汽温控制系统
2 汽温控制系统

三、过热蒸汽温度的控制手段
现代大型锅炉最常采用的是: 现代大型锅炉最常采用的是:喷水 减温法。 减温法。 但是从理论上来讲在过热蒸汽内喷 水会引起熵增,导致系统做功能力 下降。但为了维持机组安全运行, 喷水减温是最简单有效的方法。因 而被广泛采用。
对采用喷水减温器的过热蒸汽温 度控制系统,有的机组只采用一 级减温,这种系统比较简单,但 因被控对象在基本扰动下的迟延 时间太长,往往在机组负荷变动 等扰动下蒸汽温度偏差较大。 目前大多数机组都采用二级喷水 减温控制方式
稳态时,减温器出口的汽温,即 导前汽温可能与原来的数值不同, 而主汽温一定等于设定值。
(二)具有导前微分信号的 控制系统
加入导前信号,它 能迅速反映扰动影 响,所以能有效地 克服扰动对主汽温 的影响。
动态 稳态
在控制过程中,调节器根据导前汽 温θ1 的微分信号和θ两个信号动作, 由于θ1 比θ提前反映减温水量扰动且 θ1 的微分信号能反映汽温的变化速 度,使调节器能实现提前调节作用。 因此出口汽温的动态偏差显著地减 小 在控制过程结束后,导前汽温不再 变化,其微分信号消失,PI调节器 能消除静态偏差,必使θ恢复给定值。
汽温的动态特性从哪几个方面衡 量? 过热汽温度控制的基本方案有哪 几种,分析其原理。 再热汽温控制的主要手段和辅助 手段分别是什么?
随着锅炉负荷的变化,其辐射吸热面和对 流受热面的吸热比例也会随之变化。
布置在对流 吸热区的过 热器,其出 口蒸汽温度 一般随负荷 的上升而上 升
布置在辐射 吸热区的过 热器,其出 口蒸汽温度 一般随负荷 的上升而下
现代大容量锅炉的过热器系统都采 取了对流式过热器、辐射式过热器 和屏式过热器(半辐射式)过热器 交替串联布置的结构。当锅炉蒸发 量增加时,过热器出口汽温上升。
300MW的机组过热汽温控制系统的设计解读
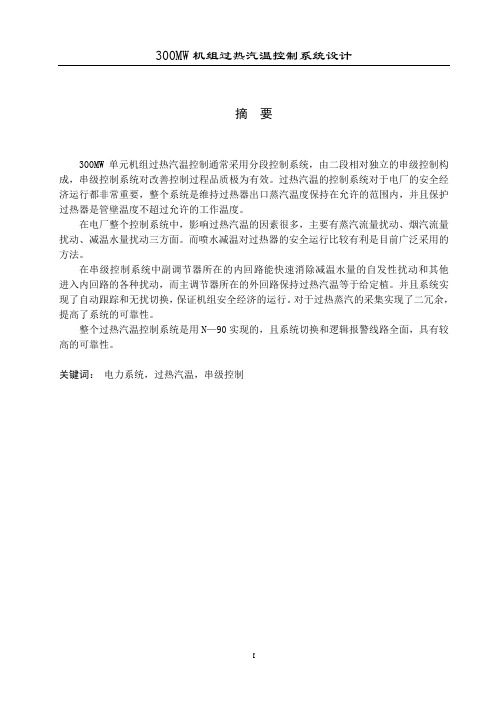
摘要300MW单元机组过热汽温控制通常采用分段控制系统,由二段相对独立的串级控制构成,串级控制系统对改善控制过程品质极为有效。
过热汽温的控制系统对于电厂的安全经济运行都非常重要,整个系统是维持过热器出口蒸汽温度保持在允许的范围内,并且保护过热器是管壁温度不超过允许的工作温度。
在电厂整个控制系统中,影响过热汽温的因素很多,主要有蒸汽流量扰动、烟汽流量扰动、减温水量扰动三方面。
而喷水减温对过热器的安全运行比较有利是目前广泛采用的方法。
在串级控制系统中副调节器所在的内回路能快速消除减温水量的自发性扰动和其他进入内回路的各种扰动,而主调节器所在的外回路保持过热汽温等于给定植。
并且系统实现了自动跟踪和无扰切换,保证机组安全经济的运行。
对于过热蒸汽的采集实现了二冗余,提高了系统的可靠性。
整个过热汽温控制系统是用N—90实现的,且系统切换和逻辑报警线路全面,具有较高的可靠性。
关键词:电力系统,过热汽温,串级控制I目录摘要 (I)1 引言............................................................... - 1 -2 DCS控制系统简介..................................................... - 2 -2.1分散控制系统的产生....................................................................................................................... - 2 -2.2分散控制系统结构........................................................................................................................... - 3 -2.2.1网络通信子系统................................................................................................................... - 3 -2.2.2过程控制子系统................................................................................................................... - 3 -2.2.3人机接口子系统(HMI) ..................................................................................................... - 4 -2.3分散控制系统(DCS)的特点............................................................................................................. - 5 -3 过热汽温控制系统概述................................................. - 7 -3.1过热蒸汽温度控制的意义和任务................................................................................................... - 7 -3.2被控对象动态特性分析................................................................................................................... - 7 -3.2.1锅炉负荷扰动下过热汽温的阶跃响应曲线 ....................................................................... - 8 -3.2.2烟汽热量扰动下过热汽温的阶跃响应曲线 ....................................................................... - 8 -3.2.3减温水量扰动下过热汽温的阶跃响应曲线 ....................................................................... - 9 -3.2.4减温水量扰动与负荷扰动或烟汽量扰动的比较 ............................................................... - 9 -3.2.5改善减温水量扰动下动态特性的方法 ............................................................................. - 10 -3.3常规过热汽温传统控制策略......................................................................................................... - 10 -3.4串级汽温调节系统.......................................................................................................................... - 10 -3.4.1过热汽温串级调节系统的组成................................................................................................. - 10 -3.4.2串级系统的结构和工作原理 ............................................................................................. - 11 -3.4.3主汽温串级控制系统原理................................................................................................. - 12 -3.4.4串级汽温调节系统的分析................................................................................................. - 12 -4 过热汽温的整定...................................................... - 14 -4.1串级控制系统方框图..................................................................................................................... - 14 -4.2过热汽温的参数整定..................................................................................................................... - 15 -5 SAMA图分析......................................................... - 17 -5.1控制系统SAMA图绘制............................................................................................................. - 17 -5.2控制系统SAMA图分析............................................................................................................. - 18 -结论................................................................. - 20 -参考文献............................................................... - 21 -II1 引言火力发电厂在我国电力工业中占有主要地位,是我国重点能源工业之一。
蒸汽温度自动控制系统

WT1S
1
1
时,1
21K
1
2.21K
;Ti1
T1K 1.2
WT1S
1
1
1
1 Ti1S
时,
(3)主、副回路投入后再作适当调整。
能源与动力工程学院 (二)衰减曲线法
步骤与临界曲线法略同,不同之处要注意!
串级控制系统产生共振效应的条件是:
1.副回路的工作频率ω2接近于共振频率ω; 2.主回路的工作频率ω1接近于副回路的工作频率ω2,即 T1P≈3T2P 。
实际生产中,通常把两种过热器结合使用,对流方式下吸收 的热量比辐射方式下吸收的热量要多,因此综合而言,过热器出 口汽温是随流量D的增加而升高的。
能源与动力工程学院
(2)动态特性 影响汽温变化的扰动因素很多,例如蒸汽负荷,烟气温度和
流速,给水温度,炉膛热负荷,送风量,给水母管压力和减温 水量。
归纳: 蒸汽流量,烟气传热量和减温水三个方面的扰动。 1)蒸汽流量扰动
能源与动力工程学院
(二)现场试验整定法
1、边界稳定法(临界曲线法) (1)先决定副调节器的比例带
主、副回路全部投入闭环,主调节器的参数设置:δ1置于较大位 置,Ti1=∞,Td1=0,副调节器的δ2 置于较大位置,且Ti2=∞,Td2=0, 而后便将副调节器的比例带由大往小调,使副回路产生不衰减振荡 (同时观察2),并记下此时的δ2K(临界比例带),T2K(振荡周 期),则副调节器的参数设置为:
2、锅炉过热汽温串级控制系统原理图
温度定值
主P调I1
副P调I2 执行器
内扰 阀门
θ2
减 导温前器区
过惰热性器区
θ1
变送器
变送器
串级过热汽温控制系统的分析与实现
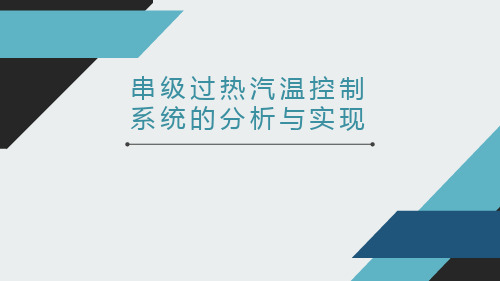
使汽轮机最后几级的蒸汽湿度增加,加速汽轮机叶片蚀
过热蒸汽温度过低
影响机组的安全运行
4
副控制器 接受主控制器的输出信号和减温器出口温度信号 ,副调节器的输出控制执行机构的位移,从而控制减温水调节阀门的开度。
主控制器 接受过热汽温信号 ,用于维持过热蒸汽温度,使其等于给定值;
5
串级过热汽温控制系统由内、外两个闭合的控制回路构成
内回路的任务是尽快消除减温水量的自发性扰动和其他进入内回路的各种扰动,对过热汽温的稳定起粗调作用,副控制器一般可采用P或PD控制器。
8
外回路分析
1.系统的动态特性
只要在主汽温偏离给定值时,由主控制器就发出校正信号 ,通过副控制器及执行器改变减温水量,使过热汽温最终恢复到给定值。其控制过程可表示为
外回路的任务 :
控制器的输入偏差信号增加时输出也增加,则选择控制器为正作用或标“INC”;若控制器输入偏差信号增加时输出减小,则选择控制器为“反作用”或标“DEC”。
ቤተ መጻሕፍቲ ባይዱ
10
THANKS
2
中压过热汽温度比额定值高25~40℃
改变过热器入口蒸汽温度的方法
喷水式减温表面式减温
因被控对象在基本扰动下的迟延时间太长,往往在机组负荷变动等扰动下蒸汽温度偏差较大。目前大多数机组都采用二级喷水减温控制方式。
过热蒸汽温度过高
容易烧坏过热器
会降低全厂的热效率
一般蒸汽温度每降低5~10℃热效率约降低1%
主控制器可采用PI或PID控制器
保持过热汽温等于给定值
9
对主控制器来说:当输入偏差 增加时,输出 减小,则主控制器的正反作用开关置于“反作用”位置。
依据控制器入口信号的接线极性来确定控制器正反作用开关的位置,从而保证系统中内、外回路全部实现负反馈,以保证系统正常进行。
热工控制系统第八章 汽温控制系统PPT课件

W X 1 S x y 1 1 S S 1 W T 1 S W W T 1 T S 2 W S T W 2 D S 1 W S D W 1 D S 2 W S D 2 W m S 1 S W Z S
(8-2) (8-3)
对于一个定值系统,扰动造成的影响应该越小越好,而定值部分应尽量保持恒定,因
1 WB 1
W0(s)
θ2
γθ2
上图中对应的主回路广义调节器的传递函数为:
W T2
sW 2B
1
2
1T1isTds
则主回路广义调节器的等效比例带为:
2
2 1 1 2
此时主回路广义调节器中各参数可以通过试验得到的等效被
控对象W0(s)的输出端过热汽温θ2在减温水量WB扰动下的阶跃响 应曲线,按单回路控制系统整定方法进行计算:(P175表6-6)
(8-5)
则有:
W b 2SK zK T 2K fK 2 1 K T 2K fK 2K m 2K z
T 2 1 K T 2K fK 2K m 2K z S 1
令: K b 2 1 K K T z2 K K T 2 fK K 2 fK K m 2 2K z,T b 2 1 K T 2K T f2 K 2K m 2K z
Iθ 2 -
I 2 1 1
内回路
γθ2
W2(s) θ2
主回路原理方框图 如果主调节器为PID调节器,其传递函数为:
WT2
s
1
2
1T1is
Tds
忽略导前区的惯性和迟延,则简化后导前区传递函数为:
W1
s
1
WB
1
1
此时主回路原理方框图可以简化为:
汽温控制系统

直流锅炉的启动旁路系统直流 Nhomakorabea炉启动旁路系统有以下主要功能: 直流锅炉启动旁路系统有以下主要功能: (1)维持水冷壁具有流速稳定的最小水流 保持锅炉启动流量和启动压力; 量,保持锅炉启动流量和启动压力; 回收工质和热量; (2)回收工质和热量; 使蒸汽参数满足汽机启动过程的需要。 (3)使蒸汽参数满足汽机启动过程的需要。 启动旁路系统分内置式和外置式两大类
第四章 汽温控制系统
一、蒸汽温度控制的任务
1. 过热蒸汽温度控制的任务 维持过热器出口温度在允许的范围之内, 维持过热器出口温度在允许的范围之内, 并保护过热器, 并保护过热器,使其管壁温度不超过允许的 工作温度。 工作温度。 蒸汽温度过高会使过热器管壁金属强度下 以至烧坏过热器的高温段, 降,以至烧坏过热器的高温段,严重影响安 过热蒸汽温度偏低, 全。过热蒸汽温度偏低,则会降低发电机组 能量转换效率。 能量转换效率。
1、再热汽温调节方式
控制烟气挡板的位置; (1)控制烟气挡板的位置; 采用烟气再循环; (2)采用烟气再循环; 改变摆动燃烧器的倾角。 (3)改变摆动燃烧器的倾角。
(1)烟气挡板控制
大型锅炉一般都用分隔墙将尾部烟道分 成两个并联烟道, 成两个并联烟道,烟道内分别布置了低温 对流过热器和低温再热器。 对流过热器和低温再热器。过热器烟道出 口挡板和再热器烟道出口挡板配合动作, 口挡板和再热器烟道出口挡板配合动作, 可改变流经再热器烟道的烟气流量, 可改变流经再热器烟道的烟气流量,从而 控制再热蒸汽温度。 控制再热蒸汽温度。由于一定的负荷对应 一定的烟气通流量, 一定的烟气通流量,为了保证烟气通流量 能从尾部烟道两侧顺利通过, 能从尾部烟道两侧顺利通过,通常一侧挡 板开大时,另一侧挡板应关小。 板开大时,另一侧挡板应关小。
河津电厂主汽温控制及评价课件

THANK YOU
感谢各位观看
温控制系统的性能。
主汽温控制系统在其他电厂的应用与实践
应用案例一
某大型燃煤电厂的主汽温控制系统采 用了先进的模糊控制算法,取得了良 好的控制效果。该电厂通过引入智能 控制技术,实现了对主蒸汽温度的高 精度控制。
应用案例二
某核电厂的主汽温控制系统采用了多 变量预测控制技术,有效地提高了系 统的稳定性和响应速度。该技术的应 用对于保障核电厂的安全、稳定运行 具有重要意义。
主汽温控制系统在河津电厂的运行效果分析
运行效果数据收集
通过收集河津电厂主汽温控制系统的历史运行数据,分析系统的运行效果。数据 显示,主蒸汽温度的控制精度得到了有效保障,波动范围较小。
运行效果评价
从运行数据来看,主汽温控制系统的调节性能良好,能够快速响应温度变化,确 保主蒸汽温度稳定在设定范围内。此外,该系统还具有操作简便、维护方便等优 点。
主汽温控制系统的历史与发展
历史
主汽温控制系统经历了从简单手动控制到智能自动控制的发展过程。
发展
随着控制理论、计算机技术和传感器技术的不断进步,主汽温控制系统的性能 和控制精度不断提高,未来将朝着更加智能化、自适应和节能环保的方向发展 。
02
主汽温控制策略与技术
经典控制理论在主汽温控制中的应用
01
主汽温控制系统主要由温度传感器、控制器、执行器和相关辅助设备组成。该系统通过温度传感器检测主蒸汽的 温度,将信号传输至控制器,控制器根据预设的参数和实际温度差值,计算出调节信号,驱动执行器进行调节, 以控制主蒸汽的温度在设定范围内。
应用情况概述
河津电厂的主汽温控制系统自投运以来,运行基本稳定。该系统对于确保电厂的安全、经济运行起到了重要作用 。
单元机组过热汽温控制系统的工程实现

单元机组过热汽温控制系统的工程实现单元机组过热汽温控制系统是一种用于调节和控制单元机组中过热蒸汽的温度的系统。
过热蒸汽是通过锅炉产生的,它的温度必须在一定范围内进行控制,以确保其稳定运行和安全性。
以下是关于单元机组过热汽温控制系统工程实现的详细介绍。
一、系统组成1.过热器:过热器是通过燃烧锅炉产生的蒸汽进行加热以增加其温度的设备。
过热器通常是由一系列管子构成,蒸汽通过这些管子流动,从而增加其温度。
2.控制阀:控制阀用于调节过热器中蒸汽的流量,从而控制蒸汽的温度。
控制阀通常由一个执行器和一个阀体组成,执行器通过电信号或气动信号控制阀体的开度。
3.温度传感器:温度传感器用于测量过热器中蒸汽的温度。
常用的温度传感器包括热电偶和热电阻。
温度传感器将蒸汽温度转换为电信号,并将其发送给控制器。
4.控制器:控制器是系统的核心部分,它接收来自温度传感器的信号,并根据预设的设定值进行比较和计算,然后通过控制阀调节过热器中蒸汽的流量,以达到设定的温度值。
5.人机界面:人机界面用于用户与系统进行交互和操作。
它通常包括显示屏和操作按钮,用户可以通过操作按钮设置温度设定值、监视当前温度和系统状态等。
二、工程实现步骤1.方案设计:根据单元机组的要求和特点,设计温控系统的整体方案。
确定控制系统的组成部分和工作原理,选择适合的控制器和传感器。
2.传感器安装:在单元机组的适当位置安装温度传感器,确保其能够准确测量蒸汽的温度,并与控制器连接。
3.控制阀安装:根据设计要求,在过热器的适当位置安装控制阀,并连接执行器和控制器。
4.控制器配置:根据单元机组的温度要求,配置控制器的相关参数。
包括设定值、比例、积分和微分等控制参数。
5.人机界面设置:配置人机界面的显示屏,以便用户可以设置设定值、监视当前温度和系统状态。
6.系统调试:经过安装和配置后,对整个系统进行调试。
通过改变设定值和监视蒸汽温度,检查系统的响应和控制准确性。
7.系统优化:根据调试的结果,对控制器的参数进行优化,以提高系统的控制精度和稳定性。
再热器汽温控制系统课程设计说明书
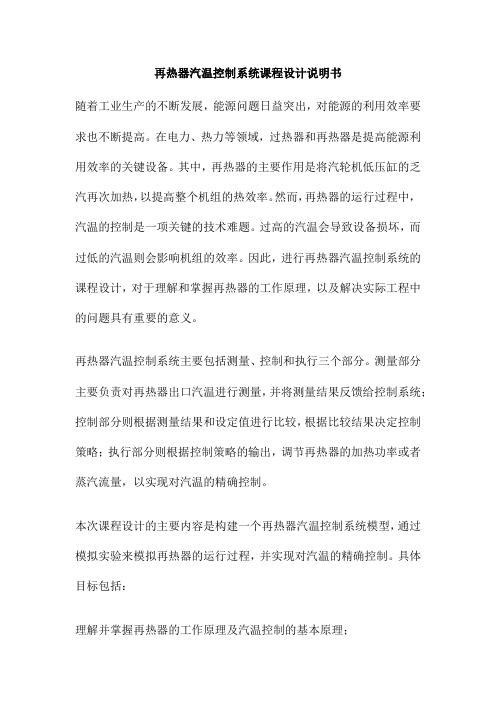
再热器汽温控制系统课程设计说明书随着工业生产的不断发展,能源问题日益突出,对能源的利用效率要求也不断提高。
在电力、热力等领域,过热器和再热器是提高能源利用效率的关键设备。
其中,再热器的主要作用是将汽轮机低压缸的乏汽再次加热,以提高整个机组的热效率。
然而,再热器的运行过程中,汽温的控制是一项关键的技术难题。
过高的汽温会导致设备损坏,而过低的汽温则会影响机组的效率。
因此,进行再热器汽温控制系统的课程设计,对于理解和掌握再热器的工作原理,以及解决实际工程中的问题具有重要的意义。
再热器汽温控制系统主要包括测量、控制和执行三个部分。
测量部分主要负责对再热器出口汽温进行测量,并将测量结果反馈给控制系统;控制部分则根据测量结果和设定值进行比较,根据比较结果决定控制策略;执行部分则根据控制策略的输出,调节再热器的加热功率或者蒸汽流量,以实现对汽温的精确控制。
本次课程设计的主要内容是构建一个再热器汽温控制系统模型,通过模拟实验来模拟再热器的运行过程,并实现对汽温的精确控制。
具体目标包括:理解并掌握再热器的工作原理及汽温控制的基本原理;学会使用常用的控制算法,如PID控制算法等;通过模拟实验,实现对再热器汽温的精确控制;讲解再热器的工作原理及汽温控制的基本原理;进行模拟实验,实现对再热器汽温的精确控制;分析实验结果,讨论控制过程中的问题及解决方法。
通过本次课程设计,我们成功地构建了一个再热器汽温控制系统模型,并实现了对汽温的精确控制。
实验结果表明,我们所设计的控制系统具有良好的性能,能够有效地应对各种工况变化,确保再热器的高效稳定运行。
我们也发现了一些潜在的问题,如测量误差、执行机构的响应速度等,这些问题需要在未来的研究中加以解决。
本次课程设计让我们更深入地理解了再热器的工作原理及汽温控制的基本原理,掌握了控制系统的基本组成及各部分的功能,学会了使用常用的控制算法。
通过模拟实验,我们成功地实现了对再热器汽温的精确控制。
汽温控制系统试验

试验所要求的几种典型负荷工况,应根据所采用的控制策略确定,至少应分别在70% 和100%两种负荷下进行,每一负荷下的试验应不少于两次。
汽温控制对 象特性试验 方法
减温水扰动下汽温动态特性 试验方法
1
减温控制切为手动方式;
2
在机组运行工况稳定的 情况下,快速手操减温 水调节阀,即一次动作 关小(阶跃)减温水调 节阀开度,使减温水流 量的变化尽量接近阶跃 响应,幅度以减小(或 开大)10%减温水流量 为宜;
3
记录主汽温度变化情况;
4
待主汽温度上升(或下 降)并稳定水调节阀应满足以下质量要求: 1)调节阀的最大流量应满足锅炉最大负荷要求,并约有10%的裕量; 2)调节阀漏流量应小于其最大流量的10%; 3)调节阀特性曲线应呈线性,线性工作段大于全行程70%,其回程误差小于最大流量3%; 4)调节阀的死行程应小于全行程的5%。 减温水调节阀流量特性试验的基本方法要点: 1)在机组运行工况稳定的情况下,手动单方向间断地开大减温水调节阀,每次以10%幅度为 宜,直至调节阀全开; 2)然后再以同样方式关小,直至全关; 3)每次减小或开大操作都须待流量稳定后进行
汽温控制系统试验
汽温控制系统
✓ 汽温控制包括过热汽温控制和再热汽温控制。 ✓ 汽温控制一直是电厂模拟量控制系统的难点,主要是汽温控制对象具有大迟延、大惯性、非线性和时变
性等特点,采用常规和简单的控制规律难以获得好的调节效果。
电厂锅炉主汽温自动控制原理

电厂锅炉主汽温自动控制原理电厂锅炉主汽温自动控制是指通过对锅炉主汽温的测量和调节,实现锅炉主汽温值的稳定控制。
主汽温是指锅炉蒸汽的温度,是影响锅炉运行和发电效率的一个重要参数。
良好的主汽温控制可以保证锅炉正常稳定运行,提高发电效率。
下面将从主汽温控制系统的组成和工作原理两个方面进行详细介绍。
一、主汽温控制系统的组成主汽温控制系统主要由三个部分组成:测量部分、执行部分和调节部分。
1.测量部分:测量部分的主要作用是获取锅炉主汽温的实时值。
常用的测量方法有热电偶和红外线测温仪。
热电偶通过测量两个不同材料的热电势来获取温度值,精度较高,但需要进行周期性校准。
红外线测温仪则是通过感应目标表面的红外线辐射来确定温度值,不受材料的影响,但对目标的表面状态有一定要求。
2.执行部分:执行部分主要包括控制阀和调节阀。
控制阀主要用于控制燃烧器的供气量,通过调节供气量来控制锅炉燃烧热负荷的大小。
调节阀主要用于控制给水的进入量,通过调节给水流量来控制锅炉蒸汽的温度。
3.调节部分:调节部分主要由控制器和传感器组成。
控制器是主汽温控制系统的核心部件,接收测量部分的反馈信号,与执行部分实现信息的传递和控制指令的执行。
传感器负责将锅炉主汽温的实时值转换成电信号,并通过控制器传递给执行部分。
二、主汽温控制系统的工作原理主汽温控制系统的工作原理可以简要分为以下几个步骤:1.测量主汽温:通过测量主汽温的实时值,将温度值转换成电信号,并传递给控制器。
2.根据设定值:控制器中设定一个主汽温的目标值,与实时测量值进行比较。
3.根据误差:根据设定值与实际测量值之间的误差,控制器会发出相应的控制指令。
4.调节执行:根据控制指令,控制器会调节控制阀和调节阀,来改变供气燃烧的热负荷以及给水的流量,从而控制锅炉主汽温的稳定。
5.反馈控制:控制器会周期性地获取实际控制效果,将反馈信息进行比较并进行调整,以实现对锅炉主汽温的精确控制。
综上所述,电厂锅炉主汽温自动控制的原理主要包括测量、计算、比较和调整。
蒸汽温度控制系统

第四节 再热汽温控制
一、再热蒸汽温度控制任务
保持再热器出口汽温为给定值。
二、再热汽温的影响因素
(1)机组负荷的变化(蒸汽流量变化)对再热汽温有很大的 影响;
(2)烟气热量变化也是影响再热蒸汽温度的重要因素。 由于再热器是纯对流布置,再热器入口工质状况取决
二、过热汽温对象特性
主要扰动有三种: (1)烟气热量扰动:燃烧器运行方式变化、
燃料量变化、燃料种类或成分变化、风量 变化等等这些变化最终均反映在烟气热量 的变化; (2)蒸汽流量(负荷)扰动; (3)减温水流量扰动。
D
GD(s)
Q
GQ(s)
W
GW(s)
+ θ
+ +
1.蒸汽流量(负荷)扰动下的汽温特性
γθ2
γθ1
+ f1(x) - PI1
D 蒸汽流量D
∑
+ +-
PI4
+
+ -
PI2
KZ
一级减温水调 节阀
二级减温 水调节阀
KZ
θ0
图13 按温差控制的过热汽温分段控制系统
D
第三节 举例
一、过热蒸汽流程
一级减温器 初级过热器
分割屏过热器 后屏过热器二级减温器
θ5
θ4
θ3
θ2
末级过热器 θ1 至汽机
蒸汽
(s) Q(s)
KQ 1 TQS
e Q s
0
τQ
t
图 4 烟气热量扰动下过热汽温响应曲线
3.减温水量扰动下的过热汽温特性
Wj
0
t
ΔWj
θ
TC
G(s) (s) K es
串级汽温控制系统设计任务(DCS系统设计)

串级汽温控制系统的工作原理
图1所示的串级汽温控制系统,只要导前汽温 发生变化,副调节器P就去改变
减温水流量,初步维持后级过热器入口汽温 在一定范围内,起粗调作用。
而
过热器出口汽温 的控制,则是通过主调节器PI来校正副调节器工作,只要 未达到给定值,主调节PI的输出信号就不断递变化,使副调节器不断去控制减温水喷水量的变化,直到 恢复到给定值为止。
稳态时,导前汽温 可能稳定在与原来数值不同的数值上,而主汽温 则一定等于给定值。
在串级汽温控制系统中,由于两个回路的任务及动态特性不同,可以选用不同的调节器。
副回路及副调节器的任务是快速消除内扰,要求控制过程的持续时间较短,但不要求无差,故一般可选用纯比例调节器。
当到前汽温惯性较大时,也可选
用比例微分调节器。
主回路及主调节器的任务是维持 恒定,一般选用比例积分调节器。
当过热器惰性区较大时,也可选用比例、积分、微分调节器。
图1 串级汽温控制系统工作原理
串级汽温控制系统设计
要求:
由上述系统完成串级汽温控制系统的、SAMA图组态、流程图组态、操作器组态,并进行参数整定与系统调试。
汽温控制系统
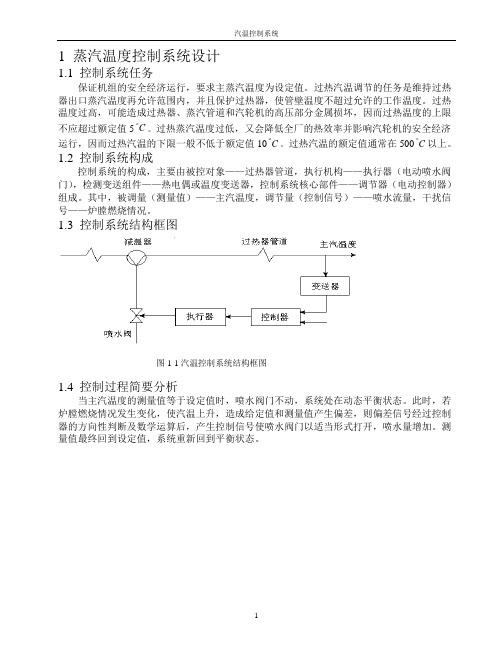
1 蒸汽温度控制系统设计1.1 控制系统任务保证机组的安全经济运行,要求主蒸汽温度为设定值。
过热汽温调节的任务是维持过热器出口蒸汽温度再允许范围内,并且保护过热器,使管壁温度不超过允许的工作温度。
过热温度过高,可能造成过热器、蒸汽管道和汽轮机的高压部分金属损坏,因而过热温度的上限不应超过额定值5C 。
过热蒸汽温度过低,又会降低全厂的热效率并影响汽轮机的安全经济运行,因而过热汽温的下限一般不低于额定值10C 。
过热汽温的额定值通常在500C 以上。
1.2 控制系统构成控制系统的构成,主要由被控对象——过热器管道,执行机构——执行器(电动喷水阀门),检测变送组件——热电偶或温度变送器,控制系统核心部件——调节器(电动控制器)组成。
其中,被调量(测量值)——主汽温度,调节量(控制信号)——喷水流量,干扰信号——炉膛燃烧情况。
1.3 控制系统结构框图图1-1汽温控制系统结构框图1.4 控制过程简要分析当主汽温度的测量值等于设定值时,喷水阀门不动,系统处在动态平衡状态。
此时,若炉膛燃烧情况发生变化,使汽温上升,造成给定值和测量值产生偏差,则偏差信号经过控制器的方向性判断及数学运算后,产生控制信号使喷水阀门以适当形式打开,喷水量增加。
测量值最终回到设定值,系统重新回到平衡状态。
2 控制系统工作原理系统中有两个调节器,构成两个闭环回路。
内回路祸福回路,包括控制对象、副参数变送器、副调节器、执行器和喷水阀,它的任务是尽快消除减水温度的干扰,在调节过程中起初调作用;外回路或主回路,包括主对象、主参数变送器、主调节器、副回路,其作用是保持过热器出口汽温等于给定值。
主调节器接受被控量出口汽温以及给定值信号,主调的输出给定汽温与喷水减温器出口汽温共同作为副调节器输入,副调节器输出汽温信号控制执行机构位移,从而控制减温水调节阀门的张开闭合程度。
当炉膛燃烧剧烈,过热器管道过热,有喷水量的自发性增加造成干扰,如果不及时加以调节,出口温度将会降低,但因为喷水干扰引起的汽温降低快于出口汽温的降低,温度测量变送器输出的汽温信号会降低,副调节器输出也降低,通过执行器使喷水阀门开度减少,则喷水量降低,使扰动引起的汽温变化波动很快消除,从而使主汽温基本上不受影响。
汽温控制系统

一级减温器出口温度 θ1j与主调节器输出的差, 加上前馈信号f形成副调节 器PID2的输入偏差信号e2。
2020/7/20
第一节 过热汽温自动控制系统
2020/7/20
• 当某种扰动引起二级减温器入口 蒸汽温度θ1上升时,主调节器 输入偏差减小,PIDl的输出下降 ,引起副调节器的输入偏差增大 ,PID2的输出增加,使减温水 增加,一级减温器出口汽温θ1j 立即下降,经延时使二级减温器 入口汽温θ1下降。θ1j下降使副 调节器的输入偏差e2减小。这 样,在主汽温的迟延期间内,当 主调节器输出还在减小时,θ1j 也在同时减小,抑制了副调节器 输出的进一步增加,从而防止了 减温水过调。
一级减温:减温器布置在低过出口集箱至全大屏过热器进口集箱的连接管上,
左右各一只,其作用是保护屏式过热器,防止屏过超温,同时改善二级减温 控制系统的控制品质。在运行中作汽温的粗调,是过热汽温的主要调节手段。 ECR:14.49T/H
二级减温:减温器全大屏过热器出口,共2只。其作用是保证主蒸汽(高过出
口)温度等于设定值,在运行中作汽温的细调节。ECR:7.75T/H
调节阀的开度,改变减温水量,初步
维持后段过热器入口(减温器出口)
处的汽温,对后段过热器出口主汽温
PID1 起粗调作用。后段过热器出口主汽温
PID2
由主调节器PID1控制。只要后段过热
器出口汽温未达到设定值,主调节器
PID1的输出就不断地变化,使副调节
器不断地去改变减温水量,直到主汽
温恢复到主汽温设定值为止。稳态时,
第一节 过热汽温自动控制系统
(二)二级减温控制系统
❖二级过热器出口蒸汽温度控制是锅炉出口蒸汽温度的最后一道控制手段, 为了保证汽轮机的安全经济运行,要求尽可能提高锅炉出口蒸汽温度的控制 品质。为此,二级减温控制系统的前馈信号采用了基于焓值计算的较为完善 的方案。 ❖其基本思想是:通过较为准确的计算,确定未段过热器入口处应具有的温 度值,将其作为副调节器的设定值。首先控制好未段过热器入口温度,使得 过热蒸汽在这一温度值的基础上,经过末段过热器吸热后,其出口汽温正好 达到或接近要求的定值。若仍有偏差,再由主调节器来消除。
- 1、下载文档前请自行甄别文档内容的完整性,平台不提供额外的编辑、内容补充、找答案等附加服务。
- 2、"仅部分预览"的文档,不可在线预览部分如存在完整性等问题,可反馈申请退款(可完整预览的文档不适用该条件!)。
- 3、如文档侵犯您的权益,请联系客服反馈,我们会尽快为您处理(人工客服工作时间:9:00-18:30)。
前馈回路 。 原使用燃料信号的前馈信号实际微分信号改为锅炉主控使用的负荷指令 信号并将该动态调节量加在调节器出口绕过调节器积分调节作用,这样 可以通过改变实际微分环节中惯性时间或微分增益来形成所需动态超调 量以满足汽温在负荷变化的动态过程中对减温水量短暂需求,进而改善 了调节系统的动态调节品质,负荷变动结束后稳态情况下不起作用,这 样即使负荷由于扰动小幅度变化,前馈不起作用使汽温调节更加稳定。 引进蒸汽流量信号代表锅炉热量信号可以快速、实时地对炉膛燃烧状况 的变化作出反应。
“特性补偿式”汽温控制方案原理框图如下图
1所示:
不同负荷工况下,自动调整调节器比例。 过热器在不同负荷对象特性差异较大,需要根据负荷情况对调节器的比 例系数进行调整,以适应调节需要,为此做了不同负荷下汽温特性试验, 据此调整不同负荷工况下调节器比例系数。 串级调节改为单回路 。 串级调节系统使用主调控制过热汽出口温度,副调控制减温器后蒸汽温 度。由于屏式过热器进口汽温较低,仅处于过热状态;而且由于屏式过 热器主要吸收的是辐射热,响应快,因此单回路已能满足要求。 二级过热汽温通过“特性补偿”调节速度加快也可改为单回路调节控制 方案,即由原过热蒸汽出口主蒸汽温度作为主调节器的被调量,二级减 温器后蒸汽温度作为副调节器被调量,改为左右侧各一个调节器,左右 侧汽温调节使用相同的被调量及过热汽温,所以现在调节控制方案中必 须考虑末级过热器入口蒸汽温度保持平衡的问题。
完全补偿,大大改善了减温水(或调整门)扰动下被控对象的动态特性。 考虑到汽温特性在锅炉不同负荷下相差较大,引入变积分、微分增益、 比例系数可以改善调节系统动态品质,适应调节对象特性要求。 根据汽温调节的特点,认为削减系统大的迟滞,克服内扰,应采用多种 前馈控制方案以克服各种外扰因素是解决这一问题的思路。为此,在不 同的机组(直吹式、中间仓储式锅炉)进行了大量的试验,并进行了比 较分析和可行性论证,决定在原常规导前微分控制方案的基础上,使用 予估控制理论。 通过拟合过热器的对象特性,形成“特性补偿式”汽温控制方案,可有 效克服系统的大滞后和减温水侧的扰动;同时引用“锅炉负荷指令”、 “锅炉热量”等多种前馈控制可最大程度克服外扰因素;另外根据调节 器温度偏差、被调温度变化率等条件组合出了十五条模糊控制规则,作 为温度调节的依据对汽温调节调节器增益进行了动态修正。四、问题分析与改进方案实践
过热汽温被控对象在工况大范围变化时,动态特性或模型参数将有很大 变化。要求控制策略针对对象动态特性准确建模。对于这类复杂被控对 象,若采用基于对象模型识别的常规自适应控制器,模糊自适应控制器, 或者基于神经网络实现的自适应控制器,都由于计算量大,控制规律复 杂,很难满足实时性要求。特别是现有DCS系统,设计中没有预估器 、 模糊控制算法,复杂算法无法实现。 实际应用表明若采用经典固定参数PID串级控制系统整定方法,很难保 证在所有工况范围内系统均具有较好的控制品质,甚至闭环系统也有可 能产生渐扩振荡。因此,认为串级控制系统本身对大惯性过程控制的有 效性是有限的,在被控对象扰动时,如果能充分考虑过热器的大惯性、 大迟延,并将其反向叠加处理予以抵消,这样在进入调节前就相当于把 原来滞后大的被调量信号过热器出口温度完全补偿为滞后小的多的减温 器后温度,相对于采用导前微分的双回路汽温调节控制系统,从控制方 式上由原来部分补偿变完成。
b.一级汽温动态特性G(s)=1.2/(1+TcS)2 , 其中Tc与机组负荷的关系见表4。 该方案已应用于阳光公司号4台机组,经过定值扰动试验和负荷扰动试验,证明 其控制品质不仅满足各种工况的运行要求,而且超过要求标准要求(10℃的定 值扰动,偏差为±1℃;20%ECR以上幅度,2%ECR/min速率的负荷扰动,动 态偏差不超过±5℃,静态偏差不超过±2℃)。
三、存在的问题
阳光汽温控制方案采用德国SIEMENS公司原设计串级汽温调节方 案,投用效果不很理想,特别由于燃烧等各种运行工况的变化,汽温控 制效果更差,满足不了运行要求。在机组变负荷或启停磨煤机过程中经 常需要运行人员手动干预以防止机组超温,增大了运行人员的工作强度, 由于调节过渡时间长,汽温波动幅度大,机组长期处于汽温大范围变化 状态,对锅炉受热面寿命威胁极大。同时,汽温长期波动不能保证机组 在最佳经济方式下运行。 简单的串级汽温调节方案以及不合理前馈回路,无法消除锅炉大惯 性、大迟延对汽温调节影响,汽温调节过渡时间长、稳定性差。同时也 没有充分考虑锅炉对象特性的不确定性,过热器在不同负荷、不同燃烧 工况下,对象特性差异较大,单一的调节参数满足不了过热器、再热器 温度调节动态、静态调节品质要求。
汽温控制系统
晋能集团 主讲人:刘红霞
一、汽温控制中的 主要难点 七、结论 二、汽温控制特点
概述 六、应用情况 三、存在的问题
五、过热汽温控制 方案
四、问题分析与改进 方案实践
概述
现代锅炉的过热器是在高温、高压条件下工作的,锅炉出口的过热蒸汽 温度是整个汽水行程下工质的最高温度,对于电厂的经济运行有较大影 响。汽温过高会使过热器和汽机高压缸承受过高的热应力而损坏,汽温 偏低会降低机组热效率,影响经济运行。
一、汽温控制中的主要难点
汽温控制的质量直接关系到机组的安全经济运行,而过热汽温的控制又 是各项控制中较为困难的任务之一,这主要是由于: 1 、造成过热汽温变化的原因很多,例如:负荷、减温水量、烟气侧的 过剩空气系数机火焰中心位置、燃料成分等都会影响汽温的变化。 2 、对象对各种扰动作用下的特性具有非线性、时变等特性,使控制的 难度加大。 3 、汽温对象具有大迟延、大惯性的特点,尤其随着机组容量和参数的 提高,蒸汽过热的受热面积比例加大,使其迟延和惯性更大,从而进一 步加大了控制的难度。
动态情况下由于使用了完全补偿汽温调节原理,汽温调节对减温水水侧扰动反 映更加迅速将原来大惯性、大迟延变为减温器后快速反映蒸汽温度,大大改善了 减温水扰动下被控对象的动态特性。
再热汽调节方案改进 。 再热汽较过热汽温调节困难更大,主要问题是迟延更大,多达20分钟, 是典型的非线性、大滞后、时变、耦合的复杂对象,随时存在诸多不确 定的扰动因素,需要通过PID等闭环控制手段来克服,而PID在不同的工 作区间,Kp、Ti、Td对输出的影响是不同的,有时甚至相反。若采用恒 定不变的PID参数,将会造成调节过程中动、静态特性恶化,因此在偏 差变化的不同区间采用不同的PID参数,形成分段PID控制,即根据偏差 及偏差变化率的不同组合,综合调节PID三项作用的强、弱,产生以下 智能多模态PID的控制规则方案见表2。该控制方案可有效改善再热汽温 调节品质。
表2
六、应用情况
“特性补偿式”汽温控制方案实施的关键是在对象特性试验的基础上,进 行模型辨识,通过数学模型拟合过热器的对象特性。补偿特性越接近过 热器的特性,对锅炉大惯性补偿效果越好。为此需要在机组不同的负荷 工况下进行大量的对象特性试验,包括减温水调整门变化对减温器后蒸 汽温度特性,调整门变化对屏过出口温度、主汽温度特性试验等。并将 试验数据进行了模型辨识,得到不同工况下过热器的数学模型(以二号 机组为例): a.二级汽温动态特性G(s)=0.58/(1+TcS)4 , 其中Tc与机组负荷的关系 见表3。
表3:二级汽温动态特性
表4:一级汽温动态特性
七、结论
经过摸索而设计的方案,在实际运行中被证明是有效的。该方案由于采 用了锅炉负荷指令作为前馈信号,从而能快速反映锅炉的燃烧工况。蒸 汽流量作为前馈信号消除由于锅炉热负荷变化过程中对汽温扰动影响, 改善了汽温调节品质。 “特性补偿式”汽温控制方案是将常规控制方案与现代控制理论相结合, 有效克服了对象的大滞后对控制系统的影响,可完全克服系统的内扰, 并通过前馈控制方案以最大程度克服系统的外扰,解决了汽温控制系统 长期存在的问题。
表一:模糊控制规则
根据“特性完全补偿”原理,克服对象大迟延。 “特性完全补偿”主要是通过多阶惯性环节拟合过热器动态特性并将其 反向叠加到调节器入口,消除由于锅炉惯性引起大迟延对汽温调节影响。 如下图所示当PTn 特性接近过热器的特性时,PTn =G2(S)过热器的 特性得到完全补偿,这时被调量Pv=UG1(S),由于喷水减温器的动态 特性可用惯性时间较小一阶惯性环节表示,它作为被测量信号将使调节 系统的调节效果得到很大改善。通过“特性完全补偿”,汽温自动控制 在动态情况下调节器被调量为:PV=Tg+T2×(1-PTN),稳态情况下: PV=Tg,(TG为被调蒸汽温度,T2为减温器后温度,PTN为过热汽对 减温水变化特性)。
二、汽温控制特点
主汽温度是火电机组安全、高效、经济运行的重要参数,汽温过高会使 过热器和汽轮机高压缸承受过高的热应力而损坏,汽温偏低会降低机组 的热效率,影响经济运行。蒸汽温度控制一直是热控方面的一大难题, 主要表现在几个方面。1)要求控制精度高(±5℃);2)系统滞后大; 3)干扰因素较多,包括:给水温度的变化、减温水扰动、负荷扰动、 燃烧扰动、风煤配比变化等;4)对象特性的不确定性,过热器在不同 负荷、不同燃烧工况下,对象特性差异较大;5)控制手段单一,过热 汽温度主要以喷水减温为主要控制手段,再热汽温度主要通过改变烟气 挡板开度控制。
五、过热汽温控制方案
根据模糊规则判断结果改变控制器增益 。 在常规PID控制基础上增加变增益的模糊控制规则后,不仅静态特性得 以改善,动态偏差也减小,并且调节速度加快,控制效果较好,对干扰 克服能力增强。其最大动态偏差和调节时间较常规串级控制明显减少, 对象特性变化后仍能正常工作。实际投用效果证明,常规的PI基础上增 加模糊控制所构成的复合系统,动态偏差可大大降低,并且调节速度加 快,控制效果变好,对干扰的克服能力增强,模糊规则如下表1所示。