压铸工艺流程与压射压力
压铸工艺流程与压射压力

压铸工艺流程与压射压力1. 压铸工艺流程概述压铸是一种常用的金属成形工艺,通过将金属加热至液态状态后注入模具,利用高压将金属充填模具腔体并固化成型。
压铸工艺具有生产效率高、生产周期短、成本低等优点,广泛应用于汽车、电子、机械等行业。
1.1 准备工作在进行压铸前,需要准备好原材料、模具、压铸设备等工艺条件。
原材料通常为铝合金、锌合金等金属材料,模具则根据产品要求设计制造。
1.2 压铸工艺步骤1.模具装配:将模具安装到压铸机上。
2.加热金属:将金属材料加热至液态状态。
3.灌注金属:将加热好的金属注入模具中。
4.施加压力:利用压铸机施加高压,将金属充填模具腔体。
5.冷却固化:金属在模具中冷却固化。
6.取出件:取出成型好的零件。
1.3 后续处理压铸完成后,可能需要进行去毛刺、砂光、热处理等后续处理工艺,以提高产品表面质量和性能。
2. 压射压力的重要性压射压力是指在压铸过程中施加的金属注射压力,是影响产品质量和成形效果的重要参数。
2.1 作用1.填充模具:适当的压射压力可以保证金属充分填充模具腔体,避免产生气孔、缺陷等质量问题。
2.提高密度:高压可以压实金属,提高成形件的密度,增强材料性能。
3.细化晶粒:适当的压射压力可以促使金属晶粒细化,改善材料组织结构。
2.2 设置方法1.根据材料:不同金属材料需要不同的压射压力,应根据材料特性设置合适的压力值。
2.试验确定:可通过工艺试验确定最佳的压射压力值,以达到最佳的成形效果。
3.监控调整:在生产过程中应定期监控压射压力,并根据需要进行调整,确保产品质量。
3. 压铸工艺流程和压射压力的关系压铸工艺流程中的压射压力直接影响着成形件的质量和性能,合理控制压射压力是保障产品质量的关键。
3.1 压射压力调整1.初次调整:首次进行压射时,可根据模具设计、金属流动性等因素进行初次调整。
2.在线调整:在生产过程中,应根据产品质量情况实时调整压射压力,确保产品合格率。
3.优化控制:可通过数据分析、工艺优化等手段,进一步优化和控制压射压力,提高成形效率和质量。
压铸工艺原理和过程

压铸工艺过程压铸工艺过程是由压铸机来完成的。
压铸机相据压室的工作条件分为热压室压铸机和冷压多压铸机两大类,而冷压常压铸机又根据压室的布置形式分为卧式和立式两类。
各种压铸机的压铸基本过程都为合模、压射、增压、持压、开模。
图1-1所示为热压室帐铸机压铸过程,图1-2所示为卧式冷压室压铸机压铸过程。
图1-3所示为立式冷压室压铸机压铸过程,图1-4所示为升举压室压铸机压铸过程。
二、压铸工艺原理从本质上来说,压铸过程与其他各种铸造过程一样都是液态合金的流动与传热过程和凝固过程,也就是动量传递、质量传递和能量传递过怪及相变过程,都是基本物理过程。
都遵循自然界中关于物质运动的动量守恒原理、质量守恒原理和能量守恒原理及相变原理。
所以压铸过程中液态合金的流动与传热问题和凝固问题也都可以由建立在动量守恒、质量守恒和能量守恒定律基础上的动量方程、连续方程、能量方程及相变(凝固)理论来描述。
但是,压铸过科又有其特殊之处,这就是压铸过程是在高压、高速条件下进行的,使得液态合金充填型腔时的形态与其他铸造方法的充填形态具有很大的差别,因而理解压力和速度在压铸过程中的作用和变化,对液态合金流动(充填)形态的影响是必要的。
压铸压力和压铸速度1、压铸压力压铸压力是压铸工艺中主要参数之一。
通常用压射力和压射比压来表示。
(1)压射力压射力可分为充填压射力和增压压射力。
充填压射力指充填过程中的压射力,其值由式(1-1)进行计算,即F y=p g A D ((1-1)式中F y—充填压射力,kN;Pg —压铸机液压系统的管路工作压力,kPa;A D—压铸机压射缸活塞截面积,m2增压压射力则是指增压阶段原压射力,其值由式(1-2)进行讲算,即F yz=p gz A D(1-2)式中Fyz—增压压射力,kN;Pgz—压铸机压射缸内增压后的液压压力,kPa(2)压射比压压射比压是指压室内与压射冲头接触的金属液在单位面积上所受到的压力压力射比压和增压比压。
压铸工艺流程图示资料

一、压铸(BODY)工艺流程图示1,压铸机调试2,压铸模安装4,模具预热、涂料7,合型(合模)10浇注压射11,保压12,开模、抽芯取件14,清理(整修)17,终检验3,压铸模设计与制造5,涂料配制6,模具清理8,合金熔炼保温9,嵌件准备13,表面质量检查15,时效处理16,铸件浸渗、喷丸处理二、压射压力P3 P4压力P2P1 P2P1T1 t2 t3 t4 保压时间升压充填增压注:t1 金属液在压室中未承受压力的时间;P1为一级(慢速)t2 金属液于压室中在压射冲头的作用下,通过内浇口充填型腔的时间;P2为二级(快速)t3 充填刚刚结束时的舜间;P3为三级(增压)t4 最终静压力;P4为补充压实铸件4P yP b=Лd2式中:P b 比压(Mpa); Py 机器的压射力(N);(压射力=压射缸直径×蓄压器压射时间最小压力)d 压室(冲头)直径(MM)选择比压考虑的的主要因素上海旭东压铸技术咨询培训资料压铸工艺参数比压因素选择条件高低壁厚薄壁厚壁压铸件结构形状复杂简单工艺性差些好些结晶温度范围大小压铸合金特性流动性差好密度大小比强度大小阻力大小浇注系统散热速度快慢公布合理不太合理排溢系统截面积大小内浇口速度快慢温度合金与压铸模具温度大小压铸各种合金常用比压表(Mpa)铸件壁厚≤3(mm) 铸件壁厚>3(mm)合金结构简单结构复杂结构简单结构复杂锌合金20-30 30-40 40-50 50-60 铝硅、铝铜合金25-35 35-45 45-60 60-70铝、镁合金30-40 40-50 50-65 65-75 镁合金30-40 40-50 50-65 65-80铜合金40-50 50-60 60-70 70-80 压力损失折算系数K直浇道导入口截面F1,K值与内浇铸口截面F2之比>1 =1 <1立式冷室压铸机0.66-0.70 0.72-0.74 0.76-0.78卧式冷室压铸机0.88压射速度浇注金属液量占压室容积百分数(%) 压射速度(cm/s)≤30 30-4030-60 20-30>60 10-20高压速度计算公式:VVh= ×[1+(n-1)×0.1]1/4Лd2T式中:Vh 高速压射速度(CM/S);V 型腔容积(CM3);N 型腔数;D 冲头直径(CM);T 适当的充填时间。
2 压铸过程原理-32(1)

2 压铸过程原理压铸的主要特点是金属液在高压、高速下充填压铸模型腔,并在高压下成型、结晶。
因此,压铸过程中压力和速度的变化及其作用是至关重要的,它们直接影响金属充填形态和金属液在型腔中的运动,从而影响压铸件的质量。
2.1 压铸压力2.1.1四级压射的概念压铸压力是压铸工艺中主要的参数之一。
压铸过程中的压力是由压铸机的压射机构产生的,压射机构通过工作液体将压力传递给压射活塞,然后由压射活塞经压射冲头施加于压室内的金属液上。
作用于金属液上的压力是获得组织致密和轮廓清晰的铸件的主要因素,所以,必须了解并掌握压铸过程中作用在金属液上的压力的变化情况,以便正确利用压铸过程中各阶段的压力,并合理选择压力的数值。
压铸过程中的压力可以用压射力和压射压力两种形式来表示。
压铸机压射缸内的工作液作用于压射冲头,使其推动金属液充填模具型腔的力,称为压射力。
其大小随压铸机的规格而不同,它反映了压铸机功率的大小。
压射压力是指压射过程中,压室内单位面积上金属液所受到的静压力。
压射力和压射压力的关系如下:24D FA F p π==(2-1)式中 p ——压射压力(Pa );F ——压射力(N );A ——压射冲头截面积(近似等于压室截面积)(m2); D ——压射缸直径(m )。
由式(2-1)可知,压射压力与压射力成正比,而与压射冲头的截面积成反比。
所以,压射压力可以通过调整压射力和更换不同直径的压射冲头来实现。
如果既考虑压射力又考虑压射压力,会把问题复杂化,而且压射压力更能反映压铸过程中金属液在充填时的各个阶段以及金属液流经各个不同截面时的力的概念,因此,压铸压力通常指的是压射压力。
在压铸过程中,作用在金属液上的压射压力并不是一个常数,而是随着压射阶段的变化而改变。
金属液在压室与压铸模型腔中的运动可分解为四个阶段,图2-1表示在不同阶段,压射冲头的运动速度与金属液所受的压力(压射压力)曲线。
图2-1压铸不同阶段,压射冲头的运动速度与金属液所受压力的变化情况τ-压铸的各个阶段v-压射冲头的运动速度p-压射压力第一阶段τ1压射冲头以慢速v1前进,封住浇口,金属液被推动,其所受压力p1也较低,此时p1仅用于克服压室与液压缸对运动活塞的摩擦阻力。
压力铸造

将熔融或半熔融的金属以高速压射入金属铸型内,并在 压力下结晶的铸造方法
01 ห้องสมุดไป่ตู้述
03 工艺流程
目录
02 特点 04 应用
压力铸造是指将熔融或半熔融的金属以高速压射入金属铸型内,并在压力下结晶的铸造方法,简称压铸。常 用压射压力为30~70MPa,充填速度约为0.5~50 m/s,充填时间为0.01~0.2 s。
近些年来,高科技已应用于压铸领域.如采用三级压射机构控制压力、压射速度和型内气体。发展特殊压铸 工艺(如真空压铸、定向引气压铸、充氧压铸等)和应用计算机控制技术,有效地清除气孔,提高铸件致密度,同 时研制新型模具材料和热处理新工艺来延长压型寿命,使黑色金属压铸有了一定进展。
谢谢观看
简述
压力铸造是一种将液态或半固态金属或合金,或含有增强物相的液态金属或合金,在高压下以较高的速度填 充入压铸型的型腔内,并使金属或合金在压力下凝固形成铸件的铸造方法。压铸时常用的压力为4~500MPa,金 属充填速度为0.5—120m/s。因此,高压、高速是压铸法与其他铸造方法的根本区别,也是重要特点。1838年美 国人首次用压力铸造法生产印报的铅字,次年出现压力铸造专利。19世纪60年代以后,压力铸造法得到很大的发 展,不仅能生产锡铅合金压铸件、锌合金压铸件,也能生产铝合金、铜合金和镁合金压铸件。20世纪30年代后又 进行了钢铁压力铸造法的试验。
压力铸造的原理主要是金属液的压射成形原理。通常设定铸造条件是通过压铸机上速度、压力,以及速度的 切换位置来调整的,其他的在压铸型行进行选择。
特点
1、压力铸造的优点 1)生产率高,易于实现机械化和自动化,可以生产形状复杂的薄壁铸件。压铸锌合金最小壁厚仅为0.3mm, 压铸铝合金最小壁厚约为0.5mm,最小铸出孔径为0.7mm。 2)铸件尺寸精度高,表面粗糙度值小。压铸件尺寸公差等级可达CT3~CT6,表面粗糙度一般为Ra0.8~ 3.2μm。 3)压铸件中可嵌铸零件,既节省贵重材料和机加工工时,也替代了部件的装配过程,可以省去装配工序,简 化制造工艺。 2、压力铸造的缺点 1)压铸时液体金属充填速度高,型腔内气体难以完全排除,铸件易出现气孔和裂纹及氧化灾杂物等缺陷,压 铸件通常不能进行热处理。 2)压铸模的结构复杂、制造周期长,成本较高,不适合小批量铸件生产。 3)压铸机造价高、投资大,受到压铸机锁模力及装模尺寸的限制,不适宜生产大型压铸件。
压铸简易教程.

简易压铸教程一、压射过程的阶段及运动方式和作用1.卧式压铸机压射过程典型的三阶段压射过程经过不断的发展,演变为多点压射过程。
多点压射的实质则是对该三个阶段分别各自进行分解为若干小段(或称为“转换点”)卧式冷室压铸典型的三阶段压射过程示意图压射过程解析卧式冷室压铸典型的三阶段奔压射曲线示意图二、压铸合金压然合金通常为有色金属,按目前的用量来说,依次为铝合金,锌合金、镁合金和铜合金。
黑色金属中的铸铁也可以采用压铸,但用量很少。
在几种压铸机中,卧式冷室压铸机具有技术含量高,通用性大、性能参数宽、型号规格多(特别是大型)等特点,上述的压铸合金都可以在卧式冷室压铸机上生产。
1.压铸铝合金压铸铝合金的密度为2.5~2.9g/cm3。
压铸铝合金的特点:优点:比强度大(强度/密谋=9~15);烦蚀性、烦磨性好;导热性、导电性好;切削性能好缺点:铝硅系合金易粘模;对金属坩埚有较强的腐蚀;体收缩大,易产生缩孔。
2.压铸锌合金压铸用锌合金密度为6.6~6.7g/cm3压铸锌合金的特点:优点:熔点低,不易粘模、填充性能良好、电镀性好多用于常温场合。
缺点:锌合金易老化、抗腐蚀性差且易生成晶间腐蚀导致强度和尺寸发生变化。
3.压铸镁合金压铸镁合金的密度为1.77~1.81g/cm3压铸镁合金的特点优点:比强度大(强度/密度=14~15);刚度和减震性好。
缺点:易氧化,要求熔化、保温设备结构复杂、工艺性复杂;高温脆性,热裂倾向大;高温强度稍差;耐蚀性差。
4.压铸铜合金压铸铜合金的密度为8.2~8.5g/cm3压铸铜合金的特点优点:力学性能好;导电导热好;耐磨性好;耐蚀性好。
缺点:熔点高,模具和压机的寿命低;成本高。
三、压铸工艺参数压铸工艺参数(1)----压力参数压力是取得铸件组织致密和轮廓清晰的主要因素。
1.压射力1.1 压射力及其计算压射力是压铸机压射机构中推动压射活塞的力。
压射力的计算公式为:p y=P g(П*D*D/4)。
压铸工艺流程图示

压铸(BODY)工艺流程图示i,压铸机调试2,压铸模安装呻3,压铸模设计与制造斗8,合金熔炼保温6,模具清理—7,合型(合模)9,嵌件准备12,开模、抽芯取件13,表面质量检查> 16,铸件浸渗、喷丸处理d压室(冲头)直径(MM )1、压射压力注:t1 ------ 金属液在压室中未承受压力的时间;P1为一级(慢速) t2 ----- 金属液于压室中在压射冲头的作用下, 通过内浇口充填型腔的时间;P2为二级(快速)t3 ------ 充填刚刚结束时的舜间; P3为三级(增压) t4 ------ 最终静压力;P4为补充压实铸件4P yP b =刃d 2式中:Pb ------ 比压(Mpa ) ; Py --------- 机器的压射力(N ); (压射力=压射缸直径x蓄压器压射时间最小压力)选择比压考虑的的主要因素艺参数压铸各种合金常用比压表( Mpa)压力损失折算系数K压射速度浇注金属液量占压室容积百分数 (%)压射速度(cm/s)< 30 30-40 30-60 20-30 >6010-20高压速度计算公式VVh= -----------2__1/4 刃 dTx [1+(n-1) x 0.1]压铸合金 铸件壁厚v 2.5MM铸件壁厚〉2,5〜6MM 锌合金 1〜2 3〜7 铝合金 1〜2 3〜8 镁合金 1〜2 3〜8 铜合金2〜35〜10式中:oCM/S);留模时间浇注温度②含铝的锌合金温度不宜超过不去450C,否则结晶粗大。
压铸模温度T m=3式中:Tm -------------------- 压铸模所需的工作温度(C);Th ------- 合金浇注温度(C);△ t ----- 温度控制公差(一般为25C)压铸涂料润滑剂,咼温粘附剂、咼温成膜剂、乳化剂、极压添加1,改善环境污染2,除润滑、脱膜作用外水基涂膜剂齐9、防腐杀菌剂、分散剂、可冷却压铸模,提高生产型腔和冲头润滑剂、抗氧剂率3,用喷枪喷涂4,便于自动化生产自配涂料。
压力铸造工艺过程
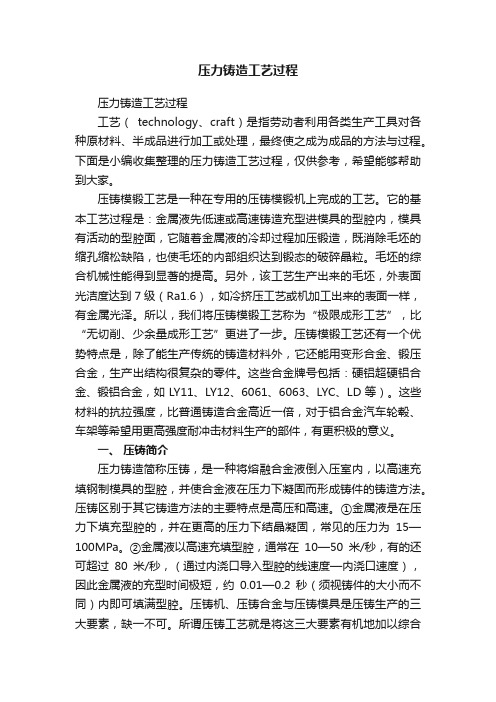
压力铸造工艺过程压力铸造工艺过程工艺(technology、craft)是指劳动者利用各类生产工具对各种原材料、半成品进行加工或处理,最终使之成为成品的方法与过程。
下面是小编收集整理的压力铸造工艺过程,仅供参考,希望能够帮助到大家。
压铸模锻工艺是一种在专用的压铸模锻机上完成的工艺。
它的基本工艺过程是:金属液先低速或高速铸造充型进模具的型腔内,模具有活动的型腔面,它随着金属液的冷却过程加压锻造,既消除毛坯的缩孔缩松缺陷,也使毛坯的内部组织达到锻态的破碎晶粒。
毛坯的综合机械性能得到显著的提高。
另外,该工艺生产出来的毛坯,外表面光洁度达到7级(Ra1.6),如冷挤压工艺或机加工出来的表面一样,有金属光泽。
所以,我们将压铸模锻工艺称为“极限成形工艺”,比“无切削、少余量成形工艺”更进了一步。
压铸模锻工艺还有一个优势特点是,除了能生产传统的铸造材料外,它还能用变形合金、锻压合金,生产出结构很复杂的零件。
这些合金牌号包括:硬铝超硬铝合金、锻铝合金,如LY11、LY12、6061、6063、LYC、LD等)。
这些材料的抗拉强度,比普通铸造合金高近一倍,对于铝合金汽车轮毂、车架等希望用更高强度耐冲击材料生产的部件,有更积极的意义。
一、压铸简介压力铸造简称压铸,是一种将熔融合金液倒入压室内,以高速充填钢制模具的型腔,并使合金液在压力下凝固而形成铸件的铸造方法。
压铸区别于其它铸造方法的主要特点是高压和高速。
①金属液是在压力下填充型腔的,并在更高的压力下结晶凝固,常见的压力为15—100MPa。
②金属液以高速充填型腔,通常在10—50米/秒,有的还可超过80米/秒,(通过内浇口导入型腔的线速度—内浇口速度),因此金属液的充型时间极短,约0.01—0.2秒(须视铸件的大小而不同)内即可填满型腔。
压铸机、压铸合金与压铸模具是压铸生产的三大要素,缺一不可。
所谓压铸工艺就是将这三大要素有机地加以综合运用,使能稳定地有节奏地和高效地生产出外观、内在质量好的、尺寸符合图样或协议规定要求的合格铸件,甚至优质铸件。
压铸工艺及操作规程(3篇)

第1篇一、压铸工艺概述压铸是一种将金属熔体在高压下注入到铸模中,冷却凝固后得到所需的铸件的金属成型方法。
压铸工艺具有生产效率高、尺寸精度好、表面光洁度高等优点,广泛应用于汽车、家电、电子等行业。
二、压铸工艺流程1. 铝合金熔炼:将铝锭或铝合金锭放入熔炼炉中,通过加热熔化成铝液。
2. 模具准备:根据产品图纸制作或选用合适的模具,并对模具进行预热。
3. 铝液准备:将熔化的铝液过滤、除气、去除杂质,使其达到压铸要求。
4. 压射成型:将铝液注入到预热的模具中,在高压下使铝液充满模具型腔。
5. 冷却凝固:铝液在模具中冷却凝固,形成铸件。
6. 取件:将铸件从模具中取出。
7. 清理:对铸件进行去毛刺、抛光等表面处理。
8. 检验:对铸件进行尺寸、表面质量、机械性能等检验。
三、压铸操作规程1. 安全操作:操作者必须穿戴好劳保用品,如工作服、手套、眼镜等,确保人身安全。
2. 设备检查:开机前,检查设备是否正常运行,如油压、冷却系统、控制系统等。
3. 模具准备:根据产品图纸制作或选用合适的模具,并对模具进行预热。
4. 铝液准备:将熔化的铝液过滤、除气、去除杂质,使其达到压铸要求。
5. 压射成型:将铝液注入到预热的模具中,在高压下使铝液充满模具型腔。
6. 冷却凝固:铝液在模具中冷却凝固,形成铸件。
7. 取件:将铸件从模具中取出。
8. 清理:对铸件进行去毛刺、抛光等表面处理。
9. 检验:对铸件进行尺寸、表面质量、机械性能等检验。
10. 设备维护:定期对设备进行保养、检修,确保设备正常运行。
四、注意事项1. 铝液温度:铝液温度应控制在合适的范围内,过高或过低都会影响铸件质量。
2. 压射压力:压射压力应根据产品材质、厚度等因素进行调整,确保铸件成型质量。
3. 模具预热:模具预热温度应控制在合适的范围内,过高或过低都会影响铸件质量。
4. 铝液过滤:铝液过滤可有效去除杂质,提高铸件质量。
5. 模具维护:定期对模具进行检查、清洗、维护,确保模具使用寿命。
压铸工艺参数(压力)教案(精)
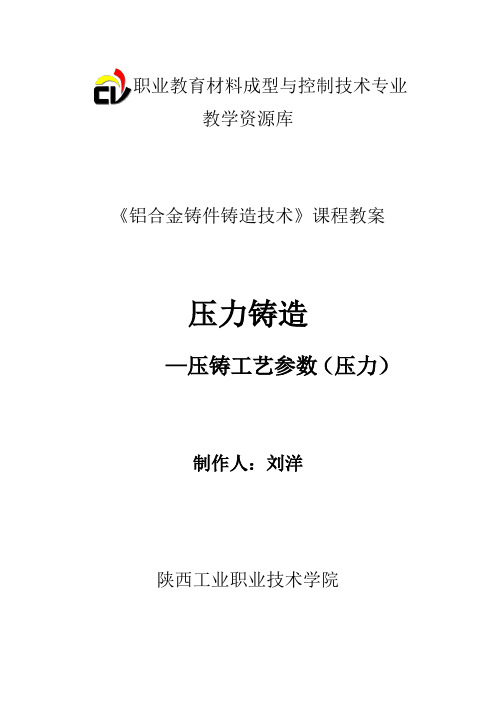
职业教育材料成型与控制技术专业教学资源库《铝合金铸件铸造技术》课程教案压力铸造—压铸工艺参数(压力)制作人:刘洋陕西工业职业技术学院压力铸造—压铸工艺参数(压力)一、压射力压射力是指压射冲头作用于金属液上的力,来源于高压泵,压铸时它推动金属液充填到模具型腔中。
在压铸过程中,作用在金属液上的压力并不是一个常数,而是随着不同阶段而变化。
压射力的大小由压射缸的截面积和工作液的压力所决定:y F 42D P g π⨯=式中 F Y —压射力(N);P g —压射缸内的工作压力(Pa),当无增压机构或增压机构未工作时,即为管道中工作液的压力; D —压射缸直径(m)。
增压机构工作时,压射力为:y F 422D P g π⨯=式中 P g2—增压时压射缸内的工作压力(Pa)。
二、压射比压比压是压室内金属液单位面积上所受的力,即压铸机的压射力与压射冲头截面积之比。
充填时的比压称压射比压,用于克服金属液在浇注系统及型腔中的流动阻力,特别是内浇口处阻力,使金属液在内浇口处达到需要的速度。
有增压机构时,增压后的比压称增压比压,它决定了压铸件最终所受压力和这时所形成的胀模力的大小。
压射比压可按下式计算:24dF P yb π=式中P b一压射比压(Pa);d—压射冲头(或压室)直径(m)。
比压与压铸机的压射力成正比,与压射冲头直径的平万成反比。
所以,比压可以通过改变压射力和压射冲头直径来调整。
在制订压铸工艺时,正确选择比压的大小对铸件的力学性能、表面质量和模具的使用寿命都有很大影响。
首先,选择合适的比压可以改善压铸件的力学性能。
随着比压的增大,压铸件的强度亦增加。
这是由于金属液在较高比压下凝固,其内部微小孔隙或气泡被压缩,孔隙率减小,致密度提高。
随着比压增大,压铸件的塑性降低。
比压增加有一定限度,过高时不但使延伸率减小,而且强度也会下降,使压铸件的力学性能恶化。
此外,提高压射比压还可以提高金属液的充型能力,获得轮廓清晰的压铸件。
压铸工艺之压力

4)内浇口速度:要求内浇口速度高,比压高些。
5)温度:金属液与模温温差大时,比压高些。
6)对于要求强度高、致密度高的大铸件,应采用高的增压比压。
(3)参考值
压铸合金常用比压参考值如表5-2所示。
表5-2压铸合金常用比压
压铸合金
铸件壁厚<3mm
铸件壁厚3~6mm
1.压射力
压射力指压射液压缸(增压缸)内工作液推动压射活塞运动的力。
P压=π/4D2Po
式中:P压为压射力,D为液压缸(增压缸)直径(mm),Po为液压缸(增压缸)的工作压力Pa
2.比压
比压指压室内金属液单位面积上所受的压力。填充时的比压称为压射比压;增压时的比压称为增压比压,它决定了压铸件充填时所受的压力和模具的胀型力。
(1)计算公式
P=4P压/πd2
式中:P为压射比压(MPa),P压为压射力(N),d为冲头直径(mm)。
(2)选择比压考虑的因素
1)压铸件结构特征:
①简单的薄壁件,比压选较低些;结构复杂的薄壁件,比压选高些。
②结构简单的厚壁件,比压选低些;结构复杂的厚壁件,比压选较高些。
2)合金特性:结晶温度范围大,流动性差.密度大,比压选高些。
60.0~70.0
70.0~80.0
(4)压力对铸件空隙率的影响
金属液在充型过程中卷气,或在凝固过程中产生的收缩得不到补缩时,铸件会产生孔洞缺陷。
增压压力可以通过冲头作用,补充金属液的凝固收缩,还可以压缩由于包气所产生的空隙。因此当压力增大时,空隙率会明显地减少。
结构较简单
结构较复杂
结构较简单
结构较复杂
锌合金
20.0~30.0
30.0~40.0
压铸工艺

第三部分压铸工艺一、工艺参数1、压力参数:①压射力用压射压力和压射比压来表示,是获得组织致密、轮廓清晰的压铸件的主要因素,在压铸机上其大小可以调节。
②压射压力压射时压射油缸内的油压,可以从压力表上直接读出,是一个变量,当压铸机进入压射动作时产生压射压力,按照压射动作分段对应的称为一级压射压力(慢压射压力)、二级压射压力(快压射压力)等;增压阶段后转变为增压压力,此时的压射压力达到极大值。
③压射比压压射时压室内金属液在单位面积上所受的压力,简称比压。
可通过改变压射力或更换不同直径的压室及冲头来进行调整。
计算公式为:比压=压射力÷(冲头直径)²×4/π2、速度参数:①压射速度压射时冲头移动的速度。
按照压射过程的不同阶段,压射速度分为慢压射速度(低速压射速度)和快压射速度(高速压射速度)。
一般慢压射速度的选择根据“压室充满度”(即压室内金属液的多少,用百分比快压射速度,是在一定填充时间条件下确定的。
根据铸件的结构特征确定其填充时间后,可用以下公式进行计算:快压射速度=坯件重量/合金比重/压室内截面积/填充时间×[1+(N-1)+0.1]式中“坯件重量”含浇冒系统;“N”为型腔穴数;“填充时间”可查表得到。
按此公式计算出来的快压射速度,是获得优质铸件的理论速度,实际生产中选其1.2倍;对有较大镶嵌件的铸件时可选1.5~2倍。
②内浇口速度金属液在压力作用下通过内浇道导入型腔时的线速度,称为内浇口速度。
内浇口速度对铸件质量有着重要影响,主要是表面光洁度、强度和塑性等方面。
内浇口速度的大小可通过查表得到,调节的方法有:调整压射速度、改变压室直径、调整比压、改变内浇口截面积。
铸件平均壁厚、填充时间、内浇口速度对照表3、时间参数:①填充时间金属液自开始进入型腔到充满铸型的过程所需要的时间。
影响填充时间的因素有:金属液的过热度、浇注温度、模具温度、涂料性能与用量、排气效果等。
铝合金压铸工艺
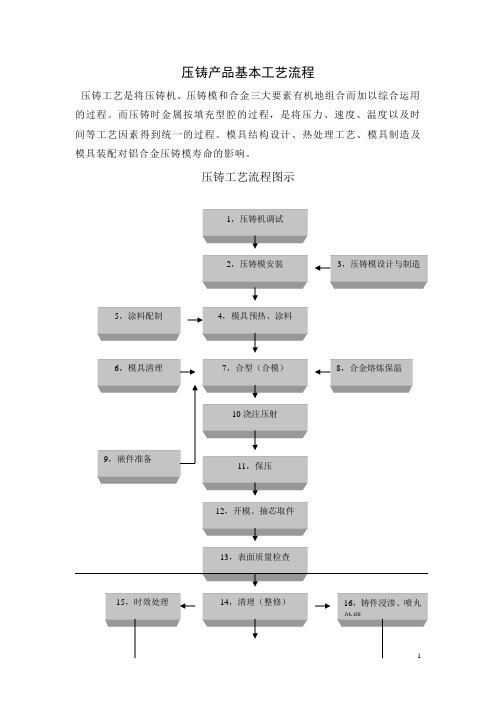
压铸产品基本工艺流程压铸工艺是将压铸机、压铸模和合金三大要素有机地组合而加以综合运用的过程。
而压铸时金属按填充型腔的过程,是将压力、速度、温度以及时间等工艺因素得到统一的过程。
模具结构设计、热处理工艺、模具制造及模具装配对铝合金压铸模寿命的影响。
压铸工艺流程图示1.11压铸工艺原理压铸工艺原理是利用高压将金属液高速压入一精密金属模具型腔内,金属液在压力作用下冷却凝固而形成铸件。
冷、热室压铸是压铸工艺的两种基本方式,其原理如图1-1所示。
冷室压铸中金属液由手工或自动浇注装置浇入压室内,然后压射冲头前进,将金属液压入型腔。
在热室压铸工艺中,压室垂直于坩埚内,金属液通过压室上的进料口自动流入压室。
压射冲头向下运动,推动金属液通过鹅颈管进入型腔。
金属液凝固后,压铸模具打开,取出铸件,完成一个压铸循环。
1.12压铸工艺的特点优点(1)可以制造形状复杂、轮廓清晰、薄壁深腔的金属零件。
压铸件的尺寸精度较高,表面粗糙度达Ra0.8—3.2um,互换性好。
(2)材料利用率高。
由于压铸件的精度较高,只需经过少量机械加工即可装配使用,有的压铸件可直接装配使用。
生产效率高。
由于高速充型,充型时间短,金属业凝固迅速,压铸作业循环速度快。
方便使用镶嵌件。
(3)缺点(1)由于高速填充,快速冷却,型腔中气体来不及排出,致使压铸件常有气孔及氧化夹杂物存在,从而降低了压铸件质量。
不能进行热处理。
(2)压铸机和压铸模费用昂贵,不适合小批量生产。
(3)压铸件尺寸受到限制。
压铸合金种类受到限制。
主要用来压铸锌合金、铝合金、镁合金及铜合金。
1.13压铸工艺的应用范围压铸生产效率高,能压铸形状复杂、尺寸精确、轮廓清晰、表面质量及强度、硬度都较高的压铸件,故应用较广,发展较快。
目前,铝合金压铸件产量较多,其次为锌合金压铸件。
第二章压铸合金2.1 压铸合金压铸合金是压铸生产的要素之一,要生产优良的压铸件,除了要有合理的零件构造、设计完善的压铸模和工艺性能优越的压铸机外,还需要有性能良好的合金。
压铸工艺参数

1、金属静压
p1
ps (1
v02 vm2 ax
)
2
p stat
p s
d1 d0
式中, p1为压射缸压力(Mpa);ps为蓄能器压力(Mpa);v0为冲头速度 (m/s);vmax为冲头最大空压射速度(m/s) ;pstat 为压射终了金属静压 (Mpa);d0为冲头直径(m);d1为压射缸直径(m)。
厚(mm)。
根据热量比可以得到几种合金的充型时间τ比
τMg:τZn︰τAl:τCu=0.51︰0.65︰1︰1.8
压铸工艺参数
1.3 时间参数
1、充时间
充型时间应该尽可能短,目的是使充型时铸件最小的部位或液流 的远端不产生早期凝固;但从另一方面考虑又要尽可能长些,以便空 气及金属熔体流动时所产生的涂料蒸汽有足够的时间逸出。根据这两 方面的矛盾要求综合考虑,选择最佳的充型时间。充型时间与壁厚有 关的推荐值,可参考下表。
压铸工艺参数
1.1 压力参数
2、充型压力
充型压力(也称为流动压力)与流速有关,按伯努利方程似稳流计算:
v 2p
式中,v为流速(m/s);p为充型压力(Mpa) ; ρ为金属密度(kg/m3)
设喷嘴或内浇口速度为 va ,则p为
p va2
2
设阻尼系数为 ξ,则p为
p
va 2
2 2
若设Q为金属熔体的流量(m3/s), Sa 为内浇口截面积(m2 ),
常用留模时间见下表
单位:h
压铸工艺参数
1.4 温度参数
1、浇注温度
金属液从压室至充满型腔的平均温度称为浇注温度。为了保证铸 件质量、提高模具寿命,浇注温度应尽可能低,一般为合金液相线以 上20~50℃,实际采用的压铸合金浇注温度,见下表。
压力铸造工艺概述总结(必备3篇)

压力铸造工艺概述总结第1篇压铸分为以下四个过程:a、合模b、压射c、开模d、推出及复位其中最关键的是压射过程:从压射冲头开始移动到型腔充满保压(热室压铸机),或者至增压结束(冷室压铸机)为止压力、速度是压射过程中两个重要工艺参数,记录压射过程中压力和速度的动态特性曲线称为压射过程曲线压射过程中,随着压射冲头的位移,速度和压力都是按设定的模式变化液态金属在压室与型腔中的运动可分解成四个阶段,目前使用的大中型压铸机为四级压射,中小型压铸机多为三级压射(将第二、第三阶段合为一个阶段),而热室压铸主要以两个阶段压射为主(一速升液和二速填充)第一阶段 τ_1 :从压射冲头起始位置至越过浇料口位置特征:低压低速、运动平稳,防止金属液从浇料口溢出,有利于气体排出第二阶段 τ_2 :从越过浇料口位置到金属液充满至内浇口处特征:压力增大,压射冲头速度加快,越过浇料口位置后,压射压力提高,压射冲头速度加快,金属液充满压室至浇注系统,该阶段应防止卷气,尽量避免金属液提前进入型腔第三阶段 τ_3 :从金属液充满内浇口处至型腔完成充满特征:压射压力再次升高,压射速度略有下降,充型速度最快,由于内浇口处截面积大幅度缩小,流动阻力剧增,压射速度略有下降,但此时充型速度最快第四阶段 τ_4 :充型结束特征:压射冲头停止运动,压力剧增,达到全过程的最高值,充满型腔后,增压压力对凝固中的金属液进行压室,压射冲头可能稍有前移,金属液凝固后,增压压力撤除,压射过程结束压铸时,影响金属液充填成型的因素很多,主要有压力、速度、温度、时间等参数压射力:压铸机压射缸内工作液作用于压射冲头,使其推动金属液充填模具型腔的力,称为压射力压射力 F_y=P_g×(πD^2)/4Pg-压射缸内的工作压力,Pa D-压射缸直径,m比压:压室内压铸合金液单位面积上所受的力,即压铸机的压射力与压射冲头截面积之比,充填时的比压称为压射比压,有增压机构时,增压后的比压称为增压比压,它决定了压铸件最终所受压力和这时所形成的胀模力的大小压射比压 P_b=(4F_y)/(πd^2 )胀模力:压铸过程中,金属液充填型腔时,给型腔壁和分型面的压力称为胀模力,压铸过程中,最后阶段的增压比压通过金属液传给压铸模,此时的胀模力最大,为了防止压铸模被胀开,锁模力要大于胀模力在合模方向上的合力胀模力 F_z=P_b×AA-压铸件、浇口、排溢系统在分型面上的投影面积之和选择合适的比压可以改善压铸件的力学性能铸件在较高的比压下凝固,其内部微小孔隙或气泡被压缩,内部组织的致密度和强度较高,但随着比压过高,铸件的塑性指标下降,强度也会下降,力学性能下降较高的压射比压可以提高金属液的充模能力,防止铸件产生冷隔或充填不足的缺陷,轮廓较为清晰,但比压过大,会加剧金属液对型腔的冲击,加速模具的磨损,一般在保证压铸件成形和使用要求的前提下,选用较低的比压速度有压射速度和内浇口速度两种形式压射速度(冲头速度):压射冲头推动金属液的移动速度,也就是压射冲头的速度内浇口速度(充型速度):金属液通过内浇口处的线速度称为内浇口速度内浇口速度 v_n=\frac{πd^2}{4A_n} v_y=η \sqrt{\frac{2P_b}{ρ}}v_n -内浇口速度(m/s)v_y -压射速度(m/s)d-压射冲头(或压室)直径(m)A_n -内浇口截面积( m^2 )η-阻力系数,一般取ρ -合金的液态密度(kg/ m^3 )压射力大,内浇口速度高;合金液密度大,内浇口截面积大,内浇口速度低,在压铸过程中,通过调整压射速度,改变压射冲头直径、比压及内浇口截面积等,都可以直接或间接调整内浇口速度压铸的温度主要指合金浇注温度和压铸模的温度合金浇注温度指的是从压室进入型腔时压铸合金液的平均温度,经验证明,在压力较高的情况下,应尽可能降低浇注温度,最好在压铸合金液呈粘稠“粥状”时压铸,这样可以减少型腔表面温度的波动和压铸合金液对型腔的冲蚀,但对含硅量高的铝合金,则不宜使压铸合金液呈“粥状”时压铸,否则硅将大量析出,以游离状态存在于铸件内部,使加工性能变坏。
压铸过程原理及压铸工艺参数确定讲解
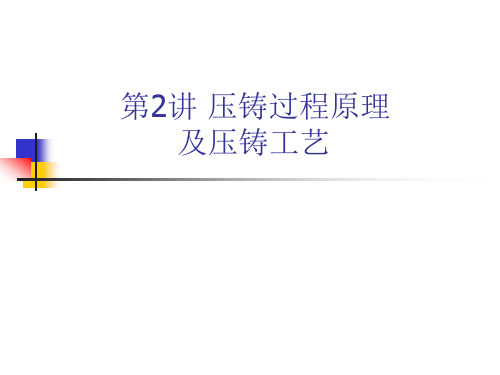
各阶段的切换起始点至结束点,或者说切换处曲线斜率,反映了 从低速切换至高速,或从低压切换至高压的响应速度。
切换时速度和压力应该同步响应为佳,以反应迅速为佳。
二、压射过程曲线
4、建压时间
建压时间表示增压压力的响应速度,建压时间是反映压铸机性能 的重要指标。 增压压力必须在金属凝固之前建立,否则将大大影响增压效果。 理论上讲,建压时间越短越好,可以在金属液凝固之前对其进行 高压压实,有效减少内部缺陷,增加压铸件的致命性。 目前先进压铸机的建压时间已达10ms以下。
发展历程:不变化-二阶段-三阶段(或四阶段) 最新进展:突破了传统的三阶段压射,可以根据工艺需要,多点 设置速度和压力,可以非常灵活地设定压射过程;某些压铸机还 具备压射冲头运动优化程序,根据压室参数、金属液充满度等参 数,计算最佳压射模式,减少卷气现象。 压射模式应根据压铸件及压铸工艺的具体状况设定,并非采用哪 一种固定模式。
二、压射过程曲线
2、压力和速度值
正常情况下,压力值和速度值相对应
如果曲线异常,出现压力过高而速度偏低,表明压射系统可能出 现问题,如压射冲头阻滞、浇道堵塞,或液压管路问题等 如果压力曲线偏低,速度无法上升,表明压力没有建立,应检查 压力设置是否合适或是存在泄压之处
二、压射过程曲线
3、压力和速度切换状况
第2讲 压铸过程原理 及压铸工艺
引言
压铸机、压铸模具及压铸合金是压铸生产的三大要素。
但要生产出合格压铸件,没有正确的压铸工艺是不可 能的。压铸工艺规定三大要素的工作方式。 换言之,如果压铸机、压铸模具及压铸合金是压铸生 产的硬件,那么压铸工艺就是压铸生产的软件。
锌合金压铸生产工艺

5.4合格品与不合格品要标示清楚,严格区分;
5.5生产操作过程中戴好劳保防护用品,保证安全生产;
5.6生产结束作好机台设备的防护和清理工作。
工艺流程图:
NOOK
1、生产操作流程:
4.1合金熔炼初始设定温度为435°C—440°C之间,待合金全部熔化后将温度调整为420℃—430℃的保温温度;
4.2合金全部熔化后进行清渣处理,并进行成份化验;
4.3合金成分控制为:
元素
Al
Cu
Mg
Fe
Pb
Cr
ቤተ መጻሕፍቲ ባይዱSn
Zn
含量
3.8~4.3
0.7~1.1
0.035~0.06
<0.02
<0.003
<0.003
<0.001
余量
4.4调整压射比压:45~50Kg/cm2;压射速度为:2.5m/s;充模时间为0.01s;增压时间为:1.5s;冷却时间为:6s;
4.5预热模具至150℃~200℃;
4.6均喷涂脱模剂和冲头油,原装脱剂与水的配比约为1:200;
4.7退出顶出杆,并进行合模动作;
4.8上料后进行压射动作,将合金熔液充入模腔;
4.9铸件冷却后,按顶出铸件,并从模上中取出;
4.10检验铸件有无冷隔、气孔、缺料、起泡、花纹等缺陷;
4.11合格铸件去除浇口、渣口、飞边等;
4.12铸件表面进行抛砂处理,进行检验入库。
5、生产注意事项:
5.1保证合金铸锭存放于清洁、干燥的区域;
5.2新料与回炉料的配比不超过50%;
压铸过程原理及压铸工艺参数确定解读
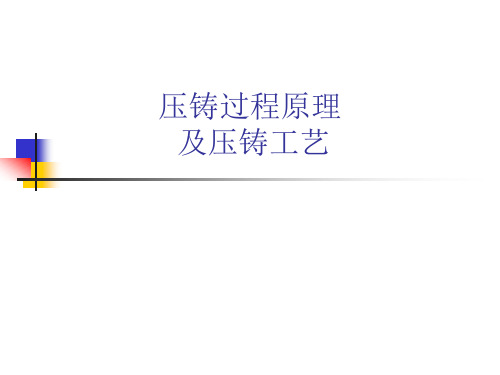
二、压铸速度
3、充型速度和冲头速度的关系
在冷室压铸机中,压室、浇道和压铸模型腔相连,成为一个密闭 系统,因而它们之间具有连续方程的关系,即
因此,充型速度确定后,根据内浇口和压射冲头面积核算冲头速度。
二、压铸速度
4、速度切换位置
A.给汤完了状态 压射时间内,溶汤 安定后,开始压射
B.低速压射,压室充填 设定防止空气卷入的速度 注意无溶汤飞溅,冲头的 卡住等的影响。
IV
起始位置:充型结束 参数:压射速度迅速减至零,增压压力p4建立 特征:压射冲头停止运动,压力剧增,达到全过程的最高值 说明:金属液完成充满型腔。增压压力对凝固中的金属液进行压实,压射冲头可能稍有
前移。金属液凝固后,增压压力撤除,压射过程结束。通过增压使压铸件密度增加 ,获得清晰压铸件
说明:压射阶段的划分来源于长期的压铸实践,但并非必须完全 遵循,根据压铸件及压铸工艺的具体状况设定。
注系统。该阶段应注意防止卷气,并尽量避免金属液提前进入型腔
III
起始位置:从金属液充满内浇口处至型腔完成充满 参数:压射速度v3,压射压力p3(动态) 特征:压射压力再次升高,压射速度略有下降,充型速度最快 说明:金属液流经内浇口充填型腔。由于内浇口处截面积大幅缩小,流动阻力剧增,压
射速度略有下降,但此时充型速度最快。要保持足够的充型速度,需更高的压射压 力,用于克服浇注系统主要是内浇口处的流动阻力。
三、时间
3、持压时间:指金属液充满型腔后,压射系统继续保持压力的时间 持压的目的是保证金属液在整个凝固期间都处于高压之下,达到 紧实压铸件的目的。 持压时间应比金属液在型腔内的凝固时间长。
表5 基于压铸件壁厚的持压时间推荐值
三、时间
- 1、下载文档前请自行甄别文档内容的完整性,平台不提供额外的编辑、内容补充、找答案等附加服务。
- 2、"仅部分预览"的文档,不可在线预览部分如存在完整性等问题,可反馈申请退款(可完整预览的文档不适用该条件!)。
- 3、如文档侵犯您的权益,请联系客服反馈,我们会尽快为您处理(人工客服工作时间:9:00-18:30)。
⏹
⏹
上海旭东压铸技术咨询培训资料压铸工艺参数
一、压铸工艺流程图示
上海旭东压铸技术咨询培训资料 压铸工艺参数
二、压射压力
压力
T1 t2 t3 t4 保压时间
升压充填增压
注:t1 金属液在压室中未承受压力的时间;P1为一级(慢速)
t2 金属液于压室中在压射冲头的作用下,通过内浇口充填型腔的时间;P2为二级(快速)
t3 充填刚刚结束时的舜间;P3为三级(增压)
t4 最终静压力;P4为补充压实铸件
4P y
P b=
Лd2
式中:P b 比压(Mpa); Py 机器的压射力(N);
(压射力=压射缸直径×蓄压器压射时间最小压力)
d 压室(冲头)直径(MM)
选择比压考虑的的主要因素
上海旭东压铸技术咨询培训资料压铸工艺参数
比压
因素选择条件
高低
壁厚薄壁厚壁压铸件结构形状复杂简单
工艺性差些好些
结晶温度范围大小压铸合金特性流动性差好
密度大小
比强度大小
阻力大小浇注系统散热速度快慢
公布合理不太合理排溢系统截面积大小
内浇口速度快慢
温度合金与压铸模具温度大小
●压铸各种合金常用比压表(Mpa)
铸件壁厚≤3(mm) 铸件壁厚>3(mm)合金结构简单结构复杂结构简单结构复杂
锌合金20-30 30-40 40-50 50-60
铝硅、铝铜合金25-35 35-45 45-60 60-70
铝、镁合金30-40 40-50 50-65 65-75
镁合金30-40 40-50 50-65 65-80
铜合金40-50 50-60 60-70 70-80
●压力损失折算系数K
直浇道导入口截面F1,K值与内浇铸口截面F2之比>1 =1 <1
立式冷室压铸机0.66-0.70 0.72-0.74 0.76-0.78
卧式冷室压铸机0.88
上海旭东压铸技术咨询培训资料压铸工艺参数
●压射速度
浇注金属液量占压室容积百分数(%) 压射速度(cm/s)
≤30 30-40
30-60 20-30
>60 10-20。