电熔镁砂生产的热工过程分析与节能
电熔镁砂生产工艺

电熔镁砂生产工艺
电熔镁砂生产工艺是一种高效的镁合金生产方法。
以下是一个简要的电熔镁砂生产工艺流程。
第一步:原料选材
电熔镁砂的主要原料是镁矿石,常见的有镁矾石和菱镁矿等。
在选材时要注意杂质的含量和矿石的质量。
第二步:破碎和磨粉
将选好的原材料破碎和磨粉,使其粒度适宜。
破碎过程可以采用破碎机,磨粉可以使用球磨机等设备。
第三步:混合和配比
将磨好的镁砂和其他需要的配料进行混合,按照一定比例进行配比。
这样可以确保最终产品的合金成份。
第四步:电熔
将混合好的材料放入电炉中进行电熔。
电炉可以加热为高温,使原材料融化。
在炉内进行加热的同时,还需要控制炉内的气氛,通常是用氮气或者惰性气体来控制。
第五步:冷却和浇铸
将熔化后的镁砂倒入模具中进行冷却和浇铸。
在模具中冷却的过程中,熔液会逐渐凝固,形成镁合金坯料。
第六步:坯料处理
将冷却好的合金坯料进行后续的处理。
可以使用机械加工、热
处理等方法,以达到最终产品的要求。
第七步:精细加工
将坯料进行精细加工,例如切割、锯齿、研磨等,以获得最终产品的形状和尺寸。
最后,要注意在整个生产过程中控制原料的质量,确保炉内的温度和气氛的稳定,以及合适的冷却过程,这样可以得到高品质的电熔镁砂产品。
电熔镁砂工艺流程
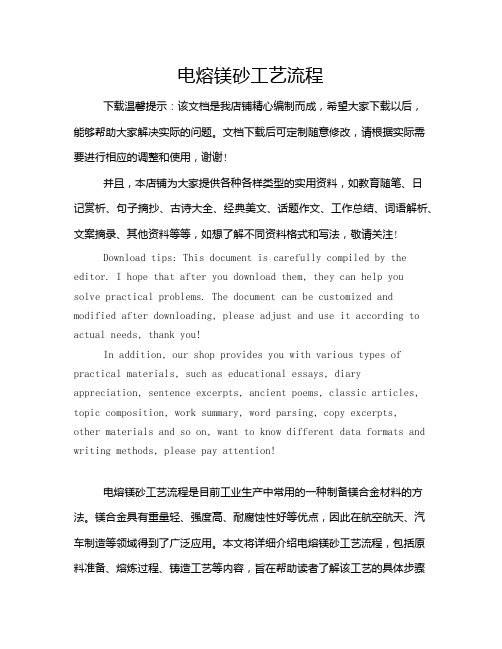
电熔镁砂工艺流程下载温馨提示:该文档是我店铺精心编制而成,希望大家下载以后,能够帮助大家解决实际的问题。
文档下载后可定制随意修改,请根据实际需要进行相应的调整和使用,谢谢!并且,本店铺为大家提供各种各样类型的实用资料,如教育随笔、日记赏析、句子摘抄、古诗大全、经典美文、话题作文、工作总结、词语解析、文案摘录、其他资料等等,如想了解不同资料格式和写法,敬请关注!Download tips: This document is carefully compiled by the editor. I hope that after you download them, they can help yousolve practical problems. The document can be customized and modified after downloading, please adjust and use it according to actual needs, thank you!In addition, our shop provides you with various types of practical materials, such as educational essays, diary appreciation, sentence excerpts, ancient poems, classic articles, topic composition, work summary, word parsing, copy excerpts,other materials and so on, want to know different data formats and writing methods, please pay attention!电熔镁砂工艺流程是目前工业生产中常用的一种制备镁合金材料的方法。
电熔镁生产工艺
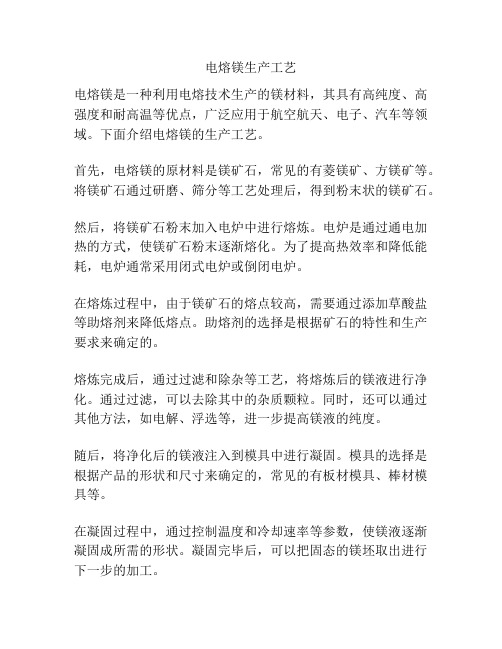
电熔镁生产工艺
电熔镁是一种利用电熔技术生产的镁材料,其具有高纯度、高强度和耐高温等优点,广泛应用于航空航天、电子、汽车等领域。
下面介绍电熔镁的生产工艺。
首先,电熔镁的原材料是镁矿石,常见的有菱镁矿、方镁矿等。
将镁矿石通过研磨、筛分等工艺处理后,得到粉末状的镁矿石。
然后,将镁矿石粉末加入电炉中进行熔炼。
电炉是通过通电加热的方式,使镁矿石粉末逐渐熔化。
为了提高热效率和降低能耗,电炉通常采用闭式电炉或倒闭电炉。
在熔炼过程中,由于镁矿石的熔点较高,需要通过添加草酸盐等助熔剂来降低熔点。
助熔剂的选择是根据矿石的特性和生产要求来确定的。
熔炼完成后,通过过滤和除杂等工艺,将熔炼后的镁液进行净化。
通过过滤,可以去除其中的杂质颗粒。
同时,还可以通过其他方法,如电解、浮选等,进一步提高镁液的纯度。
随后,将净化后的镁液注入到模具中进行凝固。
模具的选择是根据产品的形状和尺寸来确定的,常见的有板材模具、棒材模具等。
在凝固过程中,通过控制温度和冷却速率等参数,使镁液逐渐凝固成所需的形状。
凝固完毕后,可以把固态的镁坯取出进行下一步的加工。
最后,经过加工、清洗等工艺,将固态镁坯加工成所需的成品。
加工过程可以采用机械加工、热加工等方法,例如锻造、挤压、深冲压等。
在整个生产过程中,需要严格控制各项工艺参数,例如熔炼温度、熔炼时间、加工温度等,以确保产品的质量和性能。
总之,电熔镁生产工艺包括镁矿石的研磨、熔炼、净化、凝固和加工等环节。
通过控制各项工艺参数,可以生产出高纯度、高强度的电熔镁材料,满足各种工业需求。
大结晶电熔镁砂产业可行性分析 (一)

大结晶电熔镁砂产业可行性分析 (一)近年来,大结晶电熔镁砂的研究及应用已经受到越来越多的关注。
这种新型材料具有独特的物理化学性质,可以被广泛应用于建筑、冶金、化工等领域。
本文将对大结晶电熔镁砂产业的可行性进行分析。
一、市场需求大结晶电熔镁砂是一种高储能、高阻燃性、高耐磨性、高抗压强度的新型材料,具有广阔的市场前景。
在建筑行业中,大结晶电熔镁砂可用于建筑保温材料、防火材料、地面防水、隔音材料等方面;在冶金行业中,可应用于钢铁冶炼、电解铝等领域。
因此,大结晶电熔镁砂的市场需求十分广泛。
二、生产成本大结晶电熔镁砂的生产主要依靠电熔炉及其他辅助设备,并需要采购适当的原材料。
目前,国内外很多企业均已掌握了大结晶电熔镁砂的生产技术,生产成本已经明显下降。
同时,随着技术不断升级和改进,原材料成本和生产效率也将逐渐提高,有助于降低生产成本。
三、技术创新大结晶电熔镁砂的生产需要通过加热燃料和氧化物,在电弧中进行反应,这是一项高温高能的过程。
随着技术的不断创新,新型材料及适用于生产过程中的设备将不断研发和改进,可以不断降低生产成本,提高生产效率,同时还可以提高产品的稳定性、品质和性能,更好地满足市场需求。
四、政策鼓励政府的政策与鼓励也对大结晶电熔镁砂产业的发展给予了很大的支持。
政府不断加强技术研究和创新,为行业注入更多资金和技术支持,为生产企业提供更多的金融和税收优惠政策,进一步鼓励企业加大投入,提高产能和产品品质。
综上所述,大结晶电熔镁砂产业在市场需求、生产成本、技术创新和政策鼓励等方面均具有良好的可行性,未来其市场化和商业化的前景可谓相当广阔。
(459字)。
电熔镁砂制备工艺及熔炼过程
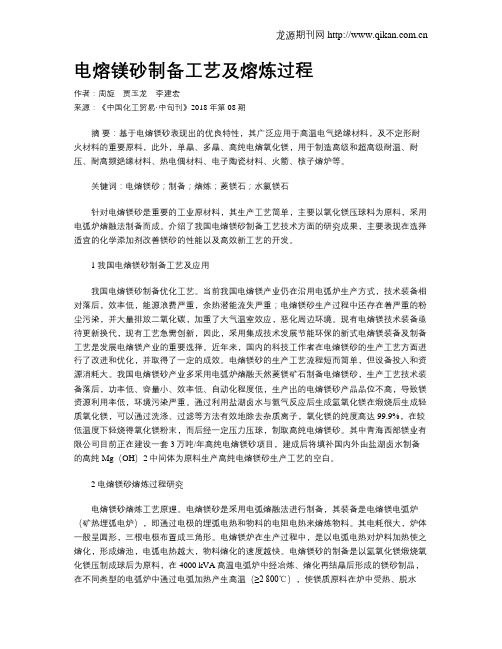
电熔镁砂制备工艺及熔炼过程作者:周旋贾玉龙李建宏来源:《中国化工贸易·中旬刊》2018年第08期摘要:基于电熔镁砂表现出的优良特性,其广泛应用于高温电气绝缘材料,及不定形耐火材料的重要原料,此外,单晶、多晶、高纯电熔氧化镁,用于制造高级和超高级耐温、耐压、耐高频绝缘材料、热电偶材料、电子陶瓷材料、火箭、核子熔炉等。
关键词:电熔镁砂;制备;熔炼;菱镁石;水氯镁石针对电熔镁砂是重要的工业原材料,其生产工艺简单,主要以氧化镁压球料为原料,采用电弧炉熔融法制备而成。
介绍了我国电熔镁砂制备工艺技术方面的研究成果,主要表现在选择适宜的化学添加剂改善镁砂的性能以及高效新工艺的开发。
1 我国电熔镁砂制备工艺及应用我国电熔镁砂制备优化工艺。
当前我国电熔镁产业仍在沿用电弧炉生产方式,技术装备相对落后,效率低,能源浪费严重,余热潜能流失严重;电熔镁砂生产过程中还存在着严重的粉尘污染,并大量排放二氧化碳,加重了大气温室效应,恶化周边环境。
现有电熔镁技术装备亟待更新换代,现有工艺急需创新,因此,采用集成技术发展节能环保的新式电熔镁装备及制备工艺是发展电熔镁产业的重要选择。
近年来,国内的科技工作者在电熔镁砂的生产工艺方面进行了改进和优化,并取得了一定的成效。
电熔镁砂的生产工艺流程短而简单,但设备投入和资源消耗大。
我国电熔镁砂产业多采用电弧炉熔融天然菱镁矿石制备电熔镁砂,生产工艺技术装备落后,功率低、容量小、效率低、自动化程度低,生产出的电熔镁砂产品品位不高,导致镁资源利用率低,环境污染严重。
通过利用盐湖卤水与氨气反应后生成氢氧化镁在煅烧后生成轻质氧化镁,可以通过洗涤、过滤等方法有效地除去杂质离子,氧化镁的纯度高达99.9%,在较低温度下轻烧得氧化镁粉末,而后经一定压力压球,制取高纯电熔镁砂。
其中青海西部镁业有限公司目前正在建设一套3万吨/年高纯电熔镁砂项目,建成后将填补国内外由盐湖卤水制备的高纯Mg(OH)2中间体为原料生产高纯电熔镁砂生产工艺的空白。
电熔镁炉节能工程
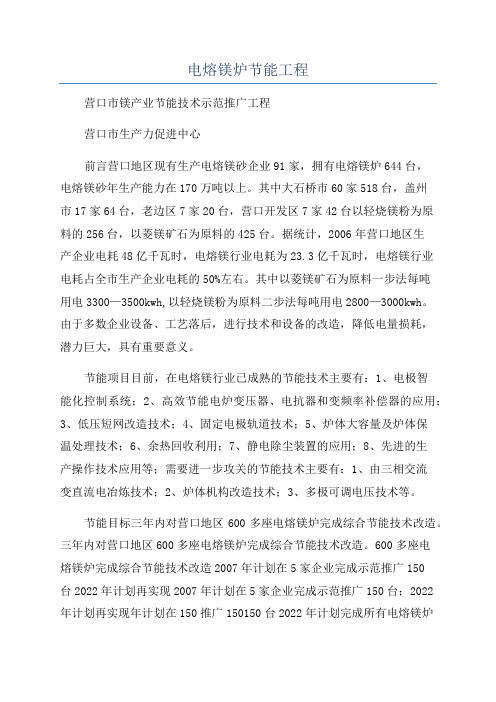
电熔镁炉节能工程营口市镁产业节能技术示范推广工程营口市生产力促进中心前言营口地区现有生产电熔镁砂企业91家,拥有电熔镁炉644台,电熔镁砂年生产能力在170万吨以上。
其中大石桥市60家518台,盖州市17家64台,老边区7家20台,营口开发区7家42台以轻烧镁粉为原料的256台,以菱镁矿石为原料的425台。
据统计,2006年营口地区生产企业电耗48亿千瓦时,电熔镁行业电耗为23.3亿千瓦时,电熔镁行业电耗占全市生产企业电耗的50%左右。
其中以菱镁矿石为原料一步法每吨用电3300—3500kwh,以轻烧镁粉为原料二步法每吨用电2800—3000kwh。
由于多数企业设备、工艺落后,进行技术和设备的改造,降低电量损耗,潜力巨大,具有重要意义。
节能项目目前,在电熔镁行业已成熟的节能技术主要有:1、电极智能化控制系统;2、高效节能电炉变压器、电抗器和变频率补偿器的应用;3、低压短网改造技术;4、固定电极轨道技术;5、炉体大容量及炉体保温处理技术;6、余热回收利用;7、静电除尘装置的应用;8、先进的生产操作技术应用等;需要进一步攻关的节能技术主要有:1、由三相交流变直流电冶炼技术;2、炉体机构改造技术;3、多极可调电压技术等。
节能目标三年内对营口地区600多座电熔镁炉完成综合节能技术改造。
三年内对营口地区600多座电熔镁炉完成综合节能技术改造。
600多座电熔镁炉完成综合节能技术改造2007年计划在5家企业完成示范推广150台2022年计划再实现2007年计划在5家企业完成示范推广150台;2022年计划再实现年计划在150推广150150台2022年计划完成所有电熔镁炉的技术改造任务年计划完成所有电熔镁炉的技术改造任务。
推广150台;2022年计划完成所有电熔镁炉的技术改造任务。
通过推广电熔镁炉节能技术及后续攻关技术的示范推广,推广电熔镁炉节能技术及后续攻关技术的示范推广,使营口地区379台电熔镁炉利用菱镁石一步法生产电熔镁砂的平均电耗由原来379台电熔镁炉利用菱镁石一步法生产电熔镁砂的平均电耗由原来3300千瓦时吨降低到3000千瓦时/千瓦时/3000千瓦时256台电熔镁炉利用轻烧的3300千瓦时/吨降低到3000千瓦时/吨,256台电熔镁炉利用轻烧粉二步法生产电熔镁砂的平均电耗由原来的2900千瓦时/2900千瓦时粉二步法生产电熔镁砂的平均电耗由原来的2900千瓦时/吨降低到2600千瓦时千瓦时/年节电量23亿千瓦时,节电率实现10%以上,10%以上2600千瓦时/吨,年节电量2—3亿千瓦时,节电率实现10%以上,电熔镁砂的高品位产品产率提升3%以上,综合效益可实现2.3亿元,3%以上2.3亿元熔镁砂的高品位产品产率提升3%以上,综合效益可实现2.3亿元,综合收益率提高15%以上。
电熔镁砂的冶炼工艺

电熔镁砂的冶炼工艺
镁砂是一种重要的工业原料,广泛用于冶金、化工等领域,是现代
化工、材料工程和新能源等领域的重要基础材料。
而电熔镁砂是常见
的冶炼方式之一,下面将对其工艺进行详细介绍。
一、材料准备
电熔镁砂的关键在于原料的选择和准备。
首先需要选用优质的镁矿石、电石以及煤焦油等作为原料,经过破碎、洗选等工序进行初步处理,
出料要求在12mm以下,含水量小于1.5%。
然后将这些原料按一定比
例混合均匀,为后续的熔炼工艺做好准备。
二、电炉操作
接下来需要将混合好的原料送入电炉进行熔炼。
电炉的加热方式一般
有电极加热和感应加热两种,其中电极加热是最常见的一种方式。
在
熔炼过程中需要控制电炉内的温度、压力等参数,保证熔化的原料达
到一定的浓度和纯度,同时要进行适当的调节,以确保熔体的质量符
合工艺要求。
三、炼制工艺
在电炉内熔化完成后,需要进行进一步的炼制工艺,包括炼铁、炼硅
等过程。
这些过程需要在一定的温度和压力下进行,同时需要控制炉
内气氛和炉膛中炉料的流动等参数。
通过这些炼制过程,可以将熔融的原料转化为高纯度的镁砂产品。
四、精炼工艺
最后一步是将产出的镁砂进行精炼处理,以提高其纯度和质量。
主要包括闪蒸、搅拌、过滤、冷却等过程。
这些过程需要严密控制,以保证产品的均匀性、质量等指标达到标准。
电熔镁砂的冶炼工艺是一个科学严谨的过程,需要有专业的设备和技术人员进行操作。
通过不断完善和创新,可以进一步提高生产效率和产品质量,为工业生产和发展做出更大的贡献。
电熔镁砂制备工艺及熔炼过程

电熔镁砂制备工艺及熔炼过程
电熔镁砂制备工艺及熔炼过程
作者:罗仙平;李建康;徐徽;王金庆;逯登琴;张贤
作者机构:青海西部矿业科技有限公司,青海西宁810006;青海省高原矿物加工工程与综合利用重点实验室,青海西宁810006;江西理工大学,江西赣州341000;青海西部镁业有限公司,青海德令哈817099;青海西部镁业有限公司,青海德令哈817099;青海省高原矿物加工工程与综合利用重点实验室,青海西宁810006;江西理工大学,江西赣州341000;青海西部矿业科技有限公司,青海西宁810006;青海省高原矿物加工工程与综合利用重点实验室,青海西宁810006;青海西部镁业有限公司,青海德令哈817099;青海西部矿业科技有限公司,青海西宁810006;青海省高原矿物加工工程与综合利用重点实验室,青海西宁810006
来源:盐业与化工
ISSN:1673-6850
年:2016
卷:045
期:008
页码:8-13
页数:6
中图分类:TQ132.2
正文语种:chi
关键词:电熔镁砂;制备;熔炼;菱镁石;水氯镁石
摘要:电熔镁砂是重要的工业原材料,其生产工艺简单,主要以菱镁石为原料,采用电弧炉熔融法制备而成.文章介绍了我国电熔镁砂制备工艺技术方面的研究成果,主要表现在选择适宜的化学添加剂改善镁砂的性能以及高效新工艺的开发.并以青海西部镁业生产的高纯氢氧化镁中间体作为原料,继续加工煅烧生产电熔镁砂产品的制备工艺进行了举例说明.在此基础上,分析了电熔镁砂熔融、结晶过程,主要是Si、Al、Ca、
Fe等杂质成分的迁移规律以及熔炼温度对MgO结晶。
大结晶电熔镁砂生产工艺

大结晶电熔镁砂生产工艺
大结晶电熔镁砂生产工艺是采用高温电熔技术将镁质原料经过一系列的炼铁流程,包括矿石的选矿、破碎、筛分、粉碎和磨细等步骤,最终形成含镁Oxide的粉末。
工艺流程如下:
1.原料选矿:对采集的矿石进行筛分、洗选去杂等步骤,确保矿石的质量。
2.矿石粉碎:将选矿后的矿石进行粉碎处理,使之成为粉状物料,便于后续炉子处理。
3.磨细:将粉状物料进行磨细,提高其表面积,使之更容易熔化。
4.电炉熔炼:将磨细后的镁砂放入电炉中进行熔炼,控制温度和氧化还原条件,使得镁元素被还原为纯镁。
5.结晶:将熔融的镁质原料从电炉中倒出,经过冷却结晶形成大块的电熔镁砂。
6.粉碎:将大块的电熔镁砂进行破碎和粉碎,使之成为符合要求的指定粒度的细粉末。
7.包装:将粉末装入包装袋中,进行分装和存储,并做好相关的质量监控,确保产品的质量安全。
在大结晶电熔镁砂生产工艺中,需要严格控制熔炼的温度、还原条件和结晶速度,以确保生产出高质量的电熔镁砂产品。
同时,对熔融过程中样品的取样、分析和检测也是一项重要的工作,这可以帮助调整工艺条件和保持生产的稳定性。
电熔镁生产工艺流程

电熔镁生产工艺流程
电熔镁的生产工艺流程主要分为原料制备、电熔过程和成品处理三个阶段。
1. 原料制备:首先需要选取高纯度的镁矿石作为原料。
将镁矿石进行粉碎,然后经过选矿和磁选等工艺处理,使得原料中的杂质和有害元素得到去除,得到纯度较高的镁砂作为电熔镁的主要原料。
2. 电熔过程:将镁砂放入电炉内进行熔炼。
电炉采用直流电弧熔炼技术,通过直流电流产生的高温和熔融电极间的电弧,使镁砂熔化成为液态镁。
同时,在电炉中加入适量的熔剂,以提高熔点和流动性。
通过控制电炉的温度和熔化时间,使得镁砂中的杂质和有害元素得到剔除,并通过重新晶化和沉淀等过程,使得镁液纯度进一步提高。
3. 成品处理:将熔融的镁液从电炉中倒出,经过除杂、过滤、冷却等工艺处理,得到电熔镁的成品。
成品根据不同的要求可以采取不同的加工方式,如浇铸成型、挤压成型等,最终得到符合要求的电熔镁产品。
需要注意的是,上述流程是典型的电熔镁生产工艺流程,具体的工艺参数和工艺流程会根据不同的生产厂家和产品要求而有所差异。
电熔镁生产工艺流程
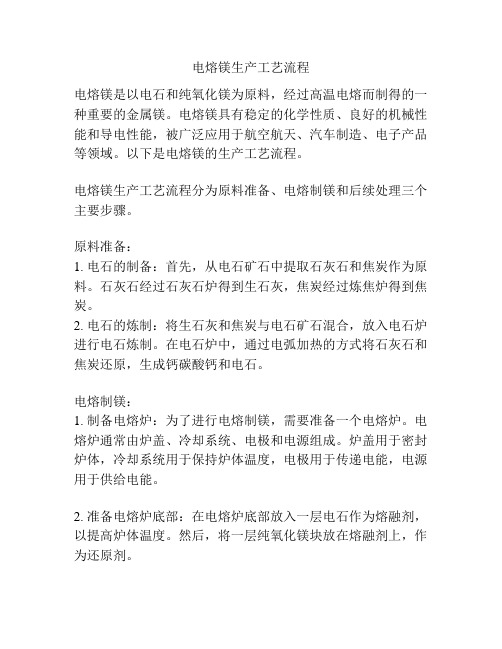
电熔镁生产工艺流程电熔镁是以电石和纯氧化镁为原料,经过高温电熔而制得的一种重要的金属镁。
电熔镁具有稳定的化学性质、良好的机械性能和导电性能,被广泛应用于航空航天、汽车制造、电子产品等领域。
以下是电熔镁的生产工艺流程。
电熔镁生产工艺流程分为原料准备、电熔制镁和后续处理三个主要步骤。
原料准备:1. 电石的制备:首先,从电石矿石中提取石灰石和焦炭作为原料。
石灰石经过石灰石炉得到生石灰,焦炭经过炼焦炉得到焦炭。
2. 电石的炼制:将生石灰和焦炭与电石矿石混合,放入电石炉进行电石炼制。
在电石炉中,通过电弧加热的方式将石灰石和焦炭还原,生成钙碳酸钙和电石。
电熔制镁:1. 制备电熔炉:为了进行电熔制镁,需要准备一个电熔炉。
电熔炉通常由炉盖、冷却系统、电极和电源组成。
炉盖用于密封炉体,冷却系统用于保持炉体温度,电极用于传递电能,电源用于供给电能。
2. 准备电熔炉底部:在电熔炉底部放入一层电石作为熔融剂,以提高炉体温度。
然后,将一层纯氧化镁块放在熔融剂上,作为还原剂。
3. 导入原料:将电石块加入电熔炉中,使其与纯氧化镁块接触。
通过电能供应,加热石灰石和焦炭,使其反应并释放出一氧化碳。
4. 进行电熔:启动电源,使电能通过电极传递到电熔炉中,产生强大的电弧。
电弧的高温状态将纯氧化镁和一氧化碳加热到极高温度,使它们发生还原反应生成金属镁。
5. 分离杂质:在电熔过程中,金属镁会与一些杂质如氯、铁、铝等发生化学反应。
为了提高金属镁的纯度,需要对熔体进行分离杂质处理。
这通常通过注入氩气等惰性气体来提取杂质。
后续处理:1. 浇铸:将电熔后的金属镁倒出炉体,借助浇注设备将其注入到模具中,进行形状定型。
2. 冷却:待金属镁冷却固化后,将模具拆除,得到金属镁块或其他所需形状的产品。
3. 加工:对固化后的金属镁进行表面处理、切割、打磨等加工工序,使其达到产品要求的尺寸、形状和表面光洁度。
总结:电熔镁的生产工艺流程包括原料准备、电熔制镁和后续处理三个主要步骤。
电熔镁砂产品单吨能耗混合预报模型

第39卷第12期自动化学报Vol.39,No.12 2013年12月ACTA AUTOMATICA SINICA December,2013电熔镁砂产品单吨能耗混合预报模型吴志伟1柴天佑1,2吴永建1摘要产品的单吨能耗是反映电熔镁砂熔炼过程产品产量和能耗的综合生产指标.通过分析炉内电热转换关系,利用能量守恒原理建立了产品单吨能耗模型.针对模型的未知非线性和参数时变等综合复杂性提出了由基于机理分析的单吨能耗主模型和基于神经网络的补偿模型组成的产品单吨能耗混合预报模型.其中神经网络补偿模型用于补偿模型的未知非线性和参数不确定性对于预报模型准确性的影响.采用某电熔镁砂熔炼过程实测数据验证了所建立的混合预报模型是有效的.关键词电熔镁砂,单吨能耗,预报模型,能量守恒,神经网络引用格式吴志伟,柴天佑,吴永建.电熔镁砂产品单吨能耗混合预报模型.自动化学报,2013,39(12):2002−2011DOI10.3724/SP.J.1004.2013.02002A Hybrid Prediction Model of Energy Consumption Per Ton for Fused MagnesiaWU Zhi-Wei1CHAI Tian-You1,2WU Yong-Jian1Abstract Energy consumption per ton is a main index of product quality and energy consumption in the smelting process of fused magnesia.By analyzing the electric heating conversion principle,an energy consumption per ton model of product is proposed by using the law of conservation of energy.For the complex characteristics such as unknown nonlinear and time-varying parameters of the energy consumption per ton model,a hybrid prediction model of energy consumption per ton which consists of a main model based on mechanism analysis and a compensation mode based on neural network is also proposed.The compensation model compensates the modeling errors caused by unknown nonlinearity and uncertainty of some parameters for the mathematical model.Industrial applications show the usefulness and effectiveness of the proposed hybrid prediction model for energy consumption per ton.Key words Fused magnesia,energy consumption per ton,prediction model,conservation of energy,neural network Citation Wu Zhi-Wei,Chai Tian-You,Wu Yong-Jian.A hybrid prediction model of energy consumption per ton for fused magnesia.Acta Automatica Sinica,2013,39(12):2002−2011电熔镁砂是一种高纯度的晶体氧化镁,具有熔点高、抗氧化、结构完整、绝缘性强等特性,是冶金、化工、建材等行业高温炉窑不可缺少的耐火材料.生产电熔镁砂的原料为菱镁矿石(主要成分为碳酸镁),熔炼设备为三相交流电熔镁炉.熔炼过程中,电熔镁炉将电能转化为热能,使炉内原料受热熔化形成氧化镁熔液,熔液经过冷却后结晶,最终的成品为氧化镁含量在95%以上的晶体.电熔镁砂的熔炼过程中电能消耗巨大,每熔炼一个炉次需耗电20000千瓦时,电能成本占整个生产成本的60%以上,因此如收稿日期2012-05-14录用日期2012-10-10Manuscript received May14,2012;accepted October10,2012国家自然科学基金(61020106003,61004009),国家重点基础研究发展计划(973项目)(2009CB320601)资助Supported by National Natural Science Foundation of China (61020106003,61004009)and National Basic Research Program of China(973Program)(2009CB320601)本文责任编委姜斌Recommended by Associate Editor JIANG Bin1.东北大学流程工业国家重点实验室沈阳1108192.东北大学自动化研究中心沈阳1108191.State Key Laboratory of Integrated Automation for Process Industries,Northeastern University,Shenyang1108192.Research Center of Automation,Northeastern University, Shenyang110819何合理利用电能是电熔镁砂生产企业最关心的问题.熔炼过程中反映单位产品产量电能利用效率的指标是产品单吨能耗,即每生产一吨合格产品所消耗的电能.电熔镁砂熔炼过程是一个批过程,单吨能耗为一个完整熔炼过程所消耗的总电能与获得的总产量的比值,一个熔炼批次对应一个单吨能耗值.由于产量只能在熔炼过程结束后通过化验获得,所以单吨能耗无法在线检测.当检测到一个熔炼过程的实际单吨能耗时,该熔炼过程已经结束,利用实测的单吨能耗值来指导电熔镁砂生产存在滞后问题.因此建立单吨能耗预报模型成为电熔镁砂熔炼过程控制的关键问题.近些年来部分学者开展了关于电熔镁砂熔炼机理的研究,并取得了一些成果.其中文献[1−2]分析了温度场对电熔镁砂晶体生成的影响;文献[3]介绍了电炉的效能、电热理论的基础以及不同类型的电炉及其在工业中的应用;文献[4−5]研究了电熔镁炉的理论热耗和热平衡问题.上述这些文献对研究电熔镁砂熔炼过程机理具有一定贡献.电熔镁砂熔炼过程中用于熔化原料、生成产品的热能完全由输12期吴志伟等:电熔镁砂产品单吨能耗混合预报模型2003入炉内的电能转化得到.在熔炼电压和熔炼总时长固定的工艺要求下,熔炼过程中三相电极电流值的大小直接影响最终产品的单吨能耗.熔炼电流过大时会造成能量的浪费,导致产品单吨能耗过高.熔炼电流过小时虽然消耗的电能相对较少,但是由于能量供应不足,造成产品产量低,最终同样导致产品的单吨能耗高.由于电熔镁砂生产过程电流与电弧之间、电弧与原料熔化之间机理复杂,加之产品产量与产品单吨能耗数据只能在熔炼过程完成后方能获得,因此如何建立单吨能耗预报模型,进而在一个批次的熔炼过程中指导生产是一个需要解决的科学问题.采用机理建模方式获得熔炼电流和产品单吨能耗数据之间的关系不同于传统的针对输入和输出响应曲线的系统建模,具有一定难度.目前还没有发现针对上述建模问题的研究.为了研究上述建模问题,进而提高电熔镁砂熔炼过程中电能的利用效率,本文将机理建模和数据建模方法相结合,建立了由基于熔炼机理分析的单吨能耗预报主模型和基于神经网络的建模误差补偿模型组成的单吨能耗混合预报模型.通过与国内某电熔镁砂生产过程的实际数据相比较,验证了所建立的单吨能耗混合预报模型精度能够满足实际要求.1电熔镁砂熔炼过程简介电熔镁炉是一种典型的高耗能设备,主要是将电能转化为热能,熔化物料、生成产品,其基本结构如图1所示.熔炼过程中电极与原料之间形成电弧,电弧放热熔化原料形成熔池.随着原料的投入和熔化,熔池上涨,控制系统通过控制电机转动来不断调整电极位置,目的是使电弧长度维持在一定范围,尽量保证电弧电阻恒定,进而确保熔炼电流跟踪电流设定值.随着熔炼过程的进行,熔池不断上涨,当熔池上升到炉口上表面时,熔炼过程结束.熔炼过程结束后,通过底车将炉体拖离熔炼工位,自然冷却.冷却过程中熔液完全结晶,再经过人工破碎、分拣,最后形成产品.电熔镁砂熔炼过程采用恒电流控制方式,被控变量为三相熔炼电流值.控制系统通过控制拖动电机转动、改变电极位置的手段来实现控制熔炼电流.熔炼过程中电能的消耗是固态原料熔化所需热量的主要来源.通常条件下,熔炼过程中三相电极的相电压和熔炼时间是固定的,因此熔炼电流值的大小是决定一个熔炼批次产品单吨能耗指标的重要因素.电流值过小,将导致输入电熔镁炉的热量不足,炉内缺少足够的热量熔化固体原料,造成产品产量低、质量差.此时虽然消耗的总电量少,但由于产量低导致产品的单吨能耗高,电能利用率低.随着熔炼电流增大,输入炉内的热能增加,熔炼过程所能熔化的原料量增加,产品产量也随之增加,产品单吨能耗降低.但由于一个熔炼批次内的产品产量不仅取决于其吸收热量的多少,还与原料填充方式、炉体容量等因素相关,因此单吨能耗不会随着熔炼电流的增大而单调减小.当产品产量达到一定阈值后,即使熔炼电流继续加大,产量也不会增加.因此,若熔炼电流过大,虽然保证了产品产量,但能量消耗大,同样导致产品的单吨能耗高,电能浪费严重.综上,研究熔炼电流与产品单吨能耗之间关系,实现在熔炼过程中利用熔炼电流对该批次单吨能耗进行预报是提高电熔镁砂熔炼过程能源利用效率的有效手段.图1电熔镁炉基本结构Fig.1Diagram of fused magnesium furnace2熔炼过程产品单吨能耗模型熔炼过程产品的单吨能耗J为消耗的电能与产品产量的比值,因此建模过程首先建立产量m的数学模型,在此基础上在建立单吨能耗模型.2.1产品产量模型产品产量m取决于整个熔炼过程中能够被熔化的原料量,因此产量m与熔炼电流I以及熔炼过程中原料的加料时间间隔 t a相关,可表示为m=f(I, t a).熔炼过程中大量电能被转化为热能,这些热能除了被用于熔化原料外还有一部分以各种不同方式被散失掉,整个熔炼过程的热平衡如图2所示.其中原料熔化吸热为原料的理论热能单耗与产品产量的乘积,输入热能与电弧耗散能量之差即为电弧输入炉内的电能.图2电熔镁炉热平衡图Fig.2The thermal equilibrium for fusedmagnesium furnace2004自动化学报39卷由现场热工测试结果可知,熔炼过程设备热损耗包括炉体散热、废气带走热、皮砂及散砂吸热、供电系统热损耗等[4].根据能量守恒原则,熔炼过程中应存在如下关系:(输入热能−电弧耗散能量)−设备热损耗=理论热能单耗×产品产量.由于电熔镁炉设备热损耗形式复杂,传导、对流、辐射三种换热方式同时存在,难以表达,因此本文引入电熔镁炉综合热效率这一参数.综合热效率表示原料熔化所吸收的热量占输入炉内电能的比值,于是上述能量守恒关系可以表达成式(1)的形式[6−7].fα(α)×(P−P0)=B t d m(1)其中,fα(α)为描述综合热效率α变化规律的函数;P=I2/G表示电弧输入功率;P0=k1G−βL表示电弧耗散功率;G表示电弧电导;L表示电弧长度;B t表示理论热能单耗;d m表示单位时间内熔炼出的产品质量;k1,β为可调参数,其取值受电极材质、直径以及原料导电性等因素影响.熔炼过程中所发生的化学反应如图3所示[3].图3电熔镁砂熔炼过程的化学反应Fig.3The chemical equation for smelting process offused magnesium furnace电熔镁砂熔炼过程的化学反应实际是沿实线箭头所示的途径进行,但是已有文献中只给出了标准生成热HΘ289,因此只能认为反应沿虚线箭头所示途径进行.根据盖斯定律(盖斯定律:定压或定容条件下的任意化学反应,在不做其他功时,不论是一步完成的还是几步完成的,其热效应总是相同的),两种途径的热效应相等.于是可以认为熔炼过程是MgCO3在298K时分解,产生的CO2加热到1000K,而MgO加热熔化并且过热到3150K.整个熔炼过程中熔化原料的能量为:Q= Q1+Q2+Q3+Q4,其中Q1表示MgCO3分解吸热;Q2表示加热CO2的热,Q3表示加热MgO 的热,Q4表示熔化潜热.各部分具体为Q1=∆H=−(−601)+(−394)−(−1112)= 117000kJ/kmolQ2=1000298C c d T c=1000298(44.14+0.00904T c−8.54×105T−2c)d T c=33093kJ/kmol其中,C c表示CO2的比热容;T c表示炉内温度.Q3=3150298C m d T c=3150298(48.99+0.00314T c−11.72×105T−2c)d T c=151480kJ/kmol其中,C m表示MgO的比热容,随温度变化.为了简化计算,这里认为MgO的比热容在加热到熔点和过热到3150K时相同,即把两个加热阶段合并计算.Q4=77.4kJ/mol=77.4×103kJ/kmol至此可以得到Q=378973kJ/kmol,熔炼过程的理论热能单耗为B t=378973×10340.32=9.4×106J/kg(2)于是式(1)可以写成fα(α)(I2G−k1G−βL)=9.4×106d md m=fα(α)(I2G−k1G−βL)9.4×106kg(3)式(3)为单位时间内产品产量的表达式,其中电弧电导G是与熔炼电流I有关的函数.电熔镁砂熔炼过程原料是分批加入的,因此需要考虑不同加料时间间隔对产品产量的影响.设加料时间间隔为∆t a,在一个加料时间间隔内加入的原料量为D a.熔炼工艺要求D a为一个固定值,但实际生产过程很难确保D a恒定,本文用函数f Da(D a)来表示生产过程中D a的真实取值.理论上一个加料时间间隔内所生产出的成品产量为m∆ta=fα(α)(I2G−k1G−βL)∆t a9.4×106kg(4)通过分析电熔镁炉熔炼机理并结合式(3)和式(4)可以得到如下结论:单个加料时间间隔内的产品产量由熔炼电流I和加料时间间隔∆t a共同决定,其中熔炼电流的变化,会导致原料的熔化速度不同.当熔炼电流相对较小时,单个加料时间间隔内所能熔化的原料质量较小,投入的原料不能全部被熔化,相应的产量较小.随着熔炼电流的增大,单位时间内向炉内输入的能量随之增加,单个加料时间间隔内所能熔化的原料质量也会随着增加.但受原料投入量的限制,单个加料时间间隔内所能熔化的原料质量不会随熔炼电流的增大而一直增加,最大只能是单个加料时间间隔内加入的原料量f Da(D a),即投12期吴志伟等:电熔镁砂产品单吨能耗混合预报模型2005入的原料全部被熔化形成产品.因此,整个熔炼过程的产品产量(kg)为m=εfα(α)(I2G−k1G−βL)T9.4×106+(1−ε)T f Da(D a)∆t aς(5)其中,ς为原料投入产出比,由原料类型决定;T为一个熔炼批次的熔炼时间,通常为10小时;ε为产量系数,其取值为:当m∆ta <f Da(D a)/ς时,ε=1;当m∆ta ≥f Da(D a)/ς时,ε=0.式(5)所表达的含义为:在整个熔炼过程中,产品产量由熔炼电流I和加料时间间隔∆t a共同决定.当单个加料时间间隔内投入的原料不能被全部熔化时,产量随熔炼电流的变化而变化,即m=fα(α)(I2/G−k1G−βL)T/9.4×106;当单个加料时间间隔内投入的原料能够被全部熔化时,产量不再由熔炼电流所决定,而是由单个加料时间间隔决定,即m=T f Da(D a)/∆t aς,此时整个熔炼过程的产品产量与单个加料时间间隔成反比关系,加料时间间隔越小,产量越大.当然,受炉体容量的限制,产量不会无限增大.式(5)中的电弧电导G=V I/(A+BL)2,其中V表示电弧电压,A表示阴极和阳极区电压降;B表示弧柱电压梯度[3,8].在变压器档位固定的情况下,电弧弧长L与电流呈反比的关系,可设L=C/I,C 表示弧长系数,于是有G=V I/(A+BC/I)2.电弧电压V与电熔镁炉内电热转换电路中各部分电阻的大小有关[8−10].图4所示为炉内电热转换电路的示意图[3],其中R m.A为电弧电阻(Ω),R m.B 为熔池电阻(Ω),R n为两电极间的料层电阻(Ω).炉子为三相供电,为简化问题,设三相功率平衡.图4炉内电热转换电路Fig.4Electric heating conversion circuit for fusedmagnesium furnace对于电熔镁炉,料层电阻可视为无穷大,即角接电路可看作开路.电弧电阻R m.A是矿热炉计算的重要参数,由于影响因素很多,尚无可靠的定量关系式,只能用实验得到的关系式R m.A= f m.A(ρm.A)/πd表示,其中f m.A(ρm.A)是描述电弧电阻率ρm.A在整个熔炼过程中变化规律的非线性函数,d为电极直径.上式不是理论推导式,只适用于埋弧.该式虽无严格理论证明,但是量纲的因次关系正确.熔池电阻R m.B为电极末端与底层间的电阻,可由欧姆定律的微分形式导出,具体推导如下[3]:∵d U m.B=−E m.B d r=f m.B(ρm.B)I2πr2d rU m.BU0d U m.B=−f m.B(ρm.B)I2πlr0d rr2U m.B−U0=f m.B(ρm.B)I2π(1r0−1l)∴R m.B=f m.B(ρm.B)πd(1−r0l)(6)其中,E m.B表示与电极中心线距离为r处的电场强度(V/m),U0表示电极侧表面电压(V).由上式可知,R m.B与描述熔池电阻率ρm.B化规律的非线性函数f m.B(ρm.B)成正比,与电极直径d(0.25m)成反比,与(1−r0/l)成正比.其中,r0为电极半径(0.125m),l为熔体层深度(m).熔炼过程稳定进行时,根据经验l约为1.5m.结合图4和式(6)可得电弧电压V.V=100R m.A√3(R m.A+R m.B)=100f m.A(ρm.A)√3(f m.A(ρm.A)+f m.B(ρm.B)(1−r0l))=100f m.A(ρm.A)√3(f m.A(ρm.A)+0.92f m.B(ρm.B))(7)结合式(2)∼(7)可得一个熔炼批次内的产品产量m的模型,如式(8)所示.2.2产品单吨能耗模型炼炼过程消耗的电能E可表示为E=√3UI cosϕT,其中U表示熔炼电压,根据工艺要求,熔炼电压为一固定值,通常为100V;cosϕ表示供电系统的功率因数.产品单吨能耗可表示为式(9)2006自动化学报39卷所示形式:m =εf α(α)(I 2/G −k 1G −βL )T 9.4×106+(1−ε)T f D a (D a )∆t a ς=εf α(α){(AI +BC )2V I −k 1[V I(A +BC/I )2]−βC I}T 9.4×106+(1−ε)T f D a (D a )∆t a ς(8)J =E m =√3UI cos ϕT m(9)当模型被用于单吨能耗在线预报时,式(9)中电能E 的表达式可改写为E =W i (t )+√3U cos ϕI (t )(T −T s )(10)其中,W i (t )表示当前时刻已经消耗的电能,为实测值;I (t )表示当前时刻之前的电流平均值;T s 表示熔炼过程已进行的时间.熔炼过程中电流值会在一定范围内波动,若仅根据当前时刻的电流值对单吨能耗进行预报会导致相邻两个预报周期内的预报值大幅波动.因此,为保证预报值的平滑性,用于计算总能耗和产量的电流值I (t )选取之前时刻的电流平均值.用于预报的总能耗为当前时刻之前的实际能耗测量值W i (t )与剩余熔炼时间内的能耗估计量√3U cos ϕI (t )(T −T s )之和,这样随着熔炼过程的进行,总能耗E 将越来越趋近于真实值.将式(8)和(10)代入式(9),整理可得如式(11)所示的产品单吨能耗模型(kWh/t).2.3单吨能耗模型的特性分析电熔镁砂熔炼过程中炉内反应剧烈且边界条件波动,影响产品产量的某些参数在实际熔炼过程中不可避免地会产生波动:受环境温度、熔炼电流、炉内皮砂厚度、料层厚度等因素的影响,每一批次的熔炼过程中热能散失量并不相同,这就导致综合热效率α会在一定范围内波动;由于原料的添加目前还采用人工手动添加的方式,虽然生产企业对单个加料时间间隔内加入的原料量D a 做出了要求,但是受主观因素的影响,工人无法保证每次加入的原料量恒定不变;电弧产生于电极下端与熔池上表面之间,熔池呈沸腾状态,导致电弧长度随机变化,电弧电阻率ρm.A 也会随之波动;原料主要是被电弧放出的热量所熔化,但同时也存在部分未完全熔化的原料落入熔池后再被熔化.这种现象导致了熔池电阻率ρm.B 会产生小范围波动.受电熔镁炉熔炼工艺的限制,参数α,D a ,ρm.A 和ρm.B 均不能在线测量,且波动具有很强的随机性,因此描述上述参数变化特性的非线性函数f α(α),f D a (D a ),f m.A (ρm.A )和f m.B (ρm.B )无法用精确的数学式表达,单吨能耗模型(11)不能直接应用于实际的单吨能耗预报过程.3单吨能耗混合预报模型3.1基于机理分析的单吨能耗预报主模型式(11)所示的单吨能耗模型中存在无法用精确数学式描述的参数,为了使其能够应用于实际的单吨能耗预报,预报模型建模过程需要利用固定的近似值来代替上述不确定的时变参数.本文将单吨能耗模型中的时变参数f α(α),f D a (D a ),f m.A (ρm.A )和f m.B (ρm.B )利用通过过程数据和经验选取的固定值α,D a ,ρm.A 和ρm.B 代替,得到了如式(12)所示的基于机理分析的单吨能耗预报主模型.J =W i (t )+√3U cos ϕI (t )(T −T s )εf α(α)(AI +BC )2V I −k 1 V I(A +BC I )2 −βC I T9.4×106+(1−ε)T f Da (D a )∆t a ς(11)J main =W i (t )+√3U cos ϕI (t )(T −T s )εα (AI +BC )2V I −k 1V I (A +BC I )2 −βCI T 9.4×106+(1−ε)T D a∆t a ς(12)其中V =100ρm.A√3(ρm.A +0.92ρm.B ),ε=1,m ∆t a <D aς0,m ∆t a ≥D aς.12期吴志伟等:电熔镁砂产品单吨能耗混合预报模型20073.2神经网络误差补偿模型单吨能耗预报主模型利用固定参数代替产品单吨能耗真实模型(11)中的时变参数,这导致预报主模型与真实模型之间必然存在如式(13)所示的建模误差:∆J=J−J main(13)为了消除∆J对预报准确性的影响,本文采用过程数据建立误差补偿模型.在基于数据的建模方法中,神经网络具有通过学习逼近任意非线性映射的能力,在非线性系统建模方面取得了较好的应用效果,因此本文采用神经网络技术对单吨能耗预报主模型的非线性建模误差部分进行补偿.目前,非线性系统辨识领域广泛应用的是前馈BP神经网络,虽然从理论上讲,三层以上的BP网络能够逼近任何非线性函数,但从其本质上讲,BP 网络所能实现的只是一一对应的静态非线性映射关系,不适合动态系统的实时预报.本文的神经网络误差补偿模型选用ELMAN神经网络[11−13],ELMAN 神经网络区别于BP网络的特点在于其承接层结点的存在.ELMAN神经网络能够通过隐含层内部的自反馈,把系统的动态直接包含于网络结构中,无需了解系统的阶数,就能学习非线性动态系统,适合于动态系统的实时预报.ELMAN神经网络一般分为输入层、隐含层、承接层和输出层.其中输入层、隐含层和输出层的连接类似于BP网络,承接层用来记忆隐含层单元前一时刻的输出值,可以认为是一个一步延时算子,其非线性状态空间表达式为x(k)=f(w1x c(k)+w2u(k−1))x c(k)=γx x c(k−1)+x(k−1)y(k)=g(w3x(k))(14)其中,y,x,u,x c分别为m维输出结点向量、n维隐层结点向量、r维输入向量和n维反馈状态向量; w1,w2,w3分别为承接层到隐含层、输入层到隐含层、隐含层到输出层的连接权重;γ为自连接反馈增益因子;g(·)为输出神经元的传递函数,是隐含层输出的线性组合;f(·)为隐含层神经元的传递函数.由式(14)可以看出,ELMAN神经网络考虑了隐含层节点的反馈,但没有考虑输出层节点的反馈.由于熔炼过程中电能的消耗为一个累加量,在利用单吨能耗的预报值来调整熔炼电流、指导实际生产时,之前时刻神经网络的输出y(k)直接影响式(12)中W i(t)的取值.因此本文根据电熔镁炉耗能特点,在文献[14−15]的基础上,对标准的ELMAN神经网络进行了改进.改进的ELMAN神经网络考虑了输出层节点的反馈,具有输出层-隐含层-输入层反馈机制,其结构如图5所示.图5改进ELMAN神经网络结构Fig.5Diagram of improved ELMAN neural network改进的ELMAN神经网络的非线性状态空间表达式为x(k)=f(w1x c(k)+w2u(k−1)+w4yc(k)) x c(k)=γ1x c(k−1)+x(k−1)yc(k)=γ2yc(k−1)+y(k−1)y(k)=g(w3x(k)+w5yc(k))(15)式中,w1,w2,w3,w4,w5分别为承接层1到隐含层、输入层到隐含层、隐含层到输出层、承接层2到输出层、承接层2到隐含层的连接权重;γ1为承接层1的自连接反馈增益因子;γ2为承接层2的自连接反馈增益因子.改进的ELMAN神经网络的误差函数如式(16)所示:e=12(y d(k)−y(k))T(y d(k)−y(k))(16)其中,y d(k)为目标值.改进的ELMAN神经网络的学习算法采用梯度下降法,各连接权重的修正式归纳如下:∆w1jl=ηmi=1(δ0iw3ij)∂x j(k)∂w1jlδ0ix j(k),j,l=1,···,n∆w2jq=ηδhju q(k−1),j=1,···,n;q=1,···,r∆w3ij=ηδ0ix j(k),i=1,···,m;j=1,···,n∆w4jl=ηmi=1(δ0iw3ij)∂x j(k)∂w4jl∆w5ij=ηδ0iy cj(k)δ0i=(y di(k)−y(k))g (·)δhi=mi=1(δ0iw3ij)f (·)(17)由式(15)可以看出,由于引进了输出层节点的2008自动化学报39卷反馈,通过权重w5使得网络的输出y(k)中直接包含了前一时刻网络输出的信息,提高了神经网络的学习能力.本文所建立的神经网络误差补偿模型输入层节点为4,输入量为之前时刻的电流平均值I(t)、加料时间间隔∆t a和生产边界条件(原料质量、原料粒度),输出层节点为1,输出量为单吨能耗预报主模型的建模误差∆J.在隐含层节点数的选择过程中需要考虑的一个问题是隐含层节点数对网络泛化性和过拟合现象的影响,这是神经网络误差补偿模型能够应用于实际单吨能耗预报的关键问题.隐含层节点数过小会导致网络训练困难、鲁棒性差、抗噪声能力不强,网络难以达到误差目标;隐含层节点数过大又会容易产生过拟合现象,使网络的泛化能力下降.为了兼顾网络的鲁棒性和泛化性等,本文在隐含层节点数的选取上采用了一种隐含层节点数自动生成的方法[16].该方法的设计思想是先设计一个仅含有一个隐含层节点的神经网络,在训练过程中根据误差目标及其下降的速率来确定是否增加一个隐含层节点,直到网络的训练达到误差目标.具体步骤如下:1)设定误差目标e;2)初始化网络结构,隐含层节点数设为n=1,初始化网络权重,计算误差函数e;3)利用训练数据对网络进行训练;4)计算误差函数e,同时利用验证数据进行验证误差e 计算,如果e<e则转到步骤7),否则继续下一步骤;5)如果验证误差e 未由减小转为增大,则到步骤3);如果验证误差e 由减小转为增大且比增加节点前更大,则到步骤7),否则继续下一步骤;6)生成新的隐节点数n+1,并为其设置权值,转到步骤3);7)网络学习结束,返回结果.隐含层节点数自动生成的方法能够获得一个最优的网络结构,但其缺点是迭代次数较多,占用计算资源较大.为解决这一问题,上述步骤2)中隐含层节点数的初始值可以根据实际情况选择一个稍大的数,这样可以减少网络的迭代次数,加快学习速度.4实验研究将本文建立的产品单吨能耗混合预报模型应用于电熔镁砂实际熔炼过程,建模过程共选择250组实际数据,其中50组数据用于预报主模型相关参数的选取,150组数据用于神经网络误差补偿模型的训练,50组数据用于神经网络模型的验证.混合预报模型中相关参数的确定方法如下:预报主模型中,综合热效率α的取值通过以往若干炉次的过程数据计算获得.具体方法为首先计算之前炉次生产过程中用于熔化原料所消耗的实际热能,即该炉次实际产量与理论热能单耗B t的乘积.再计算熔化原料所消耗的实际热能与该炉次实际消耗电能的比值即可获得该炉次的综合热效率.本文选择50个炉次的数据,计算每一炉次的综合热效率,将计算结果的平均值α=0.65作为预报主模型中α的取值;单个加料时间间隔内加入的原料量D a根据实际的生产现状取值为220kg;原料投入产出比ς根据以往50组实际生产数据统计获得,其取值为ς=1.63;电弧电阻率ρm.A和熔池电阻率ρm.B 根据文献[3],分别取值为0.005Ωm和1×10−6Ωm;电弧阴极和阳极区电压降A的取值由电极材料决定,石墨电极的实验值为30∼35V[3,17],通过实验测试,最终本文中A的取值为34V;弧柱电压梯度B在1∼10kA的低电流范围内为1000V/m,在40∼80kA大电流范围内为900∼1200V/m[3],电熔镁砂熔炼过程中电流值通常在8∼15kA,因此本文中B的取值为1000V/m;弧长系数C可以通过测量获得,具体方法为:以熔炼电流为10kA时为基准,手动下落电极同时观察电流值.当电流值发生大的突变时可以认为电极与熔池接触,电弧熄灭.记录电极的下降距离即为10kA时的电弧长度,测量实验的结果如表1所示.表1电弧长度测量值Table1The measured effect of arc length实验次数1234平均值A相(m)0.0430.0300.0340.0290.034B相(m)0.0350.0280.0390.0360.0345 C相(m)0.0370.0480.0320.0340.03775通过表1的测量结果可知10kA时的电弧长度约为35mm,则电弧系数C的取值为350.神经网络误差补偿模型中,隐含层神经元的传递函数选用双曲正切S型(Sigmoid)传递函数Tan-sig,输出层神经元的传递函数采用线性传递函数(purelin),训练目标为0.01.初始权重为绝对值小的数,本文选择[−1,1]之间的随机数.网络输入样本采用式(18)进行数据归一化处理.Y=C −C minC max−C min(18)其中,C 为未经处理的神经网络输入值;Y为经过平滑处理后的神经网络输入值;C max,C min为神经网络输入值的最大、最小值.在实际应用中,C max取实际最大输入值的1.25倍,C min取实际最小输入值的0.75倍.利用单吨能耗预报主模型可以获得如图6所示。
镁砂熔炼过程全厂电能分配实时多目标优化方法研究
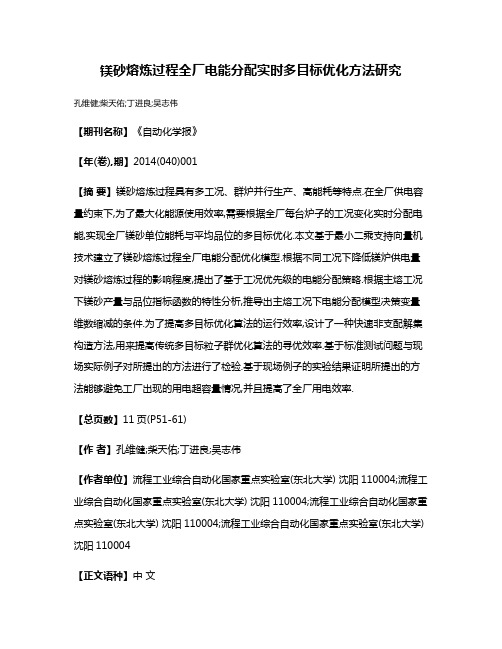
镁砂熔炼过程全厂电能分配实时多目标优化方法研究孔维健;柴天佑;丁进良;吴志伟【期刊名称】《自动化学报》【年(卷),期】2014(040)001【摘要】镁砂熔炼过程具有多工况、群炉并行生产、高能耗等特点.在全厂供电容量约束下,为了最大化能源使用效率,需要根据全厂每台炉子的工况变化实时分配电能,实现全厂镁砂单位能耗与平均品位的多目标优化.本文基于最小二乘支持向量机技术建立了镁砂熔炼过程全厂电能分配优化模型.根据不同工况下降低镁炉供电量对镁砂熔炼过程的影响程度,提出了基于工况优先级的电能分配策略.根据主熔工况下镁砂产量与品位指标函数的特性分析,推导出主熔工况下电能分配模型决策变量维数缩减的条件.为了提高多目标优化算法的运行效率,设计了一种快速非支配解集构造方法,用来提高传统多目标粒子群优化算法的寻优效率.基于标准测试问题与现场实际例子对所提出的方法进行了检验.基于现场例子的实验结果证明所提出的方法能够避免工厂出现的用电超容量情况,并且提高了全厂用电效率.【总页数】11页(P51-61)【作者】孔维健;柴天佑;丁进良;吴志伟【作者单位】流程工业综合自动化国家重点实验室(东北大学) 沈阳110004;流程工业综合自动化国家重点实验室(东北大学) 沈阳110004;流程工业综合自动化国家重点实验室(东北大学) 沈阳110004;流程工业综合自动化国家重点实验室(东北大学) 沈阳110004【正文语种】中文【相关文献】1.电熔镁砂制备工艺及熔炼过程 [J], 罗仙平;李建康;徐徽;王金庆;逯登琴;张贤2.考虑多影响因素的全厂机组间热电负荷动态优化分配方法研究 [J], 叶青;万杰;居国腾;赵佳骏;沈伟军;姚坤3.电熔镁砂熔炼过程带输出补偿的PID控制 [J], 王维洲;吴志伟;柴天佑4.航路资源协同分配的多目标优化方法研究 [J], 杨帆;田文;宋津津5.电熔镁砂熔炼过程电极电流饱和约束一步最优控制 [J], 富月;李宝因版权原因,仅展示原文概要,查看原文内容请购买。
- 1、下载文档前请自行甄别文档内容的完整性,平台不提供额外的编辑、内容补充、找答案等附加服务。
- 2、"仅部分预览"的文档,不可在线预览部分如存在完整性等问题,可反馈申请退款(可完整预览的文档不适用该条件!)。
- 3、如文档侵犯您的权益,请联系客服反馈,我们会尽快为您处理(人工客服工作时间:9:00-18:30)。
Vo. 0 No 3 13 .
Ma .2 】 v 01
冶 金 能 源
ENERCY FOR ALL MEI ' URGI CAL I NDUST RY
根据 上列反应 式及 有关热 化学 数据计 算理论 热 能单耗 ,结果 如表 1 。
表 1 电熔镁 砂 生产所 需的热 量及理 论 热能单耗
"
- -
28 7 .%
银 温度 计 ,秒 表 ,电 子 钟 ,皮 托 管 ,磅 秤 ,米 尺 ,气体 分析仪 ,万 能表 。 ( 电熔镁 炉生 产 的 原料 为菱 镁 矿 ( 4) 含
2 节能途 径
根据 能量 平衡 分析 可 以看 出 ,目前 电熔镁 砂
冶
金
能
源
Vo 0 No 3 L3 .
了成品率 ,并使工人的劳动条件也得到了改善。
3 结论
转化到生产结束后的电熔镁砣 内,总计约占电熔
s m pi n a d u to n h polto n Chn lu in i ia,te whoe fs d g e im n sr e d t p r d r e l . h l u e ma n su idu ty n e o u g a e u g nty
熔炼 时 间为 9 ,共 消耗 石墨 电极 3 0 g h 3 k ,消
耗菱 镁矿 1. t 生 电熔 镁砂 成 品 5 5 t 天 6 5 ,产 . 。每 生产 1个 坨 ,周 期 作 业 ,料 坨 周 边 有 皮砂 和散 砂 。 电 熔 镁 砂 牌 号 F 9 0 为 3 % ,F 9 0 为 M8 0 M7
炉 ,其 中原料为轻 烧粉 的炉子 4台 ,原料 为菱 镁
矿 的炉 子 4台。
( ) 电熔镁 电 弧 炉 的 操 作 过 程 为无 渣埋 弧 2 操作 ,基本熔 炼工 艺过 程是 :电熔 前 ,首先在 炉 内铺底 料 ,调整 电极位 置 ,起 弧 。起弧后 电流稳 定 即可 向电极附 近加料 ,其 中一部 分料 由电弧直 接熔化 ,在 电极下端 形成 熔池 ,一 部分料 落 入熔
池熔化 ,随着料 的投入 和熔化 ,熔 池面上 升 。先 前熔化 的熔 体逐 渐 因炉 体 散 热 降 温 而冷 凝 结 晶 , 在熔池 下形成 熔坨 。炉体 内 ,靠 近 炉壳周 边 的原 料不 能熔 化 , 自然 形 成 隔 热 层 起 到 隔 热保 温作 用 。随着熔 融时 间的延 长 ,熔 池 面上涨 ,一直 升
点高、 结构 致密 的碱性 耐火材料 , 被广泛地 应用于 冶金、 建材 、 玻璃 、 泥 、 防等领 域 。我 国菱镁矿 水 国 资 源丰 富 , 目前 已探 明储量 为 3 .4亿 t占世 界 56 , 总储量 的 2 . % , 世 界首 位 j 87 居 。其 中辽 宁 省 菱镁矿保 有储量 为 3. O5亿 t约 占全 国总储 量 的 ,
ቤተ መጻሕፍቲ ባይዱ
ENERGY F0R METAU URGI CAL I NDUS TRY
Ma . 0 1 v - 2 1
生产 由于粗放 的生 产 工艺 造 成 巨大 的能 量损 失 。 电熔镁 系统节 能的主要途 径是 回收 电熔 镁砣及 烟
变压器与 电熔镁炉 ,应 尽量使 电炉变压 器工作在
电熔镁 砂 是 以菱 镁矿 或 轻 烧 粉 ( O) 原 Mg 为
平衡 分析 , 从而找 出节能途径是 十分必要 的。 1 电熔 镁砂生产工 艺过程的热 平衡 1 1 电熔镁砂 生产的理论 热耗 . 电熔镁砂 生产 的理论 热耗是评价 炉子效能的
料, 在电弧炉内熔炼得到的。它是一种纯度高、 熔
摘 要 目前国内电熔镁砂生产工 艺落后,能耗 高、污染重 ,电熔镁产业亟待 战略 升级 。通
过对典型龟熔镁砂生产工艺现场测试及热平衡分析,提出了电熔镁砂生产的节能途径。节能
的主要途径是如何高效回收电熔镁砣高温余热和烟气余热 ,减少炉 口辐射热 损失 。
关键词 电熔镁 电弧炉 能量平衡 节能 余热 回收
基 本数据 ,也是炉 子热平衡计 算 的基础 。
8 %, 5 占世界总储量 的 2 %, 5 菱镁矿资源是我 国 重 要的战 略保 护 资源 。 目前 , 国内的 电熔 镁冶炼水 平低 , 生产设 备简 陋, 热工制度和操作规程主要凭经验确定 , 生产过 程主 要 靠 人 工 手动 控 制 , 能源 浪 费 、 环境 污 染 严
Ab ta t At rsn ,te po ut n tc n lg ffsd ma n s sb hn ih hg n ryCI sr c ee t h rd ci eh ooy o e g ei i e id wt ih e eg O * p o u a l
o n ry c n e v t n fe eg o s r ai .Ho f inl e y l se h a ffs d ma n su l mp a d f e g ss, o w t e % e t rc cewa t e t u e g e im u n u a e o i y o l
T r u h t eO1 i e t n h e ma a a c n y i fatp c x mp e l 1 8 d te me o s h g 1 一st ts a d te t r l ln e a a sso y ia e a l ,pD ) e t d o h e h b l l o h h
168Jk o 1 k / g=2 5 k h t 9 0 w /
熔 炼完 成后用小 车将 熔毕 的镁 砣连 同炉体拉
离 熔融 工位 , 自然 冷却 。然后 出炉 ,人工 破 碎 、 分级 ,包装成 品 。 ( ) 测试 仪 器 :热 电偶 ,光 学 温 度 计 ,水 3
( ) 电熔镁 砂 生产 的综合 热效率 : 3
Th r lp o e s a a y i n n r y c n e v to e ma r c s n l ss a d e e g o s r a n i o u e g e i o c i n ff s d ma n sa pr du to
T n ogun Z agWe u L Pn WagS ui o gY n ja hn i n j i eg n h a Z a ni 2 Y ogho hoWej g uH n ca n ( 。 hnU i r t o c n eadT cn l y 2 otes r nvr t) 1 Wu a nv s y f i c n eh o g , .N r at U i s y e i S e o h e n ei
4 % ,F 9 0为 2 % 。 5 M6 5
122 热平 衡计 算 ..
表 l计 算 结 果 是 按 M C ,在 10 K 分 解 , gO 00 将 M O过 热 10 [ g 0 1 时所得 。电熔 镁 砂生产 的理 论 : 热 能单耗是 2 3 Wh t 6 1 /。 k
n o o rd c e t s f h n c u h a e te man e e g o s rai t d . a d h w t e u et e h a o so e fr a e mo t r h i n r y c n e v t n me o s h l t u o h 1 (  ̄ o d f s d ma n sa a c fr a e te ma a a c e e g o s r ain w s e t e y l g r s u e g e i r u n c h r lb l e n ry c n ev t a t h a c ci n o e r n
菱镁矿石在电弧炉内熔炼发生了一系列物理 化学变化 ,从 固态 到液态 、冷凝再结 晶 j ,反
应如下 :
MC , g O 3 一
兰
M o 非晶体 ) c 2 ( ) g( + o t( 1 Mg 非 晶体 ) o ) o( +C 2 T
M o( g 晶体 )
Mg ( o 液体 )
Mg 非 晶体 ) o(
Mg 晶体 ) O(
() 2
() 3
( )式所得 的产品称为苛性镁砂 ,俗称轻 1 烧粉 ;( ) 式 为高 温 锻烧 过 程 ,所 得 产 品称 为 2 重烧镁砂 ;( )式是电熔镁砂生产的主要反应 , 3 M o在高 温下 液 化 ,经再 结 晶就 得 到 致 密 的方 g 镁 石结晶 ,即得 到 电熔镁砂 。
“ 济运行 ” 状态 ,此 时变 压器 的效 率 最高 ,可 经
显著节 电节 能。 目前 电炉 的电极 升降是靠人工手 动控制 , 由于在 熔 炼 时 电 极倾 斜 引起 极 心 圆改
气余热 ,减 少 炉 体外 表 面散 热 和炉 口辐 射 热损 失 ,降低 电能损失 。 由此 ,节 能的途径 可 以归纳
13 热 工 过 程 分 析 .
( ) 电熔镁 砂 生产 的实 际热能单 耗 : 1
l l3 J k 3 o k/ g=3 4 k 6 o WE/ £
到炉壳上 口表面,此时熔融过 程结束 ,停止供 电 。在 熔融过 程 中 ,要 随熔 池 面上涨 而不 断调整
电极上 升 。
( ) 电熔镁 砂 生产 的实 际电耗 : 2
M C 约 9 % ) gO 8 ,产 品为 大结 晶电熔 镁砂 。所 用
变 压 器 容 量 为 15 k A。石 墨 电 极 直 径 为 60 V
3 0mm 。 0
该 炉炉壳 由 l m 厚 的钢 板加工 而成 ,炉 壳 Om 直径 1 8 . m,高 度 2 5 . m。炉 口向上 敞开 。
为以下几 个方面 。 2 1 对 电熔镁砣余 热 回收 .
变 ,恶化炉 内热量分布 ,致 使局部皮 砂过厚 ,局 .
部熔 池连通不好 ,影响 了电熔 镁砂生产 质量 和产 量 。采 用 自动控制 ,不仅能节 电节能 ,同时提高