大专毕业设计(完整)
2024年大专毕业设计总结样本(2篇)

2024年大专毕业设计总结样本随着时代的不断进步和社会的发展,大专教育在培养具有实践能力和创新意识的人才方面发挥着重要的作用。
作为大专生,我在毕业设计中深入学习和实践了我所学的知识和技能,通过独自完成一个项目的全过程,不仅增强了我对专业知识的理解和运用能力,也提高了我的团队合作和解决问题的能力。
我的毕业设计主题是“智能家居系统的设计与开发”。
在这个项目中,我使用了嵌入式系统和物联网技术,设计和开发了一个能够自动控制家居设备的智能家居系统。
通过该系统,用户可以通过手机和电脑远程控制家中的灯光、电视、空调等设备,同时也可以根据习惯和需求进行自动化设置,实现自动开关和定时操作。
整个设计过程包括需求分析、系统设计、硬件和软件开发、测试和调试等多个阶段。
在需求分析阶段,我通过对市场调研和用户需求分析,确定了设计目标和功能要求。
在系统设计阶段,我绘制了系统的整体框架图和各个模块之间的关系图,并根据需求分析的结果确定了硬件和软件的配置。
在硬件开发阶段,我选用了适合该系统的各类传感器和执行器,并进行连接和调试。
在软件开发阶段,我使用了嵌入式系统的开发工具和编程语言,编写了相应的控制程序和用户界面。
最后,在测试和调试阶段,我对整个系统进行了功能性和可靠性测试,并进行了相应的优化和修正。
在整个毕业设计过程中,我积极思考和解决了许多技术和团队合作上的问题。
在技术方面,我遇到了传感器与执行器的连接问题、系统稳定性和安全性问题等。
通过查找资料、请教老师和同学的帮助,我逐渐解决了这些问题,并对相关的知识有了更深入的了解。
在团队合作方面,我与同学合作完成了系统的开发和测试,我们互相协作、相互学习,共同完成了这个项目。
通过与团队的合作,我学会了沟通协调和问题解决的能力,这对我以后的工作和学习都将有很大的帮助。
通过这个毕业设计项目,我不仅学到了很多专业知识和技能,也提高了自己的综合素质和创新能力。
在这个过程中,我不仅仅是一个学习者,更是一个实践者和创造者。
大专毕业设计范文

大专毕业设计范文好嘞,以下是为您创作的一篇文章:哎呀,咱来说说大专毕业设计这档子事儿!大专生活就像一场精彩的冒险,而毕业设计呢,那就是这场冒险里的大 boss 关卡!你想啊,三年的学习积累,不就为了在这最后的毕业设计里大展身手嘛!毕业设计一开始,那感觉就像站在一个陌生的路口,不知道往哪儿走。
选题就把人给难住了,这可不像在超市选零食,随便挑挑就行。
得琢磨自己感兴趣的,还得考虑有没有实际价值,这不是给自己找难题嘛?不过,要是选对了题,那就像是找到了通往宝藏的地图,心里那个美哟!然后就是收集资料,这可真是个大海捞针的活儿。
图书馆里的书堆得像小山,网上的信息多得像星星,眼睛都快看花啦!可还得耐着性子一点点筛选,生怕错过啥重要的。
这时候就想,要是知识能像快递一样直接送到眼前该多好!设计方案出来的时候,那心情,别提多激动啦!感觉自己就像个伟大的发明家,可再仔细一看,漏洞多得像筛子。
改来改去,都快把自己给改晕了。
有时候真想把这破方案扔一边去,可又不甘心,咬咬牙继续干。
做实验或者实践的时候,那状况百出的,仪器不听话,数据不准确,就好像全世界都在跟自己作对。
这时候心里那个着急啊,头发都快愁白了。
但是,当终于得到理想的数据,那种喜悦,就像大热天吃了一口冰西瓜,爽到心里去。
写论文的过程更是煎熬,一个字一个字地敲,一句话一句话地琢磨。
格式要求多得让人头疼,引用标注得小心翼翼,生怕出错。
这不是在写论文,简直是在绣花啊!不过,当看着自己的毕业设计一点点完善,从一个粗糙的想法变成一个完整的作品,那种成就感,没法用言语形容。
这不就像看着自己亲手种下的种子,一点点发芽、开花、结果吗?大专毕业设计,虽然过程辛苦,但是收获满满。
它让我们学会了坚持,懂得了耐心,更重要的是,让我们看到了自己的潜力。
谁说大专生就不能做出优秀的设计?咱们一样可以!所以啊,别害怕困难,别轻易放弃,冲就完事儿!这毕业设计,就是咱们证明自己的舞台,让咱们在这舞台上尽情绽放光芒!。
毕业设计范文模板大专

毕业设计范文模板大专学生姓名:[你的名字]专业:[专业名称]指导教师:[导师名字]完成日期:[具体日期]一、前言。
咱这大专的毕业设计就像是一场独特的“毕业大冒险”。
在这个过程中,我可是经历了各种酸甜苦辣,就像坐过山车一样。
现在我终于能把这个成果拿出来“显摆”一下啦。
这毕业设计不仅是对我这几年大专学习的一个总结,更是我迈向未来的一个小跳板呢。
二、设计目的。
我为啥要做这个设计呢?其实很简单,就像是饿了要吃饭一样自然。
[阐述专业相关的需求或者实际生活中的需求]比如说,在我们日常生活中,[举例说明这个设计能解决的问题],但是现有的[相关产品或方法]总是有点不尽人意。
所以我就想,为啥我不自己搞一个东西来解决这个问题呢?这就像是看到地上有个坑,就想找块砖头把它填平一样。
三、设计内容。
# (一)整体方案。
我的这个设计啊,就像是搭积木一样。
首先我确定了一个大概的框架,这个框架就像是房子的骨架,要是骨架不结实,房子可就塌了。
我把整个设计分成了几个大的模块,每个模块就像一个小房间,都有自己的功能。
比如说,[模块1名称]负责[模块1功能],就像厨房负责做饭一样;[模块2名称]负责[模块2功能],就像是卧室负责睡觉休息。
这些模块相互配合,就构成了我的整个设计。
# (二)详细设计。
1. 模块1。
这个模块可费了我不少心思呢。
我先研究了好多资料,就像探险家在寻宝之前要先看地图一样。
然后我发现[阐述模块1设计思路的来源],于是我就根据这个思路开始动手设计。
我用了[具体技术或工具]来构建这个模块,这里面的每一个小零件就像乐高积木一样,要精心挑选和组合。
比如说,[具体阐述某个重要的部分或元件],它就像发动机一样,是这个模块的核心部分。
要是它出了问题,整个模块就像没了油的汽车,跑不动了。
2. 模块2。
模块2也不是好惹的。
我在设计它的时候,遇到了好多难题,就像在迷宫里迷路了一样。
不过我可没有轻易放弃,我找了各种方法来解决。
这个模块主要是[再次强调模块2的功能],我为了实现这个功能,采用了[具体的方法或算法]。
大专会计毕业设计范文
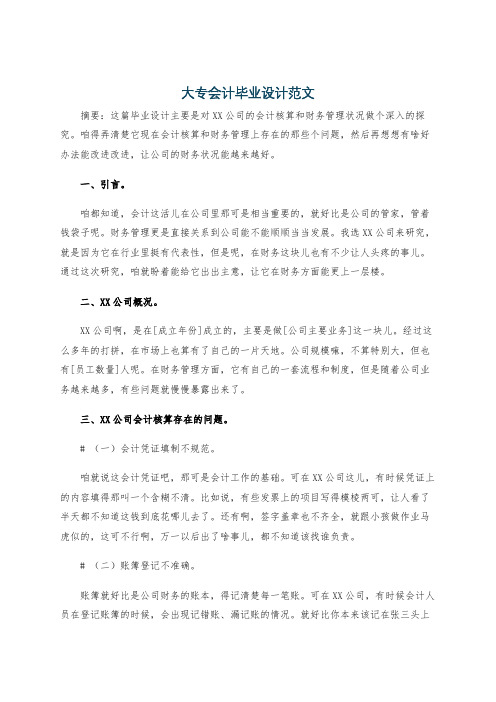
大专会计毕业设计范文摘要:这篇毕业设计主要是对XX公司的会计核算和财务管理状况做个深入的探究。
咱得弄清楚它现在会计核算和财务管理上存在的那些个问题,然后再想想有啥好办法能改进改进,让公司的财务状况能越来越好。
一、引言。
咱都知道,会计这活儿在公司里那可是相当重要的,就好比是公司的管家,管着钱袋子呢。
财务管理更是直接关系到公司能不能顺顺当当发展。
我选XX公司来研究,就是因为它在行业里挺有代表性,但是呢,在财务这块儿也有不少让人头疼的事儿。
通过这次研究,咱就盼着能给它出出主意,让它在财务方面能更上一层楼。
二、XX公司概况。
XX公司啊,是在[成立年份]成立的,主要是做[公司主要业务]这一块儿。
经过这么多年的打拼,在市场上也算有了自己的一片天地。
公司规模嘛,不算特别大,但也有[员工数量]人呢。
在财务管理方面,它有自己的一套流程和制度,但是随着公司业务越来越多,有些问题就慢慢暴露出来了。
三、XX公司会计核算存在的问题。
# (一)会计凭证填制不规范。
咱就说这会计凭证吧,那可是会计工作的基础。
可在XX公司这儿,有时候凭证上的内容填得那叫一个含糊不清。
比如说,有些发票上的项目写得模棱两可,让人看了半天都不知道这钱到底花哪儿去了。
还有啊,签字盖章也不齐全,就跟小孩做作业马虎似的,这可不行啊,万一以后出了啥事儿,都不知道该找谁负责。
# (二)账簿登记不准确。
账簿就好比是公司财务的账本,得记清楚每一笔账。
可在XX公司,有时候会计人员在登记账簿的时候,会出现记错账、漏记账的情况。
就好比你本来该记在张三头上的账,结果记到李四那儿去了,这不是闹笑话嘛。
而且啊,有些账目登记得也不及时,总是拖拖拉拉的,导致账目混乱,到月底对账的时候,那可真是让人头大。
# (三)财务报表编制不及时且不准确。
财务报表就像是公司的体检报告,得按时、准确地交出来,让老板和股东们清楚公司的财务状况。
可XX公司呢,有时候报表编制得特别慢,就像老太太走路一样,慢悠悠的。
专科生毕业设计范文

专科生毕业设计范文专科生毕业设计,那可是一段让人又爱又恨的经历啊!还记得刚开始接到毕业设计任务的时候,整个人都懵了,这啥呀?感觉就像被扔进了一个完全陌生的世界,啥都不懂,啥都不会。
心里直犯嘀咕:我能行吗?但咱专科生也不能认怂不是?于是乎,硬着头皮开始找资料,图书馆、网上,到处搜罗。
那感觉,就像在大海里捞针,好不容易找到一点有用的,就跟捡到宝似的。
设计的过程中,遇到的问题那叫一个多。
方案改了又改,数据算了一遍又一遍。
有时候真想把电脑给砸了,大喊一声:“这破玩意儿,不弄了!”可再一想,不行啊,这毕业设计可是关系到毕业的大事儿,怎么能轻易放弃?比如说有一次,为了一个小小的计算错误,我愣是熬了一个通宵。
眼睛都快睁不开了,脑袋也嗡嗡的。
当时就想,我这是图啥呀?但第二天看到自己终于把错误改过来,那种成就感,简直没法形容。
还有啊,和小组同学一起讨论的时候,那场面,可热闹了。
每个人都有自己的想法,争得面红耳赤的。
“你这个不行,太老套了!”“那你的能好到哪儿去?” 可就是在这样的争吵中,我们的思路越来越清晰,方案也越来越完善。
这毕业设计就像一场马拉松,过程虽然辛苦,但每跑一步,都离终点更近一步。
就像爬山,一路上磕磕绊绊,累得气喘吁吁,但当你终于登上山顶,看到那美丽的风景,一切都值了!想想那些为了毕业设计付出的日日夜夜,掉的头发,熬的黑眼圈,现在看来,都是成长的见证。
它让我学会了坚持,学会了面对困难不退缩,学会了团队合作。
难道这不是人生中宝贵的财富吗?专科生怎么了?我们也能通过自己的努力,完成一项出色的毕业设计!我们也有自己的梦想,也有追求卓越的权利!所以啊,别小看专科生的毕业设计,它是我们证明自己的机会,是我们走向未来的基石。
让我们一起加油,为了更美好的明天!。
专科毕业设计范本
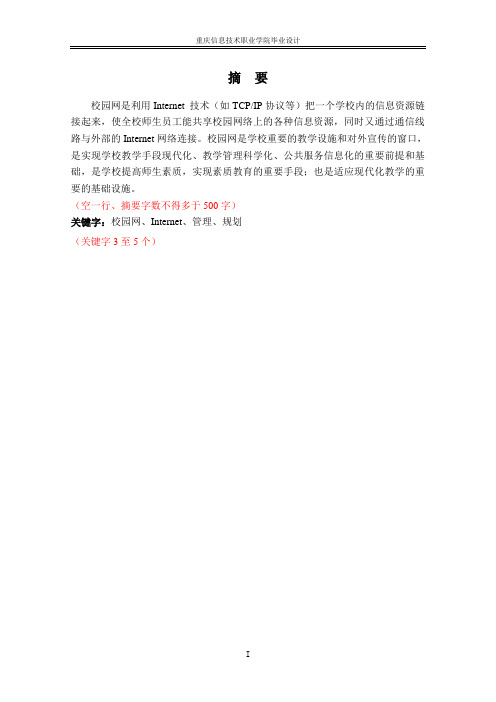
摘要校园网是利用Internet 技术(如TCP/IP协议等)把一个学校内的信息资源链接起来,使全校师生员工能共享校园网络上的各种信息资源,同时又通过通信线路与外部的Internet网络连接。
校园网是学校重要的教学设施和对外宣传的窗口,是实现学校教学手段现代化、教学管理科学化、公共服务信息化的重要前提和基础,是学校提高师生素质,实现素质教育的重要手段;也是适应现代化教学的重要的基础设施。
(空一行、摘要字数不得多于500字)关键字:校园网、Internet、管理、规划(关键字3至5个)目录摘要 (I)目录 (III)前言 (1)第1章校园网概述 (1)第1章校园网概述 (2)1.1建设背景和现状 (2)1.2 建设需求分析 (2)第2章校园网络的设计及原则 (3)第2章校园网络的设计及原则 (4)2.1 校园网实现的目的 (4)2.1.1 教学方面 (4)2.1.2 管理方面 (4)2.2 设计的原则 (5)2.2.1实用性 (5)2.2.2开放性 (5)总结 (6)参考文献 (7)(中文摘要以及目录,和论文正文之间编码方式不一样,中文摘要以及目录的编号采用希腊数字“I、II、III……”,论文从正文起采用罗马数字“1、2、3……”)前言当今世界,科学技术突飞猛进。
以计算机多媒体和网络技术为代表的信息技术,以惊人的发展速度,迅速在各领域运用,教育也面临信息技术的挑战。
校园网建设作为学校教育信息化的基础工程已引起了我国教育行政部门和学校的高度重视,并在全国掀起了一股校园网建设的热潮。
今年我有幸参与新兴中学学校园网规划和建设工作。
本文在新兴中学学校园网建设工作实践的基础上,就中小学校园网的规划和建设问题作初步的探讨。
由于网络它具有传输效率高,速度快,而且可以实时的传输和接受,所以它为现代企业和政府等部门的办公提供了方便,现在大多数企事业单位都在积极筹建校园网,为网上办公提供条件,而且能及时的接受上级指令传输给下级,笔记本还提供了移动办公,从而使网上办公不在受地理条件的约束,新兴中学校园网正是这一优点的具体体现。
(整理)专科(高职)毕业设计.
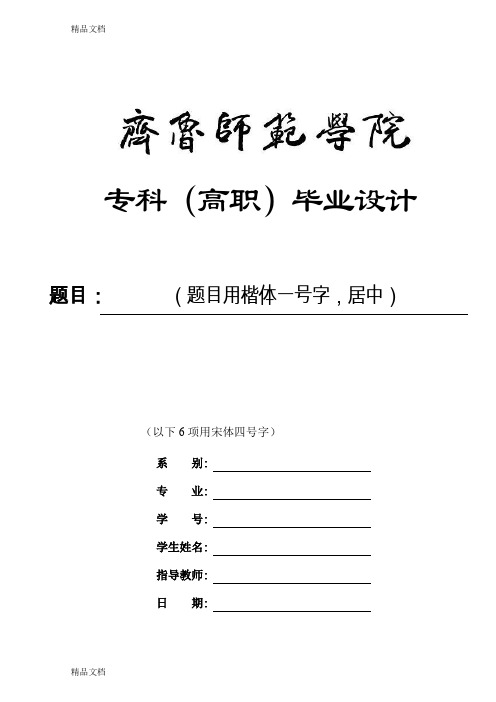
专科(高职)毕业设计题目:(题目用楷体一号字,居中)
(以下6项用宋体四号字)
系别:
专业:
学号:
学生姓名:
指导教师:
日期:
毕业设计纲要
参考标题:XXXX方案研究
摘要:对毕业设计内容概述,存在问题及改进办法作200字左右的描述。
关键词:XXXX;XXXX;XXXX;XXXX(不超过4个)
一、主要内容(选题背景、方案论证、过程描述等)
二、存在的问题
三、改进措施
规范要求:
1.毕业设计字数控制在3000字左右。
2.毕业设计可打印也可手写。
格式要求:
(1)中文题目居中、黑体、加粗、三号,英文题目三号、Times New Roman、加粗、居中放置。
(2)参考文献(黑体、小四号、加粗居、空两格)内容格式为、宋体、五号;
如:参考文献
[1] 郑霖柴宗新郑远昌等.《四川省地理》.四川科学技术出版社,1994.108-111.
(3)若有图表,图表的标题字体为宋体,小五号,居中;
(4)正文内容及参考文献全部用1.25倍行距,在“格式”选项中的“段落”设置窗口,采用多倍行距,行距设置值为1.25。
毕业设计(论文)成绩评定表系(院):专业:班级:。
大专毕业设计doc

大专毕业设计篇一:大专-毕业设计辽宁地质工程职业学院毕业(论文)设计资源系工程测量专业09 级1 班设计题目:VRS测量技术应用分析姓学号:XX02030121完成日期: XX年04月05号VRS测量技术应用分析摘要由于GPS测量定位技术是以后测量的主流,所以本文以实现基于对GPS测量定位技术能更深的发展为主要目的,先了解GPS测量技术的基本原理和特点为开始,进行细度的分析,我们知道,GPS定位技术发展到现在,已经更新了几个阶段,由最开始的只是简单的伪距单点定位,这种测量方法虽然可以达到预计的测量目的,但是测量时间长,定位效果很不好,精度低,受很多因素限制,随着信号技术处理的发展,有了GPS实时动态定位RTK技术,这种技术的出现,解决了很多问题,误差减小了,精度提高了,但是由于当时通讯技术的限制,在一些范围比较大的地区,RTK技术受到了限制,所以就出现了GPS网络RTK技术VRS系统,它的出现弥补了之前的缺陷,在之后也有很大的发展潜质。
关键字:GPS 基本原理特点 VRS 分析一、引言全球定位系统GPS(Global Positioning System)具有性能好、精度高、应用广的特点,是迄今最好的导航定位系统。
GPS定位技术原理为:卫星向地面接收机发射带有测距码的载波信号,卫星的轨道是已知的,那么地面点在某一时刻通过对接收到的卫星信号进行分析就可以得到卫星到地面点的距离,那么只需要3颗卫星就可以定出地面点的位置,但是接收机的时钟是不准确的,所以需要同时接收至少4颗卫星的信号才能准确地交会定出地面点的位置。
GPS定位可以分为绝对定位和相对定位。
绝对定位也叫单点定位,即利用GPS卫星和用户接收机之间的距离观测值直接确定用户接收机天线的绝对位置。
相对定位也叫差分定位,即至少用两台GPS接收机,同步观测相同的GPS卫星,确定两台接收机的相对位置,相对定位的精度较高。
由于信号在传播的过程中受到电离层、对流层、多路径效应等多方面的影响,GPS 发展初期定位精度一直很难达到理想的情况。
大专毕业教案设计模板范文

一、课程名称(例如:市场营销实务)二、授课对象(例如:大专三年级市场营销专业学生)三、授课时间(例如:2课时)四、教学目标1. 知识目标:- 理解市场营销的基本概念和原则。
- 掌握市场营销组合策略的构成要素。
- 了解市场调研的方法和技巧。
2. 能力目标:- 培养学生分析和解决市场营销问题的能力。
- 提高学生市场调研和营销策划的实际操作能力。
3. 情感目标:- 增强学生对市场营销的兴趣和职业认同感。
- 培养学生的团队合作精神和创新意识。
五、教学内容1. 市场营销概述- 市场营销的定义和功能- 市场营销环境分析- 市场营销的伦理和社会责任2. 市场调研- 市场调研的重要性- 市场调研的程序和方法- 市场调研报告的撰写3. 市场营销组合策略- 产品策略- 价格策略- 渠道策略- 促销策略六、教学重点与难点1. 教学重点:- 市场营销组合策略的运用- 市场调研的方法和技巧2. 教学难点:- 市场调研数据的分析和解读- 市场营销策略的综合运用七、教学方法1. 讲授法:系统讲解市场营销的基本理论和概念。
2. 案例分析法:通过实际案例分析,帮助学生理解和应用市场营销策略。
3. 讨论法:引导学生进行小组讨论,培养学生的分析和解决问题能力。
4. 实践操作法:组织学生进行市场调研和营销策划的实际操作,提高学生的实践能力。
八、教学过程第一课时1. 导入:通过市场现象引入课题,激发学生的学习兴趣。
2. 讲解市场营销概述:系统讲解市场营销的基本概念和原则。
3. 案例分析:选取典型案例,分析市场营销策略的运用。
第二课时1. 复习:回顾上节课的重点内容,巩固知识。
2. 讲解市场调研:详细介绍市场调研的程序和方法。
3. 实践操作:组织学生进行市场调研的模拟操作,指导学生撰写调研报告。
4. 总结:总结本节课的主要内容,布置课后作业。
九、课后作业1. 查阅资料,了解当前市场营销的新趋势。
2. 分析一个企业的市场营销策略,撰写分析报告。
大专毕业设计全套

大专毕业设计全套大专毕业设计全套大专毕业设计是大专学生在完成学业的最后一项任务,也是他们展示自己专业知识和技能的机会。
一套完整的大专毕业设计包括选题、调研、设计方案、实施、撰写论文和答辩等多个环节。
本文将介绍大专毕业设计全套的步骤和注意事项,帮助大专学生顺利完成毕业设计。
1. 选题选题是毕业设计的第一步,同学们可以根据自己的兴趣和专业背景选择适合的课题。
在选题时,要考虑到课题的研究价值、实施难度和可行性。
可以与导师进行交流,听取导师的建议和意见,确保选题的合理性和可行性。
2. 调研在选定课题后,需要进行相关的调研工作。
通过查阅文献、采访专家和实地调查等方式,了解相关领域的研究现状和问题。
调研的目的是为了对选题进行深入了解,为后续的设计方案提供理论依据。
3. 设计方案在调研的基础上,制定毕业设计的具体方案。
设计方案包括研究目标、方法、步骤和时间安排等内容。
要确保设计方案的合理性和可行性,同时考虑到时间和资源的限制。
4. 实施在设计方案确定后,开始实施毕业设计。
根据设计方案的要求,进行实验、调查、数据分析等工作。
实施过程中要注意数据的准确性和可靠性,遵循科学研究的原则和方法。
5. 撰写论文毕业设计的最终成果是一篇论文。
在撰写论文时,要按照学校的要求和格式进行排版和写作。
论文的结构一般包括摘要、引言、文献综述、研究方法、实验结果、讨论和结论等部分。
要注意论文的逻辑性和条理性,语言简练、清晰。
6. 答辩毕业设计完成后,需要参加答辩。
答辩是对毕业设计成果的评审和展示。
在答辩时,要准备好演讲稿和PPT,清晰地介绍自己的研究内容和成果。
同时要准备好回答评委的问题,展示自己的专业知识和能力。
在完成大专毕业设计的过程中,还有一些需要注意的事项:1. 时间管理:合理安排时间,确保每个环节都有足够的时间完成。
避免拖延和临时抱佛脚。
2. 导师指导:与导师保持良好的沟通和合作,及时向导师汇报工作进展,听取导师的指导和建议。
专科毕业设计模板
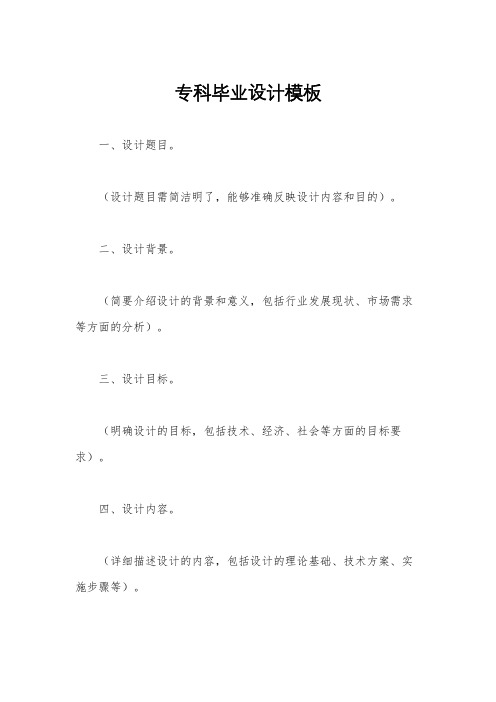
专科毕业设计模板
一、设计题目。
(设计题目需简洁明了,能够准确反映设计内容和目的)。
二、设计背景。
(简要介绍设计的背景和意义,包括行业发展现状、市场需求等方面的分析)。
三、设计目标。
(明确设计的目标,包括技术、经济、社会等方面的目标要求)。
四、设计内容。
(详细描述设计的内容,包括设计的理论基础、技术方案、实施步骤等)。
五、设计原理。
(对设计所涉及的理论知识和技术原理进行解释和阐述)。
六、设计方法。
(详细介绍设计所采用的方法和技术手段)。
七、设计步骤。
(按照时间顺序描述设计的实施步骤和计划安排)。
八、设计结果。
(对设计实施后的效果和成果进行描述和分析)。
九、设计总结。
(对整个设计过程进行总结,包括成功经验、不足之处和改进措施)。
十、参考文献。
(列举设计过程中所参考的文献、资料和数据来源)。
十一、附录。
(设计过程中所涉及的相关资料、图表、数据等的附录)。
以上就是专科毕业设计模板的内容,希望能够对您有所帮助。
祝您设计顺利,顺利完成毕业设计!。
机械专业大专毕业设计

机械专业大专毕业设计机械臂的设计与控制机械臂是一种由多个关节连接的机械装置,能够执行各种运动。
它们广泛应用于工业、医疗、军事和太空探索等领域。
本毕业设计旨在设计和控制一个具有特定运动要求的机械臂。
设计与建模机械臂设计包括确定关节数量、运动范围、力矩容量和材料选择。
针对特定任务,设计了一个具有 5 个自由度的机械臂。
使用计算机辅助设计 (CAD) 软件对机械臂进行建模,包括关节、连杆和执行器。
运动学分析运动学分析确定机械臂的运动范围和关节位置。
通过正运动学,计算特定关节位置下的末端执行器位置。
逆运动学确定末端执行器位置所需的关节角度。
动力学分析动力学分析确定机械臂运动对力矩和惯量的影响。
通过牛顿-欧拉方法,计算每个关节的力和力矩。
控制系统设计为了实现精确的运动控制,设计了一个基于微控制器的控制系统。
微控制器处理传感器的输入并生成执行器的控制信号。
控制算法采用比例-积分-微分 (PID) 控制,确保平滑且稳定的运动。
传感器集成各种传感器集成到机械臂中,以提供位置、速度、力和扭矩的反馈。
这些传感器包括编码器、加速度计、力和扭矩传感器。
传感器数据通过通信总线传输到微控制器。
仿真与验证使用计算机仿真来验证机械臂的设计和控制系统。
仿真包括运动学、动力学和控制算法。
仿真结果与分析模型进行比较,以确保准确性和鲁棒性。
实验测试构建了机械臂原型,并进行实验测试以评估其性能。
测试包括运动范围、精度、力矩容量和响应时间。
测试结果与仿真预测进行比较,并进行必要的调整。
优化与改进通过对设计和控制算法进行迭代优化,提高了机械臂的性能。
优化包括减轻重量、增加力矩容量和改进运动精度。
应用该机械臂可用于各种应用,包括:工业自动化:物料搬运、装配和焊接医疗手术:微创手术、康复治疗和药物输送军事侦察:爆炸物处理、目标识别和环境监测太空探索:航天器维修、月球和火星探索结论通过设计、控制、仿真和测试,成功开发了一个具有所需运动要求的机械臂。
大专毕业设计模板范文

大专毕业设计模板范文毕业设计模板范文
[学校名称]
[院系名称]
[专业名称]
毕业设计(论文)设计模板
一、课题名称:
二、研究的目的和意义:
三、国内外研究现状及发展趋势:
四、研究的主要内容:
五、研究的方法和途径:
六、研究的进度安排:
七、预期的研究结果:
八、毕业设计的组织和实施计划:
九、论文的组织结构:
参考文献:
附件清单:
注:
1. 该模板可根据实际情况进行调整和修改。
2. 模板中的内容仅供参考,具体课题的设计要根据实际需求进行深入研究和论证。
3. 根据学校和院系的要求,可能还需要添加其他的内容,如评审意见等。
4. 毕业设计模板范文应该明确地列出论文中各个章节的标题和内容,以便指导学生按照规定的格式进行写作。
以上是一个大专毕业设计模板范文的简要示例,具体的内容和格式可以根据实际情况进行调整和修改。
毕业设计模板范文应该包括课题名称、研究的目的和意义、国内外研究现状及发展趋势、研究的主要内容、研究的方法和途径、研究的进度安排、预期的研究结果、毕业设计的组织和实施计划、论文的组织结构等内容,以便指导学生进行毕业设计的写作和实施。
同时,根据学校和院系的要求,还可能需要添加其他的部分,如评审意见等。
大专毕业设计(完整)

长沙航空职业技术学院2021 届毕业设计说明书射线底片焊接缺点的影像辨别院 ( 系) :航空装备维修工程系学生姓名:田辉指导教师:蔡杰专业:检测技术及应用班级:检测0901达成时间:20 12-5-102021 届毕业生毕业设计(论文 )任务书长沙航空职业技术学院学生姓名田辉学号08 系别航空装备工程系班级检测 0902指导老师蔡杰设计 ( 论文 ) 题目 :射线底片焊接缺点的影像辨别1 整体设计纲要:射线检测技术 , 从最先的纯真胶片射线照相查验 , 经 100 多年的睁开 , 今日已成为以先进的数字技术为特色 , 包含射线照相查验、射线及时成像查验和射线层析检测等多种技术的无损检测手段。
因为拥有可自我监控检测工作质量和检测技术正确性的特征 , 已成为重要和宽泛应用的无损检测技术。
本文第一叙述了射线评片工作的根本要乞降原理,并联合金属资料焊接知识,要点解说了各样焊接缺点的种类和射线图像。
其次,对于射线工作中质量分级与评定做出解说,以抵达正确辨别图像的能力。
2 阶段设计任务:(1〕、确立论文题目,采集资料和参照资料,构想大概设计大纲(2〕、进行有关论文课题的编写(3〕、接受指导老师的改正建议并上交论文3 技术和量化要求:正确辨别射线照片上的影象、判断影象所代表的缺点性质的根基之一是拥有必定的资料和工艺方面的知识,进而掌握主要的缺点种类、形态及产生规律, 。
掌握缺点评级的根本方法。
4 参照文件和资料目录:[1]2021 优异毕业设计〔论文〕选编长沙航空职业技术学院教务处[2]光学手册陕西科技第一版社李景镇主编[3]无损检测手册李家伟等著[4]射线检测技术屠耀元等著[5]射线检测强天鹏主编浅谈射线检测图像的辨别纲要: X 射线与自然光并无实质的差别,都是电磁波,只是 X 射线的光量子的能量远大于可见光。
它能够穿透可见光不可以穿透的物体,并且在穿透物体的同时将和物质发生复杂的物理和化学作用,能够使原子发生电离,使某些物质发出荧光,还能够使某些物质产生光化学反应。
大专毕业教案设计模板

一、教学目标1. 知识目标:(1)了解毕业论文答辩的基本流程和注意事项。
(2)掌握论文答辩的技巧和方法。
(3)熟悉论文答辩的评分标准。
2. 能力目标:(1)培养学生独立思考、分析问题和解决问题的能力。
(2)提高学生的表达能力和沟通能力。
(3)锻炼学生的心理素质和抗压能力。
3. 情感目标:(1)激发学生对毕业论文的重视程度。
(2)增强学生的自信心和成就感。
(3)培养学生的团队协作精神和责任感。
二、教学内容1. 毕业论文答辩的基本流程2. 毕业论文答辩的注意事项3. 毕业论文答辩的技巧和方法4. 毕业论文答辩的评分标准三、教学过程1. 导入新课- 引导学生回顾毕业论文的撰写过程,激发学生对论文答辩的兴趣。
- 提出问题:什么是毕业论文答辩?毕业论文答辩有哪些流程和注意事项?2. 讲授新课- 毕业论文答辩的基本流程:答辩前准备、答辩过程、答辩结束。
- 毕业论文答辩的注意事项:着装得体、仪态大方、语言表达清晰、时间控制合理、应对突发状况等。
- 毕业论文答辩的技巧和方法:提前熟悉论文内容、做好PPT演示、提前演练、准备好答辩稿等。
- 毕业论文答辩的评分标准:论文质量、答辩表现、创新性、学术规范等。
3. 课堂互动- 分组讨论:针对答辩流程、注意事项、技巧和方法等方面进行讨论。
- 问答环节:学生提出问题,教师进行解答。
4. 实践环节- 学生分组进行模拟答辩,教师进行点评和指导。
- 学生互评,分享答辩经验。
5. 总结与作业- 教师总结本节课的主要内容,强调答辩的重要性。
- 布置作业:准备毕业论文答辩的PPT和答辩稿。
四、教学评价1. 课堂参与度:观察学生在课堂上的参与情况,包括提问、讨论、实践等环节。
2. 学生答辩表现:评估学生在模拟答辩中的表现,包括答辩内容、表达方式、时间控制等方面。
3. 学生反馈:收集学生对本节课的评价和建议。
五、教学反思1. 教师反思:针对本节课的教学内容、教学方法、教学效果等方面进行反思,为今后的教学提供借鉴。
毕业设计大专

毕业设计大专(经典版)编制人:__________________审核人:__________________审批人:__________________编制单位:__________________编制时间:____年____月____日序言下载提示:该文档是本店铺精心编制而成的,希望大家下载后,能够帮助大家解决实际问题。
文档下载后可定制修改,请根据实际需要进行调整和使用,谢谢!并且,本店铺为大家提供各种类型的经典范文,如工作总结、工作计划、心得体会、条据文书、合同协议、规章制度、应急预案、教学资料、作文大全、其他范文等等,想了解不同范文格式和写法,敬请关注!Download tips: This document is carefully compiled by this editor. I hope that after you download it, it can help you solve practical problems. The document can be customized and modified after downloading, please adjust and use it according to actual needs, thank you!Moreover, our store provides various types of classic sample essays, such as work summaries, work plans, insights, normative documents, contract agreements, rules and regulations, emergency plans, teaching materials, complete essays, and other sample essays. If you want to learn about different sample formats and writing methods, please pay attention!毕业设计大专在日常学习、工作或生活中,大家总少不了接触作文或者范文吧,通过文章可以把我们那些零零散散的思想,聚集在一块。
机械专业大专毕业设计

机械专业大专毕业设计机械设计与制造毕业设计项目背景本毕业设计旨在设计并制造一台高精度CNC加工中心,以满足现代制造业对复杂零件加工的要求。
设计目标实现高精度加工(公差小于0.005毫米)提高加工效率(加工时间小于30分钟)降低加工成本(材料和能源消耗)机械结构设计加工中心采用龙门式结构,由底座、立柱、横梁和工作台组成。
底座采用铸铁整体结构,确保稳定性和减振。
立柱采用钢结构,提供刚度和支撑。
横梁采用铝合金结构,减轻重量并提高加工速度。
工作台采用复合材料结构,吸振和隔振效果良好。
传动系统设计加工中心采用精密滚珠丝杠传动系统,由伺服电机直接驱动。
滚珠丝杠精度高、刚性好,满足高精度加工要求。
伺服电机提供高速、高扭矩和高响应性,提高加工效率。
控制系统设计控制系统采用运动控制卡和伺服驱动器。
运动控制卡对运动轨迹进行规划和控制,伺服驱动器根据指令控制电机运动。
控制系统具有高精度控制、实时监测和故障诊断功能。
电气系统设计电气系统为加工中心提供供电和控制。
电气柜内安装有配电柜、变压器、接触器和继电器。
电气系统采用安全可靠的连接方式,保证设备安全运行。
冷却系统设计加工中心采用液压冷却系统,由冷却液泵、冷却液箱和冷却管组成。
冷却液泵将冷却液输送到冷却管,冷却液流经加工区域,带走热量,保证加工精度。
试制与测试加工中心试制完成后,进行全面的性能测试,包括精度测试、速度测试、负载测试和耐久性测试。
测试结果表明,加工中心符合设计要求,能够满足高精度、高效率和低成本的加工需求。
经济分析加工中心的制造成本约为100万元。
根据市场调研,同类加工中心售价约为150万元。
因此,加工中心具有良好的经济效益。
结论本毕业设计成功设计和制造了一台高精度CNC加工中心,满足了现代制造业对复杂零件加工的要求。
加工中心具有高精度、高效率、低成本和良好的经济效益,具有广阔的市场前景。
毕业设计范文模板大专
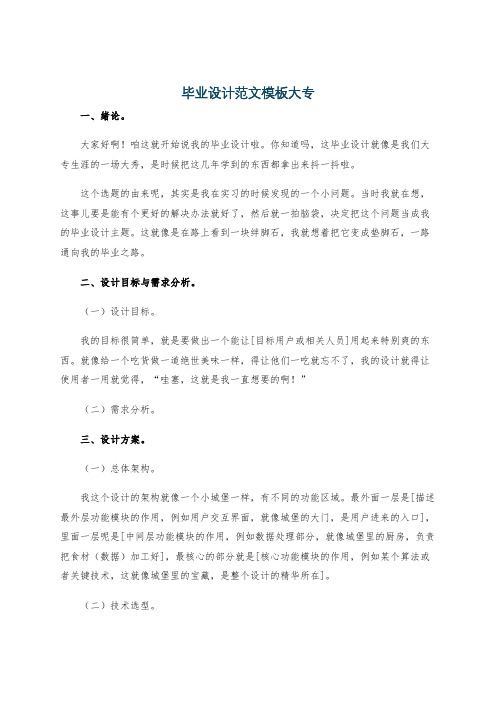
毕业设计范文模板大专一、绪论。
大家好啊!咱这就开始说我的毕业设计啦。
你知道吗,这毕业设计就像是我们大专生涯的一场大秀,是时候把这几年学到的东西都拿出来抖一抖啦。
这个选题的由来呢,其实是我在实习的时候发现的一个小问题。
当时我就在想,这事儿要是能有个更好的解决办法就好了,然后就一拍脑袋,决定把这个问题当成我的毕业设计主题。
这就像是在路上看到一块绊脚石,我就想着把它变成垫脚石,一路通向我的毕业之路。
二、设计目标与需求分析。
(一)设计目标。
我的目标很简单,就是要做出一个能让[目标用户或相关人员]用起来特别爽的东西。
就像给一个吃货做一道绝世美味一样,得让他们一吃就忘不了,我的设计就得让使用者一用就觉得,“哇塞,这就是我一直想要的啊!”(二)需求分析。
三、设计方案。
(一)总体架构。
我这个设计的架构就像一个小城堡一样,有不同的功能区域。
最外面一层是[描述最外层功能模块的作用,例如用户交互界面,就像城堡的大门,是用户进来的入口],里面一层呢是[中间层功能模块的作用,例如数据处理部分,就像城堡里的厨房,负责把食材(数据)加工好],最核心的部分就是[核心功能模块的作用,例如某个算法或者关键技术,这就像城堡里的宝藏,是整个设计的精华所在]。
(二)技术选型。
在技术方面,我就像在超市里挑东西一样,得选最适合我的。
我选择了[列出你使用的技术,比如编程语言、框架之类的],为啥选这个呢?因为这个就像一把万能钥匙,能轻松打开我在设计过程中遇到的很多锁。
而且这个技术在我们这个小圈子里就像个流行款,大家都觉得它靠谱,我也就跟着潮流走啦。
(三)详细设计。
1. 功能模块一:[功能模块名称]这个模块就像是一个小机器人,它的任务就是[具体描述功能模块的功能]。
我设计的时候就想,这个小机器人得特别听话,所以我给它设置了很多规则,就像教小孩一样,告诉他这个能做,那个不能做。
比如说,如果用户输入了[某种错误的输入],它就得像个懂事的小管家一样,提醒用户“你这样不对哦,应该这样做。
大专毕设计模板

大专毕设计模板大专毕业设计模板应由本人根据自身实际情况书写,以下仅供参考,请您根据自身实际情况撰写。
标题:XXXX(大专毕业设计)摘要:本文介绍了XXXX的基本概念、技术原理和实现方法,并对XXXX进行了实验和验证。
实验结果表明,XXXX具有较好的性能和实际应用价值。
一、引言XXXX是一种新兴的技术,其应用领域广泛,具有很大的发展潜力。
随着技术的不断发展,XXXX的应用范围越来越广泛,其技术原理和实现方法也得到了不断的研究和完善。
本文旨在介绍XXXX的基本概念、技术原理和实现方法,并通过实验和验证,探讨XXXX的性能和应用价值。
二、技术原理XXXX是一种基于XXXX技术的方法,其基本原理是通过XXXX技术对XXXX进行处理,以达到XXXX的目的。
具体来说,XXXX通过XXXX技术对XXXX进行XXXX处理,使得XXXX能够更好地适应实际应用的需求。
三、实现方法为了实现XXXX,我们需要进行以下几个步骤:1. 确定XXXX的目标和应用场景;2. 设计XXXX的算法和模型;3. 编写代码并进行实验验证;4. 对实验结果进行分析和总结。
四、实验和验证为了验证XXXX的性能和应用价值,我们进行了以下实验:1. 实验环境:我们使用了XXXX的硬件和软件环境,包括XXXX处理器、XXXX操作系统等;2. 实验数据:我们使用了XXXX的数据集进行实验;3. 实验方法:我们采用了XXXX的实验方法,对XXXX进行了多次实验,并对实验结果进行了分析和总结。
五、结论通过实验和验证,我们发现XXXX具有较好的性能和实际应用价值。
具体来说,XXXX具有以下优点:1. XXXX具有较高的准确率和召回率;2. XXXX能够处理大规模的数据集;3. XXXX具有较好的可扩展性和稳定性。
因此,我们认为XXXX是一种具有很大发展潜力的技术,未来将有广泛的应用前景。
同时,我们也希望能够得到更多研究者的关注和研究,不断完善和发展XXXX技术。
专科毕业设计样板

西京学院毕业设计(论文)题目:51单片机通信设计与分析姓名:贺忠系(院):机电工程系专业:机电一体化技术班级:机电一体化0804班学号:0812090411指导老师:宋元鹤日期:教务处制摘要本文通过对51单片机串行通信接口的分析,建立了单片机串行通讯系统,设计了其控制寄存器和特殊控制寄存器的工作方式,完成了通讯软件,并探讨了无线发射模式。
关键词:单片机,串行通信接口目录第一章概述1.1绪论 (1)1.2单片机的概述 (5)1.3单片机的发展史 (5)1.4单片机的主要特点 (6)1.5 AT89C51单片机简介 (7)第二章单片机的串行接口2.1 单片机串行接口的基本概念 (12)2.2 串行口和控制寄存器 (13)2.3 数码显示管 (15)2.4 硬件的焊接及调试过程 (17)2.5 硬件的调试机器故障排除 (18)第三章软件的设计和调整过程3.1 程序流程图 (20)3.2 通信协议 (21)第四章单片机串行通信领域的扩展4.1 无线发射电路组成及工作原理 (23)4.2 单片机串口接口 (24)第五章总结 (25)参考文献 (27)第一章概述1.1绪论我所做的单片机串行通信发射机主要在实验室完成,参考有关的书籍和资料,个人完成电路的设计、焊接、检查、调试,再根据自己的硬件和通信协议用汇编语言编写发射和显示程序,然后加电调试,最终达到准确无误的发射和显示。
在这过程中需要选择适当的元件,合理的电路图扎实的焊接技术,基本的故障排除和纠正能力,会使用基本的仪器对硬件进行调试,会熟练的运用汇编语言编写程序,会用相关的软件对自己的程序进行翻译,并烧进芯片中,要与对方接收机统一通信协议,要耐心的反复检查、修改和调试,直到达到预期目的。
单片机串行通信发射机采用串行工作方式,发射并显示两位数字信息,既显示00-99,使数据能够在不同地方传递。
硬件部分主要分两大块,由AT89C51和多个按键组成的控制模块,包括时钟电路、控制信号电路,时钟采用6MHZ晶振和30pF的电容来组成内部时钟方式,控制信号用手动开关来控制,P1口来控制,P2、P3口产生信号并通过共阳极数码管来显示,软件采用汇编语言来编写,发射程序在通信协议一致的情况下完成数据的发射,同时显示程序对发射的数据加以显示。
- 1、下载文档前请自行甄别文档内容的完整性,平台不提供额外的编辑、内容补充、找答案等附加服务。
- 2、"仅部分预览"的文档,不可在线预览部分如存在完整性等问题,可反馈申请退款(可完整预览的文档不适用该条件!)。
- 3、如文档侵犯您的权益,请联系客服反馈,我们会尽快为您处理(人工客服工作时间:9:00-18:30)。
长沙航空职业技术学院2012届毕业设计说明书射线底片焊接缺陷的影像辨认院 (系):航空装备维修工程系学生姓名:**指导教师:**专业:检测技术及应用班级:检测0901 完成时间:2012-5-102011届毕业生毕业设计(论文)任务书长沙航空职业技术学院浅谈射线检测图像的识别摘要:X射线与自然光并没有本质的区别,都是电磁波,只是X射线的光量子的能量远大于可见光。
它能够穿透可见光不能穿透的物体,而且在穿透物体的同时将和物质发生复杂的物理和化学作用,可以使原子发生电离,使某些物质发出荧光,还可以使某些物质产生光化学反应。
如果工件局部区域存在缺陷,它将改变物体对射线的衰减,引起透射射线强度的变化,这样,采用一定的检测方法,比如利用胶片感光,来检测透射线强度,就可以判断工件中是否存在缺陷以及缺陷的位置、大小。
本文首先讲述了射线评片工作的基本要求和原理,并结合金属材料焊接知识,重点讲解了各种焊接缺陷的类型和射线图像。
其次,对于射线工作中质量分级与评定做出讲解,以达到正确识别图像的能力。
关键词:影像缺陷焊接接头质量分级评定前言射线的种类很多,其中易于穿透物质的有X射线、γ射线、中子射线三种。
这三种射线都被用于无损检测,其中X射线和γ射线广泛用于锅炉压力容器管道焊缝和其他工业产品、结构材料的缺陷检测,而中子射线仅用于一些特殊场合。
射线检测最主要的应用是探测试件内部的宏观几何缺陷(探伤)。
按照不同特征(例如使用的射线种类、记录的器材、工艺和技术特点等)可将射线检测分为多种不同的方法。
射线照相法是指用X射线或γ射线穿透试件,以胶片作为记录信息的器材的无损的检查方法,该方法是应用最广泛的一种基本射线检测方法。
本文以射线探伤工作中的评片作为核心,并以此延展开介绍了金属焊接工艺中的各种缺陷在底片上的图像特点,通过学习,达到正确识别缺陷和评定缺陷等级的目标。
第一章评片技术概述(基本要求) (1)1.1评片工作的要求 (1)1.1.1底片质量要求 (1)1.1.2评片环境、设备等要求: (3)1.1.3 评片人员的要求 (3)1.1.4评片的基本条件与工作质量关系 (4)1.2投影的基本概念 (5)1.2.1 影像重叠 (5)1.2.2影像放大 (6)1.2.3影像畸变 (6)第二章常见缺陷的识别 (7)2.1熔焊接头常见缺陷识别 (7)2.1.1 焊接接头 (7)2.1.2焊接接头的主要形式 (8)2.1.3 焊接缺陷的分类及识别 (9)2.2底片上的其他影像 (13)2.2.1 常见伪缺陷 (13)2.2.2 静电斑纹 (15)2.2.3 衍射斑纹 (15)第三章质量评定 (16)3.1评定标准关于内部质量的规定 (16)3.1.1 缺陷类型 (16)3.1.2 缺陷数据测定方法 (17)3.1.3 质量分级具体规定 (17)3.1.4 质量分级评定的基本步骤 (18)3.2焊接接头射线照相缺陷影像的分级及评定 (18)3.2.1 分级 (18)3.2.2 评定方法 (19)第四章结束语 (21)第一章评片技术概述(基本要求)1.1评片工作的要求缺陷是否能够通过射线照相而被检出,取决于若干个环节。
首先,必须使缺陷在底片上留下足以识别的影像,这涉及照相质量方面的问题。
其次,底片上的影像应在适当条件下得以充分的显示,以利于评片人员观察和识别,这与观片设备和环境条件有关。
第三,评片人员对观察到的影像应能做出正确的分析与判断,这取决于评片人员的知识、经验、技术水平和责任心。
按以上所述,对评片工作的基本要求可归纳为三个方面,即底片质量要求、设备环境条件要求和人员条件要求。
1.1.1底片质量要求通常对底片的质量检查包括以下六个项目:1. 灵敏度检查从定量方面而言,是指在射线底片可以观察到的最小缺陷尺寸或最小细节尺寸;从定性方面而言,是指发现和识别细小影像的难易程度。
在射线底片上所能发现的沿射线穿透方向上的最小尺寸,称为绝对灵敏度,此最小缺陷尺寸与透照厚度的百分比称为相对灵敏度。
用人工孔槽,金属丝尺寸(像质计)作为底片影像质量的监测工具而得到的灵敏度又称为像质计灵敏度。
要求:底片上可识别的像质计影像、型号、规格、摆放位置,可观察的像质指数(Z)是否达到标准规定要求等,满足标准规定为合格。
图1 丝型像质计射线照相灵敏度是底片影像质量的综合评定指标,合格的底片其射线照相灵敏度必须符合标准的要求。
底片的射线照相灵敏度采用底片上像质计的影像的可识别性测定,对底片应达到的射线照相灵敏度没有严格的统一规定,一般是按照采用的射线照相技术级别规定应达到的射线照相灵敏度。
2. 黑度检查黑度是底片质量的一个重要指标,它直接关系底片的射线照相灵敏度和底片记录细小缺陷的能力。
为保证底片具有足够的对比度,黑度不能太小,但因受到观片灯亮度的限制,底片黑度也不能过大。
JBT4730底片评定范围内的黑度D应符合下列规定:A 级:1.5≤D≤4.0;AB级:2.0≤D≤4.0 ;B 级:2.3≤D≤4.0。
经合同各方同意,AB级最低黑度可降低至1.7,B级最低黑度可降低至2.0。
透照小径管或其它截面厚度变化大的工件时,AB级最低黑度允许降低至1.5。
采用多胶片技术时,单片观察时单片的黑度应符合以上要求,多片迭加观察时单片黑度应不低于1.3。
3. 标记底片上应有完整的标识(识别标记和定位标记)影像,它是识别底片、建立档案资料、缺陷定位必不可少的标志。
标记的影像应位于底片的非评定区,以免干扰对缺陷的识别。
1.1.2评片环境、设备等要求:1. 环境评片室应独立、通风和卫生,室温不易过高(应备有空调),室内光线应柔和偏暗,室内亮度应在30cd/m2为宜。
室内噪音应控制在<40dB为佳。
在评片前,从阳光下进入评片室应适应评片室内亮度至少为5~10min;从暗室进入评片室应适应评片室内亮度至少为30s。
2. 设备①观片灯:应有足够的光强度,确保透过黑度为≤2.5的底片后可见光度应为30cd/m2,即透照前照度至少应≥3,000 cd/m2;透过黑度为>2.5的底片后可见光度应为10cd/m2,即透照前照度至少应≥3,200 cd/m2。
亮度应可调,性能稳定,安全可靠,且噪音应<30dB。
观片时用遮光板应能保证底片边缘不产生亮光的眩晕而影响评片。
②黑度计:应具有读数准确,稳定性好,能准确测量4.0以内的透射样品密度,其稳定性分辨力为+0.02,测量值误差应≤±0.05,光孔径要求<1.0mm为佳,黑度计至少每6个月校验一次,标准黑度片至少应三年送法定计量单位检定一次。
③评片用工具:放大镜应为3至5倍,应有0—2cm长刻度标尺。
评片人可借助放大镜对底片上缺陷进行细节辨认和微观定性分析。
评片尺,应有读数准确的刻度,尺中心为“0”刻度,两端刻槽至少应有200 mm,尺上应有10×10、10×20、10×30 mm的评定框线。
1.1.3 评片人员的要求a)经过系统的专业培训,并通过相关部门考核确认具有承担此项工作的能力与资格者,一般要求具有RT—Ⅱ级资格证书人员担任。
b)具有一定的评片实际工作和经验。
并能经常到现场参加缺陷返修解剖工作,以丰富自己的评片经验和水平。
并应具有一定的焊接、材料及热处理等相关专业知识。
c)应熟悉有关规范、标准,并能正确理解和严格按标准进行评定,具有良好的职业道德、高度的工作责任心。
评片前应充分了解被评定的工件材质、焊接工艺、接头坡口型式,焊接缺陷可能产生的种类及部位及射线透照工艺情况。
d)具有较好的视力,校正视力不低于1.0,并能读出距离400mm 处,高0.5 mm间隔0.5 mm一组的印刷字母。
1.1.4评片的基本条件与工作质量关系1. 从底片上所获得的质量信息缺陷的有无、性质、数量及分布情况等;缺陷的两维尺寸(长、宽)信息,沿板厚方向尺寸可用黑度大小表示;能预测缺陷可能扩展和张口位移的趋向;能依据标准、规范对被检工件的质量做出合格与否的评价;能为安全质量事故及材料失效提供可靠的分析凭证。
2. 正确评判底片的意义预防不可靠工件转入下道工序,防止材料和工时的浪费;能够指导和改进被检工件的生产制造工艺;能消除质量事故隐患,防止事故发生。
3. 良好的评判条件是底片评判工作质量保证的基础评片人的技术素质是评判工作质量保证的关键先进的观片仪器设备是评判工作质量保证的基础良好的评片环境是评判人员技术素质充分发挥的必要条件。
1.2 投影的基本概念用一组光线将物体的形状投射到一个平面上去,称为“投影”。
在该平面上得到的图像,也称为“投影”。
投影可分为正投影和斜投影。
正投影即是投射线的中心线垂直于投影的平面,其投射中心线不垂直于投射平面的称为斜投影。
射线照相就是通过投影把具有三维尺寸的试件(包括其中的缺陷)投射到底片上,转化为只有二维尺寸的图像。
由于射线源,物体(含其中缺陷)、胶片三者之间的相对位置、角度变化,会使底片上的影像与实物尺寸、形状、位置有所不同,常见有重迭、放大、畸变、相对位置改变等现象。
图2 投影示意图a)三角形中心投影 b)三角形的平行正投影1.2.1 影像重叠影像的每个点都是物体的一系列点对射线衰减产生的总结果,或者说是物体一系列点的影像的重叠。
因此射线检测所得到的影像,是把一个立体物体表现在平面上,因此,物体质量、结构等方面的情况,在射线检测的影像上将重叠在一起。
这样,当从不同方向进行射线检测时,对同一物体得到的影像可以不同。
影像的重叠性使得物体中不同位置的缺陷,在射线检测的影像上可能表现成一个缺陷,这给射线检测影像的判断带来困难。
1.2.2影像放大影像放大是指在胶片上成像的尺寸大于影像所表示的物体的实际尺寸。
当射线源可视为是一点源时,得到的影像将都是一个放大的影像,从投影关系不难理解这一点。
影像放大的程度与射线源至被透照物体的距离相关、与影像所表示的物体和胶片的距离相关。
当射线源尺寸大于缺陷尺寸时,缺陷的实际情况将变得复杂化,这时候需考虑象的位置。
简单地说,可以认为,在一般的情况下,影像都存在一定程度的放大。
图3 影像的放大和几何不清晰度形成示意图1.2.3影像畸变影像畸变是指得到的影像的形状与物体在射线投影方向截面的形状不相似。
产生这种情况的原因是,物体截面上不同的部分在胶片上形成影像时产生的放大不同,这样就导致影像的形状与物体的形状不相似。
例如,物体中有一个球孔,当射线中心束不垂直于胶片平面时,所得到的影像将不再是圆形,即发生了影像畸变。
在实际射线照相中,缺陷影像畸变是经常发生的,这是由于缺陷总是具有一定的体积,具有一定的空间分布,形状常常是不规则的,这些情况使得透照时总会存在不同部位放大不同,造成了影像畸变。
第二章常见缺陷的识别2.1 熔焊接头常见缺陷识别2.1.1 焊接接头焊接从微观上看是材料通过原子或分子间的结合和扩散形成永久性连接的工艺过程。