白车身拼焊夹具MCP设计方法
浅谈白车身焊装夹具设计要点分析

浅谈白车身焊装夹具设计要点分析一、引言白车身焊装夹具设计是汽车生产中的关键环节之一,夹具设计的质量直接影响到整个生产线的效率和产品质量。
白车身焊装夹具设计的要点分析对于提高生产效率、降低生产成本、保证产品质量具有重要意义。
本文将从夹具设计的要点入手,分析影响夹具设计的关键因素,为相关从业人员提供参考。
二、白车身焊装夹具设计的要点分析1. 结构设计白车身焊装夹具的结构设计是决定其功能和稳定性的关键。
优秀的结构设计应该具有简单、坚固、稳定的特点。
夹具应该能够固定车身零部件,确保其在焊接过程中不会发生位移或变形。
夹具的结构应该简单,易于安装和拆卸,便于操作人员进行维护和保养。
夹具的结构应该坚固耐用,能够承受汽车生产线高频率的使用,确保生产过程的稳定性和安全性。
2. 材料选择夹具设计中的材料选择直接关系到夹具的耐用性和使用寿命。
应该选择具有良好的机械性能和抗腐蚀性能的材料,以确保夹具在高频使用的情况下不易损坏和生锈。
对于一些特殊工艺需求的夹具设计,应根据具体情况选择合适的特种材料,以保证夹具的稳定性和可靠性。
3. 工艺要求夹具设计应该考虑到生产工艺的需求,确保夹具能够适应不同产品的焊接要求。
对于多品种、小批量生产的汽车生产线,夹具设计需要具有一定的灵活性,能够适应不同车型的生产需求。
夹具的设计也应考虑到组装和拆卸的便捷性,以减少生产线上的换线时间,提高生产效率。
4. 精度控制夹具设计中的精度控制是保证产品质量的关键。
夹具应该具有良好的定位和固定能力,确保焊接工艺中的高精度要求得以满足。
对于一些需要提高精度的工序,如车身焊接中的角度、尺寸等要求,夹具的设计应该考虑到这些因素,保证产品焊接后的精度和稳定性。
5. 成本控制夹具设计中的成本控制是企业经营的重要因素。
夹具的设计应该充分考虑生产成本、工时成本等因素,选择合适的设计方案来降低生产成本。
夹具的使用寿命也是成本控制的重要因素,应尽量选择耐用、易维护的设计方案,以减少后期的维护和更换成本。
浅谈白车身焊装夹具设计要点分析
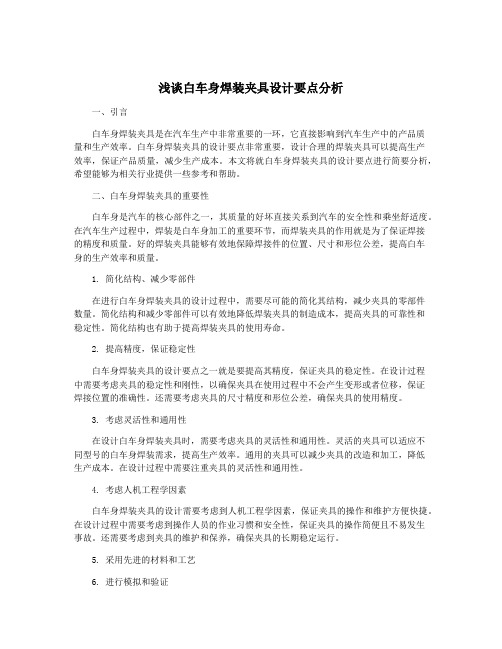
浅谈白车身焊装夹具设计要点分析一、引言白车身焊装夹具是在汽车生产中非常重要的一环,它直接影响到汽车生产中的产品质量和生产效率。
白车身焊装夹具的设计要点非常重要,设计合理的焊装夹具可以提高生产效率,保证产品质量,减少生产成本。
本文将就白车身焊装夹具的设计要点进行简要分析,希望能够为相关行业提供一些参考和帮助。
二、白车身焊装夹具的重要性白车身是汽车的核心部件之一,其质量的好坏直接关系到汽车的安全性和乘坐舒适度。
在汽车生产过程中,焊装是白车身加工的重要环节,而焊装夹具的作用就是为了保证焊接的精度和质量。
好的焊装夹具能够有效地保障焊接件的位置、尺寸和形位公差,提高白车身的生产效率和质量。
1. 简化结构、减少零部件在进行白车身焊装夹具的设计过程中,需要尽可能的简化其结构,减少夹具的零部件数量。
简化结构和减少零部件可以有效地降低焊装夹具的制造成本,提高夹具的可靠性和稳定性。
简化结构也有助于提高焊装夹具的使用寿命。
2. 提高精度,保证稳定性白车身焊装夹具的设计要点之一就是要提高其精度,保证夹具的稳定性。
在设计过程中需要考虑夹具的稳定性和刚性,以确保夹具在使用过程中不会产生变形或者位移,保证焊接位置的准确性。
还需要考虑夹具的尺寸精度和形位公差,确保夹具的使用精度。
3. 考虑灵活性和通用性在设计白车身焊装夹具时,需要考虑夹具的灵活性和通用性。
灵活的夹具可以适应不同型号的白车身焊装需求,提高生产效率。
通用的夹具可以减少夹具的改造和加工,降低生产成本。
在设计过程中需要注重夹具的灵活性和通用性。
4. 考虑人机工程学因素白车身焊装夹具的设计需要考虑到人机工程学因素,保证夹具的操作和维护方便快捷。
在设计过程中需要考虑到操作人员的作业习惯和安全性,保证夹具的操作简便且不易发生事故。
还需要考虑到夹具的维护和保养,确保夹具的长期稳定运行。
5. 采用先进的材料和工艺6. 进行模拟和验证在完成白车身焊装夹具的设计后,需要进行模拟和验证,确保夹具的性能和稳定性。
吉利汽车白车身焊装夹具设计标准

Ⅰ
GEELY 吉利集团制造工程(ME)中心技术业务标准
编号:G42•WB•ST•0002 版次:A1 版
目录 1 范围.....................................................................................................................................................1 2 规范性引用文件 ...................................................................................................................................1 3 术语和定义 ..........................................................................................................................................1 4 焊装夹具 BASE 板要求 ..........................................................................................................................3 4.1 BASE 板技术要求 .............................................................................................................................3 4.2 夹具基准点设计要求 ......................................................................................................................4 4.3 坐标线设计要求..............................................................................................................................6 4.4 起吊装置设计要求 ..........................................................................................................................6 4.5 水平调整地脚..................................................................................................................................7 4.6 平台切口及倒角..............................................................................................................................8 4.7 滚轮.................................................................................................................................................8 5 定位夹紧结构.......................................................................................................................................8 5.1 定位单元构成..................................................................................................................................8 5.2 定位销.............................................................................................................................................9 5.3 定位块...........................................................................................................................................13 5.4 压块...............................................................................................................................................15 5.5 L 块 ...............................................................................................................................................15 5.6 调整垫片/垫块..............................................................................................................................15 5.7 限位机构安装方法 ........................................................................................................................18 5.8 角座设计要求................................................................................................................................19 5.9 导向机构设计要求 ........................................................................................................................21 6 举升机构设计要求 .............................................................................................................................22 7 翻转机构设计要求 .............................................................................................................................23
白车身焊接夹具的结构设计示例

汽车白车身焊接夹具的结构设计一、焊接夹具的设计方法与步骤1.在设计焊接夹具之前,应首先了解生产纲领、产品结构特征、工艺方法与生产线布置方式,作好充分的准备。
参照国外先进的夹具结构,并结合实际情况确定夹具总体方案。
诸如是固定夹具还是随行夹具,机械化、自动化水平是高是低,几种车型主要夹具是否混型共用等。
要准备好的工艺文件包括工序卡,技术协议,产品数模,夹具式样书,焊点文件。
确定使用那种标准件,那种气动元件以与甲方的特殊要求。
2•根据焊件结构特点与所需焊接设备(焊枪或C02)型号、规格,确定定位与夹紧方式(如果有式样书直接按照式样书上的夹紧定位方式即可);同时根据冲压件的工艺特点与后续装配工艺的需要选择合适的定位点与关键定位点。
大部分厂家已经规定好了零件定位的RPS孔和RPS面,不需要我们在制定定位基准了。
但是大家也一定要了解如何确定定位的基准孔和基准面。
3•主体机构确定后,便可确定辅助装置。
如水、电、气回路,气、液动元件以与覆盖件外部焊点所需保护铜板等。
4•按照确定好的定位点开始3D设计。
定位块要求在定位面的法向有3mm的调整量。
定位销要求在与定位孔中心线垂直的平面上有两个方向的调整量。
5•在进行夹具的具体结构设计时,应尽可能多的采用标准化元件,或提高自身的通用化、系列化程度。
二、焊接夹具的组成、结构与要求汽车焊接夹具通常由夹具地板、定位装置、夹紧机构、测量系统与辅助系统等五大部分组成。
命名规则压抉 定位板姿片—阴给走屮加工善时血名规则川J 己%拆准誓件;■'誣仲11祐仁怜购件-国旅件)的细徇和网能誓同更拒惬凶加工itii 保闱同臥■^P'.ATSW -三、如遇其它耒冷名的却丁1申皆寡盟国标、丰服項耳竇却琴匚由項甘负贾人缆一临时定冥-二-茸余敏也LT 库的名瞬和宦交乐"矚郎1."定枪粧"一一兄书在日第夹具中用王L 座与执行元什上H 的崔也联搖件.2.亍广""卜“卑在动柞'堵构中且一乍固立点迪夷点执衍殖开/閒合柱菱动柞的杠杆.3<iSO*—凡指基本划构之陷用于前后談姑拘XI 的i 惚囲餡,牡‘支崖"一一凡缶在欧羸中基于迪抿面的SR-®定蹩粽接rr5."開SE 扳"一一在日集中左达EASE 祖面的馆梅丛尺寸码里豈片 定也檢一)夹具底板夹具地板是焊接夹具的基础元件,它的精度直接影响定位机构的准确性,因此对工作平面的平面度和表面粗糙度均有严格的要求。
白车身焊装夹具及其关键元件的设计分析
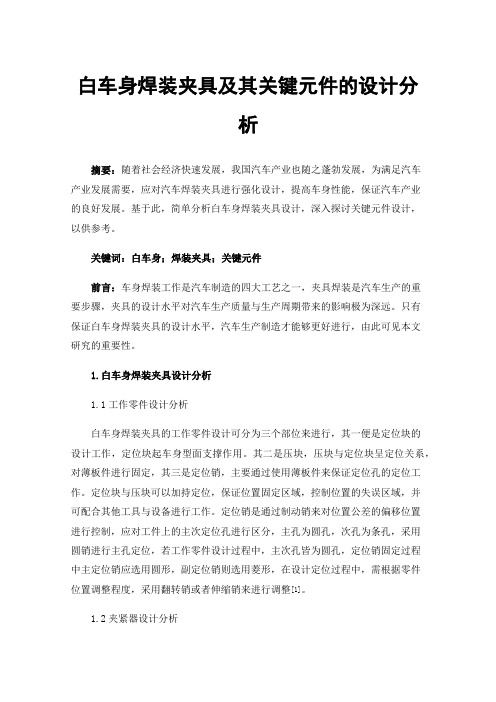
白车身焊装夹具及其关键元件的设计分析摘要:随着社会经济快速发展,我国汽车产业也随之蓬勃发展,为满足汽车产业发展需要,应对汽车焊装夹具进行强化设计,提高车身性能,保证汽车产业的良好发展。
基于此,简单分析白车身焊装夹具设计,深入探讨关键元件设计,以供参考。
关键词:白车身;焊装夹具;关键元件前言:车身焊装工作是汽车制造的四大工艺之一,夹具焊装是汽车生产的重要步骤,夹具的设计水平对汽车生产质量与生产周期带来的影响极为深远。
只有保证白车身焊装夹具的设计水平,汽车生产制造才能够更好进行,由此可见本文研究的重要性。
1.白车身焊装夹具设计分析1.1工作零件设计分析白车身焊装夹具的工作零件设计可分为三个部位来进行,其一便是定位块的设计工作,定位块起车身型面支撑作用。
其二是压块,压块与定位块呈定位关系,对薄板件进行固定,其三是定位销,主要通过使用薄板件来保证定位孔的定位工作。
定位块与压块可以加持定位,保证位置固定区域,控制位置的失误区域,并可配合其他工具与设备进行工作。
定位销是通过制动销来对位置公差的偏移位置进行控制,应对工件上的主次定位孔进行区分,主孔为圆孔,次孔为条孔,采用圆销进行主孔定位,若工作零件设计过程中,主次孔皆为圆孔,定位销固定过程中主定位销应选用圆形,副定位销则选用菱形,在设计定位过程中,需根据零件位置调整程度,采用翻转销或者伸缩销来进行调整[1]。
1.2夹紧器设计分析夹紧器负责夹具的加紧固定,在使用过程中可以通过手动方式或气缸机械方式实现夹紧器的驱动,通过对夹紧器驱动,可以保证夹具加紧力度,保证定位构件与车身部件紧密贴合,避免力大小改变对焊装薄板件产生影响。
为避免焊装位置因各种影响而发生移动,因此在进行夹紧板设计过程中,要以零件的具体情况与设计要求对夹紧器的设计方式进行改变,例如一节旋转销式、两节旋转销式、启动式和动手四连杆式[2]。
1.3连接零件设计分析连接零件作为焊装夹具的基础零件,在整体工程中起承装作用,可安装在工作台上对工作零件与夹紧器进行固定,在进行连接零件设计过程中,需要根据汽车生产过程中的具体需要,采用固定式、旋转式等方式进行设计,并选用适用的零件进行固定。
浅谈白车身焊装夹具设计要点分析
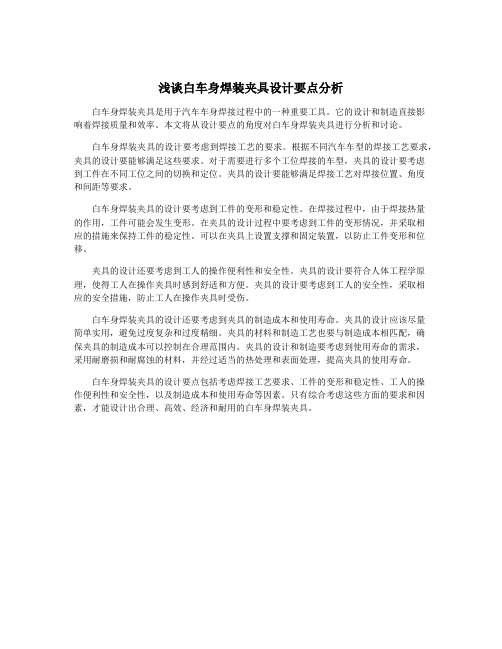
浅谈白车身焊装夹具设计要点分析白车身焊装夹具是用于汽车车身焊接过程中的一种重要工具。
它的设计和制造直接影响着焊接质量和效率。
本文将从设计要点的角度对白车身焊装夹具进行分析和讨论。
白车身焊装夹具的设计要考虑到焊接工艺的要求。
根据不同汽车车型的焊接工艺要求,夹具的设计要能够满足这些要求。
对于需要进行多个工位焊接的车型,夹具的设计要考虑到工件在不同工位之间的切换和定位。
夹具的设计要能够满足焊接工艺对焊接位置、角度和间距等要求。
白车身焊装夹具的设计要考虑到工件的变形和稳定性。
在焊接过程中,由于焊接热量的作用,工件可能会发生变形。
在夹具的设计过程中要考虑到工件的变形情况,并采取相应的措施来保持工件的稳定性。
可以在夹具上设置支撑和固定装置,以防止工件变形和位移。
夹具的设计还要考虑到工人的操作便利性和安全性。
夹具的设计要符合人体工程学原理,使得工人在操作夹具时感到舒适和方便。
夹具的设计要考虑到工人的安全性,采取相应的安全措施,防止工人在操作夹具时受伤。
白车身焊装夹具的设计还要考虑到夹具的制造成本和使用寿命。
夹具的设计应该尽量简单实用,避免过度复杂和过度精细。
夹具的材料和制造工艺也要与制造成本相匹配,确保夹具的制造成本可以控制在合理范围内。
夹具的设计和制造要考虑到使用寿命的需求,采用耐磨损和耐腐蚀的材料,并经过适当的热处理和表面处理,提高夹具的使用寿命。
白车身焊装夹具的设计要点包括考虑焊接工艺要求、工件的变形和稳定性、工人的操作便利性和安全性,以及制造成本和使用寿命等因素。
只有综合考虑这些方面的要求和因素,才能设计出合理、高效、经济和耐用的白车身焊装夹具。
浅谈白车身焊装夹具设计要点分析
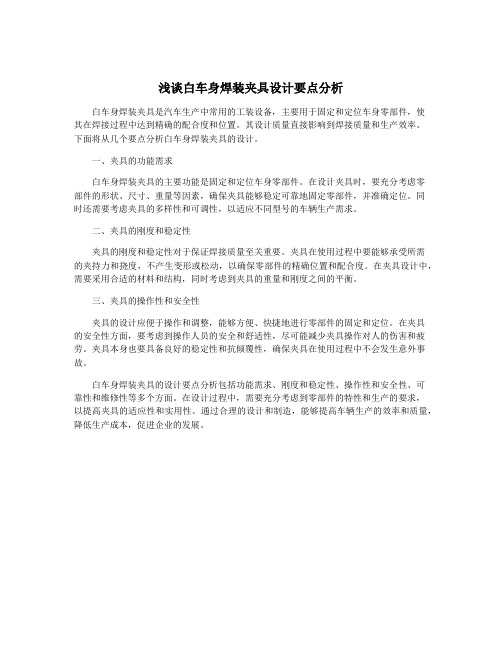
浅谈白车身焊装夹具设计要点分析
白车身焊装夹具是汽车生产中常用的工装设备,主要用于固定和定位车身零部件,使
其在焊接过程中达到精确的配合度和位置。
其设计质量直接影响到焊接质量和生产效率。
下面将从几个要点分析白车身焊装夹具的设计。
一、夹具的功能需求
白车身焊装夹具的主要功能是固定和定位车身零部件。
在设计夹具时,要充分考虑零
部件的形状、尺寸、重量等因素,确保夹具能够稳定可靠地固定零部件,并准确定位。
同
时还需要考虑夹具的多样性和可调性,以适应不同型号的车辆生产需求。
二、夹具的刚度和稳定性
夹具的刚度和稳定性对于保证焊接质量至关重要。
夹具在使用过程中要能够承受所需
的夹持力和挠度,不产生变形或松动,以确保零部件的精确位置和配合度。
在夹具设计中,需要采用合适的材料和结构,同时考虑到夹具的重量和刚度之间的平衡。
三、夹具的操作性和安全性
夹具的设计应便于操作和调整,能够方便、快捷地进行零部件的固定和定位。
在夹具
的安全性方面,要考虑到操作人员的安全和舒适性,尽可能减少夹具操作对人的伤害和疲劳。
夹具本身也要具备良好的稳定性和抗倾覆性,确保夹具在使用过程中不会发生意外事故。
白车身焊装夹具的设计要点分析包括功能需求、刚度和稳定性、操作性和安全性、可
靠性和维修性等多个方面。
在设计过程中,需要充分考虑到零部件的特性和生产的要求,
以提高夹具的适应性和实用性。
通过合理的设计和制造,能够提高车辆生产的效率和质量,降低生产成本,促进企业的发展。
白车身拼焊夹具MCP设计方法浅谈

白车身拼焊夹具MCP设计方法浅谈作者:刘长文来源:《中国科技博览》2016年第16期[摘要]白车身拼焊夹具是一项重要的技术,作为实现车身制造工艺中的重要组成部分,白车身拼焊夹具的设计质量直接关系着车身总体制造效果。
本文基于MCP相关概念,探讨白车身拼焊夹具MCP设计方法,以进一步提高白车身的拼焊精度,仅供相关人员参考。
[关键词]白车身拼焊夹具 MCP设计方法中图分类号:U463.82 文献标识码:A 文章编号:1009-914X(2016)16-0146-01引言为提高白车身设计的有效性,应当在车身的设计过程中综合考虑影响车身制造效果的多项工艺因素,充分考虑夹具制造的可行性,焊接的可行性,最大程度上降低车身制造过程中工艺问题的出现,优化设计方案,切实提高白车身设计的合理性。
为切实提高白车身的拼焊精度,加大力度探讨白车身拼焊夹具MCP设计方法,具有一定的重要性。
1、MCP相关概念MCP是产品质量控制的基准点,在夹具的焊接过程中以关键点的形式存在,实际应用中与产品设计保持同步进行。
MCP在产品质量控制方面发挥着重要的作用,贯穿于产品设计、冲压、焊接以及白车身检测等一系列生产环节中,有助于降低产品质量波动。
MCP在在零件冲压或焊接过程中能够有效的提高定位的精准度,即便是在零件强度较高的情况下,应用MCP能够有效的保证零件定位的可靠性,提高零件测量的便捷性和准确性。
1.1 MCP的组成就MCP的组成情况来看,其中主要包括三个部分,一是定位夹紧位置布局图MCP Lay-out,二是夹紧定位说明表MCP table,三是夹紧定位断面图MCS。
其中,定位夹紧位置布局图主要是对基准点在板件及总成上的设定位置进行准确描述,包括MCP编码、MCP具体设计位置以及其他相关信息等,便于相关设计人员掌握具体的数据参数。
夹紧定位说明表主要包括MCP编号以及相关符号说明,对夹紧、定位和支撑等信息进行准确描述,并以相应的符号表示出来。
白车身拼焊夹具MCP设计方法

工艺设计输入核查清单
序号 目 项 核查 内容
()MC 定位夹紧与定位销尽量单独设立,有助 7 P
于定位单元精度调整 。
零件 ①每 个焊 接总成 的零件构成 ( a i r ) F mlTe y e
()MC 定 位设定要 保证所有 工艺 的一致性 ,即 8 P 模、夹、检具 的定位一致性 。
l 组成 ②每 个焊 接总成的上件顺序 (rcsFo hr Poes l C a) w t
③列举零件信息 ( 板厚、材料 、尺寸 、重量 ) 零件 ①分 析零 件间的匹配条件 2 断面 ②检查焊 枪的可达性 ③MC 设定位 置零件的强度及精度 P ①焊接夹具 的工艺规划 ( 编号、上件流程等 ) 夹具 夹具  ̄B S 板方 向、零件重量 AE 3 工艺 ③ 自动化 线规 划 ( 上件、打点 ) 规划 ④焊枪可达性 ⑤平面布局、节拍等
8 0  ̄ 第 3 2 21 2 期
WWW. mc1 5 C O 9 0.O 7
瑾代 霹 部 件
B。 d
定性 ; P MC 的数量 应最少化 。
g y
2MC 定位位置的选取原则 . P
()控制零件的关键功能面。 1
()MC 设定在正确的位置减少公差累积 。 2 P
一
车 身 )质量控制的主要 基准点 ,是焊接夹具 的基准点 , 可 以使产品质量波 动最小化 ,需要在产 品设计 阶段 同步
完成 。MC 贯穿产品生产的整个过程 ,如产品设计 、冲 P
否与车 身线平行 ;夹紧位 置及方 向 ;控制 点是否 可调 ;
零件信息即零件图号 ; 其他信息如导向、公差等。
结果,MC Mat ot l on)即夹具式样书弥补 P( s r nr it eC o P
浅谈白车身焊装夹具设计要点分析

浅谈白车身焊装夹具设计要点分析白车身焊装夹具是指用于汽车生产中,把未涂漆的车身零部件按照设计要求进行精确定位和加工的工具。
它的设计质量直接决定了汽车生产的质量和效率。
因此在白车身焊装夹具的设计中需要注意以下几个要点:1. 确定设计参数首先,需要确定夹具的使用参数和加工要求。
设计参数包括:车身零部件的尺寸、重量、形状和焊接方式等,还需要注意车身所处的不同位置和加工站点不同的情况,夹具的设计应该考虑到每个站点所需的夹具之间的配合,以避免整体设计失配的情况。
同时需了解所需夹具结构的类型,设立待合模、定位模、涨紧销、涨紧块、支撑脚等具体设计要求,为之后的设计提供参照。
2. 进行3D建模借助计算机三维设计软件,进行优化设计,构建夹具的完整结构。
对于不同形状、重量等参数的产品,可以设计不同的夹具,比如机器手臂、物料传输带等工具可以配合夹具,帮助提高生产效率。
在3D建模的过程中要注重模型的精准度,利用模拟软件进行模型的分析和试验,以确保夹具的工作效率和可靠性。
3. 合理选择材料夹具材料应该具有足够的硬度、耐磨性和强度。
通常会选用合金钢、铝合金、镁合金等材料来制造夹具,并针对车厂的实际要求,选择最合适的材质来建造。
在根据实际工作环境对夹具材料的选择时,还需要考虑到使用寿命、加工精度和经济性的平衡。
4. 合理布局结构夹具的布局结构应该与工件相适应,方便于操作,提高生产效率。
根据不同的加工工艺要求,可以在夹具上布置旋转轴、支撑块、滑动块等附件,以更好的实现车身零部件的定位和加工。
这需要设计者具有对加工流程的深入了解,才能够合理安排夹具的布局结构,保证各个组成部分的功能协调,并且构造合适的夹具以完成预定的工作。
总之,白车身焊装夹具设计,必须依据实际的工作环境和需要设计出适用的方案,特别是在夹具的材料、结构、功能等方面的选择上,需要根据具体的需求来设计,才能够帮助制造商们提高生产效率,降低成本,提高产品的质量和竞争力。
浅谈白车身焊装夹具设计要点分析

浅谈白车身焊装夹具设计要点分析白车身焊装夹具设计是指为了完成汽车车身焊接过程中的定位、支撑、固定等工作而设计的一种专用工装。
夹具设计的好坏直接影响到焊装工艺的稳定性、生产效率和产品质量。
了解白车身焊装夹具设计要点对于提高焊装工艺水平具有重要意义。
1. 确定夹具的结构形式:白车身焊装夹具的结构形式有很多种,如单点夹具、直线导轨夹具、工作台夹具等。
在选择夹具的结构形式时,需要考虑到生产工艺的要求、焊装工位的布置等多方面因素。
2. 确定夹具的定位方式:夹具的定位方式有机械定位和气动定位两种。
机械定位可以提高夹具的稳定性和定位精度,而气动定位则可以提高夹具的调整速度和生产效率。
在确定定位方式时,需要综合考虑夹具的使用频率、焊装工艺的要求等因素。
3. 设计夹具的夹紧方式:夹具的夹紧方式有手动夹紧、自动夹紧和液压夹紧三种。
手动夹紧方式简单可靠,但生产效率较低;自动夹紧方式可以提高生产效率,但对于夹紧力的控制要求较高;液压夹紧方式可以实现夹紧力的精确控制,但设备成本较高。
在选择夹紧方式时,需要根据实际情况进行综合考虑。
4. 考虑夹具的调整范围:夹具的调整范围包括长度、宽度和高度等方面。
在设计夹具时,需要考虑到不同型号车身的焊装要求,合理确定夹具的调整范围,以适应不同车型的生产需求。
5. 考虑夹具的重量和刚度:夹具的重量和刚度对于焊装工艺的稳定性和生产效率有着重要影响。
夹具的重量要适中,以便操作人员能够方便地进行操作;夹具的刚度要足够,以保证焊装过程中不会出现变形和震动等问题。
6. 考虑夹具的可靠性和维护性:夹具在使用过程中需要经过多次调整和更换,因此夹具的可靠性和维护性尤为重要。
夹具的结构要简单,易于拆装和更换,能够方便地进行维护和保养,以提高夹具的使用寿命和可靠性。
白车身焊装夹具设计要点包括选择合适的结构形式和定位方式、合理设计夹具的夹紧方式和调整范围、考虑夹具的重量和刚度、以及注重夹具的可靠性和维护性等方面。
MCP制作规范
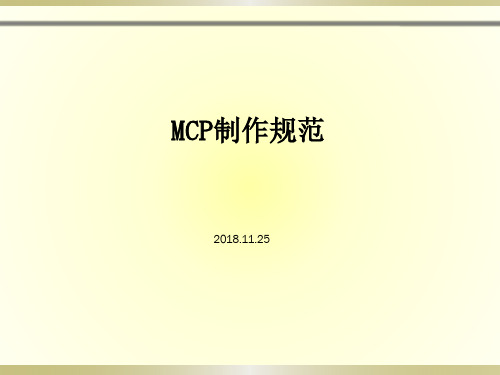
二、MCP定义原则
5、定位面选用原则
(6)考虑冲压工艺,所选平面在冲压中的精度如何,一般来说,应当选择 精度高的面作为定位面,否则无法保证定位面的精度和准确性,从而失去 了定位的意义; (7)尽可能选择平面作为定位面; (8)避开焊点位置,选择定位面; (9)检测点所在的平面也应选作定位面; (10)定位面的设定也应符合“平衡”原则,前后、左右应当相互呼应。
能保持平衡。按照3-2-1原则,保持刚体平衡状态需要六个定位点。 对于薄板柔性件,因刚性不足,为了限制零件受自身受重力变形,通
常第一基准面上的定位点多于3 个,即N≥3,
平板件
U型件 回转件
二、MCP定义原则
1、基本原则
(3)基准统一原则; 各级次部件或者总成的基准必须统一,通过避免基准的转换,进而保证制 造工艺的可靠性和可重复性利用的精确性,不然会出现整车尺寸公差链混 乱,公差无法传递等问题,从而影响整车精度以及装配公差等。
工位编号及总 成名称
总成等轴测视图
上件组成爆炸 图
上件顺序及工 艺形式
零件组成信息
三、MCP文件介绍
2、定位夹紧位置布局图(MCP-Layout)
定位夹紧位置布局图体现定位点板件及总成上的设定位置, 主要包含以下信息: ➢ 零件在夹具上定位姿态; ➢ 所有单件或分总成焊接时的定位主要控制点; ➢ 以夹具单元为基础的UNIT编号信息; ➢ 主要控制部位精确的位置信息(百格线坐标表示) ➢ 主要控制部位精确的尺寸信息(以不同符号表示) ➢ RPS一致性信息(以不同颜色区分表示)
设计顺序:总成到分总成到单件
二、MCP定义原则
4、定位孔选用原则
(1)优先选择Ø10~ Ø30之间的孔作为定位孔,地板上的定位孔一般为 Ø20以上;直径10、12、14、16、18、20、22、24、26、28、30mm为优 先选择的序列(可定义适用于本公司的定位销序列); (2)选择公差精度要求高的孔作为定位孔(定位的目的就是为了保证尺 寸),同时也可以理解为重要的安装孔作为定位孔; (3)选择检测点附近的孔; (4)定位孔在整个工件上,应尽量分开较大距离,合理分布,力争范围大, 以便定位准确,靠的太近,无法保证定位 (5)主定位孔为圆孔,辅助定位孔一般为长圆孔,也可为圆孔,但如果辅 助定位孔为圆孔,则需要菱形销定位,加工比较困难,强度较低,另外对 安装要求较高;
浅谈白车身焊装夹具设计要点分析

浅谈白车身焊装夹具设计要点分析随着汽车工业的快速发展,白车身焊装工艺作为汽车制造中的重要环节,其质量和效率直接关系着整车的品质和生产成本。
而白车身焊装夹具作为车身焊装工艺中的关键设备,其设计质量和制造精度更是对整个生产流程有着直接的影响。
白车身焊装夹具的设计要点分析显得至关重要。
白车身焊装夹具的设计需满足车身焊装的工艺要求。
在车身焊装工艺中,夹具的作用是固定车身零部件,使其能够在焊接过程中保持正确的位置和姿态。
夹具的设计要考虑到零部件的形状、重量、材料等因素,确保能够牢固地夹住工件,并不会对工件造成变形或损坏。
夹具还需考虑到焊接工艺的需求,例如焊接路径、焊接空间等因素。
在设计过程中需要充分了解车身焊装工艺,确保夹具的设计能够满足焊接工艺的要求。
白车身焊装夹具的设计需考虑生产效率和工人操作的便捷性。
在汽车生产中,生产效率是一个至关重要的指标。
夹具的设计应考虑到生产线的节奏,使得夹具能够快速、准确地完成工件的夹持和定位。
夹具的设计还需考虑到工人的操作便捷性,使得工人能够轻松地进行夹具的调整和使用,从而提高工作效率。
白车身焊装夹具的设计需具备一定的通用性和灵活性。
随着汽车产品的不断更新换代,车身零部件的设计和尺寸也在不断变化。
夹具的设计应考虑到不同车型和不同零部件的可通用性,使得夹具能够适应不同的工件并具备一定的灵活性。
这样一来,就能够在不同的生产线和生产批次中灵活使用夹具,避免因为零部件变换而需要重新设计和制造夹具,从而节省生产成本和缩短生产周期。
白车身焊装夹具的设计需考虑到使用寿命和维护保养。
在汽车生产中,夹具的使用频率很高,因此对于夹具的使用寿命和维护保养要求都相对较高。
在夹具的设计中需要考虑到材料的选择和工艺的合理性,确保夹具具备较长的使用寿命和较低的维护成本。
夹具的设计还需考虑到维护保养的便捷性,使得工人能够方便地进行夹具的维护和保养工作,从而延长夹具的使用寿命。
白车身焊装夹具的设计要点分析是一个综合考虑了工艺要求、生产效率、通用性和使用寿命等多个方面的问题。
轿车白车身焊装夹具的设计

大连职业技术学院实习报告
造的轿车白车身焊装夹具在国内的领先地位,更加坚定了我们在公司发展的信心。随 后生产部的王升君部长为我们详细讲解了生产部的工作情况,生产部下辖铆焊车间, 机加工车间以及装配车间。各个车间相互配合,统一由生产部协调生产。最后由安全 科的领导对我们进行安全生产培训,详细讲解了在车间工作时可能遇到的危险,讲解 之后并对我们掌握的安全知识进行了安全测验,直到将安全生产牢记在心。最终做到 安安全全上岗,平平安安下班。
针对我国汽车车身制造技术方面存在的差距和问题汽车生产企业应该采取学习跟随吸收消化局部超越的技术竞争策略时刻跟随前瞻性技术发展的最新动态通过引进消化吸收进行二次开发通过技术和人才储备争取实现局部超越掌握技术发展的主汽车生产企业应不断加大汽车车身制造新技术新工艺新设备的研发投入以节能减排和绿色制造为导向努力提高自主创新能力争取实现汽车车身制造的高品质低成大连职业技术学院实习报告实习工作小结经过4个月的实习我更加深入的了解了公司的产品生产流程设计流程生产投产计划安排等工作
2 夹具设计时需满足的定位要求
大连职业技术学院实习报告
所谓夹具设计时需满足的定位要求就是我们所设计的夹具可以很好的将汽车焊接零 件的位置定位稳定,保证良好的焊接质量。所以在夹具设计过程中一定要严格按照厂家提 供的图纸中定位夹紧机构来设计。
3 夹具设计时应注意的问题
夹具体是夹具的基本件,它既要把夹具的各种元件、机构、装置连接成一个整体,而 且还要考虑工件装卸的方便。因此,夹具体的形状和尺寸主要取决于夹具各组成件的分布 位置、工件的外形轮廓尺寸以及加工的条件等。在设计夹具体时应满足以下基本要求。
大连奥托股份有限公司已于 2001 年通过了 ISO9001,2000 质量体系认证。2007 年通过了环境管理体系 ISO14001 认证。这标志着企业已进入规范化运行的企业行列。 大连奥托公司是首批被大连市政府认定的高新技术企业, 并在 2006 年被辽宁省政府 评为“自主创新优秀企业”。
浅谈白车身焊装夹具设计要点分析

浅谈白车身焊装夹具设计要点分析【摘要】本文从浅谈白车身焊装夹具设计要点的角度进行分析。
在介绍了文章的背景和目的,重点概括了白车身焊装夹具设计的重要性,并引出了接下来要探讨的内容。
在详细介绍了白车身焊装夹具设计的基本原理、解决方案、要点分析、特点和优势,以及实际应用。
在总结了白车身焊装夹具设计要点的重要性,展望了其发展前景,并强调了设计要点分析对于提高生产效率和质量的重要性。
通过本文的阐述,读者可以更深入地了解白车身焊装夹具设计的关键要点,为相关领域的设计和应用提供参考和指导。
【关键词】白车身、焊装夹具设计、要点分析、原理、解决方案、特点、优势、应用、生产效率、质量、发展前景。
1. 引言1.1 介绍篇文章的背景和目的白车身焊装夹具设计是汽车生产中极为重要的环节,它直接影响到汽车产品的质量和生产效率。
为了更好地探讨白车身焊装夹具设计的要点分析,我们有必要首先介绍本文的背景和目的。
随着汽车工业的快速发展,对于汽车生产效率和质量的要求也越来越高。
白车身焊装夹具设计作为汽车生产中的重要环节,其设计质量直接关系到整个汽车生产过程的效率和质量。
深入分析白车身焊装夹具设计的要点,探讨如何提高设计质量和效率,具有重要的理论和实践意义。
本文旨在从白车身焊装夹具设计的角度入手,探讨其设计要点,并分析其特点和优势,为提高汽车生产效率和质量提供理论支持。
通过对白车身焊装夹具设计的深入研究,可以更好地指导实际生产中的设计实践,提升汽车生产的整体水平和竞争力。
1.2 概括白车身焊装夹具设计的重要性白车身焊装夹具设计对于汽车生产具有至关重要的作用。
它不仅可以提高生产效率,降低生产成本,更能确保产品的质量和稳定性。
白车身是汽车的基础结构,其焊接工艺直接影响到整车的质量和安全性。
而焊装夹具作为白车身焊接过程中的重要工具,其设计质量直接关系到焊接过程的精确度和稳定性。
良好的白车身焊装夹具设计可以有效提高生产效率,减少人力资源的浪费。
白车身装配夹具的设计标准
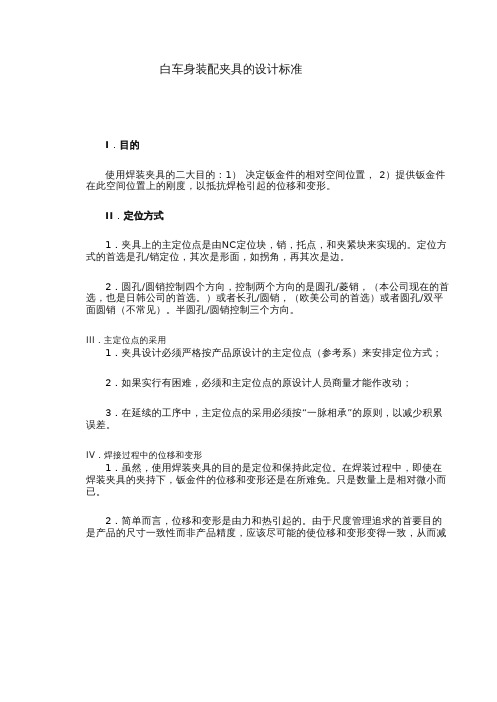
白车身装配夹具的设计标准I.目的使用焊装夹具的二大目的:1)决定钣金件的相对空间位置, 2)提供钣金件在此空间位置上的刚度,以抵抗焊枪引起的位移和变形。
II.定位方式1.夹具上的主定位点是由NC定位块,销,托点,和夹紧块来实现的。
定位方式的首选是孔/销定位,其次是形面,如拐角,再其次是边。
2.圆孔/圆销控制四个方向,控制两个方向的是圆孔/菱销,(本公司现在的首选,也是日韩公司的首选。
)或者长孔/圆销,(欧美公司的首选)或者圆孔/双平面圆销(不常见)。
半圆孔/圆销控制三个方向。
III.主定位点的采用1.夹具设计必须严格按产品原设计的主定位点(参考系)来安排定位方式;2.如果实行有困难,必须和主定位点的原设计人员商量才能作改动;3.在延续的工序中,主定位点的采用必须按“一脉相承”的原则,以减少积累误差。
IV.焊接过程中的位移和变形1.虽然,使用焊装夹具的目的是定位和保持此定位。
在焊装过程中,即使在焊装夹具的夹持下,钣金件的位移和变形还是在所难免。
只是数量上是相对微小而已。
2.简单而言,位移和变形是由力和热引起的。
由于尺度管理追求的首要目的是产品的尺寸一致性而非产品精度,应该尽可能的使位移和变形变得一致,从而减少波动误差。
一项非常可取的做法是保持夹紧顺序和焊接顺序的严格一致。
V.定位销/块的要求精度1.NC定位块的位置精度为+0.10毫米,2.NC定位块的位置精度为+0.10毫米,3.NC定位块的位置精度为+0.10毫米,(1.2.3重复)4.定位销的位置精度为+0.10毫米,5.定位销的直径精度为+0.05毫米,(先要确定定位销的直径)6.定位销的圆度精度为+0.01毫米,7.定位销的直度不控制。
8.定位销有效长度要高出制件表面≥5mm(在不顶起外侧的制件(内外两层板)情况下)9.定位销的间距精度:±0.10毫米(对称定位销)10.单个零件的两个定位销的间距精度:±0.10毫米,11.型面可动时,不能与制件干涉(前进、后退及动作途中无干涉),按动作顺序进行。
浅谈白车身焊装夹具设计要点分析

浅谈白车身焊装夹具设计要点分析白车身焊装夹具是指在汽车生产过程中,用于固定和定位车身零部件以便进行焊接和组装的工装。
夹具的设计对于白车身焊装工艺的质量和效率都有着重要的影响。
下面将对白车身焊装夹具设计的要点进行分析。
白车身焊装夹具的设计要考虑到车身零部件的形状和尺寸。
在设计夹具时,需要详细测量和分析车身零部件的尺寸和形状,确保夹具能够准确地固定和定位这些零部件。
还要考虑到不同车型之间的差异,设计夹具时需要根据具体的车型来进行调整和优化。
白车身焊装夹具的设计要考虑到夹具的结构和材料。
夹具的结构应该牢固稳定,能够承受焊接过程中的力和热。
夹具的材料选择也很重要,一般来说,夹具需要具有足够的强度和刚度,以保证工装在焊接过程中不发生变形或破坏。
夹具的材料还需要具备耐高温和耐腐蚀的特性,以适应焊接过程中的环境要求。
白车身焊装夹具的设计要考虑到夹具的可调性和通用性。
在汽车生产中,存在着不同车型和不同型号的车身零部件,因此夹具需要具备一定的可调性和通用性,能够适应不同类型和尺寸的车身零部件的组装需求。
为了实现这一点,夹具设计时可以采用可调节的零件、可替换的模具和调整机构等,以便根据具体的组装需求进行调整和改变。
白车身焊装夹具的设计还要考虑到操作人员的使用便捷性。
夹具的设计应该符合人体工程学原理,能够让操作人员在使用过程中感到舒适和方便。
夹具设计时要考虑到人机工效学的要求,包括操作空间的布局、夹具的重量和尺寸等,以便操作人员能够更加高效地进行工作。
白车身焊装夹具的设计要点主要包括对车身零部件形状和尺寸的考虑、对夹具结构和材料的选择、对夹具的可调性和通用性的认识以及对使用便捷性的考虑。
通过合理的设计和优化,可以提高白车身焊装工艺的质量和效率,提升汽车生产的整体竞争力。
白车身焊装夹具设计手册范本
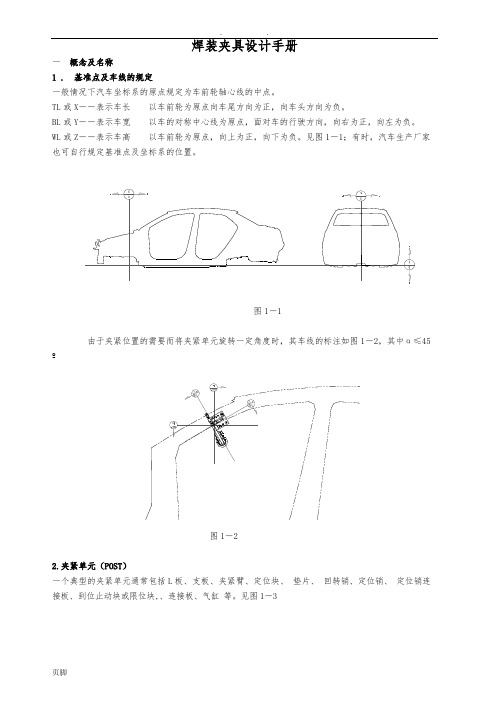
焊装夹具设计手册一概念及名称1 . 基准点及车线的规定一般情况下汽车坐标系的原点规定为车前轮轴心线的中点。
TL或X――表示车长以车前轮为原点向车尾方向为正,向车头方向为负。
BL或Y――表示车宽以车的对称中心线为原点,面对车的行驶方向,向右为正,向左为负。
WL或Z――表示车高以车前轮为原点,向上为正,向下为负。
见图1-1;有时,汽车生产厂家也可自行规定基准点及坐标系的位置。
图1-1由于夹紧位置的需要而将夹紧单元旋转一定角度时,其车线的标注如图1-2,其中α≤45º图1-22.夹紧单元(POST)一个典型的夹紧单元通常包括L板、支板、夹紧臂、定位块、垫片、回转销、定位销、定位销连接板、到位止动块或限位块,、连接板、气缸等。
见图1-3图1-33.夹具一套完整的夹具一般包含若干夹紧单元(POST)、基板(BASE)、举升机构(LIFTER)甚至旋转机构。
根据操作方式可划分为手动夹具、气动夹具及液压夹具;根据控制方式可划分为气控夹具、电控夹具等。
见图1-4(手动夹具), 见图1-5(气动夹具)。
图1-4 图1-5二基板(Base板)Base板一般由槽钢与钢板焊接而成。
槽钢多采用10#、12#、14b#、16#、20#、25b# 等,钢板厚度多采用t=20mm或t=25mm(此为加工完成的厚度,选用毛料时,因考虑加工余量,相应的板厚取t=25mm 或t=30mm)。
对于小夹具或滑台等亦可采用t=30~40mm的钢板焊接而成,而对于总拼夹具以及顶盖装焊夹具,其滑台及支架则可采用矩形方管与钢板焊接而成。
1.Base的最大外形尺寸对于Base的设计应充分考虑焊接及加工的工艺性,以及吊装、运输等方便性。
对于只加工顶底两面的普通Base而言,其长度暂不界定,但宽度不得大于2m,能够运输的最大宽度(非Base本身)为2.3m。
见图2-1图2-1而对于较宽大的Base,为了使其便于加工,往往将其划分为若干个Base,Base间则以支架相联接,此时该Base的单侧或双侧就需加工。
- 1、下载文档前请自行甄别文档内容的完整性,平台不提供额外的编辑、内容补充、找答案等附加服务。
- 2、"仅部分预览"的文档,不可在线预览部分如存在完整性等问题,可反馈申请退款(可完整预览的文档不适用该条件!)。
- 3、如文档侵犯您的权益,请联系客服反馈,我们会尽快为您处理(人工客服工作时间:9:00-18:30)。
2012年 第 3 期
车身技术
ody Technology
B ■ 安徽江淮汽车技术中心/王 艳
车身开发主要分为设计和制造两大阶段。
模夹具设计制造是车身制造的关键技术。
在车身的设计过程中综合考虑车身制造过程中的各种工艺因素,同步考虑模夹具的制造可行性,可以避免在工装制造和车身制造过程中出现大量的工艺问题。
白车身拼焊夹具是实现车身制造工艺的一个重要组成部分。
目前夹具的概念设计大量使用三维软件,缩短了夹具的设计周期,推进了夹具的标准化进程。
但是在装夹方案构思、定位夹紧点的分配上很难得到最优化的结果,MCP (Master Control Point )即夹具式样书弥补了这一不足。
夹具式样书对夹具的主要定位夹紧点进行规划,保证板件的配合精度也即保证了白车身的拼焊精度。
MCP 相关概念
MCP 意为主要控制点,是产品(板件-分总成-白车身)质量控制的主要基准点,是焊接夹具的基准点,可以使产品质量波动最小化,需要在产品设计阶段同步完成。
MCP 贯穿产品生产的整个过程,如产品设计、冲压、焊接以及白车身检测。
MCP 主要定义于下述位置:零件的重要功能面,零件冲压或者焊接过程中易于控制定位精度的位置,零件强度较高的区域以保证零件定位的可靠性,易于测量的位置。
1. MCP 的组成
MCP 主要由三部分组成:定位夹紧位置布局图MCP Lay -out 、夹紧定位说明表MCP table 和夹紧定位断面图MCS 。
(1)MCP Lay -out 即定位夹紧位置布局图,主
白车身拼焊夹具MCP
要描述主要基准点在板件及总成上的设定位置,主要包含MCP 编码、MCP 具体设计位置以及其他一些相关信息。
(2)MCP table MCP table 是夹紧定位说明表,主要描述了夹紧、定位、支撑等信息,并用相对应的符号表示;主要包括MCP 编号以及该MCP 的符号说明。
(3)MCS MCS 是Master control section ,即夹紧定位断面图。
MCS 是在定位孔、夹持点位置沿车身坐标方向或夹持方向做断面,断面图中详细显示定位销的类型、夹紧的布置及方向。
夹紧定位断面图MCS 是夹紧定位布局图完成后下一阶段的工作,主要表达板件控制方式的相关信息如夹紧、板件接触、支撑等。
MCS 断面图主要包含以下信息:支撑块位置及所用材质;定位销位置是否为伸缩销,以及定位销的方向是否与车身线平行;夹紧位置及方向;控制点是否可调;零件信息即零件图号;其他信息如导向、公差等。
2. MCP 设计输入条件
在着手进行M C P 设计之前,必须有一定的输入条件,包括产品设计和工艺设计方面的相关信息,以确保设计输出的MCP 能准确指导夹具的设计制造,最终保证现场生产。
(1)产品设计输入 包括零件三维数模、零件信息(材料、尺寸、板厚)、每个焊接总成的零件构成和特殊公差要求。
(2)工艺设计输入 如附图所示,包含车型信息及其变形产品、生产纲领、各生产线工艺划分、生产节拍、设备信息(夹具、检具等)、初步工艺流程图、焊点布局图、工艺平面布局图以及MLP 文件。
另外,MCP 开始设计前还应注意检查附表所示的内容。
83
2012年 第 3 期
车身技术
ody Technology
B
Web Info 序号项目核查内容
1
零件组成①每个焊接总成的零件构成(Family Tree )
②每个焊接总成的上件顺序(Process Flow Chart)③列举零件信息(板厚、材料、尺寸、重量)2
零件断面
①分析零件间的匹配条件②检查焊枪的可达性
③MCP 设定位置零件的强度及精度
3
夹具工艺规划①焊接夹具的工艺规划(夹具编号、上件流程等)②BASE 板方向、零件重量
③自动化线规划(上件、打点)④焊枪可达性
⑤平面布局、节拍等
4
检具工艺规划①检具的工艺规划(检具编号、上件流程等)②BASE 板方向、零件重量③检具材质构成5
模具工艺规划
①模具的工艺规划②加工方向③成形性分析
④模具生产能力评估
工艺设计输入核查清单
定性;MCP 的数量应最少化。
2. MCP 定位位置的选取原则
(1)控制零件的关键功能面。
(2)MCP 设定在正确的位置减少公差累积。
(3)MCP 设定在强度较高的区域以保证零件定位的可靠性。
(4)定位夹紧的设定要考虑上件、取件的方便性。
(5)MCP 设定在防止零件变形或者变形最小化的区域。
(6)MCP 设定正确的位置确保焊接变形最小化。
(7)MCP 定位夹紧与定位销尽量单独设立,有助于定位单元精度调整。
(8)MCP 定位设定要保证所有工艺的一致性,即模、夹、检具的定位一致性。
(9)夹紧支撑面的设定方向尽量与车身坐标系保持一致,带角度的位置要标出与对应坐标轴的角度。
3. MCP 设计优先原则
制造工艺(模具、夹具)的优先级别要高于检测工艺(单件及总成检具)。
(1)焊装车间最终输出的是白车身总成的精度指标,所以车身总成精度的稳定性更为重要,优先级别要高于其他总成或单件。
(2)车身总成的MCP 设定不合理,出现精度问题将很难进行分析。
(3)车身总成工艺最为复杂,与一般分总成或单件相比更易发生精度的偏离或者变化。
(4)MCP 设定零件特征的优先级别为搭接面>孔>边。
结语
定位支撑点、夹持点的选择确定,是MCP 编制中的重点和难点,为了了解如何确定定位支撑点,建议多到生产现场观察,观察操作过程,描摹绘制现有量产车型的各工位夹具夹紧单元布置图以及各夹紧点部位的截面,通过手工绘制量产车型的MCP 草图,体会其中夹紧单元分布的原因所在以及具体夹持点的夹持块和夹持面的分布,为后面编制新MCP 打下基础。
MCP 设计方法
MCP 设计目的是为确保车身精度无偏差,能够在要求的公差范围内,需要将单件的基准与焊接工位的基准统一,并决定焊接夹具的定位基准。
如果设备方面有一些制约条件,则需要考虑现实上可以成立的基准来设定。
1. MCP 设计方法
MCP 设计要保证在所有工艺中的一致性,即模具、夹具、检具定位位置的一致性。
同时MCP 的设计要遵循从总成、分总成到板件的优先级别;MCP 设计要遵循3-2-1守则,即要防止零件在X 、Y 、Z 三个方向发生移动或者旋转;MCP 设定要保证零件外观尺寸及定位稳
(收稿日期20120131)。