小模数弧齿锥齿轮的加工
弧齿锥齿轮加工原理简明讲义

弧齿锥齿轮加工原理简明讲义
1.弧齿锥齿轮的几何参数
2.加工工艺
设计:根据实际的传动需求和工艺要求,确定弧齿锥齿轮的几何参数和加工方案。
车削:首先,将原材料铸件的外形车削成近似的锥面形状。
然后,使用设备上的特殊刀具,分多次进行精细车削,逐步接近设计要求的锥面形状。
车削过程需要注意锥面的角度和平面度的控制。
齿面磨削:在车削完成后,需要对齿面进行磨削,以提高弧齿锥齿轮的精度和平稳性。
通常使用专用的磨削机床和磨削刀具来完成此过程。
磨削过程需要准确控制磨削刀具和齿轮的位置和相对运动,以确保磨削后的齿面符合设计要求。
齿面淬火:淬火是提高弧齿锥齿轮齿面硬度和耐磨性的重要方法。
在齿面磨削完成后,通过加热和快速冷却的方式,使齿面达到所需的硬度。
淬火后需要进行回火处理,以减轻淬火过程中可能产生的内应力和脆性。
3.加工工艺控制
为了保证弧齿锥齿轮的加工质量和精度,需要进行工艺控制。
主要包括锥面加工角度的控制、齿面加工参数的控制、齿面磨削刀具和设备的选择等。
此外,加工过程中还需进行必要的检测和调整,以确保加工精度的达标。
总之,弧齿锥齿轮的加工原理是通过设计和加工工艺来实现的。
通过准确控制各个环节的参数和工艺操作,可以获得满足设计要求的弧齿锥齿
轮。
加工过程需要注意各个环节的控制和调整,以确保加工质量和精度的达标。
小模数航空螺旋锥齿轮全工序法铣齿法综述
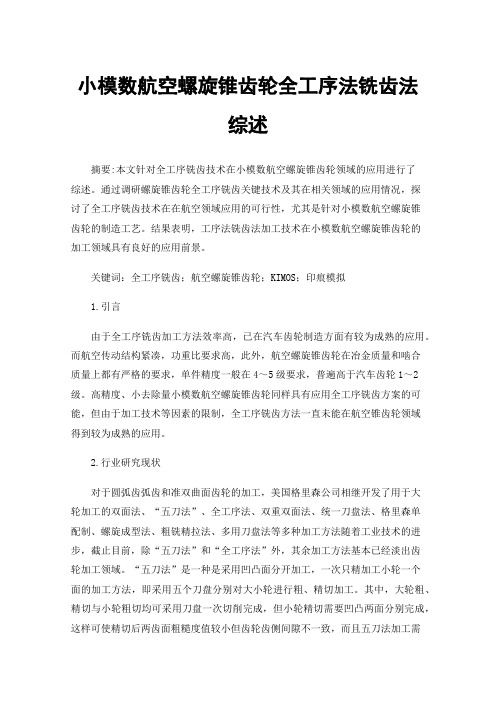
小模数航空螺旋锥齿轮全工序法铣齿法综述摘要:本文针对全工序铣齿技术在小模数航空螺旋锥齿轮领域的应用进行了综述。
通过调研螺旋锥齿轮全工序铣齿关键技术及其在相关领域的应用情况,探讨了全工序铣齿技术在在航空领域应用的可行性,尤其是针对小模数航空螺旋锥齿轮的制造工艺。
结果表明,工序法铣齿法加工技术在小模数航空螺旋锥齿轮的加工领域具有良好的应用前景。
关键词:全工序铣齿;航空螺旋锥齿轮;KIMOS;印痕模拟1.引言由于全工序铣齿加工方法效率高,已在汽车齿轮制造方面有较为成熟的应用。
而航空传动结构紧凑,功重比要求高,此外,航空螺旋锥齿轮在冶金质量和啮合质量上都有严格的要求,单件精度一般在4~5级要求,普遍高于汽车齿轮1~2级。
高精度、小去除量小模数航空螺旋锥齿轮同样具有应用全工序铣齿方案的可能,但由于加工技术等因素的限制,全工序铣齿方法一直未能在航空锥齿轮领域得到较为成熟的应用。
2.行业研究现状对于圆弧齿弧齿和准双曲面齿轮的加工,美国格里森公司相继开发了用于大轮加工的双面法、“五刀法”、全工序法、双重双面法、统一刀盘法、格里森单配制、螺旋成型法、粗铣精拉法、多用刀盘法等多种加工方法随着工业技术的进步,截止目前,除“五刀法”和“全工序法”外,其余加工方法基本已经淡出齿轮加工领域。
“五刀法”是一种是采用凹凸面分开加工,一次只精加工小轮一个面的加工方法,即采用五个刀盘分别对大小轮进行粗、精切加工。
其中,大轮粗、精切与小轮粗切均可采用刀盘一次切削完成,但小轮精切需要凹凸两面分别完成,这样可使精切后两齿面粗糙度值较小但齿轮齿侧间隙不一致,而且五刀法加工需要不断更换刀盘并重新调整刀具参数,降低了加工效率。
由于齿轮模数小,齿厚薄,在加工调整中极易产生干涉现象且不易被发现,造成质量风险、产品交付困难,急需解决。
全工序法是一种是采用凹凸面同时加工,一次成型的加工方法,该方法又称双重螺旋法,既可以提高零件表面粗糙度,保证齿隙的一致性,又可以保证渗层的均匀性,对提高产品质量具有重要意义。
精密弧齿锥齿轮的制造
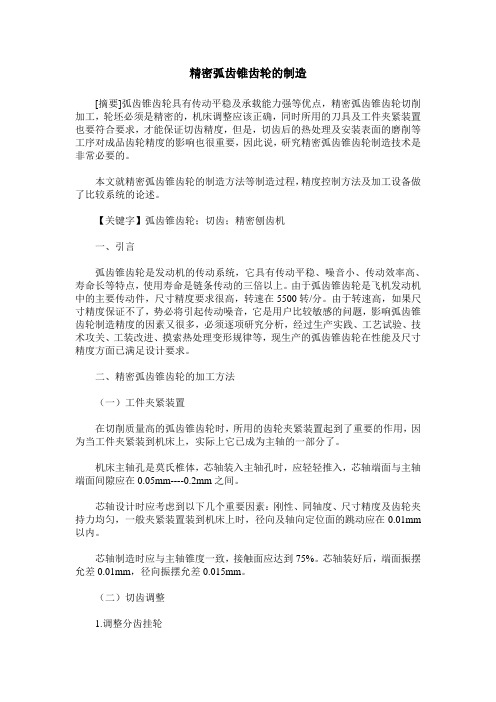
精密弧齿锥齿轮的制造[摘要]弧齿锥齿轮具有传动平稳及承载能力强等优点,精密弧齿锥齿轮切削加工,轮坯必须是精密的,机床调整应该正确,同时所用的刀具及工件夹紧装置也要符合要求,才能保证切齿精度,但是,切齿后的热处理及安装表面的磨削等工序对成品齿轮精度的影响也很重要,因此说,研究精密弧齿锥齿轮制造技术是非常必要的。
本文就精密弧齿锥齿轮的制造方法等制造过程,精度控制方法及加工设备做了比较系统的论述。
【关键字】弧齿锥齿轮;切齿;精密刨齿机一、引言弧齿锥齿轮是发动机的传动系统,它具有传动平稳、噪音小、传动效率高、寿命长等特点,使用寿命是链条传动的三倍以上。
由于弧齿锥齿轮是飞机发动机中的主要传动件,尺寸精度要求很高,转速在5500转/分。
由于转速高,如果尺寸精度保证不了,势必将引起传动噪音,它是用户比较敏感的问题,影响弧齿锥齿轮制造精度的因素又很多,必须逐项研究分析,经过生产实践、工艺试验、技术攻关、工装改进、摸索热处理变形规律等,现生产的弧齿锥齿轮在性能及尺寸精度方面已满足设计要求。
二、精密弧齿锥齿轮的加工方法(一)工件夹紧装置在切削质量高的弧齿锥齿轮时,所用的齿轮夹紧装置起到了重要的作用,因为当工件夹紧装到机床上,实际上它已成为主轴的一部分了。
机床主轴孔是莫氏椎体,芯轴装入主轴孔时,应轻轻推入,芯轴端面与主轴端面间隙应在0.05mm----0.2mm之间。
芯轴设计时应考虑到以下几个重要因素:刚性、同轴度、尺寸精度及齿轮夹持力均匀,一般夹紧装置装到机床上时,径向及轴向定位面的跳动应在0.01mm 以内。
芯轴制造时应与主轴锥度一致,接触面应达到75%。
芯轴装好后,端面振摆允差0.01mm,径向振摆允差0.015mm。
(二)切齿调整1.调整分齿挂轮分别用单分齿法和双分齿法进行计算2.调整刨刀冲程数3.调整进给挂轮一般飞机发动机的锥齿轮都属于小模数齿轮,我们用双重双面法,在弧齿机上加工,即:一对齿轮副的大轮和小轮,两齿面都是用双面刀盘,从实体齿坯上一次精加工出来,此方法生产效率较高。
弧齿锥齿轮加工原理

弧齿锥齿轮加工原理弧齿锥齿轮是一种常用的传动元件,广泛应用于各种机械设备中。
其工作原理是通过相互啮合的齿轮之间的转动,将输入轴的运动转化为输出轴的运动,实现传动功能。
在进行弧齿锥齿轮的加工过程中,需要考虑到齿轮的几何形状、啮合性能以及加工工艺等因素。
首先要进行齿轮型面的绘制。
在进行齿轮加工之前,需要根据设计要求,绘制出齿轮的各个型面图。
绘制时要准确的绘出齿数、齿廓曲线等几何尺寸。
然后,要根据齿轮的材料、硬度等参数,来确定其切削工艺。
切削工艺是实现齿轮加工的重要环节,一旦切削工艺选择不当,将会对齿轮的质量产生严重影响。
接下来,需要进行模数和参数的计算。
模数是表征齿轮几何尺寸的重要参数,它决定了齿轮的齿数、齿廓曲线等几何形状。
在计算模数时,需要根据齿数和齿轮直径来确定。
然后,需要根据齿轮的型面图,计算出齿廓曲线的参数,如法向系数、侧向系数等。
这些参数的计算需要依据齿轮的设计要求和制造要求进行,以保证齿轮的啮合性能和运动传动的稳定性。
在确定好齿轮的几何参数后,就需要选择合适的加工机床和夹具。
加工机床和夹具的选择是齿轮加工的关键环节,它们直接影响到齿轮加工的精度和效率。
一般来说,需要选择具有高精度和稳定性的加工机床,以及能够满足齿轮加工要求的夹具。
然后,要确定合适的加工刀具和工艺参数。
加工刀具的选择要根据齿轮的材料和硬度来确定,一般来说,常用的加工刀具有铣刀、车刀等。
工艺参数的确定要考虑到齿轮的加工效率和加工质量,包括切削速度、进给速度、切削深度等。
在加工工序确定之后,还需要进行添切削量的计算。
添切削量的目的是为了提高齿轮的加工质量和效率,它是在每次切削时加在切削刃上的一小量切屑,用于分离切削刃和被切削材料,并减小切削力和切削温度。
添切削量的计算可以根据经验公式和实际加工试验进行。
最后,进行实际的加工实施和检验。
在进行齿轮的加工时,需要根据工艺文件和加工要求,按照设定的加工工艺参数和工序进行实施。
加工完成后,还需要进行齿轮的检验和测量,以保证其质量和几何尺寸的准确性。
手表锥齿轮加工工艺方法

手表锥齿轮加工工艺方法手表锥齿轮是手表机芯中的重要零件之一,它具有齿数少、模数细、精度高的特点。
手表锥齿轮的加工工艺方法主要分为制齿和热处理两个步骤。
下面将详细介绍手表锥齿轮的加工工艺方法。
一、制齿工艺方法手表锥齿轮的制齿工艺主要包括车削、刨齿、插齿和制齿刀磨齿四个方法。
1. 车削法车削法是制造手表锥齿轮的主要方法之一。
其步骤如下:将原材料放在车床主轴上,使用刀具进行锥度切削,形成初步的锥度形状。
然后,通过对刀具的微调,逐渐削去多余的材料,使锥齿轮的锥度越来越接近要求的形状。
使用齿轮刀进行齿形切削,并经过不断调整,使锥齿轮的齿形达到设计要求。
2. 刨齿法刨齿法是利用刨齿机进行手表锥齿轮的加工。
具体步骤如下:将原材料固定在刨齿机工作台上,然后通过调整工作台与刨齿刀的位置,使得锥齿轮的齿轮轴线与刨齿刀轴线呈一定的夹角,从而实现锥齿轮的制齿。
刨齿法加工效率高,质量较好,适用于生产大批量的手表锥齿轮。
插齿法是通过插齿机来加工手表锥齿轮的方法。
插齿机是一种专门用于齿轮加工的机床。
其步骤如下:将锥齿轮与插齿刀压缩,使插齿刀插入锥齿轮表面,并沿锥齿轮齿向旋转,从而形成齿形。
通过不断调整插齿刀的坐标,使锥度逐渐被加工出来。
插齿法加工的手表锥齿轮质量较高,精度较高,适用于生产高精度的手表锥齿轮。
4. 制齿刀磨齿法二、热处理工艺方法手表锥齿轮加工完成后,还需要进行热处理,以提高其硬度和耐磨性。
热处理工艺方法主要包括淬火和回火两个步骤。
1. 淬火淬火是将手表锥齿轮加热至一定温度,然后快速冷却的过程。
通过淬火可以使锥齿轮的组织发生相变,从而提高其硬度和耐磨性。
淬火时,应控制加热温度和冷却速度,以保证锥齿轮的性能达到设计要求。
2. 回火手表锥齿轮的加工工艺方法主要包括制齿和热处理两个步骤。
制齿工艺方法主要有车削、刨齿、插齿和制齿刀磨齿四种方法,可根据生产需求选择适合的工艺。
热处理工艺方法主要有淬火和回火两个步骤,可以提高锥齿轮的硬度和耐磨性,以满足手表机芯的要求。
4弧齿锥齿轮的加工调整计算
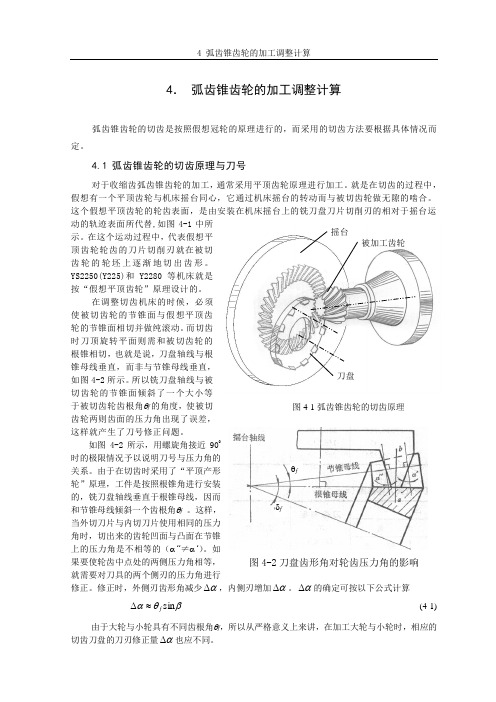
4. 弧齿锥齿轮的加工调整计算弧齿锥齿轮的切齿是按照假想冠轮的原理进行的,而采用的切齿方法要根据具体情况而定。
4.1 弧齿锥齿轮的切齿原理与刀号对于收缩齿弧齿锥齿轮的加工,通常采用平顶齿轮原理进行加工。
就是在切齿的过程中,假想有一个平顶齿轮与机床摇台同心,它通过机床摇台的转动而与被切齿轮做无隙的啮合。
这个假想平顶齿轮的轮齿表面,是由安装在机床摇台上的铣刀盘刀片切削刃的相对于摇台运动的轨迹表面所代替,如图4-1中所示。
在这个运动过程中,代表假想平顶齿轮轮齿的刀片切削刃就在被切齿轮的轮坯上逐渐地切出齿形。
YS2250(Y225)和Y2280等机床就是按“假想平顶齿轮”原理设计的。
在调整切齿机床的时候,必须使被切齿轮的节锥面与假想平顶齿轮的节锥面相切并做纯滚动。
而切齿时刀顶旋转平面则需和被切齿轮的根锥相切,也就是说,刀盘轴线与根锥母线垂直,而非与节锥母线垂直,如图4-2所示。
所以铣刀盘轴线与被切齿轮的节锥面倾斜了一个大小等于被切齿轮齿根角θf 的角度,使被切齿轮两则齿面的压力角出现了误差,这样就产生了刀号修正问题。
如图4-2所示,用螺旋角接近900时的极限情况予以说明刀号与压力角的关系。
由于在切齿时采用了“平顶产形轮”原理,工件是按照根锥角进行安装的,铣刀盘轴线垂直于根锥母线,因而和节锥母线倾斜一个齿根角θf 。
这样,当外切刀片与内切刀片使用相同的压力角时,切出来的齿轮凹面与凸面在节锥上的压力角是不相等的(α”≠α’)。
如果要使轮齿中点处的两侧压力角相等,就需要对刀具的两个侧刃的压力角进行修正。
修正时,外侧刃齿形角减少α∆,内侧刃增加α∆。
α∆的确定可按以下公式计算βθαsin f ≈∆ (4-1)由于大轮与小轮具有不同齿根角θf ,所以从严格意义上来讲,在加工大轮与小轮时,相应的切齿刀盘的刀刃修正量α∆也应不同。
图4-1弧齿锥齿轮的切齿原理 摇台 刀盘 被加工齿轮图4-2刀盘齿形角对轮齿压力角的影响 θf δf按照现有的刀号制度,将α∆的单位设置为分,并规定10分为一号,则刀号的计算公式为 小轮理论刀盘刀号βθβθαsin 610sin 6010c 111*1f f ==∆=(4-2a) 大轮理论刀盘刀号βθβθαsin 610sin 6010c 222*2f f ==∆=(4-2b) 所以,在用双面法分别加工大轮与小轮时,应该用不同刀号的刀盘。
4弧齿锥齿轮的加工调整计算

4弧齿锥齿轮的加工调整计算四弧齿锥齿轮是一种常见的齿轮类型,广泛应用于机械设备中。
在加工和调整四弧齿锥齿轮时,需要进行一系列的计算和调整,以保证齿轮的性能和运行精度。
本文将详细介绍四弧齿锥齿轮的加工调整计算。
首先,需要明确四弧齿锥齿轮的基本参数。
四弧齿锥齿轮由齿数、模数、部分齿宽系数、螺旋角等参数决定。
在加工和调整过程中,需要根据这些参数计算齿轮的各种尺寸和角度。
一、计算齿轮的齿数和模数:齿数是齿轮的重要参数之一,一般根据设计要求来确定。
模数是齿轮的副产物,是齿宽与齿数的比值。
根据齿数和模数可以计算出齿轮的模数。
齿轮的模数计算公式为:m=Z/b。
其中,m为模数,Z为齿数,b为齿宽。
二、计算齿轮的齿宽和齿高:齿宽是齿轮的另一个重要参数,一般由设计要求和工艺条件来确定。
根据齿宽和模数可以计算出齿轮的齿高。
齿轮的齿高计算公式为:h=1.25m。
其中,h为齿高、m为模数。
三、计算齿轮的分度圆半径和齿根半径:分度圆半径是齿轮最重要的参数之一,是齿轮齿槽几何形状的基准。
根据模数和齿数可以计算出齿轮的分度圆半径。
齿轮的分度圆半径计算公式为:Rm=Zm。
其中,Rm为分度圆半径,Z为齿数。
齿根半径是齿轮齿根处几何形状的基准。
根据模数可以计算出齿轮的齿根半径。
齿轮的齿根半径计算公式为:Rh=1.2m。
其中,Rh为齿根半径,m为模数。
四、计算齿轮的螺旋角和压力角:螺旋角和压力角是齿轮的重要几何参数,决定了齿轮的传动性能和运动特性。
根据设计要求和工艺条件来确定。
螺旋角的计算公式为:α=arctan(tanβ/cosγ)。
其中,α为螺旋角,β为压力角,γ为齿轮轴线与交点线之间的夹角。
压力角的计算公式为:β=10°-24°-45°(z1/z2)。
其中,β为压力角,z1为主齿轮的齿数,z2为从齿轮的齿数。
以上是四弧齿锥齿轮加工调整的一般计算方法。
在实际加工和调整过程中,还需要结合具体的工艺要求和设备精度进行一系列修正和调整。
弧齿锥齿轮加工原理
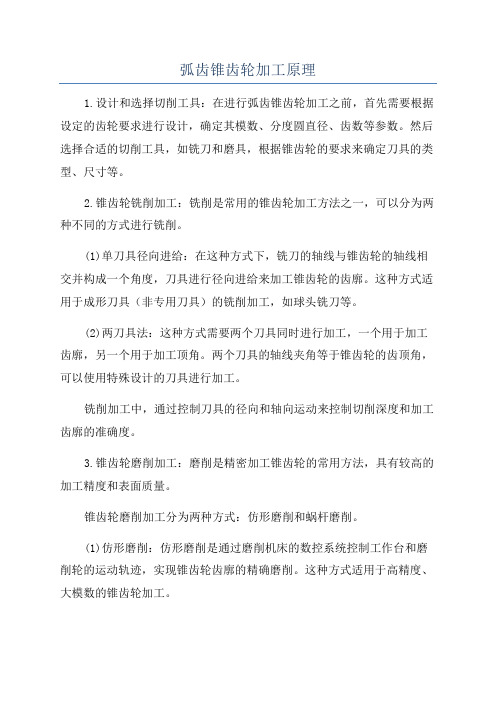
弧齿锥齿轮加工原理1.设计和选择切削工具:在进行弧齿锥齿轮加工之前,首先需要根据设定的齿轮要求进行设计,确定其模数、分度圆直径、齿数等参数。
然后选择合适的切削工具,如铣刀和磨具,根据锥齿轮的要求来确定刀具的类型、尺寸等。
2.锥齿轮铣削加工:铣削是常用的锥齿轮加工方法之一,可以分为两种不同的方式进行铣削。
(1)单刀具径向进给:在这种方式下,铣刀的轴线与锥齿轮的轴线相交并构成一个角度,刀具进行径向进给来加工锥齿轮的齿廓。
这种方式适用于成形刀具(非专用刀具)的铣削加工,如球头铣刀等。
(2)两刀具法:这种方式需要两个刀具同时进行加工,一个用于加工齿廓,另一个用于加工顶角。
两个刀具的轴线夹角等于锥齿轮的齿顶角,可以使用特殊设计的刀具进行加工。
铣削加工中,通过控制刀具的径向和轴向运动来控制切削深度和加工齿廓的准确度。
3.锥齿轮磨削加工:磨削是精密加工锥齿轮的常用方法,具有较高的加工精度和表面质量。
锥齿轮磨削加工分为两种方式:仿形磨削和蜗杆磨削。
(1)仿形磨削:仿形磨削是通过磨削机床的数控系统控制工作台和磨削轮的运动轨迹,实现锥齿轮齿廓的精确磨削。
这种方式适用于高精度、大模数的锥齿轮加工。
(2)蜗杆磨削:蜗杆磨削是利用蜗杆磨削机床进行锥齿轮的磨削加工,具有高效率、高稳定性和较低的技术要求。
蜗杆磨削适用于中小模数的锥齿轮加工。
磨削加工中,通过控制磨削轮和工件之间的相对位置和运动轨迹,来实现锥齿轮齿廓的精确磨削。
4.弧齿锥齿轮加工的注意事项:(1)切削参数控制:加工过程中需要合理控制切削速度、进给量和切削深度等参数,以提高加工效率和保证加工质量。
(2)刀具选型和刀具磨损:选择合适的刀具类型和尺寸,并及时对刀具进行磨损检查和更换,以保证加工质量和切削效率。
(3)加工精度和表面质量:弧齿锥齿轮加工需要对加工精度和表面质量进行严格控制,以满足齿轮的使用要求。
采用精密的加工设备和加工工艺,可以提高加工精度和表面质量。
(4)温度控制和润滑:加工过程中需要控制加工温度,防止过热对加工质量产生不利影响。
15弧齿锥齿轮的加工调整计算

第15章 弧齿锥齿轮的加工调整计算弧齿锥齿轮的切齿是按照“假想齿轮”的原理进行的,而采用的切齿方法要根据具体情况而定。
15.1 弧齿锥齿轮的切齿原理与刀号对于收缩齿弧齿锥齿轮的加工,通常采用平顶齿轮原理进行加工。
就是在切齿的过程中,假想有一个平顶齿轮与机床摇台同心,它通过机床摇台的转动而与被切齿轮做无隙的啮合。
这个假想平顶齿轮的轮齿表面,是由安装在机床摇台上的铣刀盘刀片切削刃的相对于摇台运动的轨迹表面所代替,如图15-1中所示。
在这个运动过程中,代表假想平顶齿轮轮齿的刀片切削刃就在被切齿轮的轮坯上逐渐地切出齿形。
YS2250(Y225)和Y2280等机床就是按“假想平顶齿轮”原理设计的。
在调整切齿机床的时候,必须使被切齿轮的节锥面与假想平顶齿轮的节锥面相切并做纯滚动。
而切齿时刀顶旋转平面则需和被切齿轮的根锥相切,也就是说,刀盘轴线与根锥母线垂直,而非与节锥母线垂直,如图15-2所示。
所以铣刀盘轴线与被切齿轮的节锥面倾斜了一个大小等于被切齿轮齿根角f的角度,使被切齿轮两则齿面的压力角出现了误差,这样就产生了刀号修正问题。
如图15-2,用螺旋角接近900时的情况予以说明刀号与压力角的关系。
由于在切齿时采用了“平顶产形轮”原理,工件是按照根锥角进行安装的,铣刀盘轴线垂直于根锥母线,因而和节锥母线倾斜一个齿根角f。
这样,当外切刀片与内切刀片使用图15-1弧齿锥齿轮的切齿原理摇台刀盘被加工齿轮相同的压力角时,切出来的齿轮凹面与凸面在节锥上的压力角是不相等的(”≠’)。
如果要使轮齿中点处的两侧压力角相等,就需要对刀具的两个侧刃的压力角进行修正。
修正时,外侧刃齿形角减少α∆,内侧刃增加α∆。
α∆的确定可按以下公式计算βθαsin f ≈∆ (15-1)其中β代表螺旋角。
由于大轮与小轮具有不同齿根角f,所以从严格意义上来讲,在加工大轮与小轮时,相应的切齿刀盘的刀刃修正量α∆也应不同。
按照现有的刀号制度,将α∆的单位设置为分,并规定10分为一号,则刀号的计算公式为小轮理论刀盘刀号βθβθαsin 610sin 6010c 111*1f f ==∆=(15-2a) 大轮理论刀盘刀号βθβθαsin 610sin 6010c 222*2f f ==∆= (15-2b)所以,在用双面法分别加工大轮与小轮时,应该用不同刀号的刀盘。
锥齿轮加工工艺

锥齿轮加工工艺1. 引言锥齿轮是一种常用的传动装置,广泛用于机械设备中。
为了生产高质量的锥齿轮,需要进行精确的加工。
本文将介绍锥齿轮加工的工艺流程和各个环节的注意事项。
2. 锥齿轮加工工艺流程锥齿轮加工的工艺流程主要包括以下几个环节:2.1 锥齿轮设计首先需要进行锥齿轮的设计,包括模数、齿数、压力角等参数的确定。
合理的设计可以保证锥齿轮在工作过程中具有良好的传动性能。
2.2 齿轮加工材料准备选择合适的材料是锥齿轮加工的关键。
常见的锥齿轮材料包括合金钢、碳素钢等。
在材料准备阶段,需要选择质量优良、机械性能良好的材料。
2.3 精密数控加工锥齿轮加工通常采用数控机床进行,以保证加工精度和生产效率。
数控加工过程包括铣削、齿轮切削、修整等操作。
2.4 轮齿磨削在锥齿轮加工中,轮齿磨削是非常重要的一步,可以提高齿轮的精度和表面质量。
轮齿磨削的工艺参数需要根据实际情况进行调整,包括磨削速度、磨削深度等。
2.5 齿轮检测和修正完成锥齿轮加工后,需要进行质量检测。
常见的检测方法包括齿距测量、齿厚测量、齿轮磨削误差测量等。
如果发现问题,需要进行相应的修正。
3. 锥齿轮加工工艺注意事项在锥齿轮加工过程中,需要注意以下几个方面的问题:3.1 材料选择选择合适的锥齿轮材料非常重要。
需要考虑材料的强度、硬度、耐磨性等性能指标,并结合具体的工作条件进行选择。
3.2 加工精度控制锥齿轮加工的精度直接影响到传动系统的性能。
在加工过程中,需要控制好各个环节的精度,特别是轮齿磨削过程中的精度控制。
3.3 加工过程中的温度控制由于锥齿轮加工过程中存在磨削、切削等高温操作,需要注意及时散热、控制温度,以避免材料的变形和质量的下降。
3.4 质量检测的重要性锥齿轮质量的合格与否,需要通过质量检测来判断。
在加工过程中,需要及时进行质量检测,并在问题发现后进行修正。
4. 结论锥齿轮加工是一项复杂的工艺,需要综合考虑材料选择、加工精度控制、温度控制等因素。
弧齿锥齿轮加工原理
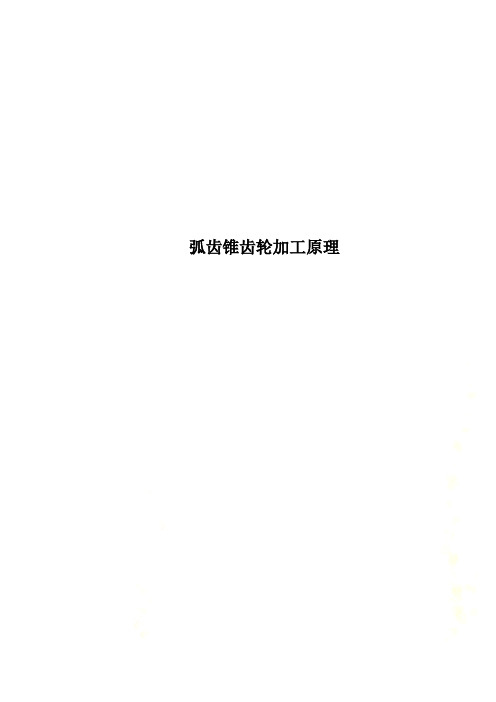
弧齿锥齿轮加工原理第一章弧齿锥齿轮及弧齿锥齿轮啮合的基本概念齿轮的种类有很多五花八门。
从齿形上分有渐开线齿轮、圆弧齿轮和其他曲线齿轮。
从齿向上分有直齿齿轮、斜齿齿轮和圆弧齿齿轮。
还有一类比较特殊的齿轮就是我们在下面将要介绍到螺旋锥齿轮。
螺旋锥齿轮目前我们能接触到的主要有两种,一个是圆弧齿锥齿轮(也叫收缩齿锥齿轮),另一个就是延伸外摆线锥齿轮(也叫等高齿锥齿轮)。
下面我们主要讨论的是圆弧齿锥齿轮。
首先我们介绍3个名词:模数模数是齿轮的一个基本参数,通俗讲模数越大,齿轮的齿距就越大,齿轮的轮齿及各部分尺寸均相应增大。
当一个齿轮的齿数为Z,分度圆直径为D,分度圆上的齿距为P时,则其分度圆的周长应为:ΠD=PZ。
则该齿轮的分度圆直径为:D=PZ/Π上式中含有无理数Π,为了设计和制造的方便,我们规定M=P/Π,称M为模数。
圆弧齿锥齿轮以大端模数作为齿轮的公称模数。
螺旋角圆弧齿锥齿轮齿面节线上任意一点的切线与该点向量半径之间的夹角,我们称之为该点的螺旋角。
而我们平常所称弧齿锥齿轮的螺旋角实际为该齿轮节线中点的螺旋角(图1-1)。
图1-1圆弧齿锥齿轮的螺旋方向即为:从齿轮正面对着齿面看,轮齿中点到大端的齿线是顺时针方向的称为右旋齿,轮齿中点到大端的齿线是逆时针方向的称为左旋齿(图1-2)。
我们要记住一对相啮合的弧齿锥齿轮,一定是其螺旋方向相反,而螺旋角的数值相等。
螺旋方向的选择一般是使其轴向力的作用方向离开锥顶,使一对齿轮在传动过程中有分离倾向,从而使齿侧间隙增大,轮齿不至于卡住。
图1-2节线(节面)(图1-3、图1-4)对于齿轮来说,无论是圆柱齿轮还是圆锥齿轮都可以抽象成两个圆柱体或圆锥体之间的纯滚动。
它们的半径由所要求的速度比值决定,此半径所确定的圆称为节圆,所确定的圆锥母线称为节线。
图1-3图1-4弧齿锥齿轮啮合属于空间啮合。
弧齿锥齿轮传动与直齿圆锥齿轮传动相比,其优点是:承载能力高,啮合平稳,对安装误差的敏感性小及噪音低等。
- 1、下载文档前请自行甄别文档内容的完整性,平台不提供额外的编辑、内容补充、找答案等附加服务。
- 2、"仅部分预览"的文档,不可在线预览部分如存在完整性等问题,可反馈申请退款(可完整预览的文档不适用该条件!)。
- 3、如文档侵犯您的权益,请联系客服反馈,我们会尽快为您处理(人工客服工作时间:9:00-18:30)。
h
4
局部综合法的基本思想
已知大轮齿面,在大轮齿面上选取一参考点,计算出大轮参考点处 的主曲率和主方向;预置参考点处的三个二阶接触参数,求出小轮参考点处的 主曲率和主方向,在此基础上确定小轮的加工参数,从而达到预控齿面接触状 况的目的。过程如下: (1)确定大轮的加工参数。 (2)在大轮齿面上选取参考点。计算大轮齿面参考点处的主曲率和主方向。 (3)预置参考点处的传动比函数的一阶导数、大轮齿面上接触迹线切线方向 、瞬时接触椭圆长半轴长度,计算小轮齿面参考点处的主曲率和主方向。 (4)确定小轮的加工参数。
h
3
格里森技术的发展-局部综合法
传统的Gleason技术以“局部共轭原理”为基础,首先确定切制大轮 齿面的加工参数,然后在大轮齿面上选取一计算参考点,求出在参 考点处与大轮齿面共轭小轮齿面的法向量及法曲率等一阶、二阶接 触参数,确定出小轮切齿调整参数。实际应用中,为了得到满意的 印痕与啮合性能指标往往需要反复修正多次。
来加工模具。
h
7
小模数弧齿的模具加工
塑胶弧齿 粉末冶金弧齿 为保证切削效率,小轮采用双面法铣齿,大轮模具采用单面法铣齿数据造型。 电火花加工模具:采用铜公,各环节的误差有:毛坯、夹具、机床调整等。 数控铣床加工模具:精度高。关键在于范成法齿面的造型。
h
8
小模数弧齿大轮的粉末冶小轮采用双面法铣齿。热处理。 3、大轮采用单面法数据分别与小轮的两个齿面相配。以该数据进行大轮的精确造型。 4、试单面法铣齿大轮,与热后小轮形成良好的啮合。以该大轮作为初始标准大轮。 5、采用合适的粉末冶金成形工艺,稳定齿形变形规律的一致性。根据大轮烧结后的啮合情况修正大轮齿
弧齿锥齿轮的加工
h
1
加工原理-局部共轭原理
概念: 根据大轮齿面,求出完全共轭的小轮齿面,在小轮齿面上选择一点M,将M点的四周铲去一层,
离M点越远,铲去的越多。从而将齿轮副的接触区修成以M点为中心的局部接触。 优点:不再对安装误差特别敏感,避免产生边缘接触。
h
2
常规方法-工艺节锥与切齿节锥分析
1、确定大轮的加工参数 2、计算齿面计算点处的曲率 3、小轮齿面计算点处的齿面曲率的修正 4、确定产形轮的参数 参考资料: 曾韬:《螺旋锥齿轮设计与加工》 北京齿轮厂译:《格里森技术资料译文集》
得到的加工参数可以保证被加工齿轮副的一阶和二阶接触参数,即 参考点的位置和参考点处的、和值,所以利用局部综合法就可以在加工之前预 先控制接触区。
h
5
小模数工业弧齿锥齿轮的加工
常规方法:双重双面法。即:大轮、小轮同时切出两个齿面。 优点:切削效率高。 缺点:从根本上不能保证齿面的正确啮合,虽采用双重收缩设计,仍存在对角接触。接触区调整困难,
调整一面同时影响另一面。 铣齿调整计算简单。
h
6
小模数弧齿的正确加工方法
为了提高切削效率,常规的双重双面法有一定的实际意义。同时造成了接触状况难以保证。 严格按照齿面啮合理论进行齿坯、铣齿参数设计,从理论上保证齿面的正确啮合。 大轮采用注塑、粉末冶金烧结成形的方法,则必须抛弃常规的双重双面法。而是要采用正确啮合的齿面
面,修模具。该过程需要反复。
h
9