塑料模具设计规范
塑料模具设计规范(繁体版)
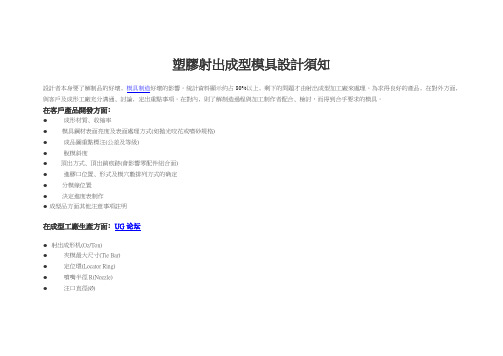
塑膠射出成型模具設計頇知設計者本身要了解制品的好壞﹐模具制造好壞的影響。
統計資料顯示約占80%以上﹐剩下的問題才由射出成型加工廠來處理。
為求得良好的產品﹐在對外方面﹐與客戶及成形工廠充分溝通﹑討論﹐定出重點事項。
在對內﹐則了解制造過程與加工制作者配合﹑檢討,而得到合乎要求的模具。
在客戶產品開發方面﹕●成形材質﹑收縮率● 模具鋼材表面亮度及表面處理方式(如拋光咬花或噴砂規格)●成品圖重點標注(公差及等級)●脫模斜度●頂出方式﹑頂出銷痕跡(會影響零配件組合面)●進膠口位置﹑形式及模穴數排列方式的确定● 分模線位置● 決定進度表制作●成型品方面其他注意事項註明在成型工廠生產方面﹕UG论坛●射出成形机(Oz/Ton)●夾模最大尺寸(Tie Bar)●定位環(Locator Ring)●噴嘴半徑R(Nozzle)●注口直徑(Ø)●模具最小與最大厚度●頂出孔(Ø)●提供流道形式﹑澆口形式﹑頂出方式等資料。
●冷卻方式(水嘴形式)●射出成形生產方面其他註經過上述討論﹑溝通之后﹐再將所得資料帶回﹐和制造加工單位檢討模具設計內容﹐滿足需求。
列出要具制造加工進度表以供追查UG模具設計之程序說明﹕●模穴布局●公母模分模面方向決定●模具及成品尺寸公差●使用鋼材選定●流道﹑澆口﹑頂出位置●冷卻水路方式●低陷處理(Under-cut)●成品頂出方式(如頂出中板﹑套筒頂出)●開模順序﹑距离(Stroke)● 省時﹑省事的方向﹐考慮公模仁(Core Insert)母模仁(Cavity Insert)的鑲嵌模具加工方式●其他如模溫控制﹑冰凍水冷卻等。
塑料模具设计方案

塑料模具设计方案一、背景介绍在现代工业生产中,塑料制品的应用越来越广泛。
而塑料制品的生产离不开塑料模具的设计与制造。
本文将针对塑料模具的设计方案进行详细介绍。
二、需求分析在开始设计塑料模具之前,我们需要对项目需求进行详细的分析。
这包括产品形状、尺寸、材料以及生产要求等。
1. 产品形状根据产品的形状,我们可以确定模具的结构类型。
常见的模具结构包括单腔模具、多腔模具、嵌件模具等。
2. 产品尺寸对于产品尺寸的要求,我们需要考虑到产品的公差范围和精度要求。
根据尺寸要求,我们可以确定模具的材料及加工方式。
3. 材料选择根据生产批量和产品要求,我们可以选择合适的模具材料。
常见的模具材料包括模具钢、铝合金等。
不同的材料具有不同的强度和耐磨性能。
4. 生产要求根据客户的要求,我们需要考虑到生产效率、模具寿命以及产品表面质量等因素。
这将直接影响到模具的设计和制造过程。
三、塑料模具设计流程根据需求分析阶段的结果,我们可以进行具体的模具设计。
塑料模具设计一般包括以下几个步骤:1. 产品设计在模具设计之前,我们需要通过CAD等设计软件完成产品的三维模型设计。
这将作为模具设计的基础。
2. 模具结构设计根据产品的形状和尺寸要求,我们可以确定模具的结构。
这包括模具腔体、模具芯、模具副以及模具附件的设计和安装。
3. 模具零件设计根据模具结构设计,我们可以开始设计各个模具零件的具体形状和尺寸。
这包括模具腔体、模具芯、滑块、顶针等零部件。
4. 模具注塑系统设计模具注塑系统是模具设计的重要组成部分。
我们需要考虑到注塑机的规格、熔融物料的流动性以及产品的冷却周期等因素。
5. 模具闭合系统设计模具闭合系统包括模具的开合、顶出及脱模等功能。
我们需要确保模具的闭合性能和稳定性,以及产品的顶出和脱模效果。
四、模具制造与试模在完成设计方案后,我们可以进行模具的制造和试模。
这包括以下几个步骤:1. 材料采购与加工根据设计方案,我们需要采购合适的模具材料,并进行相应的加工和热处理。
百度设计规范

百度设计规范篇一:设计规范塑料设计规范塑料产品设计需要关注以下几点:1、模具制作。
设计出来的产品模具也要能做的出来,而且在满足产品性能的情况下,尽量设计模具结构简单的产品。
2、材料。
设计产品要了解产品的使用位置、使用要求,确定其性能,根据性能要求选择合适的材料。
3、配合间隙。
产品设计完成后,要与其对插端做理论对插,确保配合间隙。
4、产品变形。
设计产品要考虑产品容易变形的地方。
在确保产品性能的情况下,在易变形位置做上加强筋之类的东西,减小变形量。
5、壁厚均匀。
塑料产品尽量做到壁厚均匀。
壁太薄容易出现注不满等情况,太厚容易出现缩坑等情况。
6、绘制产品图。
产品图尺寸标注要全面,配合尺寸公差标注清楚。
技术要求完整且简单明了。
模具设计要关注以下几点:1、模具结构。
接到产品后先考虑此类产品用哪种结构最适用。
易于加工,便于装配,实用于生产。
2、产品收缩率。
◎设计塑料模时,确定了模具结构之后即可对模具的各部分进行详细设计,即确定各模板和零件的尺寸,模腔和模芯尺寸等,这时将涉及有关材料收缩率等主要的设计参数,因而只有具体地掌握成形塑料的收缩率才能确定型腔各部分的尺寸,即使所选模具结构正确..但所用参数不当,就不可能生产出质量合格的塑件。
◎塑料收缩率及其影响因素,热塑性塑料的特性是在加热后膨胀..冷却后收缩..当然加压以后体积也将缩小,在注塑成形过程中..首先将熔融塑料注射入模具型腔内..充填结束后熔料冷却固化..从模具中取出塑件时即出现收缩..此收缩称为成形收缩,塑件从模具取出到稳定这一段时间内,尺寸仍会出现微小的变化..一种变化是继续收缩,此收缩称为后收缩,另一种变化是某些吸湿性塑料因吸湿而出现膨胀,例如尼龙料吸湿后尺寸会放大2-3%,但其中起主要作用的是成形收缩,目前确定各种塑料收缩率(成形收缩+后收缩)的方法。
一般都推荐德国家标准中DIN16901的规定。
即以23℃±0.1℃时模具型腔尺寸与成形后放置24小时..在温度为23℃..相对湿度为50±5%条件下测量出的相应塑件尺寸之差算出。
塑料模具结构设计规范

蘇州大智資訊配件有限公司結構設計規範中、小組:1 、模仁大小:①模仁長寬:產品一舨離模仁邊界15-20mm,如圖:⏹②模仁厚度:根據產品長寬的比例、高度來定,一般為公模仁30mm左右母模仁25mm左右⏹③模仁四周要倒C角2.02、模仁基準:根據CAD組立圖擺放位置公模側基準在右下角母模側基準在左下角3、模仁螺絲① M6:螺絲中心到模仁邊界為8mm② M8:螺絲中心到模仁邊界為10mm③ M10:螺絲中心到模仁邊界為12mm④螺絲都鎖在四個角落,一般為4顆或6顆,如圖:⑤螺絲一般是從模仁鎖到模板,如上圖4、頂針排佈要求:⏹①儘量用大支的同種規格的頂針;⏹②排佈要均勻,能使產品平衡頂針;⏹③在避免薄鐵的情況下,頂針儘量排在產品的邊界;⏹④有Rib的地方,要排頂針,且頂針邊界與Rib邊界之間的距離要有1.00mm左右,以防薄鐵的出現。
5、水路排佈有兩種:一種走模板,一種走模仁. 要求:⏹①當走模板時,水路直徑貫穿就可以,但要注意避免與頂針螺絲干涉,以防破水路;⏹②當走模仁時,先通模板,再通模仁。
模板與模仁旋接處用O型環封閉。
如下圖:⏹③O型環規格:當水路為PT 1/8時,用〝P-12〞O型環;當水路為PT 1/4時,用〝P-15〞O型環;⏹④每條水路都要有接頭沉孔;⏹⑤水路邊界與頂針、螺絲、EGP、RP、入子等邊界至少要有3mm,水路深度離成品至少要有6mm;⏹⑥水路盡良排在成品的地方和流道處。
6、常用斜梢規格:⑥斜梢行程計算7、常用滑塊規格:①外滑塊②內滑塊:8、定模架大小:①在不需要定位束塊、模仁壓塊、且無滑塊時:模架寬=模仁寬+100模架長=模仁長+(100~120)模架厚度:A、B、CA 為母模板,根據模仁的長寬高比例來定B 為公模板,根據模仁的長寬高比例來定C 為模腳=頂出行程+上下頂出板②不需要定位塊模仁壓塊但有滑塊時:模架寬=模仁寬+120以上模架長=模仁長+120以上模架厚度:A、B、CA、B、C 同上③需要定位束塊需要模仁壓塊無滑塊時模架寬=模仁寬+120模架長=模仁長+120模架厚度:A、B、CA、B、C 同上④不需要定位束塊需要模仁壓塊有滑塊時A、滑塊在天地側模架寬=模仁寬+(100~120)模架長=模仁長+120以上模架厚度同上B、滑塊在操作左右側模架寬=模仁寬+120以上模架長=模仁長+(100~120)模架厚度同上⏹⑤有定位束塊在左右側、沒有模仁壓塊,滑塊在天地側時:模架寬=模仁寬+(100~120)模架長=模仁長+120以上模架厚度同上⏹⑥有定位束塊又有模仁壓塊時模架寬=模仁寬+ 140以上模架長=模仁長+ 140以上模架厚度同上⑦不管有定位束塊或者有模仁束塊有定位束塊或者有模仁束塊的一側:模架(長寬)=模仁(長寬)+(100~120)有滑塊的一側:模架(長寬)=模仁(長寬)+120以上。
塑料水杯注塑模具设计

塑料水杯注塑模具设计注塑模具是生产塑料制品的重要工具之一,其设计质量直接影响到产品的成型质量与生产效率。
下面我们将介绍塑料水杯注塑模具的设计流程及注意事项。
一、注塑模具设计流程1.确定产品需求:首先要明确生产的水杯类型、规格和注塑机的型号等要求,确保模具设计符合产品的生产准则。
2.模具结构设计:根据产品的形状和尺寸等要求,选择合适的模具结构形式,包括单腔、多腔、分模等。
同时,还要考虑模具的易拆装性、冷却方式和导向方式等。
3.冷却系统设计:合理的冷却系统设计可以降低冷却时间,提高生产效率。
通过加入冷却水孔,将冷却水循环通过模具来降低塑料的温度,达到快速成型的目的。
4.注塑系统设计:包括模具的射嘴、喷嘴、合模机构和排胚系统的设计等,确保塑料能够顺利进入模腔并充分填充,同时也要避免出现短流、气孔等缺陷。
5.模具材料选择:根据注塑产品的要求和模具寿命的要求,选择合适的模具材料,如优质钢材、合金材料等。
6.模具加工制作:根据设计图纸进行模具的加工制作,包括数控加工、电火花加工等。
7.模具调试与试模:完成模具加工后,进行模具的调试与试模,确保模具的设计符合要求,以及检查模具的加工质量和装配情况。
8.模具使用与维护:模具使用后要进行定期的清洁和保养,确保模具的正常运行和寿命。
二、注塑模具设计的注意事项1.模具结构合理性:注塑模具的结构设计需要考虑到产品的形状、尺寸和功能等方面,尽量使用简单结构,减少模具制作成本和生产时间。
2.冷却系统设计合理性:冷却系统设计合理性直接影响到产品的成型质量和生产效率,需要根据产品的形状和材质选择合适的冷却方式和位置,充分利用冷却系统降低塑料温度。
3.模具材料选择合理性:模具材料的选择需要根据产品的要求和模具寿命的要求来确定,考虑到耐磨性、硬度、热传导性等因素。
4.模具加工精度:注塑模具的加工精度直接影响到产品的尺寸精度和表面质量,需要保证模具的加工精度,避免出现尺寸偏差或者表面缺陷。
塑胶模具的制作规范
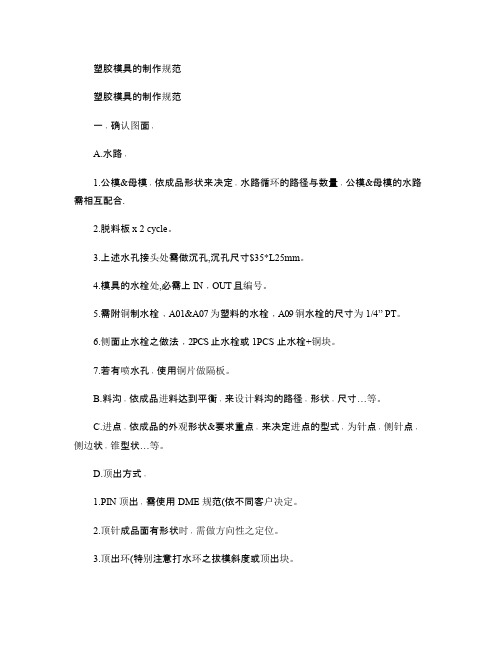
塑胶模具的制作规范塑胶模具的制作规范一﹐确认图面﹐A.水路﹐1.公模&母模﹐依成品形状来决定﹐水路循环的路径与数量﹐公模&母模的水路需相互配合.2.脱料板x2cycle。
3.上述水孔接头处需做沉孔,沉孔尺寸$35*L25mm。
4.模具的水栓处,必需上IN﹐OUT且编号。
5.需附铜制水栓﹐A01&A07为塑料的水栓﹐A09铜水栓的尺寸为1/4”PT。
6.侧面止水栓之做法﹐2PCS止水栓或1PCS止水栓+铜块。
7.若有喷水孔﹐使用铜片做隔板。
B.料沟﹐依成品进料达到平衡﹐来设计料沟的路径﹐形状﹐尺寸…等。
C.进点﹐依成品的外观形状&要求重点﹐来决定进点的型式﹐为针点﹐侧针点﹐侧边状﹐锥型状…等。
D.顶出方式﹐1.PIN顶出﹐需使用DME规范(依不同客户决定。
2.顶针成品面有形状时﹐需做方向性之定位。
3.顶出环(特别注意打水环之拔模斜度或顶出块。
E.定位块X4﹐于公母模板360度/4﹐加长方型之定位块﹐增加基准面之精度(材质:SKD-61中国塑料模具网F.模仁方式﹐1.锁公母模仁之螺丝﹐设计时愈多愈好﹐且需平均分配﹐使模仁与模座接触面更密合﹐锁螺丝时需封称锁入﹐且扭力一致。
2.公母模仁均须有卡入模座之定位梢。
3.所有insert之模仁形状为圆形时需做定位﹐且只能单方向组装﹐避免组装时方向错误。
G.4支导柱需有1pcs做偏心﹐X﹐Y轴各偏10mm。
H.模具的螺丝孔及螺丝﹐须为DME的公制规范。
I.回位销封边要有耐顶板﹐材质为TDAC+氮化处理。
J.若有斜销及滑块﹐三面需加耐磨板﹐且必须有油槽(材质﹐TDAC+氮化处理。
K,需安装计数器﹐INSERT的型式(A09客户才需要。
L.模具的长﹐宽﹐高﹐定位环与KO孔﹐需配合客户的机台尺寸。
M.若为三板模﹐A09为外部开闭器﹐A为内部开闭器。
N,CHECK母模与脱料板间﹐分开的距离是否足够﹐机械手取出料头﹐考虑LGP 的长度&机台的最大行程。
注塑模具技术规范

注塑模具技术规范美的集团家用空调国内事业部发布注塑模具技术规范1、目的1。
1、规范美的国内空调注塑模具制作规范和验收标准。
1。
2、不断提高模具质量,确保模具正常生产, 生产出合格的注塑件产品。
1。
3、模具厂家必须按照此标准进行模具设计及制造,若模具设计及制造因不符合此标准而引起的模具质量问题,由模具厂家承担一切后果。
2、范围本标准规定了塑料制件的模具工艺性,统一塑料模具的设计、制作标准、验收标准.本标准适用于家用空调国内事业部。
3、规范性引用文件无4、术语和定义无5、模具分类根据模架尺寸将模具分为大、中、小三类。
5.1、模架尺寸6060以上称为大型模具;5.2、模架尺寸3030~6060之间为中型模具;5.3、模架尺寸3030以下为小型模具.6、模架选用6.1、优先选用标准模架。
6.2、若选用非标模架,应优先选用标准板厚。
6.3、大型非标模架,导柱直径不小于Φ60mm,导套采用石墨铜套制做。
6.4、大型非标模架导套孔壁厚与模架边不得小于20mm,回针孔壁厚与模架边为35~40mm,回针直径不小于Φ30。
6.5、大型非标模架A板、B板起吊螺钉孔为M36~M48。
6.6、模架必须指定的供应商采购.6.6.1、模架非成型部分的模板零件应采用1050材质, 硬度HB170-220。
6。
6.2、导柱、导套回针等所用材料表面硬度不低于HRC60 2。
6。
6。
3、A板、B板镶件框壁厚一般为:(小模)30~50mm、(中模)50~80mm、(大模)80~120mm.6.6.4、开镶件框后B板厚度一般为:(小模)30~50mm、(中模)50~80mm、(大模)80~120mm。
6.6.5、镶件成型部位厚度一般为:(小模)25~35mm、(中模)35~50mm、(大模)50~70mm。
7、钢材选用7。
4、以下材料由模具厂家提供材料证明及采购证明。
滑块材料(外观)用738H钢料,硬度 HRC34~38,(非外观)用738钢料,硬度 HRC29~33. 斜顶材料用LKM738钢料,表面进行氮化处理,硬度HV700。
塑料模具设计与制作要求
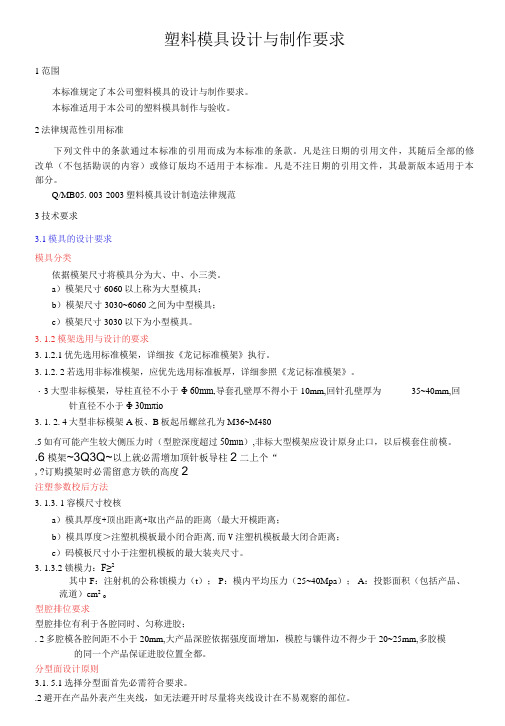
塑料模具设计与制作要求1范围本标准规定了本公司塑料模具的设计与制作要求。
本标准适用于本公司的塑料模具制作与验收。
2法律规范性引用标准下列文件中的条款通过本标准的引用而成为本标准的条款。
凡是注日期的引用文件,其随后全部的修改单(不包括勘误的内容)或修订版均不适用于本标准。
凡是不注日期的引用文件,其最新版本适用于本部分。
Q/MB05. 003-2003塑料模具设计制造法律规范3技术要求3.1模具的设计要求模具分类依据模架尺寸将模具分为大、中、小三类。
a)模架尺寸6060以上称为大型模具;b)模架尺寸3030~6060之间为中型模具;c)模架尺寸3030以下为小型模具。
3. 1.2模架选用与设计的要求3. 1.2.1优先选用标准模架,详细按《龙记标准模架》执行。
3. 1.2. 2若选用非标准模架,应优先选用标准板厚,详细参照《龙记标准模架》。
・3大型非标模架,导柱直径不小于Φ 60mm,导套孔壁厚不得小于10mm,回针孔壁厚为35~40mm,回针直径不小于Φ 30mπio3. 1. 2. 4大型非标模架A板、B板起吊螺丝孔为M36~M480.5如有可能产生较大侧压力时(型腔深度超过50mιn),非标大型模架应设计原身止口,以后模套住前模。
.6模架~3Q3Q~以上就必需增加顶针板导柱2二上个“,?订购摸架时必需留意方铁的高度2注塑参数校后方法3. 1.3. 1容模尺寸校核a)模具厚度+顶出距离+取出产品的距离〈最大开模距离;b)模具厚度>注塑机模板最小闭合距离,而V注塑机模板最大闭合距离;c)码模板尺寸小于注塑机模板的最大装夹尺寸。
3. 1.3.2 锁模力:F≥2其中F:注射机的公称锁模力(t); P:模内平均压力(25~40Mpa); A:投影面积(包括产品、流道)cm2o型腔排位要求型腔排位有利于各腔同时、匀称进胶;. 2多腔模各腔间距不小于20mm,大产品深腔依据强度面增加,模腔与镶件边不得少于20~25mm,多胶模的同一个产品保证进胶位置全都。
塑料制品的设计规范
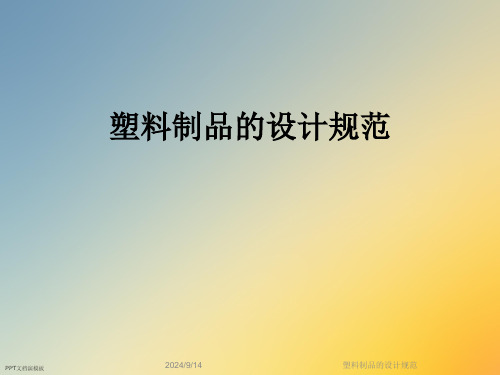
的充模流动阻力。如图3-13 ⑵应避免或减少塑料的局部集中,
以防止产生凹陷和气泡。如图3-14 ⑶加强筋以设计矮一些多一些为好。 ⑷筋与筋的间隔距离应大于塑件的
壁厚。
PPT文档演模板
塑料制品的设计规范
3.4.5 增加刚性减少变形的其他措施
将薄壳状的塑件设计为球面, 拱曲面等, 可 以有效地增加刚性、减少变形。
PPT文档演模板
塑料制品的设计规范
3.4.3 加强筋及其它增强结构
为了提高塑件的强度和防止塑件翘曲变形, 常设计加强筋,如图筋的设置位置应沿塑料 充模流向,降低充模流动阻力. 见图3-12
加强筋的正确形状和尺寸比例如图3-15 所示。
PPT文档演模板
塑料制品的设计规范
3.4.4 加强筋的主要形式
PPT文档演模板
塑料制品的设计规范
3.2 尺寸精度与表面质量
3.2.1 尺寸精度 3.2.2 尺寸精度的确定 3.2.3 表面质量
PPT文档演模板
塑料制品的设计规范
3.2 尺寸精度与表面质量
3.2.1 尺寸精度 1、塑件尺寸概念
塑件尺寸——塑件的总体尺寸。 2.塑料制品总体尺寸受限制的主要 因素:
PPT文档演模板
塑料制品的设计规范
3.2 尺寸精度与表面质量
3.2.2 尺寸精度的确定
表3—1是模塑件尺寸公差国家标 准(GB/T 14486-1993), 表 3—2是常用塑料材料的公差等级选 用。
将表3—1和表3—2结合起来使
用, 先查表3—2, 根据模塑件的材料
品种及用要求选定塑件的尺寸精度
图3—6 可强制脱模的浅侧凹结构
a)(A-B)×100%/B≤5% b) (A-B)×100%/C≤5%
中国注塑模架标准最新规范

中国注塑模架标准最新规范一、概述注塑模具是塑料加工行业的关键组成部分,其标准化对于提高生产效率、降低成本、保证产品质量具有重要意义。
本规范旨在为模具设计、制造和使用提供统一的技术要求。
二、适用范围本规范适用于各类塑料注射成型模具的设计和制造,包括但不限于单色、双色、多色及特殊成型工艺的模具。
三、材料要求1. 模具材料应具有良好的硬度、耐磨性和抗腐蚀性,以适应不同的工作环境和成型要求。
2. 模具钢材应符合国家标准或行业标准,确保材料的一致性和可靠性。
四、设计要求1. 模具设计应考虑塑料流动性、冷却速度和收缩率等因素,确保成型件的尺寸精度和表面质量。
2. 模具结构应简洁合理,便于拆卸、清洗和维护。
五、制造工艺1. 模具制造应采用精密加工技术,确保模具的尺寸精度和表面光洁度。
2. 模具的关键部件应进行热处理,以提高其硬度和耐磨性。
六、装配与调试1. 模具装配应严格按照设计图纸进行,确保各部件的配合精度。
2. 模具调试应在实际生产条件下进行,以验证模具的成型能力和稳定性。
七、质量检验1. 模具在出厂前应进行全面的质量检验,包括尺寸精度、表面质量、材料性能等。
2. 检验结果应符合本规范的要求,并附有相应的检验报告。
八、维护与保养1. 模具在使用过程中应定期进行清洁和维护,以延长模具的使用寿命。
2. 发现模具有损坏或磨损时,应及时进行修复或更换。
九、安全与环保1. 模具设计和制造过程中应严格遵守国家安全生产法规,确保操作人员的安全。
2. 模具材料和制造过程中产生的废弃物应符合环保要求,进行妥善处理。
十、附录本规范附录包含模具设计和制造过程中常用的参考数据、计算公式和图例,供设计和制造人员参考。
以上规范为注塑模架设计和制造提供了一套完整的技术指导,有助于提升模具行业的整体水平和竞争力。
塑料模具流道设计标准

塑料模具流道设计标准塑料模具的流道设计十分重要,它直接影响到模具注塑过程中的温度控制、压力变化以及产品质量等方面。
以下是关于塑料模具流道设计的一些标准:一、流道宽度:在塑料模具的流道设计中,流道宽度一般应为2-4mm,以确保塑胶的流动性能良好。
如果流道宽度过大,将导致塑胶的流动速度过快,容易产生气泡和翘曲等缺陷;而如果流道宽度过小,会增加塑胶的流动阻力,导致注塑压力过高,还会产生热嵌痕等缺陷。
二、流道截面形状:流道的截面形状有圆形、矩形、梯形等多种选择,其中矩形和梯形常用于多孔板流道设计。
在流道截面形状设计中,需要考虑到塑胶流动的速度、流动的平稳性以及压力变化等因素。
一般来说,流道截面形状越宽越好,这样可以降低注塑时的压力损失,并减少塑胶的流动阻力,提高生产效率和产品质量。
三、流道长度:流道长度是指从注塑机喂料口到模具最远端的长度。
流道长度应根据具体的产品要求和注塑机的能力来决定。
一般来说,流道长度越短越好,可以减少塑胶的流动距离和时间,提高注塑效率和产品质量。
但是,流道长度过短也会导致注塑时的压力损失增加,可能会产生熔接痕等缺陷。
四、流道表面光洁度:流道的表面光洁度对于塑胶的流动性能和产品表面质量有着重要影响。
流道设计中,流道的表面应尽量保持光洁,并且不应有明显的凹凸或毛刺等缺陷。
这样可以减少塑胶在流动过程中的摩擦阻力,提高流动的平稳性,减少产品表面的瑕疵。
综上所述,塑料模具流道设计需要考虑流道宽度、流道截面形状、流道长度以及流道表面光洁度等因素。
通过合理的流道设计,可以提高塑料模具的注塑效率和产品质量,降低生产成本,符合相关的标准和要求。
注塑模具设计制作规范与验收标准表

模具名称:模穴数: 型腔表面处理:产品材料:签名:年月日浇口及模胚制作参考标准常见浇口尺寸基本设计原则推荐如下:1。
点浇口:2. 扇形浇口:3。
潜伏式浇口:4。
边缘浇口:5。
凸耳浇口:W = 浇口宽度 ( mm )A = 型腔表面积 ( mm2 )n = 材料常数 material constant0.6 for PE, PS0.7 for POM, PC, PP6. 重叠式浇口:模架尺寸选择参考标准一、 注塑类模具镶块式模具的模架与镶件大小的选择,可参考下面的数据:图4—146 模架尺寸的确定“A"—表示镶件侧边到模板侧边的距离; “B"—表示定模镶件底部到定模板底面的距离;“C ”—表示动模镶件底部到动模板底面的距离; “D ”—表示产品到镶件侧边的距离;W=w= 浇口宽度 [mm]A= 型腔表面积[ mm 2]n= 材料常数0.6 for PE, PS0.7 for POM, PC , PP 0。
8 for CA, PMMA , PA“E”—表示产品最高点到镶件底部的距离;“H”—表示动模支承板的厚度(当模架为A型时) “X”-表示产品高度。
以上数据,仅作为一般性结构塑件摸架参考,对于特珠的塑件应注意以下几点:①当产品高度过高时(产品高度X≥D),应适当加大“D",加大值ΔD=(X—D)/2;②有时为了冷却水道的需要对镶件的尺寸做以调整,以达到较好冷却效果;③结构复杂需做特殊分型或顶出机构,或有侧向分型结构需做滑块时,应根据不同情况适当调整镶件和模架的大小以及各摸板厚度,以保证模架的强度。
④垫块高度的确定:垫块的高度应保证足够的顶出行程,然后留出一定的余量(5—10mm),以保证完全顶出时,⑤模架整体结构的确定:在基本选定模架之后,应对模架整体结构进行校核,看所确定的模架是否合适所选定或客户给定的注塑机,包括模架外形的大小、厚度、最大开模行程、顶出方式和顶出行程等,最后模架的整体尺寸以5mm为单位(例如计算所得模架尺寸为:232mm*253mm*186mm,那么实际应该取:235mm*255mm*190mm)。
塑料模具设计方案
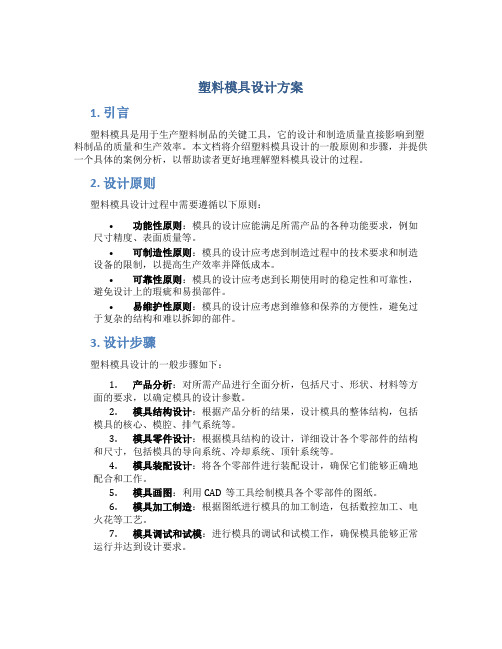
塑料模具设计方案1. 引言塑料模具是用于生产塑料制品的关键工具,它的设计和制造质量直接影响到塑料制品的质量和生产效率。
本文档将介绍塑料模具设计的一般原则和步骤,并提供一个具体的案例分析,以帮助读者更好地理解塑料模具设计的过程。
2. 设计原则塑料模具设计过程中需要遵循以下原则:•功能性原则:模具的设计应能满足所需产品的各种功能要求,例如尺寸精度、表面质量等。
•可制造性原则:模具的设计应考虑到制造过程中的技术要求和制造设备的限制,以提高生产效率并降低成本。
•可靠性原则:模具的设计应考虑到长期使用时的稳定性和可靠性,避免设计上的瑕疵和易损部件。
•易维护性原则:模具的设计应考虑到维修和保养的方便性,避免过于复杂的结构和难以拆卸的部件。
3. 设计步骤塑料模具设计的一般步骤如下:1.产品分析:对所需产品进行全面分析,包括尺寸、形状、材料等方面的要求,以确定模具的设计参数。
2.模具结构设计:根据产品分析的结果,设计模具的整体结构,包括模具的核心、模腔、排气系统等。
3.模具零件设计:根据模具结构的设计,详细设计各个零部件的结构和尺寸,包括模具的导向系统、冷却系统、顶针系统等。
4.模具装配设计:将各个零部件进行装配设计,确保它们能够正确地配合和工作。
5.模具画图:利用CAD等工具绘制模具各个零部件的图纸。
6.模具加工制造:根据图纸进行模具的加工制造,包括数控加工、电火花等工艺。
7.模具调试和试模:进行模具的调试和试模工作,确保模具能够正常运行并达到设计要求。
4. 案例分析以下是一个具体的塑料模具设计方案的案例分析:产品介绍:设计一款塑料杯子,杯子尺寸为直径80mm,高度100mm,材料为食品级聚丙烯。
模具设计参数: - 轮廓尺寸:根据产品尺寸确定模腔和模芯的轮廓尺寸。
- 分型面位置:确定模具分型面的位置,以便顺利取出制品。
- 排气系统:设计一个合适的排气系统,以避免在注塑过程中产生气泡。
- 冷却系统:设计一个有效的冷却系统,以提高生产效率。
塑料模具设计规范
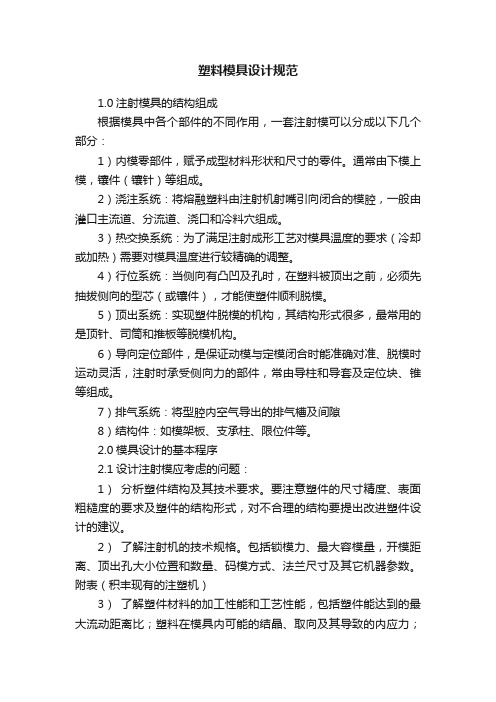
塑料模具设计规范1.0注射模具的结构组成根据模具中各个部件的不同作用,一套注射模可以分成以下几个部分:1)内模零部件,赋予成型材料形状和尺寸的零件。
通常由下模上模,镶件(镶针)等组成。
2)浇注系统:将熔融塑料由注射机射嘴引向闭合的模腔,一般由灌口主流道、分流道、浇口和冷料穴组成。
3)热交换系统:为了满足注射成形工艺对模具温度的要求(冷却或加热)需要对模具温度进行较精确的调整。
4)行位系统:当侧向有凸凹及孔时,在塑料被顶出之前,必须先抽拔侧向的型芯(或镶件),才能使塑件顺利脱模。
5)顶出系统:实现塑件脱模的机构,其结构形式很多,最常用的是顶针、司筒和推板等脱模机构。
6)导向定位部件,是保证动模与定模闭合时能准确对准、脱模时运动灵活,注射时承受侧向力的部件,常由导柱和导套及定位块、锥等组成。
7)排气系统:将型腔内空气导出的排气槽及间隙8)结构件:如模架板、支承柱、限位件等。
2.0模具设计的基本程序2.1设计注射模应考虑的问题:1)分析塑件结构及其技术要求。
要注意塑件的尺寸精度、表面粗糙度的要求及塑件的结构形式,对不合理的结构要提出改进塑件设计的建议。
2)了解注射机的技术规格。
包括锁模力、最大容模量,开模距离、顶出孔大小位置和数量、码模方式、法兰尺寸及其它机器参数。
附表(积丰现有的注塑机)3)了解塑件材料的加工性能和工艺性能,包括塑件能达到的最大流动距离比;塑料在模具内可能的结晶、取向及其导致的内应力;塑料的冷却收缩和补缩;塑料对模具温度的要求等。
4)了解特殊技术要求。
5)考虑模具的结构和制造,包括选择分型面和型腔的布置及进料点;模具的强度、刚度和模腔尺寸精度;行位机构和顶出系统;模具零件的制造方法及制造的科学性可行性及经济性;装拆的工艺性;必要的辅助工具的设计等。
6)考虑模具材料的选择,包括材料的机械、工艺性能及热处理要求,材料胚料的大小。
7)考虑模具的成型效率,合理的设置运水。
3.0模具设计的一般流程1)1.模具确认表-总指标:交货期,模具寿命。
塑胶模具设计准GB
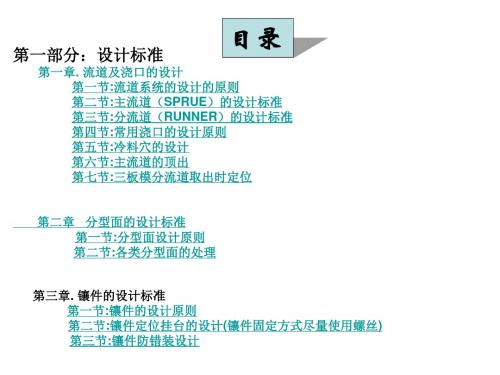
2.对于多品多穴采用非平衡式分流道和进胶口,应依照流动的距离调整水口或流道的 大小,以确保尽可能各腔填充同步。
3.为减少热量及压力损失,流道应尽量短、直,且转角处须加R角保证流动顺畅。流 道表面须用600#以上沙纸省光,如果部品品是镜面,流道须用1000#沙纸省光。
差应提交客户确认;
3、模板间距考虑:分模面的确定要保证母、公模开模行程最短;
4、应尽量避免侧抽芯机构,若无法避免侧抽芯,应使抽芯尽量短,并尽量使滑块全
部出在公模;
5、由于斜滑块合模时锁紧力较小,对于投影面积较大的大型塑件,可将塑件投影面
积大的分模面放在公母模合模的主平面上,而将投影面积较小的分模面作为侧向分模
第一章. 模架的设计
第一节、撑头 第二节、小水口的开模控制机构 第三节、中托司及中托边 第四节、顶针复位开关 第五节、锁模扣 第六节、上 下固定板高度 第七节、定位块 第八节、导柱 导套排气 第九节、模架常用标准件的选择 第十节、模架板吊环螺丝孔的规定
第二章.标准件
第一节:内部自制标准件的选择
第二节:螺丝、顶针等相关标准件数据速查表
目录
三、分流道(RUNNER)的设计标准
1.流道类型
(1).圆形流道 D
(2).U形流道 20°
H=D
D
2.D的系列值:2 2.5 3 3.5 4 4.5 5 6 7 8 (10 12参考使用)
3.D的取值方式:
对于PE、PA等材料,D值可取小值,对于PC、PMMA等材料,D值可取大值。
目录
(2).经验估算
注塑机吨位(TON) ﹤130 ﹤350 350吨以上
塑胶模具设计规范

塑胶模具设计规范模具设计规范(此规范主要应用于手机模具)一、模具排位1、根据产品大小、结构、产量、精密程度、材料或客户要求等因素确定模穴,如1X1、1X2等。
2、当几个产品出在同一套模具中时,考虑进胶的均匀性,应将大的产品排在中间位置,小的产品置于两边。
确保冲胶平衡,保证产品尺寸的精确性。
3、当几个分型面不规则的产品在同一模具中时,排位必须充分考虑其分型面连接的顺畅,且容易加工。
4、一模多穴模具中,当有镶拼,行位等结构时,不得使其发生干涉。
5、排位多时应综合模具每一方面,对流道,是否镶拼,行位,顶出,运水等结构要有一个全局性思考。
6、排位时产品在模上的定位基准要和产品图的基准一致,当一模出一件时,可以考虑以产品对称方向处分中。
7、内模钢料和模胚的大小尺寸如下图所示。
Skip Record If...?8.产品大小和胶位厚度有较大相差时尽量不要出在同一套模具中。
9.模具方铁高度尽量订做标准高度。
10.模胚型号和中托司使用情况一定要写清楚(细水口需注明SP 长度)11.必要时需注明模胚吊模孔移位情况12.考虑需不需开精框及内模料材料和规格(确定后模要不要镶大呵,如需要则一起订料,此为粗料.)二、模具系统设计一)、行位系统当塑胶产品确定前后模开模方向后,有下列情况时一般会采用行位或斜顶等结构:1)、相对出模方向塑胶产品上有倒扣或零度面;2)、产品的出模斜度不够蚀纹的角度;3)、保证特殊的外观面不能有夹线。
1、后模行位:1)、后模行位统一做镶件压块,行位压块用螺丝固定,行位压块材料为油钢淬火至HRC48-52°。
Skip Record If...?2)、所有与行位相对运动的零部件的滑动面(包括行位底耐磨片,压条,铲基斜面)须锣(磨)油坑,油坑可为平行四边行、V形或圆环形。
3)、行位铲机钢材整体采用738H,在铲机斜面上镶耐磨片,耐磨片可突出斜面0.5mm,耐磨片厚度为6mm(如下图),材料为油钢,淬硬至HRC48-52°。
塑料注塑模的标准

塑料注塑模的标准一、概述塑料注塑模是一种常见的模具类型,广泛应用于塑料制品的生产。
注塑模根据制品的形状、尺寸和性能要求而设计制造。
本文将详细介绍塑料注塑模的标准,包括模具结构、材料选择、制造工艺、精度要求、验收标准等方面的内容。
二、模具结构1.模具应具有完整的型腔布局,包括浇口、流道、型腔、排气槽等。
浇口和流道的设计应有利于塑料的流动和填充,同时减少压力损失。
型腔的设计应符合制品的形状和尺寸要求。
2.模具应设有顶出机构,以便于脱模。
顶出机构的设计应保证制品顺利脱模,避免损坏制品表面。
3.模具应具备冷却系统,以便于控制模具温度,提高制品质量。
冷却系统的设计应合理分布冷却水路,确保模具温度均匀。
4.模具应设有安全防护装置,确保操作安全。
安全防护装置应符合相关标准,能够有效防止意外伤害。
三、材料选择1.模具材料应根据制品的性能要求、模具的使用寿命以及制造工艺等因素进行选择。
常用的模具材料包括钢材、铝合金、锌合金等。
2.钢材具有较高的强度和硬度,适用于制作大型、复杂的模具。
铝合金和锌合金具有较好的加工性能和耐腐蚀性,适用于制作小型、简单的模具。
3.模具材料的采购应遵循相关标准,确保材料的质量和可靠性。
模具材料应进行严格的检验和控制,确保符合设计要求。
四、制造工艺1.模具制造应遵循相关制造标准,确保模具的精度和质量。
制造过程中应采用合理的加工方法,如铣削、钻孔、电火花加工等,确保模具型腔的精度和表面质量。
2.模具浇口和流道的设计应合理选择浇口位置和流道尺寸,以确保塑料能够顺利填充型腔。
浇口和流道的设计应进行仿真分析,以优化填充效果和提高制品质量。
3.模具顶出机构的设计应考虑顶出速度、顶出距离和顶出力等因素。
顶出机构的设计应进行仿真分析,以确保制品顺利脱模。
4.模具冷却系统的设计应考虑冷却水的流量、压力和温度等因素。
冷却系统的设计应进行仿真分析,以确保模具温度均匀分布,提高制品质量。
五、精度要求1.模具的精度包括型腔精度、表面粗糙度、尺寸精度等。
塑料模具设计产品外观要求标准
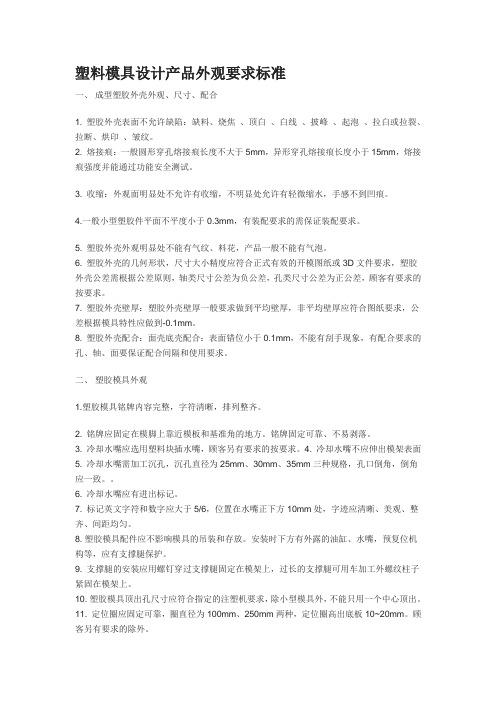
塑料模具设计产品外观要求标准一、成型塑胶外壳外观、尺寸、配合1. 塑胶外壳表面不允许缺陷:缺料、烧焦、顶白、白线、披峰、起泡、拉白或拉裂、拉断、烘印、皱纹。
2. 熔接痕:一般圆形穿孔熔接痕长度不大于5mm,异形穿孔熔接痕长度小于15mm,熔接痕强度并能通过功能安全测试。
3. 收缩:外观面明显处不允许有收缩,不明显处允许有轻微缩水,手感不到凹痕。
4.一般小型塑胶件平面不平度小于0.3mm,有装配要求的需保证装配要求。
5. 塑胶外壳外观明显处不能有气纹、料花,产品一般不能有气泡。
6. 塑胶外壳的几何形状,尺寸大小精度应符合正式有效的开模图纸或3D文件要求,塑胶外壳公差需根据公差原则,轴类尺寸公差为负公差,孔类尺寸公差为正公差,顾客有要求的按要求。
7. 塑胶外壳壁厚:塑胶外壳壁厚一般要求做到平均壁厚,非平均壁厚应符合图纸要求,公差根据模具特性应做到-0.1mm。
8. 塑胶外壳配合:面壳底壳配合:表面错位小于0.1mm,不能有刮手现象,有配合要求的孔、轴、面要保证配合间隔和使用要求。
二、塑胶模具外观1.塑胶模具铭牌内容完整,字符清晰,排列整齐。
2. 铭牌应固定在模脚上靠近模板和基准角的地方。
铭牌固定可靠、不易剥落。
3. 冷却水嘴应选用塑料块插水嘴,顾客另有要求的按要求。
4. 冷却水嘴不应伸出模架表面5. 冷却水嘴需加工沉孔,沉孔直径为25mm、30mm、35mm三种规格,孔口倒角,倒角应一致。
6. 冷却水嘴应有进出标记。
7. 标记英文字符和数字应大于5/6,位置在水嘴正下方10mm处,字迹应清晰、美观、整齐、间距均匀。
8. 塑胶模具配件应不影响模具的吊装和存放。
安装时下方有外露的油缸、水嘴,预复位机构等,应有支撑腿保护。
9. 支撑腿的安装应用螺钉穿过支撑腿固定在模架上,过长的支撑腿可用车加工外螺纹柱子紧固在模架上。
10. 塑胶模具顶出孔尺寸应符合指定的注塑机要求,除小型模具外,不能只用一个中心顶出。
11. 定位圈应固定可靠,圈直径为100mm、250mm两种,定位圈高出底板10~20mm。
- 1、下载文档前请自行甄别文档内容的完整性,平台不提供额外的编辑、内容补充、找答案等附加服务。
- 2、"仅部分预览"的文档,不可在线预览部分如存在完整性等问题,可反馈申请退款(可完整预览的文档不适用该条件!)。
- 3、如文档侵犯您的权益,请联系客服反馈,我们会尽快为您处理(人工客服工作时间:9:00-18:30)。
塑料模具设计规范一、目的:为加强模具设计人员的工作规范,减少模具设计误差返工,避免工件报废,并尽量缩短制造周期,确保品质要求和工程的排期需求。
二、范围:适用于模具设计人员管理。
三、内容:1.0注射模具的结构组成根据模具中各个部件的不同作用,一套注射模可以分成以下几个部分:1)内模零部件,赋予成型材料形状和尺寸的零件。
通常由下模上模,镶件(镶针)等组成。
2)浇注系统:将熔融塑料由注射机射嘴引向闭合的模腔,一般由灌口主流道、分流道、浇口和冷料穴组成。
3)热交换系统:为了满足注射成形工艺对模具温度的要求(冷却或加热)需要对模具温度进行较精确的调整。
4)行位系统:当侧向有凸凹及孔时,在塑料被顶出之前,必须先抽拔侧向的型芯(或镶件),才能使塑件顺利脱模。
5)顶出系统:实现塑件脱模的机构,其结构形式很多,最常用的是顶针、司筒和推板等脱模机构。
6)导向定位部件,是保证动模与定模闭合时能准确对准、脱模时运动灵活,注射时承受侧向力的部件,常由导柱和导套及定位块、锥等组成。
7)排气系统:将型腔内空气导出的排气槽及间隙8)结构件:如模架板、支承柱、限位件等。
2.0模具设计的基本程序2.1设计注射模应考虑的问题:1)分析塑件结构及其技术要求。
要注意塑件的尺寸精度、表面粗糙度的要求及塑件的结构形式,对不合理的结构要提出改进塑件设计的建议。
2)了解注射机的技术规格。
包括锁模力、最大容模量,开模距离、顶出孔大小位置和数量、码模方式、法兰尺寸及其它机器参数。
附表(积丰现有的注塑机)3)了解塑件材料的加工性能和工艺性能,包括塑件能达到的最大流动距离比;塑料在模具内可能的结晶、取向及其导致的内应力;塑料的冷却收缩和补缩;塑料对模具温度的要求等。
4)了解特殊技术要求。
5)考虑模具的结构和制造,包括选择分型面和型腔的布置及进料点;模具的强度、刚度和模腔尺寸精度;行位机构和顶出系统;模具零件的制造方法及制造的科学性可行性及经济性;装拆的工艺性;必要的辅助工具的设计等。
6)考虑模具材料的选择,包括材料的机械、工艺性能及热处理要求,材料胚料的大小。
7)考虑模具的成型效率,合理的设置运水。
3.0模具设计的一般流程1)1.模具确认表-总指标:交货期,模具寿命。
2.塑胶件:材料,表面质量,几何形状,其他要求。
3.注射机:型号规格。
4.行腔数目5.行腔排布,模架确定、6.分型面、7.塑腔尺寸8.主浇道以及分流道9.浇口10.冷却系统11.结构件设计12.行腔精确尺寸13.顶出系统14.导向定位系统15.排气系统16.安装选件2)对流程图的说明:流程图只说明了在模具设计过程中考虑问题的先后顺序;而在实际的设计过程中可能并不是按此顺序进行设计的。
并且设计中经常要再返回上步或上几步对已经的设计步骤进行修正,直至最终决定设计。
4.0模架、内模材料的订制程序1.主管2.收到产品图确认表3.分析产品结构,模具设计要求4.(1)复杂,安排画模具排位图(2)简单,画模具结构简图(3)客户要确认结构。
安排设计客户确认。
订料,调整设计5.简单和复杂。
订模架。
内膜大料。
安排设计6.之后审图7.出图纸明细表。
几点说明:1) 收到不明确的产品图可以退回技术部,并加强与技术部代表沟通2) 分析产品结构及模具设计要求要搞清注塑机吨位,然后选用适合注塑机的最大规格模架。
对已定注塑机的规格要再确认。
注射机锁模力>产品合模所需最大力≌注射压力×产品在分模面上最大投影面积=1吨/cm2×A。
(上述1吨/cm2是一般情况下精确计算计参阅附录十一《常用塑胶材料一览表》根据胶厚、流程等选用注射压力)计算锁模力后,还要计算所选注塑机最大射胶量是否合适,保证产品重量(折成体积)是最大射胶量(体积)的80%左右。
画结构简图前可以找一些相近模具设计文件夹作参考。
对不能明确认定的模架结构,可找相关人员协商定案。
开框图要以A4纸清晰表达。
安排画模具排位图要先向设计人员讲清大概思路,然后把产品图排入模架。
排位图要画出内模大小、行位、运水等。
排位图不须标尺寸,无须画顶针等,排位图要1:1打印出以方便审查,订料。
设计完成后应检讨已订材料是否与现设计一致,若有偏差应通知采购部作相应调整。
5.0塑件结构工艺性分析方法5.1塑件工艺性分析的步骤:塑件工艺性的分析包含五个方面的内容:要分析塑件使用塑胶材料的成型工艺性能(包括流动性、收缩性、结晶性、定向作用、吸水性、硬化特征等)。
分析塑件的形状是否符合成型工艺和模具制造的要求。
要了解塑件使用场合及功能,把握塑件尺寸中的重点和关键点及外观面的位置和外观质量要求。
入水方式及入水点的形状会对塑件的最终尺寸和形状产生影响。
对收缩率把握不准的场合,特别难控制的模具要预留收缩变动修模余量。
5.2塑件结构的要求注射成型的塑件要合符注射成型的工艺要求及模具结构和制造尽可能简单的要求。
从注射工艺的要求上分析,塑件的结构应具备以下特点:塑件的壁厚尽可能的均匀。
壁厚有较大差别时,也用渐变去代替壁厚的突然变化。
塑件的壁厚要恰当,即不能过薄又不能过厚,一般在1 ~ 6mm范围内表2-3 是常用塑胶材料的壁厚值。
表2-3塑料最小壁厚小型塑件推荐壁厚中型塑件推荐壁厚大型塑胶件推荐壁厚聚酰胺PA 0.45 0.75 1.6 2.4-3.2聚乙烯PE 0.6 1.25 1.6 2.4-3.2聚苯乙烯PS 0.75 1.25 1.6 2.4-5.4改性聚苯乙烯HIPS 0.75 1.25 1.6 2.4-5.4有机玻璃PMMA 0.8 1.5 2.2 3.2-5.8硬聚氯乙烯PVC 1.15 1.6 1.8 3.2-5.8聚丙烯PP 0.85 1.45 1.75 2.4-3.2聚碳酸酯PC 0.95 1.8 2.3 3-4.5聚苯醚PPO 1.2 1.75 2.5 3.5-6.4醋酸纤维素EC 0.7 1.25 1.9 3.2-4.8聚甲醛POM 0.8 1.40 1.6 3.2-5.4聚砜PSF 0.95 1.80 2.3 3-4.5ABS 0.75 1.5 2 3-3.5尽量使用圆角去代替尖锐的角,以利于塑胶的充模。
加强筋加快填充及增加壁件的强度和刚度。
一般原则是要求保证加强筋的大头尺寸,在(0.5-0.7)t的范围内,且加强筋大头的尺寸等于产品图筋位的名义尺寸。
如果加强筋落在曲面上,且较深时,从制造的角度考虑应给出筋小头的尺寸。
并且小头尺寸不应小于(表2-3)推荐的最小壁厚,拔模角在10 ~ 50范围内给出。
此时,如果大头的尺寸超出了产品图筋位的名义尺寸需要和技术部达成共识后调整。
表2-4塑料名称型腔斜度型芯斜度聚酰胺(尼龙)PA 25ˊ-40ˊ20ˊ ~40ˊ聚乙烯PE 25ˊ-45ˊ20ˊ ~45ˊ聚苯乙烯PS 35ˊ~1°30ˊ30ˊ ~1°聚甲基丙烯酸甲酯PMMA 35ˊ~ 1°30ˊ30ˊ ~1°ABS 40ˊ~1°20ˊ35ˊ ~1°聚碳酸酯PC 35ˊ~1° 30ˊ ~50ˊ聚甲醛POM 35ˊ~1°30ˊ30ˊ ~1°热固性塑料25ˊ~1° 20ˊ ~ 50ˊ从模具结构和制造上分析,塑件的结构要具备以下特点:1)塑件要有足够的拔模角,以利于塑件从模腔及模呵上脱出,(表2-4)是塑件的单边脱模角的推荐值。
蚀纹表面的脱模角要大。
2)钩、扣位工艺孔塑件的钩位、扣位等结构有些是通过前后模插穿实现的。
3)落在曲面上的孔,孔口要倒角,以避免出现尖锐的胶位。
4)用Half成型外螺纹或精密圆柱时,要削平与PL面垂直的两个面5)当内、外螺纹必须采用旋转脱模时,应合理的设置止转位6)T形切面的接合面会产生凹陷,要在模呵(core)侧边设置锲角减薄胶位7)加强筋高度的预留8)一般的,塑件上注有公差的尺寸,在计算收缩时,要取中间尺寸为名义尺寸。
9)当塑件使用的塑料收缩率变化范围较大时,如果塑件的尺寸公差要求小于可能出现的收缩变化,模具上要留有可修改的量,考虑能镶、能换,做一些防错应变措施。
10)要对大于基本胶厚的部分作吊空胶处理,保证基本肉厚一致,并考虑冷却问题。
11)面壳比底壳预大的问题。
通常要求:面壳周边大出约0.03 ~ 0.05。
但底面壳缩水可能不一样。
拿遥控器面壳来说,由于胶厚、模温、产品形状与底壳有差异,造成面壳收缩率大于底壳,这在尺寸预留时要预以考虑。
加胶要加易修正的壳。
12)上、下模有胶位时要考虑预留。
如上模出圆角、倒角时,一般下模胶位要多单边0.03 ~ 0.05。
13)变形的预留:a 反变形b 吊空胶6.0绘制模具图6.1 模具总装图包括以下内容:a. 模具成型部分结构b. 浇注系统、排气系统的结构形式。
c. 分型面及分模取件方式。
d. 外形结构及所有连接件,定位、导向件的位置。
e. 标注型腔高度尺寸(不强求,根据需要)及模具总体尺寸。
f. 按顺序将全部零件序号编出,并且填写明细表。
6.2绘制零件图由模具总装图拆画零件图的顺序应为:先内后外,先复杂后简单,先成型零件,后结构零件。
a. 图形要求:一定要按比例画,允许放大或缩小。
视图选择合理,投影正确,布置得当。
易看懂、便于装配,图形尽可能与总装图一致,图形要清晰。
b. 标注尺寸要求统一、集中、有序、完整。
标注尺寸的顺序为:先标主要零件尺寸和出模斜度,再标注配合尺寸,然后标注全部尺寸。
在非主要零件图上先标注配合尺寸,后标注全部尺寸。
c. 表面粗糙度。
把应用最多的一种粗糙度标于图纸右上角,如标注"其余3.2。
"其它粗糙度符号在零件各表面分别标出。
d. 其它内容,例如零件名称、模具图号、材料牌号、热处理和硬度要求,表面处理、图形比例、自由尺寸的加工精度、技术说明等都要正确填写。
6.0审图程序(设计人员先按表自审,然后交主管审图)分类校核事项1.品质充分检讨型模材料,硬度,精度,构造等是否与定制者之规格相符?2.成形品检讨缩水,材料流程,等诸事项是否影响成形品外观?在成形品之机能及构造无故障范围中,检讨型模加工是否容易?成形品材料之收缩率是否估计正确?3.成形机成形机之射出量,射出压力,合模压力是否充分?型模是否能正确安装于指定使用之成形机上。
亦即,装接螺丝位置,定位环之位置,喷嘴半径R,注嘴孔径,顶出用孔位置及大小,型模大小及厚度等是否适当?固定板压板位有铣薄至跟动模固定同厚。
4.基本构造(1)顶出机构选用之顶出方法对成形品是否适当?顶针、顶板、司筒、气顶,其它等。
顶针、司筒(尽量大些、顶在骨上)使用数量及位置是否适当?有无必要做三个顶辊孔?司筒有无碰顶辊孔?行位下边有顶针时,顶针板有无加行程开关?有斜推针时,顶针是要加“+”字槽防滑,有否加顶针板行程开关?(2)温度控制运水大小,数量,位置是否适当?有无标注喉牙规格?有无撞顶针等?(3)行位行位机构是否合适而确实?较大行位有无加铲鸡面垫板?用波子螺丝还是弹弓定位?(4)流道·浇口有无按要求设计流道系统?多腔模具是否入水均匀?设计制图(1)装配图模图有无画反?(产品图有无作倒影)于图内最少文字高度为2.5 mm?是否按《开模要求》绘制?产品在模具上有无明确基准位?是否对构件装配位置明确表示?部分制品是否按积丰标准来选用?有无必要的技术要求?剖切位恰当是否与切图相符?图面是否简洁明了?细微结构处有无放大处理?斜顶结构有无表达清晰(平面图要有斜顶及其滑座平面布置图)是否会与其他零件相碰。