常见风电叶片问题及风电叶片检查方案
风力发电叶片问题点及解决方案

问题点及解决方案1.表面标识:(1)基线定位:SS面尖部顶点处到根部的0米中心点的直线(2)依照铺层定位点对SS面进行定位标识(3)合模通过SS面对PS面进行定位配套工具:棉绳40M,50M米尺,测距仪(标准)2.模具翼型检验:通过翼型图纸做出翼型检板,检测点一注意检板与模具表面间隙,误差值为+-0.5MM(经验值为1-2-3-4MM),二看扭角,R28M处扭角(旋长与水平线的夹角)为13.9度,误差值工艺要求为+-0.2度,(经验值为1-2度)。
配套工具,仪器:检板,角度测量仪3.根部:SS面0米处玄长测量值为1910MM,对应标准值为1890MM,其中心点到模具投影垂直距离为925MM;PS面0米处玄长测量值为1910MM,对应标准值为1890MM,其中心点到模具投影垂直距离为925MM,容易对后期打孔产生影响。
针对以上问题对SS 面采取根部补层(大致在两米位置开始,递增铺层,间距10CM-7-5CM,十层左右)使其0米处玄长达到1890MM,对PS 面采取根部侧面补层,底部打磨,使其达到标准值1883-1890 MM (叶片根部厚度大于83MM,打孔半径为16MM,叶片外径离打孔外径距离大于25MM)。
配套工具仪器:打磨机,砂纸,数显测距仪4.合模间隙检查:在SS面沿模具根部在前后缘每隔1M放置一块橡皮泥,合模后打开测量橡皮泥厚度,标准值为4+-2MM,若间隙太小,检查前后缘是否有局部过高,间隙太大,看液压是否到位,销钉有无拉紧。
若合模前后缘有错位现象2-5MM,可在后期机加工对叶片进行刮腻子铺层补强。
5.定位支架:(1)轻木中心线定位:通过R28M(扭角,涉及发电功率,零度面,三片叶片在同一旋转面上),R26.5m,35%铉长处(重心分布最均匀),向前缘偏移4度在模具上的两投影点连成一条直线,在其上找出R27M定位点。
后与根部0M中心点连成直线即可。
(2)轻木定位支架:通过轻木中心线可找出R6M,R14M,R20M处定位点因为轻木定长(90CM)。
风电机组的日常检修维护与故障处理

风电机组的日常检修维护与故障处理风电机组是利用风能转化为电能的设备,是清洁能源发电的重要载体之一。
为了确保风电机组的正常运行和发电效率,需要进行日常的检修维护和及时处理各种故障。
本文将为大家介绍风电机组的日常检修维护与故障处理方法。
一、日常检修维护1. 定期检查机组外观风电机组在运行过程中会受到风力和恶劣天气的影响,可能会导致外观损坏和腐蚀。
定期检查机组的外观情况,包括测风塔、塔筒、叶片等部位是否有损坏,保证风电机组的外观完好。
2. 检查叶片磨损情况叶片是风电机组的关键部件,受到风力和风向变化的影响较大。
定期检查叶片的磨损情况,如有磨损需要及时更换。
3. 清除尘埃和杂物风电机组在运行过程中会积累大量尘埃和杂物,影响机组的通风散热和工作效率。
定期清除尘埃和杂物,保证机组的正常运行。
4. 润滑和保养机组部件风电机组的各个部件如轴承、齿轮等需要定期进行润滑和保养,以延长使用寿命和保证运行效率。
5. 定期检查电气系统风电机组的电气系统包括发电机、变频器、控制系统等,需要定期检查各个部件的工作情况,保证电气系统的正常运行。
二、故障处理1. 叶片故障叶片故障是风电机组常见的故障之一,可能出现叶片断裂、变形等情况。
一旦发现叶片故障,需要立即停机,并进行维修或更换叶片。
2. 齿轮箱故障齿轮箱是风电机组的重要组成部分,一旦出现故障会影响整个机组的运行。
定期检查齿轮箱的润滑情况,及时更换润滑油,避免齿轮箱的故障发生。
3. 发电机故障发电机是风电机组的核心部件,一旦发生故障会导致机组停机。
定期检查发电机的绕组、绝缘等情况,保证发电机的正常运行。
4. 塔筒故障塔筒是支撑风电机组的主要结构,一旦出现裂纹、变形等情况,需要立即停机进行维修。
定期检查塔筒的结构情况,确保塔筒的安全运行。
风电机组的电气系统包括发电机、变频器、控制系统等,可能会出现电路短路、接触不良等故障。
一旦发现电气系统故障,需要及时停机,查找故障原因并进行维修。
风电设备典型质量缺陷及其控制措施
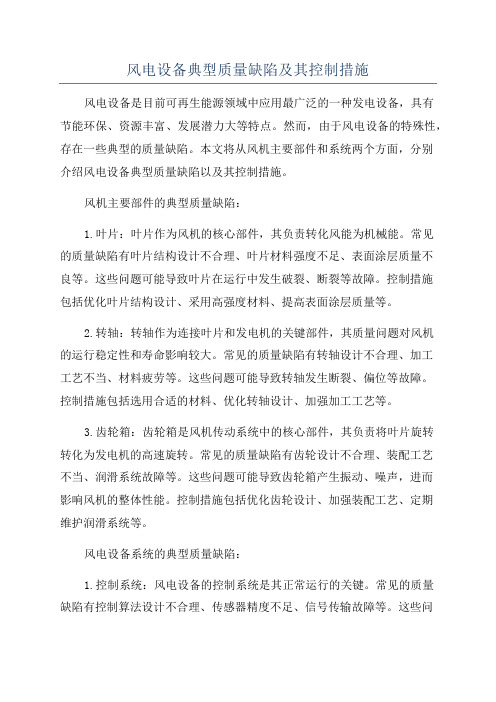
风电设备典型质量缺陷及其控制措施风电设备是目前可再生能源领域中应用最广泛的一种发电设备,具有节能环保、资源丰富、发展潜力大等特点。
然而,由于风电设备的特殊性,存在一些典型的质量缺陷。
本文将从风机主要部件和系统两个方面,分别介绍风电设备典型质量缺陷以及其控制措施。
风机主要部件的典型质量缺陷:1.叶片:叶片作为风机的核心部件,其负责转化风能为机械能。
常见的质量缺陷有叶片结构设计不合理、叶片材料强度不足、表面涂层质量不良等。
这些问题可能导致叶片在运行中发生破裂、断裂等故障。
控制措施包括优化叶片结构设计、采用高强度材料、提高表面涂层质量等。
2.转轴:转轴作为连接叶片和发电机的关键部件,其质量问题对风机的运行稳定性和寿命影响较大。
常见的质量缺陷有转轴设计不合理、加工工艺不当、材料疲劳等。
这些问题可能导致转轴发生断裂、偏位等故障。
控制措施包括选用合适的材料、优化转轴设计、加强加工工艺等。
3.齿轮箱:齿轮箱是风机传动系统中的核心部件,其负责将叶片旋转转化为发电机的高速旋转。
常见的质量缺陷有齿轮设计不合理、装配工艺不当、润滑系统故障等。
这些问题可能导致齿轮箱产生振动、噪声,进而影响风机的整体性能。
控制措施包括优化齿轮设计、加强装配工艺、定期维护润滑系统等。
风电设备系统的典型质量缺陷:1.控制系统:风电设备的控制系统是其正常运行的关键。
常见的质量缺陷有控制算法设计不合理、传感器精度不足、信号传输故障等。
这些问题可能导致风机的控制精度不高,甚至无法正常运行。
控制措施包括优化控制算法、选用高精度传感器、保证信号传输的稳定性等。
2.变频系统:风电设备的变频系统负责将从发电机输出的交流电转换为网电。
常见的质量缺陷有变频器设计不合理、电容器寿命较短、电路故障等。
这些问题可能导致变频器无法正常工作,进而影响风电设备的发电能力。
控制措施包括优化变频器设计、选用高质量的电容器、定期检查电路故障等。
3.环境监测系统:风电设备的环境监测系统负责监测风速、风向等环境参数,以便调整风机的工作状态。
风机叶片故障诊断及状态评估方法研究
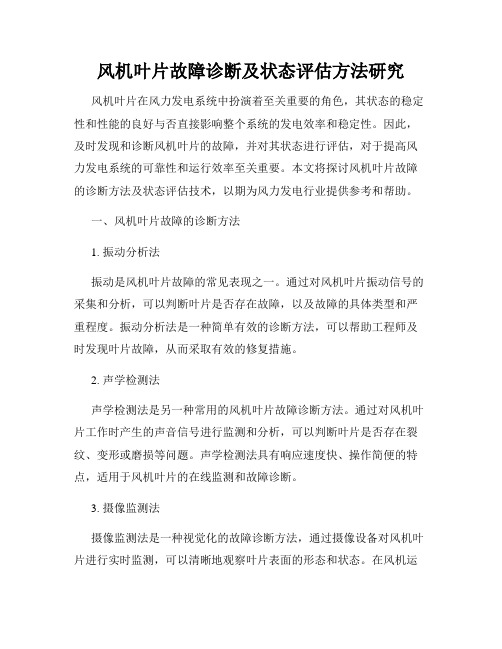
风机叶片故障诊断及状态评估方法研究风机叶片在风力发电系统中扮演着至关重要的角色,其状态的稳定性和性能的良好与否直接影响整个系统的发电效率和稳定性。
因此,及时发现和诊断风机叶片的故障,并对其状态进行评估,对于提高风力发电系统的可靠性和运行效率至关重要。
本文将探讨风机叶片故障的诊断方法及状态评估技术,以期为风力发电行业提供参考和帮助。
一、风机叶片故障的诊断方法1. 振动分析法振动是风机叶片故障的常见表现之一。
通过对风机叶片振动信号的采集和分析,可以判断叶片是否存在故障,以及故障的具体类型和严重程度。
振动分析法是一种简单有效的诊断方法,可以帮助工程师及时发现叶片故障,从而采取有效的修复措施。
2. 声学检测法声学检测法是另一种常用的风机叶片故障诊断方法。
通过对风机叶片工作时产生的声音信号进行监测和分析,可以判断叶片是否存在裂纹、变形或磨损等问题。
声学检测法具有响应速度快、操作简便的特点,适用于风机叶片的在线监测和故障诊断。
3. 摄像监测法摄像监测法是一种视觉化的故障诊断方法,通过摄像设备对风机叶片进行实时监测,可以清晰地观察叶片表面的形态和状态。
在风机运行过程中,工程师可以通过摄像监测法及时发现叶片的损坏和异常情况,为后续的维护工作提供重要参考。
二、风机叶片状态评估方法1. 数据分析法数据分析是评估风机叶片状态的关键步骤,通过对叶片运行数据的采集和处理,可以建立叶片的状态模型,实现对叶片状态的定量评估。
数据分析方法包括故障模式识别、状态估计和健康评估等技术,可以全面、准确地评估风机叶片的工作状态。
2. 超声波检测法超声波检测法是一种高精度的风机叶片状态评估方法,通过超声波传感器对叶片进行扫描和检测,可以检测叶片内部的裂纹、腐蚀和变形等问题。
超声波检测法具有灵敏度高、分辨率好的特点,可以帮助工程师准确评估叶片的健康状况。
3. 热成像技术热成像技术是一种无损检测风机叶片状态的先进方法,通过红外热像仪对叶片表面的温度进行监测和分析,可以快速、全面地评估叶片的工作状态。
风力发电机故障诊断技术分析

风力发电机故障诊断技术分析摘要:随着风电的发展,风机分布及风力机选型问题是风电场经营者必须考虑因素,尽可能地保证机组的发电能力,该试验不仅证实机组可以按照设计要求安全运行,同时也对其发电能力进行了验证,基于此,本文对风力发电机组常见运行故障以及风力发电机故障诊断技术的措施进行了分析。
关键词:风力发电;机组;故障诊断;故障预测1 风力发电机组常见运行故障1.1 叶片故障风力发电机组中叶片是其主要构件之一。
机组在工作过程中叶片将承受十分巨大的压力,由于机组全天候运作,因此叶片承受的压力会伴随在机组运行全程,是最容易出现故障的构件之一。
比如,叶片运行时会和蒸汽和空气接触,在压力的影响下会加快叶片腐蚀,从而出现陀螺的问题。
当叶片运作时间过长时,内部配件容易出现松动的问题,从而导致叶片连接不稳定,引发故障。
如果叶片受外力影响产生裂纹及形变,将释放出高频瞬态的声发射信号,此信号是叶片损伤评估的主要途径之一。
当叶片出现故障后,将导致叶片的转子受力失衡,此种受力会通过主轴传送到机组内部,从而导致机舱出现震动,轻者导致局部故障,重者导致机组基础失衡。
1.2 齿轮箱故障风力发电机组中齿轮箱的作用是连接机组主轴和发电机,可让主轴转速更快,一方面满足机组运行需求,另一方面提升经济效益。
齿轮箱中包含行星齿轮和两级平行齿轮两部分,由于齿轮箱工况恶劣,且运行中受力情况复杂,当机组处于运行状态时很容易对齿轮箱施加冲击力与交变应力,促使齿轮箱出现磨损、滑动等问题。
齿轮箱作为内部构件,大多数情况不暴露在空气中,因此发生故障的几率很小。
即便如此,齿轮箱仍然是故障诊断与异常排查的重要环节,这是因为齿轮箱故障后机组将无法运行,并且齿轮箱维修周期较长,且维修费用高昂,所以齿轮箱故障诊断是近年风电机组故障诊断的核心方向,是确保风电机组稳定运行的基础。
2 风力发电机故障诊断技术的措施2.1 实施高电压状态、低电压状态短时运行策略使双馈风力发电机组具备高电压穿越的能力;在以上措施的基础上,再增加如下技术措施:(1)当电网电压出现过低时,动态调节风力发电机的定子和网侧变频器GSC的无功功率,结合高阻抗电压的变压器,能将风机出口电压最大上调20%Un,让双馈风力发电机组在较低电压状态下短时运行;(2)当电网电压出现异常增高时,动态调节风力发电机的定子和网侧变频器GSC的无功功率,结合高阻抗电压的变压器,能将风机出口电压最大下调20%Un,让双馈风力发电机组在较高电压状态下短时运行;所述Un为风力发电机组额定电压。
风力发电机组叶片常见缺陷
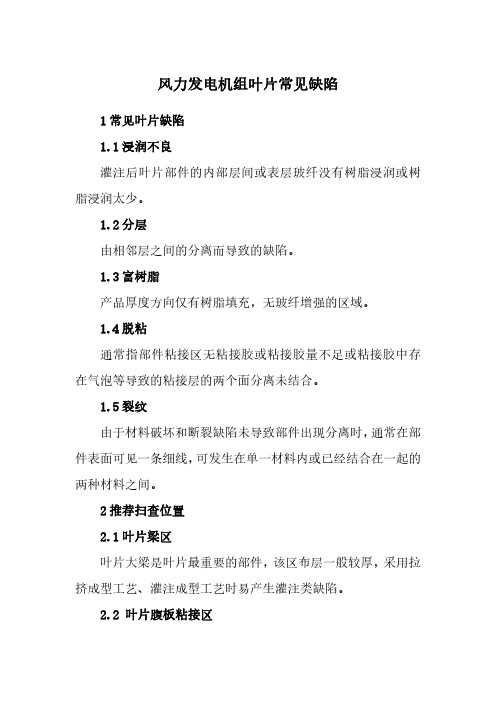
风力发电机组叶片常见缺陷
1常见叶片缺陷
1.1浸润不良
灌注后叶片部件的内部层间或表层玻纤没有树脂浸润或树脂浸润太少。
1.2分层
由相邻层之间的分离而导致的缺陷。
1.3富树脂
产品厚度方向仅有树脂填充,无玻纤增强的区域。
1.4脱粘
通常指部件粘接区无粘接胶或粘接胶量不足或粘接胶中存在气泡等导致的粘接层的两个面分离未结合。
1.5裂纹
由于材料破坏和断裂缺陷未导致部件出现分离时,通常在部件表面可见一条细线,可发生在单一材料内或已经结合在一起的两种材料之间。
2推荐扫查位置
2.1叶片梁区
叶片大梁是叶片最重要的部件,该区布层一般较厚,采用拉挤成型工艺、灌注成型工艺时易产生灌注类缺陷。
2.2叶片腹板粘接区
叶片腹板粘接区是梁与腹板法兰的结合位置,包括后缘梁区的小腹板和大梁区的主腹板,生产过程中易产生粘接类缺陷。
2.3叶片前缘粘接区
叶片前缘粘接区主要是前缘粘接角与叶片蒙皮的胶结区域,在粘接过程中易产生粘接类缺陷。
2.4叶片后缘粘接区
叶片后缘粘接区主要是后缘粘接角、后缘合模PVC(聚氯乙烯发泡板材)和后缘蒙皮粘接区,在粘接过程中易产生粘接类缺陷。
2.5叶根区域
叶根区域为玻璃钢与金属接头结合区域,有较厚的玻纤布层,易发生未灌透,浸润不良,富树脂,夹杂等缺陷。
叶片损坏的现象、原因及处理

叶片损坏的现象、原因及处理
叶片损坏是指风力发电机或者风扇等设备中的叶片出现破损、
断裂或者变形的现象。
这种损坏可能会导致设备性能下降甚至完全
失效,因此需要及时处理。
叶片损坏的原因可能有多种,包括以下
几点:
1. 外部碰撞,叶片在运行过程中可能会受到外部物体的撞击,
比如风力发电机叶片可能会被飞离的物体或者鸟类撞击,导致叶片
损坏。
2. 材料疲劳,叶片长时间受到风力或者其他外部力的作用,可
能导致材料疲劳,从而出现裂纹或者断裂。
3. 制造缺陷,叶片在制造过程中可能存在缺陷,比如材料不均匀、结构设计缺陷等,可能导致叶片在运行过程中损坏。
处理叶片损坏的方法可以从多个角度来考虑:
1. 检修维护,定期对叶片进行检查,及时发现潜在的损坏迹象,采取维修措施,可以有效减少因叶片损坏而导致的故障。
2. 强化设计,对叶片的材料和结构进行优化设计,增加其抗风能力和抗外部冲击能力,减少损坏的可能性。
3. 及时更换,一旦发现叶片损坏,应及时更换叶片,以免影响设备的正常运行。
4. 加强保护,可以在叶片周围增加防护措施,比如安装网罩或者其他防护设施,减少外部物体对叶片的损坏。
总之,对叶片损坏问题,需要综合考虑预防和及时处理两个方面,以确保设备的安全运行和性能稳定。
风电机组叶片防雷检查
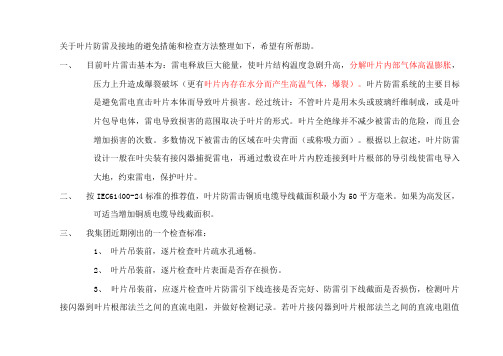
关于叶片防雷及接地的避免措施和检查方法整理如下,希望有所帮助。
一、目前叶片雷击基本为:雷电释放巨大能量,使叶片结构温度急剧升高,分解叶片内部气体高温膨胀,压力上升造成爆裂破坏(更有叶片内存在水分而产生高温气体,爆裂)。
叶片防雷系统的主要目标是避免雷电直击叶片本体而导致叶片损害。
经过统计:不管叶片是用木头或玻璃纤维制成,或是叶片包导电体,雷电导致损害的范围取决于叶片的形式。
叶片全绝缘并不减少被雷击的危险,而且会增加损害的次数。
多数情况下被雷击的区域在叶尖背面(或称吸力面)。
根据以上叙述,叶片防雷设计一般在叶尖装有接闪器捕捉雷电,再通过敷设在叶片内腔连接到叶片根部的导引线使雷电导入大地,约束雷电,保护叶片。
二、按IEC61400-24标准的推荐值,叶片防雷击铜质电缆导线截面积最小为50平方毫米。
如果为高发区,可适当增加铜质电缆导线截面积。
三、我集团近期刚出的一个检查标准:1、叶片吊装前,逐片检查叶片疏水孔通畅。
2、叶片吊装前,逐片检查叶片表面是否存在损伤。
3、叶片吊装前,应逐片检查叶片防雷引下线连接是否完好、防雷引下线截面是否损伤,检测叶片接闪器到叶片根部法兰之间的直流电阻,并做好检测记录。
若叶片接闪器到叶片根部法兰之间的直流电阻值高于20 mΩ,应仔细检查防雷引下线各连接点联接是否存在问题。
叶片接闪器到叶片根部法兰之间直流电阻测量采用直流微欧计、双臂电桥或直流电阻测试仪(仪器分辨率不低于 1 mΩ),采用四端子法测量,检查叶片叶尖及叶片上全部接闪点与叶片根部法兰之间直流电阻,每点应测三次取平均值。
4、机组吊装前后,应检查变桨轴承、主轴承、偏航轴承上的泄雷装置(碳刷、滑环、放电间隙等)的完好性,并确认塔筒跨接线连接可靠。
表1 防雷检查及测试验收清单。
关于风电叶片运行中出现缺陷的分析
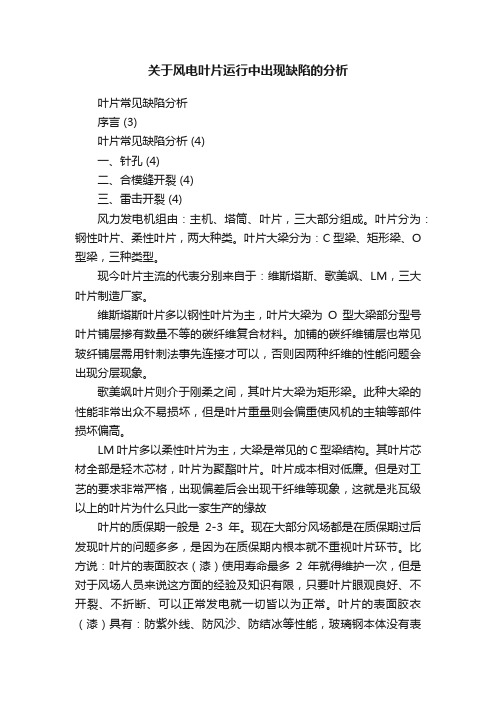
关于风电叶片运行中出现缺陷的分析叶片常见缺陷分析序言 (3)叶片常见缺陷分析 (4)一、针孔 (4)二、合模缝开裂 (4)三、雷击开裂 (4)风力发电机组由:主机、塔筒、叶片,三大部分组成。
叶片分为:钢性叶片、柔性叶片,两大种类。
叶片大梁分为:C型梁、矩形梁、O 型梁,三种类型。
现今叶片主流的代表分别来自于:维斯塔斯、歌美飒、LM,三大叶片制造厂家。
维斯塔斯叶片多以钢性叶片为主,叶片大梁为O型大梁部分型号叶片铺层掺有数量不等的碳纤维复合材料。
加铺的碳纤维铺层也常见玻纤铺层需用针刺法事先连接才可以,否则因两种纤维的性能问题会出现分层现象。
歌美飒叶片则介于刚柔之间,其叶片大梁为矩形梁。
此种大梁的性能非常出众不易损坏,但是叶片重量则会偏重使风机的主轴等部件损坏偏高。
LM叶片多以柔性叶片为主,大梁是常见的C型梁结构。
其叶片芯材全部是轻木芯材,叶片为聚酯叶片。
叶片成本相对低廉。
但是对工艺的要求非常严格,出现偏差后会出现干纤维等现象,这就是兆瓦级以上的叶片为什么只此一家生产的缘故叶片的质保期一般是2-3年。
现在大部分风场都是在质保期过后发现叶片的问题多多,是因为在质保期内根本就不重视叶片环节。
比方说:叶片的表面胶衣(漆)使用寿命最多2年就得维护一次,但是对于风场人员来说这方面的经验及知识有限,只要叶片眼观良好、不开裂、不折断、可以正常发电就一切皆以为正常。
叶片的表面胶衣(漆)具有:防紫外线、防风沙、防结冰等性能,玻璃钢本体没有表面涂层保护直接与阳光、风砂、酸雨接触就会出现发白、分层等现象久而久之会演变成更大缺陷或事故。
因此建议叶片以维护为主,大修为辅的原则。
来保证叶片的使用寿命及利用率。
叶片常见缺陷分析一、针孔叶片针孔是出厂时就没有处理完全,此种缺陷类似于千里河堤馈与蝼蚁。
二、合模缝开裂此种缺陷产生原因有粘接面未处理达标、所致风机的急停次数过于频繁,两种原因三、雷击开裂此类缺陷产生的几大原因分为:瞬间过流值大于设计、接闪器脱落、接闪器表面污垢、未击到接闪器、导线断裂。
如何做好风电叶片缺陷的检测工作
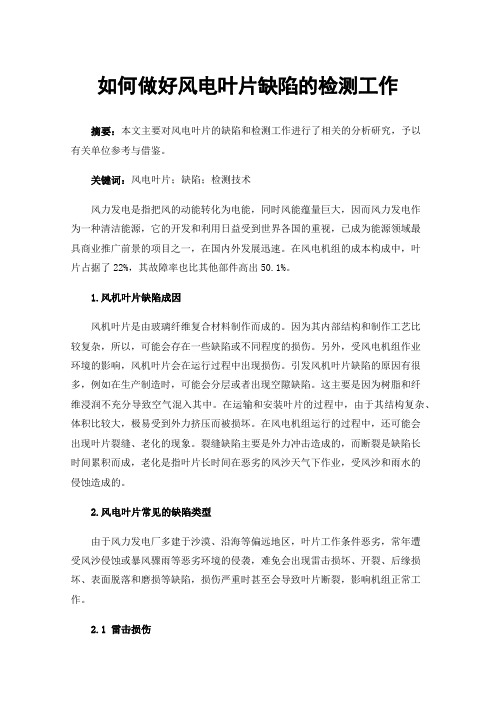
如何做好风电叶片缺陷的检测工作摘要:本文主要对风电叶片的缺陷和检测工作进行了相关的分析研究,予以有关单位参考与借鉴。
关键词:风电叶片;缺陷;检测技术风力发电是指把风的动能转化为电能,同时风能蕴量巨大,因而风力发电作为一种清洁能源,它的开发和利用日益受到世界各国的重视,已成为能源领域最具商业推广前景的项目之一,在国内外发展迅速。
在风电机组的成本构成中,叶片占据了22%,其故障率也比其他部件高出50.1%。
1.风机叶片缺陷成因风机叶片是由玻璃纤维复合材料制作而成的。
因为其内部结构和制作工艺比较复杂,所以,可能会存在一些缺陷或不同程度的损伤。
另外,受风电机组作业环境的影响,风机叶片会在运行过程中出现损伤。
引发风机叶片缺陷的原因有很多,例如在生产制造时,可能会分层或者出现空隙缺陷。
这主要是因为树脂和纤维浸润不充分导致空气混入其中。
在运输和安装叶片的过程中,由于其结构复杂、体积比较大,极易受到外力挤压而被损坏。
在风电机组运行的过程中,还可能会出现叶片裂缝、老化的现象。
裂缝缺陷主要是外力冲击造成的,而断裂是缺陷长时间累积而成,老化是指叶片长时间在恶劣的风沙天气下作业,受风沙和雨水的侵蚀造成的。
2.风电叶片常见的缺陷类型由于风力发电厂多建于沙漠、沿海等偏远地区,叶片工作条件恶劣,常年遭受风沙侵蚀或暴风骤雨等恶劣环境的侵袭,难免会出现雷击损坏、开裂、后缘损坏、表面脱落和磨损等缺陷,损伤严重时甚至会导致叶片断裂,影响机组正常工作。
2.1雷击损伤为了有效利用风能资源,风力发电机组通常被安装在地势较高的区域,而叶片是风机中位置最高的部件,易受雷电影响。
雷电击中风机叶片时,其释放的能量使得叶片内部结构的温度急剧升高,造成叶片表面复合材料灼烧,导致叶片表面出现不同程度的损伤。
2.2边缘开裂复杂的生产工艺过程使得风机叶片的质量参差不齐,受叶片粘合处缝隙含胶量不均或固化不完全等因素的影响,风机叶片在运转过程中会出现内粘合缝处开裂,尤其是叶尖和叶片迎风面的中部区域,是风机叶片最易受损、开裂的部位。
风电场风力发电机组叶片断裂后如何检查分析
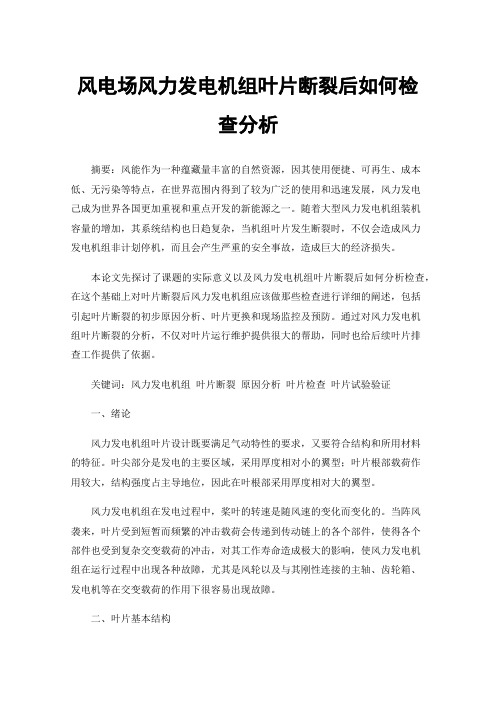
风电场风力发电机组叶片断裂后如何检查分析摘要:风能作为一种蕴藏量丰富的自然资源,因其使用便捷、可再生、成本低、无污染等特点,在世界范围内得到了较为广泛的使用和迅速发展,风力发电己成为世界各国更加重视和重点开发的新能源之一。
随着大型风力发电机组装机容量的增加,其系统结构也日趋复杂,当机组叶片发生断裂时,不仅会造成风力发电机组非计划停机,而且会产生严重的安全事故,造成巨大的经济损失。
本论文先探讨了课题的实际意义以及风力发电机组叶片断裂后如何分析检查,在这个基础上对叶片断裂后风力发电机组应该做那些检查进行详细的阐述,包括引起叶片断裂的初步原因分析、叶片更换和现场监控及预防。
通过对风力发电机组叶片断裂的分析,不仅对叶片运行维护提供很大的帮助,同时也给后续叶片排查工作提供了依据。
关键词:风力发电机组叶片断裂原因分析叶片检查叶片试验验证一、绪论风力发电机组叶片设计既要满足气动特性的要求,又要符合结构和所用材料的特征。
叶尖部分是发电的主要区域,采用厚度相对小的翼型;叶片根部载荷作用较大,结构强度占主导地位,因此在叶根部采用厚度相对大的翼型。
风力发电机组在发电过程中,桨叶的转速是随风速的变化而变化的。
当阵风袭来,叶片受到短暂而频繁的冲击载荷会传递到传动链上的各个部件,使得各个部件也受到复杂交变载荷的冲击,对其工作寿命造成极大的影响,使风力发电机组在运行过程中出现各种故障,尤其是风轮以及与其刚性连接的主轴、齿轮箱、发电机等在交变载荷的作用下很容易出现故障。
二、叶片基本结构目前叶片主要采用玻璃纤维增强材料制造,主要制造步骤如下:2.1制造生产叶片的外型模具;2.2按照生产工艺,布置玻璃纤维布、芯材和雷电保护装置以及生产部分预制件;2.3真空导入树脂,固化后合模或整体灌注成型工艺成型,为叶片整体灌注成型(在模具内);2.4脱模、打磨、打孔、布置螺栓、喷漆等工艺;叶片主要由主体、雷电保护、人孔盖板组、叶根螺栓组、刻度牌等组成。
叶片排查方案

叶片排查方案1. 简介叶片在许多机械设备中扮演着重要角色,包括风力发电机、涡轮机、风扇等。
叶片的损坏或故障可能会导致设备性能下降甚至完全失效。
因此,定期进行叶片的排查和检测非常重要。
本文档将介绍一个可行的叶片排查方案,详细描述了排查的步骤和工具。
2. 排查步骤步骤一:目视检查首先,进行目视检查以初步评估叶片的整体情况。
这可以通过裸眼检查或辅助工具(如望远镜)进行。
以下是目视检查的几个关键方面: - 叶片表面状况:检查是否有划痕、凹陷、裂缝等可见的损伤。
- 叶片结构完整性:检查叶片是否完整且没有松动的连接部分。
- 叶片污垢:检查是否有严重积尘或污垢,可能会影响叶片的性能。
步骤二:使用触摸检查触摸检查可以进一步评估叶片的结构和表面状况。
这可以通过手触叶片表面进行。
以下是触摸检查的几个关键方面: - 表面平整性:检查叶片表面是否平滑,是否有突起或凹陷。
- 粘性物质:检查是否有洞穴内的胶水、涂层或其他粘性物质。
步骤三:使用光学检查工具光学检查工具可以提供更精确和详细的叶片排查信息。
以下是几种常用的光学检查工具: - 放大镜:用于检查细小的损伤,如裂纹或划痕。
- 红外热像仪:用于检测叶片的温度分布,以确定潜在的热问题。
- 激光扫描仪:用于生成叶片的三维模型,以检测形状变化或缺陷。
步骤四:振动分析振动分析可以帮助判断叶片是否出现脆性破裂或松动。
以下是几种常用的振动分析方法: - 振动传感器:安装振动传感器来检测叶片的振动频率和幅度。
- 频谱分析:通过分析振动信号的频谱图,可以确定叶片是否存在异常振动频率。
3. 工具清单•目视检查:–裸眼–望远镜•触摸检查:–手•光学检查:–放大镜–红外热像仪–激光扫描仪•振动分析:–振动传感器–频谱分析仪4. 结论通过使用上述的叶片排查方案,可以及时发现和修复叶片的问题,确保机械设备的正常运行和性能。
定期进行叶片的排查可以提高设备的可靠性和寿命,减少故障和损失。
风机叶片的常见故障类型及诊断技术
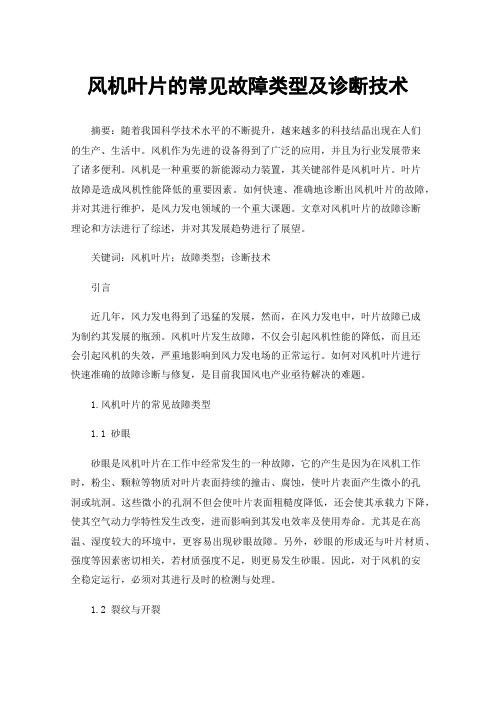
风机叶片的常见故障类型及诊断技术摘要:随着我国科学技术水平的不断提升,越来越多的科技结晶出现在人们的生产、生活中。
风机作为先进的设备得到了广泛的应用,并且为行业发展带来了诸多便利。
风机是一种重要的新能源动力装置,其关键部件是风机叶片。
叶片故障是造成风机性能降低的重要因素。
如何快速、准确地诊断出风机叶片的故障,并对其进行维护,是风力发电领域的一个重大课题。
文章对风机叶片的故障诊断理论和方法进行了综述,并对其发展趋势进行了展望。
关键词:风机叶片;故障类型;诊断技术引言近几年,风力发电得到了迅猛的发展,然而,在风力发电中,叶片故障已成为制约其发展的瓶颈。
风机叶片发生故障,不仅会引起风机性能的降低,而且还会引起风机的失效,严重地影响到风力发电场的正常运行。
如何对风机叶片进行快速准确的故障诊断与修复,是目前我国风电产业亟待解决的难题。
1.风机叶片的常见故障类型1.1 砂眼砂眼是风机叶片在工作中经常发生的一种故障,它的产生是因为在风机工作时,粉尘、颗粒等物质对叶片表面持续的撞击、腐蚀,使叶片表面产生微小的孔洞或坑洞。
这些微小的孔洞不但会使叶片表面粗糙度降低,还会使其承载力下降,使其空气动力学特性发生改变,进而影响到其发电效率及使用寿命。
尤其是在高温、湿度较大的环境中,更容易出现砂眼故障。
另外,砂眼的形成还与叶片材质、强度等因素密切相关,若材质强度不足,则更易发生砂眼。
因此,对于风机的安全稳定运行,必须对其进行及时的检测与处理。
1.2 裂纹与开裂在风机中,由于疲劳载荷、高温及过载等原因,往往会引起叶片断裂。
这些都是造成叶片材料强度、韧性降低,并产生微裂缝的主要原因。
随着使用时间的延长,这些裂纹会逐步扩展,并最终引起叶片断裂。
裂纹的产生会使叶片的强度、刚度等性能下降,并加速了裂纹的扩展。
若得不到及时的处理,将会引起风机整体的破坏,对风电场的安全可靠运行构成巨大威胁。
所以,对风机叶片的裂纹进行诊断是十分必要的,这样才能对其进行及时的检测与修补,从而保证风机叶片的正常运转。
风力机叶片故障分析及运维管理
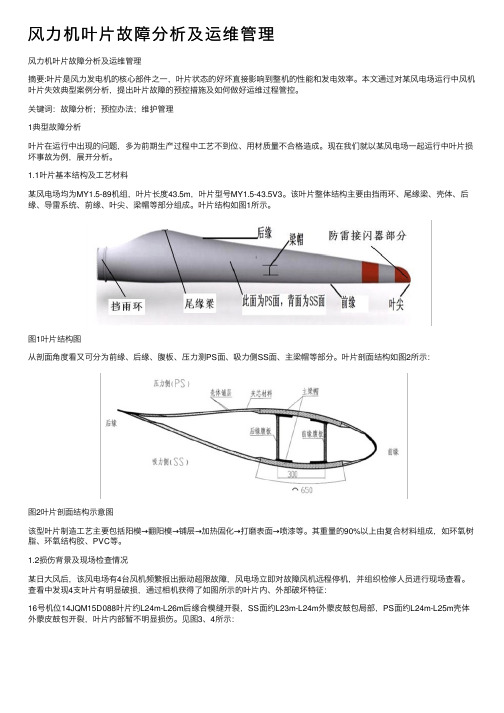
风⼒机叶⽚故障分析及运维管理风⼒机叶⽚故障分析及运维管理摘要:叶⽚是风⼒发电机的核⼼部件之⼀,叶⽚状态的好坏直接影响到整机的性能和发电效率。
本⽂通过对某风电场运⾏中风机叶⽚失效典型案例分析,提出叶⽚故障的预控措施及如何做好运维过程管控。
关键词:故障分析;预控办法;维护管理1典型故障分析叶⽚在运⾏中出现的问题,多为前期⽣产过程中⼯艺不到位、⽤材质量不合格造成。
现在我们就以某风电场⼀起运⾏中叶⽚损坏事故为例,展开分析。
1.1叶⽚基本结构及⼯艺材料某风电场均为MY1.5-89机组,叶⽚长度43.5m,叶⽚型号MY1.5-43.5V3。
该叶⽚整体结构主要由挡⾬环、尾缘梁、壳体、后缘、导雷系统、前缘、叶尖、梁帽等部分组成。
叶⽚结构如图1所⽰。
图1叶⽚结构图从剖⾯⾓度看⼜可分为前缘、后缘、腹板、压⼒测PS⾯、吸⼒侧SS⾯、主梁帽等部分。
叶⽚剖⾯结构如图2所⽰:图2叶⽚剖⾯结构⽰意图该型叶⽚制造⼯艺主要包括阳模→翻阳模→铺层→加热固化→打磨表⾯→喷漆等。
其重量的90%以上由复合材料组成,如环氧树脂、环氧结构胶、PVC等。
1.2损伤背景及现场检查情况某⽇⼤风后,该风电场有4台风机频繁报出振动超限故障,风电场⽴即对故障风机远程停机,并组织检修⼈员进⾏现场查看。
查看中发现4⽀叶⽚有明显破损,通过相机获得了如图所⽰的叶⽚内、外部破坏特征:16号机位14JQM15D088叶⽚约L24m-L26m后缘合模缝开裂,SS⾯约L23m-L24m外蒙⽪⿎包局部,PS⾯约L24m-L25m壳体外蒙⽪⿎包开裂,叶⽚内部暂不明显损伤。
见图3、4所⽰:图3 叶⽚内部损伤照⽚图4叶⽚外部损伤照⽚19号机位14JQM15D075叶⽚L22m-L30m后缘合模缝开裂,合模缝严重变形,SS⾯L15m-L29m 壳体内外蒙⽪⿎包局部开裂,SS⾯L18m-L24m处壳体外蒙⽪开裂脱落长度6m、宽度2m, PS⾯L13m-L27m壳体内外蒙⽪⿎包局部开裂。
风力发电场中叶片损伤检测与修复
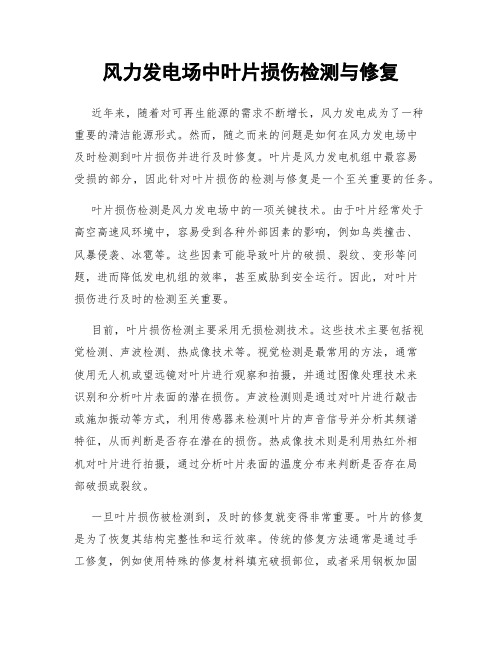
风力发电场中叶片损伤检测与修复近年来,随着对可再生能源的需求不断增长,风力发电成为了一种重要的清洁能源形式。
然而,随之而来的问题是如何在风力发电场中及时检测到叶片损伤并进行及时修复。
叶片是风力发电机组中最容易受损的部分,因此针对叶片损伤的检测与修复是一个至关重要的任务。
叶片损伤检测是风力发电场中的一项关键技术。
由于叶片经常处于高空高速风环境中,容易受到各种外部因素的影响,例如鸟类撞击、风暴侵袭、冰雹等。
这些因素可能导致叶片的破损、裂纹、变形等问题,进而降低发电机组的效率,甚至威胁到安全运行。
因此,对叶片损伤进行及时的检测至关重要。
目前,叶片损伤检测主要采用无损检测技术。
这些技术主要包括视觉检测、声波检测、热成像技术等。
视觉检测是最常用的方法,通常使用无人机或望远镜对叶片进行观察和拍摄,并通过图像处理技术来识别和分析叶片表面的潜在损伤。
声波检测则是通过对叶片进行敲击或施加振动等方式,利用传感器来检测叶片的声音信号并分析其频谱特征,从而判断是否存在潜在的损伤。
热成像技术则是利用热红外相机对叶片进行拍摄,通过分析叶片表面的温度分布来判断是否存在局部破损或裂纹。
一旦叶片损伤被检测到,及时的修复就变得非常重要。
叶片的修复是为了恢复其结构完整性和运行效率。
传统的修复方法通常是通过手工修复,例如使用特殊的修复材料填充破损部位,或者采用钢板加固等手段。
然而,这种修复方法存在一定的局限性,例如需要大量人力和物力,修复效果难以保证等。
近年来,随着材料科学和机器人技术的进步,出现了一些新的叶片修复方法。
其中一种方法是利用复合材料修复叶片。
复合材料具有优异的力学性能和耐久性,可以有效地提高叶片的结构强度和抗风能力。
修复过程可以通过手工施工或者使用机器人进行自动化修复。
另一种趋势是采用3D打印技术进行叶片修复。
3D打印技术可以根据叶片的设计需求来精确打印修复材料,大大提高修复效果和工作效率。
除了及时检测和修复叶片损伤,预防叶片损伤也是非常重要的。
试论风力发电厂风机叶片检测与维修
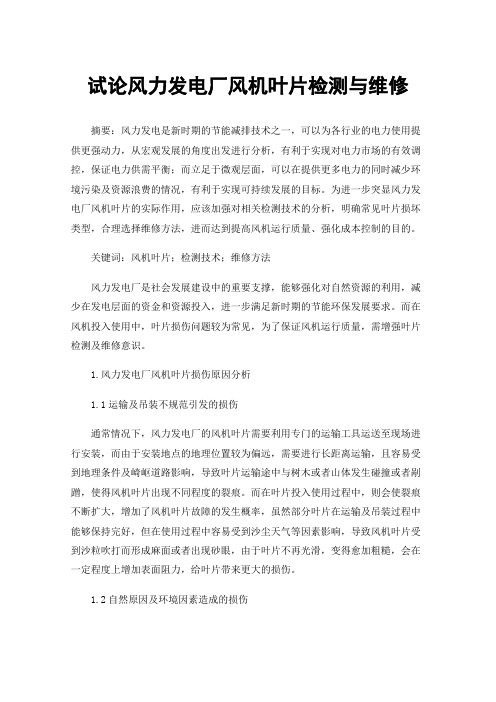
试论风力发电厂风机叶片检测与维修摘要:风力发电是新时期的节能减排技术之一,可以为各行业的电力使用提供更强动力,从宏观发展的角度出发进行分析,有利于实现对电力市场的有效调控,保证电力供需平衡;而立足于微观层面,可以在提供更多电力的同时减少环境污染及资源浪费的情况,有利于实现可持续发展的目标。
为进一步突显风力发电厂风机叶片的实际作用,应该加强对相关检测技术的分析,明确常见叶片损坏类型,合理选择维修方法,进而达到提高风机运行质量、强化成本控制的目的。
关键词:风机叶片;检测技术;维修方法风力发电厂是社会发展建设中的重要支撑,能够强化对自然资源的利用,减少在发电层面的资金和资源投入,进一步满足新时期的节能环保发展要求。
而在风机投入使用中,叶片损伤问题较为常见,为了保证风机运行质量,需增强叶片检测及维修意识。
1.风力发电厂风机叶片损伤原因分析1.1运输及吊装不规范引发的损伤通常情况下,风力发电厂的风机叶片需要利用专门的运输工具运送至现场进行安装,而由于安装地点的地理位置较为偏远,需要进行长距离运输,且容易受到地理条件及崎岖道路影响,导致叶片运输途中与树木或者山体发生碰撞或者剐蹭,使得风机叶片出现不同程度的裂痕。
而在叶片投入使用过程中,则会使裂痕不断扩大,增加了风机叶片故障的发生概率,虽然部分叶片在运输及吊装过程中能够保持完好,但在使用过程中容易受到沙尘天气等因素影响,导致风机叶片受到沙粒吹打而形成麻面或者出现砂眼,由于叶片不再光滑,变得愈加粗糙,会在一定程度上增加表面阻力,给叶片带来更大的损伤。
1.2自然原因及环境因素造成的损伤除了运输及吊装环节容易损伤风机叶片,还会因为自然因素造成风机叶片的损伤,在雷击方面有明显体现,例如,风力发电厂缺少防雷设施或者防雷系统出现异常,则容易在雷雨天气时,遭受到雷电攻击,在没有避雷措施的情况下,雷电电流会直接传到发电机位置,引发风机叶片的破损,只有保证避雷措施完善的情况下,才能强化对风机叶片的有效保护,减少雷击带来的损伤。
风电机组的日常检修维护与故障处理

风电机组的日常检修维护与故障处理风电机组是一种利用风能转化为电能的设备,其运行质量和状况对发电的效率和稳定性有着至关重要的影响。
日常检修维护与故障处理是维持风电机组运行效率和稳定性的关键环节,下面将对其进行更详细地阐述。
一、日常检修维护1、风机叶片的检查和清洗维护风机叶片是风电机组的核心部件,其状态的好坏对发电效率和总体运行状况有着重要的影响。
因此,应经常检查叶片表面是否有积尘、腐蚀等问题,并及时脱掉积尘;另外,对于一些常年在强风环境下运行的风电机组,建议进行表面防腐涂层的处理,有效延长叶片的使用寿命。
2、风机轴承的保养风机轴承是整个风电机组运行过程中最易受到磨损和故障的部件之一,需要经常检查其润滑情况,并定期添加润滑剂。
另外,对于一些磨损严重的轴承,需要及时更换,避免出现严重故障。
3、电气部件的维护风电机组的电气部件也是整个系统中比较重要的部分之一,在其安装过程中,应注意防止潮湿和灰尘的污染,避免出现短路等问题。
平常会对电气部件进行检查、焊接和停电修复等操作。
二、故障处理1、叶片变形及损坏的处理由于长期受到自然风力的吹拂和冲击,风机叶片很容易发生变形或损坏。
当叶片损坏或变形时,需要及时更换或修理,以免影响发电效率和安全运行。
当风机轴承使用时间过长,或者遇到强风等不正常情况时,可能会出现故障。
此时需要及时更换风机轴承,避免出现进一步的磨损和故障。
电气故障可能会导致整机的停运,因此需要及时排查并修复。
当发现电气故障时,需要首先检查电气部件的线路连接是否牢固,电气部件内部是否有损坏,然后再进行修复和更换。
总之,风电机组的日常检修维护和故障处理工作是保证其正常运行的关键,需要时刻保持警觉,并根据情况采取相应措施,以免出现问题影响发电效率和稳定性。
- 1、下载文档前请自行甄别文档内容的完整性,平台不提供额外的编辑、内容补充、找答案等附加服务。
- 2、"仅部分预览"的文档,不可在线预览部分如存在完整性等问题,可反馈申请退款(可完整预览的文档不适用该条件!)。
- 3、如文档侵犯您的权益,请联系客服反馈,我们会尽快为您处理(人工客服工作时间:9:00-18:30)。
常见风电叶片问题及风电叶片检查方案目录catalog 01常见叶片问题及检查方法Blade inspection methods02介绍及案例展示CobotAI-B1 introduce and inspection case风电叶片容易受到强风、雷击、疲劳的影响,引起风电叶片结构损伤;且由于出厂质量影响,有些缺陷长期存在,影响叶片的可靠性。
Wind turbine blades easily affected by strong winds, lightning, fatigue, caused blades damage ; And because of the influence of the factory quality, some defects exist for a long time, the influence on the reliability of the blade随风机运行时间增长,叶片维修需求增加,但普通叶片检查只能查出表面缺陷,存在隐患,所以需要开展叶片无损内部检测。
Grow along with the running time, blade repair demand increases, but blade visual inspection only can be found surface defect, so need for a nondestructive internal inspection.分类人为检测仪器检测检测方式Inspectionway人工目测、敲击、单反相机远距拍照visual inspect , knock, take picture超声无损检测Ultrasonic红外无损检测infrared特点Feature 简单,直接,易于操作,成本较低。
叶片成型前缺陷及人不可及处缺陷无法检测,人为因素影响检验结果Simple, direct, easy tooperate, low cost . Blade moldingdefects and the person before andcannot detect flaw, human factors affectthe test result在工厂针对断层和缺胶检查,目前无法实现风场实时检测In view of thefaults and short ofglue in the factoryinspection, at presentcan't wind field real-time detection检测灵敏度高、检测速度快,检测缺陷范围广,实时成像,能够实现风场实时检测。
Highdetection sensitivity, fastdetection, real-time imaging,the testing range of the windfield can be implemented forreal-time detection.普通叶片清晰的内部结构The internal structure of ordinary blade is clear缺陷叶片内部状态Defect blade internal state红外无损检测,直观的看出叶片内部缺陷。
Infrared nondestructive inspection, it can found internal defects for blade composite materials.常见叶片问题及检查方法blade defects and inspection methods01目录catalog 01常见叶片问题及检查方法Blade inspection methods02介绍及案例展示CobotAI-B1introduce and inspection case“大眼科宝” 是一款以红外热成像专有技术为核心的风机叶片内部缺陷检测设备。
Cobot AI-B1 is a infrared thermal imagingtechnology as the core of the blade internaldefect inspection equipment.该设备具有操作灵活、检测面积大、快速准确、实时产生结果图像。
This equipment has flexible operation, largedetection area, fast, accurate and real-timeimage produced results.地面检测设备Ground inspection 高空检测设备For high position inspection适合地面叶片扫描检查。
Suitable for the ground blade scan.用于登机检查,带有柔性机械臂,可360度旋转。
To inspection with the flexible mechanical arm, can rotate 360 degrees.技术指标index技术指标technical parameters输入电压input voltageAC220V 负载功率power 2100W检测云台 robot 水平旋转360°,俯仰角运动-45°~+45°horizontal rotation360°, Pitching Angle movement-45°~+45°BMS工作温度 work temperture <75°C 检测距离Detection distance1m大眼科宝介绍及案例展示 — 设备介绍CobotAI-B1 introduce and inspection case-equipment introduce02利用龙源设备技术中心实验室风机叶片缺陷样品进行检测。
Inspection blades defect samples at Long Yuan.大眼科宝介绍及案例展示 — 实验室验证检测CobotAI-B1 introduce and inspection case-Validation inspection in lab02褶皱的检测 Wrinkle sample inspection.褶皱样品检测,清晰的显现出褶皱图像。
内部裂纹的验证检测Validation testing of the internal crack实际模块检测结果result sample检测地点place 内蒙某风电场 Inner Mongolia测试环境温度temperture -25℃叶片尺寸size长31m,最宽处3m Length 31m,most wide 3mat wind farmat wind farm壳体撞击裂纹Shell impact crack检测外部缺陷部位附近的裂纹损伤,确认损伤的范围Confirm the scope of internal damage江苏某风电场一只叶片在运输过程中撞击损伤,进行红外叶片检查。
Collision damage in transit, infraredblade inspection.大眼科宝介绍及案例展示 — 风电场地面维修叶片检测CobotAI-B1 introduce and inspection case-Blade inspection after repair 02撞击修补质量 repair quality修复质量的检测,通过对某风场修复后叶片进行扫描,在修复区域, 修补位置纹路和正常结构不一致,判断修补时未按标准作业修补且树脂过多导致,长时间运行会产生开裂等缺陷。
Repair quality inspection, in the region of the repair, repair position do not match the normal structure, not according to standard operating when repairing, long time running can producecracking and other defects大眼科宝介绍及案例展示 —风电场地面维修叶片检测CobotAI-B1 introduce and inspection case-impact crack blade inspection at wind farm02环境温度25度条件下,山东某风场检测,将检测设备放置于吊兰上,检测人员对叶片进行由下至上的实时检测。
Under the condition of environment temperature 25 degrees. Install the inspectionequipment in place bracket plant. Scan the blade from tip to root.to inspectionto inspection壳体分层 shell layered复合层分层通过红外检测,能构清晰直观的成像出分层缺陷,此类分层随着时间推移可能会逐渐扩大并使得风叶断裂。
红外检测方法可清晰的获得复合层的热成像图。
Through infrared inspection, can clear show the defects . Such layered is likely to expand and gradually make the blades break . Infrared detection method can obtain the compound layer image.气泡Air bubbles气泡是指叶片在成型过程中形成的孔洞,包括布层内纤维束内的孔隙、纤维束与纤维束之间的孔隙以及布层间的孔隙。
Bubble is refers to the blade in the process of forming hole formation, including the pore within the fiber bundle in the cloth layer, fiber beam and fiber beam between the porosity and the pore between layers.通过红外检测成像出白点,为不饱和聚酯浸透不良,有微小气泡。
Through infrared detection imaging the white points.大眼科宝介绍及案例展示 —风电场登机检测CobotAI-B1 introduce and inspection case- climb the wind turbine to inspection 02大眼科宝介绍及案例展示 — 风电场登机检测02CobotAI-B1 introduce and inspection case- climb the wind turbine to inspection主梁内部褶皱 Girder drape大眼科宝介绍及案例展示 — 风电场登机检测02CobotAI-B1 introduce and inspection case- climb the wind turbine to inspection主梁内部褶皱 Girder drape02大眼科宝介绍及案例展示 —风电场登机检测CobotAI-B1 introduce and inspection case- climb the wind turbine to inspection雷击区域检测lightning strike inspection02大眼科宝介绍及案例展示 —风电场登机检测CobotAI-B1 introduce and inspection case- climb the wind turbine to inspection叶片加长区域检测Blade extended area detection。