如何推进TPM
TPM管理推进概要

减少能源
现在
目 标
’07年上
’08年
’09年
100
100
100
100
100
—
100
110
130
90
70
110
130
90
80
110
130
300
500
90
80
D (期限)
减少急停时间
缩短保全修理时间
100
100
90
70
90
70
S (安全)
减少灾害(工伤/火灾)
增加改善亮点
削减额率
人事费用的削减
减少人员数
减少人员数×薪给
时间的短缩
处理时间、回收时间
短缩时间×薪给率
提升机能效率
提升总合目的性
贡献目标(例如:故障、运转、顺畅)
件数、实效数、达标率、问卷调查评核
质量的提升
失误、人手修整、重复、管理密度、调整、变更的件数
件数、精度、机率
人员的有效活用
转用、业务量增加、知识、技能水平
设备管理的误区
只有修理没有维护
不区分运转率和可动率
没有“救火”观念
单兵作战
我使用你修理
迷信设备
修理:“头疼医头脚痛医脚”。维护:预防故障。
盲目追求运转率,忽视点检保养,造成可动率低。
故障出现后,使用的急修理的不急,最后是谁都不急。
我修机械你修电路,你演戏我看戏。
使用的人不做点检保养,设备是修理人员的。
通过5感来发现缺陷
改善设备清扫困难的部位 找出发生源,并解决
制定作业者自己能够遵守的基准书
4 STEP(总点检)
最新如何推进TPM教学课件

改善 提案 小组
自主 保养 小组
生产 TPM小组 提高
教育 宣导
组
效率 计划
OEE 保养
小组
附、全员参加的重复性小组活动组织
担当理事 部长
全社 TPM推进委员会
部属长 科长 系长 班长
公司 TPM推进委员会
工厂TPM协调员和 推进办公室
科别 TPM推进委员会 支柱管理委员会
个别分会 TPM小集团
高
6 如何在全公司推行TPM
TPM的推行可按三个阶段、18个步骤来具体进行。 18个步骤并不是一成不变的,仅仅作为借鉴,应根据企业的实际需要进行调整。 经过这些步骤,企业就可以一步步把TPM推向深入
阶段
引进准备阶段 引进开始
推进实施阶段
巩固阶段
步骤
1.经营层的决策导入
2.幕僚人员的设置 3.TPM的导入教育 4.基本方针与目标的设定
个自 计 教 初 品事环 别主 划 育 期 质务境 改保 保 训 管 保改安 善全 全 练 理 全善全
重复性小组活动 彻底的5S活动
企业的 体质改善
现场的 体质改善
人员的 体质改善
5 TPM运作结构图 5.1 TPM全面展开的八项活动
• 促进生产效率化的 • 以操作者为中心的 • 以保全部门为主的 • 提升运转/保全技能的 • 导入新制品/新设备的
以生产系统整个寿命周期为对象实现
“灾害为0”、“不良为0”、“故障为0”等
TPM的推进组织为“重复小团队”
重复小团队是指从最高层、到中层,直至第一线上的小团队的各阶层互相协作活动 的组织。
4. 3TPM的两大基石
4TPM的一些特点
循序渐进---从基础作起 基石一:彻底的5S活动
精选如何推进TPM活动

3、TPM活动的推进方法
3.1 善用激励激发活性
1、 对小组活动的过程和成果应给予及时的认同、肯定2、 给予员工自主实施的机会,培育员工的自主性 ,使其亲自体验活动的快乐3 、多做鼓励性的引导工作,不要强制并不等于对活动的放任,作为TPM的领导者,要及时的给予小组活动的关注和指导,及时帮助解决TPM推进过程中遇到的困难
3.2 高素质的人才是活动前进的动力
1、 在追求活动效果的同时,我们更要多着眼于员工的成长,高素质的人才是活动前进的动力2、 作为TPM的领导者,我们要有培养人和辅导人的愿望,帮助部属的工作技能提高3、 在引进教育中,彻底的教导部属有关活动的内容,使部属充分了解活动的意义和概况4、 为了使部属理解TPM活动,自己首先要先了解教育的内容,从传达教育中去学习教导的内容,在教育的方法上多下功夫,活用所掌握的知识
以设备专业保全为中心,只有设备专业保全部门参加
从经营阶层到一线员工全员参加的小集团活动
1.5 TPM的特色
1. 追求经济性(赚钱的PM) 2. 全面系统(MP-PM-CM) PM预防保全 (为预防设备故障进行的保全活动) CM改良保全 (为提高设备的存在质量进行的改善活动) MP保全预防 (为制造不易故障,不易出不良品的设备的活动) 3. 从业人员的自主保养(小集团活动) 4. 所有部门参加的全公司活动 5. 消除所有损失(零指向)
TPM的新定义(1989至今)
以追求生产系统效率化的极限(综合效率化)改善企业体制为目标
以生产系统全体寿命周期为对象,追求”零灾害、零不良、零故障”,并将所有损失在事先加以防止
从生产部门开始,扩展到技术、管理、销售等部门
从经营阶层到第一线作业员全员参加
推进TPM活动程序

推进TPM活动程序简介总体生产维护(Total Productive Maintenance,简称TPM)是一种通过全员参与提高设备可用性和生产效率的管理方法。
在企业的生产运营中,推进TPM活动是非常重要的一环。
本文将介绍一个推进TPM活动的程序,通过这个程序,企业可以高效有序地进行TPM活动的推进。
选择推进TPM活动的理由在现代制造业中,设备的可靠性和效率对于企业的竞争力至关重要。
通过推进TPM活动,企业可以达到以下目标:1.提高设备的可用性和生产效率:通过设备的预防性维护和保养,减少因设备故障引起的停机时间,提高设备的可用性和生产效率。
2.增强员工的技术能力:通过TPM活动的培训和教育,提升员工对设备的操作和维护能力,增强他们的技术能力。
3.培养全员参与的团队合作精神:通过TPM活动的开展,促进各部门之间的合作和沟通,培养全员参与的团队合作精神。
综上所述,推进TPM活动对企业的发展和竞争力具有重要意义。
推进TPM活动程序1. 建立TPM活动小组推进TPM活动的第一步是建立一个TPM活动小组。
该小组由各个关键部门的代表组成,包括生产部门、维修部门、质量部门等。
小组成员应具备一定的技术能力和对TPM活动有一定的了解。
TPM活动小组的主要职责包括:•制定TPM活动计划和目标;•组织和协调TPM活动的各项工作;•定期评估和改进TPM活动的效果。
2. 进行设备的基础评估在推进TPM活动之前,需要对企业的设备进行基础评估。
基础评估的目的是了解设备的当前状况,包括设备的故障率、停机时间、性能指标等。
通过基础评估的结果,可以确定需要进行改进的方向和重点问题。
3. 制定TPM活动计划根据设备基础评估的结果,TPM活动小组制定具体的TPM活动计划。
活动计划应包括以下内容:•设备的预防性维护计划:制定设备的定期维护计划,包括清洁、润滑、紧固等工作;•员工培训计划:确定员工的培训内容和培训方式,提升员工对设备的操作和维护能力;•设备性能改进计划:确定设备性能改进的目标和具体措施。
TPM活动的推进步骤课件

(7)行政方面 ◇使用科技手段处理事务的应用能力 ◇信息传递的能力 ◇行政成本(8)管理层方面 ◇管理层的素质 ◇管理层的士气 ◇管理层的流动率 ◇可培养为管理人员的人才数目(9)员工方面 ◇流动率 ◇士气 ◇专业知识及技术水准 ◇目前能力可适应未来趋势的人才数目 ◇未来培养的难易度 ◇劳资关系
一、导入前的准备工作
步骤一(STEP1):高层决心导入
重点工作(二):建立TPM活动组织
3、赋予机构成员任务 以下就针对推行TPM活动的组织机构(见图4-2),说明各层次岗位的组成与任务:A为企业最高管理者(公司推进委员会)。 A1……An为各支柱专题委员会,其主要任务是针对企业需求,成立各种专门委员会,以全力规划各支柱重点项目的实施方针。 B由熟悉企业内部事务的人员组成,为TPM推进办公室(日韩外企、台资企业称为事务局),其主要任务有以下各项:1)在最顶端的三角形,是指由管理层及各部门最高主管组成,为TPM推进委员会公司委员会。其主要任务为制订企业推行TPM的方针。其中: ◇制订使TPM进入正轨所需的计划; ◇研究拟订活动推进状况的持续追踪对策; ◇对现场自主管理活动进行支援; ◇企业方针与基层意见的沟通渠道; ◇规划整体教育培训课程。
TPM——推进的步骤
一、导入前的准备工作
步骤一(STEP1):高层决心导入
步骤二(STEP2):初期推进人员的设置
步骤三(STEP3):TPM的导入培训
步骤四(STEP4):基本方针与目标的设定
步骤五(STEP5):设置TPM推进专职机构
TPM活动推进管理制度

TPM活动推进管理制度首先,TPM活动推进管理制度的内容包括以下几方面:1.活动推进机构:建立TPM活动推进机构,由专门的推进组织负责组织和协调TPM活动的推进工作。
该机构应设有专职的TPM推进负责人,并由各职能部门的代表组成推进小组。
推进小组应定期召开会议,讨论和解决各种问题,促进TPM活动的顺利进行。
2.目标和指标管理:制定明确的TPM目标和指标,并与企业整体目标相衔接。
设定合理的目标和指标有助于激发员工积极性,促进TPM活动的顺利实施。
目标和指标应该具体、可量化,并根据实际情况进行调整和优化。
3.TPM培训和教育:培训和教育是推进TPM活动的重要环节。
组织全体员工进行TPM培训,提高员工的TPM意识和技能,使其能够主动参与到TPM活动中。
同时,还可以邀请专家进行讲座,分享TPM的最佳实践经验和案例,激发员工的学习热情。
4.TPM宣传和推广:宣传和推广TPM活动可以增强员工对TPM的认识和理解,激发他们的参与热情。
可以通过内部宣传栏、企业内部刊物、宣传海报等方式进行宣传,同时还可以组织举办TPM展览和示范活动,让员工亲身体验TPM的好处和成果。
5.TPM奖惩机制:建立合理的奖惩机制,对于在TPM活动中表现优秀的个人和团队给予奖励,以激励员工的积极性和创造性。
同时,对于未达到预期效果的个人和团队进行必要的惩罚和纠正,以推动TPM的不断改进和进步。
其次,TPM活动推进管理制度的重要性体现在以下几个方面:1.提高生产效率:通过TPM活动推进管理制度,可以减少设备故障和停机时间,提高设备的利用率和生产效率。
通过设备的维护保养和日常管理,可以预防故障的发生,从而减少生产中断和停工造成的损失。
2.提升产品质量:TPM活动强调从源头上杜绝质量问题的发生,通过设备保养、清洁和管理,消除生产中存在的隐患和错误,提高产品的质量和可靠性。
通过不断改进和优化工艺流程,降低产品缺陷率和不良品率。
3.增强员工参与意识:通过TPM活动推进管理制度,可以增强员工的参与意识和责任感,激发其积极性和创造性。
TPM推进技巧与方法

根据需求分析结果,设计针对性的培训课程,包括理论知 识和实践操作,以提高员工的TPM技能。
培训实施与效果评估
按照培训计划组织培训活动,并对培训效果进行评估,以 确保培训目标的达成。
激励与奖励机制
激励机制建立
为了激发员工参与TPM的积极性,需要建立 相应的激励机制,如晋升机会、奖金制度等 。
某化工企业的TPM推进案例
总结词:逐步推进
详细描述:该化工企业根据自身生产 特点,逐步推行TPM管理,从重点设 备开始,逐步推广到所有设备,提高 了生产效率和产品质量。
某电力企业的TPM推进案例
总结词:创新应用
VS
详细描述:该电力企业将TPM与智能 技术相结合,开发了设备状态监测系 统,实现了远程监控和预警,提高了 设备维护的及时性和准确性。
提高设备综合效率
TPM以提高设备综合效率 为目标,追求设备寿命周 期费用的最经济。
TPM推进的意义
01 提高设备可靠性,减少故障停机时间,提 高设备利用率。
02 提高产品质量和生产效率,降低生产成本 。
03
延长设备使用寿命,降低设备维修费用。
04
提高员工素质和参与意识,增强企业凝聚 力。
02
CATALOGUE
1. 制定详细的推进计划
制定详细的TPM推进计划,明确目标、任务、时 间节点和责任人,确保工作的有序开展。
3. 持续改进与创新
在推进TPM的过程中,不断总结经验教训,持续 改进和创新,提高TPM的实施效果和企业的竞争 力。
THANKS
感谢观看
奖励机制实施
根据员工在TPM活动中的表现和贡献,给予相应的 奖励和表彰,以激励员工持续参与和投入。
反馈与调整
TPM推进的步骤及开展方法(模板)

TPM的具体实施
第十一步:展开“员工未来能力持续成长” 活动
1、员工能力分析; 2、员工成长约束、差距、原因分析; 3、员工持续成长计划; 4、OPL程序化管理——OPL课题的挖掘、组 织撰写、评审修改、组织培训教学、奖励体系; 5、辅助实施。
TPM的具体实施
第十二步:建立TPM考核评估体系
第三步:制定公司TPM目标、推进计划和实施计划
TPM的具体实施
第四步 :TPM启动会(4月18日下午已启动) 动员大会:最高领导; 导入培训:1、请外部专家进行现场指导;
2、到外面去学习参观; 刊物、看板、电子视板:宣传部门配合。
TPM的具体实施
第五步:以6S为切入点,开展TPM 6S是基础; 6S是突破口; 6S同样要程序、规范管理:确定区域、人员、 标准、周期、方法,并有检查评估方案; 6S中必然发现根源性的问题——引入清除六源 内容。
TPM的具体实施
第八步:样板发布会。 程序: 1、领导讲话鼓励; 2、机台负责人介绍本机台的规范化文件体系和
实际执行情况、效果; 3、参观示范; 4、参观人提问、答疑; 5、组织者总结。
TPM的具体实施
第九步:公司预防维护体系的设计与实施 设计:设计适合本企业的预防维护体系; 设计与此防护体系匹配的全部管理程序; 实施:运行并修改完善。
机台操作者提出改善点 通过提案和立项方式解决 小提案:自主提案,自主改善; 大提案:专题立项,集思广益,项目管理,难题 攻关。
样板机台示范,全面推广
在样板机台(或线段)旁,召开现场发布会。 程序: 1、领导讲话鼓励; 2、机台负责人介绍本机台的规范化文件体系和 实际执行情况、效果; 3、参观示范; 4、参观人提问、答疑; 5、组织者总结。
推进TPM活动程序

重点工作(一):分析目前企业面临的各种问题。
目的:对企业所处的环境有更清楚的认识,并由此判断TPM活动在企业中进行的方向。
参考形式:可用表4-1的TPM的活动引进背景来进行分:
工作内容:一般可概分为内部环境分析及外部环境分析两方面。
1.内部环境分析。
在于了解公司的能力,藉以具体评估现行企业经营策略及预期引入TPM活动后所能达到的目标,有关分项可综列成以下各项。
基本上,实施TPM采用现行组织型态亦无不可,只要能推动顺畅即可。
步骤2:初期推进人员的设置
执行时间:6个月。
主要成员:由熟企业及部门内部事务的相关人员中筛选。
设置用意:
目的:
(1)筹划引进初期准备工作。
(2)籍由初期准备工作,学习TPM推行的相关经验,作为将来各部门推动的主导。
原则:
(1)本阶段企业内部基于人事及业务量的考量,无须成立专责推动部门;建议采用跨部门方式,由各部门推派一名人员参与初期准备工作,初期这些兼任人员的工作量与本身原有职务的分配,比例以3:7为宜。
(3)内部师资群可概分两大类:一种是概念、观念的传授,由单位主管或TPM推进机构人员担任;另一种是技术类,需挑选专门技术人员担任,一般这种技术类的师资,可聘请公司内服务已达退休年限,但未达退休年龄者担任。
(4)每次教育训练结束后,一定要有成果考核。
成败关键:师资群的建立。
步骤4:基本方针与目标的设定
工作内容:
1.建立TPM活动组织的基本原则。
(1)应包含企业各部门。
(2)应包含组织各阶层成员。
(3)各阶层间应有水平联系的架构。
(4)高阶人员不应只是挂名,须实际参与推动工作。
(5)TPM的组织应与现行各种活动及制度结合,不宜另立别支,以免造成混淆及权责不清。
TPM活动展开基础详细步骤效果和推进方法

TPM活动展开基础详细步骤效果和推进方法TPM活动,全称为全员参与生产维护(Total Productive Maintenance),是一种通过全员参与和设备维护改善来提高生产效率和设备可靠性的管理方法。
本文将详细介绍TPM活动展开的基础步骤、效果以及推进方法。
一、TPM活动展开的基础步骤1. 公司领导力和目标设定TPM活动的成功离不开公司领导力和明确的目标设定。
公司高层要明确支持TPM活动,并设定明确的目标,如提高设备利用率、减少停机时间等。
2. 建立TPM小组和推进机构公司应组建专门的TPM小组,由跨职能部门的成员组成,负责推进TPM活动。
同时,建立相应的推进机构,制定推进计划和安排资源等。
3. 设备基础管理设备基础管理是TPM活动展开的重要一环。
包括设备档案的建立、设备的分类管理、设备故障统计、备件管理等。
4. 维护知识和技能培训TPM活动要求全员参与,因此需要对员工进行维护知识和技能的培训。
培训内容包括设备操作技能、设备检修技能、故障排除等。
5. 制定设备维护标准和操作规程制定设备维护标准和操作规程,确保设备的日常维护工作得以正确执行。
标准和规程可以包括设备点检、润滑、清洁、紧固等具体内容。
6. 小班活动和设备检修改造活动通过小班活动,组织员工参与设备维护和检修改造工作,提高员工的参与度和责任感。
此外,还可以设立奖励机制,激励员工积极参与。
7. 故障率分析和持续改善通过故障率分析和持续改善活动,找出设备存在的问题和不足之处,并制定改善计划,逐步提高设备可靠性和生产效率。
二、TPM活动的效果1. 提高设备可靠性TPM活动通过定期维护、点检、润滑等措施,减少设备故障和停机时间,提高设备可靠性。
同时,也有助于预防设备故障发生,降低维修成本。
2. 提高生产效率通过减少停机时间、缩短设备调整时间、降低次品率等措施,TPM活动可以提高生产效率,实现利润的增长。
3. 增强员工参与度和责任感TPM活动强调全员参与,通过培训和班组活动,能够增强员工的参与度和责任感,推动企业文化的建设。
TPM活动成功的十大秘诀精选全文
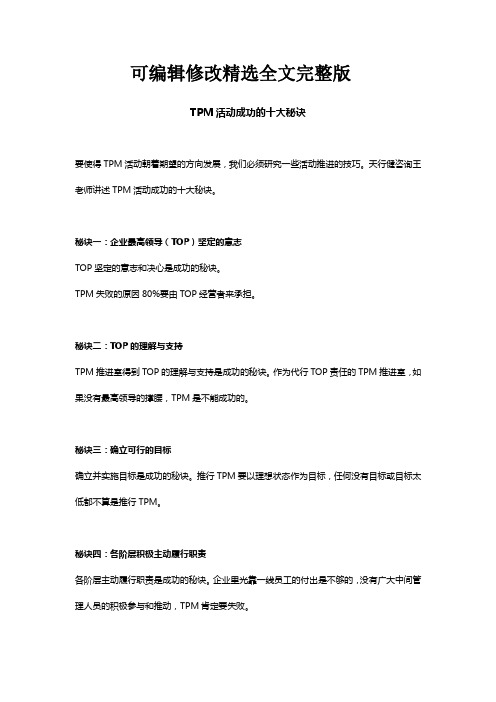
可编辑修改精选全文完整版TPM活动成功的十大秘诀要使得TPM活动朝着期望的方向发展,我们必须研究一些活动推进的技巧。
天行健咨询王老师讲述TPM活动成功的十大秘诀。
秘诀一:企业最高领导(TOP)坚定的意志TOP坚定的意志和决心是成功的秘诀。
TPM失败的原因80%要由TOP经营者来承担。
秘诀二:TOP的理解与支持TPM推进室得到TOP的理解与支持是成功的秘诀。
作为代行TOP责任的TPM推进室,如果没有最高领导的撑腰,TPM是不能成功的。
秘诀三:确立可行的目标确立并实施目标是成功的秘诀。
推行TPM要以理想状态作为目标,任何没有目标或目标太低都不算是推行TPM。
秘诀四:各阶层积极主动履行职责各阶层主动履行职责是成功的秘诀。
企业里光靠一线员工的付出是不够的,没有广大中间管理人员的积极参与和推动,TPM肯定要失败。
秘诀五:大力推进课题改善大力推进课题改善是成功的秘诀。
通过选定一些课题实实在在推行,可以给企业带来可观的成果。
秘诀六:从产品设计开始抓良品生产从产品设计开始就抓良品生产是成功的秘诀。
花时间生产不良和废品,是企业隐藏的地下加工厂。
对企业来说是最大的浪费,我们必须一开始就只生产良品。
秘诀七:切实的自主管理切实的自主管理是成功的秘诀。
只有通过自主管理才能提高现场的管理水平,也才能提升员工的技能和素质。
秘诀八:全员参与全员参与形成同一个方向是成功的秘诀。
没有全员的参与,TPM就失去了意义,但即使全员都参与,由于没有共同的方向而相互抵消作用,TPM仍然不能成功。
秘诀九:持续改善持续改善是成功的秘诀。
改善是无止境的,如果认为已经改善过了就不再需要进一步改善的话,或者认为改善过了就可以一劳永逸的话。
TPM必然会从山顶滑到山脚。
秘诀十:活动的趣味化活动的趣味化和有特色的推进工作是成功的秘诀。
TPM是一项漫长的工程,难免会感到枯燥,研究和推出TPM的活性化方案,鼓励小组展开有个性的活动可以助长TPM的火焰。
TPM活动的推进步骤

TPM活动的推进步骤TPM(全面生产维护)是一种通用的生产管理方法,旨在通过持续改善和最大化生产设备效率来提高生产效率和提高质量。
推进TPM活动的步骤可以分为以下六个阶段:1. V理念的确认:TPM推进的第一步是确认企业的目标和V理念。
V理念是指“目睹(Visualize)问题、预见(Visionize)解决方案”的理念。
在这一阶段,企业需要明确TPM的目标和价值,以及推进TPM的原因和动力。
同时,企业也需要明确TPM将要解决的问题和期望达到的效果。
2.现状分析:在确认了V理念后,企业需要对当前的生产设备和生产过程进行全面的分析。
这包括设备的运行状态、维护情况、故障率等等。
通过现状分析,企业可以了解到目前存在的问题和隐患,并且为制定后续的改进计划提供基础。
3.制定改进计划:在现状分析的基础上,企业需要制定具体的改进计划。
改进计划应当包括目标、措施和时间表。
目标是指要达到的改进效果,措施是指要采取的具体措施,而时间表则是指每个措施的实施时间和达到目标的最后期限。
4.推进改进计划:在制定完改进计划后,企业需要按照计划进行推进。
这需要企业建立相应的管理体系和推进机制,明确责任和任务。
同时,企业还需要进行必要的培训和技术支持,确保改进计划的有效实施。
5.评估改进效果:在改进计划推进的过程中,企业需要进行定期的评估,以评估改进效果和调整计划。
评估可以通过设备的生产数据、故障率等来进行,也可以通过员工的反馈和意见来进行。
通过评估,企业可以了解到改进计划的效果和不足之处,并且对下一阶段的改进计划进行调整。
6.持续改进:TPM的推进是一个持续的过程,企业需要不断地进行改进和优化。
在评估的基础上,企业可以制定下一阶段的改进计划,并且进行推进。
通过持续改进,企业可以不断提高生产设备的效率和质量,进一步提升企业的竞争力。
总之,推进TPM活动需要企业明确V理念、进行现状分析、制定改进计划、推进改进计划、评估改进效果和持续改进。
tpm推行计划方案

tpm推行计划方案TPM(全名为Total Productive Maintenance,即全面生产力维护)是一种通过强化设备维护和员工参与,提高生产效率和设备稼动率的管理方法。
本文将介绍TPM推行计划方案,帮助企业实现设备管理的全面升级。
一、概述TPM推行计划旨在通过改进设备维护和保养,减少故障停机时间,提高设备稼动率,并培养员工参与,共同维护设备保持其稳定运行。
本计划从TPM的六大支柱和五大活动入手,制定具体实施方案,以帮助企业推行TPM。
二、六大支柱TPM的六大支柱包括:1. 设备管理在这一支柱中,我们将制定完善的设备管理计划,包括设备清单、设备维护计划、设备性能评估等。
同时,我们将引入先进的设备管理技术和工具,如预防性维护、故障预测等,以确保设备的良好运行。
2. 故障消除通过设立故障响应机制、实施快速故障修复、设备故障分析和故障原因消除活动等,我们将提高设备的可靠性和稳定性,减少故障对生产的影响。
3. 工艺改善通过对工艺进行持续改进,我们将提高生产效率,减少资源浪费,改善产品质量,并为设备提供更稳定的工作环境。
4. 培训和教育培训和教育是TPM成功的关键。
我们将开展设备操作员和维护人员的培训计划,提升他们的技能水平和意识,使他们能够参与到设备的有效管理中来。
5. 安全、环境和卫生在设备管理的同时,我们将注重安全、环境和卫生的管理,确保设备的运行符合相关要求,保护员工的安全和健康。
6. TPM活动管理TPM需要全员参与和支持,因此我们将制定与TPM相关的沟通和激励机制,通过开展TPM相关活动和奖励制度,激发员工对TPM的积极性和参与度。
三、五大活动TPM的五大活动包括:1. 定期保养(Autonomous Maintenance)设备操作员将负责日常保养工作,包括设备清洁、润滑、紧固等,以确保设备的良好状态。
2. 故障预防(Preventive Maintenance)通过制定预防性维护计划,定期检查设备,更换易损件,防止故障的发生,保障设备的可靠性。
TPM推进方法与技巧
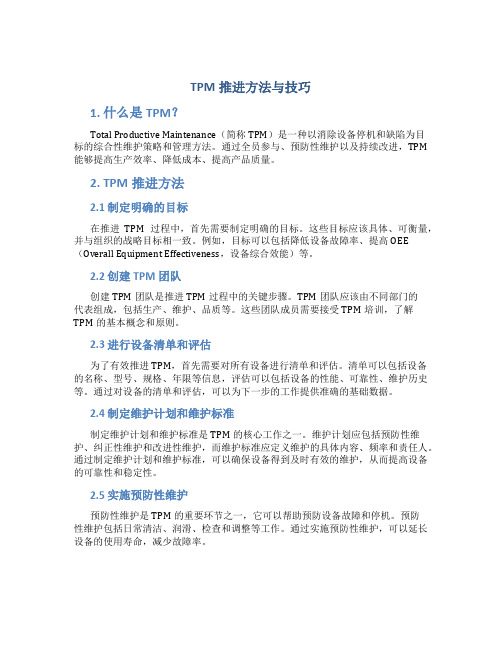
TPM推进方法与技巧1. 什么是TPM?Total Productive Maintenance(简称TPM)是一种以消除设备停机和缺陷为目标的综合性维护策略和管理方法。
通过全员参与、预防性维护以及持续改进,TPM 能够提高生产效率、降低成本、提高产品质量。
2. TPM推进方法2.1 制定明确的目标在推进TPM过程中,首先需要制定明确的目标。
这些目标应该具体、可衡量,并与组织的战略目标相一致。
例如,目标可以包括降低设备故障率、提高OEE (Overall Equipment Effectiveness,设备综合效能)等。
2.2 创建TPM团队创建TPM团队是推进TPM过程中的关键步骤。
TPM团队应该由不同部门的代表组成,包括生产、维护、品质等。
这些团队成员需要接受TPM培训,了解TPM的基本概念和原则。
2.3 进行设备清单和评估为了有效推进TPM,首先需要对所有设备进行清单和评估。
清单可以包括设备的名称、型号、规格、年限等信息,评估可以包括设备的性能、可靠性、维护历史等。
通过对设备的清单和评估,可以为下一步的工作提供准确的基础数据。
2.4 制定维护计划和维护标准制定维护计划和维护标准是TPM的核心工作之一。
维护计划应包括预防性维护、纠正性维护和改进性维护,而维护标准应定义维护的具体内容、频率和责任人。
通过制定维护计划和维护标准,可以确保设备得到及时有效的维护,从而提高设备的可靠性和稳定性。
2.5 实施预防性维护预防性维护是TPM的重要环节之一,它可以帮助预防设备故障和停机。
预防性维护包括日常清洁、润滑、检查和调整等工作。
通过实施预防性维护,可以延长设备的使用寿命,减少故障率。
2.6 引入维护自主性维护自主性是TPM的核心概念之一。
它通过培训员工进行维护和小修,减少设备故障和停机时间。
为了实现维护自主性,组织需要培训员工的技能、提供必要的工具和设备,并建立相应的激励机制。
3. TPM推进技巧3.1 建立良好的沟通机制在推进TPM过程中,建立良好的沟通机制非常重要。
TPM活动推进方法

TPM活动推进方法引言TPM(全名为Total Productive Maintenance,全面生产维护)是一种重要的生产管理理念,它旨在通过最大限度地提高设备的稼动率和生产效率,实现生产线的持续运行。
为了有效推进TPM活动并取得良好的效果,本文将介绍一些方法和技巧供参考。
1. 制定明确的TPM目标在推进TPM活动之前,首先要确立清晰明确的目标。
这些目标应当与组织的整体业务目标相一致,并能够衡量和评估TPM活动的成果。
例如,可以将目标设定为提高设备的稼动率、减少设备故障率、降低维修时间等。
2. 建立TPM团队要成功推进TPM活动,建立一个专门的TPM团队是必不可少的。
该团队应由设备操作员、维修人员、工程师等相关人员组成,他们应具备相应的技能和经验。
团队成员需要接受TPM的培训,了解TPM的原理和方法。
3. 进行设备状态评估在推进TPM活动之前,进行设备状态评估是非常重要的一步。
通过对设备进行全面的评估和分析,找出设备存在的问题和潜在的风险。
这些问题包括设备老化、磨损、零部件缺陷等。
根据评估结果,制定相应的改善计划。
4. 制定设备保养计划设备保养是TPM活动的关键环节之一。
通过制定设备保养计划,可以确保设备的正常运行和延长设备的使用寿命。
保养计划应涵盖各种保养活动,包括日常的清洁保养、定期的维护保养以及预防性保养等。
团队成员应按照保养计划执行各项保养任务,并定期进行检查和评估。
5. 实施设备故障分析设备故障是生产线中常见的问题之一,而设备故障对生产效率和产品质量有着直接的影响。
为了解决设备故障问题,可以采用设备故障分析方法。
通过对故障进行定位、分析和排查,找出故障的根本原因,并采取相应的措施进行修复和改进。
设备故障分析需要进行记录和整理,以便后续的分析和改进。
6. 进行员工培训员工是TPM活动的重要参与者,他们直接参与到设备运行和维护中。
因此,对员工进行培训和教育是非常重要的。
培训内容包括TPM的理论知识、设备操作和保养的方法、故障排除技术等。
TPM活动推进方案

TPM活动推进方案1. 概述本文档旨在提供一个TPM(Total Productive Maintenance,全面生产维护)活动推进方案,以帮助组织实施TPM并提高生产效率。
TPM是一种基于员工参与和团队合作的维护策略,旨在通过设备的全面维护,提高设备可靠性和产能。
2. 背景在竞争激烈的市场环境中,组织需要保持高效的生产运营以保持竞争力。
设备故障和停机时间是影响生产效率的重要因素之一。
通过实施TPM,组织可以提高设备的可靠性、降低停机时间,实现持续的生产效率提升。
3. 目标本TPM活动推进方案的主要目标如下:•提高设备可靠性和稳定性•减少设备停机时间•提高设备利用率•增加生产效率和产量•提高员工参与度和责任感4. 推进步骤4.1 建立TPM团队建立一个跨部门的TPM团队,由设备操作员、维护人员和管理人员组成。
该团队将负责推动TPM活动的实施,并监督和评估其效果。
4.2 建立设备维护计划制定全面的设备维护计划,包括预防性维护、定期检查和设备保养,以确保设备的正常运行和延长设备的寿命。
4.3 培训和教育提供TPM的培训和教育,帮助员工了解TPM的原理和方法,并培养其参与和负责任的态度。
4.4 设备改善设立设备改善小组,鼓励员工提出改善设备性能和效率的创意和建议,并实施这些改进措施。
4.5 工作场所管理改善工作场所的整洁度和安全性,确保工作环境符合操作标准,并为员工提供舒适和安全的工作环境。
4.6 总结和评估定期总结和评估TPM活动的效果,并根据评估结果进行必要的调整和改进。
5. 实施计划对于TPM活动的实施,建议采取以下计划:5.1 初期阶段(1个月)•建立TPM团队,明确团队成员和责任分工。
•开展TPM培训和教育活动,提高员工对TPM的理解。
•开始制定设备维护计划,包括预防性维护和定期检查。
5.2 中期阶段(3个月)•推动设备维护计划的执行,并建立设备维护记录和报告系统。
•开展设备改善活动,收集和实施员工的改进建议。
tpm推进实施方案

tpm推进实施方案TPM推进实施方案。
一、背景。
随着市场竞争的日益激烈,企业需要不断提升生产效率和产品质量,以满足客户需求并保持竞争优势。
而TPM(全面生产维护)作为一种全员参与的生产管理方法,已经被越来越多的企业所认可和采用。
在这样的背景下,我们需要制定一套全面的TPM推进实施方案,以确保企业生产运营的稳定和持续改善。
二、目标。
1. 提升设备稼动率,通过TPM的实施,提高设备的可靠性和稼动率,减少设备故障和停机时间,提高生产效率。
2. 降低生产成本,通过预防性维护和设备管理,减少维修成本和生产中断造成的损失,降低生产成本。
3. 提高产品质量,通过设备的良好管理和维护,确保产品生产过程中的稳定性和一致性,提高产品质量和客户满意度。
4. 增强员工技能,通过TPM的实施,培养员工的自主管理意识和技能,提高生产团队的整体素质和绩效。
三、关键步骤。
1. 建立TPM团队,成立跨部门的TPM推进小组,包括生产、设备维护、质量管理等相关部门的代表,明确团队成员的职责和目标。
2. 制定TPM计划,根据企业实际情况和目标,制定全面的TPM推进计划,包括设备清单、维护计划、培训计划等内容。
3. 设备信息化管理,建立设备信息化管理系统,实现设备故障的实时监控和数据分析,提前预警和预防设备故障。
4. 培训和教育,组织员工参加TPM相关的培训和教育,包括设备管理、维护技能、自主检查等内容,提高员工技能和意识。
5. 实施5S管理,推行车间的5S管理,改善工作环境和设备周围的秩序,提高生产效率和安全性。
6. 制定维护标准,制定设备维护的标准作业程序(SOP),确保设备维护的规范性和一致性。
7. 持续改善和监控,建立TPM推进的持续改善机制,通过设备运行数据的监控和分析,发现问题并及时改进,实现生产过程的持续优化。
四、实施路径。
1. 阶段目标,按照制定的TPM推进计划,将实施过程分为不同的阶段目标,逐步推进,确保实施的顺利进行。
tpm推行计划方案

tpm推行计划方案TPM 推行计划方案一、背景随着市场竞争的日益激烈,企业对于生产效率、设备可靠性和产品质量的要求越来越高。
全面生产维护(TPM)作为一种先进的设备管理理念和方法,能够有效地提高设备综合效率,降低生产成本,增强企业的竞争力。
为了在本企业成功推行 TPM,特制定本计划方案。
二、目标1、在具体时间段内,将设备故障停机时间降低X%。
2、提高设备综合效率(OEE)至X%以上。
3、培养一支具备自主维护能力的员工队伍。
4、建立完善的 TPM 管理体系,实现持续改进。
三、推行步骤(一)准备阶段(具体时间段 1)1、成立 TPM 推行小组由生产部门、设备部门、质量部门等相关人员组成,明确小组职责和分工。
2、开展 TPM 培训(1)组织内部培训课程,邀请专家讲解TPM 的理念、方法和工具。
(2)安排员工参加外部培训,学习先进的 TPM 实践经验。
3、制定推行计划详细规划每个阶段的工作内容、责任人、时间节点和预期目标。
4、宣传动员(1)通过内部会议、宣传栏、电子邮件等方式,向全体员工宣传TPM 的重要性和推行计划。
(2)组织员工讨论,激发员工参与的积极性和主动性。
(二)导入阶段(具体时间段 2)1、设备初期清扫(1)制定设备清扫计划,明确清扫的部位、方法和标准。
(2)组织员工对设备进行全面清扫,去除设备表面的灰尘、油污和杂物。
(3)在清扫过程中,发现设备的潜在问题和缺陷,并进行记录。
2、建立自主维护体系(1)制定设备自主维护标准和操作指南,明确员工在设备维护中的职责和工作内容。
(2)开展设备操作和维护培训,使员工掌握设备的基本操作和维护技能。
(3)建立设备点检制度,要求员工定期对设备进行点检,及时发现和解决问题。
3、建立计划维护体系(1)制定设备的预防性维护计划,包括定期保养、检修和更换易损件等。
(2)建立设备维修档案,记录设备的维修历史和故障信息,为设备维护提供参考。
4、个别改善(1)针对设备的重点问题和瓶颈环节,成立改善小组,进行专项改善。
- 1、下载文档前请自行甄别文档内容的完整性,平台不提供额外的编辑、内容补充、找答案等附加服务。
- 2、"仅部分预览"的文档,不可在线预览部分如存在完整性等问题,可反馈申请退款(可完整预览的文档不适用该条件!)。
- 3、如文档侵犯您的权益,请联系客服反馈,我们会尽快为您处理(人工客服工作时间:9:00-18:30)。
基石二:岗位重复小组活动
基石1、彻底的5S活动
形成习惯, 提高整体素 质。
整理
区分要物与不 要物,将不要 物处理掉。 将要物规范放 置,使寻找时 间为零。
素养
5S
保持前3个S ,制度化, 规范化。
整顿
清洁
清扫
使工作环境变 得无灰尘、干 净整洁。
5S是TPM的基础, TPM脱离了5S活动是 无法实现最终目标的。 但是,如果只推行5S 活动而不实施TPM, 那么企业也是无法达 到零消耗的目标的。 因此,5S和TPM都非 常重要,两者之间相 辅相成、缺一不可。 TPM与TQM、5S的关 系如下图所示。
推进实施阶段
巩固阶段
6 如何在全公司推行TPM
附、TPM推进方案
2012年计划
序号 工作内容
2 3 4 5 6 7 8 9 10 11 12
*年推进计划化
责任单位
1 2 3 4 5 6 7 8
TPM推行准备导入动员 活动的宣传和培训 建立组织机构(推进委员会)
制定目标 编制工作计划 启动大会 TPM的推行实施活动 规范化、TPM推进奖
TPM
TPM与TQM、5S的关系
5S
基石2、重复性小组活动
重复性小组活动是TPM活动的另 一个重要基石。 小组活动是实施改善项目或革新项 目的基本单位。 企业应当在其组织内部构建起重复 性小组活动机制,创造全员改善的 氛围,倡导员工参与到一个或多个 改善团队中去。如果缺乏这种小组 活动机制,企业的TPM活动也就 失去了活动基础,这是很难 成功的。
改善 提案 小组
自主 保养 小组
生产 TPM小组 提高 效率 计划 OEE 保养 小组
教育 宣导 组
附、全员参加的重复性小组活动组织
全社 TPM推进委员会
部长
担当理事
部属长
公司 TPM推进委员会
工厂TPM协调员和 推进办公室
科长
科别 TPM推进委员会
支柱管理委员会
5S和可视化管理 安全健康环保 自主性维护 个案改善
阶段 步骤
1.经营层的决策导入
引进准备阶段 2.幕僚人员的设置 3.TPM的导入教育 4.基本方针与目标的设定 5.建立TPM的专职机构 6.展开TPM的宣传 引进开始 7.TPM正式启动 举行仪式,宣布开始 8.彻底的5S活动 9.开展提案改善活动 10.效率化的个别改善 11.建立自主养护体制 12.建立保养部门计划保养体制 13.提升操作和保养的技能 14.建立设备初期管理体制 15.整个生产效率化活动的推升 16.阶段的成果总结 17.整个自主管理体系的建立 18.持续不断地进行改善
以生产系统整个寿命周期为对象实现
“灾害为0”、“不良为0”、“故障为0”等
TPM的推进组织为“重复小团队”
重复小团队是指从最高层、到中层,直至第一线上的小团队的各阶层互相协作活动 的组织。
4TPM的一些特点 4. 3TPM的两大基石
循序渐进---从基础作起
基石一:彻底的5S活动
全员参与---从基层作起
4TPM的一些特点
4.1.“三全”经营
全 效 率 全 系 统 全 员 目标
对象/范围
基础
全员参加为基本
4TPM的一些特点
4. 2TPM的三大管理思想
1、预防哲学 2 “零”目标(零缺陷) 3、全员参与和小集团活动
预防工作做好是TPM活动成功的关键
(预防维修 改善维修 创造维修)如果操作者不关注预防、保全人员不关注预防、 领导不关注预防,是不可能做到全方位预防的。因为一个企业这么大,光靠几个几十 个工作人员维护,就算是一天8个小时不停地巡查,也很难防止一些显在或潜在问题发 生。
内容
领导宣布TPM开始,表示决心 考虑选择一些幕僚人员 按不同层次组织培训 找准基准点和设定目标 成立推进委员会 利用各种方式开始宣传 举行仪式,宣布开始 把5S活动再彻底的实施一次 举行提案改善活动 先建立一些示范工程 步骤、方法和诊断方式 定期维护、预知维护 改善维护 创造维护 分层次进行各种技能培训 维护预防设计,前期管理程序 把整个生产活动进行推升 一个阶段的总结 把活动进行深化,让TPM的深入人心 按步骤不断地进行,持续不断地进行改善
Q------工程不良率1/10 C------生产成本降低30% D------产品、半成品库存减 S------停产损失为0 M------改善提案件数5~10倍 TPM使企业综合实力的提升: 通过改善人与设备体制以改善企业体制、各项指标的提升(工程不良率、设备综合 效率、人均产量、销售额) TPM可以使企业形成良好的企业文化(主人翁的观念),促进企业持续性发展。
系长
个别分会
班长
TPM小集团
计划性维护 质量系统的维护 培训和教育 设备早期管理 供应链/办公室TPM
5 TPM运作结构图
世界最高竞争力公司
□ 创造高效率生产系统 □ 培养设备专家级操作员工 □ 保全员的专业化(电器/机械) 企业的 体质改善
目标“0”化 八
零故障, 零Biblioteka 良,零灾害, 零废弃个 别 改 善
3施行TPM的目的
“通过人和设备体质改善的企业体质改善”
——适应FA时代( Factory Automation)的人员培养—— (1)操作人员:自主保全能力 (2)保全人员:机械设备的保全能力 (3)生产技术人员:不要保全的设备计划能力
人
的体质改善
设备
的体质改善
(1)现存设备体质改善的效率化
(2)新设备的LCC(Life Cycle Cost 生命周期成本设计)和垂直提升
个别改善 自主保全 计划保全 教育训练 初期管理
起初的5 大支柱
⑥ 构筑品质保全体制 ⑦ 间接管理部门效率化的 ⑧ 安全、卫生和环境管理的
品质保全 业务改善 环境安全
增加的3 大支柱
6 如何在全公司推行TPM
推进实施TPM的三大阶段
推进TPM的三大阶段如图7-3所示,分别为准备发动阶段、落实推行阶段、评值改进阶段。其中,在准备发动阶段主要 的工作是进行人员的培训和概念开发;在落实推行阶段则是根据既定目标,具体实施各项计划;在评估改进阶段,主要 工作为通过检查评估,找出需要改进的地方。
内容 阶段
准备发动
创造适宜的TPM环境 进行概念开发和人员 培训 确定目标,建立小组 制定计划 采取措施 攻克难题 展开推广
落实推行
评价改进
制定标准 检查评促 估 找出不足 改进提 高
6 如何在全公司推行TPM
TPM的推行可按三个阶段、18个步骤来具体进行。 18个步骤并不是一成不变的,仅仅作为借鉴,应根据企业的实际需要进行调整。 经过这些步骤,企业就可以一步步把TPM推向深入
7 TPM 推行实施
小组活动案例
7.1自主保全展开步骤
步骤 第1步 第2步 第3步 第4步 名 称 初期清扫 发生源 困难部位对策 制定自主保全 临时基准 总点检 活 动 内 容 以设备主体为中心彻底排除垃圾、灰尘,进行加油、加紧螺栓以 及发现设备的不正常并进行复原 改善垃圾、灰尘的发生源、飞溅的防止.清扫加油困难的部位,谋 求缩短清扫、加油时间 制定确定能够维持在短时间内清扫、加油、加紧螺栓的行动基准 (有必要表示能够日常、定期使用的时间范围) 根据检点手册进行检点技能教育,通过总检点的实施提出设备微缺 陷并复原 制作、实施自主检点检查表 进行各种现场管理项目的标准化,谋求维持管理的完全系统化 · 清扫加油检点基准 · 现场的物流基准 · 数据记录的标准化 · 模具、工夹具管理基准等 展开会社方针、目标,确实进行改善活动稳定化的MTBF(平均无故障时 间)分析记录,解析改善设备
第5步 第6步
自主点检 标准化
第7步
自主管理的 贯彻
TPM培训教程
制作:Paul Ma
课程内容
◆ 1 TPM的定义 ◆ 2 TPM的起源与发展 ◆ 3 施行TPM的目的 ◆ 4 TPM 的一些特点 ◆ 5 TPM运作结构图 ◆ 6 如何在全公司推行TPM ◆ 7 TPM 推行实施小组活动实例
1TPM的定义
TPM、TQM、Lean Production并称为世界级三大制造管理技术。 TPM为英语total productive management的简称,意为全员生产性 维护,运用在设备中可译为TPEM,即total productive equipment management。
自 主 保 全
计 划 保 全
教 育 训 练
初 期 管 理
品
事 务 改 善
环
境 安 全
现场的 体质改善
大
支 柱
质
保 全
两大基石
重复性小组活动 彻底的5S活动
人员的 体质改善
5 TPM运作结构图
5.1
① ② ③ ④ ⑤
TPM全面展开的八项活动
促进生产效率化的 以操作者为中心的 以保全部门为主的 提升运转/保全技能的 导入新制品/新设备的
2TPM的起源及发展
1、从美国式的PM到日本独自的TPM
生产部门保全时代(TPM) 1971年,日本人引进了PM活动并将其改造成为现场部门的TPM改善活动,即开始注重全员参与 (total)。在全员保养时代与保养预防时代的区别就在于所有的员工都应该对设备保养负责。此时 的TPM主要以生产部门为主。 全员生产保全时代(TPM) 1989年,TPM被重新定义为广义的TPM,它是指以建立不断追求生产效率最高境界(No.1) 的企业体质为目标,通过公司领导到第一线员工全员参与的创新小组改善活动,构筑预防管理 及生产工序中所有损耗发生的良好机制,最终达成损耗的最小化和效益的最大化。 供应链的TPM时代 2000年开始,TPM已经跨行业国际化发展。TPM并不是只属于日本的产业界,世界各地对 TPM的关心逐年升高。这时也不是在某个企业实施,它逐渐向服务、流通等行业发展,逐步 优化供应链系统。