内涂层防腐技术详细版
防腐涂层工艺技术

防腐涂层工艺技术防腐涂层工艺技术是一种常用的防止金属材料腐蚀的方法。
随着工艺技术的不断发展,防腐涂层的种类也越来越多样化,其中包括涂漆、喷涂、浸涂、热浸镀等技术。
本文将以涂漆为例,介绍防腐涂层工艺技术的过程和基本原理。
涂漆是一种常见的防腐涂层工艺技术,它通过涂覆一层具有阻隔氧气和防腐能力的涂料在金属表面,起到保护金属材料的作用。
涂漆的工艺流程主要包括表面处理、底漆涂装和面漆涂装三个步骤。
首先,在进行涂漆之前,需要对金属表面进行处理。
常见的表面处理方法有除油、除锈和打磨。
除油是通过化学或物理方法,将金属表面的油脂、污垢等杂质清除干净,使涂料能够与金属表面充分接触。
除锈是将金属表面的铁锈进行清除,以免影响涂层附着力和使用寿命。
打磨则是通过机械磨削,使金属表面光滑,提高涂漆的附着力。
接下来是底漆涂装过程。
底漆是涂装过程中的第一层涂料,它主要起到填充和增加附着力的作用。
底漆涂装需要控制好涂层的厚度和均匀度,以确保涂层的质量。
常见的涂装方法有手涂、刷涂和喷涂。
手涂和刷涂适用于涂装面积较小的金属材料,而喷涂则适用于涂装面积较大的金属材料。
最后是面漆涂装过程。
面漆是涂装过程中的第二层涂料,它主要起到美观和防腐的作用。
面漆涂装过程与底漆涂装类似,也需要控制好涂层的厚度和均匀度。
在面漆涂装过程中,还可以根据需要进行多次涂装,以增加涂层的厚度和防腐能力。
总结起来,防腐涂层工艺技术是一种常用的防止金属材料腐蚀的方法。
涂漆是其中一种常见的工艺技术,它通过涂覆具有阻隔氧气和防腐能力的涂料在金属表面,起到保护金属材料的作用。
涂漆的工艺流程主要包括表面处理、底漆涂装和面漆涂装三个步骤。
通过控制涂层的厚度和均匀度,可以提高涂层的质量和使用寿命。
在实际应用中,还可以根据具体需要选择不同的涂料和涂装方法,以提高防腐效果。
钢质管道液体环氧树脂涂料内防腐层技术标准(一)

钢质管道液体环氧树脂涂料内防腐层技术标准(一)钢质管道液体环氧树脂涂料内防腐层技术标准一、背景介绍钢质管道是石化、电力、化肥等行业常用的管道材料,而钢质管道的耐腐蚀性是保证管道长期稳定运行的重要因素。
因此,在钢质管道施工和维护过程中,内防腐层的作用尤为重要。
二、液体环氧树脂内涂技术液体环氧树脂内涂技术是目前内防腐层常用的一种涂层方式,其具有涂层质量高、施工过程简单、对环境污染小等优点。
三、技术标准要求1.涂料的质量应符合相关标准要求,如聚氨酯聚醇、环氧树脂等。
2.涂料应进行充分搅拌,并根据施工要求进行适当稀释。
3.钢质管道内表面应进行喷砂、喷丸或其他方式处理,保证表面清洁度符合要求。
4.施工前应进行预热处理,使钢质管道的温度达到一定要求。
5.涂料施工应按规定的厚度进行,保证涂层质量。
6.涂料施工完毕后,应进行检测,如检测不合格应及时修补。
四、结论液体环氧树脂内涂技术是目前内防腐层处理的主要方式,其施工过程中要遵守相关的技术标准,保证施工质量和涂层效果。
同时,对施工质量不合格的地方要及时进行修补,确保管道安全运行。
五、注意事项1.涂料施工时应注意环境湿度和温度,避免施工过程中出现结块、起泡等情况。
2.涂料施工时应使用适当的工具,如刷子、滚筒等,确保涂料均匀。
3.涂料施工结束后应及时清理工具和现场,避免涂料残留和污染。
4.涂料储存时应注意防火、防水、防潮,保证涂料品质。
5.施工过程中,应加强安全措施,严格遵守安全操作规程。
六、总结钢质管道液体环氧树脂涂料内防腐层技术标准是保证管道运行安全的重要措施之一,其施工过程要遵守严格的标准,确保涂层质量、涂层厚度和施工环境的卫生。
同时注意施工中的安全措施和涂料存储的细节,提高涂层质量和施工安全度,为保障管道的正常运行提供坚实保障。
钢管内壁防腐施工技术方案

钢管内壁防腐施工技术方案Anti-corrosion technique plan of the pipe’s inner wall1.施工工艺 construction technology喷砂除锈检验底漆检验面漆检验喷涂标志出厂Blast cleaning→inspection→primer→inspection→finishing coat→inspection→spraying mark→delivery2. 喷砂除锈 blast cleaning2.1管道内表面高压喷砂除锈达到AWWAC210-97规定要求,表面粗糙度达到40-70µm;The pipe’s inner face should reach the AWWAC210-97 requirements after high pressure blast cleaning, and the roughness of surface should reach 40-70um.2.2除锈后涂装前的管道表面应用高压空气吹除干净,保证管道表面无锈、无尘或其它表面附着物,确保漆膜和钢管表面的附着力。
After basting cleaning, the surface of pipes should be cleaned with high pressure air before coating to ensure the surface no rust, dust and others so as to keep the adhesion of paint film and the surface of pipes.2.3除锈后合格的管道,在4小时内尽快涂装,以防止二次生锈。
The qualified pipes after blast cleaning should be coated within 4 hours as soon as possible to prevent the second rust.3. 钢管内壁喷涂 inner wall spray coating of pipes3.1当空气中的相对湿度大于85%、钢管表面温度低与在大气露点以上3ºC时,或高与60ºC时禁止施工作业。
内外涂覆钢管技术参数

内外涂覆钢管技术参数一、概述内外涂覆钢管是一种常用的管道材料,广泛应用于石油、天然气、化工、供水等领域。
该技术通过在钢管内外表面施加涂层,提高了钢管的防腐性能和耐久性。
本文将深入探讨内外涂覆钢管的技术参数。
二、内涂层技术参数1. 内涂层材料常用的内涂层材料包括环氧树脂、聚乙烯、三层共聚物等。
不同材料具有不同的特性,选择合适的内涂层材料可以提高钢管的耐腐蚀性能和流体输送效果。
2. 内涂层厚度内涂层的厚度是衡量其防腐能力的重要参数。
一般来说,内涂层的厚度应符合设计要求,并经过严格的检测和控制。
常见的内涂层厚度为0.5mm至1.0mm。
3. 内涂层附着力内涂层的附着力是指其与钢管表面的粘结强度。
良好的附着力可以确保内涂层在运输和使用过程中不易剥离或脱落,从而提高钢管的防腐性能。
4. 内涂层耐温性能由于内涂层在输送高温介质时会受到较大的热负荷,因此其耐温性能也是重要的参数之一。
常见的内涂层耐温范围为-40℃至120℃。
5. 内涂层耐化学性能内涂层需要具有良好的耐化学性能,能够抵抗酸碱、盐霜等腐蚀性介质的侵蚀。
一般来说,合格的内涂层应能够在各种化学介质中保持稳定性。
三、外涂层技术参数1. 外涂层材料常用的外涂层材料包括环氧树脂、聚乙烯、聚脂砂浆等。
不同材料具有不同的特性,选择合适的外涂层材料可以提高钢管的耐腐蚀性能和抗撞击性能。
2. 外涂层厚度外涂层的厚度是衡量其防腐能力的重要参数。
一般来说,外涂层的厚度应符合设计要求,并经过严格的检测和控制。
常见的外涂层厚度为1.0mm至2.5mm。
3. 外涂层附着力外涂层的附着力是指其与钢管表面的粘结强度。
良好的附着力可以确保外涂层在运输和使用过程中不易剥离或脱落,从而提高钢管的防腐性能。
4. 外涂层耐温性能由于外涂层在不同环境条件下会受到不同的温度影响,因此其耐温性能也是重要的参数之一。
常见的外涂层耐温范围为-40℃至80℃。
5. 外涂层抗撞击性能外涂层需要具有良好的抗撞击性能,能够抵御外界物体的碰撞、摩擦等力量对钢管的破坏。
钢制管道液体环氧涂料内防腐涂层技术标准
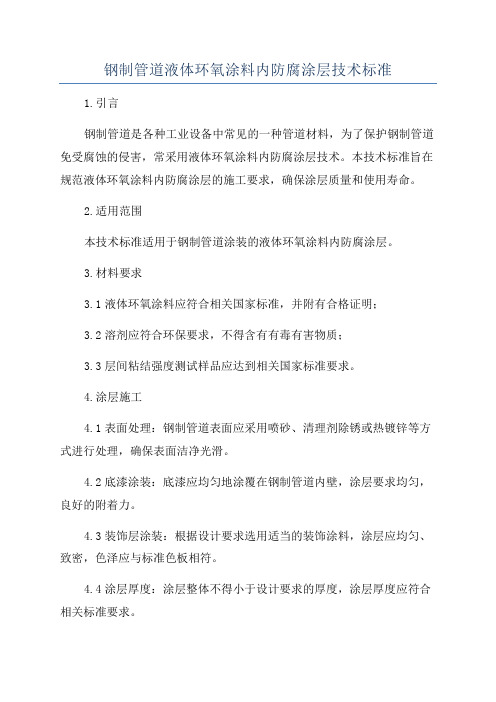
钢制管道液体环氧涂料内防腐涂层技术标准1.引言钢制管道是各种工业设备中常见的一种管道材料,为了保护钢制管道免受腐蚀的侵害,常采用液体环氧涂料内防腐涂层技术。
本技术标准旨在规范液体环氧涂料内防腐涂层的施工要求,确保涂层质量和使用寿命。
2.适用范围本技术标准适用于钢制管道涂装的液体环氧涂料内防腐涂层。
3.材料要求3.1液体环氧涂料应符合相关国家标准,并附有合格证明;3.2溶剂应符合环保要求,不得含有有毒有害物质;3.3层间粘结强度测试样品应达到相关国家标准要求。
4.涂层施工4.1表面处理:钢制管道表面应采用喷砂、清理剂除锈或热镀锌等方式进行处理,确保表面洁净光滑。
4.2底漆涂装:底漆应均匀地涂覆在钢制管道内壁,涂层要求均匀,良好的附着力。
4.3装饰层涂装:根据设计要求选用适当的装饰涂料,涂层应均匀、致密,色泽应与标准色板相符。
4.4涂层厚度:涂层整体不得小于设计要求的厚度,涂层厚度应符合相关标准要求。
4.5硬度测试:完工后的涂层应经过硬度测试,测试结果应达到相应标准要求。
5.工艺要求5.1严格按照涂料生产厂家提供的涂料配方进行调配和搅拌,确保涂料质量稳定。
5.2喷涂设备的选择和维护应符合相关标准,设备的喷射速度、角度和距离应符合涂料生产厂家的要求。
5.3施工环境的湿度和温度应符合涂料生产厂家的要求,避免施工过程中产生气泡、丝状物等缺陷。
5.4涂层干燥和固化的时间应符合相关标准要求,避免涂层过早暴露于工作环境。
6.检验方法6.1涂层厚度应使用涂膜厚度测量仪进行测量,测量结果应记录并保存。
6.2层间粘结强度应使用剥离强度测试仪进行测量,测试结果应达到相关标准要求。
6.3硬度应使用硬度计进行测量,测试结果应达到相应标准要求。
7.贮存和包装7.1涂层完全固化后,应按相关标准要求对钢制管道进行封装和标识。
7.2封装和储存的环境应干燥通风,避免阳光直射和腐蚀物质侵蚀。
7.3涂料应储存在防火储存室内,避免高温和火灾。
钢质管道内外防腐技术要求
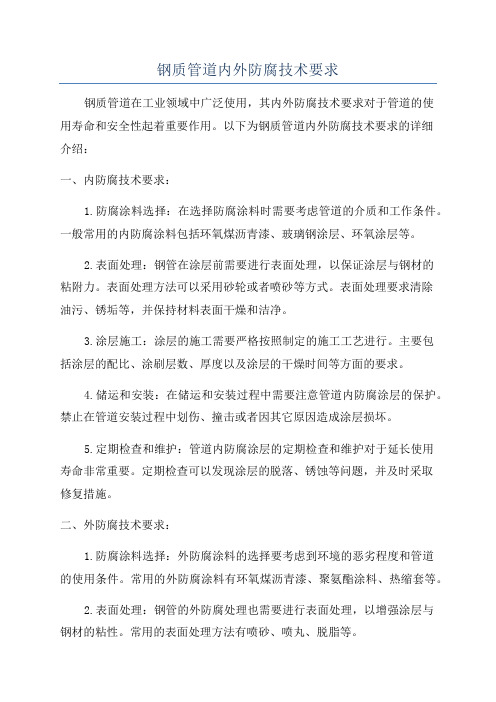
钢质管道内外防腐技术要求钢质管道在工业领域中广泛使用,其内外防腐技术要求对于管道的使用寿命和安全性起着重要作用。
以下为钢质管道内外防腐技术要求的详细介绍:一、内防腐技术要求:1.防腐涂料选择:在选择防腐涂料时需要考虑管道的介质和工作条件。
一般常用的内防腐涂料包括环氧煤沥青漆、玻璃钢涂层、环氧涂层等。
2.表面处理:钢管在涂层前需要进行表面处理,以保证涂层与钢材的粘附力。
表面处理方法可以采用砂轮或者喷砂等方式。
表面处理要求清除油污、锈垢等,并保持材料表面干燥和洁净。
3.涂层施工:涂层的施工需要严格按照制定的施工工艺进行。
主要包括涂层的配比、涂刷层数、厚度以及涂层的干燥时间等方面的要求。
4.储运和安装:在储运和安装过程中需要注意管道内防腐涂层的保护。
禁止在管道安装过程中划伤、撞击或者因其它原因造成涂层损坏。
5.定期检查和维护:管道内防腐涂层的定期检查和维护对于延长使用寿命非常重要。
定期检查可以发现涂层的脱落、锈蚀等问题,并及时采取修复措施。
二、外防腐技术要求:1.防腐涂料选择:外防腐涂料的选择要考虑到环境的恶劣程度和管道的使用条件。
常用的外防腐涂料有环氧煤沥青漆、聚氨酯涂料、热缩套等。
2.表面处理:钢管的外防腐处理也需要进行表面处理,以增强涂层与钢材的粘性。
常用的表面处理方法有喷砂、喷丸、脱脂等。
3.涂层施工:涂层施工时需要遵循规定的工艺流程,涂刷面积、厚度和干燥时间等都需要符合要求。
如采用热喷涂工艺,需要注意控制喷涂温度和喷涂速度。
4.储运和安装:在储运和安装过程中,需要保护好外防腐涂层以防止损坏。
可以采用塑料薄膜或者其他保护措施来保障涂层的完整性。
5.定期检查和维护:外防腐涂层也需要定期检查和维护。
检查时可以使用无损检测技术来评估涂层的粘附力和质量,发现问题及时修复。
以上是钢质管道内外防腐技术要求的一些基本内容。
对于不同的工程和环境条件,具体的防腐要求可能会有所不同。
因此,在实际施工中,应根据具体的要求来选择合适的防腐涂料和施工工艺,并加强日常的检查和维护工作,以确保钢质管道的使用寿命和安全性。
压力管道的管道防腐技术及其要求

压力管道的管道防腐技术及其要求压力管道是从事石化、化工、能源等行业生产的关键设备,管道防腐技术在其中起着至关重要的作用。
本篇文章就围绕着压力管道的管道防腐技术及其要求展开。
一、压力管道的基本概念压力管道是一种用于输送流体介质的管道,一般工作压力大于或等于0.1 MPa的管道均属于压力管道。
压力管道多用于石化、化工、冶金、电力等行业,由于输送的介质特性、操作条件及环境等因素的影响,使得管道材料会发生各种腐蚀、磨损、老化等现象,严重影响其使用寿命和安全性能。
其中,管道腐蚀是威胁管道生命安全的一个主要问题。
二、压力管道的管道防腐技术1. 内壁涂层防腐技术内壁涂层防腐技术是将一定性能的涂料涂在管道内壁,与管道材料形成一层整体的防腐层。
内壁涂层防腐技术不仅可以抵御腐蚀,同时还可以起到防止热能、电能、化学能等在管道内部的热、电、化学反应的作用。
内壁涂层一般分为有机涂层和无机涂层两类。
其中,有机涂层是指使用有机涂料制作的防腐层,而无机涂层是指使用无机涂料制作的防腐层。
2. 外壁防腐技术外壁防腐技术是在压力管道外壁涂上具有一定性能的涂料,从而形成一层完整的防腐层。
与内壁涂层技术相比,外壁防腐技术有着更高的技术难度和复杂性。
外壁涂层防腐材料主要分为热喷涂、机械喷涂和涂刷三种。
其中,热喷涂技术是将具有防腐性能的材料熔融喷射在管道表面,使其形成密实坚固的防腐层,具有使用寿命长、耐腐蚀性能强等特点。
3. 阴极保护技术阴极保护技术是一种常用的管道防腐技术,其工作原理是利用外部电位(电正极),通过导体、阳极保护系统和被保护金属构成电池电路,从而在金属表面形成一层保护膜,从而达到防腐的目的。
阴极保护技术主要分为直流阴极保护法、电泳均匀阴极保护法、保护电流源阴极保护法、铁素体交流阴极保护法等几个方法。
阴极保护技术具有操作简单,使用寿命长,效果稳定等诸多优点,是广泛应用的一种管道防腐技术。
三、管道防腐技术应符合的要求1. 管道防腐涂料应具有均匀、致密、无裂纹等特性;2. 管道防腐层的厚度应符合国家标准;3. 管道防腐层的质量要求达到相关国家标准;4. 管道防腐层与管道本体的结合强度要求达到相关国家标准;5. 接头处和构造细节部位的防腐处理要符合国家标准;6. 管道防腐层贮存、施工、检验均需严格按照相关标准进行。
内防腐涂层呈管道接头的连接与防腐
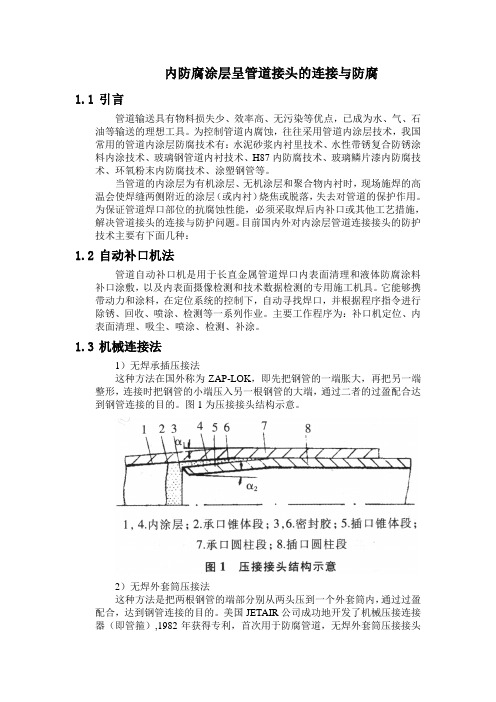
内防腐涂层呈管道接头的连接与防腐1.1引言管道输送具有物料损失少、效率高、无污染等优点,已成为水、气、石油等输送的理想工具。
为控制管道内腐蚀,往往采用管道内涂层技术,我国常用的管道内涂层防腐技术有:水泥砂浆内衬里技术、水性带锈复合防锈涂料内涂技术、玻璃钢管道内衬技术、H87内防腐技术、玻璃鳞片漆内防腐技术、环氧粉末内防腐技术、涂塑钢管等。
当管道的内涂层为有机涂层、无机涂层和聚合物内衬时,现场施焊的高温会使焊缝两侧附近的涂层(或内衬)烧焦或脱落,失去对管道的保护作用。
为保证管道焊口部位的抗腐蚀性能,必须采取焊后内补口或其他工艺措施,解决管道接头的连接与防护问题。
目前国内外对内涂层管道连接接头的防护技术主要有下面几种:1.2自动补口机法管道自动补口机是用于长直金属管道焊口内表面清理和液体防腐涂料补口涂敷,以及内表面摄像检测和技术数据检测的专用施工机具。
它能够携带动力和涂料,在定位系统的控制下,自动寻找焊口,并根据程序指令进行除锈、回收、喷涂、检测等一系列作业。
主要工作程序为:补口机定位、内表面清理、吸尘、喷涂、检测、补涂。
1.3机械连接法1)无焊承插压接法这种方法在国外称为ZAP-LOK,即先把钢管的一端胀大,再把另一端整形,连接时把钢管的小端压入另一根钢管的大端,通过二者的过盈配合达到钢管连接的目的。
图1为压接接头结构示意。
2)无焊外套筒压接法这种方法是把两根钢管的端部分别从两头压到一个外套筒内,通过过盈配合,达到钢管连接的目的。
美国JETAIR公司成功地开发了机械压接连接器(即管箍),1982年获得专利,首次用于防腐管道,无焊外套筒压接接头结构见图2。
这种接头由外套和内管(管道本身)组成,两内管接触端面之间有密封垫,为保证压接后接头材质不超过弹性极限,外套内壁加工有特殊螺纹,以适应内管的外径偏差。
内管的外径偏大时,螺纹被全部推倒;外径偏小时,螺纹被部分推倒。
螺纹内涂有密封胶,压接时密封胶起润滑作用,并在固化后形成可靠的密封带,使外套与内管紧紧压接成一体。
混凝土防腐涂层的应用技术

混凝土防腐涂层的应用技术一、引言混凝土防腐涂层是在混凝土表面形成一层保护膜,以防止混凝土内部钢筋锈蚀和混凝土表面受到腐蚀的一种技术。
它广泛应用于建筑、桥梁、水利、化工等领域,是保障混凝土结构安全的重要手段之一。
本文将从混凝土防腐涂层的原理、应用技术、材料选择、施工要点和检验方法等方面进行详细介绍。
二、混凝土防腐涂层的原理混凝土防腐涂层的原理是通过涂层形成一层保护膜,以防止混凝土内部钢筋锈蚀和混凝土表面受到腐蚀。
涂料可以阻隔氧和水分进入混凝土内部,从而减缓钢筋锈蚀和混凝土表面腐蚀的速度。
同时,涂层的防护层还可以降低混凝土表面的渗透性和提高耐久性,使混凝土结构更加坚固耐用。
三、混凝土防腐涂层的应用技术1.涂层种类混凝土防腐涂层的种类有很多,如环氧树脂、聚氨酯、丙烯酸、硅酮等。
不同种类的涂料具有不同的特性,应根据不同的环境和使用要求来选择。
2.表面处理在施工前,需要对混凝土表面进行处理。
首先,需要清除表面的杂物和污垢,清除油污和灰尘。
同时,还需要对表面进行打磨和修补,以保证涂层与混凝土表面的粘结力。
3.涂层施工在涂层施工过程中,需要注意以下几点:(1)涂层厚度应符合设计要求。
(2)涂层应均匀涂布,没有漏涂和起泡现象。
(3)每层涂料之间应留有足够的干燥时间。
(4)涂层应在室温下施工,避免在高温、低温或潮湿的环境下施工。
4.涂层养护涂层施工完成后,需要对涂层进行养护。
在养护期间,应避免机械损坏和异物污染。
同时,还需要定期检查涂层的状况,并及时进行修补。
四、材料选择混凝土防腐涂层的材料选择应根据不同的环境和使用要求来选择。
通常,可以从以下几个方面来考虑:1.防腐性能涂层的防腐性能是选择涂料的重要因素。
通常,环氧树脂涂料和聚氨酯涂料具有良好的防腐性能。
2.耐久性涂层的耐久性是考虑涂料的另一个重要因素。
通常,聚氨酯涂料具有较好的耐久性。
3.施工性能涂料的施工性能也是选择涂料的重要因素。
通常,丙烯酸涂料具有良好的施工性能。
钢质管道液体环氧树脂涂料内防腐层技术标准

钢质管道液体环氧树脂涂料内防腐层技术标准钢质管道液体环氧树脂涂料内防腐层技术标准主要包括以下内容:
1. 涂料材料要求:涂料应为环氧树脂涂料,具有优良的防腐性能、附着力和耐腐蚀性能。
涂料应符合相关国家或地区标准要求。
2. 表面处理:管道表面应进行除锈和清洁处理,确保表面无杂质、油污、锈蚀等。
可采用喷砂或喷丸等方法进行表面处理。
3. 涂料施工:涂料应按照涂料生产商的施工工艺要求进行施工。
涂料应均匀涂覆在管道内壁上,形成均匀的涂层。
涂料的厚度应符合设计要求。
4. 涂层质量控制:涂层施工完成后,应进行涂层质量检查。
检查涂层的附着力、厚度、外观等指标,确保涂层质量符合要求。
5. 温度和湿度控制:涂料施工过程中应控制施工环境的温度和湿度。
温度和湿度对涂料的干燥和固化速度有影响,应按照涂料生产商的要求进行控制。
6. 涂层养护:涂料施工完成后,应进行养护措施。
涂层需要一定的时间进行干燥和固化,期间应防止外界物质的侵入和损坏。
7. 检测和验收:涂层施工完成后,应进行涂层的检测和验收。
检测涂层的厚度、附着力、耐腐蚀性能等指标,确保涂层符合要求。
总之,钢质管道液体环氧树脂涂料内防腐层技术标准包括涂料材料要求、表面处理、涂料施工、涂层质量控制、温度和湿度控制、涂层养护、检测和验收等方面的要求,旨在确保涂层质量符合设计要求
并具有良好的防腐性能。
内部防腐涂层技术

内部防腐涂层技术1. 内部防腐涂层的作用内部防腐涂层可以提供以下几个重要的作用:1. 腐蚀阻隔:内部防腐涂层可以隔离金属表面与介质之间的接触,有效防止腐蚀发生。
腐蚀阻隔:内部防腐涂层可以隔离金属表面与介质之间的接触,有效防止腐蚀发生。
2. 抗化学腐蚀:很多工业设备需要与化学物质接触,内部涂层可以提供抗化学腐蚀的保护层。
抗化学腐蚀:很多工业设备需要与化学物质接触,内部涂层可以提供抗化学腐蚀的保护层。
3. 磨擦减少:内部涂层可以减少设备内部流体的摩擦,降低能量损失和设备的磨损。
磨擦减少:内部涂层可以减少设备内部流体的摩擦,降低能量损失和设备的磨损。
4. 增强维护:内部涂层也可以简化设备的维护工作,减少停机时间和维修成本。
增强维护:内部涂层也可以简化设备的维护工作,减少停机时间和维修成本。
2. 内部防腐涂层的种类内部防腐涂层有多种不同的类型和材料可供选择。
以下是一些常见的内部防腐涂层种类:1. 环氧涂层:环氧涂料具有良好的抗腐蚀性能和耐化学物质侵蚀能力。
环氧涂层:环氧涂料具有良好的抗腐蚀性能和耐化学物质侵蚀能力。
2. 聚酯涂层:聚酯涂料通常用于对高温和化学侵蚀有抵抗能力的场景。
聚酯涂层:聚酯涂料通常用于对高温和化学侵蚀有抵抗能力的场景。
3. 聚氨酯涂层:聚氨酯涂料适用于需要耐磨损和耐久性的设备。
聚氨酯涂层:聚氨酯涂料适用于需要耐磨损和耐久性的设备。
4. 橡胶涂层:橡胶涂料可以提供很好的物理保护和耐腐蚀性能。
橡胶涂层:橡胶涂料可以提供很好的物理保护和耐腐蚀性能。
选择适合的涂层种类应考虑设备的特殊要求、工作环境以及涂层的成本和施工难度等因素。
3. 内部防腐涂层的施工步骤内部防腐涂层的施工一般包括以下几个步骤:1. 表面准备:彻底清除设备内部表面的污垢、油脂和锈蚀物,确保表面清洁。
表面准备:彻底清除设备内部表面的污垢、油脂和锈蚀物,确保表面清洁。
2. 底漆涂覆:使用适当的底漆涂层,以增加涂层的附着力并提供额外的腐蚀保护。
内涂层防腐技术正式样本
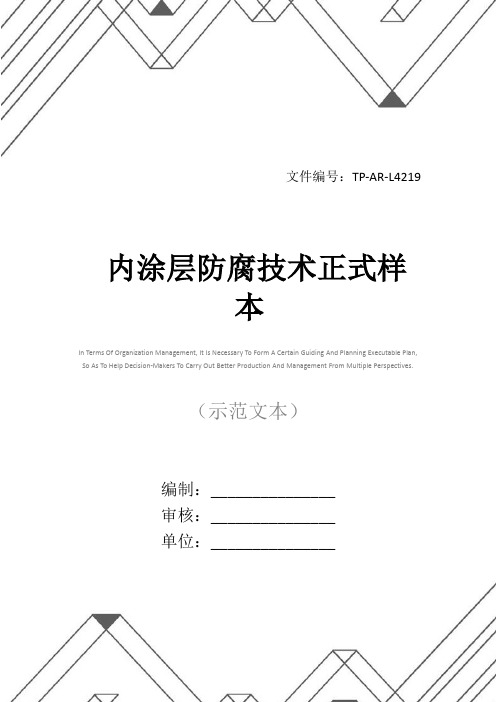
文件编号:TP-AR-L4219In Terms Of Organization Management, It Is Necessary To Form A Certain Guiding And Planning Executable Plan, So As To Help Decision-Makers To Carry Out Better Production And Management From Multiple Perspectives.(示范文本)编制:_______________审核:_______________单位:_______________内涂层防腐技术正式样本内涂层防腐技术正式样本使用注意:该解决方案资料可用在组织/机构/单位管理上,形成一定的具有指导性,规划性的可执行计划,从而实现多角度地帮助决策人员进行更好的生产与管理。
材料内容可根据实际情况作相应修改,请在使用时认真阅读。
采用涂、镀、注、渗、化学转化、热流强化、形变强化等措施,改变材料表面的化学成分、组织结构、力学状态等理化和机械性能,使材料表面获得一层保护性的覆盖层或强化层,可以避免金属基体与介质的直接接触,有的覆盖层还具有电化学保护作用或缓蚀作用。
这类方法经济有效,是目前用得最为广泛的防腐蚀措施。
(1) 材料的选择目前国外普遍采用防腐蚀的内涂层,大都是环氧型、改进环氧型、环氧酚醛型或尼龙等系列的涂层。
这些涂料是一种在苛刻的腐蚀条件下防腐性能优异、使用寿命长的特种涂料。
在腐蚀介质中具有良好的化学稳定性,附着力强,柔韧性好,抗失压起泡,机械性能(耐磨性、抗冲击性)好等优点,从而使金属减缓腐蚀,延长使用寿命。
针对一种防腐涂料它只能在某种环境中才能发挥其作用,不可能满足各种环境的不同要求,这就需要根据实际情况,采取“多层异类”结构的涂层工艺。
一般工程施工中,主要采用“底漆+中间层+面漆”的结构形式,以期达到比较满意的防腐效果。
管道内防腐涂层技术
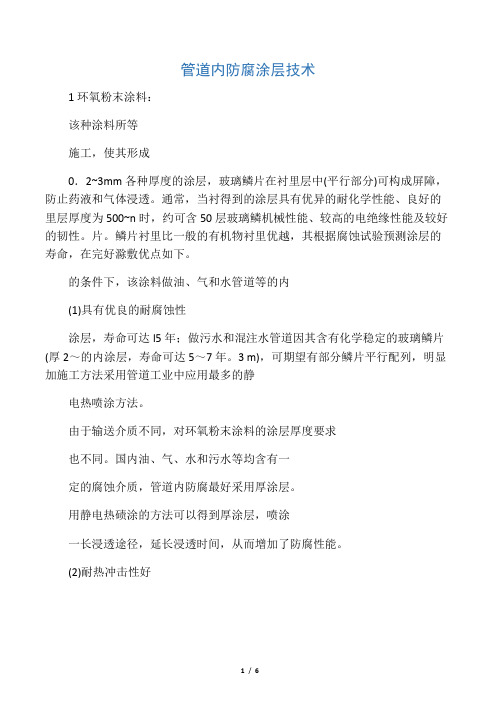
管道内防腐涂层技术1环氧粉末涂料:该种涂料所等施工,使其形成0.2~3mm各种厚度的涂层,玻璃鳞片在衬里层中(平行部分)可构成屏障,防止药液和气体浸透。
通常,当衬得到的涂层具有优异的耐化学性能、良好的里层厚度为500~n时,约可含50层玻璃鳞机械性能、较高的电绝缘性能及较好的韧性。
片。
鳞片衬里比一般的有机物衬里优越,其根据腐蚀试验预测涂层的寿命,在完好滁敷优点如下。
的条件下,该涂料做油、气和水管道等的内(1)具有优良的耐腐蚀性涂层,寿命可达l5年;做污水和混注水管道因其含有化学稳定的玻璃鳞片(厚2~的内涂层,寿命可达5~7年。
3 m),可期望有部分鳞片平行配列,明显加施工方法采用管道工业中应用最多的静电热喷涂方法。
由于输送介质不同,对环氧粉末涂料的涂层厚度要求也不同。
国内油、气、水和污水等均含有一定的腐蚀介质,管道内防腐最好采用厚涂层。
用静电热碛涂的方法可以得到厚涂层,喷涂一长浸透途径,延长浸透时间,从而增加了防腐性能。
(2)耐热冲击性好鳞片衬里的热膨胀系数相对来说比较接近于钢材。
在环境温度范匿显示出比其他材料有更接近钢材的热应变,因此界面附近的应力可期望较小,不容易发生剥离(参见表1)。
(3)耐机械冲击由于整个衬里层被玻璃鳞片均匀地强化,故有很好的耐机械冲击性能;另外,衬里层硬化时收缩较小,硬化后不会出现残留应力引起的裂纹和剥离,也使机械性强度提高。
(4)施工速度快、工期短可用离心法或喷涂法施工,所以速度快,工期亦显著缩短,因操作人员的熟练程度而产生误差的影响较小,养护时间也较短。
(5)不含溶剂在含有溶剂的情况下,溶剂蒸发时容易在衬里层发生气孔。
雨鳞片衬里刚是无溶剂型的。
道,涂层厚度可达250~350/an,最大厚度可达500,~'n。
2苏联所使用的环氧/煤瓷漆涂层.苏联乌德穆尔特油田污水的特性,是高矿化度、高腐蚀性,含有硫化氢、氧和碳酸气,污水管道使用2~3年即发生事故,经济效益也低。
管道内防腐施工工法

管道内防腐施工工法引言:管道内防腐施工是一种重要的工程技术,用来保护管道内部免受腐蚀的影响。
腐蚀不仅会导致管道破损,还可能造成环境污染和安全事故。
因此,管道内防腐施工工法的选择和实施至关重要。
本文将介绍一些常用的管道内防腐施工工法,并深入探讨其特点和适用范围。
一、涂层法涂层法是一种常见的管道内防腐施工工法。
它通过在管道内部涂上一层防腐涂料来形成保护层,起到抵御腐蚀的作用。
涂层法的优点是施工简单,工期短,适用于各种类型的管道。
常见的防腐涂料有环氧涂料、聚氨酯涂料和丙烯酸涂料等。
涂层法的施工过程主要包括以下几个步骤:1. 表面处理:在施工前,需要对管道内部进行表面处理,确保表面干净平整,无油污和杂质。
常用的表面处理方法包括喷砂、喷丸和化学处理等。
2. 涂料施工:选择适当的防腐涂料后,按照产品说明进行涂料施工。
可以使用刷涂、喷涂或滚涂等方法进行施工,确保涂层均匀且无漏涂。
3. 固化及质检:施工完成后,需要等待涂料固化,通常需要一定的时间。
固化完成后,对涂层进行质量检测,确保其防腐性能符合要求。
二、注浆充填法注浆充填法是一种常用的管道内防腐施工工法,它通过将特定的材料充填到管道内部来形成防腐层。
注浆充填法的特点是施工方便快捷,适用于各种管道材料,可以达到连续、一致的防腐效果。
注浆充填法的施工过程主要包括以下几个步骤:1. 选择注浆材料:根据管道材料和环境要求,选择适当的注浆材料。
常见的注浆材料有硫酸铜、硅酸盐和沥青等。
2. 注浆施工:将选定的注浆材料通过特定设备注入管道内部,确保充填均匀。
注浆过程要注意控制注浆速度和压力,以防止管道变形或破裂。
3. 养护及验收:注浆完成后,需要进行一定时间的养护,以确保注浆材料充分固化。
养护期间需要对防腐层进行检测,确保其完整性和防腐性能。
三、电化学防护法电化学防护法是一种高效的管道内防腐施工工法,它通过在管道表面施加电场和电流,使得管道成为阴极,从而起到防止腐蚀的作用。
钢制管道熔结环氧粉末内防腐层技术标准

钢制管道熔结环氧粉末内防腐层技术标准
钢制管道熔结环氧粉末内防腐层技术标准包括以下内容:
1. 管道表面处理:管道表面应进行清洗、除锈和表面处理,确保表面干净、光洁并且没有油污、腐蚀和锈蚀物。
2. 熔结环氧粉末涂层施工:采用静电喷涂或电极泳涂等涂层工艺施工熔结环氧粉末内防腐层。
涂层厚度应符合相关标准要求。
3. 热固化:施工完熔结环氧粉末涂层后,应进行热固化处理,确保涂层牢固附着在管道表面上,并具有良好的耐腐蚀性能。
4. 检测和检验:对熔结环氧粉末内防腐层进行检测和检验,包括涂层厚度、附着力、耐腐蚀性能等方面的测试。
5. 表面处理和修补:在涂层施工过程中,如发现涂层破损或者有缺陷,应及时进行修补,确保涂层的完整性和防腐效果。
6. 环境保护:在施工过程中,应遵守环保要求,采取相应的防护措施,减少环境污染。
以上是钢制管道熔结环氧粉末内防腐层技术标准的一些基本内容,具体标准还需根据实际情况和相关规范来确定。
- 1、下载文档前请自行甄别文档内容的完整性,平台不提供额外的编辑、内容补充、找答案等附加服务。
- 2、"仅部分预览"的文档,不可在线预览部分如存在完整性等问题,可反馈申请退款(可完整预览的文档不适用该条件!)。
- 3、如文档侵犯您的权益,请联系客服反馈,我们会尽快为您处理(人工客服工作时间:9:00-18:30)。
文件编号:GD/FS-1644
(解决方案范本系列)
内涂层防腐技术详细版
A Specific Measure To Solve A Certain Problem, The Process Includes Determining The Problem Object And Influence Scope, Analyzing The Problem, Cost Planning, And Finally Implementing.
编辑:_________________
单位:_________________
日期:_________________
内涂层防腐技术详细版
提示语:本解决方案文件适合使用于对某一问题,或行业提出的一个解决问题的具体措施,过程包含确定问题对象和影响范围,分析问题,提出解决问题的办法和建议,成本规划和可行性分析,最后执行。
,文档所展示内容即为所得,可在下载完成后直接进行编辑。
采用涂、镀、注、渗、化学转化、热流强化、形变强化等措施,改变材料表面的化学成分、组织结构、力学状态等理化和机械性能,使材料表面获得一层保护性的覆盖层或强化层,可以避免金属基体与介质的直接接触,有的覆盖层还具有电化学保护作用或缓蚀作用。
这类方法经济有效,是目前用得最为广泛的防腐蚀措施。
(1) 材料的选择
目前国外普遍采用防腐蚀的内涂层,大都是环氧型、改进环氧型、环氧酚醛型或尼龙等系列的涂层。
这些涂料是一种在苛刻的腐蚀条件下防腐性能优异、使用寿命长的特种涂料。
在腐蚀介质中具有良好的化
学稳定性,附着力强,柔韧性好,抗失压起泡,机械性能(耐磨性、抗冲击性)好等优点,从而使金属减缓腐蚀,延长使用寿命。
针对一种防腐涂料它只能在某种环境中才能发挥其作用,不可能满足各种环境的不同要求,这就需要根据实际情况,采取“多层异类”结构的涂层工艺。
一般工程施工中,主要采用“底漆+中间层+面漆”的结构形式,以期达到比较满意的防腐效果。
据有关资料介绍,在潮湿的环境下采用“无机富锌底漆+环氧中间层+环氧面漆”工艺的防腐涂层使用寿命可达15年。
但因环氧耐气候性较差,在实际使用中可采用“无机富锌底漆+环氧中间层+聚氨脂面漆”这种组合。
(2) 内涂敷的主要工艺步骤
目前国内外常用的内涂敷工艺流程为:管道预热→表面处理→除尘→端部胶带保护→无空气喷涂→加
速固化→检验→堆放(储存待运)。
其质量控制的关键为:涂料的选择、表面处理、无气喷涂、干膜厚度和涂膜固化。
①钢管内表面的预处理。
一个涂层的好坏,取决于它是否能够长期牢固的附着于金属表面并充分发挥对金属的保护作用。
涂层与金属表面间能否保持良好的附着力,往往取决于涂料底漆的性能、金属表面状态和表面处理质量等。
而管道表面处理质量是影响涂层寿命的最直接因素之一。
根据近年来工程统计资料表明,在影响涂层寿命的诸因素中,表面处理质量的影响占55%。
选择适当的表面处理方式与合理选择涂层工艺同样重要。
目前现场常用的钢管内壁预处理方法有化学清洗法、物理清洗法等。
②钢管的内涂敷。
除合理的涂层工艺和好的表面预处理质量外,严格的涂层工艺过程也是确保涂层
质量的措施之一。
在涂敷过程中,自然因素和人为因素都将给涂层质量带来影响。
施工前,应检查涂料的保质期和其他使用要求,并按使用说明调整配比,切忌单纯为施工方便而过多地加入溶剂;室外施工时气温过低,不利于涂膜流平和固化;气温过高会使涂料中溶剂挥发过快,造成针孔等缺陷从而影响涂层的致密性,造成局部破坏而影响寿命;风沙大、灰尘多、雨雪天气应停止作业,否则涂层质量难以保证。
环氧涂料的环境温度要求大于10℃,相对湿度小于85%。
挤压涂敷法是管道现场处理的一种方法,即管道内表面处理后,泵入两涂敷器之间的涂料,以一定的挤压力涂在管壁上。
这种方法不需要预制车间,减少了中间环节并避免了补口,但施工工艺复杂,质量难以控制,因而只适合于小口径短距离管道的施工。
喷涂一般是在钢管厂进行,主要涂敷新制钢管,质量易控制、周期短。
其喷涂方法主要有空气喷涂、高压无空气喷涂、静电粉末喷涂、高温离子喷涂等。
目前,国外已基本淘汰了空气喷涂装置,取而代之的高压无空气喷涂占80%以上。
高压无空气喷涂与空气喷涂相比,喷涂后的漆膜质量好、涂层均匀、不带针眼气孔,能够减少对大气的污染。
对于大口径输气管道内壁液体环氧涂料的喷涂,主要采用高压无空气型压送涂料的方式。
对于环氧粉末涂料,国外普遍采用的方法是静电喷涂法,这种方法的涂料利用率为80%~95%。
美国标准API-5L2《腐蚀性气体输送管道内涂层推荐准则》和英国天然气工程企业标准GBE/CMl都规定应(最好)采用无气喷涂设备进行内涂敷作业。
综上所述,合理选择涂层工艺,严格处理被涂物
表面和执行正确的操作程序,才能确保工程的防腐质量,更有效地发挥防腐涂料对金属钢管的防腐作用。
③内涂层的质量检验。
目前,许多国家和企业都制定了自己的管道内涂层标准,如美国石油学会(API)制定的API-RP5L2(非腐蚀性气体输送管道内涂层推荐准则》;英国气体理事会(Gas Council)制定的GIS/CM1-1968和GICP/CNI标准;荷兰制定的CS-1-N标准;法国制定的R03和20S50标准;以及加拿大阿尔伯达管道公司制定的C-1标准等。
我国石油工程建设施工专业标准化委员会制定了SY/T 0442—97《钢质管道熔结环氧粉末内涂层技术标准》和SY/T 4057—93《液体环氧涂料内防腐涂层钢管技术条件》两个行业标准。
我国对于国产液体双组分环氧涂料进行涂敷的管道,其检验内涂层的质量标准可以参照SY/T 4057—93的有关规定。
对于进
口涂料内涂的管道一般主要采用英国天然气工程企业标准GBE/CM1及GBE/CM2。
根据美国API-RP《非腐蚀性气体输送管道内涂层推荐准则》推荐,钢质管道内涂层的涂层厚度为(50.8±5.08)μm,我国SY/T 0442—97标准中规定减阻型内涂层厚度为50μm,这个厚度既能达到减阻目的,也有比较经济的涂层厚度余量。
经检验不合格的钢管应按标准中所规定的条款进行修补和复涂,复涂后的钢管经质量检查不合格不得再涂敷,只能另行使用。
④现场工艺条件的控制。
管道涂敷施工现场,应对管口进行封闭,以免泥水进入管内。
做好现场整平工作,严格按操作规程拉运预制好的内防腐钢管,以免损坏钢管防腐涂层。
管道组装焊接前,应先用清洁的棉纱或棉布清除管端内、外壁及坡口处,涂有富
锌体系底漆的部位不得有泥土、灰尘、水分及其他杂物,且不得受到破坏。
管道组装焊接时,严禁水、泥土、油等其他杂物进入管内。
管段组装焊接后,两端应进行封闭。
管道组装焊接每段长度以0.5km为宜,但最长不得大于1.5km(直管段)。
其相邻两焊口(即内补口位置)距离不得少于2.9m。
管道必须在内防腐补口作业完成和补口涂料固化后,经检测合格方可下沟回填和试压。
内防腐管道现场施工除按施工程序和有关标准精心施工外,还应满足SL-1型钢质管道内涂层补口机和SL-1型钢质管道内涂层检测补涂机进行补口和检测补涂作业施工工艺条件。
每段管道焊接后,应进行通球清障、气密性试压、超声波探伤或x射线检验。
在下沟前进行补口施工时,应根据设计要求确定涂敷的厚度及时间间隔。
在此间隔内应对管口进行封闭,
待内补口漆膜涂层干燥后,方可用检测补涂机进行补口质量的检测及补涂。
⑤管道内、外涂层的联合施工工艺。
由于长输天然气管道在实际施工中还涉及到一个外防腐问题,因此在工厂预制过程中,应充分考虑内、外涂层的涂敷工艺配合问题,以便使管体内、外涂层的施工进度尽量能同步进行,这样即可以节省投资又可以加快施工进度。
对于外防腐采用熔结环氧粉末(FBE)或三层PE、内涂层采用液体环氧涂料(减阻型)的结构而言,采用“先内后外”工艺或“先外后内”工艺在技术上都是可行的。
几家国外大涂敷设备制造厂采用“先内后外”工艺的要多一些,例如英国BG就有至少几千公里天然气管道是采用“先内后外”工艺进行涂敷的,至今运行良好。
但在技术上究竟采用“先内后外”还
专业实施方案/ Professional implementation plan 文件编码:GD/FS-1644是“先外后内”,仍然存在着一定分歧。
“先内后外”工艺,内涂要有一个固化时间,内涂作业线紧接外涂生产线,需两次搬运钢管,外涂要经过淋水冷却,这将会对已完工的内涂造成针孔处的锈蚀。
当外涂进行喷砂处理时,高速钢砂有可能进入内表面造成内涂膜的损坏,为避免这一后果,要在钢管两端加装堵头,这对于大口径管子来讲不合适。
另外,“先内后外”对内涂料还有一个短时耐高温的要求。
“先外后内”工艺要求则相对简单的多,只须在管道传送装置上采取保护措施就行了,内涂的所有工序均不会对外涂造成损害。
从外涂线上进入内涂作业线的钢管带有一定的温度,可省去内涂预热的工序,这样可节省设备投资并减少工时。
可在这里输入个人/品牌名/地点
Personal / Brand Name / Location Can Be Entered Here
-第11页-。