副车架的改装分析及设计要点
车架的改造与副车架的设计

车架的改装主车架是汽车底盘上各总成及专用工作装置安装的基础,改装时受到的影响最大,因此,要特别引起注意。
主车架是受载荷很大的部件,除承受整车静载荷外,还要受到车辆行驶时的动载荷,为了保持主车架的强度和刚度,原则上不允许在主车架纵梁上钻孔和焊接,应尽量使用车架上原有的孔。
如果安装专用设备或其它附件,不得不在车架上钻孔或焊接时.应避免在高应力区钻孔或焊接。
主车架纵梁的高应力区在轴距之间纵梁的下冀面和后悬的上冀面处。
因为这些部位纵梁应力较大,钻孔容易产生应力集中。
对于主车架纵梁高应力区以外的其余地方需要钻孔或焊接时,应注意以下事项:1)尽量减小孔径,增加孔间距离,对钻孔的位置和孔径规范,应满足图和表的要求。
主车架钻孔的孔径和孔间距2)在纵梁翼面高应力区外的其它部位钻孔,只能在中心处钻一个孔,如图所示。
3)在纵梁的边、角区域亦禁止钻孔或焊接,所示的区域即为不允许钻孔和焊接加的部位。
因为在这些部位进行钻孔或焊接,极易引起车架早期开裂。
主车架纵梁禁止钻孔区主车架纵梁禁止焊接区4)严禁将车架纵梁或横梁的男面加工成缺口形状。
本课题中由于主车架与副车架之间的连接选用止推连接板形式,故主车架不用考虑钻孔,只需考虑焊接的位置得当。
主车架的加长设计因专用汽车法布置的需要,对主车架有时要进行加长。
例如厢式零担货物运输车和轻泡货物运输车,若用普通汽车底盘改装.则需要将轴距加大,改装长货厢来提高运输效率,此时要将车架在其中部断开后再加长。
也有将车架后悬部分加长的改装设计。
车架加长部分应尽量采用与原车架纵梁尺寸规格一样、性能相同的材料。
车架的加长部分与车架的连接一般采用焊接。
首先在纵梁腹板处,按与纵梁轴线成夹角45。
或90。
的方向把纵梁断开,然后把切口断面加工成坡口形状,如图3-4所示。
最后将加部分与车架纵梁对接起来。
为了获得v型焊缝对接接头的最佳强度,防止焊缝起点出现焊接缺陷,应朱用引弧焊法或退弧焊法。
焊接时应根据纵梁的材料选择合适的焊条型号、直径及焊接规范。
一种后副车架、后悬架总成及车辆的制作方法
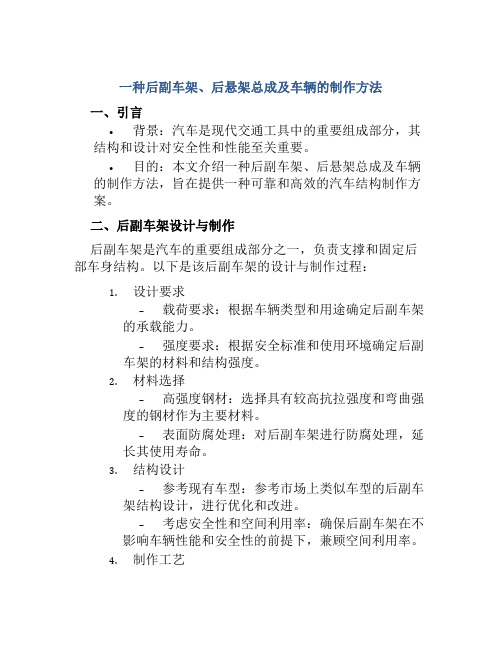
一种后副车架、后悬架总成及车辆的制作方法一、引言•背景:汽车是现代交通工具中的重要组成部分,其结构和设计对安全性和性能至关重要。
•目的:本文介绍一种后副车架、后悬架总成及车辆的制作方法,旨在提供一种可靠和高效的汽车结构制作方案。
二、后副车架设计与制作后副车架是汽车的重要组成部分之一,负责支撑和固定后部车身结构。
以下是该后副车架的设计与制作过程:1.设计要求–载荷要求:根据车辆类型和用途确定后副车架的承载能力。
–强度要求:根据安全标准和使用环境确定后副车架的材料和结构强度。
2.材料选择–高强度钢材:选择具有较高抗拉强度和弯曲强度的钢材作为主要材料。
–表面防腐处理:对后副车架进行防腐处理,延长其使用寿命。
3.结构设计–参考现有车型:参考市场上类似车型的后副车架结构设计,进行优化和改进。
–考虑安全性和空间利用率:确保后副车架在不影响车辆性能和安全性的前提下,兼顾空间利用率。
4.制作工艺–切割和弯曲:使用合适的机械设备将钢材切割成所需形状,并根据设计要求进行弯曲。
–焊接:采用高效且耐久的焊接方法将各部件焊接在一起,确保结构牢固。
三、后悬架总成设计与制作后悬架总成是支撑车辆后部车轮,并提供平稳悬挂和减震功能的重要组成部分。
以下是该后悬架总成的设计与制作过程:1.设计要求–载荷要求:根据车辆类型和用途确定后悬架总成的承载能力。
–减震要求:保证车辆在行驶过程中具备良好的减震效果,提高乘坐舒适性。
–空间利用与节约成本:确保后悬架总成结构紧凑,提高空间利用率,并减少材料和成本。
2.材料选择–弹簧:选择具有良好弹性和耐久性能的弹簧材料。
–减震器:选择高效的减震器,以提供优秀的减震效果。
3.结构设计–参考现有设计:参考市场上类似车型的后悬架总成设计,进行优化和改进。
–考虑安全性和稳定性:确保后悬架总成在高速行驶和恶劣路况下具备良好的稳定性和安全性。
4.制作工艺–弹簧制作:根据设计要求,选择适当的工艺制作弹簧。
–减震器安装:采用合适的安装方法将减震器固定在后悬架总成上,确保安全稳定。
浅谈底盘车架的改装

浅谈底盘车架的改装摘要:本文阐述专用汽车改装设计时主车架和副车架的改装设计要求。
关键词:主车架;副车架目前我国对于常规的厢式车、罐式车、自卸车等通常是采用二类汽车底盘改装设汁,这是目前专用汽车设计中选用底盘型式最多的一种。
所谓二类汽车底盘,是指在基本型整车的基础上去掉货箱。
改装设计总布置时,在没有货箱的汽车底盘上,加装所需的工作装置或特种车身。
工作装置或特种车身和底盘之间由车架进行连接固定。
1主车架的改装主车架是汽车底盘上各总成及专用工作装置安装的基础,改装时受到的影响最大,因此要特别引起注意。
1.1主车架的钻孔和焊接主车架是受载荷很大的部件,除承受整车静载荷外,还要受到车辆行驶时的动载荷,为了保持主车架的强度和刚度,原则上不允许在主车架纵梁上钻孔和焊接,应尽量使用车架上原有的孔。
如果安装专用设备或其它附件,不得不在车架上钻孔或焊接时,应避免在高应力区钻孔或焊接。
主车架纵梁的高应力区位于轴距之间纵梁的下冀面和后悬的上冀面处。
因为这些部位纵梁应力较大,钻孔容易产生应力集中。
对于主车架纵梁高应力区以外的其余地方需要钻孔或焊接时,应注意以下事项:(1)尽量减小孔径,增加孔间距离。
(2)在纵梁的边、角区域禁止钻孔或焊接。
(3)严禁将车架纵梁或横梁的截面加工成缺口形状。
1.2主车架的加长设计因专用汽车布置的需要,对主车架有时需要进行加长。
例如厢式货物运输车和轻泡货物运输车,若用普通汽车底盘改装.则需要将轴距加大,改装长货厢来提高运输效率,此时要将车架在其中部断开后再加长。
也有将车架后悬部分加长的改装设计。
车架加长部分应尽量采用与原车架纵梁尺寸规格一样、性能相同的材料。
车架的加长部分与车架的连接一般采用焊接。
首先在纵梁腹板处,按与纵梁轴线成夹角45°或90°的方向把纵梁断开,然后把切口断面加工成坡口形状,最后将加长部分与车架纵梁对接起来。
1.3主车架加强板的设计(1)主车架纵梁加强板的条件主车架改装时,为了减少车架纵梁的局部应力,或者为了使车架加长后仍能满足强度和刚度的要求,对装载质量增加;轴距和总长发生变化,使车架采用中部拼接或尾部加长时;为了使车架高应力区(危险断面)满足强度和刚度的要求,同时又使车架在某一区间的截面尺寸变化不致太大,这些情况,常常在车架纵梁上采用加强板。
前副车架设计

前副车架设计1. 引言在汽车工程中,副车架是指承载车身和连接前后悬挂系统的结构组成部分。
其中前副车架作为汽车前部的主要支撑和连接部件,承担着重要的作用。
本文将对前副车架的设计进行详细介绍,包括设计要点、材料选择、结构设计等。
2. 设计要点前副车架设计的目标是实现良好的刚度和强度,同时尽可能减轻重量,以提高汽车的操控性和燃油经济性。
下面是前副车架设计的几个重要要点:1.刚度和强度:前副车架需要具有足够的刚度和强度,以承受前部悬挂系统产生的力和扭矩。
这一点可以通过合理的结构设计和材料选择来实现。
2.重量优化:前副车架的重量对整车的性能有直接影响。
因此,在设计过程中应尽可能采用轻量化的设计方案,包括减少材料使用量、优化结构布局等。
3.安全性:前副车架需要具有良好的安全性能,能够在碰撞事故中吸收和转移能量,保护车辆乘员的生命安全。
3. 材料选择前副车架一般采用高强度钢材作为主要材料,具有良好的强度和刚度特性。
同时,为了实现重量优化,也可以考虑使用铝合金等轻质材料。
具体材料选择应根据车辆的使用环境、预算等因素进行综合考虑。
4. 结构设计前副车架的结构设计是保证刚度、强度和重量优化的关键。
下面是一些常见的结构设计方法:•框架结构:框架结构是一种常见的前副车架设计方案,可以提供较高的刚度和强度。
在设计过程中,可以通过优化框架横截面形状和尺寸,以及增加加强筋等方式来提高结构性能。
•悬挂连接:前副车架需要与前悬挂系统进行连接,以承受悬挂系统产生的力和扭矩。
悬挂连接部分的设计应保证连接强度和刚度,并考虑减少疲劳损伤。
•碰撞安全设计:前副车架在碰撞事故中起到保护车辆乘员的作用。
为了提高碰撞安全性能,可以在前副车架的设计中考虑使用可控变形结构、吸能材料等。
5. 进一步研究和发展方向随着汽车技术的不断发展,前副车架的设计也在不断创新和优化。
以下是一些可能的进一步研究和发展方向:•复合材料应用:复合材料具有高强度、轻量化和抗腐蚀等优点,可以考虑将其应用于前副车架的设计中,以进一步减轻重量。
2500HP压裂车副车架结构分析及优化设计
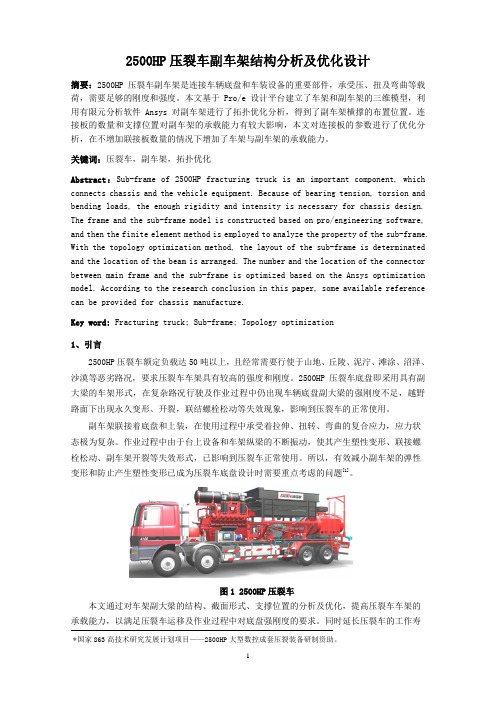
2500HP压裂车副车架结构分析及优化设计摘要:2500HP压裂车副车架是连接车辆底盘和车装设备的重要部件,承受压、扭及弯曲等载荷,需要足够的刚度和强度。
本文基于Pro/e设计平台建立了车架和副车架的三维模型,利用有限元分析软件Ansys对副车架进行了拓扑优化分析,得到了副车架横撑的布置位置。
连接板的数量和支撑位置对副车架的承载能力有较大影响,本文对连接板的参数进行了优化分析,在不增加联接板数量的情况下增加了车架与副车架的承载能力。
关键词:压裂车,副车架,拓扑优化Abstract:Sub-frame of 2500HP fracturing truck is an important component, which connects chassis and the vehicle equipment. Because of bearing tension, torsion and bending loads, the enough rigidity and intensity is necessary for chassis design. The frame and the sub-frame model is constructed based on pro/engineering software, and then the finite element method is employed to analyze the property of the sub-frame. With the topology optimization method, the layout of the sub-frame is determinated and the location of the beam is arranged. The number and the location of the connector between main frame and the sub-frame is optimized based on the Ansys optimization model. According to the research conclusion in this paper, some available reference can be provided for chassis manufacture.Key word: Fracturing truck; Sub-frame; Topology optimization1、引言2500HP压裂车额定负载达50吨以上,且经常需要行使于山地、丘陵、泥泞、滩涂、沼泽、沙漠等恶劣路况,要求压裂车车架具有较高的强度和刚度。
副车架SE分析标准

副车架分析标准1.工具可达性1.1电池或气动工具操作空间是否满足(气动工具、电池工具与周围零部件间隙至少7mm;套筒与周围零部件间隙至少2mm);1.2 针对共线生产,工具是否可通用;2.装配工艺可行性2.1装配工具不得与工装、AGV(或RGV)干涉,托盘可开避让孔,满足工具的使用2.2副车架总成安装标准件增加导向结构3.产品结构合理性3.1车型后副车架由副车架上板、副车架下板、后副车架安装套管组成。
3.2车架安装孔的最终尺寸取决于套管、上下两层钣金的安装孔尺寸的最小值3.3副车架与车身、工装有左右两个定位孔,右侧为主定位孔直径15mm,左侧为长圆孔15mm×19mm。
车身存在相应配合的定位孔,内、外层钣金孔径相同。
定位孔的深度满足定位销深度的要求。
3.4四个安装孔的尺寸,主定位位于工装主定位孔附近,主定位直径16mm,同侧为Y向的长圆孔16mm×18mm,前侧为直径18mm的大圆孔。
安装标准件型号为M14,安装力矩为210±20N·m安装孔的制定需综合考虑各个安装点的位置公差(白车身测量点报告中体现),经过尺寸公差综合分析得出结构3.5前悬总成合装时,工装定位销优先悬置定位销10mm定位,车身需配合存在相应深度的孔径,定位销与车身底部5mm无干涉。
3.6后副车架安装套管组成表面有滚花结构,作用是防滑、防止异响3.7后副车架上板存在轻微起皱现象,经过验证,现对起皱区域加筋处理,消除起皱问题。
新3.8车身前副车架配合孔,采用螺母管和螺母两种形式:螺母管与两层钣金均有焊点,易于保证螺母管的垂直度。
无问题存在问题3.9前副车架安装点直接设计在车身纵梁,安装点处螺母采用凸焊工艺。
若安装点设计在支架处,由于焊接结构复杂,且由于公差累计不易保证安装点精度。
1、前副车架安装点处采用二保焊工艺,二保焊变形量不易控制,容易出现焊瘤,现场生产过程中需要对其进行打磨。
2、前副车架安装点设计在分总成上,还需要与纵梁进行焊接,增加焊接工序,由于公差累计会造成精度问题。
副车架有限元分析及设计优化_蒋玮

《北京汽车》2010.No.2北京汽车文章编号:1002-4581(2010)02-0013-03副车架有限元分析及设计优化蒋玮Jiang Wei(上海汇众汽车制造有限公司产品工程部,上海200122)摘要:利用CAE、CAD技术对新开发的某轿车副车架进行有限元分析及设计优化,并通过试验验证设计的可靠性,从而建立合理可行的结构件设计开发流程。
关键词:副车架;有限元;优化设计;试验验证中图分类号:U463.32.02文献标识码:A随着汽车业竞争压力的加剧,CAE技术在零部件开发中被广泛使用。
目前国内外汽车结构件的设计多采用运动学分析来获得硬点、包络面及载荷等设计输入,利用有限元分析评判设计的合理性,并通过试验验证分析设计的可靠性,将设计、计算机仿真和试验有效地结合起来,大大缩短了开发周期[1]。
文中以轿车副车架作为研究对象,对设计模型进行CAE分析,并根据分析结果进行设计优化,使所设计的副车架满足设计要求。
同时通过台架模拟试验验证了CAE分析及设计的可靠性。
1概述副车架是轿车底盘中非常重要的安全及承载件,作为轿车前部的承载基体,支撑着所有簧上质量[1],承受和传递汽车行驶过程中所产生的各种力和力矩。
因此,副车架的刚度、强度、疲劳寿命等对车辆整体的强度、操纵稳定性及安全性起到至关重要的作用。
按副车架本身工艺特性来分,有冲压焊接和液压成型焊接两种。
文中所介绍的副车架为大型冲压焊接件。
该副车架的主要结构是由两根横梁和两根纵梁以及一些附属支架通过焊接构成,焊接方式为电弧焊,具体结构见图1所示。
1、前梁2、后梁3、右梁4、左梁5、发动机前支架6、发动机后支架7、控制臂前支架8、控制臂后支架9、前套筒10、后套筒11、稳定杆安装孔12、转向机安装孔13、前加强片2有限元模型的建立2.1网格划分[2]网格划分采用Hypermesh软件,副车架本体网格单元采用壳单元,以四边形为主,三角形为辅,焊缝网格采用壳单元中的四边形。
副车架的安装形式及应注意的问题

副车架的安装形式及应注意的问题副车架的安装形式及应注意的问题1. 前言在汽车制造过程中,副车架的安装是极其重要的一环。
副车架通常位于汽车底盘的后部,起到支撑和增强底盘结构的作用。
在本文中,我们将深入探讨副车架的安装形式及应注意的问题。
通过对这一主题的全面评估,希望能够帮助读者更深入地理解副车架的重要性以及安装时需要注意的细节。
2. 副车架的安装形式副车架的安装形式多种多样,根据不同的汽车类型和用途,有以下几种常见的安装形式:2.1 焊接式安装焊接式安装是最常见的一种副车架安装形式。
在这种形式下,副车架通过焊接的方式与汽车底盘连接在一起。
这种安装形式简单、可靠,常用于大型商用车辆和工程车辆中。
但需要注意的是,焊接过程中要确保副车架与底盘的连接牢固,焊接点要均匀分布,以保证整个车架的稳定性。
2.2 螺栓式安装螺栓式安装主要包括副车架与底盘的螺栓连接和螺栓紧固。
这种安装形式具有灵活性高、维修方便的优点,常用于小型乘用车和跨界SUV 等。
在螺栓紧固过程中,需要注意选择合适的螺栓材质和规格,并逐个顺序紧固,以确保副车架与底盘的连接紧密可靠。
2.3 悬挂式安装悬挂式安装是一种相对较复杂的安装形式。
在这种形式下,副车架通过悬挂装置与汽车底盘连接。
这种安装形式主要用于一些特殊用途的车辆,如越野车和赛车等。
悬挂式安装需要考虑到悬挂装置的强度和稳定性,以及车架与底盘之间的协调性。
3. 安装时应注意的问题在进行副车架的安装时,除了选择合适的安装形式,还需要注意以下几个问题:3.1 安装位置的选择副车架的安装位置应根据车辆的结构和布局进行选择。
一般来说,副车架应位于后轴后方,并与主车架相连。
在选择安装位置时,需要考虑到副车架对车辆行驶性能和操控稳定性的影响,以及与其他零部件的协调性。
3.2 强度和刚度的要求副车架的安装需要考虑到其强度和刚度的要求。
副车架应具备足够的强度,能够承受车辆行驶过程中的各种力和振动。
副车架的刚度也要适中,既要保证车辆的稳定性,又要有一定的弹性,以吸收路面不平和碰撞力。
自卸车副车架的分析及优化

by 15% ,a n dt helowestfuel consumpfion rate decrea s edby2% .
图 3 副车架有限元模型
收 稿 日期 :2011-04-07 基 金项 目:广西科学研究 与技术 开发项 目(桂科能 10100026) 作 者简介 :黄 伟 (1963一 ),男 ,广 西人 ,教授 ,工学博 士 ,研究 方 向:机械设计 及理论 ;陆海 漫 (1986一 ),男 ,广西人 ,硕 士 ,研 究方
MPa,材 料 密度 为 7 850 kg/m ,松柏 比为 0-3,屈服 极 载到车架 。自卸车举升时要求平稳的停在路面上 ,因
限为 235 MPa。
此给副车架纵梁施加 了 y方向的约束 ,对前横梁施
2.3 有 限元 模 型 网格 划 分
加了 、y 、z方 向的约束 ,对后横梁施加 了 y、z
Analysis and Optimization for Subframe of the Duck Truck
HUANG W ei,LU Hai—mall,OU Chang-song,YANG Chun—lan
(School of Mechanical Engineer ing,Guangxi University,Na nning 530004,China)
Key words:gasoline engine;electronic control system;electric supercha rger
专用汽车副车架的改装分析及设计要点

专用汽车副车架的改装分析及设计要点
司景萍
【期刊名称】《内蒙古公路与运输》
【年(卷),期】1997(000)001
【摘要】文章对专用汽车副车架的受力情况及结构设计进行了较详细的分析,邮副车架在设计中的若干要点和措施。
【总页数】2页(P28-29)
【作者】司景萍
【作者单位】内蒙古工业大学
【正文语种】中文
【中图分类】U472.7
【相关文献】
1.专用汽车副车架的设计与计算 [J], 金先龙
2.基于ABAQUS的后副车架结构分析及优化 [J], 容家坤
3.基于HyperWorks的混合动力环卫车副车架有限元分析及轻量化设计 [J], 秦东晨;林育恒;王婷婷;陈江义
4.基于HyperWorks的混合动力环卫车副车架有限元分析及轻量化设计 [J], 秦东晨;林育恒;王婷婷;陈江义
5.后副车架台架耐久开裂分析及结构优化 [J], 周德生;吴奕东;胡浩炬;王朕峰
因版权原因,仅展示原文概要,查看原文内容请购买。
厢式货车副车架设计
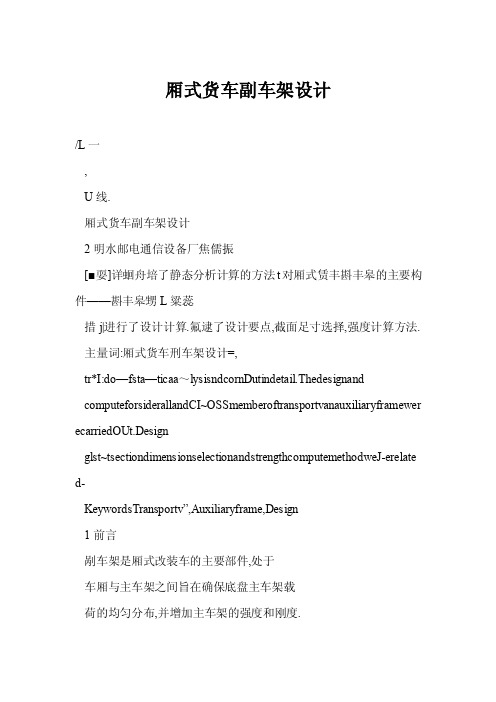
厢式货车副车架设计/L一,U线.厢式货车副车架设计2明水邮电通信设备厂焦儒振[■耍]详蛔舟培了静态分析计算的方法t对厢式赁丰斟丰皋的主要构件——斟丰皋甥L粱蕊措j|进行了设计计算.氟逮了设计要点,截面足寸选择,强度计算方法. 主量词:厢式货车刑车架设计=,tr*I:do—fsta—ticaa~lysisndcornDutindetail.Thedesignand computeforsiderallandCI~OSSmemberoftransportvanauxiliaryframewer ecarriedOUt.Designglst~tsectiondimensionselectionandstrengthcomputemethodweJ-erelate d-KeywordsTransportv”,Auxiliaryframe,Design1前言剐车架是厢式改装车的主要部件,处于车厢与主车架之间旨在确保底盘主车架载荷的均匀分布,并增加主车架的强度和刚度.探入了解酣车架的承载特性及其与主车架承蓑分配情况是副车架结构设计,设进和优化的基础.随着计算机辅助设计及有限元法的广泛应用,动态设计计算日益显得重要.但由于条件的限制,动态设计计算的准确性和可靠性尚显不足,而且大部分厢式车改装厂还难以进行动态设计计算,因此.静态计算仍然是基本的设计计算手段.本文用静态计算的方法对厢式货车副车架的主要构件——副车架纵粟(简称副纵粱)及横粱进行设计计算并予以讨论分析.2翻车集设计2.1副纵粱设计&11副纵粱设计要点a.对具有较高质心位置及载质量较大的厢式车一般采用槽形通长式副纵粱.截面如图1.b.制造材料应具有良好的焊接性和机械性能,一般要求抗拉强度a,~370N/mm.屈服极限,≥240N/ram.,延伸率以≥20.啊1剐纵粱藏面c.翼缘宽度应与主车架纵粱(简称主纵粱)翼缘宽度相同.不宜大于主纵粱翼缘宽度.d.副纵粱截面尺寸确定后,要分别对副纵粱和主纵粱进行强度计算,并根据其惯性矩,抗弯截面系数分配弯矩.2.1.2副纵粱截面尺寸选择副纵粱翼缘宽度应与主纵粱翼缘宽度相同,板材厚度}≥4ram.因此,副纵粱截面尺寸选择主要是确定鹿板高度H.鹿板高度取决于副纵粱承受弯矩的能力及结构上的需要.国外汽车生产厂家均在汽车改装指导书中提出槽形副纵粱截面的最小尺寸,供改装时选择采用,如”依维柯汽车改装指南”中给出的槽形副纵粱截面最小尺寸如表1.根据我厂多年设计生产的经验,副纵粱截面最小尺寸如表2.一2.1.3副纵粱强度计算2.1.3.1强度计算根据主,副纵粱受力特点,一般只需计算.孽墓1997?3专用池车SpecialPurposeV ehicle?15? 弯曲应力,因其剪应力较小,可略去不计.表1依雏柯改装车副纵梁截面最小尺寸酎纵粱截面车辆级别抗弯截面系数尺寸Ⅳ,mT【LH,8,”mm3~7t1600680,50,47.9~1[】{26000100,50,511~33t46000120,60,6剐纵粱截面车载质量抗弯截面系数尺寸1,mmH,B,,mm5t以下250008550,45~8t3900O120,70,58~10t56000120,70,6副纵粱采用U形夹紧螺栓与主纵粱紧密连接,因此可采用两种材料组合粱弯曲时弯矩的计算方法计算主,哥j纵粱动载荷下的摄大弯矩MM—及其弯曲应力,.M~一?M~一?=—HijMla~一Mla~,=式中:E.,E——主,副纵粱材料的弹性模量.,——主,副纵粱截面惯性矩朋.——车架动载荷下的最大弯矩——主,副纵粱抗弯截面系数一的计算方法,在”邮政车副车架设计”一文中有详细介绍(见本刊1.996年第1 期).根据上面的计算,若满足<一及<(一,.分别为主剐纵粱材料的疲劳极限),则所选副纵粱截面尺寸是合理的. 否则,应重新选取副纵梁截面尺寸,即对主,副纵梁承受弯矩进行重新分配.2.1.3.2临界弯曲应力校核当副纵粱变形时,上下翼缘分别受到压缩和拉伸作用而使翼缘断裂.因此,通过以上计算确定副纵粱截面尺寸后,应按薄板理论计算其临界弯曲应力口,并使<.否则,应重新选择副纵粱截面尺寸.E,t,0一0『=【言j式中:——泊松比,取一0.3一般来说,在选定酎纵粱材料厚度t的情况下,副纵粱翼缘的最大宽度应满足B≤16t.2.2横粱设计2.2.1横粱设计要点a制造材料要求与副纵粱制造材料要求相同.b.横粱数目及横粱截面尺寸要根据载质量及受力情况确定.c.尽可能选取同样的横粱间距.这样可使纵粱各段的扭矩相同,也有利于承受弯曲d.尽可能选取相同的横粱截面尺寸.这样可使各横粱刚性一致,协调承载.2.2Z横粱截面尺寸选择横粱截面形状有多种形式,如图2,其宽度B一般取45~50mm;高度不仅要满足强度要求,而且要考虑结构上的要求一般在80~100ram;材料厚度t在2.5~4mm.横粱的截面形状可以用板材折弯,也可使用轧镧型钢,但必须避免出现裂纹,缺口等缺陷.占一田2擅喜I截面类型2.2.3横粱强度计算横粱与剐纵粱相互垂直焊接或螺接在一16?.蕾懦|I厢成货车l9革毒设计起,形成框式结构横粱的两端与货厢骨架侧围焊接或螺接,用以承受货厢的重量.视横梁为固定于副纵粱上的悬臂粱,最大弯矩在横粱与副纵梁腹板的连接处.为了计算方便,假a.横粱等距均布在副纵粱上;b.载质量均布在每一横梁上;c.货厢质量均布在每一横粱的两端.横粱受力简化如图3.图中4,B为横粱与剐纵粱腹板的连接点.,zG1/2IIII{IIIIsIJA占r.田3横粱受力简田A处的弯矩肘为:G百I+一+式中:工——磺粱长度L——横梁悬臂长——横梁载荷中心点至的距离388’25O0.700O0105DO01820851l1775421403结束语a.由于结构的需要或为避免与其他构件发生干涉,游梁无法实现等距均布时,应计算闻距最大处的横梁强度,其承受的货厢质量及计算载荷可按每一横梁所分担的车架长度计算.b.由于普遍超载运行现象,因此,在副车架设计时应予以充分考虑.c.建议汽车底盘生产厂编制改装指导书,为汽车改装厂家提供上装指导.(收稿:1997—06—04责任编辑:张全寿)篙J庠一■l。
副车架设计规范-----------新能源汽车

副车架与车身安装点一般为4个或者6个,且左右两侧相互对称,,4个安装点设计位置一般位于副车架的4个边角处, 如图1-3、1-4、1-5所示,6个安装点设计方式相对4个安装点方案一般在下摆臂安装点之间采用焊接支架的形式增加2个对称的安装点,如图1、2所示,安装点设计完成后需进行装配可行性、可维修性校核,特别是位于下摆臂之间的副车架安装点,摆臂设计过程中应对其安装点进行避让,且此安装点装配可行性校核时需将下摆臂跳动到下极限状态进行校核,如图1-1所示。
4、副车架结构设计
4.1 副车架基本形式的选择
根据设计车型前期的悬架形式定位,选择副车架的基本形式。为降低开发成本及风险,副车架设计基本分为2种情况,情况一为完全重新设计,基本形式在标杆车基础上进行重新设计,情况二为在现有平台基础上进行改款升级,一般形式与基础车型相同。
4.2 副车架的硬点的确定
副车架硬点包括安装硬点、定位硬点、运动硬点三种。
图1-6副车架转向器安装点(左舵上,右舵下)
4.7 后悬置安装点设计
后悬置安装点需根据同平台所有动力总成后悬置点位置进行居中选定,以保证副车架后悬置安装点的平台化;后悬置安装点主要承受来自后悬置的X向力,所以在结构设计过程中需注意将其X向力均匀传递至副车架整体后横梁总成,避免应力集中风险,如图1-7所示。后悬置安装点结构形式可归纳为2类,第一种结构为在后横梁本体上焊接安装支架,如图1-7所示,第二种结构为直接安装在后横梁上下板之间,中间采用支撑板加强,如图1-8所示。
XXXXXXX有限公司
副车架设计规范
编制:
校对:ห้องสมุดไป่ตู้
审核:
批准:
2017-09-15发布 2017-09-20实施
副车架的改装分析及设计要点

疲劳破坏是由于构件外部形状的突变以及材料不均匀等原因,使构件某些局部应力特别高。而汽车是一个复杂的多质量振动系统,振动意味着交变应力长期重复出现,在交变应力的作用下,应力较高的点或材料有缺陷的点逐步形成了裂纹。当裂纹扩展到一定程度时,遇到偶然的超载冲击,构件就会沿薄弱的截面发生突然脆性断裂。
2 副车架的结构分析
专用汽车在使用中,其副车架纵梁出现的裂纹、断裂及焊缝撕裂现象,以自卸汽车尤为严重。下面以自卸汽车为例,对副车架所受的静载荷、动载荷和疲劳破坏三方面进行分析。
2 . 1 静载荷分析
副车架所受的静载荷主要有焊接应力和静弯曲应力等。
2 . 1 . 1焊接应力
副车架在焊接加工过程中产生的焊接应力对其焊缝的强度及冲击值都有较大影响,特别是三项应力集中的部位,极易产生裂纹。若焊接尺寸过长、焊缝不均匀,均可使焊接应力增大。焊接应力影响较大的部位,一般出现在纵梁焊有腹板处,如图l 中a 、b 、c 、d 等处。
专用汽车副车架的改装分析及设计耍点专用汽车的各种专用装置都直接或间接地安装在汽车底盘车架简称主车架上过近几年对专用汽车使用情况的调斉发现专用汽车副车架出现裂纹断裂及焊缝撕裂现象是专用汽车使用中存在的主耍问题而副车架的载荷分析是否正确结构设计是否合理则是产生这些现象的重要原因
专用汽车副车架的改装分析及设计要点
3 . 1 副车架纵梁(简称副梁)的前端形状
为避免副梁前端刚度的突然变化对主车架造成的应力集中,同时为防止汽车制动时和超载后副车架对主车架冲击而产生的附加集中应力,通常在设计中将副梁的前端做成逐步过渡的形式,如图3 所示。
3 . 2 腹板的采用
副车架纵梁多数采用槽形截面,在承受较大载荷部位,采用腹板将槽形盒封闭,以提高副梁的抗弯疲劳强度和抗扭疲劳强度。梁的截面尺寸取决于专用汽车的种类及所受载荷的大小;腹板的厚度为副梁厚度的70 %以上,长度可视所受载荷的大小及受载面长短而定。采用图4 所示的腹板形状,可使腹板刚性圆滑过渡,减小应力集中,提高副梁的抗弯及抗扭能力。
自行式C型旅居车前副车架轻量化设计方案

自行式C型旅居车前副车架轻量化设计方案摘要:自行式C型旅居车的前副车架是旅居车的重要组成部分,其重量对车辆性能和燃油经济性有着重要的影响。
本文基于轻量化设计的原则,采用材料选择、结构优化等手段,设计了一种前副车架轻量化方案。
该方案通过合理的材料搭配和结构优化,成功将前副车架的重量减轻了约15%,同时还能够保证其强度和刚度,提高旅居车的燃油经济性和行驶性能。
这表明,在未来的旅居车设计中,轻量化设计将会成为一个重要的研究方向,以提高车辆的性能和燃油经济性。
关键词:自行式C型旅居车;前副车架;轻量化;材料选择;结构优化引言:自行式C型旅居车因其独特的旅游体验和方便舒适的居住环境,成为现代旅游业中越来越受欢迎的选择。
然而,随着旅游车辆的不断发展和升级,其重量和能源消耗等问题也日益受到关注。
在旅居车的重要组成部分中,前副车架对于车辆的性能和燃油经济性都具有重要的影响。
因此,如何减轻前副车架的重量,提高旅居车的性能和燃油经济性,成为了一个重要的研究方向。
本文将通过轻量化设计的方法,研究如何减轻前副车架的重量,并探讨该方案对旅居车性能和燃油经济性的影响。
1 前副车架轻量化设计的原则轻量化设计是指在不影响产品性能和质量的前提下,尽可能减轻产品的重量。
在前副车架轻量化设计中,需要遵循以下原则:(1)保证强度和刚度。
在前副车架轻量化设计中,必须优先考虑保证其强度和刚度。
因为前副车架需要承受车辆的重量和各种复杂的道路环境,所以其强度和刚度是必须保证的[1]。
在设计前副车架时,需要根据所选材料的性质和前副车架的结构来进行合理的设计,以保证其强度和刚度。
(2)选择轻量化材料。
在前副车架轻量化设计中,选择轻量化材料是非常重要的一步。
轻量化材料可以有效地减轻前副车架的重量,同时还要满足强度和刚度的要求。
常用的轻量化材料包括铝合金、镁合金、碳纤维复合材料等。
选择合适的轻量化材料,可以在不影响前副车架强度和刚度的情况下,实现前副车架的轻量化设计[2]。
汽车副车架技术研究

车型适用 总结
豪华车型普遍采用
微型车、小型车普遍采用
全框式副车架使整车连接刚度更好,经特殊设计,能够吸收碰撞能量,性能较其他副车架结构好
※紧凑型车
区分 昂科塞拉 速腾 福克斯 朗动 宝来
式样
全框式副车架 (部分镂空,增加强度)
H型副车架
H型副车架
H型副车架
H型副车架
结构特点
钢制,冲压焊接 钢制 钢制 钢制 钢制
1.汽车副车架
概述
副车架可以看成是前后车桥的骨架,是前后车桥的组成部分。副车架并非完整的车架,只是支 承前后车桥、悬架的支架,使车桥、悬架通过它再与“正车架”相连,习惯上称为“副架”
路面冲击 悬架总成冲击 长波冲击 综滤: 轮胎橡胶及整体变 形 第二级过滤: 悬架总成橡胶衬 垫 第三级过滤: 悬架系统上下移 动 第四级过滤: 副车架
与车身连接方式
制造工艺
强度、刚度设计
底盘布置
足够的强度,适当的刚度: 根据底盘总布置要求
设计要素
刚性连接 (车身整体刚度大、 不利振动、噪声的隔 离) 橡胶垫连接 (利于隔绝振动、 噪声,操纵感不直 接)
刚度大,强调操控性
冲压焊接 (操纵响应性好, 液压成型 (具备优良的可延伸 性,性能优于冲压焊 接型)
全框式副车架 (部分部件镂空) 部件冲孔,重量减轻,强度增 加
结构特
(类框式结构) 铝制更轻、类框式车架刚度更 高
全框式副车架
全框式副车架 (各点连接采用橡胶衬垫)
全框式副车架
点
钢制
钢制
钢制
2.副车架结构&各级别车型应用
※中级车型
区分
3
汉兰达
奇骏
锐界
7 副车架设计指导书

副车架设计指导书1 副车架设计副车架与主车架的连接一般采用刚性连接。
副车架在设计中应考虑自身结构、刚性分布等,要尽量符合主车架在承载状况下的变形规律,使副车架顺应主车架的扭曲,达到主、副车架的刚性尽量匹配合理(如图2)。
2 车架强度校核在实际使用状况下车架受力比较复杂,在车架初始设计时,一般对车架强度校核简化为对车架纵梁进行弯曲强度校核。
2.1基本假设车架纵梁进行弯曲强度校核时,作以下假设:纵梁是支承在悬架支座上的简支梁;所有作用力均通过车架纵梁断面的弯曲中心(即纵梁只发生纯弯曲);空车簧载质量均匀分布在汽车左、右纵梁上;满载时有效载质量e 为集中载荷,分布如图3所示:主、副车架为刚性连接,即主、副车架挠度 2.2车架受力分析及计算车架受力分析如图3所示。
图三图中:G ef,Ger 为前、后支架所承受的有效载质量,由上装平衡条件”1计算可得:Gef= )2/2//()2/(n f e d n f G e++++)2/2//()2/(n f e d d e ef e er G G G G e++++=-=; F f ,F r为前后轴对车架的支反力,由车架平衡条件计算可得:F f =b n f l b G a L esG /)]()2/ [--++-,F r=[l)]/b-n (f G L)-(L/2[e ++G s ;Gs为空车簧载重质量,取Gs=2m g/3z(m 为汽车整备质量)2.3车架纵梁弯矩计算由受力分析和计算结果,可计算每侧车架纵梁各段的弯矩:21/(2)S M G X L =- 0X a <≤22/(2)()S f M G X L F X a =-+- a X a c <≤+223/(2)())s f ef M G X L F X a G X a c =-+---- a c X a c d +<≤++24/(2)()()s f ef M G X L F X a G X a c d =-+----- a c d X a b ++<≤+25()()/(2)er s M G X a b G X a b L =------ a c d X a b l n++<≤++-226()/(2)()/(2)S er M G X a b l n L G X a b l n n =----+----+a b l n X L ++-<≤式中:X 为截面至车架前端距离。
浅析汽车底盘车架改装上的重点注意事项

—109—《装备维修技术》2021年第5期1.主车架的钻孔或焊接主车架属于安装汽车底盘所需的专用设备,在改装时也是工作人员关注的焦点。
由于这一区域所受载荷非常大,如整辆车的静载荷和运行期间的动载荷,所以在改造设计时为了保障整体结构的刚度和强度,原则上规定不允许在它的纵梁上进行钻孔和焊接,必须要尽量使用原有出场的孔洞。
假设需要安装其他设施或附件,必须要在主车架上进行焊接或钻孔,那么也要减少高应力区域的操作。
一般来讲,它的高应力区域是指轴距之间、纵梁的下翼面和后悬的上翼面。
[1]因为这些区域的纵梁应力非常大,所以若是进行钻孔必然会形成集中应力。
整合以往改装设计经验分析可知,工作人员在不是高应力区域钻孔或焊接时,必须要注意以下几点问题:第一,降低钻孔的直径,增加钻孔之间的距离,通常要符合如下表1所示的要求:表1 钻孔尺寸分析尺寸车型重型中型轻型钻孔的间距(mm )A>70>60>50B >50>40>30C >50>40>30钻孔直径(mm )D<15<13<11第二,在纵梁翼面中,除了高应力区域以外,最多只能在中心区域钻1个孔,具体如下图1所示:图 1 钻孔示意图第三,绝不能在车架的纵梁或者是横梁的加工区域造成缺口,不然极容易影响汽车运行效率和安全。
2.车架后悬在改装这一区域时,需要考虑两种情况,一种为后悬缩短,另一种为后悬加长。
按照目前我国机动车安全运行提出的规章制度分析可知,在改装设计车辆时,后悬绝不能比轴距低65% ,最长长度要控制在3.5cm 。
而有的特殊汽车在达到上述要求的同时,还要整改离去角,以此提升汽车运行和操作的有效性。
了解我国通信汽车管理提出的要求可知,专用汽车底盘改造工作的离去角不能比26°低,换句话说装车厢的后部分和车架后部分之间的距离要低于400mm 。
要想缩短汽车的车架,可以直接对后横梁区域的横梁部分进行整改,此时不仅要严控板簧后吊耳和横梁之间的连接区域,而且要充分展现其具有的积极作用。
后副车架优化方案分析与确定

工艺•材料•设备后副车架优化方案今箭与确定刁兴前(辽宁曙光汽车集团股份有限公司)摘要:简要介绍了后副车架常见失效位置及形式,从后副车架开裂位置、横梁与纵梁搭接长度及形式三方面对其进行了优化,确定了最佳优化方案。
关键词:后副车架 应力集中 优化方案Analysis and determination of local stress concentration optimization scheme for rear secondary frameAbstract : It briefly introduces the common failure positions and forms of the rear auxiliary frame, optimizes itfrom three aspects: the cracking position of the rear auxiliary frame, the length and form of the connection be tween the crossbeam and the longitudinal beam tower, and determines the best optimization scheme.Key word :rear secondary frame, stress concentration, optimization scheme.0引言副车架是连接车身和各悬架的过渡件,其作用是 传递车轮与车身之间的力和力矩,缓冲由路面传给车身的冲击力,降低由此引起的震动,保证汽车平稳的行驶。
疲劳寿命是考量副车架的重要指标之一,裂纹、断裂是副车架的疲劳失效戦。
因此在对副车架进行谿 时应规避应力集中,尽量使载荷均匀分布。
1后副车架常见失效位置及形式副车架在台架试验或路试过程中,开裂位置一a 位 于薄弱位置并沿着焊缝附近开裂。
前副车架设计
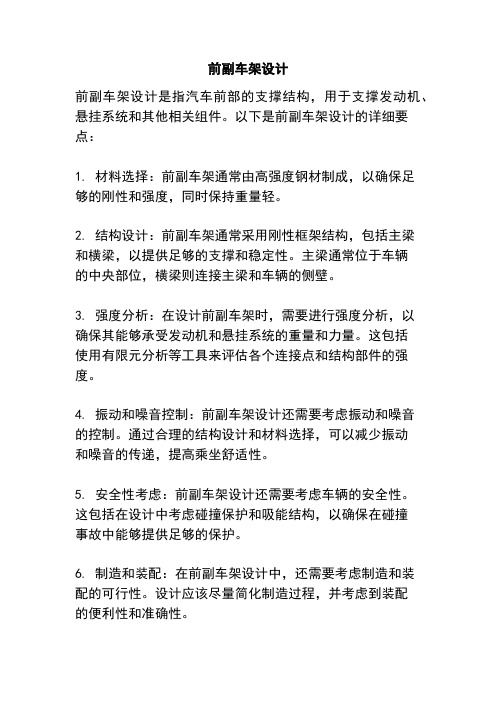
前副车架设计
前副车架设计是指汽车前部的支撑结构,用于支撑发动机、悬挂系统和其他相关组件。
以下是前副车架设计的详细要点:
1. 材料选择:前副车架通常由高强度钢材制成,以确保足
够的刚性和强度,同时保持重量轻。
2. 结构设计:前副车架通常采用刚性框架结构,包括主梁
和横梁,以提供足够的支撑和稳定性。
主梁通常位于车辆
的中央部位,横梁则连接主梁和车辆的侧壁。
3. 强度分析:在设计前副车架时,需要进行强度分析,以
确保其能够承受发动机和悬挂系统的重量和力量。
这包括
使用有限元分析等工具来评估各个连接点和结构部件的强度。
4. 振动和噪音控制:前副车架设计还需要考虑振动和噪音
的控制。
通过合理的结构设计和材料选择,可以减少振动
和噪音的传递,提高乘坐舒适性。
5. 安全性考虑:前副车架设计还需要考虑车辆的安全性。
这包括在设计中考虑碰撞保护和吸能结构,以确保在碰撞
事故中能够提供足够的保护。
6. 制造和装配:在前副车架设计中,还需要考虑制造和装
配的可行性。
设计应该尽量简化制造过程,并考虑到装配
的便利性和准确性。
总之,前副车架设计需要综合考虑强度、刚性、振动控制、安全性和制造装配等因素,以确保其能够满足汽车的需求,并提供良好的性能和乘坐舒适性。
- 1、下载文档前请自行甄别文档内容的完整性,平台不提供额外的编辑、内容补充、找答案等附加服务。
- 2、"仅部分预览"的文档,不可在线预览部分如存在完整性等问题,可反馈申请退款(可完整预览的文档不适用该条件!)。
- 3、如文档侵犯您的权益,请联系客服反馈,我们会尽快为您处理(人工客服工作时间:9:00-18:30)。
为避免副梁前端刚度的突然变化对主车架造成的应力集中,同时为防止汽车制动时和超载后副车架对主车架冲击而产生的附加集中应力,通常在设计中将副梁的前端做成逐步过渡的形式,如图3 所示。
3 . 2 腹板的采用
副车架纵梁多数采用槽形截面,在承受较大载荷部位,采用腹板将槽形盒封闭,以提高副梁的抗弯疲劳强度和抗扭疲劳强度。副梁的截面尺寸取决于专用汽车的种类及所受载荷的大小;腹板的厚度为副梁厚度的70 %以上,长度可视所受载荷的大小及受载面长短而定。采用图4 所示的腹板形状,可使腹板刚性圆滑过渡,减小应力集中,提高副梁的抗弯及抗扭能力。
2 . 1 . 2静弯曲应力
以自卸汽车为例,设主车架纵梁与副车架纵梁为一整体(简称组合梁),货物重量与车厢自重的合力G 均匀作用在组合梁上面,使后桥支点O的两边有向下弯曲的趋势,即载荷P0和Pl (参看图2 ) ,支点后边的载荷通过后翻转轴传至副车架。通过下面公式可简略地计算出组合梁所受弯曲应力σ。
2 副车架的结构分析
专用汽车在使用中,其副车架纵梁出现的裂纹、断裂及焊缝撕裂现象,以自卸汽车尤为严重。下面以自卸汽车为例,对副车架所受的静载荷、动载荷和疲劳破坏三方面进行分析。
2 . 1 静载荷分析
副车架所受的静载荷主要有焊接应力和静弯曲应力等。
2 . 1 . 1焊接应力
副车架在焊接加工过程中产生的焊接应力对其焊缝的强度及冲击值都有较大影响,特别是三项应力集中的部位,极易产生裂纹。若焊接尺寸过长、焊缝不均匀,均可使焊接应力增大。焊接应力影响较大的部位,一般出现在纵梁焊有腹板处,如图l 中a 、b 、c 、d 等处。
由可知,汽车大梁与副车架纵梁在后桥部位承受较大的弯曲应力,其后悬越长,弯曲应力越大。此外作用在组合大梁的垂直载荷在偏离各自的弯曲中心时,除产生弯曲应力外,还会产生扭转变形。
2 . 2 动载荷分析
汽车在行驶过程中,上述的弯曲应力与扭转应力都将变为动载荷,即出现动弯曲应力和扭转应力,其值将比静载荷大3~4 倍。另外,行驶路面的好坏以及载荷分布不均匀,也使副车架纵梁产生严重的扭转变形。一般来说,在副车架纵梁所受的弯曲和扭转复合应力中,扭转应力是主要的,其值将随副车架装置条件的不同而有显著变化。如纵梁在装有加强腹板的地方扭转应力会减小,但在它们的交界处(刚度变化的地方)扭转应力会增大。
2 . 3 疲劳破坏分析
疲劳破坏是由于构件外部形状的突变以及材料不均匀等原因,使构件某些局部应力特别高。而汽车是一个复杂的多质量振动系统,振动意味着交变应力长期重复出现,在交变应力的作用下,应力较高的点或材料有缺陷的点逐步形成了裂纹。当裂纹扩展到一定程度时,遇到偶然的超载冲击,构件就会沿薄弱的截面发生突然脆性断裂。
专用汽车副车架的改装分析及设计要点
专用汽车的各种专用装置都直接或间接地安装在汽车底盘车架(简称主车架)上,即主车架是专用汽车上专用装置的主要承载构件。设计中,为了防止主车架纵梁的应力集中,使纵梁载荷均匀分布,一般在专用装置与主车架之间采用副车架过渡。通过近几年对专用汽车使用情况的调查发现,专用汽车副车架出现裂纹、断裂及焊缝撕裂现象是专用汽车使用中存在的主要问题,而副车架的载荷分析是否正确、结构设计是否合理,则是产生这些现象的重要原因。
3 . 3 材料的选用
专用汽车副车架的材料一般选用低碳钢A3 材料的型材(如槽钢、I 字钢等)。材料自身强度的不足也是引起副车架各种缺陷的主要原因之一,选用A3 材料,必须设置较多的腹板才能满足其强度。如果工艺条件允许,副车架材料可采用疲劳强度高的16Mn钢板冲压成型,以提高其抗疲劳扭转强度及其他机械性能。
由于专用汽车在行驶中其副车架的受力情况比较复杂,结构设计时,必须针对其受力情况进行合理布局。否则副车架即会出现裂纹、断裂及焊缝撕裂等缺陷,严重影响专用汽车的使用寿命。
3 副车架的结构设计
了解了副车架的受力情况,则可在副车架的设计中采取相应措施,最大限度地避免副车架产生上述各种缺陷。副车架的设计应从两方面考虑其结构,一是副车架对主车架强度的影响,二是副车架自身的强度问题。