无缝钢管的热轧工艺
热轧无缝管的加工工艺流程
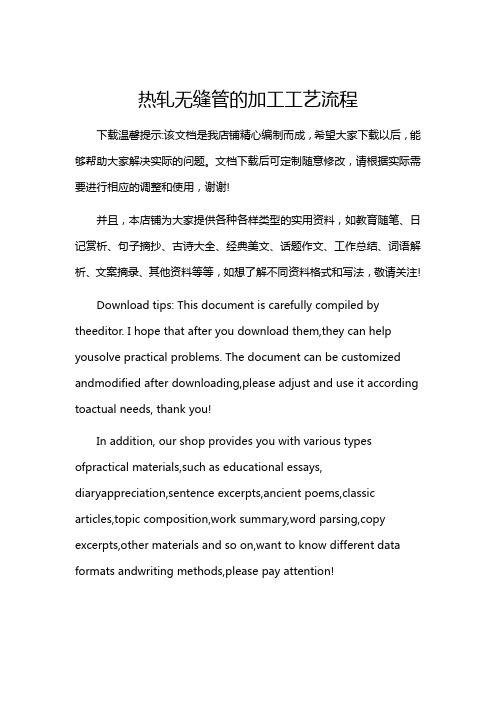
热轧无缝管的加工工艺流程下载温馨提示:该文档是我店铺精心编制而成,希望大家下载以后,能够帮助大家解决实际的问题。
文档下载后可定制随意修改,请根据实际需要进行相应的调整和使用,谢谢!并且,本店铺为大家提供各种各样类型的实用资料,如教育随笔、日记赏析、句子摘抄、古诗大全、经典美文、话题作文、工作总结、词语解析、文案摘录、其他资料等等,如想了解不同资料格式和写法,敬请关注!Download tips: This document is carefully compiled by theeditor. I hope that after you download them,they can help yousolve practical problems. The document can be customized andmodified after downloading,please adjust and use it according toactual needs, thank you!In addition, our shop provides you with various types ofpractical materials,such as educational essays, diaryappreciation,sentence excerpts,ancient poems,classic articles,topic composition,work summary,word parsing,copy excerpts,other materials and so on,want to know different data formats andwriting methods,please pay attention!热轧无缝管的加工工艺流程热轧无缝管的加工工艺流程如下:首先,将钢锭或钢坯加热至适当温度,以获得良好的塑性,便于后续轧制。
热轧无缝钢管工艺流程

热轧无缝钢管工艺流程热轧无缝钢管是一种常用的钢铁制品,广泛应用于石油、天然气、化工、电力、航空等领域。
本文将详细描述热轧无缝钢管的工艺流程,包括原材料准备、加热和轧制、冷却和修边等步骤。
1. 原材料准备热轧无缝钢管的原材料通常为圆坯(也称为毛坯)。
圆坯是通过连铸或锻造制成的,其直径和长度根据不同规格的钢管需求而定。
在生产之前,需要对圆坯进行外观检查和化学成分分析,确保其质量符合要求。
2. 加热和轧制2.1 加热圆坯需要经过加热处理,以提高其塑性和可变形性。
加热通常采用感应加热或火焰加热的方式进行。
在感应加热中,圆坯通过感应线圈中的电流产生涡流,并且由于涡流效应而发生加热。
火焰加热则是利用火焰的高温将圆坯加热至适当的温度。
2.2 轧制加热后的圆坯被送入轧机,经过一系列的轧制工序进行塑性变形。
首先,圆坯通过粗轧机进行初步轧制,将其直径减小到一定程度。
然后,通过中间轧机和精轧机进行进一步的轧制,使钢管直径逐渐减小,并且壁厚逐渐增加。
在这个过程中,可以根据需要使用多辊轧制机、斜辊轧制机等不同类型的设备。
3. 冷却和修边3.1 冷却经过轧制后的钢管需要进行冷却处理,以恢复其力学性能和尺寸稳定性。
通常采用水冷或气冷的方式进行。
水冷可以快速降低钢管温度,并且具有良好的冷却效果;气冷则相对较慢,但可以避免钢管表面出现水迹等问题。
3.2 修边经过冷却处理后的钢管可能存在一些缺陷或不规则形状,需要进行修边操作。
修边主要是通过切割或磨削等方式将钢管两端的不规则部分去除,使其具有一定的平整度和尺寸精度。
4. 检测和包装4.1 检测热轧无缝钢管在生产过程中需要进行多种检测,以确保其质量符合要求。
常见的检测方法包括尺寸检测、外观检查、化学成分分析、力学性能测试等。
通过这些检测手段,可以对钢管的尺寸、表面质量、化学成分和力学性能等进行全面评估。
4.2 包装经过检测合格的热轧无缝钢管需要进行包装,以便运输和储存。
常见的包装方式包括捆扎包装、打包包装等。
无缝钢管的冷轧与热轧工艺上区别
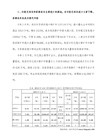
我们都知道无缝钢管可以分为冷轧无缝管和热轧无缝钢管,今天就给大家分享一下我认为的无缝钢管的冷轧与热轧在工艺上区别:
1、 冷轧成型钢允许截面出现局部屈曲,从而可以充分利用杆件屈曲后的承载力;而热轧型钢不允许截面发生局部屈曲。
2、热轧型钢和冷轧型钢残余应力产生的原因不同,所以截面上的分布也有很大差异。冷弯薄壁型钢截面上的残余应力分布是弯曲薄膜型。
3、热轧型钢的自由扭转刚度比冷轧型钢高,所以热轧型钢的抗扭性能要优于冷轧型钢。
冷轧无缝管是指在常温下,经过冷拉、冷弯、冷拔等冷加工把钢板或钢带加工成各种型式的钢材。
无缝钢管的分类

无缝钢管的分类无缝钢管是一种常用的钢材产品,广泛应用于石油、化工、电力、航空、航天等领域。
根据不同的标准和要求,无缝钢管可以被分类为不同的类型,本文将对无缝钢管的分类进行介绍。
一、按生产工艺分类:1. 热轧无缝钢管:热轧无缝钢管是通过热轧工艺生产的,通过高温下的轧制,将坯料加工成管形。
热轧无缝钢管具有较高的强度和韧性,广泛用于高压、高温和耐腐蚀的环境中。
2. 冷轧无缝钢管:冷轧无缝钢管是通过冷轧工艺生产的,通过低温下的轧制,将坯料加工成管形。
冷轧无缝钢管具有较高的尺寸精度和光滑的表面,常用于精密仪器、机械设备和汽车制造等领域。
3. 冷拔无缝钢管:冷拔无缝钢管是通过冷拔工艺生产的,通过将热轧或冷轧的管坯进行拉拔加工,使其形成无缝钢管。
冷拔无缝钢管具有较高的尺寸精度和光滑的内外表面,广泛应用于机械制造、汽车零部件和航空航天等领域。
二、按用途分类:1. 结构用无缝钢管:结构用无缝钢管主要用于承受静载和动载的结构件,如建筑结构、桥梁结构、海洋平台等。
结构用无缝钢管要求强度高、耐腐蚀性好、焊接性能优良。
2. 流体输送用无缝钢管:流体输送用无缝钢管主要用于输送液体、气体和固体颗粒,如石油、天然气、水和粉煤灰等。
流体输送用无缝钢管要求耐压、耐腐蚀、密封性好。
3. 机械用无缝钢管:机械用无缝钢管主要用于制造机械设备和工程机械,如汽车、矿山设备和农业机械等。
机械用无缝钢管要求尺寸精度高、表面光滑、机械性能优良。
三、按材质分类:1. 碳素钢无缝钢管:碳素钢无缝钢管是由碳素钢制造的,其主要成分为碳和铁。
碳素钢无缝钢管具有良好的机械性能和焊接性能,广泛应用于各个领域。
2. 合金钢无缝钢管:合金钢无缝钢管是由多种合金元素(如铬、钼、钢等)与碳素钢相结合制造的。
合金钢无缝钢管具有良好的耐高温、耐腐蚀等特性,常用于高温、高压和特殊环境下的工作。
四、按外形分类:1. 圆形无缝钢管:圆形无缝钢管是最常见的一种无缝钢管,其截面为圆形。
轧管工艺技术(1)——《热轧无缝钢管实用技术》

78技术讲座轧管工艺技术(I)-《热轧无缝钢管实用技术》轧管工序的主要任务是将芯棒穿入毛管内孔,在外部工具(轧辐或银模)的作用下,压缩毛管的外径和壁厚,从而获得尺寸和质量符合要求的荒管。
按轧管机的结构和金属变形方式的不同,可将轧管机分为纵轧管机和斜轧管机。
纵轧管机主要有连轧管机、顶管机(CPE)、自动轧管机、周期轧管机、挤压管机和径向锻管机等;斜轧管机主要有阿塞尔(Assel)轧管机、狄塞尔(Diescher)轧管机、精密(Accu Roll)轧管机、斜轧扩管机和行星轧管机等。
轧管机按机架数量的多少,可分为单机架轧管机和多机架轧管机。
单机架轧管机有自动轧管机、阿塞尔轧管机、狄塞尔轧管机、精密轧管机、周期轧管机、挤压管机、径向锻管机和行星轧管机等。
多机架轧管机有连轧管机和顶管机等。
目前,使用最为广泛的是限动芯棒连轧管机和精密轧管机,其次是周期轧管机、阿塞尔轧管机、挤压管机和顶管机。
行星轧管机还处在推广应用阶段。
1连轧管工艺技术1.1连轧管机概况连轧管法是将经过润滑后的长芯棒穿入毛管内孔,芯棒和毛管一同连续通过多个呈串列布置的轧车昆孔型,将毛管轧制成符合尺寸和质量要求的荒管的一种轧管方法。
早在1843年,就有人开始研究连轧管法,历经几代人对连轧管工艺、芯棒操作方式、机架数、机架形式和传动方式等方面的研究和生产实践,连轧管技术日臻成熟,连轧管机已成为当今业界首选的无缝钢管轧机。
连轧管机的最大延伸系数可达3.5-6.0,荒管最大出口速度可达5~7m/so其主要特点是生产能力大,生产效率高;所轧制的荒管长度长,产品质量好,规格范围广等。
连轧管机按机架型式不同,可分为二辘式连轧管机和三银式连轧管机;按芯棒操作方式的不同,可分为全浮动芯棒连轧管机、限动芯棒连轧管机和半浮动(也称半限动)芯棒连轧管机。
限动芯棒连轧管机的芯棒循环可分为芯棒在线回退和线外循环两种。
二辐式连轧管机由两个轧槽组成孔型,相邻机架的轧银呈90。
无缝不锈钢管制作工艺

无缝不锈钢管制作工艺无缝不锈钢管的制造工艺可以大致分为两类:热轧(挤压)无缝钢管和冷拔(轧制)无缝钢管。
这两类工艺在细节上有所不同,但都是为了获得高质量的无缝钢管。
一、热轧(挤压)无缝钢管的制作工艺如下:1、圆管坯:这是无缝钢管的原材料,一般由钢锭或者钢坯经过热轧或挤压成一定尺寸的圆形截面。
这是无缝钢管制造的第一步,坯料的质量直接影响到后续工艺的效果。
2、加热:将管坯加热到一定温度,使其软化,以便进行后续的穿孔和轧制。
加热过程需要严格控制温度,以确保坯料的软化效果。
3、穿孔:将加热后的管坯穿孔,形成空心钢管。
这是无缝钢管制造的关键步骤之一,穿孔的效果直接影响到钢管的内部质量。
4、三辊交叉轧制、连续轧制或挤压:根据工艺要求,使用三辊轧机、连续轧机或挤压机对钢管进行轧制或挤压,以得到所需的外径和壁厚。
这一步骤需要精确控制轧制力度和速度,以保证钢管的尺寸精度。
5、管道剥离:将钢管从穿孔中拔出。
这一步骤需要保证钢管的表面光滑,无划痕等缺陷。
6、上浆(或减量):在钢管表面涂抹润滑剂或其他材料,以减小轧制过程中的摩擦力。
这有助于提高轧制效率,降低能耗。
7、冷却:将钢管冷却至一定温度,使其保持所需的形状和性能。
冷却速度和温度控制是关键,过快的冷却可能导致钢管变形。
8、矫直:对钢管进行矫直,以消除轧制过程中产生的弯曲和扭曲。
矫直质量直接影响到钢管的直线度和平整度。
9、水压试验(或探伤):对钢管进行水压试验或无损探伤,以确保其密封性能和无缺陷。
这是质量控制的重要环节。
10、标记:在钢管上打上标记,包括规格、生产日期等。
这有助于区分不同型号和生产批次的钢管。
11、仓储:将钢管储存起来,以备后续的处理或使用。
合理的仓储条件可以保证钢管的质量稳定。
二、冷拔(轧制)无缝钢管的制作工艺如下:1、圆管坯:与热轧(挤压)无缝钢管的坯料相同。
2、加热:将管坯加热到一定温度,使其软化。
3、穿孔:将加热后的管坯穿孔,形成空心钢管。
4、退火:使钢管软化,以减小轧制过程中的变形阻力。
热轧无缝钢管生产工艺流程

热轧无缝钢管生产工艺流程热轧无缝钢管是一种常见的钢管产品,广泛应用于石油、天然气、化工、电力、航空、航天、环保等领域。
它具有高强度、耐腐蚀、耐高温等优点,因此在各个行业中都有着重要的地位。
下面将介绍热轧无缝钢管的生产工艺流程。
热轧无缝钢管的原材料是钢坯。
钢坯是经过炼钢厂熔炼后得到的一种半成品,通常为方坯或圆坯。
钢坯的质量对于钢管的生产具有重要的影响,因此要对钢坯进行严格的质量控制。
第二步是加热。
将钢坯加热到适当的温度,一般为1150℃左右。
加热的目的是使钢坯变得柔软,方便后续的轧制和成形。
在加热过程中,需要控制加热温度和加热时间,以确保钢坯达到预定的加热要求。
第三步是轧制。
将加热后的钢坯送入轧机进行轧制。
轧制一般分为粗轧和精轧两个阶段。
粗轧是将钢坯通过辊道进行初步的压制,使其形成一定的形状和尺寸。
精轧是在粗轧后对钢坯进行进一步的压制,使其达到预定的尺寸和表面质量要求。
第四步是定径。
将轧制后的钢坯通过定径机进行定径。
定径机是一种专门用于调整钢管外径的设备。
通过定径机的作用,可以使钢管的外径达到预定的尺寸要求。
第五步是坯管退火。
将定径后的钢管进行退火处理。
退火是将钢管加热到一定温度,然后缓慢冷却的过程。
退火的目的是消除钢管内部的应力,改善钢管的机械性能和物理性能。
第六步是酸洗。
将退火后的钢管进行酸洗处理。
酸洗是将钢管浸泡在酸液中,去除钢管表面的氧化物和锈蚀物,以提高钢管的表面质量。
第七步是冷拉。
将酸洗后的钢管通过冷拉机进行冷拉。
冷拉是将钢管通过模具进行拉伸,使其达到预定的尺寸和表面质量要求。
冷拉还可以提高钢管的机械性能,使其更加坚固和耐久。
最后一步是检验和包装。
对生产出来的热轧无缝钢管进行检验,包括外观质量、尺寸偏差、物理性能等方面的检测。
合格的钢管经过检验后,进行包装和标识,以便运输和使用。
以上就是热轧无缝钢管的生产工艺流程。
每个环节都非常重要,对于钢管的质量和性能有着直接的影响。
通过严格的生产工艺流程控制和质量管理,可以生产出高质量的热轧无缝钢管,满足各种工程和应用的需求。
无缝钢管的轧制

硬度检测
检测无缝钢管的硬度,以评估其材料的硬度和工艺处理效果。
06
无缝钢管的未来发展与 挑战
新技术应用
01
自动化和智能化技术
02
新材料应用
随着工业4.0和智能制造的发展,无缝 钢管轧制过程将更加自动化和智能化 ,提高生产效率和产品质量。
随着新材料技术的不断发展,新型材 料如高强度、高耐腐蚀性、高导电性 等材料将逐渐应用于无缝钢管的生产 中,满足更广泛的应用需求。
03
高效轧制技术
研究和发展更高效的轧制技术,如高 速轧制、低温轧制等,以降低能耗和 减少生产成本。
环保要求
严格的环境法规
随着全球环保意识的提高,各国政府将制定更为严格的环保法规, 要求无缝钢管行业降低污染排放和提高资源利用率。
绿色生产技术
无缝钢管企业需要积极推广和应用绿色生产技术,如废气处理、废 水循环利用等,以实现清洁生产和可持续发展。
根据无缝钢管的用途和要求选 择合适的表面处理方法
外观检测
01
02
03
表面质量
检查无缝钢管表面是否光 滑、无划痕、无裂纹、无 气泡等缺陷。
颜色均匀性
检查无缝钢管的颜色是否 均匀一致,无明显色差。
弯曲度
检查无缝钢管的直线度和 弯曲度,确保满足工艺要 求。
轧辊调整
轧辊间距
01
根据不同规格和工艺要求,调整轧辊间距,确保钢管的壁厚和
直径符合标准。
轧辊硬度
02
选择合适的轧辊硬度,以适应不同材质和规格的钢锭,提高轧
制效率和产品质量。
轧辊平衡
03
确保轧辊在高速旋转时保持平衡,减少振动和噪音,延长轧辊
使用寿命。
03
无缝钢管的轧制过程
无缝钢管制造原理
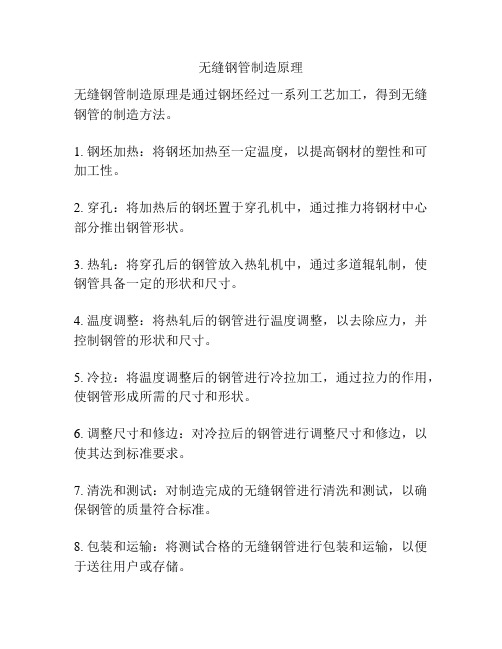
无缝钢管制造原理
无缝钢管制造原理是通过钢坯经过一系列工艺加工,得到无缝钢管的制造方法。
1. 钢坯加热:将钢坯加热至一定温度,以提高钢材的塑性和可加工性。
2. 穿孔:将加热后的钢坯置于穿孔机中,通过推力将钢材中心部分推出钢管形状。
3. 热轧:将穿孔后的钢管放入热轧机中,通过多道辊轧制,使钢管具备一定的形状和尺寸。
4. 温度调整:将热轧后的钢管进行温度调整,以去除应力,并控制钢管的形状和尺寸。
5. 冷拉:将温度调整后的钢管进行冷拉加工,通过拉力的作用,使钢管形成所需的尺寸和形状。
6. 调整尺寸和修边:对冷拉后的钢管进行调整尺寸和修边,以使其达到标准要求。
7. 清洗和测试:对制造完成的无缝钢管进行清洗和测试,以确保钢管的质量符合标准。
8. 包装和运输:将测试合格的无缝钢管进行包装和运输,以便于送往用户或存储。
通过上述的加工工艺,可以制造出质量和尺寸符合要求的无缝钢管。
无缝钢管制造原理相对简单,但在加工过程中需要严格控制各个环节,以确保最终产品的质量和性能。
热轧钢管生产工艺课件

安全教育培训情况
检查员工是否接受安全教育培训,是否掌握 安全知识和技能,培训效果是否达标。
应急预案制定和演练活动安排
应急预案制定
针对可能发生的生产安全事故, 制定相应的应急预案,明确应急 组织、通讯联络、现场处置等方
面要求。
应急演练计划
制定应急演练计划,包括演练时 间、地点、参与人员等,确保演
练活动有序进行。
分类
根据钢管的截面形状和用途,热轧钢 管可分为无缝钢管和焊接钢管两大类 。其中,无缝钢管又可分为热轧无缝 钢管和冷拔无缝钢管两种。
生产工艺流程及特点
生产工艺流程
热轧钢管的生产工艺流程包括原料准备、加热、穿 孔、轧制、定径、冷却、矫直、切割、检验等环节 。其中,加热温度和轧制速度是影响钢管质量的关 键因素。
发展趋势
未来,随着科技的不断进步和环保政策的加强,热轧钢管行业将面临转型升级的压力。一方面,企业需要加大技 术创新力度,研发高强度、耐腐蚀、轻量化的新型钢管产品;另一方面,企业需要推进绿色生产,降低能耗和排 放,实现可持续发展。
02
原料准备与加热制度
Chapter
原料选择与检验标准
原料选择
选用符合标准要求的钢坯作为原 料,确保化学成分、尺寸和表面 质量等指标合格。
热轧钢管质量控制
讲述钢管尺寸精度、表面质量、力学性能等方面的质量要求,以及 质量检查与评估的方法。
行业发展趋势分析
1 2 3
绿色环保生产
随着环保政策的日益严格,热轧钢管生产行业将 更加注重清洁生产和节能减排,推广绿色制造技 术和循环经济模式。
智能化与自动化
智能化制造和自动化技术将在热轧钢管生产中发 挥越来越重要的作用,提高生产效率和产品质量 稳定性。
无缝钢管 热轧的制作流程

无缝钢管热轧的制作流程一、无缝钢管热轧的制作流程概述近几年来,随着无缝钢管热轧的制作流程建设不断增加,给无缝钢管热轧的制作流程的经济发展带来了前所未有的机遇,无缝钢管热轧的制作流程投资越显重要。
伴随着无缝钢管热轧的制作流程数量增加和扩大,无缝钢管热轧的制作流程中存在的问题也日显突出,严重影响了无缝钢管热轧的制作流程正确的投资和发展,无缝钢管热轧的制作流程是否正确,直接决定了无缝钢管热轧的制作流程的经济效益。
(一)无缝钢管热轧的制作流程基本概念无缝钢管热轧的制作流程是选择和决定无缝钢管热轧的制作流程投资行动方案的过程,是对拟建无缝钢管热轧的制作流程的必要性和可行性进行技术经济论证,对不同无缝钢管热轧的制作流程方案进行技术经济比较选择及做出判断和决定的过程。
无缝钢管热轧的制作流程必在充分占有信息和经验的基础上,根据现实条件,借助于科学的理论和方法,从若干备选投资方案中,选择一个满意合理的方案而进行的分析判断工作。
对一个无缝钢管热轧的制作流程的科学决策,除进行宏观投资环境分析和微观无缝钢管热轧的制作流程经济评价分析外,还要专门分析无缝钢管热轧的制作流程风险,运用系统分析原理,综合考虑每个方案的优劣,最后做出决定。
而且,无缝钢管热轧的制作流程决策,是服务服从于总体经营战略的要求,和无缝钢管热轧的制作流程的技术开发战略、产品开发战略、市场营销战略以及人力资源战略密切相关。
无缝钢管热轧的制作流程的质量影响因素较多,主要取决于决策信息、正确的决策原则、科学的决策程序和优秀的决策者素质。
选择无缝钢管热轧的制作流程的主要依据是无缝钢管热轧的制作流程的可行性研究报告。
无缝钢管热轧的制作流程的可行性研究不仅是无缝钢管热轧的制作流程本身的一个工作环节,也是做出正确无缝钢管热轧的制作流程、进行无缝钢管热轧的制作流程设计和筹措资金的重要依据。
可行性研究工作,就是对无缝钢管热轧的制作流程进行研究、分析、论证和评价,以确定无缝钢管热轧的制作流程是否符合技术先进、经济合理、实施可行要求的一系列活动,通过对无缝钢管热轧的制作流程收益和风险的测算分析,判断投资和资金回收的安全性。
无缝钢管的热轧穿孔

Ⅲ区的主要是辗轧毛管管壁,改善毛管壁厚公 差和内外表面缺陷,提 高毛管管壁的尺寸精 度。顶头的母线锥角和锥形轧辊出口锥角相差 不大 ,因此辗轧区的压缩量较小,辗轧区主 要是改善毛管管壁,提高毛管质量 。
在Ⅳ区,顶头和导板已经与管坯脱离,此时只 有轧辊与毛管接触,该区主要是靠轧辊的旋转 将毛管外径转圆。这个变形区很短,而且变形 量 也不大,一般不予以考虑 。
插 90入°配芯置棒的,二通辊过式7轧~机9架连轧轧辊。轴轧线后互抽呈芯棒
, 1产 4166倍4经580。mm再~的m这加6以钢种0热下万管机后钢吨。组进管ห้องสมุดไป่ตู้1的4行,为设0特张m自备点m力动投是连减轧资适续径管大于轧,可机,生管装轧组产机机成的外组容长2径年量~达
大,芯棒长达30m,加工制造复杂。
无缝钢管的穿孔裂纹
显微组织缺陷
产生裂纹的原因
1.穿孔时不均匀变形是开裂纹的主要原因。 2.由于化学成分控制不佳,在钢坯中产生了约 少量δ铁素体相。轧热穿孔过程中,变形强度 沿横截面方向分布不均匀,δ相与γ相变形能力 不一致,在两相的界面产生高于金属断裂强度 的拉应力和切应力,从而促进微裂纹形成并扩 展。
目录
• 热轧无钢缝管简介 • 无缝钢管热轧工艺流程 • 热轧无缝钢管的穿孔 • 热轧无缝钢管的穿孔裂纹
常见无缝钢管
热轧
• 热轧是相对于冷轧而言的,冷轧是在再 结晶温度以下进行的轧制,而热轧就是 在再结晶温度以上进行的轧制。
• 热轧温度一般通过控轧 控冷来实现,即控制精 轧的开轧温度、终轧温 度.
热轧无缝钢管
• 热轧无缝钢管分一般钢管,低、中压锅炉钢管, 高压锅炉钢管、合金钢管、不锈钢管、石油裂 化管、地质钢管和其它钢管等。
• 热轧无缝管外径一般大于32mm,壁厚2.5200mm.
无缝钢管工艺
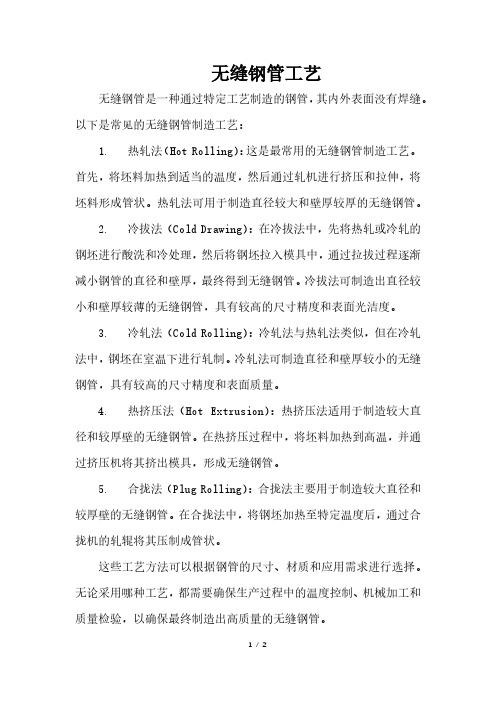
无缝钢管工艺
无缝钢管是一种通过特定工艺制造的钢管,其内外表面没有焊缝。
以下是常见的无缝钢管制造工艺:
1. 热轧法(Hot Rolling):这是最常用的无缝钢管制造工艺。
首先,将坯料加热到适当的温度,然后通过轧机进行挤压和拉伸,将坯料形成管状。
热轧法可用于制造直径较大和壁厚较厚的无缝钢管。
2. 冷拔法(Cold Drawing):在冷拔法中,先将热轧或冷轧的钢坯进行酸洗和冷处理,然后将钢坯拉入模具中,通过拉拔过程逐渐减小钢管的直径和壁厚,最终得到无缝钢管。
冷拔法可制造出直径较小和壁厚较薄的无缝钢管,具有较高的尺寸精度和表面光洁度。
3. 冷轧法(Cold Rolling):冷轧法与热轧法类似,但在冷轧法中,钢坯在室温下进行轧制。
冷轧法可制造直径和壁厚较小的无缝钢管,具有较高的尺寸精度和表面质量。
4. 热挤压法(Hot Extrusion):热挤压法适用于制造较大直径和较厚壁的无缝钢管。
在热挤压过程中,将坯料加热到高温,并通过挤压机将其挤出模具,形成无缝钢管。
5. 合拢法(Plug Rolling):合拢法主要用于制造较大直径和较厚壁的无缝钢管。
在合拢法中,将钢坯加热至特定温度后,通过合拢机的轧辊将其压制成管状。
这些工艺方法可以根据钢管的尺寸、材质和应用需求进行选择。
无论采用哪种工艺,都需要确保生产过程中的温度控制、机械加工和质量检验,以确保最终制造出高质量的无缝钢管。
无缝钢管的热轧工艺
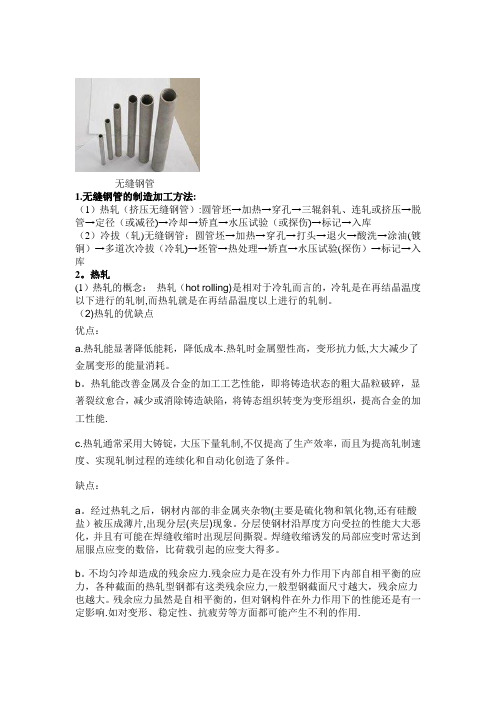
无缝钢管1.无缝钢管的制造加工方法:(1)热轧(挤压无缝钢管):圆管坯→加热→穿孔→三辊斜轧、连轧或挤压→脱管→定径(或减径)→冷却→矫直→水压试验(或探伤)→标记→入库(2)冷拔(轧)无缝钢管:圆管坯→加热→穿孔→打头→退火→酸洗→涂油(镀铜)→多道次冷拔(冷轧)→坯管→热处理→矫直→水压试验(探伤)→标记→入库2。
热轧(1)热轧的概念:热轧(hot rolling)是相对于冷轧而言的,冷轧是在再结晶温度以下进行的轧制,而热轧就是在再结晶温度以上进行的轧制。
(2)热轧的优缺点优点:a.热轧能显著降低能耗,降低成本.热轧时金属塑性高,变形抗力低,大大减少了金属变形的能量消耗。
b。
热轧能改善金属及合金的加工工艺性能,即将铸造状态的粗大晶粒破碎,显著裂纹愈合,减少或消除铸造缺陷,将铸态组织转变为变形组织,提高合金的加工性能.c.热轧通常采用大铸锭,大压下量轧制,不仅提高了生产效率,而且为提高轧制速度、实现轧制过程的连续化和自动化创造了条件。
缺点:a。
经过热轧之后,钢材内部的非金属夹杂物(主要是硫化物和氧化物,还有硅酸盐)被压成薄片,出现分层(夹层)现象。
分层使钢材沿厚度方向受拉的性能大大恶化,并且有可能在焊缝收缩时出现层间撕裂。
焊缝收缩诱发的局部应变时常达到屈服点应变的数倍,比荷载引起的应变大得多。
b。
不均匀冷却造成的残余应力.残余应力是在没有外力作用下内部自相平衡的应力,各种截面的热轧型钢都有这类残余应力,一般型钢截面尺寸越大,残余应力也越大。
残余应力虽然是自相平衡的,但对钢构件在外力作用下的性能还是有一定影响.如对变形、稳定性、抗疲劳等方面都可能产生不利的作用.c.热轧不能非常精确地控制产品所需的力学性能,热轧制品的组织和性能不能够均匀。
其强度指标低于冷作硬化制品,而高于完全退火制品;塑性指标高于冷作硬化制品,而低于完全退火制品。
d。
热轧产品厚度尺寸较难控制,控制精度相对较差;热轧制品的表面较冷轧制品粗糙Ra值一般在0.5~1.5μm。
热轧无缝钢管工艺流程
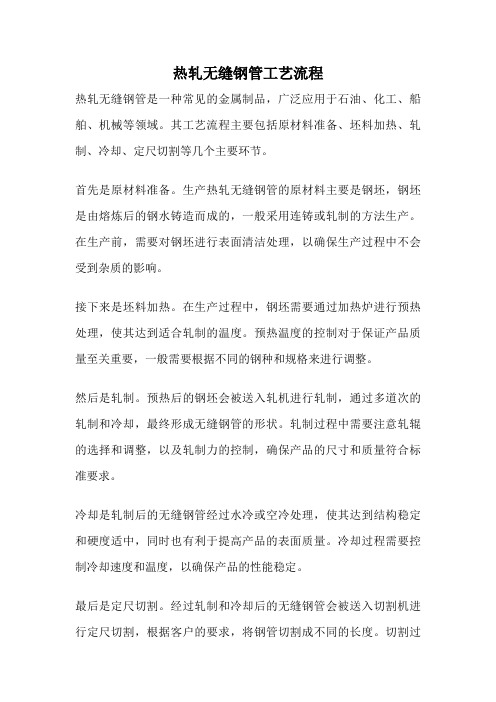
热轧无缝钢管工艺流程
热轧无缝钢管是一种常见的金属制品,广泛应用于石油、化工、船舶、机械等领域。
其工艺流程主要包括原材料准备、坯料加热、轧制、冷却、定尺切割等几个主要环节。
首先是原材料准备。
生产热轧无缝钢管的原材料主要是钢坯,钢坯是由熔炼后的钢水铸造而成的,一般采用连铸或轧制的方法生产。
在生产前,需要对钢坯进行表面清洁处理,以确保生产过程中不会受到杂质的影响。
接下来是坯料加热。
在生产过程中,钢坯需要通过加热炉进行预热处理,使其达到适合轧制的温度。
预热温度的控制对于保证产品质量至关重要,一般需要根据不同的钢种和规格来进行调整。
然后是轧制。
预热后的钢坯会被送入轧机进行轧制,通过多道次的轧制和冷却,最终形成无缝钢管的形状。
轧制过程中需要注意轧辊的选择和调整,以及轧制力的控制,确保产品的尺寸和质量符合标准要求。
冷却是轧制后的无缝钢管经过水冷或空冷处理,使其达到结构稳定和硬度适中,同时也有利于提高产品的表面质量。
冷却过程需要控制冷却速度和温度,以确保产品的性能稳定。
最后是定尺切割。
经过轧制和冷却后的无缝钢管会被送入切割机进行定尺切割,根据客户的要求,将钢管切割成不同的长度。
切割过
程中需要注意切割速度和刀具的选择,以保证切割的精度和效率。
总的来说,热轧无缝钢管的生产工艺流程复杂,需要各个环节的紧密配合和严格控制,才能生产出符合标准要求的高质量产品。
通过不断优化工艺流程和技术装备,可以提高生产效率,降低生产成本,满足市场需求,促进行业的发展。
热轧无缝钢管工艺流程

热轧无缝钢管工艺流程热轧无缝钢管工艺流程一、前处理前处理是热轧无缝钢管生产及质量控制中的一个重要环节,其目的是为了保证原料坯料的质量,从而确保管子的机械性能。
1.坯热坯热是生产热轧无缝钢管的必要环节,它的目的是使坯料内部的水分和挥发分子温度大于加工温度要求,从而改善坯料的机械性能和可加工性。
2.锻压锻压是指在热轧工艺过程中,利用锻压设备将坯料经过轧制、热处理和加工成一定形状及尺寸的钢管。
3.快速拉伸快速拉伸是指将原坯料经过快速拉伸成比较大尺寸的一块物体,以提高热轧无缝钢管表面质量,保证拉伸后形状稳定。
4.退火退火是指将钢管热处理到达一定温度,以保证钢管的机械性能和热处理性能,从而满足要求的尺寸及表面质量。
二、轧制轧制是热轧工艺的核心环节,它的目的是把原料坯料经过轧制,改变原料的形状及尺寸,从而实现按设计要求生产精细、均匀的无缝钢管。
1.轧制前准备轧制前准备是指根据订单确定尺寸,在轧辊或轧机上紧固轧制模具,确保轧制期间不发生变形。
2.轧制过程轧制过程是指将原料通过轧制机轧制成指定形状和尺寸的钢管,其中轧辊或轧机的转速要保持合理,以保证材料轧制和表面的厚度均匀。
3.轧制后处理轧制后处理是指对已轧制好的钢管进行处理,以提高其外观及性能。
通常包括超声波检测、表面抛丸处理、表面抛光等处理工艺。
三、热处理热处理是热轧无缝钢管生产及质量控制的重要环节,其目的是使材料达到设计要求的机械性能和热处理性能。
1.回火回火是指钢管经过加热到一定温度,然后在一定的时间内温度保持稳定,最后冷却到室温,以使材料获得特定的组织形态。
2.正火正火是指将钢管加热到一定温度,然后在一定时间内保持温度,最后冷却到室温,使钢管内部分子结构达到要求的机械性能。
3.空冷空冷是指在钢管热处理过程中,将钢管直接暴露在空气中,让钢管内部分子结构达到要求的机械性能。
四、检验检验是热轧无缝钢管生产及质量控制的重要环节,其目的是为了确保钢管符合生产要求,从而满足客户的需求。
轧管工艺流程简介

热轧无缝钢管生产线工艺流程一、天津钢管公司热轧无缝钢管轧机类别简介天津钢管公司拥有三种热轧无缝钢管生产线,每一种生产线对应着一种轧机,分别为MPM轧机,阿塞尔轧机和PQF轧机。
其中一套轧管生产线为φ250mm口径MPM轧机,三套轧管生产线为219mm 口径阿塞尔轧机,其余生产线为168mm、258mm和460mm口径PQF 轧机。
限动芯棒连轧管机,英文缩写MPM(即Multi-Stand Pipe Mill),是无缝钢管生产中的重要设备。
中国第一套限动芯棒连轧管机组,引进自意大利,于1992年在天津钢管集团股份有限公司投产。
经技术改造,天津钢管集团的Φ250mm限动芯棒连轧管机组已经由设计年产能力50万吨,扩大到现在的年产能力100万吨。
(注:天津钢管公司轧管厂Φ250MPM机组,引进的是意大利皮昂蒂公司的技术和设备。
该项目竣工投产时,时任意大利伊利集团总裁的普罗迪先生亲自前来剪彩。
2006年,作为意大利总理的普罗迪再次来到钢管公司)。
阿塞尔轧机由一个名叫W .J.Assel 的人于1932年发明。
天津钢管集团股份有限公司2005年新建的现代Φ219mm阿塞尔轧管机组,引进了德国SMS Meer公司近年来最新开发的阿塞尔轧制工艺技术和ABB公司最新的ACS6000SD传动控制系统。
二套轧管的168mm口径PQF(Premium Quality Finishing)轧机是世界上第一套PQF轧机,由SMS MEER公司设计,2003年底热试成功。
由于是一个新开发出的轧制技术,作为第一个使用该技术的天津钢管公司冒了很大的风险。
钢管公司与西马克公司签订合同的时候,提到了五年之内世界上的其他钢管公司不得上PQF轧机生产线,以保证自己对于该项技术的领先。
在以后的几年里。
天津钢管公司又陆续筹建了258mm口径和460mm口径PQF轧管生产线。
二、阿塞尔轧机、MPM轧机和PQF轧机的简单对比1.阿塞尔轧机:三辊式,单机架;轧制时,钢管及芯棒一起作螺旋运2.MPM轧机:两辊式,多机架;轧制时,钢管及芯棒一起作直线运3.PQF轧机:三辊式,多机架;轧制时,钢管及芯棒一起作直线运动。
- 1、下载文档前请自行甄别文档内容的完整性,平台不提供额外的编辑、内容补充、找答案等附加服务。
- 2、"仅部分预览"的文档,不可在线预览部分如存在完整性等问题,可反馈申请退款(可完整预览的文档不适用该条件!)。
- 3、如文档侵犯您的权益,请联系客服反馈,我们会尽快为您处理(人工客服工作时间:9:00-18:30)。
无缝钢管1.无缝钢管的制造加工方法:脱三辊斜轧、连轧或挤压→加热→穿孔→(1)热轧(挤压无缝钢管):圆管坯→入库标记水压试验(或探伤)→→→定径(或减径)→冷却→矫直→管(镀涂油酸洗→打头穿孔→→退火→(轧)(2)冷拔无缝钢管:圆管坯→加热→→→标记矫直热处理→→水压试验(探伤)铜)→多道次冷拔(冷轧)→坯管→入库2.热轧(1)热轧的概念:热轧(hot rolling)是相对于冷轧而言的,冷轧是在再结晶温度以下进行的轧制,而热轧就是在再结晶温度以上进行的轧制。
(2)热轧的优缺点优点:a.热轧能显著降低能耗,降低成本。
热轧时金属塑性高,变形抗力低,大大减少了金属变形的能量消耗。
b.热轧能改善金属及合金的加工工艺性能,即将铸造状态的粗大晶粒破碎,显著裂纹愈合,减少或消除铸造缺陷,将铸态组织转变为变形组织,提高合金的加工性能。
c.热轧通常采用大铸锭,大压下量轧制,不仅提高了生产效率,而且为提高轧制速度、实现轧制过程的连续化和自动化创造了条件。
缺点:a.经过热轧之后,钢材内部的非金属夹杂物(主要是硫化物和氧化物,还有硅酸盐)被压成薄片,出现分层(夹层)现象。
分层使钢材沿厚度方向受拉的性能大大恶化,并且有可能在焊缝收缩时出现层间撕裂。
焊缝收缩诱发的局部应变时常达到屈服点应变的数倍,比荷载引起的应变大得多。
b.不均匀冷却造成的残余应力。
残余应力是在没有外力作用下内部自相平衡的应力,各种截面的热轧型钢都有这类残余应力,一般型钢截面尺寸越大,残余应力也越大。
残余应力虽然是自相平衡的,但对钢构件在外力作用下的性能还是有一定影响。
如对变形、稳定性、抗疲劳等方面都可能产生不利的作用。
.热轧制品的组织和性能不能够c.热轧不能非常精确地控制产品所需的力学性能,塑性指标高于冷作均匀。
其强度指标低于冷作硬化制品,而高于完全退火制品; 硬化制品,而低于完全退火制品。
热轧制品的表面较冷轧制品d.热轧产品厚度尺寸较难控制,控制精度相对较差; ~1.5μm。
因此,热轧产品一般多作为冷轧加工的坯料。
粗糙Ra值一般在0.53.轧机简介600mm~8mm成卷热轧带钢的工艺。
带钢宽度在带钢热轧机上生产厚度为1.2年600mm的称为宽带钢。
第一台带钢热连轧机于1905以下称为窄带钢;超过200mm的带钢。
在美国投产,生产宽年以前热带钢热轧机的技术经济指标优越,发展很快。
在工业发达国家,1950左右。
热轧带钢的原年代已达50%轧宽带钢的产量约占钢材总产量的25%,70 。
130料是连铸板坯或初轧板坯,厚度为~300mm的带钢,并卷成钢卷。
25.4mm,送到轧机上轧成厚1.00~板坯在加热炉中加热后其主要用途是作冷轧带钢、不锈钢和硅钢等。
轧制的钢种有普通碳钢、低合金钢、焊管、冷弯和焊接型钢的原料;或用于制作各种结构件、容器等。
轧机组成:带钢热轧机由粗轧机和精轧机组成。
粗轧机组分半连续式、3/4连续式和全连续式三种:①半连续式有一台破鳞(去掉氧化铁皮)机架和1台带有立辊的可逆式机架;②3/4连续式则除上述机架外,还有2台串列连续布置机架;③全连续式由6~7台机架组成。
精轧机组均由5~7台连续布置的机架和卷取机组成。
带钢热轧机按轧辊辊身长度命名,辊身长度在914mm以上的称为宽带钢轧机。
精轧机工作辊辊身长度为1700mm的,称为1700mm带钢热轧机,这种轧机能生产1550mm宽的带钢卷。
带钢热轧按产品宽度和生产工艺有四种方式:宽带钢热连轧、宽带钢可逆式热轧、窄带钢热连轧以及用行星轧机热轧带钢。
4.减径机的工艺原理及主要问题人们在无缝钢管生产的三大机组——穿孔机组、定减径机组中,轧管机组、新型顶管机顶管机组、一直十分关注轧管机的研究,先后开发出自动轧管机组、MPMMM)、三辊轧管机组、连轧管机组(包括浮动芯棒、限动芯棒组(CPE轧管机组、改进型三辊轧管机组。
但对、AccuRoll 和半浮动芯棒连轧管机组等)而定减径机一直使用二年代初才提出菌式穿孔机。
世纪于穿孔机组,仅在2080新型三辊世纪辊式和三辊式,直到2090年代初才提出三辊可调式定径机技术。
它可调式定径机技术是为满足现代钢管生产高效、优质、低耗的要求而开发的,的开发成功也为无缝钢管的生产注入新的活力。
张力减径机技术的发展采用适当的孔型系使张减工艺主要特点是边连续多机架二辊或三辊无芯棒纵轧,毛管外径减缩,通过机架系列中轧辊速比的调节获得预定的壁厚变化。
年代无缝管机组被美国和西欧所用,这时的张减机都是二辊式,到了4020世纪年代,西德曼乃斯曼公司成功地奕用了三辊式张力减径机,从而代替世纪2050 了二辊式。
张力减径机的作用将钢管轧成一定要求定径的目的是在较小的总减径率和小的单机减径率条件下,直径经过定径后的钢管,的尺寸精度和真圆度,并进一步提高钢管外表面质量。
偏差较小,椭圆度较小,直度较好,表面光洁。
定径机工作机架数目较少,一般,增加定径机架数可扩大产品规格,给生产带到为3--12架总减径率约为3%7% 来方便,新设计车间定径机架数一般都较多。
静静除具有60mm直径小于的钢管,很难由轧管机轧成,而需要经过减径工序。
以实现大管料生产小口径钢管的目定径相同的作用外,还要求有较大的减径率,架。
减径5到24的,也可用来生产异型管。
减径机的机架数一般较多,一般为机有两种形式:)一般微张力减径机,作用就是减缩管径,生产机组不能轧制或加工起来很1(不经济的规格;)张力减径机,作用不但减缩管径的外径,而且可以减小钢管的壁厚,既减(2提高减径率轧制径又减壁,使机组产品进一步扩大;并可适当加大来料的重量,更长的产品。
4.1张力减径机的形式定径机的形式很多,按辊数可分为二辊、三辊、四辊式定径机;按轧制方式分为斜轧回转斜轧定径机一般多配在三辊斜轧管机组中。
纵轧定径机和斜轧定径机。
定径机的构造与二辊或三辊斜轧穿孔机相似,只是辊型不同。
与纵轧定径相比,斜轧定径的钢管外径精度高,椭圆度小,更换规格品种方便,不需要换辊,只要调整轧辊间距即可;缺点是生产率低。
减径机的形式很多,按辊数可分为二辊、三辊、四辊式减径机。
按机架张力大小可分为两种形式:)微张力减径机,减径过程中壁厚增加,横截面上的壁厚均匀性恶化,所以(1 50%;到总减径率限制在40%)张力减径机,减径时机架间存在张力,使得缩径的同时减壁,进一步扩大(2生产产品的规格范围,横截面壁厚均匀性也比同样减径率下的微张力减径效果,总延伸系数可40%35%75%好。
总减径率最大可达到80%,减壁量一般可达到14达9以上,机架数一般可达机架。
钢管定径、减径的工艺原理)压扁,开始咬入时由于孔型形状与毛管横剖面不相适应造成局部点接触,1(特点是只有断面形状的变化,压扁便首先在此开始,周长、薄厚无变化,无延伸。
)减径,随着压扁的发展孔型壁与轧件接触面不断增加,至一定程度后在径(2壁厚有所增向接触应力作用下开始减径。
特点是平均直径减小,毛管出现延伸,开始减。
因为孔型开口处金属沿径向流动的阻力较小,这里的壁厚较槽底为大,出现横剖面上的壁厚不均。
对于张力减径,不但减径,而且减壁,大大延伸。
张力减径的优点、缺点4.21 张力减径的优点:)可以大大地减少减径前的钢管规格,提高轧管机组生产效率。
轧管机组只(1 生产少数规格,而经张力减径后可以得到各种规格的成品钢管。
)可以减少前部工序生产工具的数量、提高机组作业率。
由于管坯和荒管规(2格的减少,工具、备品备件和更换时间大大减少,生产更加稳定,从而增加了作业时间。
,通过张力减径可以(3)可以扩大品种规格。
减径量高达80%45%,减壁量达直接生产小口径无缝钢管。
(165m,可以生产长达的钢管。
4)张力减径的延伸系数为6--9 张力减径的缺点:张力减径的缺点是张力减径轧制中,钢管中间部分的管壁受到张力作用而减壁,出现增厚段,这增厚头尾两端的管壁由于受不到张力或受到的张力由小变大,所以要求一般进入张力减径机的管需切掉,增加了头尾的损失,部分超过公差,子来料长度要足够长,在经济上才合理。
管理计算机和过程控制机的投入使用,得以实现,这样能在更大程度上满足工艺的要使张力减径机管端增厚控制CEC求,为张力减径生产的高产、优质、低消耗开阔了更加广阔的前景。
在广泛应用即可满足连轧管机的产量要的连轧管机后面配置一台张力减径机作为成型机组,这样用一种或两种连轧毛管即可生产出几百种不求,又可解决产品规格的要求,型同规格的热轧管。
这标志着钢管生产的最新发展方向,使无缝钢管生产实现大张力减径机已经在几乎各类轧管机组和中小型焊管机组上化、高速化和连续化。
得到广泛的应用。
4.2:三辊定径、减径机减径与二辊定径减径机相比)机架间距;三辊式定径减径机机架间距比二辊式定径、减径机间距小,但(1 机械结构复杂。
)单机架变形量;与二辊定径、减径机相比,三辊式定径、减径机每个轧辊(2 轧制变形量小,管端增厚长度小、切头切尾量少、金属损耗少。
、减径机轧辊孔型周边的速度差小,从而)钢管质量:三辊式比二棍式定径(3沿周向每个轧辊型与钢管接触弧长较小,轧辊较小。
减少轧辊与钢管的相对滑动,从而可以减少金属变形时的流动趋于均匀,这使周向上所受的变形力比较均匀,横向壁厚的不均匀程度。
三辊式定径、减径机与二辊式定径、减径机相比,生产的钢管外径圆度较好。
°,使轧机结构简化,便于布60)机架布置:三辊式定径、减径机轧辊交叉(4 置。
)张力的建立:三辊式定径、减径机轧辊数目多,则轧制时对钢管的曳入性(5 能较好,可在较短的咬入钢管长度上建立足够的张力。
)可调整性:二辊式定径、减径机容易实现在线孔型尺寸的调整,以满足标(6减径机一般不能实现在线孔型尺寸准、规范对外径偏差的要求,而三辊式定径、的调整。
现在广泛采用的是三辊式径、减径机。
:张力径机的孔型4.3即内主要考虑的因素是不要产生容易出现的几种轧制缺陷,在张减孔型设计时,多边形,壁厚不均,外表面纵向轧痕及外表面折叠,根据经验,一般认为轧制缺的增大,a 直径比(s/d),总减径率P∑孔型椭圆度陷支下面趋势有关随着壁厚/∑的增大壁厚不均也增大,轧制薄壁管金P内多边形的趋势增加,随着单架减径薄壁管应在椭圆孔型中轧制,由此人们得出结论:属容易挤入辊缝形成纵向轧痕,时,必须用圆孔)所谓椭圆孔型系9%~12%厚壁管应在圆孔型中轧制(在s/d,<0。
,而圆孔型系指指ai-bi-1>0ai-bi-1孔型的几何参数有:A—孔型高度;B—孔型宽度;C—孔型顶部圆弧半径22/4A按下式计算:R=A+B22/4A E=B-A—偏心距,按下式计算:E 毫米;4~10)一般1/15Dc—圆角半径(≈R.)Dc—平均直径(=A+B/2 2~5毫米。
△—轧辊间隙(=1/2r)一般一般都是采用分配的方法,(减径率),为了决定孔型尺寸,必须首先确定变形量为了保证第一架顺除了第一架和最后两架外,其他机架中直径压下量都取相等,为得到圆利咬入和考虑来管直径的波动,第一架压下量采用平均压下量的一半,形管,成品前机架压下量也取平均压下量的一半,而在成品机架中(最后一架)一般不给压下量。