化学退镍水
退镍剂常用配方
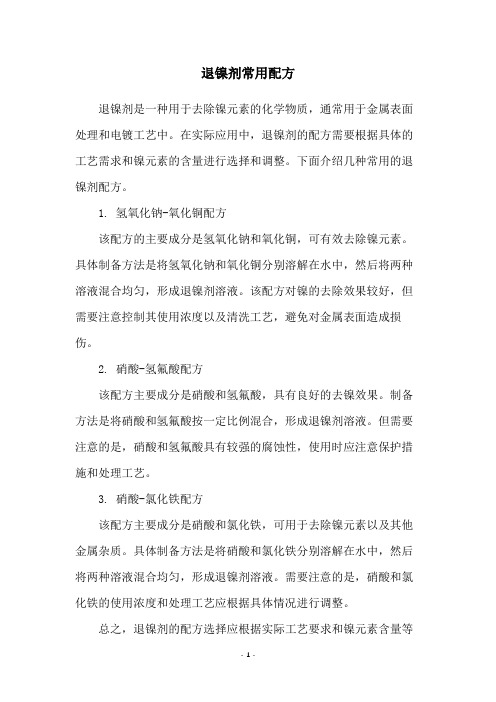
退镍剂常用配方
退镍剂是一种用于去除镍元素的化学物质,通常用于金属表面处理和电镀工艺中。
在实际应用中,退镍剂的配方需要根据具体的工艺需求和镍元素的含量进行选择和调整。
下面介绍几种常用的退镍剂配方。
1. 氢氧化钠-氧化铜配方
该配方的主要成分是氢氧化钠和氧化铜,可有效去除镍元素。
具体制备方法是将氢氧化钠和氧化铜分别溶解在水中,然后将两种溶液混合均匀,形成退镍剂溶液。
该配方对镍的去除效果较好,但需要注意控制其使用浓度以及清洗工艺,避免对金属表面造成损伤。
2. 硝酸-氢氟酸配方
该配方主要成分是硝酸和氢氟酸,具有良好的去镍效果。
制备方法是将硝酸和氢氟酸按一定比例混合,形成退镍剂溶液。
但需要注意的是,硝酸和氢氟酸具有较强的腐蚀性,使用时应注意保护措施和处理工艺。
3. 硝酸-氯化铁配方
该配方主要成分是硝酸和氯化铁,可用于去除镍元素以及其他金属杂质。
具体制备方法是将硝酸和氯化铁分别溶解在水中,然后将两种溶液混合均匀,形成退镍剂溶液。
需要注意的是,硝酸和氯化铁的使用浓度和处理工艺应根据具体情况进行调整。
总之,退镍剂的配方选择应根据实际工艺要求和镍元素含量等
因素进行综合考虑和调整,以确保去镍效果和金属表面质量。
同时,使用退镍剂时应注意相关安全措施和环境保护要求。
化学镀镍的广泛应用与环保新形势下的配方调整

化学镀镍的广泛应用与环保新形势下的创业建议5年前本人写过一篇《关于电镀行业创业的思考和建议》,其中写道:回顾在PCB药水和五金电镀药水行业的十多年经历,还有09年开涂料厂后这四年来购买我配方的朋友们反馈的创业经过,对想做电镀的创业者有如下建议:一、电镀药水行业是一个经过从分竞争的行业,暴利时代已经远去。
二、电镀行业是一个适合创业的行业。
这个行业有一定的技术含量,但是投资门槛很低,设备投资几乎可以忽略不计。
三、就像每个行业都有自己的规则,电镀行业也是如此。
回扣是电镀行业普遍存在的。
如果使用你产品的电镀师傅或者是关键角色没有获利(回扣或者好处),再好的药水也不好用。
四、化工原料市场很混乱,要学会鉴别原料。
工业级的原料分装到瓶中当试剂级别销售,这种现象很普遍。
有时你有好的配方但是原料不行,产品质量也不好。
安美特的酸铜配方很好,但是国内没有与之匹配的原料,所以搞配方的要从分考虑国内的原料情况。
五、如果你已经在生产电镀方面的药水,在更换原料供应商时要从分试验,选择一个关系最好的客户应用,没有问题才能更换。
六、如果你准备在这个行业创业,或者想将产品发展得更加全面,我可以有偿提供帮助。
欢迎咨询。
电话:七、发展你的人脉,人脉就是财富。
这对所有行业都是适用的。
这些建议目前依旧有效。
但是面对日益紧迫的环保压力和政策面经常一刀切式的执法,电镀行业生存艰难。
化学镀镍的应用每年都保持较快增长速度就是政策压力的一种体现。
市场上号称环保的合金催化液就是化学镀镍的改版,迫于环保的压力,不再使用电镀这2个字,连化学镀镍这个名称都不用了,改称:合金催化液,其实就是化学镀镍,而且是正宗的化学镀镍,改名称忽悠了不少人。
如果改叫合金催化能够避开政策压力,我们姑且接受这个名称。
但是,政府部门还制定了更严格的标准,规范了危险化学品的经营、运输,加强了危险化学品的管制,这就使得电镀行业都需要用到的硫酸盐酸氨水都变得难以购买。
而且氨氮的排放也被严格管制,这就使得以前的除油、除锈、抛光等工艺受到影响,我们需要寻找新的替代工艺。
配制化学镍

化学镍配伍硫酸镍400-460g/L A剂次磷酸钠180-200g/L+络合剂+稳定剂+促进剂 B 剂次磷酸钠480-520g/L+光剂+稳定剂 C剂化学镀镍化学镀镍已成为国际上表面处理领域中发展最快的工业技术之一,以其优良的性能,在几乎所有的工业部门都得到了广泛应用,每年总产值达10亿美元,而且每年还以5%~7%的速度递增。
一、性质和用途用次磷酸钠作还原剂获得的镀层实际上是镍磷合金。
依含磷量不同可分为低磷(1%~4%)、中磷(4%~10%)和高磷(10%~12%)。
从不同pH值的镀液中可获得不同含磷量的镀层,在弱酸性液(pH=4~5)中可获得中磷和高磷合金;从弱碱性液(pH=8~10)中可获得低磷和中磷合金。
含磷为8%以上的Ni-P合金是一种非晶态镀层。
因无晶界所以抗腐性能特别优良。
经过热处理(300~400℃)变成非晶态与晶态的混合物时硬度可高达HV=1155;化学复合镀层硬度更高,如Ni-P-SiC,镀态HV=700,350℃热处理后可达到HV=1300。
非晶态合金是开发新材料的方向,现已成为工程学科的一大热门。
近年低磷化学镀镍是研究开发的又一热点,含磷1%~4%的Ni-P合金,镀态的HV=700,热处理后接近硬铬的硬度,是替代硬铬层的理想镀层,又是可在铝上施镀的好镀种。
化学镀层的种类、性质和主要用途,列于表3-1-2。
化学镀镍层与电镀镍层的性能比较,列于表3-1-3。
表3-1-2 化学镀镍种类性质和主要用途表3-1-3 化学镀镍与电镀镍的性能比较化学镀镍的脆性较大,在钢上仅能经受2.2%的塑性变形而不出现裂纹。
在620℃下退火后,塑性变形能力可提高到6%;当热处理温度达840℃时,其塑性还可进一步改善。
化学镀镍层同钢铁、铜及其合金、镍和钴等基体金属有良好的结合力。
在铁上镀覆10~12μm的化学镀镍层,经反复弯曲180°后未出现任何裂纹和脱落现象。
但与高碳钢、不锈钢的结合力比上述金属差;同非金属材料的结合力会更差些,重要的是取决于非金属材料镀前预处理质量。
化学镀镍的常见故障及解决办法
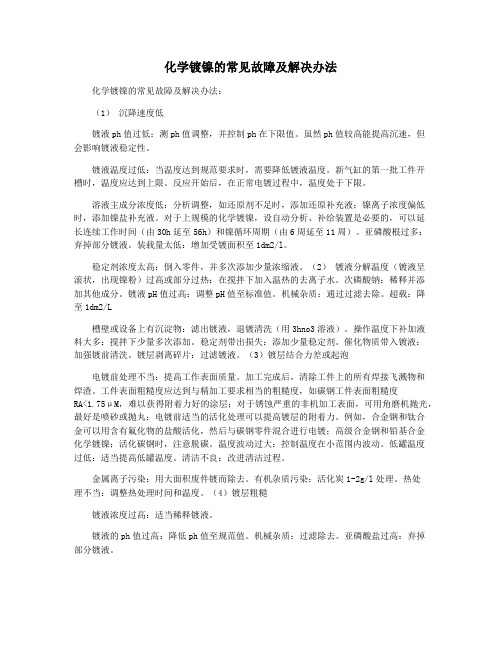
化学镀镍的常见故障及解决办法化学镀镍的常见故障及解决办法:(1)沉降速度低镀液ph值过低:测ph值调整,并控制ph在下限值。
虽然ph值较高能提高沉速,但会影响镀液稳定性。
镀液温度过低:当温度达到规范要求时,需要降低镀液温度。
新气缸的第一批工件开槽时,温度应达到上限。
反应开始后,在正常电镀过程中,温度处于下限。
溶液主成分浓度低:分析调整,如还原剂不足时,添加还原补充液;镍离子浓度偏低时,添加镍盐补充液。
对于上规模的化学镀镍,设自动分析、补给装置是必要的,可以延长连续工作时间(由30h延至56h)和镍循环周期(由6周延至11周)。
亚磷酸根过多:弃掉部分镀液。
装载量太低:增加受镀面积至1dm2/l。
稳定剂浓度太高:倒入零件,并多次添加少量浓缩液。
(2)镀液分解温度(镀液呈滚状,出现镍粉)过高或部分过热:在搅拌下加入温热的去离子水。
次磷酸钠:稀释并添加其他成分。
镀液pH值过高:调整pH值至标准值。
机械杂质:通过过滤去除。
超载:降至1dm2/L槽壁或设备上有沉淀物:滤出镀液,退镀清洗(用3hno3溶液)。
操作温度下补加液料大多:搅拌下少量多次添加。
稳定剂带出损失:添加少量稳定剂。
催化物质带入镀液:加强镀前清洗。
镀层剥离碎片:过滤镀液。
(3)镀层结合力差或起泡电镀前处理不当:提高工作表面质量。
加工完成后,清除工件上的所有焊接飞溅物和焊渣。
工件表面粗糙度应达到与精加工要求相当的粗糙度,如碳钢工件表面粗糙度RA<1.75μM,难以获得附着力好的涂层;对于锈蚀严重的非机加工表面,可用角磨机抛光,最好是喷砂或抛丸;电镀前适当的活化处理可以提高镀层的附着力。
例如,合金钢和钛合金可以用含有氟化物的盐酸活化,然后与碳钢零件混合进行电镀;高级合金钢和铅基合金化学镀镍;活化碳钢时,注意脱碳。
温度波动过大:控制温度在小范围内波动。
低罐温度过低:适当提高低罐温度。
清洁不良:改进清洁过程。
金属离子污染:用大面积废件镀而除去。
安徽得立新材料火法0319

安徽得立新材料有限公司项目建议书安徽得立新材料有限公司二零一九年三月目录一、基本情况及市场调研 (4)二、项目选址及建设规模: (4)三、处置工艺 (6)3.1各类电镀污泥及含重金属危险废物火法处置工艺 (6)3.2各类电镀污泥及含重金属危险废物湿法处置工艺: (12)3.3危险废物收集 (15)3.4退镀及退镀液处置工艺 (15)四、环境保护及产生的治理效应: (20)五、项目投资估算及经济效益分析: (20)5.1工程概况 (20)5.2投资估算 (21)5.3经济效益分析 (21)六、小结: (21)一、基本情况及市场调研依据《中华人民共和国固体废物污染环境防治法》中规定的要求,以允许的经营方式、经营类别和经营规模从事经营活动,使用符合国家安全标准、环境保护标准,为提高社会公益效益作出贡献。
国家发展和改革委员会办公厅文件发放的:发改办环资(2011)1524号要求,2012国家主要鼓励扶持五个方面:节能方面、节水方面、循环经济方面、资源综合利用方面、污染防治方面。
根据池州江南产业园当地工业结构,该危废处置利用项目可以极大的承接本地企业产生的危废,有利于本地工业更好的发展,并遵循国际鼓励的循环经济及资源综合利用的方针和政策。
二、项目选址及建设规模:本项目计划建设在池州江南产业园区内,具体处置类别及规模如下表:三、处置工艺3.1各类电镀污泥及含重金属危险废物火法处置工艺(1)火法工艺流程的简述烘干及制块工艺:含水分60~80%湿法泥经三夹层烘干窑烘干至含水分35%左右,干泥和湿泥混合并配入废碳精粉经混合搅拌制粒后送入立式烧结窑预处理成块。
立式烧结窑采用目前国内最先进的湿法泥逆流烧结炉工艺,新型节能高效立式逆流烧结炉生产工艺为:各种铜泥,镍泥,铜灰及含铜污泥料经配料混合,并混入一定量的石灰充分拌匀,抓斗行车拌料混合,再放置几天预均化.本工艺拟用抓斗行车拌料,以节约场地。
配料仓库中设置:原料仓、废碳精粉仓、石灰仓、石英砂仓等。
线路板废水处理工艺介绍
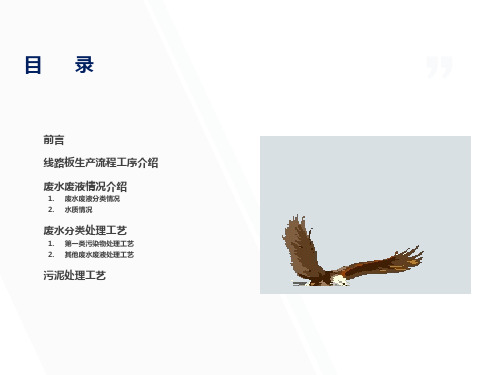
前言 线路板生产流程工序介绍 废水废液情况介绍 废水废液分类情况 水质情况 废水分类处理工艺 第一类污染物处理工艺 其他废水废液处理工艺 污泥处理工艺
目 录
前言
当前的信息社会,电子工业飞速发展,作为电子业的基础之一——线路板每年以10—20%的速度在递增,从而成为电子行业中的重要产业之一,然而其复杂的制程产生许多废弃物和废水废液。 印刷线路板制造工艺流程复杂,其废水所产生的污染物多样,主要含有铜、镍等重金属离子、高分子有机物、络合剂等,针对线路板废水种类繁多,污染成份复杂,若不采取合理有效的处理工艺,使废水稳定达标,将对环境造成严重的污染。针对线路板废水的不同特点,在处理时必须对不同的废水进行分流,采取不同的方法进行处理。
贴膜
显影/水洗
烘干
酸性蚀刻/水洗
脱膜/水洗
脱脂/水洗
微蚀/水洗
预浸酸/水洗
镀铜/水洗
镀锡/水洗
脱膜/水洗
剥锡/水洗
烘干
下一道工序
一般清洗废水
显影废水 废显影液
显影废水 脱膜废液
除油废水
一般清洗废水 废微蚀液
一般清洗废水
含锡废水 镀锡废液
显影废水 脱膜废液
废碱性蚀刻液 铜氨废水
pH调整池
反应池
慢混池
有机与络合废水沉淀池
综合废水调节池
有机污泥池
污泥
预处理废液
快混池
NaOH pH 11
Na2S ORP-400mv
FeSO4
PAM
④ 、有机与络合废水处理工艺
一般清洗废水调节池
一般清洗废水
快混池
其他预处理废水
慢混池
砂滤器
碳虑器
超滤UF装置
化学镀镍的原理及配方构成
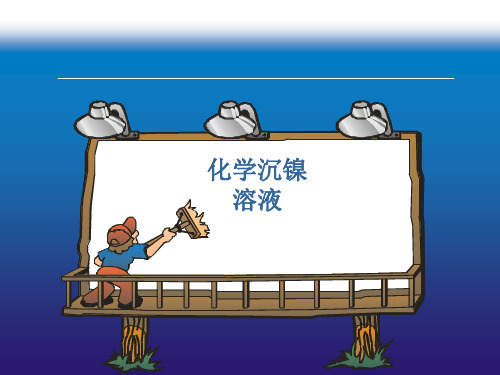
在催化表面和充分能量的情况下,次亚磷酸盐离子被氢 氧根离子与水氧化,生成亚磷酸盐。
反应
3. H+ + e
H
6. NiOH+ ads + 2e
Ni + OH-
在这些反应中产生的电子参与将H+离子还原成氢气和吸附 的NiOH 离子还原成镍的反应
反应
5. Ni2+ + H2O 6. NiOH+ ads + 2e
2H2PO3- + H2 + 2H+ + Nio
碱镍—磷体系 Ni2+ + 2H2PO2- + 4OH-*
Ni + 2HPO3- + 2H2O + H2
*催化反应
反应
1. H2PO2- ads + OH– ads 2. H2PO2- + H2O ads 3. H+ + e 4. H + H 5. Ni2+ + H2O 6. NiOH+ ads + 2e 7. H2PO2- ads 8. H2PO2- ads + 2H+ + e
铜
-
Cu
银
-
Ag
金
-
Au
碳
-
C
非催化金属(有毒的)
铜
-
Cu
铅
-
Pb
锌
-
Zn
铬
-
Cr
砷
-
As
锑
-
Sb
铋
-
Bi
镉
-
Cd
锡
-
Sn
及其它重金属
电镀园区废水分类来源及占比

0.75% 0.75% 0.75% 4.00% 1.25%
单独收集后由对应的废液管道输
浓度高的酸槽废水
送至废水处理站内的高浓酸性废 水收集池,经过处理后定量进入
前处理废水调节池
单独收集后由对应的废液管道输
活化回收槽废水、未回用于生产线的回 送至废水处理站内的高浓重金属
收槽废水、定期清洗槽废水
废水收集池,经过处理后定量进
废水收集池,经过处理后定量打
入络合废水调节池
单独收集后由对应的废液管道输
前处理除油废水、除蜡、化抛废水、定 送至废水处理站内的高浓有机废
期清洗槽废水等
水收集池,经过处理后定量打入
前处理废水调节池
单独收集后由对应的废液管道输
浓度高的酸槽废水
送至废水处理站内的高浓酸性废 水收集池,经过处理后定量进入
前处理废水调节池
镍滤芯清洗水、定期清洗槽废水 废水收集池,经过处理后定量打
入化学镍废水调节池
单独收集后由对应的废液管道输
碱性锌酸盐回收槽废水、定期清洗槽废 送至废水处理站内的高浓碱锌废
水
水收集池,经过处理后定量进入
排放系统
单独收集后由对应的废液管道输
铜氨络合、化学铜、沉铜回收槽废水、 送至废水处理站内的化学铜高浓
定期清洗槽废水
入排放系统
1.25% 2.50%
/
/
10.00%
镀槽内更换的槽液
回收利用或委外处理
序号 一、漂洗水
名称
水量(m3/d)
1
含铬废水
3000
含镉废水 2
250
3
含镍废水
4
化学镍废水
2000 1000
5
综合废水
DZN-988 锌合金化学退镀工艺汇总

DZN-988锌合金化学退镀工艺一、特点1.专用于锌合金表面之铜、镍镀层的化学退镀。
2.退镀快速,节省工序,提高效率。
3.工件退镀表面光亮、洁净,可以不经过常规前处理直接电镀。
二、溶液组成及操作条件1.退镀配制程序材料低浓度高浓度①水400ml/L 200ml/L②68%硝酸200ml/L 340ml/L③95%硫酸300ml/L 360ml/L④DZN-988A退镀剂100ml/L 100ml/L温度70-800C 70-800C时间1-3分钟1-3分钟2.除膜抛光配制程序材料用量①水800ml/L②铬酐250g/L③DZN-988B除膜抛光剂200ml/L温度20-400C时间0.5-2分钟三、生产维护1.工艺流程锌合金工件(含铜、镍镀层)—退镀—水洗—除膜抛光—水洗—返镀2.退镀工序注意事项①工作液按照配料程序在均匀搅拌下缓慢加料以防爆沸,刚配制的工作液温度在800C以上,冷却到800C左右开始退镀,由于退镀过程是放热反应,可通过控制退镀工件的装载量来控制反应温度,正常退镀温度以70-800C为宜,槽液温度低于700C时应加温至工艺范围。
②适当提高硝酸含量,有利于镍镀层的退除;适当提高硫酸含量,有利于铜镀层的退除。
③低浓度配方适用于快速退镀,高浓度配方适用于较精密零件的退镀。
④当退镀速度减慢或工件表面产生腐蚀时,应考虑更换或部分更换工作液。
3.除膜抛光工序注意事项①当工件表面光泽下降或出现轻微腐蚀时,应考虑更换或部分更换工作液。
②本工序能够一次性去除工件表面的黑膜,并对工件进行除油抛光。
经本工序处理后工件表面光亮、洁净,可不经过常规前处理直接进入电镀工序。
声明:此技术资料内所有关于本公司产品的建议,是以本公司信赖的实验及资料作为标准。
各国从业者在操作及设备上有所差异,故本公司不能保证及不负责任何不良后果。
此故障处理方法所有的资料也不能作为侵犯版权的证据。
化学镀镍液产生不稳定性原因分析

化学镀镍液产⽣不稳定性原因分析⼀、镀液⾃⾏分解现象1. ⽓体从镀液内部缓慢地放出镀液开始⾃⾏分解时,⽓体不仅在镀件的表⾯放出,⽽且在整个镀液中缓慢⽽均匀地放出。
2. ⽓体析出速度加剧出现上述情况的镀液,若不及时采取有效的措施,则⽓体的逸出速度会越来越快,会产⽣⼤量的⽓泡,使镀液呈泡沫状。
3. 形成⿊⾊镀层或沉积物当化学镀镍液出现许多泡沫,镀覆零件及器壁上就开始⽣成粗糙的⿊⾊镀层,或在镀液中产⽣许多形状不规则的⿊⾊粒状沉积物。
4. 镀液颜⾊变淡镀液在⾃⾏分解过程中,镀液的颜⾊不断变淡,例如含氨碱性化学镀镍液中,当发⽣⾃⾏分解后,镀液的颜⾊由深蓝⾊变成蓝⽩⾊,与此同时还可嗅到⼀股刺⿐的氨味,待氨味消失时,化学镀镍液已安全分解了。
⼆、影响镀液不稳定的主要因素1. 镀液的配⽐不当①次亚磷酸盐(还原剂)浓度过⾼提⾼镀液中次亚磷酸盐的浓度,可以提⾼沉积速度。
但是当沉积速度达到极限时,继续增加次亚磷酸盐的浓度,不仅沉积速度提不⾼,反⽽会造成镀液的⾃⾏分解。
尤其对于酸性镀液,当PH值偏⾼时,镀液⾃⾏分解的趋势愈严重,其原因是:次亚磷酸盐的浓度过⾼时,镀液的化学能得到提⾼从⽽处于更⾼能位,但化学镀镍是属于液相(镀液)、固相(镀层)、⽓相(析出的氢⽓)的多相反应体系。
当镀液处于⾼能位状态时,就加速了液相组元转向固相、⽓相的趋势,即加速了镀液内部的还原作⽤。
若镀液此时存在其它不稳定因素(如局部温度过⾼,有浑浊沉淀物等),最容易诱发⾃⾏分解。
当镀液中次亚磷酸盐的浓度过⾼时,如果PH值也偏⾼,就会⼤⼤降低镀液中亚磷酸镍的沉淀点,并造成⼯件表⾯上有许多颗粒状。
②镍盐的浓度过⾼提⾼镍盐的浓度,当镀液PH值⼜偏⾼时,易⽣成亚磷酸镍和氢氧化镍沉淀,从⽽使镀液混浊,极易触发镀液的⾃⾏分解,并造成⼯件表⾯上有许多颗粒状。
③络合剂的浓度过低络合剂的重要作⽤之⼀是能提⾼镀液中亚磷酸镍的沉淀点。
镀液在镍盐浓度、温度、PH值⼀定时,亚磷酸镍在镀液中的溶解度和沉淀点也是⼀定的。
铜母排镀镍层化学退镀液及其使用方法
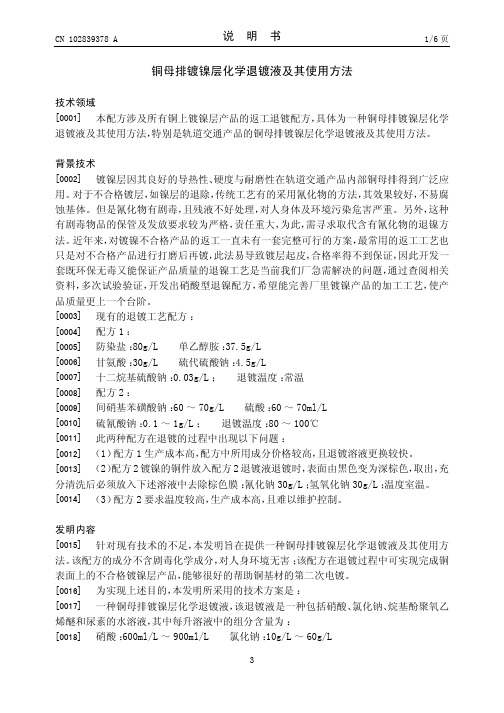
铜母排镀镍层化学退镀液及其使用方法技术领域[0001] 本配方涉及所有铜上镀镍层产品的返工退镀配方,具体为一种铜母排镀镍层化学退镀液及其使用方法,特别是轨道交通产品的铜母排镀镍层化学退镀液及其使用方法。
背景技术[0002] 镀镍层因其良好的导热性、硬度与耐磨性在轨道交通产品内部铜母排得到广泛应用。
对于不合格镀层,如镍层的退除,传统工艺有的采用氰化物的方法,其效果较好,不易腐蚀基体。
但是氰化物有剧毒,且残液不好处理,对人身体及环境污染危害严重。
另外,这种有剧毒物品的保管及发放要求较为严格,责任重大,为此,需寻求取代含有氰化物的退镍方法。
近年来,对镀镍不合格产品的返工一直未有一套完整可行的方案,最常用的返工工艺也只是对不合格产品进行打磨后再镀,此法易导致镀层起皮,合格率得不到保证,因此开发一套既环保无毒又能保证产品质量的退镍工艺是当前我们厂急需解决的问题,通过查阅相关资料,多次试验验证,开发出硝酸型退镍配方,希望能完善厂里镀镍产品的加工工艺,使产品质量更上一个台阶。
[0003] 现有的退镀工艺配方:[0004] 配方1:[0005] 防染盐:80g/L 单乙醇胺:37.5g/L[0006] 甘氨酸:30g/L 硫代硫酸钠:4.5g/L[0007] 十二烷基硫酸钠:0.03g/L;退镀温度:常温[0008] 配方2:[0009] 间硝基苯磺酸钠:60~70g/L 硫酸:60~70ml/L[0010] 硫氰酸钠:0.1~1g/L;退镀温度:80~100℃[0011] 此两种配方在退镀的过程中出现以下问题:[0012] (1)配方1生产成本高,配方中所用成分价格较高,且退镀溶液更换较快。
[0013] (2)配方2镀镍的铜件放入配方2退镀液退镀时,表面由黑色变为深棕色,取出,充分清洗后必须放入下述溶液中去除棕色膜:氰化钠30g/L;氢氧化钠30g/L;温度室温。
[0014] (3)配方2要求温度较高,生产成本高,且难以维护控制。
铁件退铜镍配方
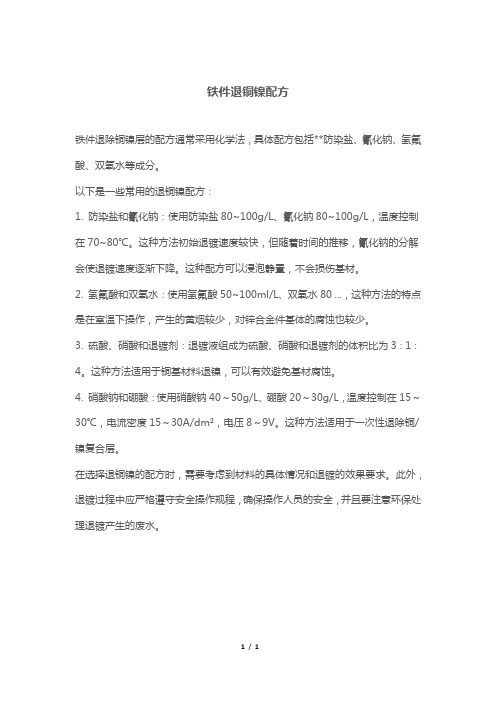
铁件退铜镍配方
铁件退除铜镍层的配方通常采用化学法,具体配方包括**防染盐、氰化钠、氢氟酸、双氧水等成分。
以下是一些常用的退铜镍配方:
1. 防染盐和氰化钠:使用防染盐80~100g/L、氰化钠80~100g/L,温度控制在70~80℃。
这种方法初始退镀速度较快,但随着时间的推移,氰化钠的分解会使退镀速度逐渐下降。
这种配方可以浸泡静置,不会损伤基材。
2. 氢氟酸和双氧水:使用氢氟酸50~100ml/L、双氧水80 ...,这种方法的特点是在室温下操作,产生的黄烟较少,对锌合金件基体的腐蚀也较少。
3. 硫酸、硝酸和退镀剂:退镀液组成为硫酸、硝酸和退镀剂的体积比为3∶1∶4。
这种方法适用于铜基材料退镍,可以有效避免基材腐蚀。
4. 硝酸钠和硼酸:使用硝酸钠40~50g/L、硼酸20~30g/L,温度控制在15~30℃,电流密度15~30A/dm²,电压8~9V。
这种方法适用于一次性退除铜/镍复合层。
在选择退铜镍的配方时,需要考虑到材料的具体情况和退镀的效果要求。
此外,退镀过程中应严格遵守安全操作规程,确保操作人员的安全,并且要注意环保处理退镀产生的废水。
1/ 1。
第二十一章 常规镀层的退镀方法
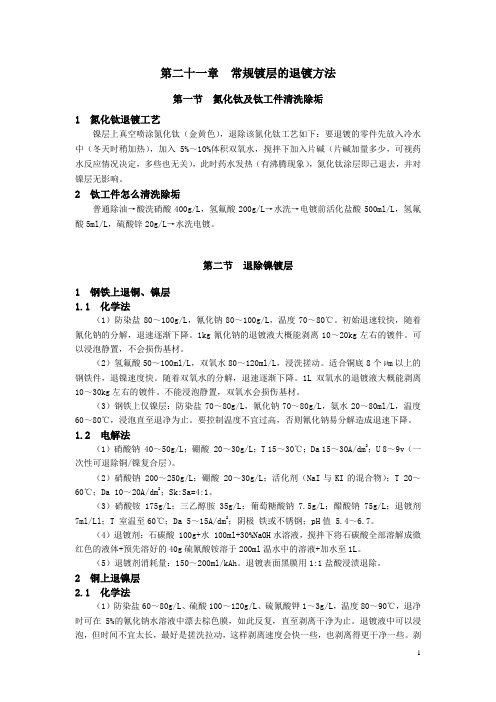
第二十一章常规镀层的退镀方法第一节氮化钛及钛工件清洗除垢1 氮化钛退镀工艺镍层上真空喷涂氮化钛(金黄色),退除该氮化钛工艺如下:要退镀的零件先放入冷水中(冬天时稍加热),加入5%~10%体积双氧水,搅拌下加入片碱(片碱加量多少,可视药水反应情况决定,多些也无关),此时药水发热(有沸腾现象),氮化钛涂层即己退去,并对镍层无影响。
2 钛工件怎么清洗除垢普通除油→酸洗硝酸400g/L,氢氟酸200g/L→水洗→电镀前活化盐酸500ml/L,氢氟酸5ml/L,硫酸锌20g/L→水洗电镀。
第二节退除镍镀层1 钢铁上退铜、镍层1.1 化学法(1)防染盐80~100g/L,氰化钠80~100g/L,温度70~80℃。
初始退速较快,随着氰化钠的分解,退速逐渐下降。
1kg氰化钠的退镀液大概能剥离10~20kg左右的镀件。
可以浸泡静置,不会损伤基材。
(2)氢氟酸50~100ml/L,双氧水80~120ml/L,浸洗搓动。
适合铜底8个µm以上的钢铁件,退镍速度快。
随着双氧水的分解,退速逐渐下降。
1L双氧水的退镀液大概能剥离10~30kg左右的镀件。
不能浸泡静置,双氧水会损伤基材。
(3)钢铁上仅镍层:防染盐70~80g/L,氰化钠70~80g/L,氨水20~80ml/L,温度60~80℃,浸泡直至退净为止。
要控制温度不宜过高,否则氰化钠易分解造成退速下降。
1.2 电解法(1)硝酸钠 40~50g/L;硼酸 20~30g/L;T 15~30℃;Da 15~30A/dm2;U 8~9v(一次性可退除铜/镍复合层)。
(2)硝酸钠 200~250g/L;硼酸 20~30g/L;活化剂(NaI与KI的混合物);T 20~60℃;Da 10~20A/dm2;Sk:Sa=4:1。
(3)硝酸铵 175g/L;三乙醇胺 35g/L;葡萄糖酸钠 7.5g/L;醋酸钠 75g/L;退镀剂7ml/Ll;T 室温至60℃;Da 5~15A/dm2;阴极铁或不锈钢;pH值 5.4~6.7。
退镀工艺
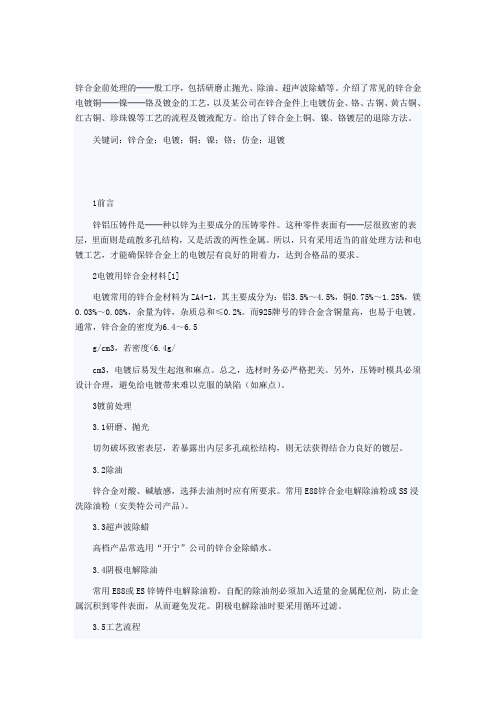
锌合金前处理的──般工序,包括研磨止抛光、除油、超声波除蜡等。
介绍了常见的锌合金电镀铜──镍──铬及镀金的工艺,以及某公司在锌合金件上电镀仿金、铬、古铜、黄古铜、红古铜、珍珠镍等工艺的流程及镀液配方。
给出了锌合金上铜、镍、铬镀层的退除方法。
关键词:锌合金;电镀;铜;镍;铬;仿金;退镀1前言锌铝压铸件是──种以锌为主要成分的压铸零件。
这种零件表面有──层很致密的表层,里面则是疏散多孔结构,又是活泼的两性金属。
所以,只有采用适当的前处理方法和电镀工艺,才能确保锌合金上的电镀层有良好的附着力,达到合格品的要求。
2电镀用锌合金材料[1]电镀常用的锌合金材料为ZA4-1,其主要成分为:铝3.5%~4.5%,铜0.75%~1.25%,镁0.03%~0.08%,余量为锌,杂质总和≤0.2%。
而925牌号的锌合金含铜量高,也易于电镀。
通常,锌合金的密度为6.4~6.5g/cm3,若密度<6.4g/cm3,电镀后易发生起泡和麻点。
总之,选材时务必严格把关。
另外,压铸时模具必须设计合理,避免给电镀带来难以克服的缺陷(如麻点)。
3镀前处理3.1研磨、抛光切勿破坏致密表层,若暴露出内层多孔疏松结构,则无法获得结合力良好的镀层。
3.2除油锌合金对酸、碱敏感,选择去油剂时应有所要求。
常用E88锌合金电解除油粉或SS浸洗除油粉(安美特公司产品)。
3.3超声波除蜡高档产品常选用“开宁”公司的锌合金除蜡水。
3.4阴极电解除油常用E88或ES锌铸件电解除油粉。
自配的除油剂必须加入适量的金属配位剂,防止金属沉积到零件表面,从而避免发花。
阴极电解除油时要采用循环过滤。
3.5工艺流程化学除油──超声波除油──电解除油──浸蚀活化(硫酸5~10mL/L+氢氟酸10~20mL/L,pH控制在0.5~1.5,视工件外形复杂性而定;室温,10~30s至刚开始全面反应产生气泡后立即取出零件,然后彻底清洗干净)。
3.6热浓硫酸除蜡除油[2]为减少工序和时间,在投资少、见效快,操作方便、稳定的条件下,锌铸件经磨抛光后(零件必须干燥!)采用浓硫酸加热脱水除油;而锌合金铸件在热的浓硫酸中除油快,又不会受腐蚀。
铜基退镍方法及案例分享

铜基退镍方法两则及退镀案例分享铜与镍的化学性质很相近,紫铜件退镍一直都比较困难,退不好很容易导致基材腐蚀。
常用的有化学退镀法和电解退镀法。
方法1、化学退镀:防染盐S70g/L硫酸100g/L硫氰酸钾1g/L温度:80-90℃时间:褪尽为止镍退尽后,铜基材表面会有一层深棕色的膜,这个膜需要在30g/L 的氰化钠溶液中或者铬酐硫酸溶液中退去,才能漏出紫红的铜表面来。
此退镀液很容易失效,适合现配现用。
方法2、电解退镀:盐酸5%(体积比)添加剂30g/L需退镀工件置于阳极,阴极可用不锈钢板或者铜板,阳极电流密度0.5-3ASD,温度为室温。
镍层退尽后,铜基材表面也会生成暗红色的钝化膜,这个膜来自于添加剂,正是由于这个钝化膜的存在,才阻止了铜材的进一步溶解。
退镀时宜用定电压,镍层退尽后,电流会急剧下降,既可以表明退尽了,也可以防止过腐蚀。
该钝化膜比较容易溶解,使用化学抛光液就可以清洗干净。
抛光液配方如下:配方1:硫酸10%双氧水50ml/L稳定剂50ml/L温度:室温,适当加热可提高反应速度,但不宜超过40℃时间1-5分钟,表面黑膜溶解干净露出新鲜的铜表面为止配方2:硫酸400ml/L硝酸30ml/L盐酸5ml/L光亮剂10ml/L温度:室温时间10秒-1分钟,表面光亮为止电解退镀液跟化学退镀相比,无需加热,寿命极长,后续的退膜也无需使用剧毒的氰化物和同样剧毒和污染环境的六价铬,事实上,很多电镀厂并没有使用这两种物质的资质。
唯一的劣势是对于某些形状复杂具有深孔的零件不太适用。
下面是笔者曾主导过的两次退镀案例,分享一下,给需要的同仁以作参考:案例1:某连续镀厂,笔者在其中任职技术人员。
该厂有条连续线专门做铜带镀镍镀锡加工,在镀镍的过程中由于导电不良,极易发生镍的折弯起皮问题,即使一卷料首末件都是好的,仍然无法保证中间就不会出现折弯起皮的问题,而每卷料在客户处冲压时,只要发现起皮,只能是整卷退回,要么整卷报废,要么退镀重做,在笔者到该公司任职前,由于没有好的退镀方法,一般都是报废处理,费用也只能由电镀厂承担。
环保绿色退镍剂,退镍水使用说明

新型退镍剂,无需加热化学退镍,无重金属及氰化钠,可回收镍。
不添加硝酸无酸雾,无黄烟,不污染环境。
一升母液稀释后可以溶解40-50克镍,退镀快,退镀速度1μm/min,退镀后溶液成分单一,有机添加剂含量低于50ppm,可以通过萃取、电积回收金属镍,废水可以回用,经济价值大。
现有市售退镍剂的缺点:1、需要加热到80-90℃。
2、使用大量的类似防染盐(间硝基苯磺酸钠)类的有机物,有大量的有机物,溶液难处理。
3、退镀后基材铜颜色发暗,不够明亮,有的时候退镀后基材表面还有棕黑色物需要用氰化钠或铬酐处理。
4、部分退镀剂中就有加入铬酐,数据有毒物质。
新型退镍剂优点:1、常温下使用,最好控制退镀温度不超过30-50℃。
2、使用硫酸体系,除了微量的无毒添加剂外只有硫酸镍,可以方便的实现镍回收,废水回用,实现零排放。
3、药剂退镀后铜的颜色依然明亮。
4、处理能力大,一公斤母液稀释后使用,可以溶解40-50克镍。
需要免费试用的请跟我联系,可在电商平台搜博智润商贸或者博智润退镍。
使用说明1、使用温度为20~70℃,以30-50℃为宜,加热能够加速退镀。
2、退镀液配置方法:1L母液+2.7L水+200mL双氧水(30%)+200克硫酸(115mL的98%浓硫酸)搅拌混匀之后既可以使用。
3、将待退镀材料放入退镀液中即可进行退镀,当无退镀能力时补加入100mL双氧水(30%)即可继续退镀,累积加双氧水(30%)量达到450mL依然无退镀能力后,说明镍已经饱和。
有条件可以测试双氧水量控制双氧水浓度在10-20g/L为宜,或者通过计算镍融入量补加双氧水,每克镍需要消耗1.4g的双氧水,相当于4.7mL30%双氧水。
4、30℃时退镀速度1μm/min,50℃退镀速度2μm/min。
5、退镀完成后应及时从退镀液中取出,并用清水清洗,防止残余退镀液对基材腐蚀。
6、1L母液可以配置4L退镀液,可以溶解45-60g的镍,配置大量溶液按照上诉比例放大即可。
- 1、下载文档前请自行甄别文档内容的完整性,平台不提供额外的编辑、内容补充、找答案等附加服务。
- 2、"仅部分预览"的文档,不可在线预览部分如存在完整性等问题,可反馈申请退款(可完整预览的文档不适用该条件!)。
- 3、如文档侵犯您的权益,请联系客服反馈,我们会尽快为您处理(人工客服工作时间:9:00-18:30)。
化学镀镍水(厂家直销)
一、产品编号:Q/YS.602(贻顺牌)
二、产品特点:本产品适用于铁件、钢件,锌合金,浸锌处理后的铝合金及铜合金表面镀镍合金层。
本产品无毒、无重金属。
不需电镀设备。
只需恒温装置,镀层是光亮的镍磷合金层,耐蚀性极好,结合力极佳。
镀液稳定性强,寿命超过12个周期。
三、产品组成:产品由A、B、C三剂组成,A和B按比例1:2开缸,以A和C按比例1:1添加,作为中间补充剂。
四、开缸药剂的配制及使用方法:
1、用A剂与B剂加水配兑,
2、配兑比例为A:B:水=1:2:7。
3、用纯净水把镀槽清洗干净。
然后在槽内加入槽容积一半大小的纯净水。
4、先将B剂按比例加入到槽内搅拌均匀,
5、在搅拌的同
6、时缓缓加入A剂。
7、搅拌均匀后测试镀液PH值,8、用10%的氨水调节PH值到4.7±0.2。
9、加入去离子水到规定的体积.
10、加热镀液将镀液温度稳定在意86-92摄氏度.
五、操作工艺流程.1.工件前处理:前处理对镀层质量至关重要,要使镀前的工件表面无污染,并且是处于活化状态,此过程主要有:除油,除锈,抛光,水洗。
2.酸洗活化:用酸洗活化剂浸泡工件2-3分钟,再水洗干净。
3.用热的去离子水冲洗工件,使工件升温,以避免下一步施镀时,冷工件吸收镀液热量而降温,导致停镀。
4.按照0.5-1.5dm2/升的装载比分散地吊挂在镀液中,控制镀液温度在意85-92摄氏度。
5.施镀过程中要有适度的轻搅拌,使温度及镀液分布均匀,从而保证化学镀镍的稳定进行,和镀层的一致性。
同时,要对镀液进行循环过滤。
滤网:孔径1-8微米,耐100摄氏度,耐酸。
六、化学镀镍的维护。
1.在施镀过程中,由于成分的不断消耗,镀速会有所减慢,可根据气泡的多少来添加补充剂A和C,按A:C=1:1添加。
要少量多次地补加。
每消耗一克金属镍,需补加A和C 各式各10毫升。
当大量补充A 和C 时,要先降温停镀,再加入A,C补充剂,并搅拌均匀,才能进行镀镍。
2.施镀过程中,镀液PH值会有变化,新鲜镀液PH控制在4.7-4.8,随着镀液老化,PH值会慢慢升高。
3.对于铜及其合金表面镀镍要用洁净铁丝或铝丝与铜工件接触进行引镀。
4.施镀过程要经常对镀液进行分析检测:PH值和镍离子含量。
镍的检测方法:取5.00ml 镀液放入500ML的三角瓶中,加入100ml去离子水,再加入100ml氨水,加紫脲酸胺指示剂。
用0.05mol/L的EDTA滴定至由橙黄变为紫色为终点,消耗EDTA的体积毫升数记为V 。
公式:镍(克/升)=0.587 * V
5.化学镀镍前要经严格的前处理,保证工件表面处于洁净活化态。
6.经常对设备进行检察:自动温控系统,循环过滤系统,及时发现及时排除。
7.镀液装载比要控制在0.5dm2 -1.5dm2.。