原材料_进厂检验流程图(1)
冲压厂的QC 流程图
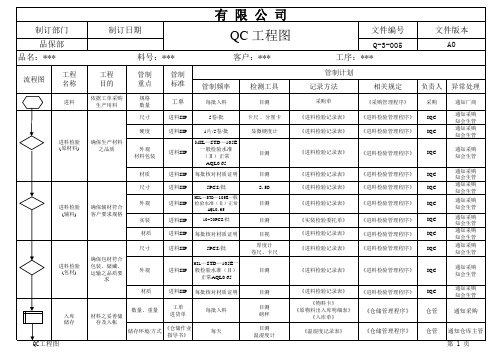
批号
规格 数量
设备、模具、产 品结构、模高、
转速、5S
模高、料厚 料宽、硬度 材料批号、尺寸
物料标签 工单
SOP
SOP/制程 SIP
料厚、硬度 、尺寸、外观
制程SIP
字模 冲孔 整形
字模 切边 压毛边
设备、模具、产 品结构、模高、
转速、5S
模高
SOP SOP
尺寸、外观 制程SIP
设备、模具、产 品结构、模高、
《冲压作业点检表》
《首件点检记录表》
《首件点检记录表》
《冲压作业点检表》
《首件点检记录表》 《首件点检记录表》 《制程检验记录表》 《丝攻更换记录表》 《冲压作业点检表》 《首件点检记录表》 《首件点检记录表》 《冲压自主检查表》 《冲压自主检查表》
《制程管理程序》
主机手
《制程检验管理程序》 IPQC
目视 厚度计 卷尺、卡尺
目测
进料SIP 每批核对材质证明
目测
材料之妥善储 存及入帐
数量、重量
工单 进货单
储存入料 每天
目测 磅秤
目测 温湿度计
管制计划 记录方法
相关规定
负责人 异常处理
采购单 《进料检验记录表》 《进料检验记录表》
《采购管理程序》
采购
《进料检验管理程序》 IQC 《进料检验管理程序》 IQC
每批核对材质证明
显微硬度计 目测 目测
进料SIP 进料SIP 进料SIP
5PCS/批
MIL—STD—105E一般 检验水准(Ⅱ)正常
AQL0.65
10~20PCS/批
2.5D 目测 目测
进料SIP 每批核对材质证明
进料SIP
原材料质量检验流程图

传递验收单
总库、供应科
材料工艺员
原材料质 量情况汇 总
原材料质 量检验汇 总表
材料工艺员
下发
总库、供应科
注 1 :斜体加方框字—在流程中指责任部门或人员。 注 2 :虚线方框字—在流程中指接口的载体。 注 3 :方框字—在流程中指过程活动。
图一:原材料质量检验流程
总库
通知检验
检验委托单
材料工艺员
外观检查
口头通知 检查结果
总库、供应科
取样、送检
理化检验员
理化检验
材料分析 报告单
材料工艺员
结果判断
质量验收单
部门负责人
审批
质量验收单
材料分析 报告单 传递材料 分析报告 原材料使 用选择
生产车间
材料工艺员
总库
质量
进料检验流程图及表格

1、进料检验流程图
1.1进料检验通知单(送检单)
被通知部门:________________ 通知单编号:______________
仓储部主管:______________ 收料仓管专员:______________ 1.2进料检验记录表
1.3进料检验报告表
编号:日期:
限,则判定物料验收结果为“合格”;若检验物料的不合格数量达到或超过企业规定的数量,则判定物料验收结果为“不合格”
进厂零件质量检验表
零件编号:零件名称:号码:
检验主管:检验员:检验日期:年月日进厂零件检验报告表
编号:填写日期:年月日
进厂材料试用检验表
编号:填写日期:
进料检验质量异常处理报告
编号:____________ 填表日期:______________
进料检验日统计表
原材料供应商质量检测表
供应商名称:编号:
外协厂商质量检查表
填写日期:年月日
检验主管:检验人员:
十二、供应商不合格品记录表
年度:月份:编号:
十三、供应商物料拒收月统计表
月份:日期:
主管:制表:
十四、供应商质量评价体系表
十五、供应商综合评价表
编号:填写日期:
岗位职责
1、进料检验主管
2、进料检验专员。
原材料验收标准程序
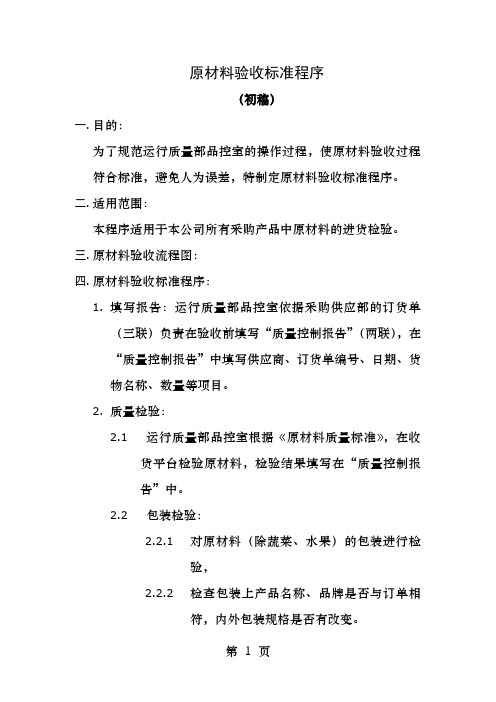
原材料验收标准程序(初稿)一.目的:为了规范运行质量部品控室的操作过程,使原材料验收过程符合标准,避免人为误差,特制定原材料验收标准程序。
二.适用范围:本程序适用于本公司所有采购产品中原材料的进货检验。
三.原材料验收流程图:四.原材料验收标准程序:1.填写报告:运行质量部品控室依据采购供应部的订货单(三联)负责在验收前填写“质量控制报告”(两联),在“质量控制报告”中填写供应商、订货单编号、日期、货物名称、数量等项目。
2.质量检验:2.1运行质量部品控室根据《原材料质量标准》,在收货平台检验原材料,检验结果填写在“质量控制报告”中。
2.2包装检验:2.2.1对原材料(除蔬菜、水果)的包装进行检验,2.2.2检查包装上产品名称、品牌是否与订单相符,内外包装规格是否有改变。
2.2.3检查外包装箱是否破损,是否有污垢,是否灰尘过多。
2.2.4检查内包装是否破损,是否有原材料外溢,是否被污染。
2.2.5检查罐头是否磕碰变形,若有凹陷、小孔、膨胀等缺陷应不予接收。
2.3标识检验:2.3.1对原材料(除蔬菜、水果)的标识进行检验。
2.3.2检查原材料的产品标识是否完整,是否正确标示产品名称、配料、净重、厂家名称、厂址、储存/运输条件等产品信息。
2.3.3对进口产品检查是否有中文标识以及国内经销商名称。
2.3.4检查原材料的生产日期与保质期,以及检查内外日期标识是否一致。
检查结果记录在“质量控制报告”中。
2.3.5确定原材料是否临近或已经超过保质期。
一般原材料不得超过其保质期的2/3,对于保质期超过2年的原材料,生产日期与接收日期之间的差别应该小于18个月。
2.3.6对于需要进行QS认证的产品,检查是否有QS认证标识。
2.4温度检验:2.4.1对所有冷藏、冷冻品使用温度枪进行表面温度检测。
2.4.2所有冷藏原材料在到达收货平台时的表面温度不得高于8℃。
2.4.3所有冷冻原材料在到达收货平台时的表面温度不得高于-5℃。
完整版)生产机加工件工艺流程图

完整版)生产机加工件工艺流程图制造工艺流程图如下:1.原材料入库:将原材料送入仓库。
2.原材料检查:检查原材料是否符合要求。
3.原材料储存:将原材料分别放置在不同的仓库中。
4.原材料分类:根据加工工艺将原材料进行分类。
5.原材料粗加工:将原材料进行初步加工。
C加工:使用CNC机床进行加工。
7.精加工:对产品进行精密加工。
8.线切割加工:使用线切割机进行加工。
9.零部件尺寸检验:对零部件的尺寸进行检验。
10.氧化、着色、抛光:进行表面处理。
11.零件组装:将零部件组装成产品。
12.产品装配:将产品进行组装。
13.激光打标:使用激光进行打标。
14.成品检验:对成品进行检验。
制造工艺流程表如下:NO 工程名称作业内容管理项目记录操作人员1 原材料入库将原材料送入仓库先入先出原材料出库表仓库检验2 原材料检查检查原材料是否符合要求 N/A 外部采购合同书,输入检验报告保管员3 原材料储存将原材料分别放置在不同的仓库中分规格保管作业日志精工车间4 原材料分类根据加工工艺将原材料进行分类按加工工艺分原材料出库表技术人员5 原材料粗加工将原材料进行初步加工按顺序进行作业日志精工车间6 CNC加工使用CNC机床进行加工尺寸生产作业指导书技术人员7 精加工对产品进行精密加工尺寸生产作业指导书技术人员8 线切割加工使用线切割机进行加工尺寸生产作业指导书技术人员9 零部件尺寸检验对零部件的尺寸进行检验尺寸检验报告技术人员10 氧化、着色、抛光进行表面处理表面管理作业日志精工车间11 零件组装将零部件组装成产品产品的结合性生产作业指导书技术人员12 产品装配将产品进行组装产品的结合性生产作业指导书技术人员13 激光打标使用激光进行打标作业日志技术人员14 成品检验对成品进行检验产品检验达标检验报告技术人员以上是机加工制造工艺流程图和制造工艺流程表。
我们将原材料进行分类、加工、精加工、线切割加工、零部件尺寸检验、氧化、着色、抛光、零件组装、产品装配、激光打标和成品检验。
锚固剂原材料进厂、工序、出厂检验
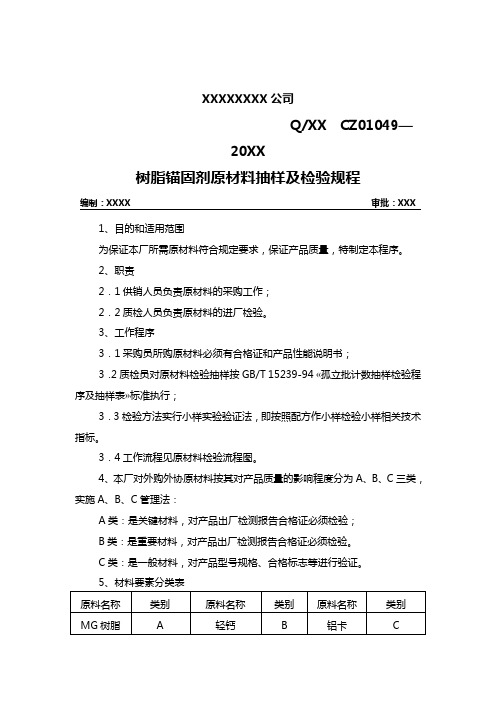
XXXXXXXX公司Q/XX CZ01049—20XX 树脂锚固剂原材料抽样及检验规程编制:XXXX 审批:XXX1、目的和适用范围为保证本厂所需原材料符合规定要求,保证产品质量,特制定本程序。
2、职责2.1供销人员负责原材料的采购工作;2.2质检人员负责原材料的进厂检验。
3、工作程序3.1采购员所购原材料必须有合格证和产品性能说明书;3.2质检员对原材料检验抽样按GB/T 15239-94 «孤立批计数抽样检验程序及抽样表»标准执行;3.3检验方法实行小样实验验证法,即按照配方作小样检验小样相关技术指标。
3.4工作流程见原材料检验流程图。
4、本厂对外购外协原材料按其对产品质量的影响程度分为A、B、C三类,实施A、B、C管理法:A类:是关键材料,对产品出厂检测报告合格证必须检验;B类:是重要材料,对产品出厂检测报告合格证必须检验。
C类:是一般材料,对产品型号规格、合格标志等进行验证。
5、材料要素分类表6、技术要求:所有采购原材料均满足采购控制清单的要求,小样试验检验结果均满足以下要求:1)稠度:在环境温度为(22±1)℃时,不小于16mm。
2)凝胶时间:项目CKa CK K Z M 备注8~25 8~40 41~90 91~180 >180 环境温度(22±1)℃凝胶时间(S)3)抗压强度:环境温度(22±1)℃、龄期24h条件下,用于端锚的锚固剂,其抗压强度应不小于60 MPa,用于全锚的锚固剂其抗压强度应不小于40 MPa。
4)有效期: 80℃热稳定性试验16h,室内(22±1)℃存放4个小时后;稠度保留率不小于原测平均值的40%。
5)树脂酸值: 24 +4粘度: 400+30%固化含量:65+36) BPO 含量>70% 7) DC含量>70%7. 判定原则:一个项目一次抽检结果有0个不合格,判定该项目合格。
一个项目一次抽检结果有两个以上(含两个)不合格,判定该项目不合格。
产品质量检验规程
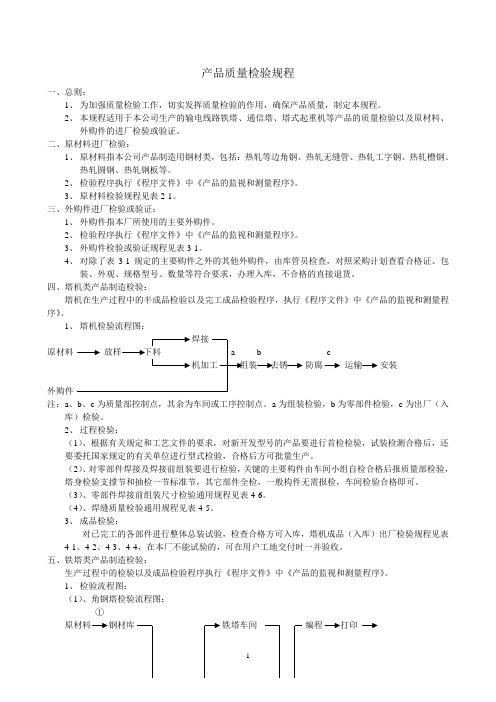
产品质量检验规程一、总则:1、为加强质量检验工作,切实发挥质量检验的作用,确保产品质量,制定本规程。
2、本规程适用于本公司生产的输电线路铁塔、通信塔、塔式起重机等产品的质量检验以及原材料、外购件的进厂检验或验证。
二、原材料进厂检验:1、原材料指本公司产品制造用钢材类,包括:热轧等边角钢、热轧无缝管、热轧工字钢、热轧槽钢、热轧圆钢、热轧钢板等。
2、检验程序执行《程序文件》中《产品的监视和测量程序》。
3、原材料检验规程见表2-1。
三、外购件进厂检验或验证:1、外购件指本厂所使用的主要外购件。
2、检验程序执行《程序文件》中《产品的监视和测量程序》。
3、外购件检验或验证规程见表3-1。
4、对除了表3-1规定的主要购件之外的其他外购件,由库管员检查,对照采购计划查看合格证、包装、外观、规格型号、数量等符合要求,办理入库,不合格的直接退货。
四、塔机类产品制造检验:塔机在生产过程中的半成品检验以及完工成品检验程序,执行《程序文件》中《产品的监视和测量程序》。
1、塔机检验流程图:原材料 b c组装去锈防腐运输安装外购件注:a、b、c为质量部控制点,其余为车间或工序控制点。
a为组装检验,b为零部件检验,c为出厂(入库)检验。
2、过程检验:(1)、根据有关规定和工艺文件的要求,对新开发型号的产品要进行首检检验,试装检测合格后,还要委托国家规定的有关单位进行型式检验,合格后方可批量生产。
(2)、对零部件焊接及焊接前组装要进行检验,关键的主要构件由车间小组自检合格后报质量部检验,塔身检验支撑节和抽检一节标准节,其它部件全检,一般构件无需报检,车间检验合格即可。
(3)、零部件焊接前组装尺寸检验通用规程见表4-6。
(4)、焊缝质量检验通用规程见表4-5。
3、成品检验:对已完工的各部件进行整体总装试验,检查合格方可入库,塔机成品(入库)出厂检验规程见表4-1、4-2、4-3、4-4,在本厂不能试验的,可在用户工地交付时一并验收。
生产工艺流程图

服装生产工艺流程图验布│→│裁剪│→│印绣花│→│缝制│→│整烫│→│检验│→│包装│ (一)面辅料进厂检验面料进厂后要进行数量清点以及外观和内在质量的检验,符合生产要求的才能投产使用。
在批量生产前首先要进行技术准备,包括工艺单、样板的制定和样衣制作,样衣经客户确认后方能进入下一道生产流程。
面料经过裁剪、缝制制成半成品,有些梭织物制成半成品后,根据特殊工艺要求,须进行后整理加工,例如成衣水洗、成衣砂洗、扭皱效果加工等等,最后通过锁眼钉扣辅助工序以及整烫工序,再经检验合格后包装入库。
(二)面料检验的目的和要求把好面料质量关是控制成品质量重要的一环。
通过对进厂面料的检验和测定可有效地提高服装的正品率。
面料检验包括外观质量和内在质量两大方面。
外观上主要检验面料是否存在破损、污迹、织造疵点、色差等等问题。
经砂洗的面料还应注意是否存在砂道、死褶印、披裂等砂洗疵点。
影响外观的疵点在检验中均需用标记注出,在剪裁时避开使用。
面料的内在质量主要包括缩水率、色牢度和克重(姆米、盎司)三项内容。
在进行检验取样时,应剪取不同生产厂家生产的、不同品种、不同颜色具有代表性的样品进行测试,以确保数据的准确度。
同时对进厂的辅料也要进行检验,例如松紧带缩水率,粘合衬粘合牢度,拉链顺滑程度等等,对不能符合要求的辅料不予投产使用。
(三)技术准备的主要内容在批量生产前,首先要由技术人员做好大生产前的技术准备工作。
技术准备包括工艺单、样板的制定和样衣的制作三个内容。
技术准备是确保批量生产顺利进行以及最终成品符合客户要求的重要手段。
工艺单是服装加工中的指导性文件,它对服装的规格、缝制、整烫、包装等都提出了详细的要求,对服装辅料搭配、缝迹密度等细节问题也加以明确。
服装加工中的各道工序都应严格参照工艺单的要求进行。
样板制作要求尺寸准确,规格齐全。
相关部位轮廓线准确吻合。
样板上应标明服装款号、部位、规格、丝绺方向及质量要求,并在有关拼接处加盖样板复合章。
产品质量控制流程图 (全图)
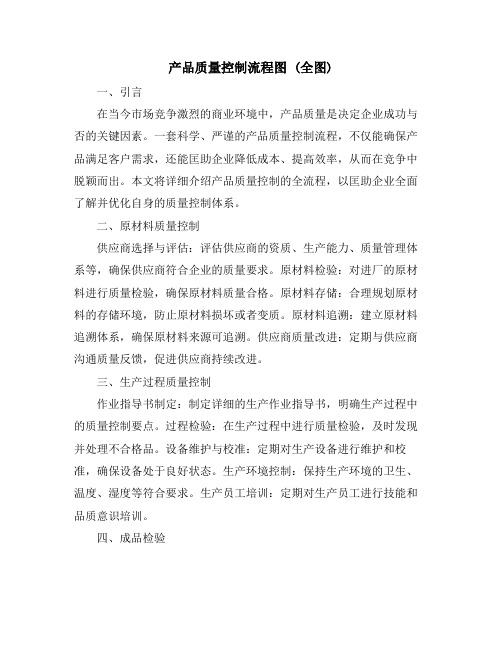
产品质量控制流程图 (全图)一、引言在当今市场竞争激烈的商业环境中,产品质量是决定企业成功与否的关键因素。
一套科学、严谨的产品质量控制流程,不仅能确保产品满足客户需求,还能匡助企业降低成本、提高效率,从而在竞争中脱颖而出。
本文将详细介绍产品质量控制的全流程,以匡助企业全面了解并优化自身的质量控制体系。
二、原材料质量控制供应商选择与评估:评估供应商的资质、生产能力、质量管理体系等,确保供应商符合企业的质量要求。
原材料检验:对进厂的原材料进行质量检验,确保原材料质量合格。
原材料存储:合理规划原材料的存储环境,防止原材料损坏或者变质。
原材料追溯:建立原材料追溯体系,确保原材料来源可追溯。
供应商质量改进:定期与供应商沟通质量反馈,促进供应商持续改进。
三、生产过程质量控制作业指导书制定:制定详细的生产作业指导书,明确生产过程中的质量控制要点。
过程检验:在生产过程中进行质量检验,及时发现并处理不合格品。
设备维护与校准:定期对生产设备进行维护和校准,确保设备处于良好状态。
生产环境控制:保持生产环境的卫生、温度、湿度等符合要求。
生产员工培训:定期对生产员工进行技能和品质意识培训。
四、成品检验抽样检验:按照规定的抽样方案对成品进行抽样检验。
性能测试:对成品进行各项性能测试,确保产品性能符合要求。
外观检查:检查成品外观是否符合要求,无明显缺陷。
不合格品处理:对不合格成品进行标识、隔离和处置。
成品合格判定:根据检验结果判定成品是否合格,出具检验报告。
五、包装运输质量控制包装材料选择:选择合适的包装材料,确保产品在运输过程中不受损伤。
包装设计:设计合理的包装结构,提高产品的抗震、抗压性能。
材料送检流程图

36
预应力锚具锚固性试
以同一材料和同一生产工艺、不超过200套为一批。
1、从同一批中抽取6套锚具,将锚具装在预应力筋的两端,组成3个预应力筋锚具组装体
2、如有一套不合格,则取双倍数量的锚具重新检验
37
2、高强度大六角头螺栓连接副出厂时应随箱带有扭矩系数的检验报告。
27
漏电开关、空气断路器
1、产品合格证
2、出厂抽检报告
1、楼层(或梯间)配电系统、户照明配电系统及公共照明配电系统末端100A以下的漏电开关和断路器,其余部分由建设、监理、施工单位和监督机构根据实际情况决定是否取样或取样的批量
2、漏电开关取样批量按照进场的同一生产厂家、同一规格型号的材料总数量为基数取样,材料总数量(个数)在100个及以下取样一组,100个以上按照每100个取样一组,不少于两组;
3、检建筑材料环境污染检验报告
1、墙乳胶漆:同一批号抽2桶。
2、外墙乳胶漆、溶剂型外墙涂料及外墙无机建筑涂料等:同一批号抽一升*2桶,无机外墙涂料抽2*2桶
9
瓷墙(地)砖
1、产品合格证
2、出厂抽检报告
3、建筑材料放射性指标检验报告
10
石、天然花岗岩
1、产品合格证
2、出厂抽检报告
3、建筑材料放射性指标检验报告
(b)冷轧带肋钢筋:≤50t/批。
(c)钢筋焊接网应成批验收,每批应由同一厂家生产的、受力主筋为同一直径的焊接网组成,重量不应大于20t/批
做到先检验后使用,严禁先施工后检验
拉伸L=200mm+10d(2支/组)
弯曲L=140mm+6.2d(2支/组)
进料检验规范(含表格)
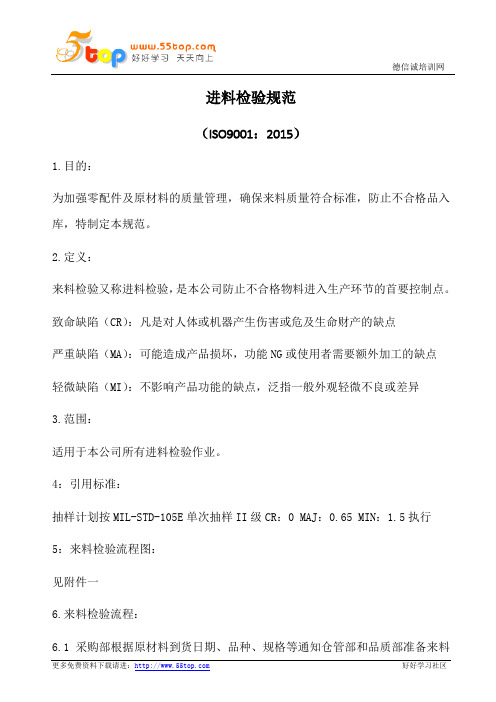
进料检验规范(ISO9001:2015)1.目的:为加强零配件及原材料的质量管理,确保来料质量符合标准,防止不合格品入库,特制定本规范。
2.定义:来料检验又称进料检验,是本公司防止不合格物料进入生产环节的首要控制点。
致命缺陷(CR):凡是对人体或机器产生伤害或危及生命财产的缺点严重缺陷(MA):可能造成产品损坏,功能NG或使用者需要额外加工的缺点轻微缺陷(MI):不影响产品功能的缺点,泛指一般外观轻微不良或差异3.范围:适用于本公司所有进料检验作业。
4:引用标准:抽样计划按MIL-STD-105E单次抽样II级CR:0 MAJ:0.65 MIN:1.5执行5:来料检验流程图:见附件一6.来料检验流程:6.1采购部根据原材料到货日期、品种、规格等通知仓管部和品质部准备来料验收及检验工作。
6.2原材料到厂时,由仓管员,根据采购单,对产品规格、品种、数量、包装方式进行确认,并把来料放置待检区,并通知检验人员对该批物料进行检验,6.3IQC检验PASS合格后,则仓库执行入库处理。
6.4对检测不合格的物料根据《不合格品控制程序》的规定处置,不合格的物料禁止入库,应将其做好相应标识移入不合格品区放置。
6.4.1不合格物料评审,对不合格物料IQC填写IQC检验报告,并附不良样板经品质主管确认后,由公司MRB委员会进行物料评审,最终决定不合格物料的处理方式。
6.4.2评审结果为退货,由IQC在物料上贴不良标签,并注明不良原因和附不良样板,通知采购,由采购开具退货单,由仓库作退货处理。
6.4.3评审为特采之物料,由IQC在物料外箱贴上特采标签,并通知仓库按合格物料正常入库。
6.4.5评审结果为返工返修之物料,经供应商或本司返工后,IQC再次按正常检查进行复检,直到返工返修OK为止,挑选出的不良品通知采购,由采购开退货单,再由仓库退回供应商。
6.5.IQC检验人员将检验结果填写《进料检验报告单》,原材料的检验和记录由检验人员按规定期限限及方法保发生不合格之物料时,有必要时需发品质异常单给供货商,对其进行纠正和预防6.6.1每批ROSH环保物料,IQC要核对供应商SGS报告及材质证明报告,及环保物料是否贴环保标示。
来料检验作业流程

来料检验作业流程1 目的为对来料进行质量控制,确保符合公司要求,防止不良物料流入或投入使用,特制订本流程。
2 适用范围本流程适用于原材料(原料、包材)和重要生产辅料。
3 职责3.1品质部负责来料的质量标准制定,检测、质量判定,并控制不良物料和紧急放行来料的使用。
3.2采购部负责来料不合格品的处理。
3.3仓储部负责来料品名、规格、数量、供应商的核对及送检。
3.4市场部/生产部负责不良物料的评审。
3.5 PMC负责来料是否需要紧急处理的通知。
4 术语和定义无5 流程图无6 程序6.1来料点收、送检6.1.1供应商交货后,仓管员参照《送货单》,核对来料品名、规格、数量、标识、生产商等。
6.1.2仓管员确认无误后,开具《物料送检单》,同时标注是否急料,通知品质部来料检验员。
6.2急料处理6.2.1由于生产及出货等原因,有些物料需要尽快检验时,PMC部应书面通知仓储部,仓管在送检单上标注。
6.2.2厂长确定该物料可否先用后检,可以的仓管员在物料上贴上“紧急放行”标签并做好记录,同时按正常标准进行抽样检测。
6.2.3不可以先用后检的物料,品质部安排第一时间检测,并及时将检测结果通知PMC部。
6.3取样6.3.1包材取样包材检验人员根据《送检单》中的送检数量,按照“包材检验标准”中的抽样标准进行抽样。
在抽样过程中不得使包材受污染、受损,抽样完毕后,将包装箱原样封好。
6.3.2原料取样6.3.2.1取样时应先将抽取的原料外包装表面用纱布擦试干净,用专用工具打开包装,分别从样本中平均抽取所需试样。
6.3.2.2取液体样应搅拌后抽取,同时检查试样中是否有杂质,并将从多个样本中所抽取的样品混合在一烧杯内。
固体样品应用特定取样器具从样本中部取样。
6.3.2.3有菌检指标的原料,在来料时每批号只抽检1个包装单位,取样后应特别标注,加强密封。
6.3.3 机加工产品取样6.3.3.1 取样时应采取均匀取件法进行抽样,以减少检测误差。
生产工艺流程及说明
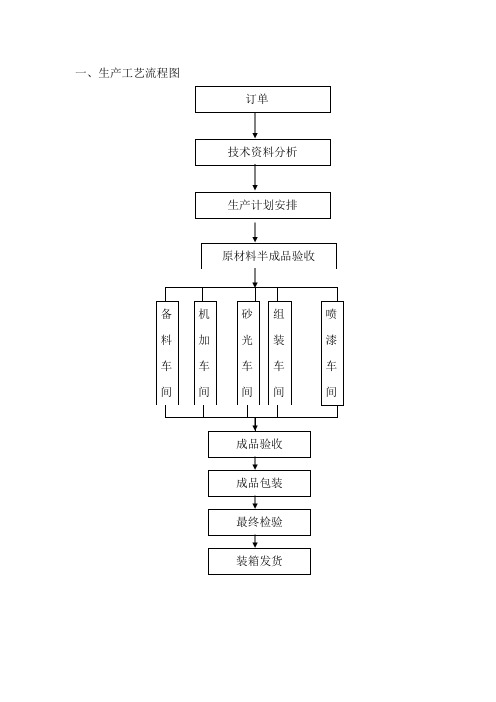
(一)备料车间:根据图纸要求到仓库领取水份在8-12%以下、验收合格的木料,按照质量要求,加工木料。
(二)机加工车间:1、查证进入数量。
半成品进入机加工车间后,由专人查点进入的确切数量,在查验无误后,由机加工人员签字领料。
2、严格检查。
在加工前,由当值班组长对产品的加工尺寸、用料标准精度等各项指标进行详细检查,确保无误后正式进入下一步加工工艺。
(三)砂光车间:对机加工车间转入的合格产品部件进行砂光,砂光完成后由班组长根据不同订单要求等标准进行检查验收,合格后转入组装车间。
(四)组装车间:按照图纸要求,经上道工序质检员检验合格进行组装。
组装完毕后,由经过专门培训的质检员严格按照我厂制定的企业标准进行验收。
验收合格后进入下一个流程——打磨。
(五)喷漆车间:打磨符合要求后,即进入喷漆车间,进行喷底漆,要求喷漆要均匀。
无划痕,无碰伤。
底漆喷得是否均匀,直接关系到下一道工序—面漆质量的高低。
因此,我们规定底漆喷完后,对底漆进行打磨,并由经过严格培训的专门验收人员进行严格检查、验收,杜绝不合格产品进入下道工序。
面漆工序是影响产品外观质量的工序之一,因此,我们制定了非常严格的工序标准和操作规程,面漆喷完后,即进行干燥,然后转入产品周转库。
(六)包装:产品干燥出库后,由专业验收人员严格按照企业内部的质量标准和客户要求进行全方位检查验收,在确定产品质量完全符合质量标准后,由验收员签字填写物流卡,将产品进到包装车间。
在包装车间,按照客户要求的包装外观质量进行包装。
检查客户所需要印刷的唛头是否正确,包装材料是否清洁,包装人员在包装时要对包装的产品再一次进行挑选,将开裂、霉变、颜色不均,松动的产品挑出。
(七)产品入库:产品包装完毕经检验合格后,由包装车间人员品存入指定的产品存放区,做好记录,并标明产品批次,发地区,等待发货。
**木业科技有限公司生产工艺流程说明。
检验和试验控制程序(含流程图)
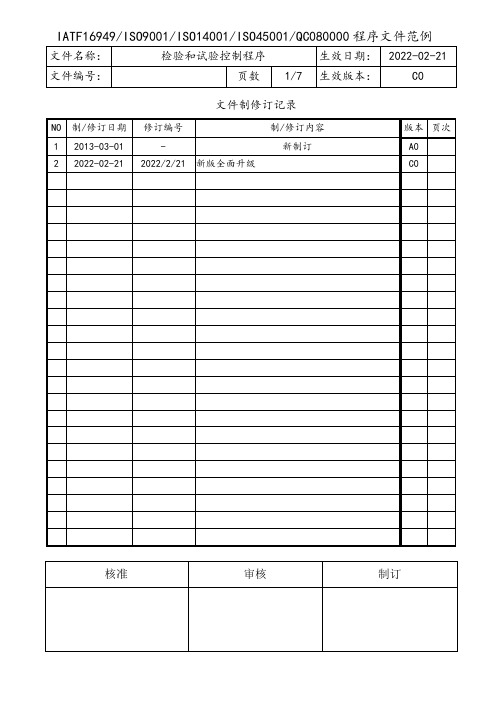
文件制修订记录1.0目的建立一个适合于对公司生产的所有产品(包括半成品与成品)及用于公司生产的所有原物料、辅料、零配件的检验与试验程序,规范公司的检验与试验作业,确保公司生产的产品质量/HSF达到客户所需的要求。
2.0范围:2.1适用于公司产品实现过程中所有物料包括原材料、半成品、成品的检验与试验。
2.2适用于公司制程管理值的验证作业。
3.0定义:3.1 IQC:Incoming Quality Control 指进料质量控制,即进料检验。
3.2 IPQC:In-process Quality Control 指生产过程中的质量控制,即制程检验,包含对产品以及生产过程中质量控制状态的检查与监视。
3.3 FQC:Final Quality Control制造过程最终检查验证,本公司指入库前的检验过程。
3.4 OQC:Outgoing Quality Control 指产品出货前由品质检验员对其进行的检验。
3.5 SQE:Supplier Quality Engineer 供应商质量工程师。
3.6 QE: Quality Engineer 质量工程师。
3.7自主检验:由操作员对本岗位材料、半成品、成品的检查,发现问题自己及时向直接上司汇报并作相应处理;同时也必须对过程质量(包括参数设定及是否按作业指导书要求作业等)的监控。
3.8首件检查:指生产者和技术员对生产调试阶段生产出来的产品(成品或半成品)进行确认并由品质检验员对其进行检验。
3.9巡检:指由品质检验员即IPQC人员对生产过程中的产品随机抽样检验或对制程过程状态(包括参数设置及是否按作业指导书要求作业等)的检查。
3.10抽检:指品质人员定期或定量对过程或项目进行抽样检查。
3.11半成品:指本公司还需要经下工序加工或装配后才能出货给客户的零组件。
3.12成品:指本公司可直接出货给客户的产品,对客户而言可能是半成品。
3.13原材料:指用于生产/加工成品的原料如塑胶粒、钢材等和组装产品用的零配件如螺丝、螺母、贴纸、辅料等,也包括包装产品用的包装材料如气泡袋、珍珠棉、PE袋、纸箱等。
来料检验规范

5.1来料检验流程图(如附件1)。
5.2点收:依《仓库管制程序》办理。
5.3来料检验
5.3.1.货仓依据送货单核对数量、料号、物料标示正确后签收,并填写〈品质检查报告〉送检,将ROHS物料放在RoHS物料待验区:非ROHS物料放在非ROHS物料待验区,或以“待验”标示管制。其中代工业务客供物料货仓按“套单”开《品质检查报告〉,IQC依BOM单核对料件规格、型号。
5.3.9.检查作出检验结论后,IQC将《品质检查报告》第二联(红联)发到采购,由采购知会供应商、货仓、PMC,生产部,由仓库办理入库或退货手。采购并将不合格《品质检查报告》传真给客户或供应商。第一联(白联)品质部保存,并由品质文员或班组长进行统计汇总。制程来料不良IQC出《纠正预防通知书》反馈给供应商要求改善并回复对策,品质部将《品质检查报告》《纠正预防通知书》表单存档便于追溯。
5.3.10.对于生产急需物料,IQC应进行优先检验或由采购部提出《特采申请单》品质部、工程部确认批准后方可采取特殊放行,并在《品质检查报告》上注明特采放行,对于特采放行的物料IQC应保留适当样品进行检验或对下线之物料进行跟踪,如发现不合格则立即上报部门主管或经理。
5.4.11.免检物料,必须由物料申请部门或PMC开《来料免检申请单》注明免检原因,并由品质、货仓、生产、PUC、工程签名确认,方可免检上线。
程序文件
编写部门
文件编号
制定日期
版本
名称:来料检验规范
修订日期
页数
修改状态
5.3.5.除非客户规定一般使用M11-STD-105E,一般抽样水准II级单次正常检验抽样,特殊抽样S-2,AQ1:电子类(MA0.4/MT0.65);塑胶类、包材类(MAO.4/MI1.0)ROUS:AC:0REJ:1
- 1、下载文档前请自行甄别文档内容的完整性,平台不提供额外的编辑、内容补充、找答案等附加服务。
- 2、"仅部分预览"的文档,不可在线预览部分如存在完整性等问题,可反馈申请退款(可完整预览的文档不适用该条件!)。
- 3、如文档侵犯您的权益,请联系客服反馈,我们会尽快为您处理(人工客服工作时间:9:00-18:30)。
退货不符合符合
通知质检部
检验NG
OK
使用
成品进仓检验流程
成品
待检区
检验不合格不合格品区
隔离存放
合格
外包装箱右上角贴合格证填不合格反馈处理表
做好检验记录做好检验记录
通知生产部
入库/贮存组织评审处理
返工
让步放行返修
外包材料控制流程图
外包材料进厂
待检区
仓库填写物资标签
通知质检部
原材料进厂检验流程图
原材料进厂
待需不合格物资标签上盖不合格章
检验填不合格反馈处理表
材料不合格反馈处理表
采购申请部门意见总经理审批
合格通知采购/仓库
紧急放行标签上盖合格章
不合格品区
隔离存放
生产合格品区组织评审处理
通知供方供方挑选
入库/贮存/发放
退货让步接收选用
通知生产部
检验不合格物资标签上盖不合格章
填不合格反馈处理表/材料不合格反馈处理表
合格通知采购/仓库
物资标签上盖合格章不合格品区
做好检验记录隔离存放
通知仓库
组织评审处理
合格品区
通知供方
技术文件
送外协二次加工退货/选用/让步接收
(外包)
质量保证协议书
首次检验确认不合格
合格
质检部监控继续加工
不合格
进厂检验
合格
接收