等温锻造
60MN等温锻造液压机结构设计概述

60MN等温锻造液压机结构设计概述摘要:等温锻造液压机是主要面对航空、航天等领域的高端锻件成形,以及针对小批量、定制化产品而专门设计的锻造液压机。
文中从设备主体结构上阐述了60MN等温锻造液压机的主要结构和设计思路,可以为设计者提供一些设计思路、注意要点和借鉴性意见。
关键词:60MN;等温锻造;液压机;主体结构引言由于金属钛具有一系列优质特性,钛合金、高温合金等难变形材料已成为“大型飞机”“载人航天和探月工程”等国家科技专项重要的航空材料。
难变形材料成形装备是航空高性能零件制造的基础装备。
普通模锻成形的锻件存在精度差、材料利用率低、锻件性能不稳定等问题。
超塑性成形的总压力仅相当于普通模锻的几分之一到十几分之一,可一次性成形出高精度的薄壁、薄腹板、高筋和其他形状复杂的锻件,且超塑成形后锻件的晶粒细小均匀,有高而且均匀的整体力学性能。
采用较小吨位的成形机即可成形出较大和结构复杂的零件,使用过程中节能效果十分明显。
1、60MN等温锻造特点60MN等温锻造是一种先进的热加工锻造工艺,即在相对恒温条件下,以一种较低的变形速度和速率,实现较少的锻造火次,达到对特种锻件精密成型。
其特点有:(1)大幅度减小锻造材料的抗应变能力;(2)锻件内外密度分布均匀、变形均匀、组织性均匀;(3)可以准确控制,提升产品质量和性能;(4)避免模具激冷,提高了模具寿命和锻造材料流动性及填充模腔的能力;(5)节约原材料,减少机械加工;(6)可实现一致性批量生产。
随着航空、航天、造船行业的发展,对等温锻造工艺的要求也越来越高,为了获得高精度、高性能的等温锻造工件,对等温锻造设备的工作速度和四角偏差精度的要求及稳定性提出了更高的指标。
2、60MN等温锻造液压机结构设计2.1移动工作台设计方案等温锻造液压机由于模具、工装复杂,重力比较大,所以一般此类液压机均设置有移动工作台,方便工装工具和模具加热炉的整体移出。
有些企业更会根据自身工件的批量需求设置双移动工作台(T形),这样会缩短模具加热和工装工具的安装等待时间,效率提高近1倍。
6061铝合金锻件等温锻造的工艺设计

2. Dongguan Polytechnic College,Dongguan 523808,Guangdong)
南方金属 SOUTHERN METALS
Sum. 185 April 2012
文章编号: 1009 - 9700( 2012) 02 - 0049 - 04
6061 铝合金锻件等温锻造的工艺设计
林燕虹1 ,彭 燕2
( 1. 广东松山职业技术学院,广东 韶关 512126; 2. 东莞职业技术学院,广东 东莞 523808)
图 2 多模膛模具
总第 185 期
林燕虹,等: 6061 铝合金锻件等温锻造的工艺设计
51
与普通模锻相比,精密模锻具有提高锻件的尺 寸精度和表面质量的优点. 精密模锻工艺能获得表 面质量好、机械加工余量少且尺寸精度较高的锻件. 终锻模膛是为锻件的精密模锻设计的. 如图 3 所示.
出模.
图 3 闭式精密模膛与粗锻模膛
收稿日期: 2011 - 11 - 02 作者简介: 林燕虹( 1984 - ) ,女,2010 年五邑大学机械制造及自动化专业硕士研究生毕业.
南方金属
50
SOUTHERN METALS
2012 年第 2 期
图 1 刹车踏杆锻件
1. 2 锻件材料特性 铝合金在锻造时通常具有一些特点如流动性
差,在高温范围内变形抗力对变形速度的变化敏感, 锻造温度范围很窄,导电性好等; 再加上产品对象加 工成形时变形程度较大,给锻造带来更多的困难. 因 此,对复杂铝合金零件,特别是高强度铝合金零件的 成形加工,大多采用等温锻造的方法来完成.
国内外镁合金等温锻造进展_付传锋

[3] Chen Shuang,Liu Weimin.Preparation of DDP-coated PbS Nanoparticles and Investigation of theAnti-wear Ability of the Prepared Nanoparticlesas Additive in Liquid Paraffin[J].Wear,1998,218:153Ο158.[4] Hu Z S,Dong J X.Study on Anti-wear and Re2ducing Friction Additive of Nanometer TitaniumOxide[J].Wear,1998,216:92Ο96.[5] Rapoprt L,Leshchinsky V,Lapsker I,et al.Tribo2logical Properties of WS2Nanoparticles underMixed L ubrication[J].Wear,2003,255:785Ο793.[6] 赵修臣,刘颖,王富耻.添加油酸修饰的纳米Fe3O4粒子润滑油的摩擦学性能研究[J].润滑与密封,2005(2):103Ο104.(编辑 郭 伟)作者简介:赵修臣,男,1971年生。
北京理工大学材料科学与工程学院讲师。
研究方向为纳米材料制备与应用。
发表论文10余篇。
刘 颖,男,1957年生。
北京理工大学材料科学与工程学院教授。
余智勇,男,1959年生。
北京理工大学材料科学与工程学院副教授。
国内外镁合金等温锻造进展付传锋1张钰成1赖周艺2胡亚民21.中国南车集团戚墅堰机车车辆工艺研究所,常州,2130112.重庆工学院,重庆,400050摘要:镁合金常温下塑性差、散热快,在共晶温度以上锻造时会发生严重开裂,这就决定了镁合金不宜采用常规锻造方法。
等温锻造成形过程中温度基本不变,可消除镁合金在常温下成形性能差的问题。
Ti60合金等温锻造工艺研究

供 。用金 相法 测 得 其相 变 点 为 100℃ 。原 材 料 棒 5 坯 经陕西 宏远 航 空锻 造 有 限责 任 公 司 改 锻 后 的显 微 组 织为 典型 的等轴组 织 ,见 图 1 。
优点¨ 。从 2 J 0世纪 5 O年代开始 ,被广泛应用于航 空航天 、军事、医疗 、石油 、化 工等领域 ,并且范 围逐步 扩大 ,受 到世 界 各 国的 高 度 重视 。 目前 在 国
作者 简介 :毛智勇( 9 3 ) 16 一 ,男 ,高级工程师 。
钛 工 业 进 展
1 8
Ttnu d sr Pors i imI ut rges a n y
2 9卷
降低。这主要是由于随着锻造温度的升高 ,组织 中
的初 生等 轴 O相 减少 ,在 随后 的 热处 理 过 程 中 ,更 L
逐渐减 少 , 转 变 组 织 所 占比 例增 多 ,次 生 板 条
te a fr ig a df r n e eau e n e t r am n h r l o gn t i ee ttmp r tr sa d h a e t e t m t
厚度增 加 。单 相 区锻造 得 到 全 片 层 组织 。不 同组 织结构 经 同样 热处 理工艺 处理后 组织差 别较 大 。 () 2 在两 相 区低 温 锻 造 的合 金 具有 最 好 的塑性 , 常规锻 造合 金强 度 升 高 ,塑 性 降 低 。近 J 造 合 金 B锻 的强 度较 常规锻 造 合 金 低 ,塑 性 略 高 。而 锻 造 合
最 大 ,其 次为 常规 锻 造 合金 ,近 锻造 的合 金 塑 性 损 失程度 最小 。
LD11铝合金的等温锻造与超塑性参数探析
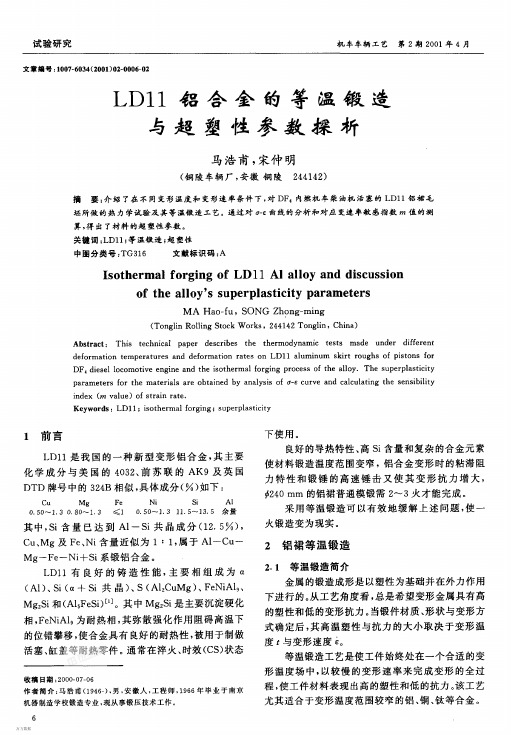
呱 了0 .
心 山
! G L 冲
库)
峨 1 】01
叼 1 众2
峨 1 ,03
国. 2份.
叮 30.
尸 ,
叼
充 氮
叼1 人 “输 功瓜5
心 16 0 01 立了
氢
胜 卜
田.  ̄ 40 以 SG 冲
+4以 2丫 习
为, 在上述条件下 L l Dl 材料呈现超塑性。
图1 0℃时不同E 曲线 4 8 下的。 一。
23 等温锻造效果 . 根据铝裙内腔为变截面的结构特点, 变形方式 以反挤压为主, 按上述工艺参数用 L 1 热挤压棒 D 1 材在液压机上进行实物等温挤压工艺试验, 获得了 一火挤出样品的结果。 在此基础上, 又进行了小批量 生产性试验, 优化和稳定了工艺, 已投人批量生 现 产。锻件充填饱满, 轮廓清晰, 余量明显减少。剖面 流线均匀, 无穿流、 涡流现象。等温条件下的变形使 锻件组织与性能的稳定性提高, 工件经淬火、 时效 后, 性能完全满足设计要求。 3 超 塑性探 析
C F u Mg e N i S i A l -. 0 0 -. 05^13 8"13 (1 05-13 .^1. 余量 .0 . .0v . 1 5 - 5 1 3
其中,i S 含量已达到 A -S 共 晶成分(2 5 0, I i 1. 0) C , 及F,i uMg eN 含量近似为 1 1属于 A -C - ,, I u
2 铝裙等温锻造
21 等温锻造简介 .
金属的锻造成形是以塑性为基础并在外力作用 下进行的。 从工艺角度看, 总是希望变形金属具有高 的塑性和低的变形抗力。 当锻件材质、 形状与变形方 式确定后, 其高温塑性与抗力的大小取决于变形温
等温锻造加热系统

等温锻造加热系统等温锻造加热系统可真是个超有趣的玩意儿呢!你想啊,在锻造的世界里,温度就像一个调皮的小精灵。
如果温度控制不好,那锻造出来的东西可能就歪七扭八,完全不是我们想要的样子。
而等温锻造加热系统就像是一个超级保姆,把温度这个小精灵照顾得服服帖帖的。
这个系统啊,就像是一个温暖的小窝,让金属材料在里面舒舒服服地接受加热。
它可不是那种简单粗暴的加热方式哦。
它会很温柔地、慢慢地让金属达到合适的温度,就像我们在冬天慢慢给冰冷的手取暖一样。
这样的话,金属在锻造的时候就不会因为突然的温度变化而发脾气,变得难以塑形。
在工厂里,这个等温锻造加热系统就像是一个默默奉献的小英雄。
那些工人叔叔阿姨们可喜欢它啦。
因为有了它,他们的工作就变得轻松不少呢。
不用老是担心温度过高或者过低,只要把材料放进这个系统里,就可以放心地去做其他准备工作啦。
而且哦,这个系统还特别聪明。
它就像一个有着敏锐感觉的小动物,能准确地感知到金属材料的温度需求。
它不会过度加热,也不会加热不足。
就像我们做饭的时候,火候刚刚好,做出来的菜才美味,这个系统也是,给金属的温度刚刚好,锻造出来的成品才完美。
从材料的角度来看呢,这个系统简直就是它们的福音。
原本那些硬邦邦、冷冰冰的金属材料,进入这个加热系统后,就像是被施了魔法一样,变得柔软又听话。
就像小朋友在温暖的被窝里变得懒洋洋的,特别好摆弄。
要是没有这个等温锻造加热系统,那锻造的世界可就乱套啦。
可能到处都是不合格的产品,大家都会愁眉苦脸的。
所以啊,这个小小的系统,虽然可能看起来不起眼,但它在整个锻造的大舞台上可是起着至关重要的作用呢。
它就像一颗小小的螺丝钉,虽然小,但是缺了它,整个机器都运转不起来啦。
它让锻造这个工作变得更加高效、更加精准,也让我们的生活中能够有更多高质量的锻造产品。
这就是等温锻造加热系统的魅力所在呀。
钛合金等温锻造模具设计

目录1 绪论 (2)1.1 什么是等温锻造 (2)1.2 钛合金等温锻造技术的国内外现状和差距 (3)1.2.1 国外等温锻技术的应用 (3)1.2.2 国内等温锻技术的应用 (4)1.3 钛合金产品及其性能组织简介 (4)1.4 总结 (8)2 等温锻造工艺分析及过程 (8)2.1 钛合金(TC4)零件等温锻造的工艺性分析 (8)2.2 钛合金等温锻造特点 (11)2.3 工艺方案及参数的选择计算............................ 错误!未定义书签。
2.3.1 温度和应变速率..................................... 错误!未定义书签。
2.3.2 等温锻造变形力的计算及设备吨位的的选择............. 错误!未定义书签。
2.5 锻造过程中常见的缺陷和对策........................... 错误!未定义书签。
2.6 锻件的冷却方法....................................... 错误!未定义书签。
2.7 锻件的冷却规范...................................... 错误!未定义书签。
2.8 锻件的表面清理....................................... 错误!未定义书签。
3 等温锻造模具及加热炉设计 (13)3.1 模具设计总体分析 (13)3.1.1 模具结构分析 (13)3.1.2模具制造 (14)3.2 锻件及坏料的设计 (14)3.2.2 制定零件锻件图 (14)3.2.3 锻坯设计.......................................... 错误!未定义书签。
3.2.4 材料利用率的计算.................................. 错误!未定义书签。
3.3 上模、下模及模套的设计.............................. 错误!未定义书签。
等温锻造用模具材料的国内外研究发展状况

工艺设计
钛合金等温锻造技术的工艺设计包括锻造温度、压力和时间等方面的选择和优 化。锻造温度是影响钛合金塑性变形和组织结构的关键因素。一般来说,钛合 金的锻造温度范围为900℃~1100℃。在压力方面,等温锻造过程中应选择合 适的压力,以保证钛合金的充分变形和模具的寿命。此外,锻造时间也是影响 钛合金等温锻造效果的重要因素。
未来,国内等温锻造用模具材料的研究发展需以下几个方面。首先,提高材料 的基础研究水平,深入了解材料的性能与微观结构之间的关系,为材料的优化 设计提供理论支撑。其次,加强与国际先进国家的交流与合作,引进和发展先 进的材料制备技术和管理经验。此外,提高企业对模具材料研发和生产的投入 力度,加强产学研合作,推动科技成果转化。
等温锻造用模具材料的国内外研究发展 状况
目录
01 一、国外研究发展状 况
02
二、国内研究发展状 况
03 三、关键技术探讨
04 四、应用前景展望
05 五、结论
06 参考内容
等温锻造是一种先进的金属成形工艺,能够在恒温下实现金属材料的塑性成形。 等温锻造用模具材料作为关键组成部分,对于提高模具的使用寿命和锻造效率 具有重要意义。本次演示将介绍等温锻造用模具材料的国内外研究发展状况, 以期为相关领域的研究和实践提供有益的参考。
随着科技的不断发展,对高品质模具用钢的需求将不断增加。特别是在新能源 汽车、智能家居、5G通信等领域,对高品质的模具用钢的需求尤为迫切。因此, 未来模具用钢市场将面临巨大的发展机遇。随着绿色制造和智能制造的推广, 模具用钢产业也将不断进行技术和设备的升级改造,以适应新的市场需求和发 展趋势。
总之,国内外模具用钢市场均具 有广阔的发展前景。
锻造时间过短可能导致钛合金变形不充分,而锻造时间过长则可能导致钛合金 出现过热现象。因此,针对不同的钛合金和零件形状,工艺设计需要进行充分 的试验和优化。
等温锻造技术

等温锻造技术简介等温锻造技术是一种先进的金属加工技术,通过控制金属材料的温度和变形参数,实现对金属材料的精密成形和改善材料性能的目的。
等温锻造技术在航空航天、汽车制造、电子设备等领域具有广泛的应用前景。
工艺原理等温锻造技术的核心原理是在金属材料的等温区进行锻造,即在一定温度范围内保持金属材料的温度稳定。
通过等温锻造,可以使金属材料在锻造过程中保持一定的塑性,减少应力和变形速率对材料的影响,从而获得更好的成形效果。
工艺流程等温锻造技术的工艺流程主要包括以下几个步骤:1.材料预热:将金属材料加热至等温区的温度范围,并保持一定时间,使材料温度均匀。
2.锻造模具准备:准备好适合等温锻造的模具,包括上下模具和顶杆等。
3.材料装料:将预热好的金属材料放入锻造模具中,并确保材料的位置和摆放方式正确。
4.锻造过程:通过控制锻造机械的动作,施加适当的力和变形速率,使金属材料在等温区内进行变形。
5.冷却退火:在锻造完成后,对金属材料进行冷却退火处理,使材料的组织结构得到稳定和调整。
6.后续处理:根据需要,对锻造后的金属材料进行进一步的加工和处理,例如热处理、表面处理等。
技术优势等温锻造技术相比传统的锻造技术具有以下几个优势:1.提高材料性能:通过等温锻造,可以使金属材料的晶粒细化、均匀化,提高材料的强度、硬度和耐磨性等性能。
2.减少变形应力:等温锻造过程中,材料保持一定的塑性,减少应力和变形速率对材料的影响,降低变形应力,减少材料的变形和缺陷。
3.改善成形效果:等温锻造可以在保持材料塑性的同时,实现更精确的成形,获得更高的尺寸精度和表面质量。
4.扩大材料选择范围:等温锻造技术适用于多种金属材料,包括高温合金、钢、铝合金等,具有较大的材料选择范围。
应用领域等温锻造技术在许多领域都有广泛的应用,主要包括以下几个方面:1.航空航天领域:等温锻造可以制备高温合金的复杂零件,提高发动机和航空部件的性能和可靠性。
2.汽车制造领域:等温锻造可以制造汽车发动机的关键部件,如曲轴、连杆等,提高汽车发动机的功率和燃油效率。
等温锻造温度对TC18钛合金组织性能的影响

金相图像分析软件完成定量金相分析, 用 S- 570 型 扫描电镜对拉伸试样断口进行 SEM 观察并照相。
3 试验结果及分析
31 1 等温锻造温度对显微组织的影响 图 2 是在不同锻造温度下进行 60% 变形和标准
热处理后的显微组织照片。由图 2 可以看出, 变形 组织比较均匀, 在 755~ 860 e 两相区变形后, 合金 的微观组织均为一定数量的白色等轴初生 A 相加黑 白相间的 B 转变组织。初生 A相的数量随着温度的 升高明显减少, 颗粒增大, 等轴化程度增加; 另外 部分次生片状 A 相由于大变形也得到了球化, 形成 许多很小颗粒的 A相, 特别在图 2d 和图 2e 中更加 明显。随着温度的上升, 将发生 A相到 B 相的自发 转变, 较高的温度也提供了更多的能量, 使 A 相的 相界扩散能力增强, 有机会吞并周围细小的 A 晶粒 从而使 A相晶粒数量减少。
2. Baoji N on- Fer rous M etals W or ks, Baoji 721014, China)
Abstract: T he effect of isother mal fo rg ing temperature o n micr ostr ucture and mechanical pro per ties of T C18 allo y w as studied by isothermal for ging at the st rain r ate of 51 5 @ 10- 4 s- 1 and 60% defor matio n. T he result indicates that t he micro str uctur e o f T C18 alloy is sensitive to fo rg ing temperatur e. T he micro structur e consist s o f primar y A and tr ans-i tion B phase when the allo y is defo rmed in A+ B field. T he vo lume fr action of prima ry A decreases and its size incr eases wit h the rising o f the t em perat ur e . T y pical Widmanstat en st ruct ur e can be obtained w hen forg ing above transfor matio n po int. T he tensile str eng th is enhanced w ith t he temper ature being increased and the tensile ductility and the impact pr operty reduce. W hen fo rg ing at 860 e , bimo dal st ruct ur e co uld be o btained, the tensile str eng th and the plasticity wer e in best combination. So 860 e is a better option in iso ther mal fo rg ing. Keywords: T C18 t itanium alloy; iso thermal forg ing temper atur e; pr imar y A phase; mechanical pro pert ies
等温模锻流程

等温模锻流程等温模锻是一种金属加工工艺,主要用于生产高精度、高强度的零部件。
它通过加热金属坯料至其等温点,并在这个温度下进行模锻加工,最终得到成形零件。
这一过程包括坯料预热、模具设计、锻造工艺等多个环节。
接下来,我们将就等温模锻流程进行详细介绍。
一、坯料预热等温模锻的第一步是对金属坯料进行预热。
在预热过程中,坯料被加热至其等温点以上,通常在1200°C以上,以使其达到加工温度。
预热温度的选择影响着零件的成形质量,需要根据材料的特性和最终零件的要求来确定。
预热结束后,坯料的温度均匀性和稳定性对后续的模锻质量至关重要。
二、模具设计等温模锻的成功与否离不开合理的模具设计。
模具在等温模锻中扮演着至关重要的角色,决定着最终成品的质量和形状。
模具设计需要根据零件的形状、尺寸和工艺要求来确定,同时还需要考虑到金属的流动、材料的变形以及锻造工艺参数的设定。
合理的模具设计有利于减少材料损耗、优化成形精度和提高生产效率。
三、锻造工艺在确定好合适的模具设计后,等温模锻的锻造工艺就显得尤为重要。
在等温锻造的过程中,需要控制好坯料的温度和加工速度,以确保金属在等温点附近具有良好的延展性和流动性。
通过合理的锻造工艺,可以实现坯料的塑性变形,并最终得到成形零件。
在锻造过程中还需要注意对温度、变形量、应力等参数的实时监测和控制,以提高产品的成形精度和一致性。
四、冷却处理等温模锻完成后,需要对成形零件进行适当的冷却处理。
冷却处理一方面可以增加成形零件的硬度和强度,另一方面还可以消除由于锻造过程产生的残余应力,改善零件的机械性能和稳定性。
冷却处理的方式通常包括空冷和水冷两种,需要根据不同材料和零件的具体情况来选择合适的方法和工艺参数。
五、质量检测等温模锻的最后一道工序是质量检测。
通过对成形零件进行尺寸检测、硬度测试、金相分析等多项检测,可以确保产品达到设计要求和客户要求。
质量检测的结果将为产品的后续加工和使用提供重要参考,也有利于找出生产中存在的问题并进行及时改进。
等温锻造

等温锻造等温锻造,简称等温锻,是模具加热到坯料变形温度并以低应变速率变形的模锻。
等温锻造技术自20世纪70年代开始不断成熟,并普遍用于航空与航天飞行器重要结构零件的制造中,取得了非常明显的技术经济效益。
1 工作原理等温锻造与常规锻造不同,在于它解决了毛坏与模具之间的温度差影响,使热毛坯在被加热到锻造温度的恒温模具中,以较低的应变速率成形。
从而解决了在常规锻造时由于变形金属的表面激冷造成的流动阻力和变形抗力的增加,以及变形金属内部变形不均匀而引起的组织性能的差异。
使得变形抗力降低到常规模锻的1/10-1/5,实现了在现有设备上完成较大锻件的成形,也使复杂程度较高的锻件精锻成形成为可能。
这项技术也是目前国际上实现净成形或近净成形技术的主要方法之—。
等温锻造通常指的是毛坯成形的工艺条件,它不包含毛坏在变形过程产生热效应引起的温升所造成的温差;由于热效应与金属成形时的应变速率有关,所以在考虑到这一影响时,一般在等温成形条件下,尽可能选用运动速度低的设备,如液压机等。
为使等温锻用模具易加热、保温和便于使用维护,等温锻装置的一般构造如图1所示。
2 等温锻造的分类从等温锻造技术的研究与发展看,等温锻造可分为三类。
等温精密模锻。
即金属在等温条件下锻造得到小斜度或无图1 等温模锻用模具装置原理图斜度、小余量或无余量的锻件。
这种方法可以生产一些形状复杂、尺寸精度要求一般,受力条件要求较高、外形接近零件形状的结构锻件。
等温超塑性模锻。
即金属不但在等温条件下,而且在极低的变形速率(10-4/s)条件下呈现出异常高的塑性状态,从而使难变形金属获得所需形状和尺寸。
粉末坯等温锻造。
这类工艺方法是以粉末冶金预制坯(通过热等静压或冷等静压)为等温锻原始坯料,在等温超塑条件下,使坯料产生较大变形、压实,从而获得锻件。
这种方法可以改善粉末冶金传统方法制成件的密度低、使用性能不理想等问题。
上述三类等温锻工艺方法,可根据锻件选材和使用性能要求选用。
等温锻造技术
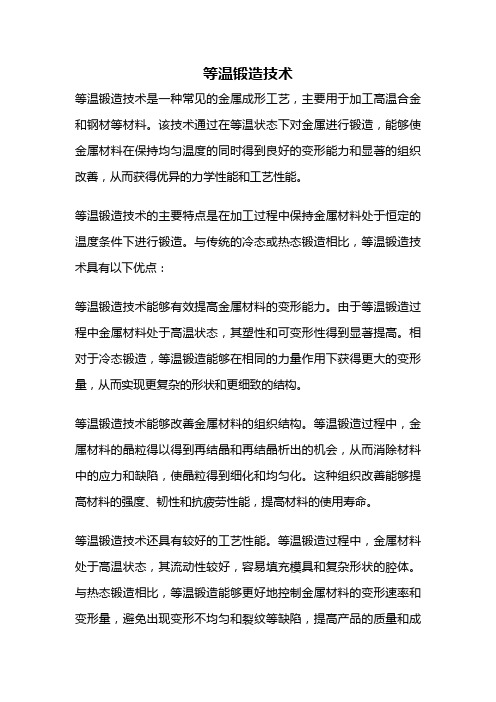
等温锻造技术等温锻造技术是一种常见的金属成形工艺,主要用于加工高温合金和钢材等材料。
该技术通过在等温状态下对金属进行锻造,能够使金属材料在保持均匀温度的同时得到良好的变形能力和显著的组织改善,从而获得优异的力学性能和工艺性能。
等温锻造技术的主要特点是在加工过程中保持金属材料处于恒定的温度条件下进行锻造。
与传统的冷态或热态锻造相比,等温锻造技术具有以下优点:等温锻造技术能够有效提高金属材料的变形能力。
由于等温锻造过程中金属材料处于高温状态,其塑性和可变形性得到显著提高。
相对于冷态锻造,等温锻造能够在相同的力量作用下获得更大的变形量,从而实现更复杂的形状和更细致的结构。
等温锻造技术能够改善金属材料的组织结构。
等温锻造过程中,金属材料的晶粒得以得到再结晶和再结晶析出的机会,从而消除材料中的应力和缺陷,使晶粒得到细化和均匀化。
这种组织改善能够提高材料的强度、韧性和抗疲劳性能,提高材料的使用寿命。
等温锻造技术还具有较好的工艺性能。
等温锻造过程中,金属材料处于高温状态,其流动性较好,容易填充模具和复杂形状的腔体。
与热态锻造相比,等温锻造能够更好地控制金属材料的变形速率和变形量,避免出现变形不均匀和裂纹等缺陷,提高产品的质量和成形效率。
等温锻造技术的应用范围广泛,特别适用于高温合金和钢材等难以加工的材料。
在航空航天、能源、汽车和机械制造等领域,等温锻造技术被广泛应用于制造复杂结构件、高精度零件和高性能材料。
然而,等温锻造技术也存在一些挑战和限制。
首先,等温锻造设备和工艺要求较高,需要具备精确的温度控制和快速的加热和冷却能力。
其次,等温锻造过程中金属材料容易受到氧化和腐蚀,需要采取相应的防护措施。
此外,等温锻造的工艺周期长,成本较高,对设备和人力资源的需求也较高。
等温锻造技术是一种重要的金属成形工艺,能够在保持金属材料均匀温度的条件下实现优异的变形能力和组织改善效果。
在未来的发展中,随着材料科学和工艺技术的进步,等温锻造技术有望在更广泛的领域得到应用,为制造业的发展提供更多的可能性。
等温锻造速率对7085铝合金组织与性能的影响

第 1卷第 2 6 期
V_1I 0 . 6 No. 2
粉 末 冶 金材 料 科 学 与工 程
M atr a sSc e e a e i l inc nd Eng ne r ngofPowde e a l g i ei rM t lur y
2 1 年 4月 01
Ap . 0 1 r 2 1
LI AN G i CHEN a hu ,CHEN X n, K ng— a Xueha,CH EN ng yiPEN G - i So — , Guo s n -he g
(t e yL b rtr f o e t l g , et l o t U iesy C a gh 1 03 C i ) Sa a oa yo P wdr a u yC nr uh nvri , hn sa 0 8 , hn t Ke o Me l r aS t 4 a
等锻造速率可以得到较好的力学与腐 蚀性 能。
关键 词 :7 8 合金 ;等 温锻 造 ;再 结 晶 ;显 微 组 织 ;力 学 性 能 :剥 落 腐 蚀 0 5铝 中 图分 类 号 :T 16 G . 44 文 献标 识 码 :A 文章 编 号 : 1 7.2 42 1)—9 .6 6 30 2 (0 122 00
Ab t a t Hi h s e g h au n m l y i t eman sr cu e mae il i v ai n a d s a e ih e d Th eai n h p sr c : g f n t l miu al i t t r t r s n a i o n p c f g t l . e r lt s i o sh u a t l i f o
铝合金等温锻造技术的发展

3 .国外铝合金等温锻造的进展
16 ,美 国国际商务机器公 司开始 用等温锻造成 94年
小 ,可等温模 压出形状 复杂 的且 满足尺寸精度 要求的纵 向摇臂 ,避免 了锻件 的外表 面和 内部 的冶金缺陷 ,质量
当时达到或超过法 国锻件的技术要求。
形零件 ,在 2 世纪 7 0 0年代就使用 特种等温锻 造设备和
锻件 的微观组织和综合性能具有 良好的均匀性 和一致性。
( ) 显著提高金属材料 的塑性 ,毛坯
() 由于减少或消除了模 具激冷 和材 料应变硬化 的 3
影响 ,不仅锻造载荷 小,设 备吨位 大大降低 ,而且还有 助于简 化成形过程 ,因此 可以锻造出形状 复杂 的大型结
形方法。在较 高温度条 件下 ,锻件 以较 低的应 变速率变 形 ,因此变形 材料能够充 分再结 晶,从 而可 以大 部分或
全 部 克 服 加工 硬 化 的影 响 。
所示为某型号直升飞机的铝合金 简式绝缘套 。每辆空 中
客车上使用了 10 厚铝板 ,大多数巡航导 弹的壳体是用 8t
优质铝合金铸锻 件制造的。 目前 ,铝材 在 民用 飞机 结构
合金 发 生 过 烧 ,在 3 0~40 、应 变 速 率 0 05~ 9 5% .0 00 s 范围内变形较为合适。低应变速率变形 时 , . 5 发生
高温合金 及飞机用大型结构锻件的精密设备和先进技 术。
8 0年代初期 ,前苏联 系列生产 了等 温锻造专用 液压 机, 如 20 、60 、10 t 4 0 t 5 t 3 t 60 和 0 0 液压机 。这些设 备均 安装 在现俄罗斯有关厂所 院校 ,进行 铝合金叶 片、飞机 结构 件和粉末高温合金 涡轮盘等零件的等温锻造研究 和应用 。 9 O年代 ,美 国相继开发了 50 t 1 0 t 00 和 00 0 的液压机 ( 当 时世界上最大的等温锻造液压机 ,如图 2所示) 。
- 1、下载文档前请自行甄别文档内容的完整性,平台不提供额外的编辑、内容补充、找答案等附加服务。
- 2、"仅部分预览"的文档,不可在线预览部分如存在完整性等问题,可反馈申请退款(可完整预览的文档不适用该条件!)。
- 3、如文档侵犯您的权益,请联系客服反馈,我们会尽快为您处理(人工客服工作时间:9:00-18:30)。
类别 常规锻造 等温锻造 模具温度/℃ 480 954 加压速度 /(mm/s) 76.2 0.42 变形抗力 /MPa 492.1 140.6
(4)等温锻造与热模锻造的区别 等温锻造与热模锻造的原理相似。 热模锻造是等温锻造的前期工艺方法。它是将 锻模加热到比变形坯料始锻温度低110~225℃ 的范围内。 由于减小了坯料与模具之间的温差,坯料的冷 却速度降低,特别是坯料表面温度不会过低,提 高了坯料的塑性,降低了坯料的变形抗力。 但热模锻造过程中,坯料温度不是恒定的,随 变形的进行,温度逐渐降低。
2.对润滑剂的要求 在整个锻造过程中,能在模具和毛坯间形成连 续的润滑膜,并具有低的摩擦系数; 对毛坯表面具有防护作用,防止氧化或吸收其 它气体; 兼有脱模剂作用; 不应与毛坯和模具发生化学反应; 易涂复和去除; 无毒、非易燃、非稀缺。
3.等温锻造与超塑性锻造的润滑剂 按温度区间划分: 280℃以下,用硅油或硅橡胶,成形表面光滑, 润滑剂效果好,无残留物; 280~430℃,用MoS2或MoS2钙基脂,可形成 薄而均匀的润滑层; 亚中温(600~720℃)、中温(700~900℃)、 高温区(800~1000℃),采用软化点不同的玻 璃润滑剂。
带顶出装置:制件常采用下顶出装置脱模,顶 出装置应具有足够的顶出行程与顶出力。 有控温系统:工作部分的加热温度控制是必需 的。 值得注意的是 ,等温锻造与超塑性锻造可以 使变形力降低1~2个数量级,可选用吨位较小的 液压机。
变形力计算: 常用经验公式,估算变形力:
P = p ⋅ F / 1000
式中: P--变形力(kN); F--锻件的总变形面积(mm2); p--单位变形力(MPa), 是流动应力的2~4倍, 闭式模锻、薄腹板模锻取上限; 开式模锻取下限。
§4-3等温模锻与超塑性模锻 1.锻模及加热装置 (1)加热装置 由于在变形过程中需 要保持恒温,等温模锻 与超塑性模锻需设置加 热装置。 加热装置常用的是电 感应加热和电阻加热。
模锻方法 锤上模锻 压力机模锻 液压机等温 模锻 设备吨位 3t 2500t 300t a/mm b/mm 4.5 4 0.5 8 8 4 l/mm 15 10 6 L/mm 45 40 16
模锻斜度:闭式无模锻斜度,或模锻斜度很小; 开式模锻斜度,与普通模锻相同。 顶出机构:闭式模锻须设置顶出机构; 开式模锻根据需要取舍。 收缩值:等温状态下,除了考虑坯料收缩,还 要考虑模具膨胀。
3.等温闭式模锻与超塑性闭式模锻的工艺特点 闭式模锻在等温锻造和超塑性锻造中较常见。 常规锻造中,闭式模锻常用于轴对称锻件, 而等温模锻和超塑性模锻可用于长轴类锻件与异 形锻件。 闭式模锻分为精模锻与粗模锻。 精模锻一般不需后续机加工,或仅需少量机 加工;但某些薄腹板件,由于成形需要和避免在 顶出时发生翘曲,需增加机加工余量,采用粗模 锻。 闭式模锻无飞边,其高度方向尺寸取决于坯 料大小,故下料重量公差较严。
4.模锻过程 工艺流程为: 坯料:TC4经大变形锻造后,制成φ101.6mm ×7mm的 坯料; 喷涂润滑剂:坯料预热至300℃后,在专用旋转装置上 喷涂; 锻前加热:900℃,氩气保护。装模后均热,调整模温; 锻造:速度0.1~1mm/min,压力500~1200kN,保压 3~6min; 顶出:顶出力50~200kN,顶出前对易变形部位冷却; 后续处理:在石棉堆中缓冷。喷砂去除涂层。
(5)为使等温锻 造的模具易加热、 保温和便于使用 维护,等温锻造 装置的基本结构 如图所示。
2.超塑性锻造的基本特点 (1)超塑性 指材料在低载荷作用下,其拉伸变形的延伸率 超过100%的现象。凡具有能超过100%延伸率 的材料,称为超塑性材料。目前,世界上超塑性 材料的最高延伸率达到了5000%。
∆为收缩量;t1、t2分别为室温和模锻温度;a1、 a2分别为坯料与模具的线膨胀系数;L为模具尺 寸。
∆ = (t 2 − t1 )(a1 − a2 ) L
(3)模具材料 常规锻造、热模具锻造、等温锻造及超塑性锻 造时,模温与锻造时间的差异,见图。
选取模具材料时,应保证模具零件在不同温 度下,有可靠的使用性能。 铝、镁合金:可采用热模具钢; 钛合金及钢:采用高温合金。 有时,为了提高模具寿命。适当降低模具温度, 适当提高变形速度。
§4-4等温锻造与超塑性锻造的摩擦与润滑 1.特点 与常规锻造相比,具有下列特点: 模具的高温:模具在高温时,增强了变形金属 与模具接触面上的相互扩散作用,提高了摩擦系 数,使变形金属易发生向模具表面转移,脱模难 度加大; 应变速率低:使接触面的咬合与润滑剂的挤出 更容易,导致摩擦系数的增加; 变形时间长:延长变形时间,为金属的氧化和 接触面扩散提供了有利条件。
3.设备与模具 (1)设备 成形设备为Y32-200型四柱液压机,台面尺 寸大,封闭高度高,下液压缸顶出。 (2)模具材料 选用镍基铸造高温合金,其断裂强度均为相同 条件下TC4超塑流动应力的三倍以上,满足强度 要求。 (3)模具结构 采用闭式模锻,模口直接导向。
(4)加热装置 采用感应加热。 上下模各用一个 感应器加热,上 下模温度一致, 且开模时也可加 热,降温少。
§4-5工艺实例 以钛合金涡轮盘的超塑性锻造为例。 1.零件 涡轮盘材料为TC4,直径101.6mm,带有72 个轴向小叶片。零件净重125g。 原工艺采用仿形铣床,材料利用率低,刀具消 耗大,废品率高。 采用超塑性锻造工艺成形。
2.工艺条件 TC4的超塑性锻造规范为: 等轴细晶的α+β双相组织,晶粒尺寸小于5µm; 在α+β相区锻造,锻造温度900~950℃; 锻造速度较低,0.1~1mm/min; 此时,TC4的单向拉伸伸长率为175~500%, 流动应力为10~40MPa。
形状复杂零件;
超塑性 开式 铝、镁、钛合金的叶片、 充模好,变形力低,组织性能 锻造 模锻 翼板等薄腹板带筋件或 好,变形道次少,弹性恢复小; 超塑性 闭式 难变形复杂零件, 锻造 模锻 如钛合金涡轮盘。
成形件精度高,较少机加工余 量。
4. 等温锻造和超塑性锻造锻件的特点 (1)余量小,精度高,复杂程度高。锻后机械 加工量小,只局部加工,甚至不加工。 (2)锻件纤维连续,力学性能好,各向异性不 明显。毛坯一次变形量大,金属流动均匀,锻件 可获得等轴细晶组织,使锻件的屈服强度、低周 疲劳性能及抗应力腐蚀能力显著提高。 (3)锻件无残余应力。由于应变速率小,金属 软化充分,内部组织均匀,消除了残余变形,不 存在变形不均匀引起的内外应力差。 (4)材料利用率高。 (5)提高了材料的塑性:金属中变形的位错, 由于回复与再结晶而消除,使得金属具有良好的 塑性
第四章
等温锻造与超塑性锻造
§4-1等温锻造与超塑性锻造的特点及分类 在常规锻造条件下,一些难成形的金属材料, 如钛合金、镁合金及合金钢等,或者因为锻造温 度范围窄,或者因为塑性较差,或者因为变形抗 力较高,成形时困难较大。 特别是形状复杂件,如薄壁、高肋零件,毛 坯热量很快散发,变形温度急剧下降,变形抗力 迅速增大,塑性急剧降低,不仅需要大吨位设备, 也会造成锻件开裂。 为解决这些问题,发展了等温锻造和超塑性 锻造技术。
(2)超塑性锻造的基本特点 材料具有等轴稳定的细晶组织; 锻造温度在再结晶温度以上, 即T≥(0.5~0.65)T熔; 应变速率非常低,控制在 0.01~0.0001(1/s)范围内。 此时,材料具有很低的变形抗力、超高的延伸 率。在低载荷下,可以加工出高精度的薄壁、高 肋复杂锻件。
3.等温锻造和超塑性锻造的分类
§4-2等温锻造与超塑性锻造设备选择 等温锻造与超塑性锻造均在低速下进行,一般 采用液压机,且要求: 可调速:工作行程的速度调节范围在 0.1~1mm/s; 可保压:工作滑块在额定压力下,可保压30min 以上; 封闭高度高、工作台面尺寸大:为安装模具、 加热装置、冷却板、隔热板等工装,便于操作, 需较大尺寸的封闭高度和工作台面,活动工作台 更好;
1.等温锻造的基本特点 (1)为防止毛坯温度散失,等温锻造时,模具 和坯料要保持在相同的恒定温度下。这一温度, 或等于热锻温度,或稍低于热锻温度。 (2)材料在等温锻造时,具有一定的粘性,即 对应变速率非常敏感,等温锻造变形速度很低。
等温锻造一般在运动速度较低的液压机上进行, 选择的活动横梁工作 速度为0.2~2mm/s, 坯料的应变速率低于 0.01(1/s)。 此时,坯料的变形 抗力降低,塑性大大 增加,呈现超塑性现 象。
材料在超塑性拉伸时,应力很低,无加工硬化, 对变形速度极为敏感。流动应力与应变速率的关 系为:
S = kε
•m
m为应变速率敏感性指数,m值越大,延伸率也 越大。普通金属m≈0.02 ~0.2;超塑性金属m ≈0.3 ~1.0;m=1时,变为粘性流动。
超塑性一般分为: 细晶超塑性:又称结构超塑性。材料必须具有 必要的组织结构,即具有直径在5µm以下的稳定 的超细晶粒,然后给以一定的恒温和变形速度条 件。 相变超塑性:又称动态超塑性。金属具有相变, 或同素异构转变,在低载荷作用下,金属在相变 点,附近反复加热、冷却,经过一定次数的温度 循环后,获得很大延伸率。
(2)模具结构设计 模膛结构:闭式锻造用模具,多采用镶块组合 结构;开式多采用整体式结构; 导向:闭式多用模口导向;开式多用导柱导向
飞边槽:开式锻模带有飞边槽。其作用有:产 生径向阻力,使金属充填型腔深处;容纳多余的 金属,缓冲上下模的冲击。 由于等温状态下,飞边不易冷却,故需要大大 减小尺寸,特别是桥部厚度尺寸,以产生足够的 桥部阻力,弥补等温条件带来的飞边阻力下降。
下表列出了等温模锻和超塑性模锻的应用及特点: 分类 等温 锻造 等温 锻造 锻造 形式 应用 特点
开式 形状复杂零件,薄壁件, 余量小,弹性恢复小,可一次 成形; 模锻 难变形材料零件; 闭式 机加工复杂的、性能要 无飞边,无斜度、需顶出,模 求高的和无斜度的锻件; 具成本高,锻件性能高、精度 模锻 高、余量小;