管壳式换热器制造工艺规程
管壳式换热器标准

管壳式换热器标准
管壳式换热器是一种常见的热交换设备,广泛应用于化工、石油、电力等工业领域。
为了确保管壳式换热器的安全、高效运行,
制定了一系列的标准来规范其设计、制造、安装和运行。
本文将就
管壳式换热器标准进行详细介绍,以便更好地了解和应用这些标准。
首先,管壳式换热器的设计标准是非常重要的。
设计标准包括
换热器的结构尺寸、材料选用、工作压力、温度范围等方面的规定。
这些规定旨在确保换热器在各种工况下都能够安全可靠地运行,同
时提高换热效率,降低能耗。
设计标准的严格执行对于保证换热器
的性能和使用寿命具有重要意义。
其次,制造标准是管壳式换热器生产过程中必须遵循的规定。
制造标准包括对于材料的选用、加工工艺、焊接质量、无损检测等
方面的要求。
只有严格按照制造标准进行生产,才能保证换热器的
质量达到设计要求,从而确保其安全可靠地运行。
此外,安装和维护标准也是管壳式换热器运行过程中必须遵守
的规定。
安装标准包括换热器的安装位置、连接方式、管路布置等
方面的规定,旨在确保换热器在安装后能够正常运行。
维护标准则
包括换热器的日常维护、定期检查、故障处理等方面的要求,旨在延长换热器的使用寿命,保证其长期稳定运行。
总之,管壳式换热器标准是保证换热器安全、高效运行的重要保障。
只有严格遵守这些标准,才能够确保换热器在各种工况下都能够正常运行,为工业生产提供可靠的热能支持。
因此,我们在使用管壳式换热器时,必须要深入了解并严格遵守这些标准,以确保换热器的正常运行,从而提高生产效率,降低能源消耗,保障生产安全。
管壳式换热器换热管与管板焊接工艺

控 制 活 塞 行 程 , 工 件 双 向受 力 双 面变 形 , 过 对 工 使 通 件 上 施 压 线 逐 条 施 加 压 力 , 受 压 工 件 达 到 设 计 要 使
求 , 方便 又快捷 。 既 收稿 E :01 1 5 l 20 —1—1 期
维普资讯
—7 2 6 4 8 — — — — 。接 着 , 重 新 从 第 一 个 区 域 将 错 再
开 的单 元 按 上 述 顺 序 逐 一 焊 完 , 成 整 个 焊 接 工 作 。 完 采 取 上 述 焊 接 顺 序 , 接 产 生 的 热 量 集 中 在 尽 焊 量 小 的范 围 内 , 产 生 的 应 力 较 小 , 板 的 变 形 也 且 管 小 , 工 也 便 于 操 作 , 免 了 管 板 由 于焊 接 变 形 而 影 焊 避 响 密 封 面 的密 封 效 果 。
按 G 1 1 备 试 板 和 试 管 管 束 , 板 厚 度 = B5 制 试 换 热 管 与管 板 的 焊 接 接 头 质 量 好 坏 , 接 影 响 直 换 热器制造质量 , 方 面接头质量差 容易发生泄漏 , 一 6 'l试 管 规 格 2 0nl, l T 5×2. , 对 前 将 试 板 与 试 管 表 5组 面 的油 、 、 等 杂 质 清 理 干 净 , 焊 采 用 钨 极 氩 弧 污 锈 点 焊 , 材 为 H 8 2 i 每 个 接 头 点 两 处 , 焊 位 置 焊 0 Mn S A, 点 在 图 3中 的 3点 和 9点 位 置 。 焊 接 工 艺 参 数 见 表 1 。 焊 接 位 置 为水 平 固定 , 接 时 引 弧及 熄 弧 应 避 焊
L I n ri l
H0 Mn s 8 2 i
2 o 9 ~ l0 l . 0 2 8~ 2 l
管壳式换热器通用工艺守则(修改)
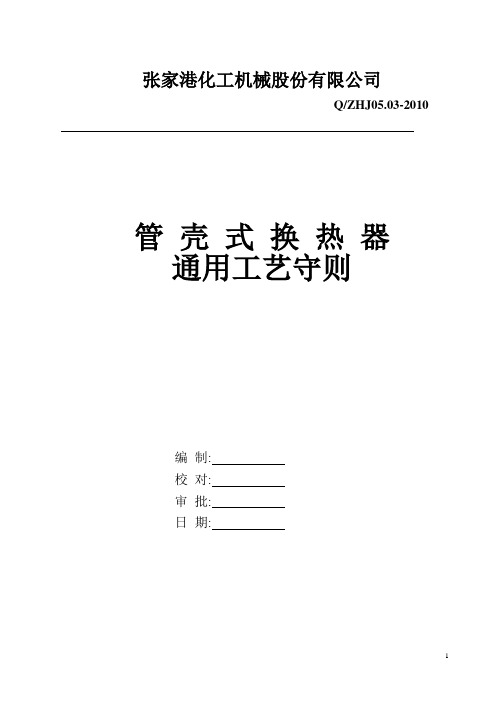
张家港化工机械股份有限公司Q/ZHJ05.03-2010 管壳式换热器通用工艺守则编制:校对:审批:日期:管壳式换热器通用工艺守则本守则若与图样及工艺文件有矛盾时,应按图样及工艺文件为准,低于国家有关标准时以国家标准为准,反之以本守则为准。
1、材料1.1制造换热容器的主要受压元件(如壳体、封头、换热管等)的材料,质量及规格应符合国标、部标和有关技术条件要求。
材料证明上的内容按有关规定必须填写齐全。
采用国外材料时,应按《固定式压力容器安全技术监察规程》的第2.9条要求进行检验、验收及复验。
1.2 含碳量大于0.25%的材料不得用于焊制换热容器。
1.3制造换热容器的材料标准,热处理状态及许用应力值按GB150及GB151的规定。
1.4钢板的表面应光滑平整,不得有裂纹、分层、气泡、夹杂、结疤等缺陷。
钢板表面存在的深度缺陷不得超过钢板厚度公差1/2的下限,个别损伤,允许用细砂轮清除,但不得低于钢板厚度名义尺寸的下偏差。
1.5钢板的低倍组织不得有肉眼可见的缩孔、裂纹和夹杂。
1.6换热管的内外表面不得裂纹、折迭、轧折、离层、发纹和结疤缺陷存在,上述个别缺陷其深度未超过管壁厚负偏差时允许清除,并进行压力试验合格。
1.7 对于双管板换热器,换热管和管板材料还应符合以下要求:1.7.1换热管应采用较高级精度的管子,换热管外径的许用偏差控制在±0.10mm,管子壁厚偏差为±7%。
1.7.2换热管应按材料的不同规定材料的硬度。
1.7.3根据换热管材料的力学性能要求对管板的屈服强度和硬度提出采购要求。
通常将硬度差控制在管板比换热管硬度高HB30~HB60。
1.8 所有材料都必须有接货检验记录,并按公司相关规定进行标识。
1.9 材料在切割前应将标记进行移植。
2、筒体制造2.1施工者根据施工图,要求画下料展开图。
2.1.1焊缝布置:a、立式换热器左右对称布置。
b、卧式换热器,水平线以上部位对称布置(并不被鞍座覆盖)。
管壳式换热器胀管工艺
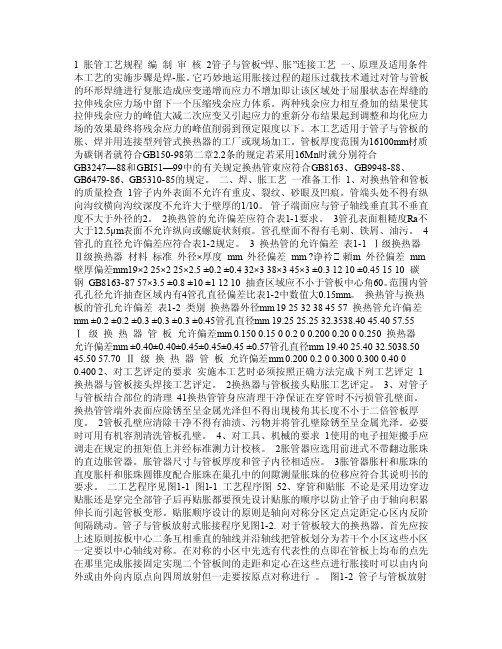
1 胀管工艺规程编制审核2管子与管板“焊、胀”连接工艺一、原理及适用条件本工艺的实施步骤是焊-胀。
它巧妙地运用胀接过程的超压过载技术通过对管与管板的环形焊缝进行复胀造成应变递增而应力不增加即让该区域处于屈服状态在焊缝的拉伸残余应力场中留下一个压缩残余应力体系。
两种残余应力相互叠加的结果使其拉伸残余应力的峰值大减二次应变又引起应力的重新分布结果起到调整和均化应力场的效果最终将残余应力的峰值削弱到预定限度以下。
本工艺适用于管子与管板的胀、焊并用连接型列管式换热器的工厂或现场加工。
管板厚度范围为16100mm材质为碳钢者就符合GB150-98第二章2.2条的规定若采用16Mn时就分别符合GB3247—88和GBI51—99中的有关规定换热管束应符合GB8163、GB9948-88、GB6479-86、GB5310-85的规定。
二、焊、胀工艺一准备工作1、对换热管和管板的质量检查1管子内外表面不允许有重皮、裂纹、砂眼及凹痕。
管端头处不得有纵向沟纹横向沟纹深度不允许大于壁厚的1/10。
管子端面应与管子轴线垂直其不垂直度不大于外径的2。
2换热管的允许偏差应符合表1-1要求。
3管孔表面粗糙度Ra不大于12.5μm表面不允许纵向或螺旋状刻痕。
管孔壁面不得有毛刺、铁屑、油污。
4管孔的直径允许偏差应符合表1-2规定。
3 换热管的允许偏差表1-1 Ⅰ级换热器Ⅱ级换热器材料标准外径×厚度mm 外径偏差mm ?诤衿 頼m 外径偏差mm 壁厚偏差mm19×2 25×2 25×2.5 ±0.2 ±0.4 32×3 38×3 45×3 ±0.3 12 10 ±0.45 15 10 碳钢GB8163-87 57×3.5 ±0.8 ±10 ±1 12 10 抽查区域应不小于管板中心角60。
管壳式换热器的制造检验要求

管壳式换热器的制造检验要求The final revision was on November 23, 2020管壳式换热器的制造、检验要求作为压力容器管壳式换热器制造、检验及验收应符合GB150的要求,但同时也要符合换热器本身的特殊要求。
一、焊接接头分类与一般压力容器类似,管壳式换热器也将主要受压部分的焊接接头分为A、B、C、D四类,如图7-1所示(教材P192)。
A类接头为筒体、前后管箱或膨胀节的轴向焊缝;B类接头为筒体、前后管箱或膨胀节的周向焊缝或带径发兰与接管的对接环向焊缝;C类接头为筒体或前后管箱与无径发兰或无径发兰与接管的平焊环向焊缝;D类接头为接管与筒体或前后管箱的环向焊缝。
二、零部件制造要求1.管箱与壳体壳体内径允许偏差:对于用板材卷制的壳体,起内径允许偏差可通过控制外圆周长的方式加以控制,外圆周长的允许上偏差为10mm,下偏差为零。
2.圆度:壳体同一断面上的最大直径和最小直径之差e应符合以下要求:对于公称直径DN(以mm为单位)不大于1200mm的壳体:e≤min(%DN,5)mm;对于公称直径DN(以mm为单位)大于1200mm的壳体:e≤min(%DN,7)mm。
3.直线度:壳体沿圆周0°、90°、180°、270°四个部位(即通过中心线的水平面和垂直面处)测量的壳体直线度允许偏差应满足以下要求:当壳体总长L≤6000mm时,直线度允许偏差≤min (L/1000, mm;当壳体总长L>6000mm时,直线度允许偏差≤min (L/1000,8) mm。
热处理要求`:碳钢、低合金钢制的焊有分程隔板的管箱和浮头平盖、侧向开孔超过1/3圆筒内径的管箱,焊后需作清除应力处理,有关密封面在热处理后加工。
4.其它要求:壳体在制造中应防止出现影响管束顺利安装的变形。
有碍管束装配的焊缝应磨至与母材表面平齐。
接管、管接头等不应伸出管箱、壳体的内表面。
管壳式换热器 GB151讲义

管壳式换热器 GB151-1999一.适用范围 1.型式固定——P t 、P S 大,△t 小浮头、U 形——P t 大,△t 大*一般不用于MPa P D 5.2>,易燃爆,有毒,易挥发和贵重介质。
结构型式:外填料函式、滑动管板填料函、双填料函式(径向双道) 2.参数41075.1,35,2600X PN DN MPa P mm D N N ≤⨯≤≤。
参数超出时参照执行。
D N :板卷按内径,管制按外径。
3.管束精度等级——仅对CS ,LAS 冷拔换热管Ⅰ级——采用较高级,高级精度(通常用于无相变和易产生振动的场合) Ⅱ级——采用普通级精度 (通常用于再沸,冷凝和无振动场合) 不同精度等级管束在换热器设计中涉及管板管孔,折流板管孔的加工公差。
GB13296不锈钢换热管,一种精度,相当Ⅰ级;有色金属按相应标准。
4.不适用范围受直接火焰加热、受核辐射、要求疲劳分析、已有其它行业标准(制冷、造纸等)P D <0.1MPa 或真空度<0.02MPa+二.引用标准1.压力容器安全技术监察规程——监察范围,类别划分*等*按管、壳程的各自条件划类,以其中类别高的为准,制造技术可分别要求。
*壳程容积不扣除换热管占据容积计,管程容积=管箱容积+换热管内部容积。
壳程容积=内径截面积X管板内侧间长度。
2. GB150-1998《钢制压力容器》——设计界限、载荷、材料及许用应力、各受压元件的结构和强度计算。
3.有关材料标准。
管材、板材、锻件等4.有关零部件标准。
封头、法兰(容器法兰、管法兰)紧固件、垫片、膨胀节、支座等三.设计参数1.有关定义同GB1502.设计压力Mpa分别按管、壳程设计压力,并取最苛刻的压力组合(一侧为零或真空)。
管板压差设计仅适用确能保证管、壳程同时升降压,如1)自换热 2)Pt P s均较高,操作又能绝对保证同时升降压。
3.设计温度℃0℃以上,设计温度≥最高金属温度。
0℃以下,设计温度≤最低金属温度。
管壳式换热器制造工艺

两道冷压和一道热压 水压机,冲头,温度 900-1000
100%射线探伤 立车坡口加工,钻床钻孔
2-20 椭圆封头尺寸
2.筒体 材料为 16MnR,展开的坯料尺寸为 9850X8325X16 (mm),拼接图如图 2-69
所示。它的制造过程列于表 2-19 2-19 筒体的制造过程
液化石油气储罐示意图一储罐主要构件的加工制造板材成型前的通用工艺流程列于表217序号工作内容要求加工方法加工内容或设备原材料复验外观几何尺寸和理化检验及钢板的超声波探伤钢印标记小于5毫米的板材用风刻电刻和不退色的墨水标记边缘加工气割或等离子弧坡口用机加工方法进行边缘加工二主要受压元件的成型和焊接工艺该封头为标准椭圆形封头材料为16mnr
许偏差分别列于表 2-25 和表 2-28。
3. 折流板等
下图为最常用的 20%DN 圆缺高度的弓形折流板,为保证加工精度和效率,常将圆板
坯以 8~10 块为一叠进行钻孔和切削加工外圆,折流板孔的允许偏差列于表 2-26。
4. 管子 换热器的管表面就是传热面积。常用管子外径 10~57 (mm);其长度一般用 2000、 3000、6000(mm)等。管子应作下列试验:以管子数的 5%,且不少于 2 根作拉力、硬度 和扩口等抽样检验;进行水压试验(试验压力为设计压力的(1.5~2)倍,合格者才可使 用。 如采用胀接,管子两端应作软化退火处理,使管端的硬度低于管板硬度;另外,还 应对管端两倍于管板厚度的长范围内进行打磨,打磨后的粗糙度,钢管为
<0.5%DN
<5
<7
壳体内径过大或圆度误差会引起壳程介质短路而降低换热效率。
壳体的直线度误差会影响管束的抽装,对其要求列于表 2-24。
GB151-2014 热交换器

温度高于或者等于其标准沸点的液体。
GB/T151-2014《热交换器》是一个什 么样的标准,具有怎样的地位?
相关标准 GB150-2011《压力容器》
——压力容器行业基础标准 ——给出了压力容器建造的通用要求,包括材料、设计、 制造检验与验收等内容
1、本标准适用的设计压力 1.1、钢制容器不大于35MPa。 1.2、 其他金属材料制容器按相应引用标准确定。 2、本标准适用的设计温度范围 2.1 设计温度范围:-269℃~900℃。 2.2 钢制容器不得超过按GB 150.2 中列入材料的允许使用温度范围。 2.3 其他金属材料制容器按本部分相应引用标准中列入的材料允许使用温度确定
换器管
换器管
8.3.2 管端清理长度: 焊接时:不小于换热管外径,且不小于25mm 胀接时:不小于强度胀接长度,且不得影响胀接质量 (不小于两倍管板厚度) 双管板时:按设计文件规定 8.3.3.3 U形管的弯制: U形管弯制后应逐根进行耐压试验,试验压力不得小于热交换器的耐压试验压 力(管、壳程试验压力的高值)(新增) 8.3.4换热管的拼接(换热管直管或直管段长度大于6000mm时允许拼接) b)最短直管段长不应小于300mm,且应大于管板厚度50mm以上。 f)对接接头100%射线检测,合格级别不低于Ⅲ级,检测技术等级不低于AB级。 (抽检10%,不合格加倍,再100%) g)对接后应逐根进行耐压试验,试验压力不得小于热交换器的耐压试验压力(管、 壳程试验压力的高值)(设计压力2倍液压试验)
换热管与管板的连接
6.6.4内孔焊(新增) 适用于大口径换热管
其他
增加了热交换器传热计算的基本要求 修订了单管板设计计算,增加了双管板设 计计算 增加振动计算
换热器加工工艺规程(过程装备制造工艺)

紧密面形式 用途或名称
平面
通道积水出口
平面 平面 平面 平面
冷凝用水入口 纯苯蒸汽入口 冷凝用水出口 纯苯凝液出口
E
端盖与密封板连接详图 不按比例
14
拉杆φ16 L=2270
2 Q235-A
13
筒体DN400×6L=2890 2 16MnR
12 R2003-6-4 右管箱
1 组合件
11 R2003-6-3 管板
2 16MnR
10
法兰 DN90
2
20
9
换热管φ25×2.5L=3000 78 Q235-A
8
定距管φ25×2.5L=297 30
20
过程装备制造工艺
西北大学
陕西 西安
以换热器加工为例
讨论 主要零部件有哪些? 加工要求? 安装要求?
×
、、
×
× ×4
第2、4、6块
×
技术要求
本设备按GB150《钢制压力容器》和GB151《钢制管壳式换热器》进 行制造。检验和验收并接受国家质量监督局监督颁发的《压力容器 安全技术监察》规程的监督。 焊接采用电弧焊,低合金钢之间焊条牌号:J507焊条,低合金钢与 碳钢之间,碳钢之间采用J426焊条。 焊接接头型式及尺寸除图注明外,均按HG20583-1998的规定,法兰 焊接按相应法兰的焊接标准的规定进行。 筒体和管板之间的焊接采用弧焊打底,焊底表面进行着色检验。 容器上的A类和B类焊缝应进行X射线探伤检查,探伤长度为20%, X 射线应符合相应的标准规定。 换热管与管板的连接采用焊接法。 设备制造完毕后,应按有关标准进行水压试验。
压力容器通用制造工艺规程(第二版)
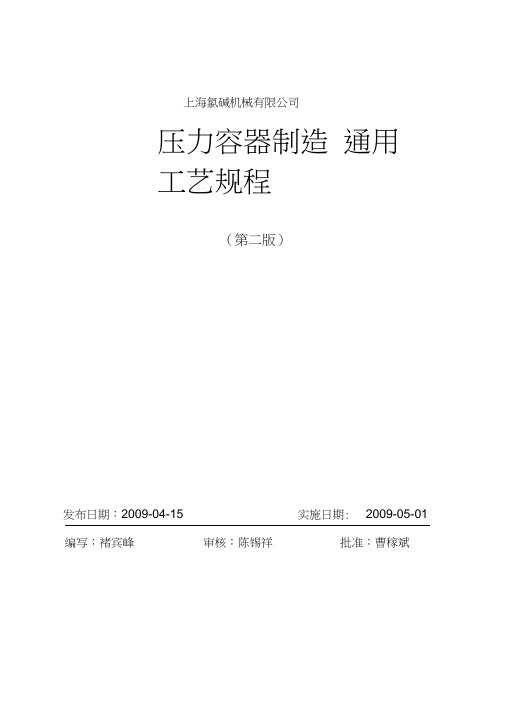
上海氯碱机械有限公司压力容器制造通用工艺规程(第二版)发布日期:2009-04-15 实施日期: 2009-05-01 编写:褚宾峰审核:陈锡祥批准:曹稼斌编写说明本规程适用于我公司一、二类压力容器、类外压力容器(正文中简称容器)及管壳式换热器(正文中简称换热器)的制造。
常压容器的制造及容器、换热器的修理可参照执行。
本规程根据GB150-1998《钢制压力容器》、GB151-1999《管壳式换热器》、HG20584-199&钢制化工容器制造技术要求》、《压力容器安全技术监察规程》(1999)的有关规定,并结合我公司几年来压力容器、换热器制造经验和现有装备能力而制订。
对于制造较复杂的、大型的、有特殊要求的容器设备,应由公司技术总负责人、技术管理部门、技术人员及有经验的工人师傅一起讨论研究,制订出具体可行的施工方案进行施工。
施工人员在施工过程中,应严格按图纸和工艺卡要求进行施工,如因图纸错误或加工制作误差等原因影响到零部件组装,应及时与工艺人员取得联系,以求问题解决。
在制造过程中,要树立质量第一的思想,严把质量关,制造出高质量的产品。
1、总则1.1、容器、换热器应按图纸、工艺卡、本规程及有关国家、行业标准和法规的要求进行制造。
并严格按我公司压力容器质量保证体系的要求运行。
1.2、制造容器、换热器用材料必须符合相应国家标准、行业标准规定。
材料采购时应从材料生产单位获取符合相应标准的材料质量合格证(原件);如果从非材料生产单位获得压力容器用材料时,应取得材料质量证明书原件或加盖供材单位检验章和经办人章的有效复印件(有效指复印件上盖有供材单位红色印泥检验章)。
对有复验或特殊检验要求的材料,须经复验或检验合格才能使用。
1.3、容器、换热器的焊接应按焊接工艺及我公司的《通用焊接工艺规程》要求进行。
1.4、对我公司无能加工的零部件,如封头、膨胀节等要严格按有关标准进行验收把关,确保外协件质量。
1.5、要通过装备能力的不断提升,工艺手段的不断完善,实现产品质量的持续提高。
管壳式换热器制造工艺规程

管壳式换热器制造工艺规程1、主题内容与适用范围:本规程规定了本公司管壳式换热器组装制造中的具体工艺要求外,还应执行JB3343《高压加热器技术条件》,JB8184《汽轮机低压加热汽技术条件》,JB7838《热网加热器》等标准中的规定。
2、引用标准:《固定式压力容器安全技术监察规程》——TSG《管壳式换热器》——GB151-2011《固定式压力容器》——GB150-20143、基本要求管壳式换热器主要受压部分的焊接接头分为A、B、C、D、E五类,按下图所示。
a) 壳体圆筒部分的纵向接头、球形接头与圆筒连接的环向接头、各类凸形封头中的所有拼焊接头以及嵌入式接管与壳体对接连接的接头,均属A类焊接接头。
b) 壳体部分的环向接头、锥形封头小端与接管连接的接头、长颈法兰与接管连接的接头,均属B类焊接接头,但已规定为A类的焊接接头除外。
c) 平盖、管板与圆筒非对接连接的接头,法兰与壳体、接管连接的接头,内封头与圆筒的搭接接头,均属C类焊接接头。
d) 接管、人孔、凸缘、补强圈等与壳体连接的接头,均属D类焊接接头,但已规定为A、B类的焊接接头除外。
e)非受压元件吊耳、支座垫板与压力容器连接的焊缝,均属E类焊接接头。
3.1 对不同板厚对接的规定:a) 下列不同板厚必须削薄厚板:当2≤10mm,且1-2>3mm及2>10mm且1-2≥0.3n 或>5mm时,必须削薄厚板:削薄形式分单面削薄和双向削薄。
见图2。
b) 下列不同板厚对接无须削薄:当≤10mm且1-2≤3mm及2>10mm且1-2≤0.32或≤5mm时,无须削薄板厚,且对口错边量b以较薄板厚度为基准确定。
在测量对口错边量时,不应计入两板厚度的差值。
3.2 筒节长度应不小于300mm。
组装时不应采用十字焊缝,相邻圆筒的A类焊缝的距离(或封头A类焊缝,焊缝的端点与相邻圆筒A类焊缝的距离)应大于名义厚度n 的三倍,且不小于100mm,(当板厚不同时,n按较厚板计算)。
换热管和管板连接通用工艺规程
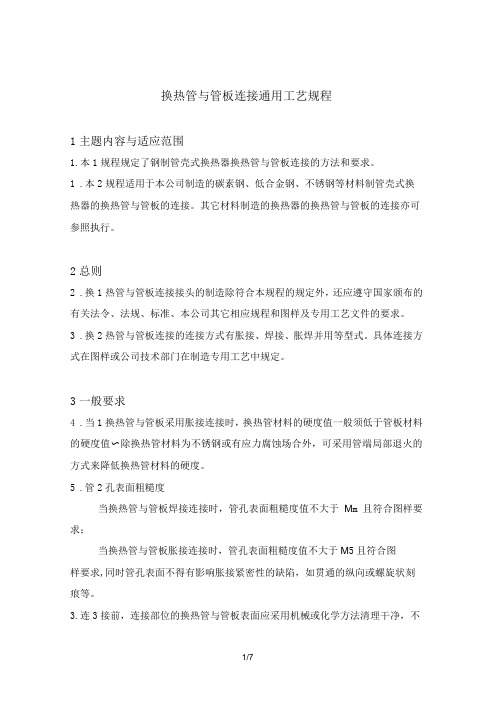
换热管与管板连接通用工艺规程1主题内容与适应范围1.本1规程规定了钢制管壳式换热器换热管与管板连接的方法和要求。
1.本2规程适用于本公司制造的碳素钢、低合金钢、不锈钢等材料制管壳式换热器的换热管与管板的连接。
其它材料制造的换热器的换热管与管板的连接亦可参照执行。
2总则2.换1热管与管板连接接头的制造除符合本规程的规定外,还应遵守国家颁布的有关法令、法规、标准、本公司其它相应规程和图样及专用工艺文件的要求。
3.换2热管与管板连接的连接方式有胀接、焊接、胀焊并用等型式。
具体连接方式在图样或公司技术部门在制造专用工艺中规定。
3一般要求4.当1换热管与管板采用胀接连接时,换热管材料的硬度值一般须低于管板材料的硬度值〜除换热管材料为不锈钢或有应力腐蚀场合外,可采用管端局部退火的方式来降低换热管材料的硬度。
5.管2孔表面粗糙度当换热管与管板焊接连接时,管孔表面粗糙度值不大于M m且符合图样要求;当换热管与管板胀接连接时,管孔表面粗糙度值不大于M5且符合图样要求,同时管孔表面不得有影响胀接紧密性的缺陷,如贯通的纵向或螺旋状刻痕等。
3.连3接前,连接部位的换热管与管板表面应采用机械或化学方法清理干净,不应留有影响胀接或焊接连接质量的毛刺、铁屑、锈斑、油污等。
穿管前,应对换热管进行机加工平头,平管公差L+mrn。
穿管前,应采用钢丝刷、钢丝轮、砂纸将换热管管头(包括管口端部)毛刺、铁屑、锈斑、油污去除干净,至呈金属光泽。
用于焊接时,换热管刷管范围不小于换热管外径尺寸,且不小于2mm;用于胀接时,换热管应呈现金属光泽,其长度应不小于二倍的管板厚度。
刷管后,换热管应放置在干燥通风处,已经刷管处理的换热管必须在7天内与管板进行胀接或焊接连接,否则应重新进行刷管处理。
c)换热管的外伸长度,按产品焊接工艺规程执行。
对需打磨的管头要求打磨平整,不得有卷边现象,并用机械或化学方法清除管板、管端表面残留的砂轮灰等杂物。
d)当换热管与管板定位后实施焊接或胀接前(不超过4小时),应采用钢丝刷将连接部位的换热管与管板表面的锈斑、油污清理干净。
GB151-1999讲义管壳式换热器

管壳式换热器 GB151-1999固定——P t 、P S 大,△t 小浮头、U 形——P t 大,△t 大*一般不用于MPa P D 5.2>,易燃爆,有毒,易挥发和贵重介质。
结构型式:外填料函式、滑动管板填料函、双填料函式〔径向双道〕41075.1,35,2600X PN DN MPa P mm D N N ≤⨯≤≤。
参数超出时参照执行。
D N :板卷按内径,管制按外径。
——仅对CS ,LAS 冷拔换热管Ⅰ级——采用较高级,高级精度〔通常用于无相变和易产生振动的场合〕 Ⅱ级——采用普通级精度 〔通常用于再沸,冷凝和无振动场合〕不同精度等级管束在换热器设计中涉与管板管孔,折流板管孔的加工公差。
GB13296不锈钢换热管,一种精度,相当Ⅰ级;有色金属按相应标准。
受直接火焰加热、受核辐射、要求疲劳分析、已有其它行业标准〔制冷、造纸等〕P D+二.引用标准1.压力容器安全技术监察规程——监察X围,类别划分*等*按管、壳程的各自条件划类,以其中类别高的为准,制造技术可分别要求。
*壳程容积不扣除换热管占据容积计,管程容积=管箱容积+换热管内部容积。
壳程容积=内径截面积X管板内侧间长度。
2. GB150-1998《钢制压力容器》——设计界限、载荷、材料与许用应力、各受压元件的结构和强度计算。
3.有关材料标准。
管材、板材、锻件等4.有关零部件标准。
封头、法兰〔容器法兰、管法兰〕紧固件、垫片、膨胀节、支座等三.设计参数1.有关定义同GB1502.设计压力Mpa分别按管、壳程设计压力,并取最苛刻的压力组合〔一侧为零或真空〕。
管板压差设计仅适用确能保证管、壳程同时升降压,如1〕自换热 2〕Pt P s均较高,操作又能绝对保证同时升降压。
3.设计温度℃0℃以上,设计温度≥最高金属温度。
0℃以下,设计温度≤最低金属温度。
〔一般可参照HG20580《设计根底》〕材料允许使用温度)≯(元件表面温度算用最高部位温度,强度计壳程元件平均温度壳程元件厚度截面金属管程元件平均温度管程元件厚度截面金属⎭⎬⎫--t t ][][σσ()()固定管板式温差可不计环境温度壳材线胀系数温壳程筒体沿全长平均壁按附录F确定管材线胀系数换热管沿全长平均壁温⎪⎭⎪⎬⎫**-*-St αα 应力计算用* 对气-气或液-液可近似取管、壳程介质平均温度的平均值。
换热器制造工艺指导流程
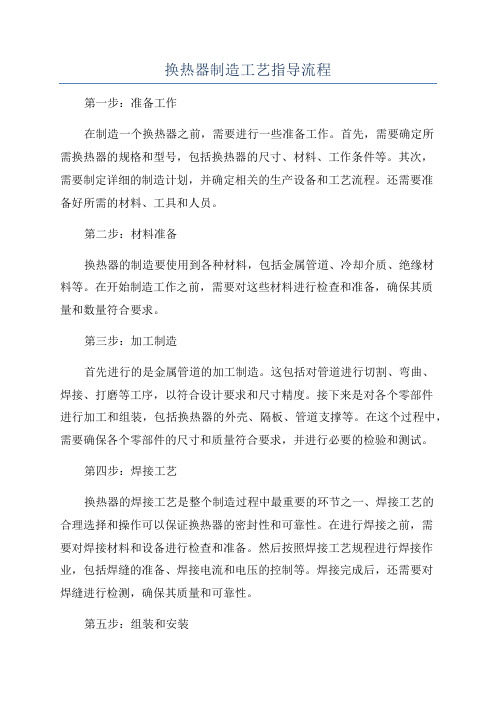
换热器制造工艺指导流程第一步:准备工作在制造一个换热器之前,需要进行一些准备工作。
首先,需要确定所需换热器的规格和型号,包括换热器的尺寸、材料、工作条件等。
其次,需要制定详细的制造计划,并确定相关的生产设备和工艺流程。
还需要准备好所需的材料、工具和人员。
第二步:材料准备换热器的制造要使用到各种材料,包括金属管道、冷却介质、绝缘材料等。
在开始制造工作之前,需要对这些材料进行检查和准备,确保其质量和数量符合要求。
第三步:加工制造首先进行的是金属管道的加工制造。
这包括对管道进行切割、弯曲、焊接、打磨等工序,以符合设计要求和尺寸精度。
接下来是对各个零部件进行加工和组装,包括换热器的外壳、隔板、管道支撑等。
在这个过程中,需要确保各个零部件的尺寸和质量符合要求,并进行必要的检验和测试。
第四步:焊接工艺换热器的焊接工艺是整个制造过程中最重要的环节之一、焊接工艺的合理选择和操作可以保证换热器的密封性和可靠性。
在进行焊接之前,需要对焊接材料和设备进行检查和准备。
然后按照焊接工艺规程进行焊接作业,包括焊缝的准备、焊接电流和电压的控制等。
焊接完成后,还需要对焊缝进行检测,确保其质量和可靠性。
第五步:组装和安装在完成零部件的加工和焊接之后,需要对它们进行组装和安装。
这包括对各个零部件进行清洁和处理,以保证其表面的洁净度和光滑度。
然后进行零部件的组装,包括换热器的外壳和管道的安装等。
组装完成后,还需要进行总体调试和测试,以确保换热器的性能和功能正常。
第六步:质量检测在换热器制造过程中,还需要进行质量检测和控制。
这包括对原材料的质量进行检测,对加工和焊接过程进行检测和控制,以及对最终产品进行检测和测试等。
通过这些检测和控制措施,可以确保换热器的质量,提高其可靠性和使用寿命。
第七步:包装和运输最后一步是对换热器进行包装和运输。
在包装过程中,需要对换热器的各个零部件进行保护,以防止在运输过程中受到损坏。
包装完成后,还需要进行相应的标识和记录,以便于追溯和检查。
管壳式换热器通用工艺规程
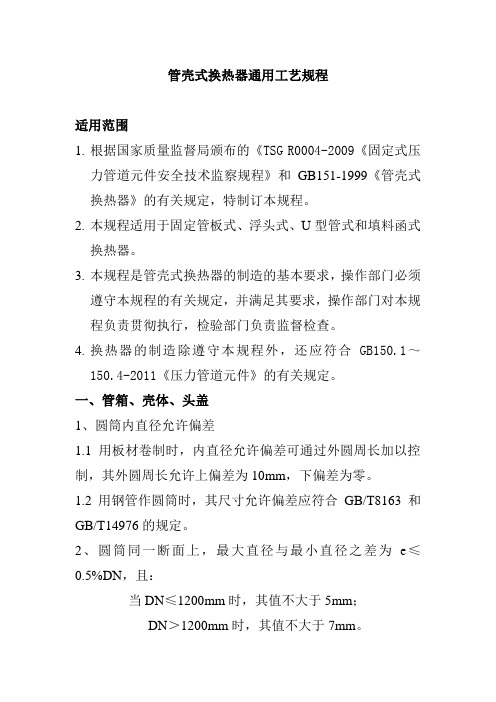
管壳式换热器通用工艺规程适用范围1.根据国家质量监督局颁布的《TSG R0004-2009《固定式压力管道元件安全技术监察规程》和GB151-1999《管壳式换热器》的有关规定,特制订本规程。
2.本规程适用于固定管板式、浮头式、U型管式和填料函式换热器。
3.本规程是管壳式换热器的制造的基本要求,操作部门必须遵守本规程的有关规定,并满足其要求,操作部门对本规程负责贯彻执行,检验部门负责监督检查。
4.换热器的制造除遵守本规程外,还应符合GB150.1~150.4-2011《压力管道元件》的有关规定。
一、管箱、壳体、头盖1、圆筒内直径允许偏差1.1用板材卷制时,内直径允许偏差可通过外圆周长加以控制,其外圆周长允许上偏差为10mm,下偏差为零。
1.2用钢管作圆筒时,其尺寸允许偏差应符合GB/T8163和GB/T14976的规定。
2、圆筒同一断面上,最大直径与最小直径之差为e≤0.5%DN,且:当DN≤1200mm时,其值不大于5mm;DN>1200mm时,其值不大于7mm。
3、圆筒直线度允许偏差为L/1000(L为圆筒总长),且:当L≤6000mm时,其值不大于4.5mm;L>6000mm时,其值不大于8mm。
直线度检查按GB150-2011的有关规定。
4、壳体内壁凡有碍管束顺利装入或抽出的焊缝均应磨至母材表面齐平。
5、在壳体上设置接管或其它附件而导致壳体变形较大,影响管束顺利安装时,应采取防止变形措施。
6、插入式接管、管接头等,除图样另有规定外,不应伸出管箱、壳体和头盖的内表面。
二、换热管1、碳素钢、低合金钢换热管管端外表面应除锈,换热管管端应清除表面附着物及氧化皮。
用于焊接时,管端清理长度应不小于管外径,且不小于25 mm;用于胀接时,管端应呈现金属光泽,其长度应不小于二倍的管板厚度。
2、换热管拼接时,应符合以下要求:2.1对接接头应作焊接工艺评定。
试件的数量、尺寸、试验方法按NB/T47014的规定;2.2同一根换热管的对接焊缝,直管不得超过一条;U形管不得超过二条;最短管长不应小于300 mm;包括至少50 mm 直管段的U形弯管段范围内不得有拼接焊缝;2.3管端坡口应采用机械方法加工,焊前应清洗干净;2.4对口错边量应不超过换热管壁厚的15%,且不大于0.5mm;直线度偏差以不影响顺利穿管为限;2.5 对接后,应按表1选取钢球直径对焊接接头进行通球检查,以钢球通过为合格;表1注:di—换热管内径2.6对接接头应进行射线检测,抽查数量应不少于接头总数的10%,且不少于一条,以JB/T4730的Ⅲ级为合格;如有一条不合格时,应加倍抽查;再出现不合格时,应100%检查;2.7对接后的换热管,应逐根进行液压试验,试验压力为设计压力的2倍。
《管壳式换热器设计》课件

支撑结构设计要点
考虑支撑结构的承载能力、稳定性 、防腐和防震等方面,以确保支撑 结构在各种工况下的安全性和可靠 性。
有限元分析
利用有限元分析方法对支撑结构进 行强度和稳定性分析,优化结构设 计,降低成本并提高设备性能。
密封设计
01
02
03
密封类型选择
根据工艺操作条件和介质 特性,选择合适的密封类 型,如垫片密封、机械密 封、磁力密封等。
计算公式法
根据传热基本方程和物性参数,通过计算公式计算传热系数。
热平衡计算
热平衡方程
换热器入口和出口的流体温度满足一定的关系,可以根据热 平衡方程计算换热器的效率。
效率计算
根据热平衡方程和实验数据,可以计算出换热器的效率,从 而评估换热器的性能。
05
管壳式换热器的强度设计
压力设计
压力等级
根据工艺要求和操作条件,确 定管壳式换热器的压力等级, 确保设备在正常操作和异常工 况下的安全性和可靠性。
密封设计要点
考虑密封性能、耐腐蚀性 、寿命和维护性等方面, 以确保密封装置在长期运 行中的可靠性和安全性。
密封失效预防措施
为防止密封失效,采取相 应的预防措施,如定期检 查、更换密封元件、加强 设备维护等。
06
管壳式换热器的制造与检验
制造工艺
制造流程
01
管壳式换热器的制造流程包括材料准备、切割、焊接、组装等
THANK YOU
感谢聆听
多个环节。
关键工艺参数
02
在制造过程中,需要严格控制关键工艺参数,如焊接温度、压
力、时间等,以确保产品质量。
质量标准
03
制造完成后,应按照相关质量标准进行检验,确保产品符合设
管壳式换热器ppt课件

类型与结构
类型
根据结构特点和使用要求,管壳式换热器可分为固定管板式 、浮头式、U形管式、填料函式等类型。
结构
主要由壳体、管束、管板、封头等组成,其中管束是换热器 的核心部件,通过两端固定在管板上,与壳体形成封闭空间 。
02
管壳式换热器的工作原理
传热原理
热传导
管壳式换热器中的传热过程主要 以热传导为主,热量从高温介质 传递到低温介质,通过管壁和壳
适用范围与限制
适用范围
管壳式换热器适用于高温高压的工况, 以及需要承受较大压力和温度变化的场 合。此外,由于其结构简单、可靠性强 ,管壳式换热器也常用于工业生产中的 加热、冷却和冷凝等操作。
VS
限制
管壳式换热器的传热效率较低,因此不适 用于需要高效传热的场合。此外,由于其 体积较大,管壳式换热器也不适用于空间 受限的场合。
在石油化工领域,管壳式换热器的优点包括高可靠性、耐高温高压、良好的热效 率以及适应性强等,使其成为该领域不可或缺的设备之一。
能源工业领域
能源工业是另一个管壳式换热器得到广泛应用的重要领域。在火力发电、核能发电、水力发电等过程中,管壳式换热器都扮 演着重要的角色。
在能源工业中,管壳式换热器被用于加热和冷却各种流体,如水、蒸汽、油等,以实现能量的转换和回收。其高效可靠的运 行对于提高能源利用效率和降低能源成本具有重要的作用。
维护方便
管壳式换热器的结构简单,拆装方便,便于进行维修和清 洗。
缺点
01
02
03
传热效率较低
相比于其他类型的换热器 ,管壳式换热器的传热效 率相对较低。这是由于其 结构特点所决定的。
体积较大
管壳式换热器的体积较大 ,需要占用较多的空间。
- 1、下载文档前请自行甄别文档内容的完整性,平台不提供额外的编辑、内容补充、找答案等附加服务。
- 2、"仅部分预览"的文档,不可在线预览部分如存在完整性等问题,可反馈申请退款(可完整预览的文档不适用该条件!)。
- 3、如文档侵犯您的权益,请联系客服反馈,我们会尽快为您处理(人工客服工作时间:9:00-18:30)。
管壳式换热器制造工艺规程1. 主题内容与适用范围本规程规定了管壳式换热器的壳体、管箱、折流板、支持板和管束的制造,以及换热器的组装、耐压试验及油漆包装等内容。
适用于换热器制造。
2.引用标准GB150-1998《钢制压力容器》GB151-1999《管壳式换热器》《压力容器安全技术监察规程》3. 壳体制造3.1 壳体的制造除符合本规程外,还应符合《压力容器壳体制造工艺规程》和GB151-1999《管壳式换热器》中的规定。
3.2 圆筒内直径允许偏差3.2.1 用板材卷制时,内直径允许偏差可通过外圆周长加工以控制,其外圆周长允许上偏差为10mm,下偏差为0。
3.2.2用钢管作圆筒时,其尺寸允许偏差应符合GB/T8163和GB/T14976的规定。
在遵循GB1514.4.2规定时,GB151附录 C的奥氏体不锈钢焊接钢管也可用作圆筒。
3.2.3 圆筒同一断面上最大最小直径之差e≤0.5%DN且当:(1)D N≤1200mm时,其值不大于5mm;(2)D N>1200mm时,其值不大于7mm;3.2.4 圆筒直线度允许偏差为L/1000(L为圆筒总长)。
且当:(1)L≤6000mm时,其值不大于4.5mm;(2) L>6000mm时,其值不大于8mm;直线度检查应通过中心线的水平和垂直面,即沿圆周0°、90°、180°、270°四个部位测量。
3.3 壳体内壁凡有碍管束顺利装入或抽出的焊缝均应修磨至与母材表面齐平。
3.4 壳体长度公差按GB/T1804-2000中m级规定。
3.5 接管、补强圈与壳体装配,须待壳体与法兰的两道环缝焊接完毕后,再划线开孔。
装配接管法兰及补强圈,先从壳体内部将接管焊到壳体上,并对正接管以千斤顶或支撑胎具在壳体内部顶住,然后在外面焊接接管及补强圈。
4. 管箱制造4.1 管箱短节与管箱法兰组对时,应以法兰背面为基准。
法兰的螺栓孔在施工图样无规定时均应跨中,如施工图样有规定时,按图样要求加工。
4.2 管箱法兰密封面及隔板密封面应在接管、补强圈等零部件与管箱组焊完毕并经热处理后再进行加工。
4.3 管箱接管开孔划线时,应使短节纵焊缝处于水平位置。
4.4 管箱隔板装配前,应将管箱内部环缝凸起处铲平,然后再组装焊接隔板。
4.5 焊接管箱隔板时,焊缝应与法兰端面齐平,不得凹下。
4.6 碳钢、低合金钢制的焊有分程隔板的管箱和浮头盖以及管箱的侧向开孔超过1/3圆筒内径的管箱,应在施焊后作消除应力的热处理。
奥氏体不锈钢制管箱、浮头盖一般不作焊后消除应力热处理(图样、工艺文件另有规定的除外)。
5. 管板的制造工艺要求5.1 管板、管箱盲板若用钢板制作时,非加工面(一般为管板、管箱盲板内侧表面)不平度不得超过以下规定值,否则应进行校平:(1)D N<1000mm时,≯2mm;(2)D N≥1000mm时,≯3mm;5.2 拼接管板的焊缝应进行100%的射线或超声检测,按JB4730规定的Ⅱ级或Ⅰ级为合格,除不锈钢外,拼接后的管板还应作消除应力热处理。
5.3 用20R和16MnR制作的厚度大于50mm的管板管箱盲板,其板料应在正火状态下使用。
5.4 管板孔直径及允许偏差按GB151表16~表21规定,钻孔后,应抽查不小于60°的管板中心角区域内的管孔,在这一区域内允许有4%的管孔上偏差比表16~表21中的数值大0.15mm.5.5 终钻(出钻)一侧管板表面,其相邻两管孔之间的管桥宽度B,最小孔桥宽度B min按GB1516.4.5.1要求。
终钻后抽查不小于60°管板中心角区域内的孔桥宽度,B值的合格率应不于96%,B min值的数量应控制在4%之内,超过上述合格率时,则应全管板检查。
5.6 管孔表面粗糙度5.6.1 当换热器与管板焊接连接时,管孔表面粗糙度Ra值不大于25μm.5.6.2 当换热器与管板胀接连接时,管孔表面粗糙度Ra值不大于12.5μm.5.7 胀接连接时,管孔表面不应有影响胀接紧密性的缺陷,如贯通的纵向或螺旋状刻痕等。
5.8 钻管板孔时,应用冷却液冷却以保持管板孔内表面的清洁,不准有油漆及铁屑。
胀接管孔划槽时应使用专用划槽器加工。
5.9 管板钻孔时的加工工序一般为钻、扩两道工序,有特殊要求时应增加铰制工序,一般不允许一次钻削成形。
6. 折流板支持板的制造工艺要求6.1 环形折流板、支持板及弓形折流板等须按整圆下料(特殊情况按工艺文件)。
折流板毛坯下料的后,必须除掉毛刺并校平,拼接板料要将焊缝磨平,再将每台换热器的折流板、支持板压紧后沿周边点焊成一摞。
划线钻孔每次钻60~70mm,留一块作模板,直到钻完,最后加工外圆。
折流板、支持板机加工后,打上顺序标记和方向标记,然后再划线,剪切多余部分,在组装时不得调换其钻孔方向,以保证多块折流板管孔的同心度。
6.2 折流板、支持板的管孔直径及允差按GB151中5.9.3的规定,但允许超差0.1mm的管孔数不得超过4%。
6.3 折流板和支持板外直径及允许偏差应符合GB151表41的规定。
6.4 折流板、支持板钻孔后应按图样要求,对管孔进行倒角修磨,去除毛刺。
7. 管束制造7.1 换热器与管板连接型式及尺寸要求7.1.1 强度胀适用于设计压力小于或等于4Mpa,设计温度小于或等于300℃以及操作中无剧烈运动、无过大的温度变化和无明显的应力腐蚀的情况,换热管材料的硬度值一般须低于管板材料的硬度值,有应力腐蚀时,不应采用管端局部退火的方式来降低换热处管的硬度。
其结构型式和尺寸按GB151表32和图33的规定。
7.1.2 强度焊可用于GB151标准规定的设计压力,但不适用于有较大振动及有间隙腐蚀的场合,其结构型式和尺寸按GB151表33和图34的规定。
7.1.3 胀焊结构适用于密封性能要求较高,承受振动或疲劳载荷,有间隙腐蚀及采用复合管板的场合。
其结构型式和尺寸按GB151表35和图36,同时还应遵守本规程7.1.1和7.1.2的规定。
7.2 换热管和管板的连接连接部位的换热管和管板孔表面应清理干净,不得留有影响胀接或连接质量的毛刺、铁屑、锈斑、油污等。
7.2.1 胀接连接(1)、胀接连接时,其胀接长度,不得伸出管板背面(壳程侧),换热管的胀接部分和非胀接部分应圆滑过渡,不得有急剧的棱角。
(2)、胀接可采用柔性胀接(液压胀、橡胶胀、液袋式液胀)。
胀接前,应通过计算胀接压力进行试胀,试胀试样不少于5个,测试胀接接头的拉脱力,贴胀应达到1Mpa,强度胀接应达到4Mpa,(此测试可按不同换热管的规格先行进行工艺测试,制造产品时直接应用测试结果)。
(3)、选用机械胀接时应控制胀管率以保证胀紧度。
7.2.2 焊接连接(1)、焊接连接时,焊渣及凸出于换热管内壁的焊瘤均应清除,焊缝缺陷的返修,应先清除缺陷,后补焊。
(2)、换热管与管板焊接接头,施焊时应进行焊接工艺评定。
7.3 换热管的制造工艺要求7.3.1 用于胀接的碳钢管,无耐应力腐蚀要求时,可对管端进行退火处理。
管端退火长度不宜小于2倍的管板厚度。
7.3.2 管端外表面应除锈,用于焊接时,管端长度应不小于管径,且不小于25mm 用于胀接连接时,管端应除锈至呈金属光泽,其长度不小于2倍的管板厚度。
7.3.3 换热管拼接(1)、对接焊接接头应作焊接工艺评定。
试件的数量、尺寸、试验方法按JB4708的规定;铜、铝、钛焊接接头可参照执行。
(2)、同一根换热管,其对接焊缝不得超过1条(直管)或2条(U形管);最短管长不应小于300mm,包括至少50mm直管段的U形弯管范围内不得有拼接焊缝。
(3)、管端坡口应采用机械加工方法加工,焊前应清洗干净。
(4)、对口错量应不超过换热管壁厚的15%。
且不大于0.5mm;直线度偏差以不影响顺利穿管为限。
(5)、对接后,应按表8.3.3-5选取钢球直径,对焊接接头进行通球检查,以钢球通过为合格。
表7.3.3.-5 单位: mm注:di-----换热管内径(6)、对接接头应进行射线检测,抽查数量应不少于接头总数的10%。
且不少于1条,JB4730Ⅲ级为合格,如有一条不合格时,应加倍抽查;再出现不合格时,应100%检查。
(7)、对接后的换热管,应逐根进行液压试验,试验压力为设计压力的2倍。
7.3.4 U形管的弯制(1)、U形管弯段的圆度偏差,应不大于换热管名义外径的10%。
但弯曲半径小于2.6倍换热管名义外径的U型弯管段可按15%验收。
(2)、U形管不宜热弯(3)、当有耐应力腐蚀要求时,冷弯U型管的弯管段及至少包括150mm的直管段应进行热处理:a、碳钢、低合金钢管作消除应力热处理;b、奥氏体不锈钢管可按供需双方商定的方法进行热处理。
(4)、有色金属管一般不作消除应力热处理,确有需要时,可按供需双方协商的方法及要求进行消除应力热处理。
7.4 管束的组装7.4.1 调整管板间距,保证管束长度的偏差符合图7.4.1的规定。
拉杆上的螺母应拧紧,以免在装入和抽出管束时因折流板窜动而损伤换热管。
7.4.2 管束在组装时,应保证管板与换热管垂直及两管板的平行。
测量两管板的四点,两管板之差不得超过;DN<1000mm 2mmDN≥1000mm 3mm7.4.3 穿管时不应强行敲打,换热管表面不应出现凹瘪或划伤。
7.4.4 予装调试合格的管束,应先沿管板周边选数根管子对称定位胀接或焊接,先胀或先焊固定管板,后胀或后焊浮动管板,为防止因胀焊次序不当而产生的管板变形,要分区对称跳胀或跳焊,不要在局部区域过于集中胀焊。
7.4.5 胀焊后管板密封面不平度不得超过1mm。
8. 换热器组装8.1 换热器零、部件在组装前应先认真检查和清扫,不得留有焊疤、焊条头、焊接飞溅物、浮锈及其它杂物等。
8.2 接管与法兰及筒体组装时,应保证法兰面的水平或垂直,其偏差不大于法兰外径的1%,且不大于3mm。
法兰螺栓孔一般应跨中布置。
8.3 支座垫板、补强圈和壳体的搭接焊缝与任意相邻焊缝的距离,以及接管与壳体连接的角焊缝与任意相邻焊缝的距离均不应小于3倍的壳体壁厚,且不小于50mm。
8.4 吊装管束时,应采取必要的措施,防止管束变形和损伤换热管。
8.5 螺栓的紧固至少应分3遍进行,每次的起点应相互错开120°,紧固顺序可按图8.5的规定。
图8.58.6 重叠式换热器须进行予组装,并留出不焊的支座及接管,调整中心距,待予组装后再进行焊接。
重叠支座间的调整板应在压力试验合格后点焊于下面换热器的支座上,并在重叠支座和调整板外侧标有永久标记,以备现场组装对中。
8.7 换热器组装尺寸的允许偏差见图8.7 .图8.79. 压力试验9.1 换热器的压力试验除符合本规程外,还应符合《压力容器压力试验和气密性试验工艺规程》中的有关规定。