.C.I的二倍,因此一段炉炉管阻力降大,阻力降达0.5MPa,动力损耗较大。
4、3 Kellogg型转化炉结构与材料4、3、1、Kellogg型转化炉结构Kellogg型转化炉又称为排管型顶烧炉1)炉管结构转化炉在辐射段有九段转化管,每排有一根上集气管、42根猪尾管、42根转化管、底部有一根下集气管和一根从下集气管中点通向炉顶输气管的上升管。
42根转化管对称地分布于上升管两侧,每侧21根,组成转化管排结构(亦称竖琴管系),见图11-17.气体经对流段混合原料器加热到510℃,然后进入进气总管,再分配到九根并列的上集气管中(见图11-18)。
每根上集气管则通过42根挠性的入口猪尾管与42根转化管相通,组成原料气进气系统。
进气总管构成尺寸很大的“门”形,以解决管系的热膨胀,因为由常温下安装到开工后加热操作,进气总管、进气支管、上集气管均有相当达的热膨胀量,这种三维空间的热膨胀势必再进气管系中引起数值很大的热应力。
为了吸收这以热应力,进气总管采用六个弹簧支架支撑。
进气总管尺寸为∮305mm,总长度为35.87m,管材为含碳0.3%的碳钢(ASTM106GrB)。
九根上集气管的直径为∮152mm,材质与进气总管相同。
每根上集气管的末端都用盲板法兰封死,必要时可以拆开检查或清理内部。
每根上集气管用三个支座支撑在炉顶钢梁上(见图11-19)。
考虑到上集气管热膨胀量较大,三个支座中只有中间那个支座用螺栓固定死,其余两个都是活动支座。
这样,受热后上集气管可以从中间支座处向两端伸长,比只向一端热膨胀移动量小。
上集气管与猪尾管间采用承插管座焊接,藉以对管子开孔进行补强,管座材料为ASTMA105GrⅡ段件。