数控机床误差过大故障的分析与处理.
数控机床跟踪误差大故障分析与排除

F 耋
Pr
图 2 指 令 与 实际 速度 曲 线对 比 图 4 跟踪误差大故 障成 因分析 数控机床 中跟踪误差大是一个较为复杂的问题 , 其故障原因多种多 样, 看似毫无规律可循。 但从 跟踪误差大报警机理出发, 可以知道跟踪误 差 大报警 条件可 以简单描 述为 :控制 指令值 一实 际反馈值 l I >允许 误 差, 确定排除此类 故障的三条主线 : 指令值过 大 、 实际反馈值过小或允许 误差过小。 1是 否为允许误差过/ ) b?
科技 论坛
2 1 年第 1 期 01 2
民 科技 营
数控机床跟踪误差 大故障分析 与排除
张 勇 吕家 将 z
(、 1 九江职业技术 学院继续教 育部 , 江西 九江 32 0 2 九江职业技 术学院机械工程学院, 300 、 江西 九江 3 20 ) 3 0 7
摘 要: 现从跟踪误差概念入手 , 深入 浅出地 阐述 了跟踪误差产生机理 , 并据此进行跟踪误差 大故 障成 因分析 , 最后 用“ 排故五 步法” 示范跟 踪 误 差大故障排除过程 。 关键词 : 跟踪误 差; 位置环 ; 故障诊 断; 步法 五 数控机床加工 时 , 经常会出现跟踪误差过 大的报警 , 探究其故 障机 所 以, 我们需要人 为的确定一个极 限值作 为最大跟踪误差 , 超过此 极限 理 ,找到快速有效 的排除此故障的方法与思路就 是本 文所要讨论 的内 值 , 机床就报警 , 避免产 品的成批报废 , 最大跟踪 误差 的设定 与加工 零件 容。 的位置与形状 的精度有密切关系。
1 什 么是 跟 踪 误 差 ?
为了保பைடு நூலகம்加工精度 , 目前的数控机床一般采取 了三环结构的伺服系 统, 系统实际位移值被反馈 到数控 装置或伺服驱动 中, 直接 与输 入的指 令位移值进行 比较 , 用误差进行 控制 , 最终实现移动部件 的精 确运动和 定位。所谓跟随误差 , 是指伺服系统发 出的指令位置与系统输出的实际 位置之 间的动态误差 , 其大小反映 的是当前采样周期 , C指令位置值与 N 坐标轴实 际运行值之间的差值 。 到底 , 说 跟踪误差与位置有关 , 了 究 为 研 跟踪误差 , 就少不得理解位置环 的工作原理。 位置环 的结构简图如图 1 所示 , 其核心为位置偏差计数器。P 来 自 z 于N 。 C 这是 N C根据输入数据经过插补计算及刀补计算 , 速度的均化等 处理 , 向各轴发出的脉 冲, 个数代表距 离 , 频率代表速度 , 于位 置偏差 对 计算器而言, 是加计数。 f 自于脉 冲编码器的反馈脉冲, P来 个数代表工作 台运行 的实际距离 , 频率代表电机旋转速度。 它通过同步, 四分频等控制 和转换 后送到偏差计算器中去 , 是减计数。 在每个采样周期 内, 置偏差 计数器得到一个数 , 位 这个数就 是跟踪 误差 , 表示 N C要求这个轴运行的距 离还有 多少 没有走 出去 。数 大表 明 实际运行距离与 N C要求 运行 距离差得远 , 望坐标轴 走快 点 , 以这 希 所 个数经过 DA转换 , / 转换为模拟量去控制 电机速度。数小 表明 目前距离 目 标近 , 就要慢慢接近 目 , 标 最后准确停车。
数控机床跟踪误差过大的故障诊断

任务2 跟踪误差过大的故障诊断【任务目标】1、掌握伺服进给系统的位置控制原理;2、掌握跟踪误差过大的原因;3、掌握跟踪误差过大故障的诊断思路;4、能够排除跟踪误差过大的故障。
【任务描述】有一台YL559数控车床,配备FANUC 0i TD数控系统,采用半闭环控制,在手动移动X 轴的时候,出现“SV0411 (X)移动时误差太大”报警,故障现象见图6-2-1。
本次任务的工作是找出故障原因并能排除故障。
图6-2-1 故障现象【资讯计划】一、资料准备要完成本任务中的故障诊断及排除工作,需要配备以下资料:1、FANUC 0i D数控系统硬件连接说明书;2、FANUC 0i D数控系统维修说明书;3、YL559数控机床电气原理图;4、FANUC PMC梯形图语言说明书;5、故障记录单。
二、工具、材料准备要完成本任务中的故障诊断及排除工作,需要配备以下工具和材料,具体见表6-2-1。
表6-2-1 工具和材料清单三、知识准备伺服进给系统的任务是尽可能使系统的输出准确地跟踪给定输入,位置控制的实质是位置的随动控制。
位置控制包含两部分:位置比较和速度控制指令的实现,如图6-2-2所示。
图6-2-2 位置控制原理1、位置控制原理下面以脉冲比较法实现位置的比较为例,说明伺服系统位置控制的原理。
脉冲比较法是将CNC 插补输出脉冲P C 与位置检测装置输出脉冲P f 相比较,得到脉冲偏差信号P e ,如图6-2-3所示。
12323432323232321212121指令信号Pc 反馈信号Pf 误差量图6-2-3 脉冲比较示意图当数控系统控制工作台向一个方向(比如X 轴)进给时,经插补运算得到一系列脉冲作为指令脉冲,该脉冲的数量代表了工作台的移动量,脉冲的频率代表了工作台的进给速度,方向代表了工作台的进给方向。
以增量型光电编码器为例,当光电编码器与伺服电动机和滚珠丝杠直连时,随着伺服电动机的转动,产生序列脉冲输出,脉冲的频率将随着转速的快慢而升降。
数控机床孔加工的常见问题与解决方式

数控机床孔加工的常见问题与解决方式数控机床是一种高精度、高效率的机械加工设备,广泛应用于各个制造行业。
在数控机床的孔加工过程中,常常会遇到一些问题,如孔径误差过大、孔底质量差等。
本文将针对数控机床孔加工的常见问题进行分析,并提供相应的解决方式。
首先,孔径误差过大是孔加工中常见的问题之一。
造成孔径误差过大的原因有很多,如机床热变形、刀具磨损等。
解决这个问题的方法是进行机床的温度补偿,通过监测机床温度的变化来控制机床的加工过程,以保证孔径的精度。
其次,孔底质量差也是常见的问题之一。
孔底质量差主要是由于切削过程中产生的毛刺和残留物导致的。
解决这个问题的方法是合理选择切削参数,并使用合适的润滑剂来降低摩擦力,减少残留物的产生。
此外,还可以采用后处理的方式进行除毛刺,如采用锉刀或砂纸进行修整。
此外,孔壁粗糙度高也是数控机床孔加工中常见的问题之一。
孔壁粗糙度高主要是由于切削刀具损耗和润滑不良导致的。
解决这个问题的方法是定期更换切削刀具,保证切削刀具的锋利度;同时,加强切削润滑,使用合适的润滑剂来降低摩擦力,以提高加工效果。
另外,孔位误差是孔加工中常见的问题之一。
孔位误差主要是由于机床定位不准确或刀具位置不稳定导致的。
解决这个问题的方法是定期检查和校准机床定位装置,确保机床的精度;同时,采用稳定的刀具固定方式,如采用刀具夹紧器固定刀具等,以保证刀具位置的稳定性。
此外,孔加工过程中还可能遇到其他一些问题,如微抖动、断屑等。
微抖动主要是由于机床刚性不足导致的,解决方法是增加机床的刚性,例如加装稳定支撑或调整刀具切入角度。
断屑主要是由于切削刀具切削力过大或润滑不良导致的,解决方法包括降低切削刀具的切削力、增加润滑剂的使用量等。
综上所述,数控机床孔加工中常见的问题包括孔径误差过大、孔底质量差、孔壁粗糙度高、孔位误差等。
针对这些问题,我们可以采取相应的解决方式,如温度补偿、合理选择切削参数、定期更换切削刀具、加强切削润滑、检查和校准机床定位装置等。
数控车床常见故障及解决对策

数控车床常见故障及解决对策近年来,随着数控技术的迅猛发展,数控车床在工件加工中表现出来的优点越来越多,如加工质量稳定、生产率高、适应性好等,因此许多的工厂企业都将数控车床作为重要的机械加工设备;大部分的技工院校也都面向社会需求,把数控车床的教学作为一项常规的教学任务,而非见习性教学任务。
数控车床在使用过程中不可避免地会发生一些故障,笔者结合自己在实习教学工作中遇到的一些实际问题作以下几点分析。
一、出现“数据位数过多”的报警信息数控车床在多次进行图形模拟、验证确保程序基本正确后再对刀,准备进行工件加工时,却发现总是提示“数据位数过多”的报警信息。
这一现象比较多地发生在数控车床的检测反馈元件采用的是增量式编码器机床上,其原因在于:在图形显示空运行程序时,都是在机床锁定的状态下,此时机床面板上显示的坐标位置是按照程序当中的设定进行变化,但是实际上机床位置不动。
这样程序运行结束后,面板上所显示的坐标位置和运行前就存在一定的偏差,如此所述情况,在进行了多次的图形显示(机床锁定空运行)后,机床面板上显示的坐标值就会对所有的偏差进行累加,最终导致坐标值超出机床的行程范围。
这样在对刀时(目的是设定工件坐标系在机床坐标系下的相对位置),机床的运算就会出现问题,从而产生报警。
此时,复位、机床回零并不能解决问题,必须对系统断电,然后重新开机,报警才能解除,机床才能够正常使用。
二、“急停报警”或“变频器报警”数控车床在发生撞车事件时,都会下意识地拍下急停,可是松开急停后,会出现“急停报警”或“变频器报警”。
这一现象一般发生在采用变频器进行无级调速的数控机床上,其原因在于,由于撞车,对电动机的输出功率(扭矩)产生很大需求,可是电动机的输出功率又是有一定的极限的,当超出此极限后,电机产生过载现象,为了防止事故的进一步扩大,系统都有过载保护措施。
机床就处于这种状态时,需要断电,重新开机,让数控系统重新初始化一下,就可以正常使用。
数控机床伺服系统常见故障的诊断及其处理

数控机床伺服系统常见故障的诊断及其处理数控机床伺服系统是机床的重要组成部分,其故障会严重影响机床的生产效率和质量。
本文将对数控机床伺服系统常见故障进行分析,提供相应的诊断和处理方法,帮助机床维修工程师进行有效的故障排查。
一、伺服电机输出不稳定或不工作的故障1. 伺服电机电气连接故障。
在伺服电机输出不稳定或不工作的情况下,首先要检查电气连接是否良好,包括伺服电机与伺服主轴电机之间的电气连接是否正常、伺服驱动器电气与伺服电机之间的连接是否正确、接地是否合格等,排除电气连接问题。
2. 伺服电机本身故障。
伺服电机的故障如轴承磨损、线圈断路、电机转子故障等都会导致输出不稳定或不工作的情况,需要进行检测和维修。
常见的检测方法如用万用表测量电机的电阻,检查电机转动是否灵活、轴承是否正常等。
3. 伺服驱动器故障。
伺服驱动器的故障如防护电路故障、电源故障、接口板连接不良等都会导致伺服电机输出不稳定或不工作,需要检查相应的部件进行排查。
常见的检测方法如检查驱动器是否有报警信号、电源是否正常、接口板是否正确插接等。
二、伺服系统位置偏移或误差过大的故障1. 导轨故障。
导轨质量差、磨损严重或进刀太大等都会导致伺服系统位置偏移或误差过大,需要检查导轨表面是否有磨损痕迹以及导向面是否平整。
2. 动态中的机械振动、系统震动或机床本身质量不好。
这些因素在机床运行中都会产生影响,导致伺服系统位置偏移或误差过大,需要进行检查和调整。
调整方法可采用优化机床支撑结构、调整伺服参数等。
3. 伺服系统参数设置错误。
如伺服系统的比例系数、积分系数和微分系数未能正确设置,将导致位置偏移或误差过大。
此时需要检查和调整伺服系统的参数设置。
三、伺服系统温度过高或过低的故障伺服系统的温度过高或过低都会导致数控机床性能下降,进而影响机床的精度和稳定性。
常见的故障原因包括:1. 冷却系统故障。
如冷却水温度过高或过低、冷却系统中水泵或水管路堵塞、扇叶损坏等都会导致伺服系统温度异常。
数控机床误差过大故障的分析与处理(精)

措施 延长加/减速时间设定 减小位置环增益或提高机 床的刚性 若正确,见第2项,否则 第3项 调整机床机械传动系统
提高位置环、速度环增益
若正确,见第2项,否则 第3项 调整机床机械传动系统
更换不良板 更换不良位置检测期间 (编码器、光栅) 维修、更换不良板 若轴向变形,则见第2项, 若45°方向上成椭圆,则 见第3项 调整机床,进行定位精度、 反向间隙的补偿 调整位置环增益以消除各 轴间的增益差
排除措施 依照参数说明书, 正确设置个参数
数控机床误差过大故障分析与处理
一加工误差过大故障的分析与处理
项目 超调 1
2
单脉 1 冲精 度差 2
3
定位 1 精 不良 2
3 4
5 圆弧 1 插补 加工 的圆 2 度差
3
4 5
6
故障原因 加/减速时间设定过小 与机床的连接部分刚性差或连接不牢固
需要根据不同情况进行故障分析
检测位置检测器件(编码器、光 栅)
测量不圆度,检查周向上是否变 形,45°方向上是否成椭圆
机床反向间隙大、定位精度差
测量各轴的定位精度与反向间隙
位置环增益设定不当
各插补轴的检测增益设定不良 感应同步器或旋转变压器的接口板调整不 良 丝杠间隙或传动系统间隙
调整控制单元,使同样的进给速 度下各插补轴的位置跟随误差的 差值在±1%以内 在项目3调整后,在45°上成椭圆 检查接口板的调整
一 数控机床振荡故障分析与处理 案例分析
分析及处理过程:进一步观察、测量机床Y 轴移动情况, 发现该机床 Y 轴伺服在移动到某一固定角度时,都有一冲 击过程:在无冲击的区域,测量实际移动距离与指令值相符, 根据以上现象,初步判定,故障原因与位置检测系统有关。
数控机床加工误差原因及对策分析

数控机床加工误差原因及对策分析数控车床为零件加工的主要方式,对于零件加工具有较高的自动化水平,但是就实际情况来看,零件加工经常会因为设备自身或者操作不当等因素限制,而造成工件精度达不到专业要求,存在一定误差。
零件加工精度最终由机床刀具与零件间相对位移误差决定,因此需要确定加工误差存在的原因,以降低误差为面对,采取措施进行优化。
本文选择经济性数控机床为对象,就其加工误差与优化对策进行了简要分析。
标签:数控机床;加工误差;补偿0 引言数控机床零件加工经常会因为各项因素的影响而出现误差,即加工后零件实际几何参数与设计几何参数间存在一定偏差,导致零件精确度不能满足设计要求,最终只能作为不合格或者废品处理。
以提高数控机床加工精确度为的目的,需要对各类加工误差原因进行分析,有针对性的采取措施进行处理,对存在的误差进行有效补偿。
1 数控机床加工误差分析经济性数控车床对零件的加工,应用为步进电机开环伺服系统或者半闭环伺服系统来驱动刀具,在这个过程中就会因为受各项因素的影响而存在加工误差。
一方面,数控机床自身因素。
主要是因为数控机床所用构件精确度较低,以及机床装配过程中存在误差,导致零件加工后精确度达不到设计要求。
针对此种误差原因,一般可以就高精度零部件进行更换,以及在装配环节做好控制,争取提高机床自身精确度。
另外,对于部分技术能力可以达到要求的企业,还可以选择对步进电机构成的开环伺服系统进行适当的改造,使其成为闭环伺服系统,来提高零件加工精度[1]。
另一方面,工艺操作因素。
部分零件在加工过程中,会因为机床以及零件本身的热变形,造成切削、振动、装夹、磨损等细节存在误差。
想要对此类误差进行补偿,需要建立补偿模型在CNC系统内补偿,实施难度比较大,对提高数控机床零件加工精确度需要重点研究。
2 数控机床加工误差原因与对策分析2.1 数控机床自身原因2.1.1 控制系统误差(1)开环控制系统。
开环控制系统并未设置反馈装置,数控信号为单向流程,并不能对移动部件实际位移量进行测量与反馈,进而会影响对加工过程中所存误差的调整。
数控机床的加工精度误差分析与校正方法
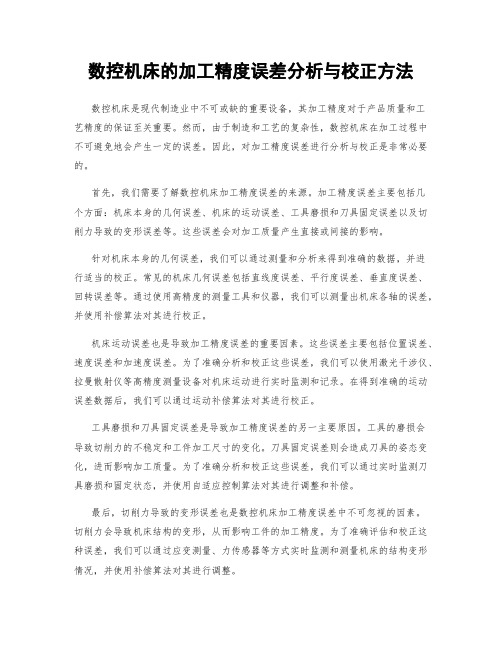
数控机床的加工精度误差分析与校正方法数控机床是现代制造业中不可或缺的重要设备,其加工精度对于产品质量和工艺精度的保证至关重要。
然而,由于制造和工艺的复杂性,数控机床在加工过程中不可避免地会产生一定的误差。
因此,对加工精度误差进行分析与校正是非常必要的。
首先,我们需要了解数控机床加工精度误差的来源。
加工精度误差主要包括几个方面:机床本身的几何误差、机床的运动误差、工具磨损和刀具固定误差以及切削力导致的变形误差等。
这些误差会对加工质量产生直接或间接的影响。
针对机床本身的几何误差,我们可以通过测量和分析来得到准确的数据,并进行适当的校正。
常见的机床几何误差包括直线度误差、平行度误差、垂直度误差、回转误差等。
通过使用高精度的测量工具和仪器,我们可以测量出机床各轴的误差,并使用补偿算法对其进行校正。
机床运动误差也是导致加工精度误差的重要因素。
这些误差主要包括位置误差、速度误差和加速度误差。
为了准确分析和校正这些误差,我们可以使用激光干涉仪、拉曼散射仪等高精度测量设备对机床运动进行实时监测和记录。
在得到准确的运动误差数据后,我们可以通过运动补偿算法对其进行校正。
工具磨损和刀具固定误差是导致加工精度误差的另一主要原因。
工具的磨损会导致切削力的不稳定和工件加工尺寸的变化。
刀具固定误差则会造成刀具的姿态变化,进而影响加工质量。
为了准确分析和校正这些误差,我们可以通过实时监测刀具磨损和固定状态,并使用自适应控制算法对其进行调整和补偿。
最后,切削力导致的变形误差也是数控机床加工精度误差中不可忽视的因素。
切削力会导致机床结构的变形,从而影响工件的加工精度。
为了准确评估和校正这种误差,我们可以通过应变测量、力传感器等方式实时监测和测量机床的结构变形情况,并使用补偿算法对其进行调整。
总结来说,数控机床的加工精度误差分析与校正是确保产品质量和工艺精度的关键步骤。
在这个过程中,我们需要准确地识别和分析加工精度误差的来源,并采取相应的校正措施。
数控机床加工误差分析及改善方案

数控机床加工误差分析及改善方案数控机床加工误差分析及改善方案随着制造业的发展,数控机床在工业生产中扮演着重要的角色。
然而,由于各种因素的影响,数控机床在加工过程中常常会出现误差,影响产品的精度和质量。
因此,对于数控机床加工误差的分析和改善变得至关重要。
下面将介绍一种逐步思考的方法,帮助我们分析加工误差,并提出改善方案。
第一步:收集数据首先,我们需要收集加工误差的相关数据。
这些数据可以包括加工零件的尺寸测量结果、加工过程中的工艺参数、机床的精度参数等。
通过收集这些数据,我们可以了解到加工误差的具体情况,并为后续的分析提供依据。
第二步:分析误差来源在收集到数据之后,我们需要对误差的来源进行分析。
数控机床加工误差通常可以分为几个主要来源,如机床本身的刚度、工具刀具的磨损、加工时的热变形等。
通过对这些来源的分析,我们可以确定造成加工误差的主要因素。
第三步:确定改善方向在了解了误差来源之后,我们需要确定改善的方向。
根据误差来源的不同,我们可以采取不同的改善措施。
例如,如果误差主要来自机床的刚度不足,我们可以考虑加强机床的刚性结构,提高其稳定性;如果误差来自于工具刀具的磨损,我们可以采取定期更换刀具的措施,保证其切削效果。
第四步:实施改善措施在确定了改善方向之后,我们需要实施相应的改善措施。
这些措施可以包括机床结构的调整、刀具更换的计划、加工过程中的温度控制等。
通过实施这些措施,我们可以有效地降低加工误差,提高产品的加工精度和质量。
第五步:监控和评估效果最后,我们需要监控和评估改善措施的效果。
通过对改善后的加工数据进行分析,我们可以了解到改善措施的实际效果。
如果误差得到了有效的降低,我们可以继续保持改善措施;如果效果不理想,我们可以重新评估误差来源,并调整改善方案。
综上所述,数控机床加工误差的分析和改善是一个逐步思考的过程。
通过收集数据、分析误差来源、确定改善方向、实施改善措施以及监控和评估效果,我们可以有效地降低加工误差,提高产品的加工精度和质量。
数控机床的故障分析及处理

数控机床的故障分析及处理关键词:伺服系统的故障;外部故障;维修中图分类号:g718文献标识码:b文章编号:1672-1578(2013)09-0197-01目前,数控机床的应用越来越广泛,其加工柔性好,精度高,生产效率高,具有很多的优点。
但由于技术越来越先进、复杂,对维修人员的素质要求很高,要求他们具有较深的专业知识和丰富的维修经验,在数控机床出现故障才能及时排除。
我们学校有十几台数控设备,数控系统有多种类型,几年来这些设备出现一些故障,通过对这些故障的分析和处理,我们取得了一定的经验。
下面结合一些典型的实例,对数控机床的故障进行系统分析,以供参考。
1.简述数控机床常见的故障所谓数控机床故障,就是数控机床全部或者部分丧失了规定的功能,导致数控机床无法正常运行。
下文主要介绍三种数控机床常见的故障,即数控机床的结构性故障、数控机床的动作性故障和数控机床的功能性故障。
1.1数控机床的结构性故障。
数控机床的结构性故障主要是指主轴电动机运行噪声大、发热量大、切削时产生振动、速度不稳定等,针对此类故障,应根据其与主轴的安装、档位、润滑、轴承和动平衡的关系,在找出具体故障点的同时做出相应的排除故障的处理。
数控机床的结构性故障的表现是,其主轴转动的速度随着一个加工中心的主轴启动而转动,当转动的速度达到指令速度时,停车也随之停下来。
1.2数控机床的动作性故障。
数控机床的动作性障碍是指机床的各执行部件出现的动作障碍,出现此类障碍时,常伴有报警提示,常见的数控机床动作性障碍有刀库或刀盘不能定位或者不能被松开,刀具松不开或夹不紧,旋转工作台不转等等,因此,在处理数控机床的动作性故障时,利用动作性故障发生时的报警提示,按照数控机床维修的一般规律对数控机床进行故障处理,是排除数控机床动作性故障的有效途径。
1.3数控机床的功能性故障。
数控机床的功能性故障主要表现为运动方向误差大、加工精度差、机床没有任何报警显示等,因此,面对数控机床的功能性故障,在处理数控机床功能性故障时,从运动误差的特点出发,结合运动误差产生大小的程度和不合格零件的特征,有针对性地进行检查,便于快速找出导致故障的原因,此类故障常见的现象是,在对某一工件进行检查时,发现轴方向的实际尺寸跟程序编辑的实际尺寸存在偏差。
数控系统跟踪误差过大报警现象及实例分析

(1)机械故障 机械传动系统是数控机床进 行正常加工工作的首要条件,机械部分出现了故 障,后续的控制将“无从谈起”。机械故障主要发 生在进给传动系统中,进给传动系统的主要任务是 完成各坐标轴的定位与切削进给,其传动精度、灵 敏度和稳定性直接影响被加工工件的最后轮廓精度 和加工精度,为此,对数控机床进给传动系统的要 求是:低惯量、低摩擦力、高刚度、高谐振和无传 动间隙等。
1. 相关概念 跟踪误差指的是数控机床在移动过程中的误 差,即在移动过程中,理论移动量和实际移动量的 差值(这里是和位移量“相当”的一个量值,大 多数情况下是一个电量,因为此时经过了反馈环 节),是动态的概念范畴,即E(S)=R(S)-B(S)。 这 里 , 还 要 特 别 提 及 另 外 一 个 概 念 —— 定 位 误差。定位误差指的是数控机床移动停止后产生 的误差,即位移结束后,理论位移量和实际位移 量的差值,是静态概念范畴,即E′(S)= C(S)理论- C(S)实际。 一般通用闭环控制系统结构如图1所示,其中 R(S)为输入信号,C(S)为输出信号,E(S)为输入端 定义的误差信号,G(S)为前向通道传递函数,H(S) 为反馈通道传递函数,B(S)为反馈信号。
图1 通用闭环控制系统结构 而对于全闭环数控机床,其控制系统框图如图 2所示。 参照图1、图2并进行比对,我们不难发现数学
模型中的各个环节在实际机床内包含的部件和机 构。
图2 全闭环控制数控机床控制结构框图
2. 故障理论根源 跟踪误差过大报警产生的原因是机床在运行过 程中,实际坐标位置与反馈坐标位置不相符,且其 值超过系统规定的允许值,此时,系统便会产生 “跟踪误差过大”报警,即E(S)=R(S)-B(S)≥给 定规定值。图3为数控机床加工过程结构示意图, 从系统的控制回路看,凡是和跟踪误差数学关系表 达式相关的量都有可能成为造成此类报警的原因。 详细来说有以下几个环节:
数控机床的故障分析及消除措施
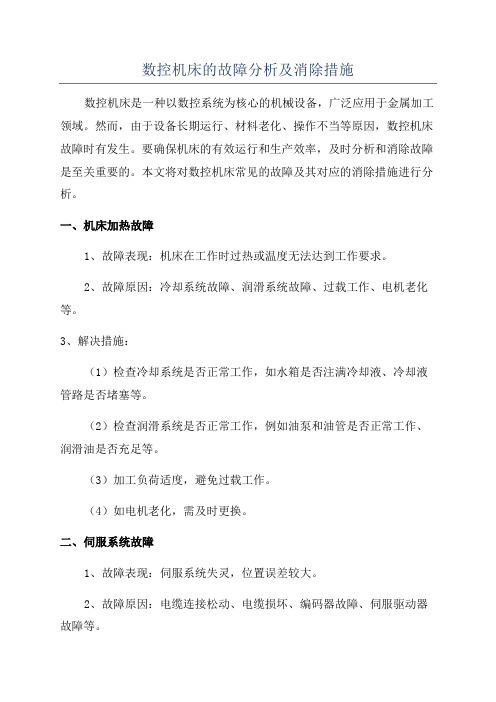
数控机床的故障分析及消除措施数控机床是一种以数控系统为核心的机械设备,广泛应用于金属加工领域。
然而,由于设备长期运行、材料老化、操作不当等原因,数控机床故障时有发生。
要确保机床的有效运行和生产效率,及时分析和消除故障是至关重要的。
本文将对数控机床常见的故障及其对应的消除措施进行分析。
一、机床加热故障1、故障表现:机床在工作时过热或温度无法达到工作要求。
2、故障原因:冷却系统故障、润滑系统故障、过载工作、电机老化等。
3、解决措施:(1)检查冷却系统是否正常工作,如水箱是否注满冷却液、冷却液管路是否堵塞等。
(2)检查润滑系统是否正常工作,例如油泵和油管是否正常工作、润滑油是否充足等。
(3)加工负荷适度,避免过载工作。
(4)如电机老化,需及时更换。
二、伺服系统故障1、故障表现:伺服系统失灵,位置误差较大。
2、故障原因:电缆连接松动、电缆损坏、编码器故障、伺服驱动器故障等。
3、解决措施:(1)检查电缆连接是否松动或损坏,如有问题,修复或更换电缆。
(2)检查编码器是否正常工作,例如检查其供电电压是否稳定、信号是否正常等。
(3)检查伺服驱动器是否正常工作,例如检查其供电电压是否稳定、参数设置是否正确等。
三、系统软件故障1、故障表现:机床不能正常启动、程序运行错误等。
2、故障原因:系统软件错误、病毒感染等。
3、解决措施:(1)检查系统软件是否正常运行,如有问题,及时更新或修复软件。
(2)定期对系统进行杀毒,确保系统安全运行。
四、进给系统故障1、故障表现:进给系统工作不稳定、进给速度异常等。
2、故障原因:进给伺服电机故障、滚珠丝杆松动、过载等。
3、解决措施:(1)检查进给伺服电机是否正常工作,例如检查电机供电电压是否稳定、转子是否正常转动等。
(2)检查滚珠丝杆是否松动,如有问题,需及时进行紧固。
(3)避免过载工作,适度调整进给速度。
五、机床报警故障1、故障表现:机床出现报警信息,无法正常工作。
2、故障原因:各个传感器故障、机床配件老化等。
数控机床误差过大故障的分析与处理(“故障”相关文档)共6张
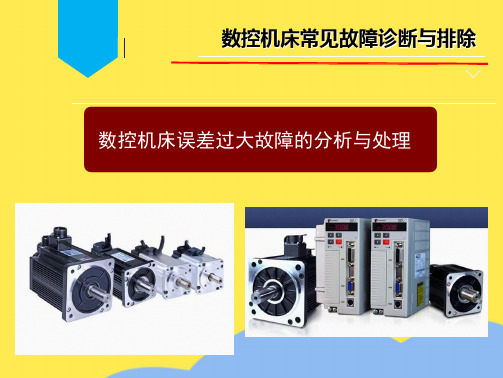
分析及处理过程:进一步观察、测量机床Y 轴移动情况,发现 故障现象:一台配套 DYNAPATH 20M 系统的二手数控铣床,加工零件时的Y向加工尺寸与编程尺寸存在较大的误差,而且误差值与Y轴的移动
数控机床误差过大故障的分析与处理
分析及处理过程:为了进一步确认故障原因,维修时对机 考虑到更换编码器的成本与时间问题,维修时对编码器进行了仔细的清洗,洗去了由于轴承润滑脂融化产生的黑斑。
分析及处理过程:进一步观察、测量机床Y 轴移动情况,发现该机床 Y 轴伺服在移动到某一固定角度时,都有一冲击过程:在无冲击的区域,
根据故障现象,机床存在以上问题的原因似乎与系统的参数设定有关,即:系统的指令倍率、检测倍率、反馈脉冲数等参数设定错误,是产生以
故障原因与位置检测系统有关。 上故障的常见原因。
考虑到更换编码器的成本与时间问题,维修时对编码器进行了仔细的清洗,洗去了由于轴承润滑脂融化产生的黑斑。
但测在量本 后机发床现上,,机因由床于Y该轴机每床机移参动数床一被个存采螺储距用于,E实P的R际O移是M动上半距,离因闭均此要参环相数差出系左错右的统,可而能,且性维具较有小修固。定时的规拆律。下了伺服内装式编码器检
热爱学习,勤于思考,善于发现,敢于实践
敬请指导
THANKS
省级精品在线开放课程
距离成正比,距离越长,误差越大。 数控机床误差过大故障的分析与处理
加数工控误 机差床该过误大差机故过障大床的故分障析分与析Y处与理处轴理伺服在移动到某一固定角度时,都有一冲击过程:在无冲
数控车床对刀误差及解决方法

毕业论文(设计)题目数控车对刀误差及解决方法系部机械工程系专业数控技术班级10级数控技术一班学生姓名马伟光指导教师李彦魁王成成职称讲师助理讲师2013年3月目录摘要第1章数控加工过程中产生的加工误差 (1)第2章对刀方法 (1)2.1试切法 (2)2.2对刀仪对刀 (2)2.3 ATC对刀 (2)2.4 自动对刀 (2)第3章加工误差的原因及采取的措施 (3)3.1 产生误差原因 (3)3.2 减少误差的主要措施 (3)致谢 (4)参考文献 (5)摘要随着社会的快速发展,科学事业也正在飞速的发展。
机械制造业也在日益的扩大,而且对于产品的精度要求也越来越高。
因此,以数字控制技术为核心的新型数字程序控制机床应运而生。
1952年美麻省理工学院研发第一台数控机床。
数控技术是综合了计算机技术、微电子技术、自动化技术、电力电子技术及现代机械制造技术等的柔性制造自动化技术。
数控技术的发展向着高速化,精密化,高效能化,系列化及复合化方向发展。
高速、高精加工技术可极大地提高效率,提高产品的质量和档次,缩短生产周期和提高市场竞争能力。
而且为了保证产品的合格率,就要保证加工时的精准度。
本文:介绍了数控机床的各种误差和对刀方法,详细分析了数控机床的对刀误差来源及相应可采取的改善措施。
通过研究这些问题,对提高数控机床的加工精度提供了依据。
关键词:数控机床对刀点刀位点对刀第1章数控加工过程中产生的加工误差1.1编程误差主要是数控编程时数控系统产生的插补误差,主要由于用直线段或圆弧段避近零件轮廓时产生的。
这是影响零件加工精度的一个重要因素。
可以靠增加插补节点数解决,但会增加编程工作量。
1.2刀尖圆弧误差在切削内孔、外因或端面时,刀尖圆弧不影响其尺寸、形状,但在加工锥面或圆弧时受刀尖圆弧影响造成过切或少切。
此误差可通过测量刀尖圆弧半径,采用刀具半径补偿功能来消除误差。
1.3测量误差主要是受量具测量精度以及测量者操作方法影响,导致的实测尺寸不准确。
数控机床定位误差过大故障的判断分析及排除

一
61 —
机床 电器 2 1 . 022
数控 ・ 数显——数控 机床定位误差过大故 障的判 断分析及排除
承( 上油 ) , 后 再运行 l轴 , , 点动 , 自动运 行无 报警 。观 察 “ 服 电机 运 行监 视 画面 ”工 作 电 流 ( 0~3 ) 。 伺 2 0%
需 过 个 能 端就 以 时 程 制 栋 的 网 通 一 智 终 ,可 实 远 控 整 楼 电 。 、
} 录”获批“ 、 上海高新技术产,4重大投资项 目 等 , Jt k ” 受到多项政府产业政策扶持。
i
{
目前 , 上海诺雅 克电气有限公 司已经通过 “ 上海市 高新技 术企业 ” 定 , 列入“ 海市智 能 电网产业重 点企 业名 ; 认 被 上
05 0 2”。
3 故 障处 置
a 更换 编码器 电缆 .
按 照循序渐进 , 由轻到重 的原则 , 与编码 器有 对于 关 的故 障首先检查 或更 换编 码 器 电缆 。( 曾经 有 编码 器 电缆被 老 鼠啃破 的故障 ) 更换 编码器 电缆后 , 故障依 旧 。这样 排除编码器 电缆导致故 障的原 因 ;
各轴 运行是 否抖 动是 常规 的方 法 。只是 要注 意 安全 。
本例 中 , 用触摸方 法 检查 轴 承是 否损 坏 是 钳工 常用 的
方法 。
借 鉴 “ 证施 治 ” 辨 的一 个 方 面就 是 要 判 断 故 障发
生 的阶段 。在调试 阶段 出现的故障 和运行数 年后 出现
特别 是要借 助数 控 系统 本 身强 大韵 自诊 断功 能 , 分 充 使用 “ 诊断 画面” 监视各 输入 输 出点 的连接 状 态 。监 ,
数控加工产生误差的根源及解决方案(二篇)

数控加工产生误差的根源及解决方案本文从数控机床加工过程中误差产生的根源入手,分析了各类误差产生的原因并找出了减少误差的解决方案。
数控机床是机电一体化的高科技产品,用数控加工程序控制数控机床自动加工零件,不必使用复杂、特制的工装夹具,就能够较好地解决中、小批量,多品种复杂曲面零件的自动化加工问题。
但在零件加工过程中,由于种种原因,会造成零件不合格,甚至于产生废品。
本文从加工中误差产生的原因入手,分析并找出减少误差的解决办法。
零件在数控机床上加工过程中,误差主要四个方面:一、误差是制造工艺不合理造成的;二、误差是程序编制不科学造成的;三、是工装使用不当造成的;四、是机床系统自身误差产生的。
制造工艺不合理造成的加工误差在现实生产中,由于工艺设计不合理而造成的误差一般有以下几种形式。
2.1.加工路线不合理而产生的误差由于孔的位置精度要求较高,因此安排镗孔路线问题就显得比较重要,安排不当就有可能把坐标轴的反向间隙带入,直接影响孔的位置精度。
2.2.刀具切入切出安排不当产生的误差铣削整圆时,要安排刀具从切向进入圆周进行铣削加工,当整圆加工完毕之后,不要在切点处取消刀补或退刀,要安排一段沿切线方向继续运动的距离,这样可以避免在取消刀补时,刀具与工件相撞而造成工件和刀具报废。
当铣切内圆时也应该遵循此种切入切出的方法,最好安排从圆弧过渡到圆弧的加工路线,切出时也应多安排一段过渡圆弧再退刀,这样可以降低接刀处的接痕,从而可以降低孔加工的粗糙度和提高孔加工的精度。
2.3.工艺分析不足而造成的误差普遍性的零件结构工艺性并不完全适用于数控加工中,但以下几点的特别注意:2.3.1.采用统一的定位基准,数控加工中若没有统一的定位基准,会因零件的重新___而引起加工后两个面上的轮廓位置及尺寸不协调,造成较大的误差。
2.3.2.避免造成欠切削或过切削现象,在数控车床上加工圆弧与直线或圆弧与圆弧连接的内外轮廓时,应充分考虑其过渡圆弧半径的大小,因为刀具刀尖半径的大小可能会造成欠切削或过切削现象。
FANUC 系统数控机床误差过大报警处理

FANUC 系统数控机床误差过大报警处理摘要:阐述了FANUC系统数控机床410#、411#误差过大报警的工作原理,总结了出现上述报警的原因,并通过实例给出了排除此类故障的方法和步骤。
关键词:410#报警411#报警FANUC系统数控机床编码器、光栅尺、反馈电缆伺、服放大器、伺服电机或传动机构出现故障时往往系统会触发误差过大报警,如FANUC系统的410#报警和411#报警。
410#报警:SERVO ALARM:n- TH AXIS- EXCESS ERROR报警解释:①第n轴的停止位置偏差值超过参数1829的设定值。
②在简易同步控制中,同步补偿量超过参数8325的设定值。
411#报警:SERVO ALARM:n- TH AXIS- EXCESS ERROR报警解释:第n轴移动时的位置偏差值超过参数1828的设定值。
一、工作原理如图1所示,在数控机床进行伺服控制的过程中,系统的移动指令经脉冲分配处理,进入误差寄存器,对误差寄存器的数值递增,通过伺服的速度回路以及电流回路,由伺服放大器驱动伺服电机转动,使安装在电机后面的增量式编码器发出数字脉冲,反馈到伺服放大器,通过FSSB光缆由进入误差寄存器,对误差寄存器的数值进行递减,正常情况下误差寄存器里的数值始终保持在一定范围以内,伺服停止时,误差寄存器的数值为0。
如果移动指令或编码器反馈两者中有一个没有,就会造成误差寄存器里的绝对数值过大,在移动时,如果误差寄存器里的绝对数值>参数1828里设定的数值,机床就会出现411报警,在停止时如果误差寄存器里的绝对数值>参数1829里设定的数值,机床就会出现410报警。
误差寄存器的数值可以在FANUC系统的诊断300号看到。
图1 误差计数器的读数过程二、故障原因通过以上分析可知,每当伺服使能接通,或者轴定位完成时,都要进行上述误差比较。
当以上误差比较超值后,就会出现410#报警,即停止时的误差过大。
- 1、下载文档前请自行甄别文档内容的完整性,平台不提供额外的编辑、内容补充、找答案等附加服务。
- 2、"仅部分预览"的文档,不可在线预览部分如存在完整性等问题,可反馈申请退款(可完整预览的文档不适用该条件!)。
- 3、如文档侵犯您的权益,请联系客服反馈,我们会尽快为您处理(人工客服工作时间:9:00-18:30)。
机床反向间隙大、定位精度差 位置环增益设定不当
4
5 6
各插补轴的检测增益设定不良
感应同步器或旋转变压器的接口板调整不 良 丝杠间隙或传动系统间隙
调整检测增益
重新调整接口板 调整间隙或改变间隙补偿 值
数控机床振荡故障分析与处理
案例分析
一
故障现象:一台配套 DYNAPATH 20M 系统的二手数 控铣床,加工零件时的Y向加工尺寸与编程尺寸存在较大 的误差,而且误差值与Y轴的移动距离成正比,距离越长, 误差越大。 分析及处理过程:为了进一步确认故障原因,维修时 对机床 Y轴的定位精度进行了仔细测量。测量后发现, 机床Y轴每移动一个螺距,实际移动距离均要相差 0.1mm 左右,而且具有固定的规律。 根据故障现象,机床存在 以上问题的原因似乎与系统的参数设定有关,即:系统 的指令倍率、检测倍率、反馈脉冲数等参数设定错误, 是产生以上故障的常见原因。但在本机床上,由于机床 参数被存储于EPROM上,因此参数出错的可能性较小。
数控机床常见故障诊断与排除
数控机床误差过大故障的分析与处理
数控机床误差过大故障分析与处理
一
定位超调故障的分析与处理
可能原因 加减速时间 设定不当 位置环比例 增益设置不 当
速度环比例 增益设置不 当 速度环积分 时间设置不 当
检查步骤 依次检查数控装置 或伺服驱动器上的 这几个参数的设置 是否与说明书要求 相同
热爱学习,勤于思考,善于发现,敢于实践
THANKS
省级精品在线开放课程
敬请指大故障分析与处理
项目 超调 1 2 单脉 1 冲精 度差 2 故障原因 加/减速时间设定过小 与机床的连接部分刚性差或连接不牢固 需要根据不同情况进行故障分析 机械传动系统存在爬行或松动
一 加工误差过大故障的分析与处理
检查步骤 检测起、制动电流是否已经饱和 检查故障是否可以通过减小位置 环增益改善 检查定位时位置跟随误差是否正 确 检查机械部件的安装精度与定位 精度 调整速度控制单元扮傻姑娘的相 应旋钮,提高速度环增益 检查定位是位置跟随误差是否正 确 检查机械部件的安装精度与定位 精度 更换位置控制单元板(主板) 检测位置检测器件(编码器、光 栅) 测量不圆度,检查周向上是否变 形,45°方向上是否成椭圆 测量各轴的定位精度与反向间隙 调整控制单元,使同样的进给速 度下各插补轴的位置跟随误差的 差值在±1%以内 在项目3调整后,在45°上成椭圆 检查接口板的调整 测量、重新调整间隙 措施 延长加/减速时间设定 减小位置环增益或提高机 床的刚性 若正确,见第2项,否则 第3项 调整机床机械传动系统
数控机床振荡故障分析与处理
案例分析
一
分析及处理过程:进一步观察、测量机床Y 轴移动情况, 发现该机床 Y 轴伺服在移动到某一固定角度时,都有一冲 击过程:在无冲击的区域,测量实际移动距离与指令值相符, 根据以上现象,初步判定,故障原因与位置检测系统有关。 因该机床采用的是半闭环系统,维修时拆下了伺服内装 式编码器检查,经仔细观察发现,在冲击的区域,编码器动 光栅上有一明显的黑斑。 考虑到更换编码器的成本与时间问题,维修时对编码器 进行了仔细的清洗,洗去了由于轴承润滑脂融化产生的黑斑。 重新安装编码器后,机床可以正常工作,Y 轴冲击现象消失, 精度恢复。
3
定位 1 精度 不良 2 3 4 5 圆弧 1 插补 加工 的圆 2 度差 3
伺服系统的增益不足
需根据不同情况进行故障分析 机械传动系统存在爬行或松动 位置控制单元不良 位置检测器件(编码器、光栅)不良 速度控制单元控制板不良 需根据不同情况进行故障分析
提高位置环、速度环增益
若正确,见第2项,否则 第3项 调整机床机械传动系统 更换不良板 更换不良位置检测期间 (编码器、光栅) 维修、更换不良板 若轴向变形,则见第2项, 若45°方向上成椭圆,则 见第3项 调整机床,进行定位精度、 反向间隙的补偿 调整位置环增益以消除各 轴间的增益差