电化学抛光工艺及影响因素
电解抛光技术(优.选)

影响电解抛光效果的主要因素:一、电解抛光电解液,电解液选用的合理与否是直接影响电解抛光效果的最基本因素之一。
1扩散系数小,黏度大。
2易与溶解下来的金属离子形成扩散速度更小的多核聚合配合物。
本身是一种黏膜稠的酸。
二、电解抛光电流密度和电压,通常应控制在极限扩散电流控制区,中阳极极化曲线的平坦区。
1低于此区的电流密度时,表面会出现腐蚀。
2高于此电流密度区时,因有氧气析出,表面易出现气孔、麻点或条纹。
3平坦区不是固定不变的,它会随温度、配位剂的浓度和添加剂的种类而变化。
三、温度,温度对阳极极化曲线的影响曲线。
1电解液温度升高,极限扩散电流逐渐增大,当温度高于90度时,表面抛光的起始电流密度大,阳极铜片的溶解速度过快,因而铜片表面易生成点状或条状腐蚀。
2当电解液温度低于60度时,传质过程慢,抛光的起始电流密度太低,阳极铜片的溶解速度慢,溶解下来的离子不能很快地扩散开来,容易在阳极表面形成CU和HEDP的多核配合物,使用权铜片表面出现沉淀物膜槿麻点。
四、抛光时间。
1被抛光零件的材质及其表面的预处理程度。
2阳、阴极间的距离。
3电解液的抛光性能及温度。
4电抛光过程使用的阳极电流密度的大小及槽电压的高低。
5工艺上对抛光表面光亮度的要求等。
五、阳极、阴极极间距离。
1便于调整电流密度到工艺规范,并尽量使抛光件表面的电流密度分布得均匀一致些。
2尽量减少不必要的能耗,因电解液浓度高、电阻大、耗电量较大。
3阴极产生的气体搅拌是否已破坏了黏液层,降低了抛光效果。
六、抛光前工件表面状态及金相组织。
1被抛光工件表面的金相组织越均匀,越细密,(如纯金属)越有利于抛光过程的进行,而且抛光效果也越好。
2被抛光工件的材料为合金,特别是多组分合金时,抛光工艺的控制比较麻烦。
3当被抛光工件的金相组织不均匀,特别是含有非金属万分时,就会使电抛光体系呈现出不一致的电化学敏感性。
4工件在抛光前表面处理得越干净越细密,越有利于电抛光过程的进行,越容易获得预期的抛光效果。
金属表面的电化学抛光全解
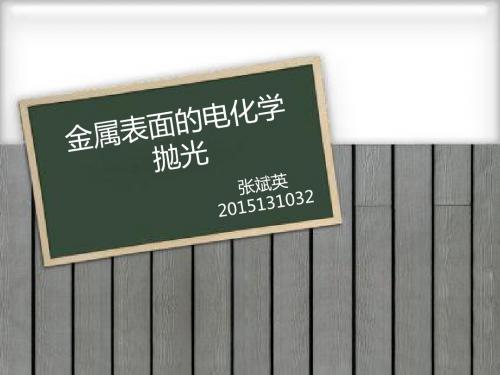
三、铝的电化学抛光
铝在化学抛光时,表)速度快,而低凹部位的溶解(腐蚀)速 度小,形成局部阳极,发生部分钝化作用,溶解速度慢所致。 Fischer和和Koch等科学家研究了高纯铝的抛光过程,并根据抛 光过程中铝的溶解速度、逸出气体量及腐蚀电流密度等实验数据, 得出铝在化学抛光中发生的化学反应是由于形成(-)Al/酸(或 碱)/氧化还原体系/惰性金属(+)构成局部电池发生氧化-还原 反应的结果。化学抛光机理模型如下图(1)
二、金属的电化学抛光
电化学抛光又称为电解抛光,是一种在特殊条件 下的电化学腐蚀,它是通过控制金属表面选择性的溶 解,使金属表面微观突出部位较其凹洼部位优先溶解, 而达到表面平整和光亮的目的。以铝电解抛光为例: 铝材做为阳极浸入到配置好的电解质溶液中,以耐腐 蚀且导电性良好的材料做为阴极,根据电化学尖端放 电原理,通电后的铝材表面微小突出部位优先溶解, 与此同时溶解产物与表面的电解液形成高电阻的粘稠 性液膜层,微小突出部位的液膜层较薄,其电阻较小, 从而继续保持优先溶解。同时表面凹洼部位的液膜层 厚,电阻大,凹洼部位的溶解速度相对缓慢,经过短 时间电解处理后,突出部位被溶解整平至凹洼部位的 位置,铝材表面粗糙度降低达到平滑光亮。
一、电极的极化现象
金属的电化学腐蚀热力学分析是判断金属 材料在腐蚀介质中的腐蚀倾向,即判断金属是 否会发生腐蚀,而金属的电化学腐蚀动力学分 析是探究腐蚀作用的动力学规律来解决腐蚀反 应发生、腐蚀扩展机制和原理以及腐蚀发生和 扩展的速度等问题。 根据热力学研究可知,当电化学反应的阳 极氧化反应和阴极还原反应的反应速度大小相 等,则整个反应处于稳定平衡态。且电极电位 处于该电极反应的平衡电极电位。
四、电化学抛光的阳极极化曲线
图1-1(a)为处于活化状态的极化曲线,如图示 电流密度随阳极金属溶解作用均随阳极电位的提高而 增大,阳极金属表面一直处于电化学阳极溶解状态 (又称活化状态)。铁在盐酸中的电化学阳极极化曲 线就属于这一类型。
电化学抛光内容

电化学抛光
抛光液组成:含铬酸的不锈钢电解抛光液(配方一般是磷酸+硫酸+铬酸+甘油或明胶)
电化学抛光也称电解抛光。
1.定义:电解抛光是以被抛工件为阳极,不溶性金属为阴极,两极同时浸入到电解槽中,通以直流电而产生有选择性的阳极溶解,从而达到工件表面光亮度增大的效果。
2.原理:工件作为阳极接直流电源的正极。用铅﹑不锈钢等耐电解液腐蚀的导电材料作为阴极﹐接直流电源的负极。两者相距一定距离浸入电解液(一般以硫酸﹑磷酸为基本成分)中﹐在一定温度﹑电压和电流密度(一般低于1安/厘米2 )下﹐通电一定时间(一般为几十秒到几分)﹐工件表面上的微小凸起部分便首先溶解﹐而逐渐变成平滑光亮的表面。
阳极电流密度,DA 6–15A/dm2 最佳10–12A/dm2 电压 5–8 伏 抛光时间 3–5分钟 阴极材料 铅或铅合金 阴极面积∶阳极面积 2–3∶1
三、开槽步骤
WB-260添加剂是一种表面活性剂,在其使用初期电解抛光时会产生大量泡沫,因此抛光液液面与抛光槽顶部之间的距离不应≤15cm。准确计算将欲配制的电解抛光液的体积,再根据抛光液组成将所要加入的抛光液各组分按下列顺序加入抛光槽内。
六、环保性能
1.钝化液不含有害物资,有SGS检测证书。
2.废水中和处理后可直接排放,对环境无影响
七、槽液维护及补加
1 不锈钢工件在进入抛光槽之前应尽可能将残留在工件表面的水份除去,因工件夹带过多水份有可能造成抛光面出现严重的麻点,局部浸蚀而导致工件报废.
2长时间不通电情况下,应将阴极的铅板或不锈钢板取出清洗,除去酸液。
1.电抛光后,表面为什么会发现似未抛光的斑点或小块?原因分析:抛光前除油不彻底,表面尚附有油迹。解决方法:选用“云清牌 除油除蜡液”,1:10兑水使用,60-90℃条件下浸泡5-20分钟。如长时间使用后应考虑更换新液。
电解抛光工艺(3篇)
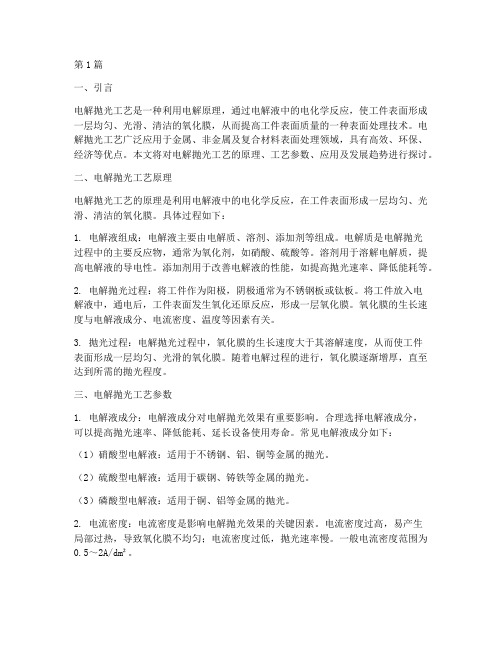
第1篇一、引言电解抛光工艺是一种利用电解原理,通过电解液中的电化学反应,使工件表面形成一层均匀、光滑、清洁的氧化膜,从而提高工件表面质量的一种表面处理技术。
电解抛光工艺广泛应用于金属、非金属及复合材料表面处理领域,具有高效、环保、经济等优点。
本文将对电解抛光工艺的原理、工艺参数、应用及发展趋势进行探讨。
二、电解抛光工艺原理电解抛光工艺的原理是利用电解液中的电化学反应,在工件表面形成一层均匀、光滑、清洁的氧化膜。
具体过程如下:1. 电解液组成:电解液主要由电解质、溶剂、添加剂等组成。
电解质是电解抛光过程中的主要反应物,通常为氧化剂,如硝酸、硫酸等。
溶剂用于溶解电解质,提高电解液的导电性。
添加剂用于改善电解液的性能,如提高抛光速率、降低能耗等。
2. 电解抛光过程:将工件作为阳极,阴极通常为不锈钢板或钛板。
将工件放入电解液中,通电后,工件表面发生氧化还原反应,形成一层氧化膜。
氧化膜的生长速度与电解液成分、电流密度、温度等因素有关。
3. 抛光过程:电解抛光过程中,氧化膜的生长速度大于其溶解速度,从而使工件表面形成一层均匀、光滑的氧化膜。
随着电解过程的进行,氧化膜逐渐增厚,直至达到所需的抛光程度。
三、电解抛光工艺参数1. 电解液成分:电解液成分对电解抛光效果有重要影响。
合理选择电解液成分,可以提高抛光速率、降低能耗、延长设备使用寿命。
常见电解液成分如下:(1)硝酸型电解液:适用于不锈钢、铝、铜等金属的抛光。
(2)硫酸型电解液:适用于碳钢、铸铁等金属的抛光。
(3)磷酸型电解液:适用于铜、铝等金属的抛光。
2. 电流密度:电流密度是影响电解抛光效果的关键因素。
电流密度过高,易产生局部过热,导致氧化膜不均匀;电流密度过低,抛光速率慢。
一般电流密度范围为0.5~2A/dm²。
3. 温度:电解液温度对抛光效果有较大影响。
温度过高,易产生气泡,影响抛光质量;温度过低,抛光速率慢。
一般电解液温度范围为20~40℃。
铝制品的电化学抛光
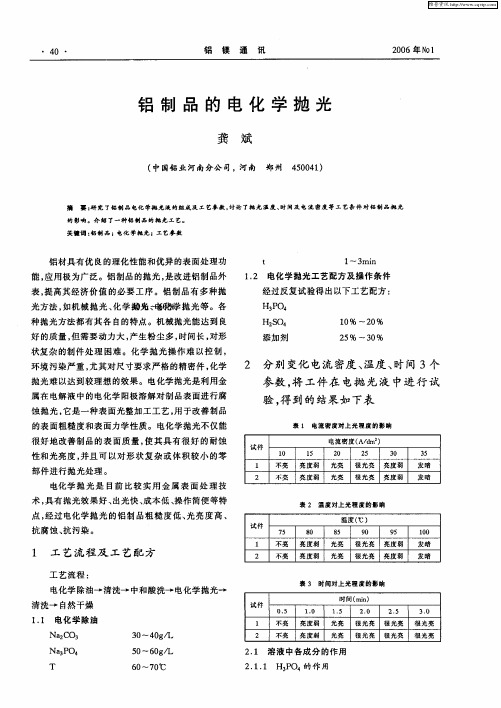
维普资讯
20 0 6年 N l o
铝
镁
通
讯
・4 ・ 1
磷 酸 是 电化 学 抛 光 溶 液 的 主 要成 分 , 抛 光 过 在
程 中溶 解 铝表 面 , 同时 在铝 表面 形成 磷酸 盐保 护膜 ,
3 结论
3 1 当温 度 、 问 在 规 定 范 围 内 , 流 密 度 低 于 . 时 电 2 A/ m2试 件不 亮 , 于 3 A/ m , 件会 发 暗 。 0 d , 高 0 d 试
发 暗
电化 学 除油一 清洗 一 中和酸 洗一 电化 学抛 光一 清 洗一 自然干 燥
1 1 电化学 除 油 .
Na CO3 2 3 — 0g L 0-4 /
试 件
O. 5
表 3 时 间对 上 光 程 度 的影 响 时 间 ( i) a r n
1. O 1. 5 2. O 2. 5 3. O
阻止 铝表 面发 生过 腐蚀 。
2 12 H2 0 的作 用 . . S 4
增加 溶液 的导 电率 , 解铝表 面 , 高光洁 度 。 溶 提
2 13 添加 荆 的作 用 ..
32 当 电 流 密 度 、 间 在 规 定 范 围 内 , 度 低 于 . 时 温 8 ℃ , 件不亮 。温度 高于 9 ℃ , 0 试 5 试件 会 发 暗 。
维普资讯
・
4 ・ 0
铝 镁
通 讯
20 0 6年 N 1 o
铝 制 品 的 电 化 学 抛 光
龚 斌
40 4 ) 5 0 1
( 国铝 业 河南 分公 司 ,河 南 郑 州 中
摘
要 : 兜 了铝 制 品 电化 学抛 光 液 的 组 成厦 工 艺参 数 , 论 了抛 光 温度 、 阐 厦 电 流 密 度 等 工 艺 条 件 对 铝 制 品 抛 光 研 讨 时
电化学抛光技术简介

的电解液及时抽回, 使其不留在模具的型腔中, 从而可方便地显露出抛光的进展状况; ( 7) 仅需轻微接触工件, 减轻了劳动强度, 工作效率高。 ( 8) 不必频繁更换工具, 导电石墨油石接触头可与模具形状自吻合。
7
电化学抛光技术的发展与展望
目前, 在工件特种抛光方面对脉冲电化学的研究正方兴未艾, 随着对模具镜面效果的大量需求和微细电化学理论的完善, 脉冲电化学抛光技术在材料表面微、纳米级加工领域的抛光 能力会大大提高,并且将发挥越来越重要的作用。 电化学抛光因其速度快、劳动强度小、不受抛光工件形状 限制及抛光质量好等优点得到人们的关注。 进一步阐明电化学抛光的机理, 开发新的电化学抛光技术和 研究新的抛光液, 实现电化学抛光过程的自动化和智能化, 提 高电化学抛光的质量和抛光效率, 是电化学抛光的主要研究 方向。
5
影响电化学抛光效果的因素
1.电解液( 抛光液) 的组成 抛光液通常有酸性、中性和碱性抛光液[5] 。
其中酸性抛光液有: 磷酸系、硫酸系、高氯酸系、磷酸 硫酸系, 以及在各系基础上派生出的硫酸 铬酐磷酸 铬酐、 硫酸 磷酸 铬酐, 再配以各种添加剂而成的抛光液。通 用性较好的酸性抛光液为磷酸 硫酸系抛光液。
4
电化学抛光工艺及特点
3.电化学抛光在处理金属表面时, 还有一些不足存在[4] (1) 所得表面质量取决于被加工金属的组织均 匀性和纯度, 金属结构的缺陷被突出地显露出来。 对表面有序化组织敏感性较大; (2) 较难保持零件尺寸和几何形状的精确度; (3) 表面必须预加工到比较高的粗糙度. 很难 在粗加工或砂型铸造零件上获得高的抛光质量。
电解抛光工艺介绍

电解抛光工艺介绍公司标准化编码 [QQX96QT-XQQB89Q8-NQQJ6Q8-MQM9N]电解抛光工艺1.定义:电解抛光是以被抛工件为阳极,不溶性金属为阴极,两极同时浸入到电解槽中,通以直流电而产生有选择性的阳极溶解,从而达到工件表面光亮度增大的效果。
2.原理:电解抛光原理现在世界各界人士争论很多,被大家公认的主要为黏膜理论。
该理论主要为:工件上脱离的金属离子与抛光液中的磷酸形成一层磷酸盐膜吸附在工件表面,这种黏膜在凸起处较薄,凹处较厚,因凸起处电流密度高而溶解快,随黏膜流动,凹凸不断变化,粗糙表面逐渐被整平的过程。
3.电解抛光优点:⑴内外色泽一致,光泽持久,无法抛到的凹处也可整平。
⑵生产效率高,成本低廉。
⑶增加工件表面抗腐蚀性,可适用于所有不锈钢材质。
4.电化学抛光所需条件及设备(1)电源:电源可选用双相220V,三相380V。
(2)整流器电解抛光对电源波形要求不是太严格,可选用可控硅整流器或高频整流器。
整流器空载电压:0—20v负载电压(工作电压):8—10v工作电压低于6v,抛光速度慢,光亮度不足。
整流器电流:根据客户工件大小而定。
(3)电解槽及配套设施(阳极棒)可选用聚氯乙烯硬板材焊接而成。
在槽上装三根电极棒,中间为可移动的阳极棒,接电源阳极(或正极),两侧为阴极棒,连接电源阴极(负极)。
(4)加热设施及冷却设备①加热可选用石英加热管,钛加热管。
②冷却可选用盘管,盘管可加热可冷却。
(5)夹具最好选用钛做挂具,因为钛较耐腐蚀,寿命长,钛离子对槽液无影响。
建议最好不要用铜挂具,因为铜离子进入会在不锈钢表面沉积一层结合力不好的铜层,影响抛光质量。
铜裸露部位可用聚氯乙烯胶烘烤成膜,在接触点刮去绝缘膜。
(6)阴阳极材料阴极材料选用铅板,阳极材料选用紫铜连接。
阳极比阴极为1:2—之间。
阴极距阳极最佳距离为10—30厘米。
就目前来说,电解抛光主要针对不锈钢工件的表面光亮处理。
不锈钢工件又分为200系列,300系列,400系列材质,各系列材质有必须用针对性电解抛光液。
低温电解抛光
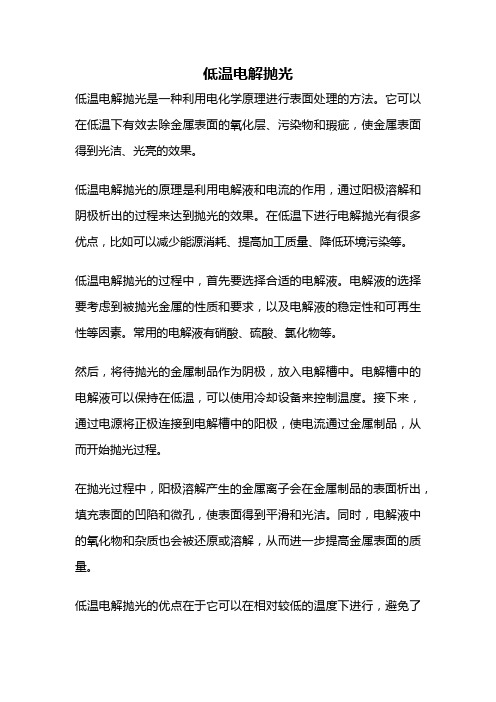
低温电解抛光低温电解抛光是一种利用电化学原理进行表面处理的方法。
它可以在低温下有效去除金属表面的氧化层、污染物和瑕疵,使金属表面得到光洁、光亮的效果。
低温电解抛光的原理是利用电解液和电流的作用,通过阳极溶解和阴极析出的过程来达到抛光的效果。
在低温下进行电解抛光有很多优点,比如可以减少能源消耗、提高加工质量、降低环境污染等。
低温电解抛光的过程中,首先要选择合适的电解液。
电解液的选择要考虑到被抛光金属的性质和要求,以及电解液的稳定性和可再生性等因素。
常用的电解液有硝酸、硫酸、氯化物等。
然后,将待抛光的金属制品作为阴极,放入电解槽中。
电解槽中的电解液可以保持在低温,可以使用冷却设备来控制温度。
接下来,通过电源将正极连接到电解槽中的阳极,使电流通过金属制品,从而开始抛光过程。
在抛光过程中,阳极溶解产生的金属离子会在金属制品的表面析出,填充表面的凹陷和微孔,使表面得到平滑和光洁。
同时,电解液中的氧化物和杂质也会被还原或溶解,从而进一步提高金属表面的质量。
低温电解抛光的优点在于它可以在相对较低的温度下进行,避免了高温处理可能带来的变形和残余应力。
同时,低温电解抛光也可以在较短的时间内完成,提高了加工效率。
此外,该方法还可以在一定程度上修复金属表面的缺陷,提高金属制品的使用寿命。
然而,低温电解抛光也存在一些限制。
首先,电解液的选择和控制对抛光效果有很大影响,需要进行一定的实验和优化。
其次,抛光过程中需要控制电流密度、电解液浓度和温度等参数,以避免出现过度抛光或不足抛光的情况。
此外,低温电解抛光对金属制品的形状和尺寸要求较高,不适用于复杂形状或大尺寸的金属制品。
低温电解抛光是一种高效、环保的表面处理方法。
通过合理选择电解液、控制参数和优化工艺,可以实现金属表面的光洁、光亮效果。
随着科技的不断进步,低温电解抛光技术将在金属制造和加工领域得到广泛应用,为提高产品质量和降低能源消耗做出贡献。
电解抛光工艺及常见问题

电解抛光工艺:除油--水洗--除锈--水洗--电解抛光--水洗--中和--水洗--钝化--包装电解抛光常见问题1.电抛光后,表面为什么会发现似未抛光的斑点或小块?原因分析:抛光前除油不彻底,表面尚附有油迹。
解决方法:选用“云清牌除油除蜡液”,1:10兑水使用,60-90℃条件下浸泡5-20分钟。
如长时间使用后应考虑更换新液。
2.抛光过后表面局部为什么有灰黑色斑块存在?原因分析:可能氧化皮未彻底除干净。
局部尚存在氧化皮。
解决方法:加大清除氧化皮力度,可选用“云清牌不锈钢氧化皮清除液”,“不锈钢氧化皮清除膏”等产品。
因除锈除氧化皮产品较多,具体适用产品可咨询威海云清化工开发院。
3.抛光后工件棱角处及尖端过腐蚀是什么原因引起的?原因分析:棱角、尖端的部位电流过大,或电解液温度过高,抛光时间过长,导致过度溶解。
解决方法:调整电流密度或溶液温度,或缩短时间。
检查电极位置,在棱角处设置屏蔽等。
4.为什么工件抛光后不光亮并呈灰暗色?分析原因:可能电化学抛光溶液已不起作用,或作用不明显。
解决方法:检查电解抛光液是否使用时间过长,质量下降,或溶液成分比例失调。
5.工件抛光后表面有白色的条纹是怎么回事?原因分析:溶液相对密度太大,液体太稠,相对密度大于1.82。
解决方法:增大溶液的搅拌程度,如果溶液相对密度太大,用水稀释至1.72。
在90~100℃条件下并加热一小时。
6.为什么抛光后表面有阴阳面,及局部无光泽的现象?原因分析:工件放置的位置没有与阴极对正,或工件互相有屏蔽。
解决方法:将工件进行适当的调整,使工件与阴极的位置适当,使电力分布合理。
7.抛光后工件表面平整光洁,但有些点或块不够光亮,或出现垂直状不亮条纹,一般是什么原因引起的?原因分析:可能是抛光后期工件表面上产生的气泡未能及时脱离并附在表面或表面有气流线路。
解决方法:提高电流密度,使析气量加大以便气泡脱附,或提高溶液的搅拌速度,增加溶液的流动。
8.零件和挂具接触点无光泽并有褐色斑点,表面其余部分都光亮是什么原因?原因分析:可能是零件与挂具的接触不良,造成电流分布不均,或零件与挂具接触点少。
电化学抛光的特点

C
D
ቤተ መጻሕፍቲ ባይዱ10
A
0
1
2
槽电压/V
3
4
2.4、电化学抛光的机理
2.4.1 电化学抛光机理的研究概况:
电解抛光机理研究的核心集中在金属表面为何能在抛光过程中变得平整和光亮.
2.4.2 阳极宏观整平
紧密固体皮膜
本体溶液 金属 Jacquet层
2.4.3 微观整平或二级电流分布
2.5.4 阴阳极间的距离
阴阳极的选择应兼顾以下几个因素: 1、便于调整电流密度到工艺范围,并使工作表面电流分布均匀,便于取放工件 2、尽量减少不必要的能耗,因为电解液的浓度高、电阻大,耗电量也大 3、阴极产生的气体是否会破坏黏膜层,降低抛光效果
一般阴极距离的设置大的工件距离可以大些,小制件就可以小些。一般取值为70250mm,一般实际应用取150mm为多,如果仅是作去披锋用选用50-80mm即可 对于形状复杂的工件,如有内腔的工件应制作象形阴极予以辅助,以便电流分布均匀抛光 效果一致的产品
Jacquet=加奎得
在电解过程中,由于在阳极上形成 “ 黏液层 ” Viscous Layer 的 结果
电化学抛光与机械抛光法的比较
电化学抛光法 1、通过电抛光的方法使金属表面平滑光亮 2、电解后表面易形成钝化膜 3、电解后表面形成等电势表面,不易粘手印 4、形状复杂、细小的工件都可以处理 5、速度快、产量大,容易满足自动后生产 6、大于 10丝以上的加工纹路难以处理彻底 机械抛光法 1、通过切削、变形和磨耗使金属表面平滑光亮 2、表面引起结晶破坏,无钝化膜形成 3、表面带电荷易粘手印和吸附灰尘 4、难以抛光这一些工件 5、速度慢、生产效率低,难以自动化。成本高 6、处理后不留痕迹
抛光方法种类、基本程序、注意事项以及影响因素

抛光方法种类、基本程序、注意事项以及影响因素1 目前常用的抛光方法有以下几种:1.1机械抛光机械抛光是靠切削、材料表面塑性变形去掉被抛光后的凸部而得到平滑面的抛光方法,一般使用油石条、羊毛轮、砂纸等,以手工操作为主,特殊零件如回转体表面,可使用转台等辅助工具,表面质量要求高的可采用超精研抛的方法。
超精研抛是采用特制的磨具,在含有磨料的研抛液中,紧压在工件被加工表面上,作高速旋转运动。
利用该技术可以达到Ra0.008μm的表面粗糙度,是各种抛光方法中最高的。
光学镜片模具常采用这种方法。
1.2化学抛光化学抛光是让材料在化学介质中表面微观凸出的部分较凹部分优先溶解,从而得到平滑面。
这种方法的主要优点是不需复杂设备,可以抛光形状复杂的工件,可以同时抛光很多工件,效率高。
化学抛光的核心问题是抛光液的配制。
化学抛光得到的表面粗糙度一般为数10μm。
1.3电解抛光电解抛光基本原理与化学抛光相同,即靠选择性的溶解材料表面微小凸出部分,使表面光滑。
与化学抛光相比,可以消除阴极反应的影响,效果较好。
电化学抛光过程分为两步:(1)宏观整平溶解产物向电解液中扩散,材料表面几何粗糙下降,Ra>1μm。
(2)微光平整阳极极化,表面光亮度提高,Ra<1μm。
1.4超声波抛光将工件放入磨料悬浮液中并一起置于超声波场中,依靠超声波的振荡作用,使磨料在工件表面磨削抛光。
超声波加工宏观力小,不会引起工件变形,但工装制作和安装较困难。
超声波加工可以与化学或电化学方法结合。
在溶液腐蚀、电解的基础上,再施加超声波振动搅拌溶液,使工件表面溶解产物脱离,表面附近的腐蚀或电解质均匀;超声波在液体中的空化作用还能够抑制腐蚀过程,利于表面光亮化。
1.5流体抛光流体抛光是依靠高速流动的液体及其携带的磨粒冲刷工件表面达到抛光的目的。
常用方法有:磨料喷射加工、液体喷射加工、流体动力研磨等。
流体动力研磨是由液压驱动,使携带磨粒的液体介质高速往复流过工件表面。
电化学抛光简介PPT课件

10
Thank You!
11
3
电化学抛光工艺及特点
1设备及工艺流程[2]
设备有: 电解槽、清洗槽、阳极架辅助阴极( 铅
板、石墨板) 、直流电源等。
工艺流程: 装料 除油
清洗 除锈
清洗 抛光 清洗
钝化 清洗
晾干 卸料
4
电化学抛光工艺及特点
2.电化学抛光作为一种金属表面处理方法, 它具有以下优点[3] :
( 1) 不受材料硬度和韧性的限制, 几乎所有的模具材料都可进行电解抛光; ( 2) 电化学抛光可对模具表面起整平作用; ( 3) 可抛光各种较复杂的型腔; ( 4) 经电化学抛光后的表面无任何条纹; ( 5) 抛光速度快慢可方便调节电化学抛光速度与电流大小成正比。电流大, 阳极( 工件) 溶
5
电化学抛光工艺及特点
3.电化学抛光在处理金属表面时, 还有一些不足存在[4] (1) 所得表面质量取决于被加工金属的组织均 匀性和纯度, 金属结构的缺陷被突出地显露出来。 对表面有序化组织敏感性较大; (2) 较难保持零件尺寸和几何形状的精确度; (3) 表面必须预加工到比较高的粗糙度. 很难 在粗加工或砂型铸造零件上获得高的抛光质量。
[ 电化学抛光简介 ]
1
主要内容
电化学抛光原理 1
电化学抛光工ቤተ መጻሕፍቲ ባይዱ及特点 2
影响电化学抛光的因素 3
电化学抛光的问题与展望 43
2
电化学原理
电化学抛光是金属阳极溶解的独特电解过程,它受众多可变因素的影响。根据阳极金属 的性质、电解液组成、浓度及工艺条件的不同, 在阳极表面上
• 可能发生下列一种或几种反应[1] :
( 1) 金属氧转化成金属离子溶人到电解液中
不锈钢的电解抛光工艺
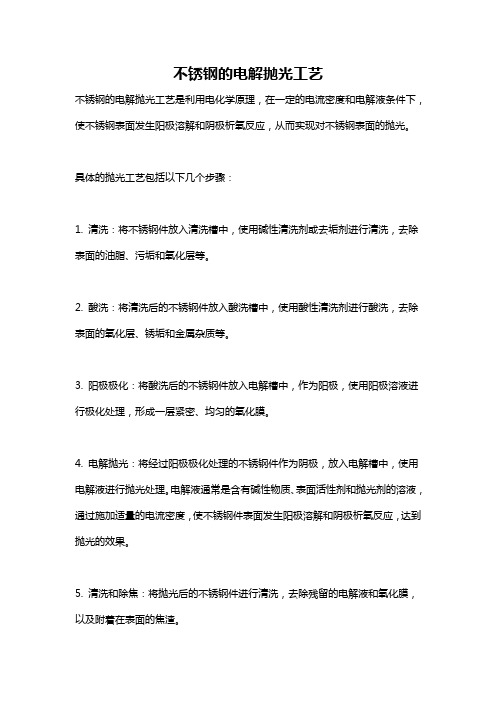
不锈钢的电解抛光工艺
不锈钢的电解抛光工艺是利用电化学原理,在一定的电流密度和电解液条件下,使不锈钢表面发生阳极溶解和阴极析氧反应,从而实现对不锈钢表面的抛光。
具体的抛光工艺包括以下几个步骤:
1. 清洗:将不锈钢件放入清洗槽中,使用碱性清洗剂或去垢剂进行清洗,去除表面的油脂、污垢和氧化层等。
2. 酸洗:将清洗后的不锈钢件放入酸洗槽中,使用酸性清洗剂进行酸洗,去除表面的氧化层、锈垢和金属杂质等。
3. 阳极极化:将酸洗后的不锈钢件放入电解槽中,作为阳极,使用阳极溶液进行极化处理,形成一层紧密、均匀的氧化膜。
4. 电解抛光:将经过阳极极化处理的不锈钢件作为阴极,放入电解槽中,使用电解液进行抛光处理。
电解液通常是含有碱性物质、表面活性剂和抛光剂的溶液,通过施加适量的电流密度,使不锈钢件表面发生阳极溶解和阴极析氧反应,达到抛光的效果。
5. 清洗和除焦:将抛光后的不锈钢件进行清洗,去除残留的电解液和氧化膜,以及附着在表面的焦渣。
6. 中和和涂层:将清洗后的不锈钢件放入中和槽中,使用中和剂中和表面的残留酸性物质。
最后,根据需要,可以将不锈钢件进行喷涂或溅射等表面涂层处理,以增加其抗腐蚀性能和装饰性能。
需要注意的是,电解抛光工艺中的参数设置和电解液配方都需要根据具体的不锈钢材质和要求进行调整,以达到最佳的抛光效果。
同时,操作人员也需要掌握相关的操作技术和安全知识,确保操作过程的安全性和效果。
电解抛光工艺流程

电解抛光工艺流程
电解抛光工艺是一种利用电化学原理进行表面处理的技术,可以使金属表面获得更好的光亮度和平滑度。
下面将介绍一下电解抛光工艺的流程。
首先,为了保证电解抛光的效果,需要选取合适的电解液。
常用的电解液有硫酸、盐酸、氢氟酸等。
根据不同的金属材料、抛光要求和工艺条件选择合适的电解液。
其次,准备好工件,并进行表面处理。
通常情况下,工件会经过机械的打磨、抛光、清洗等步骤,以获得相对平滑和光洁的表面。
然后,将工件放入电解槽中。
电解槽应选用耐腐蚀、绝缘性能好的材料制作,以确保电解液的稳定性和安全性。
接着,将阴极和阳极连接到电源上。
阴极可以选择不锈钢、铝等金属,阳极则是工件本身。
电源的电压和电流需要根据具体的工件材料和抛光要求进行调整。
在工作过程中,需要控制好电流密度和工件与电解液的距离。
电流密度太低会导致抛光效果差,电流密度太高则容易导致表面粗糙度增大。
而工件与电解液的距离过远会使电解液的流动性变差,影响整个抛光过程。
抛光时间的长短也会影响抛光效果。
通常情况下,抛光时间较长可以使工件表面更加光滑,但时间过长也会导致表面腐蚀和
材料的损失。
最后,完成抛光后,将工件从电解槽中取出,并进行清洗和干燥处理。
清洗可以去除表面的电解液残留物和杂质,干燥可以防止工件表面重新氧化。
总的来说,电解抛光是一种高效、易于控制和操作的表面处理工艺。
通过合理调整电解液、电流密度和工艺条件,可以获得理想的抛光效果。
但是需要注意的是,电解抛光过程中需要严格遵守安全操作规范,避免发生意外事故。
电化学抛光的基本原理与特点、抛光方式以及影响因素

电化学抛光一电化学抛光的基本原理和特点1、基本原理如图7-6:零件接直流电源的阳极,耐腐蚀材料(不锈钢或铝材)作为工具接负极,将零件、工具放入电解液槽中,形成电路产生电流,阳极失去电子产生溶解现象,表面被不断蚀除,随着溶解的进行,在阳极表面会生成黏度高、电阻大的氧化物薄膜,凸出处较薄,电阻较小,电流密度比凹处大,这样突出处先被溶解,从而降表面低粗糙度,达到抛光的目的。
2、特点①电化学抛光量很小,抛光后的尺寸精度和形状精度可控制在0.01mm以内。
②电化学抛光效率高,抛光速度不受材料的软硬而影响。
③工艺简单,操作容易,设备简单,投资小。
④电化学抛光不能消除原表面的“粗波纹”,对工件表面的基体粗糙度有要求,一般应为Ra1.6以下才好。
二影响电化学抛光质量的因素决定(电镀手册)1、电解液电解液的配方和比例要根据加工零件和选用的阴极材料来2、电流密度电化学抛光都是在较高的电流密度下进行的,过高时,阳极析出的氧气过多,使电解液近似沸腾,又会影响抛光质量。
3、电解液的温度一般情况下,温度低,溶解速度低,生产效率就低,此外对电解液应进行搅拌,促使流动,及时排除电解产物,减少温度梯度。
4、抛光时间抛光的时间不能太长,一般都有一个最佳抛光时间。
5、工件的金相组织状态愈均匀、致密抛光效果就愈好。
非金属成分多抛光效果差。
象铸铁就不宜进行电化学抛光。
6、抛光表面的原始粗糙度一般情况下,原始粗糙度要求在2.5-0.8时,采用电化学抛光才能有较好的效果。
三抛光的方式1、整体电化学抛光法(图7-7)直流电源0-50V,电流密度为80-100A/dm2,上下伺服控制,左右前后拖板调节,间隙5-10mm,液面高出15-20阴极采用不锈钢、铅或石墨,不断搅拌电解液,保持工作温度。
2、逐步电化学抛光法(图7-8为DMP-10型电化学修研抛光机)脉冲直流电源0-24V无级调节,最大输出电流10A,脉冲波为矩形,160W的电动抛光器,抛光轮的转速为8000-20000 r/min无级调速,快速擦除电化学生产的氧化膜。
铝合金电化学抛光工艺_胡拥军

图 3 电流对抛光的影响 Fig. 3 Current s effect on polishing 最后在此基础上作 了综 合试 验, 工艺 条件 为: NaOH 16 g/ L, PEG 28 mL/ L, Na2CO3 30 g/ L , 酒石酸钠 8 g/ L, 葡萄糖 酸钠 8 g/ L, 电流密度 25 A/ dm2 , 操作电压 6. 5 V, 温度 50 , 抛光时间 15 min。 抛光后铝材表面反射率为 87%、铝 材损耗为 0. 017 4 g/ cm2、溶液 中 Al3+ 浓度为 30 g/ L 时, 抛光 后铝表 面反 射率 仍可达 81%。综 合比较抛光效果、操作 环境、能耗、溶液使 用寿 命、铝 材损 耗和生 产成本等, 此方法与酸性电化学抛光法和经 典碱性电化学抛光法 ( Brytal 法[ 4] ) 相比都有较大的优点 ( 采用 Brytal 法时, 操 作温度为 82 , 电压 10~ 12 V , 抛光时间 30 min, 获得 的反射 率 88%, 铝材 损耗为 0. 021 6 g/ cm2, 且 Al3+ 达到 20 g/ L就不能进行抛光) 。
3结 论
( 1) 选用 PEG 作 光亮 剂 可以 明 显改 善 整 平效 果, 加 快 抛光 速度。
( 2) 加入合适稳定剂可以延长抛光溶液使用周期。 ( 3) 试验获得了最佳工艺条件, 其溶液组成 为: PEG 28 mL/ L、 Na2CO3 30 g/ L、酒石酸 钠 8 g / L、葡萄糖 酸钠 8 g/ L, 操作电 压 6. 5 V, 电流密度 25 A/ dm2 。 ( 4) 采用上述工艺对铝 材抛光 获得的 表面 反射率 高、操作温 度低、工作环境好、铝材损耗 小、生产成本 低, 综合效 果优 于酸性 电化学抛光和碱性 Brytal 抛光。
电化学抛光工艺(3篇)
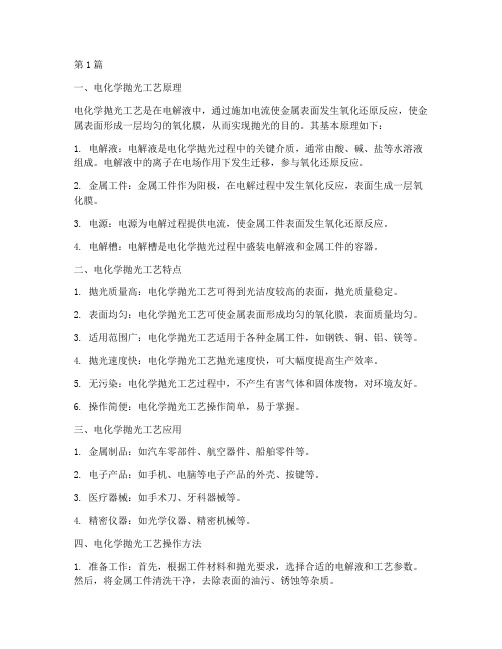
第1篇一、电化学抛光工艺原理电化学抛光工艺是在电解液中,通过施加电流使金属表面发生氧化还原反应,使金属表面形成一层均匀的氧化膜,从而实现抛光的目的。
其基本原理如下:1. 电解液:电解液是电化学抛光过程中的关键介质,通常由酸、碱、盐等水溶液组成。
电解液中的离子在电场作用下发生迁移,参与氧化还原反应。
2. 金属工件:金属工件作为阳极,在电解过程中发生氧化反应,表面生成一层氧化膜。
3. 电源:电源为电解过程提供电流,使金属工件表面发生氧化还原反应。
4. 电解槽:电解槽是电化学抛光过程中盛装电解液和金属工件的容器。
二、电化学抛光工艺特点1. 抛光质量高:电化学抛光工艺可得到光洁度较高的表面,抛光质量稳定。
2. 表面均匀:电化学抛光工艺可使金属表面形成均匀的氧化膜,表面质量均匀。
3. 适用范围广:电化学抛光工艺适用于各种金属工件,如钢铁、铜、铝、镁等。
4. 抛光速度快:电化学抛光工艺抛光速度快,可大幅度提高生产效率。
5. 无污染:电化学抛光工艺过程中,不产生有害气体和固体废物,对环境友好。
6. 操作简便:电化学抛光工艺操作简单,易于掌握。
三、电化学抛光工艺应用1. 金属制品:如汽车零部件、航空器件、船舶零件等。
2. 电子产品:如手机、电脑等电子产品的外壳、按键等。
3. 医疗器械:如手术刀、牙科器械等。
4. 精密仪器:如光学仪器、精密机械等。
四、电化学抛光工艺操作方法1. 准备工作:首先,根据工件材料和抛光要求,选择合适的电解液和工艺参数。
然后,将金属工件清洗干净,去除表面的油污、锈蚀等杂质。
2. 电解液配制:按照配方配制电解液,确保电解液的浓度、pH值等符合要求。
3. 工艺参数设置:根据工件材料和抛光要求,设置合适的电流密度、电解液温度、处理时间等工艺参数。
4. 抛光过程:将工件放入电解槽中,通电进行抛光。
在抛光过程中,观察工件表面变化,适时调整电流密度、电解液温度等参数。
5. 清洗与干燥:抛光完成后,将工件从电解槽中取出,用清水冲洗干净,去除表面的电解液和氧化膜。
航空标准不锈钢电化学抛光_解释说明

航空标准不锈钢电化学抛光解释说明1. 引言1.1 概述引言部分旨在介绍本篇文章的主题和背景。
航空标准不锈钢电化学抛光是一种在航空领域中常见的表面处理技术,用于提高航空器不锈钢表面的质量和光洁度。
本文将对该技术的原理、方法及其在航空领域中的应用研究进行详细探讨。
1.2 文章结构本文分为五个主要部分: 引言、航空标准不锈钢电化学抛光的原理与方法、航空标准不锈钢电化学抛光在航空领域中的应用研究与实践、未来发展方向与展望以及结论。
每个部分都有其特定的内容和目标,通过这种结构,我们可以全面了解这项技术及其在航空领域中的重要性。
1.3 目的本文旨在介绍航空标准不锈钢电化学抛光技术,并探讨该技术在航空领域中的应用情况。
通过深入研究该技术的原理与方法,我们可以了解其对航空标准不锈钢表面质量的影响,并分析其在航空器表面处理中的重要性和挑战性。
此外,我们还将就未来发展方向提出展望并提供建议。
通过本文的撰写,旨在促进该技术的进一步研究与应用。
2. 航空标准不锈钢电化学抛光的原理与方法2.1 不锈钢电化学抛光的基本原理航空标准不锈钢电化学抛光是一种通过在电解液中施加恒定的电压,利用阳极氧化和阳极溶解来改善不锈钢表面光洁度和质量的方法。
该方法基于阳极处发生的氧化反应和阴极处发生的溶解反应,通过控制电流密度、电解液成分和温度等参数来实现对不锈钢表面质量的调控。
2.2 航空标准不锈钢的电化学抛光方法航空标准不锈钢电化学抛光方法主要包括以下步骤:首先,选择适当的电解液。
常用的电解液包括硫酸、硝酸、磷酸等,其浓度和配方需要根据具体需要进行调整。
然后,准备工作件并进行预处理。
将航空标准不锈钢材料切割为所需形状,并进行去污、清洗等预处理步骤,以确保表面无杂质和油脂。
接下来,将工作件置于电化学抛光设备中。
通过调节电解槽的电流密度、温度和处理时间等参数,控制阳极氧化和阳极溶解反应的进行。
在抛光过程中,应确保工作件与电极之间的距离适当,并保证良好的电流传导。
- 1、下载文档前请自行甄别文档内容的完整性,平台不提供额外的编辑、内容补充、找答案等附加服务。
- 2、"仅部分预览"的文档,不可在线预览部分如存在完整性等问题,可反馈申请退款(可完整预览的文档不适用该条件!)。
- 3、如文档侵犯您的权益,请联系客服反馈,我们会尽快为您处理(人工客服工作时间:9:00-18:30)。
电化学抛光工艺及影响因素
钢铁工件的电化学抛光工艺和其他金属的抛光工艺一样,主要由拋光前处理、电化学抛光过程和抛光后的处理三大部分组成,每一部分都是必不可少的。
电化学抛光前的表面预处理主要是除油除锈(或膜),如果处理得不好、不彻底干净,将会严重影响表面的抛光效果和质量,同时还把表面的油、锈等污物带进电抛光液,影响后续工件的抛光质量、毒化抛光溶液的性能甚至缩短溶液的寿命。
电化学抛光时如不严格按照操作规程进行则直接影响工件的表面抛光质量。
抛光后的表面,不管抛光质量如何,如果不及时进行处理则会马上生锈,或者由于清洗不干净、处理不彻底、抛光表面尚有酸迹,当遇到潮湿的大气后也会很快腐蚀生锈。
很多钢铁工件的电化学抛光不是最后工序,而仅是中间工序,抛光后接着要电镀或涂装,如果抛光表面清洗不干净,将会在工件表面埋下隐患。
普通碳素钢是应用得最广最多的钢铁材料之一,有许多用碳素钢经过机械加工的零件需要抛光处理作为中间工序或最后工序。
电化学抛光最适合用于碳素钢的处理上,现以国产的Q235普通碳素钢工件为例说明钢铁件电化学抛光工艺操作过程及步骤。
文章编辑:抛光机第一品牌——郑州中原抛光机械总厂http://www.paoguangji8
推荐文章:
去毛刺机
去毛刺抛光机
钢领抛光机
钢筘抛光机
综丝抛光机
织针抛光机
抛光磨料
⊕
呋嗯呌抛光机。