轮胎胶囊概述
高使用寿命的轮胎硫化胶囊

命下降 。最佳的树脂用量范围为 5~7 份 。 制在 110~114 份左右 。
(1) 促进剂 DM
(2) 氧化锌
促进 剂 DM 常 用 于 胶 囊 的 树 脂 交 联 。
氧化锌常用于催化树脂硫化 。但当其用
低配合量的促进剂 DM 可以提高树脂交联 量达到 1 份时才会发生作用 ,但反应将是很
胶料的交联度 ,但降低屈挠寿命 。高配合量 慢的 ,而且也不完全 。当用量超过 5 份时 ,除
10 0 轮 胎 工 业 1998 年第 18 卷
213 模压硫化 EXXPRO 胶料的模压硫化与 一 般 IIR
相比 ,除了硫化时间和温度上的差别外没有 什么不同 ,只是 EXXPRO 的胶条不得预热 。 胶条最好预接头 ,胶条接头在模具圆周上均 匀地间隔开 。硫化机闭合应十分迅速 。生产 轿车轮胎的硫化胶囊时 ,达到硫化全压的时 间应控制在 20 s ,而对于载重轮胎用的胶囊 应控制在 30 s。用 EXXPRO 胶料制作的胶 囊的硫化温度控制在 190 ℃或以下 ,建议采 用 185 ℃。硫化时间的制定要在使胶囊最厚 部位不再产生气孔时再延长 2 min 。 214 注压硫化
1 溴化异丁烯/ 对甲基苯乙烯共聚物 异丁烯基弹性体的耐热氧化性能历来就
非常优异 。这是由其大分子主链上的高度饱 和结构所决定的 (见图 1) 。IIR 的交联是通 过 1 ,42异戊二烯在大分子链上提供少量的 不饱和组分完成的 。
CH3
CH2 C
+ CH2 CH
CH3
CH3
CH3
CH2 C CH2 CH CH2 C
离剂 ,而不用硬脂酸类物质 ,因为它会影响和 降低焦烧安全性 。应严格控制终炼胶的停放 时间 (最长为两周 ,夏季建议为一周) 。建议 不要对混炼胶施加应力 ,因为这样会明显延 长胶料的热历程 ,并降低胶料焦烧安全性 。 212 挤出的准备
轮胎胶囊概述

轮胎胶囊概述作者:刘帅轮胎硫化胶囊(后面简称胶囊)主要是轮胎硫化的一个工具。
材质为丁基橡胶。
相当于轮胎模具的内模。
胶囊根据硫化机、夹具不同,分为不同型号:斜交A型、斜交B型、斜交AB型、子午A型(成为RA)、子午B型(RB)和子午AB型(RAB)。
其作用主要在轮胎硫化过程中内部充压缩气、充氮气或充过热水等。
使其伸张,撑起轮胎胶胚形成内压硫化轮胎。
其优点为导热快,效率高,劳动强度低,操作简便。
胶囊在硫化轮胎时有一定的伸张比,一般径向伸张R=外胎胎里直径(DK)/胶囊原始状态直径(DB)。
斜交胎B型胶囊径向伸张取值为1.6-1.85,斜交胎A 型与B型伸张比相似。
子午胎取值为1.10-1.15,允许值为1.05-1.20。
在胶囊和轮胎的选型时除了胶囊直径外还有一个重要条件需要注意就是胶囊断面周长。
胶囊断面周长伸张L=外胎断面内轮廓周长/胶囊断面周长。
胶囊的断面周长伸张应尽可能小,与轮胎内轮廓的伸张不应超过20%,一般轻型载重轮胎B型胶囊的断面周长为1.08-1.15%。
重型轮胎断面周长伸张值为1.02-1.04,A型胶囊断面周长伸张值较大,斜交、子午胎均为1.1-1.15左右。
胶囊是反复伸张的工作条件。
所以使用寿命除了高伸张也受到高温和耐氧化情况,即轮胎公司过热水的除氧情况。
这个是有具体指标规定的。
一般为过热水氧指数含量不超过0.05PPm(氮气硫化除外)。
一.轮胎硫化胶囊配方思路胶囊使用温度一般为180-200度。
接触的介质主要是过热水,过热蒸汽,压缩空气或者氮气。
胶囊伸张比很大尤其是斜交类型的胶囊。
所说义针对以上我们胶囊配方设计思路为耐高温,高伸张,耐氧化,高伸张后的还原性即扯断永久变形。
思路分析为:高温达不到就是直接导致硫化胶囊的使用寿命折损。
伸张和扯断永久变形是想关联考虑的,伸张太低有损使用寿命。
伸张太高由于应力松弛回原性下降,所以在保证扯断伸长率的前提下也要保证含胶率,交联密度和胶料的强度。
TBR帖合、成型、硫化

HF220
26
14
14
366
340
17.5″成型机
HF230
36
16
16
400
360
19.5″成型机
HF260
25
13
14
334
310
16″成型机
成型机胎圈锁定环
外型尺寸及适用规格
代号 L1 L2 φ1 φ2 适用规格
HF1 00
44
16
44 0
39 0
7.50/8.25/9.0 0/10.00R20 成型机
胎圈填充胶条贴合机反包胶囊
胎圈填充胶条贴合机反包胶囊
代号 L H φ1 φ2 φ3 适用规格
HA100
515
5.25
452.5
431.5
442
20″贴合机
HA200
520
5.25
481.5
460.5
471
22″/22.5″贴合机
HA210
520
5.25
531.5
510.5
521
24″/24.5″贴合机
225/70R19.5 215/75R17.5 11.00R22、
代号 规格 ØA ØB ØC ØD E F G R1 R2 R3 R4 R5 M N
HG210 790×620 790
HG200 900×620 900
HG190 620×430 620
备注
桦林佳通
银川佳通
银川佳通
银川佳通
胎圈填充胶条贴合机反包胶囊
HA220
500
5
352.5
332
342.5
17.5″贴合机
小规格轮胎胶囊膨胀结构成型鼓的研制及应用

小规格轮胎胶囊膨胀结构成型鼓的研制及应用赵洪金,刘爱月(辽宁轮胎集团有限责任公司,辽宁朝阳 122009) 摘要:介绍应用于4100-8,5100-8和6100-9,7100-9四种规格轮胎的胶囊膨胀结构成型鼓的构造、工作原理以及其重要技术参数的确定、主要部件的设计与制造及轮胎成型的主要施工标准的确定。
实际应用表明,与传统卸鼓肩成型鼓相比,运用胶囊成型鼓可降低劳动强度,提高劳动生产率,改善产品质量。
关键词:胶囊成型鼓;卸鼓肩成型鼓;轮胎 中图分类号:TQ33616+6 文献标识码:B 文章编号:100628171(2002)022******* 轮胎成型鼓结构优劣直接影响着工人的劳动强度及轮胎产品的产量和质量。
多数厂家在4100-8,5100-8,6100-9和7100-9四种规格轮胎成型时使用卸鼓肩成型鼓,由于其轮辋直径相对较小,成型鼓折叠比大于1133,且主、副连杆空间位置小,连杆强度低,卸胎时须先卸鼓肩,致使劳动强度大,生产效率低,产品质量不稳定。
为解决这一问题,我公司研制出胶囊膨胀结构成型鼓,在实际生产应用中取得显著效果。
1 胶囊成型鼓结构与工作原理 胶囊成型鼓主要由导向盘、限位盘、胶囊和鼓条等组成,具体结构见图1。
其工作原理是:成型鼓直径的变化由胶囊(4)膨胀和收缩完成;限位盘(6)控制成型鼓最大直径;导向盘(5)限定缩合直径。
采用层贴法成型时,为了便于扣圈和内层帘图1 胶囊成型鼓结构图1—外胶圈;2—加强胶圈;3—鼓条;4—胶囊;5—导向盘;6—限位盘;7—通风管;8—轴连接管;9—圆柱头六角螺钉布反包操作,在成型鼓缩合状态下贴内层帘布后,往胶囊内通入压缩空气,胶囊开始膨胀,同时推动鼓条(3)沿鼓条导向盘滑动,至直径达到最大,胶囊不再膨胀。
然后进行扣圈和反包操作,再贴外层帘布和胎面,胎坯成型后,放出胶囊内压缩空作者简介:赵洪金(19632),男,辽宁北票人,辽宁轮胎集团有限责任公司工程师,从事轮胎结构设计工作。
福诺 轮胎 硫化隔离剂 胶囊隔离剂SBC-7086——技术简介

Fihonor胶囊隔离剂SBC-7086福诺技术简介SBC-7086是一种水性半永久性胶囊隔离剂,专为胶囊工作温度介于120到230℃的条件设计。
在120℃以上,SBC-7086可在胶囊表面形成一层附着力良好的保护膜;该膜具有高温润滑、多重脱模、耐磨等特性,而且能保护胶囊,延长胶囊使用寿命。
适用范围轮胎生产中,硫化胶囊与胎胚之间的隔离和润滑。
产品优点§固化速度适中,方便使用§无污染,易脱模§不含C.F.C.,对人体无害理化特性§外观--乳白色粘稠液体§不挥发物(%)--11~15%§粘度(25℃)-- 500~900cps §pH-- 4~8§储存期--6个月§保存--30℃以下保存使用方法1、根据现场情况,SBC-7086可兑水使用,只需将其与自来水按1:0.5~1:2混合,搅匀即可,建议现用现兑。
2、新胶囊在第一次使用之前,可使用本隔离剂进行预涂装,预涂可在胶囊装机之前和装机之后进行。
涂装方式可采用刷涂、蘸涂和喷涂的方式进行,涂装时应尽量保持胶囊处理张开状态,以便隔离剂能够均匀的覆盖在胶囊表面。
涂装完后可在室温下晾干不少于6小时或在65℃以上的模具环境中温模20分钟以上;温度越高,所需的温模时间越短。
3、在预涂结束后,正式硫化开始前,建议再涂装一遍隔离剂,并让胶囊收缩/膨胀2~3次,以使隔离剂充分覆盖胶囊的表面,同时加速水分的蒸发,防止有水存在引起的窝气。
待胶囊表面水分蒸发后,即可装模硫化。
新囊前三次使用,建议每次都涂装一遍隔离剂,使其能够快速在胶囊表面形成保护膜,以延长胶囊使用寿命。
4、后续硫化根据实际情况补刷隔离剂,并让胶囊收缩/膨胀2~3次,待胶囊表面水分蒸发后,再装模硫化。
5、胶囊使用前300次,每班只需涂刷1~2次隔离剂,300次之后视胶囊老化情况,可适当增加涂刷次数。
注意:隔离剂要涂装均匀适量,不要有漏涂的区域,以免影响隔离效果储存请勿存放于30℃以下阴凉干燥处。
轮胎定型硫化机胶囊炸裂安全防护控制浅谈

第46卷 第11期·40·作者简介:杨华(1976-),男,电气工程师,产品工程师,本科,主要从事双模定型硫化机的电气设计研发工作。
收稿日期:2019-12-05在轮胎定型硫化机的使用过程中,为保护人员和设备安全有很多安全要求和保护措施,其中一项很重要的安全要求和保护措施就是胶囊炸裂防护。
硫化胶囊(curing adle),是安装在轮胎硫化机上的空薄壁橡胶制品,用于装入待硫化的胎坯,用来承受由内压管路输送定型蒸汽(氮气)、高压蒸汽、氮气(过热水)等各种介质,给胎坯加温加压,实现轮胎硫化前的胎坯定型和轮胎的正硫化。
如果胶囊炸裂,胶囊碎片飞出,高温高压介质喷射而出,会直接危害操作维修人员人身生命安全,所以对胶囊炸裂的防护至关重要。
经过对该危险点的分析评估和长期的实践总结,得出胶囊炸裂的主要原因有以下几种:胶囊本身有薄弱部位;胶囊老化或使用时间过长;一次定型开始到二次定型前,胶囊压力过高(设定过高或介质失控);二次定型开始到合模闭锁启动硫化,胶囊压力过高(设定过高、合模挤压或介质失控);解锁开模胶囊压力超过开模安全压力;等料待机时,阀门密封老化、损坏等造成胶囊串气。
针对这些胶囊炸裂的原因,我们对应采取安全措施,实施安全防护,确保人身安全和设备安全。
1 胶囊本身有薄弱部位若存在薄弱部位的胶囊流入车间,安装到硫化机上,胶囊内介质随时都可能突破薄弱部位造成胶囊炸裂,一旦使用了这样的胶囊,就留下了安全隐患。
通过以下步骤,从采购源头到使用,排除安全隐患。
轮胎定型硫化机胶囊炸裂安全防护控制浅谈杨华,梁帅,张晓琳,周志伟(青岛双星橡塑机械有限公司,山东 青岛 266400)摘要:系统的论述了安装在轮胎定型硫化机上的胶囊,在使用时可能出现的胶囊炸裂的几种主要原因,以及针对这些主要原因对应采取的安全防护措施;电气控制原理和电气控制如何实现这些安全防护措施;以及出现超出安全标准时,报警灯报警,界面窗口弹出报警内容,提示维修人员维护等应对措施。
轮胎硫化胶囊隔离剂的成份

轮胎硫化胶囊隔离剂的成份引言轮胎硫化胶囊隔离剂是一种用于轮胎制造过程中的辅助材料。
它的主要作用是隔离轮胎硫化过程中产生的硫化气体,以防止气泡和气孔的形成,从而提高轮胎的质量和性能。
本文将详细介绍轮胎硫化胶囊隔离剂的成份,包括主要成份的功能和作用。
成份1. 胶粉胶粉是轮胎硫化胶囊隔离剂的主要成份之一。
它通常由天然橡胶、合成橡胶和其他辅助材料组成。
胶粉的主要功能是提供粘性和弹性,以便将其他成份牢固地粘合在一起。
胶粉还可以增加硫化胶囊的强度和耐久性。
2. 硫化剂硫化剂是轮胎硫化胶囊隔离剂中的关键成份之一。
它通常是一种含有硫的化合物,如硫黄。
硫化剂的主要作用是促进轮胎中橡胶的硫化反应,从而使橡胶变得更加坚固和耐用。
硫化剂还可以提高轮胎的热稳定性和抗老化能力。
3. 填充剂填充剂是轮胎硫化胶囊隔离剂中的另一个重要成份。
它通常由一种或多种无机材料组成,例如二氧化硅、炭黑等。
填充剂的主要作用是增加轮胎的硬度和强度,改善轮胎的耐磨性和抗撕裂性。
填充剂还可以调整轮胎的导热性和电导率。
4. 硫化促进剂硫化促进剂是轮胎硫化胶囊隔离剂中的一种辅助成份。
它通常是一种有机化合物,如二苯基二甲基二苯基硫脲(DPG)等。
硫化促进剂的主要作用是加速轮胎中橡胶的硫化反应,提高硫化速度和效率。
硫化促进剂还可以改善轮胎的硬度、弹性和耐磨性。
5. 抗氧化剂抗氧化剂是轮胎硫化胶囊隔离剂中的一种重要成份。
它通常是一种有机化合物,如二苯基二甲基二苯基硫脲(DPG)等。
抗氧化剂的主要作用是防止轮胎中橡胶的氧化反应,延长轮胎的使用寿命。
抗氧化剂还可以提高轮胎的耐候性和抗老化能力。
结论轮胎硫化胶囊隔离剂的成份包括胶粉、硫化剂、填充剂、硫化促进剂和抗氧化剂。
这些成份共同作用,可以提高轮胎的质量和性能,防止气泡和气孔的形成。
了解轮胎硫化胶囊隔离剂的成份对于轮胎制造过程中的质量控制和性能改进具有重要意义。
通过不断优化成份的配比和使用新型材料,可以进一步提高轮胎的质量和性能,满足不同车辆和道路条件的需求。
轮胎硫化胶囊寿命提升措施
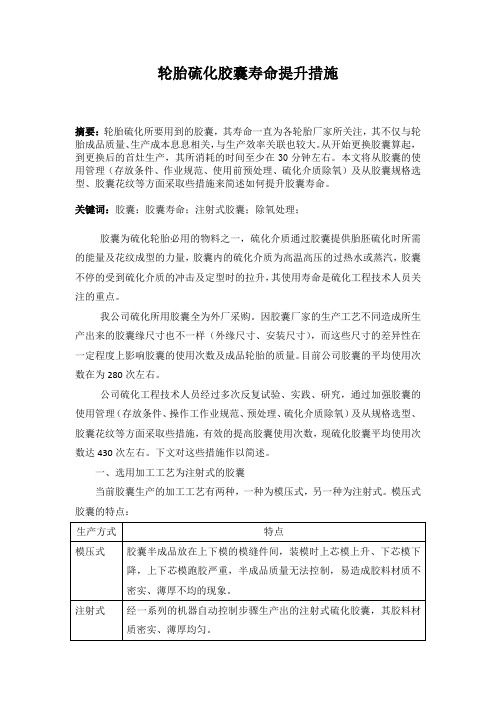
轮胎硫化胶囊寿命提升措施摘要:轮胎硫化所要用到的胶囊,其寿命一直为各轮胎厂家所关注,其不仅与轮胎成品质量、生产成本息息相关,与生产效率关联也较大。
从开始更换胶囊算起,到更换后的首灶生产,其所消耗的时间至少在30分钟左右。
本文将从胶囊的使用管理(存放条件、作业规范、使用前预处理、硫化介质除氧)及从胶囊规格选型、胶囊花纹等方面采取些措施来简述如何提升胶囊寿命。
关键词:胶囊;胶囊寿命;注射式胶囊;除氧处理;胶囊为硫化轮胎必用的物料之一,硫化介质通过胶囊提供胎胚硫化时所需的能量及花纹成型的力量,胶囊内的硫化介质为高温高压的过热水或蒸汽,胶囊不停的受到硫化介质的冲击及定型时的拉升,其使用寿命是硫化工程技术人员关注的重点。
我公司硫化所用胶囊全为外厂采购。
因胶囊厂家的生产工艺不同造成所生产出来的胶囊缘尺寸也不一样(外缘尺寸、安装尺寸),而这些尺寸的差异性在一定程度上影响胶囊的使用次数及成品轮胎的质量。
目前公司胶囊的平均使用次数在为280次左右。
公司硫化工程技术人员经过多次反复试验、实践、研究,通过加强胶囊的使用管理(存放条件、操作工作业规范、预处理、硫化介质除氧)及从规格选型、胶囊花纹等方面采取些措施,有效的提高胶囊使用次数,现硫化胶囊平均使用次数达430次左右。
下文对这些措施作以简述。
一、选用加工工艺为注射式的胶囊当前胶囊生产的加工工艺有两种,一种为模压式,另一种为注射式。
模压式胶囊的特点:选定一台双模硫化机其一边安装注射式胶囊、另一边安装模压式胶囊,硫化胶囊为同一厂家生产,其胶囊配方相同,经过工程技术人员硫化测温试验、胶囊使用次数记录对比,可得出:1、注射式胶囊较模压式胶囊传热要快,可缩短轮胎生产的硫化时间,从而提高产能、降低能耗,相关数据见表1。
表1 A13#硫化机注射式胶囊与模压式胶囊测温试验数据2、同时胶囊耐老化性能更优越,使用寿命长,比模压式硫化胶囊使用次数增加160次左右,相关数据见表2。
表2 A13#硫化机注射式硫化胶囊与模压式硫化胶囊使用次数数据二、选用合适规格的硫化胶囊胶囊厂家的不同,其胶囊规格尺寸(胶囊断面周长、外直径、夹缘高度等)存在一定差异,如何让胶囊外缘尺寸与成品轮胎规格尺寸、设备工装尺寸的吻合性最优,在胶囊选型时需考虑相关伸张值及胶囊尺寸。
不同类型轮胎胶囊隔离剂的应用对比

第 6 期霍占东等.不同类型轮胎胶囊隔离剂的应用对比375不同类型轮胎胶囊隔离剂的应用对比霍占东1,叶 强1,纪丽丽2,高利辉1,郭 洵1(1.陕西延长石油集团橡胶有限公司,陕西咸阳 712000;2.陕西延长石油西北橡胶有限责任公司,陕西咸阳 712000)摘要:试验研究不同类型轮胎胶囊隔离剂的应用性能。
结果表明:使用油性隔离剂易出现胎里胎趾圆角、缺胶、裂口、窝气等次品,喷涂后胶囊表面应充分晾干,并擦掉钢圈和夹具上的隔离剂,同时定期清理排气线和排气孔;使用干性隔离剂硫化的轮胎质量最高;喷涂周期为8锅(每次)时,喷涂油性隔离剂、水性隔离剂和干性隔离剂的胶囊可分别使用460,410和500次,干性隔离剂喷涂周期为16锅(每次)时,胶囊可使用460次;使用各类隔离剂时均应定期清理钢圈和夹具上的污垢。
关键词:轮胎;硫化胶囊;胶囊隔离剂;使用寿命中图分类号:U463.341;TQ330.38+7 文章编号:1006-8171(2019)06-0375-03文献标志码:B DOI:10.12135/j.issn.1006-8171.2019.06.0375胶囊隔离剂是在胎坯硫化前喷涂在硫化胶囊表面,起到胶囊与胎坯隔离作用的液体。
目前市场上较常见的胶囊隔离剂包括油性隔离剂、水性隔离剂和干性隔离剂。
水性隔离剂价格略高于油性隔离剂,干性隔离剂的价格最高。
其他如喷涂胎坯上的胶囊隔离剂、永久型隔离剂、有机硅隔离剂等目前应用较少。
本工作主要对油性隔离剂、水性隔离剂及干性隔离剂进行应用试验,分别从模具污染性、轮胎质量和胶囊寿命等方面进行对比分析。
1 实验1.1 试验材料轮胎硫化胶囊,型号RB12003L,天津市大津胶囊有限公司产品;SG-206油性隔离剂、SG-206A 水性隔离剂和SG-205干性隔离剂,三合源橡胶科技有限公司产品。
1.2 主要设备和仪器B型热板式双模硫化机,福建华橡自控技术股份有限公司产品,标识为1号、2号和3号,生产同规格同花纹12.00R20 Y601全钢载重子午线轮胎;专用喷壶3个;清洁干净的模具夹具和下钢圈。
半钢子午线轮胎硫化胶囊使用过程中异常损坏原因分析及解决措施

生产•技术2019年第17卷半钢子午线轮胎硫化胶囊使用过程中异常损坏原因分析及解决措施孙奇涛,姚秀红[倍耐力轮胎(焦作)有限公司,河南焦作454000]摘要:对半钢子午线轮胎硫化胶變在使用过程中出现的异常损坏进行原因分析,并提出相应的解决措施。
半钢子午 线轮胎硫化胶囊的异常损坏包括硫化机铜套夹坏胶囊、胶囊老化裂口、于冰侵蚀胶囊造成细孔等。
通过采取相应的解决措施,可以有效减少胶囊的异常损坏,延长胶囊的使用寿命。
关键词:半钢子午线轮胎;硫化;胶囊;异常损坏中图分类号:U463.341.4/.6;TQ336.1+5文献标志码:B半钢子午线轮胎硫化胶囊根据轮胎设计尺寸不同,可以分为很多种,不同种类硫化胶囊的使用次数也存在差异。
硫化胶囊在使用过程中经常出现异常损坏,造成胶囊提前报废,从而缩短了胶囊的使用寿命,并使硫化介质进入轮胎内部,造成轮胎欠硫或窝气等现象,导致成品轮胎没有达到最佳硫化状态,物理性能和安全性能下降,一经发现即被判为废品,这使得轮胎企业运行压力增大E。
半钢子午线轮胎硫化胶囊在使用过程中出现的异常损坏包括铜套夹坏胶囊、胶囊老化裂口、干冰侵蚀胶囊造成细孔、硫化机抽真空不良夹坏胶囊、胎坯钢丝刺出划伤胶囊等。
本工作根据我公司半钢子午线轮胎氮气硫化生产实际情况,对硫化胶囊在使用过程中出现的异常损坏进行原因分析,并提岀相应解决措施。
1铜套夹坏胶囊硫化机中心机构铜套夹坏胶囊是硫化胶囊损坏最多且最严重的问题,铜套夹裂口处均在胶囊内部,裂口处呈咬合状,如图1所示。
1.1原因分析(1)中心机构密封泄漏:硫化机开模后胶囊已作者简介:孙奇涛(1990-),男.黑龙江佳木斯人,倍耐力轮胎(焦作)有限公司工程师,学士.主要从事半钢子午线轮胎硫化工艺技术管理工作。
E mail:410089106@ 文章编号:2095-5448(2019)10-0586-03DOhlO.12137/j.issn.2095-5448.2019.10.0586图1铜套夹坏胶囊处于抽真空状态,中心机构密封泄漏会导致中心机构上环上窜,已抽真空的胶囊进入铜套结合处,通过卸胎机械手压下上环来卸胎,造成铜套夹坏胶囊。
轮胎硫化胶囊工艺

轮胎硫化胶囊工艺我要打印 IE收藏放入公文包我要留言查看留言来源:昆山模具网添加人:netlink 添加时间:2009-2-16 16:17:49我国是世界轮胎生产第一大国,目前,国内年产各种轮胎2亿条以上。
在现有轮胎厂中,除极少厂商(这些厂商的年总产量还不到国内轮胎总产量的十分之一)仍保留了部分水胎硫化外,几乎所有的厂商均采用胶囊定型硫化轮胎。
本文阐述了中国用于轮胎硫化生产的轮胎硫化胶囊的现状及市场发展趋势,并对中国现行轮胎硫化胶囊的几种生产工艺进行了简要对比。
轮胎硫化胶囊市场概况根据行业相关信息统计,目前国内各种轮胎胶囊总需求量约450万条左右,其中乘用轮胎硫化胶囊占总量的55%左右,载重轮胎硫化胶囊占总量的35%左右,其他(包括农用、工程轮胎硫化胶囊)占总量的10%左右。
总市场容量折合人民币约25亿元左右。
就市场生产供销来说,目前产品质量较好的胶囊市场供不应求,用户厂家先付款后交货的情形很平常,故大多数轮胎胶囊生产厂家效益较好。
在市场供应链上,国内的轮胎胶囊主要分进口和国内生产两大部分,其中国产胶囊占总需求量的75%左右,其余均为进口,进口的以生产高档乘用轮胎用和大型全钢子午线轮胎用的胶囊为主。
在国内,目前轮胎胶囊生产厂家主要有:山东大王金泰集团产品,以各种轮胎硫化胶囊和轮胎成型反包胶囊为主,年最大生产能力达30万条左右;山东西水集团永一橡胶有限公司,年生产各种轮胎胶囊15万条左右;天津大津胶囊厂,年生产各种轮胎胶囊30万条左右;南京胶囊厂,年生产各种胶囊15万条左右;江阴胶囊厂,年产各种胶囊15万条左右;另外还有其他一些轮胎厂自产。
发展趋势众所周知,轮胎行业是与汽车工业密切相关的国民经济重要支柱产业,目前国内外现有汽车的保有量每年都在随着世界经济水平的提高而增长,所以轮胎行业是个永远不会落幕的产业。
首先,我国已成为世界轮胎产量第一大国、消费大国、出口大国,随着轮胎生产技术的不断进步,各种乘用轮胎、载重轮胎、工程轮胎、农用轮胎的产量仍将会逐年递增。
- 1、下载文档前请自行甄别文档内容的完整性,平台不提供额外的编辑、内容补充、找答案等附加服务。
- 2、"仅部分预览"的文档,不可在线预览部分如存在完整性等问题,可反馈申请退款(可完整预览的文档不适用该条件!)。
- 3、如文档侵犯您的权益,请联系客服反馈,我们会尽快为您处理(人工客服工作时间:9:00-18:30)。
轮胎胶囊概述作者:刘帅轮胎硫化胶囊(后面简称胶囊)主要是轮胎硫化的一个工具。
材质为丁基橡胶。
相当于轮胎模具的内模。
胶囊根据硫化机、夹具不同,分为不同型号:斜交A型、斜交B型、斜交AB型、子午A型(成为RA)、子午B型(RB)和子午AB型(RAB)。
其作用主要在轮胎硫化过程中内部充压缩气、充氮气或充过热水等。
使其伸张,撑起轮胎胶胚形成内压硫化轮胎。
其优点为导热快,效率高,劳动强度低,操作简便。
胶囊在硫化轮胎时有一定的伸张比,一般径向伸张R=外胎胎里直径(DK)/胶囊原始状态直径(DB)。
斜交胎B型胶囊径向伸张取值为1.6-1.85,斜交胎A 型与B型伸张比相似。
子午胎取值为1.10-1.15,允许值为1.05-1.20。
在胶囊和轮胎的选型时除了胶囊直径外还有一个重要条件需要注意就是胶囊断面周长。
胶囊断面周长伸张L=外胎断面内轮廓周长/胶囊断面周长。
胶囊的断面周长伸张应尽可能小,与轮胎内轮廓的伸张不应超过20%,一般轻型载重轮胎B型胶囊的断面周长为1.08-1.15%。
重型轮胎断面周长伸张值为1.02-1.04,A型胶囊断面周长伸张值较大,斜交、子午胎均为1.1-1.15左右。
胶囊是反复伸张的工作条件。
所以使用寿命除了高伸张也受到高温和耐氧化情况,即轮胎公司过热水的除氧情况。
这个是有具体指标规定的。
一般为过热水氧指数含量不超过0.05PPm(氮气硫化除外)。
一.轮胎硫化胶囊配方思路胶囊使用温度一般为180-200度。
接触的介质主要是过热水,过热蒸汽,压缩空气或者氮气。
胶囊伸张比很大尤其是斜交类型的胶囊。
所说义针对以上我们胶囊配方设计思路为耐高温,高伸张,耐氧化,高伸张后的还原性即扯断永久变形。
思路分析为:高温达不到就是直接导致硫化胶囊的使用寿命折损。
伸张和扯断永久变形是想关联考虑的,伸张太低有损使用寿命。
伸张太高由于应力松弛回原性下降,所以在保证扯断伸长率的前提下也要保证含胶率,交联密度和胶料的强度。
如果胶囊伸张以后不能很快的恢复可能造成胶囊打折现象。
所以胶囊就是针对耐高温,高强度,高伸张,低扯断永久变形考虑设计。
1.生胶的选择国内胶囊公司大都采用不饱和度1.5%-2%之间的丁基橡胶。
大多数公司采用拜耳,埃克森或者JSR的268或者301牌号丁基。
但是人们往往有一个误区,认为是一个牌号的丁基橡胶其性能是相同的,其他的一些指标也是一样的。
其实不然,拜耳、埃克森的268牌号丁基是门尼粘度71-80,非污染型橡胶。
JSR 公司的268则是门尼粘度41-50,非污染型橡胶。
JSR所对应的拜耳、埃克森的牌号则是265型。
但是国内丁基硫化胶囊的生产厂家都是采用三个厂家的268进行同一个工艺的操作。
俄罗斯生产的1675和国内燕化的1751牌号丁基属于是不饱和度1.6%-2%的橡胶,是属于门尼粘度75的污染型橡胶。
市场的价格国内和俄罗斯的丁基比其他国家的便宜近一万左右,有的时候价格相差更是离谱。
国内的丁基橡胶原来出现不稳定现象但现在我国的丁基橡胶的稳定性已经提高。
其物理性能和其他国家的丁基也几乎持平。
我认为完全可以用国内丁基代替或部分代替国内丁基生产胶囊,以降低成本。
2.轮胎硫化胶囊的硫化体系丁基一般采用硫磺,醌钨或者树脂硫化。
但是鉴于使用条件一般采用树脂硫化。
硫化树脂一般为酚醛树脂,不得不提到酚醛树脂临位羟甲基含量对酚醛树脂硫化性能有很大影响。
当羟甲基含量小于%时,酚醛树脂缺乏交联能力,不能进行硫化,胶料一直出于未硫化状态。
只有当临位羟甲基含量达6%以上时,它才具有正常的交联能力。
树脂硫化丁基常用树脂有:对叔丁基酚醛树脂,含羟甲基8~11%,如2402树脂,101B树脂等;对叔辛基酚醛树脂。
如Amberol ST-137、SP-1045等;烷基酚醛树脂,如R17152等;酚醛树脂2123;溴甲基对叔丁基酚醛树脂,如SP-1055, SP-1056、溴化酚醛树脂201等;2,6-羟二甲基-4-氯苯酚树脂,如YDO等。
介于2402树脂硫化速度缓慢大都采用对叔辛基酚醛树脂,或溴甲基对叔丁基酚醛树脂。
试验证明溴甲基对叔丁基酚醛树脂硫化速度最快,对辛基酚醛树脂其次。
溴化酚醛树脂不但可以快速硫化,且硫化胶物性好,老化后硬度变化也小。
试验表明溴化酚醛树脂用量为4~12份范围内,丁基橡胶硫化胶性能随树脂用量增加而变化:硫化速度加快,硫化胶硬度和定伸应力增大,扯断伸长率降低。
树脂用量超过8份时,对上述性能影响不大,一般为8份为好。
树脂硫化我没见过什么高效促进剂,但是一般都要加卤化物来提高活性。
一般的活性剂一般为:金属氯化物,如氯化亚锡、氯化铁,一般用量为1.5~2.5份;含卤聚合物,如氯丁橡胶、氯磺化聚乙烯、聚氯乙烯、溴化丁基橡胶等,一般用量为5~10份。
鉴于金属氯化物会降低较量耐焦烧时间,胶料易粘棍,分散不均,且腐蚀辊筒所以一般不予使用。
丁基老化属于分子降解,变软而CR老化产生结构性变硬。
介于两个胶种的特性大都采用加CR当做胶囊的活化剂以提高硫化速度并改善丁基的老化性能。
3.补强体系因为丁基橡胶为结晶型橡胶,生胶本身即有较高的强度,补强剂对其效果不大,而且往往会降低其扯断伸长率,但能提高撕裂强度、定伸应力。
丁基橡胶为饱和橡胶,大分子链中双键较少,补强剂和填充剂难以获得理想的补强效果。
因为聚合物与补强剂之间的补强作用,通常时在聚合物分子链带双键和补强剂表面完成的。
因此,补强剂的表面性质和结构状况对于丁基橡胶就显得格外重要。
试验表明如果炭黑表面含有足够的氧,则对丁基橡胶补强作用就大;如果炭黑表面没有足够的氧,则硫化胶性能就差。
此时,可通过使用化学处理剂,如:聚亚硝基苯等代替填充剂便面的氧来完成填充剂与聚合物之间的补强结合。
炭黑是丁基橡胶的主要补强剂。
其补强作用决定于炭黑的粒径、结构和表面或定三个主要参数。
炉法炭黑粒径为20—90nm,其排列顺序为SAF<ISAF<CF<HAF<FF<FEF<GPE<SRF。
热烈法炭黑粒径最大FT为170nm,MT为375nm。
按结构可分吸油值分高、中、低三类。
高结构有:CF,FEF,GPF,HAF,ISAF;中结构的有:SAF,ISAF,HAF,SRF,CC,MPC,EPC,FT,MT同种结构也有高低。
炭黑在50份以后随份数增加拉伸强度下降,且以细粒子炭黑较为显著。
定伸应力随炭黑会两增加而提高,三热烈法炭黑几乎不增加。
伸长率降低。
硬度随增加提高。
弹性随增加下降。
压缩永久变形随增加变差,尤其以超耐磨为甚,但粗热烈法炭黑则增加不大。
撕裂强度因超耐磨、中超耐磨、高耐磨增加降低,其他炭黑增加会提高。
国内胶囊一般都采用N220或者N330作为补强剂,以提高强度、撕裂强度等数值。
但是往往出现N220和N330牌号炭黑分散性的质疑,N220混炼过程中生热大,不利于胶囊的焦烧时间和流动性,伸长率偏低。
N330牌号炭黑强度略低,混炼胶断面分层,加完树脂冷却后胶片断面有蜂窝状密闭的微小气孔。
在长期的工业原料的发展,炭黑已经有了很多的更新产品,如高结构炭黑,低结构炭黑,新工艺炭黑等,对于胶囊我认为高结构炭黑为宜。
因为从微观说结构提高聚集体形态复杂,枝杈多,与橡胶混合后的吸硫橡胶多,吸硫橡胶的形成对提高在混炼胶的分散性有提高,可以改善压出等操作性,使压出口型膨胀收缩率减小,半成本挺性大,表面光滑,胶片断面无蜂窝状密闭气孔。
有利于硫化时胶囊的憋气,气泡等问题的解决。
对于强度和伸长率如图:炭黑型号硬度绍尔A 扯断伸长率% 强度,Mpa 300%定伸N347 61 523 17.7 3.9N339 60 518 17.5 3.38N330 60 467 14.3 4.13注:本配方硫化时间为170度*60min,炭黑用量为40份。
通过上述数据可以看出高结构炭黑的强度和扯断伸长率都有比普通炭黑好。
有利于胶囊产品的物性指标。
一些外企或者大型规模的胶囊公司已经采用高结构炭黑生产胶囊。
实际的使用次数和稳定性也确实有所提高。
考虑到强度控制一般使用细粒子炉法炭黑,用量在50份下随份数的增加硫化胶的强度增大,硬度增加,伸长率下降。
当50份以上时随添加份数的增加硬度增加其强度下降,扯断伸长率下降。
看下表:炭黑份数硬度绍尔A 扯断伸长率% 强度,MPa 300%定伸40 60 467 14.3 4.1350 65 432 18.3 4.5260 69 406 16.5 5.0470 76 382 15.1 5.36注;硫化时间为170*60min,炭黑为N330型号。
在实际的配方设计时要根据胶囊伸长,强度等条件寻找适合胶囊使用所对应的份数关系。
很多公司标准定位强度大于13Mpa,伸长大于等于700%,扯断永久变形小于16。
但是有的一些公司采用加一些乙炔炭黑来增加导热性。
但是会影响一些强度。
所以标准又为强度大于等于10Mpa。
伸长大于等于750%。
扯断永久变形为小于20。
通过上面的实验数据显示只是生胶用炭黑的补强伸长率明显不会达标。
所以我们就考虑软化体系的配合。
在丁基橡胶中软化增塑体系的主要作用是改善工艺性能、低温定能和动态性能,提高伸长率,并降低成本。
但同时也会降低强度和耐磨性等性能。
适用于丁基橡胶的是低极性、高饱和度增塑剂,高不饱和的油会严重影响其硫化速度,避免使用。
与丁基橡胶相容性好的增塑剂常有4类:石油系增塑剂;煤焦油系增塑剂;蜡类增塑剂,和脂类增塑剂。
芳烃含量好的操作油对丁基橡胶性能会产生不良影响,不宜使用。
石油系操作油是丁基橡胶中主要的增塑剂之一,能降低胶料门尼黏度,对压出行能略有改善,改善低温性能。
但对硫化胶的耐臭氧性、耐热性和压缩变形以及力学性能均有不利影响。
虽然石蜡油相容性比较好。
但是分子链较长,粘度较大。
对于伸长率没有明显的作用。
所以更多的公司把软化剂选择了低分子的植物系软化剂(蓖麻油)上。
蓖麻油分子量比较低,较利于加工性,扯断伸长率,胶料的流动性等,但时会比石蜡油更多的影响丁基的强度、扯断伸长率。
但是由于分子量比较低在高温度中容易迁移,所以耐老化性下降。
如图:软化剂种类硬度绍尔A 扯断伸长率% 强度,MPa 300%定伸; k$ ~0 O/ n" ^. |/ a蓖麻油67 746 13.6 5.07高分子石蜡油66 622 16.8 7.46180*24h老化后硬度变化绍尔A 扯断伸长变化率% 强度变化率% 300定伸变化率%蓖麻油+15 -46% -25% +56%高分子石蜡油+16 -37% -27% +32%注:硫化时间为170*60min。
在保证胶囊的物理性能的条件下做合理的配合体系。
对于软化体系除了蓖麻油我也看好石蜡油(分子量低一些的牌号)但是本人由于一些原因并没有试验。
只是想法供大家参考。
对于老化性,胶料的流动性,强度,伸长等做到平衡就时一个优秀的胶囊补强软化体系了。