机动车模具基准孔设计规范标准
汽车模具结构设计标准有哪些

汽车模具结构设计标准有哪些
汽车模具的结构设计标准主要包括以下几个方面:
1. 制造材料选择:汽车模具需要选择高强度、耐磨损、耐腐蚀的材料,如优质合金钢、工具钢或工程塑料等。
2. 结构稳定性:模具在工作过程中需要承受较大的压力和冲击,因此需要保证其结构具有足够的刚性和稳定性,以确保模具的精度和寿命。
3. 表面质量要求:模具的表面质量直接影响到汽车零部件的外观和功能,因此需要保证模具加工的表面光洁度、平整度和精度满足要求。
4. 模具尺寸精度:对于汽车模具而言,尺寸精度是非常重要的指标之一,因为模具的精度直接决定了汽车零部件的装配性能和使用寿命。
5. 模具生产工艺要求:模具的生产工艺应该合理,方便制造、安装和维修。
同时,还需要考虑到模具的耐磨耐蚀性能和容易修复性。
6. 模具使用寿命要求:汽车模具在使用过程中需要经受大量的工作循环和冲击,因此要求具有较长的使用寿命,一般应能够达到百万次以上的冲击寿命。
7. 安全性要求:汽车模具的设计应考虑到安全因素,防止意外
发生。
例如,模具中应该设置防护装置,确保操作员的安全。
8. 维修与更换要求:汽车模具在使用过程中可能会发生磨损或损坏,因此需要设计方便的维修和更换方式,以减少停机时间和成本。
9. 环境保护:汽车模具的制造和使用应符合环保要求,尽量减少对环境的污染。
总结来说,汽车模具的结构设计标准涵盖了材料选择、结构稳定性、表面质量、尺寸精度、生产工艺、使用寿命、安全性、维修与更换以及环境保护等多个方面,以确保模具的质量和性能符合汽车制造的要求。
模具本体基准孔的设计

下模本体(轴侧)
此处基准孔(工艺 面的)台可不设计
图 3.3 3.4 若因模具整体结构(限制)不满足基准孔(工艺面的)台设计的基本原则和基本要求,则可
不设计基准孔(工艺面的)台。
制订:史茂华/2006.1 5
审核:苗培/2006.1
廓上)机构的(定位)挡墙的上表面【挡墙上表面的基准孔(工艺面的)台必须在 110×80 区域
内】。见图 3.1。
制订:史茂华/2006.1 1
审核:苗培/2006.1
天津汽车模具有限公司技术公司企业标准
模具设计标准
TQM-SJ-01
QB-TS-2006-V1.0
下模【本体(俯视)】
50(~60)
基准孔(工艺面 的)台的宽可与 支撑筋等宽
下模【本体 (轴侧)】
挡墙上表面的基准 孔(工艺面的)台必
须在 110×80 区域内 内
=110
25
制订:史茂华/2006.1 2
审核:苗培/2006.1天津汽车模具有限公司术公司企业标准模具设计标准
TQM-SJ-01
QB-TS-2006-V1.0
上模【本体(仰视)】
上模【本体(仰视~轴侧)】
制订:史茂华/2006.1
图 3.1
审核:苗培/2006.1 3
天津汽车模具有限公司技术公司企业标准
模具设计标准
TQM-SJ-01
QB-TS-2006-V1.0
3.2 基准孔(工艺面的)台不要设计在镶块挡墙的上表面上、不要设计在与废料刀或其它机构 的位置与高度尺寸在 X<130、Z>120 的刀具加工干涉处。要设计在 X≥130、Z≤120 的模 具本体框架的上表面,且保证基准孔中心至模具本体轮廓 40 毫米处。见图 3.2。
汽车钣金模具设计规范

设计规范目录一、模具通用规格要求二、模具设计结构、强度要求三、模具材料及淬火硬度四、模具零件制造精度要求一、模具通用规格要求1.1退料装置退料装置要求设计合理,必须保证足够退料力,稳定可靠地将工件和废料退出凸模和凹模口之外,无任何滞阻和粘附现象。
1.2 进料、出料装置1.2.1 合理设计模具进、出料装置,保证进、出料方便可靠。
1.2.2 根据工件特征及模具结构,在进、出件侧要求设置托架,防止板料及冲压的磕碰划伤。
1.2.3 托架长度超出模具底部时,要求设计成折叠式。
1.3 托架装置为便于送料取件要求设置托架装置,采用气动装置或弹性装置(视情况而定),应保证冲压件可靠、平稳升起,冲压件外表面不变形、无擦伤。
气管接头采用3/8,设置在上料者的右侧。
1.4 导向部分采用导柱、导板或导柱加导板三种结构。
1.5 起重装置1.5.1 起重和用于翻转模具的起重,起吊装置采用甲方认可的标准设计,模具尺寸(长+宽)<2500mm时模座应采用起重棒结构,模具尺寸(长+宽)≥2500mm时模座采用插入吊棒式吊耳结构,起重棒要求安装于模具的前后侧。
1.5.2 凡取放不方便的零部件均要求设置起吊螺孔或起重孔,但不得破坏模具结构强度。
1.5.3 起吊螺孔采用公制标准螺孔。
起重孔采用M12或M16,深度为直径的2.5倍。
1.6 安全性及设施1.6.1 模具上的活动部件均要求有安全防护措施,应有防护板、防护罩等。
1.6.2 模具码放用限位器、安全块、防护板、防护罩等可按甲方认可的乙方标准设计。
模具零部件必须充分考虑防松、防崩、防脱落、防反、防冲击等措施;模具的布置应考虑到压机的安全性、合理性以及操作方便性。
1.6.3 模具结构设计,要求充分考虑抗冲击强度,合理的操作空间以及操作的方便性、安全性。
1.6.4 导向机构、限位器、斜楔机构等尽量远离操作区;限位器要求定位可靠并且满足操作方便性。
1.6.5 模具应便于拆装,维修,调整;所有模具结构必须考虑生产中进、出料防护装置及冲压件的顶出装置等;保证手工操作的安全性,良好的视野以及足够的操作空间。
汽车模具设计标准与要求
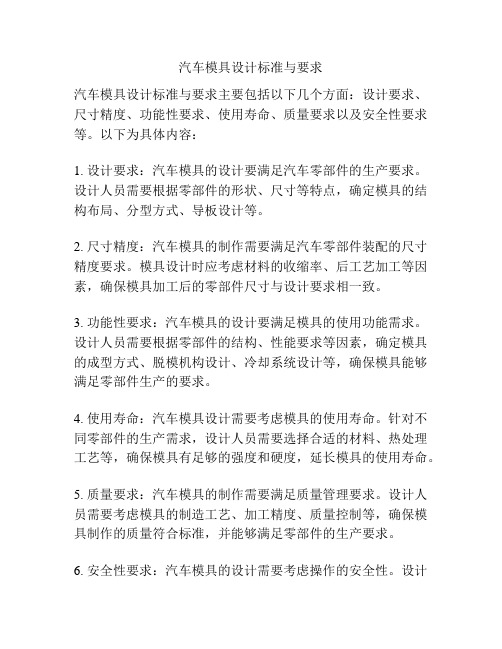
汽车模具设计标准与要求
汽车模具设计标准与要求主要包括以下几个方面:设计要求、尺寸精度、功能性要求、使用寿命、质量要求以及安全性要求等。
以下为具体内容:
1. 设计要求:汽车模具的设计要满足汽车零部件的生产要求。
设计人员需要根据零部件的形状、尺寸等特点,确定模具的结构布局、分型方式、导板设计等。
2. 尺寸精度:汽车模具的制作需要满足汽车零部件装配的尺寸精度要求。
模具设计时应考虑材料的收缩率、后工艺加工等因素,确保模具加工后的零部件尺寸与设计要求相一致。
3. 功能性要求:汽车模具的设计要满足模具的使用功能需求。
设计人员需要根据零部件的结构、性能要求等因素,确定模具的成型方式、脱模机构设计、冷却系统设计等,确保模具能够满足零部件生产的要求。
4. 使用寿命:汽车模具设计需要考虑模具的使用寿命。
针对不同零部件的生产需求,设计人员需要选择合适的材料、热处理工艺等,确保模具有足够的强度和硬度,延长模具的使用寿命。
5. 质量要求:汽车模具的制作需要满足质量管理要求。
设计人员需要考虑模具的制造工艺、加工精度、质量控制等,确保模具制作的质量符合标准,并能够满足零部件的生产要求。
6. 安全性要求:汽车模具的设计需要考虑操作的安全性。
设计
人员需要合理设置模具的安全装置、警示标识等,确保操作人员的人身安全。
总之,汽车模具设计标准与要求是为了保证模具能够满足汽车生产的需求,并达到高质量、高效率的生产目标。
模具设计人员应严格按照标准要求进行设计,确保模具的质量和安全性。
10-汽车模具基准设计规范
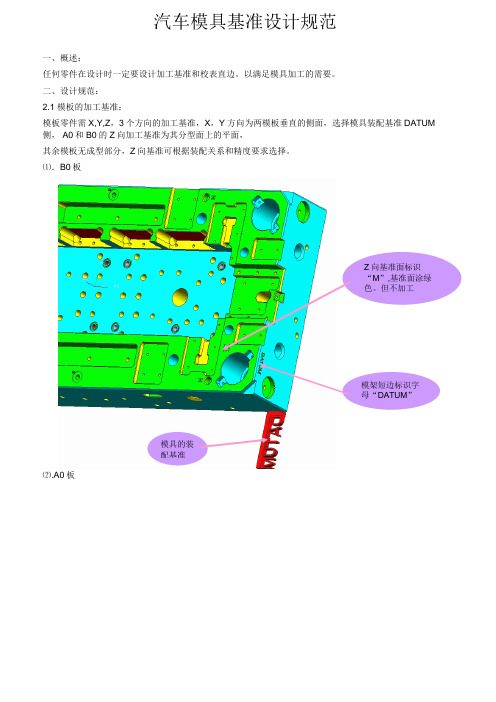
汽车模具基准设计规范一、概述:任何零件在设计时一定要设计加工基准和校表直边。
以满足模具加工的需要。
二、设计规范:2.1 模板的加工基准:模板零件需X,Y,Z,3个方向的加工基准,X,Y方向为两模板垂直的侧面,选择模具装配基准DATUM 侧, A0和B0的Z向加工基准为其分型面上的平面,其余模板无成型部分,Z向基准可根据装配关系和精度要求选择。
⑴.B0板Z向基准面标识“M”,基准面涂绿色。
但不加工模架短边标识字母“DATUM”模具的装配基准⑵.A0板⑶.面针板B2Z 向基准面标识“M ”,基准面涂绿色。
Z 向基准面标识“M ”,模架短边标识字母“DATUM ”针板顶杆胚头孔厚度尺寸有装配要求,需以针板底面为Z 向基准面。
模具的装配基准模架短边标识字母“DATUM ”⑷.DATUN加工基准DATUM模具的装配基准2.2 镶块的加工基准:加工基准装配基准设计镶块类零件的加工基准时,应尽量保证加工基准与模具的装配基准方向一致.铍铜镶块基准打“PM”,用的是铜电极。
其它铁的材料基准打“M”用的是石墨电极。
2.3 行位的加工基准:行位类零件的加工基准由准备车间打上“M”,使加工基准与装配基准同向。
2.4 斜顶的加工基准:斜顶加工基准分整体式斜顶和分体式斜顶两种。
2.4.1整体斜顶:a. 斜顶特点:斜顶头部存在一段水平面和垂直面 。
如下图:斜顶基准面b. 斜顶特点:斜顶头部存在一段水平面,斜顶尾部存在一垂直面。
如下图:c. 斜顶特点:斜顶尾部存在一段水平面和一垂直面。
如下图:d.整体斜顶布料,如下图:2.4.2 分体式斜顶:加工基准一般留在装夹侧此种斜顶头修模加工时夹斜顶杆加工。
需考虑两个问题:a,校正工件;b,加工基准。
A、校正工件:校正工件的方法:第一,可以选择水平或垂直面校正(此方法最简单,最常用);第二,可以选择单斜度面在同一高度上校正(此方法顶块常用); 第三,可以选择两个基准孔校正(此方法用在形状无直面不规范的零件)。
模具设计之典型零件基准规范.

典型零件基准规范目的:统一基准,确保基准可延续使用,提高模具精度。
要求:1、基准面加工完后,任何后续工序,改模都不允许加工或打磨基准面。
如特殊情况需加工基准面,必须经技术部审批改图。
2、基准面必须保证角尺(垂直度 , 200mm 内垂直度误差保证在 0.02mm 。
基准面粗糙度3、图纸标注出基准符号:抽芯1、铣磨六面到数 +0。
02 0。
00保证六面角尺。
2、 CNC 、 EDM 以底面为基准,分中加工。
3、钳工装配时一定保证碰穿位碰穿时,定位台与模板定位面相碰,起定位作用。
4、抽芯基准面如图示:定模板1、加工时以基准孔与分型面为基准加工。
2、检查基准孔与基准角,保证±0.02。
3、定模板基准如图示:动模芯以基准角对应两面,底面为基准加工。
动模芯基准如图示:镶件 (装模芯加工1、铣加工按 A 、 B 面为基准加工,其余面留配磨量 0.10mm 。
2、修配组以 A 、 B 面为基准配磨其余各面。
3、铣胶位时,以底面、 C 面为基准加工。
胶位厚度以 A 、 B 面为基准加工。
镶件基准如图示:铍铜镶件以底面与模芯相配的两面夹角为基准角加工。
镶件(单独加工完成1、铣磨六面 +0.040.00, 保证角尺。
2、 CNC 、 EDM 加工以底面为基准分中加工。
3、修配组配镶件时应分中磨配。
铍铜镶件基准如图示:动模板1、以基准孔,分型面为基准加工。
2、检查基准孔与基准角,保证±0.02。
行位1、 CNC 加工以 A 面, B 面, Y2、 CNC 加工后的定位台, B 面为基准, Y 分中加工。
行位基准如图示:喇叭镶件1、铣磨六面(单边留量 0。
10mm 。
2、 CNC 、 EDM 以底面为基准, X , Y 分中加工。
3、修配组配镶件时分中磨配。
汽车模具结构设计标准规范

汽车模具结构设计标准规范
汽车模具结构设计需要遵循一定的标准规范,以确保其质量和安全,具体要求如下:
1. 尺寸标准:模具尺寸应符合汽车零部件的尺寸要求。
参考汽车零部件的图纸和技术要求,确保模具的尺寸精度满足设计标准。
2. 材料要求:模具材料应选择高强度、高硬度和耐磨损的材料,如合金钢、硬质合金等。
材料的选择应满足使用寿命和使用环境的要求。
3. 结构设计:模具的结构设计应合理,确保其刚度和稳定性。
模具应易于加工和组装,并且便于维护和维修。
模具的零件要求尽量简化,以降低生产成本。
4. 冷却系统:模具应设计合理的冷却系统,以确保汽车零部件在注塑过程中能够快速冷却并保持一定的温度控制。
5. 注塑工艺要求:模具设计应考虑汽车零部件的注塑工艺要求,如射胶系统、射胶口的设置、充模比例等。
确保汽车零部件的质量和表面质量满足设计要求。
6. 模具的标准件选用:模具应尽量选用标准件进行设计和组装,并确保标准件的质量和可靠性。
7. 强度和刚度计算:模具结构应进行强度和刚度计算,确保其
能够承受正常工作状态下的载荷和应力,并防止变形。
8. 表面处理:模具的表面处理应根据汽车零部件的要求进行选择,如电镀、喷涂等。
确保汽车零部件的表面质量和外观满足设计要求。
总之,汽车模具结构设计应符合汽车零部件的要求,并满足强度、刚度、耐磨性和可维护性等方面的要求,以确保模具在使用过程中的安全和稳定性。
同时,还需要考虑到生产工艺和成本等因素,综合各个方面进行设计,以提高汽车零部件的生产效率和质量。
汽车冲模设计标准国标

汽车冲模设计标准国标
汽车冲模设计标准国标是指针对汽车冲压模具的设计和生产所制定的国家标准。
该标准规定了汽车冲模的设计、加工、装配、试验和验收等方面的要求,旨在确保汽车冲模的质量和安全性,提高汽车冲压件的质量和产能。
汽车冲模设计标准国标主要包括以下方面的内容:
1. 冲模结构:规定了冲模的结构形式、大小、精度等要求,包括冲头、模座、导柱、导套等部分。
2. 材料选用:规定了冲模所使用的材料的种类、性能、加工工艺等要求,以确保冲模的质量和使用寿命。
3. 加工工艺:规定了冲模的加工工艺和工艺要求,包括加工精度、表面处理、热处理等方面的要求。
4. 安全性要求:规定了冲模的安全性要求,包括冲模的使用寿命、安装和维护等方面的要求,以确保冲模在使用过程中的安全性。
5. 试验和验收:规定了冲模的试验和验收要求,包括冲模的试验方法、试验标准、验收标准等方面的要求。
总的来说,汽车冲模设计标准国标为汽车冲压件的生产和质量保障提供了重要的技术支持,对于保障汽车工业的发展和提高汽车产品的质量水平具有重要意义。
模具设计标准--汽车比亚迪

模具设计标准–汽车比亚迪概述本文档旨在介绍汽车模具设计的标准和规范,以汽车制造商比亚迪为例进行阐述。
模具设计是汽车生产过程中的重要环节之一,对于确保产品质量和生产效率具有重要影响。
本文将从模具设计的基本原则、技术要求、文件规范等方面进行详细介绍。
模具设计的基本原则1.工艺性原则:模具设计需要符合产品的生产工艺要求,确保模具的可制造性和生产效率。
2.可靠性原则:模具设计要求模具具有稳定的结构,能够满足长期生产的需求,并且能够保证模具的使用寿命。
3.经济性原则:模具设计需要考虑成本,尽量降低制造成本,提高模具的使用寿命,并且能够实现生产效益最大化。
技术要求材料选择模具的材料选择对模具的性能和寿命有重要影响。
在比亚迪的模具设计中,常用的材料有高速钢、合金工具钢、耐磨钢等。
根据具体模具的功能和使用要求,选择合适的材料。
结构设计模具的结构设计需要根据产品的要求和工艺流程进行合理的布局和设计。
比亚迪的模具设计中,采用了模块化设计思路,将复杂的模具拆分成多个模块,方便制造和维护。
工艺参数模具设计需要考虑各种工艺参数,如开模力、射出压力等。
这些参数需要根据具体产品的要求和工艺流程进行合理的设计和调整。
模具试验与调整模具设计完成后,需要进行试验和调整,以验证模具的性能和可靠性。
比亚迪采用了严格的试验流程和标准,确保模具能够满足生产要求。
文件规范在模具设计过程中,需要产生和管理大量的文件和文档。
为了统一管理和确保设计质量,比亚迪制定了一系列的文件规范。
设计文件设计文件主要包括设计任务书、设计方案、设计验证报告等。
这些文件需要详细描述模具的设计思路、关键技术参数和设计验证结果。
零部件图纸零部件图纸是模具设计的基础,需要包括零件的几何尺寸、材料要求、加工工艺等信息。
装配图纸装配图纸描述了模具的组成和装配方式,需要清晰地标注各个零部件的位置和连接方式。
模具标准件目录模具设计中使用的标准件需要进行统一管理,比亚迪制定了模具标准件目录,包括标准件的名称、规格、供应商等信息。
汽车冲压模具设计标准
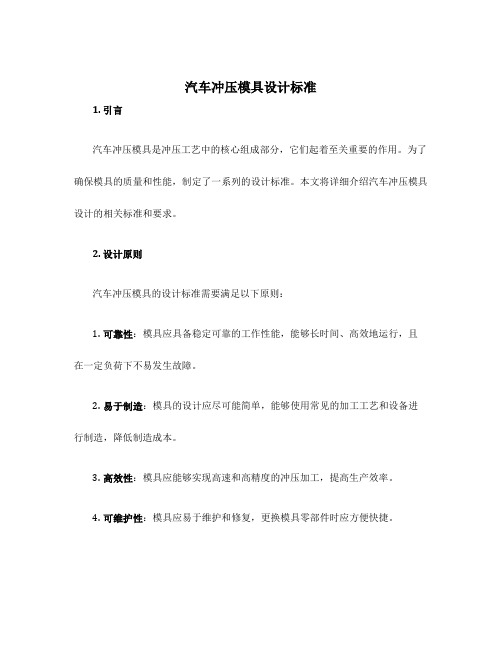
汽车冲压模具设计标准1. 引言汽车冲压模具是冲压工艺中的核心组成部分,它们起着至关重要的作用。
为了确保模具的质量和性能,制定了一系列的设计标准。
本文将详细介绍汽车冲压模具设计的相关标准和要求。
2. 设计原则汽车冲压模具的设计标准需要满足以下原则:1.可靠性:模具应具备稳定可靠的工作性能,能够长时间、高效地运行,且在一定负荷下不易发生故障。
2.易于制造:模具的设计应尽可能简单,能够使用常见的加工工艺和设备进行制造,降低制造成本。
3.高效性:模具应能够实现高速和高精度的冲压加工,提高生产效率。
4.可维护性:模具应易于维护和修复,更换模具零部件时应方便快捷。
3. 结构设计要求根据汽车冲压模具的不同类型和具体工艺要求,模具的结构设计需要满足以下要求:3.1 组合件结构汽车冲压模具通常由多个组合件组成,每个组合件都有特定的功能。
模具的组合件结构应满足以下要求:•简单可靠:组合件设计应尽可能简单,避免过多的连接点和复杂的结构,以提高稳定性和可靠性。
•便于组装和拆卸:组装和拆卸组合件时应方便快捷,避免使用过多的紧固件和工具,节约时间和人力成本。
•可互换性:组合件之间的连接应采用标准化的接口和紧固件,以实现模具部件的互换和共用。
3.2 材料选择汽车冲压模具的材料选择应满足以下要求:•硬度:模具材料应具有足够的硬度,以保证冲压过程中的切削和变形性能。
•耐磨性:模具材料应具有良好的耐磨性能,能够在长时间冲压加工中保持良好的表面质量。
•耐腐蚀性:模具材料应具有一定的抗腐蚀性能,能够应对冲压工艺中的润滑剂和金属氧化物的腐蚀。
•导热性:模具材料应具有良好的导热性能,以加速冲压工艺中的冷却和卸载过程。
3.3 寿命设计模具的寿命设计应考虑以下因素:•材料疲劳:模具在长时间使用过程中可能会发生疲劳损伤,设计时应考虑增加材料的强度和耐疲劳性能。
•应力集中:模具在冲压过程中会受到较大的应力,应避免应力集中,通过结构设计和材料选择来缓解应力分布。
企业汽车覆盖件模具设计通用规范标准
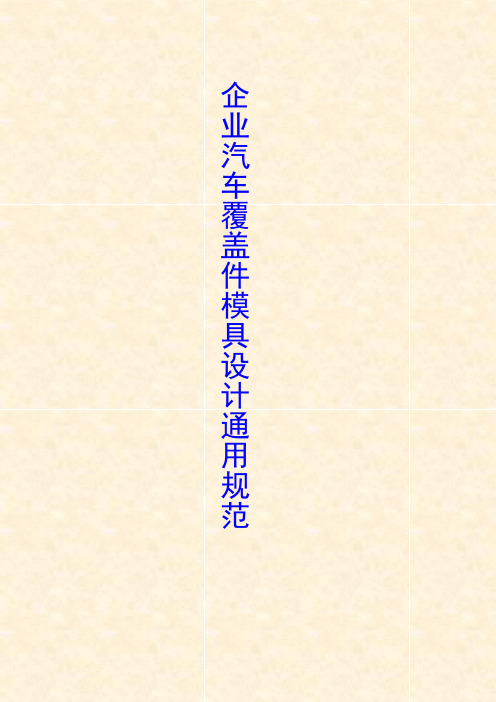
企业汽车覆盖件模具设计通用规范一、冲压生产纲领1、模具使用寿命:30万次二、大中小模具定义类型尺寸范围小型模具模具的长度+宽度≤1500中型模具1500<模具的长度+宽度<3500大型模具模具的长度+宽度≥3500三、模具导向方式模具类型外形导向方式导向腿结构拉延类小型□ A □ B □ C □ D ■ E □Ⅰ■Ⅱ中型■ A □ B □ C □ D □ E □Ⅰ■Ⅱ大型■ A □ B □ C □ D □ E □Ⅰ■Ⅱ修边冲孔类小型□ A □ B ■ C □ D □ E □Ⅰ■Ⅱ中型□ A ■ B □ C □ D □ E □Ⅰ■Ⅱ大型□ A ■ B □ C □ D □ E □Ⅰ■Ⅱ斜楔模、成形、翻边整形类(不带冲切)小型□ A □ B □ C □ D ■ E □Ⅰ■Ⅱ中型■ A □ B □ C □ D □ E □Ⅰ■Ⅱ大型■ A □ B □ C □ D □ E □Ⅰ■Ⅱ斜楔模、成形、翻边整形类(带冲切)小型□ A ■ B □ C □ D □ E □Ⅰ■Ⅱ中型□ A ■ B □ C □ D □ E □Ⅰ■Ⅱ大型□ A ■ B □ C □ D □ E □Ⅰ■Ⅱ落料冲孔类小型□ A □ B ■ C □ D □ E □Ⅰ■Ⅱ中型□ A □ B ■ C □ D □ E □Ⅰ■Ⅱ大型□ A ■ B □ C □ D □ E □Ⅰ■Ⅱ防差错措施■需要,右侧两导柱间距及导板加大10mm。
或右侧向下减小10MM □不需要。
类型方式类型A、导向退B、导向退+导柱C、导柱D、导柱组E、导板导向方式注意:导向装置不能承受侧向力,有侧向力时需增加直接反侧装置平衡侧向力导向腿结构Ⅰ、角落导向腿(外导)Ⅱ、中心导向腿(内导)三、平衡块墩死块的大小尺寸类型尺寸小型模具Ø40mm 、Ø50mmMISUMI 中型模具Ø50mm 、Ø60mm大型模具Ø60mm 、Ø70mm四、模具安全区小型模具中型模具大型模具尺寸■需要,数量为:□ 4个■ 2个□结构设计会签时,视模具结构协商确定。
汽车模具设计制造标准
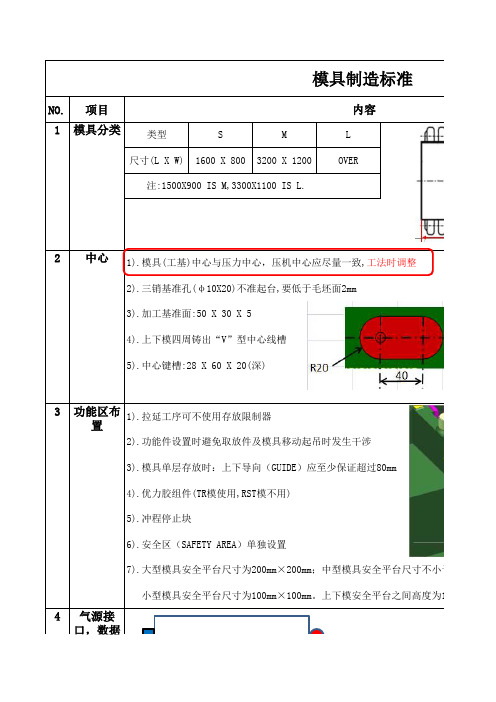
模钮选用EKSD 25-25-P10.10,冲头使用φ10定位销
①尽量设置在平面
②尽量设置在模具凹形面
③尽量设置在最终成型部位
④尽量选择材料不流动部位
⑤数量:2个,设置在钣件对角平面位置
⑥后工程冲压角有变更时,需变更角度
⑦后工程C/H位置下模型面保留
⑧后工程C/H位置上模逃让
钢块定位 铸物定位
DR/RST/FL使
18 弹簧线图 *应在弹簧压力曲线图中标示的项目
1).弹簧规格 2).压缩量
将压料力的计算过程与弹簧线图放
3).常数(K) 4).作业开始时行程及压料芯压力(F) 5).吃入量 6).压料芯行程(PAD ST) 7).最终作业结束时的力(F') 8).弹簧(SPRING)数量(n)
19 压料行程 1).剪边冲孔模无纵无凸轮时取 ST=30
无
U沟高度公差:+10
14 吊耳 1).下列是一个起重耳(HOOK)的重量,选择时按照总重量的1/2
450,750
吊耳类型
6型
10型
14型
20型
吊棒规格d
35
40
50
60
容许负载KG
3000
5000
7000
10000
使用范围
6吨至10吨 10吨至14吨 14吨至20吨
2).形状及尺寸 C30
3).注 意事 项
卷耳
HEM
HEMMING
包边
CAM
CAM
斜楔
PRO
PROGRASSIVE
级进模
TRA
TRANS FAR
多工位
2).表示方法
OP 05 BL(落料)
OP1/4 DR(落料除外)
模具设计标准汽车某汽车
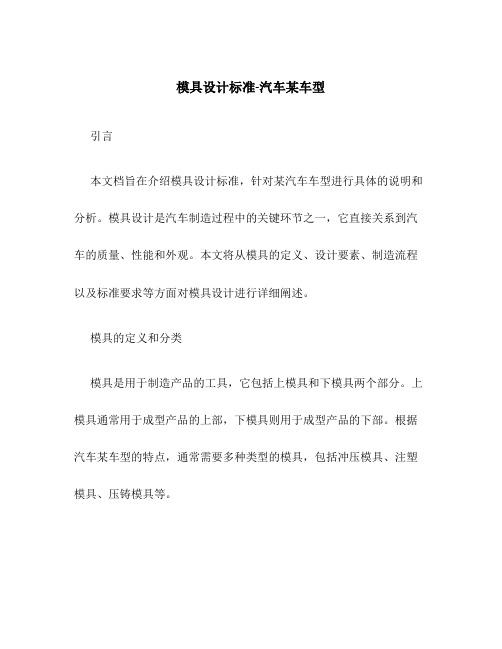
模具设计标准-汽车某车型引言本文档旨在介绍模具设计标准,针对某汽车车型进行具体的说明和分析。
模具设计是汽车制造过程中的关键环节之一,它直接关系到汽车的质量、性能和外观。
本文将从模具的定义、设计要素、制造流程以及标准要求等方面对模具设计进行详细阐述。
模具的定义和分类模具是用于制造产品的工具,它包括上模具和下模具两个部分。
上模具通常用于成型产品的上部,下模具则用于成型产品的下部。
根据汽车某车型的特点,通常需要多种类型的模具,包括冲压模具、注塑模具、压铸模具等。
冲压模具冲压模具是最常见的模具类型之一,用于汽车零部件的冷冲压成型。
它包括上下模板、导向装置、定位销、冲头、导柱等部件。
冲压模具的设计要素包括模具结构、材料选择、成形工艺等。
注塑模具注塑模具用于汽车塑料零部件的注塑成型。
它包括模仁、模板、模芯、顶针、喷嘴等部件。
注塑模具的设计要素包括模具材料、射出系统、冷却系统、顶出系统等。
压铸模具压铸模具用于汽车零部件的熔融金属压铸成型。
它包括模仁、模板、射杆、压铸腔等部件。
压铸模具的设计要素包括模具结构、冷却系统、压铸工艺参数等。
模具设计要素模具设计要素是模具设计的重要考虑因素,对于保证模具的质量和性能至关重要。
以下是一些模具设计要素的简要介绍。
精度要求模具的精度要求直接关系到成型产品的质量和尺寸精度。
根据汽车某车型的设计要求,模具的精度要求应满足相应的标准,如国家汽车工程研究中心制定的相关标准。
强度和刚性模具的强度和刚性对模具的使用寿命和稳定性有着重要影响。
模具的设计应考虑材料的选择、结构的合理性和加工工艺等因素,以确保模具具有足够的强度和刚性。
导向和定位模具的导向和定位是模具工作过程中的关键问题,它直接关系到产品的定位精度和尺寸一致性。
合理设计导向装置和定位销等部件,能够减小模具的运动误差,提高产品的一致性。
散热和冷却模具的散热和冷却系统对模具的寿命和成型效果有着重要影响。
合理设计冷却系统,能够有效降低模具的温度,提高模具的使用寿命和产品的表面质量。
汽车模具结构设计标准最新
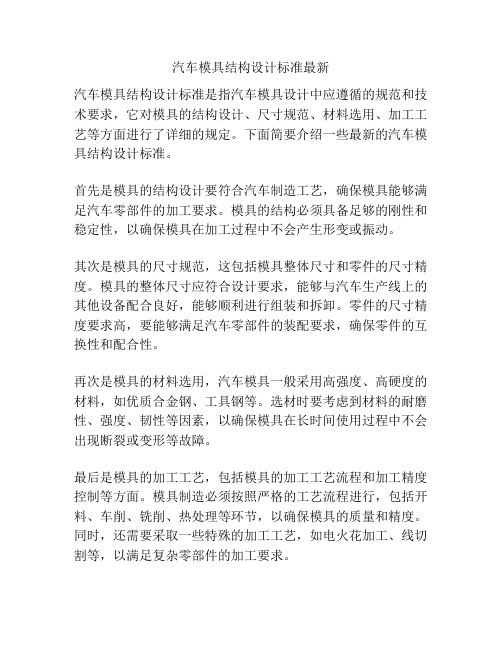
汽车模具结构设计标准最新
汽车模具结构设计标准是指汽车模具设计中应遵循的规范和技术要求,它对模具的结构设计、尺寸规范、材料选用、加工工艺等方面进行了详细的规定。
下面简要介绍一些最新的汽车模具结构设计标准。
首先是模具的结构设计要符合汽车制造工艺,确保模具能够满足汽车零部件的加工要求。
模具的结构必须具备足够的刚性和稳定性,以确保模具在加工过程中不会产生形变或振动。
其次是模具的尺寸规范,这包括模具整体尺寸和零件的尺寸精度。
模具的整体尺寸应符合设计要求,能够与汽车生产线上的其他设备配合良好,能够顺利进行组装和拆卸。
零件的尺寸精度要求高,要能够满足汽车零部件的装配要求,确保零件的互换性和配合性。
再次是模具的材料选用,汽车模具一般采用高强度、高硬度的材料,如优质合金钢、工具钢等。
选材时要考虑到材料的耐磨性、强度、韧性等因素,以确保模具在长时间使用过程中不会出现断裂或变形等故障。
最后是模具的加工工艺,包括模具的加工工艺流程和加工精度控制等方面。
模具制造必须按照严格的工艺流程进行,包括开料、车削、铣削、热处理等环节,以确保模具的质量和精度。
同时,还需要采取一些特殊的加工工艺,如电火花加工、线切割等,以满足复杂零部件的加工要求。
综上所述,汽车模具结构设计标准的最新要求是要求模具具备良好的结构设计、尺寸规范、材料选用和加工工艺等方面的要求,以确保模具能够满足汽车零部件的加工要求,提高汽车生产效率和产品质量。
汽车模具设计人员在设计过程中应严格遵循这些标准,不断创新和改进,提高模具的品质和竞争力。
汽车模具设计国标
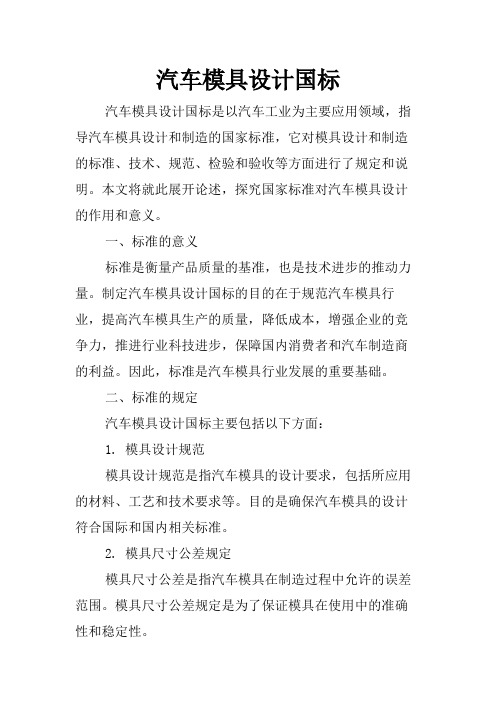
汽车模具设计国标汽车模具设计国标是以汽车工业为主要应用领域,指导汽车模具设计和制造的国家标准,它对模具设计和制造的标准、技术、规范、检验和验收等方面进行了规定和说明。
本文将就此展开论述,探究国家标准对汽车模具设计的作用和意义。
一、标准的意义标准是衡量产品质量的基准,也是技术进步的推动力量。
制定汽车模具设计国标的目的在于规范汽车模具行业,提高汽车模具生产的质量,降低成本,增强企业的竞争力,推进行业科技进步,保障国内消费者和汽车制造商的利益。
因此,标准是汽车模具行业发展的重要基础。
二、标准的规定汽车模具设计国标主要包括以下方面:1. 模具设计规范模具设计规范是指汽车模具的设计要求,包括所应用的材料、工艺和技术要求等。
目的是确保汽车模具的设计符合国际和国内相关标准。
2. 模具尺寸公差规定模具尺寸公差是指汽车模具在制造过程中允许的误差范围。
模具尺寸公差规定是为了保证模具在使用中的准确性和稳定性。
3. 模具检验规范模具检验规范是为确保汽车模具质量稳定,毫发无瑕的进行模具的检测与评估。
模具检验规范无疑可以提高模具供应商的产品质量水平,改善汽车模具的信誉度和经济效益。
4. 模具评估规定模具评估规定是指对汽车模具在使用过程中产生的效益进行评价,包括对使用寿命、维修和维护成本、使用效率等方面的评估,以便更好地为汽车制造商选购优质、经济、持久的模具提供依据。
5. 模具验收规定模具验收规定是为了确保汽车模具的质量、准确性和使用效率达到标准要求,制定的验收标准。
目的是检验汽车模具的质量与性能是否已达到要求,包括结构设计、尺寸准确性、表面质量、生产工艺等的规定。
三、标准的作用1. 提高模具的技术水平制定汽车模具设计国标可以推动模具设计技术的进步,促进设计和制造技术的传播和共享,提高模具的技术水平。
标准的制定和实施对于模具的合理设计和生产,提高模具质量、降低成本和提高模具效率具有积极意义。
2. 优化汽车模具产业结构标准的制定和实施结合汽车模具市场的实际需求,对汽车模具生产的具体方面进行规范,这些规范不仅仅局限于设计和制造技术,还包括供应商的选择、质量管控、维修服务等方面。
汽车模具圆孔标准直径及斜度规范

汽车模具圆孔标准直径及斜度规范(总4页)本页仅作为文档封面,使用时可以删除This document is for reference only-rar21year.March一、概述:为了提高加工效率,降低加工成本,需对部分型孔的设计指定其标准孔径和斜度,各工程师设计时严格按照标准型孔设计。
二、设计规范:斜导柱孔孔径设计规范:斜导柱孔直径及其避空直径:见图1,表1所示:图1斜导柱直径φ12φ16φ20φ25φ30φ35φ40φ50备注安装孔直径Dφ12φ16φ20φ25φ30φ35φ40φ50精孔,按+0公差加工避空孔直径D2φ14φ17φ21φ27φ32φ38φ42φ52避空孔,按+0公差加工圆形斜顶杆孔设计规范:根据模具结构,斜顶杆的配合方式可分如下几种:见图2、图3所示图2(镶拼模具)图3(原身模具)斜顶圆杆直径及其导滑套外径尺寸规格:见表2斜顶杆规格φ16φ20φ25φ30φ40φ50斜顶头安装φ16φ20φ25φ35φ45孔d斜顶杆配合φ16φ20φ25φ30φ40φ50孔D导滑套配合φ25φ30φ35φ40φ50φ60孔D1斜顶杆避空φ18φ22φ27φ32φ42φ52孔D2热流道喷嘴孔设计规范:、加热圈直径Φ18Φ25Φ35Φ45备注避空孔直径DΦ22Φ30Φ42Φ50粗孔,按±公差加工喷嘴避空孔直径可按热流道厂家提供的避空直径,若厂家提供避空孔我司无法加工,可按单边避空2-3MM 调整避空孔直径。
热流道厂家喷嘴头配合段直径d孔精度要求YUDO热流道Φ8、Φ12、Φ14、Φ20精孔,直径公差按H6级公差加工。
Synventive热流道Φ7、Φ14、Φ16、Φ20、Φ22、Φ24、Φ25机构类型标准角度斜顶杆孔斜度3°、5°、7°、8°、10°、12°、13°、15°斜导柱孔斜度8°、10°、12°、15°、20°、25°、30°※注意事项⑴.型孔的设计需考虑两个方面的因素:①.要满足结构的需要,②.要满足加工的要求(加工的可能性和加工效率)。
汽车模具数控加工规范

数控加工规范一Ф10基准孔加工顺序1顺序:①用Ф20刀铣直角平面(见亮即可)。
②用Ф10 专用键槽刀直窝,深度11 -16 mm。
③用Ф10专用键槽刀直窝成活。
④ S=600 rpm⑤ F=200 mm / min⑥深度10 -15 mm(用MDI、G91方式即可)⑦尽量: X 对称;Y 为0。
⑧无论何种位置或对称与否,一律用小号钢字头刻印标数!2要求:①Ф10基准孔一律在粗加工的第一序完成,并作为今后加工的唯一基准依据。
②Ф10基准孔分布情况:A上下本体的上面;B压边圈、托芯的底面及上面。
③工件再加工找正时,两孔取中误差不大于0.01 mm。
二Ф6冲头定位孔加工顺序1 精度要求:(2 加工顺序:① 中心钻点窝。
(图2)② Ф5.5钻头钻孔,深至15mm 5mm③ 6 +0。
025 两刃超硬刀加工。
S=700 F=20 图2A . 上刀后首先用百分表检测,摆动在0.02以内。
(图3)B . 第一孔加工至5mm 深时,用Ф6的销子确认如有松动,应重新检查刀具振动情况,如果合格,继续加工。
(图4) A .百分表检测 B .精度确认部分 (5mm )图C . 最后孔再次用Ф销检测确认。
3 注意:①Ф6孔应与其他轮廓、刃口、导孔同序完成。
②为保证Ф6孔与上平面的垂直度,在加工Ф6孔后,可将上平面进行光刀,切削深度为0.05mm。
三侧向基准加工规范选用φ50的精加工刀,将非加工面进行光刀,保证Y向基准在同一条直线上,然后用寻边器或百分表进行测量,并把数据记录准确,以备找正使用。
四导向面加工规范1、粗加工:选择φ63的牛鼻铣刀,转速1000转/分,进给量3000mm到4000mm之间,留0.5mm加工余量。
2、精加工:选择φ50的螺旋合金立铣刀,转速200转/分左右,进给量100~120mm,精加工完成后,反复光刀,提高加工精度。
3、测数:用杠杆表或寻边器进行测量4、插铣导板:精插时用竖走刀,步距0.5mm,转速800转/分,进给量2000mm到3000mm,然后测量数值、垂直度。
汽车覆盖件模具之CH孔做法

CH孔设计方法及用途01.合模冲头安装在拉延或成型模具上冲孔,该孔一般称为CH 孔,用于模具研配时板件的定位的基准,该孔应该尽量设置在平面上。
如果需要设置在斜面上时,最大角度不能超过15°,且CH 孔凹模要用φ4 止转销进行固定。
02.拉延(DR)或成型模(FO):其安装结构见下图:名称材质热处理规格CH孔凹模套(下) CR12MoV HRC58-62 ¢20*20CH孔冲头(上) CR12MoV HRC58-62 ¢10*20注:设计出图时制作CH 孔的冲头和凹模。
凹安装孔下方加工一个接废料的孔(打穿忽略此条),Φ14×30(装5-8片废料),CH孔凹模与冲头之间的间隙值A 由钣件的材质和料厚决定。
凹模入子型面是异形的,要做基准平位。
03.后序的模具,CH 孔的位置和大小要和拉延模的一致,即下模(需符型)设计出定位销孔Φ10×15(涂色186);上模相应的地方符型的做出避让孔Φ15×30(涂色29),不符型的避让孔至少Φ30×30mm。
CH 孔的使用要求和注意事项:①.C/H 的作用是通过同一基准孔合模,保证各工序型面精度。
②.如果拉延之后的所有工序都有两个精定位(孔定位),拉延和后序都不需要做出,预留位置即可。
如果拉延之后有任何一个工序没有两个精定位,则拉延上需要做出,没有两个精定位的工序也要做出,其他工序预留位置即可。
③.CH 孔需要做出来时,C/H 孔在拉延模上冲出(注意:双动拉延冲CH 孔的,冲头放在凹模处;凹模入子放在凸模处)。
④.特殊外观件不能设置在A 面上,可通过第二工序转换到 A 面上。
⑤.如拉延模上冲出来的只能给第二工序用,则第二工序中再冲出两个供后面的工序用。
⑥.尽量设置在平缓的面上,斜面在15°以内。
⑦.两孔距离一般是大于零件长度的2/3,零件较宽时对角设置,左右件合并,不在最后一序分离时,需要设置4 处C/H 孔。
- 1、下载文档前请自行甄别文档内容的完整性,平台不提供额外的编辑、内容补充、找答案等附加服务。
- 2、"仅部分预览"的文档,不可在线预览部分如存在完整性等问题,可反馈申请退款(可完整预览的文档不适用该条件!)。
- 3、如文档侵犯您的权益,请联系客服反馈,我们会尽快为您处理(人工客服工作时间:9:00-18:30)。
一、概述:加工基准孔的必要性:
由于机床加工精度的限制和加工取数的不准确性,要求模具在型腔加工时必须加工基准孔或基准槽,以保证后续加工取数的准确。
基准孔或基准槽和型腔需同一次装夹加工,即使出现取数不准,也可保证基准孔或基准槽和型腔的形状/位置精度相对准确.
模具的主镶和原身模板必须按要求设计相应的基准孔。
二、设计规范
2.1基准的设计原则
客户没有要求的优先设计基准槽,设计一个25*25*12mm的方槽,数量只需要一个,优先放在靠近基准角的长边上,其次放在靠近基准角的短边上
在没有空间的情况下设计φ10和φ20的基准孔,客户有要求的按照客户标准设计。
2.1基准孔的形式
基准孔应加工在平面上,对于制品分型面为曲面的,应设计并加工一平面区域来加工基准孔,并在基准孔旁设一平面标注X Y坐标值,由NC一次加工到位.如图1所示:
图1:模板或主镶上的基准孔
对于空间不足无法设计凹槽基准面的零件,可取消基准面的设计,如图2所示:
图2:空间不足的基准孔
2.2、基准孔的规格:
序号 D D1 L1 L2 W
1 20 6 1
2 2 /
2 20 10 12 2 /
3 40 20 12 3 25
⑴.φ6基准孔:小模具的主镶在没有空间的情况下,可设计φ6的基准孔,基准面可以没有;(特殊情况
下可以设计成φ6,目前φ3的基准球正在申购中,在未到货之前停止设计φ6的基准孔)
⑵.φ10基准孔:一般的中型模具A,B板尺寸在500-1500mm之间的可设计φ10基准孔;
⑶.φ20基准孔:保险杠,仪表板,风道,双门板类A,B板尺寸大于1500的模具,优选设计φ20或φ25
的基准孔。
注:因为车间机床所使用的探测棒直径尺寸为φ6和φ10的,所以基准孔的设计应首先考虑比探测棒直径大一号的基准孔。
但由于模具空间的限制,所以通常设计φ6和φ10的基准孔,加工在碰数时在基准孔中插一基准棒,用探测棒碰基准棒取数加工。
φ20的基准孔直接碰基准孔取数加工。
2.3基准孔的设计位置及设计数量:
⑴. 对于一些长度超过450mm 的原身模板,有时由于设备限制,应通过工艺评审在长度中间设计2个基准孔,以便电蚀加工碰数。
⑵.对于大型汽车模具保险杠,仪表板,风道,双门板类A,B 板尺寸大于1500的模具,需在长宽方向各设计2个基准孔.
1.原身出模板设计2个或4个基准孔,如图3、图4、图5所示:
图3
模号:B2215
设计者:王磊
长X 宽:750*650
原身模板,长度方向中间设计2个Φ10基准孔,
图4
图5
2.前后模主镶块设计1个,2个或4个基准孔。
1)主镶块长宽尺寸小于400MM 的,可设计一个基准孔。
如图6、图7所示:
模号:B2599仪表板
设计者:巴连磊
飞模定位销孔
飞模定位销孔
长X 宽:1800*1000
长X 宽:2600*1200
模号:B1208保险杠
设计者:邓作栋
应设计Φ20或Φ25
原身模板,长宽度方向中间共设计4个Φ20基准孔。
原身模板A0,长宽度方向中间共设计4个Φ10基准孔。
飞模定位销孔
飞模定位销孔
图 6
图7
2)主镶块长宽尺寸大于400MM 的,可设计2个基准孔。
模号:B2600
设计者:陈天
长X 宽:370*250
模号:B2597
设计者:王磊
长X 宽:330*205
后模镶块C201,共设计1个Φ10基准孔。
后模镶块C201,设计1个Φ10基准孔。
图8
图9
3)对于镶块Z 向尺寸落差比较大的情况,需在高处和底处各设计1个基准孔,方便Z 向碰数
模号:B1208保险杠
设计者:邓作栋
长X 宽:1800*1200
模号:B0944
设计者:崔久龙
长X 宽:570*190
后模镶块C201,设计2个Φ10基准孔。
设计在镶块中间最好
后模镶块C201,长度方向中间设计2个Φ10基准孔。
最好设计Φ20.
图10
图11
基准孔此种设计的作用:由于Z向落差比较大,此两基准孔可用于Z向的加工取数。
3)主镶块长宽尺寸大于400MM且镶块形状比较复杂的,可设计四个基准孔。
Z向
基准孔
后模镶块C201,设计
2个Φ10基准孔。
模号:B1730-C201 设计者:邓作栋
此镶块为B1730中控台后模主镶,四面形状比较复杂,为加工取数方便,可在镶块的四面都做基准孔。
φ10基准孔(建议此基准孔靠镶块中间部位设计)
长X 宽:1000*400 可更改,设计在此处
图12
图13
φ10基准孔
3. 斜顶,行位和顶块基准孔的设计
1)斜顶基准孔设计
A :比较小的斜顶
图16
B :比较大的斜顶
此面无基准孔,估计此面空间不够,和其它型孔干涉,当时没设计上。
基准孔应设计在有胶位的一侧,像此处基准孔
模号:B2319-C3B01 设计者:郑建伟
图14
图15
φ10基准孔
直边 此种比较小的斜顶头,由于是装夹斜顶杆加工,只要保证能够校表,可以不做直边和基准孔。
但为修模取数方便,在斜顶有空间的情况下能做直边和基准孔的尽量做上
图17
2)行位基准孔设计。
图18
吊装孔
此两面垂直
基准孔
对于大多数的行位,行位的尾部制动面和行位底面都可以设计成垂直的,如左图所示的行位,可以在行位上找到3个互相垂直面做为加工基准面。
此种小行位无需设计基准孔,对于大行位胶位面比较大的情况还需根据行位的尺寸设计1个或2个基准孔(基准孔打在胶位侧)。
但当行位尾部制动面和行位底面因结构决定无法设计成垂直的时候,可以在行位上设计加工基准孔。
如下图B1730-C3A04所示: 因结构决定无法设计成垂直的时候,可以在行位上设计加工基准孔。
如下图B1730-C3A04所示:
3.顶块基准孔的设计
模号:B1730-C3A04 设计者:邓作栋
此孔为设计的基准孔,可用于XYZ 三个方向的加工碰数。
比较小的形状简单的顶块
图19
图20
装夹面和基准面 (两面垂直)
装夹面和基准孔
由于结构决定,当此两面不垂直的情况时,需在行位上打基准孔,后期打电蚀和修模用。
此两面用做后期装夹的平面。
图21
图22 此小顶块的基准孔可不设计,镶块装入模板一起加工筋位。
比较小的顶块,产品胶位也不大,可以不设计基准孔和直边。
此种顶块一般不会修。
如有镶拼筋位的,也是顶块和模板或镶块装到一起火花加工。
顶块上无需基准碰数。
如下图所示:
尺寸大,胶位复杂的顶块,需设计基准孔。
图23 基准孔
同时为保证后续加工校表,此顶块需在中间切一直边长度150MM,高度
8MM,若一段不好切,可也分开切两段,每段至少30MM,保证校表的准确。
另外将两基准孔设置在与胚料棱边平行的直线上,也可用于校表用。
2.4、注意事项
1.设计时注意防止基准孔与其它型孔的干涉。
2.设计基准时要同时考虑有无加工校表的直边,若没有需要设计直边,目的是保证加工时可以把零件放正。
3.基准孔在三维图上的颜色标示为绿色,基准孔旁边刻字母“D”,由NC把“D”加工出来,与飞模定位销孔“H”区别开。
4.基准孔与飞模定位销孔不要太近,即与其它的型孔不要太近,防止基准孔开始加工不圆,后面要扩孔与其它型孔干涉。