2000m3焊接工艺解析
2000m3球罐焊缝裂纹缺陷修复

2000m3球罐焊缝裂纹缺陷修复摘要:本文对一例使用两年的2000m3球形储罐,在全面检验时发现罐体焊缝内存在多处裂纹的原因进行了分析,详细介绍了针对该球罐焊缝缺陷所制定的修复方法,确保了该球罐的安全运行,同时对以后进行其他同类球罐的检验以及缺陷处理提供了借鉴。
关键词:球罐;焊缝裂纹;缺陷修复中图分类号: tg457.5 文献标识码: a 文章编号: 1009-8631(2013)02-0026-02引言球形容器亦称球罐,通常作为有压介质的储存器。
球罐与常用的圆筒形容器相比具有以下特点: 1)球罐的表面积最小,即在相同容量下球罐所需钢材面积最小; 2)球罐壳板承载能力比圆筒形容器大一倍,即在相同直径、相同压力下,采用相同钢板时,球罐的板厚只需圆筒形容器板厚的一半; 3)球罐占地面积小,且可向空间高度发展,有利于地表面积的利用; 4)球罐还有基础简单、受风面小、外观漂亮等特点。
因此,广泛用于冶金、化工、石油和城市煤气等行业中。
球形容器是在复杂应力状态下工作的,若在制造中存在某些缺陷,运行中就易出现脆性失效,以致发生恶性事故,因此,必须按照国家有关规定认真开展对球罐的定期检验、缺陷修复和安全等级评定工作,确保球罐的安全运行。
本文对t-4303民用液化气球罐全面检验中发现的缺陷进行了原因分析和修复方法介绍,确保了该液化石油气球罐的安全运行,对以后进行其他同类球罐的检验以及缺陷处理提供了借鉴。
1 球罐概况简介1.1 该2 000m3液化石油气球罐于2009 年 6月投入运行,2011年 5月开始对其进行首次全面检验,球罐各项主要技术参数见表一。
1.2 球罐结构形式:10支柱3带混合式。
球壳板数:34 块。
安装对接焊缝总长:381.2m。
2 检验前期准备倒空罐内介质,泄压,用氮气置换,断开进出口管线并加装盲板,蒸汽蒸罐,水洗,氧含量、可燃气体分析合格。
搭接脚手架,罐外壁所有焊缝表面及其两侧边缘向外200 mm宽除锈打磨。
2000m3储罐施工方案解析

140万吨/年延迟焦化装置2000M3冷焦溢流放空储水罐施工方案(中国石化股份有限公司北京燕山分公司1000万吨/年炼油系统改造工程)编制:审核:HSE:批准:洛阳隆惠石化工程有限公司1工程概况中国石化股份有限公司北京燕山分公司1000万吨/年炼油系统改造工程140万吨/年延迟焦化装置新建一台2000M3冷焦溢流放空储水罐,此2000M3冷焦溢流放空储水罐(D-2403)由中国石化工程建设公司设计。
储罐由罐底、罐壁、罐顶、罐顶平台和栏杆、盘梯等组成,结构为拱顶罐。
其主体尺寸φ16150×14751mm,罐体有七层壁板组成,罐底、罐壁、罐顶材质均为Q235-B罐体罐壁厚度从下至上依次是10mm、9mm、8mm、8mm、7mm、7mm、7mm。
油罐总重~72778KG。
2编制依据及施工规范2.1工程合同。
2.2设计图纸(25200EQ-DWA1-0501~25200EQ-DWA1-0506,中国石化工程建设公司设计)。
2.3 GBJ128-90《立式圆筒形钢制焊接油罐施工及验收规范》。
2.4 SH3530-93《石油化工立式圆筒形钢制储罐施工工艺标准》。
2.5 GB985-88《气焊、手工电弧焊及气体保护焊焊缝坡口的基本形式与尺寸》。
2.6JB4730-94《压力容器无损检测》。
2.7《储罐焊接施工方案》。
3施工组织机构2000立方米储罐倒装法工艺流程图5.1施工前准备5.1.1技术准备5.1.1.1施工技术人员组织有关施工人员进行技术交底,保证相关施工人员熟悉施工图纸及相关技术标准。
5.1.1.2根据罐体材料进行焊接试验,制定相应的焊接工艺。
5.1.1.3培训并选择取得相应位置合格证的焊工,保证储罐各位置都有相应合格的焊工进行施焊。
5.1.2材料准备材料供应部门应保证原材料及附属构件质量符合设计要求,不得有不合格或不符合设计要求的原材料、成品、半成品投用到工程中。
5.1.3施工手段用料、机具准备:数量及规格分别详见第11.1、11.2条。
2000立方米空气球罐组焊方案(01)
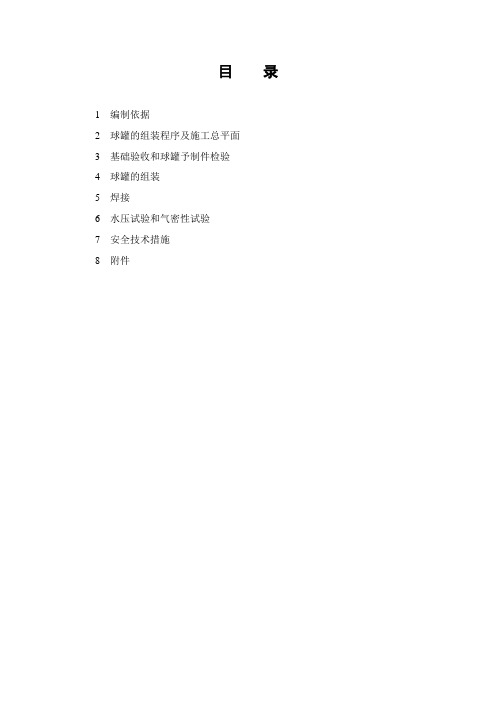
目录1 编制依据2 球罐的组装程序及施工总平面3 基础验收和球罐予制件检验4 球罐的组装5 焊接6水压试验和气密性试验7 安全技术措施8 附件1 编制依据1.1 《压力容器安全监察规程》;1.2 《钢制球形贮罐施工及验收规范》GBJ94-901.3 《钢制压力容器》GB150-981.4 《现场设备、工业管道焊接工程施工及验收规范》GB50236-822 球罐的组装程序及施工总平面2.1 球罐的组装方法该球罐采用分带组焊施工方法,即把球守则分成两个半球帽和一个独立带,在平台上合拢组焊,吊装总成。
2.2 球罐的组装程序a、组装准备球罐组装准备工作包括基础验收,球罐予制件检查、平台铺设及工卡具准备。
b、南温带组装,下极板人孔,接管安装并与南温带组装成下球帽。
将下球帽吊起放在事先准备好的底座上,找正值置和上弦口的水平,加以固定。
c、赤道带组装、加固。
将加固好的赤道带吊起,同下球帽合拢,调整环缝并点焊固定。
d、安装支柱并与赤道带焊接。
吊起上球帽,同赤道带合拢,调整后点焊环焊缝,检验后焊接两道环焊缝。
f、检验、探伤、消除应力外处理后安装梯子平台及其它附件。
g、水压试验、气密试验后竣工。
球罐的组装程序见《200m3球罐的组装施工程序图》(附图二)。
各带的拼装按《200m3球罐排板图》进行(见附图三)。
组装时的工卡具按《龙门卡具布置图》的要求进行(见附图四)。
3 基础验收和球罐予制件检验3.1 基础验收3.1.1 球罐在组装前,应按设计图纸和土建竣工文件对基础进行全面检查和验收,其检查项目和验收标准见表2。
基础检查项目及验收标准表23.1.2 检查方法及其它检验项目按规范及有关文件的要求进行。
3.1.3 基础检查验收合格后,应对基础和地脚螺栓进行保护,以防碰伤和损坏。
3.2 球罐予制件检查验收。
3.2.1 球罐的球壳板、人孔、接管、支柱等零部件出厂证明文件应包括GBJ94-86和2.1.1条所列内容。
3.2.2 按出厂证明文件、设计图纸、质量证明书和发货装箱单、进行数量清点和质量检查。
2000m 3储油罐现场自动焊

mi,第 1 、第 7 壁 板 板 幅 分别 为9 0m l l 节 节 0 m和 80mm,其余 皆 0
为 15 om l 0 i 。罐 内径 为 1 . m。 l 58 2 1 焊 接工 艺 评 定 .
进行 20 0m 油罐 现 场 施 工 。 0 稍
按 G J 2- 19 《 式 圆筒 形钢 制 焊 接油罐 施 工 验收 规 范> B 8 90 立 1
固定 在 磁 吸 轨道 上 。可 根 据需 要 进 行 向上 立 焊 和 向下 立 焊 。 纵缝 、环 缝 焊 机 行 走 机 构 在 同 一 轨 道 上 运 行 ,两 类 设 备
形 式 及 组 对 要 求 如 图 1 示 , 焊 接 方 法 为 C 保 焊 。罐 壁 板 所 0气
纵 缝 焊 接 参 数见 表 1 。
J 5 实 心 镀 铜 焊 丝 ( . r ,C 2 体 纯 度 ≥9 . ,坡 口 M一 6 1 m) O 气 2a 95 %
小 型 立 式 圆筒 储 罐 ( 0 —00 0m ) 的焊 接 。 20 0 2 0
环 缝 焊机 ( G 2 :焊 接 方 法 为 细 丝 埋 弧 焊 。设 有 焊 缝 A W一 ) 光点跟 踪装 置 ,以确保焊 枪 随时对 准坡 口。配有 焊剂 回收 、
气 总 公 司 工 程技 术 研 究 院研 制 开 发 ,适 用 于 倒 装 法 施 工 的 中 、
伤 、拉 伸及 弯 曲 ( 弯 、面 弯 )试 验 ,结果 均 符合 标 准要 求 。 背 2 . 焊 接 参数 2 ( ) 纵 缝 :母 材 为 Q 3A, = m, = 1 2 5 8m 8mm,焊 材 为
l 焊 接 设 备
和J 7 8 20 《 制 压 力 容器 焊 接 工 艺 评 定 > 的 要 求 ,对 油 B4 0- 00 钢
2000m3球罐现场组焊及热处理

2000m3球罐现场组焊及热处理摘要本文介绍球罐的现场组装、焊接及焊后热处理的要点,提出质量控制措施。
关键词球罐;现场组装;焊接;质量控制球罐是一种在石油、化工等行业被广泛应用设备。
由于其制造和场地限制,大多数的球罐在现场制造安装。
我以公司为用户制作的一2000 m3球罐为例子,介绍其制作方法和后续的热处理经过。
1简介该球罐为四带混合式结构,体积2000m3,直径Φ15650mm,质量257140 kg。
球壳板52块,材质Q345R,壁厚32mm,支柱10根。
球罐设计压力1.10MPa,设计温度50 ℃,水压试验压力1.38MPa,焊接接头系数1.1,腐蚀裕量2.0mm,抗震设防烈度为7,场地土类别为I。
此球罐施工的重点是吊装、焊接难度大,为此,对球罐吊装、焊接及后期的热处理进行严格控制,而且,在焊接后的检测方面也严格控制,以保证的安全和质量。
2 对接球罐施工步骤为:安装前准备—对设备基础校验—球壳检查—罐体的连接制造—焊缝探伤—后续热处理—附件装配—水压试验—防腐及保温—验收和报检。
2.1吊装采用竖立中心塔架分瓣吊装,组对的方法法施工,利用1台70 t吊和1台50t吊装。
2.1.1 上、下段支柱组装上、下段支柱组装在现场钢平台上进行,采用千斤顶进行下段支柱的精确调整。
2.1.2 中心柱塔架吊立用50 t汽车吊吊立中心柱塔架。
2.1.3 赤道部分壳体安装按图纸安装前编辑好的顺序吊装,焊接赤道部分壳体,先安装2块带支柱的壳体,注意径向和轴向安装角度,然后把1块不带支柱的赤道壳体安装就位,根据以上方法安装完赤道壳体。
安装时应保证上、下环口的安装间隙。
2.1.4 温带壳体的安装把一块温带壳体安装到位,依次安装相邻的温带壳体,从两支柱中间开始安装温带壳体板,直至对称位置,在其垂直方向遵照此方法依次安装,直到全部完成温带赤道壳体的安装。
把下部一端用支柱与中心柱塔架固定,根据图纸提供的尺寸,保证对接接口处间隙满足施工前严格制作的安装样板要求。
2000M3丙烯球罐焊接方案

东营市海科瑞林化工有限公司2000m3丙烯球罐焊接施工方案编制:审核:批准:山东五维华信化工设备有限公司二○一四年一月十四日1 概述球罐的安装质量主要是通过焊接质量来体现的,因而焊接是极其重要的关键环节。
施工中必须认真对待,确保焊缝质量。
2 编制依据2.1 图纸1331-设B242.2 TSG R0004-2009《固定式压力容器安全技术监察规程》2.3 GB150-2011《压力容器》2.4 NB/T47014-2011《承压设备焊接工艺评定》2.5 NB/T47015-2011《承压设备焊接工艺规程》2.6 GB12337-1998《钢制球形储罐》2.7 GB50094-2010《球形储罐施工规范》3 焊接前的准备工作及要求3.1 焊接工艺评定球壳板材质为Q345R,厚度为δ=52mm,球罐焊接工艺评定可按横焊、立焊以及平焊加仰焊三种焊评分别进行评定。
焊接工艺评定前,应针对钢板的钢号,厚度,焊接材料及焊接方法初步确定球罐焊接适用的预焊接工艺规程,以确定预热温度。
3.2 焊接工艺焊接工艺、焊缝返修及焊接设备的管理应严格执行本公司《大型设备现场组焊管理制度》、《压力容器焊接管理制度》的规定。
从事球罐现场组装人员,应认真学习、熟悉本公司质量保证体系文件有关管理制度。
3.3 焊工资格3.3.1 从事球罐焊接的焊工必须具备劳动部门颁发的特种设备焊接操作人员合格证书,且批准施焊的钢材种类、焊接方法、焊接位置等要求与施焊工程相符。
3.3.2 本球罐所需焊接合格证项目为SMAW-FeII-2G-12-Fe3J、SMAW-FeII-3G-12-Fe3J、SMAW-FeII-4G-12-Fe3J共3项。
参加球罐焊接的焊工名单及合格证项目附后。
3.4 焊材检验及管理焊接材料的管理、烘烤,发放应严格执行本公司《压力容器焊接材料管理制度》的规定。
3.4.1 焊条必须具有质量证明书,其中应包括熔敷金属的化学成分、力学性能、扩散氢含量等,各项指标应符合NB/T47018-2011《承压设备用焊接材料订货条件》的有关规定。
2000立方米大型球罐设计说明书

课程设计资料标签资料编号:题目球形储罐设计姓名学号专业材料成型指导教师成绩资料清单注意事项:1、存档内容请在相应位置填上件数、份数,保存在档案盒内。
每盒放3-5名学生资料,每份按序号归档,如果其中某项已装订于论文正本内,则不按以上顺序归档。
各专业可依据实际情况适当调整保存内容。
2、所有资料必须保存三年。
课程设计论文(说明书)装订格式可参照毕业设计论文装订规范要求。
3、资料由学院资料室统一编号。
编号规则是:年度—资料类别代码·学院代码·学期代码—顺序号,顺序号由四位数字组成(参照《西安理工大学实践教学资料整理归档要求》)。
4、各院、系应在课程设计结束后一个月内按照规范进行资料归档。
5、特殊情况请在备注中注明,并把相关资料归档,应有当事人和负责人签名。
课程与生产设计(焊)设计说明书设计题目球形储罐设计专业材料成型及控制工程班级学生指导教师2016 年秋学期目录一、设计说明课程设计任务书-------------------------------------------------------------------------------11.1 选材-----------------------------------------------------------------------------------------------21.2 球壳计算----------------------------------------------------------------------------------------21.3 球壳薄膜应力校核---------------------------------------------------- --------------------31.4 球壳许用外力----------------------------------------------------------------------- ----------41.5 球壳分瓣计算----------------------------------------------------------------------------------5二、支柱拉杆计算2.1 计算数据---------------------------------------------------------------------------------------92.2 支柱载荷计算---------------------------------------------------------------------------------102.3 支柱稳定性校核-----------------------------------------------------------------------------132.4 拉杆计算---------------------------------------------------------------------------------------14三、连接部位强度计算3.1 销钉直径计算-----------------------------------------------------------------------------------153.2 耳板和翼板厚度计算-------------------------------------------------------------------------153.3 焊缝剪应力校核-------------------------------------------------------------------------------153.4 支柱底板的直径和厚度计算---------------------------------------------------------------163.5 支柱与球壳连接处的应力验算------------------------------------------------------------163.6 支柱与球壳连接焊缝强度计算------------------------------------------------------------18四、附件设计4.1 人孔结构-----------------------------------------------------------------------------------------194.2 接管结构-----------------------------------------------------------------------------------------194.3 梯子平台---------------------------------------------------------------------------------------194.4 液面计--------------------------------------------------------------------------------------------20五、工厂制造及现场组装5.1 工厂制造----------------------------------------------------------------------------------------215.2 现场组装--------------------------------------------------------------------------------------------22六、焊接与检查6.1 钢材的可焊性----------------------------------------------------------------------------------------236.2 焊接工艺的确定------------------------------------------------------------------------------------236.3 焊后热处理-------------------------------------------------------------------------------------------24七、检查7.1 支柱尺寸精度检查---------------------------------------------------------------------------------247.2 竣工检查----------------------------------------------------------------------------------------------247.3 气密性试验-------------------------------------------------------------------------------------------257.4 开罐检查----------------------------------------------------------------------------------------------25参考文献----------------------------------------------------------------------------------------------------26《生产设计与实践》课程设计任务书一、设计题目球形储罐设计二、主要设计参数内径Dn=15.7m,体积V=2000m3设计压力P=0.69MPa; 工作压力Pg=0.64MPa,水压试验压力P gx=1.03 MPa水压试验总重:2200吨,立柱数:12根实际温度:20℃自选参数:充装系数K= 0.95模拟使用地点(西安)三、设计内容1、选材2、整体设计3、焊材选择4、焊接设备选择5、焊接工艺6、检验及质量标准四、提交内容1、设计说明书2、主要焊缝焊接工一、 选材1、选材 根据设计条件及GB12337-2014《钢制压力容器》 表4 球壳材料选取Q345R[]189tMpa σ=。
2000立方储罐焊接方案

2000立方原料油罐储罐焊接施工方案编制:审核:批准:中石化建设安装有限公司二零一九年十一月八日目录1.编制说明 (3)2.概述 (3)3. 编制依据 (3)4. 焊接方法及设备 (3)5. 焊接材料及烘干规范 (3)6. 接坡口形式及焊接电流参数 (3)7. 焊接坡口形式及焊接电流参数 (7)8. 焊接工艺评定 (7)9. 焊接工艺 (7)10. 中幅板的焊接 (8)11. 弓形边缘板的焊接 (8)12. 罐顶的焊接 (8)13. 罐壁板立缝、环缝的焊接 (8)14. 底层壁板与弓形边缘板环角缝的焊接. (9)15 . 中幅板与弓形边缘板的焊接 (9)16. 盘管焊接 (9)17. 焊接要求 (9)18. 焊接检验 (10)19. 焊缝返修 (11)20. 焊接管理资料 (11)21. 安全措施 (11)1、编制说明1.1 为了保证储罐焊接工程质量,满足设计和生产对工艺的要求,特编制本方案。
1.2 本方案作为施焊过程中必须遵守的焊接技术文件和合格焊接工艺评定作为编制焊接工艺卡的依据。
1.3本方案经监理及业主审查通过后,即可用于指导储罐制作的焊接工作,其所规定的内容与其它方案不符时,一律以本方案为准。
各有关人员要严格依照执行,加强工艺纪律,以确保储罐焊接质量和进度。
2、概述罐区原料油罐罐壁油罐罐壁最大高度为16575mm ,最大直径14150mm , 所用钢板材质为Q235-B。
罐底厚度为8-10 mm,罐壁厚度为6-14mm 。
油罐顶板及底板(除边缘板)均为搭接,罐底边缘板、罐壁立缝、环缝为对接。
其主体结构形式是立式油罐,该结构的主要特点是,焊接量大、焊接变形控制要求严,因此要求施工人员严格按照施工方案、施工技术交底卡进行施工。
确保油罐优质、高效、按期完成。
3、编制依据《立式圆筒形钢制焊接油罐设计规范》 GB 50341 -2014《立式圆筒形钢制焊接油罐施工及验收规范》GB50128-2014《压力容器焊接规程》NB-T 47015-2011《钢制化工容器结构设计规定》HG/T 20583-2011有关施工图、招标文件及补充文件4、焊接方法及设备•焊接方法采用手工电弧焊。
2000m3球罐安装工法
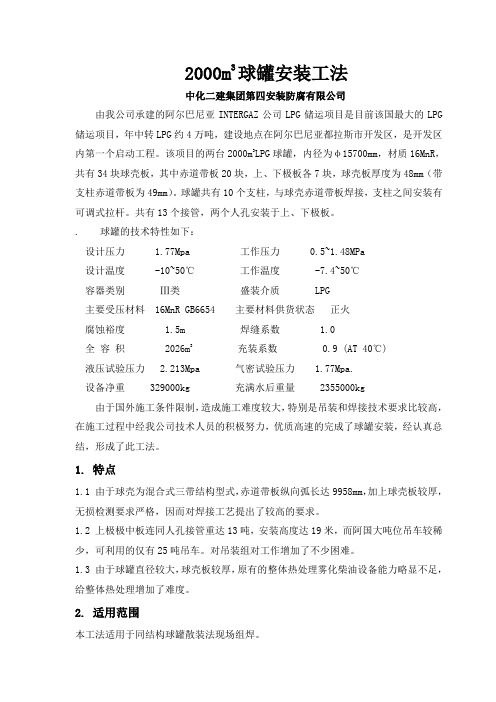
2000m3球罐安装工法中化二建集团第四安装防腐有限公司由我公司承建的阿尔巴尼亚INTERGAZ公司LPG储运项目是目前该国最大的LPG 储运项目,年中转LPG约4万吨,建设地点在阿尔巴尼亚都拉斯市开发区,是开发区内第一个启动工程。
该项目的两台2000m3LPG球罐,内径为φ15700mm,材质16MnR,共有34块球壳板,其中赤道带板20块,上、下极板各7块,球壳板厚度为48mm(带支柱赤道带板为49mm)。
球罐共有10个支柱,与球壳赤道带板焊接,支柱之间安装有可调式拉杆。
共有13个接管,两个人孔安装于上、下极板。
. 球罐的技术特性如下:设计压力 1.77Mpa 工作压力 0.5~1.48MPa设计温度 -10~50℃工作温度 -7.4~50℃容器类别Ⅲ类盛装介质 LPG主要受压材料 16MnR GB6654 主要材料供货状态正火腐蚀裕度 1.5m 焊缝系数 1.0全容积 2026m3充装系数 0.9 (AT 40℃)液压试验压力 2.213Mpa 气密试验压力 1.77Mpa.设备净重 329000kg 充满水后重量 2355000kg由于国外施工条件限制,造成施工难度较大,特别是吊装和焊接技术要求比较高,在施工过程中经我公司技术人员的积极努力,优质高速的完成了球罐安装,经认真总结,形成了此工法。
1. 特点1.1 由于球壳为混合式三带结构型式,赤道带板纵向弧长达9958mm,加上球壳板较厚,无损检测要求严格,因而对焊接工艺提出了较高的要求。
1.2 上极极中板连同人孔接管重达13吨,安装高度达19米,而阿国大吨位吊车较稀少,可利用的仅有25吨吊车。
对吊装组对工作增加了不少困难。
1.3 由于球罐直径较大,球壳板较厚,原有的整体热处理雾化柴油设备能力略显不足,给整体热处理增加了难度。
2. 适用范围本工法适用于同结构球罐散装法现场组焊。
3 施工工艺3.1 球罐组对采用分带组对,整体几何尺寸调整点固焊。
2000m^3液氨球罐设计方案确定的浅析

2020年03月2000m 3液氨球罐设计方案确定的浅析安赢(云南化工设计院有限公司,云南昆明650041)摘要:目前在我国球形容器应用领域非常广泛。
化工行业球形容器通常被称为球形储罐。
文章通过甘肃瓮福化工的2000m3液氨球罐的工程设计实例,来叙述在设计过程中应注意的一些事项。
通过对2000m3液氨球罐的实例,对液氨球罐的设计制造检验的标准、主体、焊接、检测、涂敷等的确定进行描述。
关键词:标准;主体方案;焊接;检测;涂敷1设计、制造与检验标准的确定球罐是一种储存带压气体或者液体的大型储罐,球罐与圆筒容器(即一般贮罐)相比,在相同直径和压力下,壳壁厚度仅为圆筒容器的一半,钢材用量省,且占地较小,基础工程简单。
但由于容积大,需要制造厂成型及组焊单位现场组装焊接,制造、焊接和组装要求很严,检验工作量大,制造技术复杂。
为确保球罐的安全使用,设计、制造及检验等的工作就显得非常重要。
目前我国压力容器设计、制造、检验所遵循的规范标准主要有GB150-2011《压力容器》、GB12337-2014《钢制球形储罐》、TSG R0004-2009《固定式压力容器安全技术监察规程》。
2球罐主体方案的确定2.1介质特性氨,是一种无色,有刺激性气味的气体,中毒危害,吸入体内会使人昏迷、呕吐、甚至于窒息死亡。
氨火灾爆炸危险性为乙类,在空气中的爆炸极限为15%-28%,在氧气中的爆炸极限为13.5%-79%,很容易遇明火发生爆炸。
氨的临界温度132.4℃,通过加压或者降温,可以将其从气态变为液态。
通常液氨储罐就是利用加压,使氨变成液态来进行储存的。
氨有非常广泛的用途,主要用于生产尿素、硝酸及其他化学肥料,还可用作医药和农药的原料。
2.2设计参数用户为甘肃瓮福化工有限责任公司新建一台2000m3的液氨球罐,工作压力0.3~1.44MPa ,设计压力1.6MPa ,工作温度-2~39℃,设计温度为43℃,属于三类压力容器。
操作介质为中度危害,腐蚀裕量3.0mm ,焊接接头系数1.0全容积2026m3,充装系数0.9,最大允许工作压力1.67MPa ,设计基本风压0.9KN/M2,设计雪压值0.25KN/M2,抗震设防烈度7度(0.15g),保冷层厚度100mm 。
2000立方米球罐安装方案解析

2000⽴⽅⽶球罐安装⽅案解析第五节球罐安装施⼯⽅案⼀、编制依据由于⽆详细的球罐装配图纸,本⽅案根据以往的经验进⾏编制,若球罐材质与设计不符,施⼯时另⾏编制详细的施⼯⽅案1、 GB12337-1998《钢制球形储罐》;2、GB150-1998《钢制压⼒容器》;3、《压⼒容器安全技术监察规程》(1999版);4、JB4708-2000《钢制压⼒容器焊接⼯艺评定》;5、JB/T4709-2000《钢制压⼒容器焊接规程》;6、《锅炉压⼒容器焊⼯考试规则》(劳动部);7、B4744-2000《钢制压⼒容器产品焊接试板的⼒学性能检验》8、SHJ505-87《炼油、化⼯施⼯安全规程》;⼆、主要的施⼯程序和⽅法1、主要的施⼯程序施⼯准备→基础验收→球⽪验收→球罐组装→球罐焊接→焊缝检测、返修→球罐热处理→⽔压试验→⽓密性试验→球罐防腐、保温→交⼯验收2、主要的施⼯⽅法2.1焊接采⽤⼿⼯电弧焊2.2球⽪吊装采⽤80吨汽车吊2.3焊缝预热采⽤电加热带进⾏加热2.4焊缝清根采⽤碳弧⽓刨2.5球罐焊缝热处理采⽤整体热处理法三、施⼯准备1、球罐资料的审查资料审查包括三个⽅⾯,即球罐制造半成品的合格证书资料、球罐基础的完⼯资料利球罐安装单位应具备的施⼯资质及制定的施⼯⽂件资料等。
2、基础的检查和验收标准如下(见下图1和表1)图1基础⽰意图表13、到现场的球壳板逐张进⾏下列各项复验并作好记录3.1曲率检查根据规范的要求,分别制作⼆个弧度的样板,横向弧度板的弧长应为1.5m,纵向弧度样板的弧长应为2m,曲率允差≤3mm。
3.2 坡⼝检查坡⼝表⽽平滑,坡⼝钝边及坡⼝深度的允许偏差为±1.5mm,坡⼝表⾯不允许有裂纹、分层等缺陷。
该球罐坡⼝为不对称型X 坡⼝,其⾓度为60°±5°和55°±5°,坡⼝⾓度的允许偏差±2°30′。
和⽤坡⼝检验尺检验内,外坡⼝,每道坡检测5点。
2000m3氢气球罐建造技术

Technology Forum︱432︱2017年7期2000m 3氢气球罐建造技术李腾蛟河南省锅炉压力容器安全检测研究院,河南 郑州 450000摘要:本文介绍了国内某2000m 3氢气球罐的建造技术。
本文对氢气介质的特殊特性进行分析。
具体介绍了球罐在建造过程中的技术工艺,包括焊接及无损检测的技术要求,为我国氢气球罐大型化提供参考。
关键词:氢气;球罐;焊接;无损检测中图分类号:TU996.7+1 文献标识码:B 文章编号:1006-8465(2017)07-0432-011 概述 氢气导热系数大、扩散性及渗透性强,极易爆炸,在空气中爆炸极限为4.1%~74.5%,在氧气中爆炸极限为4.0%~94%,最低爆炸能为0.2×104J,其蒸汽能与空气形成爆炸性混合物,遇火花即可爆炸,由于氢气储存设备多安装于钢厂及火电厂等安全生产要求等级较高场所,如果发生火灾、爆炸,将造成重大的经济损失和人员伤亡,因此氢气储存设备的设计及建造安全可靠显的尤为重要。
该项目氢气球罐由于设计压力大,体积大,安全要求性高。
氢气球罐在使用过程中存在充气和放气过程,气体工作压力会在一定范围内进行波动,球罐设备存在交变载荷的疲劳问题。
据此,设备设计方法选用参照JB4732–1995《钢制压力容器 — 分析设计标准》(2005确认)的分析设计。
表1 球罐的主要性能参数 公称容积/m3 2000 工作介质 氢气设计压力/MPa 2.2 设计温度/℃ -20/50球罐壳体材质 Q370R 腐蚀裕度/mm 1.5焊缝系数 1.0 充装系数 1.0地震设防烈度 6度(0.05g,第一组) 水压试验压力/MPa 2.75气压试验压力/MPa 2.2 设计寿命/年 20结构型式 三带十支柱混合式 容器类别 Ⅲ2 球罐的设计参数2.1球罐钢板本项目球罐采用Q370R 低合金钢板,按NB/T 47013.3-2015《承压设备无所检测》的规定对钢板逐张进行100%超声检测,球壳用钢板等级合格定为Ⅰ级合格,以此减少钢板内部缺陷;球壳用Q370R按批进行力学性能复验。
2000m3球罐热处理方案
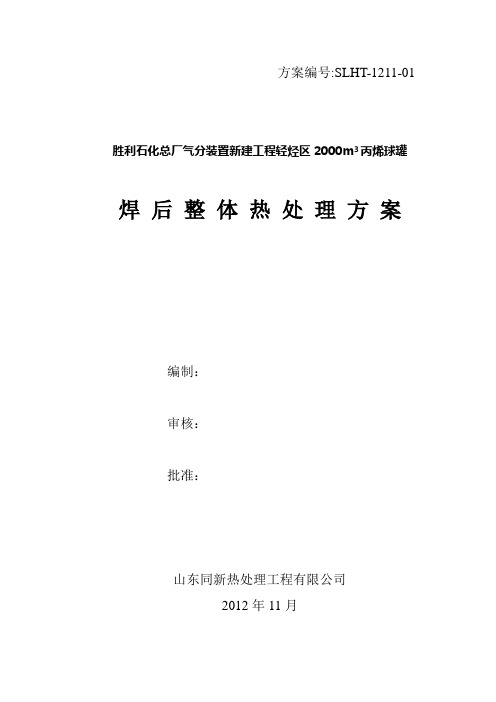
方案编号:SLHT-1211-01 胜利石化总厂气分装置新建工程轻烃区2000m3丙烯球罐焊后整体热处理方案编制:审核:批准:山东同新热处理工程有限公司2012年11月1 工程概况胜利石化总厂气分装置新建工程轻烃区新上一台2000m3丙烯球罐,根据球罐的设计制造技术条件和国家现行压力容器制造技术法规、标准要求,需进行焊后整体热处理。
采用内部燃油法对球罐进行焊后整体热处理。
为确保热处理质量满足设计规定的要求,特制定本方案。
1.1球罐主要设计参数(见表1)表1 球罐主要设计参数序号项目参数丙烯球罐1 球罐规格Ф157002 设计壁厚54mm3 公称容积2000m34 球罐材质Q370R5 操作介质丙烯6 金属质量(kg)≈3303501.2热处理施工依据《固定式压力容器安全技术监察规程》TSG R0004-2009《压力容器》GB150-2011《球形储罐施工规范》GB50094-2010《钢制球形储罐》GB12337-19982 热处理方法及工艺规程2.1热处理方法采用球罐内部燃油法进行整体热处理,用球罐腔体为炉膛,球罐外侧用保温材料进行绝热保温作为炉体,选用全自动比例燃烧器进行加热,随着燃油不断燃烧,产生的高温气流在球罐内进行对流传导和辐射,使球罐升温到热处理所需的温度。
2.2热处理工艺规范根据国家现行压力容器制造技术法规、标准要求,选择如下热处理工艺参数(表2)和工艺曲线。
表2 热处理工艺参数序号 项目 技术指标 1 保温温度 565℃±25℃ 2 保温时间130min 3 升温速度(≤400℃时可不予控制) 宜为50~80℃/h 4 降温速度(≤400℃时可不予控制) 宜为30~50℃/h5 升温时的最大温差 ≤120℃6 保温时的最大温差 ≤50℃3 热工计算 3.1热工计算参数表3 热工计算参数序号 项目参数 1 球罐内径 d Ф15700mm 2 球罐壳体厚度 δ 54mm 3 材质Q370R 4 球罐金属质量 G 330350kg 5 保温棉厚度 δ 60mm 6 保温层外表面积 S ≈796m 27 保温棉重量 G 4301kg (采用无碱玻璃棉)8 保温棉密度 γ 60kg/m 39 钢材比热 C 600℃:0.586kJ/(kg·℃);700℃:0.645(kJ/kg·℃) 10 钢材导热系数 λ1 600℃:32.56W/(m·℃);650℃:31 W/(m·℃) 11 保温棉导热系数 λ0 600℃:0.15W/(m·℃);700℃:0.187 W/(m·℃) 12 保温棉比热 λ 600℃:1.04kJ/(kg·℃);700℃:1.04kJ/(kg·℃)13 环境温度 ℃14 燃烧油 0号柴油(根据气温选择标号)565±25℃ 温度 565℃时间(h )400℃130min自由升温30~50℃/h50~80℃/h热处理工艺曲线自由降温3.2计算在500℃~550℃区间以50℃/h速率升温时,单位时间耗油量数值最大,具体数值见表4。
2000m3球罐安装工法

2000m3球罐安装工法中化二建集团第四安装防腐有限公司由我公司承建的阿尔巴尼亚INTERGAZ公司LPG储运项目是目前该国最大的LPG 储运项目,年中转LPG约4万吨,建设地点在阿尔巴尼亚都拉斯市开发区,是开发区内第一个启动工程。
该项目的两台2000m3LPG球罐,内径为φ15700mm,材质16MnR,共有34块球壳板,其中赤道带板20块,上、下极板各7块,球壳板厚度为48mm(带支柱赤道带板为49mm)。
球罐共有10个支柱,与球壳赤道带板焊接,支柱之间安装有可调式拉杆。
共有13个接管,两个人孔安装于上、下极板。
. 球罐的技术特性如下:设计压力 1.77Mpa 工作压力 0.5~1.48MPa设计温度 -10~50℃工作温度 -7.4~50℃容器类别Ⅲ类盛装介质 LPG主要受压材料 16MnR GB6654 主要材料供货状态正火腐蚀裕度 1.5m 焊缝系数 1.0全容积 2026m3充装系数 0.9 (AT 40℃)液压试验压力 2.213Mpa 气密试验压力 1.77Mpa.设备净重 329000kg 充满水后重量 2355000kg由于国外施工条件限制,造成施工难度较大,特别是吊装和焊接技术要求比较高,在施工过程中经我公司技术人员的积极努力,优质高速的完成了球罐安装,经认真总结,形成了此工法。
1. 特点1.1 由于球壳为混合式三带结构型式,赤道带板纵向弧长达9958mm,加上球壳板较厚,无损检测要求严格,因而对焊接工艺提出了较高的要求。
1.2 上极极中板连同人孔接管重达13吨,安装高度达19米,而阿国大吨位吊车较稀少,可利用的仅有25吨吊车。
对吊装组对工作增加了不少困难。
1.3 由于球罐直径较大,球壳板较厚,原有的整体热处理雾化柴油设备能力略显不足,给整体热处理增加了难度。
2. 适用范围本工法适用于同结构球罐散装法现场组焊。
3 施工工艺3.1 球罐组对采用分带组对,整体几何尺寸调整点固焊。
2000立方米储罐焊缝长度

2000立方米储罐焊缝长度储罐的焊缝长度是指储罐内部焊接缝的总长度。
焊缝是指将两个或更多金属构件进行连接时,采用焊接方法所形成的连接部位。
在储罐的制作过程中,焊缝是不可避免的一部分,它起到了连接和固定储罐构件的作用,并且对储罐的密封性和结构强度起着重要的影响。
2000立方米的储罐是一种常见的工业设备,广泛应用于石化、化工等行业。
由于储罐是用来存储大量的液体或气体,其制作要求非常严格。
焊接是储罐制作过程中最关键的环节之一,而焊缝长度是焊接质量的一个重要指标。
首先,需要明确的是焊缝的长度与储罐的体积并不直接相关。
焊缝的长度与储罐的形状、尺寸、结构等因素相关。
对于2000立方米的储罐来说,其焊缝长度会受到以下几个方面的影响:1.储罐的形状和尺寸:不同形状和尺寸的储罐在制作时所需的焊缝长度会有所差异。
例如,如果储罐采用圆柱形状,则焊缝长度主要集中在储罐的圆周上;如果储罐采用球形底部,则焊缝长度会更多地集中在底部区域。
2.储罐的结构设计:储罐的结构设计也会对焊缝长度产生影响。
例如,如果储罐采用多层结构设计,焊缝长度会更长;如果储罐采用单层结构设计,焊缝长度会相对较短。
3.焊接工艺和要求:不同的焊接工艺和要求也会对焊缝长度产生影响。
例如,如果储罐要求焊缝具有较高的强度和密封性,那么可能需要增加焊缝长度以提高焊接质量。
储罐的焊接技术通常分为手工弧焊、埋弧焊和自动焊等方法。
在储罐制作过程中,焊缝的长度不只是简单的加工过程,还需要考虑到焊接工艺、焊接材料的选择、焊接人员的技能等方面。
因此,在设计和制造储罐时,必须根据规范和标准来确定焊缝的长度,以确保储罐的使用安全和性能。
焊缝的长度是一个重要的质量指标,与焊接工艺、材料和设备的选择等密切相关。
合理控制焊缝的长度可以提高焊接质量和储罐的使用寿命。
过长的焊缝长度可能导致焊缝质量不稳定,增加了焊接过程中的焊接变形和应力集中,从而降低了储罐的使用寿命。
为了确保储罐焊缝的质量,制造商通常会采取以下措施:1.选择合适的焊接工艺和材料:根据储罐的用途和工作条件,选择适合的焊接工艺和材料,以提高焊缝的质量和可靠性。
- 1、下载文档前请自行甄别文档内容的完整性,平台不提供额外的编辑、内容补充、找答案等附加服务。
- 2、"仅部分预览"的文档,不可在线预览部分如存在完整性等问题,可反馈申请退款(可完整预览的文档不适用该条件!)。
- 3、如文档侵犯您的权益,请联系客服反馈,我们会尽快为您处理(人工客服工作时间:9:00-18:30)。
140万吨/年延迟焦化装置2000M3冷焦溢流放空储水罐焊接方案(中国石化股份有限公司北京燕山分公司1000万吨/年炼油系统改造工程)编制:审核:审定:安全:会签:洛阳隆惠石化工程有限公司二○○六年四月十八日一、编制说明本方案仅适用于中国石化股份有限公司北京燕山分公司1000万吨/年炼油系统改造工程140万吨/年延迟焦化装置新建一台2000M3冷焦溢流放空储水罐主体及其附属设施的预制、组装、焊接施工和检查。
罐体材料主要为Q235-B,采用倒装法进行安装。
二、编制依据2.1中国石化股份有限公司北京燕山分公司1000万吨/年炼油系统改造工程140万吨/年延迟焦化装置2000M3冷焦溢流放空储水罐设计图:25200EQ-DWA1-0501~25200EQ-DWA1-0506。
2.2《立式圆筒形焊接油罐施工和验收规范》GB128-90。
三、油罐设计技术条件设计技术条件见表1:2000立方米内浮顶油罐设计技术条件。
表1 2000立方米内浮顶油罐设计技术条件四、油罐材料概况油罐主体材料见表2:2000立方米内浮顶油罐主体材料表2 2000立方米内浮顶油罐主体材料五、焊前准备5.1焊接方法及设备的选择5.1.1根据油罐焊接施工位置的不同,从提高焊接施工效率,并保证焊接质量的角度出发,应选择不同的焊接方法和设备。
结合我公司的设备状况,油罐各位置焊接施工可选择的焊接方法及设备如表3所示。
表3 主要部位焊接方法和设备选用表5.1.2焊接设备必须适应焊接工艺和材料的要求,必须配置指示准确的电压、电流及焊接速度检测仪表,以控制、记录和检查焊接质量。
5.2焊接接头坡口型式及其加工5.2.1焊接接头坡口型式5.2.1.1罐底中幅板采用搭接型式,如图1所示;边缘板采用对接接头型式,如图2所示;中幅板和边缘板采用搭接型式,如图3所示。
图1:中幅板搭接焊接缝式图2:边缘板对接焊缝型式图3:中幅板与边缘板搭接焊缝型式5.2.1.2底层壁板与边缘板丁字接头焊缝型式如图4所示。
图4:底层壁板与边缘板丁字接头焊缝型式5.2.1.3罐壁板纵缝坡口型式如图5所示。
图5:罐壁板纵向坡口型式图(S≤10)5.2.1.4罐壁板环缝坡口型式如图6所示。
图6 罐壁板环向坡口型式图(7≤S1,S2<10)5.2.1.5包边角钢与罐壁的焊接角接头型式如图7所示。
图7 包边角钢与罐顶的焊接角接头型式5.2.1.6罐顶搭接接头型式如图8所示。
图8 罐顶搭接接头型式5.2.1.7接管与法兰、接管与壁板、接管与补强板等的坡口型式见相应的焊接工艺卡。
5.2.2坡口的加工5.2..2.1坡口加工可采用机械加工或自动、半自动氧—乙炔火焰切割、砂轮打磨成型。
5.2.2.2加工成型的破口必须采用砂轮打磨清除破口表面及两侧20㎜范围内的铁锈、油污、氧化皮及硬化层,坡口表面不得有凹陷、夹渣、溶渣、裂纹等缺陷存在。
5.3焊接接头现场组对5.3.1罐底版5.3.1.1边缘板采用带垫板的对接接头,采用不等间隙组对,其内侧间隙应比外侧间隙稍大。
垫板应与对接的两块边缘板贴紧,其间隙不得大于1㎜。
5.3.2罐壁板5.3.2.1壁板组装时,应保证内表面齐平。
纵焊缝的错边量不得大于板厚的1/10,且不得大于1.5㎜;环焊缝的错边量不得大于板厚的2/10,且不得大于3㎜。
5.3.1.2除设计文件规定者外,其他罐壁开口接管或接管补强板边缘与罐壁纵缝之间的距离不得小于300㎜,与罐壁环缝之间的距离不得小于200㎜。
5.4焊接工艺评定5.4.1油罐施焊前,必须按照《钢制压力容器焊接工艺评定》标准(JB4708-2000)和《立式圆筒形焊接油罐施工和验收规范》标准(GBJ128-90)的规定进行焊接工艺评定。
5.4.2焊接工艺的评定,应采用对接焊缝试件几T形角焊缝试件,对接焊缝的试件应包括底圈壁板的立焊及横焊位置。
T形接头角焊缝的试件。
应由底圈壁板与罐底边缘板组成的角焊缝的试件切取。
T形接头角焊缝的制和检验,应符合《立式圆筒形焊接油罐施工和验收规范》标准(GBJ128-90)附录一的规定。
5.4.3对接焊缝的试件,应作拉伸和横向弯曲实验。
5.5焊工考核5.5.1参与储罐焊接施工的焊条电弧焊、埋弧焊、CO2气体保焊的焊工,应按《锅炉压力容器压力管道焊工考试规则》考试合格并取得技术监督部门颁发的相应钢材类别、组别和试件分类代号合格证的焊工,可以从事储罐相应部位的焊接。
5.5.2焊工考试应在焊接工艺评定合格后进行,各项目的考试按照工艺评定合格的参数进行。
5.6焊接材料5.6.1焊接材料的选用5.6.1.1焊接材料的选用应符合设计和焊接工艺评定的要求。
5.6.1.2焊接材料(焊条、焊剂和焊丝)应符合相应标准,并有相应的出厂质量合格证明书,焊条质量合格证明书应包括熔敷金属的化学成分和机械性能;低氢焊条还应包括熔敷金属的扩散氢含量。
5.6.1.3当无质量证明书或对质量合格证明书有疑问时,应对焊接材料进行复验。
5.6.1.4焊接材料的选择见表4。
表4 焊接材料的选用表5.6.2焊接材料的烘干、储藏及保管5.6.2.1焊接材料应设专人负责烘干、保管、发放和回收,并做好记录。
5.6.2.2焊接材料应分类堆放,库房应防风、雨并有去湿机、温度计、湿度计且湿度不得超过60%。
5.6.2.3焊接材料的烘干、保存技术条件见表5。
表5 焊材的烘干、保存技术条件5.6.2.4施焊时,焊条应放在保温筒内携带。
对于药芯锈蚀、药皮变质或脱落、有明显裂纹的焊条不得使用。
5.6.2.5埋弧焊焊丝、焊剂及CO2气体保护焊焊丝必须放在干燥处妥善保管,特别是焊丝要防止生锈,焊剂要防止雨淋。
5.6.2.6焊条的发放,每人每次不得超过4㎏;埋弧焊焊丝、焊剂及CO2气体保护焊焊丝必须用完后方可领取。
5.6.2.7二氧化碳气体保护焊所用的CO2气体,使用前应预热和干燥,其纯度不低于99.5%,水分含量不应超过0.005%。
六焊接施工6.1焊接一般要求6.1.1定位焊及工卡具焊接的焊工也应具有相应的焊接资格,定位焊的引弧和收弧必须在破口内进行,且焊接工艺与正式焊接相同。
定位焊的焊缝长度不宜小于50㎜。
6.1.2焊接前破口及其两侧20㎜内的有害附着物,如水、油迹、铁锈等应清除干净。
6.1.3焊接施工中多层焊的层间接头必须错开50㎜以上,板厚大于或等于6㎜的搭接焊缝,至少应焊接两层。
焊条摆动宽度不得超过焊条直径的3倍。
6.1.4在下述任何一种焊接环境中,如不采取有效的防护措施禁止施焊:a.雨天和雪天;b.焊条电弧焊时,风速超过8m/s时,气体保护焊时,风速超过2.2m/s;c.空气相对湿度超过90%;d.焊接环境气温:普通碳素钢焊接时,气温低于-20℃;钢材16MnR焊接时,气温低于-10℃。
6.1.5焊接施工总工序见下图9所示。
图9 焊接施工总工序6.2罐底的焊接6.2.1 罐底边缘板的组对与焊接6.2.1.1该2000立方米储罐的罐底边缘板由8块厚度为10㎜厚的Q235-B钢板组成。
边缘板与垫板点焊固定在坡口内进行,只能将坡口一侧的边缘板与垫板点焊固定,另一侧的边缘板与垫板不得进行点焊固定。
6.2.1.2焊接施工先焊边缘板外侧300㎜的对接缝,焊工必须均布在罐底边缘板外侧的整个圆周上同时对称施焊,隔一条缝焊一条,最后对称留下两条焊缝先不焊,待调节好因对接缝收缩造成的总体变形后再由两名焊工对称施焊。
焊接时自边缘板外侧向内600㎜的坡口内引弧,然后采用退焊法向边缘板外侧施焊,起弧位置的层间接头应错开5mm以上,焊后边缘板与罐壁组对位置的焊缝表面必须磨平。
6.2.1.3边缘板剩余的对接焊缝在罐底与罐壁连接的大角缝焊完后且边缘板与中幅板的收缩缝焊接前进行施焊,焊接时由多名焊工均布同时由外向内采用退焊法进行施焊。
6.2.2罐底中幅板的组对与焊接6.2.2.1中幅板厚度为8㎜,采用熔化极气体保护焊或手工电弧焊进行焊接。
6.2.2.2焊接时先焊短缝、后焊长缝,由中心向外进行焊接;焊接时采用分段退步焊或跳焊法。
6.3罐壁的焊接6.3.1罐壁纵缝的焊接6.3.1.1纵缝焊接可采用手工电弧焊或二氧化碳气体保护焊。
焊缝的返修采用手工电弧焊。
6.3.1.2罐壁纵缝的焊接必须沿圆周对称施焊,先焊外侧,后焊内侧,焊完外侧后,用碳弧气刨加砂轮打磨的方法清根。
6.3.2壁板环缝的焊接6.3.2.1壁板环缝的焊接必须在上、下两圈壁板的纵缝全部焊完后,并且按照T 型接头部位的处理要求(将纵缝焊入环缝坡口内,打磨清楚环缝坡口内多余的焊肉)对环缝坡口进行处理后方可焊接,焊接时T型接头部位两侧300㎜范围内尽量避免作为焊接的起弧点和收弧点。
6.3.2.2壁板环缝的焊接采用手工电弧焊或二氧化碳气体保护焊,采用多名焊工沿罐壁圆周均布并沿同一方向施焊的方法进行焊接,先焊环缝外侧焊道,清根后再焊内侧焊道。
6.3.2.3环缝焊接由于采用多层多道焊,在各层的焊道排列中,必须注意排道顺序及位置,以确保焊缝成型后平整、美观;同时,同时多层焊道的层间接头必须打磨平并相互错开至少50mm以上。
6.3.2.4环缝内侧清根采用手工碳弧气刨沙轮打磨,清根时,应清除外侧焊道的打底层,根据外侧焊道的角变形情况保证一定的清根深度,同时,刨槽应均匀、圆滑、整齐、具有足够的宽度。
6.3.2.5环缝焊接过程中出现的焊接缺陷必须及时清楚,并进行修补,修补应根据不同的位置选择相应的焊接材料和工艺条件。
6.3.2.6罐壁纵缝、环缝焊接完毕,经检查合格后,应对罐壁内侧所有纵、环缝全部进行打磨与母材平齐,不得留有焊缝余高存在。
6.4罐壁与罐底大角焊缝的焊接6.4.1利用倒装法安装的2000立方米储水罐的大角缝的组焊应在罐壁板完全焊接完毕后进行,采用手工电弧焊焊接。
6.4.2罐壁与罐底大角缝的焊接,打底层焊条电弧焊由多名焊工对称均匀分布,沿罐内、罐外同一方向同时采用分段退焊或跳焊的方法进行焊接;填充、盖面层由多名焊工对称分布沿同一方向分段焊接,先焊内侧后焊外侧。
6.4.3大角缝的焊缝表面必须圆滑过渡,内侧焊缝成下凹形,否则应采用杀轮机打磨成凹形。
6.5罐顶焊接6.5.1罐顶包边角钢焊接:采用手工电弧焊,多名焊工沿圆周方向均布饶同一方向施焊。
6.5.2罐顶板焊接6.5.2.1罐顶板的焊接采用手工电弧焊,焊条牌号为J427,φ3.2㎜或φ4.0㎜。
6.5.2.2顶板的焊接先焊内侧焊缝,后焊外侧焊缝,径向的长焊缝宜采用隔缝对称由中心向外分段退焊的施焊方法进行焊接。
6.6其它附件的焊接6.6.1盘梯、平台等钢结构均是Q235-B钢材及型钢制作的,其焊接方法为手工电弧焊,焊材选用J427焊条。
6.6.2与罐壁相焊的钢结构,当焊缝与罐壁纵缝、环缝相碰时,应适当移动钢结构的位置,使之离开环缝的距离不得小于200㎜,离开纵缝的距离不得小于300㎜。