考虑装配误差的齿轮接触应力仿真(精)
考虑安装误差的弧齿锥齿轮齿面接触印痕仿真分析

考虑安装误差的弧齿锥齿轮齿面接触印痕仿真分析苏宇龙;徐敏;赵兴龙;张宝锋;李旗【摘要】齿面接触印痕是衡量齿轮啮合质量的重要指标,安装误差的不可避免使得弧齿锥齿轮接触印痕的形状、大小和位置往往偏离最初设计.为了探索安装误差对弧齿锥齿轮齿面接触印痕的影响规律,本文基于齿轮啮合原理,以一对弧齿锥齿轮副啮合为例,建立了弧齿锥齿轮切齿加工数学模型,推导了大小轮理论齿面方程,分析了小轮轴向安装误差、大小轮轴间距和轴交角误差对齿面接触印痕的影响,对弧齿锥齿轮的设计制造提供参考.%Tooth contact pattern is one of the important indicators for measuring gear meshing quality.Assembly misalignment inevitably makes the shape,size and location of spiral bevel gear contact pattern tend to deviate from the original design.In order to explore the influence of assembly misalignment upon spiral bevel gear tooth surface contact pattern,the authors use a pair of spiral bevel gear meshing as an example;based on the principle of gear meshing they have established spiral bevel gear cutting mathematical mode and deduced the theoretical tooth surface equation of the gear and pinion and analyzed the effect of pinion axial assembly misalignment,distance between shafts and shaft angle on the contact pattern,providing the reference for the design and manufacture of spiral bevel gear.【期刊名称】《西安理工大学学报》【年(卷),期】2017(033)001【总页数】6页(P107-112)【关键词】弧齿锥齿轮;接触印痕;安装误差;仿真分析【作者】苏宇龙;徐敏;赵兴龙;张宝锋;李旗【作者单位】西安理工大学机械与精密仪器工程学院,陕西西安710048;西安航空动力控制科技有限公司,陕西西安710077;西安航空动力控制科技有限公司,陕西西安710077;西安理工大学机械与精密仪器工程学院,陕西西安710048;西安理工大学机械与精密仪器工程学院,陕西西安710048【正文语种】中文【中图分类】TH132弧齿锥齿轮具有承载能力高,传动平稳等特点,适用于转速较高或要求结构紧凑的场合,在航空、汽车及舰船等领域应用广泛。
基于ANSYS WORKBENCH的齿轮接触应力分析
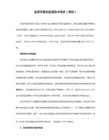
基于ANSYS WORKBENCH 的齿轮接触应力分析蓝娆1 杨良勇 2 罗昌贤3(1柳州市采埃孚机械有限公司 广西柳州5450072四川工程职业技术学院 四川 德阳 6180003广西柳工机械股份有限公司 广西柳州545007) 摘要:在理论分析的基础上,建立齿轮接触对的有限元模型,在有限元分析软件ANSYS Workbench 建立接触对,添加约束和加载,得到齿轮接触应力大小,齿轮应力集中主要发生在齿根圆角处,和理论计算分析对比。
得出相关结论为以后齿轮接触的有限元分析提供了依据。
关键词:齿轮接触对;ANSYS Workbench ;接触应力;有限元分析0引言齿轮是传动系统中承受载荷和传动动力的主要零部件,也是最容易出故障的零件之一。
据统计,在各种机械故障中,齿轮失效就占总数的6 0 %以上,其齿面损坏又是齿轮失效的主要原因之一。
因此,工程中需要发大量工作对齿面强度及其应力进行分析。
ANSYS Workbench 是用 A NS YS 求解实际问题的新一代产品,它是专门从事于模型分析的有限元软件,拥有与CAD 的无缝接口、新一代的参数化建模工具,其强大的分析功能可以很准确地反映实际物体的状态。
可进行静力学分析、动力学分析、非线性分析等。
本文从柳州市采埃孚机械有限公司实际问题出发,建立齿轮接触对的三维有限元模型,在有限元分析软件ANSYS Workbench 计算得到齿轮接触对的接触应力,与传统理论计算公式得出比较,为齿轮的快速设计和进一步的优化设计提供条件。
1齿轮参数化建模齿轮的设计,加工,生产是一个复杂、严格的过程 ,如果能够实现齿轮在设计上的参数化建模,那么就避免了齿轮的反复设计,每次只要改变参数就能得到自己想要的齿轮,这将为齿轮的生产带来极大的方便。
利用CAD 软件UG ,其与ANSYS Workbench 可以实现无缝连接,其参数化建模功能和有限元分析模块可以在同一平台完成,避免了从CAD 软件到CAE 软件的转换,提高了设计效率,同时又有利于设计数据的统一管理。
ANSYS齿轮接触应力分析案例精品

Preprocessor>Modeling>Operate>Booleans>Glue>Lines。
选择”Copied”,如下图。镜像结果。
齿轮的接触分析实例
齿轮的接触分析实例
(23)把齿顶上的两条线粘起来。 a.从主菜单选择
Preprocessor>Modeling>Operate>Booleans>Glue>Lines。 b.选择齿顶上的两条线,点击【OK】。 (24)把齿顶上的两条线加起来,成为一条线。 a.从主菜单选择
齿轮的接触分析实例
b.从主菜单选择Preprocessor>Modeling>Copy>Lines。 c.点击【Pick All】。 d.在弹出的提示框中按下图输入,点击【OK】。(Fit view)
齿轮的接触分析实例
(26)把齿底上的所有线粘起来。 a.从主菜单选择
Preprocessor>Modeling>Operate>Booleans>Glue>Lines。 b.分别选择齿底上的两条线,点击【OK】。 (27)把齿顶上的两条线加起来,成为一条线。 a.从主菜单选择
齿轮的接触分析实例
(20)将工作平面旋转13°。 a.从实用菜单中选择WorkPlane>Offset WP by Increments。 b.在“XY,YZ,ZX Angles”文本框中输入13,0,0,点击【OK】。 (21)将激活的坐标系设置为工作平面坐标系:
齿轮建模与接触应力分析
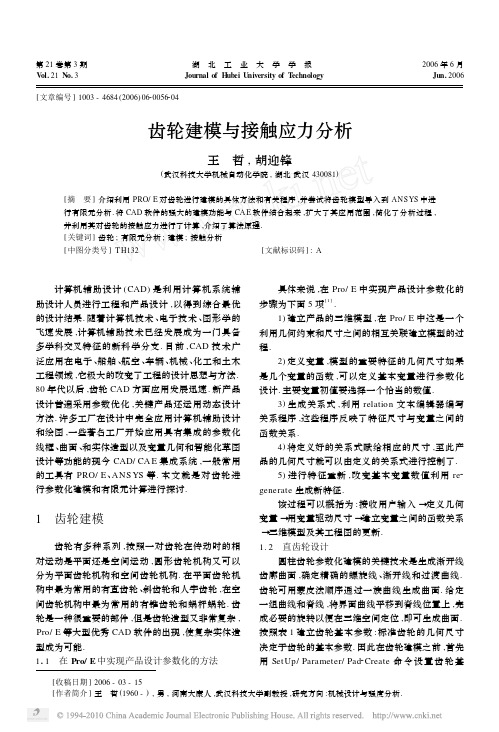
湖 北 工 业 大 学 学 报 Journal of Hubei University of Technology
[ 文章编号 ] 1003 - 4684 (2006) 0620056204
齿轮建模与接触应力分析
2006 年 6 月 Jun. 2006
58
湖 北 工 业 大 学 学 报
2006 年第 3 期
这里从背锥原理出发 ,结合 Pro/ E 造型命令 , 最大限度地实现了锥齿轮的真实三维造型 (图 5) .
2 有限元计算
面如图 7 (a) 进行划分 ,用目标单元 TA R GE170 对 小齿轮的啮合面如图 7 ( b) 进行划分 ,两个接触对用 两组实常数来分别定义. 实常数值的确定应根据具 体环境而定 ,比如对于法向接触刚度因子 F KN ,由 于齿轮变形以弯曲为主 ,则其值建议为 0. 01~0. 1 , 这里取 0. 01 ,其余参数均取缺省值 ,摩擦系数定义 为 0. 2. 此外非常有必要检查接触单元与目标单元 的外法线方向是否是“面对面”,否则在开始分析计 算时程序可能会认为有面的过度穿透而很难找到初 始解. 对于 3D 单元外法线方向是按节点顺序号以 右手定则来确定的[3] .
应力为 408. 74M Pa ,最大与最小应力的位置分别如 图. 可导入 AN S YS 中进行不同状态下齿轮的有限 元分析 ,达到了 CAD/ CA E 的一体化.
2. 1 接触应力分析 接触是一种非线性行为 ,是状态变化非线性类
型中一个特殊而重要的子集 ,对于齿轮分析其接触 应力有很重要的意义.
第 21 卷第 3 期 王 哲等 齿轮建模与接触应力分析
59
3 结论
考虑安装与制造误差的齿轮动态接触仿真

考虑安装与制造误差的齿轮动态接触仿真佟操;孙志礼;马小英;柴小冬【期刊名称】《东北大学学报(自然科学版)》【年(卷),期】2014(035)007【摘要】根据齿轮精度标准中误差的定义和说明,提出一种用于齿轮动力学分析的安装与制造误差等效定义,采用Pro/E二次开发,建立带有安装与制造误差的齿轮参数化模型;基于动态接触力学和显式动力学有限元算法,建立齿轮有限元模型;采用大变形显式动力学软件ANSYS/LS-DYNA对其进行动态仿真,从而实现求解齿轮在接触过程中安装与制造误差影响下的动态接触应力.研究表明,各类随机误差愈大,则对齿轮啮合冲击应力的影响愈大,其中齿距方向的偏差和啮合面上转角误差对齿轮接触应力的影响最大,啮合垂直面上转角误差的影响最小,当齿轮的安装误差与制造误差同时存在时,齿面接触应力变化最为剧烈.【总页数】5页(P996-1000)【作者】佟操;孙志礼;马小英;柴小冬【作者单位】东北大学机械工程与自动化学院,辽宁沈阳110819;东北大学机械工程与自动化学院,辽宁沈阳110819;东北大学机械工程与自动化学院,辽宁沈阳110819;东北大学机械工程与自动化学院,辽宁沈阳110819【正文语种】中文【中图分类】TH113【相关文献】1.考虑安装误差的拓扑修形斜齿轮承载接触分析 [J], 王会良;邓效忠;徐恺;杨建军;苏建新2.考虑轮齿制造误差的螺旋锥齿轮加载接触分析 [J], 王延忠;周云飞;周济;蔡春源3.考虑安装误差的弧齿锥齿轮齿面接触印痕仿真分析 [J], 苏宇龙;徐敏;赵兴龙;张宝锋;李旗4.考虑安装误差的弧齿锥齿轮接触分析初始点计算方法 [J], 陆凤霞;疏奇;戈文昌;靳广虎5.考虑安装误差的渐开线圆柱齿轮接触分析 [J], 施延栋;张瑞亮因版权原因,仅展示原文概要,查看原文内容请购买。
齿轮仿真耦合实验报告(3篇)
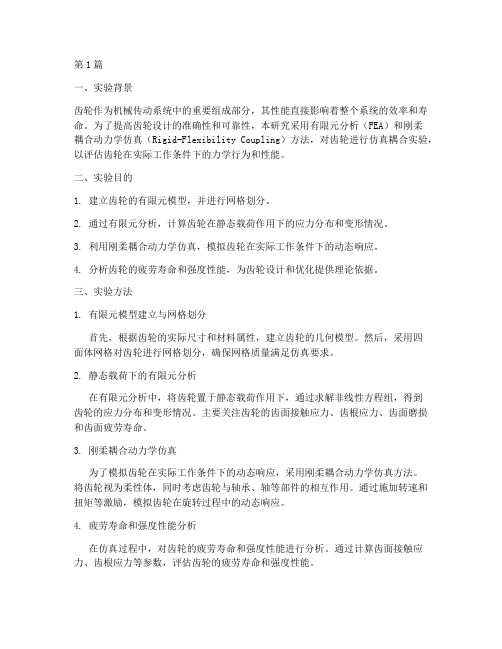
第1篇一、实验背景齿轮作为机械传动系统中的重要组成部分,其性能直接影响着整个系统的效率和寿命。
为了提高齿轮设计的准确性和可靠性,本研究采用有限元分析(FEA)和刚柔耦合动力学仿真(Rigid-Flexibility Coupling)方法,对齿轮进行仿真耦合实验,以评估齿轮在实际工作条件下的力学行为和性能。
二、实验目的1. 建立齿轮的有限元模型,并进行网格划分。
2. 通过有限元分析,计算齿轮在静态载荷作用下的应力分布和变形情况。
3. 利用刚柔耦合动力学仿真,模拟齿轮在实际工作条件下的动态响应。
4. 分析齿轮的疲劳寿命和强度性能,为齿轮设计和优化提供理论依据。
三、实验方法1. 有限元模型建立与网格划分首先,根据齿轮的实际尺寸和材料属性,建立齿轮的几何模型。
然后,采用四面体网格对齿轮进行网格划分,确保网格质量满足仿真要求。
2. 静态载荷下的有限元分析在有限元分析中,将齿轮置于静态载荷作用下,通过求解非线性方程组,得到齿轮的应力分布和变形情况。
主要关注齿轮的齿面接触应力、齿根应力、齿面磨损和齿面疲劳寿命。
3. 刚柔耦合动力学仿真为了模拟齿轮在实际工作条件下的动态响应,采用刚柔耦合动力学仿真方法。
将齿轮视为柔性体,同时考虑齿轮与轴承、轴等部件的相互作用。
通过施加转速和扭矩等激励,模拟齿轮在旋转过程中的动态响应。
4. 疲劳寿命和强度性能分析在仿真过程中,对齿轮的疲劳寿命和强度性能进行分析。
通过计算齿面接触应力、齿根应力等参数,评估齿轮的疲劳寿命和强度性能。
四、实验结果与分析1. 静态载荷下的应力分布和变形通过有限元分析,得到齿轮在静态载荷作用下的应力分布和变形情况。
结果表明,齿轮的齿面接触应力主要集中在齿根附近,齿根应力较大。
同时,齿轮的变形主要集中在齿面和齿根处。
2. 刚柔耦合动力学仿真结果通过刚柔耦合动力学仿真,模拟齿轮在实际工作条件下的动态响应。
结果表明,齿轮的齿面接触应力、齿根应力等参数在旋转过程中发生变化,但总体上满足设计要求。
江苏大学第13批大学生科研立项一般项目一览

J软件工程1201 18352868171 刘璐 J能源经济1201 18352867907 房杰 车辆1201 18352866716 J医学检验1203 18352867133 医学检验1201 18352868725 张碧莹 医学检验1202 18061009009 金鑫 J机械1203 18352867601 材料成型及控制工程1201 18796011739 裴飞 医学检验1204 18352869167 王蓉敏 食品科学与工程1201 18352868177 蔡露 食品科学与 工程1201 18352868219 汤淑婷 通信工程1201 18352868393 韩羽 化工1201 J车辆1204 化工 1201 化工1201 J自动化1201 J软件1201 J化工11 18352867209 刘璐 18352866642 董睿 18352866292 朱志翔 18352866361 崔威 18352869337 周佳怡 18352868145 18260635983 倪亚亚 J机械(模具)1202 18352867660 陈佳佳 安全工程1201 18352866581 姚丽丽
段亚伟 京江 李鹏宇江 宋春艳 食品 谯琴 王萌 江淮 食品 食品 食品
J化工11 自动化1103 J车辆 J车辆1204
18260635049 刘猛 18362880043 邵辉 18352866639 刘成洋 18352866693 施佳裕
周子龙 化工 张一珂 化工 张怀良 化工 冯峰 田飞 化工 化工
硕士 TiO2-ZnO/Fe2O3/FTO复合膜制备及太阳能燃料电池的应用 郝臣 化学化工 本科 基于氨基葡萄糖结构的手性相转移催化剂的制备 华明清 本科 磷灰石的制备羟基与运用 王爱丽 本科 硅基荧光磁性分子印迹材料选择性识别与分析菊酯类农药残留及其机理研究 潘建明 化学化工 本科 萘并卟啉及其金属配合物的合成与电化学性质研究 欧忠平 本科 纳米碳管/羟基磷灰石复合材料的制备与表征姜廷顺 本科 卤化氧铋/氧化锌复合光催化剂的合成及光催化性能 赵谦 本科 介孔碳化氮的合成改性与光催化性能 赵谦 本科 ZnS/g-C3N4复合光催化剂的合成及其光催化性能研究 陈敏
基于接触有限元的斜齿轮传动误差仿真与修形

基于接触有限元的斜齿轮传动误差仿真与修形汪中厚;赵超凡【摘要】以标准斜齿轮为研究对象,基于Pro/e软件实现斜齿轮参数化建模,提出齿轮修形方案与修形齿面构建方法.基于接触有限元法,利用Abaqus软件对标准斜齿轮进行有限元仿真,分析得到产生传动误差的主要原因,进而提出一种修形方案,将齿顶待修缘量转化为x、y、z3个方向上的向量形式,通过偏移齿面节点的方法得到修形后的齿面节点集,利用齿面节点集构建出修形后的齿轮模型,并对其进行有限元仿真.文中通过对比修形前后齿轮的传动误差,验证了修形的有效性.【期刊名称】《电子科技》【年(卷),期】2017(030)012【总页数】4页(P59-61,66)【关键词】参数化建模;斜齿轮;接触有限元法;偏移节点;修形【作者】汪中厚;赵超凡【作者单位】上海理工大学机械工程学院,上海200093;上海理工大学机械工程学院,上海200093【正文语种】中文【中图分类】TP391.9齿轮传动系统的动态特性和动力学研究的发展过程,是从静力学分析阶段逐渐发展到动力学分析阶段[1-2]。
文献[3]对齿轮箱系统的预测方法和耦合非线性等问题展开了探索,对齿轮系统的理论建模和动态分析进行了初步的研究。
文献[4]利用有限元法对蜗轮蜗杆传动系统进行传动仿真分析,其理论成果对于蜗轮蜗杆的可靠性具有重要意义。
齿轮传动误差对齿轮传动系统的动态特性有较大的影响,文献[5~6]研究了齿轮的齿廓误差对动态传动误差的影响,文献[7]采用了单纯形法研究了传动误差对动态特性的影响。
根据文献[8]可以得到,数化建模与动态性能仿真分析。
利用有限元法分析传动误差,定义为当小齿轮转过一定角度时大齿轮实际转角与理论转角的偏差,表达式为式中,φ1和φ2为小、大轮实际转角;和为小、大轮初始位置;为齿轮副理论传动比。
齿轮修形是齿轮动力学系统中的重要研究内容,同时也是减小齿轮传动误差的最有效措施之一[9]。
齿轮修形主要指对齿轮进行微观的修整,包括齿廓修形和齿向修形,最终达到减振降噪的目的[10]。
齿轮啮合动态接触过程仿真分析
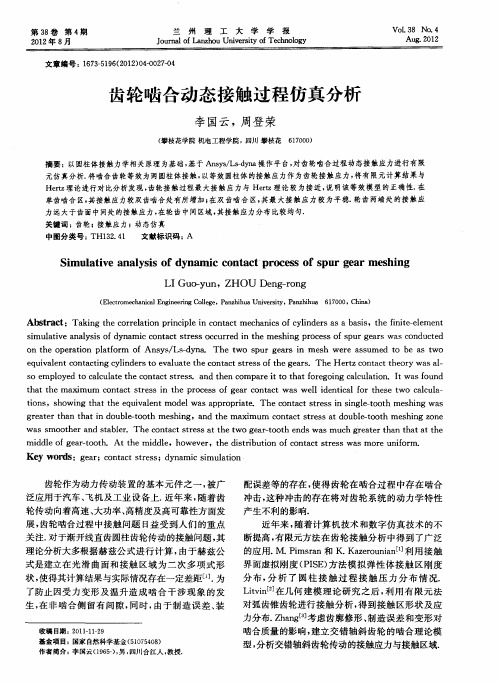
S m p o e oc lua et ec n a ts r s. a d t e o p r ot a o e on ac lto . I sfu d O e ly d t ac lt h o t c te s n h n c m a ei t h tfr g ig c lua in t t wa o n
Het 理论进行对 比分析发现 , r z 齿轮接触过程 最大接触 应力与 Het r z理论 较为接 近 , 明该 等效模 型 的正确 性. 说 在 单齿啮合 区, 其接触应力较双齿啮合处有所增加 ; 在双 齿啮合 区, 其最 大接 触 应力较 为平稳. 轮齿 两端处 的接触 应 力远大于齿面 中间处 的接触应力 , 在轮齿 中间区域 , 其接触应力分布 比较均匀.
o h p rt n pafr o s sI - y a Th wo s u er n meh wee as me o b st nteo eai l om fAn y / d n. o t s et p rga si s r su d t ea wo
e uv ln o tc igc l d r oe a u t h o tc te so h e r .Th et o tc h o ywa l q iae tc n a t yi e st v l a et ec n a tsr s ft eg a s n n eH rzc n a t e r sa— t
基于有限元方法的齿轮接触仿真分析

120
140
160
180
200
220
仿真值 /MPa
305100 341167 375106 405147 433195 460118 485123 508163
理论值 /MPa
306104 342127 374191 405102 432190 459114 484103 507114
误差 /MPa
el of involute
3 基金项目 : 广东省汽车工程重点实验室项目 ( 3007A03013) . 收稿日期 : 2008 - 07 - 28 作者简介 : 张永栋 ( 1983—) , 男 , 硕士研究生 , 研究领域 : 有 限元仿真在内燃机领域的应用研究 1E2mail: zhang1yongdong@ mail1 scut1edu1cn1
利用 ANSYS接触向导通过目标单元和接触单元 来定义目标面 、接触面 , 建立 2个接触对 , 以主动小 齿轮轮廓面作为接触面 , 从动大齿轮轮廓面为目标 面 , 分 布 设 置 刚 度 接 触 因 子 FKN 和 最 大 渗 透 量 F ILON 为 110和 011。
ANSYS分析主要目的在于得到齿轮系统在外加 边界条件 、扭矩作用下的响应 , 因此正确地施加约 束 、载荷是有限元分析的关键之一 。本文通过主 、从 齿轮安装孔内表面的节点施加影响 。一般情况下 , 节 点坐标与总体坐标中的笛卡尔系方向相同 。首先 , 将 当前坐标激活为柱坐标系 , 旋转大齿轮节点坐标系到 当前坐标 , 此时 节 点 x 轴 、 y 轴 分 别代 表 径向 、周
关键词 : 齿轮 ; 接触分析 ; 有限元法 ; 赫兹公式 中图分类号 : TH132141 文献标识码 : A 文章编号 : 0254 - 0150 (2009) 1 - 049 - 3
某差速器齿轮的动态接触仿真与疲劳分析_端木萍萍
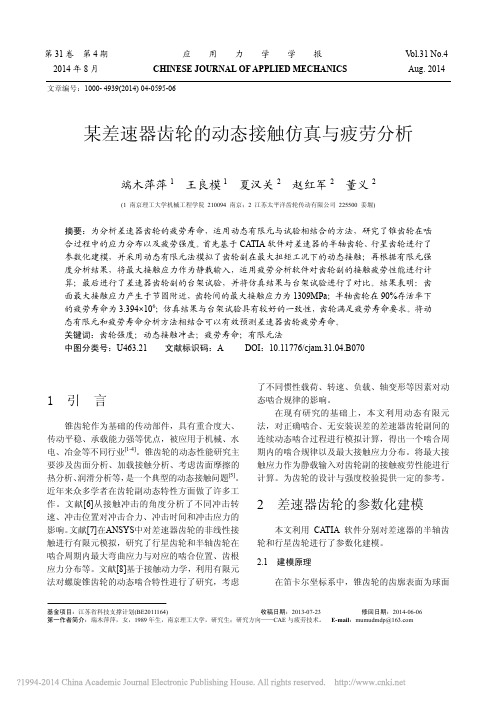
基金项目:江苏省科技支撑计划(BE2011164) 收稿日期:2013-07-23 修回日期:2014-06-06 第一作者简介:端木萍萍,女,1989年生,南京理工大学,研究生;研究方向——CAE 与疲劳技术。
E-mail :mumudmdp@应 用 力 学 学 报 CHINESE JOURNAL OF APPLIED MECHANICS第31卷 第4期2014年8月V ol.31 No.4Aug. 2014文章编号:1000- 4939(2014) 04-0595-06某差速器齿轮的动态接触仿真与疲劳分析端木萍萍1 王良模1 夏汉关2 赵红军2 董义2(1 南京理工大学机械工程学院 210094 南京;2 江苏太平洋齿轮传动有限公司 225500 姜堰)摘要:为分析差速器齿轮的疲劳寿命,运用动态有限元与试验相结合的方法,研究了锥齿轮在啮合过程中的应力分布以及疲劳强度。
首先基于CATIA 软件对差速器的半轴齿轮、行星齿轮进行了参数化建模,并采用动态有限元法模拟了齿轮副在最大扭矩工况下的动态接触;再根据有限元强度分析结果,将最大接触应力作为静载输入,运用疲劳分析软件对齿轮副的接触疲劳性能进行计算;最后进行了差速器齿轮副的台架试验,并将仿真结果与台架试验进行了对比。
结果表明:齿面最大接触应力产生于节圆附近,齿轮间的最大接触应力为1309MPa ;半轴齿轮在90%存活率下的疲劳寿命为3.394×106;仿真结果与台架试验具有较好的一致性,齿轮满足疲劳寿命要求。
将动态有限元和疲劳寿命分析方法相结合可以有效预测差速器齿轮疲劳寿命。
关键词:齿轮强度;动态接触冲击;疲劳寿命;有限元法中图分类号:U463.21 文献标识码:A DOI :10.11776/cjam.31.04.B0701 引 言锥齿轮作为基础的传动部件,具有重合度大、传动平稳、承载能力强等优点,被应用于机械、水电、冶金等不同行业[1-4]。
同步带带齿啮合应力仿真与分析
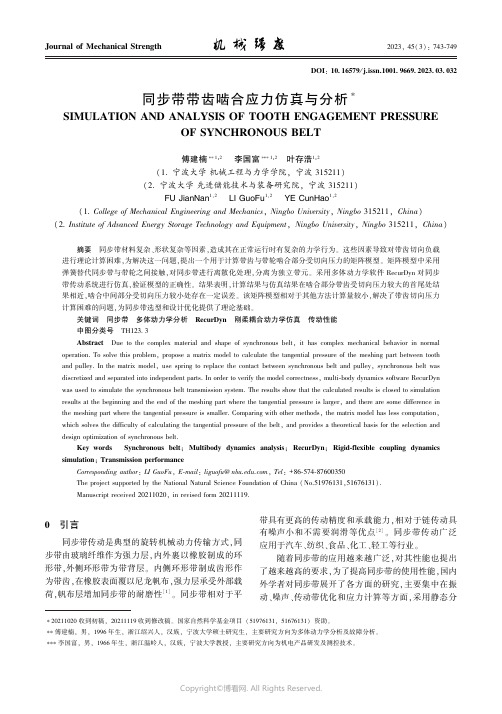
JournalofMechanicalStrength2023,45(3):743⁃749DOI:10 16579/j.issn.1001 9669 2023 03 032∗20211020收到初稿,20211119收到修改稿㊂国家自然科学基金项目(51976131,51676131)资助㊂∗∗傅建楠,男,1996年生,浙江绍兴人,汉族,宁波大学硕士研究生,主要研究方向为多体动力学分析及故障分析㊂∗∗∗李国富,男,1966年生,浙江温岭人,汉族,宁波大学教授,主要研究方向为机电产品研发及测控技术㊂同步带带齿啮合应力仿真与分析∗SIMULATIONANDANALYSISOFTOOTHENGAGEMENTPRESSUREOFSYNCHRONOUSBELT傅建楠∗∗1,2㊀李国富∗∗∗1,2㊀叶存浩1,2(1.宁波大学机械工程与力学学院,宁波315211)(2.宁波大学先进储能技术与装备研究院,宁波315211)FUJianNan1,2㊀LIGuoFu1,2㊀YECunHao1,2(1.CollegeofMechanicalEngineeringandMechanics,NingboUniversity,Ningbo315211,China)(2.InstituteofAdvancedEnergyStorageTechnologyandEquipment,NingboUniversity,Ningbo315211,China)摘要㊀同步带材料复杂㊁形状复杂等因素,造成其在正常运行时有复杂的力学行为㊂这些因素导致对带齿切向负载进行理论计算困难,为解决这一问题,提出一个用于计算带齿与带轮啮合部分受切向压力的矩阵模型㊂矩阵模型中采用弹簧替代同步带与带轮之间接触,对同步带进行离散化处理,分离为独立带元㊂采用多体动力学软件RecurDyn对同步带传动系统进行仿真,验证模型的正确性㊂结果表明,计算结果与仿真结果在啮合部分带齿受切向压力较大的首尾处结果相近,啮合中间部分受切向压力较小处存在一定误差㊂该矩阵模型相对于其他方法计算量较小,解决了带齿切向压力计算困难的问题,为同步带选型和设计优化提供了理论基础㊂关键词㊀同步带㊀多体动力学分析㊀RecurDyn㊀刚柔耦合动力学仿真㊀传动性能中图分类号㊀TH123 3Abstract㊀Duetothecomplexmaterialandshapeofsynchronousbelt,ithascomplexmechanicalbehaviorinnormaloperation.Tosolvethisproblem,proposeamatrixmodeltocalculatethetangentialpressureofthemeshingpartbetweentoothandpulley.Inthematrixmodel,usespringtoreplacethecontactbetweensynchronousbeltandpulley,synchronousbeltwasdiscretizedandseparatedintoindependentparts.Inordertoverifythemodelcorrectness,multi⁃bodydynamicssoftwareRecurDynwasusedtosimulatethesynchronousbelttransmissionsystem.Theresultsshowthatthecalculatedresultsisclosedtosimulationresultsatthebeginningandtheendofthemeshingpartwherethetangentialpressureislarger,andtherearesomedifferenceinthemeshingpartwherethetangentialpressureissmaller.Comparingwithothermethods,thematrixmodelhaslesscomputation,whichsolvesthedifficultyofcalculatingthetangentialpressureofthebelt,andprovidesatheoreticalbasisfortheselectionanddesignoptimizationofsynchronousbelt.Keywords㊀Synchronousbelt;Multibodydynamicsanalysis;RecurDyn;Rigid⁃flexiblecouplingdynamicssimulation;TransmissionperformanceCorrespondingauthor:LIGuoFu,E⁃mail:liguofu@nbu.edu.com,Tel:+86⁃574⁃87600350TheprojectsupportedbytheNationalNaturalScienceFoundationofChina(No.51976131,51676131).Manuscriptreceived20211020,inrevisedform20211119.0㊀引言㊀㊀同步带传动是典型的旋转机械动力传输方式,同步带由玻璃纤维作为强力层,内外裹以橡胶制成的环形带,外侧环形带为带背层㊂内侧环形带制成齿形作为带齿,在橡胶表面覆以尼龙帆布,强力层承受外部载荷,帆布层增加同步带的耐磨性[1]㊂同步带相对于平带具有更高的传动精度和承载能力,相对于链传动具有噪声小和不需要润滑等优点[2]㊂同步带传动广泛应用于汽车㊁纺织㊁食品㊁化工㊁轻工等行业㊂随着同步带的应用越来越广泛,对其性能也提出了越来越高的要求,为了提高同步带的使用性能,国内外学者对同步带展开了各方面的研究,主要集中在振动㊁噪声㊁传动带优化和应力计算等方面,采用静态分㊀744㊀机㊀㊀械㊀㊀强㊀㊀度2023年㊀析㊁仿真分析和实验研究等方法㊂郭建华等[3]对新型人字齿同步带的传动精度展开研究,建立了传动误差数学模型,验证了新齿廓同步带抗爬齿能力更强,说明新齿廓同步带齿形设计更合理㊂YANGG等[4]研究了同步带传动的振动问题,采用多体动力学软件RecurDyn进行同步带传动仿真,分析了同步带的各种运动特性㊂史尧臣等[5⁃6]验证了啮合冲击和横向振动是同步带传动系统主要的噪声来源㊂以上都是学者针对振动和噪声等展开的研究㊂卢小锐等[7]对正时同步带传动系统展开研究,得出减小输入轴的转速波动能有效提高传动力学性能的结论㊂曹忠亮等[8]采用RecurDyn建立汽车同步带传动系统的虚拟样机模型,对同步带在不同运行条件下的同步带等效力展开研究㊂LONGS等[9]针对汽车同步带展开研究,采用同步带传动系统整体布局的方法,提出了一种计算系统动力响应的模型㊂JIASS等[10]研究了基于绝对节点坐标的无剪切变形二维梁单元的HTD同步带传动系统的预紧力和弹性动力分析,验证了梁单元运用于同步带传动系统中的可行性㊂采用二维梁单元对于同步带传动系统进行计算,计算结果与仿真结果误差小,但是计算过程较为复杂,计算量相对较大㊂JOHANNESSONT等[11]提出了一种能够承受动态载荷的弹簧模型,采用弹簧来代替HTD同步带的拉伸以及接触产生的形变,还考虑了啮合效应,该强非线性方程采用打靶法进行求解,求解结果与实际结果相近㊂BASSOR[12]对于该弹簧模型进行了优化,该模型将线性与非线性进行分离计算,对于非线性方程中的未知值给予假设值进行迭代计算㊂给定所有已知参数后,假设第一个齿的位移,在迭代过程中,当迭代中的差值满足误差后,得出计算结果㊂采用弹簧模型应用于同步带传动系统计算中是可行的,相对于梁单元,弹簧模型简便,但是总体计算量依旧较大㊂本文主要针对同步带带齿的切向压力展开研究,采用弹簧代替同步带的拉伸以及带齿的挤压,建立一个矩阵模型,采用RecurDyn进行动力学仿真,仿真结果与计算结果接近,简化了同步带的带齿切向压力计算,为同步带的设计优化和故障检测提供理论基础㊂1 同步带传动系统多体动力学分析㊀㊀同步带传动系统中,带轮与同步带通过啮合进行力矩传递,如图1所示,带轮由金属材料加工制作,带齿由相对刚度较低的橡胶制作㊂在带齿与带轮啮合传递力矩时,带轮发生的形变相对于带齿的形变可以忽略,因此将带轮定义为刚性体,同步带定义为柔性体㊂将同步带简化为带元与弹簧,如图2所示,采用多体动力学方程进行计算[13]1⁃4㊂弹簧替代同步带与带图1㊀同步带传动示意图Fig.1㊀Schematicdiagramofsynchronousbeltdrive轮之间的相互作用力可以简便计算过程,减小计算量㊂简化后的同步带传动系统由刚体㊁弹簧㊁接触面组成,组成一个多体动力学系统㊂同步带各带齿由一个刚体代替,带齿与带齿之间连接采用弹簧替代㊂同步带稳定运行的情况下,将带齿与带轮之间相互作用力,采用平面多体动力学方程进行计算:Mq㊆+Kq+CTq㊃=Q(1)图2㊀同步带简化示意图Fig.2㊀Simplifieddiagramofsynchronousbelt㊀㊀对同步带进行离散化处理,将各带元用多体动力学方程式(1)进行计算,式中,M为质量矩阵,K为刚度矩阵,CT为阻尼矩阵,q为位移矩阵,Q为所有所受外力矩阵㊂将每个带齿作为一个单独的带元进行计算㊂由于同步带的横截面一致,将同步带二维平面化,采用式(1)进行计算,且在正常运行时带齿的惯性力可以忽略不计,带齿用一个无质量的刚体代替㊂带齿与带轮之间接触采用3个弹簧代替,如图3所示㊂图3㊀带元受力示意图Fig.3㊀Diagramofforceofbeltelement带齿与带轮之间的法向力Fn1来源于圆弧面接触部分传递拉力Fc导致形变所产生的法向分力,这部分㊀第45卷第3期傅建楠等:同步带带齿啮合应力仿真与分析745㊀㊀法向分力由带齿与带轮接触面的摩擦力和Fc在y方向的分力抵消,从而实现正常运行中同步带与带轮紧密贴合,不会发生爬齿现象,即满足不等式(2):Fc(i)sinα4+Fc(i-1)sinα4+μFtæèçöø÷ȡFn1(2)式中,α为带轮齿角㊂在同步带表面有油污或长时间运行,会导致带轮与带齿之间摩擦因数μ减小,可能会导致爬齿的发生㊂在同步带张紧力较小时,沿着法向的分力不能满足不等式(2),也会导致爬齿㊂此外,同步带过载,摩擦力及Fc的法向分力之和小于传递力矩所需的法向分力也会导致爬齿[14]㊂㊀㊀切向压力是研究的重点,带齿的切向动力方程中,将带齿视为一无质量刚体,方程中的质量所导致的惯性力为零,即式(1)中首项为零,根据图3受力示意图,刚体切向受力计算式为kc(ui-ui-1)cosα2+μΔykn1sgn(-ui)+μFn2sgn(-ui)+ktΔx=0(3)式中,kc为强力层拉伸刚度;kn1为带齿法向刚度;kt为带齿切向刚度;μ为齿面与带轮之间摩擦因数㊂㊀㊀带齿的切向压力主要来源为同步带安装张紧力和所需传递力矩转变的切向压力,同步带传递力矩主要是通过带齿与带轮啮合进行传递,摩擦力作用方向主要在法向上,切向分力相对较小,且同步带与带轮并非通过摩擦力进行传递,因此式(3)可化简为kc(ui-ui-1)cosα2+ktΔx=0(4)㊀㊀关于切向压力,同步带可以由图3简化为图4,刚体之间采用刚度为kc的弹簧进行连接,其中啮合部分带齿满足以下等式:第一个齿的切向受力平衡方程为Tc+kcuisgn(u1)+ktΔx1=0(5)㊀㊀第i个齿的切向受力平衡方程为kc(ui-ui-1)cosα2+ktΔxi=0(6)㊀㊀最后一个齿的切向受力平衡方程为Ts+kcuisgn(ui)+ktΔxi=0(7)图4㊀带元切向受力示意图Fig.4㊀Diagramoftangentialforceofbeltelement㊀㊀带轮与带齿的节距相等,同步带与带轮啮合区域内,带齿i与i-1个齿之间的ui,带齿i+1与带齿i之间的ui+1,与带齿i的x向形变存在式(8)的关系,即可将各带齿的受力平衡方程联立为一个矩阵:ui+1-ui=Δxi(8)F=Δxkt(9)㊀㊀将式(9)代入受力平衡方程联立成的矩阵,即可得式(10),在已知同步带参数和张紧力的情况下,将其代入矩阵中,即可求得各带齿所受的切向压力Fi㊂F1F2F3Fi[]kc+kt100-kc-(2+ktkccosα2)1 001-(2+ktkccosα2)00010︙︙︙⋱︙000 0000 -kc000kc+ktéëêêêêêêêêêêêêêêêêêùûúúúúúúúúúúúúúúúúú=Ttkt00︙0Tcktéëêêêêêêêêùûúúúúúúúú(10)2㊀基于RecurDyn同步带运动仿真㊀㊀对同步带传动系统进行多体动力学仿真,采用SolidWorks进行三维建模,Workbench进行网格划分,多体动力学软件RecurDyn进行同步带运行仿真㊂在SolidWorks中建立节距Pb为5mm㊁宽度为15mm㊁齿数为60的HTD同步带三维模型,并建立两个28齿与同步带相匹配的同步带带轮㊂同步带分为三层:带背和带齿为氯丁二烯橡胶,橡胶密度为12 7ˑ103kg/m3,弹性模量为70MPa,泊松比为0 4㊂㊀746㊀机㊀㊀械㊀㊀强㊀㊀度2023年㊀强力层为玻璃纤维,玻璃纤维的密度为2 6ˑ103kg/m3,弹性模量为200MPa,泊松比为0 4㊂采用Workbench进行网格划分如图5所示,内侧和外侧分别为带背和带齿,中间部分为强力层㊂图5㊀同步带网格划分局部模型Fig.5㊀Synchronizationbeltmesheslocalmodels在同步带工况系数取1的情况下,带轮的转速为1440r/min,基础带宽为9mm的同步带,在该带轮和带长的情况下的基本额定功率为0 463kW,可求得15mm宽的同步带在1440r/min的工况下传动的最大功率为0 828kW㊂主动轮转速为48πrad/s,从动轮负载为4 5N㊃m㊂在RecurDyn中将同步带定义为柔性体,即为FFlxbody㊂同步带轮为金属材质,与其进行接触的同步带带齿为橡胶材质,为减小计算量,将带轮作为刚体导入,组成一个同步带传动系统模型如图6所示㊂图6㊀同步带传动系统模型Fig.6㊀Synchronousbeltdrivesystemmodel仿真总时长为1s㊂0 0 1s,采用Time函数控制从动轮沿x方向平移,移动到距离主动轮中心距为80 76mm的位置,进行同步带张紧阶段仿真㊂0 1 0 2s,用Time函数对主动轮进行加速至48πrad/s,将从动轮负载增加至4 5N㊃m,在这之后同步带进入平稳运行状态㊂在带齿侧面选取位于带齿底部,强力层中间处的一个节点,如图7所示㊂对于每个带齿均建立一个节点,这些节点进行数据输出,用于求解同步带两齿之间的距离变化㊂设置仿真时长为1s,输出采样数据集的数量为3000㊂图7㊀节点位置示意图Fig.7㊀Nodelocationdiagram3 仿真结果与分析㊀㊀同步带在0 2s后开始平稳运行,同步带应力云图如图8所示㊂带齿不与带轮啮合部分同步带只受拉力,由强力层承受拉力,带齿并不承受拉力㊂带齿与带轮啮合部分,带齿承受切向压力,且处于啮合部分的带齿受切向压力分布不均匀㊂图9为主动轮端同步带局部应力云图,即将啮出和刚啮入带齿所受切向压力最大,向内带齿所受切向压力逐渐减小,在与带轮啮合同步带中间部分带齿近似不受切向压力㊂因此,带齿的受力在同步带运动时处于不断的波动,以同步带旋转一周为周期,呈现周期性波动㊂且受力最大处,位于紧边的带齿与主动轮的啮入处和从动轮的啮出处㊂图8㊀同步带传动系统应力云图Fig.8㊀Stressnephogramofsynchronousbeltdrivesystem图9㊀主动轮端同步带局部应力云图Fig.9㊀Localstressnephogramofsynchronousbeltatdrivepulley在同步带带齿啮合过程中会产生啮合冲击[13]1⁃4,带轮与同步带之间传递的转矩会发生波动,由于转矩的波动会导致从动轮角速度发生波动,如图10所示㊂在Time函数控制下,主动轮转速达到目标转速稳定后,从动轮的转速在不断波动,但是波动值相对较小㊂从动轮转速不稳定,则维持主动轮保持稳定转速转动的驱动转矩也会发生波动,如图11所示,在负载转矩上下区间不断波动㊂同步带传动具有精确的传动比,但是在同步带运行的瞬间传动比具有波动,这是由带齿与带轮的啮入和啮出产生的冲击造成的㊂㊀第45卷第3期傅建楠等:同步带带齿啮合应力仿真与分析747㊀㊀图10㊀带轮角速度曲线Fig.10㊀Pulleyangularvelocitycurve同步带在正常运行情况下,与带轮啮合部分同步带带齿,相邻带齿之间受力不同㊂带齿受切向压力大,则该带齿下部分强力层所受拉力也相应较大㊂刚啮入的带齿随着带轮转动带齿所受切向压力逐渐减小,该带齿所对应节距内的强力层所受拉力也变小㊂这就形成了如图8所示的云图,在紧边上强力层所受应力最大,随着带齿的啮合,强力层受力逐渐减小㊂图11㊀带轮转矩曲线Fig.11㊀Pulleytorquecurve在RecurDyn仿真软件中,结果输出中可选择输出每个采样时刻节点的坐标值,同步带在x⁃y平面中转动,选择任一节点输出x㊁y两个坐标值,如图12所示㊂图12㊀节点坐标值变化曲线Fig.12㊀Variationcurveofnodecoordinatevalue在同步带稳定运行后,旋转一周时间为0 089s,节点坐标值呈周期性变化㊂两相邻节点之间的距离,即为两齿节距Pb所对应强力层的长度㊂将相邻节点坐标值进行相减所得向量的模即为两个节点之间的距离,图13所示为相邻两节点在0 8 1s之间的距离变化㊂相邻两节点之间的距离变化也呈现周期性,每个图13㊀节距变化曲线Fig.13㊀Pitchchangingcurve周期可分为8个阶段,分别对应于紧边㊁啮入主动轮阶段㊁与主动轮完全啮合㊁啮出主动轮阶段㊁松边㊁啮入从动轮阶段㊁与从动轮完全啮合㊁啮出从动轮阶段,之后回归紧边㊂根据式(9)可知,节点之间距离越大,节点所对应带齿受切向压力越大㊂根据节点之间的距离变化,带齿在2,4,6,8四种情况下受力,其中又以2和8两种情况下受力最大㊂根据图13所示带齿之间的距离在与带轮啮合后逐渐减小至原始值,在脱离带轮后又将逐渐增大,带齿在与带轮啮入和啮出阶段受力较大,在与同步带啮合的其他时段受力相对较小㊂根据云图可知,强力层受力最大时在紧边,受力最小时在与带轮完全啮合后,松边受力趋于两种情况之间㊂采用两节点之间距离的变化值来进行分析,带轮为28齿,在同步带上任意选取连续的21个节点,对20个相邻节距变化值进行分析㊂各节距随时间波动如图14所示㊂图14㊀节距变化三维图Fig.14㊀3⁃dimensionaldiagramofpitchvariation同步带在运行时转矩有波动,这部分转矩波动是由于带齿与带轮的啮合所产生的㊂带齿在完全啮合后,节点之间的距离随时间近似呈线性减小,且每个节距的减小情况近乎相似,在图14中体现为不同节距减小,曲线可以组成一个平面㊂对图14截取某一时刻的㊀748㊀机㊀㊀械㊀㊀强㊀㊀度2023年㊀曲线,如图15所示,即为所有啮合带齿之间的距离变化值㊂由图15可知,在距离增加以及减小时可近似视为线性,相邻齿之间的受力大小呈线性下降或增加㊂图15㊀节距距离波动曲线Fig.15㊀Fluctuationcurveofpitchdistance对啮合带齿进行分析,针对在前一个带齿刚好完全啮合后一个带齿还没有接触带轮的情况下,该时刻共有16个带齿啮合㊂图15中节距波动有负数,其原因在于同步带与带轮啮合,同步带呈现圆弧状,但在图14中的节距计算的是两节点之间的直线距离,两者之间存在差值㊂因此,对于距离波动进行圆弧补偿,其中a由式(11)求得:a=(Pb-d1sinα2)/d1sinα2(11)式中,d1为带轮节圆直径;Pb为同步带原始节距,Pb=5mm;α是带轮齿角距㊂带齿所受切向压力可以通过式(12)进行计算:F=kc(Δdi-Δdi-1)(1+a)(12)式中,Δdi为节距编号为i的距离波动,带齿相邻节距强力层的拉力差即为该带齿所受切向压力㊂4㊀结果对比与分析㊀㊀对于理论计算结果与仿真分析结果展开对比,图16即为两种结果的对比图㊂其中理论计算结果由式(10)求解得到,仿真结果由式(12)计算得到,其中的kc和kt,采用有限元的方法对同步带进行齿体刚度和强力层刚度实验[15]得到,其中强力层拉伸刚度kc=759 8N/mm,带齿切向刚度kt=465 7N/mm㊂由图16可知,有限元分析结果与计算结果在首尾误差较小,在中间部分误差较大,主要原因在于这部分带齿受切向力较小,易产生误差,但是误差对于整条同步带的受力影响较小㊂且计算结果与云图较为符合,啮合部分带齿的首尾部分受力较大,中间部分受力较小㊂带齿不啮合部分带齿基本不受力,与带轮啮合部分带齿只有刚啮入带轮以及即将啮出带轮部分带齿受力最大,带齿受力并不均匀㊂每个带齿都在经历切向压力变化的循环,但是在循环中带齿切向压力波动较图16㊀仿真结果与理论计算结果对比Fig.16㊀Comparisonofsimulationresultsandtheoreticalcalculationresults大,在负载较大的情况下,则带齿经历的切向压力循环中最大值会较大,长时间运行,带齿会在切向压力作用下将圆弧挤压为类似三角形的齿形㊂带齿在太大的切向压力下,也可能出现齿根断裂,甚至是带齿断裂脱落㊂5㊀结论㊀㊀本文针对同步带带齿受力展开研究,同步带与带轮之间接触采用弹簧替代,对同步带进行离散化处理,推导出一个计算带齿切向压力矩阵模型,解决了带齿切向压力计算困难的问题㊂采用有限元仿真对矩阵模型进行验证,结果表明,矩阵模型与仿真结果差距较小㊂1)该模型在已知同步带参数的情况下,可简便计算出啮合区域各带齿切向受力大小,为同步带传动系统设计提供了一个准确且简便的计算方法㊂2)由矩阵模型可知,优化带齿刚度和强力层拉伸刚度的比值,可实现带齿受力更均匀,增加同步带使用寿命和额定负载,为同步带的优化提供一个优化方式㊂3)同步带齿根断裂㊁带齿脱落等故障发生时,带齿切向刚度降低,即带齿切向压力变化,带齿造成的转矩波动也发生相应变化,为同步带带齿故障诊断提供理论基础㊂参考文献(References)[1]㊀刘㊀军,夏梦毫,黄㊀斌.同步齿形带传动中带的发展及制造[J].现代制造技术与装备,2020,56(12):52⁃54.LIUJun,XIAMengHao,HUANGBin.Manufactureanddevelopmentofbeltinsynchronousbeltdrive[J].ModernManufacturingTechnologyandEquipment,2020,56(12):52⁃54(InChinese).[2]㊀秦书安,周㊀鹏,周玉杰,等.带传动行业发展状况综述[J].机械传动,2020,44(8):1⁃7.QINShuAn,ZHOUPeng,ZHOUYuJie,etal.Summaryofthedevelopmentofbeltdriveindustry[J].JournalofMechanicalTransmission,2020,44(8):1⁃7(InChinese).[3]㊀郭建华,孟庆鑫,于㊀鑫,等.基于RecurDyn同步带传动精度研㊀第45卷第3期傅建楠等:同步带带齿啮合应力仿真与分析749㊀㊀究[J].机械强度,2017,39(4):858⁃863.GUOJianHua,MENGQingXin,YUXin,etal.TransmissionaacuracyofsynchronousbeltbasedonRecurDyn[J].㊀JournalofMechanicalStrength,2017,39(4):858⁃863(InChinese).[4]㊀YANGG,YANGL,CAOM.SimulationanalysisoftimingbeltmovementcharacteristicsbasedonRecurDyn[J].VibroengineeringProcedia,2019(22):13⁃18.[5]㊀史尧臣,陈国平,李占国,等.基于声阵列技术的汽车同步带噪声源识别[J].汽车工程,2020,42(11):1566⁃1570.SHIYaoChen,CHENGuoPing,LIZhanGuo,etal.Noisesourceidentificationofvehiclesynchronousbeltbasedonsoundtechnology[J].AutomotiveEngineering,2020,42(11):1566⁃1570(InChinese).[6]㊀史尧臣,陈国平,李占国,等.三轮一带传动系统噪声仿真与试验验证[J].西安交通大学学报,2019,53(8):76⁃81.SHIYaoChen,CHENGuoPing,LIZhanGuo,etal.Noisesimulationandexperimentalverificationofthree⁃pulleyone⁃beltdrivesystem[J].JournalofXiᶄanJiaotongUniversity,2019,53(8):76⁃81(InChinese).[7]㊀卢小锐,高文志,张良良,等.基于Excite⁃TimingDrive的正时同步带系统动力学分析[J].振动与冲击,2013,32(11):66⁃69.LUXiaoRui,GAOWenZhi,ZHANGLiangLiang,etal.Dynamicanalysisofasynchronousbeltdrivebasedonexcite⁃timing[J].JournalofVibrationandShock,2013,32(11):66⁃69(InChinese).[8]㊀曹忠亮,胡清明,杨英东,等.基于RecurDyn的汽车同步带传动性能研究[J].机械强度,2017,39(3):652⁃656.CAOZhongLiang,HUQingMing,YANGYingDong,etal.ResearchontransmissioncharacteristicofautomotivesynchronousbeltbasedonRecurDyn[J].JournalofMechanicalStrength,2017,39(3):652⁃656(InChinese).[9]㊀LONGS,ZHAOX,SHANGGUANWB,etal.Modelingandvalidationofdynamicperformancesoftimingbeltdrivingsystems[J].MechanicalSystemsandSignalProcessing,2020(144):106910.[10]㊀JIASS,SONGYM.Elasticdynamicanalysisofsynchronousbeltdrivesystemusingabsolutenodalcoordinateformulation[J].NonlinearDynamics,2015,81(3):1393⁃1410.[11]㊀JOHANNESSONT,DISTNERM.Dynamicloadingofsynchronousbelts[J].JournalofMechanicalDesign,2002,124(1):79⁃85.[12]㊀BASSOR.Detectionofreducedtoothstiffnessinsynchronousbeltsbymeansofpulleyvibrationmonitoring[J].ProceedingsoftheInstitutionofMechanicalEngineersPartD,JournalofAutomobileEngineering,2006,220(7):947⁃957.[13]㊀郭建华,魏㊀来,曹忠亮,等.基于RecurDyn的新圆弧齿同步带啮合传动性能研究[J].机械传动,2019,43(1):1⁃4.GUOJianHua,WEILai,CAOZhongLiang,etal.Researchofthemeshingdrivingperformanceofnewarctooth㊀synchronousbeltbasedonRecurDyn[J].JournalofMechanicalTransmission,2019,43(1):1⁃4(InChinese).[14]㊀史尧臣,李占国,李水清,等.汽车同步带传动噪声仿真分析与试验研究[J].机械传动,2016,40(9):145⁃149.SHIYaoChen,LIZhanGuo,LIShuiQing,etal.Simulationanalysisandexperimentalstudyoftheautomobilesynchronousbeltdrivenoise[J].JournalofMechanicalTransmission,2016,40(9):145⁃149(InChinese).[15]㊀李㊀妍.汽车圆弧齿同步带的传动性能动力学仿真与试验研究[D].长春:长春理工大学,2014:15⁃19.LIYan.DynamicSimulationandteststudyontransmissionperformanceofautomotivearctoothedsynchronousbelt[D].Changchun:ChangchunUniversityofScienceandTechnology,2014:15⁃19(InChinese).。
基于SolidWorks simulation 分析齿轮接触应力

检测鉴定基于SolidWorks simulation分析齿轮接触应力农业机械运用齿轮传动,传动比准确,传动效率高,使用寿命长,设计齿轮时科学分析齿轮失效原因非常必要。
本文基于SolidWorks simulation分析齿轮接触应力,通过仿真实验证实,提出的有效性方法,可以大大提高农机齿轮的寿命和效率。
一、问题提出轮齿的失效主要包括轮齿折断、齿面点蚀、齿面胶合、齿面磨损、轮齿塑性变形等。
其中,轮齿折断主要发生在轮齿的齿根部,因为轮齿啮合受力时根部的应力最大,齿根过渡部分的形状突变等原因引起应力集中。
齿轮的危险处应力分析是进行强度校核计算的,也是为下一步其相配合轴的设计、选择作准备。
SolidWorks Simulation是一个与 SolidWorks 完全集成的设计分析系统,设计仿真一体化无缝集成,将仿真操作界面,模拟仿真流程无缝融入到SolidWorks的整个设计过程中。
实现了同一软件下计算机辅助设计与计算机辅助有限元分析无缝集成结合。
SolidWorks Simulation 提供了通过计算机解决方案来进行应力分析、频率分析、扭曲分析、热分析和优化分析。
凭借着快速解算器的强有力支持,使得设计师能够使用个人计算机快速解决大型问题。
SolidWorks Simulation 节省了大量设计所需的时间和精力,可大大缩短产品上市周期。
本文通过在 SolidWorks simulation 环境下对齿轮进行应力有限元分析。
模拟仿真分析齿轮齿根处的应力分布情况,找到齿根最有可能出现的危险截面,从而完善优化设计,避免齿轮折断失效引起的故障情况出现。
二、前期准备1.建模根据实际需要,运用slidwoks设计功能创建一对啮合的渐开线直齿齿轮。
利用solidwoks设计功能创建三维图形并模拟装配配合。
小齿轮模数为2,齿数31,压力角20度,齿宽21;大齿轮模数为2,齿数67,压力角20度,齿宽20。
2.指派材料材料选用SolidWorks simulation自带材料库中的材料:合金钢。
齿轮接触应力的有限元分析在UG和ANSYS中的实现
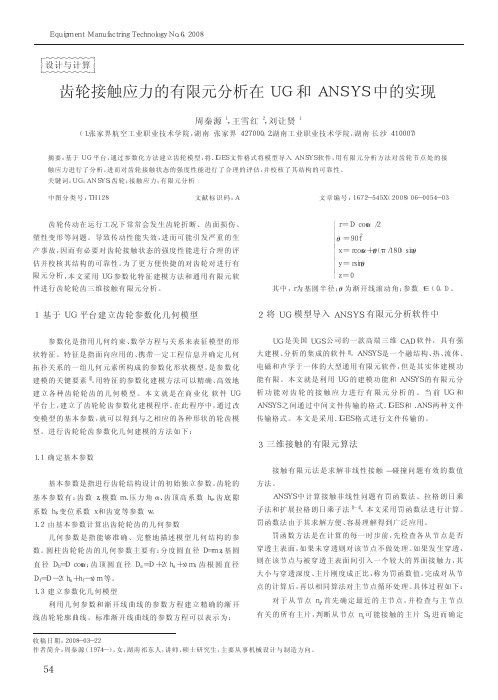
EquipmentManufactringTechnologyNo.6,2008设计与计算"!"!!!!"!"收稿日期:2008-03-22作者简介:周秦源(1974—),女,湖南祁东人,讲师,硕士研究生,主要从事机械设计与制造方向。
齿轮接触应力的有限元分析在UG和ANSYS中的实现周秦源1,王雪红2,刘让贤1(1.张家界航空工业职业技术学院,湖南张家界427000;2.湖南工业职业技术学院,湖南长沙410007)摘要:基于UG平台,通过参数化方法建立齿轮模型,将.IGES文件格式将模型导入ANSYS软件,用有限元分析方法对齿轮节点处的接触应力进行了分析,进而对齿轮接触状态的强度性能进行了合理的评估,并校核了其结构的可靠性。
关键词:UG;ANSYS;齿轮;接触应力;有限元分析中图分类号:TH128文献标识码:A文章编号:1672-545X(2008)06-0054-03齿轮传动在运行工况下常常会发生齿轮折断、齿面损伤、塑性变形等问题。
导致传动性能失效,进而可能引发严重的生产事故,因而有必要对齿轮接触状态的强度性能进行合理的评估并校核其结构的可靠性。
为了更方便快捷的对齿轮对进行有限元分析,本文采用UG参数化特征建模方法和通用有限元软件进行齿轮轮齿三维接触有限元分析。
1基于UG平台建立齿轮参数化几何模型参数化是指用几何约束、数学方程与关系来表征模型的形状特征。
特征是指面向应用的、携带一定工程信息并确定几何拓扑关系的一组几何元素所构成的参数化形状模型,是参数化建模的关键要素[1]。
用特征的参数化建模方法可以精确、高效地建立各种齿轮轮齿的几何模型。
本文就是在商业化软件UG平台上,建立了齿轮轮齿参数化建模程序。
在此程序中,通过改变模型的基本参数,就可以得到与之相应的各种形状的轮齿模型。
进行齿轮轮齿参数化几何建模的方法如下:1.1确定基本参数基本参数是指进行齿轮结构设计的初始独立参数。
齿轮强度有限元分析疲劳仿真接触应力弯曲应力硕士论文
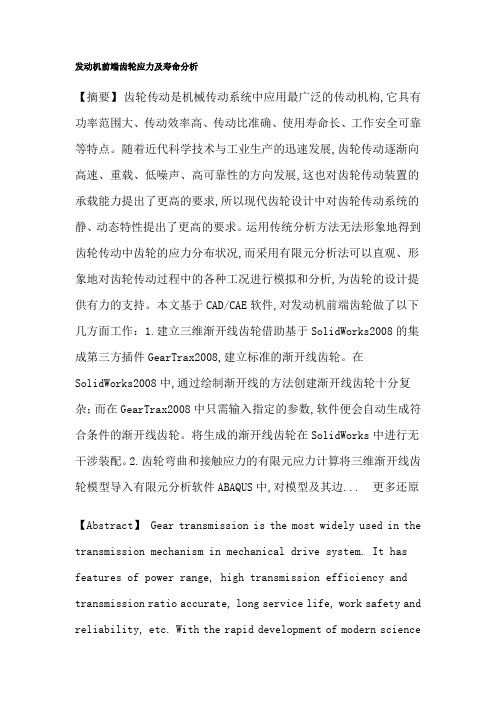
发动机前端齿轮应力及寿命分析【摘要】齿轮传动是机械传动系统中应用最广泛的传动机构,它具有功率范围大、传动效率高、传动比准确、使用寿命长、工作安全可靠等特点。
随着近代科学技术与工业生产的迅速发展,齿轮传动逐渐向高速、重载、低噪声、高可靠性的方向发展,这也对齿轮传动装置的承载能力提出了更高的要求,所以现代齿轮设计中对齿轮传动系统的静、动态特性提出了更高的要求。
运用传统分析方法无法形象地得到齿轮传动中齿轮的应力分布状况,而采用有限元分析法可以直观、形象地对齿轮传动过程中的各种工况进行模拟和分析,为齿轮的设计提供有力的支持。
本文基于CAD/CAE软件,对发动机前端齿轮做了以下几方面工作:1.建立三维渐开线齿轮借助基于SolidWorks2008的集成第三方插件GearTrax2008,建立标准的渐开线齿轮。
在SolidWorks2008中,通过绘制渐开线的方法创建渐开线齿轮十分复杂;而在GearTrax2008中只需输入指定的参数,软件便会自动生成符合条件的渐开线齿轮。
将生成的渐开线齿轮在SolidWorks中进行无干涉装配。
2.齿轮弯曲和接触应力的有限元应力计算将三维渐开线齿轮模型导入有限元分析软件ABAQUS中,对模型及其边... 更多还原【Abstract】 Gear transmission is the most widely used in thetransmission mechanism in mechanical drive system. It has features of power range, high transmission efficiency and transmission ratio accurate, long service life, work safety and reliability, etc. With the rapid development of modern scienceand technology and industrial production, gear transmission develops gradually to high-speed, overlap, low noise and high reliability. All these put forward higher request to carrying capacity of the gear tra... 更多还原【关键词】齿轮强度;有限元分析;疲劳仿真;接触应力;弯曲应力;【Key words】gear strength;finite element analysis;fatigue simulation;contact stress;bending stress;摘要5-7ABSTRACT 7第一章绪论11-161.1 本文研究背景及意义11-121.2 齿轮研究的现状与发展趋势12-131.2.1 齿轮强度研究的历史与发展121.2.2 齿轮CAD/CAE的研究现状与发展12-131.3 疲劳研究的历史及发展13-151.3.1 疲劳研究的历史13-141.3.2 疲劳仿真的发展14-151.4 本文研究的主要内容15-16第二章发动机前端齿轮的三维建模及接触理论16-222.1 发动机前端齿轮简介16-172.2 前端齿轮的三维建模17-182.3 赫兹接触理论18-22第三章齿轮接触和弯曲应力的有限元计算22-543.1 有限单元法及有限元软件简介22-263.1.1 有限单元法22-243.1.2 接触问题有限元法介绍24-253.1.3 有限元软件简介25-263.2 齿轮中接触应力的有限元计算26-443.2.1 非线性有限元理论273.2.2 接触应力的有限元计算27-363.2.3 计算结果的处理与分析36-443.2.4 摩擦力对接触应力的影响443.3 齿轮中弯曲应力的有限元计算44-543.3.1 弯曲应力的有限元计算45-493.3.2 弯曲应力的对比分析49-54第四章齿轮疲劳寿命的仿真分析54-684.1 疲劳的基本概念544.1.1 疲劳的特点544.2 疲劳理论54-594.2.1 疲劳累积损伤理论54-564.2.2 疲劳设计方法56-584.2.3 疲劳载荷谱的获取与处理58-594.2.4 材料的疲劳性能594.3 齿轮疲劳寿命仿真计算59-654.3.1 MSC.fatigue简介604.3.2 疲劳仿真分析及结果60-654.4 影响疲劳寿命的主要因素65-68第五章总结与展望68-705.1 总结685.2 展望68-70参考文献【索购全文】Q联系Q:138113721 Q联系Q: 139938848全文提供服务费:25元RMB 即付即发支付宝账号:xinhua59168@【说明】1、本站为中国学术文献总库合作代理商,作者如对著作权益有异议请与总库或学校联系;2、为方便读者学习和引用,我们可将图片格式成WORD文档,费用加倍。
齿轮轮齿接触力仿真研究

点 c 时为零 ,转为负值后继续减
小。
设啮合摩擦力为 f , 如图 4
所示 ,当 b 点在 N1 与 c 之间 ,有
T = Fn ×r1′×cosα- f ×N1 b (8)
当 b 点落于 c 点时 ,有
T = Fn ×r1′×cosα
(9)
图 4 轮齿载荷图
当 b 点在 c 点与 N2 之间时 ,有
6 ,经计算得出传动比在 0. 6981 与 0. 7043 之间围绕 0. 70 上下浮动 ,最大误差为 0. 6 % , 与设计传动比相符 , 因此认为建立的虚拟样机是准确的 , 可以代替实物样 机进行试验 。
(2) 如图 7 所示 , 每对轮齿啮合开始和结束 , 即有 两对轮齿同时啮合时 , 单齿齿廓法向力约为最大法向 力的 1/ 2 ,总载荷在两对齿间等比例分配 ; 只有一对轮 齿啮合时 , 随着摩擦力方向的改变 , 法向力将产生突 变 。由 曲 线 图 得 节 点 啮 合 前 一 点 的 法 向 力 均 值 为 16149N ,由式 ( 8) 得出的结果为 15878N , 相对误差为 1. 70 % ;节点啮合后一点的法向力均值为 15564N , 由 式 (10) 得出的结果为 15837N , 相对误差为 1. 72 % 。误 差在合理范围内 ,结果与理论规律完全相符 ,证实此模 型正确可靠 。
分别在两齿轮与箱体之间施加了旋转副 ( Revo2 lute) ,在大齿轮质心施加驱动力矩 ( Torque) ,在小齿轮 上加运动约束 (Motion) ,轮齿共轭齿面间接触用曲线 - 曲线接触 (curve - curve) 来定义 ,方法如下 : 写出大 齿轮与小齿轮齿廓渐开线方程 ,用 Matlab 编程并计算 , 得出轮廓曲线离散数据点 ,写成 ADAMS 的矩阵格式 (MATRIX) 文件 ,在 ADAMS 中读入矩阵文件生成矩阵 数据 元 素 , 利 用 ADAMS/ View 提 供 的 样 条 曲 线 工 具 (Spline) 依据矩阵数据元素创建二维样条曲线 ,通过定 位 ,准确地嵌入到实体零件中去 ,并将不具备质量 、转 动惯量等物理特性的此样条曲线与相应的齿轮合并为 一个刚体 ,而此合并对齿轮刚体的力学行为并不产生 影响 。至此 ,齿轮系统虚拟样机已建成 。设置合适的 接触参数就可进行仿真 。
- 1、下载文档前请自行甄别文档内容的完整性,平台不提供额外的编辑、内容补充、找答案等附加服务。
- 2、"仅部分预览"的文档,不可在线预览部分如存在完整性等问题,可反馈申请退款(可完整预览的文档不适用该条件!)。
- 3、如文档侵犯您的权益,请联系客服反馈,我们会尽快为您处理(人工客服工作时间:9:00-18:30)。
考虑装配误差的齿轮接触应力仿真
变速箱是各种重卡及其它汽车的“心脏”,重卡中变速箱工作的正常与否直接决定了该重卡的性能,而变速箱中的每个齿轮又是组成这颗“心脏”的一条条“血管”。
随着工业商业推动物流业的飞速发展,使得各类卡车逐步向大载重发展,这样对卡车的性能,特别是对卡车中变速箱的性能提出了更高的考验,这样对变速箱内部各种齿轮的性能及装配就提出了更高的要求。
在实际生产生活中,重卡变速箱的齿轮时常因过载而出现各种损坏。
某齿轮集团,在某型号的变速箱进行过载实验的过程中,一对啮合的齿轮多次发生了齿根裂纹甚至断齿的情况。
这种情况在重卡运行过程中,一旦发生后果极为严重,轻者影响正常运输,重者极易出现安全问题。
该集团在生产中发现多数齿根裂纹甚至断齿的情况,绝大多数是由各种原因导致的装配误差所引起的,而在诸多原因中,装配时的齿间隙误差和心轴的平行度误差成为导致齿轮啮合异常的主要原因。
在实际生产中变速箱齿轮装配时齿间隙误差和心轴的平行度误差均是由工程师凭经验给出,而在学术研究时,分析啮合齿轮所受的接触应力时,多为理论上的计算和算法上的研究,很少将齿轮啮合的实际工况因素考虑在内。
所以对实际生产时的考虑装配误差的齿轮啮合时的应力分析就显得尤为重要。
本文针对某齿轮集团生产的变速箱中的一对出现啮合异常的斜齿轮进行了Pro/E建模,在仿真分析时,分别从静力学和动力学两个方面进行分析,每个方面分别计算分析了装配时带有齿侧隙误差的工况和装配时带有轴平行度误差的工况。
在具体计算分析时,利用ANSYS与Pro/E之间的较好的链接性,将在Pro/E中建好的模型导入ANSYS中进行计算与分析,在静力学分析时主要运用ANSYS有限元分析软件对其进行计算与分析,在动力学分析时主要运用ANSYS中LS-DYNA模块对其进行计算分析。
通过静力学与动力学两个方面的系列的计算与分析,最终给出该对齿轮在装配时齿侧隙误差与轴平行度误差的误差范围。
课题的实验分析计算结果对实际生产中齿轮的装配与安装具有实际的指导意义。
同主题文章
[1].
乐晓斌,胡宗武,范祖尧. 齿轮接触疲劳可靠度的计算方法' [J]. 机械设计与研究. 1993.(03)
[2].
乔人光. 浅谈齿轮传动的噪音和啮合关系' [J]. 机械设计与制造. 1998.(05)
[3].
乐晓斌,邹苏燕. 齿轮接触疲劳可靠性寿命的计算' [J]. 机械传动. 1994.(S1)
[4].
苏宝生
,朱爱民
,许建飞. 2OCrMnTi齿轮接触疲劳强度的试验研究' [J]. 华东船舶工业学院学报(自然科学版). 1987.(02)
[5].
李绍彬. 起重机用齿轮接触强度计算方法的研讨' [J]. 机电产品开发与创新. 2008.(02)
[6].
齐人光. 浅谈齿轮传动的噪音和啮合关系' [J]. 机械研究与应用. 1998.(04)
[7].
关云飞,沈晓明. ANSYS在齿轮设计和计算中的应用' [J]. 机电工程技术. 2004.(02)
[8].
郭长城,翟仕儒,韩福辉. 斜齿轮副的测绘方法' [J]. 一重技术. 2005.(06)
[9].
DSG变速箱' [J]. 汽车与运动. 2007.(01)
[10].
刘斌彬. ANSYS有限元齿轮接触及弯曲应力研究' [J]. 机电技术. 2009.(03)
【关键词相关文档搜索】:机械制造及其自动化; 斜齿轮; 装配误差; ANSYS/LS-DYNA; 应力
【作者相关信息搜索】:太原理工大学;机械制造及其自动化;李文斌;孙志星;。