型钢线材常见缺陷及原因
热轧型钢常见外观缺陷与控制方法.docx
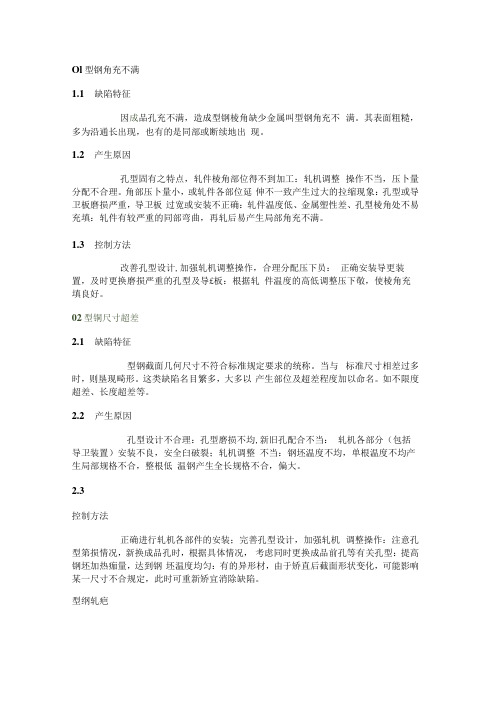
Ol型钢角充不满1.1缺陷特征因成品孔充不满,造成型钢棱角缺少金属叫型钢角充不满。
其表面粗糙,多为沿通长出现,也有的是同部或断续地出现。
1.2产生原因孔型固有之特点,轧件棱角部位得不到加工:轧机调整操作不当,压卜量分配不合理。
角部压卜量小,或轧件各部位延伸不一致产生过大的拉缩现象:孔型或导卫板磨损严重,导卫板过宽或安装不正确:轧件温度低、金属塑性差、孔型棱角处不易充填:轧件有较严重的同部弯曲,再轧后易产生局部角充不满。
1.3控制方法改善孔型设计,加强轧机调整操作,合理分配压下员:正确安装导更装置,及时更换磨损严重的孔型及导£板:根据轧件温度的高低调整压下敬,使棱角充填良好。
02型铜尺寸超差2.1缺陷特征型钢截面几何尺寸不符合标准规定要求的统称。
当与标准尺寸相差过多时,则垦现畸形。
这类缺陷名目繁多,大多以产生部位及超差程度加以命名。
如不限度超差、长度超差等。
2.2产生原因孔型设计不合理:孔型磨损不均,新旧孔配合不当:轧机各部分(包括导卫装置)安装不良,安全臼破裂;轧机调整不当:钢坯温度不均,单根温度不均产生局部规格不合,整根低温钢产生全长规格不合,偏大。
2.3控制方法正确进行轧机各部件的安装;完善孔型设计,加强轧机调整操作:注意孔型第损情况,新换成品孔时,根据具体情况,考虑同时更换成品前孔等有关孔型:提高钢坯加热痂量,达到钢坯温度均匀:有的异形材,由于矫直后截面形状变化,可能影响某一尺寸不合规定,此时可重新矫宜消除缺陷。
型纲轧疤3.1缺陷特征由于轧制中造成的粘接在型钢表面的金属块状物。
其外形类似结疤,与结疤不同的主要是,轧疤的形状及其在型钢表面上的分布有一定规律性。
缺陷下面常无非金屈氧化物夹杂。
3.2产生原因粗轧机孔型磨损严重,在型钢的固定面上产生断续分布的活轧疤:金属外物(或轧件本身被导T!装置刮下的金属)压入轧件表面形成轧疤:由于在成品孔前某道轧件表面产生周期性凸块或凹坑,再也后形成周期性轧疤,具体原因有:孔槽刻痕不良:轧槽有砂眼或掉肉:轧槽被“黑头”轧件撞伤或粘有结疤等凸起物:轧件在孔型内打滑,造成金属堆积在变形区表面上,再轧后形成轧疤:轧件局部被困盘、短道、翻钢机等机械设备卡(刮)伤或刮弯,再轧后也会形成轧疤。
(整理)钢铁材料常见缺陷图谱及产生原因
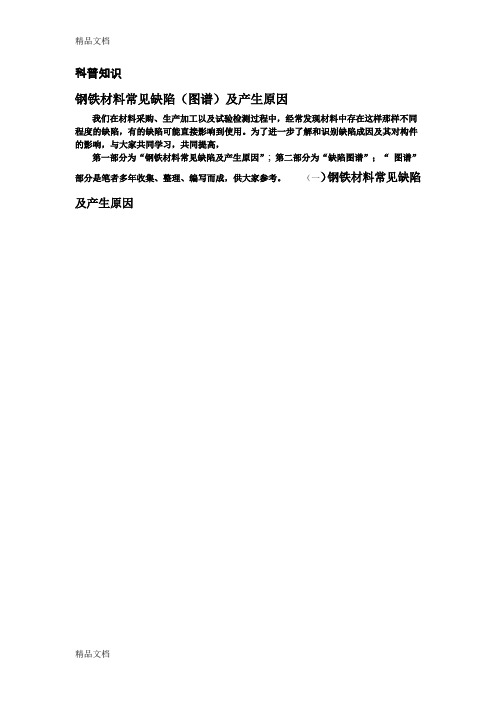
科普知识
钢铁材料常见缺陷(图谱)及产生原因
我们在材料采购、生产加工以及试验检测过程中,经常发现材料中存在这样那样不同程度的缺陷,有的缺陷可能直接影响到使用。
为了进一步了解和识别缺陷成因及其对构件的影响,与大家共同学习,共同提高,
第一部分为“钢铁材料常见缺陷及产生原因”; 第二部分为“缺陷图谱”;“图谱”部分是笔者多年收集、整理、编写而成,供大家参考。
(一)钢铁材料常见缺陷及产生原因
型钢常见缺陷
重轨常见缺陷
线材常见缺陷
中厚板常见缺陷
热轧板(卷)常见缺陷
冷轧板(卷)常见缺陷
镀锌板(卷)常见缺陷
镀锡板(卷)常见缺陷
彩涂板(卷)常见缺陷
硅钢产品常见缺陷
二:缺陷图谱
图1-8为弯曲试验缺陷,图9-21为拉伸断口
图1:刮伤图2:角钢中夹渣分层图3:角钢夹渣分层图4:夹杂分层
图5:气泡起层图6:三分层缺陷
图7:气泡形成三分层图8:角钢上的缩管分层
图9:结晶状断口和星状断口图10:全杯状断口和半杯状断口
图11:菊花状断口和燕尾断口图12:燕尾断口和斜断口
图13:中心增碳和心部增碳图14:心部增碳
图15:表面增碳图16:结晶胎性断口和残余增碳
图17:结晶胎性断口和残余缩孔断口图18:残余缩孔断口和残余缩孔
精品文档
精品文档
图19:缩孔断口和缩孔横截面劈开成二半 图20:缩孔断口
图21:白点断口和劈开断口。
钢铁产品常见缺陷

型钢常见缺陷缺陷名称缺陷特征产生原因结疤型钢表面上的疤状金属薄块。
其大小、深浅不等,外形极不规则,常呈指甲状、鱼鳞状、块状、舌头状无规律地分布在钢材表面上,结疤下常有非金属夹杂物。
由于钢坯未清理,使原有的结疤轧后仍残留在钢材表面上。
表面夹杂暴露在钢材表面上的非金属物质称为表面夹杂,一? 般呈点状、块状和条状分布,其颜色有暗红、淡黄、灰白等,机械的粘结在型钢表面上,夹杂脱落后出现一定深度的凹坑,其大小、形状无一定规律。
???(1)钢坯带来的表面非金属夹杂物。
(2)在加热或轧制过程中,偶然有非金属夹杂韧(如加热炉的耐火材料及炉渣等),炉附在钢坯表面上,轧制时被压入钢材,冷却经矫直后部分脱落分层此缺陷在型钢的锯切断面上呈黑线或黑带状,严重的分离成两层或多层,分层处伴随有夹杂物。
?(1)主要是由于镇静钢的缩孔或沸腾钢的气囊未切净。
(2)钢坯的皮下气泡,严重疏松,在轧制时未焊台,严重的夹杂物也会造成分层。
(3)钢坯的化学成份偏析严重,当轧制较薄规格时,也可能形成分层。
气泡(凸包)型钢表面呈现的一种无规律分布的园形凸起称为凸包,凸起部分的外缘比较园滑,凸包破裂后成鸡爪形裂口或舌形结疤,叫气泡。
多产生于型钢的角部及腿尖。
钢坯有皮下气泡,轧制时未焊合。
裂纹顺轧制方向出现在型钢表面上的线形开裂,一般呈直线形,有时呈“Y”形,多为通长出现,有时局部出现。
(1)钢坯有裂缝或皮下气泡、非金属夹杂物,经轧制破裂暴露。
(2)加热温度不均匀,温度过低,轧件在轧制时各部延伸与宽展不一致。
(3)加热速度过快、炉尾温度过高或轧制后冷却不当,易形成裂纹,此种情况多发生在高碳钢和低合金钢上。
尺寸超差(尺寸不合、规格不合)尺寸超差是指型钢截面几何尺寸不符标准规定要求的统称。
这类缺陷名目繁多,大部以产生部位以及其超差程度加以命名。
例工、槽、角钢的腿长、腿短、腰厚、腰薄及一腿长,一腿短。
(1)对工字钢成品孔腿长往往表现在开口腿上,主要由于腰部压下量不够,角钢和槽钢成品孔压下量的大小,直接影响腿长和腿短。
在工厂干了17年,总结了17种型钢表面缺陷,收藏吧!
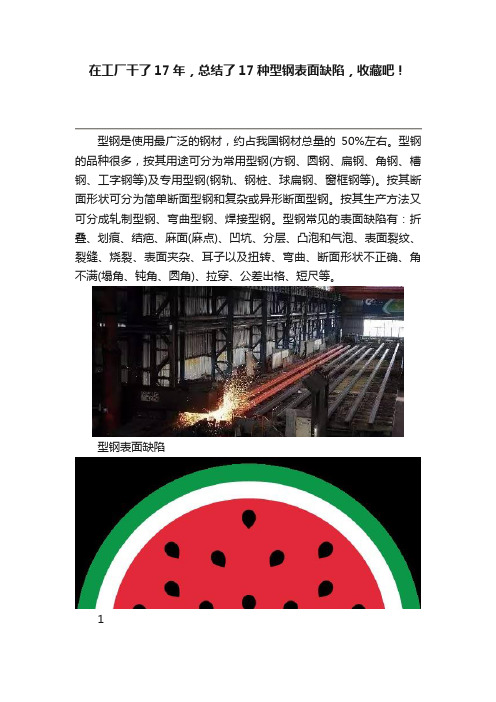
在工厂干了17年,总结了17种型钢表面缺陷,收藏吧!型钢是使用最广泛的钢材,约占我国钢材总量的50%左右。
型钢的品种很多,按其用途可分为常用型钢(方钢、圆钢、扁钢、角钢、槽钢、工字钢等)及专用型钢(钢轨、钢桩、球扁钢、窗框钢等)。
按其断面形状可分为简单断面型钢和复杂或异形断面型钢。
按其生产方法又可分成轧制型钢、弯曲型钢、焊接型钢。
型钢常见的表面缺陷有:折叠、划痕、结疤、麻面(麻点)、凹坑、分层、凸泡和气泡、表面裂纹、裂缝、烧裂、表面夹杂、耳子以及扭转、弯曲、断面形状不正确、角不满(塌角、钝角、圆角)、拉穿、公差出格、短尺等。
型钢表面缺陷1折叠沿钢材长度方向表面有倾斜的近似裂纹的缺陷,称折叠。
通常是由于钢材表面在前一道锻、轧中所产生的突出尖角或耳子,在以后的锻、轧时压入金属本体叠合形成的。
折叠一般呈直线状,亦有的呈锯齿状,分布于钢材的全长,或断续状局部分布,深浅不一,深的可达数十毫米,其周围有比较严重的脱碳现象,一般夹有氧化铁皮。
钢材表面的折叠,可采用机械加工方法进行去除。
型材表面因不再进行机械加工,如果表面存在严重的折叠,就不能使用,因为在使用过程中会由于应力集中造成开裂或疲劳断裂。
2划痕在生产、运输等过程中,钢材表面受到机械性刮伤形成的沟痕,称划痕,也称刮伤或擦伤。
其深度不等,通常可看到沟底,长度自几毫米到几米,连续或断续分布于钢材的全长或局部,多为单条,也有双条和多条的划痕。
划痕会降低钢材的强度,对于薄板还会造成应力集中,在冲压时成为裂纹发生和扩展的中心。
对于耐压容器,严重的划痕可能成为使用过程中发生事故的根源。
3结疤钢材表面呈舌状、指甲状或鱼鳞状的片块,称结疤。
它是钢锭表面被污溅的金属壳皮、凸块,经轧制后在钢材表面上形成的。
与钢材相连牢固的结疤,称生根结疤;与钢材相连不紧或不相连,粘着在表面上的结疤,称为不生根结疤。
不生根结疤容易脱落,脱落后表面形成凹坑。
有些结疤的一端翘起,称翘皮。
4麻面(麻点) 麻点是钢材表面凹凸不平的粗糙面。
轧钢常见缺陷之欧阳德创编
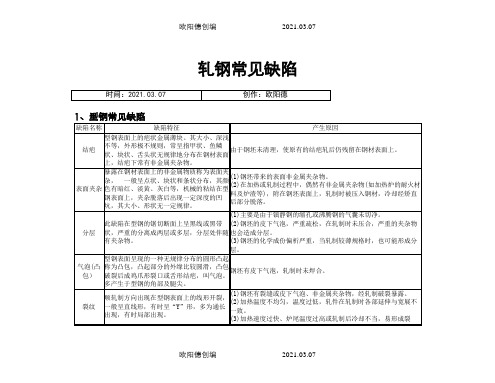
(3)成品孔出口卫板过低,锯齿磨损太老,垫板太低,在辊道运送速度过快时,碰撞档板等都容易产生弯头。
尺寸超差(规格不合)
钢轨断面几何尺寸不符合标准规定,统称尺寸超差。
其中:钢轨头部超过正偏差的叫头大,超过负偏差的叫头小。轨腰厚度超过正偏差的叫腰厚.超过负偏差的叫腰薄。轨底宽度超过正偏差的叫底宽,超过负偏差的叫底小。轨腰高度超过正偏差的叫腹高,超过负偏差的叫腹低。轨的高度超过正偏差的叫轨高,超过负偏差的叫轨低。断面不与其垂直轴线对称的叫不对称(又叫偏称)。
(1)卫板安装不良,使钢轨产生力偶,形成扭转。
(2)轧件温度不均或压下量不均,造成各部延伸不一致。
(3)矫直机调整不当,钢轨受力偶作用。
(4)在冷却台架上翻钢时因温度较高也会出现扭转。
弯曲
钢轨沿垂直或水平方向呈现不平直的现象叫弯曲,一般呈镰刀形或波浪形,仅在端部的弯曲又叫弯头。
(1)由于重轨的头、腰、底面积相差较大,使轧制、冷却等工序操作易产生弯曲。
(2)钢坯的皮下气泡,严重疏松,在轧制时未压合,严重的夹杂物也会造成分层。
(3)钢坯的化学成份偏析严重,当轧制较薄规格时,也可能形成分层。
气泡(凸包)
型钢表面呈现的一种无规律分布的圆形凸起称为凸包,凸起部分的外缘比较圆滑,凸包破裂后成鸡爪形裂口或舌形结疤,叫气泡。多产生于型钢的角部及腿尖。
钢坯有皮下气泡,轧制时未焊合。
(1)钢坯带来的表面非金属夹杂物。
(2)在加热或轧制过程中,偶然有非金属夹杂物(如加热炉的耐火材料及炉渣等),附在钢坯表面上,轧制时被压入钢材,冷却经矫直后部分脱落。
分层
此缺陷在型钢的锯切断面上呈黑线或黑带状,严重的分离成两层或多层,分层处伴随有夹杂物。
轧钢常见缺陷
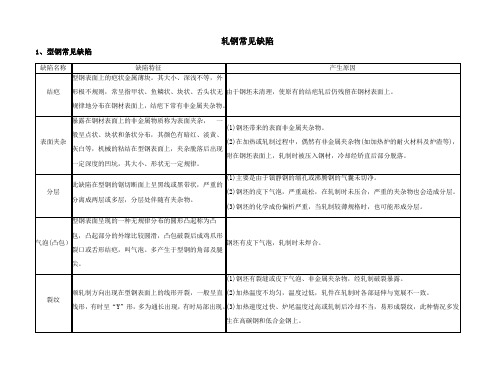
2)腰厚、腰薄产生的主要原因是:如按孔型设计头部压下量为77—=6.7mm;腰部压下量为16一=1.5mm,如果六孔压下量加大l.5mm,则头部尺寸为75.5mm压下量由6.7mm减少到5.2mm,腰部压下量由1.5mm减少到0,自然头部对腰部有拉伸加之腰部无压下而宽展,所以腰变薄,反之腰部变厚。
(1)因辊式或立式矫直机调整操作不当,将钢轨矫断。
(2)钢质不好,如局部夹杂、偏析,在矫直过程中被矫(压)裂(断)。
3、线材常见缺陷
缺陷名称
缺陷特征
产生原因
耳子
盘条表面沿轧制方向的条状凸起称为耳子,有单边耳子,也有双边耳子。在高速线材轧机(连轧)生产中,最终产品头尾两端很难避免耳子的产生。
1)轧槽导卫安装不正及放偏过钢,使轧件产生耳子。
(1)卫板安装不良,使钢轨产生力偶,形成扭转。
(2)轧件温度不均或压下量不均,造成各部延伸不一致。
(3)矫直机调整不当,钢轨受力偶作用。
(4)在冷却台架上翻钢时因温度较高也会出现扭转。
弯曲
钢轨沿垂直或水平方向呈现不平直的现象叫弯曲,一般呈镰刀形或波浪形,仅在端部的弯曲又叫弯头。
(1)由于重轨的头、腰、底面积相差较大,使轧制、冷却等工序操作易产生弯曲。
(1)钢坯带来的表面非金属夹杂物。
(2)在加热或轧制过程中,偶然有非金属夹杂物(如加热炉的耐火材料及炉渣等),附在钢坯表面上,轧制时被压入钢材,冷却经矫直后部分脱落。
分层
此缺陷在型钢的锯切断面上呈黑线或黑带状,严重的分离成两层或多层,分层处伴随有夹杂物。
(1)主要是由于镇静钢的缩孔或沸腾钢的气囊未切净。
(1)主要因钢坯缩孔部分未切净。
钢铁材料常见缺陷(图谱)及产生原因
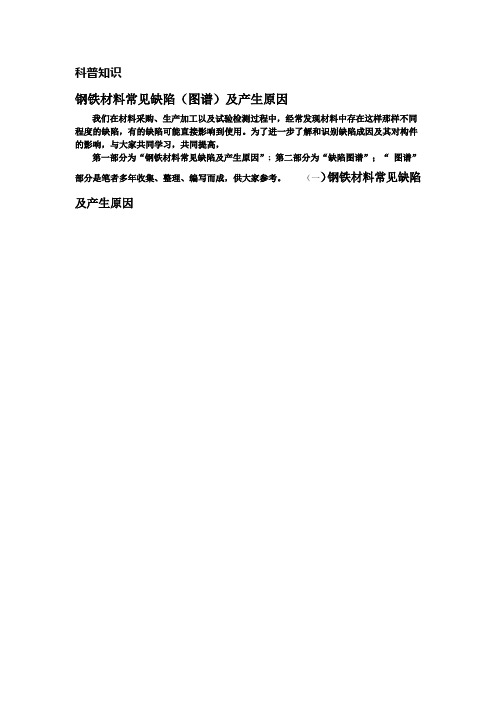
科普知识钢铁材料常见缺陷(图谱)及产生原因我们在材料采购、生产加工以及试验检测过程中,经常发现材料中存在这样那样不同程度的缺陷,有的缺陷可能直接影响到使用。
为了进一步了解和识别缺陷成因及其对构件的影响,与大家共同学习,共同提高,第一部分为“钢铁材料常见缺陷及产生原因”; 第二部分为“缺陷图谱”;“图谱”部分是笔者多年收集、整理、编写而成,供大家参考。
(一)钢铁材料常见缺陷及产生原因型钢常见缺陷重轨常见缺陷线材常见缺陷中厚板常见缺陷热轧板(卷)常见缺陷冷轧板(卷)常见缺陷镀锌板(卷)常见缺陷镀锡板(卷)常见缺陷彩涂板(卷)常见缺陷硅钢产品常见缺陷露晶带钢表面上可看到隐约可见的晶粒。
(1)CA3线MgO底层含水率较高。
(2)带钢在CA3线过氢化或油污清洗不净。
(3)CB炉露点高。
保护气体中的含氧量高或含有水份。
(4)保护气体供给量不是。
(5)钢卷装CB炉前滞留时间长使MgO含水率增高。
(6)密封不严吸人空气。
二:缺陷图谱图1-8为弯曲试验缺陷,图9-21为拉伸断口图1:刮伤图2:角钢中夹渣分层图3:角钢夹渣分层图4:夹杂分层图5:气泡起层图6:三分层缺陷图7:气泡形成三分层图8:角钢上的缩管分层图9:结晶状断口和星状断口图10:全杯状断口和半杯状断口图11:菊花状断口和燕尾断口图12:燕尾断口和斜断口图13:中心增碳和心部增碳图14:心部增碳图15:表面增碳图16:结晶胎性断口和残余增碳图17:结晶胎性断口和残余缩孔断口图18:残余缩孔断口和残余缩孔图19:缩孔断口和缩孔横截面劈开成二半图20:缩孔断口图21:白点断口和劈开断口。
轧制缺陷及质量控制
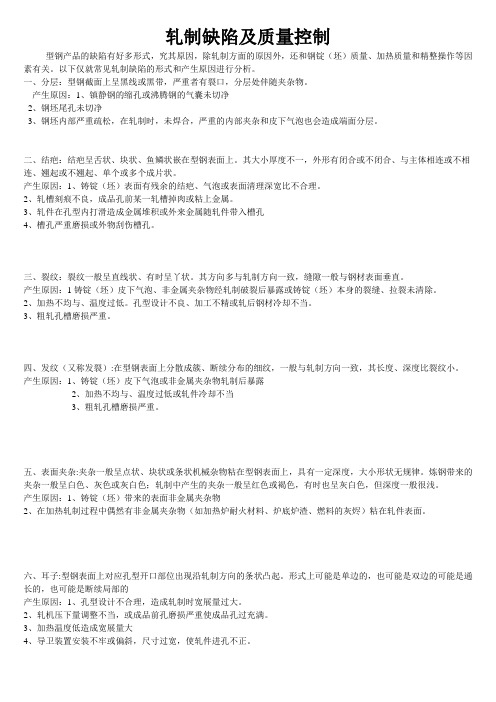
轧制缺陷及质量控制型钢产品的缺陷有好多形式,究其原因,除轧制方面的原因外,还和钢锭(坯)质量、加热质量和精整操作等因素有关。
以下仅就常见轧制缺陷的形式和产生原因进行分析。
一、分层:型钢截面上呈黑线或黑带,严重者有裂口,分层处伴随夹杂物。
产生原因:1、镇静钢的缩孔或沸腾钢的气囊未切净2、钢坯尾孔未切净3、钢坯内部严重疏松,在轧制时,未焊合,严重的内部夹杂和皮下气泡也会造成端面分层。
二、结疤:结疤呈舌状、块状、鱼鳞状嵌在型钢表面上。
其大小厚度不一,外形有闭合或不闭合、与主体相连或不相连、翘起或不翘起、单个或多个成片状。
产生原因:1、铸锭(坯)表面有残余的结疤、气泡或表面清理深宽比不合理。
2、轧槽刻痕不良,成品孔前某一轧槽掉肉或粘上金属。
3、轧件在孔型内打滑造成金属堆积或外来金属随轧件带入槽孔4、槽孔严重磨损或外物刮伤槽孔。
三、裂纹:裂纹一般呈直线状、有时呈丫状。
其方向多与轧制方向一致,缝隙一般与钢材表面垂直。
产生原因:1铸锭(坯)皮下气泡、非金属夹杂物经轧制破裂后暴露或铸锭(坯)本身的裂缝、拉裂未清除。
2、加热不均与、温度过低。
孔型设计不良、加工不精或轧后钢材冷却不当。
3、粗轧孔槽磨损严重。
四、发纹(又称发裂):在型钢表面上分散成簇、断续分布的细纹,一般与轧制方向一致,其长度、深度比裂纹小。
产生原因:1、铸锭(坯)皮下气泡或非金属夹杂物轧制后暴露2、加热不均与、温度过低或轧件冷却不当3、粗轧孔槽磨损严重。
五、表面夹杂:夹杂一般呈点状、块状或条状机械杂物粘在型钢表面上,具有一定深度,大小形状无规律。
炼钢带来的夹杂一般呈白色、灰色或灰白色;轧制中产生的夹杂一般呈红色或褐色,有时也呈灰白色,但深度一般很浅。
产生原因:1、铸锭(坯)带来的表面非金属夹杂物2、在加热轧制过程中偶然有非金属夹杂物(如加热炉耐火材料、炉底炉渣、燃料的灰烬)粘在轧件表面。
六、耳子:型钢表面上对应孔型开口部位出现沿轧制方向的条状凸起。
线材产品质量缺陷
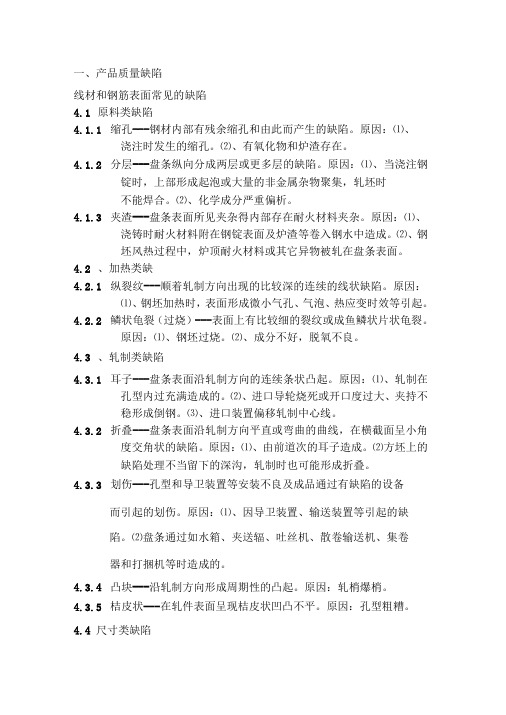
一、产品质量缺陷线材和钢筋表面常见的缺陷4.1原料类缺陷4.1.1缩孔---钢材内部有残余缩孔和由此而产生的缺陷。
原因:⑴、浇注时发生的缩孔。
⑵、有氧化物和炉渣存在。
4.1.2分层---盘条纵向分成两层或更多层的缺陷。
原因:⑴、当浇注钢锭时,上部形成起泡或大量的非金属杂物聚集,轧坯时不能焊合。
⑵、化学成分严重偏析。
4.1.3夹渣---盘条表面所见夹杂得内部存在耐火材料夹杂。
原因:⑴、浇铸时耐火材料附在钢锭表面及炉渣等卷入钢水中造成。
⑵、钢坯风热过程中,炉顶耐火材料或其它异物被轧在盘条表面。
4.2、加热类缺4.2.1纵裂纹---顺着轧制方向出现的比较深的连续的线状缺陷。
原因:⑴、钢坯加热时,表面形成微小气孔、气泡、热应变时效等引起。
4.2.2鳞状龟裂(过烧)---表面上有比较细的裂纹或成鱼鳞状片状龟裂。
原因:⑴、钢坯过烧。
⑵、成分不好,脱氧不良。
4.3、轧制类缺陷4.3.1耳子---盘条表面沿轧制方向的连续条状凸起。
原因:⑴、轧制在孔型内过充满造成的。
⑵、进口导轮烧死或开口度过大、夹持不稳形成倒钢。
⑶、进口装置偏移轧制中心线。
4.3.2折叠---盘条表面沿轧制方向平直或弯曲的曲线,在横截面呈小角度交角状的缺陷。
原因:⑴、由前道次的耳子造成。
⑵方坯上的缺陷处理不当留下的深沟,轧制时也可能形成折叠。
4.3.3划伤---孔型和导卫装置等安装不良及成品通过有缺陷的设备而引起的划伤。
原因:⑴、因导卫装置、输送装置等引起的缺陷。
⑵盘条通过如水箱、夹送辐、吐丝机、散卷输送机、集卷器和打捆机等时造成的。
4.3.4凸块---沿轧制方向形成周期性的凸起。
原因:轧梢爆梢。
4.3.5桔皮状---在轧件表面呈现桔皮状凹凸不平。
原因:孔型粗糟。
4.4尺寸类缺陷4.4.1横肋纵肋偏小---沿轧制方向形成的连续的偏小现象,原因:来料小,孔型充不满。
4.4.2、水平尺寸超标---沿扎制方向形成的连续超标现象。
⑴、来料大。
⑵、进口有倒钢现象。
轧钢常见缺陷之欧阳歌谷创编

(3)坯料的缺陷,如缩孔、偏析、分层、外来夹杂物,影响轧件的正常变形,形成耳子。
折叠
盘条表面沿轧制方向平直或弯曲的细线,在横断面上与表面呈小角度交角状的缺陷多为折叠。折叠两侧伴有脱碳层或部分脱碳层,折缝中间常存在氧化铁夹杂。
(1)前道次的耳子及其他纵向凸起物折倒轧入本体所造成。再轧形成折叠。
轧痕(凸、凹、压印)
在钢轨表面出现的各种不连续的伤痕叫轧痕。各种轧痕都存在热加工的痕迹、般呈周期性出现,有时无规律分布。
(1)由于轧槽掉肉,使轧件表面呈现周期性的凸包。
(2)孔型内粘结铁皮,结疤等,使轧件产生周期性的口坑,又称缺肉。
(3)在轧制过程中,氧化铁皮压入轧件表面,冷却或矫直后脱落。形成无规律的压痕。
(2)切深孔切人太深,造成腿长无法消除。
(3)轧辊不水平或有轴向串动,以及800咬入不正,成品孔夹板上偏等都会造成一腿长,一腿短等。
(4)腰的厚、薄主要是成品孔及成品前孔压下量不合理所造成。
划伤(刮伤、擦伤、划痕)
一般呈直线或弧形的沟槽,其深度不等,通长可见沟底,长度自几毫米到几米,连续或断续地分布于钢材的局部或全长,多为单条,有时出现多条。
耳子
在型钢表面上与L型开口处相对应的地方,出现顺轧制方向延伸的凸起部分称为耳子。有单边的,也有双边的,有时耳子产生在型钢的全长,也有局部或断续的,方、圆钢产生较多。
(1)轧机调整不当或孔型磨损严重,使成品前孔来料过大或成品孔压下量过大,产生过充满,多产生双边耳子。
(2)进入成品孔前因事故造成温度过低,进入成品孔时延伸降低,宽展过大,多产生双边耳子。
(2)导卫板安装不当,有棱角或粘有铁皮使轧件产生划痕,再轧形成折叠。
棒线材常见表面缺陷及成因

棒线材常见表面缺陷及成因线材常见的表面缺陷有裂纹、耳子、折叠、结疤(翘皮或鳞皮)、划痕、麻面、分层、氧化及脱碳等。
表面缺陷最大的危害就是降低线材的断面收缩率等塑性指标,从而影响冷拉加工性能。
1裂纹裂纹是指线材表面沿轧制方向有平直或弯曲、折曲,或以一定角度向线材内部渗透的缺陷。
主要典型缺陷为表面细小裂纹簇、单道长条裂纹、平行裂纹等,如图1[1]。
表面裂纹簇形貌单道线缺陷形貌平行裂纹形貌图1典型裂纹形貌图表面裂纹的形成与钢的化学成分和炼钢、轧制控制均有关系[2]-[4]。
轧制方面的原因:①轧槽表面磨损或损坏;②粗轧前几道导位划伤;③氧化铁皮被轧入轧件;④导位尺寸不合适或偏离轧制线;⑤高压水除鳞的冷却水路堵塞或偏离;⑥错辊;⑦表面保护、吊装方法不当等储运过程中的擦伤。
冶炼方面的原因:钢坯上未消除的裂纹、皮下气泡及非金属夹杂物,它们都会在线材表面造成裂纹。
炼钢时钢液未得到净化,在连铸坯加工中形成皮下夹杂,轧前加热,表层氧化,皮下夹杂逐渐裸露,随后轧制中脱落形成裂纹。
2耳子线材表面沿轧制方向的凸起称为耳子,根据生成的位置可分为:单边耳子、双边耳子及错边耳子[3]-[7]。
图2是实际生产中的耳子[3]。
图2耳子耳子主要是由于轧制方面的原因引起的[2]-[7]。
轧制方面的原因:①过充满,坯料尺寸过大,压下量过大;②入口导卫偏离轧制线、磨损严重或烧坏;③上下辊偏移量不合适引起错辊;④轧件温度不均匀引起变形不均匀;⑤连轧机设置不当引起的堆钢、拉钢。
炼钢方面的原因:冶炼-铸造引起坯料的缩孔、偏析、分层及外来夹杂等,轧制时,影响正常变形,也会导致耳子的出现。
3折叠钢铁表面形成沿轧制方向的各种角度的折线,一般为在横断面与表面呈小角度交角状缺陷,两侧一般伴有脱碳层或部分脱碳层,中间常存在氧化铁夹杂,图3[3]是典型的折叠。
图3折叠轧件折叠的很大一部分原因是前面轧制时形成的各种耳子。
此外,轧辊轴向固定不佳发生窜动;入口导卫磨损严重或烧损时钢坯咬入不稳定;炼钢提供的坯料存在缺陷,未清理等也会导致折叠[2]-[5]、[7]。
所有钢材常见缺陷及原因

钢材常见缺陷及原因一、圆钢1 划伤特征:一般呈直线型沟痕,可见沟底,长度由肉眼刚刚可见到几毫米不等,长度自几毫米至几米不等,可断续分布,也可能通长分布。
原因:导卫表面不光滑,有毛刺或磨损严重;滚动导轮不转或磨损严重;翻钢板表面不光滑刮伤;在运输过程中辊道盖板等刮伤。
2 折叠特征:沿轧制方向呈直线状分布,外形似裂纹,边缘有时呈锯齿状,连续或断续分布,深浅不一,内有氧化铁皮,在横断面上看,一般呈折角。
原因:前某一道次出耳子;前某道次产生划伤、轴错、轧槽损坏或磨损严重、飞边等;原料表面有尖锐棱角或裂纹。
3 结疤特征:一般呈舌形或指甲形,宽而厚的一端和基体相连;有时其外形呈一封闭的曲线,嵌在钢材表面上。
原因:前一孔型轧槽损坏破损或磨损严重;外界金属落在轧件上被带入孔型,压入钢材表面;前一道次轧件表面有深度较大的凹坑。
4 耳子特征:出现于成品的两旁辊缝处,呈平行于轴线的突起条状。
有两侧耳子、单侧耳子、全长出耳、局部出耳和周期出耳等。
原因:孔型设计不良,宽展估计过小;成品前料型高度较大;成品孔辊缝小;终轧温度低,宽展增加;成品导板安装不正、尺寸大或磨损严重;横梁或导板盒松动;轧槽更换错误或轧机轴承损坏。
特征:有头部弯曲、局部弯曲、全长弯曲等。
原因:出口导卫安装过高或过低;温度不均;上下辊径差过大;冷床不平,成品在冷床上排列不齐,移动速度不一致,翻钢设备不良;冷却水分布不均匀,成品冷却不均;精整操作不良。
6 翘皮特征:呈鱼鳞状或分层翘起的薄皮,大部分是生根的,也有不生根的。
原因:导卫装置加工或安装不良,围盘有尖锐棱角,刮伤了轧件表面,再轧后,引起翘皮;输送辊道表面粗糙,刮起伤了轧件表面,再轧后造成翘皮;轧件带有薄耳子;轧槽磨损严重,轧件在孔型内打滑;连铸坯内部有较大的皮下气泡,轧后破裂形成翘皮。
7 表面夹杂特征:一般呈点状、条状或块状分布,其颜色有暗红、暗黄、灰白等,机械地粘结在成品表面上,不易剥落,且有一定的深度。
线材质量常见五大问题及措施.doc
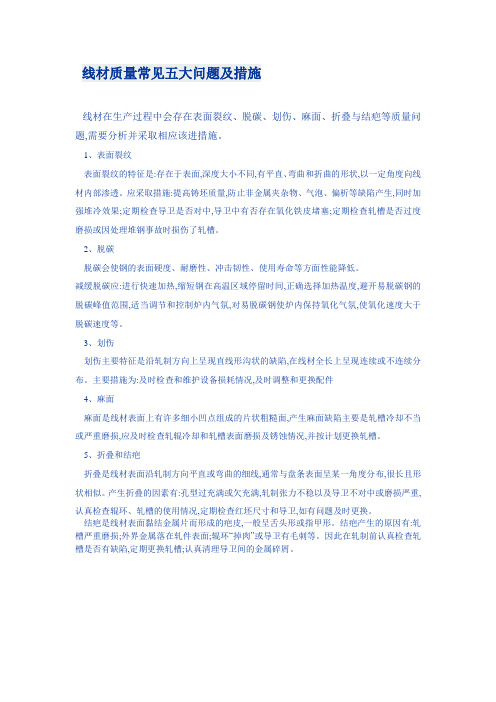
线材质量常见五大问题及措施线材在生产过程中会存在表面裂纹、脱碳、划伤、麻面、折叠与结疤等质量问题,需要分析并采取相应该进措施。
1、表面裂纹表面裂纹的特征是:存在于表面,深度大小不同,有平直、弯曲和折曲的形状,以一定角度向线材内部渗透。
应采取措施:提高铸坯质量,防止非金属夹杂物、气泡、偏析等缺陷产生,同时加强堆冷效果;定期检查导卫是否对中,导卫中有否存在氧化铁皮堵塞;定期检查轧槽是否过度磨损或因处理堆钢事故时损伤了轧槽。
2、脱碳脱碳会使钢的表面硬度、耐磨性、冲击韧性、使用寿命等方面性能降低。
减缓脱碳应:进行快速加热,缩短钢在高温区域停留时间,正确选择加热温度,避开易脱碳钢的脱碳峰值范围,适当调节和控制炉内气氛,对易脱碳钢使炉内保持氧化气氛,使氧化速度大于脱碳速度等。
3、划伤划伤主要特征是沿轧制方向上呈现直线形沟状的缺陷,在线材全长上呈现连续或不连续分布。
主要措施为:及时检查和维护设备损耗情况,及时调整和更换配件4、麻面麻面是线材表面上有许多细小凹点组成的片状粗糙面,产生麻面缺陷主要是轧槽冷却不当或严重磨损,应及时检查轧辊冷却和轧槽表面磨损及锈蚀情况,并按计划更换轧槽。
5、折叠和结疤折叠是线材表面沿轧制方向平直或弯曲的细线,通常与盘条表面呈某一角度分布,很长且形状相似。
产生折叠的因素有:孔型过充满或欠充满,轧制张力不稳以及导卫不对中或磨损严重,认真检查辊环、轧槽的使用情况,定期检查红坯尺寸和导卫,如有问题及时更换。
结疤是线材表面黏结金属片而形成的疤皮,一般呈舌头形或指甲形。
结疤产生的原因有:轧槽严重磨损;外界金属落在轧件表面;辊环“掉肉”或导卫有毛刺等。
因此在轧制前认真检查轧槽是否有缺陷,定期更换轧槽;认真清理导卫间的金属碎屑。
型钢线材常见缺陷及原因
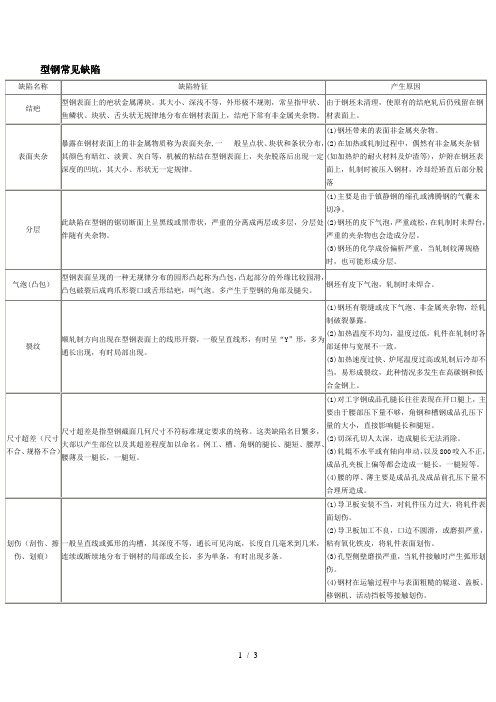
(4)冷床拉钢小车不同步或滑轨不光滑。
(5)运输辊道速度过快,容易把钢材头部撞弯。
(6)矫直温度过高,冷却后容易产生弯曲。
(7)成品捆扎长短不齐较大。在运输中装卸不当。
(8)堆垛时不按规定进行。
(9)锯片用的太老,也容易产生弯头。
形状不正
型钢断面几何形状歪斜不正,这类缺陷对不同品种各异,名称繁多。如工槽钢的内并外斜,弯腰挠度,角钢顶角大、小腿不平等。
耳子
在型钢表面上与}L型开口处相对应的地方,出现顺轧制方向延伸的凸起部分称为耳子。有单边的,也有双边的,有时耳子产生在型钢的全长,也有局部或断续的,方、圆钢产生较多。
(1)轧机调整不当或孔型磨损严重,使成品前孔来料过大或成品孔压下量过大,产生过充满,多产生双边耳子。
(2)进入成品孔前因事故造成温度过低,进入成品孔时延伸降低,宽展过大,多产生双边耳子。
(1)导卫板安装不当,对轧件压力过大,将轧件表面划伤。
(2)导卫板加工不良,口边不圆滑,或磨损严重,粘有氧化铁皮,将轧件表面划伤。
(3)孔型侧壁磨损严重,当轧件接触时产生弧形划伤。
(4)钢材在运输过程中与表面粗糙的辊道、盖板、移钢机、活动挡板等接触划伤。
缺肉
型钢其一侧面沿轧制方向全长或周期性的缺少金属称缺肉,缺陷处没有成品孔轧槽的热轧印迹,色暗、表面较粗糙。
(2)轧制温度的波动或局部不均匀,影响轧件的宽展量,产生耳子。
(3)坯料的缺陷,如缩孔、偏析、分层厦外来夹杂物,影响轧件的正常变形,形成耳子。
折叠
盘条表面沿轧制方向平直或弯曲的细线,在横断面上与表面呈小角度交角状的缺陷多为折叠。折叠两侧伴有脱碳层或部分脱碳层,折缝中间常存在氧化铁夹杂。
钢在轧制中常见的缺陷总结
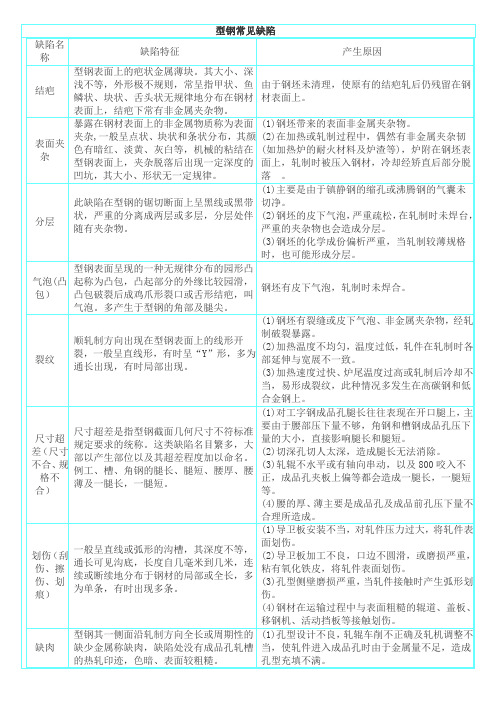
开裂_{V_8uk_ $
钢坯在轧制中,自动裂开称开裂。工业轨尤为多见。_\#_F>_R,
sN_M_F(TY
(1)由于钢锭中心部位集中大量气体和非囊属夹杂物所致。`-?`H>+OG_
(2)由于钢“内裂”或“穿孔”所致。ZQ_-6n1O_
8~B___LT_Z
过烧G_ 6x__N R
因钢坯加热不当,钢轨表面出现的横向粗糙裂口叫“过烧”。裂口多出现在轨头和轨底侧边,金相观察裂口处金属晶粒粗大。7Rc>LI*'
(1)轧机操作调整不当或成品前孔磨损严重,造成成品孔压下量过大。=c%gV]>_G
(2)钢坯温度低,造成轧制过程中的宽展大。Ow__v}l_J_
(3)入口导板安装偏斜、松动,轧件进孔不正。l7_Wdbx5x0
zh_Y]__!
轧痕(凸、凹、压印)__t"5ZYa__
在钢轨表面出现的各种不连续的伤痕叫轧痕。各种轧痕都存在热加工的痕迹、般呈周期性出现,有时无规律分布。R{6_M__(!x
一般呈直线或弧形的沟槽,其深度不等,通长可见沟底,长度自几毫米到几米,连续或断续地分布于钢材的局部或全长,多为单条,有时出现多条。xr7}@rq"U<
)#_cZ_& O_
(1)导卫板安装不当,对轧件压力过大,将轧件表面划伤。F8"J_<_VJ7
(2)导卫板加工不良,口边不圆滑,或磨损严重,粘有氧化铁皮,将轧件表面划伤。!'p
(1)钢坯带来的表面非金属夹杂物。1_vdG \$_
(2)在加热或轧制过程中,偶然有非金属夹杂韧(如加热炉的耐火材料及炉渣等),炉附在钢坯表面上,轧制时被压入钢材,冷却经矫直后部分脱落_U#|6n ,_。cp_6I]#_X
轧钢常见缺陷之欧阳家百创编

(2)矫直机调整操作不当。
(3)矫直辊磨损严重。
(4)轧辊磨损或成品孔出口卫板安装不良。
2、重轨常见缺陷
缺陷名称
缺陷特征
产生原因
结疤
在钢轨的头、腰底部等处局部粘附的金属蒲片状疤皮为重轨结疤,外形轮廓不规则,有闭合和不闭合的,有生根和不生根的,结疤下面常有肉眼可见的非金属夹杂物。
尺寸超差(尺寸不合、规格不合)
尺寸超差是指型钢截面几何尺寸不符标准规定要求的统称。这类缺陷名目繁多,大部以产生部位以及其超差程度加以命名。例工、槽、角钢的腿长、腿短、腰厚、腰薄及一腿长,一腿短。
(1)对工字钢成品孔腿长往往表现在开口腿上,主要由于腰部压下量不够,角钢和槽钢成品孔压下量的大小,直接影响腿长和腿短。
(4)轧辊安装不正确,上、下轧辊轴线不在同一垂直平面内,即上、下辊成水平投影交叉,使轧件扭转。
(5)矫直机调整不当。
弯曲(弯头)
型钢沿垂直或水平方向呈现不平直的现象称为弯曲,一般为镰刀形或波浪形,仅只头部的弯曲叫弯头。
(1)轧机调整不当,轧辊倾斜或跳动,上、下辊径差大,造成速度差大。
(2)出口卫板安装不正确,卫板梁过低或过高。
(2)切深孔切人太深,造成腿长无法消除。
(3)轧辊不水平或有轴向串动,以及800咬入不正,成品孔夹板上偏等都会造成一腿长,一腿短等。
(4)腰的厚、薄主要是成品孔及成品前孔压下量不合理所造成。
划伤(刮伤、擦伤、划痕)
一般呈直线或弧形的沟槽,其深度不等,通长可见沟底,长度自几毫米到几米,连续或断续地分布于钢材的局部或全长,多为单条,有时出现多条。
耳子
在型钢表面上与L型开口处相对应的地方,出现顺轧制方向延伸的凸起部分称为耳子。有单边的,也有双边的,有时耳子产生在型钢的全长,也有局部或断续的,方、圆钢产生较多。
- 1、下载文档前请自行甄别文档内容的完整性,平台不提供额外的编辑、内容补充、找答案等附加服务。
- 2、"仅部分预览"的文档,不可在线预览部分如存在完整性等问题,可反馈申请退款(可完整预览的文档不适用该条件!)。
- 3、如文档侵犯您的权益,请联系客服反馈,我们会尽快为您处理(人工客服工作时间:9:00-18:30)。
型钢线材常见缺陷及原因
————————————————————————————————作者:————————————————————————————————日期:
型钢常见缺陷
缺陷名称 缺陷特征
产生原因
结疤
型钢表面上的疤状金属薄块。
其大小、深浅不等,外形极不规则,常呈指甲状、鱼鳞状、块状、舌头状无规律地分布在钢材表面上,结疤下常有非金属夹杂物。
由于钢坯未清理,使原有的结疤轧后仍残留在钢材表面上。
表面夹杂
暴露在钢材表面上的非金属物质称为表面夹杂,一 般呈点状、块状和条状分布,其颜色有暗红、淡黄、灰白等,机械的粘结在型钢表面上,夹杂脱落后出现一定深度的凹坑,其大小、形状无一定规律。
(1)钢坯带来的表面非金属夹杂物。
(2)在加热或轧制过程中,偶然有非金属夹杂韧
(如加热炉的耐火材料及炉渣等),炉附在钢坯表面上,轧制时被压入钢材,冷却经矫直后部分脱落
分层
此缺陷在型钢的锯切断面上呈黑线或黑带状,严重的分离成两层或多层,分层处伴随有夹杂物。
(1)主要是由于镇静钢的缩孔或沸腾钢的气囊未切净。
(2)钢坯的皮下气泡,严重疏松,在轧制时未焊台,严重的夹杂物也会造成分层。
(3)钢坯的化学成份偏析严重,当轧制较薄规格时,也可能形成分层。
气泡(凸包)
型钢表面呈现的一种无规律分布的园形凸起称为凸包,凸起部分的外缘比较园滑,
凸包破裂后成鸡爪形裂口或舌形结疤,叫气泡。
多产生于型钢的角部及腿尖。
钢坯有皮下气泡,轧制时未焊合。
裂纹
顺轧制方向出现在型钢表面上的线形开裂,一般呈直线形,有时呈“Y”形,多为通长出现,有时局部出现。
(1)钢坯有裂缝或皮下气泡、非金属夹杂物,经轧制破裂暴露。
(2)加热温度不均匀,温度过低,轧件在轧制时各部延伸与宽展不一致。
(3)加热速度过快、炉尾温度过高或轧制后冷却不当,易形成裂纹,此种情况多发生在高碳钢和低合金钢上。
尺寸超差(尺寸
不合、规格不合) 尺寸超差是指型钢截面几何尺寸不符标准规定要求的统称。
这类缺陷名目繁多,
大部以产生部位以及其超差程度加以命名。
例工、槽、角钢的腿长、腿短、腰厚、
腰薄及一腿长,一腿短。
(1)对工字钢成品孔腿长往往表现在开口腿上,主要由于腰部压下量不够,角钢和槽钢成品孔压下
量的大小,直接影响腿长和腿短。
(2)切深孔切人太深,造成腿长无法消除。
(3)轧辊不水平或有轴向串动,以及800咬入不正,
成品孔夹板上偏等都会造成一腿长,一腿短等。
(4)腰的厚、薄主要是成品孔及成品前孔压下量不合理所造成。
划伤(刮伤、擦伤、划痕) 一般呈直线或弧形的沟槽,其深度不等,通长可见沟底,长度自几毫米到几米,连续或断续地分布于钢材的局部或全长,多为单条,有时出现多条。
(1)导卫板安装不当,对轧件压力过大,将轧件表面划伤。
(2)导卫板加工不良,口边不圆滑,或磨损严重,
粘有氧化铁皮,将轧件表面划伤。
(3)孔型侧壁磨损严重,当轧件接触时产生弧形划伤。
(4)钢材在运输过程中与表面粗糙的辊道、盖板、移钢机、活动挡板等接触划伤。
缺肉型钢其一侧面沿轧制方向全长或周期性的缺少金属称缺肉,缺陷处没有成品孔轧
槽的热轧印迹,色暗、表面较粗糙。
(1)孔型设计不良,轧辊车削不正确及轧机调整不
当,使轧件进入成品孔时由于金属量不足,造成
孔型充填不满。
(2)轧槽错牙或入口导板安装不当,造成轧件某一
面缺少金属,再轧时孔型充填不满。
(3)前、后孔磨损程度不一样。
(4)园轧件弯、扭造成进孔不正。
(5)对于工、槽钢,困钢坯不清理,往往出现结疤
掉到闭口腿内,在轧制过程中便会出现周期性的
腿尖缺肉。
耳子在型钢表面上与}L型开口处相对应的地方,出现顺轧制方向延伸的凸起部分称为
耳子。
有单边的,也有双边的,有时耳子产生在型钢的全长,也有局部或断续的,
方、圆钢产生较多。
(1)轧机调整不当或孔型磨损严重,使成品前孔来
料过大或成品孔压下量过大,产生过充满,多产
生双边耳子。
(2)进入成品孔前因事故造成温度过低,进入成品
孔时延伸降低,宽展过大,多产生双边耳子。
(3)成品孔入口夹板向孔型一侧安偏或松动。
金属
挤人孔型一侧辊缝里,产生单面耳子。
(4)成品入口夹板间隙过大或松动,进钢不稳,易
产生双面断续耳子。
扭转型钢绕其轴线扭成螺旋状称为扭转(1)卫板安装不良,使轧件出孔时受到力偶的作用产生扭转。
(2)两侧延伸不一致,主要是压下不均或辊子有轴向串动。
(3)方、园钢由于入口夹板安装不正确,使钢料进孔不正,造成延伸不一致。
(4)轧辊安装不正确,上、下轧辊轴线不在同一垂直平面内,即上、下辊成水平投影交叉,使轧件扭转。
(5)矫直机调整不当。
弯曲(弯头)型钢沿垂直或水平方向呈现不平直的现象称为弯曲,一般为镰刀形或波浪形,仅
只头部的弯曲叫弯头。
(1)轧机调整不当,轧辊倾斜或跳动,上、下辊径
差大,造成速度差大。
(2)出口卫板安装不正确,卫板梁过低或过高。
(3)轧件温度不均匀,使金属延伸不一致。
(4)冷床拉钢小车不同步或滑轨不光滑。
(5)运输辊道速度过快,容易把钢材头部撞弯。
(6)矫直温度过高,冷却后容易产生弯曲。
(7)成品捆扎长短不齐较大。
在运输中装卸不当。
(8)堆垛时不按规定进行。
(9)锯片用的太老,也容易产生弯头。
形状不正型钢断面几何形状歪斜不正,这类缺陷对不同品种各异,名称繁多。
如工槽钢的
内并外斜,弯腰挠度,角钢顶角大、小腿不平等。
(1)矫直辊孔型设计不合理。
(2)矫直机调整操作不当。
(3)矫直辊磨损严重。
(4)轧辊磨损或成品孔出口卫板安装不良。
线材常见缺陷
缺陷名称缺陷特征产生原因
耳子盘条表面沿轧制方向的条状凸起称为耳子,有单边耳子,也有双边耳
子。
在高速线材轧机(连轧)生产中,最终产品头尾两端很难避免耳子
的产生。
1)轧槽导卫安装不正及放偏过钢,使轧件产生耳子。
(2)轧制温度的波动或局部不均匀,影响轧件的宽展量,产生耳子。
(3)坯料的缺陷,如缩孔、偏析、分层厦外来夹杂物,影响轧件的
正常变形,形成耳子。
折叠盘条表面沿轧制方向平直或弯曲的细线,在横断面上与表面呈小角度
交角状的缺陷多为折叠。
折叠两侧伴有脱碳层或部分脱碳层,折缝中
间常存在氧化铁夹杂。
(1)前道次的耳子及其他纵向凸起物折倒轧入本体所造成。
再轧形
成折迭。
(2)导卫板安装不当,有棱角或粘有铁皮使轧件产生划痕,再轧形
成折迭。
裂纹盘条表面沿轧制方向有平直或弯曲、折曲的细线,这种缺陷多为裂纹。
由于钢坯上的缺陷经轧制后形成的裂纹常判有氧化圆点、脱碳现象,
裂纹中间常存在氢化亚铁。
由于轧后控冷不当形成的裂纹无脱碳现象
伴生,裂缝中一般无氧化亚铁。
(1)钢坯上未消除的裂纹(无论纵向或横向),皮下气泡及非金属夹
杂物都会在盘条上造成裂纹缺陷。
(2)钢坯上的针孔直口不清除,经轧制被延伸、氧化、熔接就会造
成成品的线状发纹。
针孔是铸坯常见的重要缺陷之一,不显露时
很难检查出来,应特别予以注意。
(3)高碳钢盘条或合金舍量高的钢坯加热工艺不当(预热速度过
快,加热温度过高等),以及盘条轧成后冷却速度过快,也可能造
成成品裂纹,后者还可能出现横向裂纹。
凸起及压痕盘条表面呈现一些连续性、周期性的凸起或凹下的印痕(某些印痕无规
律性),缺陷形状、大小相似。
凸起、压痕主要是轧槽损坏或磨损造成的。
缩孔盘条截面中心部位的疏松或空洞称为缩孔,缩孔处存在非金属夹杂,
同时某些非铁元素富集。
连铸方坯按“小钢锭理论”有时出现周期性的缩孔,轧后不能焊
台。
截面夹杂暴露在钢材截面上的非金属物质称为截面夹杂。
这样的缺陷般是铸钢时外来的非金属物质进入钢液,粘附铸坯某个部位造成的。