液态金属的流动性及充型能力
液态金属的充型能力1
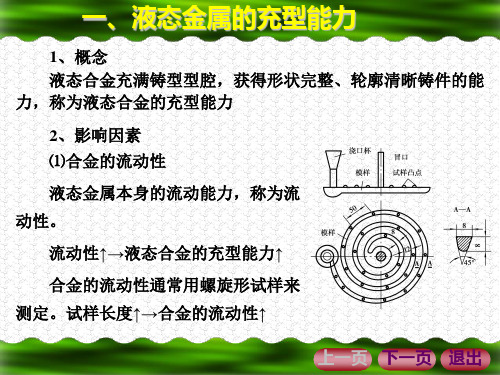
冷
低
裂
温
形状曲折而不规则,裂纹表面 呈氧化色,无金属光泽;裂口 沿晶粒边界通过。 一般分布在铸件易产生应力集
外形呈连续直线状(没有分叉)
或圆滑曲线,裂纹表面干净,具 有金属光泽,有时呈轻微氧化色;
穿过晶粒。
常出现在铸件表面
分
布
中的部位或铸件最后凝固部位 的内部
上一页 下一页
退出
2、防止措施 ⑴设计上:合理设计铸件结构,以减少铸造内应力 ⑵工艺上 a.降低磷、硫含量 b.改善型(芯)砂的退让性 c.控制打箱时间
上一页 下一页
退出
充型能力的前提下,尽可能采用“高温出炉,低温浇注”的原则。
◆ 浇注系统的结构
浇注系统的结构越复杂,流动的阻力就越大,流动性就越差。
故在设计浇注系统时,要合理布置内浇口在铸件上的位置,选择
恰当的浇注系统结构和各部分的断面积。 ⑶充填条件 铸型中凡能增加金属流动阻力、降低流速和增加冷却速度的 因素,均会降低合金的充型能力。诸如:型腔过窄、型砂含水分 或透气性不足、铸型排气不畅和铸型材料导热性过大等,均能降 低充型能力,使铸件易于产生浇不足、冷隔等缺陷。
P S
尺寸变化
固态
K
Q 产生应力、变形、裂 产生缩孔、缩松 0 0.02 0.77 2.11 4.3 纹的基本原因 ω c ,% 的基本原因
6.69
图
上一页 下一页
ቤተ መጻሕፍቲ ባይዱ退出
2、影响因素 ①化学成分
凡是促进石墨化的元素增加,收缩减少,否则收缩增大
②浇注温度 T浇↑→过热度↑→液 态收缩↑→总收缩↑ ③铸件结构和铸型条件 A
等固相法
内切圆法 特 征:形状不规则,表面不光滑,可以看到发达的树 枝晶末梢 2、缩松的形成 形成过程:
液态金属(合金)的流动性及充型能力-PPT课件
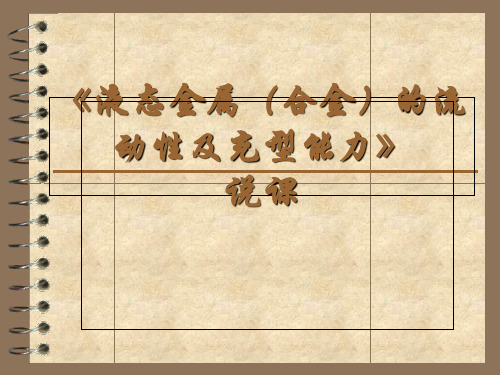
三、教法分析
基于本课题的特点,我主要采用了 以下的教学方法:
1. 直观演示法:利用多媒体进行直观演示,激 发学生的学习兴趣,活跃课堂气氛,促进学生 对知识的掌握。课节内容公式较多,采用板书 推导的方法便于学生理解。 2. 引导提问法:通过提出问题引导学生,以学 生为主体,使学生的独立探索性得到了充分的 发挥,培养学生的自觉能力、思维能力。 3. 集体讨论法:针对学生提出的问题,组织学 生进行集体和分组语境讨论,促使学生在学习 中解决问题,培养学生团结协作的精神。
(2)、教材内容要点
①、液态金属流动性及充型能力的 概念 ②、液态金属(合金)充型能力的 计算
(3)、教学目标 ①、知识目标: 了解液态金属在成形过程中的流动特点 了解影响充型能力的因素和提高措施 熟悉并掌握液态金属停止流动机理及液态金属充 型能力的计算方法 ②、能力目标: 由于本节课内容是本门课的重点内容之一,属于 理论性较强的内容。通过多媒体演示和板书的合理应 用,培养学生勤于思考的学习能力。并且本节内容计 算部分较多,锻炼学生独立思考,独立分析问题的能 力。 ③、德育目标: 培养学生从事研究工作认真、严谨的作风。
ቤተ መጻሕፍቲ ባይዱ
2. 讲授新课:(39分钟) 在讲授新课的过程中,我突出教材的重点 ,明了地分析教材的难点。我选择了多媒体的 教学手段,可以使抽象的知识具体化,枯燥的知 识生动化,乏味的知识兴趣华。还重视教材中 的疑问,适当对题目进行引申,使它的作用更 加突出,有利于学生对知识的串联、积累、加 工,从而达到举一反三的效果。教学过程:通 过幻灯片演示展开本节内容——液态金属在成 形过程中的流动特点——液态金属流动性和充 型能力概念——重点分析液态金属停止流动机 理——着重讲解液态金属充型能力的计算方法 ——影响充型能力的因素和提高措施。
第一章 金属液态成形理论基础

第一节 液态金属充型能力与流动性
0、什么是液态金属的充型能力
1)定义:
液体金属充满铸型型腔,获得尺寸精确、轮廓清晰的 成型件的能力,称为充型能力。
2)充型能力对成型的影响
充型能力不足时,会产生浇不足、冷隔、夹渣、气孔 等缺陷。
3)影响充型能力的因素
充型能力首先取决于金属本身的流动性(流动能力),同 时又受铸型性质、浇注条件和铸件结构等因素影响。
一、铸件的凝固方式
在铸件凝固过程中,其断面上一般存在三个区 域:固相区、凝固区和液相区。
1、分类
依据对铸件质量影响较大的凝固区的宽窄划分 铸件的凝固方式为如下三类:
(1)逐层凝固
纯金属和共晶成分的合金在凝固过程中不存在液、固并 存的凝固区,随着温度下降,固体层不断加厚,液体不 断减少,直达铸件中心,这种凝固方式称为逐层凝固。
机械应力
二、铸件的变形及其防止
1、变形的原因:
铸件内部残余内应力。 只有原来受拉伸部分产生压缩 变形、受压缩部分产生拉伸变 形,才能使铸件中的残余内应 力减小或消除。
平板铸件的变形
杆件的变形
床身铸件的变形
粱形铸件的弯曲变形
2、防止措施:
减小应力; 将铸件设计成对称结构,使其内应力互相平衡; 采用反变形法; 设置拉肋; 时效处理。
2、冷裂纹的特征
裂纹细小,呈连续直线状,裂缝内有金属光泽或轻 微氧化色。
3、防止措施
凡是能减少铸件内应力和降低合金脆性的因素 均能防止冷裂。 设置防裂肋亦可有效地防止铸件裂纹。
防裂肋
三、合金的吸气性
液态合金中吸入的气体,若在冷凝过程中不能溢 出,滞留在金属中,将在铸件内形成气孔。
一)气孔的危害
气孔破坏了金属的连续性,减少了其承载的有效 截面积,并在气孔附近引起应力集中,从而降低 了铸件的力学性能。 弥散性气孔还可促使显微缩松的形成,降低铸件 的气密性。
材料成形原理-第一章(2)液态金属的充型能力

2013-7-9
一、金属性质方面的因素
这类因素是内因,决定了金属本身的流动能力-----流动性。 1、 合金的成分 合金的流动性与其成分 之间存在着一定的规性。 在流动性曲线上,对应 着纯金属、共晶成分和 金属间化合物的地方出 现最大值,而有结晶温 度范围的地方流动性下 降,且在最大结晶温度 范围附近出现最小值。
2013-7-9
5
对于同一种合金,也可以用流动性试样研究各铸造因 素对其充型能力的影响。例如,采用某一种结构的流 动性试样,改变型砂的水分、煤粉含量、浇注温度、 直浇道高度等等因素中的一个因素,以判断该变动因 素对充型能力的影响。 螺旋试样 流动性试样的类型很多,如螺旋形、球形等。 在生产和科学研究中应用最多的是螺旋试样,如图所 示。其优点:灵敏度高、对比形象、可供金属液流动 相当的距离,而铸型的轮廓尺寸并不太大。缺点:金 属流线弯曲,沿途阻力损失较大,流程越长散热越多, 故金属的流动条件和温度条件都在随时间改变,这必 然影响到所测流动性的准确度;各次试验所用铸型条 件也很难精确控制;每做一次试验要造一次铸型。
2013-7-9
8
合金成分对流动性的影响
9
Fe-C合金流动性与成分的关系
2013-7-9
10 在过热度相同时:纯铁的流动性好,随碳量的增加,结晶温度范围 扩大,流动性下降。在Wc=2.1%附近,结晶温度范围最大,在液相 线以上过热度相同的情况下,流动性最差。 在亚共晶铸铁中,越接近共晶成分,流动性越好,共晶成分铸铁的 流动性最好。这是因为含碳量越低,结晶温度范围越宽,初生奥氏 体枝晶就越发达,数量不多的奥氏休枝晶,即足以阻塞液流的流动。 共晶铸铁的结晶组织比较细小,凝固层的走向平整,流动阻力小, 而且共晶成分铁液浇注温度低,向铸型散热慢,流动时间也较长, 所以流动性最好。碳量增加时,亚共晶铸铁的液相线温度下降,在 相同的浇注温度下,铁液的流动性随碳量增加而迅速提高。 铸铁的结晶温度范围一般都比铸钢的宽,但铸铁的流动性却比铸钢 的好。这是由于铸钢的熔点高,钢液的过热度一般都比铸铁的小, 维持液态的流动时间就要短;另外,由于钢液的温度高,在铸型中 散热速度大,很快就析出一定数量的枝晶,使钢液失去流动能力。 高碳钢的结晶温度范围虽然比低碳钢的宽,但是,由于液相线温度 低,容易过热,所以实际流动性并不比低碳钢差。
金属液态成型基础作业
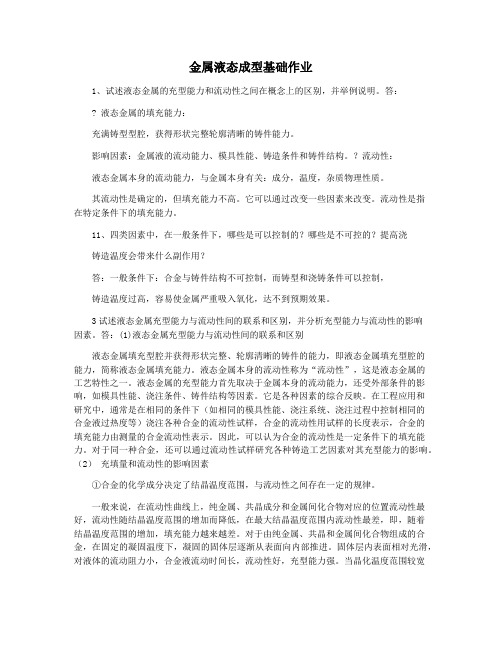
金属液态成型基础作业1、试述液态金属的充型能力和流动性之间在概念上的区别,并举例说明。
答:? 液态金属的填充能力:充满铸型型腔,获得形状完整轮廓清晰的铸件能力。
影响因素:金属液的流动能力、模具性能、铸造条件和铸件结构。
?流动性:液态金属本身的流动能力,与金属本身有关:成分,温度,杂质物理性质。
其流动性是确定的,但填充能力不高。
它可以通过改变一些因素来改变。
流动性是指在特定条件下的填充能力。
11、四类因素中,在一般条件下,哪些是可以控制的?哪些是不可控的?提高浇铸造温度会带来什么副作用?答:一般条件下:合金与铸件结构不可控制,而铸型和浇铸条件可以控制,铸造温度过高,容易使金属严重吸入氧化,达不到预期效果。
3试述液态金属充型能力与流动性间的联系和区别,并分析充型能力与流动性的影响因素。
答:(1)液态金属充型能力与流动性间的联系和区别液态金属填充型腔并获得形状完整、轮廓清晰的铸件的能力,即液态金属填充型腔的能力,简称液态金属填充能力。
液态金属本身的流动性称为“流动性”,这是液态金属的工艺特性之一。
液态金属的充型能力首先取决于金属本身的流动能力,还受外部条件的影响,如模具性能、浇注条件、铸件结构等因素。
它是各种因素的综合反映。
在工程应用和研究中,通常是在相同的条件下(如相同的模具性能、浇注系统、浇注过程中控制相同的合金液过热度等)浇注各种合金的流动性试样,合金的流动性用试样的长度表示,合金的填充能力由测量的合金流动性表示。
因此,可以认为合金的流动性是一定条件下的填充能力。
对于同一种合金,还可以通过流动性试样研究各种铸造工艺因素对其充型能力的影响。
(2)充填量和流动性的影响因素①合金的化学成分决定了结晶温度范围,与流动性之间存在一定的规律。
一般来说,在流动性曲线上,纯金属、共晶成分和金属间化合物对应的位置流动性最好,流动性随结晶温度范围的增加而降低,在最大结晶温度范围内流动性最差,即,随着结晶温度范围的增加,填充能力越来越差。
材料基本原理名词解释

51、加工硬化-随着变形程度的增加,(位错运动所受到的阻力增大),金属的强度和硬度增加,而塑性和韧性下降,即产生了加工硬化。
52、应变速率-单位时间内的应变,又称变形速度。
53、滑移-晶体在外力的作用下,其一部分沿着一定的晶面和该晶面上的一定晶向,相对于另一部分产生的相对移动。
45 塑性-指金属材料在外力作用下发生变形而不破坏其完整性的能力。
46热塑性变形-金属在再结晶温度以上的变形。
47、张量-由若干个当量坐标系改变时满足转换关系的所有分量的集合。
48 塑性-指固体材料在外力作用下发生永久变形而不被破坏其完整性的能力。
49 简单加载-是指在加载过程中各应力分量按同一比例增加,应力主轴方向固定不变。
11、粗糙界面和光滑界面-从原子尺度上来看,固-液界面固相一侧的点阵位置只有50%左右被固相原子所占据,从而形成一个坑坑洼洼凹凸不平的界面层。粗糙界面在有些文献中也称为“非小晶面”。
光滑界面—从原子尺度上来看,固-液界面固相一侧的点阵位置几乎全部为固相原子占满,只留下少数空位或台阶,从而形成整体上平整光滑的界面结构。也称为“小晶面”或“小平面”。
25沉淀脱氧-是指溶解于液态金属中的脱氧剂直接和熔池中的[FeO]起作用,使其转化为不溶于液态金属的氧化物,并脱溶沉淀转入熔渣中的一种脱氧方式。
26真空脱氧-钢液的熔化过程是在真空条件下进行,利用抽真空降低气相中CO分压来加强钢液中碳的脱氧能力。
27 偏析-合金在凝固过程中发生的化学成分不均匀现象。
33焊接-通过加热或加压,或者两者并用,用或不用填充材料,使两个分离的工件(同种或异种金属或非金属,也可以是金属与非金属)产生原子(分子)间结合而形成永久性连接的工艺工程。
金属液的流动性和液态金属的充型-英汉双语
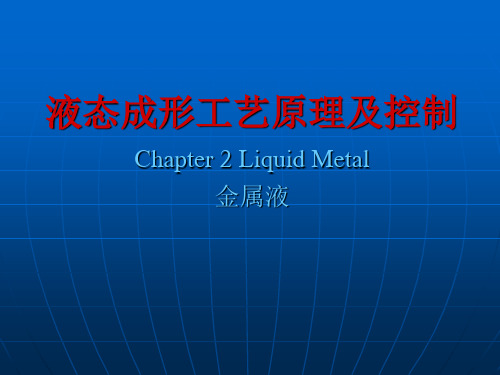
7.54
2.32
Copper/Cu
9.79
2.30
Gold/Au
9.78
2.21
Iron/Fe
15.5
2.00
△Sm/ △S
0.54 0.47 0.37 0.31 0.24 0.23 0.13
Structural characteristics of liquid metal 液态金属的结构特征
液态金属内存在近程有序(short-range order)的原子集团(clusters of atoms)。这种原子集团是不稳定的,瞬时出现又瞬时消失。所以,液态金 属结构具有如下特点:
Ordering
Richter等人利用X线衍射、中子及电子衍 射手段,对碱金属、Au、Ag、Pb和Ti等熔 体进行了十多年的系统研究,经过仔细分析结 果认为,液体中存在着拓扑球状密排结构以及 层状结构,它们的尺寸范围约为10-6 cm
液体金属球状密排结构以及 层状结构
液态成形工艺原理及控制
Chapter 3 Fluidity and liquid metal filling process
Metal
Change in entropy
298k to melting point △S (cal/mol.k)
Entropy of melting △Sm (cal/mol.k)
Cadmium/Cd
4.53
2.46
Zinc/Zn
5.45
2.55
Aluminium/Al
7.51
2.75
Magnesium/Mg
缺线,crucible坩埚,reservoir储气罐,manometer压力计,cartesian笛卡儿, Manostat压力稳定器,aspirator气吸管道
铸造成形工艺原理

300 200 100 0 80 60 40 20 0
温度 (℃)
a)在恒温下凝固
流动性 (cm)
b)在一定温度范围内凝固
40 60 80
Pb 20
Sb
合金的充型能力与成分之间的关系
b) 影响金属流动性:结晶潜热
对于纯金属和共晶成分合金,结晶潜热越多,流动性越好。 对结晶温度范围较宽的合金,对流动性影响不大。但是, 当初生晶为非金属或者合金能在液相线以下呈液固混合状 态,结晶潜热可能是一个重要的因素。
2)铸件的凝固方式
凝固区域:固相区、凝固区和液相区
铸件的凝固方式:
1.逐层凝固 纯金属或共晶成分合金凝固过程中不存在液、固并存现象,其断面上固相 和液相由一条界线清楚地分开,液固界限清楚分开,称为逐层凝固。常见合金如灰铸 铁、低碳钢、工业纯铜、工业纯铝、共晶铝硅合金及某些黄铜都属于逐层凝固的合金。
b) 铸件复杂程度
填就困难。
铸件结构复杂,流动阻力大,铸型的充
提高充型能力的措施:
1)铸型性质方面: 提高铸型温度;增加铸型热阻;提高铸型的排气能力;减 小铸型的发气速度。
2)浇注条件方面: 提高浇注温度;提高充型压头;简化浇注系统;增大浇口 面积。
2.2 铸件的凝固
铸件的凝固是指金属或合金在铸型中由液态转变为固态的过 程。 2.2.1 铸件的温度场
w(C+Si)=4.2%
铸钢:w(C)=0.4% 砂型 金属型() 砂型
1300
1600 1640 680~720 700 1040 1100 砂型
600
100 200 700~800 400~600 420 1000
铝硅合金 镁合金(Mg-Al-Zn) 锡青铜:w(Sn)=9%~11% w(Zn)=2%~4% 硅黄铜:w(Si)=1.5%~4.5%
液态金属的充型能力
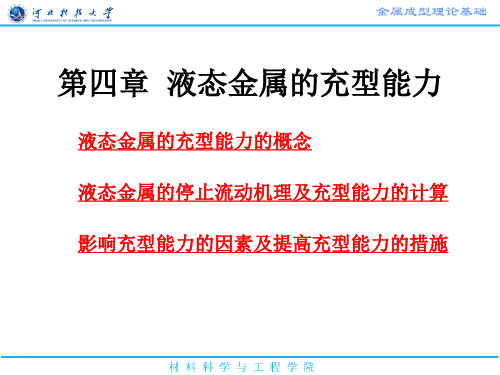
4.流动性式样
衡量金属或合金的流动 性,常用螺旋形式样浇 铸后得到的长度制来衡 量。
1-浇口杯;2-低坝;3直浇道;4-螺旋试样; 5-高坝;6-溢流道;7全压井
金属成型理论基础
第二节
液态金属的停止流动机理及充型能 力的计算
一 液态金属的停止流动机理 二 液态金属充型能力的计算
金属成型理论基础
一、液态金属的停止流动机理
金属成型理论基础
二、铸型性质方面的因素
1. 铸型蓄热系数大,激冷作用强,流动性减小。 2.涂层,金属型铸造中浇冒口处涂料中加入蓄热系数小的 石棉粉,砂型铸造中加入烟黑材料等。 3. 铸型温度高,减小温差;提高充型能力。 4.发气量:铸型有一定的发气能力,在铸型和金属液之间 形成气层,减小摩擦阻力,利于充型,但应适当,气压力 过大导致浇不进,甚至飞溅等,减小发气物质含量,增加 铸型透气性。
金属成型理论基础
三、浇注条件性质方面的因素
1.适当的提高浇注温度: 浇注温度(决定性影响),提高利于充型,但到一程度 后,吸气量增加,氧化严重,不利充型;还会出现结晶 组织粗大,缩孔,缩松等缺陷。 2.充型压头高,浇注位置合适,顶注式浇注等,都提高充 型能力。 3.合理地布置内浇道在铸件上的位置,选择适当的浇注系 统结构。
1.纯金属、共晶成分合金和结晶范围很窄的合金: 纯金属、共晶成分合金和结晶范围很窄的合金: 纯金属
金属成型理论基础
2.结晶范围很宽的合金: 结晶范围很宽的合金: 结晶范围很宽的合金
金属成型理论基础
二、液态金属的充型能力的计算
假设某成分合金浇注一棒形试 样,充型能力l=vτ v:静压头H作用下液态金属 在型腔中的平均流速。 τ:液态金属进入型腔到停止 流动的时间 ≈ τ浇 V=µ(2gh)1/2 H:液态金属静压头 µ: 流量消耗系数
液态金属的流动性及充型能力
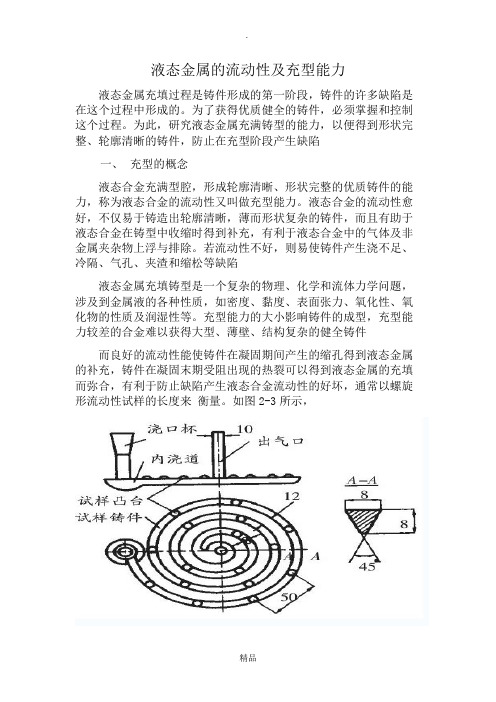
液态金属的流动性及充型能力液态金属充填过程是铸件形成的第一阶段,铸件的许多缺陷是在这个过程中形成的。
为了获得优质健全的铸件,必须掌握和控制这个过程。
为此,研究液态金属充满铸型的能力,以便得到形状完整、轮廓清晰的铸件,防止在充型阶段产生缺陷一、充型的概念液态合金充满型腔,形成轮廓清晰、形状完整的优质铸件的能力,称为液态合金的流动性又叫做充型能力。
液态合金的流动性愈好,不仅易于铸造出轮廓清晰,薄而形状复杂的铸件,而且有助于液态合金在铸型中收缩时得到补充,有利于液态合金中的气体及非金属夹杂物上浮与排除。
若流动性不好,则易使铸件产生浇不足、冷隔、气孔、夹渣和缩松等缺陷液态金属充填铸型是一个复杂的物理、化学和流体力学问题,涉及到金属液的各种性质,如密度、黏度、表面张力、氧化性、氧化物的性质及润湿性等。
充型能力的大小影响铸件的成型,充型能力较差的合金难以获得大型、薄壁、结构复杂的健全铸件而良好的流动性能使铸件在凝固期间产生的缩孔得到液态金属的补充,铸件在凝固末期受阻出现的热裂可以得到液态金属的充填而弥合,有利于防止缺陷产生液态合金流动性的好坏,通常以螺旋形流动性试样的长度来衡量。
如图2-3所示,将液态合金注入螺旋形试样铸型中,冷凝后,测出其螺旋线长度。
为便于测量,在标准试样上每隔50mm 作出凸点标记,在相同的浇注工艺条件下,测得的螺旋线长度越长,合金的流动性越好。
常用合金的流动性如表2-1所示。
其中,灰铸铁、硅黄铜的流动性最好,铝合金次之,铸钢最差通常,流动性好的合金,充型能力强;流动性差的合金,充型能力差,在实际的铸造生产中,可以通过改善外界条件来提高其充型能力,根据铸件的要求及合金的充型能力采取相应的工艺措施以获得健全的优质铸件。
二、影响充型能力的因素影响充型的因素是通过两个途径发生作用的:一是影响金属与铸型之间的热交换条件,从而改变金属液的流动时间;二是影响液态金属在铸型中的水力学条件,从而改变金属液的流速。
铸造知识(全)汇总

第一章铸造工艺基础§1 液态合金的充型充型: 液态合金填充铸型的过程.充型能力: 液态合金充满铸型型腔,获得形状完整,轮廓清晰的铸件的能力充型能力不足:易产生: 浇不足: 不能得到完整的零件.冷隔:没完整融合缝隙或凹坑, 机械性能下降.一合金的流动性液态金属本身的流动性----合金流动性1 流动性对铸件质量影响1) 流动性好,易于浇出轮廓清晰,薄而复杂的铸件.2) 流动性好,有利于液态金属中的非金属夹杂物和气体上浮,排除.3) 流动性好,易于对液态金属在凝固中产生的收缩进行补缩.2 测定流动性的方法:以螺旋形试件的长度来测定: 如灰口铁:浇铸温度1300℃试件长1800mm.铸钢: 1600℃100mm3 影响流动性的因素主要是化学成分:1) 纯金属流动性好:一定温度下结晶,凝固层表面平滑,对液流阻力小2) 共晶成分流动性好:恒温凝固,固体层表面光滑,且熔点低,过热度大.3) 非共晶成分流动性差: 结晶在一定温度范围内进行,初生数枝状晶阻碍液流二浇注条件1 浇注温度: t↑合金粘度下降,过热度高. 合金在铸件中保持流动的时间长,∴t↑提高充型能力. 但过高,易产生缩孔,粘砂,气孔等,故不宜过高2 充型压力: 液态合金在流动方向上所受的压力↑充型能力↑如砂形铸造---直浇道,静压力. 压力铸造,离心铸造等充型压力高.三铸型条件1 铸型结构: 若不合理,如壁厚小, 直浇口低, 浇口小等充↓2 铸型导热能力: 导热↑金属降温快,充↓如金属型3 铸型温度: t↑充↑如金属型预热4 铸型中气体: 排气能力↑充↑减少气体来源,提高透气性, 少量气体在铸型与金属液之间形成一层气膜,减少流动阻力,有利于充型.§2 铸件的凝固和收缩铸件的凝固过程如果没有合理的控制,铸件易产生缩孔,缩松一铸件的凝固1 凝固方式:铸件凝固过程中,其断面上一般分为三个区: 1—固相区2—凝固区3—液相区对凝固区影响较大的是凝固区的宽窄,依此划分凝固方式.1) 逐层凝固:纯金属,共晶成分合金在凝固过程中没有凝固区,断面液,固两相由一条界限清楚分开,随温度下降,固相层不断增加,液相层不断减少,直达中心.2) 糊状凝固合金结晶温度范围很宽,在凝固某段时间内,铸件表面不存在固体层,凝固区贯穿整个断面,先糊状,后固化.3) 中间凝固大多数合金的凝固介于逐层凝固和糊状凝固之间.2 影响铸件凝固方式的因素1) 合金的结晶温度范围范围小: 凝固区窄,愈倾向于逐层凝固如: 砂型铸造, 低碳钢逐层凝固, 高碳钢糊状凝固2) 铸件的温度梯度合金结晶温度范围一定时,凝固区宽度取决于铸件内外层的温度梯度.温度梯度愈小,凝固区愈宽.(内外温差大,冷却快,凝固区窄)二合金的收缩液态合金从浇注温度至凝固冷却到室温的过程中,体积和尺寸减少的现象---.是铸件许多缺陷(缩孔,缩松,裂纹,变形,残余应力)产生的基本原因.1 收缩的几个阶段1) 液态收缩: 从金属液浇入铸型到开始凝固之前. 液态收缩减少的体积与浇注温度质开始凝固的温度的温差成正比.2) 凝固收缩: 从凝固开始到凝固完毕. 同一类合金,凝固温度范围大者,凝固体积收缩率大.如: 35钢,体积收缩率3.0%, 45钢 4.3%3) 固态收缩: 凝固以后到常温. 固态收缩影响铸件尺寸,故用线收缩表示.2 影响收缩的因素1) 化学成分: 铸铁中促进石墨形成的元素增加,收缩减少. 如: 灰口铁C, Si↑,收↓,S↑收↑.因石墨比容大,体积膨胀,抵销部分凝固收缩.2) 浇注温度: 温度↑液态收缩↑3) 铸件结构与铸型条件铸件在铸型中收缩会受铸型和型芯的阻碍.实际收缩小于自由收缩.∴铸型要有好的退让性.3 缩孔形成在铸件最后凝固的地方出现一些空洞,集中—缩孔. 纯金属,共晶成分易产生缩孔*产生缩孔的基本原因: 铸件在凝固冷却期间,金属的液态及凝固受缩之和远远大于固态收缩.4 影响缩孔容积的因素(补充)1) 液态收缩,凝固收缩↑缩孔容积↑2) 凝固期间,固态收缩↑,缩孔容积↓3) 浇注速度↓缩孔容积↓4) 浇注速度↑液态收缩↑易产生缩孔5 缩松的形成由于铸件最后凝固区域的收缩未能得到补足,或者,因合金呈糊状凝固,被树枝状晶体分隔开的小液体区难以得到补缩所至.1) 宏观缩松肉眼可见,往往出现在缩孔附近,或铸件截面的中心.非共晶成分,结晶范围愈宽,愈易形成缩松.2) 微观缩松凝固过程中,晶粒之间形成微小孔洞---凝固区,先形成的枝晶把金属液分割成许多微小孤立部分,冷凝时收缩,形成晶间微小孔洞. 凝固区愈宽,愈易形成微观缩松,对铸件危害不大,故不列为缺陷,但对气密性,机械性能等要求较高的铸件,则必须设法减少.(先凝固的收缩比后凝固的小,因后凝固的有液,凝,固三个收缩,先凝固的有凝,固二个收缩区----这也是形成微观缩松的基本原因.与缩孔形成基本原因类似)6 缩孔,缩松的防止办法基本原则: 制定合理工艺—补缩, 缩松转化成缩孔.顺序凝固: 冒口—补缩同时凝固: 冷铁—厚处. 减小热应力,但心部缩松,故用于收缩小的合金.l 安置冒口,实行顺序凝固,可有效的防止缩孔,但冒口浪费金属,浪费工时,是铸件成本增加.而且,铸件内应力加大,易于产生变形和裂纹.∴主要用于凝固收缩大,结晶间隔小的合金.l 非共晶成分合金,先结晶树枝晶,阻碍金属流动,冒口作用甚小.l 对于结晶温度范围甚宽的合金,由于倾向于糊状凝固,结晶开始之后,发达的树枝状骨状布满整个截面,使冒口补缩道路受阻,因而难避免显微缩松的产生.显然,选用近共晶成分和结晶范围较窄的合金生产铸件是适宜的.§3 铸造内应力,变形和裂纹凝固之后的继续冷却过程中,其固态收缩若受到阻碍,铸件内部就发生内应力,内应力是铸件产生变形和裂纹的基本原因.(有时相变膨胀受阻,负收缩)一内应力形成1 热应力: 铸件厚度不均,冷速不同,收缩不一致产生.塑性状态: 金属在高于再结晶温度以上的固态冷却阶段,受力变形,产生加工硬化,同时发生的再结晶降硬化抵消,内应力自行消失.(简单说,处于屈服状态,受力—变形无应力)弹性状态: 低于再结晶温度,外力作用下,金属发生弹性变形,变形后应力继续存在.举例: a) 凝固开始,粗细处都为塑性状态,无内应力∵两杆冷速不同,细杆快,收缩大,∵受粗杆限制,不能自由收缩,相对被拉长,粗杆相对被压缩,结果两杆等量收缩.b) 细杆冷速大,先进如弹性阶段,而粗杆仍为塑性阶段,随细杆收缩发生塑性收缩,无应力.c) 细杆收缩先停止,粗杆继续收缩,压迫细杆,而细杆又阻止粗杆的收缩,至室温, 粗杆受拉应力(+),(-) 由此可见,各部分的温差越大,热应力也越大,冷却较慢的部分形成拉应力,冷却较快的部分形成压应力.预防方法: 1 壁厚均匀2 同时凝固—薄处设浇口,厚处放冷铁优点: 省冒口,省工,省料缺点: 心部易出现缩孔或缩松,应用于灰铁锡青铜,因灰铁缩孔、缩松倾向小,锡青铜糊状凝固,用顺序凝固也难以有效地消除其显微缩松。
铸造工程概论思考题
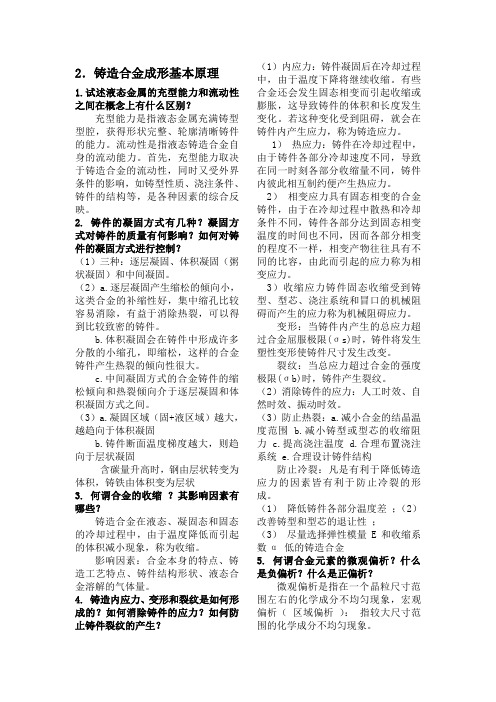
2.铸造合金成形基本原理1.试述液态金属的充型能力和流动性之间在概念上有什么区别?充型能力是指液态金属充满铸型型腔,获得形状完整、轮廓清晰铸件的能力。
流动性是指液态铸造合金自身的流动能力。
首先,充型能力取决于铸造合金的流动性,同时又受外界条件的影响,如铸型性质、浇注条件、铸件的结构等,是各种因素的综合反映。
2. 铸件的凝固方式有几种?凝固方式对铸件的质量有何影响?如何对铸件的凝固方式进行控制?(1)三种:逐层凝固、体积凝固(粥状凝固)和中间凝固。
(2)a.逐层凝固产生缩松的倾向小,这类合金的补缩性好,集中缩孔比较容易消除,有益于消除热裂,可以得到比较致密的铸件。
b.体积凝固会在铸件中形成许多分散的小缩孔,即缩松,这样的合金铸件产生热裂的倾向性很大。
c.中间凝固方式的合金铸件的缩松倾向和热裂倾向介于逐层凝固和体积凝固方式之间。
(3)a.凝固区域(固+液区域)越大,越趋向于体积凝固b.铸件断面温度梯度越大,则趋向于层状凝固含碳量升高时,钢由层状转变为体积,铸铁由体积变为层状3. 何谓合金的收缩?其影响因素有哪些?铸造合金在液态、凝固态和固态的冷却过程中,由于温度降低而引起的体积减小现象,称为收缩。
影响因素:合金本身的特点、铸造工艺特点、铸件结构形状、液态合金溶解的气体量。
4. 铸造内应力、变形和裂纹是如何形成的?如何消除铸件的应力?如何防止铸件裂纹的产生?(1)内应力:铸件凝固后在冷却过程中,由于温度下降将继续收缩。
有些合金还会发生固态相变而引起收缩或膨胀,这导致铸件的体积和长度发生变化。
若这种变化受到阻碍,就会在铸件内产生应力,称为铸造应力。
1)热应力:铸件在冷却过程中,由于铸件各部分冷却速度不同,导致在同一时刻各部分收缩量不同,铸件内彼此相互制约便产生热应力。
2)相变应力具有固态相变的合金铸件,由于在冷却过程中散热和冷却条件不同,铸件各部分达到固态相变温度的时间也不同,因而各部分相变的程度不一样,相变产物往往具有不同的比容,由此而引起的应力称为相变应力。
实验一 金属液的充型能力及流动性测定实验

实验一 金属液的充型能力及流动性测定实验一、实验目的1、 了解合金的化学成分和浇注温度对金属液充型能力和流动性的影响。
2、 熟悉采用螺旋型试样测定铸造金属液的流动性和评定其充型能力的方法。
3、 具备设计和实施常用金属材料充型比较的能力,并能够对实验结果进行分析。
二、实验的主要内容利用电阻坩埚炉熔化合金;使用螺旋形试样的模样造型;完成浇注;冷凝后得到试样。
通过测量试样长度来判断合金在不同条件下的流动性和充型能力。
三、实验设备和工具电阻坩埚炉(5KW )、螺旋形试样模样(见图1)、热电偶测温仪、型砂、砂箱、造型工具、浇注工具等。
四、实验原理充型能力是金属液充满铸型型腔、获得轮廓清晰、形状准确的铸件的能力。
充型能力主要取决于液态金属的流动性,同时又受相关工艺因素的影响。
金属液的流动性是金属液本身的流动能力,用在规定铸造工艺条件下流动性试样的长度来衡量。
流动性与金属的成分、杂质含量及物理性能等有关。
影响金属液充型能力的工艺因素主要有浇注温度、充型压力等。
提高浇注温度或充型压力,均有利于提高充型能力。
五、实验方法和步骤 1.合金的熔化、保温方案一:将某一成分的铝硅合金在坩埚炉中,加热熔化并过热到一定的温度保温。
方案二:将同一成分的铝硅合金(适量)分别置于两个坩埚炉中,加热熔化并过热到不同的温度保温。
2.造型方案一:采用同一个螺旋形试样的模样分别制作两个直浇道高度不同的砂型。
方案二:采用同一个螺旋形试样的模样分别制作两个直浇道高度相同的砂型。
3.浇注方案一:将熔化并保温的铝硅合金液分别浇注到两个直浇道高度不同的砂型中。
方案二:将两个坩埚炉中加热熔化并保温的铝硅合金液分别浇注到两个直浇道高度相同 的砂型中。
4.开型、落砂 待试样凝固后即可开型并落砂。
图1 螺旋形试样5.测定流动性分别测出不同试样螺旋形部分的长度。
(凸点间距L0=50mm,设凸点数为n,不足L0的长度A0估出,L=L0×n+A0)6.填写实验记录,并整理好工具、模样、砂箱,清扫造型场地。
液态金属的充型能力
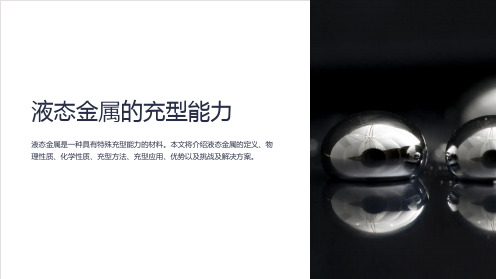
液态金属是一种具有特殊充型能力的材料。本文将介绍液态金属的定义、物 理性质、化学性质、充型方法、充型应用、优势以及挑战及解决方案。
什么是液态金属?
液态金属是一种在常温下处于液体状态的金属。它具有高导电性、高导热性 和优异的机械性能。
液态金属的物理性质
1 高流动性
液态金属具有较高的流动性,能够被轻松注 入复杂的形状和细小的空隙。
1 氧化问题
液态金属容易与空气中的 氧气发生反应,需要采取 相应措施,如惰性气体保 护。
2 温度控制
液态金属的充型过程需要 精确控制温度,以确保质 量和性能。
3 模具设计
液态金属充型对模具的要 求较高,需要进行适当的 设计和优化。
与其他材料反应性低
液态金属与大多数材料的反应 性较低,不会导致副反应和损 坏。
可与其他金属合金化
液态金属能够与其他金属进行 合金化,提高材料的性能和应 用范围。
液态金属的充型方法
1
重力充型
将液态金属通过自由流动充入模具,适用于简单形状的零件充型。
2
压力充型
利用机械力将液态金属压入模具,适用于复杂形状和精密零件的充型。
液态金属充型的优势
高精度
液态金属充型可以制造高精度、高质量的零件, 满足复杂应用的要求。
高效率
液态金属充型过程快速、高效,可大幅提高生 产效率。
材料节约
液态金属充型不需要额外的材料加工,有效减 少浪费。
设计自由度
液态金属充型技术可以实现复杂形状和细节的 自由设计,提供更多创新空间。
液态金属充型的挑战及解决方案
2 低表面张力
液态金属的表面张力相对较低,使其能够更 好地与其他材料接触和结合。
材料成型原理及工艺第一章液态成型工艺基础理论
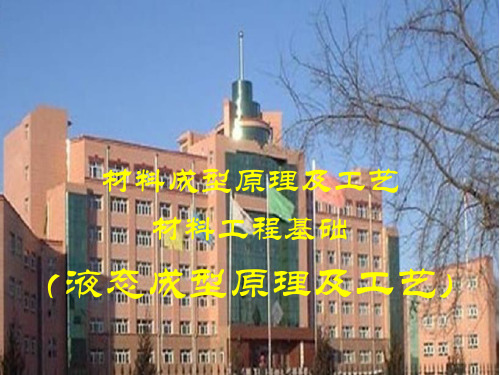
二、液态金属的收缩
(一)收缩的概念
合金从液态冷却至室温的过程中,其体积 或尺寸缩减的现象,称为收缩。收缩是合 金的物理本质。合金的收缩给液态成型工 艺带来许多困难,是许多铸造缺陷(如缩孔、 缩松、裂纹、变形等)产生的根源。
液态成型原理及工艺
合金的收缩经历如下三 个阶段,如图1-4:
又同老的核心一起长大,直至凝固
结束。
液态成型原理及工艺
3、形核方式:
均质形核
依靠液态金属(合 金)内部自身的结
构自发地形核
异质形核
依靠外来夹杂 所提供的异质 界面非自发地
形核液态成型原理及工艺
4、纯金属晶体长大:
形成稳定的晶核后,液相中的
原子不断地向固相核心堆积,
使固-液界面不断地向液相中
推移,导致液态金属(合金)的
态 陷产生,导致成型件力学性能,
成 特别是冲击性能较低。
型 2. 涉及的工序很多,难以精确控
的 制,成型件质量不稳定。
缺 3.由于目前仍以砂型铸造为主,
点:
自动化程度还不很高,且属于热 加工行业,因而工作环境较差。
4.大多数成型件只是毛坯件,需 经过切削加工才能成为零件。
液态成型原理及工艺
冲天炉出铁
的 游离原子
级,在此范围 内仍具有一定
近
液
的规律性。原
程
态
子集团间的空
结
空穴或裂纹 穴或裂纹内分
布着排列无规
有 序
构
则的游离的原
子。
液态成型原理及工艺
这样的结构不是静止的,而是 处于瞬息万变的状态,即原子 集团、空穴或裂纹的大小、形 态及分布及热运动的状态都处 于无时无刻不在变化的状态。 液态中存在着很大的能量起伏。
第二章 液态金属的充型能力
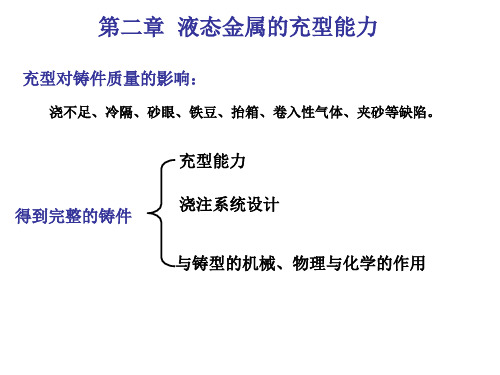
L:合金的结晶潜热, / g carl
F 1 kL C 1 TP Tk l vt 2 gH p T LTm 合金成分 结晶潜热 合金的比热容、密度和 换热系数 1.合金性质
液态金属的粘度 表面张力
§2-3 影响充型能力的因素
影响充型能力的因素
铸型的蓄热系数 2.铸型性质 铸型的温度 铸型中的气体
末端之前的某个部位从型壁向中心生长的柱 状晶相接触,金属的流通道被堵塞。
液态金属的停止 流动机理
2.宽结晶合金停止流动机理
液态金属的停止 流动机理
液态金属的温度是沿程下降的,液流前端冷 却最快,首先结晶,当晶体达到一定数量时, 变结成了一个连续的网状,发生堵塞,停止 流动。
二、液态金属充型能力的计算
4.金属的流动性 液态金属本身的流动能力,称为流动性。
二、流动性、充型能力及铸造缺陷的关系
流动性好,排气排杂,净化金属,还可以凝固后补缩 流动性不好,充型能力弱,浇不足和冷隔,夹杂夹气
三、不同合金及造型方法对金属充型能力的影响 不同金属和不同合金铸造方法铸厚/mm
金属种类
液态金属的充型能力:
TP Tm TL Tm vF 1 C 1 ln l vt C 1 ln p TL Tm Tk Tm
x
v 2gH
ln x x 1
TP Tm TP TL ln TL Tm TL Tm
F 1 kL C 1 TP Tk l vt 2 gH p T LTm 浇注温度
3.浇注条件
充型压头 浇注系统的结构
影响充型能力 的因素
折算厚度(模数)
4.铸件结 构方面
V (铸件的体积 ) F (铸件的断面面积 ) M S (铸件的散热表面积 P (铸件的断面周长 ) )
液态金属的充型能力1
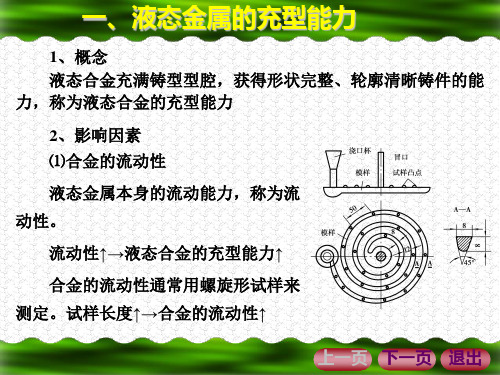
等固相法
内切圆法 特 征:形状不规则,表面不光滑,可以看到发达的树 枝晶末梢 2、缩松的形成 形成过程:
产生原因:液态收缩+凝固收 缩>固态收缩
产生条件:宽结晶温度范围的 合金 出现部位:铸件中心轴线处 上一页 下一页 退出
3、防止措施
顺序凝固原则
同时凝固 原则
内冷铁:铸件 的一部分
冷铁
外冷铁:铸型 的一部分
以上影响因素错综复杂,在实际生产中必须根据具体情况具 体分析,找出其中的主要矛盾,采取措施,才能有效地提高液态 金属的充型能力。
上一页 下一页 退出
3、对铸件质量的影响
充型能力好:
◆ 可获得外形完整、尺寸准确、轮廓清晰的铸件 ◆ 有利于排气和排渣
◆ 有利于补缩
充型能力不好,铸件易产生以下缺陷: 浇不足:液态金属未充满铸型而产生缺肉的现象。 冷隔:两股金属流汇合时因表层氧化而未能融合而产生凹坑 或缝隙的现象。
2、防止措施 ⑴设计上:合理设计铸件结构,以减少铸造内应力;使铸 件形状对称,抵消变形 ⑵工艺上 a.反变形法 b.设置拉筋(热处理后去除) c.控制打箱时间 上一页 下一页 退出
㈤ 裂纹及其防止
1、裂纹的形成 当铸造内应力超过金属的强度极限时,铸件便产生裂纹。
热
形成区域 外观形状 (特征) 高
裂
温
冷
低
裂
温
形状曲折而不规则,裂纹表面 呈氧化色,无金属光泽;裂口 沿晶粒边界通过。 一般分布在铸件易产生应力集
外形呈连续直线状(没有分叉)
或圆滑曲线,裂纹表面干净,具 有金属光泽,有时呈轻微氧化色;
穿过晶粒。
常出现在铸件表面
分
布
中的部位或铸件最后凝固部位 的内部
液态金属的流动性与充型能力有何异同

液态金属的流动性与充型能力有何异同(1)液态金属的流动性指液态金属本身的流动能力,与金属成分,温度杂质含量及物理性质有关。
充型能力是指液态金属充满型腔而获得的结构完整轮廓清晰的能力,与液态金属自身性能和金属种类及铸型等有关。
2)液态金属的浇动性是通过浇注流动的方法衡量的,以式样的长度或某处的厚薄程度表示其流动性;而充型能力的影响影响因素很多,故用流动性表示其充型能力,因此液态金属的流动性可以认为是确定条件下的充型能力。
提高充型能力:1)正确选择合金成分。
2)合理浇注条件。
3)铸件结构适当。
2、什么是流变铸造?其工艺特点。
在固液两相区进行,强烈搅拌,使普通铸造易形成树枝晶被打碎而保留分散的颗粒状,当固相率为50%-70%时仍具有一定的流动性,使得可以在固液两相区温度进行的铸造工艺。
特点:1)可以在固液两相区温度进行铸造。
2)由于固相存在,凝固收缩小,气孔少缩孔缩松大幅度度减少且组织细密3)结晶潜热的释放,对模具冲击性能减小,模具寿命提高。
3、灰口铸铁成型时为什么不设置冒口?灰口铸铁在凝固过程中初生A形成骨架,间隙内部的A与石墨相按共生生长方式生长,石墨相横向生长少,纵向生长多,膨胀力主要作用在液相上,使得液态收缩量加上凝固收缩量小于固态收缩量,使缩孔缩松产生空间减小,即自补缩现象,故不用设置冒口。
4、铸件模数以及其意义。
铸件体积V与铸件散热面积S的比即R=V/S使凝固时间计算更加简便即T=R2/K2。
引入模数的意义:1)计算更加简便2)是对平方根定律的补充,考虑到了铸件形状这个主要影响因素,使计算更接近实际。
5、分析说明纯金属的热过冷仅取决于凝固时熔体中的实际温度分布。
纯金属的平衡凝固温度为T0,S-L界面温度T*=T0GLX,由于△Tk很小,可以略去,所以△T(x)=-GLx,要获得过冷,即GL<0,负的温度梯度,所以纯金属的热过冷仅取决于凝固时熔体的实际温度分布。
6、逐层凝固:△Tc/δT<<1凝固区宽度很小或为0,凝固时,由表及里逐层凝固,通常是窄结晶温度温度范围合金,纯金属以及共晶合金。
- 1、下载文档前请自行甄别文档内容的完整性,平台不提供额外的编辑、内容补充、找答案等附加服务。
- 2、"仅部分预览"的文档,不可在线预览部分如存在完整性等问题,可反馈申请退款(可完整预览的文档不适用该条件!)。
- 3、如文档侵犯您的权益,请联系客服反馈,我们会尽快为您处理(人工客服工作时间:9:00-18:30)。
液态金属的流动性及充型能力
液态金属充填过程是铸件形成的第一阶段,铸件的许多缺陷是在这个过程中形成的。
为了获得优质健全的铸件,必须掌握和控制这个过程。
为此,研究液态金属充满铸型的能力,以便得到形状完整、轮廓清晰的铸件,防止在充型阶段产生缺陷
一、充型的概念
液态合金充满型腔,形成轮廓清晰、形状完整的优质铸件的能力,称为液态合金的流动性又叫做充型能力。
液态合金的流动性愈好,不仅易于铸造出轮廓清晰,薄而形状复杂的铸件,而且有助于液态合金在铸型中收缩时得到补充,有利于液态合金中的气体及非金属夹杂物上浮与排除。
若流动性不好,则易使铸件产生浇不足、冷隔、气孔、夹渣和缩松等缺陷
液态金属充填铸型是一个复杂的物理、化学和流体力学问题,涉及到金属液的各种性质,如密度、黏度、表面张力、氧化性、氧化物的性质及润湿性等。
充型能力的大小影响铸件的成型,充型能力较差的合金难以获得大型、薄壁、结构复杂的健全铸件
而良好的流动性能使铸件在凝固期间产生的缩孔得到液态金属的补充,铸件在凝固末期受阻出现的热裂可以得到液态金属的充填而弥合,有利于防止缺陷产生液态合金流动性的好坏,通常以螺旋形流动性试样的长度来衡量。
如图2-3所示,
将液态合金注入螺旋形试样铸型中,冷凝后,测出其螺旋线长度。
为便于测量,在标准试样上每隔50mm 作出凸点标记,在相同的浇
注工艺条件下,测得的螺旋线长度越长,合金的流动性越好。
常用
合金的流动性如表2-1所示。
其中,灰铸铁、硅黄铜的流动性最好,铝合金次之,铸钢最差
通常,流动性好的合金,充型能力强;流动性差的合金,充型能
力差,在实际的铸造生产中,可以通过改善外界条件来提高其充型
能力,根据铸件的要求及合金的充型能力采取相应的工艺措施以获
得健全的优质铸件。
二、影响充型能力的因素
影响充型的因素是通过两个途径发生作用的:一是影响金属与铸
型之间的热交换条件,从而改变金属液的流动时间;二是影响液态
金属在铸型中的水力学条件,从而改变金属液的流速。
影响液态金
属充型的因素很多,可以归纳为四类:
①第一类因素,属于金属性质方面的,主要有金属的密度、比热、导热系数、结晶潜热、动力黏度、表面张力及结晶特点等。
不同的合金,其流动性有很大差异,对同种合金而言,化学成
分不同,其流动性也不同。
当熔化至液相线以上相同温度时,纯金属、共晶成分和化合物具有最大的充型能力,而位于结晶温度间隔
最大处的合金其充型能力最小。
合金成分对流动性的影响,主要是成分不同时,合金的结晶特
点不同造成的。
纯金属、共晶成分和化合物是在固定温度下凝固的,已凝固的固体层从铸件表面逐层向中心推进,与尚未凝固的液体之
间界面分明,且固体层内表面比较平滑,对液体的流动阻力小,即
流动速度大。
另外,这几类合金在析出较多的固相时,才停止流动,流动的时间较长,所以它们的流动性好。
具有宽结晶温度范围的合金在型腔中流动时,由于在铸件断面
上既存在着发达的树枝晶,又有未凝固的液体与固相混杂的两相区,而且越靠近液流前端枝晶数量越多,所以当液流前端枝晶数量达到
临界值时,金属液就停止流动;合金的结晶温度间隔越宽,两相区
就越宽,枝晶也就越发达,金属液就越早地停止流动,所以流动性差。
主要是由于树枝晶使固体层内表面粗糙,增加了对液态合金流
动的阻力。
合金的结晶温度范围愈宽,则液固两相共存的区域愈宽,液态合金的流动阻力愈大,故流动性愈差。
显然,合金成分愈接近
共晶成分,流动性愈好。
图2 -4所示为 Fe-C合金的流动性与含C量的关系。
由图图2-4 可见,
亚共晶铸铁随含C量的增加,结晶温度范围减小,流动性提高
②第二类因素属于铸型性质方面的主要有铸型的蓄热系数、密度、比热、导热系数、温度、涂料层和发气性、透气性等。
铸型的阻力影响金属液的充填速度,铸型与液态金属的热交换强度影响其流动时间。
因此,通过调整铸型的热物理性质来改善金属的充型能力往往能收到良好的效果。
比如,预热铸型能减少金属液与铸型的温度差,减少两者的热交换,从而提高其充型能力
铸型材料的导热速度愈大,液态合金的冷却速度愈快,从而使其流动性变差。
如液态合金在金属型中的流动性比在砂型中差; 铸件壁厚过小,形状复杂,会增加液态合金的流动阻力,也会降低合金的流动性。
因此,设计铸件时,铸件的壁厚必须大于规定的最小允许壁厚值,并力求形状简单
型砂含水分多或铸型透气性差,会使浇注时产生大量气体且又不能及时排出,造成型腔内气体压力增大,使液态合金流动的阻力
增加,从而降低合金的流动性。
因此,提高铸型的透气性,减少型
砂的水分,多设出气口等,有利于提高液态合金的流动性
当铸型具有一定的发气能力时,在液态金属和铸型之间形成一
层气膜,减少流动的摩擦力,有利于充型。
根据实验研究,湿砂型
中加入小于6%的水和小于7%的煤粉时,液态金属的充型能力提高,但水和煤粉含量过高时,充型能力则下降。
水、煤粉和其他有机物
含量过高时,液态金属的冷却速度加大,在金属液的热作用下,型
腔中的气体膨胀,铸型中的水分大量蒸发,煤粉及有机物燃烧产生
大量气体,如果不能及时排出,则会阻碍金属液流动
③第三类因素,属于浇注条件方面的,主要有液态金属的浇注
温度、静压头,浇注系统中压头的损失及外力场拯力、真空、离心、振动勘的影响等
浇注温度对液态金属的充型能力有决定性的影响。
在一定温度
范围内,浇注温度提高,增加了合金的过热热量,合金单位体积的
热含量增加,充型能力随浇注温度的提高而直线上升;超过一定温
度后,由于金属吸气增多,氧化严重,充型能力则下降
充型压头越大,液态金属在流动方向上所受的压力越大,液态
金属流动速度越大,充型能力越好。
生产中常用增加液态金属静压
头的方法提高充型能力,但是,液态金属充型速度过高时,会发生
喷射和飞溅现象,增加金属液的氧化,产生“铁豆”缺陷,而且型
腔中气体来不及排出,反压增加,造成浇不足或冷隔缺陷
浇注系统结构越复杂,流动阻力越大,静压头相同时,充型能
力越差。
在铝合金、镁合金铸造中,为使金属液流动平稳,常采用
蛇形及扁平状直浇道,流动阻力越大,充型能力显著下降
中减少薄壁铸件的浇不足、冷隔等缺陷的重要措施。
但浇注温
度过高,铸件易产生缩孔、缩松、黏砂、气孔、粗晶等缺陷,在保
证铸件薄壁部分能充满的前提下,浇注温度不宜过高。
各种合金的
浇注温度范围是:铸铁为1230-.14500C;铸钢为1520-16200C; 铝合
金为680--780gC。
薄壁复杂件取上限,厚大件取下限
④第四类因素,属于铸件结构方面的,主要有铸件的折算厚度,及由铸件结构所规定的型腔的复杂程度引起的压头损失
在铸件体积相同、浇注条件一致时,折算厚度大的铸件,由于其与铸型接触的表面积小,散热慢,则充型能力好。
铸件壁越薄,折算厚度越小,则不易被充满。
铸件结构复杂,薄壁部分过渡面多,型腔的结构复杂程度增加,流动阻力大,充型能力也会下降
三、常用提高充型能力的措施针对影响充型能力的因素提出改善充型能力的措施,仍然可以从上述四类因素入手
①合金设计方面,在不影响铸件使用性能的情况下,可根据铸件大小、厚薄和铸型性质等因素,将合金成分调整到共晶成分附近;采取某些工艺措施,使合金晶粒细化,也有利于提高充型能力
由于夹杂物影响充型能力,故在熔炼时应使原材料清洁,并采取措施减少液态金属中的气体和非金属夹杂物
②铸型方面,对金属铸型、熔模型壳等提高铸型温度,利用涂料增加铸型的热阻,提高铸型的排气能力,减小铸型在金属填充期间的发气速度,均有利于提高充型能力
③浇注条件方面,适当提高浇注温度,提高充型压头,简化浇注系统均有利于提高充型能力
④铸件结构方面能提供的措施则有限
应该指出的是:在采取上述措施时,往往会带来其他问题,这
时要抓住主要矛盾,解决主要问题,由此引起的其他问题应是次要的,且可用另外的措施来解决
在生产中,尤其是对要求高的铸件,在合金成分及铸件结构设计两方面采取措施都是不现实的。
对大型薄壁铸件,一般采用以下三条措施来改善成型问题
①提高浇注温度
②增加充填速度。
这里所说的速度不是液流的线速度,而是充填的体积速度。
增大浇口面积可在线速度较小的情况下很快充型。