精度等级4级精度加工工艺
精度等级4级精度加工工艺

精度等级4级精度加工工艺四级精度加工工艺是一种高精度的机械加工工艺,广泛应用于各个领域,尤其是精密仪器制造、航空航天、汽车制造等行业。
本文将从四个方面介绍四级精度加工工艺的特点、应用、发展和未来趋势。
一、四级精度加工工艺的特点四级精度加工工艺是一种高精度的机械加工工艺,其特点主要有以下几点:1.高精度:四级精度加工工艺能够实现非常高的精度要求,通常可以达到亚微米级别的精度。
这对于一些对尺寸精度要求极高的零件来说,是非常重要的。
2.高稳定性:四级精度加工工艺在加工过程中具有较高的稳定性,能够保证加工结果的稳定性和一致性。
这对于一些大规模生产的工件来说,是非常关键的。
3.高效率:虽然四级精度加工工艺的精度要求很高,但其加工效率并不低。
现代四级精度加工设备和工艺已经非常成熟,能够高效地完成加工任务。
4.多样性:四级精度加工工艺能够适应不同材料、不同形状和不同尺寸的工件加工需求。
无论是金属材料还是非金属材料,都可以通过四级精度加工工艺进行加工。
二、四级精度加工工艺的应用四级精度加工工艺被广泛应用于各个领域,主要包括以下几个方面:1.精密仪器制造:四级精度加工工艺在精密仪器制造领域应用广泛,可以用于加工各种精密仪器的零部件,如光学仪器、电子仪器等。
2.航空航天:航空航天领域对于零部件的精度要求非常高,四级精度加工工艺在航空航天领域有着重要的应用,可以用于加工飞机发动机、航天器零部件等。
3.汽车制造:汽车制造是一个大规模生产的行业,但同时也对零部件的精度要求很高。
四级精度加工工艺在汽车制造领域有着重要的应用,可以用于加工发动机零部件、底盘零部件等。
4.医疗器械:医疗器械对于精度要求非常高,特别是一些微创手术器械。
四级精度加工工艺可以用于加工各种医疗器械的零部件。
三、四级精度加工工艺的发展随着科技的进步和工艺的不断改进,四级精度加工工艺也在不断发展。
主要表现在以下几个方面:1.新材料的加工:随着新材料的不断发展,四级精度加工工艺也在适应新材料的加工需求。
滚珠丝杠精度等级

滚珠丝杠精度等级标准化管理处编码[BBX968T-XBB8968-NNJ668-MM9N]国内的等级精度分为P1,P2,P3,P4,P5,P7,P10这7个等级,JIS等级精度分为C0,C1,C3,C5,C7,C10这6种精度,各种螺杆长度之导程误差(单位为um)如下表所示:另外螺杆也有标示任意300mm长的精度 , 意即就是不论你的滚珠螺杆有多长 , 任取一段300mm内之的精度皆为规格中保证之精度以内,如下表所示:【机床定位精度要求与丝杠精度】的精度将直接影响数控机床各坐标轴的定位精度。
普通精度的数控机床,一般可选用D 级,精密级数控机床选用C级。
精度中的导程误差对机床定位精度影响最明显。
而丝杠在运转中由于温升引起的丝杠伸长,将直接影响机床的定位精度。
当L为丝杠螺纹有效长度时,L即为方向目标值T,在丝杠图纸上标示为负值。
用户在定购滚珠丝杠时,必须提出滚珠丝杠的方向目标值。
【提高传动的精度和刚度】主要是提高进给系统中传动零件的精度和支承刚度。
首先是保证各个零件的加工精度,尤其是提高滚珠丝杠螺母副(直线进给系统)、蜗杆副(圆周进给系统)的传动精度。
另外,在进给传动链中加人减速齿轮传动副,对滚珠丝杠和轴承进行预紧,消除齿轮、蜗杆等传动件的间隙,从而提高进给系统的精度和刚度。
对梯形丝杠的精度要求】1.螺旋线公差螺旋线误差是指在中径线上,实际螺旋线相对于理论螺旋线偏离的最大代数差。
又分为:(1)丝杠一转内螺旋线误差;(2)丝杠在指定长度上(25 mrn、100 mm或200 mm)的螺旋线误差:(3)丝杠全长的螺旋线误差。
螺旋线误差较全面地反映了丝杠的位移精度,但由于测量螺旋线误差的动态测量仪器尚未普及,国家标准中只对3、4、5、6级的丝杠规定了螺旋线公差。
2.螺距公差标准中规定了各级精度丝杠的螺距公差。
【丝杠的精度等级与公差】根据机械工业部颁布的JB2886–81《机床和螺母的精度》规定,及其螺母分为6个等级,即4、5、6、7、8和9级,4级精度最高,9级精度最低,适用情况如下:4级用于精度特别高的地方,如加工中心、螺纹磨床等。
镜片加工精度等级表
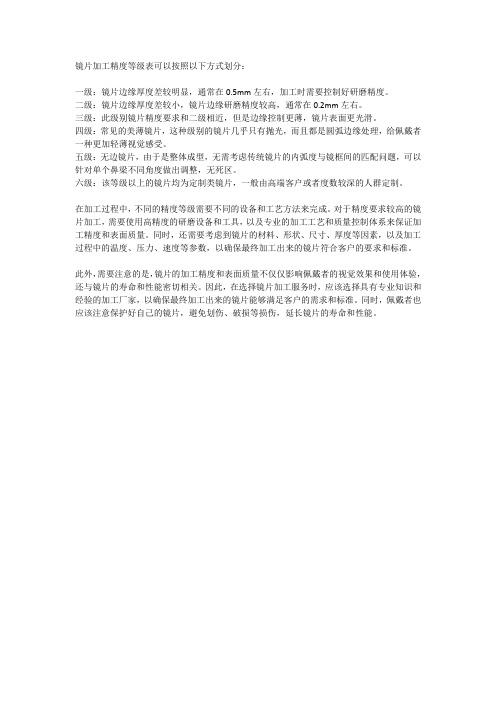
镜片加工精度等级表可以按照以下方式划分:
一级:镜片边缘厚度差较明显,通常在0.5mm左右,加工时需要控制好研磨精度。
二级:镜片边缘厚度差较小,镜片边缘研磨精度较高,通常在0.2mm左右。
三级:此级别镜片精度要求和二级相近,但是边缘控制更薄,镜片表面更光滑。
四级:常见的美薄镜片,这种级别的镜片几乎只有抛光,而且都是圆弧边缘处理,给佩戴者一种更加轻薄视觉感受。
五级:无边镜片,由于是整体成型,无需考虑传统镜片的内弧度与镜框间的匹配问题,可以针对单个鼻梁不同角度做出调整,无死区。
六级:该等级以上的镜片均为定制类镜片,一般由高端客户或者度数较深的人群定制。
在加工过程中,不同的精度等级需要不同的设备和工艺方法来完成。
对于精度要求较高的镜片加工,需要使用高精度的研磨设备和工具,以及专业的加工工艺和质量控制体系来保证加工精度和表面质量。
同时,还需要考虑到镜片的材料、形状、尺寸、厚度等因素,以及加工过程中的温度、压力、速度等参数,以确保最终加工出来的镜片符合客户的要求和标准。
此外,需要注意的是,镜片的加工精度和表面质量不仅仅影响佩戴者的视觉效果和使用体验,还与镜片的寿命和性能密切相关。
因此,在选择镜片加工服务时,应该选择具有专业知识和经验的加工厂家,以确保最终加工出来的镜片能够满足客户的需求和标准。
同时,佩戴者也应该注意保护好自己的镜片,避免划伤、破损等损伤,延长镜片的寿命和性能。
滚珠丝杠精度等级

滚珠丝杠精度等级Pleasure Group Office【T985AB-B866SYT-B182C-BS682T-STT18】国内的等级精度分为P1,P2,P3,P4,P5,P7,P10这7个等级,JIS等级精度分为C0,C1,C3,C5,C7,C10这6种精度,各种螺杆长度之导程误差(单位为um)如下表所示:另外螺杆也有标示任意300mm长的精度 , 意即就是不论你的滚珠螺杆有多长 , 任取一段300mm内之的精度皆为规格中保证之精度以内,如下表所示:【机床定位精度要求与丝杠精度】的精度将直接影响数控机床各坐标轴的定位精度。
普通精度的数控机床,一般可选用D级,精密级数控机床选用C级。
精度中的导程误差对机床定位精度影响最明显。
而丝杠在运转中由于温升引起的丝杠伸长,将直接影响机床的定位精度。
当L为丝杠螺纹有效长度时,L即为方向目标值T,在丝杠图纸上标示为负值。
用户在定购滚珠丝杠时,必须提出滚珠丝杠的方向目标值。
【提高传动的精度和刚度】主要是提高进给系统中传动零件的精度和支承刚度。
首先是保证各个零件的加工精度,尤其是提高滚珠丝杠螺母副(直线进给系统)、蜗杆副(圆周进给系统)的传动精度。
另外,在进给传动链中加人减速齿轮传动副,对滚珠丝杠和轴承进行预紧,消除齿轮、蜗杆等传动件的间隙,从而提高进给系统的精度和刚度。
对梯形丝杠的精度要求】1.螺旋线公差螺旋线误差是指在中径线上,实际螺旋线相对于理论螺旋线偏离的最大代数差。
又分为:(1)丝杠一转内螺旋线误差;(2)丝杠在指定长度上(25 mrn、100 mm或200 mm)的螺旋线误差:(3)丝杠全长的螺旋线误差。
螺旋线误差较全面地反映了丝杠的位移精度,但由于测量螺旋线误差的动态测量仪器尚未普及,国家标准中只对3、4、5、6级的丝杠规定了螺旋线公差。
2.螺距公差标准中规定了各级精度丝杠的螺距公差。
【丝杠的精度等级与公差】根据机械工业部颁布的JB2886–81《机床和螺母的精度》规定,及其螺母分为6个等级,即4、5、6、7、8和9级,4级精度最高,9级精度最低,适用情况如下:4级用于精度特别高的地方,如加工中心、螺纹磨床等。
齿轮常用的精度等级
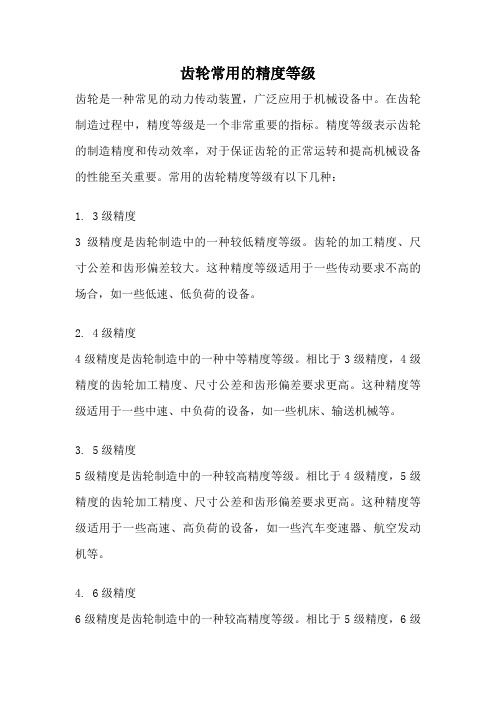
齿轮常用的精度等级齿轮是一种常见的动力传动装置,广泛应用于机械设备中。
在齿轮制造过程中,精度等级是一个非常重要的指标。
精度等级表示齿轮的制造精度和传动效率,对于保证齿轮的正常运转和提高机械设备的性能至关重要。
常用的齿轮精度等级有以下几种:1. 3级精度3级精度是齿轮制造中的一种较低精度等级。
齿轮的加工精度、尺寸公差和齿形偏差较大。
这种精度等级适用于一些传动要求不高的场合,如一些低速、低负荷的设备。
2. 4级精度4级精度是齿轮制造中的一种中等精度等级。
相比于3级精度,4级精度的齿轮加工精度、尺寸公差和齿形偏差要求更高。
这种精度等级适用于一些中速、中负荷的设备,如一些机床、输送机械等。
3. 5级精度5级精度是齿轮制造中的一种较高精度等级。
相比于4级精度,5级精度的齿轮加工精度、尺寸公差和齿形偏差要求更高。
这种精度等级适用于一些高速、高负荷的设备,如一些汽车变速器、航空发动机等。
4. 6级精度6级精度是齿轮制造中的一种较高精度等级。
相比于5级精度,6级精度的齿轮加工精度、尺寸公差和齿形偏差要求更高。
这种精度等级适用于一些对传动效率和噪声要求极高的设备,如一些高速电机、精密仪器等。
在齿轮制造过程中,要保证齿轮的精度等级,需要注意以下几点:1. 材料选择齿轮的材料选择对于保证其精度等级至关重要。
应选择具有良好机械性能和热处理性能的材料,如优质合金钢等。
2. 设备选择齿轮的加工设备也是影响其精度等级的重要因素。
应选择具备高精度的齿轮加工设备,如数控齿轮磨床、数控齿轮滚齿机等。
3. 加工工艺齿轮的加工工艺也是影响其精度等级的关键因素。
应采用合理的加工工艺,如精密滚刀、精密磨齿等,以保证齿轮的加工精度。
4. 检测手段齿轮的精度等级需要通过检测手段进行验证。
常用的检测手段包括齿轮测量仪、轮廓仪等。
通过这些手段可以对齿轮的尺寸公差、齿形偏差等进行精确测量,以保证其精度等级。
齿轮的精度等级是保证其正常运转和提高机械设备性能的重要指标。
圆弧齿轮精度等级的选用
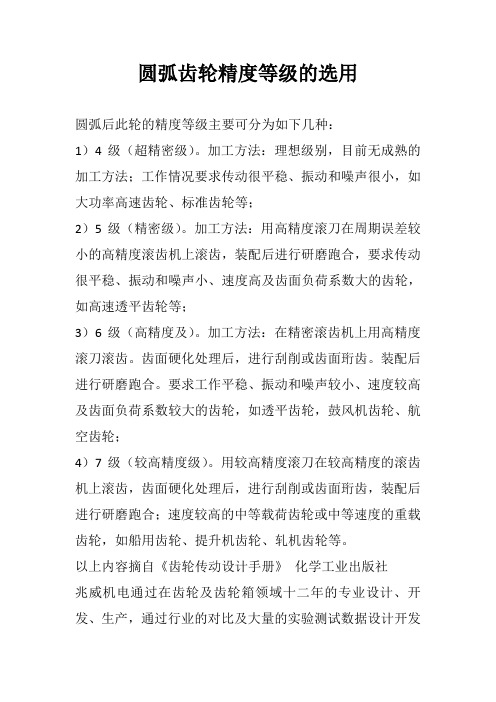
圆弧齿轮精度等级的选用
圆弧后此轮的精度等级主要可分为如下几种:
1)4级(超精密级)。
加工方法:理想级别,目前无成熟的加工方法;工作情况要求传动很平稳、振动和噪声很小,如大功率高速齿轮、标准齿轮等;
2)5级(精密级)。
加工方法:用高精度滚刀在周期误差较小的高精度滚齿机上滚齿,装配后进行研磨跑合,要求传动很平稳、振动和噪声小、速度高及齿面负荷系数大的齿轮,如高速透平齿轮等;
3)6级(高精度及)。
加工方法:在精密滚齿机上用高精度滚刀滚齿。
齿面硬化处理后,进行刮削或齿面珩齿。
装配后进行研磨跑合。
要求工作平稳、振动和噪声较小、速度较高及齿面负荷系数较大的齿轮,如透平齿轮,鼓风机齿轮、航空齿轮;
4)7级(较高精度级)。
用较高精度滚刀在较高精度的滚齿机上滚齿,齿面硬化处理后,进行刮削或齿面珩齿,装配后进行研磨跑合;速度较高的中等载荷齿轮或中等速度的重载齿轮,如船用齿轮、提升机齿轮、轧机齿轮等。
以上内容摘自《齿轮传动设计手册》化学工业出版社
兆威机电通过在齿轮及齿轮箱领域十二年的专业设计、开发、生产,通过行业的对比及大量的实验测试数据设计开发
出微型减速电机,直流行星减速电机,齿轮箱电机,齿轮箱马达。
轴的精度等级一览表

轴的精度等级一览表轴承的精度等级标准为,0级、6X级、6级、5级、4级、2级六个等级。
轴承精度从0级起依次提高,对于一般用途来说0级已经足够满足需求,但在用于一些要求高精度条件或场合时,需要5级或更高的精度。
精度等级虽然是以ISO标准为基准制定的,但那仅限于国内。
相对于国外,各国的对产品的叫法和衡量标准是不一样的。
轴承的公差等级主要根据轴对支撑的旋转精度要求来确定的。
0级:在旋转精度大于10um的一般轴承系中,应用十分广泛。
如普通机床的变速机构、进给机构、汽车、拖拉机的变速机构,普通电机、水泵及农业机械等一般通用机械的旋转机构中。
4、2级:在旋转精度小于5um或转速很高的超精密仪器中,例如精密坐标镗床,精密磨床的齿轮系统,精密仪器、仪表以及高速摄像机的等精密系统。
6、5级:在旋转精度在5-10um或转速较高的精密轴承系中,如普通车床所用轴承(前支撑用5级,后支撑用6级)较精密的仪器、仪表以及精密仪器、仪表,和精密的旋转机构。
精度标准说明各国的制定的标准都是依据ISO标准制定,一般都是和ISO一致,个别严格于ISO标准。
精度分为尺寸精度和旋转精度。
分为0级、6X级、6级、5级、4级、2级。
国轴承以前旧代号标准是G级(0级)、E级(6级)、D级(5级)、C级(4级)、B级(2级)。
现行代号一般采用德国DIN标准。
PO级(0级)、P6级(6级)、P5级(5级)、P4级(4级)、P2级(2级)。
一般标准等级PO级,反应在轴承型号上是省略的,只有P6级或P6级以上的,等级代号才出现在轴承型号当中.例如:6205和6205/P5,其中6205的精度等级是PO级,只不过是省略了。
这就给人们造成了,PO级是非精度等级轴承的印象。
另外,各种精度的轴承除了区别在加工工艺上,也区别在价值上。
例如:国内轴承的价值,P6级精度的轴承是PO级的1.5倍,P5精度的轴承是PO的2倍,P4精度的是P5精度的2.5倍。
一个好的轴承最重要的就是用在适合的地方,轴承适合的地方,就要有精度等级来划分。
钻孔工艺精度标准
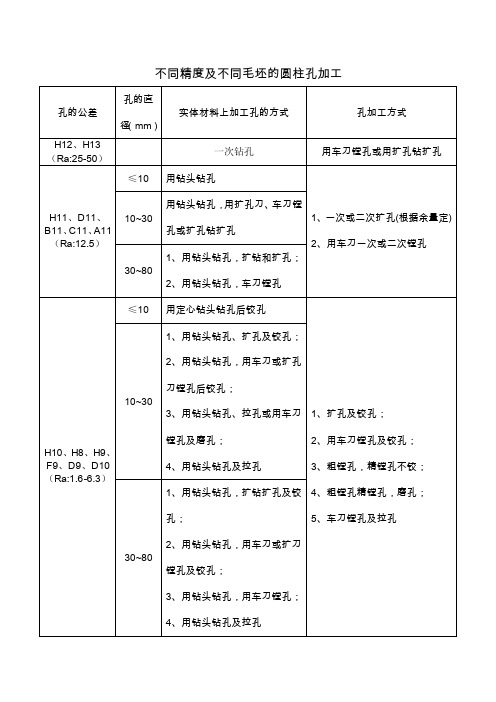
不同精度及不同毛坯的圆柱孔加工例:孔Φ25(0,+0.033),孔公差H8,麻花钻至孔Φ24.8,铰孔至Φ25(0,+0.033)孔Φ35(0,+0.062),孔公差H7,麻花钻Φ34.8,铰孔至Φ35(0,+0.062)Φ8(0,+0.018),孔公差约H7-H8,中心钻定位,麻花钻至Φ6,粗镗至Φ7.5,精镗至Φ8(0,+0.018)1、钻削直径较大的孔(大于30mm)时,不宜用大钻头一次钻出,最好分多次钻削,即先用直径较小的钻头钻孔,再用较大直径钻头扩到所要求的尺寸。
基孔制选作基准的孔称为基准孔,基准孔代号H(下偏差值0,上偏差值正值)基轴制选作基准的轴称为基准轴,基准轴代号h(上偏差值0,下偏差值负数)外圆面加工1.粗车:主要作为外圆的预加工,除淬硬钢以外,各种零件的加工都适用。
当零件的外圆要求精度低、表面粗糙度较大时,只粗车即可。
2.粗车-半精车:用于各类零件上不重要的表面或非配合表面。
3.粗车-半精车-精车:精度更高4.粗车-半精车-磨削:用于加工精度稍高、粗糙度值较小、且淬硬的钢件外圆面,也可广泛地用于加工未淬硬的钢件或铸铁件。
平面加工方法未注公差等级GB/T1804-2000公差等级约IT10-IT14之间下面是赠送的励志的100句经典话,需要的朋友可以学习下,不需要的朋友可以下载后编辑删除!!谢谢!!【励志的话】平凡却无私的人啊千万不要抱怨命运的不公。
也许,命运只是用另一种方式偏爱着你那是因为善良的她想让你尽快长大感知人间悲喜,聆听世间哀乐。
虽然有时跌倒,有时失败但请记住跌倒不是失败,失败不是否定。
平凡却无私的人啊千万不要抱怨命运的不公也许,命运只是用透明的方式倾向与你那是因为,慈爱的她想让你尽早成熟看尽人间繁华,尝便世间甘苦。
虽然有时哭泣,有时逃避但请记住哭泣不是永久逃避不是永恒平凡却无私的人啊千万不要抱怨命运的不公也许,命运只是施舍于被它偏爱的人那是因为严厉的她不想让你溺爱长大,感受人们欢呼,享受世界鼓舞虽然有时悲愤,有时无助。
加工精度公差等级标准

加工精度公差等级标准# 加工精度公差等级标准## 一、前言嘿,朋友们!在现代工业的大舞台上,加工精度那可是相当重要的角色呢。
就好比我们搭积木,每个小积木块的尺寸精确程度都会影响到整个积木大厦的稳固和美观。
在机械制造、电子设备生产等众多领域,加工精度公差等级标准就像是一把神奇的尺子,它衡量着零件加工的精确程度,确保各个零件能够完美地配合在一起,就像拼图一样严丝合缝。
这个标准可是工业生产的“交通规则”,大家都遵守它,生产出来的产品质量才有保障,咱们今天就来好好唠唠这个加工精度公差等级标准。
## 二、适用范围1. 机械制造领域- 在汽车制造中,发动机里的各种零件,像活塞、曲轴等,它们的加工精度必须要符合公差等级标准。
比如说活塞的直径,如果加工精度不够,活塞和气缸壁之间的间隙就可能不合适。
间隙太大,发动机动力会下降,还可能烧机油;间隙太小呢,活塞就容易卡死在气缸里,整个发动机就报废了。
你可以想象一下,这就好比你的鞋子太大或者太小,走路都会很不舒服,甚至走不了路。
- 机床制造也离不开这个标准。
机床的各个部件,如导轨、丝杆等,其加工精度直接影响到机床的加工精度。
如果导轨的直线度公差等级不达标,加工出来的零件就可能是歪的,就像在弯弯曲曲的路上开车,车子肯定跑不直。
2. 电子设备生产领域- 在手机制造中,电路板上的各种芯片、电容、电阻等元件的安装位置精度是有要求的。
如果某个元件的安装孔位置公差太大,元件就可能安装不上,或者安装后接触不良。
这就好比你给手机充电,插头插不进充电口或者插进去了但是充电断断续续,多让人头疼啊。
- 电脑硬盘的磁头和盘片之间的间隙也需要精确控制,这就需要遵循加工精度公差等级标准。
如果间隙不符合标准,要么磁头容易划伤盘片,导致数据丢失;要么读写数据的效率低下,电脑运行就会变得很慢。
3. 模具制造领域- 制造注塑模具时,模具型腔的尺寸精度至关重要。
如果型腔尺寸的公差太大,注塑出来的塑料制品就会尺寸不合格,可能会出现装配不上的情况。
滚珠丝杠精度等级
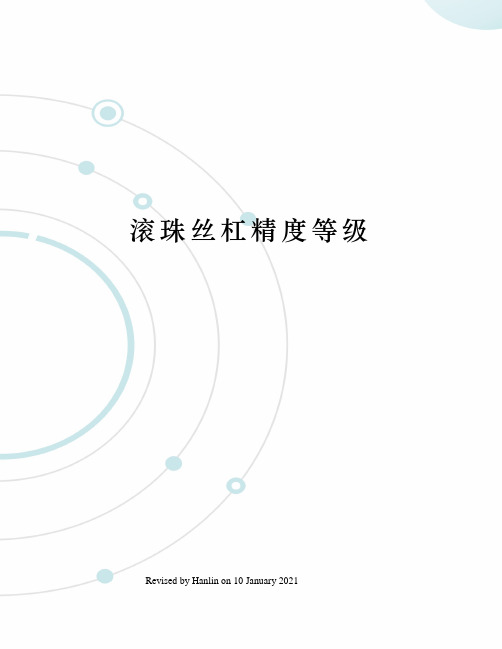
滚珠丝杠精度等级 Revised by Hanlin on 10 January 2021国内的等级精度分为P1,P2,P3,P4,P5,P7,P10这7个等级,JIS等级精度分为C0,C1,C3,C5,C7,C10这6种精度,各种螺杆长度之导程误差(单位为um)如下表所示:另外螺杆也有标示任意300mm长的精度 , 意即就是不论你的滚珠螺杆有多长 , 任取一段300mm内之的精度皆为规格中保证之精度以内,如下表所示:【机床定位精度要求与丝杠精度】的精度将直接影响数控机床各坐标轴的定位精度。
普通精度的数控机床,一般可选用D级,精密级数控机床选用C级。
精度中的导程误差对机床定位精度影响最明显。
而丝杠在运转中由于温升引起的丝杠伸长,将直接影响机床的定位精度。
当L为丝杠螺纹有效长度时,L即为方向目标值T,在丝杠图纸上标示为负值。
用户在定购滚珠丝杠时,必须提出滚珠丝杠的方向目标值。
【提高传动的精度和刚度】主要是提高进给系统中传动零件的精度和支承刚度。
首先是保证各个零件的加工精度,尤其是提高滚珠丝杠螺母副(直线进给系统)、蜗杆副(圆周进给系统)的传动精度。
另外,在进给传动链中加人减速齿轮传动副,对滚珠丝杠和轴承进行预紧,消除齿轮、蜗杆等传动件的间隙,从而提高进给系统的精度和刚度。
对梯形丝杠的精度要求】1.螺旋线公差螺旋线误差是指在中径线上,实际螺旋线相对于理论螺旋线偏离的最大代数差。
又分为: (1)丝杠一转内螺旋线误差; (2)丝杠在指定长度上(25 mrn、100 mm或200 mm)的螺旋线误差: (3)丝杠全长的螺旋线误差。
螺旋线误差较全面地反映了丝杠的位移精度,但由于测量螺旋线误差的动态测量仪器尚未普及,国家标准中只对3、4、5、6级的丝杠规定了螺旋线公差。
2.螺距公差标准中规定了各级精度丝杠的螺距公差。
【丝杠的精度等级与公差】根据机械工业部颁布的JB2886–81《机床和螺母的精度》规定,及其螺母分为6个等级,即4、5、6、7、8和9级,4级精度最高,9级精度最低,适用情况如下:4级用于精度特别高的地方,如加工中心、螺纹磨床等。
车工_4级_鉴定要素细目表

《车工》(四级)理论知识鉴定要素细目表职业(工种)名称职业代码车工 等级四级鉴定点代码序号章节目点鉴定点名称分数系数重要系数备注 1 基础知识50 11 机械制图10 111 机械制图的基本常识4 11111制图基础知识0.55 21112投影知识0.55 31113视图的形成极其相应的关系0.59 41114点、直线、平面的投影关系0.55 51115零件的测绘方法0.59 61116零件的尺寸标注0.59 71117标准件画法0.55 81118螺纹连接的画法0.59 91119螺纹的规定画法和代号标注方法0.55 1011110键与销的规定画法和代号标注方法0.59 1111111齿轮的规定画法0.55 1211112滚动轴承的规定画法和代号标注方法0.59 1311113零件表达方法0.59 112 公差与配合4 141121形位公差的基础知识0.59 151122形位公差的标注方法0.55 161123表面粗糙度的基础知识0.59 171124表面粗糙度的标注方法0.55 181125零件图的组成0.55 191126装配图识读0.55 201127配合的种类0.59 211128配合的特性0.59 221129公差与偏差的区别0.59 2311210机械加工精度等级0.59 2411211基孔制和基轴制0.59 2511212公差与配合的选用0.59 2611213公差与配合的基本规定0.55 113 形位公差与表面粗糙度2 271131形位公差符号表示方法0.59 281132形位公差的代号0.59 291133形位公差的项目特征0.59 301134形位公差的选用0.59 311135形位公差的标注方法0.59 321136表面粗糙度0.59 321137表面粗糙度的概念0.59 331138表面粗糙度的分类0.59 341139表面粗糙度的选用0.59 3511310表面粗糙度标注方法0.59 3611311互换性概念0.55 12 常用量具的结构和使用2 121 常用量具2 371211测量技术0.59 381212测量与测量工具0.55 391213车工常用测量工、量器具0.59 401214常见零件的几种测量方法0.55 411215形状、位置误差的测量0.59 421216表面粗糙度的测量0.55 431217百分表的结构和使用方法0.59 4412182′万能角度尺的结构和使用方法0.59 451219常用量具的维护和保养知识0.59 13 机械制造工艺5 131 机械制造工艺基本概念5 461311机械制造工艺基本概念0.59 471312机械工艺过程0.55 481313工艺尺寸链0.59 491314简单尺寸链的基础知识计算0.55 501315工件的装夹0.59 511316加工工艺过程0.59 521317机械加工工艺过程的组成0.59 531318生产类型的工艺特征0.55 541319工艺流程的确定0.55 5513110工艺系统0.51 5613111机械加工精度0.59 5713112工艺规程的基本要求0.55 5813113加工精度和表面质量0.59 14 切削原理和刀具16 141 刀具的概念2 591411金属切削原理及刀具0.59 601412常用刀具材料及用途0.59 611413刀具材料的基本要求0.59 621414刀具材料应具备的性能0.59 631415刀具材料的种类0.59 641416刀具切削部分材料的基本要求0.59 651417刀具切削部分的几何参数0.59 142 刀具的角度5 661421车刀的种类0.59 671422车刀的选择0.59 681423刀具切削部分的几何参数0.59 691424刀具的工作角度0.59 701425刀具的工作角度选择0.59 711426车刀六个基本角度的选择原则0.59 721427前角的选择0.55 731428后角的选择0.55 741429主、副偏角的选择0.55 7514210刃倾角选择0.55 7614211负倒棱的作用及选择0.55 7714212车刀装夹高低对前后角的影响0.59 143 麻花钻的结构2 781431麻花钻的特点0.59 791432钻头的结构和几何参数0.55 801433麻花钻的组成部分0.55 811434麻花钻工作部分的几何参数0.59 821435麻花钻的安装方法0.55 831436麻花钻的切削用量和切削液0.55 841437麻花钻的修磨方法0.59 851438硬质合金可转位刀具的特点0.55 861439机夹刀具使用注意事项0.55 144 金属切削原理6 871441金属切削原理0.59 881442金属切削过程要求0.59 891443金属切削过程0.59 901444切削力各分力的意义0.59 911445车削加工所具备的运动0.59 921446车削工件形成的三个表面0.59 931447切削加工0.55 941448切削液的分类、作用及选用0.55 951449切削用量三要素的定义与计算0.55 9614410粗加工切削用量的选择0.59 9714411精加工切削用量的选择0.59 9814412切削用量的选择0.59 9914413切削热0.55 10014414切削力及影响切削力的因素0.59 10114415切削热及切削热对切削过程的影响0.59 10214416扩孔与车孔的区别0.59 10314417车削加工精度0.55 10414418刀具磨损形式0.59 10514419刀具磨钝标准0.59 10614420影响刀具寿命的因素0.59 10714421影响工件表面粗糙度值的因素0.59 10814422减小工件表面粗糙度值的方法0.59 10914423加工表面质量0.59 145 其他切削知识1 1101451数控机床0.55 1111452磨削的基础知识0.55 1121453砂轮的选用0.59 1131454砂轮的种类选择0.59 1141455机械加工精度0.55 15 电工学2 151 电工常识2 1151511电动机的种类0.55 1161512常用低压电器的名称0.55 1171513工作原理和作用0.59 1181514机床上有那些常用的电器装置0.55 1191515熔断器的种类0.59 1201516继电器的种类0.55 1211517热继电器的种类0.55 1221518安全用电的常识0.59 1231519触电急救知识0.59 16 机械传动知识5 161 机械传动知识2 1241611机器、机构和运动副概念及定义0.59 1251612带传动的工作原理和传动特点0.59 1261613螺旋传动的工作原理和传动特点0.59 1271614链传动的工作原理和传动特点0.59 1281615齿轮传动的工作原理和传动特点0.59 1291616传动比的概念和计算方法0.59 1301617直齿圆柱齿轮的几何尺寸计算0.55 162 气压传动知识1 1311621气压传动的工作原理0.59 1321622气压传动的组成0.55 1331623气缸的种类0.55 1341624气压马达0.51 1351625方向控制阀的工作原理0.55 1361626方向控制阀的种类0.55 1371627压力控制阀的工作原理0.55 1381628流量控制阀的工作原理0.55 1391629流量控制阀的种类0.55 14016210减压阀0.51 14116211安全阀0.51 163 液压传动2 1421631液压传动基础知识0.59 1431632液压传动的基本概念0.59 1441633液压传动中流量、压力的概念0.59 1451634液压传动的压力流量损失0.59 1461635液压传动0.59 1471636液压传动元件0.55 1481637常用液压油0.59 1491638液压传动辅件0.59 1501639液压回路0.59 15116310液压系统的维护0.55 17 金属材料与热处理一般知识10 171 金属材料的性能2 1521711金属材料的物理性能和力学性能0.59 1531712碳素钢的种类、牌号及力学性能0.59 1541713合金钢的种类、牌号及力学性能0.59 1551714铸铁的种类、牌号及力学性能0.59 1561715常用有色金属的种类、牌号0.55 172 热处理的常识8 1571721退火目的0.59 1581722淬火目的0.59 1591723常用淬火方法0.59 1601724回火的种类0.59 1611725回火的应用0.59 1621726回火定义概念0.59 1631727钢的退火种类及其目的0.59 1641728钢的正火和淬火的目的0.59 1651729钢的回火种类及其目的0.59 16617210钢的调质处理0.59 16717211表面淬火的种类0.59 16817212表面淬火的应用0.59 16917213钢的化学热处理概念0.59 17017214渗碳目的0.55 17117215渗碳后的热处理0.55 17217216渗碳用钢的成分0.55 17317217碳氮共渗的概念0.55 17417218渗碳用钢的特点0.55 17517219其他表面处理技术应用0.55 17617220钢的表面淬火的种类及特点0.55 17717221钢的表面热处理种类及特点0.55 2 专业知识45 21 车削原理23 211 车削加工的基本概念7 1782111切削方式0.59 1792112切削层参数0.59 1802113车削过程0.59 1812114积屑瘤对工件表面粗糙度的影响0.59 1822115积屑瘤对切削加工的影响0.59 1832116减少积屑瘤产生的措施0.59 1842117加工表面硬化0.59 1852118特种金属材料与非金属材料的车削0.55 1862119车削时各分力的实用意义0.59 18721110影响切削力的因素0.59 18821111切削热的来源、传散0.59 18921112影响切削温度的因素0.59 19021113切削温度测定原理0.59 19121114选择切削用量的一般原则0.59 19221115影响工件表面粗糙度的因素0.59 19321116减小工件表面粗糙度的方法0.59 19421117工件表面的加工质量0.59 212 车削的基本内容8 1952121零件的外圆车削加工0.55 1962122零件的镗孔加工0.55 1972123圆锥面应用0.59 1982124圆锥面基本概念0.59 1992125标准圆锥的种类0.55 2002126圆锥各部分的计算0.55 2012127圆锥面的车削方法0.55 2022128斜度和锥度的计算方法0.59 2032129圆锥孔车削方法0.59 20421210尾座偏移量的计算0.55 20521211铰内圆锥的方法0.55 20621212车圆锥产生双曲线的原因0.55 20721213圆锥的精度与检验方法0.59 20821214成形面的车削方法0.55 20921215螺纹名称解释0.55 21021216三角螺纹主要尺寸计算0.59 21121217三角螺纹车刀的选择应用0.59 21221218三角螺纹的加工方法0.59 21321219三角螺车削产生废品原因及预防方法0.59 21421220用板牙和丝锥切削螺纹0.55 213 梯形螺纹车削2 2152131螺纹名称解释0.55 2162132梯形螺纹主要尺寸计算0.59 2172133梯形螺纹车刀的选择应用0.59 2182134梯形螺纹的加工方法0.59 2192135梯形螺纹的测量0.59 214 蜗杆车削6 2202141蜗杆的用途和分类0.55 2212142蜗杆的主要参数及计算0.59 2222143蜗杆车刀和装夹方法0.59 2232144螺纹升角对车刀工作角度的影响0.55 2242145车刀前角对牙型角的影响0.55 2252146蜗杆车削方法0.59 2262147多线螺纹的概念0.59 2272148多线螺纹的尺寸计算0.59 2282149多线螺纹的分线方法0.59 22921410多线螺纹的车削步骤0.59 23021411多线螺纹的测量方法0.59 23121412正确判断乱扣螺纹0.59 23221413车螺纹的挂轮计算0.55 22 机床夹具与定位10 221 定位基准的选择4 2332211基准选择0.59 2342212工件六点定位原理0.59 2352213完全定位的应用0.59 2362214不完全定位的应用0.59 2372215重复定位的应用0.55 2382216欠定位的分析0.55 2392217工件的定位装置0.59 2402218工件的定位误差0.59 2412219工件的定位和装夹知识0.59 24222110轴类零件定位基准的选择0.59 24322111套类零件定位基准的选择0.59 222 夹具的概念及作用6 2442221夹紧力的三要素0.59 2452222夹紧力大小与作用点0.59 2462223夹紧装置的基本要求0.59 2472224夹紧机构0.59 2482225软卡爪的正确使用0.59 2492226常用两种心轴的特点0.59 2502227保证套类零件同轴度和垂直度的方法0.59 2512228机床夹具的概念0.59 2522229机床夹具的组成0.59 25322210机床夹具的作用0.59 25422211夹具的组成0.59 25522212组合夹具0.55 25622213自动定心夹紧机构0.55 25722214车床夹具设计0.55 23 复杂工件的装夹和车削6 231 在花盘上加工复杂零件1 2582311在花盘上装夹工件和校正方法0.59 2592312在花盘角铁上装夹工件和校正方法0.59 2602313在花盘角铁上保证工件形位公差的方法0.59 232 偏心工件车削2 2612321偏心工件概念0.59 2622322偏心工件的车削方法0.59 2632323用三爪卡盘车偏心的垫块计算0.59 2642324测量偏心距的方法0.59 233 其他复杂零件的加工3 2652331防止和减少薄壁工件变形的方法0.59 2662332细长轴车削特点0.59 2672333中心架、跟刀架的使用0.59 2682334加工细长轴容易出现的问题0.55 2692335解决细长轴加工问题的措施0.59 2702336深孔加工的关键技术问题0.55 2712337深孔加工的排屑方式0.55 24 CA614型卧式车床6 241 车床的传动系统3 2722411机床型号的含义0.59 2732412CA614型卧式车床主要技术参数0.55 2742413车床主轴传动系统0.59 2752414进给箱传动系统0.59 2762415车米制螺纹和米制蜗杆传动路线0.55 2772416车扩大、非标准和精密螺纹传动路线0.59 2782417溜板箱传动路线0.51 242 车床的结构及作用3 2792421双向多片式摩擦离合器的作用及调整0.55 2802422制动装置的作用及调整0.55 2812423超越离合器的作用0.55 2822424安全离合器的作用0.59 2832425互锁机构的作用0.59 2842426开合螺母的作用0.59 2852427中滑板丝杠螺母的间隙调整0.59 2862428立式车床的特点0.55 3 相关知识5 31 机床操作规程及安全文明生产2 311 机床操作规程1 2873111金属切削机床的润滑0.59 2883112金属切削机床的维护保养0.55 2893113金属切削机床的操作注意事项0.55 312 安全生产文明生产知识1 2903121车工安全知识0.59 2913122机械设备安全技术0.59 2923123消防知识0.55 2933124一般起吊安全知识0.51 2943125文明生产知识0.59 32 相关机加工基础知识2 321 磨削基础知识1 2953211磨削的特点0.59 2963212内外圆磨削基础知识0.59 2973213平面磨削形式0.55 2983214光整加工基础知识0.51 322 其他机加工1 2993221铣削加工基础知识0.59 3003222刨插加工基础知识0.55 3013223镗削加工基础知识0.59 33 生产技术管理1 331 生产技术管理的内容1 3023311企业生产准备和组织0.55 3033312全面质量管理基础知识0.55 3043313生产技术管理基础内容0.55 3053314设备工具管理基础知识0.55 3063315生产过程,工艺过程,工艺规程0.59 《车工》(四级)操作技能鉴定要素细目表职业(工种)名称车工职业代码等级四级序号项目鉴定要求重要系数备注1)正确刃磨外圆车刀的几何角度52)合理选择切削用量5 1车外圆3)外圆尺寸公差达到IT7级~IT8级,表面粗糙度Ra1.691)掌握工件十字孔的找正和装夹92)合理选择切削用量5 2车内孔3)内孔尺寸公差达到IT8级~IT9级,表面粗糙度Ra1.691)正确刃磨割槽刀的几何角度5 3割槽2)掌握槽尺寸控制和测量,尺寸公差达到IT9级,表面粗糙度Ra3.251)正确刃磨三角螺纹车刀和装夹52)掌握车三角螺纹的方法5 4车内三角螺纹3)螺纹尺寸精度达到6级,表面粗糙度Ra3.291)正确刃磨梯形螺纹车刀和装夹52)掌握多线螺纹挂轮调整和车削方法53)正确运用多线螺纹的分线方法54)掌握三针测量螺纹的方法5 5车多线梯形螺纹5)梯形螺纹尺寸公差达到8级,螺纹表面粗糙度Ra3.291)车圆锥面对车刀的安装要求52)掌握圆锥面的车削方法和测量5 6车外圆锥体3)正确判断圆锥角度大小及调整, 圆锥接触面>6%,表面粗糙度Ra1.697车偏心掌握工件偏心距的找正和装夹,达到偏心距偏差±.498形位公差要求掌握达到形位公差要求的方法达到图样上同轴度9级、垂直度9级、圆跳动9级、平行度7级、对称度9级9。
常见机械加工能达到的精度等级介绍
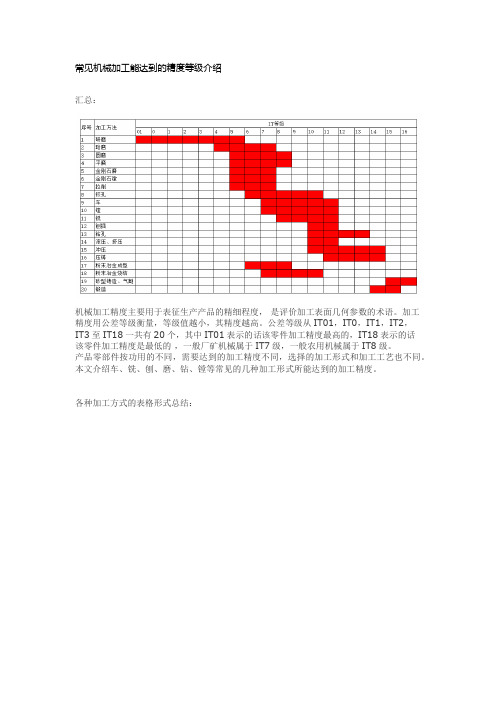
常见机械加工能达到的精度等级介绍汇总:机械加工精度主要用于表征生产产品的精细程度,是评价加工表面几何参数的术语。
加工精度用公差等级衡量,等级值越小,其精度越高。
公差等级从IT01,IT0,IT1,IT2,IT3至IT18一共有20个,其中IT01表示的话该零件加工精度最高的,IT18表示的话该零件加工精度是最低的,一般厂矿机械属于IT7级,一般农用机械属于IT8级。
产品零部件按功用的不同,需要达到的加工精度不同,选择的加工形式和加工工艺也不同。
本文介绍车、铣、刨、磨、钻、镗等常见的几种加工形式所能达到的加工精度。
各种加工方式的表格形式总结:一、车削工件旋转,车刀在平面内作直线或曲线移动的切削加工。
车床加工认准钛浩,车削一般在车床上进行,用以加工工件的内外圆柱面、端面、圆锥面、成形面和螺纹等。
车削加工精度一般为IT8—IT7,表面粗糙度为1.6—0.8μm。
1、粗车力求在不降低切速的条件下,采用大的切削深度和大进给量以提高车削效率,但加工精度只能达IT11,表面粗糙度为Rα20—10μm。
2、半精车和精车尽量采用高速而较小的进给量和切削深度,加工精度可达IT10—IT7,表面粗糙度为Rα10—0.16μm。
3、在高精度车床上用精细修研的金刚石车刀高速精车有色金属件,可使加工精度达到IT7—IT5,表面粗糙度为Rα0.04—0.01μm,这种车削称为镜面车削。
二、铣削铣削是指使用旋转的多刃刀具切削工件,是高效率的加工方法。
适于加工平面、沟槽、各种成形面(如花键、齿轮和螺纹)和模具的特殊形面等。
钛浩机械是以回转顶尖、丝杠、轴加工、数控车床加工、刀柄刀杆、夹头接杆为公司的主打产品!按照铣削时主运动速度方向与工件进给方向的相同或相反,又分为顺铣和逆铣。
铣削的加工精度一般可达IT8—IT7,表面粗糙度为6.3—1.6μm。
1、粗铣时的加工精度IT11—IT13,表面粗糙度5—20μm。
2、半精铣时的加工精度IT8—IT11,表面粗糙度2.5—10μm。
螺纹精度4h5h和4h区别

螺纹精度4h5h和4h区别螺纹精度是指螺纹的制造精度,可以衡量螺纹的精确程度和质量。
常见的螺纹精度等级有4H和5H,本文将从几个方面介绍4H和5H螺纹精度的区别。
4H和5H螺纹精度是依据国际标准ISO 1502制定的。
其中,4H 是指内螺纹的螺纹精度等级,而5H是指外螺纹的螺纹精度等级。
因此,4H和5H螺纹精度是分别适用于内螺纹和外螺纹的。
4H和5H螺纹精度的数值不同。
螺纹精度等级是通过测量螺纹的偏差来确定的,数值越小表示螺纹的精度越高。
4H的螺纹精度等级为0.028mm,而5H的螺纹精度等级为0.035mm。
因此,4H的螺纹精度比5H更高。
这也意味着在相同的螺纹尺寸下,4H的螺纹更加精确。
4H和5H螺纹精度的适用范围也有所不同。
4H螺纹精度适用于对螺纹精度要求较高的场合,如汽车制造、航空航天等领域。
而5H 螺纹精度适用于对螺纹精度要求相对较低的场合,如家电制造、建筑业等领域。
因此,在选择螺纹精度等级时,需要根据具体应用场景来确定。
4H和5H螺纹精度对应的螺纹加工工艺也有所不同。
由于4H螺纹精度要求更高,因此对螺纹加工的要求也更严格。
在螺纹加工过程中,需要选择合适的切削工具、加工参数和加工方式,以确保螺纹的精度达到要求。
而5H螺纹精度相对较低,对螺纹加工的要求也相对较低。
螺纹精度还与螺纹的尺寸有关。
通常情况下,螺纹精度等级越高,螺纹的尺寸范围就越小。
例如,在4H精度等级下,M6螺纹的尺寸范围为6.000-6.018mm,而在5H精度等级下,M6螺纹的尺寸范围为6.000-6.025mm。
因此,在选择螺纹精度时,还需要考虑螺纹的尺寸范围。
总结起来,4H和5H螺纹精度的区别主要体现在精度等级、数值、适用范围和加工工艺等方面。
4H螺纹精度更高,适用于对螺纹精度要求较高的场合;而5H螺纹精度相对较低,适用于对螺纹精度要求相对较低的场合。
在选择螺纹精度时,需要根据具体应用场景和要求来确定。
通过正确选择螺纹精度等级,可以保证螺纹的质量和可靠性,提高产品的性能和使用寿命。
机械加工都有那些等级区别?
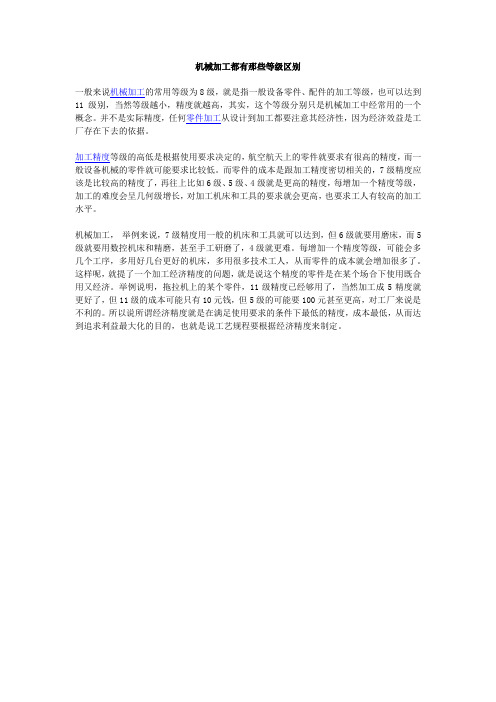
机械加工都有那些等级区别
一般来说机械加工的常用等级为8级,就是指一般设备零件、配件的加工等级,也可以达到11级别,当然等级越小,精度就越高,其实,这个等级分别只是机械加工中经常用的一个概念。
并不是实际精度,任何零件加工从设计到加工都要注意其经济性,因为经济效益是工厂存在下去的依据。
加工精度等级的高低是根据使用要求决定的,航空航天上的零件就要求有很高的精度,而一般设备机械的零件就可能要求比较低。
而零件的成本是跟加工精度密切相关的,7级精度应该是比较高的精度了,再往上比如6级、5级、4级就是更高的精度,每增加一个精度等级,加工的难度会呈几何级增长,对加工机床和工具的要求就会更高,也要求工人有较高的加工水平。
机械加工,举例来说,7级精度用一般的机床和工具就可以达到,但6级就要用磨床,而5级就要用数控机床和精磨,甚至手工研磨了,4级就更难。
每增加一个精度等级,可能会多几个工序,多用好几台更好的机床,多用很多技术工人,从而零件的成本就会增加很多了。
这样呢,就提了一个加工经济精度的问题,就是说这个精度的零件是在某个场合下使用既合用又经济。
举例说明,拖拉机上的某个零件,11级精度已经够用了,当然加工成5精度就更好了,但11级的成本可能只有10元钱,但5级的可能要100元甚至更高,对工厂来说是不利的。
所以说所谓经济精度就是在满足使用要求的条件下最低的精度,成本最低,从而达到追求利益最大化的目的,也就是说工艺规程要根据经济精度来制定。
车、铣、刨、磨、钻、镗分别能达到什么样的精度“公差等级”?

车、铣、刨、磨、钻、镗分别能达到什么样的精度“公差等级”?我们天天与数控加工打交道,相信你一定对加工精度有深刻的印象,但是你对用于表达加工精度的“公差等级”了解多少呢?公差等级是指确定尺寸精确程度的等级,国标规定分为20个等级,从IT01、IT0、IT1、IT2~IT18, 数字越大,公差等级(加工精度)越低,尺寸允许的变动范围(公差数值)越大,加工难度越小。
产品零部件按功用的不同,需要达到的加工精度不同,选择的加工形式和加工工艺也不同。
本文介绍车、铣、刨、磨、钻、镗等常见的几种加工形式所能达到的加工精度。
01车削工件旋转,车刀在平面内作直线或曲线移动的切削加工。
车削一般在车床上进行,用以加工工件的内外圆柱面、端面、圆锥面、成形面和螺纹等。
车削加工精度一般为IT8~IT7,表面粗糙度为1.6~0.8μm。
1)粗车力求在不降低切速的条件下,采用大的切削深度和大进给量以提高车削效率,但加工精度只能达IT11,表面粗糙度为Rα20~10μm。
2)半精车和精车尽量采用高速而较小的进给量和切削深度,加工精度可达IT10~IT7,表面粗糙度为Rα10~0.16μm。
3)在高精度车床上用精细修研的金刚石车刀高速精车有色金属件,可使加工精度达到IT7~IT5,表面粗糙度为Rα0.04~0.01μm,这种车削称为"镜面车削"。
02铣削铣削是指使用旋转的多刃刀具切削工件,是高效率的加工方法。
适于加工平面、沟槽、各种成形面(如花键、齿轮和螺纹)和模具的特殊形面等。
按照铣削时主运动速度方向与工件进给方向的相同或相反,又分为顺铣和逆铣。
铣削的加工精度一般可达IT8~IT7,表面粗糙度为6.3~1.6μm。
1)粗铣时的加工精度IT11~IT13,表面粗糙度5~20μm。
2)半精铣时的加工精度IT8~IT11,表面粗糙度2.5~10μm。
3)精铣时的加工精度IT16~IT8,表面粗糙度0.63~5μm。
03刨削刨削加工是用刨刀对工件作水平相对直线往复运动的切削加工方法,主要用于零件的外形加工。
常用加工方法可以达到的标准公差等级范围

常用加工方法可以达到的标准公差等级范围在制造业中,加工是非常常见的工艺环节。
无论是机械加工、模具制造还是电子元件加工,都需要依靠各种加工方法来实现产品的加工和制造。
在加工过程中,为了保证产品的质量和精度,通常会参考一定的标准公差等级范围。
本文将从简单到复杂,由表面到内部,逐步探讨常用加工方法可以达到的标准公差等级范围,在文章的结尾,我将共享对这个主题的个人观点和理解。
1. 表面加工:在传统的机械加工中,例如铣削、磨削、切削等加工方法中,通常需要对工件表面进行加工。
根据加工方法和工艺要求,可以达到的标准公差等级范围也会有所不同。
采用车削加工方法可以达到的标准公差等级范围为IT6-IT7级别,而采用磨削加工方法可以达到的标准公差等级范围为IT5-IT6级别。
2. 内部加工:除了表面加工外,一些工件还需要进行内部加工,例如钻孔、镗削、铰削等。
这些内部加工方法在实现产品精度和质量控制方面也有着不同的标准公差等级范围。
采用铰削加工方法可以达到的标准公差等级范围为IT9-IT10级别,而采用镗削加工方法可以达到的标准公差等级范围为IT7-IT8级别。
3. 精密加工:除了常规的机械加工外,一些精密加工方法,如电火花加工、激光切割、激光焊接等,对产品精度和表面质量要求更高。
这些精密加工方法可以达到的标准公差等级范围也相应更高。
采用激光切割加工方法可以达到的标准公差等级范围为IT2-IT3级别,而采用激光焊接加工方法可以达到的标准公差等级范围为IT4-IT5级别。
总结回顾:从以上的探讨可以看出,不同的加工方法在实现产品精度和质量控制方面有着不同的标准公差等级范围。
在实际加工生产中,需要根据具体工件的加工要求和工艺特点,选择合适的加工方法和标准公差等级范围,以确保产品的质量和精度。
个人观点和理解:在实际工程项目中,我认为了解各种加工方法可以达到的标准公差等级范围,有助于工程师和技术人员更好地选择合适的加工方法,合理设置公差等级,从而提高产品的质量和精度。
丝杠加工工艺
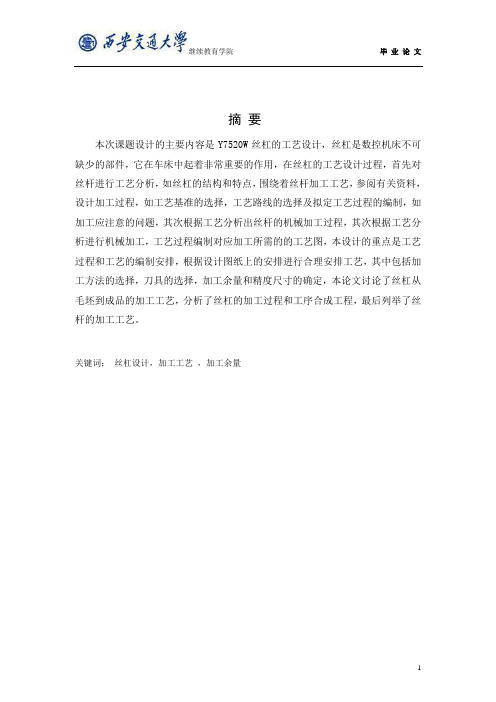
摘要本次课题设计的主要内容是Y7520W丝杠的工艺设计,丝杠是数控机床不可缺少的部件,它在车床中起着非常重要的作用,在丝杠的工艺设计过程,首先对丝杆进行工艺分析,如丝杠的结构和特点,围绕着丝杆加工工艺,参阅有关资料,设计加工过程,如工艺基准的选择,工艺路线的选择及拟定工艺过程的编制,如加工应注意的问题,其次根据工艺分析出丝杆的机械加工过程,其次根据工艺分析进行机械加工,工艺过程编制对应加工所需的的工艺图,本设计的重点是工艺过程和工艺的编制安排,根据设计图纸上的安排进行合理安排工艺,其中包括加工方法的选择,刀具的选择,加工余量和精度尺寸的确定,本论文讨论了丝杠从毛坯到成品的加工工艺,分析了丝杠的加工过程和工序合成工程,最后列举了丝杆的加工工艺。
关键词;丝杠设计,加工工艺,加工余量目录摘要 (1)前言 (5)第1章零件的分析 (6)1.1 零件的作用 (6)1.2 零件的结构简介 (6)1.2.1 丝杠的分类 (6)1.2.2 丝杠的结构特点及技术要求 (6)1.2.3零件的加工工艺分析 (7)第2章工艺规程的设计 (8)2.1 确定毛坯材料 (8)2.2 基面选择 (8)2.3 拟定丝杆的工艺路线 (9)2.4 填写工艺卡片 (9)2.5 确定工序尺寸 (12)2.6 细长轴工件安装 (12)2.6.1 在双顶尖间或一夹一顶安装工件 (12)2.6.2 用中心架加工工件时装夹和找正 (12)2.7 机床、刀具、夹具、量具的选择 (13)2.7.1 机床的选择: (13)2.7.2刀具的选择: (13)2.7.3 夹具的选择: (13)2.7.4 量具的选择: (14)设计小结 (15)致谢 (16)参考文献 (17)前言在实际生产中,要要完成零件的加工,通常需要铁件车铣刨磨钳热处理等多种步骤,而其最基本的、最冷的工种就是车工,然而车工在加工中,很多零件时配合的,这时就要车丝杠。
丝杠是一种精度很高的零件,它能精确地确定工作台坐标位置,将旋转运动转换成直线运动,面且还要传递一定的动力,所以在精度、强度及耐磨性等方面都有很高的要求。
- 1、下载文档前请自行甄别文档内容的完整性,平台不提供额外的编辑、内容补充、找答案等附加服务。
- 2、"仅部分预览"的文档,不可在线预览部分如存在完整性等问题,可反馈申请退款(可完整预览的文档不适用该条件!)。
- 3、如文档侵犯您的权益,请联系客服反馈,我们会尽快为您处理(人工客服工作时间:9:00-18:30)。
精度等级4级精度加工工艺
精度等级4级精度加工工艺是一种高精度的加工工艺,能够实现
高精度的加工要求。
它适用于需要高精度的零件加工,例如航空航天、汽车制造、精密仪器等领域。
精度等级4级精度加工工艺主要包括以下几个方面的内容。
首先,该工艺要求设备和工具的精度达到较高水平。
在精度等级4级加工中,精密设备和高精度的工具是不可或缺的。
这些设备和工具
需要经过严格的校准和调试,确保其精度达到要求。
比如使用经过精
确度校验的数控车床、数控铣床、高精度量具等。
其次,精度等级4级加工工艺要求材料的选材和处理达到一定的
标准。
材料的选择和处理对产品的精度有着很大的影响。
在选择材料
方面,需要考虑材料的物理和化学性质,以及其加工性能。
在处理方面,需要使用一些特殊的工艺,例如热处理、表面处理等,以提高材
料的机械性能。
再次,精度等级4级加工工艺要求加工过程中各项参数的控制严格。
加工过程中各项参数的控制是保证产品精度的关键。
例如,在数
控加工过程中,需要控制切削速度、进给速度、切削深度等参数,以
确保加工出的零件精度达到要求。
同时,要加强对加工过程中的温度、润滑液、冷却液等环境因素的控制,以防止产生热变形和振动等不利
因素。
最后,精度等级4级加工工艺还要求产品的质量检测和控制。
只
有对产品进行严格的质量检测和控制,才能确保产品的精度达到要求。
常用的检测方法有三坐标测量、光学测量、金相分析等。
在质量控制
方面,需要制定完善的检测标准和流程,建立良好的质量管理体系,
以确保产品的质量。
总之,精度等级4级精度加工工艺是一种高精度的加工工艺,它
能够满足需要高精度的零件加工的要求。
通过提高设备和工具的精度、合理选择和处理材料、严格控制加工参数和质量检测,可以保证产品
的精度达到要求。
精度等级4级加工工艺在航空航天、汽车制造、精
密仪器等领域有着广泛的应用。