SQE工程师日常工作职责
sqe工程师岗位职责
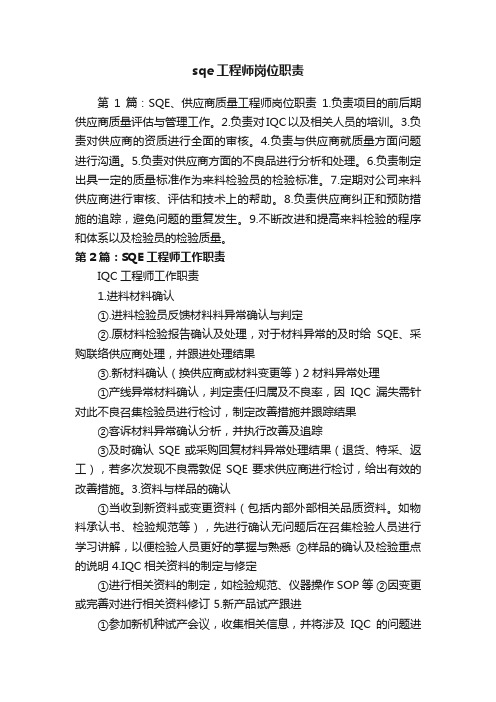
sqe工程师岗位职责第1篇:SQE、供应商质量工程师岗位职责1.负责项目的前后期供应商质量评估与管理工作。
2.负责对IQC以及相关人员的培训。
3.负责对供应商的资质进行全面的审核。
4.负责与供应商就质量方面问题进行沟通。
5.负责对供应商方面的不良品进行分析和处理。
6.负责制定出具一定的质量标准作为来料检验员的检验标准。
7.定期对公司来料供应商进行审核、评估和技术上的帮助。
8.负责供应商纠正和预防措施的追踪,避免问题的重复发生。
9.不断改进和提高来料检验的程序和体系以及检验员的检验质量。
第2篇:SQE工程师工作职责IQC工程师工作职责1.进料材料确认①.进料检验员反馈材料料异常确认与判定②.原材料检验报告确认及处理,对于材料异常的及时给SQE、采购联络供应商处理,并跟进处理结果③.新材料确认(换供应商或材料变更等)2材料异常处理①产线异常材料确认,判定责任归属及不良率,因IQC漏失需针对此不良召集检验员进行检讨,制定改善措施并跟踪结果②客诉材料异常确认分析,并执行改善及追踪③及时确认SQE或采购回复材料异常处理结果(退货、特采、返工),若多次发现不良需敦促SQE要求供应商进行检讨,给出有效的改善措施。
3.资料与样品的确认①当收到新资料或变更资料(包括内部外部相关品质资料。
如物料承认书、检验规范等),先进行确认无问题后在召集检验人员进行学习讲解,以便检验人员更好的掌握与熟悉②样品的确认及检验重点的说明 4.IQC相关资料的制定与修定①进行相关资料的制定,如检验规范、仪器操作SOP等②因变更或完善对进行相关资料修订 5.新产品试产跟进①参加新机种试产会议,收集相关信息,并将涉及IQC的问题进行宣导②跟催新机种相关资料、样品及工夹具等③新机种物料检验相关要求及注意事项讲解及确认④新机种总结会议相关问题的提出及相关内容改善 6.检验员的培训①制定年度培训计划对检验员进行培训,以提高其技能②对新员工制定培训计划,按照计划使其逐步掌握,考核上岗。
2024年sqe工程师岗位职责要求3篇

2024年sqe工程师岗位职责要求3篇目录第1篇汽车sqe工程师岗位职责描述岗位要求第2篇sqe工程师岗位职责描述岗位要求第3篇sqe工程师岗位职责工作内容及任职资格要求sqe工程师岗位职责工作内容及任职资格要求sqe工程师工作职责岗位职责:1、负责保障供应商所供原材料的质量,由于供应商供货物料质量缺陷引发的问题要及时反馈供应商要求其改善;2、负责追踪确认供应商的改善报告及实施效果,必要时可进行现场审核检查以及辅导;3、负责制定进货检验部门的检验规范及检验计划,并适时对检验员进行培训指导;4、参与供应商初始样品的评估放行工作;5、每月或每季度,对现有供应商的质量状况进行统计评分,对评分较低的供应商提出限期改善要求;6、参与新供应商开发与审核,与采购、研发部门一起对新供应商进行考核打分。
企业对sqe工程师要求以下内容来自制度大全企业对sqe工程师的职责要求岗位职责及任职资格a岗位职责:任职要求:1、25岁以上,本科以上学历,电子或管理专业;2、3年以上照明行业工作经验,其中1年以上供应商管理经验;3、熟悉led灯具、电子的生产工艺、制造流程、质量标准。
岗位职责及任职资格b岗位职责:iqc工作管理,来料不良品的处理及跟踪,供应商管理任职要求:28-35岁,男女不限,大专以上学历,机械或电子专业,5年以上工作经验(其中3年以上iqc管理工作经验)福利待遇:5天8小时,周末双休,入职满一个月后购买医疗、失业、工伤保险岗位职责及任职资格c岗位职责:1、负责保障供应商所供原材料的质量,由于供应商供货物料质量缺陷引发的问题要及时反馈供应商要求其改善;2、负责追踪确认供应商的改善报告及实施效果,必要时可进行现场审核检查以及辅导;3、负责制定进货检验部门的检验规范及检验计划,并适时对检验员进行培训指导;4、参与供应商初始样品的评估放行工作;5、每月或每季度,对现有供应商的质量状况进行统计评分,对评分较低的供应商提出限期改善要求;6、参与新供应商开发与审核,与采购、研发部门一起对新供应商进行考核打分。
SQE工程师岗位职责

SQE工程师岗位职责
作为一个软件质量工程师(SQE),他们的工作是确保软件产品质量。
以下是SQE工程师的主要职责:
1. 质量标准和指南:SQE工程师制定和实施软件开发过程中的质量标准和指南,以确保软件交付达到高质量要求。
2. 质量计划:制定和执行软件质量计划,通过质量评审、代码审查、单元测试、功能测试、性能测试和安全测试等手段来验证软件质量。
3. 缺陷管理:对测试结果进行跟踪,记录和跟踪缺陷,协调测试、开发及各方面之间的沟通,确保软件的质量达到客户要求。
4. 自动化测试:推动自动化测试技术的应用,开发和维护自动化测试工具和框架,提升测试效率和质量。
5. 内部培训:针对QA和开发人员提供相关的软件质量管理标准和实践等方面的培训,确保所有的人员都了解并遵守软件质量管理标准。
6. 与开发团队的协调:与开发团队沟通,确保他们了解并理解软件质量标准和指南并遵守这些标准,确保开发过程中的质量问题能够得到解决。
7. 质量报告:向上级汇报软件质量状况,并提出改善意见。
8. 过程改进:提出关于软件开发过程改进的建议和意见,不断提升软件的质量和效率。
总结:
SQE工程师的职责是确保软件产品达到高质量要求。
他们需要制定和实施软件质量标准和指南,制定和执行软件质量计划,推动
自动化测试技术的应用,与开发团队协调,向上级汇报软件质量状况并提出改善意见。
他们还要提出关于软件开发过程改进的建议和意见。
2024年sqe岗位职责要求5篇
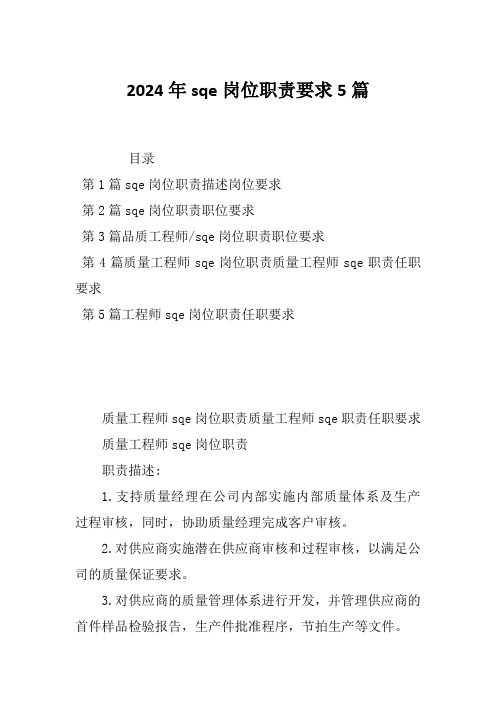
2024年sqe岗位职责要求5篇目录第1篇sqe岗位职责描述岗位要求第2篇sqe岗位职责职位要求第3篇品质工程师/sqe岗位职责职位要求第4篇质量工程师sqe岗位职责质量工程师sqe职责任职要求第5篇工程师sqe岗位职责任职要求质量工程师sqe岗位职责质量工程师sqe职责任职要求质量工程师sqe岗位职责职责描述:1.支持质量经理在公司内部实施内部质量体系及生产过程审核,同时,协助质量经理完成客户审核。
2.对供应商实施潜在供应商审核和过程审核,以满足公司的质量保证要求。
3.对供应商的质量管理体系进行开发,并管理供应商的首件样品检验报告,生产件批准程序,节拍生产等文件。
4.帮助供应商改进产品质量并纠正质量失效以达成供应商在质量,交付及成本上的持续改进。
任职要求:1.本科以上学历,至少5年汽车行业供应商质量管理工作经验2.熟悉pcba电路板的制造工艺及相关技术,对smt制程有一定经验,了解ipc标准。
3.熟悉汽车工业的质量保证规范和方法,包括iso/ts16949,vda,产品质量先期策划,统计过程控制,测量系统分析,生产件批准程序,潜在失效模式及后果分析,节拍生产。
4.通过六西格玛,精益原则及质量管理体系的质量管理方法,在帮助供应商改进过程,质量及成本有成功的经历及经验。
5.掌握vda,ts16949及六西格玛的质量方法6.熟练的英文阅读,书写及口语能力7.可以适应出国及在国内出差sqe岗位职责描述岗位要求职位描述:供应商管理(外协加工)2名工作岗位及职责:1.负责开发新工艺或新供应商,并收集资料,以及对供应商进行调查,创建供应商主档申请;2.负责收集报价,并进行比价/议价等贸易条款的谈判,负责维护外发加工产品价格info;3.负责po的下达,交期追踪、交收或验收、品质追踪、对账、发票校验、请款工作的跟进;4.负责跟进供应商提供之环保报告有效性的追踪及更新;5.负责定期对供应商的绩效进行评估考核;6.负责及时清理open pr、open po、open payment;7.负责量产产品与供应商谈判每季度costdown;8.负责根据实际情况(瓶颈工序或供应商)寻找替代工序及供应源;9.负责供应商能力分析;10.负责采购资料的按时归集存档。
SQE工程师日常工作职责
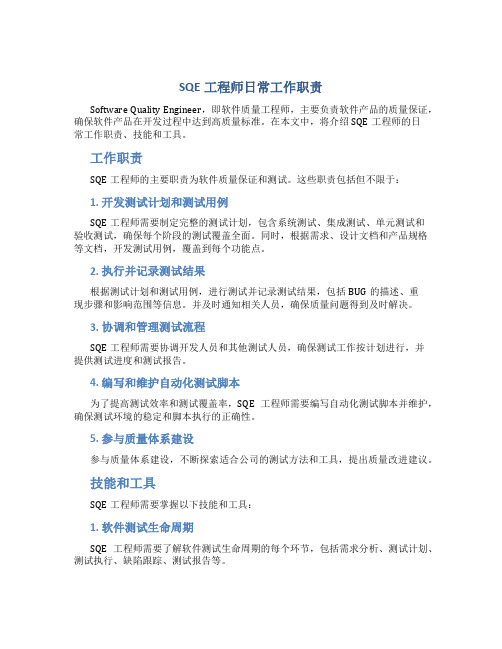
SQE工程师日常工作职责Software Quality Engineer,即软件质量工程师,主要负责软件产品的质量保证,确保软件产品在开发过程中达到高质量标准。
在本文中,将介绍SQE工程师的日常工作职责、技能和工具。
工作职责SQE工程师的主要职责为软件质量保证和测试。
这些职责包括但不限于:1. 开发测试计划和测试用例SQE工程师需要制定完整的测试计划,包含系统测试、集成测试、单元测试和验收测试,确保每个阶段的测试覆盖全面。
同时,根据需求、设计文档和产品规格等文档,开发测试用例,覆盖到每个功能点。
2. 执行并记录测试结果根据测试计划和测试用例,进行测试并记录测试结果,包括BUG的描述、重现步骤和影响范围等信息。
并及时通知相关人员,确保质量问题得到及时解决。
3. 协调和管理测试流程SQE工程师需要协调开发人员和其他测试人员,确保测试工作按计划进行,并提供测试进度和测试报告。
4. 编写和维护自动化测试脚本为了提高测试效率和测试覆盖率,SQE工程师需要编写自动化测试脚本并维护,确保测试环境的稳定和脚本执行的正确性。
5. 参与质量体系建设参与质量体系建设,不断探索适合公司的测试方法和工具,提出质量改进建议。
技能和工具SQE工程师需要掌握以下技能和工具:1. 软件测试生命周期SQE工程师需要了解软件测试生命周期的每个环节,包括需求分析、测试计划、测试执行、缺陷跟踪、测试报告等。
2. 软件测试方法和工具SQE工程师需要了解多种软件测试方法和工具,如黑盒测试、白盒测试、UI测试、性能测试等,以及测试管理工具、缺陷管理工具、自动化测试工具等。
3. 编程语言SQE工程师需要至少熟悉一种编程语言,如Python、Java、Javascript等,以编写自动化测试脚本。
4. 操作系统和网络知识SQE工程师需要了解常用操作系统和网络协议,如Linux、Windows、TCP/IP 等,以适应测试环境和开发过程中的需求。
sqe岗位职责说明书

sqe岗位职责说明书SQE 岗位职责说明书一、岗位概述SQE(Supplier Quality Engineer,供应商质量工程师)是企业中负责管理和提升供应商产品或服务质量的关键岗位。
他们在保障供应链的稳定性和可靠性方面发挥着重要作用,通过与供应商的密切合作,确保所采购的物资和服务符合企业的质量要求和标准。
二、岗位职责1、供应商开发与评估(1)协助采购部门寻找潜在供应商,收集供应商的相关信息,包括生产能力、质量体系、技术水平等。
(2)对潜在供应商进行实地考察和评估,评估内容包括生产设备、工艺流程、质量管理体系、人员素质等方面。
(3)根据评估结果,撰写供应商评估报告,为采购部门提供决策依据,确定合格的供应商名录。
2、质量体系管理(1)推动供应商建立和完善质量管理体系,使其符合企业的质量要求和行业标准。
(2)定期对供应商的质量管理体系进行审核和监督,确保其有效运行。
(3)协助供应商制定质量改进计划,并跟踪改进效果。
3、质量检验与监控(1)制定供应商产品的检验标准和检验流程,明确检验项目、抽样方法和检验频率。
(2)对供应商提供的原材料、零部件和成品进行检验和测试,确保其质量符合要求。
(3)收集和分析检验数据,及时发现质量问题,并向供应商反馈。
4、质量问题处理(1)当供应商产品出现质量问题时,及时与供应商沟通,要求其采取紧急措施进行整改。
(2)组织相关部门对质量问题进行分析,确定问题的根本原因和责任归属。
(3)监督供应商实施纠正措施,并对整改效果进行验证,确保问题不再重复发生。
5、供应商绩效评估(1)建立供应商绩效评估指标体系,包括质量、交付、服务等方面。
(2)定期对供应商进行绩效评估,根据评估结果对供应商进行分级管理。
(3)与供应商沟通绩效评估结果,提出改进建议和要求,激励供应商持续提升绩效。
6、持续改进(1)收集和分析供应商质量数据,总结经验教训,提出改进措施和建议,优化供应商质量管理流程和方法。
sqe供应商质量管理工程师工作职责与职位要求

sqe供应商质量管理工程师工作职责与职位要求(经典版)编制人:__________________审核人:__________________审批人:__________________编制单位:__________________编制时间:____年____月____日序言下载提示:该文档是本店铺精心编制而成的,希望大家下载后,能够帮助大家解决实际问题。
文档下载后可定制修改,请根据实际需要进行调整和使用,谢谢!并且,本店铺为大家提供各种类型的经典范文,如工作报告、合同协议、心得体会、演讲致辞、规章制度、岗位职责、操作规程、计划书、祝福语、其他范文等等,想了解不同范文格式和写法,敬请关注!Download tips: This document is carefully compiled by this editor. I hope that after you download it, it can help you solve practical problems. The document can be customized and modified after downloading, please adjust and use it according to actual needs, thank you!Moreover, our store provides various types of classic sample texts, such as work reports, contract agreements, insights, speeches, rules and regulations, job responsibilities, operating procedures, plans, blessings, and other sample texts. If you want to learn about different sample formats and writing methods, please pay attention!sqe供应商质量管理工程师工作职责与职位要求sqe供应商质量管理工程师工作职责与职位要求怎么写1.供应商评估:SQE需对潜在供应商进行严格的资质审查,包括质量管理体系、生产设施、工艺流程、过往业绩等方面,以确定其是否具备满足公司质量标准的能力。
sqe岗位职责是什么

sqe岗位职责是什么【SQE岗位职责是什么】SQE(Software Quality Engineer)岗位是软件质量工程师的职位,主要负责软件开发过程中的质量保证和质量控制工作。
本文将介绍SQE岗位的职责及其相关内容。
一、SQE岗位职责概述SQE岗位是软件开发过程中非常重要的一环,其职责涵盖了质量保证和质量控制两个方面。
质量保证主要包括制定质量保证计划、评审需求及设计规范、制定测试策略、培训团队成员等;而质量控制则包括测试方案制定、测试用例设计和执行、缺陷管理、性能测试等工作。
二、SQE岗位具体职责1. 与项目团队合作:SQE需要与软件开发团队、测试团队和其他相关部门合作,确保软件开发过程中的质量问题得到有效解决。
2. 制定质量保证计划:根据项目需求和相关标准,制定质量保证计划,明确质量目标和质量评审流程,为项目的质量管理提供指导。
3. 评审需求和设计规范:SQE需要参与需求评审和设计评审,确保项目需求和设计的准确性、完整性和一致性。
4. 制定测试策略:根据项目特点和需求,制定适合的测试策略,包括测试范围、测试目标、测试方法和测试工具的选择等。
5. 编写与执行测试用例:SQE需要根据需求和设计规范,编写详细的测试用例,并确保测试用例的覆盖率和准确性。
同时,SQE需要组织和执行测试过程,记录测试结果和问题。
6. 缺陷管理:SQE需要负责对测试过程中发现的缺陷进行跟踪和管理,与开发团队合作解决问题,并确保缺陷及时修复和验证。
7. 性能测试和优化:SQE需要进行性能测试,并根据测试结果分析和优化系统性能,确保系统在高负载情况下的稳定性和可靠性。
8. 进行培训:SQE需要对团队成员进行相关质量管理和测试技术的培训,提高团队整体的质量意识和测试水平。
9. 持续改进:SQE需要不断总结经验和教训,对软件开发过程进行分析和改进,提高项目整体质量和效率。
三、SQE岗位的技能要求1. 扎实的软件质量理论基础:SQE需要具备扎实的软件质量理论知识,熟悉相关标准和规范。
SQE工作职责范文
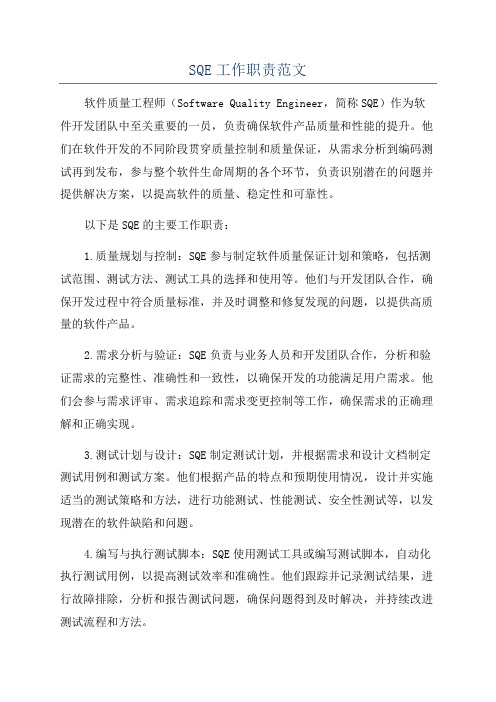
SQE工作职责范文软件质量工程师(Software Quality Engineer,简称SQE)作为软件开发团队中至关重要的一员,负责确保软件产品质量和性能的提升。
他们在软件开发的不同阶段贯穿质量控制和质量保证,从需求分析到编码测试再到发布,参与整个软件生命周期的各个环节,负责识别潜在的问题并提供解决方案,以提高软件的质量、稳定性和可靠性。
以下是SQE的主要工作职责:1.质量规划与控制:SQE参与制定软件质量保证计划和策略,包括测试范围、测试方法、测试工具的选择和使用等。
他们与开发团队合作,确保开发过程中符合质量标准,并及时调整和修复发现的问题,以提供高质量的软件产品。
2.需求分析与验证:SQE负责与业务人员和开发团队合作,分析和验证需求的完整性、准确性和一致性,以确保开发的功能满足用户需求。
他们会参与需求评审、需求追踪和需求变更控制等工作,确保需求的正确理解和正确实现。
3.测试计划与设计:SQE制定测试计划,并根据需求和设计文档制定测试用例和测试方案。
他们根据产品的特点和预期使用情况,设计并实施适当的测试策略和方法,进行功能测试、性能测试、安全性测试等,以发现潜在的软件缺陷和问题。
4.编写与执行测试脚本:SQE使用测试工具或编写测试脚本,自动化执行测试用例,以提高测试效率和准确性。
他们跟踪并记录测试结果,进行故障排除,分析和报告测试问题,确保问题得到及时解决,并持续改进测试流程和方法。
5.缺陷跟踪与管理:SQE负责跟踪和管理发现的软件缺陷和问题,与开发团队合作,确保及时修复和验证缺陷的修复。
他们还识别和记录常见的缺陷模式和原因,并提出预防措施,以降低缺陷再次发生的可能性。
6.性能优化与评估:SQE负责对软件的性能进行评估和优化,通过负载测试、压力测试等手段,发现性能瓶颈和潜在的问题,并提供相应的改进建议。
他们还与开发团队合作,优化程序代码、数据库设计等,以提高软件的性能和响应速度。
7.测试环境和工具的维护:SQE负责维护和管理测试环境,包括硬件、软件和网络等,保证测试环境的稳定和可靠性。
SQE(现场问题解决工程师)工作职责
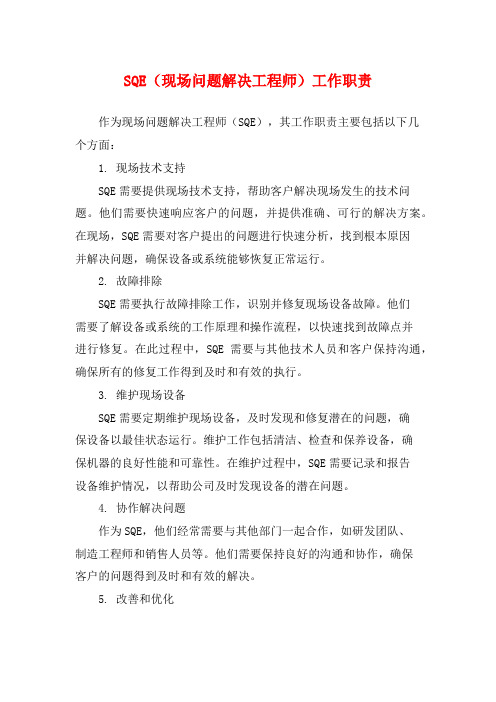
SQE(现场问题解决工程师)工作职责作为现场问题解决工程师(SQE),其工作职责主要包括以下几个方面:1. 现场技术支持SQE需要提供现场技术支持,帮助客户解决现场发生的技术问题。
他们需要快速响应客户的问题,并提供准确、可行的解决方案。
在现场,SQE需要对客户提出的问题进行快速分析,找到根本原因并解决问题,确保设备或系统能够恢复正常运行。
2. 故障排除SQE需要执行故障排除工作,识别并修复现场设备故障。
他们需要了解设备或系统的工作原理和操作流程,以快速找到故障点并进行修复。
在此过程中,SQE需要与其他技术人员和客户保持沟通,确保所有的修复工作得到及时和有效的执行。
3. 维护现场设备SQE需要定期维护现场设备,及时发现和修复潜在的问题,确保设备以最佳状态运行。
维护工作包括清洁、检查和保养设备,确保机器的良好性能和可靠性。
在维护过程中,SQE需要记录和报告设备维护情况,以帮助公司及时发现设备的潜在问题。
4. 协作解决问题作为SQE,他们经常需要与其他部门一起合作,如研发团队、制造工程师和销售人员等。
他们需要保持良好的沟通和协作,确保客户的问题得到及时和有效的解决。
5. 改善和优化SQE需要思考如何改善和优化现有的设备和系统,以提高其稳定性、效率和可靠性。
他们需要紧密关注市场和技术的变化,并提出改进设备和系统的建议。
同时,他们还需要负责开发和实施这些改进方案,并确保清楚地解释升级或更改的必要性。
总之,现场问题解决工程师(SQE)需要具备高度的技术能力、沟通能力和团队合作精神,以有效解决客户现场遇到的问题并优化设备和系统。
质量工程师(SQE)工作职责

质量工程师(SQE)工作职责
质量工程师(SQE)的工作职责是确保所有产品和服务都遵循规定的质量标准,使其达到客户和企业的期望。
他们需要在整个生产过程中实施质量计划和控制,解决质量问题,并建立并维护有效的供应商关系。
以下是SQE的具体工作职责:
1. 开发和执行质量计划:SQE需要开发和执行质量计划,确保产品符合质量标准。
他们也需要与其他部门合作,确保产品设计和制造过程符合质量要求。
2. 进行质量审核:SQE需要审核产品设计和制造过程,检查是否符合规定的质量标准和指南。
3. 识别和分析质量问题:SQE需要调查和识别质量问题,并采取措施进行纠正和预防。
他们还需要在整个生产过程中管理过程变化控制,并确保产品能满足质量标准。
4. 形成决策支持:SQE需要分析数据,并提供决策支持,包括关于产品制造过程和质量改进方案的建议。
5. 建立供应商关系:SQE还需要与供应商合作,建立并维护有效的供应商关系。
他们需要确保供应商符合质量要求,并提供支持以确保供应链可靠。
6. 实施质量控制:SQE需要监督产品制造过程,并实施质量控制方法以确保产品符合质量要求。
7. 客户沟通:SQE需要与客户合作,并确保生产的产品符合客户的期望。
综上所述,SQE的工作职责在整个生产过程中处境重要,在确保产品质量和客户满意度方面很关键。
他们需要有扎实的技术能力
和分析能力,以便正确识别和解决质量问题,保证产品和服务符合要求。
此外,SQE还需要具备良好的团队合作和沟通能力,以确保与其他部门和供应商的合作有效地实现。
SQE 工程师工作职责

SQE 工程师工作职责
软件质量工程师(SQE,Software Quality Engineer)的职责
是确保软件产品质量符合客户需求和公司的要求。
以下是SQE工程
师的工作职责:
1. 质量标准管理:负责制定并维护公司软件质量标准,为开发
团队提供指导,促进软件质量的提升。
2. 质量监控:监控软件开发过程中的质量状况,开展代码检查、软件测试、审查等工作,及时发现并解决问题,保证软件质量。
3. 缺陷管理:负责记录、跟踪和管理软件缺陷,包括缺陷的发现、分析、分类、定位和跟踪处理,确保缺陷得到及时修复,并对
数据进行统计和分析,为产品的持续改进提供数据支持。
4. 测试策略和计划:负责制定测试策略、测试计划和测试用例,指导测试团队的工作,并协调与开发团队的沟通和联动。
5. 质量评估:参与软件产品的评估工作,评估软件的可靠性、
可维护性、可用性等方面的质量,提出改进建议,并监督改进实施。
6. 改进流程:参与流程改进,负责开发和实施优化方案,制定
流程规范和指导文件,推动公司质量文化建设,提高公司软件开发
的质量水平。
7. 知识管理:收集、整理和归纳软件质量相关的知识和经验,
制作和维护知识库、流程库和工具库等,支持团队和公司的学习和
提高。
8. 团队协作:与开发团队、测试团队、产品团队、运维团队等
协调工作,建立良好的沟通机制和协作模式,以达到团队协作最佳
效果。
总之,SQE工程师是软件开发中质量管理的专家和推动者,通过监控、分析和改进软件开发流程,提高软件产品的质量,为客户提供满意的产品和服务。
SQE工作内容及职责
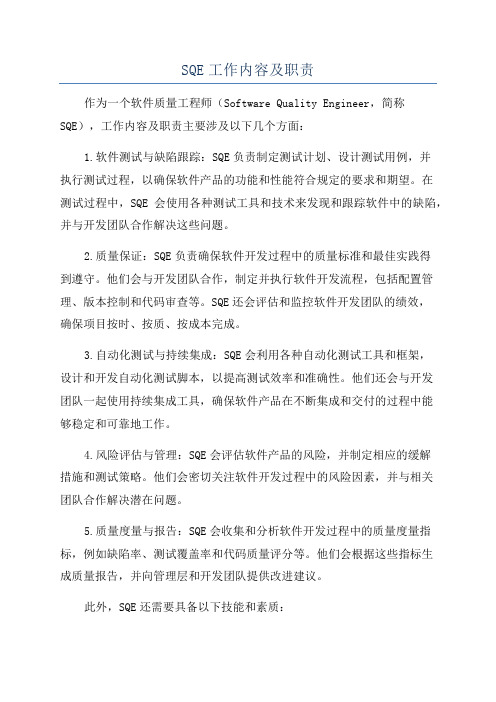
SQE工作内容及职责作为一个软件质量工程师(Software Quality Engineer,简称SQE),工作内容及职责主要涉及以下几个方面:1.软件测试与缺陷跟踪:SQE负责制定测试计划、设计测试用例,并执行测试过程,以确保软件产品的功能和性能符合规定的要求和期望。
在测试过程中,SQE会使用各种测试工具和技术来发现和跟踪软件中的缺陷,并与开发团队合作解决这些问题。
2.质量保证:SQE负责确保软件开发过程中的质量标准和最佳实践得到遵守。
他们会与开发团队合作,制定并执行软件开发流程,包括配置管理、版本控制和代码审查等。
SQE还会评估和监控软件开发团队的绩效,确保项目按时、按质、按成本完成。
3.自动化测试与持续集成:SQE会利用各种自动化测试工具和框架,设计和开发自动化测试脚本,以提高测试效率和准确性。
他们还会与开发团队一起使用持续集成工具,确保软件产品在不断集成和交付的过程中能够稳定和可靠地工作。
4.风险评估与管理:SQE会评估软件产品的风险,并制定相应的缓解措施和测试策略。
他们会密切关注软件开发过程中的风险因素,并与相关团队合作解决潜在问题。
5.质量度量与报告:SQE会收集和分析软件开发过程中的质量度量指标,例如缺陷率、测试覆盖率和代码质量评分等。
他们会根据这些指标生成质量报告,并向管理层和开发团队提供改进建议。
此外,SQE还需要具备以下技能和素质:-扎实的软件开发和测试基础知识,熟悉常用的软件开发过程和测试方法。
-熟悉主流的编程语言和脚本语言,能够开发和维护自动化测试脚本。
-熟悉测试工具和框架,能够有效地利用它们进行测试和缺陷跟踪。
-具备良好的沟通能力和团队合作能力,能够与开发团队密切合作,解决软件质量问题。
-有较强的分析和解决问题的能力,能够快速定位和修复软件中的缺陷。
-具备自主学习和持续学习的能力,能够及时了解和掌握新的测试技术和工具。
总体而言,SQE的工作内容和职责是确保软件产品的质量和稳定性,同时促进软件开发团队的效率和合作。
sqe岗位职责是什么

sqe岗位职责是什么随着技术的发展,软件质量工程师(SQE)这个职位也越来越受到重视。
那么SQE岗位职责到底是什么呢?本文将分别从工作职责、技能要求、工作流程和职业发展等方面进行探讨。
一、工作职责1. 测试计划制定:SQE需要理解产品的业务需求,并根据需求推导出测试用例,制定测试计划。
这些计划要考虑不同的测试场景,例如功能测试、性能测试、安全测试等。
2. 测试环境搭建:实际测试需要依赖测试环境,包括硬件设备和软件配置等。
SQE需要确保测试环境的准备工作充分,并保证测试的可重复性和准确性。
3. 测试执行与跟踪:在测试计划制定完成后,SQE需要执行测试用例,并记录测试结果。
同时还需要跟踪开发人员对于测试问题的解决情况,并进行回归测试。
4. 缺陷分析和报告:在测试过程中,SQE需要发现并分析软件缺陷。
如果发现问题,需要及时上报,并跟踪解决过程,确保问题得到妥善解决。
5. 测试文档编写:作为测试过程的记录,SQE需要编写测试文档,包括测试报告、测试用例、测试记录和升级说明等。
二、技能要求1. 具备软件测试基础知识:SQE需要掌握测试理论和方法,熟悉测试流程和测试工具。
具备较好的编程基础,能够进行测试脚本编写和自动化测试。
2. 良好的沟通与协作能力:SQE需要与团队成员、开发人员以及其他相关工作人员保持良好的沟通。
能够根据不同团队的业务需求进行协作,解决问题。
3. 细致认真负责:SQE需要非常细致,认真负责,以确保测试的准确性和全面性。
4. 学习能力强:SQE需要保持敏锐的观察力和学习能力,及时跟踪和掌握新技术和工具的动态。
三、工作流程1. 需求分析:在测试前,SQE需要先理解业务需求,分析业务场景,制定测试计划。
2. 测试策略和过程制定:根据需求和场景,SQE需要制定不同的测试策略和过程,包括测试计划、测试进度、测试用例等。
3. 测试执行与记录:在测试过程中,SQE需要执行测试用例,并记录测试结果和缺陷情况。
SQE主要工作职责

SQE主要工作职责SQE(软件质量工程师)主要负责软件开发过程中的质量管理。
他们是团队中的关键成员,通过测试和验证软件产品的质量,并确保其符合客户的需求和标准。
以下是SQE主要的工作职责:1.质量策划:SQE负责制定软件质量保证计划,包括质量目标、测试策略和测试计划。
他们与项目管理团队和开发团队合作,确保软件开发过程中有一套适当的质量控制措施。
2.测试计划:SQE根据软件需求和规格,制定详细的测试计划。
他们定义测试方法和测试环境,并准备测试用例和测试数据。
3.测试执行:SQE负责执行测试计划,使用适当的测试工具和技术进行测试。
他们进行功能测试、性能测试、安全测试和兼容性测试等不同类型的测试。
测试过程中,他们记录和跟踪缺陷,并与开发团队合作进行修复。
4.缺陷管理:SQE在测试过程中发现缺陷并跟踪缺陷修复过程。
他们使用缺陷管理工具来跟踪缺陷的状态、优先级和解决方案。
他们与开发团队和产品团队合作,确保缺陷及时修复。
5.自动化测试:SQE使用自动化测试工具和脚本来执行重复性的测试任务。
他们开发和维护自动化测试脚本,并确保其准确性和可靠性。
自动化测试可以提高测试效率,减少人力资源和时间成本。
6.风险评估:SQE评估软件开发过程中的风险,并提供相应的风险管理策略和解决方案。
他们分析潜在的风险并制定相应的测试计划,以确保软件质量。
7.报告和沟通:SQE负责编写测试报告,总结测试结果和质量问题。
他们向项目管理团队和开发团队提供准确的测试信息,并就测试结果和质量问题进行沟通和讨论。
他们可以对测试结果进行定期的会议和演示。
8.质量监控:SQE监控软件开发过程中的质量指标,并采取相应的措施以保证产品质量。
他们进行统计分析和质量评估,以及对各个阶段的质量可控性进行评估。
9.持续改进:SQE不断寻求改进软件质量管理过程,提高测试效率和质量准确性。
他们研究新的测试方法和工具,通过持续改进,提高软件产品的质量。
总之,SQE在软件开发过程中扮演着关键的角色,他们负责确保软件产品的质量,并与项目管理团队、开发团队和产品团队密切合作,以确保软件符合客户的需求和标准。
sqe岗位职责是什么
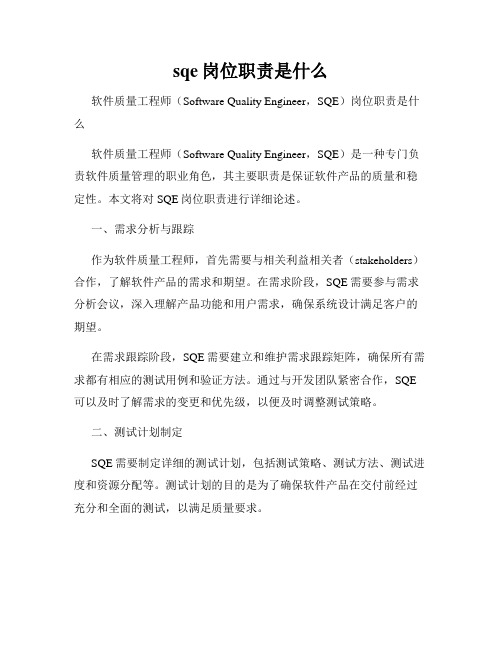
sqe岗位职责是什么软件质量工程师(Software Quality Engineer,SQE)岗位职责是什么软件质量工程师(Software Quality Engineer,SQE)是一种专门负责软件质量管理的职业角色,其主要职责是保证软件产品的质量和稳定性。
本文将对SQE岗位职责进行详细论述。
一、需求分析与跟踪作为软件质量工程师,首先需要与相关利益相关者(stakeholders)合作,了解软件产品的需求和期望。
在需求阶段,SQE需要参与需求分析会议,深入理解产品功能和用户需求,确保系统设计满足客户的期望。
在需求跟踪阶段,SQE需要建立和维护需求跟踪矩阵,确保所有需求都有相应的测试用例和验证方法。
通过与开发团队紧密合作,SQE 可以及时了解需求的变更和优先级,以便及时调整测试策略。
二、测试计划制定SQE需要制定详细的测试计划,包括测试策略、测试方法、测试进度和资源分配等。
测试计划的目的是为了确保软件产品在交付前经过充分和全面的测试,以满足质量要求。
测试计划制定需要综合考虑项目的时间限制、资源分配、测试环境等因素。
SQE需要与各方合作,明确测试的范围和目标,并制定相应的测试用例、测试数据和测试环境。
三、测试执行与缺陷管理SQE需要根据测试计划进行测试执行,并管理测试过程中发现的缺陷(bugs)。
测试执行包括执行测试用例、记录测试结果、检查和分析测试日志等。
在测试执行过程中,SQE需要根据测试策略选择合适的测试方法,包括黑盒测试、白盒测试、性能测试、安全测试等。
同时,SQE需要及时记录和报告系统中发现的缺陷,并与开发团队合作,跟踪和解决缺陷。
四、质量监控与度量SQE需要进行质量监控和度量,以评估软件产品的质量水平。
通过对测试结果和缺陷数据的分析,SQE可以发现软件产品中的问题,并提出改进措施。
质量监控和度量包括对软件产品的功能、性能、可靠性、安全性等方面进行评估。
SQE需要使用合适的工具和方法,采集和分析测试数据,生成相关的测试报告和指标。
sqe供应商质量管理工程师职责工作职责与职位要求【16篇】

sqe供应商质量管理工程师职责工作职责与职位要求【16篇】(经典版)编制人:__________________审核人:__________________审批人:__________________编制单位:__________________编制时间:____年____月____日序言下载提示:该文档是本店铺精心编制而成的,希望大家下载后,能够帮助大家解决实际问题。
文档下载后可定制修改,请根据实际需要进行调整和使用,谢谢!并且,本店铺为大家提供各种类型的经典范文,如工作报告、合同协议、心得体会、演讲致辞、规章制度、岗位职责、操作规程、计划书、祝福语、其他范文等等,想了解不同范文格式和写法,敬请关注!Download tips: This document is carefully compiled by this editor. I hope that after you download it, it can help you solve practical problems. The document can be customized and modified after downloading, please adjust and use it according to actual needs, thank you!Moreover, our store provides various types of classic sample texts, such as work reports, contract agreements, insights, speeches, rules and regulations, job responsibilities, operating procedures, plans, blessings, and other sample texts. If you want to learn about different sample formats and writing methods, please pay attention!sqe供应商质量管理工程师职责工作职责与职位要求【16篇】第1篇 sqe供应商质量管理工程师职责工作职责与职位要求职位描述:职责描述:1.参与新供应商开发与审核,与采购、技术部门一起对新供应商进行评定,确定其合格供方资格。
sqe岗位职责是什么
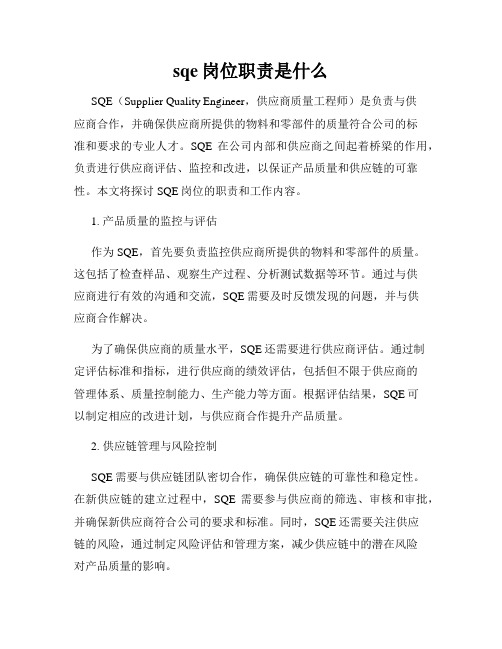
sqe岗位职责是什么SQE(Supplier Quality Engineer,供应商质量工程师)是负责与供应商合作,并确保供应商所提供的物料和零部件的质量符合公司的标准和要求的专业人才。
SQE在公司内部和供应商之间起着桥梁的作用,负责进行供应商评估、监控和改进,以保证产品质量和供应链的可靠性。
本文将探讨SQE岗位的职责和工作内容。
1. 产品质量的监控与评估作为SQE,首先要负责监控供应商所提供的物料和零部件的质量。
这包括了检查样品、观察生产过程、分析测试数据等环节。
通过与供应商进行有效的沟通和交流,SQE需要及时反馈发现的问题,并与供应商合作解决。
为了确保供应商的质量水平,SQE还需要进行供应商评估。
通过制定评估标准和指标,进行供应商的绩效评估,包括但不限于供应商的管理体系、质量控制能力、生产能力等方面。
根据评估结果,SQE可以制定相应的改进计划,与供应商合作提升产品质量。
2. 供应链管理与风险控制SQE需要与供应链团队密切合作,确保供应链的可靠性和稳定性。
在新供应链的建立过程中,SQE需要参与供应商的筛选、审核和审批,并确保新供应商符合公司的要求和标准。
同时,SQE还需要关注供应链的风险,通过制定风险评估和管理方案,减少供应链中的潜在风险对产品质量的影响。
3. 缺陷分析与质量改进SQE在工作中经常会接触到供应商提供的物料和零部件的质量问题。
在发现问题后,SQE需要进行缺陷分析,寻找问题的根源,并与供应商合作制定相应的质量改进计划。
这包括质量问题的调查、数据统计与分析、制定改进措施等。
SQE还需要对改进计划进行跟踪和监督,确保问题的解决和改进的有效性。
4. 技术支持与培训作为SQE,还需要为供应商提供技术支持与培训。
这包括了对供应商的生产工艺、质量控制方法和检测手段等进行指导和培训。
通过提升供应商的技术水平和质量意识,可以提高供应商的产品质量和供货能力,同时也有利于维护公司与供应商的长期合作关系。
SQE工程师日常工作职责
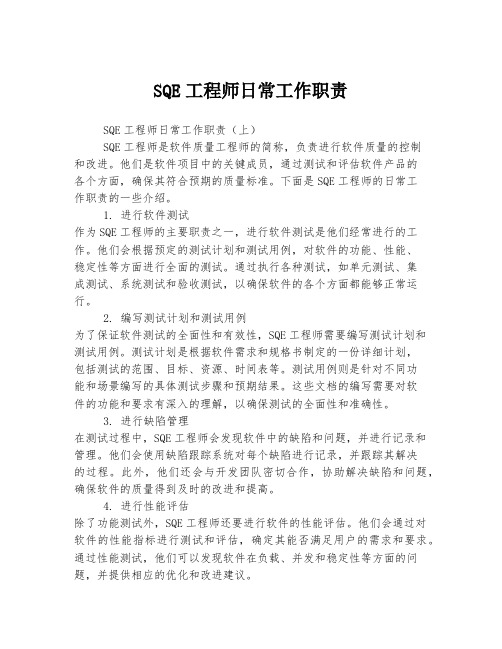
SQE工程师日常工作职责SQE工程师日常工作职责(上)SQE工程师是软件质量工程师的简称,负责进行软件质量的控制和改进。
他们是软件项目中的关键成员,通过测试和评估软件产品的各个方面,确保其符合预期的质量标准。
下面是SQE工程师的日常工作职责的一些介绍。
1. 进行软件测试作为SQE工程师的主要职责之一,进行软件测试是他们经常进行的工作。
他们会根据预定的测试计划和测试用例,对软件的功能、性能、稳定性等方面进行全面的测试。
通过执行各种测试,如单元测试、集成测试、系统测试和验收测试,以确保软件的各个方面都能够正常运行。
2. 编写测试计划和测试用例为了保证软件测试的全面性和有效性,SQE工程师需要编写测试计划和测试用例。
测试计划是根据软件需求和规格书制定的一份详细计划,包括测试的范围、目标、资源、时间表等。
测试用例则是针对不同功能和场景编写的具体测试步骤和预期结果。
这些文档的编写需要对软件的功能和要求有深入的理解,以确保测试的全面性和准确性。
3. 进行缺陷管理在测试过程中,SQE工程师会发现软件中的缺陷和问题,并进行记录和管理。
他们会使用缺陷跟踪系统对每个缺陷进行记录,并跟踪其解决的过程。
此外,他们还会与开发团队密切合作,协助解决缺陷和问题,确保软件的质量得到及时的改进和提高。
4. 进行性能评估除了功能测试外,SQE工程师还要进行软件的性能评估。
他们会通过对软件的性能指标进行测试和评估,确定其能否满足用户的需求和要求。
通过性能测试,他们可以发现软件在负载、并发和稳定性等方面的问题,并提供相应的优化和改进建议。
5. 提供质量保证建议作为软件质量专家,SQE工程师会根据对软件测试和评估的结果,提供质量保证的建议和方案。
他们会与开发团队和项目经理进行交流和讨论,就如何改进软件质量提出专业的意见。
通过他们的专业建议,可以从根本上提高软件的质量和可靠性。
SQE工程师是软件开发过程中不可或缺的一环,他们负责保证软件的质量和可靠性。
- 1、下载文档前请自行甄别文档内容的完整性,平台不提供额外的编辑、内容补充、找答案等附加服务。
- 2、"仅部分预览"的文档,不可在线预览部分如存在完整性等问题,可反馈申请退款(可完整预览的文档不适用该条件!)。
- 3、如文档侵犯您的权益,请联系客服反馈,我们会尽快为您处理(人工客服工作时间:9:00-18:30)。
SQE工程师日常工作职责
1. 来料材料确认:IQC反馈来料异常确认与判定;进料检验报告确认与处理,对于材料异常
及时联络供应商处理,并跟进处理结果;新材料确认(供应商变更或材料变更)。
2. 产线材料异常处理:及时地处理产线来料不良投诉 .必要时上线处理,并准确判定不良率
及责任归属(是否纯属IQC漏失),将IQC漏失记录于《生产线抱怨一览表》内,并针对不良问题点召集IQC进行检讨,制定改善措施并跟踪结果;客户材料异常确认分析,并执行改善及追踪;
及时确认材料异常处理结果(退货、特采、返工),若多少发现不良需敦促供应商进行检讨,给出有效的改善措施。
3. 巡查生产线:每日巡查产线物料不良状况(如轴心、碳片、LED等物料,依实际来料质量
状况作定义),并对来料不良的原因分析或保留样板交给供应商分析,并记录于《供应商
来料不良清单》中,整理后及时传供应商处;
4. IQC检验员素质提升:每日临督及稽核检验员作业状况(包括实际检验、报表填写、仪器操作、
处理事务等各方面状况),对检验方法及作业程序不正确的检验员进行教育培训(包括现场示范)并确认培训后检验员是否有改善;
5. 周、月总结及问题改善:每天晚上确认当天的生产线相关报表(如品质异常联络单、LQC
报表、维修报表,并针对主要不良物料进行追踪改善并在每周例会上汇报。
每周一前统计本周的问题点(物料不良、检验漏失、作业方法不正确等),并针对检验漏失分析原因,针对性地培训漏失最高的检验员,并提供改善方案;每月进行供应商月度评核、进料月统计
(合格率、退货率、特采、返工)特采单汇总进行提交;每月进料状况总结以及改善措施提交;6. 处理物料异常报告:确认各站别异常报告(LQC IPQG QA制程MRB •将确认属实的异常问题点写
SCAR于供应商.并追踪供应商的SCAR回复时间及正确性、合理性、有效性. 确认0K后通知IQC 重点跟踪及以便有效跟踪检验供应商来料的改善效果;
7. 协助处理物料异常问题:针对多次来料不良的供应商,切实了解不良状况及原因,并要求其供应
商来检讨;
8. 新数据的确认及讲解:当收到新资料或变更资料(包括内部制定及外部发行之相关品质资料.
如检验指导书、物料承认书等)先进行确认并召集相关人员进行讲解,以确保相关人员更好的掌握与熟悉新资料;样品的确认及检验重点的说明;
9. 新机种试产前的跟进:参加或追踪新机种相关会议(如试产前准备、试产总结会议等),
收集相关信息。
并将涉及IQC的问题进行宣导与培训;跟催新机种相关资料、样品及工夹具等;
新机种物料相关要求及注意事项讲解及确认;新机种总结会议相关问题的提出及相关内容的改善;
10. 供应商管理:每月会同采购、工程、PMC生产对供应商进料合格率、交货周期、服务、价格等进
行评价,对于不合格供应商发改善报告,要求供应商进行改善并回复措施;针对供应商的改善进行跟踪验证,未改善及时联络供应商处理;对供应商进行稽核;
11. 其它:协调与外部沟通,处理外部邮件、联络书、工程变更等
QE X程师日常工作职责
1. 参与新产品、新材料、新工艺、新变更等全过程验证和确认工作:
1.1导入时首先需协同工程人员向客户了解产品的管控重点。
1.2新产品试产期间各站别良率的统计及重大质量异常的分析与改善。
每个制程生产当天结束后将问题点整理,最晚第二天将问题点发出,并跟踪至结案!
注:(1)良率的统计时不良现象对应的不良率。
(2)检讨前将不良品按照ISSUEIist顺序
整理标示,便于检讨时看不良品检讨时看不良品(3)不良的问题描述时请务必清楚,拒绝
笼统的诸如:色差不良这样的描述。
色差的L,a,b标准是多少,实测多少?
1.3 相关信赖性测试报告的追踪、整理。
1.4 协助QS陪同客户稽核(包括厂内,供货商),以及缺失的改善与追踪。
1.5 试产各阶段FAI&CPK资料的整理并分析。
及时督促对应工程人员及时报验产品!
1.6 针对厂内制程无法改善达到客户标准的部分与客户检讨
1.7 新产品导入时相关检验方式的确认、治具的验证!
1.8 试产期间客户端标准要转换成厂内标准。
1.9 其它资料的整理(FMEA,FLOWCHAT产品材质证明,SGS报告,GR&F治具清单,制程参数等等其它所有客户要求的数据)
1.10制定在制品、成品SIP、QC工程表等,并监督其实施.产品设变后相关作业文件的更新!
2. 在新品量产之前向各站别QC及生产相关人员讲解品质管制重点及合理的检验方法等,第一次量
产时协助IPQC签首件。
2.1新品会议参加后必须将新机种的 PARTLIST以及产品的注意事项告知各站别 QC千万不可以自己去开会,开完了什么也不转告其它站别 QC.
2.2产品试模(从T1开始)时,务必从现场跟踪,了解产品的每一道工序以及每道工序的重点及难点,便于后续制作SIP时能掌握重点。
2.3产品外发时,与工程一同追踪产品的委外制程,要了解委外的工艺流程及常见的问题点、改善对策!
3. 对现场作业中不合理之处提出改善建议,并协助对生产中品质控制能力进行分析和改进。
3.1每天需定时,不定时去产线稽核,确认自己所负责的机种在管控之内:产线作业人员能按照SOP 乍业,机器制程参数符合SOP管控要求。
现场品保按照SIP规定的检验频率及检验重点检验产品。
4. 制程异常处理及改善与追踪。
4.1厂内制程有异常发生后,第一时间对异常进行确认(when,where, who, what,why, howmany):出现不良的站别,不良的具体现象,不良率,然后使用5M1E分析法对
不良进行分析然后根据不良的原因实施相应的改善对策。
然后时对策验证,标准化,最后为同类产品或者同类制程的展开--预防再发生;
5. 客户抱怨
5.1客户抱怨的来源有四个方面:①客户的邮件通知、②客户的电话通知、③客户端采购向本司业务抱怨,由业务端转达、④上级告知。
5.2接到以任何方式告知的异常之后:①首先要了解异常状况同样从5W1H^式确认异常一②
然后将此次的异常以邮件或电话方式告知所有站别品保以及产线,仓库(以及委外站别)—③接着尽一切可能配合客户所要求的应急处理方式一④然后召集工程、品保、业务、资材、生产等相关部门检讨不良原因(不良原因包括流出原因,表面原因以及根本原因)-⑤商讨出短期对策以及长期对策—⑥对策实施的验证—⑦标准化—⑧同类结构之产品、同制程预防再发生(需将质量异常以质量履历表形式以备后续各站别检验人员参考使用)—⑨追踪注:㈠针对异常处理部分若自己的经验无法准确无误的判定不良产生的原因,无法妥善处理异常,请及时向同事及上级汇报一汇报时务必准确客观,遵循5W2H g则!㈡处理客诉过程
中必须从头到尾完成跟踪动作,对于短期对策中的重工的产品客户端重工及厂内重工必须每日将重工进度告知厂内相关站别(业务、品保、工程、生管、生产)。
㈢对于自己或者代
其他QE处理异常,在客户端重工时,领料退料必须核对数量,单据务必保留,不良品的退货单须由CHI仓库人员签核,除非自己签核后可以将不良品带回交至CHI仓库.
5.3客诉确实为****责任的原则上均需回复异常改善报告(除部分刁难的客户,无法达到要求的产品)
5.4客诉处理后务必在品保部公共盘客诉统计里面将异常登记备忘。
6. 重大质量异常项目分析、改善、追踪,标准化。
6.1例如:2010年11月份年扬皓产品、恭硕 CPU支架的铆钉频繁发生断裂现象,QE就可以成立项目,从铆钉结构,铆钉材质,铆钉的铆接方式等各方面着手进行验证,从而获得经验值。
根据经验值制定相关标准文件,供后续各站别参考使用。
7. 品质数据的收集统计与分析
7.1公司内部所有产品各个站别的良率以及直通率(按照客户要求及时上传至客户网站)。
7.2客户端异常问题的汇总整理,分析。
8. 任何会议检讨必须有会议记录,参会人员必须在会议记录上签名,将会议记录以电子件形
式通知相关单位,开会后必须要追踪,各自案子自的会议记录必须要整理汇总!“会而必议,议而必决,决而必行,行而必果”
9. 自己所负责客户或者机种的数据
9.1 FAI&CPK格式
9.2检验规范
9.3信赖性测试标准
9.4 HSF标准及管控文件&HSF送测标准
9.5 QSA&QF稽核窗体
9.6客户出货包装标准
9.7客户出货检验报告的要求
9.8客户端联系方式汇总
10. 厂内各个部门的组成部分(通讯簿上的人基本上都要认识,并要知道是干什么的)
10.1生产部有几个课别,每一个课别所负责的工艺,对应的课长及副理是谁?各个生计所负责的制程。
10.2自己负责的客户及机种所对应的业务,工程及其主管是谁?
10.3资材部每一个采购所负责的外购料(包括原材料,外观件的塑件、电子件等辅材,内置件的麦拉),负责的外发工艺;及其主管是谁?各个生管所负责的料件?仓库各个库别的负责人及对应的主管是谁?
10.4管理部的采购,人事,总务是谁?司机的队长是谁?
10.5品保部各站别的的组长?品保部 SQE所负责厂商及机种、对应的代理人?
10.6公司的老板有哪些人,
11. 客户端年度稽核的陪同
12. 上级交办的各种任务。