柴油机汽车悬置系统优化设计
动力总成悬置系统优化及稳健性分析
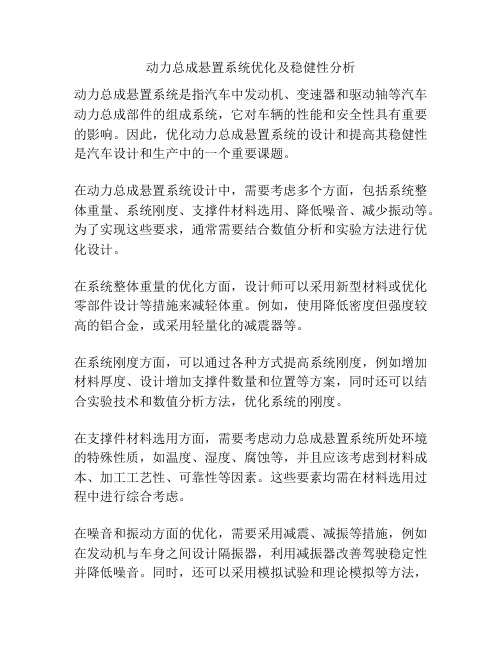
动力总成悬置系统优化及稳健性分析动力总成悬置系统是指汽车中发动机、变速器和驱动轴等汽车动力总成部件的组成系统,它对车辆的性能和安全性具有重要的影响。
因此,优化动力总成悬置系统的设计和提高其稳健性是汽车设计和生产中的一个重要课题。
在动力总成悬置系统设计中,需要考虑多个方面,包括系统整体重量、系统刚度、支撑件材料选用、降低噪音、减少振动等。
为了实现这些要求,通常需要结合数值分析和实验方法进行优化设计。
在系统整体重量的优化方面,设计师可以采用新型材料或优化零部件设计等措施来减轻体重。
例如,使用降低密度但强度较高的铝合金,或采用轻量化的减震器等。
在系统刚度方面,可以通过各种方式提高系统刚度,例如增加材料厚度、设计增加支撑件数量和位置等方案,同时还可以结合实验技术和数值分析方法,优化系统的刚度。
在支撑件材料选用方面,需要考虑动力总成悬置系统所处环境的特殊性质,如温度、湿度、腐蚀等,并且应该考虑到材料成本、加工工艺性、可靠性等因素。
这些要素均需在材料选用过程中进行综合考虑。
在噪音和振动方面的优化,需要采用减震、减振等措施,例如在发动机与车身之间设计隔振器,利用减振器改善驾驶稳定性并降低噪音。
同时,还可以采用模拟试验和理论模拟等方法,以确定系统的不同工况下的振动和噪声水平,并加以适当的改善。
此外,动力总成悬置系统的稳健性分析也是一个非常关键的方面。
系统的稳健性指的是系统能够在各种不确定情况下保持良好的性能和稳定性。
在系统的稳健性分析中,需要考虑到各种可能的负载情况、失效情况和故障情况,并结合设计要求和汽车行驶情况,确定系统的最佳稳健性设计方案。
这一过程需要采用可靠性分析方法,综合评估系统的稳健性。
总之,动力总成悬置系统的优化和稳健性设计是汽车工程设计中的一个重要环节。
通过采用先进的设计方法和技术手段,可以不断提高汽车的性能和安全性,满足消费者不断增长的需求和期望。
此外,为了实现动力总成悬置系统的优化和稳健性设计,需要充分了解系统的工作原理和特性。
汽车动力总成悬置系统优化设计PPT课件
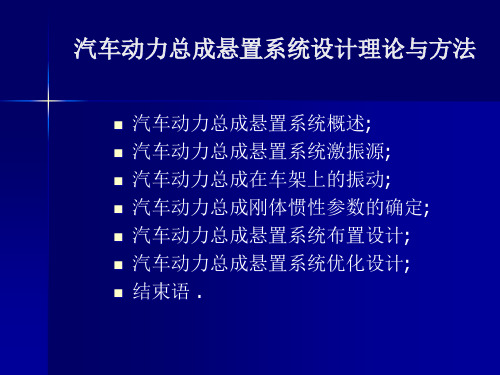
旋转惯性力
Pr m1r 2
其水平和垂直的两个分量:
PjⅡ m2r2 cos 2 二级往复惯性力;
注:二级以上往复惯性力很小,已略去。
Prx m1r2 cost Pry m1r 2 sint
二、汽车动力总成悬置系统激振源
2. 发动机的干涉力和力距
c. 惯性力系的平衡 发动机平衡的含义:
惯性力系平衡; 转矩的均匀性。
三、汽车动力总成在车架上的振动
1. 发动机的自由振动
2)系统模型
如图3-1所示。
3)、自由振动方程
整机振动可分解为随同它的质心c点沿 X 、Y 、Z
的三个平动,和绕质心的转动。在微振动条件下,其角
位移可用绕 X 、Y 、Z 轴的转角 、 、 表示。当刚
体作六自由度自由振动时,有如下的表达式:
Mxc Fx
对因汽车摆动造成的车架扭转具有良好的运动顺从性。 阻抗和隔绝动载荷
有效地抑制在汽车行驶中,因道路凹凸不平而引起的激振影响 支承动、静载荷
在所有工况下,承受所有动、静载荷,并使动力总成在所有方 向上的位移处于可接受的范围内,不与底盘上的其他零部件发 生干涉。 保证发动机机体与飞轮壳的连接面弯矩不超过允许值。 保证合理的使用寿命
二、汽车动力总成悬置系统激振源
4. 激振频率分析
经分析可知:
a. 由不平衡量引起的激振力是离心力,它与转速成正比,只有在高转速时其作用 才显著。
b. 均匀点火脉冲的激励作用只有在低速时才明显。由上可知,发动机作为激振源 的激振频率范围为:
c. 地面激振频率范围:
1.5~2.5
可作为悬置设计时依据。
式中:Q -比例常数,一阶不平衡力Q=1,二阶不平衡力Q=2 c. 传动轴(变速器挂直接档)不平衡质量引起的激振频率:
动力总成悬置系统优化设计与匹配---基本理论
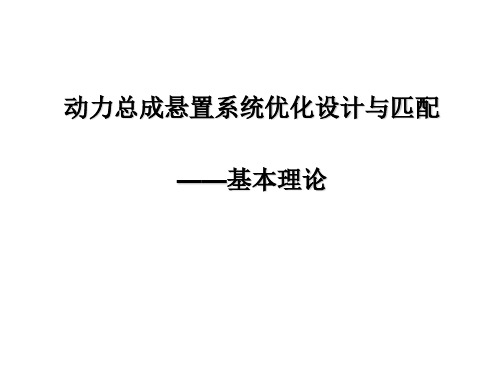
目录
一、悬置系统的典型结构及基本理论 二、悬置系统的主要布置方式 三、悬置系统的设计原则 四、悬置系统对汽车N&V特性的影响 五、悬置系统的设计流程和计算方法 六、悬置系统的匹配样车要求及N&V匹配方法
一、悬置系统的基本理论及典型结构
1、悬置的定义:装配在动力总成与车身(架)之间起支撑连接作用并使二者间 的力的传递产生衰减的弹性减振元件。
动力总成的完全解耦布置
动力总成的部分解耦布置
四、悬置系统的设计原则
撞击中心理论:
撞击中心理论主要用于选择前后悬置的位置。当动力总成视为 刚体,前后悬置如果处于互为撞击中心的位置上时,当一个悬置受 到干扰时或冲击时,另一个悬置上的响应为零。
扭轴理论:
当发动机的主惯性轴偏离曲轴轴线 一定角度, 在发动机激振力矩作用下, 发动机体将绕某一固定的“扭轴”作 白由振动。这时悬置布置应围绕“扭 轴”布置更为合理。
2、悬置系统(悬置+发动机+变矩器+变速箱)典型结构
3、各种类型悬置结构
一、悬置系统的基本理论及典型结构
悬置的结构型式日趋复杂。主要分为:橡胶悬置、液压悬置、 半主动/主动悬置。
橡胶悬置:结构简单,成型容易、成本低廉,被大量的使用在各型 车辆。缺点:存在高频硬化现象。下面为橡胶悬置常见结构:
压缩式
一、悬置系统的基本理论及典型结构
悬置系统六自由度力学方程的建立(势能)
一、悬置系统的基本理论及典型结构
悬置系统六自由度力学方程的建立(势能)
一、悬置系统的基本理论及典型结构
悬置系统六自由度力学方程的建立(耗散能)
一、悬置系统的基本理论及典型结构
《汽车动力总成悬置系统振动分析及优化设计》

《汽车动力总成悬置系统振动分析及优化设计》篇一一、引言随着汽车工业的飞速发展,消费者对汽车的性能和舒适性要求日益提高。
汽车动力总成悬置系统作为汽车的重要组成部分,其性能的优劣直接影响到整车的振动噪声水平以及乘坐舒适性。
因此,对汽车动力总成悬置系统的振动进行分析,并进行优化设计,对于提高汽车的整体性能具有重要意义。
本文将针对汽车动力总成悬置系统的振动进行分析,并提出相应的优化设计方案。
二、汽车动力总成悬置系统概述汽车动力总成悬置系统是指将发动机、变速器等动力总成与车身进行连接的装置,其作用是减小动力总成产生的振动和噪声对整车的影响。
该系统主要由橡胶支座、液压支座、金属支座等组成,通过这些支座将动力总成的振动和冲击传递给车身,并起到减振、降噪的作用。
三、汽车动力总成悬置系统振动分析1. 振动产生原因汽车动力总成悬置系统振动的主要原因是发动机工作时产生的激励力,包括往复运动产生的惯性力和旋转运动产生的扭矩。
此外,路面不平、轮胎非线性等因素也会对系统产生一定的振动影响。
2. 振动传递路径动力总成的振动通过悬置系统传递到车身,再传递到车内乘客。
传递路径主要包括橡胶支座、液压支座等部件的弹性变形以及金属支座的刚度传递。
3. 振动分析方法针对汽车动力总成悬置系统的振动分析,可采用实验分析和数值分析两种方法。
实验分析主要通过实车测试和台架试验获取数据;数值分析则通过建立动力学模型,运用有限元等方法进行仿真分析。
四、汽车动力总成悬置系统优化设计1. 设计目标汽车动力总成悬置系统优化设计的目标是在保证动力总成正常工作的前提下,降低整车的振动噪声水平,提高乘坐舒适性。
同时,还需考虑系统的耐久性、可靠性以及制造成本等因素。
2. 优化设计方案(1)材料选择:选用高弹性、高阻尼的材料制作橡胶支座,以提高系统的减振性能。
同时,根据实际需要,可考虑在部分支座中加入液压减振元件,进一步提高减振效果。
(2)结构优化:对悬置系统的结构进行优化设计,如调整支座的布置位置、改变支座的刚度等,以改变振动的传递路径和传递速度,从而达到降低整车振动噪声的目的。
车辆悬挂系统的优化设计

车辆悬挂系统的优化设计车辆悬挂系统作为汽车重要的组成部分,直接关系到车辆行驶的平稳性、舒适性和安全性。
优化悬挂系统设计能够提高车辆性能和乘坐体验,本文将围绕车辆悬挂系统的优化设计展开论述。
一、悬挂系统的基本原理与作用车辆悬挂系统通过悬挂弹簧、减震器和悬挂支架等部件,连接车身和车轮,起到支撑和缓冲作用。
悬挂系统能够吸收路面不平,减少车身的颠簸,保证驾乘的舒适性和稳定性。
同时,悬挂系统还能够保护车身、发动机和传动系统等重要部件,延长其使用寿命。
二、悬挂系统的优化设计目标1. 提高车辆的行驶稳定性。
悬挂系统的优化设计需要考虑车辆在高速行驶、转弯、制动等情况下的稳定性,减少侧翻和摇晃。
2. 提升乘坐的舒适性。
通过减震器的优化设计,降低车辆受到的颠簸和震动,提供舒适的驾乘环境。
3. 提高悬挂系统的可靠性和耐久性。
悬挂系统需要在各种复杂的路况下保持良好的工作状况,提升其使用寿命和可靠性。
4. 降低车辆的燃油消耗。
通过优化悬挂系统的设计,减少不必要的能量损耗,提高车辆的燃油利用效率。
三、悬挂系统的优化设计方法1. 材料选择与强度分析。
选用高强度、耐疲劳的材料,同时进行强度分析和优化设计,确保悬挂系统在受力情况下不会发生变形或破裂。
2. 建立悬挂系统的数学模型。
通过建立悬挂系统的数学模型,包括弹簧刚度、减震器参数等,进行仿真分析和优化设计。
3. 减震器的优化设计。
减震器的合理设计能够有效抑制车身的振动,提供更好的驾乘体验。
优化设计减震器的阻尼特性和刚度,以满足车辆不同行驶状态下的需求。
4. 悬挂系统的悬架结构优化。
悬挂系统的悬架结构也会影响整个系统的性能。
通过优化悬挂支架等部件的结构,降低重量,提高刚度和强度,进一步改善悬挂系统的性能。
5. 考虑多种路况和行驶状态。
在悬挂系统的优化设计中,需要考虑不同的路况和行驶状态,如高速行驶、弯道行驶、起步和制动等情况,以确保悬挂系统在各种条件下都能提供最佳的性能和驾乘体验。
《汽车动力总成悬置系统振动分析及优化设计》范文

《汽车动力总成悬置系统振动分析及优化设计》篇一一、引言汽车动力总成悬置系统作为车辆动力传递与振动控制的关键部分,其性能的优劣直接关系到整车的驾驶舒适性和行驶稳定性。
因此,对汽车动力总成悬置系统的振动进行分析,并进行相应的优化设计,是汽车工程领域研究的重要课题。
本文将深入探讨汽车动力总成悬置系统的振动问题,分析其成因,并针对现有问题提出优化设计方案。
二、汽车动力总成悬置系统概述汽车动力总成悬置系统主要由发动机、变速器、离合器等组成,通过悬置装置与车架相连。
其作用是支撑和固定动力总成,同时减少振动和噪声的传递,保证驾驶的舒适性和行驶的稳定性。
三、汽车动力总成悬置系统振动分析1. 振动产生原因汽车动力总成悬置系统振动的主要原因是发动机运转时产生的激励力,包括燃烧力、惯性力和摩擦力等。
此外,道路不平、车辆行驶中的颠簸等也会对悬置系统产生振动。
2. 振动影响分析振动不仅会影响驾驶的舒适性,还会对车辆的行驶稳定性、零部件的寿命和车辆的噪音产生影响。
长期受到振动的零部件容易出现松动、磨损等问题,影响车辆的正常运行。
四、汽车动力总成悬置系统优化设计针对汽车动力总成悬置系统的振动问题,本文提出以下优化设计方案:1. 材料选择优化选用高强度、轻量化的材料,如铝合金、高强度塑料等,以降低系统质量,提高其刚度和减振性能。
同时,采用阻尼材料,如橡胶等,以吸收振动能量,减少振动传递。
2. 结构优化设计对悬置系统的结构进行优化设计,如增加支撑点、改变支撑方式等,以提高系统的稳定性和减振性能。
同时,采用多级减振设计,使系统在不同频率下的减振效果更加明显。
3. 控制系统优化通过引入先进的控制系统,如液压控制系统、电子控制系统等,对悬置系统的振动进行实时监测和控制。
通过调整控制参数,使系统在不同工况下都能保持良好的减振性能。
五、结论通过对汽车动力总成悬置系统的振动分析,我们发现其产生的主要原因包括发动机运转产生的激励力和道路、行驶中的颠簸等外部因素。
上海众力动力总成悬置系统最优化设计与匹配
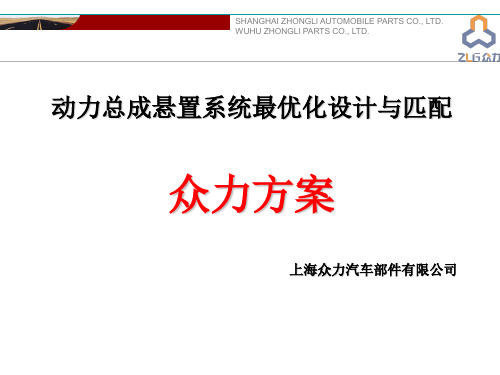
一、悬置系统的基本理论及典型结构
(5.2)液压悬置:为实现悬置低频高阻尼高刚度、高频(30250Hz,0.05-0.1mm)低阻尼低刚度以及解决橡胶悬置的高频硬化现 象而诞生。典型结构:
搅拌式
节流孔式
惯性流道式
惯性流道解耦盘(膜)式
液阻衬套式
SHANGHAI ZHONGLI AUTOMOBILE PARTS CO., LTD. WUHU ZHONGLI PARTS CO., LTD.
三、悬置系统对汽车N&V特性的影响
动力总成的 振动
悬置
车身的 振动
对车内噪声 产生影响
隔 振
较大的振动
衰减后较小 的振动 车内振动影 响车内噪声
SHANGHAI ZHONGLI AUTOMOBILE PARTS CO., LTD. WUHU ZHONGLI PARTS CO., LTD.
三、悬置系统对汽车N&V特性的影响
5.悬置的结构:通过近百年的发展,悬置的结构型式日趋复杂。主要 表现为:橡胶悬置、液压悬置、半主动/主动悬置。
(5.1)橡胶悬置:结构简单,成型容易、成本低廉;被大量的使用在 各型车辆。缺点:存在高频硬化现象。
常见的结构:压缩式
剪切式
复合式
SHANGHAI ZHONGLI AUTOMOBILE PARTS CO., LTD. WUHU ZHONGLI PARTS CO., LTD.
悬置元件最主要的两个作用: 1、支撑动力总成,约束动力总成的位移。 2、隔离动力总成的振动向车身的传递,提高整车的N&V水平。 悬置的刚度越高有利于支撑动力总成,对整车的N&V不利。 悬置的刚度越低对整车的N&V有利,不利于动力总成的支撑。
《汽车动力总成悬置系统振动分析及优化设计》范文

《汽车动力总成悬置系统振动分析及优化设计》篇一一、引言随着汽车工业的快速发展,汽车动力总成悬置系统的性能逐渐成为影响汽车舒适性和稳定性的关键因素。
本文将重点对汽车动力总成悬置系统的振动特性进行分析,并提出相应的优化设计方案,以期为提高汽车性能提供有益的参考。
二、汽车动力总成悬置系统概述汽车动力总成悬置系统是连接发动机、变速器等动力总成部件与车身的重要装置,其主要作用是减少振动、降低噪音、提高汽车的乘坐舒适性。
该系统通常由橡胶支座、金属支架、减震器等组成,其性能直接影响着汽车的行驶稳定性和乘坐舒适性。
三、汽车动力总成悬置系统振动分析1. 振动来源:汽车动力总成悬置系统的振动主要来源于发动机的运转、变速器的换挡以及路面不平度等因素。
这些因素产生的振动会通过悬置系统传递到车身,影响汽车的行驶性能。
2. 振动特性:汽车动力总成悬置系统的振动具有高频、低频及复杂性的特点。
其中,高频振动主要与发动机运转有关,低频振动则与路面不平度等因素有关。
此外,由于汽车行驶环境的复杂性,悬置系统还可能受到多种因素的耦合作用,导致振动更加复杂。
四、汽车动力总成悬置系统优化设计针对汽车动力总成悬置系统的振动问题,本文提出以下优化设计方案:1. 材料选择:选用高弹性、高阻尼性能的材料制作橡胶支座,以提高悬置系统的减震性能。
同时,采用轻质材料制作金属支架,以降低系统重量,提高整体性能。
2. 结构优化:对悬置系统的结构进行优化设计,如增加减震器数量、改变支座布置方式等,以更好地吸收和分散振动能量。
此外,还可以采用柔性连接方式,使悬置系统在受到外界冲击时能够产生一定的变形,从而减少振动传递。
3. 控制系统设计:引入现代控制技术,如主动悬挂控制系统等,对汽车动力总成悬置系统的振动进行实时监测和控制。
通过调整减震器的刚度和阻尼等参数,实现对振动的主动控制,提高汽车的行驶稳定性和乘坐舒适性。
五、结论通过对汽车动力总成悬置系统的振动分析及优化设计,可以有效提高汽车的行驶稳定性和乘坐舒适性。
《汽车动力总成悬置系统振动分析及优化设计》范文

《汽车动力总成悬置系统振动分析及优化设计》篇一一、引言随着汽车工业的飞速发展,消费者对汽车的性能和舒适性要求越来越高。
其中,汽车动力总成悬置系统的振动问题直接影响着汽车的乘坐舒适性和驾驶稳定性。
因此,对汽车动力总成悬置系统的振动进行分析及优化设计显得尤为重要。
本文将重点探讨汽车动力总成悬置系统的振动分析方法及优化设计策略,以期为相关研究和应用提供参考。
二、汽车动力总成悬置系统概述汽车动力总成悬置系统是连接发动机、变速器等动力总成部件与车身的重要装置,其主要作用是减少振动传递,提高乘坐舒适性和驾驶稳定性。
该系统通常由发动机悬置、变速器悬置、支撑架等组成。
三、汽车动力总成悬置系统振动分析1. 振动来源及传递路径汽车动力总成悬置系统的振动主要来源于发动机的运转、路面不平引起的车身振动等。
这些振动通过发动机悬置、变速器悬置等传递到车身,进而影响乘坐舒适性和驾驶稳定性。
2. 振动分析方法(1)理论分析:通过建立动力学模型,分析系统在不同工况下的振动特性。
(2)实验分析:利用传感器、数据采集系统等设备,对实际车辆进行振动测试,获取振动数据。
(3)仿真分析:运用计算机仿真技术,对系统进行仿真分析,预测振动特性。
四、汽车动力总成悬置系统优化设计1. 设计目标优化设计的目标是在保证动力总成部件安全性的前提下,降低振动传递,提高乘坐舒适性和驾驶稳定性。
2. 优化策略(1)材料选择:选用高强度、轻质材料,降低系统质量,提高系统刚度。
(2)结构优化:通过优化悬置结构、支撑架结构等,降低振动传递。
例如,采用多级减震设计、橡胶减震垫等措施。
(3)动力学性能优化:通过理论分析和仿真分析,对系统动力学性能进行优化,提高乘坐舒适性和驾驶稳定性。
3. 优化设计流程(1)需求分析:明确设计目标,了解用户需求。
(2)方案设计:根据需求分析,提出多种设计方案。
(3)理论分析:运用动力学理论,对各方案进行理论分析。
(4)仿真分析:运用计算机仿真技术,对各方案进行仿真分析,预测振动特性。
《汽车动力总成悬置系统振动分析及优化设计》

《汽车动力总成悬置系统振动分析及优化设计》篇一一、引言随着汽车工业的快速发展,汽车动力总成悬置系统的性能已成为决定汽车乘坐舒适性和驾驶稳定性的关键因素之一。
然而,由于动力总成系统在运行过程中产生的振动和噪音,严重影响了汽车的性能和使用寿命。
因此,对汽车动力总成悬置系统的振动进行分析,并进行优化设计,具有重要的理论价值和实践意义。
本文将重点对汽车动力总成悬置系统的振动进行分析,并探讨其优化设计的方法和措施。
二、汽车动力总成悬置系统概述汽车动力总成悬置系统主要由发动机、变速器、离合器等组成,是汽车的核心部件之一。
其作用是支撑和固定动力总成,减少振动和噪音的传递,保证汽车行驶的平稳性和舒适性。
然而,由于动力总成系统的复杂性和运行环境的多样性,使得其振动问题较为突出。
三、汽车动力总成悬置系统振动分析(一)振动产生的原因汽车动力总成悬置系统振动产生的原因主要包括发动机的燃烧过程、变速器的齿轮啮合、离合器的接合与分离等。
此外,道路不平度、车辆行驶速度等因素也会对系统振动产生影响。
(二)振动分析的方法目前,常用的汽车动力总成悬置系统振动分析方法包括实验分析和仿真分析。
实验分析主要通过在真实环境下对系统进行测试,获取其振动数据;仿真分析则通过建立系统的数学模型,利用计算机软件进行模拟分析。
(三)振动的影响汽车动力总成悬置系统的振动会直接影响汽车的乘坐舒适性和驾驶稳定性。
同时,长时间的振动还会导致系统零部件的磨损和损坏,影响汽车的使用寿命。
四、汽车动力总成悬置系统优化设计(一)优化设计的目标汽车动力总成悬置系统优化设计的目标主要包括提高汽车的乘坐舒适性和驾驶稳定性,延长汽车的使用寿命,降低噪音和振动等。
(二)优化设计的措施1. 改进材料:采用高强度、轻量化的材料,提高系统的刚度和减振性能。
2. 优化结构:通过改变系统的结构形式和参数,如增加橡胶减振器、调整悬置点的位置等,提高系统的减振效果。
3. 智能控制:利用现代控制技术,如主动悬挂系统、半主动悬挂系统等,实现对系统振动的主动控制。
a6改装柴油机后发动机悬置系统和冷却系统的优化设计
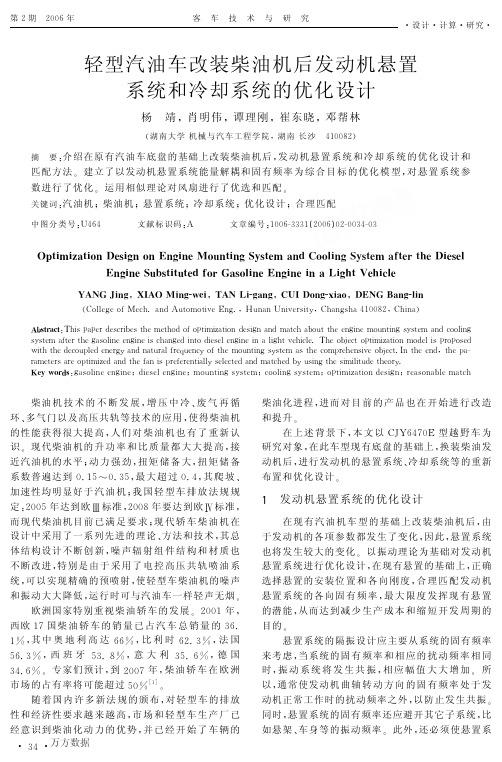
《2024年汽车动力总成悬置系统振动分析及优化设计》范文

《汽车动力总成悬置系统振动分析及优化设计》篇一一、引言随着汽车工业的快速发展,汽车动力总成悬置系统的性能对于整车舒适性和稳定性越来越重要。
汽车动力总成悬置系统作为连接发动机和车身的重要部件,其振动特性直接影响到汽车的乘坐体验和行驶安全。
因此,对汽车动力总成悬置系统的振动进行分析,以及进行优化设计,已经成为汽车研发过程中的重要课题。
二、汽车动力总成悬置系统概述汽车动力总成悬置系统主要由发动机、悬置支架、橡胶支座等组成。
其主要功能是减少发动机振动对车身的影响,同时通过合理的布局和设计,提高整车的乘坐舒适性和行驶稳定性。
在汽车行驶过程中,由于发动机的工作特性和路面条件等因素的影响,动力总成悬置系统容易产生振动和噪声。
因此,如何对这种振动进行分析并对其进行优化设计是本研究的重点。
三、汽车动力总成悬置系统振动分析1. 动力学模型建立为了更好地了解动力总成悬置系统的振动特性,需要建立其动力学模型。
该模型应包括发动机的振动特性、悬置支架的结构特性以及橡胶支座的动态特性等。
通过建立模型,可以模拟出汽车在不同路况下的振动情况,为后续的振动分析和优化设计提供依据。
2. 振动特性分析通过动力学模型的分析,可以得出动力总成悬置系统的振动特性。
主要包括系统的固有频率、振型和阻尼比等参数。
这些参数对于理解系统的振动特性和进行优化设计具有重要意义。
四、汽车动力总成悬置系统优化设计1. 设计目标与约束条件在进行优化设计时,需要明确设计目标。
一般来说,优化设计的目标包括提高乘坐舒适性、降低噪声和减少振动等。
同时,还需要考虑一些约束条件,如发动机的安装空间、悬置支架的结构强度等。
2. 优化方法与步骤针对上述设计目标和约束条件,可以采用多种优化方法进行设计。
如多目标优化算法、有限元分析等。
在优化过程中,需要逐步调整系统的参数,如橡胶支座的刚度、阻尼等,以达到最优的振动性能。
五、实例分析以某款汽车的动力总成悬置系统为例,通过建立其动力学模型,对其振动特性进行分析。
《汽车动力总成悬置系统振动分析及优化设计》范文

《汽车动力总成悬置系统振动分析及优化设计》篇一一、引言随着汽车工业的飞速发展,消费者对汽车性能的要求日益提高,其中,汽车的舒适性和稳定性成为了重要的考量因素。
汽车动力总成悬置系统作为连接发动机与车身的重要部分,其性能的优劣直接影响到整车的振动特性和乘坐舒适性。
因此,对汽车动力总成悬置系统的振动进行分析及优化设计显得尤为重要。
本文旨在探讨汽车动力总成悬置系统的振动特性,并提出相应的优化设计方案。
二、汽车动力总成悬置系统概述汽车动力总成悬置系统主要由发动机、离合器、变速器、传动轴等组成,通过一系列的悬置元件将动力总成与车身连接起来。
其作用主要是支撑和固定动力总成,同时通过减震元件减少发动机产生的振动对整车的传递,从而提高整车的舒适性和稳定性。
三、汽车动力总成悬置系统振动分析(一)振动来源汽车动力总成悬置系统的振动主要来源于发动机的工作过程、路面的不平度以及发动机和车身之间的共振等。
其中,发动机的振动是主要的振动源。
(二)振动传递路径发动机的振动通过悬置元件传递到车身,再传递到乘员。
其中,悬置元件的刚度和阻尼特性对振动的传递具有重要影响。
(三)振动分析方法通过对汽车动力总成悬置系统进行理论分析和仿真模拟,可以有效地分析其振动特性。
常用的分析方法包括有限元法、多体动力学法和实验分析法等。
四、汽车动力总成悬置系统优化设计(一)优化设计目标汽车动力总成悬置系统的优化设计旨在降低发动机的振动和噪声传递,提高整车的舒适性和稳定性。
(二)优化设计方案1. 改进悬置元件的设计:通过改变悬置元件的刚度和阻尼特性,优化其减震效果。
2. 优化发动机与车身的连接方式:采用更合理的连接方式,减少振动和噪声的传递。
3. 增加附加减震装置:在关键部位增加附加减震装置,进一步提高整车的减震效果。
4. 优化整车结构:通过优化整车结构,提高整车的刚度和稳定性,从而降低振动和噪声的传递。
五、实例分析以某款汽车为例,对其动力总成悬置系统进行振动分析及优化设计。
《2024年汽车动力总成悬置系统振动分析及优化设计》范文

《汽车动力总成悬置系统振动分析及优化设计》篇一一、引言随着汽车工业的快速发展,汽车动力总成悬置系统的性能对于整车舒适性和稳定性越来越重要。
动力总成悬置系统的主要功能是支撑和固定发动机、变速器等重要部件,同时通过减震和隔振技术来降低系统振动对整车的影响。
本文旨在分析汽车动力总成悬置系统的振动问题,并提出相应的优化设计方案。
二、汽车动力总成悬置系统概述汽车动力总成悬置系统主要由发动机悬置、变速器悬置等组成,其结构形式和性能直接影响整车的舒适性和稳定性。
在汽车行驶过程中,由于道路不平、发动机运转等因素,动力总成会产生振动和噪声,这些振动和噪声会通过悬置系统传递到车身,影响整车的舒适性和稳定性。
三、汽车动力总成悬置系统振动分析(一)振动来源及传递路径汽车动力总成的振动主要来源于发动机运转、道路不平等因素。
这些振动会通过发动机悬置、变速器悬置等传递到车身,进而影响整车的舒适性和稳定性。
(二)振动问题分析在汽车动力总成悬置系统中,由于设计、制造和装配等因素,可能会产生以下振动问题:1. 悬置系统刚度不足,导致系统在受到外力作用时产生过大变形;2. 悬置系统阻尼不足,导致振动衰减缓慢,影响整车的舒适性;3. 悬置系统与发动机、变速器等部件的连接不紧密,导致振动传递到车身。
四、优化设计方案(一)提高悬置系统刚度为了提高悬置系统的刚度,可以采用高强度材料制作悬置元件,同时优化悬置系统的结构形式,使其能够更好地承受外力作用。
此外,还可以通过增加悬置系统的支撑点数量来提高其整体刚度。
(二)增加悬置系统阻尼为了增加悬置系统的阻尼,可以在系统中加入液压减震器等装置。
这些装置能够有效地吸收和消耗振动能量,从而降低整车的振动和噪声。
(三)优化连接方式为了确保悬置系统与发动机、变速器等部件的连接紧密可靠,可以采用先进的连接方式和技术。
例如,可以采用高强度螺栓、焊接等方式来确保连接部位的牢固性和密封性。
此外,还可以在连接部位设置减震垫等装置,以降低振动传递到车身的幅度。
发动机悬置系统研究与优化设计

而 可 简 化 为 二 自 由 度 悬 架 振 动 系 统 。 垂 直 振 动 、俯 仰 振 动
与 俯 仰 振 动 引 起 的 车 辆 纵 向 水 平 振 动 都 是 和 车 辆 行 驶 平
顺 性 有 关 。
2.缸 体 受 力
车 辆 发 动 机 总 成 由 机 体 组 、活 塞 连 杆 组 和 曲轴 飞 轮 组
其 结 构 方 式 和 工 作 原 理 可 以 分 为 :控 制 节 流 孔 开 度 的 半 主 总 成 位 移 ,u为 控 制 力 ,对 悬 架 动 悬 置 、电流 变 液 体 半 主 动 悬 置 、磁 流 变 液 体 半 主 动 悬 置 的 能 量 输 入 。
等 几 种 。
由微 分变 换得 出悬置 系统
主 簧
上 液 室
解 耦膜 惯 性 通 道 下 液 室 底 膜
发 动 机 悬 置 数 学 模 型 ,汽 车 在 行 驶 过 程 中 ,发 动 机 正 常 激 励 下 ,对
简单 节流 孔 式
可 能 影 响 车 辆 NVH 性 能 的 因 素 进 行 研 究 和 优 化 。
一 、 发 动 机 悬 置 系 统 分 类 和 结 构 组 成 1.橡 胶 悬 置 最 初 ,动 力 总 成 不 是 经 弹 性 元 件 ,而 是 直 接 用 螺 栓 刚性
图 2 液压 悬置 主 要 结 构 形 式 1.路 面 激 励 汽 车 是 一 个 复 杂 的振 动 系 统 ,假 定 左 右 车 轮 受 到 的 路 面 激 励 对 称 于 纵 向 轴 线 且 相 等 ,此 种 情 况 下 ,汽 车 振 动 系 统 可 简 化 为 I/2车 辆 模 型 。 当 质 量 分 配 系 数 接 近 l时 ,进
上 。 其 中 主 要 包 括 有 气 体 作 用 力 、运 动 质 量 的 惯 性 力 、旋
(仅供参考)柴油轿车动力总成悬置系统优化设计

1. 动力总成悬置系统的设计原则及流程
动力总成悬置系统的主要作用为隔离动力总成振动向车身及车厢内部的传递,尤其是控制 发动机怠速工况下的低频抖动,并隔离发动机的高速运转时引起的车室内部的高频噪声;支承发 动机的重量,控制动力总成的相对运动和位移,克服和平衡因最大扭矩输出或紧急制动产生的 反作用力和惯性力;避免与整车其他部件发生干涉,保证动力总成工作安全可靠等。悬置系统完 整的设计方案如图 1 所示。动力总成悬置系统在设计上受到了许多约束条件的限制和制约,在 设计时应结合具体实际情况。综合考虑,既要满足自身的性能和功能要求,也要满足整车性能 对动力总成悬置系统设计提出的要求。
2. 动力总成悬置系统优化设计
2.1 项目介绍 先进柴油轿车开发项目,轿车使用广西玉林柴油机厂生产的 1.8L 型号为 YC4W110-40 的
直列四缸水冷四冲程柴油机,发动机与车架之间通过悬置支承连接。由于是由汽油机改为柴油 机,质量和转动惯量发生了改变,针对悬置而言,在不改变其安装位置和安装角度的情况下, 原始悬置系统导致该轿车振动过大,影响舒适性,同时易造成发动机与其它机械构件发生较大 运动干涉而失效,为改善乘坐舒适性,有必要对悬置系统进行重新匹配优化设计。 2.2 动力总成悬置系统的频率布置
3)振动传递率和支承处动反力最小 悬置系统应该尽量降低振动传递率的大小,这样才能彻底或最大限度地隔离发动机的振 动。在发动机的整个工作频率区内,都应将振动传递率保持在一个很低的水平。因为振动传递 率的大小反映了整个系统的隔振水平。考虑到作用在悬置的力与悬置元件的使用寿命有关,因 此,还应减少悬置处动反力的大小。 除此之外,在设计动力总成悬置系统时还得考虑发动机的运动空间、车架结构、最小离地 间隙等因素。 1.2 设计流程 一般的悬置设计包括以下过程:
发动机悬置系统优化设计及其可靠性分析
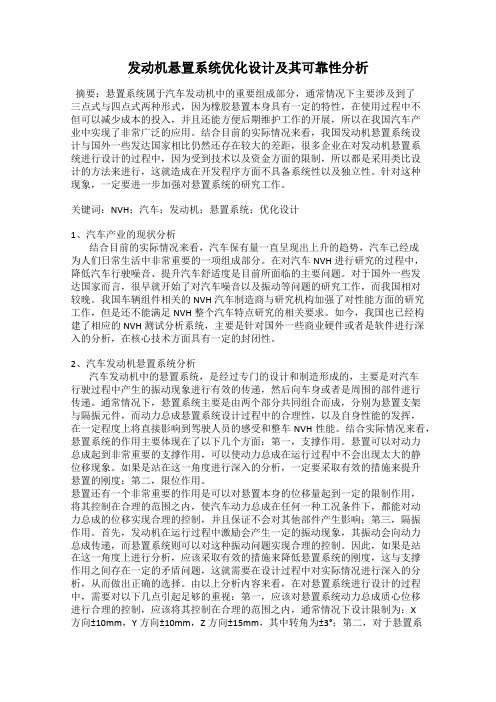
发动机悬置系统优化设计及其可靠性分析摘要:悬置系统属于汽车发动机中的重要组成部分,通常情况下主要涉及到了三点式与四点式两种形式,因为橡胶悬置本身具有一定的特性,在使用过程中不但可以减少成本的投入,并且还能方便后期维护工作的开展,所以在我国汽车产业中实现了非常广泛的应用。
结合目前的实际情况来看,我国发动机悬置系统设计与国外一些发达国家相比仍然还存在较大的差距,很多企业在对发动机悬置系统进行设计的过程中,因为受到技术以及资金方面的限制,所以都是采用类比设计的方法来进行,这就造成在开发程序方面不具备系统性以及独立性。
针对这种现象,一定要进一步加强对悬置系统的研究工作。
关键词:NVH;汽车;发动机;悬置系统;优化设计1、汽车产业的现状分析结合目前的实际情况来看,汽车保有量一直呈现出上升的趋势,汽车已经成为人们日常生活中非常重要的一项组成部分。
在对汽车NVH进行研究的过程中,降低汽车行驶噪音、提升汽车舒适度是目前所面临的主要问题。
对于国外一些发达国家而言,很早就开始了对汽车噪音以及振动等问题的研究工作,而我国相对较晚。
我国车辆组件相关的NVH汽车制造商与研究机构加强了对性能方面的研究工作,但是还不能满足NVH整个汽车特点研究的相关要求。
如今,我国也已经构建了相应的NVH测试分析系统,主要是针对国外一些商业硬件或者是软件进行深入的分析,在核心技术方面具有一定的封闭性。
2、汽车发动机悬置系统分析汽车发动机中的悬置系统,是经过专门的设计和制造形成的,主要是对汽车行驶过程中产生的振动现象进行有效的传递,然后向车身或者是周围的部件进行传递。
通常情况下,悬置系统主要是由两个部分共同组合而成,分别为悬置支架与隔振元件,而动力总成悬置系统设计过程中的合理性,以及自身性能的发挥,在一定程度上将直接影响到驾驶人员的感受和整车NVH性能。
结合实际情况来看,悬置系统的作用主要体现在了以下几个方面:第一,支撑作用。
悬置可以对动力总成起到非常重要的支撑作用,可以使动力总成在运行过程中不会出现太大的静位移现象。
- 1、下载文档前请自行甄别文档内容的完整性,平台不提供额外的编辑、内容补充、找答案等附加服务。
- 2、"仅部分预览"的文档,不可在线预览部分如存在完整性等问题,可反馈申请退款(可完整预览的文档不适用该条件!)。
- 3、如文档侵犯您的权益,请联系客服反馈,我们会尽快为您处理(人工客服工作时间:9:00-18:30)。
Equipment Manufacturing Technology No.11,2012汽车发动机动力总成悬置系统分析设计技术是以提高乘坐舒适性为目的的NVH(Noise,Vibration,Harshness)拟制技术的核心,由于NVH性能是衡量汽车品质的一个综合性重要指标,因此提高动力总成悬置系统隔振效果的问题越来越受到人们的重视和关注。
发动机悬置系统的基本功能[1]有:支承、限位以及隔振。
作为研究重点的隔振是利用悬置元件的缓冲与吸能作用,隔离衰减来自发动机动力总成激励力引起的车架振动和来自路面随机激励力引起的发动机动力总成的振动。
悬置系统的一个主要隔振设计方式是通过合理设计悬置元件的各向刚度、悬置点的位置与以及悬置元件的角度,使整个悬置系统具有较高的振动解耦程度,以达到最大限度的减振、隔振性能,改善汽车的乘坐舒适性和稳定性。
柴油机悬置系统的特色是:由于发动机质量较大,为区别于汽油机的三点正装悬置,一般采用刚度较大的四点斜装悬置。
传统的悬置系统分析设计理论虽然有了很大的发展,但未能很好的与工程实际需要相结合,且由于受到发动机安装位置等因素的限制,一般解耦度并不高。
目前国内外对悬置系统进行自动优化设计的文献[2,6],优化模型考虑因素不够全面,且采用遗传算法,导致计算量大,优化效果并不明显[4]。
本文在悬置系统动力学分析的基础上,建立了以提高悬置系统解耦度和各向谐振频率与其期望值接近程度为目标的悬置系统自动优化设计数学模型,采用以敏度为基础的优化算法,配合粗粒度离散寻优,通过自动迭代计算,可以快速准确地找到悬置系统的最优设计方案。
本文给出的某柴油机汽车算例充分表明本文优化算法可提高悬置系统解耦度和各向谐振频率与期望值接近程度,改善了悬置系统的减振、隔振效果。
1悬置系统模态分析1.1悬置系统模态分析为对悬置系统进行优化设计,先需对悬置系统进行模态分析,求出其固有频率和振型。
由于悬置元件刚度远小于发动机与车架刚度,通常只考虑发动机的6个刚体位移自由度,同时将各悬置元件简化为空间三向弹簧单元。
动力总成悬置系统的自由振动模态分析方程为:M 准咬+K 准=0(1)其中向量准=[x y z θX θY θZ ]T 由6个刚体位移自由度组成,刚度矩阵K 由各悬置元件的弹性主轴方向刚度、弹性主轴空间角度以及弹性中心的位置决定,质量阵MM =m 000000m 000000m 000000IXX -IXY -YXZ 000-IYX IYY -IYZ 000-IZX -IZY IZZ(2)柴油机汽车悬置系统优化设计王科富,卢汉奎,陈树勋(广西大学机械工程学院,广西南宁530004)摘要:柴油机汽车发动机悬置系统设计主要是通过合理设计悬置元件各向刚度、位置以及角度,以提高系统各向能量解耦度,并使各向自振频率落在期望值内。
建立了以提高悬置系统解耦度和各向谐振频率与期望值接近程度为目标的悬置系统优化设计数学模型,采用自创的基于敏度的优化算法,通过自动迭代计算,快速准确地找到悬置元件刚度、位置与角度的最优设计方案。
某柴油机汽车发动机悬置系统的优化设计算例结果表明本方法优化效果明显,改善了悬置系统的减振、隔振效果。
关键词:发动机悬置系统;解耦度;谐振频率,优化设计中图分类号:U464.2文献标识码:A文章编号:1672-545X(2012)11-0030-03收稿日期:2012-08-12基金项目:广西制造系统与先进制造技术重点实验室课题基金资助09-007-05S016。
作者简介:王科富(1987—),男,在读研究生,研究方向:车辆系统动力学。
设计与计算ZZZZ Z Z ZZ Z Z Z ZZ Z30《装备制造技术》2012年第11期式中:m为动力总成的质量;I xx、I yy、I zz为动力总成的惯性矩;I xy、I yz、I zx为动力总成的惯性积。
求解(1)式所示广义特征值问题,可得到悬置系统的6个模态(ωi、准i)(i=1 ̄6),ωi为系统谐振圆频率,准i为相应的振型向量。
由此可以解出悬置系统的固有频率和相应阵型。
1.2惯性矩和惯性积的测量对于惯性矩和惯性积,采用三线摆法进行测量。
三线摆测量表达式为[7]:I=T23i=1ΣW i r i24π2L(3)理论上,通过测定6组不同位置的转动惯量,就可以得出动力总成悬置系统的惯性矩和惯性积。
在实际测量时测量七组不同位置的转动惯量,其中六组用于求出悬置系统的惯性矩和惯性积,最后一组用于验证惯性矩和惯性积的合理性。
在试验过程中,每个姿态位置均尽可能摆放准确,以免引起角度误差,同时物体中心尽可能在圆盘中心位置,防止附加质量对测量引起误差。
2.3解耦度发动机悬置系统自由振动时,在第i阶模态中,第k方向振动的动能占全部动能的比例为[3]:T i k =6i=1Σ(准i)l(准i)k m kl6i=1Σ6k=1Σ(准i)l(准i)k m kl×100%(4)称为第i阶模态中第k方向振动的解耦度,其中,(准i)k为第i阶振型中的第k向位移;m kl为质量阵M的第k行第l列元素。
解耦度的高低是衡量悬置系统隔振设计优劣的主要指标之一,因为提高悬置系统各向能量解耦度,可减少悬置系统各向振动的相互耦合的影响,以便设计悬置系统各向谐振频率分别避开系统所受到的各向激振力的频率和车架结构的固有频率等,从而远离共振区,达到提高悬置系统的隔振效果的目的。
2悬置系统自动优化设计2.1悬置系统优化设计问题的数学模型本文提出的悬置系统解耦度与固有频率优化设计问题在满足给定的约束条件下,寻求一组设计变量,使得目标函数达到最优,其数学模型可表示为:Find X=K0R0X0ΣΣminf(x)=α6i=1Σαi(1-maxk=1,…,6{Tik})2+β6i=1Σβi(f i(X)-f i0)/f i0)2s.t.3燮γi(X)燮8(i=1,2,3,…)X L燮X燮X U燮燮燮燮燮燮燮燮燮燮燮燮燮燮燮燮燮燮燮燮燮(5)其中:设计变量X=[K0R0X0]T由各悬置元件的各向刚度K0、各弹性主轴空间角度R0、各弹性中心坐标X0组成。
最小化的目标函数f(X)由两部分构成:(1-6i=1Σa imax{T ik})2为解耦度的优化目标,该值越小,各向振动解耦度越接近于100%;而6i=1Σβi(f i(X)-f i0)/f i0)2为谐振频率优化目标,该目标值越小,悬置系统的各向振动的谐振频率f i(X)越接近于给定的期望频率fi0。
谐振频率优化目标可以有效控制悬置系统的各向振动的谐振频率,更有利于提高悬置系统的隔振效果,这是目前悬置系统自动优化模型文献所未考虑的。
在(5)式中α、αi、β、βi为加权系数;优化设计的约束条件3≤γi(X)≤8(i=1,2,3,...)为各橡胶悬置元件的剪压刚度比应在3 ̄8之间;约束X L≤X≤X U为各设计变量取值必须在其可允许取值范围内。
2.2优化算法由于悬置系统解耦度与固有频率优化设计问题的目标函数与约束函数有确定的数学表达,本文采用以敏度为基础的最速下降法,设计方案X的寻优迭代公式为:X(k+1)=X(k)-S(k)▽f(X(k))(6)式中迭代方向-▽f(X(k))为目标函数在当前设计点X(k)处差分敏度构成的负梯度,目标函数差分敏度是目标函数近似偏导数,其算式为:[f(X+△x n)-f(X+△x n)]/△x n(7)迭代步长S(K)由以下一维寻优确定:求S,最小化f(X(k+1))=f(X(k)-S▽F(X(k)))(8)采用如下算法求解上列一维无约束优化问题:先由(5)式设计变量的最大取值范围预定S最大搜索区间,在该区间内进行粗粒度离散寻优:均匀的取若干个(10 ̄20个)S值,求得使(7)式目标函数最小的S值,在以该值为中心,取比它大和比它小的两个相邻S值为S的精确搜索区间,在该区间内采用黄金分割法寻优即可得到(6)式迭代步长S(K)的精确值。
优化算法具体步骤为:(1)给定初始设计点X(0),收敛精度,令k=0;31Equipment Manufacturing Technology No.11,2012(2)对X (k )进行模态分析,计算解耦度和目标函数;(3)差分敏度分析求目标函数的负梯度-▽f (X (K ));(4)在S 最大搜索区间内进行粗粒度离散寻优;(5)确定S 精确搜索区间;(6)在S 精确搜索区间内用黄金分割法寻优得S (K );(7)由(6)式得到新的设计点X (K +1);(8)优化收敛判断,收敛停机,不收敛转;(9)令k =k +1,转(2)。
对于本悬置系统优化问题,大量计算实践表明局部极值点密度大于上述离散步长粒度,故可成功避免陷入局部极值点,从而保证快速有效地找到全局最优解。
采用本优化模型和优化算法对多个汽车发动机悬置系统进行了优化设计,在变量范围宽松的情况下,通过本文提供的优化方法可以使各向振动解耦度达到100%,并使自振频率严格等于期望值;在变量范围较小,优化结果变量取值临界的情况下,优化后各向振动解耦度虽然可能达不到100%,自振频率可能不严格等于期望值,但只要采用本文提供的优化方法就可得到本优化问题在满足设计变量取值范围等所有约束条件下的最优解。
3算例某柴油机汽车悬置系统优化设计。
动力总成质量:m=687kg惯性阵:(单位:kg.m2)I g =43.2022.2563-32.2202.2563152.223.5708-32.2203.7508135.60!""""""""#$%%%%%%%%&4本优化设计根据生产企业实际需要,对于悬置元件的位置和角度不需要改变,只需优化各向刚度和能量解耦度。
悬置元件的位置、角度见表1,各向刚度和各向能量分布百分比优化前后结果见表2和表3。
结果显示,利用本文算法优化,使得悬置系统的最高模态频率得到了显著降低,分布也更合理;同时悬置系统的各向刚度得到了很大改善,各向解耦度最大为99.9﹪,除了θz 的解耦度稍低外,其它模态阵型的解耦率接近90﹪及以上,优化效果比较明显,优化后悬置系统振动会有所改善。
4结束语(1)本文建立的以提高悬置系统解耦度和各向谐振频率与期望值接近程度为目标的悬置系统优化设计数学模型更加符合工程实际,通过自动优化迭代计算,可以快速准确地找到悬置元件位置、刚度与角度的最优设计方案,从而提高悬置系统的减振、隔振的性能,改善汽车的乘坐舒适性和稳定性。
(2)本文采用以敏度为基础最速下降法,采用粗粒度离散寻优与黄金分割法寻优相结合的算法确定步长因子,可快速有效地找到问题的全局最优解,所以基于敏度的求解算法比遗传算法更适用于悬置系统优化[4]。