球墨铸铁开花状石墨的防止
球墨铸铁石墨漂浮的产生及防止
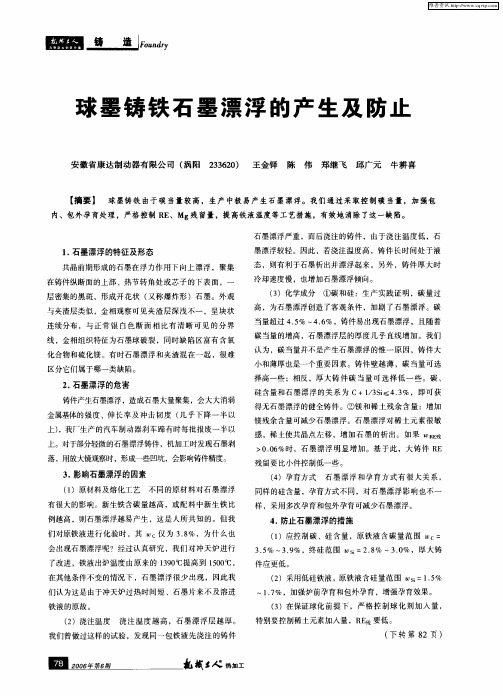
挥作用,授权与责任制相结合会产生权、责一致而责无
旁贷 的效果 ;奖励制 度 中以光 大先进 为 主,抓 点促 面 ,
非正式 奖励 要及时 、多变 ,起 到 赏罚分 明 的公正 作用 ;
其次是让企业 导向与员工 内在追求相结合 ,员 工的 内在 追求才是企业 发展 的最大 动力源。这种 内在追 求会产生
高 ,为石墨漂浮创造 了客观 条件 ,加剧 了石墨漂 浮。碳 当量超过 4 5 ~ .% ,铸件 易出现石 墨漂 浮,且 随着 .% 4 6 碳 当量 的增高 ,石墨漂浮层 的厚度几乎 直线增加 。我们 认 为,碳 当量并不是产生石墨漂浮 的惟 一原 因,铸件 大 小和薄厚也是一个重要 因素。铸件壁越 薄 ,碳 当量可 选 择高一些 ;相反 ,厚大铸 件 碳 当量可 选择 低一 些 。碳 、 硅含量和石 墨漂 浮的关系 为 c+13 i . %,即可 获 / S≤4 3
始终坚持以人为本的理念并将企业的优势连点成线以增强企业的吸引力和模仿难度从而引导企业用现代管理经济学服务营销和客户忠诚的理论去指导研发实践生产实践和营销实践把企业做强做大
维普资讯 http://Biblioteka
圜
球 墨 铸 铁 石 墨 漂 浮 的产 生 及 防 止
安徽省康 达制 动器有限公司 ( 阳 涡 2 3 2 ) 王金铎 3 6 0 陈 伟 郑继飞 邱广元 牛耕喜
4 防止石墨漂浮的措施 .
( )应控制碳 、硅 含量 ,原铁 液含碳 量范 围 Wc 1 : 3 5 ~ . %,终硅范 围 Ws_2 8 ~3 0 ,厚大铸 .% 3 9 _ .% .%
件应更低 。
( )采用低硅铁液 , 2 原铁液含 硅量范 围 Ws:15 i .%
~
球墨铸铁常见缺陷的分析与对策
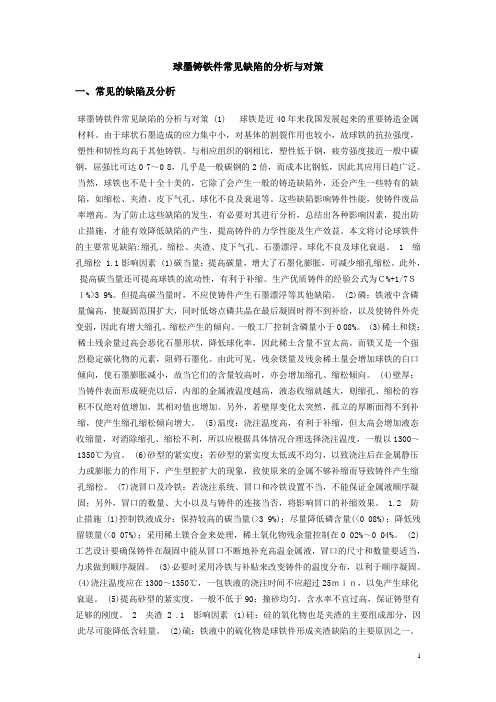
球墨铸铁件常见缺陷的分析与对策一、常见的缺陷及分析球墨铸铁件常见缺陷的分析与对策 (1) 球铁是近40年来我国发展起来的重要铸造金属材料。
由于球状石墨造成的应力集中小,对基体的割裂作用也较小,故球铁的抗拉强度,塑性和韧性均高于其他铸铁。
与相应组织的钢相比,塑性低于钢,疲劳强度接近一般中碳钢,屈强比可达0 7~0 8,几乎是一般碳钢的2倍,而成本比钢低,因此其应用日趋广泛。
当然,球铁也不是十全十美的,它除了会产生一般的铸造缺陷外,还会产生一些特有的缺陷,如缩松、夹渣、皮下气孔、球化不良及衰退等。
这些缺陷影响铸件性能,使铸件废品率增高。
为了防止这些缺陷的发生,有必要对其进行分析,总结出各种影响因素,提出防止措施,才能有效降低缺陷的产生,提高铸件的力学性能及生产效益。
本文将讨论球铁件的主要常见缺陷:缩孔、缩松、夹渣、皮下气孔、石墨漂浮、球化不良及球化衰退。
1 缩孔缩松 1.1影响因素 (1)碳当量:提高碳量,增大了石墨化膨胀,可减少缩孔缩松。
此外,提高碳当量还可提高球铁的流动性,有利于补缩。
生产优质铸件的经验公式为C%+1/7Si%>3 9%。
但提高碳当量时,不应使铸件产生石墨漂浮等其他缺陷。
(2)磷:铁液中含磷量偏高,使凝固范围扩大,同时低熔点磷共晶在最后凝固时得不到补给,以及使铸件外壳变弱,因此有增大缩孔、缩松产生的倾向。
一般工厂控制含磷量小于0 08%。
(3)稀土和镁:稀土残余量过高会恶化石墨形状,降低球化率,因此稀土含量不宜太高。
而镁又是一个强烈稳定碳化物的元素,阻碍石墨化。
由此可见,残余镁量及残余稀土量会增加球铁的白口倾向,使石墨膨胀减小,故当它们的含量较高时,亦会增加缩孔、缩松倾向。
(4)壁厚:当铸件表面形成硬壳以后,内部的金属液温度越高,液态收缩就越大,则缩孔、缩松的容积不仅绝对值增加,其相对值也增加。
另外,若壁厚变化太突然,孤立的厚断面得不到补缩,使产生缩孔缩松倾向增大。
球墨铸铁开花状石墨的防止

球墨铸铁开花状石墨的防止
魏传颖;钱进;王劲松
【期刊名称】《现代铸铁》
【年(卷),期】2010(030)003
【摘要】在铁路机车弹簧外套(QT450-10)的厚壁处易出现开花状石墨,认为是该铸件两耳孔处为热节部位,加之浇注系统不合理所致.为此采用垂直封闭式浇注系统、选用低RE球化剂,以及控制铁液出炉温度≥1 520℃,浇注温度在1 420~1 460℃等措施,改善了铸件内在质量,提高了外套铸件的成品率.
【总页数】3页(P79-81)
【作者】魏传颖;钱进;王劲松
【作者单位】安徽神剑科技股份有限公司,安徽,合肥,230022;安徽天元动力设备厂,安徽,合肥,230022;安徽神剑科技股份有限公司,安徽,合肥,230022
【正文语种】中文
【中图分类】TG250.6
【相关文献】
1.球墨铸铁石墨开花问题的分析与防止 [J], 熊英;周友松
2.球墨铸铁中碎块状石墨的形成原因及防止措施 [J], 程凤军;高顺;莫俊超;张俊新;杨志刚
3.球墨铸铁石墨开花问题的分析与防范 [J], 周友松;熊英
4.球墨铸铁中碎块状石墨的形成原因及防止措施 [J], 韩虎;王娟
5.球墨铸铁石墨开花问题的分析与处理 [J], 魏家鹏;潘宏歌
因版权原因,仅展示原文概要,查看原文内容请购买。
球墨铸铁生产中石墨漂浮缺陷分析及预防措施
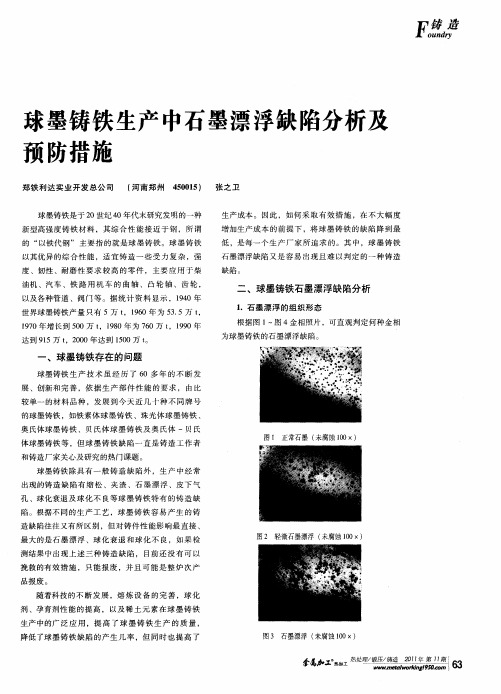
图 4 严重石墨漂浮 ( 未腐蚀 10x) 0
墨漂 浮 。
F 以上金 相 图片 可 以直 观 地 看 到 ,正 常 金 相 组 b 织 与石 墨漂 浮 组 织 的 区 别 ,图 2金 相 组 织 由于 只是 局部 存在 轻 微 的石 墨 漂 浮 ,通 过 进 行 力 学 性 能 试 验 可 知 ,其 对铸 件 的力 学 性 能 影 响 不大 ;图 3金 相 组
增加 生产 成 本 的前 提 下 ,将 球 墨 铸 铁 的 缺 陷 降 到 最
低 ,是 每一 个 生 产 厂 家 所 追 求 的。 其 中 ,球 墨 铸 铁
的 “ 以铁 代 钢 ” 主 要 指 的就 是 球 墨 铸 铁 。球 墨 铸 铁 以其优 异 的综 合 性 能 ,适 宜 铸 造 一 些 受 力 复 杂 ,强 度 、韧性 、耐磨 性 要 求 较 高 的零 件 ,主要 应 用 于 柴 油 机 、汽 车 、铁 路 用 机 车 的 曲轴 、凸 轮 轴 、齿 轮 ,
展 、创 新 和完 善 ,依 据 生产 部 件性 能 的 要 求 , 由 比
较 单 一的 材 料 品 种 ,发 展到 今 天 近 几 十 种 不 同 牌 号
的球 墨铸铁 ,如铁 索 体球 墨铸 铁 、珠 光体 球 墨铸 铁 、 奥 氏体 球墨 铸 铁 、贝 氏体 球 墨 铸 铁 及 奥 氏体 一贝 氏
石墨 漂浮 缺陷 又 是 容 易 出 现且 难 以判 定 的一 种 铸 造
缺 陷。
二 、球 墨铸 铁 石墨漂 浮缺 陷分 析
1 .石 墨 漂 浮 的 组 织 形 态
根 据 图 1一图 4金相 照片 ,可直 观判 定何 种 金相 为 球墨 铸铁 的石 墨漂 浮缺 陷。
浅析球墨铸铁件缺陷产生原因及防止措施
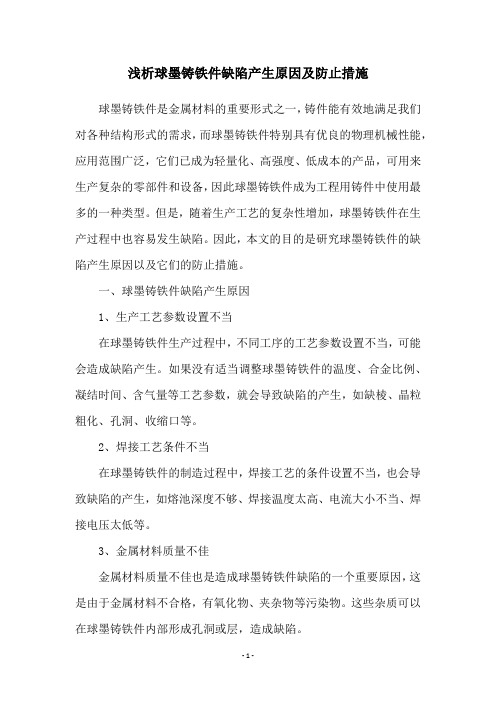
浅析球墨铸铁件缺陷产生原因及防止措施球墨铸铁件是金属材料的重要形式之一,铸件能有效地满足我们对各种结构形式的需求,而球墨铸铁件特别具有优良的物理机械性能,应用范围广泛,它们已成为轻量化、高强度、低成本的产品,可用来生产复杂的零部件和设备,因此球墨铸铁件成为工程用铸件中使用最多的一种类型。
但是,随着生产工艺的复杂性增加,球墨铸铁件在生产过程中也容易发生缺陷。
因此,本文的目的是研究球墨铸铁件的缺陷产生原因以及它们的防止措施。
一、球墨铸铁件缺陷产生原因1、生产工艺参数设置不当在球墨铸铁件生产过程中,不同工序的工艺参数设置不当,可能会造成缺陷产生。
如果没有适当调整球墨铸铁件的温度、合金比例、凝结时间、含气量等工艺参数,就会导致缺陷的产生,如缺棱、晶粒粗化、孔洞、收缩口等。
2、焊接工艺条件不当在球墨铸铁件的制造过程中,焊接工艺的条件设置不当,也会导致缺陷的产生,如熔池深度不够、焊接温度太高、电流大小不当、焊接电压太低等。
3、金属材料质量不佳金属材料质量不佳也是造成球墨铸铁件缺陷的一个重要原因,这是由于金属材料不合格,有氧化物、夹杂物等污染物。
这些杂质可以在球墨铸铁件内部形成孔洞或层,造成缺陷。
4、操作人员技术素养不足操作人员的技术素养也是产生缺陷的一个重要原因,如果操作人员缺乏技术素养,他们就不能熟练掌握工艺流程,也会导致生产过程中的缺陷。
二、防止球墨铸铁件缺陷的措施以上是球墨铸铁件缺陷的原因,那么如何防止缺陷产生呢?1、优化工艺参数设置在球墨铸铁件生产过程中,加强对工艺参数的监控,优化工艺参数设置,确保金属材料在加工上能满足一定的质量要求。
2、严格控制焊接工艺条件焊接是一项技术复杂的任务,因此我们应该在焊接工艺中严格控制各项工艺参数,确保球墨铸铁件能获得良好的焊接性能,从而防止缺陷的产生。
3、挑选优质金属材料在球墨铸铁件生产中,应该重视金属材料的质量,仅选用合格的金属材料,这样可以减少出现缺陷的概率。
4、提升操作人员技术素养提升操作人员的技术素养是防止球墨铸铁件缺陷的重要措施之一,建立科学的操作流程,以此来提高操作人员的技术水平,减少因技术不足而导致的缺陷。
10大技术要点分析防止球墨铸铁件缩孔、缩松方法
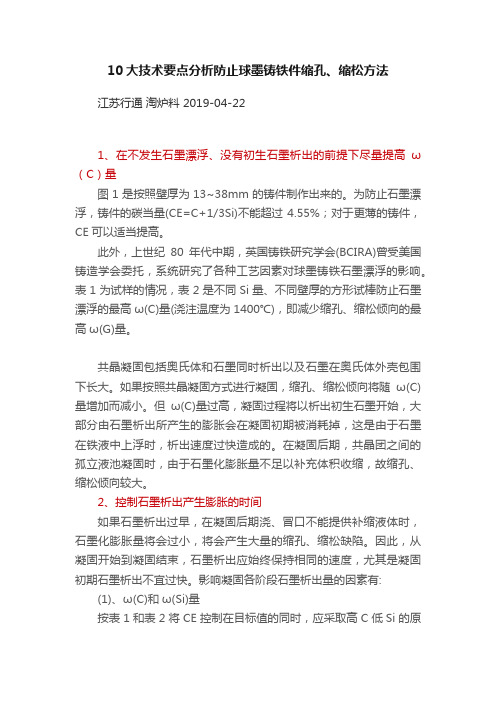
10大技术要点分析防止球墨铸铁件缩孔、缩松方法江苏行通淘炉料 2019-04-221、在不发生石墨漂浮、没有初生石墨析出的前提下尽量提高ω(C)量图1是按照壁厚为13~38mm的铸件制作出来的。
为防止石墨漂浮,铸件的碳当量(CE=C+1/3Si)不能超过4.55%;对于更薄的铸件,CE可以适当提高。
此外,上世纪80年代中期,英国铸铁研究学会(BCIRA)曾受美国铸造学会委托,系统研究了各种工艺因素对球墨铸铁石墨漂浮的影响。
表1为试样的情况,表2是不同Si量、不同壁厚的方形试棒防止石墨漂浮的最高ω(C)量(浇注温度为1400℃),即减少缩孔、缩松倾向的最高ω(G)量。
共晶凝固包括奥氏体和石墨同时析出以及石墨在奥氏体外壳包围下长大。
如果按照共晶凝固方式进行凝固,缩孔、缩松倾向将随ω(C)量增加而减小。
但ω(C)量过高,凝固过程将以析出初生石墨开始,大部分由石墨析出所产生的膨胀会在凝固初期被消耗掉,这是由于石墨在铁液中上浮时,析出速度过快造成的。
在凝固后期,共晶团之间的孤立液池凝固时,由于石墨化膨胀量不足以补充体积收缩,故缩孔、缩松倾向较大。
2、控制石墨析出产生膨胀的时间如果石墨析出过早,在凝固后期浇、冒口不能提供补缩液体时,石墨化膨胀量将会过小,将会产生大量的缩孔、缩松缺陷。
因此,从凝固开始到凝固结束,石墨析出应始终保持相同的速度,尤其是凝固初期石墨析出不宜过快。
影响凝固各阶段石墨析出量的因素有:(1)、ω(C)和ω(Si)量按表1和表2将CE控制在目标值的同时,应采取高C低Si的原则。
因为C是使石墨膨胀的元素,Si是影响凝固初期膨胀量的元素,ω(Si)量较高,使石墨球数增加,出现较多的铁素体,并且会使石墨析出较早,进而导致凝固初期膨胀量过大,凝固后期残余铁液凝固时膨胀量不足。
因此,ω(Si)量只要能够防止碳化物形成、强化铁素体达到力学性能要求即可,不宜过高。
(2)、孕育剂孕育剂的加入量过多或采用含Bi的孕育剂将导致石墨球数增多,耐石墨球的尺寸均匀,进而使缩孔、缩松倾向增大。
铸铁件常见铸造缺陷的防止方法

铸铁件经常会发生各种不同的铸造缺陷,如何防止这些缺陷发生,一直是铸件生产厂关注的问题。
本文介绍了笔者在这方面的一些认识和实践经验。
1 气孔特征:铸件中的气孔是指在铸件内部,表面或接近表面处存在的大小不等的光滑孔洞。
孔壁往往还带有氧化色泽,由于气体的来源和形成原因不同,气孔的表现形式也各不相同,有侵入性气孔,析出性气孔,皮下气孔等。
1.1 侵入性气孔这种气孔的数量较少,尺寸较大,多产生在铸件外表面某些部位,呈梨形或圆球形。
主要是由于铸型或砂芯产生的气体侵入金属液的未能逸出而造成。
防止措施:(1)减少发气量:控制型砂或芯砂中发气物质的含量,湿型砂的含水量不能过高,造型与修模时脱模剂和水用量不宜过多。
砂芯要保证烘干,烘干后的砂芯不宜存放太长时间,隔天使用的砂芯在使用前要回炉烘干,以防砂芯吸潮,不使用受潮、生锈的冷铁和芯撑等。
(2)改善型砂的透气性,选择合适的型空紧实度,合理安排出气眼位置以利排气,确保砂芯通气孔道畅通。
(3)适当提高浇注温度,开排气孔和排气冒口等,以利于侵入金属液的气体上浮排出。
1.2 析出性气孔这种气孔多而分散,一般位于铸件表面往往同批浇注的铸件大部分都发现有。
这种气孔主要是由于在熔炼过程中,金属液吸收的气体在凝固前未能全部析出,便在铸件中形成许多分散的小气孔。
防止措施:(1)采用洁净干燥的炉料,限制含气量较多的炉料使用。
(2)确保“三干”:即出铁槽、出铁口、过桥要彻底烘干。
(3)浇包要烘干,使用前最好用铁液烫过,包中有铁液,一定要在铁液表面放覆盖剂。
(4)各种添加剂(球化剂、孕育剂、覆盖剂)一不定期要保持干燥,湿度高的时候,要烘干后才能使用。
1.3 皮下气孔这种气孔主要出现在铸件的表层皮下2~3mm处,直径为1~3mm左右。
而且数量较多,铸件经热处理或粗加工去除外皮后,就会清晰地显露出来。
防止措施;(1)适当提高浇注温度,严格控制各种添加剂的加入量,尽可能缩短浇注时间。
(2)孕育剂的加入量最好控制在(质量分数)0.4%~0.6%,同时要严格控制孕育剂中A1的质量分数,w(Al)偏高容易和型腔表面的水分发生反应:2Al+3H2O=Al2O3+3H2↑,一般情况下孕育剂含Al量不宜超过1.5%。
球墨铸铁缺陷的金相分析及防止措施

302020年第5期工艺试验与应用球墨铸铁缺陷的金相分析及防止措施球墨铸铁是近几十年才发展起来的高强度铸造金属材料。
与钢材相比,球墨铸铁还有很多优点。
比如铸造性能好,成本相对较低。
由于球墨铸铁产量的不断增加,性能不断开发, 现已成功地部分取代了锻钢和铸钢,成为前景广阔的金属结构材料。
力学性能与金属的金相组织密切相关,什么样的金相结构决定了什么样的力学性能。
球墨铸铁也不例外,因此,对球墨铸铁的金相研究,是我们了解球墨铸铁的先决条件[1]。
下面对我厂生产的材质为QT450-10A 铸件,在生产过程中出现的两种不同缺陷进行分析[2]。
1 显微缩松1.1 微观结构球墨铸铁的显微缩松在显微下观察类似呈片状、多角形,有时连续、有时断续,分布在共晶团边界,有时类似片状石墨(图1),往往我们会误认为该缺陷是由球化不良造成。
这样极大的影响判断问题的改进方向,同时有可能使问题更加突出[3]。
我们对同样试块的缺陷位置进行能谱分析,能谱图像显示该缺陷区域呈乳突状立体结构(图2)。
1.2 形成原因铸件凝固过程中,奥氏体支晶凝固后,残余的铁液则在支晶间最后凝固,因得不到补缩而形成显微缩松,这类显微缩松的形成原因有如下几种原因:(1)碳当量CE 值过低,使得石墨膨胀体积不足以补充凝固过程中的体积收缩;(2)合金成分如Cu、Mn、Cr、P 及残留Mg 过高,增大缩松倾向[4];(3)砂型强度偏低,在铸件凝固过程中铸件体积增大,在体积增大的部位得不到其他部位铁液的补充;(4)工艺设计不合理,热节处在凝固过程中周围没有足够的铁水补充收缩[5];(5)孕育不充分或孕育过量等。
毛洪宇,勾洋洋,张 森(沈阳远大压缩机有限公司,辽宁 沈阳 110020)摘要:摘要:通过显微镜和能谱分析,观察球铁渣气孔和显微缩松的微观特征,找出种差别并分析了形成缺陷的原因;提出的防止缺陷产生的措施,能有效地控制和减少废品的产生,提高了铸件合格率。
关键词:关键词:渣气孔;缩松;预防措施中图分类号:中图分类号:TG245 文献标识码:文献标识码:B 文章编号:文章编号:1673-3320(2020)05-0030-03收稿日期:2020-04-16定稿日期:2020-08-10作者简介:毛洪宇(1986-),男,毕业于辽宁工业大学材料成型及控制工程专业,工程师,主要从事铸造工艺及材料、模具设计制造。
球墨铸铁金相组织缺陷原因及防止方法概述
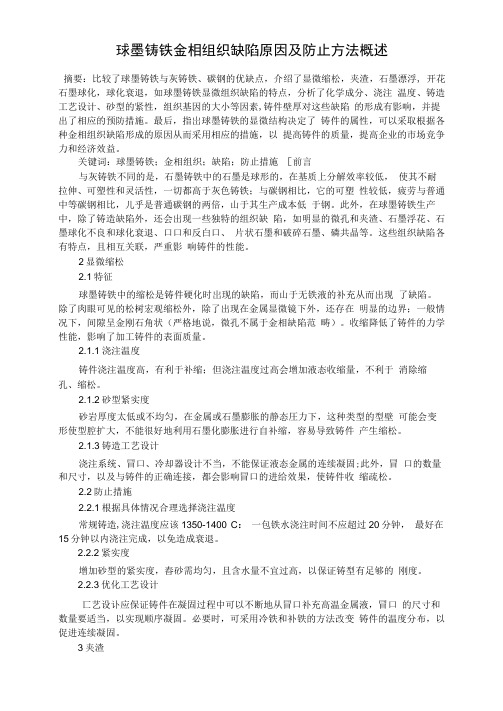
球墨铸铁金相组织缺陷原因及防止方法概述摘要:比较了球墨铸铁与灰铸铁、碳钢的优缺点,介绍了显微缩松,夹渣,石墨漂浮, 开花石墨球化,球化衰退,如球墨铸铁显微组织缺陷的特点,分析了化学成分、浇注温度、铸造工艺设计、砂型的紧性,组织基因的大小等因素,铸件壁厚对这些缺陷的形成有影响,并提出了相应的预防措施。
最后,指岀球墨铸铁的显微结构决定了铸件的属性,可以采取根据各种金相组织缺陷形成的原因从而采用相应的措施,以提高铸件的质量,提高企业的市场竞争力和经济效益。
关键词:球墨铸铁;金相组织;缺陷;防止措施[前言与灰铸铁不同的是,石墨铸铁中的石墨是球形的,在基质上分解效率较低,使其不耐拉伸、可塑性和灵活性,一切都高于灰色铸铁;与碳钢相比,它的可塑性较低,疲劳与普通中等碳钢相比,儿乎是普通碳钢的两倍,山于其生产成本低于钢。
此外,在球墨铸铁生产中,除了铸造缺陷外,还会出现一些独特的组织缺陷,如明显的微孔和夹渣、石墨浮花、石墨球化不良和球化衰退、口口和反白口、片状石墨和破碎石墨、磷共晶等。
这些组织缺陷各有特点,且相互关联,严重影响铸件的性能。
2显微缩松2.1特征球墨铸铁中的缩松是铸件硬化时岀现的缺陷,而山于无铁液的补充从而出现了缺陷。
除了肉眼可见的松树宏观缩松外,除了出现在金属显微镜下外,还存在明显的边界;一般情况下,间隙呈金刚石角状(严格地说,微孔不属于金相缺陷范畴)。
收缩降低了铸件的力学性能,影响了加工铸件的表面质量。
2.1.1浇注温度铸件浇注温度高,有利于补缩;但浇注温度过高会增加液态收缩量,不利于消除缩孔、缩松。
2.1.2砂型紧实度砂岩厚度太低或不均匀,在金属或石墨膨胀的静态圧力下,这种类型的型壁可能会变形使型腔扩大,不能很好地利用石墨化膨胀进行自补缩,容易导致铸件产生缩松。
2.1.3铸造工艺设计浇注系统、冒口、冷却器设计不当,不能保证液态金属的连续凝固;此外,冒口的数量和尺寸,以及与铸件的正确连接,都会影响冒口的进给效果,使铸件收缩疏松。
生产厚大断面球磨铸铁的关键控制点
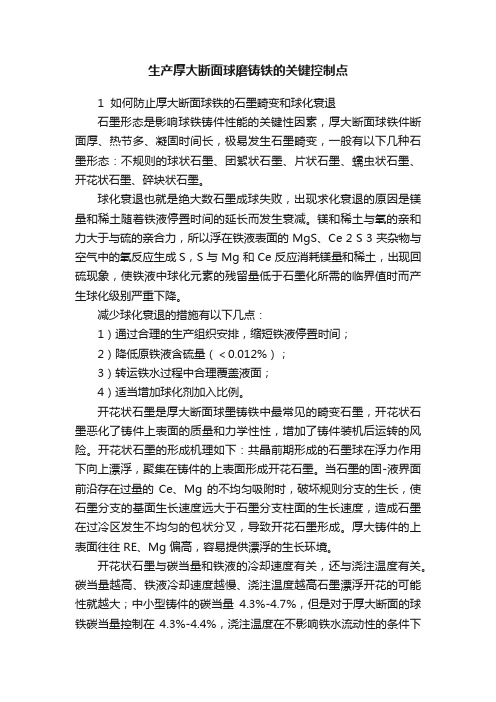
生产厚大断面球磨铸铁的关键控制点1 如何防止厚大断面球铁的石墨畸变和球化衰退石墨形态是影响球铁铸件性能的关键性因素,厚大断面球铁件断面厚、热节多、凝固时间长,极易发生石墨畸变,一般有以下几种石墨形态:不规则的球状石墨、团絮状石墨、片状石墨、蠕虫状石墨、开花状石墨、碎块状石墨。
球化衰退也就是绝大数石墨成球失败,出现求化衰退的原因是镁量和稀土随着铁液停置时间的延长而发生衰减。
镁和稀土与氧的亲和力大于与硫的亲合力,所以浮在铁液表面的 MgS、Ce 2 S 3 夹杂物与空气中的氧反应生成S,S 与 Mg 和 Ce 反应消耗镁量和稀土,出现回硫现象,使铁液中球化元素的残留量低于石墨化所需的临界值时而产生球化级别严重下降。
减少球化衰退的措施有以下几点:1)通过合理的生产组织安排,缩短铁液停置时间;2)降低原铁液含硫量(<0.012%);3)转运铁水过程中合理覆盖液面;4)适当增加球化剂加入比例。
开花状石墨是厚大断面球墨铸铁中最常见的畸变石墨,开花状石墨恶化了铸件上表面的质量和力学性性,增加了铸件装机后运转的风险。
开花状石墨的形成机理如下:共晶前期形成的石墨球在浮力作用下向上漂浮,聚集在铸件的上表面形成开花石墨。
当石墨的固-液界面前沿存在过量的Ce、Mg 的不均匀吸附时,破坏规则分支的生长,使石墨分支的基面生长速度远大于石墨分支柱面的生长速度,造成石墨在过冷区发生不均匀的包状分叉,导致开花石墨形成。
厚大铸件的上表面往往 RE、Mg 偏高,容易提供漂浮的生长环境。
开花状石墨与碳当量和铁液的冷却速度有关,还与浇注温度有关。
碳当量越高、铁液冷却速度越慢、浇注温度越高石墨漂浮开花的可能性就越大;中小型铸件的碳当量4.3%-4.7%,但是对于厚大断面的球铁碳当量控制在4.3%-4.4%,浇注温度在不影响铁水流动性的条件下尽可能低,一般在1300℃-1360℃为宜;控制碳硅与残余稀土的含量以及提高冷却速度可以减少漂浮石墨形成。
球墨铸铁中球状石墨相互粘连原因及预防措施何晓晨秦红李国乾黄学慧

球墨铸铁中球状石墨相互粘连原因及预防措施何晓晨秦红李国乾黄学慧发布时间:2023-07-04T10:04:15.303Z 来源:《中国科技信息》2023年8期作者:何晓晨秦红李国乾黄学慧[导读] 近年来球墨铸铁因其较为优良的性能受到越来越多的应用,而球墨铸铁中石墨的形态对性能有重要的影响。
为了保证球墨铸铁的优良性能,不仅要求石墨的球化率高,并且要求球状石墨分布均匀。
球墨铸铁中偶有出现球状石墨相互粘连的情况,该情况将会严重降低球墨铸铁构件的力学性能。
为避免该情况的出现,本文从原理及制造过程中分析出现该情况的原因,并提出相应的预防措施。
中车大连机车车辆有限公司辽宁大连 116041摘要:近年来球墨铸铁因其较为优良的性能受到越来越多的应用,而球墨铸铁中石墨的形态对性能有重要的影响。
为了保证球墨铸铁的优良性能,不仅要求石墨的球化率高,并且要求球状石墨分布均匀。
球墨铸铁中偶有出现球状石墨相互粘连的情况,该情况将会严重降低球墨铸铁构件的力学性能。
为避免该情况的出现,本文从原理及制造过程中分析出现该情况的原因,并提出相应的预防措施。
关键词:球墨铸铁;球状石墨;石墨粘连中图分类号:文献标识码:B前言球墨铸铁是20世纪50年代发展起来的一种材料,除具有铸铁本身拥有的优良的切削加工性能、铸造工艺性、消振性及耐磨性外,因其中石墨是以球状形态存在于基体组织中,对金属基体割裂作用相对最小,故球墨铸铁的强度和塑性较其他铸铁有了很大的提高[1]。
基于其优异的综合性能,目前球墨铸铁应用广泛。
轨道交通车辆中的曲轴、抱轴箱、机体等构件大多是球墨铸铁材质的。
但球墨铸铁在制造过程中会出现各种类型的缺陷,常见的有缩孔、缩松、皮下气孔等。
本人在工作中检测球墨铸铁试样时发现球墨铸铁中偶有出现球状石墨相互粘连的情况,该情况会导致石墨对金属基体的割裂加重,严重降低球墨铸铁构件的力学性能。
本文针对上述情况产生的原因加以分析,并提出相应的工艺优化提升措施。
【热坛交流】球墨铸铁的石墨漂浮及其防止
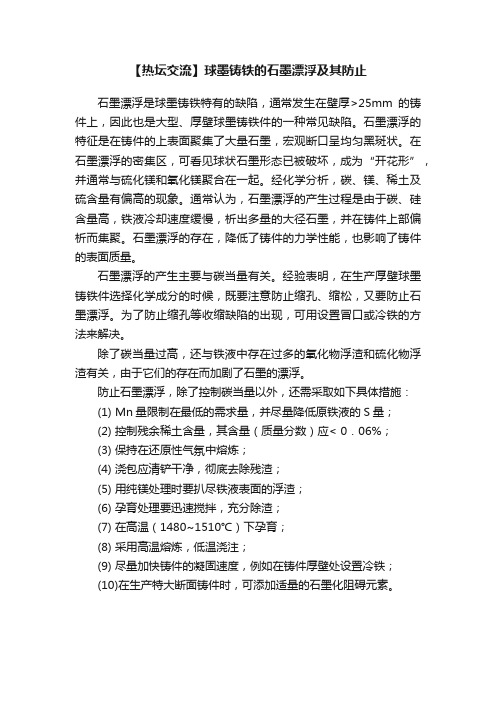
【热坛交流】球墨铸铁的石墨漂浮及其防止
石墨漂浮是球墨铸铁特有的缺陷,通常发生在壁厚>25mm的铸件上,因此也是大型、厚壁球墨铸铁件的一种常见缺陷。
石墨漂浮的特征是在铸件的上表面聚集了大量石墨,宏观断口呈均匀黑斑状。
在石墨漂浮的密集区,可看见球状石墨形态已被破坏,成为“开花形”,并通常与硫化镁和氧化镁聚合在一起。
经化学分析,碳、镁、稀土及硫含量有偏高的现象。
通常认为,石墨漂浮的产生过程是由于碳、硅含量高,铁液冷却速度缓慢,析出多量的大径石墨,并在铸件上部偏析而集聚。
石墨漂浮的存在,降低了铸件的力学性能,也影响了铸件的表面质量。
石墨漂浮的产生主要与碳当量有关。
经验表明,在生产厚壁球墨铸铁件选择化学成分的时候,既要注意防止缩孔、缩松,又要防止石墨漂浮。
为了防止缩孔等收缩缺陷的出现,可用设置冒口或冷铁的方法来解决。
除了碳当量过高,还与铁液中存在过多的氧化物浮渣和硫化物浮渣有关,由于它们的存在而加剧了石墨的漂浮。
防止石墨漂浮,除了控制碳当量以外,还需采取如下具体措施:
(1) Mn量限制在最低的需求量,并尽量降低原铁液的S量;
(2) 控制残余稀土含量,其含量(质量分数)应< 0.06%;
(3) 保持在还原性气氛中熔炼;
(4) 浇包应清铲干净,彻底去除残渣;
(5) 用纯镁处理时要扒尽铁液表面的浮渣;
(6) 孕育处理要迅速搅拌,充分除渣;
(7) 在高温(1480~1510℃)下孕育;
(8) 采用高温熔炼,低温浇注;
(9) 尽量加快铸件的凝固速度,例如在铸件厚壁处设置冷铁;
(10)在生产特大断面铸件时,可添加适量的石墨化阻碍元素。
球墨铸铁石墨开花问题的分析与防止
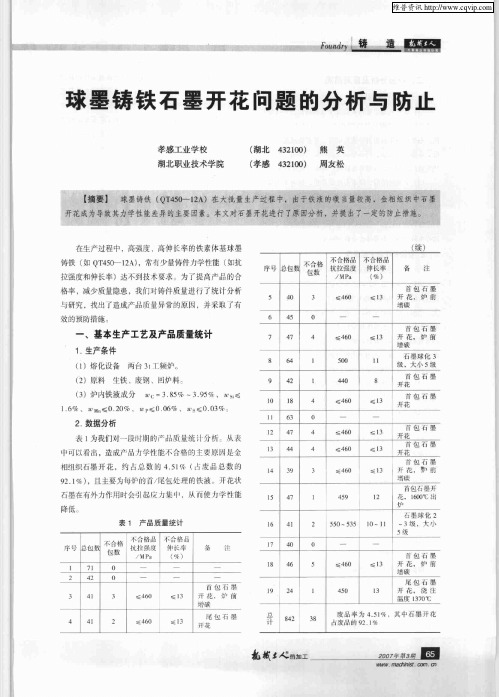
】 4 < 0 8  ̄ 1 4 6 0
1 I 6 3 0Leabharlann 3 开 墨 嘉 开 墨 兽
≤ I 3 首 包 石 墨 开花 酋 包 石 墨
≤I 3 坪花. 前
2 数据分析 .
表I 为我们对一段时期 的产 品质 量统计分析 从表
1 7 4 ≤ 2 4 4 6 0
占废 品的 9 1 2 谨
废 品率 为 45 % . 中 石墨 开 花 .l 其
杠槭 ,拇I l二加 ‘
盟 I 卿 塑 冒
n w f ∞m ∞
维普资讯
二、原因分析及应对措施
1 开花状石墨的形成 .
()球状 石墨主要是从铁液 中直接析 出,并按 螺形 1 位错生长 。石 墨 刚从 铁 液 中析 出 时 ,由于铁 液 温度 较 高 ,石墨可能生长也有可能被熔 解。随着铁液 温度 的降 低 ,石墨生长加快 ,当石墨 长大到一定尺 寸后 ,在铁液 热混流的作用 下 , 石墨容易破裂 ,形成开花状石墨。 ()共 晶转变 时,随着温度 的降低 ,铁液 中的碳通 2 过奥氏体边界 析出到被奥氏体包 围的石墨球上 的速度加 快 ,这样 石墨球 的体积增大而奥 氏体的边界被 束缚 ,使
际生产过程 中采取增碳处理后应将炉 内铁 液温度提 高到
16 —18℃,并过热 1 1rn 50 50 0 5 i,使未熔的大石墨充 a
分熔解为均匀的小颗粒 石墨 ,以保证球化 良好 ;另一方 面,配料时铁液中的碳最 好一 次性 配到工艺要 求的范 围 内,这就要求配料人员必须准确估算炉 内剩余 铁液量 和 使用 的回炉料的化学成分 ,这会使生产节 奏好 ,并 降低
增碳
石墨在有外力作用时会 引起应 集L ,从而使 力学 性能 I _ J 降低
球铁开花状石墨成因分析
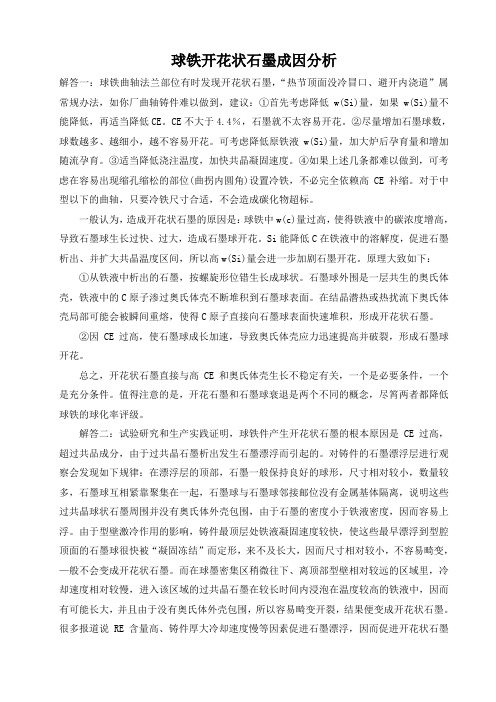
球铁开花状石墨成因分析解答一:球铁曲轴法兰部位有时发现开花状石墨,“热节顶面没冷冒口、避开内浇道”属常规办法,如你厂曲轴铸件难以做到,建议:①首先考虑降低w(Si)量,如果w(Si)量不能降低,再适当降低CE。
CE不大于4.4%,石墨就不太容易开花。
②尽量增加石墨球数,球数越多、越细小,越不容易开花。
可考虑降低原铁液w(Si)量,加大炉后孕育量和增加随流孕育。
③适当降低浇注温度,加快共晶凝固速度。
④如果上述几条都难以做到,可考虑在容易出现缩孔缩松的部位(曲拐内圆角)设置冷铁,不必完全依赖高CE补缩。
对于中型以下的曲轴,只要冷铁尺寸合适,不会造成碳化物超标。
一般认为,造成开花状石墨的原因是:球铁中w(c)量过高,使得铁液中的碳浓度增高,导致石墨球生长过快、过大,造成石墨球开花。
Si能降低C在铁液中的溶解度,促进石墨析出、并扩大共晶温度区间,所以高w(Si)量会进一步加剧石墨开花。
原理大致如下:①从铁液中析出的石墨,按螺旋形位错生长成球状。
石墨球外围是一层共生的奥氏体壳,铁液中的C原子渗过奥氏体壳不断堆积到石墨球表面。
在结晶潜热或热扰流下奥氏体壳局部可能会被瞬间重熔,使得C原子直接向石墨球表面快速堆积,形成开花状石墨。
②因CE过高,使石墨球成长加速,导致奥氏体壳应力迅速提高并破裂,形成石墨球开花。
总之,开花状石墨直接与高CE和奥氏体壳生长不稳定有关,一个是必要条件,一个是充分条件。
值得注意的是,开花石墨和石墨球衰退是两个不同的概念,尽筲两者都降低球铁的球化率评级。
解答二:试验研究和生产实践证明,球铁件产生开花状石墨的根本原因是CE过高,超过共品成分,由于过共晶石墨析出发生石墨漂浮而引起的。
对铸件的石墨漂浮层进行观察会发现如下规律:在漂浮层的顶部,石墨一般保持良好的球形,尺寸相对较小,数量较多,石墨球互相紧靠聚集在一起,石墨球与石墨球邻接邮位没有金属基体隔离,说明这些过共晶球状石墨周围并没有奥氏体外壳包围,由于石墨的密度小于铁液密度,因而容易上浮。
球墨铸铁件缺陷产生的原因与预防措施

球墨铸铁件缺陷产生的原因与预防措施球墨铸铁件缺陷产生的原因与预防措施球墨铸铁是20世纪五十年代发展起来的一种高强度铸铁材料,其综合性能接近于钢,正是基于其优异的性能,已成功地用于铸造一些受力复杂,强度、韧性、耐磨性要求较高的零件。
球墨铸铁已迅速发展为仅次于灰铸铁的、应用十分广泛的铸铁材料。
所谓“以铁代钢”,主要指球墨铸铁。
下面跟着店铺来看看球墨铸铁件缺陷产生的原因与预防措施吧!希望对你有所帮助。
球墨铸铁件缺陷产生的原因与预防措施11、球墨铸铁管件产生夹渣缺陷的原因有:(1)硅:硅的氧化物也是夹渣的主要组成部门,因此尽可能降低含硅量。
(2)硫:铁液中的硫化物是球铁件形成夹渣缺陷的主要原因之一。
硫化物的熔点比铁液熔点低,在铁液凝固过程中,硫化物将从铁液中析出,增大了铁液的粘度,使铁液中的熔渣或金属氧化物等不易上浮。
因而铁液中硫含量太高时,铸件易产生夹渣。
球墨铸铁原铁液含硫量应控制在006%以下,当它在009%~0135%时,铸铁夹渣缺陷会急剧增加。
(3)稀土和镁:近年来研究认为夹渣主要是因为镁、稀土等元素氧化而致,因此残余镁和稀土不应太高。
(4)浇注系统:浇注系统设计应合理,具有挡渣功能,使金属液能平稳地充填铸型,力求避免飞溅及紊流。
(5)浇注温度:浇注温度太低时,金属液内的金属氧化物等因金属液的粘度太高,不易上浮至表面而残留在金属液内;温度太高时,金属液表面的熔渣变得太稀薄,不易自液体表面往除,往往随金属液流进型内。
而实际出产中,浇注温度太低是引起夹渣的主要原因之一。
此外,浇注温度的选取还应考虑碳、硅含量的关系。
(6)型砂:若型砂表面粘附有多余的砂子或涂料,它们可与金属液中的氧化物合成熔渣,导致夹渣产生;砂型的紧实度不平均,紧实度低的型壁表面等闲被金属液侵蚀和形成低熔点的化合物,导致铸件产生夹渣。
2、防止措施:(1)控制铁液成分:尽量降低铁液中的含硫量(<006%),适量加进稀土合金(01%~02%)以净化铁液,尽可能降低含硅量和残镁量。
球墨铸铁的常见缺陷及防止方法

文章编号:1007-967X(2009)05-0031-02球墨铸铁的常见缺陷及防止方法3田承飞(中冶葫芦岛有色金属集团有限公司,辽宁葫芦岛125003)摘 要:本文通过对球墨铸铁的常见缺陷原因进行了分析,找出了解决问题的方法。
由于铸造工序复杂,每一点疏漏都会给铸件带来不良影响,如型砂水分、浇铸温度、浇铸系统等。
因此,每一工序都必须认真操作,才能获得健全铸件。
关键词:球墨铸铁;缺陷;气孔中图分类号:TG143.5 文献标识码:A0 前 言球墨铸铁因其具有良好的减震性能、韧性及成本低廉等优点而越来越受到人们的重视,应用范围越来越广。
但一些铸造缺陷始终困扰着我们,在一定程度上制约了球墨铸铁的生产和应用。
葫芦岛有色金属集团有限公司技术人员经过多年的实践,积累了丰富的经验,使一些铸造缺陷得到了较好的解决。
1 球墨铸铁常见铸造缺陷1.1 气 孔气孔是球墨铸铁最常见的缺陷之一,气孔种类主要有三种。
1.1.1 侵入性气孔外界气体侵入金属液中形成气孔。
气孔一般在铸铁表面,靠近铸型或砂型表面,多呈集中孔洞,呈梨形、椭圆形、扁平圆形。
1.1.2 析出性气孔金属液在冷却和凝固过程中,因气体溶解度下降,析出气体来不及排除,铸件因此而产生的气孔。
这种气孔多发生在铸件最后凝固部位,冒口附近、热节中心部位最为密集,多呈分散的小圆孔。
形状呈团球形、断裂状多角形、断续裂纹状及混合型。
1.1.3 反应性气孔金属液与铸型之间或金属液内部发生化学反应。
一类是金属、铸型间的反应;另一类是金属液内部化学成分之间或化学成分与非金属夹杂物发生化学反应,产生蜂窝状气孔,呈梨状或团球形均匀分布。
这种气孔一般位于铸件表皮下,常为针状或蝌蚪状,称为针孔或皮下气孔。
1.2 夹 杂金属液中物质之间或金属液中物质与铸型物质之间发生的化学反应而生成的固态物质。
铸件中通常存在包含有渣、砂、涂料、氧化物、硫化物等非金属杂物。
夹杂物过分集中便形成渣孔或砂眼,导致铸件报废。
球墨铸铁中碎块状石墨的形成原因及防止措施

245管理及其他M anagement and other球墨铸铁中碎块状石墨的形成原因及防止措施韩 虎,王 娟(江苏力源金河铸造有限公司,江苏 如皋 226500)摘 要:在球墨铸铁之中,碎块状石墨是一种较为常见的缺陷组织,碎块状石墨会对球墨铸铁件造成十分不利的影响,一方面表现为球墨铸铁件力学性能的降低,另一方面也会导致加工面呈现出灰斑特征。
除此之外,碎块状石墨的存在还会促使球墨铸铁的抗拉强度、冲击韧度等方便的参数出现一定程度的降低。
因此了解碎块状石墨形成的原因,并采取针对性措施进行有效防止与解决成为业内人士十分关注的问题。
本文就针对球墨铸铁中碎块状石墨的形成原因及防止措施进行研究与分析。
关键词:球墨铸铁;碎块状石墨;原因;措施中图分类号:TG255 文献标识码:A 文章编号:11-5004(2019)07-0245-2收稿日期:2019-07作者简介:韩虎,男,生于1982年,汉族,江苏宿迁人,本科,研究方向:液压泵、阀、马达、壳体、工业阀、阀门铸造及加工。
1 碎块状石墨的形成原因相比于正常球状石墨,碎块状石墨的差异性主要表现在两个方面,一方面是形态上的差异性,正常石墨以球状形式呈现,而碎块状石墨则为不规则碎块;另一方面是分布特点的差异性,一般情况下正常石墨分布在奥氏体基体之上,而碎块状石墨则是沿奥氏体枝晶分布。
从碎块状石墨与正常球状石墨的差异性表现可以看出,两者的形成机理也有所不同。
国外有学生认为二次石墨会产生的一定的膨胀压力,在这一压力作用之下初生是石墨球会出现发生破裂的情况,进而形成碎块状石墨,但是这一理论无法对碎块状石墨沿奥氏体枝晶分布进行合理的解释,这一理论的准确性有待商榷;国内学者周继扬等人认为碎块状石墨形成的原因主要是石墨与奥氏体之间的松散耦合所形成的,但是他们没有对为何会形成松散耦合做出合理的解释与说明。
结合多年的时间经验,并查阅了相关资料,本人认为无论是球状石墨还是碎块状石墨,它们都是从液态中直接析出而成,但具体形成的原因与生长条件存在着一定程度的差异[1-3]。
- 1、下载文档前请自行甄别文档内容的完整性,平台不提供额外的编辑、内容补充、找答案等附加服务。
- 2、"仅部分预览"的文档,不可在线预览部分如存在完整性等问题,可反馈申请退款(可完整预览的文档不适用该条件!)。
- 3、如文档侵犯您的权益,请联系客服反馈,我们会尽快为您处理(人工客服工作时间:9:00-18:30)。
魏传 颖 1 , 钱
(. 1 安徽神剑科技股份有限公司 , 安徽 合肥
进 2王 劲松 1 ,
合肥 20 2 ) 3 0 2
2 0 2 ;. 30 2 2安徽天元动力设备厂 , 安徽
摘要 : 在铁路机车弹簧Cf ( T 5 — 0 的厚壁处易 出现开花状石墨 , b  ̄Q 4 0 1 ) A 认为是该铸件两耳孔处为热 节部位 , 加之浇注系统 不合理所致。为此采用垂直封闭式浇注 系统 、 选用低 R E球化剂 , 以及控制铁液 出炉温度 ≥15 0o 浇注温度在 1 2 ~ 2 C, 0 4
4 0℃ . h tr a u l yo e c si g a r v d a d te q a i e a e w si c e s d 6 t e i e n l a i ft a t sw s i o e n h u l id r t a r a e . n q t h n mp f n Ke r s o u a o ; x l d d g a ht ; co t eu e g t g s se y wo d :n d lri n e p o e p i mi r s u t r ; a i y t m r r e r n
和力 学性 能 , 件 外 观质 量 、 寸 精 度及 内在 质 铸 尺 量均 大 幅度提 高 。
作者 简介 : 魏传 颖( 901 一 , , 17 . ) 男 汉族 , 0 工程师 , 主要 从 事铸 铁
合 金 的研 究 工作 。
度 由以前的 13m ~ m下降到 目前 的 1 m以下 。 m
P e e to fEx l d d Gr p ie o d l r I o r v n n o p o e a h t fNo u a r n i
WE h a— i , I N J 2WA GJ g sn I u n y QA B C n i N i - og n
3级 , 织 致 密 , 组 内部 不 允许 有 任 何 缩 孑 、 松 、 L缩
收 稿 日期 :00 0 — 8 21—20 修 定 日期 :0 0 0 — 3 2 1— 4 1
孕育工艺上进行了研究 ,确保 了铸件球化率等 级、 消除 了石墨 畸 变 现象 , 改善 了铸 件金 相 组 织
n d l ri n a d u e n lc moi e I wa o sd r d b n lsst a h e v e t n o ee ta e n mp o e a ig o u a o n s d o o o t . t s c n ie e y a ay i h tt e h a y s c i fd fc r a a d i r p rg t r v o n
16 0℃等措施 , 4 改善 了铸件内在质量 , 提高了外套铸件的成品率。 关键词 : 球墨铸铁 ; 开花状 石墨 ; 金相组织 ; 浇注系统
中图分类号: A 文献标识码 :G 5 . T 206 文章编号 :0 3 8 4 (0 0)3 0 7 — 3 10 — 35 2 1 0 — 0 9 0
铁路机车弹簧外套 的主要作用是保证机车
弹 簧有 效 工作 、 发挥 良好 的减 振 性 能 , 求具 有 要
夹渣 、 气孔 等缺 陷 。 针 对 弹簧 外 套 产 品在 生 产 过程 中容 易 出现 开花状 畸变 石墨 的现 象 , 铸 造浇 注工 艺及球 化 从
较高的力学性能以及尺寸精度 : 球化率不得低于
由于铁液得 到充 分净 化 , 管 的力 学性 能也 大 幅 铸
参 考 文 献
提高 , 伸长率 由 7 1%提高到 9 4 同时 %~ 1 % 1%,
大大 降低 了管壁 夹渣 的倾 向 , 管 的一 次水 压合 铸
[ 中国机械工 程学会铸造分会编 . 1 ] 铸造手册 ・ 铸铁 ( 1 ) 】 第 卷 [1 M
H f 2 0 2 ;C ia e i 3 0 2 hn ) e
Abtat T eew sepoe rp i p er gi eh aysc o rao sr gca cs n a eo T 5 — 0gae src: hr a xl dgaht apai t ev et nae f pi ot at gm d f 4 0 1 d d e n c uige po e rp i . h rfr, ya o t gtev r c l rsueg t gs se a d n d lr ig yt w sterao a sn x ld dga h t T eeoe b d pi h et a es r ai ytm n o uai n e e n i p n z
al y wi o E c n e t e p n r n tp i g tmp r tr ≥ 1 5 0 ℃ ,a d p u n e e a u e i h a g f 1 4 0 l t l w R o tn ,k e i g i a p n e e au e o h o 2 n o r g t mp r t r n t e r n e o 2 ~1 i
(.n u S e a cec n eh o g o Ld, ee 2 02 . hn; .n u Taya o e q im n Wok , 1 h i h ̄i SineadT c nl yC . t.H f 3 0 2 C ia 2A h i inunPw r up et rs A n o i E