轮胎内胎胶配方设计
NR内胎配方的优化设计
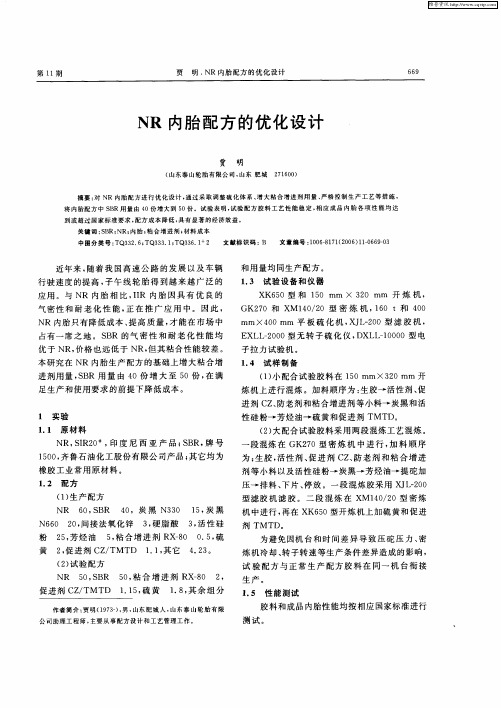
胶 料 和成 品 内胎性 能均按 相应 国家标 准进行
测试 。
维普资讯
60 7
轮 胎 工 业
2 0 第 2 卷 0 6年 6
2 结 果 与 讨 论
从 表 2可 以看 出 , 生产 配方 相 比 , 验 配方 与 试
2 1 小配 合试 验 .
1 2 配 方 .
段混 炼 在 G 7 K2 0型 密 炼 机 中进 行 , 料 顺 序 加
为: 胶, 生 活性 剂 、 进 剂 C 、 老剂 和 粘 合 增进 促 Z防 剂等 小料 以及活性 硅粉一 炭黑 一 芳烃油一 提砣 加 压一 排料 、 片 、 放 。一 段t 炼胶 采 用 X L 2 0 下 停 昆 J -0 型滤胶 机 滤 胶 。二 段 昆炼 在 X 4 / 0型 密 炼 M1 0 2 机 中进行 , 再在 XK6 0型开炼 机上 加硫 黄和 促进 5
进 剂用 量 , B 用 量 由 4 SR 0份 增 大 至 5 0份 , 满 在
() 1 小配合 试验 胶料 在 1 0mm×3 0mm 开 5 2
足 生产 和使用 要求 的前 提下 降低 成本 。
1 实 验
炼机 上进 行混炼 。加 料顺 序为 : 生胶一 活性 剂 、 促 进剂 C 、 Z 防老剂 和粘 合增进 剂等 小料一 炭黑 和活
性 硅粉一 芳烃 油一 硫黄 和促进 剂 T MT D。 () 2 大配合 试验 胶料 采用两 段混炼 工艺 混炼 。
一
1 1 原材 料 .
NR, I 2 , 度 尼 西 亚 产 品 ; B 牌 号 SR 0 印 S R, 10 , 5 0 齐鲁石 油 化工股 份有 限公 司产 品 ; 它均 为 其 橡胶 工业 常用原 材料 。
新的轮胎胶料配方
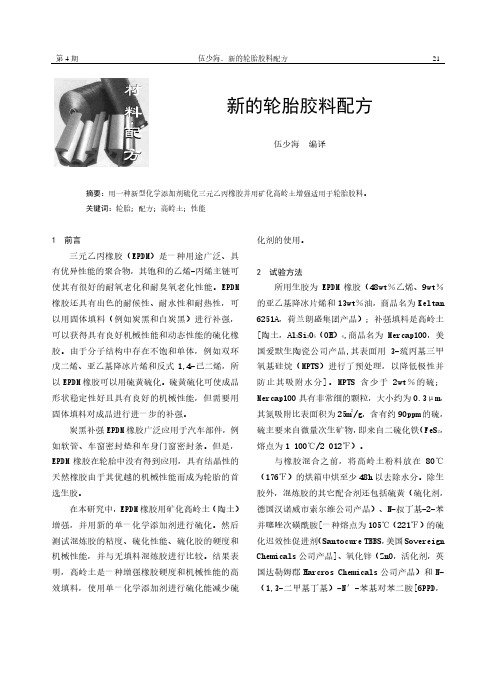
新的轮胎胶料配方伍少海编译摘要:用一种新型化学添加剂硫化三元乙丙橡胶并用矿化高岭土增强适用于轮胎胶料。
关键词:轮胎;配方;高岭土;性能1 前言三元乙丙橡胶(EPDM)是一种用途广泛、具有优异性能的聚合物,其饱和的乙烯-丙烯主链可使其有很好的耐氧老化和耐臭氧老化性能。
EPDM 橡胶还具有出色的耐候性、耐水性和耐热性,可以用固体填料(例如炭黑和白炭黑)进行补强,可以获得具有良好机械性能和动态性能的硫化橡胶。
由于分子结构中存在不饱和单体,例如双环戊二烯、亚乙基降冰片烯和反式1,4-己二烯,所以EPDM橡胶可以用硫黄硫化。
硫黄硫化可使成品形状稳定性好且具有良好的机械性能,但需要用固体填料对成品进行进一步的补强。
炭黑补强EPDM橡胶广泛应用于汽车部件,例如软管、车窗密封垫和车身门窗密封条。
但是,EPDM橡胶在轮胎中没有得到应用,具有结晶性的天然橡胶由于其优越的机械性能而成为轮胎的首选生胶。
在本研究中,EPDM橡胶用矿化高岭土(陶土)增强,并用新的单一化学添加剂进行硫化。
然后测试混炼胶的粘度、硫化性能、硫化胶的硬度和机械性能,并与无填料混炼胶进行比较。
结果表明,高岭土是一种增强橡胶硬度和机械性能的高效填料,使用单一化学添加剂进行硫化能减少硫化剂的使用。
2 试验方法所用生胶为EPDM橡胶(48wt%乙烯、9wt%的亚乙基降冰片烯和13wt%油,商品名为Keltan 6251A,荷兰朗盛集团产品);补强填料是高岭土[陶土,Al2Si2O5(OH)4,商品名为 Mercap100,美国爱默生陶瓷公司产品,其表面用3-巯丙基三甲氧基硅烷(MPTS)进行了预处理,以降低极性并防止其吸附水分]。
MPTS含少于2wt%的硫;Mercap100具有非常细的颗粒,大小约为0.3μm,其氮吸附比表面积为25m2/g,含有约90ppm的硫,硫主要来自微量次生矿物,即来自二硫化铁(FeS2,熔点为1 100℃/2 012℉)。
与橡胶混合之前,将高岭土粉料放在80℃(176℉)的烘箱中烘至少48h以去除水分。
导向轮胎胎面胶配方
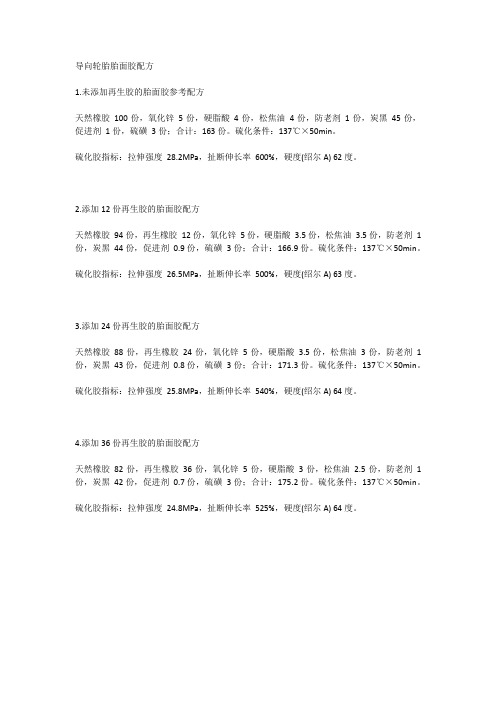
导向轮胎胎面胶配方
1.未添加再生胶的胎面胶参考配方
天然橡胶100份,氧化锌5份,硬脂酸4份,松焦油4份,防老剂1份,炭黑45份,促进剂1份,硫磺3份;合计:163份。
硫化条件:137℃×50min。
硫化胶指标:拉伸强度28.2MPa,扯断伸长率600%,硬度(绍尔A) 62度。
2.添加12份再生胶的胎面胶配方
天然橡胶94份,再生橡胶12份,氧化锌5份,硬脂酸3.5份,松焦油3.5份,防老剂1份,炭黑44份,促进剂0.9份,硫磺3份;合计:166.9份。
硫化条件:137℃×50min。
硫化胶指标:拉伸强度26.5MPa,扯断伸长率500%,硬度(绍尔A) 63度。
3.添加24份再生胶的胎面胶配方
天然橡胶88份,再生橡胶24份,氧化锌5份,硬脂酸3.5份,松焦油3份,防老剂1份,炭黑43份,促进剂0.8份,硫磺3份;合计:171.3份。
硫化条件:137℃×50min。
硫化胶指标:拉伸强度25.8MPa,扯断伸长率540%,硬度(绍尔A) 64度。
4.添加36份再生胶的胎面胶配方
天然橡胶82份,再生橡胶36份,氧化锌5份,硬脂酸3份,松焦油2.5份,防老剂1份,炭黑42份,促进剂0.7份,硫磺3份;合计:175.2份。
硫化条件:137℃×50min。
硫化胶指标:拉伸强度24.8MPa,扯断伸长率525%,硬度(绍尔A) 64度。
轮胎内胎胶配方设计
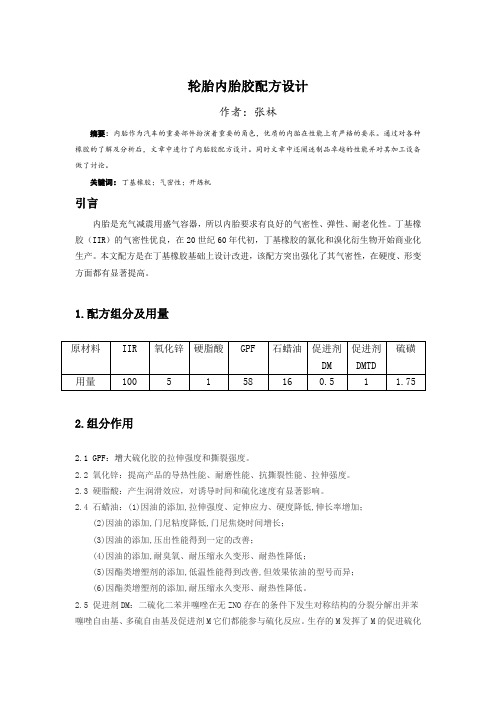
轮胎内胎胶配方设计作者:张林摘要:内胎作为汽车的重要部件扮演着重要的角色,优质的内胎在性能上有严格的要求。
通过对各种橡胶的了解及分析后,文章中进行了内胎胶配方设计。
同时文章中还阐述制品卓越的性能并对其加工设备做了讨论。
关键词:丁基橡胶;气密性;开炼机引言内胎是充气减震用盛气容器,所以内胎要求有良好的气密性、弹性、耐老化性。
丁基橡胶(IIR)的气密性优良,在20世纪60年代初,丁基橡胶的氯化和溴化衍生物开始商业化生产。
本文配方是在丁基橡胶基础上设计改进,该配方突出强化了其气密性,在硬度、形变方面都有显著提高。
1.配方组分及用量原材料IIR 氧化锌硬脂酸GPF 石蜡油促进剂DM 促进剂DMTD硫磺用量100 5 1 58 16 0.5 1 1.75 2.组分作用2.1 GPF:增大硫化胶的拉伸强度和撕裂强度。
2.2 氧化锌:提高产品的导热性能、耐磨性能、抗撕裂性能、拉伸强度。
2.3 硬脂酸:产生润滑效应,对诱导时间和硫化速度有显著影响。
2.4 石蜡油:(1)因油的添加,拉伸强度、定伸应力、硬度降低,伸长率增加;(2)因油的添加,门尼粘度降低,门尼焦烧时间增长;(3)因油的添加,压出性能得到一定的改善;(4)因油的添加,耐臭氧、耐压缩永久变形、耐热性降低;(5)因酯类增塑剂的添加,低温性能得到改善,但效果依油的型号而异;(6)因酯类增塑剂的添加,耐压缩永久变形、耐热性降低。
2.5 促进剂DM:二硫化二苯并噻唑在无ZNO存在的条件下发生对称结构的分裂分解出并苯噻唑自由基、多硫自由基及促进剂M它们都能参与硫化反应。
生存的M发挥了M的促进硫化功能。
在有活性剂氧化锌与硬脂酸存在的情况下它的作用与M相同,DM与硫黄一起硫化时,还分解出双基活性硫或多基活性硫可使橡胶分子进行交联。
2.6 促进剂DMTD:加速硫化链反应的引发和链增长反应,提高硫化反应速度,同时改善硫化胶的结构和性能。
2.7 硫磺:提供硫化原料。
3.加工设备3.1 开炼机:应用于生胶的塑炼、破碎、洗涤、压片;胶料的混炼、压片以及胶料中的杂质清除;混炼胶的热炼、供胶;再生胶的粉碎、混炼、压片。
丁基橡胶内胎配方分析配方成分制备工艺改进建议
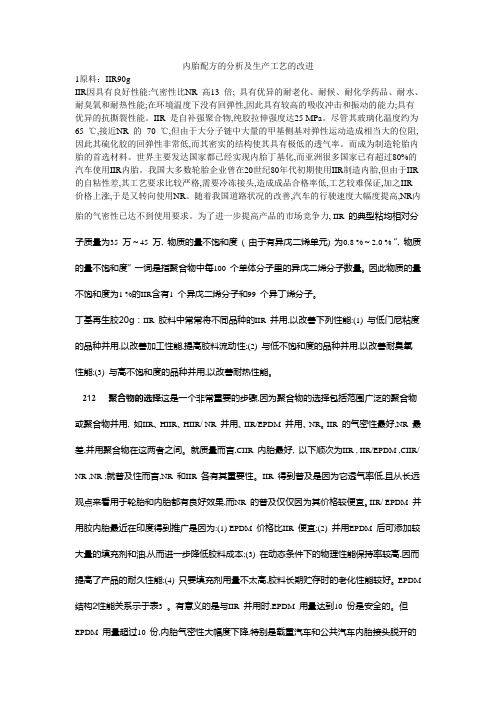
内胎配方的分析及生产工艺的改进1原料:IIR90gIIR因具有良好性能:气密性比NR 高13 倍; 具有优异的耐老化、耐候、耐化学药品、耐水、耐臭氧和耐热性能;在环境温度下没有回弹性,因此具有较高的吸收冲击和振动的能力;具有优异的抗撕裂性能。
IIR 是自补强聚合物,纯胶拉伸强度达25 MPa。
尽管其玻璃化温度约为- 65 ℃,接近NR 的- 70 ℃,但由于大分子链中大量的甲基侧基对弹性运动造成相当大的位阻,因此其硫化胶的回弹性非常低,而其密实的结构使其具有极低的透气率。
而成为制造轮胎内胎的首选材料。
世界主要发达国家都已经实现内胎丁基化,而亚洲很多国家已有超过80%的汽车使用IIR内胎。
我国大多数轮胎企业曾在20世纪80年代初期使用IIR制造内胎,但由于IIR 的自粘性差,其工艺要求比较严格,需要冷冻接头,造成成品合格率低,工艺较难保证,加之IIR价格上涨,于是又转向使用NR。
随着我国道路状况的改善,汽车的行驶速度大幅度提高,NR内胎的气密性已达不到使用要求。
为了进一步提高产品的市场竞争力, IIR 的典型粘均相对分子质量为35 万~45 万, 物质的量不饱和度( 由于有异戊二烯单元) 为0.8 %~2.0 %“, 物质的量不饱和度”一词是指聚合物中每100 个单体分子里的异戊二烯分子数量。
因此物质的量不饱和度为1 %的IIR含有1 个异戊二烯分子和99 个异丁烯分子。
丁基再生胶20g:IIR 胶料中常常将不同品种的IIR 并用,以改善下列性能:(1) 与低门尼粘度的品种并用,以改善加工性能,提高胶料流动性;(2) 与低不饱和度的品种并用,以改善耐臭氧性能;(3) 与高不饱和度的品种并用,以改善耐热性能。
212 聚合物的选择这是一个非常重要的步骤,因为聚合物的选择包括范围广泛的聚合物或聚合物并用, 如IIR、HIIR、HIIR/ NR 并用、IIR/EPDM 并用、NR。
IIR 的气密性最好,NR 最差,并用聚合物在这两者之间。
轮胎配方及原材料介绍

海中载沉汽车轮胎胎里胶配圆单位:品量份之阳内胎战睦门嘴垫胶的配圆轮胎主要不妨由天然橡胶(NR)散同戊两烯,丁苯橡胶(SBR)丁两烯战苯乙烯,逆丁橡胶(BR)是由丁两烯,同戊橡胶(IR)是由同戊两烯,丁基橡胶(IIR)是同丁烯战少量同戊两烯或者丁两烯为主要本料,硬脂酸,氧化锌,微晶蜡,防老剂,收配油,硬量冰乌,防焦剂,促进剂,硫磺等为配料制成.1、天然橡胶(NR)以橡胶烃(散同戊两烯)为主,含少量蛋黑量、火分、树脂酸、糖类战无机盐等.弹性大,定伸强度下,抗撕裂性战电绝缘性劣良,耐磨性战耐涝性劣良,加工性好,易于其余资料粘合,正在概括本能圆里劣于普遍合成橡胶.缺面是耐氧战耐臭氧性好,简单老化蜕变;耐油战耐溶剂性短好,第抗酸碱的腐蚀本领矮;耐热性没有下.使用温度范畴:约-60℃~+80℃.创制轮胎、胶鞋、胶管、胶戴、电线电缆的绝缘层战护套以及其余通用制品.特天适用于制制扭振取消器、收效果减震器、呆板收座、橡胶-金属悬挂元件、膜片、模压制品.2、丁苯橡胶(SBR)丁两烯战苯乙烯的同散体.本能靠近天然橡胶,是暂时产量最大的通用合成橡胶,其个性是耐磨性、耐老化战耐热性超出天然橡胶,量天也较天然橡胶匀称.缺面是:弹性较矮,抗伸挠、抗撕裂本能较好;加工本能好,特天是自粘性好、死胶强度矮.使用温度范畴:约-50℃~+100℃.主要用以代替天然橡胶创制轮胎、胶板、胶管、胶鞋及其余通用制品.3、逆丁橡胶(BR)是由丁两烯散合而成的逆式结构橡胶.便宜是:弹性取耐磨性劣良,耐老化性好,耐矮温性劣同,正在动向背荷下收热量小,易于金属粘合.缺面是强度较矮,抗撕裂性好,加工本能取自粘性好.使用温度范畴:约-60℃~+100℃. 普遍多战天然橡胶或者丁苯橡胶并用,主要创制轮胎胎里、输收戴战特殊耐热制品.4、同戊橡胶(IR)是由同戊两烯单体散合而成的一种逆式结构橡胶.化教组成、坐体结构取天然橡胶相似,本能也非常靠近天然橡胶,故有合整天然橡胶之称.它具备天然橡胶的大部分便宜,耐老化由于天然橡胶,弹性战强力比天然橡胶稍矮,加工本能好,成本较下.使用温度范畴:约-50℃~+100℃可代替天然橡胶创制轮胎、胶鞋、胶管、胶戴以及其余通用制品.5、氯丁橡胶(CR)是由氯丁两烯干单体乳液散合而成的散合体.那种橡胶分子中含有氯本子,所以取其余通用橡胶相比:它具备劣良的抗氧、抗臭氧性,没有简单焚,着火后能自熄,耐油、耐溶剂、耐酸碱以及耐老化、气稀性好等便宜;其物理板滞本能也比天然橡胶好,故可用做通用橡胶,也可用做特种橡胶.主要缺面是耐热性较好,比沉较大、相对于成本下,电绝缘性短好,加工时易粘滚、易焦烧及易粘模.别的,死胶宁静性好,没有简单保存.使用温度范畴:约-45℃~+100℃.主要用于制制央供抗臭氧、耐老化性下的电缆护套及百般防备套、呵护罩;耐油、耐化教腐蚀的胶管、胶戴战化工衬里;耐焚的天下采矿用橡胶制品,以及百般模压制品、稀启圈、垫、粘结剂等.6、丁基橡胶(IIR)是同丁烯战少量同戊两烯或者丁两烯的同散体.最大个性是气稀性好,耐臭氧、耐老化本能好,耐热性较下,少久处事温度可正在130℃以下;本领无机强酸(如硫酸、硝酸等)战普遍有机溶剂,吸振战阻僧个性劣良,电绝缘性也非常好.缺面是弹性好,加工本能好,硫化速度缓,粘着性战耐油性好.使用温度范畴:约-40℃~+120℃.主要用做内胎、火胎、气球、电线电缆绝缘层、化工设备衬里及防震制品、耐热输收戴、耐热老化的胶布制品.7、丁阴橡胶(NBR)丁两烯战丙烯阴的同散体.个性是耐汽油战脂肪烃油类的本能特天好,仅次于散硫橡胶、丙烯酸酯战氟橡胶,而劣于其余通用橡胶.耐热性好,气稀性、耐磨及耐火性等均较好,粘结力强.缺面是耐热及耐臭氧性较好,强力及弹性较矮,耐酸性好,电绝缘性短好,耐极性溶剂本能也较好.使用温度范畴:约-30℃~+100℃.主要用于制制百般耐油制品,如胶管、稀启制品等.8、氢化丁阴橡胶(HNBR)丁两烯战丙烯阴的同散体.它是通过局部或者部分氢化NBR的丁两烯中的单键而得到的.其个性是板滞强度战耐磨性下,用过氧化物接联时耐热性比NBR好,其余本能取丁阴橡胶一般.缺面是代价较下.使用温度范畴:约-30℃~+150℃. 主要用于耐油、耐下温的稀启制品.9、乙丙橡胶(EPM\\EPDM)乙烯战丙烯的同散体,普遍分为两元乙丙橡胶战三元乙丙橡胶.个性是抗臭氧、耐紫中线、耐天候性战耐老化性劣同,居通用橡胶之尾.电绝缘性、耐化教性、冲打弹性很好,耐酸碱,比沉小,可举止下弥补协同.耐热可达150℃,耐极性溶剂-酮、酯等,但是没有耐脂肪烃战芳香烃,其余物理板滞本能略次于天然橡胶而劣于丁苯橡胶.缺面是自粘性战互粘性很好,没有简单粘合.使用温度范畴:约-50℃~+150℃. 主要用做化工设备衬里、电线电缆包皮、蒸汽胶管、耐热输收戴、汽车用橡胶制品及其余工业制品.。
高速轿车子午线轮胎胎面胶的配方设计
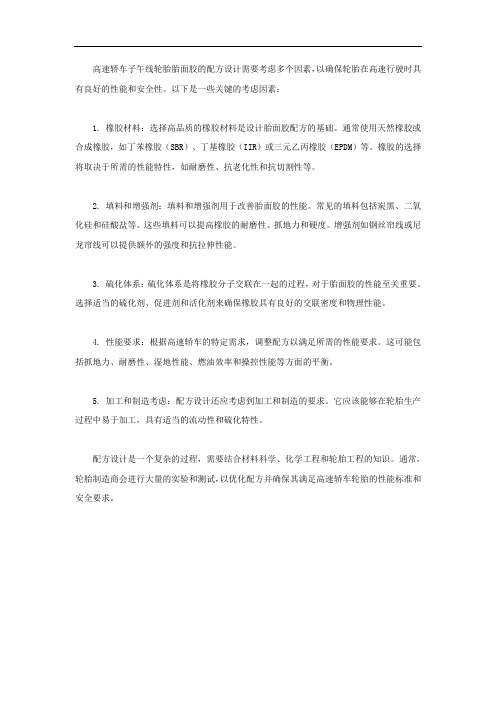
高速轿车子午线轮胎胎面胶的配方设计需要考虑多个因素,以确保轮胎在高速行驶时具有良好的性能和安全性。
以下是一些关键的考虑因素:
1. 橡胶材料:选择高品质的橡胶材料是设计胎面胶配方的基础。
通常使用天然橡胶或合成橡胶,如丁苯橡胶(SBR)、丁基橡胶(IIR)或三元乙丙橡胶(EPDM)等。
橡胶的选择将取决于所需的性能特性,如耐磨性、抗老化性和抗切割性等。
2. 填料和增强剂:填料和增强剂用于改善胎面胶的性能。
常见的填料包括炭黑、二氧化硅和硅酸盐等。
这些填料可以提高橡胶的耐磨性、抓地力和硬度。
增强剂如钢丝帘线或尼龙帘线可以提供额外的强度和抗拉伸性能。
3. 硫化体系:硫化体系是将橡胶分子交联在一起的过程,对于胎面胶的性能至关重要。
选择适当的硫化剂、促进剂和活化剂来确保橡胶具有良好的交联密度和物理性能。
4. 性能要求:根据高速轿车的特定需求,调整配方以满足所需的性能要求。
这可能包括抓地力、耐磨性、湿地性能、燃油效率和操控性能等方面的平衡。
5. 加工和制造考虑:配方设计还应考虑到加工和制造的要求。
它应该能够在轮胎生产过程中易于加工,具有适当的流动性和硫化特性。
配方设计是一个复杂的过程,需要结合材料科学、化学工程和轮胎工程的知识。
通常,轮胎制造商会进行大量的实验和测试,以优化配方并确保其满足高速轿车轮胎的性能标准和安全要求。
轮胎橡胶配方

轮胎橡胶配方
轮胎橡胶配方是制造轮胎的关键部分,它决定了轮胎的主要性能。
配方中包含多种成分,每种成分都有其特定的作用。
以下是一个典型的轮胎橡胶配方及其成分说明:
1、基础橡胶:这是配方的核心成分,通常使用天然橡胶或合成橡胶。
天然橡胶具有良好的弹性和耐久性,而合成橡胶则提供了更多的性能选项,如低滚动阻力、高耐磨性和耐高温性。
2、填充剂:用于增加橡胶的体积,使其更坚固和耐磨。
常见的填充剂包括碳黑和白炭黑。
碳黑提供了优异的耐磨性和抗撕裂性,而白炭黑则增加了橡胶的抗湿滑性能。
3、硫化剂:使橡胶分子相互交联,形成网状结构,从而提高其弹性和耐久性。
4、增塑剂:如石油和油脂,有助于改善橡胶的加工性能和柔韧性。
5、防老剂:有助于延缓橡胶老化过程,提高其耐久性。
6、抗氧剂:防止橡胶在高温下氧化,有助于延长轮胎的使用寿命。
7、抗紫外线剂:用于抵抗紫外线对橡胶的降解,延长轮胎的使用寿命。
8、粘合剂:有助于增强橡胶与纤维材料之间的粘附力,提高轮胎的结构稳定性。
9、钢丝与纤维材料:用于增强轮胎的结构强度和稳定性。
钢丝主要用于轮胎的骨架结构,而纤维材料则提供额外的支撑和稳定性。
10、其他添加剂:根据特定需求,还可以添加其他一些添加剂,如抗湿滑剂、降噪剂等,以改善轮胎的性能。
除了以上成分外,正确的配方比例也是至关重要的。
不同成分的比例会直接影响轮胎的性能。
通过精确控制这些成分的比例,可以生产出具有优异性能的轮胎。
这需要经验丰富的工程师和技术人员来研发和调整配方,以满足各种不同的应用需求。
丁基内胎配方设计基本组成
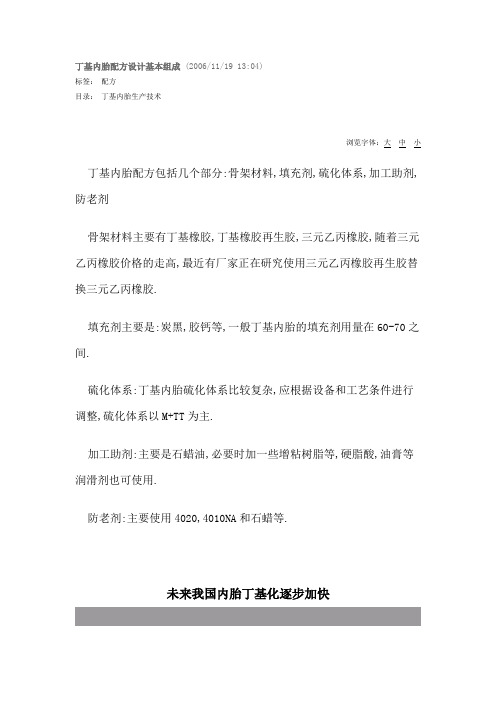
丁基内胎配方设计基本组成(2006/11/19 13:04)标签:配方目录:丁基内胎生产技术浏览字体:大中小丁基内胎配方包括几个部分:骨架材料,填充剂,硫化体系,加工助剂,防老剂骨架材料主要有丁基橡胶,丁基橡胶再生胶,三元乙丙橡胶,随着三元乙丙橡胶价格的走高,最近有厂家正在研究使用三元乙丙橡胶再生胶替换三元乙丙橡胶.填充剂主要是:炭黑,胶钙等,一般丁基内胎的填充剂用量在60-70之间.硫化体系:丁基内胎硫化体系比较复杂,应根据设备和工艺条件进行调整,硫化体系以M+TT为主.加工助剂:主要是石蜡油,必要时加一些增粘树脂等,硬脂酸,油膏等润滑剂也可使用.防老剂:主要使用4020,4010NA和石蜡等.未来我国内胎丁基化逐步加快hc360慧聪网化工行业频道2004-04-09 15:20:35【hc360慧聪网化工行业频道】:据中国橡胶工业协会力车胎分会分析预测,今后5~10年中国力车胎(自行车胎、摩托车胎和手推车胎)内胎丁基化步伐将加快。
目前中国自行车内胎丁基化率仅26%,与世界先进水平相比有较大差距。
内胎丁基化早已是世界潮流,欧美、日本等经济发达地区已百分之百内胎丁基化,印度的内胎丁基化率达到90%,印尼、泰国、马来西亚也达到70%,菲律宾达40%。
中国自行车内胎、摩托车内胎丁基化率低有多方面的原因:一是丁基胶主要依靠进口,价格贵,造成丁基胶内胎生产成本远高于天然胶内胎;二是工艺技术掌握慢;三是推介宣传不力;四是市场混乱。
目前中国力车胎行业总体情况是:市场容量有所扩大,行业有所发展,但供过于求,竞争激烈。
力车胎行业是劳动密集型行业,国际经济一体化进程加快有利于发挥中国的优势,因此估计中国力车胎生产仍将保持较快增长速度,估计今后5~10年中国丁基内胎将进入发展期。
随着国民经济发展,城乡人民生活水平提高,国内消费者已逐渐接受了丁基内胎,力车胎行业也有不少企业已经掌握了批量生产丁基内胎的技术,估计3~5年内我国内胎丁基化率会提高到50%。
IIR内胎 第1 部分 配方设计

项 目 门尼粘度下降 乙烯质量分数下降 相对分子质量分布变宽 二烯质量分数降低
表 3 EPDM 结构2性能关系
改 善 聚合物分散性 、挤出口型膨胀 、收缩率 、
生胶粘性 (V2200 :34ML) 拉伸永久变形 、生胶强度 ( HO T)
(V2200 :中2低) 混炼 、分散性 (V2200 :中2宽)
Exxon Butyl 077
Polysar Butyl 101
Exxon Butyl 007
Polysar Butyl 10123
注 :1) 用非污染型防老剂稳定的品种 ;2) 此品种不含防老剂 。
73 0 轮 胎 工 业 1997 年第 17 卷
的缺点 。
2 IIR 内胎的配方设计 下面将讨论配方设计技术和 IIR 内胎的
配方设计 ,其中包括聚合物 、填充剂 、加工助 剂和硫化体系等配合剂的选择 。在开始讨论 内胎的配方要求之前 ,必须先了解内胎的性
能要求 ,其中包括 : ·低透气率 ; ·耐热 ; ·低拉伸永久变形 ; ·耐热老化性能 ; ·良好的物理性能和这些性能较高的保
1 IIR 的性能和品种 埃克森为不同用途和改善加工性能开发
了一系列异丁烯产品 ,其中包括 : ·HIIR (CIIR 和 B IIR) ; ·星形支化丁基橡胶 ( SBB) ; ·HSBB (CSBB 和 BSBB) ; ·Exxpro 。
IIR 的性能可以归纳如下 : (1) 气密性比 N R 高 13 倍 ; (2) 具有优异的耐老化 、耐候 、耐化学药 品 、耐水 、耐臭氧和耐热性能 ; (3) 在环境温度下没有回弹性 ,因此具有 较高的吸收冲击和振动的能力 ; (4) 具有优异的抗撕裂性能 。 IIR 是自补强聚合物 ,纯胶拉伸强度达 25 M Pa 。尽管其玻璃化温度约为 - 65 ℃,接 近 N R 的 - 70 ℃,但由于大分子链中大量的 甲基侧基对弹性运动造成相当大的位阻 ,因 此其硫化胶的回弹性非常低 ,而其密实的结 构使其具有极低的透气率 。 表 1 示出了按不饱和度和门尼粘度差别 划分的不同品级的商品 IIR 。表 2 示出了不 同弹性体的气密性 。 IIR 的典型粘均相对分子质量为 35 万 ~45 万 , 物 质 的 量 不 饱 和 度 ( mole percent unsaturation) ( 由 于 有 异 戊 二 烯 单 元 ) 为 018 %~210 %“, 物质的量不饱和度”一词是 指聚合物中每 100 个单体分子里的异戊二烯 分子数量 。因此物质的量不饱和度为1 %的
轮胎用橡胶塑料及配方
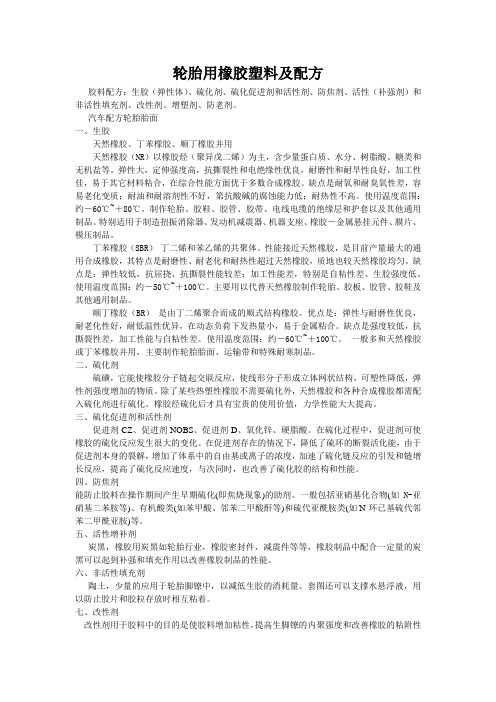
轮胎用橡胶塑料及配方胶料配方:生胶(弹性体)、硫化剂、硫化促进剂和活性剂、防焦剂、活性(补强剂)和非活性填充剂、改性剂、增塑剂、防老剂。
汽车配方轮胎胎面一、生胶天然橡胶、丁苯橡胶、顺丁橡胶并用天然橡胶(NR)以橡胶烃(聚异戊二烯)为主,含少量蛋白质、水分、树脂酸、糖类和无机盐等。
弹性大,定伸强度高,抗撕裂性和电绝缘性优良,耐磨性和耐旱性良好,加工性佳,易于其它材料粘合,在综合性能方面优于多数合成橡胶。
缺点是耐氧和耐臭氧性差,容易老化变质;耐油和耐溶剂性不好,第抗酸碱的腐蚀能力低;耐热性不高。
使用温度范围:约-60℃~+80℃。
制作轮胎、胶鞋、胶管、胶带、电线电缆的绝缘层和护套以及其他通用制品。
特别适用于制造扭振消除器、发动机减震器、机器支座、橡胶-金属悬挂元件、膜片、模压制品。
丁苯橡胶(SBR)丁二烯和苯乙烯的共聚体。
性能接近天然橡胶,是目前产量最大的通用合成橡胶,其特点是耐磨性、耐老化和耐热性超过天然橡胶,质地也较天然橡胶均匀。
缺点是:弹性较低,抗屈挠、抗撕裂性能较差;加工性能差,特别是自粘性差、生胶强度低。
使用温度范围:约-50℃~+100℃。
主要用以代替天然橡胶制作轮胎、胶板、胶管、胶鞋及其他通用制品。
顺丁橡胶(BR)是由丁二烯聚合而成的顺式结构橡胶。
优点是:弹性与耐磨性优良,耐老化性好,耐低温性优异,在动态负荷下发热量小,易于金属粘合。
缺点是强度较低,抗撕裂性差,加工性能与自粘性差。
使用温度范围:约-60℃~+100℃。
一般多和天然橡胶或丁苯橡胶并用,主要制作轮胎胎面、运输带和特殊耐寒制品。
二、硫化剂硫磺,它能使橡胶分子链起交联反应,使线形分子形成立体网状结构,可塑性降低,弹性剂强度增加的物质。
除了某些热塑性橡胶不需要硫化外,天然橡胶和各种合成橡胶都需配入硫化剂进行硫化。
橡胶经硫化后才具有宝贵的使用价值,力学性能大大提高。
三、硫化促进剂和活性剂促进剂CZ、促进剂NOBS、促进剂D、氧化锌、硬脂酸。
橡胶英才网_轮胎胶料配方设计
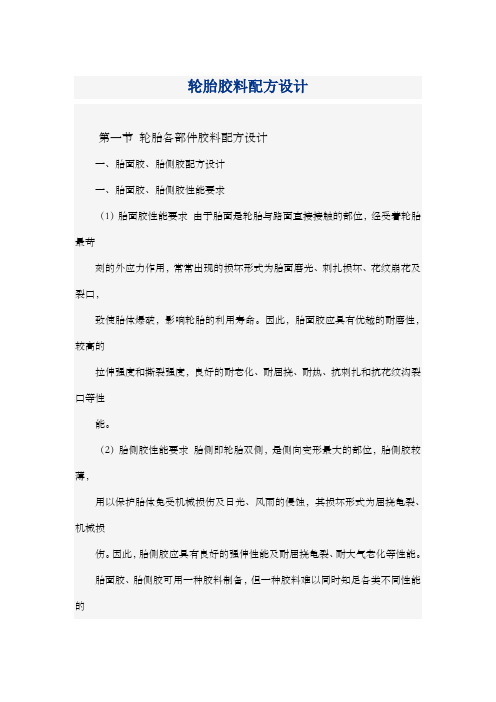
轮胎胶料配方设计第一节轮胎各部件胶料配方设计一、胎面胶、胎侧胶配方设计一、胎面胶、胎侧胶性能要求(1)胎面胶性能要求由于胎面是轮胎与路面直接接触的部位,经受着轮胎最苛刻的外应力作用,常常出现的损坏形式为胎面磨光、刺扎损坏、花纹崩花及裂口,致使胎体爆破,影响轮胎的利用寿命。
因此,胎面胶应具有优越的耐磨性,较高的拉伸强度和撕裂强度,良好的耐老化、耐屈挠、耐热、抗刺扎和抗花纹沟裂口等性能。
(2)胎侧胶性能要求胎侧即轮胎双侧,是侧向变形最大的部位,胎侧胶较薄,用以保护胎体免受机械损伤及日光、风雨的侵蚀,其损坏形式为屈挠龟裂、机械损伤。
因此,胎侧胶应具有良好的强伸性能及耐屈挠龟裂、耐大气老化等性能。
胎面胶、胎侧胶可用一种胶料制备,但一种胶料难以同时知足各类不同性能的要求。
目前大中型载重轮胎已普遍采用分层出形的复合胎面胶,既利于提高产品质量,又可降低本钱。
分层压出形式常常利用的有以下三种形式。
①胎冠上层用一种胶料,胎冠基层胶与胎侧共用一种胶料。
②胎冠上、基层用一种胶料,胎侧用另一种胶料。
③胎冠、胎肩、胎侧别离采用三种胶料。
二、胎面胶、胎侧胶配方(1)胎面胶配方特点胎面胶与胎冠上层胶配方相同。
①常常利用生胶品种有NR、SBR 和BR。
NR 具优良的弹性、拉伸强度和耐磨性能,是轮胎胶料中理想的胶种,虽然利用中出现裂口较快,但其扩展速度比SBR 和BR慢。
SBR 具有优良的耐磨和耐老化性能。
BR 的弹性更优于NR 并具有良好的耐磨性和生热低的特点,适宜用于轮胎胎面胶较料中。
通常大型轮胎如工程机械轮胎胎面以NR 单用为宜。
中小型轮胎胎面胶则以NR为主,掺用SBR 或BR,拖沓机轮胎胎面也可采用三胶并用的配方。
②主要补强剂是cb,可按照胶料性能要求和生胶类别肯定cb 品种及用量。
胎面胶采用活性cb,一般总用量为45~50 质量份。
以下均用“份”代表“质量份”来表示配合剂用量。
③硫化体系中硫磺用量按照选用胶种而定,全天然橡胶配方硫磺用量为~份,掺用SBR 或BR 的配方,以采用低硫高促体系。
一种全钢子午线轮胎基部胶配方

一种全钢子午线轮胎基部胶配方全钢子午线轮胎是一种高性能轮胎,其具有较高的抗剪切性能和胎侧稳定性,适用于各种复杂路况下的高速行驶。
下面是一种全钢子午线轮胎基部胶的配方示例。
1.橡胶基料-天然橡胶(NR):45份-丁苯橡胶(BR):55份-高耐磨橡胶:25份-聚异戊二烯橡胶(IR):15份2.碳黑-尖晶石碳黑(N339):80份-针状碳黑(N550):40份3.防老剂-防老剂RD:2份-防老剂4010NA:1份4.加固剂-石蜡:2份-草酸石墨:1份5.软化剂-塑化剂DAE:5份6.加工助剂-偏磷酸钠:2份-硫磺:2份7.粘合剂-乳化胶:10份8.抗热老化剂-强力抗氧剂:2份9.其他添加剂-网络剂、硫醇交联剂等:适量以上配方的基本比例可以根据具体的要求进行调整。
制备过程如下:1.将天然橡胶、丁苯橡胶和高耐磨橡胶混合搅拌,加入到密封搅拌机中,加入适量的软化剂DAE,搅拌至均匀。
2.将碳黑、防老剂、加固剂、硫磺等添加到橡胶中,继续搅拌混合,使各成分充分分散。
3.加入粘合剂乳化胶,搅拌至均匀。
4.将网络剂和硫醇交联剂等其他添加剂适量加入橡胶中,继续搅拌混合。
5.将搅拌好的胶料放入混炼机中进行混炼,控制混炼温度、混炼时间和混炼速度,使胶料达到理想的混合效果。
6.将混炼好的胶料通过挤压机挤压成型,形成轮胎基部胶条。
以上制备过程中的温度、时间和速度等参数需要根据具体的橡胶材料和设备条件进行调整,以保证胶料的品质。
这种全钢子午线轮胎基部胶配方具有很好的耐磨性和抗剪切性能,能够提供良好的行驶稳定性和舒适性。
同时,经过适当的调整,还可以改善轮胎的抗热老化性能和湿滑性能,以满足不同路况下的要求。
轮胎胶料配方设计

轮胎胶料配方设计
设计轮胎胶料配方需要考虑以下几个方面:
1. 耐磨性:轮胎胶料需要具备较高的耐磨性,以满足长时间高速行驶的要求。
可添加磨损抗剥离剂和碳黑等填充材料来提高耐磨性。
2. 抗老化性:轮胎胶料需要具备良好的抗氧化和抗紫外线老化性能,以延长使用寿命。
可添加抗氧剂和紫外线吸收剂等添加剂来提高抗老化性。
3. 激活剂:轮胎胶料需要通过添加活化剂来促进交联反应,提高胶料的强度和耐久性。
4. 弹性和耐撕裂性:轮胎胶料需要具备较好的弹性和耐撕裂性,以确保在各种路况下的安全性能。
可添加交联剂、增韧剂和增强剂等来提高弹性和耐撕裂性。
5. 粘附性:轮胎胶料需要能够与胎面和胎体良好的粘接,以确保稳定和安全的使用。
可添加粘合剂和胶黏剂等来提高粘附性。
以上只是一些常见的考虑因素,具体的轮胎胶料配方设计还需要根据具体的应用和要求来确定,可以通过实验和测试来优化和调整配方。
全钢丝载重子午轮胎原材料及胶料配方设计
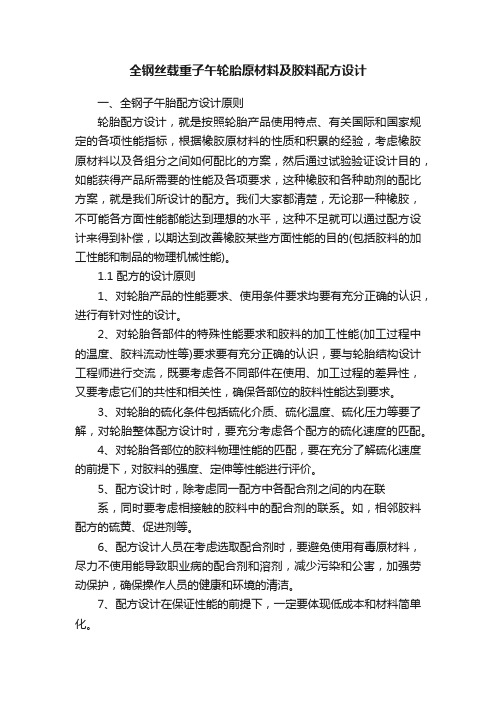
全钢丝载重子午轮胎原材料及胶料配方设计一、全钢子午胎配方设计原则轮胎配方设计,就是按照轮胎产品使用特点、有关国际和国家规定的各项性能指标,根据橡胶原材料的性质和积累的经验,考虑橡胶原材料以及各组分之间如何配比的方案,然后通过试验验证设计目的,如能获得产品所需要的性能及各项要求,这种橡胶和各种助剂的配比方案,就是我们所设计的配方。
我们大家都清楚,无论那一种橡胶,不可能各方面性能都能达到理想的水平,这种不足就可以通过配方设计来得到补偿,以期达到改善橡胶某些方面性能的目的(包括胶料的加工性能和制品的物理机械性能)。
1.1 配方的设计原则1、对轮胎产品的性能要求、使用条件要求均要有充分正确的认识,进行有针对性的设计。
2、对轮胎各部件的特殊性能要求和胶料的加工性能(加工过程中的温度、胶料流动性等)要求要有充分正确的认识,要与轮胎结构设计工程师进行交流,既要考虑各不同部件在使用、加工过程的差异性,又要考虑它们的共性和相关性,确保各部位的胶料性能达到要求。
3、对轮胎的硫化条件包括硫化介质、硫化温度、硫化压力等要了解,对轮胎整体配方设计时,要充分考虑各个配方的硫化速度的匹配。
4、对轮胎各部位的胶料物理性能的匹配,要在充分了解硫化速度的前提下,对胶料的强度、定伸等性能进行评价。
5、配方设计时,除考虑同一配方中各配合剂之间的内在联系,同时要考虑相接触的胶料中的配合剂的联系。
如,相邻胶料配方的硫黄、促进剂等。
6、配方设计人员在考虑选取配合剂时,要避免使用有毒原材料,尽力不使用能导致职业病的配合剂和溶剂,减少污染和公害,加强劳动保护,确保操作人员的健康和环境的清洁。
7、配方设计在保证性能的前提下,一定要体现低成本和材料简单化。
1.2 配方设计程序根据配方的设计原则进行配方的设计,指定配方的程序如下:1、先要调查研究,确切了解产品的具体使用条件,诸如使用温度、压力、接触的介质、受力情况等。
根据这些调节,收集有关资料,总结以前的经验教训,拟出一系列的性能指标。
- 1、下载文档前请自行甄别文档内容的完整性,平台不提供额外的编辑、内容补充、找答案等附加服务。
- 2、"仅部分预览"的文档,不可在线预览部分如存在完整性等问题,可反馈申请退款(可完整预览的文档不适用该条件!)。
- 3、如文档侵犯您的权益,请联系客服反馈,我们会尽快为您处理(人工客服工作时间:9:00-18:30)。
轮胎内胎胶配方设计
作者:张林
摘要:内胎作为汽车的重要部件扮演着重要的角色,优质的内胎在性能上有严格的要求。
通过对各种橡胶的了解及分析后,文章中进行了内胎胶配方设计。
同时文章中还阐述制品卓越的性能并对其加工设备做了讨论。
关键词:丁基橡胶;气密性;开炼机
引言
内胎是充气减震用盛气容器,所以内胎要求有良好的气密性、弹性、耐老化性。
丁基橡胶(IIR)的气密性优良,在20世纪60年代初,丁基橡胶的氯化和溴化衍生物开始商业化生产。
本文配方是在丁基橡胶基础上设计改进,该配方突出强化了其气密性,在硬度、形变方面都有显著提高。
1.配方组分及用量
原材料IIR 氧化锌硬脂酸GPF 石蜡油促进剂
DM 促进剂
DMTD
硫磺
用量100 5 1 58 16 0.5 1 1.75 2.组分作用
2.1 GPF:增大硫化胶的拉伸强度和撕裂强度。
2.2 氧化锌:提高产品的导热性能、耐磨性能、抗撕裂性能、拉伸强度。
2.3 硬脂酸:产生润滑效应,对诱导时间和硫化速度有显著影响。
2.4 石蜡油:(1)因油的添加,拉伸强度、定伸应力、硬度降低,伸长率增加;
(2)因油的添加,门尼粘度降低,门尼焦烧时间增长;
(3)因油的添加,压出性能得到一定的改善;
(4)因油的添加,耐臭氧、耐压缩永久变形、耐热性降低;
(5)因酯类增塑剂的添加,低温性能得到改善,但效果依油的型号而异;
(6)因酯类增塑剂的添加,耐压缩永久变形、耐热性降低。
2.5 促进剂DM:二硫化二苯并噻唑在无ZNO存在的条件下发生对称结构的分裂分解出并苯噻唑自由基、多硫自由基及促进剂M它们都能参与硫化反应。
生存的M发挥了M的促进硫化
功能。
在有活性剂氧化锌与硬脂酸存在的情况下它的作用与M相同,DM与硫黄一起硫化时,还分解出双基活性硫或多基活性硫可使橡胶分子进行交联。
2.6 促进剂DMTD:加速硫化链反应的引发和链增长反应,提高硫化反应速度,同时改善硫化胶的结构和性能。
2.7 硫磺:提供硫化原料。
3.加工设备
3.1 开炼机:应用于生胶的塑炼、破碎、洗涤、压片;胶料的混炼、压片以及胶料中的杂质清除;混炼胶的热炼、供胶;再生胶的粉碎、混炼、压片。
3.2 平板硫化机:主要用于硫化平型胶带,属于液压机械;主要功能是提供硫化所需的压力和温度。
3.3 橡胶注塑成型机
4.产品特点
4.1 优异的机械性能:粘结强度、抗拉强度高,弹性、延伸性能好,对于界面形变和开裂适应性强。
4.2 稳定的化学性能:具有优良的耐化学性,耐候性和耐腐蚀性。
4.3 可靠的应用性能:粘结性、防水性、密封性、耐低温性和追随性好,尺寸的稳定性好。
4.4 施工操作工艺简单
虽然该产品有众多优点,但其缺点也很明显。
典型就是生产过程中硫化速度慢, 高不饱和橡胶相比, 其硫化速度慢3倍左右, 需要高温或长时间硫化。
所以对配方的研究要进行下去,我国是车辆大国,内胎的研究发展对我国汽车行业有重大意义。
参考文献:
[1]武爱军,王丽娟.1999-2009丁基橡胶专利技术进展[J].《弹性体》,2009(10)65-70.
[2]胡开放, 刘志琴, 潘广勤, 焦宏宇, 刘秀兰[J].《广州化工》,2010.(38):11.
[3]梁星宇.丁基橡胶应用技术[M].北京:化学工业出版社,2004:1一3
[4]皮红, 周诗雨, 郭少云. 丁基橡胶的改性研究[J].高分子材料科学与工程, 2006, 22( 4) : 110- 113.
[5]张静,谢涛.合成技术研究进展述评[J].《化学工业》,2012(3):30.。