铁矿选矿技术分析论文
铁矿山选矿技术
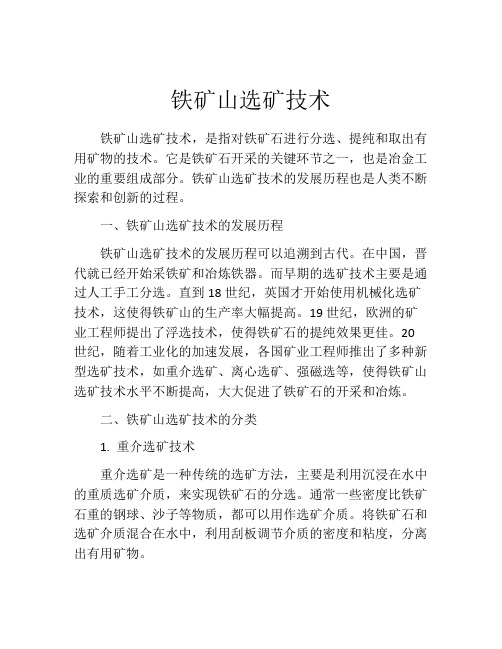
铁矿山选矿技术铁矿山选矿技术,是指对铁矿石进行分选、提纯和取出有用矿物的技术。
它是铁矿石开采的关键环节之一,也是冶金工业的重要组成部分。
铁矿山选矿技术的发展历程也是人类不断探索和创新的过程。
一、铁矿山选矿技术的发展历程铁矿山选矿技术的发展历程可以追溯到古代。
在中国,晋代就已经开始采铁矿和冶炼铁器。
而早期的选矿技术主要是通过人工手工分选。
直到18世纪,英国才开始使用机械化选矿技术,这使得铁矿山的生产率大幅提高。
19世纪,欧洲的矿业工程师提出了浮选技术,使得铁矿石的提纯效果更佳。
20世纪,随着工业化的加速发展,各国矿业工程师推出了多种新型选矿技术,如重介选矿、离心选矿、强磁选等,使得铁矿山选矿技术水平不断提高,大大促进了铁矿石的开采和冶炼。
二、铁矿山选矿技术的分类1. 重介选矿技术重介选矿是一种传统的选矿方法,主要是利用沉浸在水中的重质选矿介质,来实现铁矿石的分选。
通常一些密度比铁矿石重的钢球、沙子等物质,都可以用作选矿介质。
将铁矿石和选矿介质混合在水中,利用刮板调节介质的密度和粘度,分离出有用矿物。
2. 浮选技术浮选技术,是利用矿物表面性质和密度、络合能等因素的差异,把含有某种有用矿物的矿石,从其他矿物中分离出来的方法。
经过研磨处理后,将选矿浮剂添加进去,提高目标矿物与浮剂的亲和力,使其浮起来,而不浮起来的其他矿物沉下去。
浮选技术广泛应用于铁矿山选矿过程中。
3. 磁选技术磁选技术是一种利用铁矿石和相间物的磁性差异实现分选的方法。
在铁矿石分选中,利用磁性选矿,可以使磁性物质更快速地分离出来,取得更佳的分选效果。
强磁选、弱磁选、高梯度磁选、扑磁选、自然磁选等都是常用的铁矿石分选方法。
三、铁矿山选矿技术发展趋势1. 现代化技术的推广应用现代化技术应用于铁矿山选矿技术已经成为趋势。
数字化、自动化、信息化、新材料等技术的推广应用,通常可以有效降低铁矿山选矿过程中的成本,提高选矿效率,降低污染排放。
2. 精细化选矿随着铁矿石品质的下降,矿石储藏量的减少,精细选矿技术的应用将变得越来越重要。
磁铁矿石选矿工艺的分析与研究

磁铁矿石选矿工艺的分析与研究摘要:本文对磁铁矿石选矿工艺进行了分析研究,重点探讨了破碎与磨矿、干选粗精矿单一弱磁选、干式预选抛尾的磁选工艺以及磁浮联合选矿工艺等关键技术在应用中的相关要点和关键,以供参考。
关键词:磁铁矿石;选矿工艺;研究引言磁铁矿石作为一种重要的资源,在工业和科技领域的应用不断扩大。
研究选矿工艺在磁铁矿石开发利用中的重要性是十分必要的。
通过深入探讨选矿工艺的作用和主要研究内容,可以有效地提高磁铁矿石的精度、降低成本、提高回收率和选择性。
同时,拓展磁铁矿石的应用市场,有助于推动磁铁矿石产业的可持续发展。
未来,随着科技的不断进步,磁铁矿石选矿工艺将面临更多的挑战和机遇,需要不断深入研究和发展。
1磁铁矿石的概述磁铁矿石是一种含铁量较高的矿物,其主体为磁铁矿,主要成分为四氧化三铁(Fe3O4)。
根据其磁性的不同,磁铁矿石可以分为硬磁铁矿石和软磁铁矿石两类。
硬磁铁矿石具有较高的矫顽力和剩磁,常温下不易被高强度的磁场吸引;而软磁铁矿石则具有较低的矫顽力和剩磁,容易被高强度的磁场吸引。
在物化性质方面,磁铁矿物多为粒块状集合体,外表呈黑色或钢灰色。
其晶体结构为六方晶系,具有强磁性、高密度、硬度较高等特点。
磁铁矿石不易加工,脆性较大,在加工过程中易产生碎屑。
此外,磁铁矿物的化学成分主要为Fe3O4,其中FeO和Fe2O3的含量比例决定了其磁性和其他物理化学性质。
磁铁矿石中还含有少量的硅、铝、钙、镁、钾、钠等元素,这些元素的含量和比例也对其物理化学性质产生影响。
由于磁铁矿石具有高磁性、高密度、高硬度等特点,因此其被广泛应用于各种领域[1]。
但是磁铁矿在进行冶炼前,必须经过进一步的选矿才能够符合冶炼要求。
所以在现阶段需要进一步加强对磁铁矿选矿工艺的研究,不断提高选矿效率降低,并选矿中的能耗污染。
2磁铁矿石选矿中的工艺技术要点分析2.1破碎与磨矿破碎与磨矿是磁铁矿石选矿工艺中的两个重要环节,其主要作用是将大块的磁铁矿石破碎成小颗粒,并通过磨矿作业将矿石中的有用矿物与无用矿物分离。
关于铁矿选矿技术分析

关于铁矿选矿技术分析【摘要】随着近些年来我国经济的发展,我国的产业结构不断优化,各采矿业也都取得了显著的发展成绩,尤其是作为主要矿物资源供应的铁矿业,其无论是开采规模还是开采技术都有了显著的扩大和提高。
下文中笔者将结合自己的工作经验,对铁矿的选矿技术进行分析,以其完善和改进现行的铁矿技术,促进我国铁矿业的发展,笔者将从菱铁矿石选矿技术、褐铁矿石选矿技术、复合铁矿石选矿技术、多金属共生铁矿石选矿技术、鲕状赤铁矿石选矿技术、高硫、磷铁矿石选矿技术等几个方面对该问题进行浅析,诸多不足,还望批评指正。
【关键词】铁矿选矿技术;选矿技术随着世界经济的复苏和结构调整的加快,特别是我国经济的快速发展,拉动了我国钢铁工业持续高增长,我国钢铁总产量已经居世界第一,对于铁矿石进口依存度越来越高,已成为我国钢铁工业经济安全的重大隐患。
同时,在世界资源和环境问题日益严峻的情况下,提高资源的有效利用率,实现资源的最大化价值也是我们每个生产行业应该思考的问题。
因此,迫切需要依靠技术进步来最大限度地利用国内现有铁矿资源,提高铁矿石的自给率,缓解进口矿的压力,维持稳定、足量、优质的铁矿原料供给,以保障钢铁工业持续稳定的发展。
而铁矿的选矿技术作为这样一种直接关系到铁矿开采和使用的重要技术,也应该引起有关部门的重视,下文中笔者将结合自己的工作经验,对几种常见的铁矿选矿技术进行分析。
1.菱铁矿石选矿技术菱铁矿作为铁矿的最常见形式之一,其选矿技术对于整个铁矿的利用率影响是非常大的。
从菱铁矿石的性质上看,其理论铁品位相对于其他种类的铁矿石要低,并且从形式上看,经常与钙、镁、锰呈类质同象共生,以一种化合物或者混合物的形式共存,给铁矿的分析和开采都带来了不便,这也是菱铁矿在选矿过程中遇到的最大的困难。
实践中我们发现,如果采用传统的物理方法对菱铁矿进行选矿,那么精准度是非常低的,一般只能达到百分之四十五左右,因为菱铁矿的存在形式决定了其探测过程中,易受到其他元素的干扰。
铁矿选矿中存在的问题及优化方法研究

铁矿选矿中存在的问题及优化方法研究摘要:铁矿选矿是铁矿石加工过程中的关键环节,对提高矿石品位和提取率具有重要意义。
然而,铁矿选矿过程中存在一些问题,限制了其效率和经济性。
在大红山矿体开采深度持续增加的背景下,矿石性质变得更加复杂,硬度也在不断提升,可磨性变差,严重影响到流程稳定和选矿技术指标提升。
本文将分析铁矿选矿中存在的问题及优化方法,结合相关项目简述FX-610型旋流器。
关键词:铁矿选矿;优化方法;矿石品位;经济性在全球范围内,铁矿矿石的需求量持续增长,因为铁是现代工业的基础材料之一。
然而,铁矿选矿过程中存在一些问题,这些问题限制了选矿过程的效率和经济性,同时也影响了最终产品的质量。
本论文旨在研究铁矿选矿中存在的问题,并探讨一系列优化方法来改善选矿过程。
通过对问题的深入分析和优化方法的应用,我们希望能够提高铁矿选矿的效率和经济性,同时增加最终产品的质量和市场竞争力。
一、铁矿选矿中存在的问题(一)矿石品位波动问题1.影响因素铁矿石的品位波动是铁矿选矿中常见的问题。
品位是指矿石中所含有价值矿物的含量。
多种因素可以导致矿石品位的波动,包括矿石矿体的异质性、矿床地质条件的变化、采矿方法的不同以及采样和分析误差等。
这些因素导致了矿石品位在空间和时间上的不均匀分布,给选矿过程带来了困难。
2.后果和挑战矿石品位波动给铁矿选矿过程带来了一系列后果和挑战。
首先,由于矿石品位的不稳定性,选矿过程中的产量和品位往往难以稳定控制,导致了资源的浪费和能源的过度消耗。
其次,矿石品位的波动也增加了选矿工艺的复杂性,使得选矿设备的运行参数和操作条件需要频繁调整,降低了选矿过程的效率和稳定性。
此外,矿石品位的不稳定性还会影响到最终产品的质量和市场竞争力【1】。
(二)矿石颗粒大小分布不均匀问题1.影响因素铁矿石的颗粒大小分布不均匀也是铁矿选矿过程中的一个重要问题,见图1。
矿石颗粒的大小对选矿过程中的矿石分选效果和提取率具有重要影响。
铁矿石选矿中新技术的应用探究
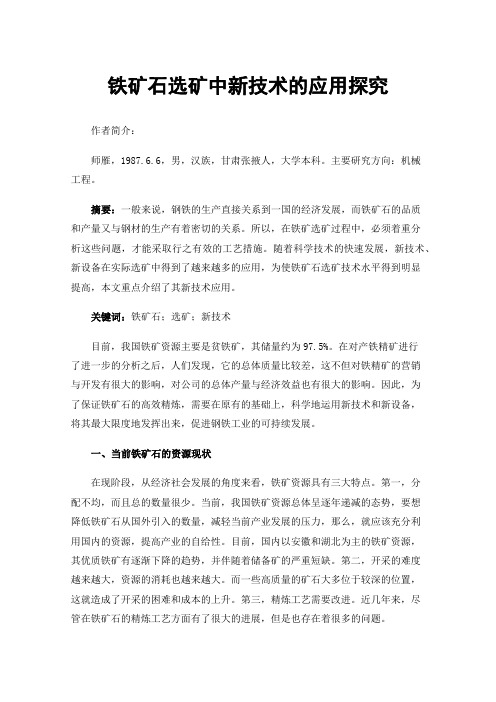
铁矿石选矿中新技术的应用探究作者简介:师雁,1987.6.6,男,汉族,甘肃张掖人,大学本科。
主要研究方向:机械工程。
摘要:一般来说,钢铁的生产直接关系到一国的经济发展,而铁矿石的品质和产量又与钢材的生产有着密切的关系。
所以,在铁矿选矿过程中,必须着重分析这些问题,才能采取行之有效的工艺措施。
随着科学技术的快速发展,新技术、新设备在实际选矿中得到了越来越多的应用,为使铁矿石选矿技术水平得到明显提高,本文重点介绍了其新技术应用。
关键词:铁矿石;选矿;新技术目前,我国铁矿资源主要是贫铁矿,其储量约为97.5%。
在对产铁精矿进行了进一步的分析之后,人们发现,它的总体质量比较差,这不但对铁精矿的营销与开发有很大的影响,对公司的总体产量与经济效益也有很大的影响。
因此,为了保证铁矿石的高效精炼,需要在原有的基础上,科学地运用新技术和新设备,将其最大限度地发挥出来,促进钢铁工业的可持续发展。
一、当前铁矿石的资源现状在现阶段,从经济社会发展的角度来看,铁矿资源具有三大特点。
第一,分配不均,而且总的数量很少。
当前,我国铁矿资源总体呈逐年递减的态势,要想降低铁矿石从国外引入的数量,减轻当前产业发展的压力,那么,就应该充分利用国内的资源,提高产业的自给性。
目前,国内以安徽和湖北为主的铁矿资源,其优质铁矿有逐渐下降的趋势,并伴随着储备矿的严重短缺。
第二,开采的难度越来越大,资源的消耗也越来越大。
而一些高质量的矿石大多位于较深的位置,这就造成了开采的困难和成本的上升。
第三,精炼工艺需要改进。
近几年来,尽管在铁矿石的精炼工艺方面有了很大的进展,但是也存在着很多的问题。
二、铁矿石选矿中新技术的应用对该矿石进行了化学分析,结果表明,该矿石中的有害组分中,硅酸铁占到了1.862%;结果表明,土壤中碳酸盐铁质元素含量均为0.844%,且具有明显的空间非均匀性。
在铁矿中,按行业分类,又可分为磁铁矿、赤铁矿等;根据天然类型的不同,又可分为假磁体石英岩、和磁体石英岩。
浅析铁矿选矿技术和工艺方法

浅析铁矿选矿技术和工艺方法摘要:伴随着我国能源采矿技术的持续提高,在我国矿产资源的采矿过程中,选矿技术和工艺方法方面也出现了巨大的变化,因此,在今后的选矿环节中,最终将会被更加简洁、环保且自动化的设备所取代,因此,选矿技术人员应该主动地参加选矿技术和工艺的改革,在满足原有选矿技术的应用要求的基础上,将更加现代化的选矿技术、工艺改革思维运用到现实的选矿中,从而促进我国选矿技术和工艺的发展,从而达到我国经济与资源的和谐发展。
关键词:铁矿选矿技术;工艺;方法1我国矿产资源开采现状近年来,随着全球矿产资源储备总量的下降,我国的能源采矿行业也出现了总体的下降,由于各种原因,我国的矿产资源开采状况大多集中在以下两个方面:第一,就是矿产资源的分布不平衡问题。
当前,安徽和湖北是中国最主要的矿藏,由于长期的开发,已有的矿藏已不多,因此,寻找新的矿藏显得十分紧迫;其次,采矿的难度每年都在增加,特别是对于已发现的矿业来说,地表上的好矿基本都被挖空了,剩下的好矿大部分都被埋在了地下,这不但增加了采矿的难度,还增加了采矿的成本与风险。
因此,在这种情况下,要推进我国能源开采产业的发展,就必须整合现有的资源,提高对有限的资源的利用效率,进而推进未来矿企的发展。
2铁矿选矿技术2.1矿石破碎目前,国内选矿厂采用的矿石粉碎技术一般采用粗破、中破和细破三个阶段,粗破采用的大多是旋回式破碎机,中破采用的一般是标准型圆锥式破碎机,而细破一般采用的是具有2.1或2.2 m的直径的短头型圆锥式破碎机。
在这个工序中,将原矿进行粉碎,然后进行筛选,筛选出来的产品再输送到研磨槽中进行二次加工。
2.2磨矿工艺在国内,磨矿过程是铁矿石加工的一个关键环节,一般都是两级磨矿,而在中小选矿企业中,一般都是多级磨矿。
随着科学技术的持续发展,磨矿过程中所使用的技术也在发生着变化,近年来,许多选矿厂都逐步使用了三级磨矿来取代原来的两级磨矿过程。
目前所使用的磨矿装置都比较小型,在磨矿过程结束后,一般都会使用螺杆式分级器来对矿石进行进一步的分级。
铁矿石精矿选矿技术的提高研究

铁矿石精矿选矿技术的提高研究1. 背景介绍随着经济的快速发展,铁及钢材需求量急剧增长,铁矿石成为重要的原材料。
选择高品质铁矿石、有效地利用资源,成为治理铁矿石资源延续与节约环境的走向。
从矿产资源的利用效率上来说,矿石精矿选矿技术,可以高效地分离出所需原矿,并降低其他无关物质对精矿的影响。
因此,研究铁矿石精矿选矿技术的提高,是必要的。
2. 精矿选矿工艺精矿选矿通常采用物理选矿、化学选矿、磁选、浮选等工艺。
其中物理选矿是提高精矿质量的传统方法之一,其最大的缺点在于无法去除矿石中的难浮铁矿物,这个问题可以通过化学选矿法解决。
磁选法适用于含铁磁矿物较高的土石矿和低品位磁铁矿选别,也可作为初步分选工艺,带高强磁的永磁分选机被广泛使用。
磁选的优点:环保、节能、干法选矿不污染环境、成本低;缺点:仅适用于被磁分离选别的矿物和产量的分离不如浮选。
铁矿石的浮选选别,是一种传统的铁矿石加工选别方法,适用于铁矿石的高效率加工分选,其优点是加工机械简单,节水环保,可以快速提高铁精矿的品位及回收率,成为目前应用最广泛的铁矿石精矿选别方法。
3. 精矿选别中的问题与解决方案精选的原理是根据物理化学性质不同,在选别介质中利用分离机械进行分离,并得到所需物质。
但是,铁矿石的精选过程中,仍然存在以下问题:3.1 矿石的难浮问题铁矿石中含有的难浮铁矿物,特别是石英、花岗岩和蛋白石类矿物等,这些难浮铁矿物会降低浮选的品位和回收率,影响铁矿石的应用价值。
对于这一问题,可以通过双链碳酸钙复合磁化材料和高强度永磁分选机进行解决,双链碳酸钙是一种新型无机多元复合磁化材料,具有磁性和稳定性,在磁化过程中可以选别掉一部分难浮铁矿物,高强度永磁分选机则可以在磁化后实现高效分离。
3.2 磁矿物选别问题铁矿石中含有的磁性矿物会增加磁选过程中的复杂度,磁矿物具有相似的磁性性质和磁化强度,高强度永磁分选机和涡流分选机被广泛应用于磁矿物的精选,可有效提高精选回收率。
铁矿选矿技术和工艺方法探讨

铁矿选矿技术和工艺方法探讨我国铁矿资源的分布区域比较明显,铁矿资源非常有限,已经表现出矿山不足的情况。
铁矿采矿过程中规划好选矿技术与工艺方法,提高铁矿找矿的准确性,进而提升铁矿资源的利用效率。
文章主要探讨铁矿选矿时的技术与工艺方法。
标签:铁矿;选矿技术;工艺方法Abstract:The distribution of iron ore resources in China is obvious and the iron ore resources are very limited. In order to improve the accuracy of iron ore prospecting and improve the utilization efficiency of iron ore resources,the ore dressing technology and technological method should be planned well in the course of iron ore mining. This paper mainly discusses the technology and processing methods of iron ore dressing.Keywords:iron ore;processing technology;processing method随着我国铁矿选矿技术的发展,铁矿选矿工艺中解决了大量的技术难度,致力于推进铁矿研究工作的发展,在此基础上提高铁矿选矿的技术水平。
我国在铁矿的选矿工作中投入了大量的研究,考虑到我国铁矿矿床复杂化、多样性的特点,应该有效落实选矿技术与工艺方法,以此来完善铁矿选矿的过程。
1 铁矿选矿技术1.1 矿石破碎技术矿石破碎技术是铁矿选矿的首要技术,其可分为粗破、中破、细破3个阶段。
矿石破碎中的粗破技术采用了旋回式破碎机,规格是 1.2m、1.5m,粗破铁矿石的块度不能超过1m,中破碎石技术采用的是标准型的圆锥式破碎机,规格为2.1m、2.2m,细破碎石技术中采用了短头型圆锥式破碎机,规格是2.1m、2.2m,中破、细破碎石技术处理后的铁矿石块度粒径不能超过12mm,经过矿石破碎技术处理后的铁矿石要送到磨矿槽内。
- 1、下载文档前请自行甄别文档内容的完整性,平台不提供额外的编辑、内容补充、找答案等附加服务。
- 2、"仅部分预览"的文档,不可在线预览部分如存在完整性等问题,可反馈申请退款(可完整预览的文档不适用该条件!)。
- 3、如文档侵犯您的权益,请联系客服反馈,我们会尽快为您处理(人工客服工作时间:9:00-18:30)。
关于铁矿选矿技术分析【摘要】随着近些年来我国经济的发展,我国的产业结构不断优化,各采矿业也都取得了显著的发展成绩,尤其是作为主要矿物资源供应的铁矿业,其无论是开采规模还是开采技术都有了显著的扩大和提高。
下文中笔者将结合自己的工作经验,对铁矿的选矿技术进行分析,以其完善和改进现行的铁矿技术,促进我国铁矿业的发展,笔者将从菱铁矿石选矿技术、褐铁矿石选矿技术、复合铁矿石选矿技术、多金属共生铁矿石选矿技术、鲕状赤铁矿石选矿技术、高硫、磷铁矿石选矿技术等几个方面对该问题进行浅析,诸多不足,还望批评指正。
【关键词】铁矿选矿技术;选矿技术随着世界经济的复苏和结构调整的加快,特别是我国经济的快速发展,拉动了我国钢铁工业持续高增长,我国钢铁总产量已经居世界第一,对于铁矿石进口依存度越来越高,已成为我国钢铁工业经济安全的重大隐患。
同时,在世界资源和环境问题日益严峻的情况下,提高资源的有效利用率,实现资源的最大化价值也是我们每个生产行业应该思考的问题。
因此,迫切需要依靠技术进步来最大限度地利用国内现有铁矿资源,提高铁矿石的自给率,缓解进口矿的压力,维持稳定、足量、优质的铁矿原料供给,以保障钢铁工业持续稳定的发展。
而铁矿的选矿技术作为这样一种直接关系到铁矿开采和使用的重要技术,也应该引起有关部门的重视,下文中笔者将结合自己的工作经验,对几种常见的铁矿选矿技术进行分析。
1.菱铁矿石选矿技术菱铁矿作为铁矿的最常见形式之一,其选矿技术对于整个铁矿的利用率影响是非常大的。
从菱铁矿石的性质上看,其理论铁品位相对于其他种类的铁矿石要低,并且从形式上看,经常与钙、镁、锰呈类质同象共生,以一种化合物或者混合物的形式共存,给铁矿的分析和开采都带来了不便,这也是菱铁矿在选矿过程中遇到的最大的困难。
实践中我们发现,如果采用传统的物理方法对菱铁矿进行选矿,那么精准度是非常低的,一般只能达到百分之四十五左右,因为菱铁矿的存在形式决定了其探测过程中,易受到其他元素的干扰。
因此,我们必须要寻求一个更加准确和高校的选矿方法,经过学界的反复研究和试验发现,焙烧后的菱铁矿的铁精矿的品位明显上升,究其原因是因为在铁矿烧损的过程中,铁的含量和品位都会随着燃烧的化学反应而增大,于是烧损越大,铁精矿品位也就越大。
所以,我们必须探求一种更加经济合理且科学的铁矿选矿方式,经过实践的反复摸索,笔者认为目前比较经济的菱铁矿的选矿方法主要以重选、强磁选为主,这两种方法充分的利用了菱铁矿的烧损后的铁品位的变化,使得铁矿选矿的精度明显增大,这个特点无疑能够有效的避免传统的物理选矿法造成的菱铁矿的选矿精准度低的现象。
但是这种做法也并不是十分完善的,实践中我们发现,采用该方法对菱铁矿进行选矿时,比较难以有效地降低铁精矿中的杂质含量,上文中我们也提到了菱铁矿的最大特点之一就是比较容易同其他的矿物质相结合,而在选矿过程中将这届杂质剔除对于铁矿的品位和精度来说都是非常重要的,因此在选用上述两种方法对菱铁矿进行选矿处理时,还应该从将低杂质含量的角度出发,采用一些辅助手段结合重选和强磁选方法对铁路进行选矿。
通过反复的试验,我们发现强磁选—浮选联合工艺能有效地降低铁精矿中的杂质含量,铁精矿焙烧后仍不失为一种优质炼铁原料。
2.褐铁矿石选矿技术对于褐铁矿石的选矿就相较于菱铁矿来说更为复杂,因为褐铁矿的性质决定了褐铁矿中富含结晶水,虽然结晶水对于物理选矿方法的选矿反应要高于菱铁矿,但是其铁精矿品位仍然很难达到百分之六十以上,这就给物理选矿方法的使用带来了很大障碍。
所以,同菱铁矿医院,如果选用物理方法对褐铁矿进行选矿,也应该对其进行一定的焙烧处理,只有焙烧到一定程度,铁精矿品位才会发生变化,其变化规律也同菱铁矿一样,烧损越大,铁精矿品位就越大,这也是褐铁矿同菱铁矿的主要相同点之一。
另外,由于褐铁矿的性质特点,致使其在破碎磨矿过程中极易泥化,而不似其他铁矿较易形成块状固体,这个特点一定程度上加大了褐铁矿的回收难度,同样的也降低了褐铁矿的回收价值,难以获得较高的金属回收率,所以我们在制定褐铁矿的选矿方式时,要充分考虑是否要进行破碎磨矿的步骤,尽可能的避免对褐铁矿的大规模的碾压,保留其完整度,有利于提高其回收价值。
实践中通过工程人员的不断检验和反复试验,筛选出几种最合适的褐铁矿选矿工艺,其中包括还原磁化焙烧—弱磁选、强磁选、重选、浮选等单独工艺和联合工艺,采用这些方式对褐铁矿进行选矿,可以有效的提高其铁精矿品位,有效的避免由于褐铁矿的破碎造成的回收难的问题,是较为理想的褐铁矿选矿方式,此外,为了达到更加理想的选矿效果,弥补以上方法中存在的不足,实践中我们还可以根据实际情况,将这些方法组合起来使用。
下面笔者就以某地的铁矿选矿实例,对其进行说明,即我国某省境内的著名铁坑褐铁矿石在进行了选择性絮凝—强磁选技术工业试验后发现,该褐铁矿内的铁金属回收率并不高,并且以现在的回收技术和选矿技术为基础,有关部门在认真计算后认为通过改造,其回收率至少可以提高10个百分点以上。
而同时又对该铁矿的相关技术设备进行了分析后发现,导致其回收率达不到标准的主要原因是由于絮凝设备及选择性絮凝工艺条件的控制尚未过关造成的,这种设备和技术上的缺陷严重的影响了铁矿的利用率,从而进一步影响了该铁矿的全面工业化,只有对其进行全面的技术升级和改革,才能实现更加高效的选矿和开采,才能发挥该褐铁矿的最大使用价值。
在科研单位向有关部门反映了这一问题后,该省的矿业管理部门对该问题给予了足够的重视,并投入资金和技术对褐铁矿的回收和选矿工作进行了完善,取得了显著的成果。
而这些成果也离不开近两年来的新型高梯度强磁选机及新型高效反浮选药剂的研制成功,正是由于这两种设备的问世和应用,才使得强磁选—反浮选—焙烧联合工艺取得了较大的技术进步,能够更加精准和高校的分选褐铁矿石。
即先通过强磁—反浮选获得低杂质含量的铁精矿,然后通过普通焙烧或者与磁铁精矿混合生产球团矿可大幅度提高产品的铁品位,仍不失为优质炼铁原料。
3.复合铁矿石选矿技术所谓复合铁矿,就是指在铁矿中含有不止一种铁矿物,这种情况对于铁矿石来说还是非常常见的。
并且由于我国的铁矿石的分布较广,地质结构较为复杂,导致我国大多铁矿石中都含有两种以上的铁矿物,这种情况一定程度上增加了铁矿石的选矿难度。
因为铁矿石的种类越多,相应的其可选性越差。
所以在对符合铁矿石进行选矿的时候我们要注意先对其定性和区分,一般来说,常见的复合铁矿石主要的共生铁矿成分为赤铁矿、镜铁矿、针铁矿、菱铁矿以及褐铁矿等,这些铁矿的共同点表现为他们都属于弱磁性铁矿物,所以在选矿时上文中我们提到的一些诸如强磁选等方法就比较不适用,不能很好的区分矿石中存在的不同铁矿成分,给选矿工作造成了不便。
但是,为了能够使铁矿更加合理高效的被开采,我们应不断完善和改进铁矿选矿技术,特别是对于复合铁矿的选矿,应该采取新型技术提高其铁精矿品位。
对此,有关部门也引起了足够重视,并组织了有关研究部门对该问题进行了分析和试验,最后经过反复的验证,认为在进行复合铁矿的选矿工作时,采用弱磁—强磁—浮选和磁化焙烧—反浮选等联合工艺可以取得较好的效果。
4.多金属共生铁矿石选矿技术所谓多金属共生,就是指在铁矿石中含义多种金属矿物,且各个矿物之间的共生关系较为复杂,从而导致了铁矿选矿的困难。
多金属共生铁矿是除了复合铁矿之外,另一个较为复杂的铁矿存在形式,同样也是铁矿选矿的难点所在。
就我国境内的多金属共生铁矿的类型来看,主要有包头白云鄂博稀土铁矿和攀枝花钒钛磁铁矿等,这些类型的铁矿石的特点是矿物组成及共生关系复杂,由此造成铁精矿选别指标低及共伴生有价元素的回收率低,因为对其采用常规的物理选矿法并不能达到良好的选矿效果,其铁精矿品位甚至比菱铁矿还要低,这种情况下是无法达到采矿需要的选矿效果的。
而就以上两种多金属共生铁矿来说,其中以包头白云鄂博稀土氧化铁矿石尤为难选,在有关部门和专家经过了一系列的研究和试验后发现,采用目前包钢选矿厂氧化铁矿行的弱磁—强磁—反浮选工艺进行选铁能够达到相对理想的效果。
因为在白云鄂博稀土氧化铁矿石中,其强磁精矿中主要有易浮类萤石、碳酸盐等矿物和难浮难选的含铁硅酸盐类矿物,所以要针对这些金属物质的特性制定专门的选矿方法进行各个击破,经过反复的试验和论证,我们发现对于易浮类萤石、碳酸盐等矿物的选矿必须的选矿必须要采用多种磁处理工艺和浮选工艺才能完成,包钢选矿厂通过几十年研究和生产实践已经形成了较成熟方法,即以水玻璃为抑制剂、ge-28为捕收剂的弱碱性反浮选生产工艺,而难浮难选的含铁硅酸盐类矿物一直没有得到有效分离,致使铁精矿品位较低(徘徊在百分之五十五以下),精矿中钾纳含量高。
对于取自于现场,细度为-0.076mm占百分之88左右、铁品位百分之43.5左右的强磁精矿样,采用优化组合的反浮选—正浮选工艺流程,并在正浮选作业采用新型高效捕收剂,全流程浮选闭路试验指标为精矿产率百分之53左右、精矿铁品位百分之62左右、回收率百分之75左右,同时有害元素如p、k2o、na2o、f降低幅度很大,为改善该类型铁矿石的选别指标开辟了一条有效的新途径,就目前选矿工艺来看,该方法是最为行之有效的针对白云鄂博稀土氧化铁矿石的选矿方法,可以有效的处理其中存在的不同金属含量对矿石选矿结果的影响,得到一个较为符合实际情况的结果。
另外,对于另一种较难处理的多金属共生铁矿形式的攀枝花钒钛磁铁矿石,有关单位和工程部门也在认真的研究和分析了其自身的金属特点后,结合白云鄂博稀土氧化铁矿石相关选矿处理方法,制定了一个较为符合实际的选矿工艺流程,即分别采用细筛—再磨工艺选铁和高梯度强磁—浮选工艺选钛等方法对其进行多层次的选矿处理,旨在减少其他金属形式对铁矿中铁的含量的影响,实践证明该矿石的各项选别指标均得到显著提高。
5.鲕状赤铁矿石选矿技术鲕状赤铁矿的最主要的特点就是嵌布粒度极细且经常与菱铁矿、鲕绿泥石和含磷矿物共生或相互包裹,因此其选矿工作也较为困难。
相较于上述的几种矿石的选矿来说,鲕状赤铁矿石是目前国内外公认的最难选的铁矿石类型。
过去曾对该类型铁矿石进行了大量的选矿试验研究工作,其中还原焙烧—弱磁选工艺的选别指标相对较好,但由于其技术难点是需要超细磨,而目前常规的选矿设备及药剂难以有效地回收-10μm的微细粒铁矿物,因此该类型铁矿石资源基本没有得到利用。
由此可见,处理好鲕状赤铁矿中的细粒,就可以有效的解决其选矿难题,但是在传统的技术条件下,这个问题一直没有被攻克,也就导致了大量的鲕状赤铁矿无法被开采和利用,呆滞了资源的闲置甚至是浪费。
但是近些年,随着我国可利用的铁矿资源逐渐减少,研究鲕状赤铁矿石的高效选矿技术已凸显重要性和紧迫性,又因为科学技术水平的不断提高,给鲕状赤铁矿的选矿技术和工艺的实现带来了可能,所以有关部门加大了在这方面的资金和技术投入,旨在研发和探索一种能够克服鲕状赤铁矿中的细粒结构的方法。