PVD涂层技术在齿轮滚刀上的应用
PVD涂层在刀具和模具的应用

PVD涂层在刀具和模具的应用摘要:近十几年,在模具表面上,由气相沉积技术制备硬质化合物涂层的方法,由于技术上的优越性及涂层的良好特性,正引起人们的高度重视。
其是今后各种模具、切削工具和精密机械零件等进行表面强化的主要技术,有着广泛的应用前景。
关键词:PVD涂层;刀具模具;应用一、PVD(物理气相沉积)法及其特点PVD法(离子镀膜)技术是在真空条件下,采用低电压、大电流的电弧放电技术,利用气体放电使靶材蒸发,蒸发物质与气体都被电离,利用电场的加速作用,使蒸发物质及其反应产物沉积在工件上,形成一层所需要的固态薄膜或涂层的技术。
涂层处理可增加工件硬度、抗磨力和降低摩擦系数,延长工件寿命(一般可延长3~5倍)。
目前主要的涂层包括:TiN、TiCN、TiAlN、CrN、AlTiN及DLC等,每种涂层各有其不同特性和用途。
PVD法的特点之一是沉积温度低于600℃,其可在工具钢和模具钢的高温回火温度以下进行表面处理,故变形小,最适合尺寸形状精密的机械零件;可不改变传统的制造工艺,仅仅在最终加工后进行一次处理。
二、PVD涂层的加工流程(1)收到模具后,检测运输途中工件是否有碰损及抛光效果是否达到要求,之前是否有做过类似的涂层处理;(2)对模具进行清洗,去磁,去除工件所有油污、油漆及杂质,螺钉孔内的异物也要清洗干净;(3)如果工件前有做过类似的涂层,要做脱涂处理;(4)将工件装夹、定位好后放进炉中加工;(5)设置好加工参数,选择涂层的类型、厚度后,机器根据设定的程序自行进行加工;(通过炉内抽真空,加温及等离子电弧技术,同时被加工的工件在炉中匀速旋转,将靶材在离子状态下均匀地沉积在工件的表面.)(6)约8-10个小时左右出炉,卸下,自然冷却,并进行检测(检测涂层的厚度及附着力);(7)经检测合格后,将工件包装好,安排发货给客户。
三、模具发来做PVD涂层前应注意的事项(1)工件在涂层之前必须需要清洗干净(用清洗液及表面喷沙)及去掉锈迹,不能有油污。
PVD法的应用

切削刀具随着制造技术的进步,机械加工不断向高精化、高速化方向发展,因此对切削刀具在强度、耐高温、耐磨损和使用寿命等方面的性能要求也不断提高。
对刀具进行涂层处理是提高刀具性能的重要手段之一。
由于涂层处理可以提高加工效率和精度、延长刀具使用寿命、降低加工成本,因此,涂层刀具在金属切削加工中的应用越来越广泛常用的涂层材料有碳化物、氮化物、氧化物、硼化物和硫化物等,近年来还发展了聚晶金刚石、立方氮化硼等Ti-Al-N 涂层由于高的硬度(~33GPa)和良好的高温抗氧化能力(~850 ℃)而被作为硬质耐磨涂层广泛应用于切削刀具领域.当涂层中的Al 含量增加到一定程度超过TiN 中Al 的固溶度(原子分数约64%)时,涂层的结构会从面心立方c-TiN 结构向密排六方h-AlN 结构转化涂层的力学性能及抗氧化能力急剧下降.因此,在保持立方结构的前提下提高涂层中Al 含量可有效地改善涂层的性能CrN 涂层为目前过渡金属氮化物涂层中含Al 固溶度最高的氮化物。
以TiN 为代表的工具涂层显著提高了机械加工刀具的切削效率与使用寿命, 有力地支持了加工中心机床的应用和制造业规模化生产的技术进步。
涂层技术已和刀具材料与刀具设计与制造一起成为切削刀具的三大关键技术。
继TiN 后又开发了TiC、CrN和ZrN等二元化合物涂层, 以及TiCN、TiAlN,CrAlN等多种三元化合物工具涂ZrN 涂层除具有优良的耐腐蚀、耐高温、耐磨损性能,还有良好的力学性能和导电性能,美观的金黄色外表等优点,已广泛应用于电子电路中的电接触层、珠宝业中的装饰层和机械摩擦中的减摩层等生物医用材料血管内支架和人工瓣膜是治疗心血管疾病的重要方法,应该具有良好的力学特性和血液相容性, 并且必须无毒、无炎症反应、无致癌性主要材料包括不锈钢、钽、钛合金以及热解碳微波电阻器随着电子技术迅速发展,通讯、卫星、遥感、雷达、WLAN 和GPS 等领域使用频率进入微波的中高端频段,必须研发新型元器件的材料和结构,使其性能满足微波电路的要求。
新型PVD刀具涂层--AlCrN

新型PVD刀具涂层—AlCrNTiAlN和AlTiN是将Al元素沉积到TiN中而形成的PVD刀具涂层。
迄今为止,通过增加TiAlN、AlTiN 涂层中的铝含量,从而增强刀具涂层的耐高温性能和硬度,一直是刀具制造商和涂层公司关注的重大技术课题。
自1995年以来,人们一直在持续不断地研究和改进相关的气相沉积工艺。
到2000年,TiAlN和AlTiN 涂层中铝元素与钛元素的成分比例已从原来的1∶2提高到3∶2,即铝含量已从33%增加到60%。
为了进一步提高涂层中的铝含量,总部位于列支敦士登的巴尔查斯(Balzers)涂层公司经过大量研究开发,发明了用铬元素取代钛元素的涂层技术,并于2004年推出了商品名为“Balinit Alcorna”的单层AlCrN涂层。
AlCrN涂层的铝含量比一般的AlTiN涂层更高,适用于包括齿轮滚刀、立铣刀、铣刀片在内的多种高速钢和硬质合金刀具。
此外,它也可以用于车削刀具,但仅限于耐热性和扩散稳定性极好的基体材料,如PCBN 和Si3N4陶瓷。
在EMO Hannover 2005展览会上,巴尔查斯公司又推出了商品名为“Balinit Helica”,专为孔加工刀具设计的多层AlCrN涂层。
这种超光滑涂层可应用于任何硬质合金或高速钢钻头上,从而显著增强了钻头的耐磨性和剪切强度,并有利于提高钻头的排屑性能。
在扫描电子显微镜(SEM)下观察硬质合金基体上Balinit Alcorna涂层的剖面微观结构时,可以清楚地看到厚度为3~4μm,呈连续结构的单层涂层;而在Balinit Helica涂层的SEM图像中,多层涂层结构清晰可辨。
Helica多层涂层的总厚度约为4μm,但对于直径小于1/8″的小钻头,涂层厚度以1~2μm更为适宜。
虽然100%的Al2O3(纯氧化铝)PVD 涂层可为切削刀具提供最佳的热防护作用(在切削加工时,AlTiN和AlCrN涂层中的AlN成分将“转化”为Al2O3),但是这种涂层的应用范围十分有限。
新结构高效双切齿轮滚刀
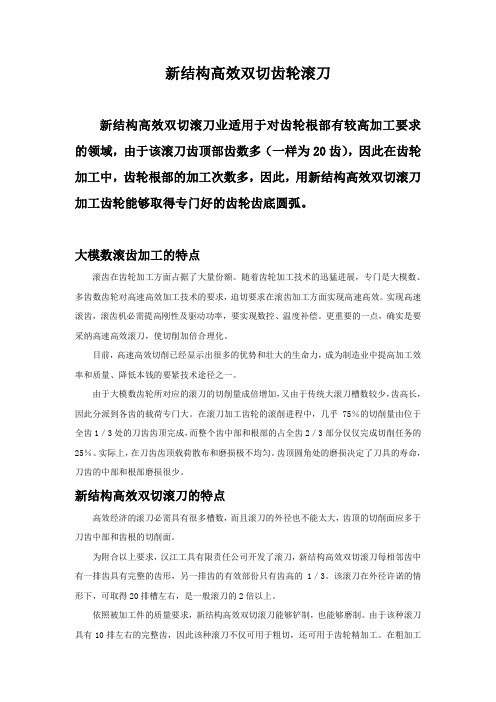
新结构高效双切齿轮滚刀新结构高效双切滚刀业适用于对齿轮根部有较高加工要求的领域,由于该滚刀齿顶部齿数多(一样为20齿),因此在齿轮加工中,齿轮根部的加工次数多,因此,用新结构高效双切滚刀加工齿轮能够取得专门好的齿轮齿底圆弧。
大模数滚齿加工的特点滚齿在齿轮加工方面占据了大量份额。
随着齿轮加工技术的迅猛进展,专门是大模数、多齿数齿轮对高速高效加工技术的要求,迫切要求在滚齿加工方面实现高速高效。
实现高速滚齿,滚齿机必需提高刚性及驱动功率,要实现数控、温度补偿。
更重要的一点,确实是要采纳高速高效滚刀,使切削加倍合理化。
目前,高速高效切削已经显示出很多的优势和壮大的生命力,成为制造业中提高加工效率和质量、降低本钱的要紧技术途径之一。
由于大模数齿轮所对应的滚刀的切削量成倍增加,又由于传统大滚刀槽数较少,齿高长,因此分派到各齿的载荷专门大。
在滚刀加工齿轮的滚削进程中,几乎75%的切削量由位于全齿1/3处的刀齿齿顶完成,而整个齿中部和根部的占全齿2/3部分仅仅完成切削任务的25%。
实际上,在刀齿齿顶载荷散布和磨损极不均匀。
齿顶圆角处的磨损决定了刀具的寿命,刀齿的中部和根部磨损很少。
新结构高效双切滚刀的特点高效经济的滚刀必需具有很多槽数,而且滚刀的外径也不能太大,齿顶的切削面应多于刀齿中部和齿根的切削面。
为附合以上要求,汉江工具有限责任公司开发了滚刀,新结构高效双切滚刀每相邻齿中有一排齿具有完整的齿形,另一排齿的有效部份只有齿高的1/3。
该滚刀在外径许诺的情形下,可取得20排槽左右,是一般滚刀的2倍以上。
依照被加工件的质量要求,新结构高效双切滚刀能够铲制,也能够磨制。
由于该种滚刀具有10排左右的完整齿,因此该种滚刀不仅可用于粗切,还可用于齿轮精加工。
在粗加工的场合,该滚刀也能够带前角,如此,可减少切削力和磨损。
新结构高效双切滚刀可在任一标准的滚刀刃磨床上刃磨。
装卡后即可保证前刃面的精度,所需的只是调整砂轮进入滚刀槽的深度。
刀具涂层技术的应用

刀具涂层技术的应用自20世纪60年代化学气相沉积(CVD)涂层硬质合金刀片问世发来,涂层技术被广泛应用于硬质合金可转位刀具的表面处理。
而20世纪80年代初,TiN物理气相沉积(PVD)涂层高速钢刀具的出现,以使高速钢刀具的性能发生了革命性的变革。
由于涂层技术可有效提高切削刀具的使用寿命,使用刀具获得优良的综合机械性能,大幅度地提高机械加工效率,因此涂层技术已经在切削刀具提高性能的工艺中得到极为广泛的应用于。
刀具涂层技术通常可分为化学气相沉积(CVD)技术和物理气相沉积(PVD)技术两大类,本文拟从这两方面分别介绍国内外刀具涂层技术的应用情况。
1、刀具涂层技术的应用(1)CVD涂层技术的应用CVD是使挥发性化合气体发生分解或化学反应,并在被镀工件上形成沉积成膜的方法。
在CVD工艺中,气相沉积所需金属源的制备相对容易,可实现TiN、TiC、TiCN、TiBN、TiB2、AL2O3等单层及多元多层复合涂层。
CVD涂层镀层密实,涂层与基体结合强度高,附着力强,均匀性好,形状复杂的工件也可得到合金副的镀层,薄膜厚度可达5—12微米,因此CVD涂层具有更好的耐磨性。
但其工艺处理温度高,易造成刀具材料抗弯强度的下降,薄膜内部为拉应力状态,使用中易导致微裂纹的产生,因此只适合于硬质合金车削类刀具的表面涂层,其涂层刀具适合于中型、重型切削的高速加工及半精加工。
自1968年第一批CVD涂层硬质合金刀具问世至今,该涂层技术已发展了近35年。
在这35年间,CVD涂层技术从单一成份发展到多种成份、从单一膜层发展到多元多膜层,经过大量的试验,完成了批量大规模的工业化生产。
如今,CVD涂层硬质合金在涂层硬质合金刀具中占到了80%以上的份额,CVD涂层技术已广泛应用于各类硬质合金刀具。
其涂层工艺的主要发展阶段及应用领域见下表:1968——TiN、TiN——方法CVD——硬质合金刀具、模具涂层1973——TiCN、TiC+AL2O3——CVD ——硬质合金刀具、模具涂层1981——TiC+AL2O3+TiN、AL-O-N——CVD——硬质合金涂层1982——TiCN——MT-CVD——硬质合金刀具涂层1986——Diamond、CBN——CVD、PVD——硬质合金刀具涂层1990——TiN、TiCN、TiC——PCVD——模具、螺纹刀具、铣刀等1993——TiN+TiCN(CVD)+TiN(PVD)——CVD+PVD——硬质合金铣削类刀具涂层1993——厚膜纤维状TiCN——MT-CVD——硬质合金车削类刀具涂层(用于粗、半精加工)从上表可以发现,CVD涂层技术主要用于硬质合金类各种切削刀具。
加厚的PVD涂层提高转位式刀片的使用寿命

8~10μm的涂层已经算是很厚的涂层了。
现在可以采用PVD技术进行涂层,从而达到光滑的表面质量和较低的加工温度。
经过了近十年的时间,现在终于可以第一次尝试进行厚度达8μm的PVD涂层。
此技术在转位式刀片上得到了非常成功的应用,由此PVD技术为自身打开了一个广阔的应用天地。
这种厚的PVD涂层由CemeCon公司研制成功,可用于客户独特的涂层应用场合,如涂层材质为Alox SN2或金Alox SN2的材料可与各类型刀片或客户的要求相匹配。
这种涂层多年来成功地应用于铣削和车削的加工中。
图1 加厚的PVD涂层在转位式刀片上的应用非常成功究竟该怎样定义厚涂层呢?实际上,这种厚涂层也只有千分之几毫米,目前大多数厚度在10~12μm之间的涂层均采用CVD工艺制作,涂层的成分主要有TiN、TiCN和氧化铝的化合物。
但是技术发展和需求的趋势却是要扩大涂层材料的选材品种和范围。
刀具生产厂家愿意对铝、铬或硅进行任意的组合,以改善涂层材料的特性,来满足新的要求。
为了完成这项工作,目前只考虑采用PVD涂层技术。
对此,用户可以获得不少好处,如可以获得很光滑的表面和较低的工艺温度,从而不会出现材料的脆化问题。
如今氧化层对于PVD技术来说,已经不存在局限性。
今后,新涂层材料借助于铝、铬、锆和其他元素成分,将可以很好地适应市场,并开启新的远景。
这类涂层材料可以与超级氮化物进行组合,无论是典型的PVD 3μm,还是厚度在8~10μm 或是更大的,都可以根据刀片不同的边刃特征和运用场合来制造。
此外,还有一些新的预处理和二次处理的方法可供使用,结合采用最佳的涂层材料,即可使客户生产出很多独特的产品。
图2 如同珍珠链一样,图中所示是在涂层设备上的转位刀片采用较厚的涂层的好处是显而易见的。
一方面可以保护物体免受切削过程的影响(如高温);另一方面用户采用双倍厚度的涂层时,也可以获得几乎可以延长100%使用寿命的效果。
不管是目前已经可供应的CemeCon涂层材料,还是将来新研发的材料,均可适合于常见的钢材和铸铁工件的车削和粗铣削场合。
表面处理和涂层技术在齿轮上的应用初探

2005年2月重庆大学学报(自然科学版)Feb.2005 第28卷第2期Journal of Chongqing University(N tur l Science Editi on)Vol.28 No.2 文章编号:1000-582X(2005)02-0001-04表面处理和涂层技术在齿轮上的应用初探3钱文富1,曹兴进1,卢 龙1,黄 楠2,孙 鸿2,冷永祥2(1.重庆大学机械传动国家重点实验室,重庆 400030;2.西南交通大学教育部先进材料技术重点实验室,成都 610000)摘 要:利用气相物理沉积(P VD)技术和磁过滤弧源沉积的方法(DF AD),在由20Cr M o制造的直齿圆柱齿轮表面分别制备了Ti N以及C:N薄膜,并在齿轮传动实验台上进行了性能测试。
结果表明:齿轮表面上覆C:N薄膜后,在1800r pm,12Nm的工况下,连续运行50h,对齿轮表面在体式显微镜下进行观察,薄膜无明显破损,而未覆膜的淬火齿轮表面已经失效。
因此,齿轮表面覆膜对改善齿轮的减摩抗磨性的效果是十分明显的,也是切实可行的。
同时,还探讨了P VD技术在齿轮传动中应用时出现的问题,如用常用的多弧磁控溅射技术在齿轮表面涂覆Ti N膜,因温度太高导致渗碳淬火齿轮表面硬度因回火而降低,无法正常使用,采用磁过滤弧源沉积的方法对齿轮表面进行覆膜,能获得满意效果。
关键词:磁过滤弧源沉积;物理气相沉积;齿轮表面;减摩抗磨性 中图分类号:TG174.46文献标识码:A 齿轮是机械传动系统中的重要部件,它工作时的受力和运动情况是十分复杂的,由此产生的损伤形式多样,较常见的、后果较严重的损伤有3种:破坏性点蚀、断齿和破坏性胶合[1-2]。
因此需要齿轮具有高的抗弯曲疲劳强度,齿轮芯部要有高的强度和耐冲击韧性,齿面要有高硬度、高耐磨性和一定的抗腐蚀性能[3-4]。
德国国家标准(D I N3979,Zzahnschaden an Zahnradgetri2eben)将齿轮的损伤简单的分为两大类:表面损伤和折断[5]。
PVD涂层技术的使用为何能占半壁江山?看完你就明白了

PVD涂层技术的使⽤为何能占半壁江⼭?看完你就明⽩了 为探究PVD涂层技术在⾼速钢⼑具上的应⽤性能及性价⽐情况,我公司(⼭东临⼯⼯程机械有限公司技术中⼼⼯艺研究所)与某涂层公司合作进⾏了相关试验。
涂层⼑具已成为现代切削⼑具的标志,在⼑具中的使⽤⽐例已超过50%。
切削加⼯中使⽤的各种⼑具,包括车⼑、镗⼑、钻头、铰⼑、拉⼑、丝锥、螺纹梳⼑、滚压头、铣⼑、成形⼑具、齿轮滚⼑和插齿⼑等都可采⽤涂层⼯艺来提⾼其使⽤性能。
市场上涂层⼑具多以硬质合⾦涂层为主,⾼速钢涂层⼑具较少,这与⾼速钢⼑具成本及基体材料性能有关。
1. 试验过程 我公司分别在丝锥和滚⼑上做了PVD涂层试验。
(1)丝锥试验。
⼑具:⾼速钢机⽤丝锥M16-H2;涂层:PVD技术TiAlCrN,厚度2~4µm;加⼯⼯件:装载机后车架(见图1);材质:Q345B;螺纹孔数量:8个M16-6H↓16、2个M16-6H↓12。
图 1 试验⽅法:分别取5⽀涂层丝锥与5⽀普通丝锥加⼯⼯件,因基体材料相同,故采⽤相同切削参数。
研究丝锥的寿命及⼯件加⼯质量。
加⼯对⽐情况:丝锥及加⼯质量对⽐情况如图2所⽰。
图 2 丝锥寿命对⽐如表1所⽰。
(2)滚⼑试验。
⼑具:⾼速钢齿轮滚⼑m4.25;涂层:PVD技术TiAlCrN,厚度2~4µm;加⼯⼯件:变速箱⼀挡倒挡架(见图3);材质:ZG310-570;齿数:57;齿宽:40.5mm。
图 3 试验⽅法:分别取3把新涂层滚⼑与3把新的普通滚⼑加⼯⼯件,采⽤相同切削参数。
研究滚⼑第⼀次刃磨前的寿命及⼯件加⼯质量。
加⼯对⽐情况:滚⼑及加⼯质量对⽐情况如图4所⽰。
图 4 滚⼑寿命对⽐如表2所⽰。
2. 数据及成本分析 (1)丝锥寿命、成本分析。
5 种涂层丝锥寿命总和是5 种普通丝锥寿命总和的327÷173=1.87倍。
M16丝锥市场价格约为30元,涂层价格约为15元,成本降低为 [(1-30+15)÷(30×1.87)]×100%=20% 使⽤涂层丝锥与普通丝锥相⽐,寿命提⾼为原来的1.87倍,成本降低20%。
我国刀具PVD涂层技术发展的问题与对策
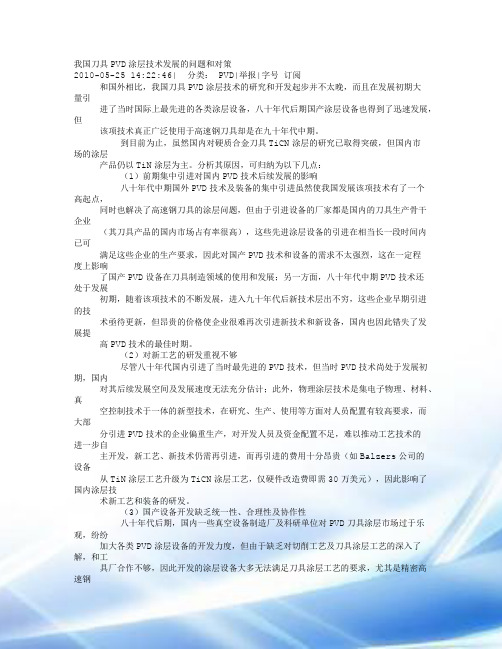
我国刀具PVD涂层技术发展的问题和对策2010-05-25 14:22:46| 分类: PVD|举报|字号订阅和国外相比,我国刀具PVD涂层技术的研究和开发起步并不太晚,而且在发展初期大量引进了当时国际上最先进的各类涂层设备,八十年代后期国产涂层设备也得到了迅速发展,但该项技术真正广泛使用于高速钢刀具却是在九十年代中期。
到目前为止,虽然国内对硬质合金刀具TiCN涂层的研究已取得突破,但国内市场的涂层产品仍以TiN涂层为主。
分析其原因,可归纳为以下几点:(1)前期集中引进对国内PVD技术后续发展的影响八十年代中期国外PVD技术及装备的集中引进虽然使我国发展该项技术有了一个高起点,同时也解决了高速钢刀具的涂层问题,但由于引进设备的厂家都是国内的刀具生产骨干企业(其刀具产品的国内市场占有率很高),这些先进涂层设备的引进在相当长一段时间内已可满足这些企业的生产要求,因此对国产PVD技术和设备的需求不太强烈,这在一定程度上影响了国产PVD设备在刀具制造领域的使用和发展;另一方面,八十年代中期PVD技术还处于发展初期,随着该项技术的不断发展,进入九十年代后新技术层出不穷,这些企业早期引进的技术亟待更新,但昂贵的价格使企业很难再次引进新技术和新设备,国内也因此错失了发展提高PVD技术的最佳时期。
(2)对新工艺的研发重视不够尽管八十年代国内引进了当时最先进的PVD技术,但当时PVD技术尚处于发展初期,国内对其后续发展空间及发展速度无法充分估计;此外,物理涂层技术是集电子物理、材料、真空控制技术于一体的新型技术,在研究、生产、使用等方面对人员配置有较高要求,而大部分引进PVD技术的企业偏重生产,对开发人员及资金配置不足,难以推动工艺技术的进一步自主开发,新工艺、新技术仍需再引进,而再引进的费用十分昂贵(如Balzers公司的设备从TiN涂层工艺升级为TiCN涂层工艺,仅硬件改造费即需30万美元),因此影响了国内涂层技术新工艺和装备的研发。
工程齿轮的耐磨涂层与表面处理技术
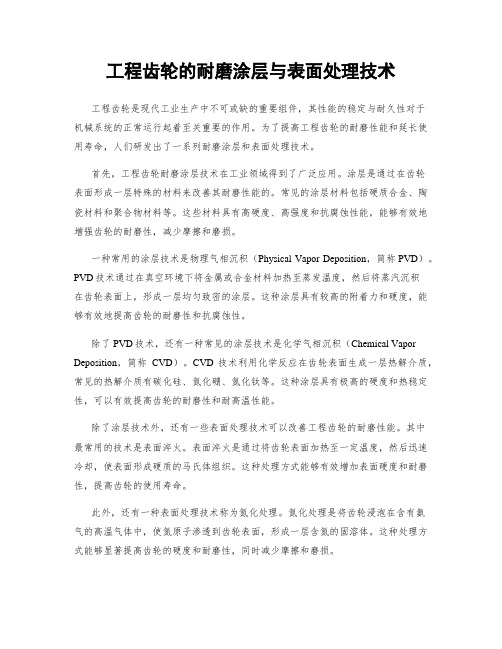
工程齿轮的耐磨涂层与表面处理技术工程齿轮是现代工业生产中不可或缺的重要组件,其性能的稳定与耐久性对于机械系统的正常运行起着至关重要的作用。
为了提高工程齿轮的耐磨性能和延长使用寿命,人们研发出了一系列耐磨涂层和表面处理技术。
首先,工程齿轮耐磨涂层技术在工业领域得到了广泛应用。
涂层是通过在齿轮表面形成一层特殊的材料来改善其耐磨性能的。
常见的涂层材料包括硬质合金、陶瓷材料和聚合物材料等。
这些材料具有高硬度、高强度和抗腐蚀性能,能够有效地增强齿轮的耐磨性,减少摩擦和磨损。
一种常用的涂层技术是物理气相沉积(Physical Vapor Deposition,简称PVD)。
PVD技术通过在真空环境下将金属或合金材料加热至蒸发温度,然后将蒸汽沉积在齿轮表面上,形成一层均匀致密的涂层。
这种涂层具有较高的附着力和硬度,能够有效地提高齿轮的耐磨性和抗腐蚀性。
除了PVD技术,还有一种常见的涂层技术是化学气相沉积(Chemical Vapor Deposition,简称CVD)。
CVD技术利用化学反应在齿轮表面生成一层热解介质,常见的热解介质有碳化硅、氮化硼、氮化钛等。
这种涂层具有极高的硬度和热稳定性,可以有效提高齿轮的耐磨性和耐高温性能。
除了涂层技术外,还有一些表面处理技术可以改善工程齿轮的耐磨性能。
其中最常用的技术是表面淬火。
表面淬火是通过将齿轮表面加热至一定温度,然后迅速冷却,使表面形成硬质的马氏体组织。
这种处理方式能够有效增加表面硬度和耐磨性,提高齿轮的使用寿命。
此外,还有一种表面处理技术称为氮化处理。
氮化处理是将齿轮浸泡在含有氨气的高温气体中,使氮原子渗透到齿轮表面,形成一层含氮的固溶体。
这种处理方式能够显著提高齿轮的硬度和耐磨性,同时减少摩擦和磨损。
总结起来,工程齿轮的耐磨涂层技术和表面处理技术是提高齿轮耐磨性能和延长使用寿命的重要手段。
涂层技术包括PVD和CVD技术,能够形成高硬度、高强度和抗腐蚀的涂层,有效改善齿轮的耐磨性能。
PVD高性能超硬涂层刀具的应用

PVD高性能超硬涂层刀具的应用【摘要】随着涂层技术的进步,具有高硬度,高耐磨性及抗高温氧化性能的PVD涂层刀具是近年来研究的热点,在整体钨钢刀具、高速钢刀具等方面都显示出良好的应用前景。
【关键词】PVD技术;刀具涂层;钻头;丝锥0 引言涂层作为化学屏障和热屏障,涂层刀具的构成减少了刀具与工件间的扩散和化学反应,从而减少了月牙槽磨损,其刀具具有表面硬度高、耐磨性好、化学性能稳定、耐热耐氧化、摩擦因数小和热导率低等特性。
作为切削刀具主流的高速钢刀具,涂层刀具已占到80%以上。
其中PVD技术,鉴于其工艺温度较低,通常对刀具基材的性能的影响力度低,再者工艺方案样式变化快,从而使用范围颇广,涂层技术已经成为构成现代切削刀具的三大核心技术之一。
1 高速钢钻头和丝锥表面的Co离子注入金属离子注入技术是将金属蒸气引入电离室,经高压电场作用进行离化和加速,引出大束流金属正离子流并以极高速度和能量注入表面组织中,通过改变注入工艺参数可进行单元素和多元素金属的单注或共注。
依据刀具切削性能的规范要求,从而择取需要注入的金属元素,为达到切削效果的最佳境界,针对注入后的表面效果和检测显示,注入好金属元素的表面晶格有明显畸变和强化现象,物体表层组织与已注入的金属元素离子产生了化合反应,产生了金属化合物和弥散金属硬质相,如氧化物、碳化物和氮化物等,例如注入Ti、Co、C等金属元素,金属表面硬度可达1600-2000HV。
注入后成就的硬化改性层深度可控制值几埃米到几百纳米。
除此之外,此硬质层是混合物,无传统涂层的显著表面,所以此硬质层与金属基体含有超高的结合强度,因而提高改性表面的耐磨性、抗冲击性和耐腐蚀性。
我们对高速钢钻头、丝锥进行Co离子注入并和没有注入并处理的钻头、丝锥作了切削性能对比试验,注入Co离子丝锥的材料为W6Mo5Cr4V2,尺寸为M10×1 (带刃倾角),试件为1Cr18Ni9Ti 不锈钢,硬度190HB;,抗拉强度642MPa,选用切削速度3.6m/min,浇注乳化切削液,流量5L/min。
PVD涂层技术在我国刀具制造中的现状及发展

PVD涂层技术在我国刀具制造中的现状及发展切削刀具表面涂层技术是近几十年应市场需求发展起来的材料表面改性技术。
采用涂层技术可有效提高切削刀具使用寿命,使刀具获得优良的综合机械性能,从而大幅度提高机械加工效率。
我国的刀具涂层技术经过多年发展,目前正处于关键时期,充分了解国内外刀具涂层技术的现状及发展趋势,瞄准国际涂层技术先进水平,有计划、按步骤地发展刀具涂层技术,对于提高我国切削刀具制造水平具有重要意义。
标签:PVD涂层技术现状存在的问题应对措施1PVD涂层技术简介物理气相沉积(PVD)是一种表面处理的标准化称谓。
从高精密加工刀具、装饰件、高要求机械零部件到高精密集成电路的模具等等具有很广泛的用途,它是一种真正能够获得微米级镀层且无污染的环保型表面处理方法,且在不影响工件原来的尺寸情况,PVD膜可用来改善表面的外观,提高表面的强度,增强耐磨性,而且具有很好的导热,防腐蚀及防刮擦的能力。
PVD技术出现于二十世纪七十年代末,由于其工艺处理温度可控制在500℃以下,因此可作为最终处理工艺用于高速钢类刀具的涂层。
由于采用PVD工艺可大幅度提高高速钢刀具的切削性能,所以该技术自八十年代以来得到了迅速推广,至八十年代末,工业发达国家高速钢复杂刀具的PVD涂层比例已超过60%。
2PVD涂层技术在我国刀具制造中的现状我国PVD涂层技术的研发工作始于八十年代初期,至八十年代中期研制成功中小型空心阴极离子镀膜机,并开发了高速钢刀具TiN涂层工艺技术。
在此期间,由于对切削刀具涂层市场前景看好,国内共有七家大型工具厂从国外引进了大型PVD涂层设备。
技术及设备的引进调动了国内PVD技术的开发热潮,许多科研单位和各大真空设备厂纷纷展开了大型离子镀膜机的研制工作,并于九十年代初开发出多种PVD涂层设备。
但由于多数设备性能指标不高,无法保证刀具涂层质量,同时预期的市场效益未能实现,因此大多数企业未对PVD刀具涂层技术作进一步深入研究,导致近十年国内PVD刀具涂层技术的发展徘徊不前。
延长刀具使用寿命的PVD涂层

物理气相沉积技术 (PVD) 常被用在切削刀具上,以延长刀具的使用寿命及提高其硬度。
当然,不同的应用情况都有其特定的涂层,能够达到最好的应用效果。
一般情况下,AlTiN是常见的刀具涂层。
对于一些特殊的加工材料,Al2O3涂层能够取得更好的效果。
在加工过程中,切削刀具将承受几方面的损伤,如切削热、高压、磨损和热振荡。
刃口的温度将超过1000℃。
这种极端的热量将破坏刀具材料各成分的结合力及其他成分,还有可能导致刀具和被加工材料间发生有害的化学反应。
磨损是切削过程中始终发生的情况,刀具和被加工材料间的接触面将承受大于140bar(1bar=0.1MPa)的压力。
热振荡:刀具的快速加热和冷却是加工过程中非常普遍的情况;在切削过程中,刀片被加热,当刀片离开切削面时,刀片被冷却。
机械振荡在加工断续表面时经常发生。
根据具体操作和被加工工件的情况,机械振荡有时扮演着车削加工的角色。
粘连磨损经常发生在被加工材料粘连在刀具表面的情况下。
为了解决上述这些在切削过程中不利因素的影响,许多切削刀具都通过在PVD设备内的电弧沉积技术沉积了一层 AlTiN涂层。
AlTiN类的涂层主要应用在干式高速切削加工中,具有很多的优点,如高硬度(HV>30GPa),很好的耐磨损性能,很好的耐高温氧化性(850℃),以及低的热传导性。
在一些应用上需要特殊的涂层,如Al2O3涂层。
比如硬质合金刀片上的Al2O3涂层具有抗月牙洼和抗热裂化的优点。
Al2O3涂层的刀片通常是CVD(化学气相沉积)方法沉积的,但是有一些缺点:因为是在高温下的沉积(1000℃),硬质合金变脆将影响刀片在金属切削方面的应用,尤其是在铣削方面。
Al2O3的PVD 涂层因为其较低的沉积温度范围(一般在350~600℃)带来了很多优点。
特别是高温稳定性,化学稳定性和低导热导电性能是其优于其他涂层的特点。
在不锈钢的铣削或者是难切削材料的切削方面,PVD的Al2O3涂层与传统PVD涂层相比显示了更好的性能。
pvd和cvd的应用场景
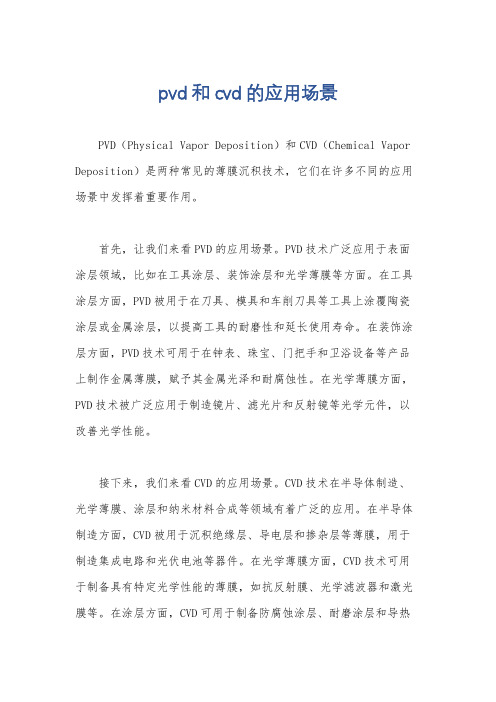
pvd和cvd的应用场景
PVD(Physical Vapor Deposition)和CVD(Chemical Vapor Deposition)是两种常见的薄膜沉积技术,它们在许多不同的应用场景中发挥着重要作用。
首先,让我们来看PVD的应用场景。
PVD技术广泛应用于表面涂层领域,比如在工具涂层、装饰涂层和光学薄膜等方面。
在工具涂层方面,PVD被用于在刀具、模具和车削刀具等工具上涂覆陶瓷涂层或金属涂层,以提高工具的耐磨性和延长使用寿命。
在装饰涂层方面,PVD技术可用于在钟表、珠宝、门把手和卫浴设备等产品上制作金属薄膜,赋予其金属光泽和耐腐蚀性。
在光学薄膜方面,PVD技术被广泛应用于制造镜片、滤光片和反射镜等光学元件,以改善光学性能。
接下来,我们来看CVD的应用场景。
CVD技术在半导体制造、光学薄膜、涂层和纳米材料合成等领域有着广泛的应用。
在半导体制造方面,CVD被用于沉积绝缘层、导电层和掺杂层等薄膜,用于制造集成电路和光伏电池等器件。
在光学薄膜方面,CVD技术可用于制备具有特定光学性能的薄膜,如抗反射膜、光学滤波器和激光膜等。
在涂层方面,CVD可用于制备防腐蚀涂层、耐磨涂层和导热
涂层等功能性涂层。
此外,CVD还被广泛应用于纳米材料的合成,如碳纳米管、石墨烯和纳米颗粒等。
总的来说,PVD和CVD技术在工业生产、科研领域和日常生活中都有着重要的应用,它们通过沉积不同性质的薄膜,为各种材料赋予特定的功能和性能,推动着许多领域的发展和进步。
基于切削力的pvd涂层刀具性能研究

基于切削力的pvd涂层刀具性能研究近几十年来,随着科技的发展和社会的进步,刀具技术也取得了长足的发展。
传统的刀具受到时间、空间、环境条件的限制,使得刀具的性能受到较大的影响。
为了改善这一现状,PVD(物理气相沉积)技术应运而生,并且得到了广泛的应用。
本文旨在利用PVD技术对刀具进行涂层,以提高其性能,并研究基于切削力的PVD涂层刀具性能。
PVD涂层技术实际上是采用物理气相沉积制备出材料层次结构,不包括化学反应。
通过物理气相沉积技术,可以在涂层表面形成一层具有抗腐蚀性、耐磨性、导电性和或容易抛光的薄膜。
基于此,PVD 技术被广泛应用于刀具制作和涂层表面。
传统的刀具制作技术,会出现刀具太坚硬或者太软的情况,这将会影响刀具的使用寿命和性能。
通过PVD技术,可以调节刀具的硬度和表面粗糙度,以达到较好的切削性能。
所以,采用PVD涂层技术进行刀具涂层能够较好地提高刀具的性能,保证刀具的高效性能和长期使用寿命。
基于此,本文将利用基于切削力的PVD技术研究刀具的性能,以探讨PVD涂层刀具的性能。
首先,本文介绍了PVD涂层技术的基本原理和优点,以及PVD涂层刀具在某些行业方面的应用。
其次,本文在研究模型及刀具试验机器上,采用PVD技术进行刀具涂层,同时采用实验法研究不同涂层层数和深度对切削力的影响,以了解基于切削力的PVD涂层刀具性能。
实验结果表明,当刀具采用PVD涂层技术涂层时,具有较低的切削力,更稳定可靠的性能,并且还可以提高刀具的耐用性和可靠性。
此外,PVD涂层刀具比非涂层刀具具有更高的刀片强度,且具有更长的使用寿命,可以提高工作效率。
综上,PVD技术结合切削力的研究,为刀具的涂层提供了一种有效的方法,而且可以满足刀具表面硬度和密度的调整要求,达到长寿命、高效、可靠性能等要求。
本文仅对采用PVD技术涂层刀具的性能进行研究,在实际应用中仍存在诸多不足之处,例如涂层层数的限制、涂层过程的复杂性和质量控制的难度等,因此,如何改进PVD技术,以提高其在刀具上的应用能力,仍有待进一步研究。
超晶PVD涂层技术在刀工具上的应用PPT文档共37页

2、要冒一次险!整个生命就是一场冒险。走得最远的人,常是愿意 去做,并愿意去冒险的人。“稳妥”之船,从未能从岸边走远。-戴尔.卡耐基。
梦 境
3、人生就像一杯没有加糖的咖啡,晶PVD涂层技术在刀工具上的应用 4、守业的最好办法就是不断的发展。 5、当爱不能完美,我宁愿选择无悔,不管来生多么美丽,我不愿失 去今生对你的记忆,我不求天长地久的美景,我只要生生世世的轮 回里有你。
谢谢你的阅读
❖ 知识就是财富 ❖ 丰富你的人生
71、既然我已经踏上这条道路,那么,任何东西都不应妨碍我沿着这条路走下去。——康德 72、家庭成为快乐的种子在外也不致成为障碍物但在旅行之际却是夜间的伴侣。——西塞罗 73、坚持意志伟大的事业需要始终不渝的精神。——伏尔泰 74、路漫漫其修道远,吾将上下而求索。——屈原 75、内外相应,言行相称。——韩非
锥齿轮模具表面PVD技术的应用

一 n女 I r 、『 f rl 等 )fI,Jf微)} If 涂 r fi邑较 低 的 ,斗f小 发 展 为 TiC、 FiCN、Zi N、(:I-N、Mo. S 、rriAlN、 A N、 、 l .fI i }f: f小 l J’!E/iJ:I!t(J rl 订邑 是j肯1,{ - 条f f:下 ,采 TiN—AIN、CNx、DI (:和 h卜( 等多几 复 合涂层
PVD J 小 方 法 : — 熊 发 、溅 射 、离 子镀 ( 心
造 、选 材 )进 f ,小艾 行 介乡 摸 具 处 技 术 『I] 做离 子 镀 、热 l;J]搬 离子 镀 、i 弧 离 子镀 、活 反心 离 j
的 l \I)技 术I;73'I!、4‘、 点 7曼 『 I-.以及 l )&I 处 技 镀 、射 离 于镀 、r1:流 放 }tJ.离子镀 ) I)披 术 仃 :
(收砌 … }jj:2()1 8-()1—1 2)t互:
摸具 制]  ̄ 7- v、1 8年 第 4期
11 1j‘lII 【1IlIA Jew/2061‘·57f1f_ 46517tI324()¨ ,094 h,mI.201 1—10— 14
作 者 简介 :连 什 强 ,男 ,1986年 生 ,2008年 毕 业 于 武 汉 理 工 大 学 ,目前 工作 单 位 为 东风 本 田汽 车 有 限公 司 ,从 事新 车型技 术 的导 入 及能 扩 工 作
种 失 效 式 ,提 高 了 具 寿命
关 键 词 :锥 齿轮 模 具 ;失效 形 式 ;I D技 术
中图 分 类号 :T( l62
文 献标 识 码 :B
Application 0f PV D Technology in the Bevel G ear Die
PVD涂层技术的发展与应用
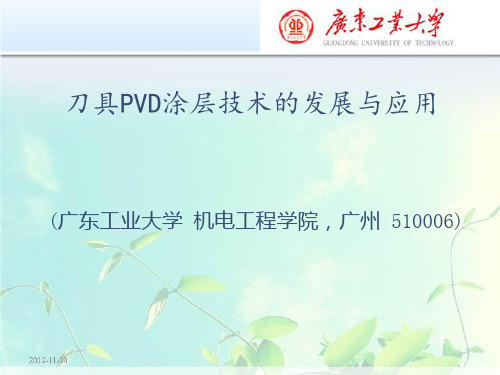
2.PVD技术的工作原理和主要技术
在刀具涂层中,最常用的物理涂层为溅射沉积和阴极弧蒸发沉积, 后者属于蒸发法。图2-1为溅射沉积和阴极弧蒸发沉积过程的示意图, 两种沉积过程都是由低压放电气体组成的等离子体环境中完成。 图2-1溅射和阴极弧蒸发沉积示意图
2.1 溅射沉积技术原理
溅射沉积是在由低压放电气体组成的等离子体环境中完成,它利用 带有电荷的离子在电场中加速后具有一定动能的特点,将离子引向欲 被溅射的靶电极。在离子能量足够的情况下,靶表面的原子在入射离 子的轰击下被溅射出来。这些被溅射的原子带有一定的动能,并且会 沿着一定的方向射向基体,从而实现在基体上薄膜的沉积。 图2-2 溅射沉积示意图
3.2 氮化碳涂层
近年来,氮化碳(C3N4 ) 作为一种新型的超硬材料,已成为 有实用价值的刀具涂层材料对于高速钢刀具,经过C3N4涂层,对 刀具耐磨性的提高极为显著,其 效 果 超 过 了 TiN涂 层; 高 速 钢 麻 花 钻,经 过C3N4涂层,能使其耐用度大为提高,可取代常用 的TiN涂层麻花钻; 硬质合金刀片( 刀具) ,经过C3N4涂层,亦能提 高刀片( 刀具) 的耐用度,但提高幅度不如高速钢刀具那样大。美 国物理学家A.M.Liu和M.L.Cohen 首先用分子工程理论,设计出 超硬无机化合物氮化碳,根据体弹性模量的计算,可能达到金刚 石的硬度氮化碳作为一种超硬薄膜材料,除了具有高硬度外,还 有低摩擦系数高导热性能很好的化学稳定性和抗氧化性能,能切 削加工铁族元素,作为刀具涂层材料具有广阔的应用前景。
称之为“阴极点”,阴极点的电流密度达到 10A/cm2,高的电流密度 引起弧侵蚀并完成蒸发材料的离化。靶材侵蚀过程中,参与放电的导 电介质由高度离化的阴极材料所组成,这是由阴极斑点中强烈的金属 蒸气发射所产生。阴极材料的蒸发是由于阴极表面局部的高温所造成。 非常高的功率密度形成小的熔池。每个阴极斑点产生高速的阴极材料 喷射,离子流相当于总弧电流的7%~10%。如果没有额外装置的控制, 产生的弧将会随机地在阴极表面随即漂移,靶材的浸蚀也将是随机不 可控,这样将会减少靶材的利用率。为了使靶材的侵蚀过程处于可控 状态,通常在阴极背后加一磁控系统来控制弧在靶材表面的运动(类 似于磁控溅射控制电子的运动),用以控制靶材的侵蚀。
磨齿机刀具的涂层与表面特性优化研究

磨齿机刀具的涂层与表面特性优化研究摘要:磨齿机刀具的涂层与表面特性优化研究是针对提高刀具性能和延长刀具寿命的一项重要研究内容。
本文以磨齿机刀具为研究对象,利用不同的涂层技术和优化方法,对刀具的表面特性进行改善,旨在提高刀具的耐磨性、硬度和切削效果,为切削加工提供更好的解决方案。
1. 引言磨齿机刀具在机械加工中起到至关重要的作用,其性能直接影响到加工质量和效率。
传统的刀具材料往往无法满足高速加工、高硬度、高耐磨性的要求,因此,采用涂层技术来改善刀具的表面特性成为一种有效的方法。
2. 涂层技术目前常用的涂层技术主要有物理气相沉积(PVD)和化学气相沉积(CVD)两种。
PVD涂层具有高硬度、低摩擦系数、良好的耐磨性等特点,适用于高温和高速切削;CVD涂层具有较好的耐高温性能和化学稳定性,适用于高温切削。
3. 涂层参数的优化涂层参数的优化对刀具性能有着重要的影响。
其中,涂层厚度、成分、结构以及表面粗糙度等参数的选择能够显著改善刀具的性能。
涂层厚度的选择需要兼顾刀具的硬度和切削性能,过厚的涂层可能影响切削效果,过薄的涂层则可能降低刀具的耐磨性。
成分的选择需要根据刀具材料和加工条件进行考虑,以提高刀具的抗氧化、耐磨和硬度。
涂层结构的优化能够减少残余应力和增加涂层的结合强度,提高刀具寿命。
表面粗糙度的控制对于涂层的附着力和耐磨性至关重要,合适的表面粗糙度能够提高刀具的性能。
4. 涂层与切削性能涂层对切削性能有着直接的影响。
优良的涂层能够显著降低刀具的摩擦系数,提高切削表面的质量,并减少刀具的磨损。
此外,涂层还能增加切削力的承受能力,提高切削的稳定性和效率。
因此,在选择涂层时,需要综合考虑切削材料、切削速度、温度和切削力等因素,以获得最佳的切削性能。
5. 表面特性的测试与评价为了研究涂层与切削性能的关系,需要对刀具的表面特性进行测试与评价。
常见的测试方法包括扫描电子显微镜(SEM)、X射线衍射(XRD)、纳米硬度测试等。
- 1、下载文档前请自行甄别文档内容的完整性,平台不提供额外的编辑、内容补充、找答案等附加服务。
- 2、"仅部分预览"的文档,不可在线预览部分如存在完整性等问题,可反馈申请退款(可完整预览的文档不适用该条件!)。
- 3、如文档侵犯您的权益,请联系客服反馈,我们会尽快为您处理(人工客服工作时间:9:00-18:30)。
超微集团简介
目前超微集团已有苏州、平湖、镇江、东莞、常州五 个涂层中心,随着中国汽车工业、机械、机床、精密五 金、模具工业,以及电子等行业飞速发展,我们还将在 华南、华东、华北以及西南等地建立新的涂层中心,为 更广大的客户服务。
涂层滚刀加工案例
线速度小于80m/min的低速加工一般 选用TiN涂层;速度达80-100m/min的 高速加工选用AlTiN或CrAlTiN涂层。
TiN涂层滚刀
经过超微TiN涂层处理的滚齿刀寿 命比别家涂层提高了11%,且磨损 量从0.3mm降到0.2mm,减少了 每次修磨量,使修磨次数从原来的 18次左右增加到25次左右 ,从而 使齿轮加工的单位成本大幅下降
根据加工需要正确选择刀具涂层有可能是一件令人困惑和费 劲的工作。每一种涂层在切削加工中都既有优势又有缺点, 如果选用了不恰当的涂层,有可能导致刀具寿命低于未涂层 刀具,有时甚至会引出比涂层以前更多的问题。 涂层的特性 : (1)硬度 (2)耐磨性 (3)表面润滑性 (4)氧化温度 (5)抗粘结性
&
加工条件: (1)切削参数(速度,进给) (2)被加工材料 (3)干/湿,切削液 (4)加工工艺(车、铣) (5)机床
钝化前
钝化后
刃口钝化减少微崩
较大的刀刃半径 降低应力集中 减少刀刃微崩
研磨毛刺对涂层的影响
卷边
毛刺
缺口
滚刀研磨后的毛刺现象
未做钝化的滚刀涂层后形貌
涂层剥落
涂层附着在卷边上
做钝化的滚刀涂层后形貌
刀具钝化技术
1. 干/湿喷砂 2. 尼龙刷钝化轮 3. 立式旋转钝化 4. 滚刀钝化
正确选择刀具涂层
涂层特性与选择
涂层 TiN 特点 通用 加工速度 <80m/min 加工材料 钢材 干 /湿 湿
TiCN
CrN
高韧性
低亲合性
<80m/min
<80m/min 80-120m/min >120m/min
不锈钢
有色金属
湿
湿
AlTiN
AlCrN
高硬度,耐高温
高韧性,耐高温
钢材
钢材
干 /湿
干 /湿
根据刀具主要失效模式选择涂层
耐磨涂层 耐高温涂层 低亲和性涂层
磨损
月牙洼
积屑瘤
沟槽
塑性变形
崩刃
刀具重磨,退镀及再涂层
硬质合金和高速钢刀具的重磨和再涂层是目前常见的工艺。尽 管刀具重磨或再涂层的价格仅为新刀具制造本钱的一小部分, 但却能延长刀具寿命。重磨工艺是特殊刀具或价格昂贵刀具的 典型处理方法。可进行重磨或再涂层的刀具包括钻头、铣刀、 齿轮滚刀以及成形刀具等。 刀具重磨重镀工艺: 1.刃口重磨:砂轮,磨削量 2.涂层退除:高速钢OK,硬质合金NG 3.刃口处理:刃口重新钝化 4.重新涂层 :先择合适工艺与涂层
涂层滚刀加工案例
AlTiN涂层滚刀
其他厂家
超微
切削工艺: 滚刀: 高速钢 加工参数:转速725r/min 线速度:137m/min 切削液:无
机床:高速干滚机 kashifuji 刀具规格:80*140 进给量:2.5mm
层滚刀加工案例
CrAlTiN涂层
3000 2500 2000 1500 1000 500 0 2400
PVD涂层在齿轮加工刀具的应用
汽车变速箱齿轮
风电增速箱齿轮
减速机齿轮
滚刀涂层流程
检验 检验 检验
清洗 退镀 钝化 清洗 装夹 镀膜 下挂 包装 取货 出货
入库 修磨 入库
还刀
加工
领刀
入库
刀具涂层前处理
各类刀具都要经过仔细的刃磨,并使加工粗糙度值达到了 Ra0.8um,甚至是Ra0.4um。 刀具制造工序的最后一道工序——磨削工序完成后,再对 刀具刃口进行一次钝化处理,则刀刃处将会出现一细微的 圆弧刃口,刃带也将变得光滑,这就消除了豁牙、锯齿和 裂纹等缺陷。
产品参数 · CG125正时齿轮 (M1.5 Z22 α20° β28° 左 旋) · 材料:40Cr (硬度:HRC14~18)
刀具参数 · 规 格: 120*6 5*32 N1 Z12 · 材料:M35 · 涂层:TiN
切削参数 · 主轴转速:330rpm(V切 =67.35m/min) · 走刀量:1.9 窜刀量0.12mm/3 件 · 切削量:一刀切 ·装夹件数:3件 · 切削液:32#机械油 · 刀具磨损量:0.20mm
2000 720
无涂层
AlTiN
CrAlTiN
切削条件: 滚刀材质:粉末高速钢 涂层材料:CrAlTiN 主轴转速:500rpm 切削液:机械油
滚刀规格:70 x 120 工件材料:20CrMoTi 线速度:105m/min
TiN插齿加工实例
TiN涂层滚刀寿命是无涂层的8-10倍,切削速度可提高 30%,进给提高10%。 例如:插齿生产70个齿的汽车内啮 合齿轮,有TiN涂层的插齿刀每刃磨一次可以生产300件, 磨损量0.25mm;无涂层的插齿刀每刃磨一次生产75件, 磨损量0.92mm。