(可修改)生产效率提升方案.ppt
合集下载
制程优化,生产效率提升改善案(应对产能爬坡)
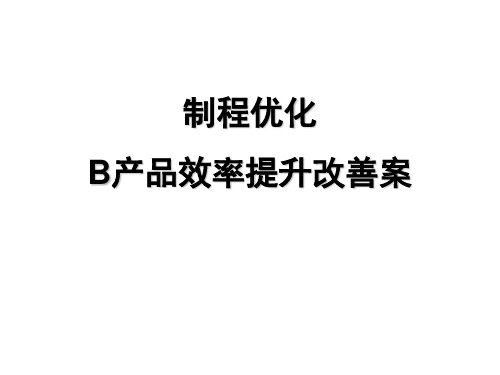
C2 1/2 1 1/2 0.630 0.190 3.136 C.I.=(λmax-3)/(3-1)=0.068<0.1
C3 3 2 1 1.817 0.547 3.136
B4
C1 C2 C3
Wi
Wi0
λmi
C1 1 1/4 1/7 0.329 0.082 3.004 λmax=1/3(λm1+λm2+λm3)=3.002
C1 0.081 0.540 0.263 0.082
Cj=ΣbiCji
0.156
C2 0.188 0.188 0.190 0.315 0.239
C3 0.731 0.163 0.547 0.603 0.593
方案三制程优化得分最高, 为最佳改善方向
二. 改善历程 (选择改善项目)
已改善过
量少影 响不大
无形效益
及时满足了出货 需求;
有形效益
使我建立了改善降理低念成, 本 ✓ 节省3人;
并已在E机种2上6应1万用R, MB/年✓. 产能提升30%;
产能从380台↗450台. ✓ 可降低成本261
万RMB/年.
工时: (280万台/年÷350台-280万台/年÷460台)
×1,273RMB/线.H =2, 435KRMB/年
1. 装HDD锁扣/贴贴纸工站 ( 8.8 〞)
1. 拆布套5〞/投基座2.2〞 2. 装遮片扣4.5〞 3. 装HDD扣5.5〞/贴贴纸3.3〞
无附加价值 能否取消布套?
二. 改善历程 (程序分析法﹑ECRS)
套布套
运输
拆布套
烤完漆
重取用复消E作套P业E/拆隔,无布开价套基值作座动业, 作.
运输
100% 81%
精益六西格玛效率提升方案

精益六西格玛效率提升实 施方案
制作:张照明
审核:
目录
1 项目概述
2
组织架构
3
实施步骤
4
项目总结
一、项目概述
1.生产效率的是一个综合性指标,它包括时间的可用性、有效时间的利用率和良品率三个方面,这是 工厂运营生产阶段效率管理的主线。 • 每个方面存在X1……Xn等N个影响因素,N个因素中依据二八原则需筛选出关键少数做改善。要想
例:
负荷率用 率
换型时间 修机时间
责任人
改善计划
.............................
生产性
线体平衡率 待料时间 首件确认
............................. .............................
不良率
作业问题(Man) 工艺问题(Method) 物料问题(Materials)
三、实施步骤
步骤四 Improve(改善、效果确认)
(1).每周IE发送上周效率分析报告,报告内容包括: ①.上周效率情况,及上升或者下降原因,并要求相关部门给出对策和完成日期; ②.异常工时分析报告,报告包括各部门问题点对效率影响的比重,各部门TOP项问题,并要求相关部门给出对策和完成日期; ③.不良日报TOP项通报,并要求工艺给出对策; ④.上周对策完成情况,并将疑难问题反馈给相关部门领导,要求其给出有效对策及完成时间; ⑤.专项改善项目进度及开展过程遇到的问题,要求项目负责人给出对策; ⑥.其他改善项目进度及开展过程遇到的问题,要求项目负责人给出对策;
(2).相关责任部门责任人在规定日期内回复对策给IE,IE按计划完成日期确认相关部门问题点关闭情况,并予以通报。
制作:张照明
审核:
目录
1 项目概述
2
组织架构
3
实施步骤
4
项目总结
一、项目概述
1.生产效率的是一个综合性指标,它包括时间的可用性、有效时间的利用率和良品率三个方面,这是 工厂运营生产阶段效率管理的主线。 • 每个方面存在X1……Xn等N个影响因素,N个因素中依据二八原则需筛选出关键少数做改善。要想
例:
负荷率用 率
换型时间 修机时间
责任人
改善计划
.............................
生产性
线体平衡率 待料时间 首件确认
............................. .............................
不良率
作业问题(Man) 工艺问题(Method) 物料问题(Materials)
三、实施步骤
步骤四 Improve(改善、效果确认)
(1).每周IE发送上周效率分析报告,报告内容包括: ①.上周效率情况,及上升或者下降原因,并要求相关部门给出对策和完成日期; ②.异常工时分析报告,报告包括各部门问题点对效率影响的比重,各部门TOP项问题,并要求相关部门给出对策和完成日期; ③.不良日报TOP项通报,并要求工艺给出对策; ④.上周对策完成情况,并将疑难问题反馈给相关部门领导,要求其给出有效对策及完成时间; ⑤.专项改善项目进度及开展过程遇到的问题,要求项目负责人给出对策; ⑥.其他改善项目进度及开展过程遇到的问题,要求项目负责人给出对策;
(2).相关责任部门责任人在规定日期内回复对策给IE,IE按计划完成日期确认相关部门问题点关闭情况,并予以通报。
生产效率提升的五大改善PPT32页
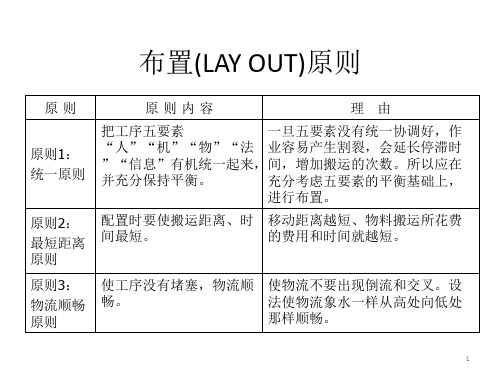
混
适合于数量多、重复的流水生产线
合
搬运距离短。
式 布
流程式 以物流为中心 布置
工序间中途中断、停工待料少。 生产效率高。 难以适应产品的变化。
置
受流水线中断的影响大。
固定式 以产品为中心 布置
适应于钢架、钣金、大型机械组装: (必须有组装和装卸设备) 具备灵活性,容易适应变化。 把产品固定,作业人员移动。 对产品的爱护(质量意识)意识提高。 改进作业方法等的余地很大。
12
搬运活性系数
13
改善搬运方式的着眼点
1、整理整顿。良好的习惯是成功的保证。 2、注意操作环节。搬运不仅是搬运,有时更是装卸。 3、重视放置方法。无数次“提”与“放”,是否值得
关注?
4、减少不合理的搬运。搬运空气和空载现象。 5、重视搬运的连接点。问题的暴露点。
14
有效搬运的原则
1、使货物便于移动。 2、自动化。 3、消除待料停工和空搬运。 4、缩短移动通路距离,并使之简化。 5、一般性原则
传统
优化
1
2
3
4
5
平面分析
将生产线的平面布局按实际比例画成图纸,对物流实施记录, 目的在于消除流程路线的起伏所导致的浪费。
线路前后起伏
间隙
6
正面分析
•
将生产线的正面布局按实际比例画成图纸,对物流实施记录,
目的在于消除流程路线的起伏所导致的浪费。
线路前后起伏
间隙
7
改进的手法
1、作业单位相关表
符号
外部准备
• 必须在机器停机状态下进行 的工作
(如:放置或拆卸设备)
• 可在机器运行或启动状态下进 行的工作
(如:第一个产品下线检查、 加料、安装或回装设备)
精益持续改善PPT课件
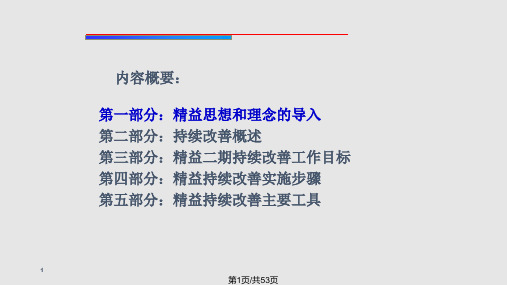
27
第27页/共53页
第四部分:持续改善活动实施步骤
1、实施步骤 步骤三:应对收集到的数据进行深入分析,以 便能弄清事情的真正背景及原因。 步骤四:在分析的基础上研究对策。 步骤五:导入、执行对策。
28
第28页/共53页
第四部分:持续改善活动实施步骤
1、实施步骤 步骤六:观察并记录采用对策后的影响。 步骤七:修改或重新制订标准,以避免类似问 题的再次发生。 步骤八:检查从步骤1到7的整个过程,据以引 入下一步的行动。
■工作场所人员改善意识的提高 ■改善氛围的营造 ■员工发现问题、解决问题能力的提高
各部门
持续
■标准作业表的优化及完善 ■现场各种浪费的杜绝 ■员工作业目标设定及执行 ■现场作业工具的改善,劳动生产率的提高 ■作业流程改善 ■现场安全作业标准制定
■“5S”及目视化推行
■物料出入库管理办法完善
■仓库呆废料的处置方法的制定
(2)能力开发和活用 养成经常考虑问题的习惯 加强发现问题的意识 提高工作的主人翁责任感 提高成本意识
第15页/共53页
16
第二部分:持续改善概述
7、“改善提案” 作用和意义
(3)提高人与人之间关系 加强部下与上司交流 加强横向交流 提高工作场所内的协作关系 (4)提高参与经营的意识 加强公司与个人的一体感 提高工作热情
26
第26页/共53页
第四部分:持续改善活动实施步骤
1、实施步骤
步骤一:选择工作任务
首先要阐明选择这个项目或工作任务的理由。这些 任务通常是根据企业的发展目标确定的,但有时企业的 现状也会影响这种选择—依据其重要性、紧迫性或经济 性。
步骤二:弄清当前的情况
在项目开始前必须要弄清项目当前情况的本质,并 予以分析。这需要人们去现场了解情况,运用KAIZEN 的“三现”原则,收集数据。
第27页/共53页
第四部分:持续改善活动实施步骤
1、实施步骤 步骤三:应对收集到的数据进行深入分析,以 便能弄清事情的真正背景及原因。 步骤四:在分析的基础上研究对策。 步骤五:导入、执行对策。
28
第28页/共53页
第四部分:持续改善活动实施步骤
1、实施步骤 步骤六:观察并记录采用对策后的影响。 步骤七:修改或重新制订标准,以避免类似问 题的再次发生。 步骤八:检查从步骤1到7的整个过程,据以引 入下一步的行动。
■工作场所人员改善意识的提高 ■改善氛围的营造 ■员工发现问题、解决问题能力的提高
各部门
持续
■标准作业表的优化及完善 ■现场各种浪费的杜绝 ■员工作业目标设定及执行 ■现场作业工具的改善,劳动生产率的提高 ■作业流程改善 ■现场安全作业标准制定
■“5S”及目视化推行
■物料出入库管理办法完善
■仓库呆废料的处置方法的制定
(2)能力开发和活用 养成经常考虑问题的习惯 加强发现问题的意识 提高工作的主人翁责任感 提高成本意识
第15页/共53页
16
第二部分:持续改善概述
7、“改善提案” 作用和意义
(3)提高人与人之间关系 加强部下与上司交流 加强横向交流 提高工作场所内的协作关系 (4)提高参与经营的意识 加强公司与个人的一体感 提高工作热情
26
第26页/共53页
第四部分:持续改善活动实施步骤
1、实施步骤
步骤一:选择工作任务
首先要阐明选择这个项目或工作任务的理由。这些 任务通常是根据企业的发展目标确定的,但有时企业的 现状也会影响这种选择—依据其重要性、紧迫性或经济 性。
步骤二:弄清当前的情况
在项目开始前必须要弄清项目当前情况的本质,并 予以分析。这需要人们去现场了解情况,运用KAIZEN 的“三现”原则,收集数据。
精益改善项目案例生产效率提升PPT课件(42页)(2024版)

项目范围: 项目通过推进精益生产,减少生产制造全流程内的浪费,有效减少作业人员、提升产量,缩短交付周期,在降低制造成本的同时,快速满足客户的需求。以工厂为试点,三地工厂同步实施,在制冷集团各事业部推广。
变量
名称
CTQ
单位
Y
生产效率提升
月人均产出
套/人
Y1
生产组织模式变革
订单交付周期
天
Y2
制造技术提升
大线组长 柔性线组长 柔性线巡检
减少1人 两两合并 两两合并
15
Y2改善(节选)—管理优化减员
改善效果:计划减员101人,实际减员101人,计划达成率100%。
部门(分厂)
总一
总二
总三
部装
注塑
财务
品质
职能部
目标(人)
7
2
6
3
31
14
18
20
推进 方向
Y1的改善 摘录1
改善项目名称:订单下达规范性
改善类别
技术
管理
设备
材料
费用
其它
√
改善前
改善后
问题点
改善方案
1、针对计划下达准确率、计划完成及时性的责任划分不明晰,产销责权关系不清,存在管理真空; 2、相关流程时间节点不规范、不合理,且操作随意性较强; 3、产销信息传递不畅。经常出现生产计划与销售计划间的信息不对称;
1、以文件形式彻底固化尾数清理流程、明确激励考核要求; 2、计划管理建立专人监控机制,按周、月通报 3、物资管理监督车间生产过程物料损耗,并每日统计滚动输出; 4、供应商建立安全库存,保证欠产物料补缺的及时性,减少超期作业任务产生; 5、车间物料管护规范每周稽查不少于2次。
作业效率提升方案-作业效率提升方案51页PPT

例如,某一单元观测时间为0.8min, 评比为110%,宽放为5%,则正 常时间为0.88min,标准时间为0.924min
作业效率分析—降低投入标准
标准• 时宽间放的的形定义成
1.操作过程中,作业人员的疲劳,需休息,以资恢复. 2.满足操作人员的个人需要. 3.领班之作业指示或外人干扰. 4.工作准备与清扫. 5.操作时之机器干扰. 6.材料不良 以上等因个人私务,疲劳或暂停工作所给予的时间称之. 宽放的种类: 1.生理宽放:因操作人员领生理需要或为操作人员工作书市所给予的时间;如
工时记录表
行动措施
4.按制程给出宽放表 5.汇总所有工位时间,完成标工资料初表
各个工位宽放系数表 标准人力工时资料表
6.缺人转嫁项目清单和责任单位
转嫁责任明细责任单位表,含内部工位间转嫁
7.设计生产效率日报表
生产日效率报表
8.试统计日生产效率
生产日效率报表数据
工作分工时间表
项目行动计划
D 措施执行 定期项目进度内部交流
熟练程度
精确区分、量化损 失工时,及时把握 作业效率与生产效 率起伏原因
不同班组的各种停线, 转化为责任工时,统一 做80/20分析及则责任 考核
生产效率分析
作业效率分析--提升实际产出
按工时责任单位层别分析改善 按工时损失原因层别分析改善
精确区分、量化损 失工时,及时把握 作业效率与生产效
率起伏原因
作业效率体系 工时组成:
作业工时
总出勤工时(投入工时) (投入人员*作业时间)
直接工时 直接人员*作业时间
投入工时
实动工时
(直接工时-无作业工时)
效率 损失
标准 生产 量 工时
纯作业工时
作业效率分析—降低投入标准
标准• 时宽间放的的形定义成
1.操作过程中,作业人员的疲劳,需休息,以资恢复. 2.满足操作人员的个人需要. 3.领班之作业指示或外人干扰. 4.工作准备与清扫. 5.操作时之机器干扰. 6.材料不良 以上等因个人私务,疲劳或暂停工作所给予的时间称之. 宽放的种类: 1.生理宽放:因操作人员领生理需要或为操作人员工作书市所给予的时间;如
工时记录表
行动措施
4.按制程给出宽放表 5.汇总所有工位时间,完成标工资料初表
各个工位宽放系数表 标准人力工时资料表
6.缺人转嫁项目清单和责任单位
转嫁责任明细责任单位表,含内部工位间转嫁
7.设计生产效率日报表
生产日效率报表
8.试统计日生产效率
生产日效率报表数据
工作分工时间表
项目行动计划
D 措施执行 定期项目进度内部交流
熟练程度
精确区分、量化损 失工时,及时把握 作业效率与生产效 率起伏原因
不同班组的各种停线, 转化为责任工时,统一 做80/20分析及则责任 考核
生产效率分析
作业效率分析--提升实际产出
按工时责任单位层别分析改善 按工时损失原因层别分析改善
精确区分、量化损 失工时,及时把握 作业效率与生产效
率起伏原因
作业效率体系 工时组成:
作业工时
总出勤工时(投入工时) (投入人员*作业时间)
直接工时 直接人员*作业时间
投入工时
实动工时
(直接工时-无作业工时)
效率 损失
标准 生产 量 工时
纯作业工时
生产效率提升与效益优化计划
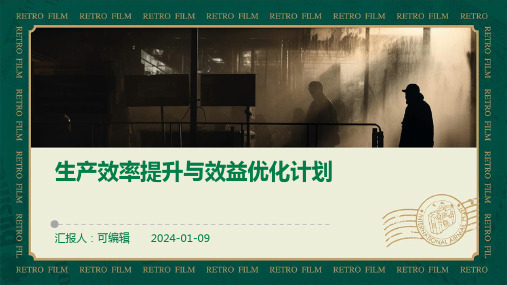
标准化作业
制定标准作业程序,确保生产过程的一致性和稳 定性,提高产品质量。
设备升级与技术改造
引入自动化设备
采用先进的自动化设备,提高生产线的自动化程度,降低人工成 本。
技术改造与创新
对现有设备进行技术改造和创新,提高设备性能和生产效率。
维护与保养
建立设备维护和保养制度,确保设备正常运行,延长设备使用寿命 。
风险应对
预测可能出现的风险和问题,制定应对措施,确保实施计划的顺 利进行。
05 预期效果与收益预测
生产效率提升预测
生产流程优化
通过改进生产流程,减少生产环节和操作步骤,提高生产效率。
自动化设备引入
引入先进的自动化设备,降低人工操作比例,提高生产速度和准确 性。
员工培训与激励
加强员工培训和激励措施,提高员工技能和工作积极性,促进生产 效率提升。
应对措施
加强员工培训和技能提升,提高员工工作效率。同时,建 立完善的绩效考核机制,激励员工提高工作效率。
市场风险与应对措施
市场变化
市场需求的变化可能导致产能过剩或 不足。
竞争加剧
竞争对手的策略变化可能导致市场份 额减少。
应对措施
密切关注市场动态,及时调整生产计 划,保持合理的产能利用率。同时, 加强市场营销和客户关系管理,提高 产品知名度和市场占有率。
成本降低预测
1 2
原材料成本控制
通过集中采购、优化供应商选择等措施,降低原 材料成本。
能源消耗降低
优化设备运行和生产工艺,降低能源消耗,节约 能源成本。
3
减少浪费与损耗
通过改进生产流程和操作方法,减少生产过程中 的浪费与损耗,降低成本。
收益增长预测
产品品质提升
制定标准作业程序,确保生产过程的一致性和稳 定性,提高产品质量。
设备升级与技术改造
引入自动化设备
采用先进的自动化设备,提高生产线的自动化程度,降低人工成 本。
技术改造与创新
对现有设备进行技术改造和创新,提高设备性能和生产效率。
维护与保养
建立设备维护和保养制度,确保设备正常运行,延长设备使用寿命 。
风险应对
预测可能出现的风险和问题,制定应对措施,确保实施计划的顺 利进行。
05 预期效果与收益预测
生产效率提升预测
生产流程优化
通过改进生产流程,减少生产环节和操作步骤,提高生产效率。
自动化设备引入
引入先进的自动化设备,降低人工操作比例,提高生产速度和准确 性。
员工培训与激励
加强员工培训和激励措施,提高员工技能和工作积极性,促进生产 效率提升。
应对措施
加强员工培训和技能提升,提高员工工作效率。同时,建 立完善的绩效考核机制,激励员工提高工作效率。
市场风险与应对措施
市场变化
市场需求的变化可能导致产能过剩或 不足。
竞争加剧
竞争对手的策略变化可能导致市场份 额减少。
应对措施
密切关注市场动态,及时调整生产计 划,保持合理的产能利用率。同时, 加强市场营销和客户关系管理,提高 产品知名度和市场占有率。
成本降低预测
1 2
原材料成本控制
通过集中采购、优化供应商选择等措施,降低原 材料成本。
能源消耗降低
优化设备运行和生产工艺,降低能源消耗,节约 能源成本。
3
减少浪费与损耗
通过改进生产流程和操作方法,减少生产过程中 的浪费与损耗,降低成本。
收益增长预测
产品品质提升
生产车间改善提效方案,生产现场改善的一些措施与细节
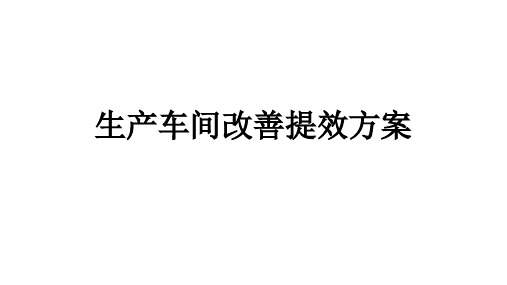
• 管理看板,可分为静态的和动态的管理看板。静态的看板主要是 传达组织长期的管理理念,动态的看板是管理者随时要把握的管 理信息,更能反映一个工厂的管理水平和能力。
• 6、工具设备状态 • 在好的工厂里,设备整洁而且保养良好,设备相关信息一目了然
并且即时更新。 • 在一个铸造厂的机加工车间,虽然各种车床都不是很先进,甚至
否有异味,噪音是否太大,车间是否整洁,因为这些也会直接影 响工人的工作状态,进而影响生产效率和产品质量。
• 2、空间利用与布局
• 例如同一批零件从A区搬到B区加工完后再搬回A区做后道加工, 然后搬到C区处理,最后还要再搬回B区,搬运的浪费简直达到极 致。
• 原则上当天使用的生产物料应沿生产线存放,而不是在几个库存 区分隔存储,工具和工装摆放应尽量靠近机器。
一、现场管理篇
• 质优价廉、适销对路、按期交货的产品是生产 现场中制造出来的,要靠现场管理来保证.从这 种意义来讲,现场管理水平的高低,是决定企业 优势和实力的基础.
1.现场管理的含义,现场管理的 对象和范围
• 目标
企业经营目标
• 现场管理
一线干部 科学管理制度、标准和方法
计划、组织、协调、控制和激励
历史很长,但都在良好的状态下运转。 • 每台机器的侧面都醒目地贴着一张卡片,上面记录着该设备的型
号、采购日期、价格、供应商、维修记录、保养记录等等。 • 日常点检表也记录得很完整,有的点检表上清晰地记录着操作工
发现的隐患,以及设备部门的签字及处理方案。
• 此外,一线工人和参与产品开发和生产的人员最清楚新设备的优 缺点,也最了解生产线的实际需求。在很多工厂设备采购都是由 高层或设备部决定,很少征求一线人员意见,这也会导致后续使 用中大量问题产生。
• 6、工具设备状态 • 在好的工厂里,设备整洁而且保养良好,设备相关信息一目了然
并且即时更新。 • 在一个铸造厂的机加工车间,虽然各种车床都不是很先进,甚至
否有异味,噪音是否太大,车间是否整洁,因为这些也会直接影 响工人的工作状态,进而影响生产效率和产品质量。
• 2、空间利用与布局
• 例如同一批零件从A区搬到B区加工完后再搬回A区做后道加工, 然后搬到C区处理,最后还要再搬回B区,搬运的浪费简直达到极 致。
• 原则上当天使用的生产物料应沿生产线存放,而不是在几个库存 区分隔存储,工具和工装摆放应尽量靠近机器。
一、现场管理篇
• 质优价廉、适销对路、按期交货的产品是生产 现场中制造出来的,要靠现场管理来保证.从这 种意义来讲,现场管理水平的高低,是决定企业 优势和实力的基础.
1.现场管理的含义,现场管理的 对象和范围
• 目标
企业经营目标
• 现场管理
一线干部 科学管理制度、标准和方法
计划、组织、协调、控制和激励
历史很长,但都在良好的状态下运转。 • 每台机器的侧面都醒目地贴着一张卡片,上面记录着该设备的型
号、采购日期、价格、供应商、维修记录、保养记录等等。 • 日常点检表也记录得很完整,有的点检表上清晰地记录着操作工
发现的隐患,以及设备部门的签字及处理方案。
• 此外,一线工人和参与产品开发和生产的人员最清楚新设备的优 缺点,也最了解生产线的实际需求。在很多工厂设备采购都是由 高层或设备部决定,很少征求一线人员意见,这也会导致后续使 用中大量问题产生。
生产效率提升的五大改善.pptx
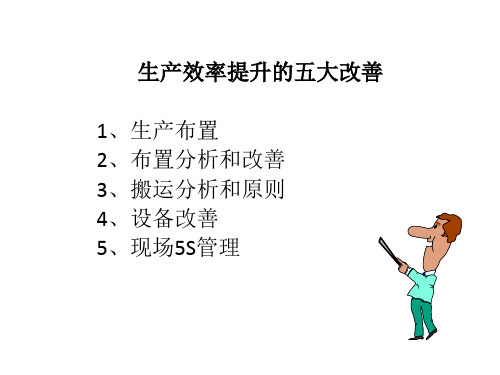
符号
密切程度
A
U 非常重要
B
V 重要
C
X 一般
D
E
Y 不重要
F
Z 完全没有必要
G
根据密切程度,标准UVXYZ,然后看其中的数量来决定布置 方式。
根据以下工艺做LAYOUT
B
A
B
D
E
G
I
123 456
C
F
H
D
789
物流与作业单位相关图
A、物流的数量 B、物流的重量 C、物流的运输频繁程度
搬运——企业理所当然的浪费
混
适合于数量多、重复布
流程式 以物流为中心 布置
工序间中途中断、停工待料少。 生产效率高。 难以适应产品的变化。
置
受流水线中断的影响大。
固定式 以产品为中心 布置
适应于钢架、钣金、大型机械组装: (必须有组装和装卸设备) 具备灵活性,容易适应变化。 把产品固定,作业人员移动。 对产品的爱护(质量意识)意识提高。 改进作业方法等的余地很大。
设备管理的要点
1.可动率和稼动率 2.追求100%的可动率 3.自主保养---谁使用,谁保养
快速切换的8大步骤
STEP 1 STEP 2 STEP 3 STEP 4 STEP 5 STEP 6 STEP 7 STEP 8
现场观察并写下换型步骤 记录时间和各种浪费 区分内部及外部活动 分析所有换型动作
配置时要使搬运距离、时间 移动距离越短、物料搬运所花费的费
最短。
用和时间就越短。
使工序没有堵塞,物流顺畅。 使物流不要出现倒流和交叉。设法使 物流象水一样从高处向低处那样顺畅。
原则
原则4: 利用立体 空间原则
- 1、下载文档前请自行甄别文档内容的完整性,平台不提供额外的编辑、内容补充、找答案等附加服务。
- 2、"仅部分预览"的文档,不可在线预览部分如存在完整性等问题,可反馈申请退款(可完整预览的文档不适用该条件!)。
- 3、如文档侵犯您的权益,请联系客服反馈,我们会尽快为您处理(人工客服工作时间:9:00-18:30)。
演示课件
现场管理的“单一最好”原则
一处保管 一日处理 一个资料夹 一小时会议 一张纸 一分钟电话 一件工具 一个单元 一个流 一天班长
户口管理 今日事,今日毕 资料夹一册化 一事一议,半小时更好 报告、表格一张篇幅完全表达 长话短说,不拖泥带水 多样工具简化成一件 在一个小组或一组设备内完工 生产过程“一个流” 员工多能化培养
摸 有无异常的发热或抖动、振动等现象
查
监测,关键、特殊工序受控情况 油管阀门等有无跑、冒、滴、漏数据
看
有无松动、晃动、移动、错位、开裂、缺损现象 设备运行参数是否符合规定要求
闻
有无泄漏或其他引起的焦味、异常气味
演示课件
现场管理的 “A B C” 法
把现场所看到的东西或感想用笔记下来 把自己希望改进或与要求不符的部分分为 A B C 三级 A 是明天马上要改善的 B 是一周后需要改善的 C 是一个月后计划改善的 策划具体改善措施 检查改善情况并予以奖励
可视化管理
员工提案
QC小组
现场管理之屋
演示课件
目前的现场
半成品堆积如山,生产线却停工待料 成品积压,客户却天天催货 放在旁边的是不需要做的,需要做的却不在旁边 一边交期紧急,一边返工返修不断 很容易买到的螺栓、螺母却保留一、二年的用量 整批产品常常因为一二个零件而搁浅耽误 有人没事做,有事没人做
演示课件
最少资金 最少人力 5M 最少设备 最少材料 最佳方法
演示课件
P 最佳品种 Q 最优质量 C 最低成本 D 准时交货 S 安全环保 M 良好情绪
为什么要加强生产 现场管理?
演示课件
80%的工作在现场 80%的人员在现场 80%的问题在现场 80%的事故在现场
演示课件
现场 现场 改善 管理 什么? 什么?
演示课件
_____车间1-5月管理目标改善计划表
序
计划改善项目
1 交货期 2 生产周期 3 改机时间 4 停机时间 5 操作人员数 6 在制品数量 7 零部件(半成品)数量 8 库存品总额 9 搬运距离 10 不合格品发生率 11 一次交验合格率 12 返工返修品
1月
2月
3月
4月
5月
单 位
目标 计 -% 划
现场改善与生产效率提升
Andy
苏州工业园区新凯精密五金有限公司
演示课件
生产管理的铁三角
D
交
成
期 安全 本
Q
C
质量
用最低的成本 符合要求的质量 达成规定的交期
演示课件
企业管理面临的共同难题
内部 救火式生产
质量不稳定 浪费严重
人员流动大
演示课件
外部 小批量 多品种 低价格 快交货
以最少的投入来获取最大的产出
%
+50 10
%
50 10
20
35
50
60
20
30
40
50
20
30
40
50
演示课件
在当今的工业时代,用“农业头脑”办事 肯定是不行的,但也不是一步跨越到“电子计 算机头脑”就行得通。在“农业头脑”和“电 子计算机头脑”之间应该还应该有一个“工业 头脑”的时代。
演示课件
IE工业工程简介
工业工程(IE)是一门应用科学,它将传统的工程 技术融合于现代的科学管理技巧之中 ,弥补原有管理 及工程技术之脱节。IE是藉着设计、改善或设定人、料 机的工作系统,以求得到更高生产力的专门技术。IE要 求以工程技术为基础,配合科学管理的技巧来发现问题、 解决问题、预防问题。
演示课件
生产现场管理普遍存在问题
生产无计划 质量无标准 作业无方法 堆放无区域 物品无标识 消耗无定额 过程无记录
演示课件
现场管理的五大要素(4M1E)
人
思想意识 配合度 能力 个体差异
设备
设备功能 精确度 设备能力 故障预警
材料
及时 适宜 合格
方法
方法合理 过程受控 标准化
环境
温度 湿度 灰尘 污染
现阶段的IE(工业工程)的主要工作范围大致是: 价值分析、动作分析、工程分析、时间分析、平面布 置、搬运设计、可视化管理、员工多能化、快速换模等
演示课件
工业工程可以让生活与工作井然有序
北京市某机构的办事人潮不断,要办事有排不完的队;领表要排队、 申办要排队、照相要排队、缴费要排队、领证要排队。由于当时设计并 未考虑到现在的人潮,而现在的需求已经远超过几年前的情况,所以排 队的空间、设施以及规则都已经不适用。因此几乎每天都发生这样的情 况:让有礼貌的市民排得心烦意乱,让急着办事的市民直跺脚,让不守 规矩的人拼命钻空子;甚至因排队起的争吵与冲突此起彼落。
演示课件
四大目标 Q 质量 C 成本 D 交期 S 安全
现场管理要求
现场管理方法
一消:消除不增值活动 二化:标准化、可视化 三不:现场质量“三不” 三现:现场、现实、现物
四M:4M1E
五S:5S管理
演示课件
利润
Q
质 量
C
成 本
D
交 期
S
安 全
生产
设备
物料
人、机、料、法、环
作业标准化
现场5S 消除现场浪费
实计 绩划
实计 绩划
实计 绩划
实计 绩划
实 绩
加权 平均
天
50 10
天
30 6
小时 75 15
小时 50 10
个
5
千件 25 5
千件 20 4
万元 10 2
米/件 30 6
20
30
40
50
12
18
24
30
30
45
60
75
20
30
40
50
2
5
10
15
20
25
8
12
16
20
4
6
8
10
12
18
ቤተ መጻሕፍቲ ባይዱ24
30
%
60 10
现场管理的五项要求
一、当问题发生时,要先去现场; 二、检查现物(有关的物品); 三、当场采取暂行处置措施; 四、发掘真正原因并将其排除; 五、标准化以防止再发生。
演示课件
案例分析
某班组自动车床经常发生故障,维修人员 只能通过维修和更换备件解决故障。目前该设 备故障平均约每半年发生一次,主要原因是主 轴轴承发生故障,一套轴承的备件价格为3000 元,每年更换备件费用达6000元。如何应用 “五问”活动对主轴轴承故障的原因进行分析。
演示课件
现场管理的“三五”要求
操作“五按”: 按图纸、按标准、按程序、按时间、按操作指令 工作“五干”: 干什么、怎么干、什么时间干、按什么方法干、 干到什么程度
结果“五查”: 由谁来检查、什么时间检查、检查什么项目、检 查的标准是什么、检查的结果由谁来落实
演示课件
现场管理的“五字检查”法
听 听设备运转过程中是否有异常声音
演示课件
管理的根本 在于不断改善
改善
维持
改善的能力 是评价管理者的重要基 准
演示课件
改善的十条基本原则
1、“存在的都是不合理的” 2、强调理由是不思进取的表现 3、立即改进,及时比正确更重要 4、反复追问为什么,总能找到问题根源 5、许多问题的解决,就在于否定不可能 6、更应该重视的是不花大钱的改善 7、不要追求完美,完美都是从不完美开始的 8、最清楚改善的是处于第一线的操作人员 9、只要是改善,最小的事也值得去做 10、改善永无止境,没有最好,只有更好