金属表面的电化学抛光共20页文档
铝件电化学抛光工艺流程

铝件电化学抛光工艺流程铝件电化学抛光啊,这可是个挺有趣的事儿呢。
一、电化学抛光的基础。
电化学抛光简单来说,就是利用电化学反应来让铝件表面变得超级光滑。
就像给铝件做一个超级精致的美容护理。
咱们都知道铝件在很多地方都能用,像那些漂亮的铝制装饰品啦,还有一些工业上用的铝制品部件。
但是铝件刚生产出来的时候,表面可能有点粗糙,或者有一些小瑕疵。
电化学抛光就像一个魔法,能把这些问题统统解决掉。
二、前期准备工作。
在开始电化学抛光之前呢,有好多准备工作要做。
铝件得先清洗干净呀,不能带着一身的灰尘和油污就去“做美容”对吧。
就像我们人洗脸一样,要把脸洗得干干净净的才能化妆。
这个清洗过程可不能马虎,要用合适的清洗剂,把铝件表面的脏东西都去除掉。
而且呀,铝件的形状和大小也很重要哦。
不同形状和大小的铝件,在抛光的时候可能需要不同的处理方式。
比如说那种小小的、形状很奇特的铝件,可能就需要更细致的固定,这样才能保证在抛光的时候每个地方都能被照顾到。
三、电解液的选择。
电解液就像是这个抛光魔法的魔法药水。
对于铝件电化学抛光来说,选择合适的电解液那是相当关键的。
这里面的学问可不少呢。
有些电解液可能对铝的反应比较温和,适合那些比较精细的铝件,就像给小婴儿擦面霜,得用温和的产品。
而有些电解液可能对铝的腐蚀作用稍微强一点,但是能更快地让铝件表面变得光滑,这就像是给皮肤比较粗糙的人用那种强力一点的磨砂膏。
不过不管是哪种电解液,都得根据铝件的具体要求和实际情况来选择。
而且呀,电解液的浓度也很重要,浓度太高或者太低都可能影响抛光的效果。
四、抛光过程。
五、后期处理。
抛光完成之后,铝件可不能就这么直接拿出来用。
还得进行后期处理呢。
要把铝件从电解液里拿出来,然后清洗干净。
这个清洗可不像前期清洗那么简单了。
因为铝件刚刚经历了电化学反应,表面可能会残留一些电解液的成分。
如果不清洗干净,这些残留成分可能会对铝件造成损害,就像我们皮肤接触了脏东西不洗干净就会过敏一样。
电化学抛光工艺(3篇)
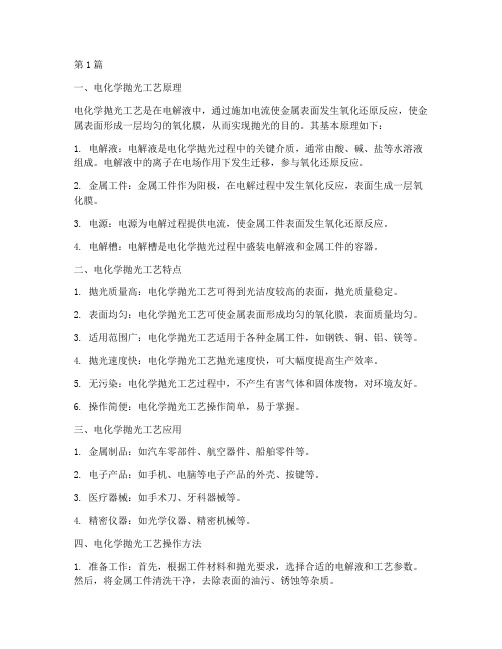
第1篇一、电化学抛光工艺原理电化学抛光工艺是在电解液中,通过施加电流使金属表面发生氧化还原反应,使金属表面形成一层均匀的氧化膜,从而实现抛光的目的。
其基本原理如下:1. 电解液:电解液是电化学抛光过程中的关键介质,通常由酸、碱、盐等水溶液组成。
电解液中的离子在电场作用下发生迁移,参与氧化还原反应。
2. 金属工件:金属工件作为阳极,在电解过程中发生氧化反应,表面生成一层氧化膜。
3. 电源:电源为电解过程提供电流,使金属工件表面发生氧化还原反应。
4. 电解槽:电解槽是电化学抛光过程中盛装电解液和金属工件的容器。
二、电化学抛光工艺特点1. 抛光质量高:电化学抛光工艺可得到光洁度较高的表面,抛光质量稳定。
2. 表面均匀:电化学抛光工艺可使金属表面形成均匀的氧化膜,表面质量均匀。
3. 适用范围广:电化学抛光工艺适用于各种金属工件,如钢铁、铜、铝、镁等。
4. 抛光速度快:电化学抛光工艺抛光速度快,可大幅度提高生产效率。
5. 无污染:电化学抛光工艺过程中,不产生有害气体和固体废物,对环境友好。
6. 操作简便:电化学抛光工艺操作简单,易于掌握。
三、电化学抛光工艺应用1. 金属制品:如汽车零部件、航空器件、船舶零件等。
2. 电子产品:如手机、电脑等电子产品的外壳、按键等。
3. 医疗器械:如手术刀、牙科器械等。
4. 精密仪器:如光学仪器、精密机械等。
四、电化学抛光工艺操作方法1. 准备工作:首先,根据工件材料和抛光要求,选择合适的电解液和工艺参数。
然后,将金属工件清洗干净,去除表面的油污、锈蚀等杂质。
2. 电解液配制:按照配方配制电解液,确保电解液的浓度、pH值等符合要求。
3. 工艺参数设置:根据工件材料和抛光要求,设置合适的电流密度、电解液温度、处理时间等工艺参数。
4. 抛光过程:将工件放入电解槽中,通电进行抛光。
在抛光过程中,观察工件表面变化,适时调整电流密度、电解液温度等参数。
5. 清洗与干燥:抛光完成后,将工件从电解槽中取出,用清水冲洗干净,去除表面的电解液和氧化膜。
金属表面的电化学抛光全解
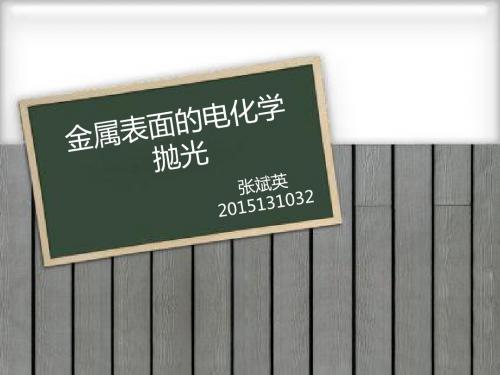
三、铝的电化学抛光
铝在化学抛光时,表)速度快,而低凹部位的溶解(腐蚀)速 度小,形成局部阳极,发生部分钝化作用,溶解速度慢所致。 Fischer和和Koch等科学家研究了高纯铝的抛光过程,并根据抛 光过程中铝的溶解速度、逸出气体量及腐蚀电流密度等实验数据, 得出铝在化学抛光中发生的化学反应是由于形成(-)Al/酸(或 碱)/氧化还原体系/惰性金属(+)构成局部电池发生氧化-还原 反应的结果。化学抛光机理模型如下图(1)
二、金属的电化学抛光
电化学抛光又称为电解抛光,是一种在特殊条件 下的电化学腐蚀,它是通过控制金属表面选择性的溶 解,使金属表面微观突出部位较其凹洼部位优先溶解, 而达到表面平整和光亮的目的。以铝电解抛光为例: 铝材做为阳极浸入到配置好的电解质溶液中,以耐腐 蚀且导电性良好的材料做为阴极,根据电化学尖端放 电原理,通电后的铝材表面微小突出部位优先溶解, 与此同时溶解产物与表面的电解液形成高电阻的粘稠 性液膜层,微小突出部位的液膜层较薄,其电阻较小, 从而继续保持优先溶解。同时表面凹洼部位的液膜层 厚,电阻大,凹洼部位的溶解速度相对缓慢,经过短 时间电解处理后,突出部位被溶解整平至凹洼部位的 位置,铝材表面粗糙度降低达到平滑光亮。
一、电极的极化现象
金属的电化学腐蚀热力学分析是判断金属 材料在腐蚀介质中的腐蚀倾向,即判断金属是 否会发生腐蚀,而金属的电化学腐蚀动力学分 析是探究腐蚀作用的动力学规律来解决腐蚀反 应发生、腐蚀扩展机制和原理以及腐蚀发生和 扩展的速度等问题。 根据热力学研究可知,当电化学反应的阳 极氧化反应和阴极还原反应的反应速度大小相 等,则整个反应处于稳定平衡态。且电极电位 处于该电极反应的平衡电极电位。
四、电化学抛光的阳极极化曲线
图1-1(a)为处于活化状态的极化曲线,如图示 电流密度随阳极金属溶解作用均随阳极电位的提高而 增大,阳极金属表面一直处于电化学阳极溶解状态 (又称活化状态)。铁在盐酸中的电化学阳极极化曲 线就属于这一类型。
不锈钢电抛光及电化学钝化

不锈钢电抛光及电化学钝化不锈钢电抛光及电化学钝化我厂生产的各种仪表中,绝大部分零件需要承受强腐蚀介质的考验,因此,需用各种不锈钢材料制作。
常用的不锈钢材料有:1Cr18Ni9Ti、CrWMn、1Cr13、2Cr13、3Cr13和4Cr13等。
不锈钢零件的形状和大小也各不相同。
简单的如管材、线材、板线、带材制作件;复杂的有叶轮、齿轮、阀体、壳体等。
从不到1克重的小空心杆到几十公斤重的大壳体。
其表面状态也各式各样,有经机械加工的表面,有毛坯表面;有经点焊、电焊、氢弧焊的表面;还有经热处理的表面( 具有一层很厚的氧化皮〉。
以前对各种不锈钢零件分别进行机械抛光、酸洗,或松膜、去膜、酸洗、化学钝化等处理。
不锈钢机械抛光, 比钢铁、铜、铝及其合金零件机械抛光困难。
而且复杂零件的一些部位,不易抛到。
酸洗,特别是酸洗有黑色氧化皮的零件,首先需在含氧化剂的高浓度NaOH溶液中高温松膜,再用H2SO4、H2Cr04、HF混酸溶液去膜, 还要在HCl、HN03和H2S04的水溶液中酸洗,最后在HN03的水溶液中钝化处理。
这些处理方法,工艺烦琐、生产效率低, 操作条件恶劣, 而且还易造成废品。
不得不研究改进。
我们曾试验采用过电抛光。
电解液组分为硫酸15% ,磷酸65%,甘油12%, 铬酸5%, 水3%( 重量百分比〉。
试验结果:对1Cr18Ni9Ti及CrWMn不锈钢零件有抛亮效果, 但对有氧化皮的零件,仍需松膜、去膜、酸洗后才能进行电抛光。
而且这种电解液的浓度很高( 比重高达1.7以上),不能带水入槽〈零件需干燥后才能入槽),给操作带来很大的麻烦。
同时电解液很不稳定,不易调整再生, 吸水性强,大而复杂的零件有阴暗面。
而且阳极电流密度(Da)高、电压(V)高、速度慢, 不能满足生产需要。
经过较长时间的反复试验, 我们研制出一种槽液稳定易调,操作方便,成本低,效率高,无污染的不锈钢电抛光新配方。
在较长时间的生产实践中, 效果较好。
镍钛电化学抛光

镍钛电化学抛光镍钛电化学抛光是一种在金属表面进行抛光和清洁的技术方法。
它利用了镍钛合金在电化学过程中的特殊性质,通过控制电流和电压来实现对金属表面的抛光作用。
这种方法不仅能够提高金属表面的光洁度和平滑度,还可以去除表面的氧化物和污垢,使金属表面恢复原有的光亮度和美观度。
在镍钛电化学抛光中,首先需要准备一个合适的电解槽,槽中装有适当浓度的镍钛溶液。
然后将待抛光的金属样品连接到电解槽中的阳极,同时将另一块金属作为阴极。
接下来,通过控制电流和电压的大小和方向,使金属表面发生氧化还原反应,从而实现抛光效果。
镍钛电化学抛光的一个重要特点是可以实现对金属表面的局部抛光。
通过在阳极上加装遮罩,可以限制氧化还原反应的发生范围,从而只对需要抛光的部分进行处理。
这种局部抛光的能力使得镍钛电化学抛光在微细加工和修复金属表面缺陷方面具有广泛的应用前景。
与传统的机械抛光方法相比,镍钛电化学抛光具有许多优点。
首先,它可以在较低的温度下进行,避免了热变形和烧伤等问题。
其次,它可以实现对金属表面的高精度抛光,避免了机械抛光过程中可能产生的划痕和凹陷。
此外,镍钛电化学抛光还可以在短时间内完成,提高了生产效率。
然而,镍钛电化学抛光也存在一些挑战和限制。
首先,镍钛合金的制备和处理过程相对复杂,需要合适的设备和技术支持。
其次,镍钛电化学抛光对金属材料的选择有一定的要求,不同材料的抛光效果可能存在差异。
此外,镍钛电化学抛光还需要严格控制电流和电压的大小和方向,以避免对金属样品造成损伤。
镍钛电化学抛光是一种有效的金属表面抛光和清洁技术。
它能够提高金属表面的光洁度和平滑度,去除氧化物和污垢,恢复金属表面的光亮度和美观度。
尽管存在一些挑战和限制,但随着技术的不断发展和改进,镍钛电化学抛光在金属加工和表面修复领域的应用前景仍然广阔。
通过继续研究和改进,相信镍钛电化学抛光将为金属加工行业带来更多的机遇和挑战。
金属表面处理电化学法共页

纳米金自组装电极的制备方法
裸金电极 预处理 cysteine 冲洗 浸泡 纳米金 4 ºC下保存
(2)共价键合型修饰电极
基底电极:碳电极,金属电极、金属氧化物电极; 键合方法:
基底电极表面处理→引入化学活性基团→修饰物
四.化学修饰电极的表征
• 电化学法 • 光谱电化学法 • 波谱法 • 能谱法 • 显微学法 • 石英晶体微天平法
用机械或加热的办法处理。
抛光电极的材料:金刚砂,CeO2,ZrO2,MgO ,α-Al2O3粉等。
抛光时按粒径降低的顺序进行研磨。抛光后移 入超声水浴中清洗,直至干净。
2. 化学法和电化学法处理
化学的和电化学的处理,是最常用来清洁,活 化电极表面的手段。
电化学法常用强的矿物酸或中性电解质溶液, 有时也用配位作用弱的缓冲溶液在恒电位,恒 电流或循环电位扫描下极化,可获得氧化的、 还原的或干净的电极表面。
• 鉴定电极表面是否清洁的方法
✓对于碳电极,采用观测Fe(CN)63-在中性电解 质水溶液中的伏安曲线的方法。在1×10-3 mol/L的K3Fe(CN)6磷酸盐缓冲溶液中扫描,直 到出现可逆的阴极和阳极峰。
✓对于铂电极,在稀硫酸中进行循环电位扫描, 观察氢和氧的电化学行为,即出现了氢和氧的各 自的吸附和氧化峰就表示表面已清洁。
电化学方法
通过研究电极表面修饰剂 发生相关的电化学反应的 电流、电量、电位和电解 时间等参数的关系来定性 、定量的表征修饰剂的电 极过程和性能。
• 循环伏安法 • 计时电流法 • 计时电位法 • 计时库仑法 • 脉冲伏安法 • 交流阻抗法
中性鲁米诺体系在纳米金自组装金电极与 在裸金电极上CV行为的比较
纳米金自组装金电极的紫外-可见 等离子体共振吸收差谱
铜及铜合金化学及电化学抛光

铜及铜合金化学及电化学抛光:化学抛光(1)普通型化学抛光溶液配方及工艺规范见表1。
(2)清洁型化学抛光溶液①工艺流程。
上夹具一超声波脱脂一热水洗一三级逆流漂洗一除膜一化学抛光一流动水洗一无铬钝化一流动水洗一封闭干燥一成品下架。
②清洁型化学抛光溶液配方及工艺规范硫酸(H2S04)450mL/L表1铜及铜合金化学抛光工艺规范配方工艺规范12345硫酸(H2S04,密度1.84g/mL)/(mL/L)250~280400~500硝酸(HN03,密度1.50g/mL,质量分数)/%40~50 mL/L106~829.5~6.440~60g/L磷酸(H3P04,密度1.70g/mL,质量分数)/%5440~5070.5~95.6冰醋酸(CH3CO OH)/%3035~45铬酐(Cr03)/(g/L)180~200盐酸(HCl,密度1.19g/mL)/(mL/L)3尿素/(g/L)40~60明胶/(g/L)1~2聚乙二醇/(g/L)1~2温度/℃20~4055~6540~6025~45<40时间/min0.2~33~53~101~215~30s用途适用于比较精密度高的制品适用于钢及黄铜制品适用于铜和黄铜制品,降低温度至20℃,可抛光白铜制品适用于铜铁组合制品适用于黄铜制品添加剂70mL/LO P乳化剂1.0mL/L温度40℃时间l5s③抛光液各成分对抛光质量的影响a·硫酸。
主要作用是溶解剥离铜及其合金表面的氧化膜,与抛光添加剂A配合使用,可起到光亮整平作用。
硫酸浓度高时,抛光速度快,表面光亮度好。
但浓度过高时,抛光效果会变差。
硫酸浓度低时,抛光速度慢,光亮度差。
b·抛光添加剂。
抛光添加剂分为A、B两组分。
A为添加剂,B为调整剂。
添加剂A是抛光液的主要组成部分,能起到促进反应速度和提高光亮度的作用。
添加剂A含量高时,抛光速度快,光亮度好,但含量再高时,无明显作用。
含量低时,抛光速度慢,抛光表面达不到镜面光泽。
金属的化学和电化学蚀刻加工及抛光

金属的化学和电化学蚀刻加工及抛光一、实验导言金属材料和非金属材料各有不同的加工处理方法。
金属材料的加工成形和提高表面光洁度的方法很多,历史悠久的传统加工方法有:热加工,即将材料加热至熔融状态,放到模具里冷却成形;机械加工:在常温下,用车床、刨床、镗床、铣床以及冷扎等加工工具的机械能量,使被加工材料成形。
随着被加工材料组成、材质的变化,仅仅用传统加工方法已不能满足生产和科研的需要。
20世纪50年代以来,对材料的化学和电化学加工方法迅速发展起来。
化学加工是利用自发进行的氧化还原反应将电极电势低的金属氧化掉,保留下需要的部分成为产品。
这种加工方法又称为化学蚀刻。
之所以称为“蚀刻”,是因为其加工反应原理与金属腐蚀原理相同,也可以说是金属腐蚀原理在材料加工中的应用。
随着电讯技术的迅猛发展,电子器件的生产加工技术不断更新,越来越趋向于微型化、精密化,集成化,以至如在“微波水热合成法制备纳米材料”中所述:在分子和原子量级上加工器件已不足为奇。
不过截至目前,印刷电路板的制作工艺仍在沿用始于上世纪初的化学蚀刻方法。
电化学加工是利用电化学中电解的原理使非自发进行的氧化还原反应得以进行,而将金属加工成为需要的产品的。
这种加工方法又称为电化学蚀刻。
不锈钢是具有抵抗大气、酸、碱、盐等腐蚀作用的合金钢的总称。
在钢中添加元素铬,其含量达12%~13%以上,含量超过17%的不锈钢为耐酸钢。
典型不锈钢的化学成分为:1Crl8Ni9Ti。
不锈钢的强耐腐蚀性使得一般的化学加工对它来说不适宜。
因此常用电化学加工法。
化学蚀刻和电化学蚀刻二者的区别在于前者不必通电流,而后者需要外电源通电实现加工反应。
从加工速率来说,电化学加工来得快。
化学蚀刻和电化学蚀刻主要用于:各种难切削材料的加工(硬质合金、钛合金等)、各种复杂表面的加工(喷气涡轮机叶片、整体涡轮、发动机机匣等)、各种超精、光整及特殊要求的加工(航天、航空陀螺仪等)。
为了提高加工效率和质量,人们寻找更加有效的加工方法,还创造出了将化学或电化学加工与机械加工有机结合、同步进行的加工方法,例如,电解磨翻、电解珩磨等。
金属管件内表面的电化学抛光

珠海市格力特科技金属管件内表面的电化学抛光1引言金属管件用途极为广泛,一般希望电化学内表面比较光滑。
对于一些特殊用途的管件,则对管件内表面的表面粗糙提出了更高的要求。
这时,就需要对管件内表面进行抛光。
而传统的机械抛光方法生产效率低,劳动强度大,往往不能胜任对管件内表面的抛光,特别是对细长管件,用机械抛光的方法往往无法达到要求。
金属管件内表面的抛光可以采用电化学抛光的方法,电化学抛光的速度不受金属本身硬度和韧性的影响,生产效率较高,电解液可以循环使用,加工费用大大低于机械抛光。
与传统的机械抛光相比具有明显的优势。
2电化学抛光原理和工具阴极的结构电化学抛光的原理与电解加工一样,是利用金属在电解液中会发生阳极溶解的原理对工件进行抛光的。
不同的是电化学抛光时采用的电压和电流值要比电解加工时的小,工具阴极和工件阳极之间的距离要比电解加工时的大,一般的管件电化学抛光时可用酸性溶液,如硫酸、磷酸、铬酐等组成的复合溶液,也可以采用中性溶液,如氯化钠溶液。
由于酸性溶液价格高,对设备腐蚀大,在实际生产中通常使用中性溶液。
采用中性溶液时管件内表面电化学抛光所使用的阴极有很多种,较典型的是移动式管件内表面电化学抛光阴极。
图1是这种阴极的结构示意图。
电化学抛光时将待抛光的管件(阳极)接直流电源的正极,工具阴极接直流电源的负极;用泵打出的电解液经过阴极体2中的孔和前引导4的整流腔进入抛光区,使正、负极之间通以流动的电解液;抛光之后,电解液经过后引导1上的槽和回水管再流回电解池。
对于长管件可用卧式电化学抛光机床,或将车床改造作为电化学抛光机床。
工具阴极的移动可以由机床的进给系统实现。
工具阴极的材料科采用铜或钢。
工具阴极与阳极管件之间的距离一般为0.5~1.5㎜。
3电解液的选择和工艺参数的确定不同材料的管件应采用不同的电解液和工艺参数,经过多次工艺试验我们刷选出了针对几种不同材料的较为理想的抛光电解液。
对于不同的抛光要求,可分别采用酸性抛光电解液或中性抛光电解液。
电化学抛光技术及其在金属合金表面抛光中的运用

电化学抛光技术及其在金属合金中表面抛光的运用电化学抛光技术及其在金属合金中表面抛光的运用摘要:本文通过查阅和总结电化学抛光技术的相关文献,介绍了电化学抛光技术的原理,阐述电化学的复合抛光技术和其在主要金属及其合金上的表面抛光处理的运用,并展望了电化学抛光的展望。
关键词:电化学抛光;复合抛光;金属;表面抛光Electrochemical polishing technology and its application in the surface polishing of metal alloysAbstract:Through reading and summarizing electrochemical polishing technology related literatures, this paper introduces the principle of electrochemical polishing technology, expounds the electrochemical combination polishing technology and its application in surface polishing of main metals and their alloys, and also expresses the prospect of electrochemical polishing.Key words:electrochemical polishing technology;combination polishing;metal alloy;surface polishing引言在生产中,我们经常需要对于一些材料进行表面加工,从传统的金属冶炼业的金属抛光到现代的硅芯片的表面封装,这些都离不开电化学技术。
而其中的金属表面抛光常用的技术就是电化学抛光。
电化学抛光是指在一定电解液中金属工件的阳极溶解,从而使其表面粗糙度下降、光亮度提高,并产生一定金属光泽的表面光整技术[1]。
常见几种金属的电化学抛光_王文忠

2 0 1 3年1 1月
电镀与环保
·5 第3 总第 1 3 卷第 6 期 ( 9 4期) 3·
电流较小 , 在金属溶 解 的 同 时 有 水 或 其 他 含 氧 离 子 放电 , 有氧气析出 , 此时有较好的抛光效果 。 当然电 流密度过高 、 阳 极 析 出 大 量 氧 气, 造成工件表面过 产生电化学过腐蚀 , 也得不到良好的抛光效果 。 热, 2. 3 温度的影响 在一 定 的 电 流 密 度 下 , 升高温度可提高抛光速 率。但 温 度 过 高, 溶 液 的 黏 度 下 降, 对 流 作 用 加 强, 扩散速率加快 , 阳 极 溶 解 快, 引 起 化 学 腐 蚀 严 重, 降 低抛光效果 。 温度低 , 导电性差 , 抛光速率慢 。 2. 4 时间的影响 时间要根据材质 、 工件表面的原始状态 、 电流密 度、 温度和电解 液 的 成 分 等 来 确 定 。 一 般 电 流 密 度 大、 温 度 高, 抛 光 时 间 可 短 一 些。若 反 复 抛 光 数 次, 每次都在规定时间范围内可得到较高的光亮度 。 2. 5 搅拌的影响 搅拌 可 使 工 件 表 面 的 镀 液 不 断 更 新 , 使温度均 消除滞留在工件表面的气泡 , 防止产生麻点和条 匀, 纹 。 搅拌可采用阳 极 移 动 , 有平行往返式和上下移 动式两种 。
1 电抛光的基本原理
( 电抛光过程中 , 工件表面发生如下反应 : 1)阳 ( 极金属发生电离 , 以离子状态转移到溶液中 ; 2)工 ( )气 态 氧 气 析 出 ; ( 件表面生成氧化膜 ; 3 4)溶 液 中 的其他物质被氧化 , 生成某种气体物质及其盐类 。 从阳 极 反 应 中 可 以 看 出 : 电抛光时工件表面有 氧化膜生成而使其 表 面 钝 化 , 但钝态的氧化膜在电 在整个抛光过程中氧 解液中不断溶解 。 也 就 是 说 , — — 生成和溶解 。 从 化膜不间断地进行着两个过程 — 微观上来看 , 工件表面凹凸很不均匀 , 而且凸起处的 金属表面较凹洼处的活泼 。 再加上两处电流存在差 异, 凸起处的电流大 , 表面溶液更新快 。 所有这些都 最终使工件表面趋于平整 促使凸起处的金属 溶 解 , 并产生光泽 。 这种 氧 化 膜 理 论 认 为 , 抛光是氧化膜 的不间断生成和溶解完成的 。 目前对于钢 铁 件 、 不 锈 钢 件、 铜 及 铜 合 金、 铝及 大都采用以磷酸为主 铝合金等金属的电 化 学 抛 光 , 的抛光液 。 其机制有人认为是阳极电化学过程和金 即黏膜理 属表面形成的磷酸 盐 膜 共 同 作 用 的 结 果 , 论 。 阳极溶解所产生的金属离子与抛光液中的磷酸
电化学抛光简介PPT课件

10
Thank You!
11
3
电化学抛光工艺及特点
1设备及工艺流程[2]
设备有: 电解槽、清洗槽、阳极架辅助阴极( 铅
板、石墨板) 、直流电源等。
工艺流程: 装料 除油
清洗 除锈
清洗 抛光 清洗
钝化 清洗
晾干 卸料
4
电化学抛光工艺及特点
2.电化学抛光作为一种金属表面处理方法, 它具有以下优点[3] :
( 1) 不受材料硬度和韧性的限制, 几乎所有的模具材料都可进行电解抛光; ( 2) 电化学抛光可对模具表面起整平作用; ( 3) 可抛光各种较复杂的型腔; ( 4) 经电化学抛光后的表面无任何条纹; ( 5) 抛光速度快慢可方便调节电化学抛光速度与电流大小成正比。电流大, 阳极( 工件) 溶
5
电化学抛光工艺及特点
3.电化学抛光在处理金属表面时, 还有一些不足存在[4] (1) 所得表面质量取决于被加工金属的组织均 匀性和纯度, 金属结构的缺陷被突出地显露出来。 对表面有序化组织敏感性较大; (2) 较难保持零件尺寸和几何形状的精确度; (3) 表面必须预加工到比较高的粗糙度. 很难 在粗加工或砂型铸造零件上获得高的抛光质量。
[ 电化学抛光简介 ]
1
主要内容
电化学抛光原理 1
电化学抛光工ቤተ መጻሕፍቲ ባይዱ及特点 2
影响电化学抛光的因素 3
电化学抛光的问题与展望 43
2
电化学原理
电化学抛光是金属阳极溶解的独特电解过程,它受众多可变因素的影响。根据阳极金属 的性质、电解液组成、浓度及工艺条件的不同, 在阳极表面上
• 可能发生下列一种或几种反应[1] :
( 1) 金属氧转化成金属离子溶人到电解液中
电解不锈钢抛光技术.

一.电化学抛光理论:1.电化学抛光定义(即什么是电解?):以被抛工件为阳极,不溶性金属为阴极,两极同时浸入到电解槽中,通以直流电而产生有选择性的阳极溶解,从而达到工件表面光亮度增大的效果。
2.电解原理:电解原理现在世界各界人士争论很多,被大家公认的主要为黏膜理论。
工件上脱离的金属离子与抛光液中的磷酸形成一层磷酸盐膜吸附在工件表面,这种黏膜在凸起处较薄,凹处较厚,因凸起处电流密度高而溶解快,随黏膜流动,凹凸不断变化,粗糙表面逐渐被整平。
3.电解抛光优点:⑴内外色泽一致,光泽持久,机械抛光无法抛到的凹处也可整平。
⑵生产效率高,成本低廉。
⑶增加工件表面抗腐蚀性。
二.电化学抛光所需条件及设备1.电源:电源可选用双相220V,三相380V。
2.整流器电解抛光对电源波形要求不是太严格,可选用可控硅整流器好高频整流器。
整流器空载电压:0—20v负载电压(工作电压):8—10v工作电压低于6v,抛光速度慢,光亮度不足。
整流器电流:根据客户工件大小而定。
3.电解槽及配套设施(阳极棒)可选用聚氯乙烯硬板材焊接而成。
在槽上装三根电极棒,中间为可移动的阳极棒,接电源阳极(或正极),两侧为阴极棒,连接电源阴极(负极)。
4.加热设施及冷却设备(1)加热可选用石英加热管,钛加热管。
(2)冷却可选用盘管,盘管可加热可冷却。
5.夹具最好选用钛做挂具,因为钛较耐腐蚀,寿命长,钛离子对槽液无影响。
建议最好不要用铜挂具,因为铜离子进入会在不锈钢表面沉积一层结合力不好的铜层,影响抛光质量。
铜裸露部位可用聚氯乙烯胶烘烤成膜,在接触点刮去绝缘膜。
6.阴阳极材料阴阳极棒应用铜棒或铜管,铜管长是电解槽长加20厘米,阴极板应用铅板,铅板固定在阴极棒上,铅板长为槽高加10厘米,铅板宽根据槽长而定,一般为10厘米,20厘米规格。
三.电解液:这里具体介绍下“云清牌不锈钢通用电解液“。
1.电解液指标:(1)电解液密度:1.68—1.72(2)电解液状态:微黄色透明液体(3)PH值:<7(4)电解液工作电压:5—9v(5)各材质在电解液内的电流密度(单位为每平方分米),200系列15—25安培,300系列10—15安培,400系列20—30安培。
电化学抛光技术简介ppt课件
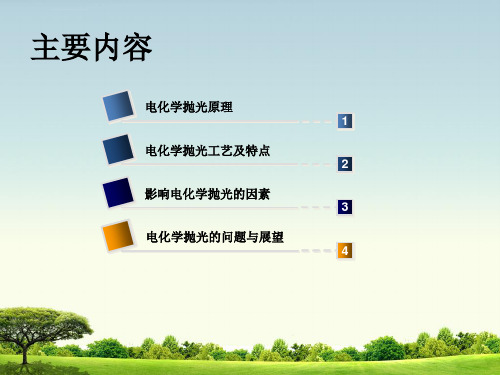
为深入学习习近平新时代中国特色社 会主义 思想和 党的十 九大精 神,贯彻 全国教 育大会 精神,充 分发挥 中小学 图书室 育人功 能
进一步阐明电化学抛光的机理, 开发新的电化学抛光技术和 研究新的抛光液, 实现电化学抛光过程的自动化和智能化, 提 高电化学抛光的质量和抛光效率, 是电化学抛光的主要研究 方向。
为深入学习习近平新时代中国特色社 会主义 思想和 党的十 九大精 神,贯彻 全国教 育大会 精神,充 分发挥 中小学 图书室 育人功 能
为深入学习习近平新时代中国特色社 会主义 思想和 党的十 九大精 神,贯彻 全国教 育大会 精神,充 分发挥 中小学 图书室 育人功 能
影响电化学抛光效果的因素
2.电流密度 电流密度太小, 抛光时间长, 工作效率低; 电流密度太
大, 因阳极溶解过快易出现浸蚀。另外, 电解时间和电解温 度也对抛光效果有一定的影响。
电化学抛光技术的发展与展望
目前, 在工件特种抛光方面对脉冲电化学的研究正方兴未艾, 随着对模具镜面效果的大量需求和微细电化学理论的完善, 脉冲电化学抛光技术在材料表面微、纳米级加工领域的抛光 能力会大大提高,并且将发挥越来越重要的作用。
电化学抛光因其速度快、劳动强度小、不受抛光工件形状 限制及抛光质量好等优点得到人们的关注。
电化学抛光液中加入少量添加剂, 可显著改善溶液的抛光效 果。刘爱华等研究发现: 含羟基( -OH) 、羧基( - COOH) 类 添加剂主要起缓蚀作用; 含胺基( - NH2) 、环烷烃类添加剂 主要起整平作用; 糖类及其它杂环类添加剂主要起光亮作用。 但它们的作用并非截然分开, 相互匹配可起到多功能作用。
铝合金电化学抛光工艺_胡拥军

图 3 电流对抛光的影响 Fig. 3 Current s effect on polishing 最后在此基础上作 了综 合试 验, 工艺 条件 为: NaOH 16 g/ L, PEG 28 mL/ L, Na2CO3 30 g/ L , 酒石酸钠 8 g/ L, 葡萄糖 酸钠 8 g/ L, 电流密度 25 A/ dm2 , 操作电压 6. 5 V, 温度 50 , 抛光时间 15 min。 抛光后铝材表面反射率为 87%、铝 材损耗为 0. 017 4 g/ cm2、溶液 中 Al3+ 浓度为 30 g/ L 时, 抛光 后铝表 面反 射率 仍可达 81%。综 合比较抛光效果、操作 环境、能耗、溶液使 用寿 命、铝 材损 耗和生 产成本等, 此方法与酸性电化学抛光法和经 典碱性电化学抛光法 ( Brytal 法[ 4] ) 相比都有较大的优点 ( 采用 Brytal 法时, 操 作温度为 82 , 电压 10~ 12 V , 抛光时间 30 min, 获得 的反射 率 88%, 铝材 损耗为 0. 021 6 g/ cm2, 且 Al3+ 达到 20 g/ L就不能进行抛光) 。
3结 论
( 1) 选用 PEG 作 光亮 剂 可以 明 显改 善 整 平效 果, 加 快 抛光 速度。
( 2) 加入合适稳定剂可以延长抛光溶液使用周期。 ( 3) 试验获得了最佳工艺条件, 其溶液组成 为: PEG 28 mL/ L、 Na2CO3 30 g/ L、酒石酸 钠 8 g / L、葡萄糖 酸钠 8 g/ L, 操作电 压 6. 5 V, 电流密度 25 A/ dm2 。 ( 4) 采用上述工艺对铝 材抛光 获得的 表面 反射率 高、操作温 度低、工作环境好、铝材损耗 小、生产成本 低, 综合效 果优 于酸性 电化学抛光和碱性 Brytal 抛光。