板形的概念和分类
板形控制技术--板型

2020/2/4
2
2020/2/4
3
1.1.1 板形的描述
如图1.1所示建立坐标系, x为轧件宽
度方向(操作侧指向传动侧), y为
轧件运行方向, z为轧件厚度方向。
记来料板廓为 Hf(x) ,轧后带材板廓
为hf(x),记带材的浪形函数为 W(x,y)
。
2020/2/4
4
2020/2/4
5
? 凸度:
板带材产生翘曲,实质上是横向各点的不均匀延伸造 成的,因而表示板形的一个简单方法是取横向不同位置的 相对长度差表示板形,即
2020/2/4
14
式中 ε0、ε1——分别为来料和轧后的相对长度差; L 0p、L1p ——分别为来料和轧后平均长度;
ΔL 0b 、 ΔL 1b —— 分别为来料和轧后长度差,可用下式表 示:
22
? 宽度方向翘曲
板带材以其纵截面的x轴为中性轴产生的弯 曲变形。又称横向弯曲或C瓢曲。在轧制过 程中,轧辊承受轧制力发生弹性变形,工 作辊出现挠度,板带材会出现横向厚差。 进行辊型设计时要确定合理的轧辊原始凸 度。考虑到轧辊磨削方便。四辊轧机轧辊 原始凸度设计应用较广泛的一种方法是一 个工作辊有凸度,另一个工作辊及两个支 撑辊都是圆柱形。
2020/2/4
7
式中: be——带材边缘位置,一般取 be = 5 mm
EM —— 传动侧边部减薄量; EO —— 操作侧边部减薄量。 ? 局部凸起量
指横切面上局部范围内的厚度凸起。
2020/2/4
8
?平直度
定义:平直度是不平坦程度的定量表示。
在板带钢生产过程中,由于轧制力沿轧辊轴 向分布不均匀、轧辊热膨胀不均匀、轧辊磨损不 均匀、带钢横向温度分布不均匀,造成带钢各处 长度不一致,带钢较长的部分波浪起伏,即平时 所说的浪形,浪形为不可恢复变形。
3-4 板凸度和板平直度理论

Δ C p = C p 2 − C p1
(4-23)
根据比例凸度定义有:
C p2
Ch hc − he = = h h
h、H
则有:
CH H c − H e = C p1 = H H
分别用 he、He 代替上式中的
hc − he H c − H e hc H c ΔC p = − = − he He he H e
ΔCp
⎛h⎞ −80 ⎜ ⎟ ⎝B⎠
⎛h⎞ 40 ⎜ ⎟ ⎝B⎠
1.86
1.86
⎛h⎞ < ΔC p < 40 ⎜ ⎟ ⎝B⎠
λ
1.86
h B
死区 F1 F2 F3 F4 F5
1.86
F6
F7
中浪
边浪
⎛h⎞ −80 ⎜ ⎟ ⎝B⎠
ΔCp
4.2 影响板形和板凸度的因素
金属在轧辊作用下经过一系列变形过程轧成需要的板带材。最终产品 的板形受到许多因素的影响,总括起来,这些因素可以分为内因(金属 本性)和外因(轧制条件)两个方面。 金属本身的物理性能(例如硬化特性、变形抗力)直接影响轧制力的 大小,因而与板形密切相关。金属的几何特性,特别是板材的宽厚比、 原料板凸度是影响板形的另一个重要因素。 轧制条件的影响更为复杂,它包括更广泛的内容。凡是能影响轧制压 力及轧辊凸度的因素(例如摩擦条件、轧辊直径、张力、轧制速度、弯 辊力、磨损等)和能改变轧辊间接触压力分布的因素(例如轧辊外形、 初始轧辊凸度)都可以影响板形。
一般所指的板凸度,严格来说,是针对除去边部减薄区以 外的部分。边部厚度是以接近边部但又在边部减薄区以外的一 点的厚度来代表,板凸度即为板中心处的厚度与边部代表点处 的厚度之差。
中心板凸度 :
《板形控制方法》课件

当轧制力增大时,轧机的弹塑性 变形程度增加,轧材的延伸率增 大,从而使得板材的横向厚度差 减小,板形趋向于平坦。
重要因素
•·
然而,过大的轧制力可能导致轧 机负荷过大,影响轧机的稳定性 和寿命,同时也会使得轧材表面 粗糙度增加,影响产品质量。
轧制温度对板形的影响
关键因素
同时,轧材温度的均匀性也会影响板形 的质量。温度不均匀会导致轧材的变形 不均匀,进一步影响板形的平整度。
当轧材温度升高时,其变形抗力减小, 轧机的功率消耗降低,有利于提高轧机 的生产效率。
轧制温度是影响板形的关键因素之一。 在轧制过程中,轧材的温度变化会影响 其变形抗力和轧机的功率消耗。
•·
轧制速度对板形的影响
间接影响
轧制速度对板形的影
•·
响是间接的,主要通
过影响轧机的振动特
性和轧材的变形过程
来影响板形。
02
板形是衡量板带材质量的一项重 要指标,对于后续加工和使用具 有重要影响。
板形的重要性
良好的板形可以提高板带材的平直度 、表面质量和整体性能,从而满足各 种加工和使用的需求。
不良的板形会导致板带材出现波浪、 翘曲、瓢曲等缺陷,影响其使用性能 和外观质量。
板形控制技术的发展历程
1
早期的板形控制技术主要依靠经验和实践,通过 调整轧机参数和操作技巧来控制板形。
详细描述
通过机器学习和人工智能技术,可以对板形控制过程中的数据进行实时分析和处理,实 现更加精准和智能的控制效果。同时,利用深度学习等技术,可以对板形控制算法进行
优化和改进,进一步提高控制精度和效率。
多目标优化与协同控制在板形控制中的研究
总结词
多目标优化和协同控制是当前控制领域 研究的热点问题,将其应用于板形控制 中具有重要的意义。
板形理论ppt

式中: Kw—工作辊磨损系数;Dw—工作辊直径; LS—该道次轧制带钢的长度; L—工作辊压扁接触弧长; pB—单位宽度轧制力; KS—工作辊磨损指数;vt—边部磨损倍率。
RAL NEU
RAL
(2) 工作辊磨损的计算
工作辊8个特定磨损点将工作辊辊面分为9个磨损 段。首先确定8个特定点的磨损量;然后沿工作辊 辊面全长共分301个磨损点。根据各磨损点所处磨 损段的不同,进行工作辊各点的磨损插值计算。
RAL NEU
RAL
板形缺陷
1 边浪 2 中浪 3 单边浪 4 二肋浪 5 复合浪
4.1 板形缺陷
RAL NEU
RAL
板形的度量
板形度量的目的: 定量地表示板形,既是生产中衡量板形质量的需要, 也是研究板形问题和实现板形自动控制的前提条件。 因此,人们依据各自不同的研究角度及不同的板形控 制思想,采取不同的方式定量地描述板形。
RAL
板凸度
与板形密切相关的另一个重要的概念是所谓的板凸 度。除板带边部外,90%的中间带材断面大致具有二次曲 线的特征,而在接近边部处,厚度突然迅速减小,这种现 象称为边部减薄。
he2 w2
he1 w1 w
hc w1
he1 w
he2 w2
带钢宽度方向厚度分布
RAL NEU
RAL
影响板形和板凸度的因素
金属在轧辊作用下经过一系列变形过程轧成需要的板带材。最终 产品的板形受到许多因素的影响,总括起来,这些因素可以分为内因 (金属本性)和外因(轧制条件)两个方面。 金属本身的物理性能(例如硬化特性、变形抗力)直接影响轧制 力的大小,因而与板形密切相关。金属的几何特性,特别是板材的宽 厚比、原料板凸度是影响板形的另一个重要因素。 轧制条件的影响更为复杂,它包括更广泛的内容。凡是能影响轧 制压力及轧辊凸度的因素(例如摩擦条件、轧辊直径、张力、轧制速 度、弯辊力、磨损等)和能改变轧辊间接触压力分布的因素(例如辊 形、初始轧辊凸度)都可以影响板形。
轧制理论
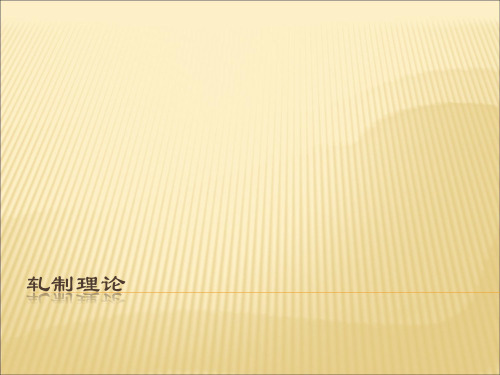
二、轧件厚度波动的原因及厚度控制的基本原理
中 厚 板 板 形 控 制 技 术
中厚钢板板形一直是困扰轧钢工作者的难题。生产初期采用烫辊、原始辊型以及加大轧 辊直径等办法,但收效甚微;之后增加轧机刚度、完善辊系,减少轧辊挠度、配臵弯辊装臵 及附设立辊轧机,已取得明显的效果;进而采用了AGC、计算机控制、BBR法、MSA法、 HCW轧机、VC辊、阶梯辊、PC轧机及CVC轧机等板形控制技术,将中厚钢板板形控制技术提 高到更高水平。 当前,为了提高中厚钢板的尺寸精度、成材率及其性能的均匀性、扩大钢板规格与品种、 减少精整工序,板形控制已成为中厚钢板生产中一项不可缺少的技术。 板形控制也是一项钢板主体三维形状的控制技术。最佳目标是生产出尺寸偏差非常小、 切头尾和切边极少、矩形、近似矩形及齐边(不切边或铣边)的平直钢板,并借此技术可以扩 大产品,生产出楔形(长度方向上不同厚度倾斜)、梯形(宽度方向上不同厚度倾 斜)、圆形、厚、异宽、防挽及带肋等各种异形钢板。 板形控制目标: (1)纵向厚度偏差,不大于±0.08mm; (2)横向厚度偏差, 不大于± 0.05mm; (3)不平直度,不大于0.04mm; (4)头尾异形总长,不大于50mm; (5)边部余量,不大于20mm; (6)镰刀弯,不大于1.5mm/全长; (7)宽度偏差,力0一+2mm; (8)长度偏差,不大于+ 0.02%全长; (9)平面识别,不大于+2mm; (10)成材率, 达96%以上。
二、轧件厚度波动的原因及厚度控制的基本原理
中 厚 板 板 形 控 制 技 术
纵向板厚控制 钢板轧制随着定尺长度的增大、纵向厚差的减小、板厚尺寸进级范围的缩小、异形板 轧制及平面板形控制的需要,因此,纵向板厚控制越来越重视,已成为现代化中厚板轧机 板形控制所必不可缺的重要手段。 随着中厚板轧机轧制速度的提高,轧制过程中坯料的厚度偏差、轧件头尾温差与黑印、 原料的强度与硬度不同、轧机刚度的变化、轧辊磨损、压扁、挠度成偏心、压下装臵调整 与检测的偏差等诸多因素的影响,钢板纵向板厚与偏差是不断变化的。 目前,国内外中厚板轧机上已普遍采用AGC技术来对纵向板厚进行控制。 AGC是根据 材料变形抗力或入口侧厚度偏差来控制压下量变化,使长度方向厚度恒定或很少变动。作 为厚度基础的厚度计AGC是以板厚计算公式计算出轧制中板厚来控制AGC 。 横向板厚控制 中厚板的横向板形控制,也叫凸度板形控制。 由于中厚板凸度的存在,板厚偏差值增大。特别是对桥梁和多层容器的影响最大,容 易产生弯曲应力和剪切应力,降低了工作应力与安全系数。另外,当一块宽板分割为两条 板时,造成钢板两边厚度不一致,也合影响用户的使用。因此,现代中厚板生产已将减少 凸度提高到非常高的地位,也是提高经济效益的一项重要措施。中厚板凸度是由轧辊的挠 度、不均匀磨损、温度变化、辊型及偏心等因素造成的。另外,轧机刚度和轧件温差的影 响也很大。其中轧辊产生挠度对钢板凸度的影响最为明显。因此,许多减少钢板凸度的措 施都是从减少轧辊挠度出发的。早期采用过烫辊的办法,目前,采用补偿与修正的措施有 加大支撑辊及机架立柱断面、合理设计机架与辊系、原始辊型、由宽至窄板的程序轧制、 弯工作辊、弯支撑辊,同时弯工作辊和支撑辊、阶梯辊、VC辊、HCW轧机、PC轧机及CVC 轧机等。
板形理论基础

板形理论基础孙蓟泉北京科技大学板形研究的意义随着汽车、机械行业的发展,热轧带钢用户对热轧带钢的尺寸精度和组织性能提出了更高的要求;热轧板形直接影响冷轧板形质量;后步工序常要求有微小浪形,如罩式退火炉希望来料为微双边浪的板形状态,而有些厂家的连续退火希望对应微中浪的应力状态;板形影响到镀锌层厚度的均匀性,为保证质量要求板形误差越小越好;从后续深加工上看,需要板形优良,如板形好坏影响板材的深冲性能等,如汽车板、家电板等。
带钢横截面轮廓楔形h e1-h e2中心凸度C h =h c -(h e1+h e2)/2 边部减薄h e1-h e3比例凸度C p =C h /h c *100%局部高点和局部低点h e1h e2h e4h e3h c板形及其度量板形所谓板形直观地说是指板材的翘曲程度;其实质是指带钢内部残余应力的分布。
板形不良:带钢中存在残余内应力称为板形不良。
潜在板形不良:带钢中存在残余内应力,但不足以引起带钢翘曲,称为潜在板形不良。
表观板形不良:带钢中存在残余内应力足够大,以致引起带钢翘曲,则称为表观的板形不良。
平直度热轧成品带钢平直度一般指边浪和中浪,并以二次浪为主要控制指标,对于宽度大而厚度很薄的情况才要适当考虑四次浪a-侧弯;b-中浪;c-边浪;d-小边浪;e-小中浪;f-小偏浪带钢的应力分布承载辊缝轧件残力应力 理论分布板形仪显示 应力分布生成浪形双侧边浪中浪四分之一浪边中复合浪单侧边浪+σ0 -σ-σ 0 +σ板形的度量板形度量的目的:定量地表示板形,既是生产中衡量板形质量的需要,也是研究板形问题和实现板形自动控制的前提条件。
因此,人们依据各自不同的研究角度及不同的板形控制思想,采取不同的方式定量地描述板形。
¾相对长度差表示法¾波形表示法¾张力差表示法¾带材断面形状的多项式表示法¾厚度相对变化量差表示法相对长度差表示的板形翘曲带钢(a)及其分割(b)R VaL VLΔLb这是一种比较简单的表示板形的方法,就是取横向上不同点的相对延伸差D L /L 来表示板形。
轧钢板形讲解
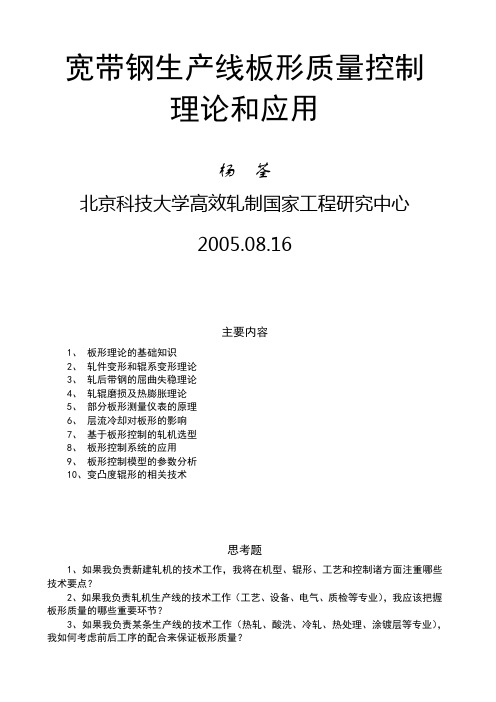
板形控制的基本理论包含三个方面相互关联的理论体系,即:
轧件三维弹塑性变形理论。
辊系变形理论(弹性变形、热变形和磨损变形)。
轧后带钢失稳理论。
根据这三个方面的理论和实验所建立的数学模型也是相互联系、密不可分的统一体。轧件弹塑性三维变形为辊系弹性变形模型提供轧制压力的横向分布,同时为带钢失稳判别模型提供前张力的横向分布,辊系变形模型为轧件变形模型提供有载辊缝横向分布。三者关系如图1.5所示。
2.1.1解析法
解析法是三维轧制理论研究的开端,其物理模型仍然是构建于Karman或Orown的力平衡方程式上,只不过三维轧制理论在平面变形理论基础之上又添加了一个板宽方向(轧辊轴向)的平衡方程式,再结合三个主应力的塑性条件进行求解。柳本左门应用解析法给出了热轧问题的近似解析解。柳本在计算中采用了以下假设:
自20世纪60年代以来,人们对构成板形理论体系的三个模型进行了大量的研究。辊系弹性变形模型的研究起步较早,发展至今日已形成相对完善的理论体系,无论从计算精度及计算效率方面均可满足工程应用的要求;由于轧件变形特性的高度非线性,轧件的弹塑性变形计算较辊系的弹性变形计算复杂得多,虽然借助有限元法方法也能获得较好的计算精度,但计算量大,计算时间过长,不具有工程应用 价值;相对来说,对于轧后带钢失稳判别模型的研究较少。
图1.2带钢的平坦度
图1.3带钢的应力分布
1.1.2.3带钢的张力分布
带钢的张力分布可以回归为多项式形式:
σ(x) = A0+A1x+A2x2+A4x4+…(1-8)
式中σ(x)-带钢横向张力分布;
A0-带钢横向张力分布平均值;
A1-带钢横向张力分布的线性不对称分量;
热轧带钢板形控制

热轧带钢板形控制一、 板形基本概念板形是指成品带钢的断面形状和平直度两项指标,二者都是标志带钢质量的重要指标,并且在生产中有着密不可分的联系。
1、断面形状断面形状是带钢厚度沿板宽方向的分布情况,如图1所示。
在实际生产中,以凸度来简单表示,如下式:e c h h -=δ式中:δ——带钢凸度。
h c ——带钢中部厚度。
h e ——带钢两边厚度平均值(由于存在“边部减薄”现象,一般取距带钢边部25~50mm 处的厚度作为边部厚度)。
2、平直度平直度指标表示带钢是否存在翘曲及翘曲的程度,即浪形,见图2。
可用以下几种方法表示:(1) 相对波峰值表示法%1000⨯=L hλ式中:h 、L 0——分别表示浪高和浪距。
(2) 相对长度差表示法相对长度差表示波浪部分的曲线长度对于平直部分标准长度的相对增长量。
可用下式表示:I L L x L x 5010)()(⨯-=ε 式中:L(x)——宽度方向任一点x 上的波浪弧长I ——表示平直度的单位,1I 单位相当于1m 长的带材中有10μm 的相对长度差。
图1 带钢横断面形状图2 带钢浪形示意图另外,还有张力差表示法、向量表示法和带钢断面的多项式表示法等。
二、 板形控制原理 1、凸度控制在带钢轧制过程中,其断面形状最终将取决于两工作辊间的辊缝形状。
因为辊缝形状由工作辊辊型曲线决定,所以,凡是影响工作辊辊型曲线形状的因素都会改变带钢的断面形状。
影响带钢凸度的因素有:(1) 工作辊原始凸度; (2) 工作辊热凸度; (3) 工作辊磨损凸度;(4) 工作辊在轧制力及弯辊力作用下产生的弯曲挠度;(5) 工作辊在不均匀分布的轧制力作用下沿板宽方向产生的弹性压扁。
控制带钢凸度(即控制工作辊辊缝形状)的方法因轧机的技术装备水平不同而不同。
(1) 以原始辊型设计为基础,合理地编制轧制规程。
通过合理分配各架轧机的负荷,来补偿因轧辊热凸度、磨损凸度和弹性变形而带来的辊缝形状的改变。
板形与板形控制基础知识
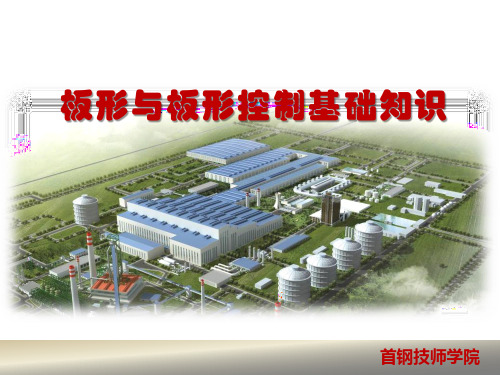
的分布,以达到控制辊型的目的。
控制手段是对沿辊身长度方向的冷却液流量进行分段控制,这种控制 方法见效比较慢(原因是轧辊的热容量比较大),难以满足高速轧制的需
要,只能作为一种其它板形控制的辅助手段。
首钢技师学院
板形与板形控制基础知识
② 液压弯辊控制法。
液压弯辊利用液压缸施加在轧辊辊颈处的压力使轧辊辊身产生一个人为的附
凸辊型
凹辊缝
凹断面
首钢技师学院
板形与板形控制基础知识
⑵ 板形控制的基本原理 设轧制前板带边缘的厚度为h1,轧前板凸度量(或称厚度差)为c1, 轧后板凸度量为c2,所以轧前中间的厚度为h1+ c1,轧制后板带横断面上的 边缘厚度和中间厚度分别为h2和h2+c2 。
h2 h1+ c1 h2+c2 h1
对于普通的四辊轧机,在工 作辊与钢板不接触的部分,受到 支撑辊的悬臂弯曲力的压迫,产 生比较大的附加挠度,其大小与 钢板的宽度成反比,若能根据钢 板的宽度调整支撑辊的有效长度, 就能减小工作辊的附加挠度。
首钢技师学院
板形与板形控制基础知识
HC 轧机具有以下特点: a 具有良好的板凸度和板形控制能力。由于它的中间辊可以轴向移动,
CVC 轧机示意图
PC 轧机示意图
VC 轧机示意图
首钢技师学院
板形与板形控制基础知识
⑶ 板形控制轧机 ① HC轧机 HC 轧机起源于上世纪 70 年代的冷轧带钢,由日立与新日铁联合研制,其基 本思路是:通过改变支撑辊与工作辊的接触状况来改变工作辊的挠度,特别是能有 效的减轻支撑辊与工作辊之间的有害接触,进而改善板型。 结构特点:在支承辊与工作辊之间安装一对可相反轴向移动的中间辊而成为 六辊轧机。
冷轧铝板带材生产的板形控制

冷轧铝板带材生产的板形控制 Ξ胥福顺1,李 全1,杨 钢2,杨 鹏1(1.云南铝业股份有限公司,云南 昆明 650502,2.云南冶金集团总公司,云南 昆明 650051) 摘 要:阐述了冷轧板形的定义和控制方法,研究了铝铸轧坯料板形、轧制油、轧辊粗度、道次加工率的分配、张力分配、弯辊控制、热凸度等因素对冷板板形的影响机理和相应的控制方法,通过控制达到改善冷轧板形的目的。
关键词:冷轧铝板;板形;影响因素;控制方法中图分类号:TG33518 文献标识码:A 文章编号:1006-0308(2006)01-0053-03Plate Shape Control in Cold R olling of Aluminum SheetsX U Fu-shun1,LI Quan1,Y ANG G ang2,Y ANG Peng1(1.Y unnan Aluminium C o.Lte.,K unming,Y unnan650502,China2.Y unnan Metallurgy G roup C o.,K unming,Y unnan650051,China)ABSTRACT:The controlling methods and definition of plate shape of rolling alum inum are described.The in fluences of factors such as plate shape of blank,rolling oil,roughness of roller,distribute of process rate on rolling pass,tension distribution,roller bending,thermal crown and corresponding control methods are studied so as to im prove the plate shape.KE YWOR DS:cold rolling alum inum plate;plate shape;in fluential factors;control methods冷轧铝板带材是建筑装饰板、PS印刷版、制罐板、铝箔等的上游产品,其板形质量好坏直接影响产品的档次,影响使用效果,特别是一些要求较高的行业,如PS印刷版、制罐板对板形质量的要求更严格,近年来铝板带应用范围的扩大和不断增强的质量需求对板形控制提出了更高的要求。
CVC六辊轧机板形控制原理及冷轧带钢板形的概念解读
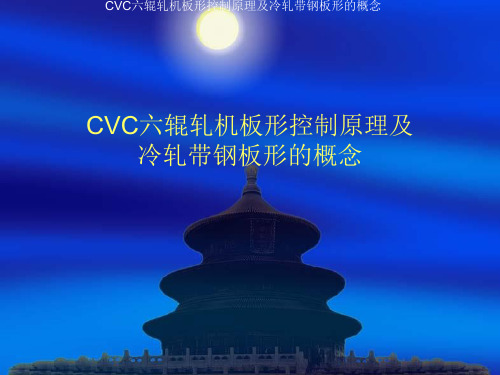
成品平直度 综 合 最 佳
成品横断面
24
CVC六辊轧机板形控制原理及冷轧带钢板形的概念
一、板形控制理论
⑤ 板形良好(带材失稳)判别模型——判断带材是否失稳
基本原理 最小势能原理
求解方法 经典特征值求解
CVC六辊轧机板形控制原理及冷轧带钢板形的概念
一、板形控制理论
⑥ 板形模式识别模型1——根据残余应力的分布及大小判断
PC四辊,HC轧机,UC轧机,UCMW轧机等
21
CVC六辊轧机板形控制原理及冷轧带钢板形的概念
一、板形控制理论
③ 轧件与轧辊温度场模型——计算带材与轧辊温度场 带材温度场
互为边界条件
轧辊温度场
基本方法 有限差分法:快速、稳定 基本原理
能量守恒原理 热传导方程
T 2T 1 T 2T c ( 2 ) t r r z 2 r
y2 ( x) a0 a1 (L x) a2 (L x) 2 a3 (L x) 3 y2 ( x) a0 a1 (L x) a2 (L x)2 a3 (L x)3 a4 (L x)4 a5 (L x)5
CVC六辊轧机板形控制原理及冷轧带钢板形的概念
a2 (2sm L)Cm (2sm L)Cn 2 L2 sm
2
R Rt (B0 ) Rt (0) B0 (a1 a2 B0 a3 B0 )
a1 与辊缝凸度无关,为了减小带钢参与应力 及改善带钢质量,实际生产中可以用辊径差 最小作为设计依据
解得:a1
1 2 3 (R a2 B0 a3 B0 ) B0 a0 R ( ) t 0
板凸度和板形控制
改变负载辊缝的形状
中厚板板形控制

4板形控制4.1 板形的基本概念板形是指成品带钢断面形状和平直度两项指标,通常说的板形控制的实质是对承载辊缝的控制,断面形状和平直度是两项独立存在的指标,但相互存在着密切关系。
板形可以分为视在板形和潜在板形两类。
所谓的视在板形是指在轧后状态下即可用肉眼辨别的板形;潜在板形是指在轧制后不能立即发现,而是在后部加工时才会暴露。
例如在有时从轧机出来的板子看起来并无浪瓢,但一经纵剪后,即出现旁弯和浪皱,于是便称这种轧后板材具有潜在板形缺陷。
图4-1给出了断面厚度分布的实例,轧出的板材断面呈鼓肚形,有时带楔形后者其他的不规则形状。
这种断面厚度差主要来自不均匀的工作辊缝。
如果不考虑轧件在脱离轧辊后所产生的弹性回复,则可认为实际的板材断面后度差即等于工作辊缝在板宽范围内的开口厚度。
从用户的角度看,最好是断面厚度等于零。
但是这在目前的技术条件下还不可能达到。
在以无张力轧制为其特征的中厚板热轧过程中,为保证轧件运动的稳定性,从而确保轧制操作稳定可靠,尚要求工作辊缝(因而也就是所轧出的成品断面)稍带鼓形。
断面形状实际上是厚度在板宽方向(设为x坐标)的分布规律可用一项多项式加以逼近。
h(x)=he+ax+bx2+cx3+dx4式中he——带钢边部厚度,但由于边部减薄(由轧辊压扁变形在板宽处存在着过渡区而造成的),一般取离实际带边40mm处的厚度为he。
其中一次项实际为楔形的反映,二次抛物线对称断面形状,对于宽而薄的板带亦可能存在三次和四次项,边部减薄一般可用正弦和余弦函数表示。
在实际控制中,为了简单,往往以其特征量——凸度为控制对象。
出口断面凸度式中He ——板带(宽度方向)中心的出口厚度。
δ=Hc-He为了确切表述断面形状,可以采用相对凸度CR=δ/h作为特征量考虑到测厚仪所测的实际厚度为he或hc,也可以用。
δ/he或δ/hc(见图4-2)平直度是指浪形、瓢曲或旁弯有无及存在的程度。
平直度和带钢在每个机架入口与出口的相对凸度是否匹配有关(见图4-3)。
板凸度和板平直度理论

DC p
le lc
1
Dl lc
再根据3-11式,可知翘曲度 和比例凸度DCp 之间有下述关系:
DC p
Dl lc
2
4
2
2
DC p
热轧时上述关系可以放松,原因是热轧时轧件比较厚,易发生横向流动。相
邻道次之间的凸度改变量可以在下面范围内变化:
DCp
80
h B
1.86
DCp
40
h B
1.86
h x hc ai x2 bi x4
(4-16)
hc h(x)
x
x
x1
x2
b
板带断面形状
式中:ai、bi是表示断面特征的系数
任何一个给定的断面形状,都可以用式 4-16 表达,该式对宽度上
任何两点x1、x2都是成立的。所以,对x1、x2 两点可以建立下述两个关 于ai、bi 的线性方程:
h x1 hc ai x12 bi x14
设轧前板带中心和边部的厚度分别为Hc和He,轧后相应的厚度为hc
和he,则根据式(3-3),应该有
Hc He hc he
H c hc H e he
利用分比定理,可得
Hc He hc he
He
he
he hc he He Hc He
考虑到
he h He H Ch hc he
CH Hc He
Lv Lv
Rv
Rv
板带翘曲的两种情况
Rv
Lv+△Lv
式中: Rv
平台 Lv
正弦波的波形曲线
Rv 100%
Lv
波幅 Lv
波长
(4-8)
这种方法直观、易于测量,所以许多工作者都采用这种 方法表示板形。
板形控制讲解学习

板形控制四、板形控制板形包括带钢的板廓和带钢的平坦度。
板廓即带钢的凸度和楔形,表示带钢的横向厚度差用凸度和楔形表示。
平坦度包括带钢平直度、不对称度;带钢的浪形,用纵向带钢的延伸差值表示或用带钢的浪形高度表示;平直度表示带钢的综合对称浪形,不对称度表示带钢的不对称浪形。
带钢板形分类:1)理想板形是平坦的,内应力沿带钢宽度向上均匀分布;2)潜在板形是带钢内应力沿带钢宽度方向上不均匀分布,但其内部应力足以抵制带钢平直度的改变,当内应力释放后,带钢板形就会发生不规则的改变;3)表观板形是带钢内应力沿宽度方向上不均匀分布,同时其内部应力不足以抵制带钢平直度的改变,导致局部区域发生了翘曲变形。
1、影响板形的因素1.1 影响板形的因素很多、很复杂,主要有以下几方面:力学条件:带钢沿宽度方向的轧制压力、弯辊力、辊间接触压力几何条件:原始辊型、负荷辊型、热膨胀辊型、磨损辊型来料条件:来料板廓、轧件钢种特性、轧件厚度、轧件宽度、轧件温度、轧件长度等。
1.2 轧制过程中带钢的板形取决于负载下轧辊的凸度、金属的流动和带钢的原始板形:轧辊的空载凸度=轧辊原始辊型+轧辊热态凸度+轧辊磨损凸度轧辊的负载凸度=轧辊空载凸度+轧辊挠度+轧辊弹性压扁以上因素决定了轧机的辊缝形状,轧机的辊缝形状影响着带钢的板形,构成了板形数学模型的主要参数和控制因素。
通过制定原始辊型制度,控制弯辊和窜辊,来改善带钢的凸度和平直度。
1.3 板形不良的产生机理如果带钢的入口凸度和入口厚度的比值与带钢的出口凸度和出口厚度的比值相等,则轧出的带钢是平直的,带钢的平直度为零,即:当入口比值与出口比值不相等时,带钢边部纤维与中部纤维的延伸长度不相等,纤维间产生内应力;内应力在一定的范围内,只发生弹性变形;当纤维之间的内应力超出弹性范围,则纤维之间会产生塑性变形,产生中间浪或两边浪,造成板形不良。
板形控制就是消除带钢纤维内应力或控制在弹性范围内,使带钢的纵向纤维内应力值趋近于零,从而得到良好的凸度和平直度。
板形与板形控制基础知识
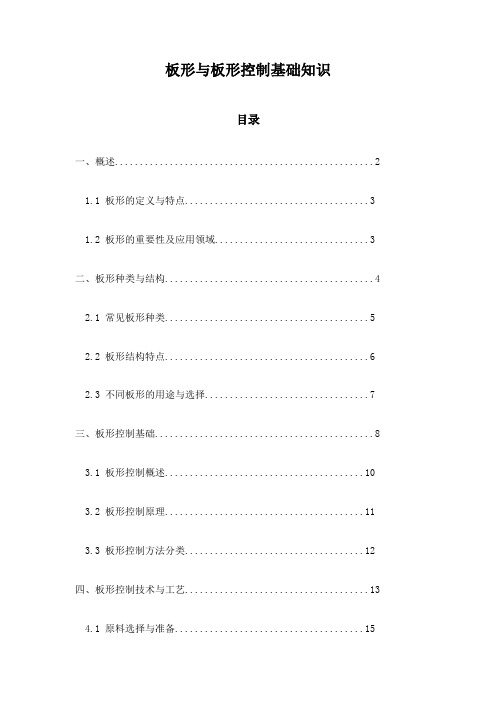
板形与板形控制基础知识目录一、概述 (2)1.1 板形的定义与特点 (3)1.2 板形的重要性及应用领域 (3)二、板形种类与结构 (4)2.1 常见板形种类 (5)2.2 板形结构特点 (6)2.3 不同板形的用途与选择 (7)三、板形控制基础 (8)3.1 板形控制概述 (10)3.2 板形控制原理 (11)3.3 板形控制方法分类 (12)四、板形控制技术与工艺 (13)4.1 原料选择与准备 (15)4.2 轧制技术与工艺 (16)4.3 热处理技术与工艺 (18)4.4 板形检测与调整技术 (19)五、板形控制实践中的注意事项 (20)5.1 安全操作规范 (21)5.2 设备维护与保养 (22)5.3 生产过程中的质量控制 (23)六、板形控制技术发展趋势与挑战 (25)6.1 国内外板形控制技术现状 (26)6.2 新型板形控制技术应用前景 (27)6.3 板形控制技术面临的挑战与机遇 (28)七、结语 (29)7.1 学习板形与板形控制的重要性 (30)7.2 未来展望与建议 (31)一、概述板形与板形控制基础知识是涉及材料加工、制造业等领域的重要概念。
在现代工业生产中,对于板材的形状、尺寸和表面质量的要求越来越高,掌握板形与板形控制基础知识对于提高产品质量、优化生产流程具有至关重要的意义。
即板材的形状和尺寸精度,直接影响到产品的使用性能和外观质量。
在金属板材加工过程中,由于原材料的不均匀性、加工过程中的热应力、机械应力等因素,往往会导致板形出现各种缺陷,如弯曲、扭曲、翘曲等。
对板形进行控制,是保证产品质量的关键环节。
板形控制则是通过一系列工艺措施和技术手段,对板材的加工过程进行调控,以达到预期的板形要求。
这涉及到材料科学、力学、工艺学等多个学科的知识。
在实际生产中,常见的板形控制方法包括热处理控制、机械矫直、辊压控制等。
了解板形与板形控制基础知识,可以帮助从业人员更好地理解生产过程中的各种问题,提高产品质量和生产效率。
板形与板形控制基础知识

有害接触区 使轧辊弯曲
支撑辊 中间辊
中间辊 支撑辊
第19页/共27页
板形与板形控制基础知识
b 工作辊的一端呈悬臂状态,用很小的力就能使工作辊的挠度明显改变,增强 了弯辊的效能;
c 可采用小直径工作辊(比普通四辊轧机的工作辊小30%)、大压下量,减少 轧制道次和中间退火的次数,节约了能源;
d 工作辊可不带原始凸度,减少了磨辊、换辊次数及备用辊的数量。
板形与板形控制基础知识
1.板形的基本概念 板形是描述板带材形状的一个综合性的概念,主要包括:板 凸 度 和平 直 度 两个基本概念。 板凸度-指板带材沿宽度方向横截面的中部与边部的厚度差,也称为 横向厚差。该厚度差取决于板带材轧后的断面形状或轧制时的实际辊缝形状。
正凸度
理想断面形状
负凸度
从用户的角度,厚差是零最好;从轧制稳定的角度,应该有一定量的 “中厚量”,异常的厚差存在将导致板形出现问题。
第2页/共27页
板形与板形控制基础知识
平直度-指板带材的翘曲度,有无浪形、瓢曲等及其程度。其实质是 板带材内部残余应力的分布,只要板带材内部存在残余应力,即为板形不 良。如残余应力不足以引起板带翘曲,称为“潜在”的板形不良;如残余 应力引起板带失稳,产生翘曲,则称为“表观”的板形不良。
平直度良好
中间浪形
板形与板形控制基础知识
如果在轧制时上述各个影响因素都是稳定的,则通过合理的轧辊原始 辊型设计,就可获得良好的板形。但是,在轧制过程中各因素是在不断变 化的,需要随时补偿这些变化因素对轧辊工作辊缝的影响,以便获得良好 的板形。
传统板形控制的基本原则是:按照轧制过程中的实际情况,随 时改变辊缝凸度,使其能满足获得良好板形的要求。
双阶梯辊支撑辊
板形与板凸的概念
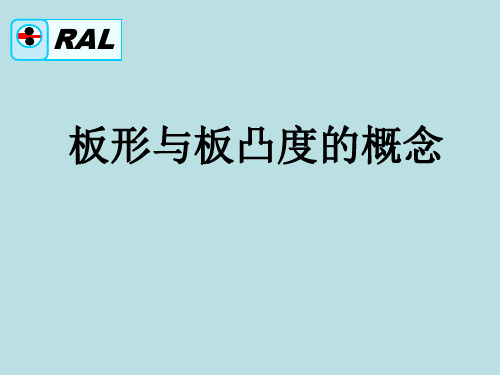
取基准点的轧后长
度 , DL 是 其 它 点
相对基准点轧后长
度之差。相对长度
差也称为板形指数
r ,r = DL/L。
RAL
相对长度差的单位
A) 英国的相对长度差的单位是蒙(mon),该术语是由W.K.泼森
建议的,1蒙相当于相对长度差为10-4。泼森定义板形为横向
上单位距离上的相对长度差,以mon/cm表示,即:
RAL
板形与板凸度的概念
RAL
板带材断面形状
• 楔形(钢带的楔形为钢带横 截面上一侧边部厚度与另 一侧边部厚度之差。边部 厚度为距纵边40㎜处的厚 度)
• he1-he2 • 中心凸度(钢带的凸度为钢
带横截面上中部厚度与两 边部平均厚度之差。边部 厚度为距纵边40㎜处的厚 度。)
a. 板带材横断面
RAL
1.2.2 边部减薄发生的原因
轧辊压扁变形的特点: • 边部压扁量少,边部变薄 • 轧制力的分布,由于边部的金属三维流动,压扁量少 • 中间和边部的轧制力作用区域不同,造成边部压扁量
少
RAL
1.2.3 楔形发生的原因
• 原料带有楔形; • 两侧压下不均; • 带钢两侧温度不均; • 带钢未对正。
设与 Lv 的直线部分相对应的曲线部分长为Lv+DLv,并认为曲线
按正弦规律变化:
y
Rv 2
sin
2 x
Lv
(1-5)
则可利用线积分求出曲线部分的长度:
Lv DLv
Lv 0
1 dy dx2 dy
Lv
2
2 0
1 Rv
Lv 2 cos2 d
Lv 1 Rv
2
轧制自动控制5-板形分析模型
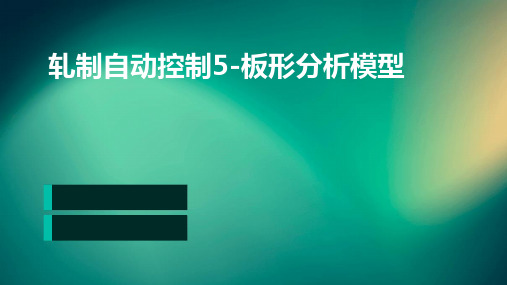
根据实际生产需求选择合适的评价指标, 如准确率、召回率、F1分数等。
结果分析
模型应用
对验证结果进行分析,找出模型的优点和 不足,并提出改进措施。
将经过验证的模型应用到实际生产中,以 指导轧制工艺参数的调整和优化,提高板 材的质量和产量。
04 轧制过程中的板形控制
控制策略
前馈控制
基于对轧制过程的理解和预测, 提前调整相关参数,以减少或消
05 板形分析模型的应用
在轧制过程中的应用
实时监测
预防设备故障
板形分析模型可以实时监测轧制过程 中的板材形状变化,及时发现并解决 板形问题,确保产品质量。
板形分析模型可以监测轧制设备的运 行状态,及时发现设备故障或异常情 况,避免生产中断和产品质量下降。
优化轧制参数
通过分析板形数据,可以优化轧制参 数,如轧制力、轧制速度和轧辊间距 等,提高板材的平直度和一致性。
轧制自动控制5-板形分析模型
目 录
• 引言 • 板形的基本概念 • 板形分析模型 • 轧制过程中的板形控制 • 板形分析模型的应用 • 结论与展望
01 引言
背景介绍
轧制技术是金属加工领域中的重要技术,广泛应用于钢铁、 有色金属、木材等材料的加工。随着科技的发展,轧制技术 也在不断进步,其中板形控制是轧制技术中的重要研究方向 之一。
板形是指金属板材的平面形状,其质量直接影响到后续加工 和最终产品的性能。因此,研究板形控制技术对于提高产品 质量和降低生产成本具有重要意义。
研究目的和意义
研究目的
本研究旨在建立轧制自动控制5-板形分析模型,通过对实际生产数据的分析和模拟,探究轧制过程中板形的形成 机制和控制方法,为实际生产提供理论支持和技术指导。
板带轧制理论与工艺 4 板凸度和板平直度理论
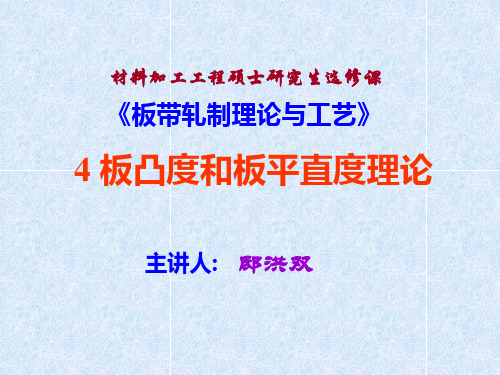
材料加工工程硕士研究生选修课板带轧制理论与工艺》4 板凸度和板平直度理论主讲人:邸洪双热轧卷板的主要质量问题性能:强度,塑性,冲击韧性表面:氧化铁皮,麻点,划伤,挂腊,夹杂,边裂,翘皮尺寸精度:厚度,宽度板形(平直度,凸度,边部减薄,局部高点)由于带钢板形质量问题对用户使用及最终产品质量带来不利影响。
如汽车制造、工程机械设备、集装箱和冷轧生产等汽车梁成型后腿部距离回弹不一致,热轧卷板表面局部高点造成冷轧卷板成品表面产生粘结浪形导致下工序衬板、加强板组装困难集装箱板浪形影响集装箱整体焊接质量和外观工程机械钢卷板瓢曲造成吊车吊臂无法焊接4.1 板形和板凸度的概念板形(shape )(平直度)直观来说:指板材的翘曲程度Flatness, Buckle, Cambershape实质:板带材内部残余应力的分布只要板带内部存在有残余的内应力,就称为板形不良。
如果这个应力虽然存在,但不足以引起板带翘曲,则称为“潜在”的板形不良;如果这个应力足够大,以致于引起板带翘曲,则称为“表观”的板形不良。
板形缺陷的产生残余应力板形不良“潜在”的板形不良“表观”的板形不良带钢实际平直度照片平直中浪边浪板形缺陷的分类板带中残余应力分布的规律不同,其所引起的板带翘曲形式也不同。
所以,可以根据内应力的分布规律和板带的翘曲情况,将板形缺陷分成不同的类型。
()22121pcr cr p E h k B πσν⎛⎫= ⎪+⎝⎭crσ板带产生翘曲的临界应力crk 临界应力系数pE 板带的弹性模量pν板带的泊松比h板带的厚度B板带的宽度(4-1)式中:板带翘曲的力学条件根据弹性力学的研究结果,板带发生翘曲的力学条件可表达为:研究结果表明,对于冷轧宽带钢,产生边浪时,k cr ≈12.6,产生中浪时,k cr ≈17.0。
对于热轧宽带钢,边浪时k cr ≈14,中浪时k cr ≈20良好板形的几何条件如右图所示,横坐标表示各点的横向位臵,即横向各点距板带中心的距离,纵坐标分别为入口和出口轧件半厚,入口断面形状函数为H(x),出口断面形状函数为h(x)。
- 1、下载文档前请自行甄别文档内容的完整性,平台不提供额外的编辑、内容补充、找答案等附加服务。
- 2、"仅部分预览"的文档,不可在线预览部分如存在完整性等问题,可反馈申请退款(可完整预览的文档不适用该条件!)。
- 3、如文档侵犯您的权益,请联系客服反馈,我们会尽快为您处理(人工客服工作时间:9:00-18:30)。
带材横截面中点厚度与两侧边部标志点平均厚度 之差。有时也用到比例凸度,即凸度与横截面中 点厚度之比。比例凸度也称为相对凸度。 (2)楔形。楔形指冶金机械设备带材横
ቤተ መጻሕፍቲ ባይዱ
整体的(内部或外部的)压应力减小到将表观板 形转变为潜在板形的水平,则张力影响的板形可 能是平的。
好的。由此可以得出,对于平坦来料,保证札后 带材板形平坦度良好的几何条件是比例凸度恒定。 在冶金机械设备板形的各项指标中以凸度和平坦 度为主要指标,这两个指标在控
制中往往存在矛盾,但它们之间又存在紧密关系。 凸度取决于轧棍有载辊缝形状,因此凡是对轧辊 有载辊缝形状有影响的因素,如轧制力、弯辊力、 热辊形、轧辊磨损辊形以及轧辊凸
平坦度的定义方法,如波高法、波浪度法、纤维 相对长度差法和应力(应变)差法。 1)波高法。波高圯是自然状态下带材瓢曲表面上 偏离检查平台的最大距离,也可近似为曲面
函数的最大值。 2)波浪度法。波浪度必是波高&和波长比值的百 分率。 3)纤维相对长度差法。在自由带钢的某一取定长 度区间内,示沿横向的最大纤维相对长度差。
纵切带钢时,带钢板形仍然保持平直。 (2)潜在板形。潜在板形产生的条件是内部应力沿 带钢宽度方向上不均匀分布,但是带钢的内部应 力足以抵制带钢平直度的改变。当去除
带钢所受外力时,带钢板形仍然保持平直。然而 当纵切带钢时,潜在的应力会使带钢板形发生不 规则的改变。 (3)表观板形。表观板形产生的条件是内部应力沿 带钢宽度方向上
度(冷辊形及在线可调辊凸度)都将对出口带钢 的断面形状有影响。而平坦度则取决于带宽方向 各假想小条的均匀延伸,因此将和入口带钢相对 凸度及出口带钢相对凸度是否匹配有关
。所谓匹配,从板形方程可知,即入口和出口相 对凸度(也可称为比例凸度)应相等。 当入口和出口带钢相对凸度不相互匹配时,将使 带钢上带宽方向各小条受到不均匀压缩,因
而产生不均匀延伸,但实际上带钢为一整体,因 此这种带宽方向各点的不均匀延伸将使带钢内部 产生内应力,轧制结束后转为残余内应力,当残 余内应力超过带钢产生翘曲的极限应力
时,带钢将发生翘曲。带钢越薄、越宽,越容易 产生翘曲。当带钢轧制具有前、后张力时,带钢 内部张应力将由于存在内部应力而分布不均,只 要张应力与内应力合成后尚大于零,带
钢表面上就不会产生翘曲;一旦张力释放(取一 段带钢放平台上),带钢将产生翘曲。正因为如 此,轧制时冷轧带钢的平坦度可以用剖分式张力 测量辊或其他能测量带宽方向张应力分
布的装置来进行在线测蛩。 常见的冶金机械设备带钢板形分类如下: (1)理想板形。理想板形应该是平坦的,内应力沿 带钢宽度方向上均匀分布,当去除带钢所受外应 力和
截面操作侧与传动侧边部标志点厚度之差。 (3)边部减薄量。边部减薄量指带材横截面操作侧 和传动侧边部标志点厚度与边缘位置厚度之差。 (4)局部高点。局部高点指
横截面上局部范围内的厚度凸起。 (5)平坦度。平坦度指板带材表观平坦程度。由于 在轧制过程中和成品检验时一直使用着多种平坦 度测量手段(方法),所以也就存在着多种
不均匀分布,同时带钢内部应力不足以抵制带钢 平直度的改变。结果局部区域产生了弹性翘曲变 形。去除带钢所受外力和纵切带钢都会加剧带钢 的表观板形。 (4)混合板形。混
合板形是指带钢的各个部分板形形式不同。例如, 带钢的一部分呈现潜在板形,其他的部分呈现表 观板形。 (5)张力影响的板形。如果张力产生的内应力足够 大,以至于可以将
4)应力(应变)差法。当使用测张力式板形仪时, 就以实测的在线带材中不均匀分布前的张应力与 平均张应力的差值表示平坦度,称为板形检测应 力。 当带材卸掉张力作用或离
lkj来源: 三箭气 抢
开轧制线后,板形检测应力消失,但带材中仍存 在不均匀分布的内应力,称为带材的残余应力。 一般认为,如果在轧制过程中塑性延伸率沿带材 横向处处相同,则板形平坦度是良