降低钢包浇余提高钢水收得率的实践
降低120t转炉钢铁料消耗生产实践
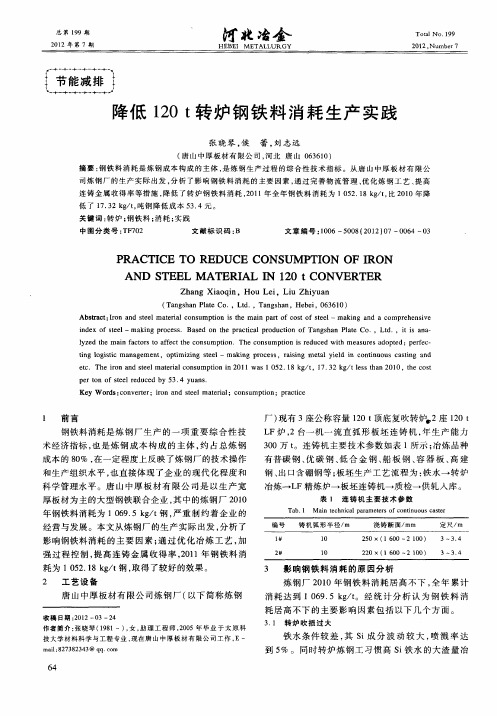
奖惩 考核 调动职 工 的积极 性 。
4 2 优 化 炼 钢 工 艺 .
4 2 1 调 整 炉 料 结 构 ..
转炉 的装 入量 为 10~10 t而铁 水量 仅 为 10 4 5 , 2
( ) 据 浇 铸 周 期 确 定 转 炉 装 入 量 , 装 入 量 1根 将 由原来 10~10t 整为 10~10t 4 5 调 3 4 。之 后炼 铁 厂
21 0 0年 连铸 机高 温钢 事故 占总事 故 率 的 6 % 以上 , 0
由于事故 多发 导致 回浇 余钢 水 、 连铸坯 甩废 量 增 多 。
同 时 由于切割 割 嘴 更换 不 及 时 , 压不 合 理 致 使 割 氧 口较 大 , 大大 降低 了钢 水收 得率 。
3 4 物 流 管理 不 完 善 .
机 的浇铸周 期 为 3 6~3 n 炉 机 生 产 不 匹配 。 为 8 mi , 缓 解 生产 节奏 的影 响 , 采取 了“ 高温 慢 铸 ” 的操 作 思
1 5t以满足 一次 装铁 的需 求 。与 公 司 技术 科 等 相 2 , 关部 门配 合 , 定铁 水成 分及 温度控 制 , 炼 钢铁 水 稳 供
ma l 8 7 8 3 3@ q c r i: 2 3 2 4 q. o n
铁 水 条件较 差 , s 成 分 波 动 较 大 , 其 i 喷溅 率 达
到 5 。 同时转炉炼 钢工 习惯 高 S 铁水 的大 渣量 冶 % i
河 北 冶金 Leabharlann 21 0 2年 第 7期
炼 , 到低 s 铁水 时易 因热 量 不 充 足 、 作不 当造 遇 i 操 成 严重 后 吹 , 渣 中氧化 铁含 量大 增 , 加 了铁损 。 使 增
炼钢工—简答题 207

1.什么是溅渣护炉技术?答案:溅渣护炉技术是向炉渣中加入含MgO的造渣剂造粘渣补炉技术的基础上, 采用氧枪喷吹高压N2在2-4mm 内将出钢后留在炉内的残余炉渣喷溅涂敷在转炉内衬表面上,生成炉渣保护层的护炉技术。
2.炉渣来源何处?它在炼钢中起什么作用?答案:来源:(1)钢铁料中夹杂氧化的产物。
(2)造渣材料(石灰、白云石、萤石等)。
(3)冷却剂(氧化铁皮、矿石等)。
(4)被浸蚀和冲刷下来的炉衬耐火材料。
(5)各种原料带来的泥沙。
作用:(1)去夹杂(P、S);(2)传氧媒介;(3)清洁钢液;(4)对熔池保温;(5)影响金属损失;(6)影响炉衬浸蚀。
3.脱碳反应对炼钢过程的重要意义是什么?答案:(1)铁水中C氧化到钢种所要求的范围。
(2)氧化产生CO气泡对熔池起着循环搅拌作用,均匀钢液成份、温度, 改变各种化学反应的动力学条件。
(3)CO气泡有利于去除N2、H2等。
(4)利于非金属夹杂物上浮。
(5)提供炼钢的大部分热源。
(6)CO气泡使炉渣形成泡沫渣。
4.造成钢包回磷的原因是什么?如何防止?答案:原因:(1)出钢下渣;(2)脱氧产物SiO2;(3)氧含量降低。
防止措施:(1)挡渣出钢,尽量减少出钢带渣。
(2)采用碱性钢包或渣线部位用碱性材料。
(3)出钢过程中投入钢包中石灰粉。
(4)减少钢水在钢包中停留时间。
5.为什么兑铁时,有时会发生大喷?答案:因为转炉吹炼到终点,钢中氧含量和炉渣氧化性高, 留渣或未倒净的渣子和钢水,兑铁时炉内碳含量急剧增加且铁水温度低及钢水温度骤然下降, 促使碳氧反应剧烈进行在炉内产生强烈沸腾,如果兑铁水过猛且炉内残留钢渣较多就会大喷。
6.为什么转炉炼钢脱硫比脱磷困难?答案:碱性转炉渣中含有较高的(FeO),炉渣脱硫的分配比较低,降低了炉渣的脱硫能力,高(FeO)对脱磷工艺是一个相当有利的因素, 转炉炼钢条件下钢渣间磷的分配比较高, 一般可达100-400,而硫的分配比一般为6-15,此外,脱磷反应速度快,很快可达到平衡,而脱硫速度较慢,一般达不到平衡。
LF炉热态钢渣的循环利用技术

Ke o ds LF f r c y W r : u na e;h tse lsa o t e l g;cr u a ng u iia o ic lt tlz t n;tc ni e i i e h qu
1
前 言
表 1 渣 料 的 组 成 及 脱 氧 剂 的 加 入 量
总 第 1 7期 9 21 0 2年 第 5期
河 北 冶全
H EBEI M ETALLU R G Y
Tot O. 9 a N l 17 2 1 N u b r5术
黄康 乐 , 江波 , 孙 窦为 学 , 张鹏飞
s p urc n e ti h t te sa a a e m a n nd x a tr se l l g beng ic l tn tlz d f r t r e ulh o t n n o se l lg nd M nn s n i e fe t e sa i cr u a g u ie o h e i i
Ta . Co p st n o l g b 1 m o ii f sa o m ae i la d a dng a o n fd o i a in a e t tra n d i m u to e x d to g n
在 生产 过 程 中 , 们 发 现 L 我 F炉 精炼 后 的 钢 渣 仍 含有 一定 量 的硫 , 有再 利 用 的价值 。此 外 钢 水 浇
关 键 词 : F炉 ; 态 钢 渣 ; 环利 用 ; 术 L 热 循 技 中 图 分 类 号 : F 6 . T 792 文献 标 识 码 : B 文 章 编 号 :0 6—5 0 ( 0 2 0 0 6 0 10 0 8 2 1 ) 5— 0 4— 2
CⅡ CULA1 旺NG UTⅡ ATI ON
转炉炼钢挡渣工艺简介
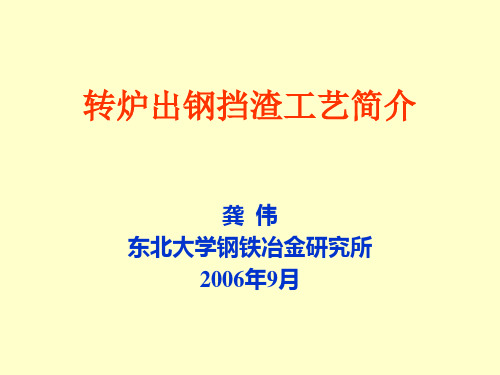
龚 伟 东北大学钢铁冶金研究所 2006年9月 年 月
转炉出钢挡渣的必要性
可以减少钢水回磷,提高合金收得率 可以减少钢水回磷 提高合金收得率; 提高合金收得率 减少钢中夹杂物,提高钢水清洁度 提高钢水清洁度; 减少钢中夹杂物 提高钢水清洁度 可以减少钢包粘渣,提高钢包包龄 提高钢包包龄; 可以减少钢包粘渣 提高钢包包龄 同时可减少耐材消耗; 同时可减少耐材消耗 也可为钢水精炼提供良好的条件。 也可为钢水精炼提供良好的条件。
挡渣塞法
该装置呈陀螺形,粗端有 3个凹槽、6个棱角,能够 破坏钢水涡流,减少涡流 卷渣。其比重与挡渣球 相近,在4.5 ~ 4.7 g/cm3之 间,能浮于钢渣界面,伴随 着出钢过程,逐渐堵住出 钢口,实现抑制涡流和挡 渣的作用。
能抑制涡流的挡渣塞
挡渣料法
• 原理:此法也称硬吹或干渣吹炼法。 原理:此法也称硬吹或干渣吹炼法。 它是在吹炼结束时喷射一种固态混合 提高渣稠度,使渣局部或全部凝固 物,提高渣稠度 使渣局部或全部凝固 提高渣稠度 使渣局部或全部凝固, 以改变渣的流动性来挡渣;或在出钢 以改变渣的流动性来挡渣 或在出钢 口上部渣面投入粒状耐火材料,形成 口上部渣面投入粒状耐火材料 形成 块状堵塞物,防止渣流出 防止渣流出。 块状堵塞物 防止渣流出。
挡渣棒法
• 1983年日新制钢研究成功挡渣棒法。 • 挡渣棒吊在支臂上在炉内可以自由移动, 在即将出完钢时从转炉内部将出钢口塞 住,以挡住炉渣,如再配以荷重器、高频电 流信号,效果更佳。该装置操作与维护较 复杂。
其他Байду номын сангаас法
• • • • 出钢口吹气干扰涡流法 转动悬壁法 挡渣罐挡渣法 均流出钢口法
带保护外壳的红外摄像仪
炼钢工—论述题 131

1.提高炉龄的措施?答案:(1)采用溅渣护炉技术。
(2)提高炉衬耐火材料质量。
(3)采用综合砌筑技术。
(4)炉渣配适量的氧化镁。
(5)采用计算机动态控制,即采用最佳冶炼控制,提高终点命中率,缩短冶炼周期。
(6)进行有效喷补及合理维护。
(7)改进喷枪结构。
(8)尽可能降低出钢温度。
(9)减少停炉时间。
2.分析冶炼终点硫高的原因及处理措施?答案:一般有以下原因:(1)铁水、废钢硫含量高;(2)造渣剂、冷却剂含硫高;(3)冶炼不正常,化渣不好等。
处理措施:(1)进行铁水预脱硫处理;(2)多倒终渣,再加石灰造高碱度高温炉渣;(3)终点加一定锰铁合金,炉内发生[FeS]+[Mn]=[MnS]+[Fe]反应脱一部分硫;(4)出钢在钢包中加入脱硫剂;(5)采用炉外精炼脱硫等。
3.炉衬损坏原因?答案:由于炉衬工作条件恶劣,损坏原因是多方面的,其主要原因是:(1)废钢、铁水对炉衬冲击及机械磨损;(2)钢液及炉渣的搅动及气体冲刷;(3)炉渣对炉衬的化学侵蚀;(4)炉衬温度激冷激热变化和组织变化的开裂剥落;(5)开炉初期的机械剥落;(6)炉衬内部碳素的氧化。
4.转炉出钢为什么要挡渣?目前挡渣方法有那些?答案:挡渣出钢的主要目的是净化钢水,同时还可以减少合金和脱氧剂的消耗量;减少回磷;减轻耐材侵蚀;有利于钢水二次精炼。
目前国内外普遍采用挡渣挡渣方法有:挡渣球、挡渣棒(塞)、挡渣锥、气动阀(气动挡渣)等。
5.炉渣“返干”及成因?答案:在顶吹转炉吹炼的中期,冶炼温度足够高,碳氧反应激烈,此时枪位比较低,已形成的炉渣的流动性往往会突然减低,甚至会造成结块,即炉渣“返干”出现炉渣“返干”的钢渣组成:钢渣基本代表组成成分SiO2、CaO、FeO三元相图可知,在R=2.33时,当(FeO)比较高时,炉渣是一个均匀的液体;但当(FeO)<16%以后,便有固相的2CaO.SiO2析出;当R=4时,当(FeO)<16%以后,便有固相的3CaO.SiO2及固相的CaO析出。
大包下渣检测应用
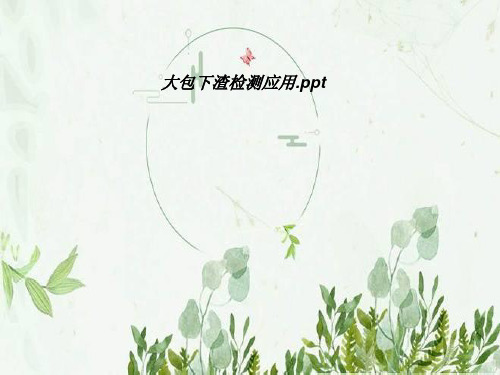
1)三维监控及视频信号处理 软硬件结合,从三维立体空间全方面监测振动信号,两者综合
更加准确更加明显的突出了下渣特征,准确的给出报警信息,见图 5。
图5 信号分析处理图
振动式大包下渣自动检测系统 在湘钢5米宽厚板的应用
3.4 系统特点
2)屏蔽处理及警戒线动态更新 对滑板动作、外界坐包等强烈冲击振动做分析及屏蔽处理,警
月份
月平均值 %
1月 97.59
表22月2012年连铸金3属月收得率 4月
97.58
96.99
97.49
5月 97.67
平均 97.46
大包下渣检测应用.ppt
振动式大包下渣自动检测系统 在湘钢5米宽厚板的应用
1 前言
钢包下渣检测已成为现代连铸生产和质量控制的重要技术之一,使 用此技术的主要优点有:
1)防止钢包过量下渣、提高钢水洁净度; 2)提高连铸钢水浇铸收得率; 3)改善大包操作工的劳动强度和工作环境。 目前国内外研制了多种下渣检测方法,如红外线技术检测、电磁感 应法检测、超声波检测等,但这些检测系统在安装、使用和维护过程中 的成本都较高。由于上述方法存在的不足以及投资及使用成本问题,我 们考虑了使用振动式下渣检测技术。
振动式大包下渣自动检测系统 在湘钢5米宽厚板的应用
2.1 成本问题
在没有使用镭目振动式大包下渣检测系统以前,一些对质量要求 特别高的钢种采用留钢操作来避免大包下渣,这样一来连铸的金属收得 率大大降低,同时由于称重的误差也不能完全避免下渣。
大包下渣检测系统可以根据不同钢种设计延迟关滑板操作。如果 以延迟3秒关闭计算,50分钟浇一炉钢,3000秒,一炉钢按130吨计算 ,每秒钟过钢量43公斤,每炉可多收得钢水130公斤,每天浇20炉钢, 一天即可多得钢水2.6吨,一年可多得钢水949吨;每吨钢水按成本 2000元计算,一套大包下渣检测系统一年可降耗节支:949吨×2000 元/吨=189.8万元。
对炼钢工艺不断学习的心得

心得体会通过学习让我对专业及现场实践有了更深的认知和理解,同时也将在我个人的职业生涯中勾画出浓重的一笔开端。
下面谈谈自己的学习心得。
一、对理论知识的再温习在工作学习阶段,翻开炼钢工艺及炼钢500问相关书籍,让我的思绪又回到学生时代,打开笔记本和记忆老师勾画的知识要点。
目前阶段钢铁企业的发展越发靠近客户,越发靠近信息化及自动化,将书中的知识点及工艺如何通过现在的智慧制造实现自动、实现智能管控的一个大趋势。
二、对理论知识转换为解决现场问题的工具的体会在工作实践中,本人充分利用时间,不畏现场工作高温环境的艰苦,努力工作,基本完成了现场基本的工种的学习,并能够熟练的掌握工作要领,在工作期间里使自己在工作能力上得到了很大的提。
工作之余认真学习专业理论知识,并能并能够很好的理论与实践相结合,在实践中能善于思考发现问题、分析问题、解决问题,同时也对炼钢厂的整个生产工艺也有一个更为全面的认识和了解。
结合现场实际,围绕如何降低钢铁料消耗这个问题在导师的指导下独立完成一篇关于提高冶炼收得率降低钢铁料消耗的实习论文以及针对如何降低S废废品发表QC一篇。
在炼钢专工师傅的利用业余实践结合转炉湿法除尘工艺,总结“不同铁水成分条件下不同冶炼阶段除尘环缝开度的优化”、“氮封基座及加料口氮封流量的选优确定以及氮封基座安全安装”等方法,通过微调试验及不断归纳总结,最终确定了在冶炼各阶段环缝最佳开度同时形成了环缝控制pattern、除尘风机服役期转速的调控参照表、氮封基座及加料口氮封流量范围等,为产线环保冶炼提供技术保证,实现了厂房外排事件为零的记录,也为绿色持续发展贡献炼钢环保管控方案。
在不断关注技术指标的同时,跟炼钢班组成员一块研讨并提出可行的举措实现指标的进一步提升。
通过持续推进少渣留渣冶炼实现钢铁料消耗的持续降低,截至目前150t产线钢铁料最低消耗为1048.73kg/t,40t为1056.34kg/t,围绕钢铁料指标,从技术角度剖析Fe平衡,开展高效去磷控制终点碳含量、少渣留渣、窄缝切割等手段降低Fe流失。
提高钢包自开率的生产实践
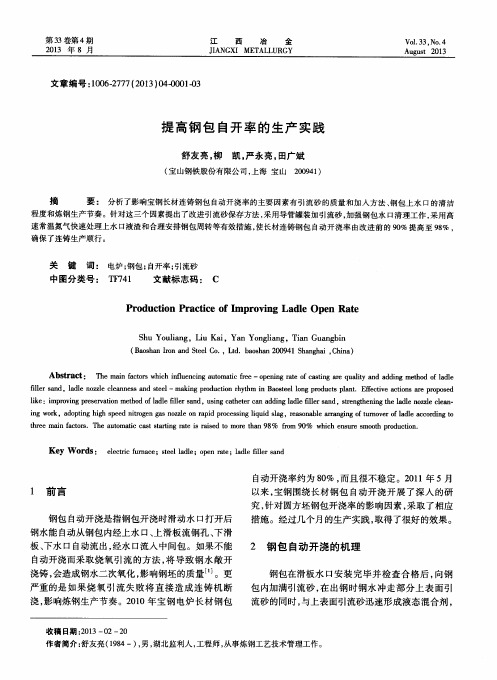
l i k e:i mp ov r i n g p r e s e r v a t i o n me t h o d o f l a d l e i f l l e r s a n d,u s i n g c a t h e t e r c a n a d d i n g l a d l e il f l e r s a n d,s t r e n g t h e n i n g t h e l a d l e n o z z l e c l e a n .
常 的传搁 时 间。钢 水 的传 搁 时 间越 长 , 钢 包 的 自开
3 影 响钢 包 自动 开 浇 的 因素 分 析
3 . 1 引流砂 的质 量和加入 方 法 引流 砂 的质 量 主要 取 决 于 材 质 、 粒度 、 流 动 性
率就 越低 , 这是 因为 引流 砂 受 钢水 高 温 作 用 的 时 间 越长, 会 导致钢 包水 口内引流砂烧 结层 增厚 , 不 利 于
4 改进 措 施
4 . 1 提 高引流 砂质量
能够被 钢水 静压 力 破 坏 。引 流 砂 的 热膨 胀 率 要 小 , 因为膨 胀率 大会 导 致 引 流砂 的 内应 力 增 大 , 互 相 挤
压而增 加与水 口内壁 的 附着 力 , 不 利 于 开浇 时 引流
钢包 全部使 用铬 质引 流砂 。铬质 引流 砂具 有 比 重大, 导 热率高 , 热 膨 胀性 适 中 , 烧 结 性 适 中和抗 钢 渣 渗透性 好 的优 点 。对 于 引流 砂 的管 理 , 要求 引
所决 定 的 , 而操 作 者 投 入 引 流 砂 全 凭 经 验 , 用 力 具 有 随意性 , 在 生 产 中存 在 投 入 不 到 位 的情 况 , 更 不 能保 证 水 口内加 满 引 流砂 。若 水 口内 引 流砂 量 不 足, 出钢 时 水 口内 空 位 处 容 易 进 入 钢 水 , 由于水 口 孔位 置低 于 包 底 , 故 即使 在 钢 包 吹 氩 过 程 中 , 水口 内钢 液亦 不 能 与钢 包 内钢 水循 环 对 流 , 仍滞 留于 水 口内 , 被 引 流砂 吸热 而 温 度 逐 渐 降 低 , 导 致 钢 液 与 引流 砂粘 结 成块 , 使 引流 砂 流动 性变 差 。当滑 板 打 开后 , 引 流 砂 很 难 自然 下 落 , 最 终 造 成 钢 包 自开
连铸坯表面夹渣控制

Zhanjiang Iron & Steel Co., LTD. 第7页
7
问题解答
问题二:动态轻压下作用
轻压下技术是在容易形成铸坯中心偏析的凝固末端实施一定的压下量,使 容易形成偏析及疏松的地方的非浓化钢液均匀流动,一方面消除或减少了因 铸坯收缩形成的内部空隙,从而防止晶间富集溶质的钢液向铸坯中心横向流 动;另一方面轻压下所产生的挤压作用还可以促使液芯中心富集溶质的钢液 沿拉坯方向反向流动,使溶质元素在钢液中重新分配,从而使铸坯的凝固组 织更加均匀致密.
Zhanjiang Iron & Steel Co., LTD. 第4页
4
连铸板坯夹渣封锁率控制——控制措施
1. 合适的浸入式水口及适宜的插入深度 圆柱形水口侧孔流出来的流股造成的上下相反方向上出现的两对回流始终 是均匀对称的;矩形水口的侧孔流出的流股容易发生偏流造成两侧流动不均 匀和不对称。因此,采用圆柱形内腔水口。
2. 夹杂物的卷入 皮下夹渣还与 Al2O3 等钢水中的非金属夹杂被坯壳捕捉有关,聚集在 水口内的 Al2O3等夹杂周期性脱落而被带入结晶器内,从而被弯月面捕获。 钢水中的氧化物系非金属夹杂物主要来源于钢水中未及时上浮的脱氧产物、
钢水二次氧化的生成物及钢包、中包等耐火材料的熔损。
湛江钢铁
2015-1-22
1. 结晶器卷渣 使一部分保护渣在此环流方向上被延伸,当流速超过某一临界值,被拉动的 液渣最后断裂成乳化渣滴。此渣滴被卷入钢液有可能被凝固坯壳的前沿捕捉, 形成皮下夹渣。 b. 漩涡卷渣:由于水口对中不良、水口堵塞等原因造成结晶器偏流从而形成漩 涡,这种漩涡把保护渣卷入钢液内部,形成皮下夹渣。 c. 弯月面扰动:水口周围的氩气泡引起渣-钢界面的扰动,并牵引液态钢高于正 常液面形成钢水局部波动,产生卷渣: d. 液面结壳:当钢水温度太低时造成结晶器保护渣结壳,形成絮状渣团,容易
大包浇余渣回收利用工艺研究及对成本影响实践
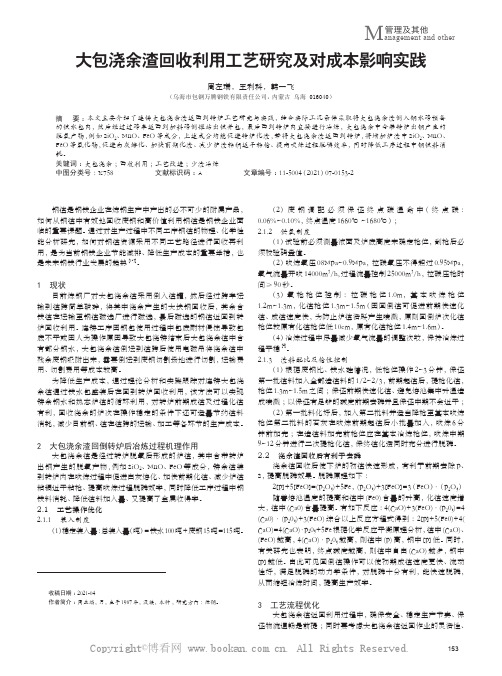
153管理及其他M anagement and other大包浇余渣回收利用工艺研究及对成本影响实践周左瑞,王利科,韩一飞(乌海市包钢万腾钢铁有限责任公司,内蒙古 乌海 016040)摘 要:本文主要介绍了连铸大包浇余渣返回到转炉工艺研究与实践,结合实际工况条件采取将大包浇余渣倒入钢水跨预备的铁水包内,然后经过过跨车返回到加料跨倒罐站出铁并包,最后回到转炉内直接进行冶炼,大包浇余中含带转炉出钢产生的脱氧产物,例如SiO 2、MnO、FeO 等成分,上述成分均能促进转炉化渣,若将大包浇余渣返回到转炉,将增加炉渣中SiO 2、MnO、FeO 等氧化物,促进白灰熔化、加快前期化渣、减少炉渣粘稠返干粘枪、提高吹炼过程脱磷效率,同时降低工序过程中钢铁料消耗。
关键词:大包浇余;回收利用;工艺改进;少渣冶炼中图分类号:X758 文献标识码:A 文章编号:11-5004(2021)07-0153-2 收稿日期:2021-04作者简介:周左瑞,男,生于1987年,汉族,本科 ,研究方向:炼钢。
钢渣是钢铁企业在炼钢生产中产出的必不可少的附属产品,如何从钢渣中有效地回收废钢和高价值利用钢渣是钢铁企业面临的重要课题。
通过对生产过程中不同工序钢渣的物理、化学性能分析研究,如何对钢渣资源采用不同工艺路径进行回收再利用,是为当前钢铁企业节能减排、降低生产成本的重要举措,也是未来钢铁行业发展的趋势[1-3]。
1 现状目前炼钢厂对大包浇余渣采用倒入渣罐,然后经过跨车运输到渣跨简单破碎,将其中浇余产生的大块钢回收后,其余含铁渣在运输至钢渣磁选厂进行磁选,最后磁选的钢渣返回到转炉回收利用。
连铸工序因钢包使用过程中包底耐材侵蚀导致包底不平或因人为操作原因导致大包浇铸结束后大包浇余渣中含有部分钢水,大包浇余渣倒运到渣跨后使用电磁吊将浇余渣中残余废钢吸附出来,需要倒运到废钢切割场地进行切割,运输费用、切割费用等成本较高。
为降低生产成本,通过理论分析和实践跟踪对连铸大包浇余渣通过铁水包盛装后在回到转炉回收利用,该方法可以实现铸余钢水和热态炉渣的循环利用,对转炉前期成渣及过程化渣有利,回收浇余的炉次在操作稳定的条件下还可适量节约渣料消耗,减少目前钢、渣在渣跨的运输、加工等各环节的生产成本。
钢水过程温度控制技术的研究与实践
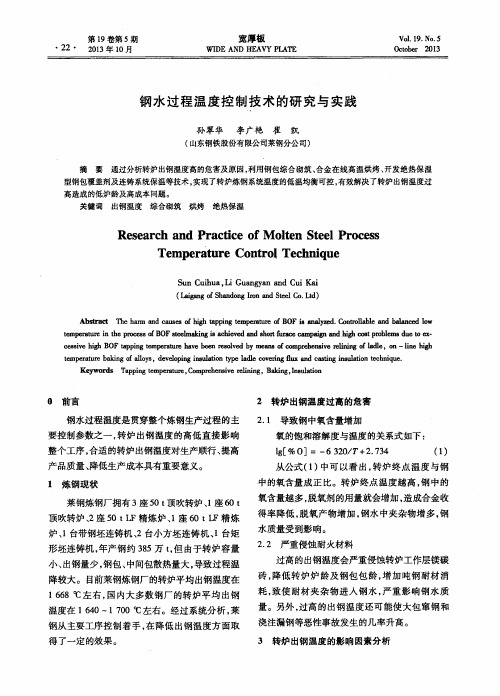
过高的出钢温度会严重侵蚀转炉工作层镁碳 砖, 降低转炉炉龄及钢包包龄 , 增加 吨钢耐材消
耗, 致使耐材夹杂物进入钢水 , 严 重 影 响 钢 水 质
Re s e a r c h a n d Pr a c t i c e o f Mo l t e n S t e e l Pr o c e s s
Te mp e r a t u r e Co n t r o l Te c h n i q u e
S u n C u i h u a , L i Gu a n g y a n a n d C u i Ka i
第1 9卷第 5期
・
宽 厚板
DE ND HE AV Y P L T E
V 0 1 . 1 9 . N o . 5 Oc t o b e r 2 OI 3
2 2‘ 2 0 1 3年 1 0月
钢水 过程 温度 控 制 技术 的研 究 与实 践
孙 翠 华 李 广艳 崔 凯
Ke y wo r d s T a p p i n g t e mp e r a t u r e , C o mp eh r e n s i v e r e l i n i n g,B a k i n g, I n s u l a t i o n
0 前言 钢水 过程 温度 是贯穿 整个 炼钢生 产过程 的 主
t e m p e r a t u r e i n t h e p r o c e s s o f B O F s t e e l m a k i n g i s a c h i e v e d a n d s h o r t f u r a o c c a m p a i g n a n d h i g l l c o s t p r o b l e m s d u e t o e x -
连铸钢包下渣的影响及控制研究
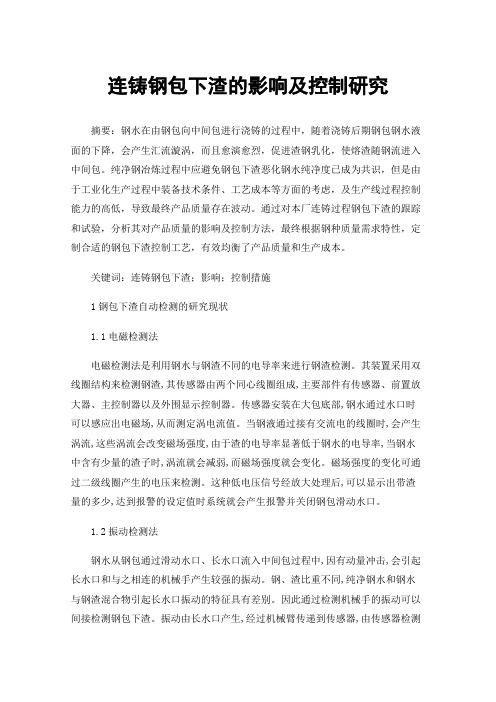
连铸钢包下渣的影响及控制研究摘要:钢水在由钢包向中间包进行浇铸的过程中,随着浇铸后期钢包钢水液面的下降,会产生汇流漩涡,而且愈演愈烈,促进渣钢乳化,使熔渣随钢流进入中间包。
纯净钢冶炼过程中应避免钢包下渣恶化钢水纯净度已成为共识,但是由于工业化生产过程中装备技术条件、工艺成本等方面的考虑,及生产线过程控制能力的高低,导致最终产品质量存在波动。
通过对本厂连铸过程钢包下渣的跟踪和试验,分析其对产品质量的影响及控制方法,最终根据钢种质量需求特性,定制合适的钢包下渣控制工艺,有效均衡了产品质量和生产成本。
关键词:连铸钢包下渣;影响;控制措施1钢包下渣自动检测的研究现状1.1电磁检测法电磁检测法是利用钢水与钢渣不同的电导率来进行钢渣检测。
其装置采用双线圈结构来检测钢渣,其传感器由两个同心线圈组成,主要部件有传感器、前置放大器、主控制器以及外围显示控制器。
传感器安装在大包底部,钢水通过水口时可以感应出电磁场,从而测定涡电流值。
当钢液通过接有交流电的线圈时,会产生涡流,这些涡流会改变磁场强度,由于渣的电导率显著低于钢水的电导率,当钢水中含有少量的渣子时,涡流就会减弱,而磁场强度就会变化。
磁场强度的变化可通过二级线圈产生的电压来检测。
这种低电压信号经放大处理后,可以显示出带渣量的多少,达到报警的设定值时系统就会产生报警并关闭钢包滑动水口。
1.2振动检测法钢水从钢包通过滑动水口、长水口流入中间包过程中,因有动量冲击,会引起长水口和与之相连的机械手产生较强的振动。
钢、渣比重不同,纯净钢水和钢水与钢渣混合物引起长水口振动的特征具有差别。
因此通过检测机械手的振动可以间接检测钢包下渣。
振动由长水口产生,经过机械臂传递到传感器,由传感器检测得到,并经过放大、滤波等预处理,然后由采集卡采样、A/D转换成数字信号送入计算机,进行分析处理、特征提取和模式识别。
当有钢渣时系统自动优化关闭滑动水口,同时发出报警指示信号。
2连铸钢包下渣的影响连铸钢包下渣是钢铁生产过程中非常重要的一个环节,它直接影响到钢铁的质量和生产效率。
连铸技术总结

连铸技术总结20XX年连铸车间工作总结今年以来,在公司和厂领导的正确带领下,在相关车间、科室的大力支持下,我连铸车间充分依靠全体员工,紧紧围绕今年我司工作部署和生产经营目标,以提高经济效益、促进企业发展为核心,同心协力,真抓实干,奋发图强,在各项工作中都取得了较好的成绩。
截止20XX年9月31日止,车间共生产铸坯1237539.04吨,比去年同期增加326284.87吨(今年3#高炉提供的铁水较多);铸坯合格率XX.X%,比公司要求的XX.X%高XX.X%;平均月产量137504.34吨,比去年每月增加36253.87吨;最高日产量5581.2吨(7月22日118炉),最高月产量150914.9吨(8月份),最高班产量964.1吨(6月15日3#连铸机丙班20炉);铸机台时产量91.37吨/小时,比去年同期增加3.55吨/小时;铸机作业率XX.X%,比去年同期降低XX.X%(因铁水不足,3台连铸机一般只生产两台机,总有一台机闲置);中间包平均包龄52.3炉/包,最高包龄66炉(30小时);最高连浇炉数179炉/组;结晶器铜管平均通钢量5340.5吨/支,比去年增加782.9吨/支;月平均漏钢次数为0.59次/万吨钢,比去年同期减少0.75次/万吨钢;全流率XX.X%,比去年同期提高XX.X%;钢水收得率XX.X%。
1、提高钢水收得率20XX年钢水收得率仅为XX.X%,最低的是去年9月只有XX.X%。
为此车间从今年6月份开始从各个环节严抓细管,并出台对应的管理措施:(1)定期校核行车和轧钢炉头电子称,确保其精度。
(2)减少非计划停浇事故。
(3)减少漏钢、顶坯、重接等次数。
(4)确保设备运行正常,减少因设备和人为操作原因造成的非定尺坯和弯坯数量。
(5)提高大包工在浇注末期分清钢水和红渣的能力,把钢水浇完。
(6)控制好切头和尾坯的尺寸,并减少废品。
(7)制订对标挖潜奖励措施,奖好罚差,提高职工积极性。
炼钢生产线中降低钢铁料消耗措施及实践
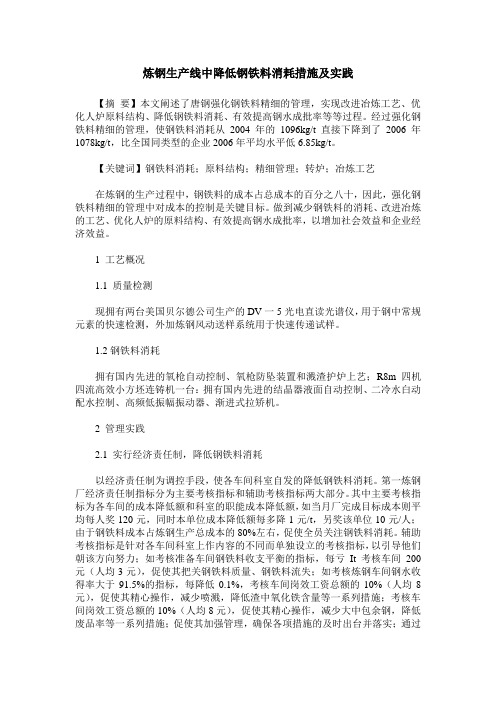
炼钢生产线中降低钢铁料消耗措施及实践【摘要】本文阐述了唐钢强化钢铁料精细的管理,实现改进冶炼工艺、优化人炉原料结构、降低钢铁料消耗、有效提高钢水成批率等等过程。
经过强化钢铁料精细的管理,使钢铁料消耗从2004年的1096kg/t直接下降到了2006年1078kg/t,比全国同类型的企业2006年平均水平低6.85kg/t。
【关键词】钢铁料消耗;原料结构;精细管理;转炉;冶炼工艺在炼钢的生产过程中,钢铁料的成本占总成本的百分之八十,因此,强化钢铁料精细的管理中对成本的控制是关键目标。
做到减少钢铁料的消耗、改进冶炼的工艺、优化人炉的原料结构、有效提高钢水成批率,以增加社会效益和企业经济效益。
1 工艺概况1.1 质量检测现拥有两台美国贝尔德公司生产的DV一5光电直读光谱仪,用于钢中常规元素的快速检测,外加炼钢风动送样系统用于快速传递试样。
1.2钢铁料消耗拥有国内先进的氧枪自动控制、氧枪防坠装置和溅渣护炉上艺;R8m四机四流高效小方坯连铸机一台:拥有国内先进的结晶器液面自动控制、二冷水白动配水控制、高频低振幅振动器、渐进式拉矫机。
2 管理实践2.1 实行经济责任制,降低钢铁料消耗以经济责任制为调控手段,使各车间科室自发的降低钢铁料消耗。
第一炼钢厂经济责任制指标分为主要考核指标和辅助考核指标两大部分。
其中主要考核指标为各车间的成本降低额和科室的职能成本降低额,如当月厂完成目标成本则平均每人奖120元,同时本单位成本降低额每多降1元/t,另奖该单位10元/人;由于钢铁料成本占炼钢生产总成本的80%左右,促使全员关注钢铁料消耗。
辅助考核指标是针对各车间科室上作内容的不同而单独设立的考核指标,以引导他们朝该方向努力;如考核准备车间钢铁料收支平衡的指标,每亏It考核车间200元(人均3元),促使其把关钢铁料质量、钢铁料流失;如考核炼钢车间钢水收得率大于91.5%的指标,每降低0.1%,考核车间岗效工资总额的10%(人均8元),促使其精心操作,减少喷溅,降低渣中氧化铁含量等一系列措施;考核车间岗效工资总额的10%(人均8元),促使其精心操作,减少大中包余钢,降低废品率等一系列措施;促使其加强管理,确保各项措施的及时出台并落实;通过以_L经济责任制的制定,使各车间科室自发的关注钢铁料消耗,全员千方百计想办法降低钢铁料消耗。
炼钢全流程降低钢铁料消耗的实践攻关
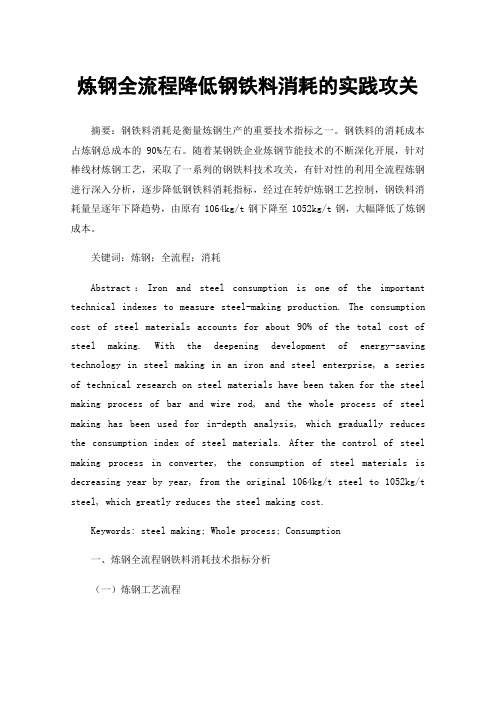
炼钢全流程降低钢铁料消耗的实践攻关摘要:钢铁料消耗是衡量炼钢生产的重要技术指标之一。
钢铁料的消耗成本占炼钢总成本的90%左右。
随着某钢铁企业炼钢节能技术的不断深化开展,针对棒线材炼钢工艺,采取了一系列的钢铁料技术攻关,有针对性的利用全流程炼钢进行深入分析,逐步降低钢铁料消耗指标,经过在转炉炼钢工艺控制,钢铁料消耗量呈逐年下降趋势,由原有1064kg/t钢下降至1052kg/t钢,大幅降低了炼钢成本。
关键词:炼钢;全流程;消耗Abstract:Iron and steel consumption is one of the important technical indexes to measure steel-making production. The consumption cost of steel materials accounts for about 90% of the total cost of steel making. With the deepening development of energy-saving technology in steel making in an iron and steel enterprise, a series of technical research on steel materials have been taken for the steel making process of bar and wire rod, and the whole process of steel making has been used for in-depth analysis, which gradually reduces the consumption index of steel materials. After the control of steel making process in converter, the consumption of steel materials is decreasing year by year, from the original 1064kg/t steel to 1052kg/t steel, which greatly reduces the steel making cost.Keywords: steel making; Whole process; Consumption一、炼钢全流程钢铁料消耗技术指标分析(一)炼钢工艺流程图1 某钢铁企业炼钢工艺流程简图(二)钢铁料消耗统计分析某钢铁企业第二钢扎厂钢铁料消耗统计口径如下:钢铁料消耗(kg/t)=(铁水+废钢)(kg)/合格钢坯产量(t)。
- 1、下载文档前请自行甄别文档内容的完整性,平台不提供额外的编辑、内容补充、找答案等附加服务。
- 2、"仅部分预览"的文档,不可在线预览部分如存在完整性等问题,可反馈申请退款(可完整预览的文档不适用该条件!)。
- 3、如文档侵犯您的权益,请联系客服反馈,我们会尽快为您处理(人工客服工作时间:9:00-18:30)。
到低顶 低用
量
低顶渣 渣量 3 钢包增加
的 量采用钢包程加稳定钢包
度等工艺 改 钢包
期钢渣 性,
钢渣
程度, 有 钢渣分离,
钢包内残留钢水 能
包?
(五)控制钢渣漩涡形成及临界高度
在钢包浇注末期,钢水液面下降到一定高
度时, 钢 在
能及
的相
用下产生
,直
水
口, 在此 程 钢渣
不
到 包,
钢渣
化, 样不
钢水二次 化, 产生 物 钢
2019年第1期
柳钢科技
29
关"download-按f
19
r
降低钢包浇余提高钢)收得翩.践 □张德俊;王志国,李栋』耀环,■柱国利二(转/106),
连铸生产过程中,控制每炉钢包浇注后期
钢渣下渣量的大小,是钢铁企业普遍面临的现
实问题。如果钢包下渣量过大不但会降低钢水
的结净度,影响铸坯质量,而且还会加快中间
为尽可能地降低钢 余,提高钢水
率,
钢厂对钢
部采用倾斜式的砌筑方
法,即垫高 除水口的其它 ,
一定
的
水口 倾斜, 于
期钢渣 流
水口,
砌筑一 程 上
钢
,也 于
的
使用 也 钢厂
期通过 大 臂的平衡使钢渣迅速流
水口 ,但同时也增加了操作难 增大了
全风险456 钢钢厂一钢 部大部分为
平底砌筑,在离水口位置300 ~ 400 mm处开始
过对比、分析电压变化信号,判断出钢柱中含渣
量的变化及大小,当达到某个设定值时,触发声
光报警提醒操作工及时关闭水口。该套系统投入
使用以来一定程度上提高了钢水 率,
钢渣流入中 ,提高钢水 度,
工
人的
度。
实际生产过程中,通过跟
踪观发现,
钢 钢水:比较
, 时 工观到
l~2t钢水。为
此,进一化进:(1
系统中
通过 、 时 为
炼钢成本增加,造成极大的资源浪费。因此,
钢包下渣量的控制 理
面的因素。年
钢包注后期
控制钢渣量的
, 如 钢渣
理
临 度 钢渣
等理 研
的
,
果
用
注 期钢水 炉
渣 其量的 小 不。目前,普遍采用
的是基于重力差异、电磁场、超声波、红外信
号 振 式等原理开发出的 下渣
,具体应用中 其特点存在的问
题。因此,各钢企根据实际选用下渣检测技术
来控制下渣量具有独特性。近年来柳钢转炉炼
钢厂出于对于自身发展的需要,不断加大
区钢包后期钢渣流动的研究和实践,优化、改
进下渣
加强系统性管控,2016年
150 t钢包平均浇余146.56 kg, 2017年为85.7
kg,降低了 41.52%,钢水
提高0.03%,
增加合格铸坯1 434 to 量的技术措施。
种对夹杂物的 求 严格, 普通的建筑用钢、
工业用钢如HRB400、Q235等钢种的要求相对较 低一 由于钢中夹杂物的数量、形状、大小及组
成 复杂,因控的方法手段、控制的重点环
也各相
渣 系统作为其中一个环既
证
大量的炉渣进入中 污染钢水、侵
蚀耐材,R 尽量减少钢包中残留的钢水,提高钢
水 率,如口果使用 的 参数和方法来生产
钢,势必会影响质量指标和经济技术指标。
对,
渣
报警的基础上,对 的
钢增加了延时报警功.,通过人为设延时报警
时来提醒操作工关闭钢水口 实际生产跟踪
中发现,投入使用了延时报警功的钢包翻渣时很
发现余钢,对质量求高的钢,则取消延
时报警功 訓高下渣
,尽可能地减
钢渣进入中
钢包翻渣时明显观察到
残留钢水
(三) 避免钢包底部产生凹陷
臂 水平,
钢
上出现前高低,钢渣法流入水
口的
(四) 改善钢渣流动性
生产过程中, 钢 钢水通过钢 上水口、
水口 断 入中 , 钢
钢水会 来
, 炉渣的 会 来 高, 到
期钢
大量炉渣 量钢水的 物 通过实
际跟踪调查和对比分析发现,板坯钢水经过二次
,钢
期炉渣的 、
、
、
、
以及流 性对渣、 钢的分
影响 大 由于 钢 成分 一 , 对
包耐火材料的侵蚀,缩短其使用寿命,增加中
间包渣量,甚至导致拉漏事故,影响连铸正常
生产的进行。钢包下渣量少能够有效地阻止大
量钢渣流入中间包,但是钢包内不可避免地还
残留大量的纯净钢水,据宝钢申屠理锋等人研
ቤተ መጻሕፍቲ ባይዱ
, 钢包浇注结 ,3001的钢包 「浇余
6t,其中纯净钢水 3t以上,
的钢
水一般会当钢渣处理,导致钢水收得率降低,
够明显观察到有1~2t钢水,曾尝试采用大量
下渣后人工关闭水口、钢包二次
低下
渣
度等
不明显。
板坯
控铝钢 含量均较低且稳定造渣工艺采用高
度白渣精炼,钢渣
较大,钢渣分离
较硅 钢要好。因此,板坯钢水的要
分离
1 化造渣工艺及 工艺 高钢渣 ,在 顶二元渣碱度相对稳定的前
下,
低顶渣 AI2O3的
渣度的的;(2)在一定程度
上的电 来
大 小 渣电压信号 值, 达到 时
渣
的的。⑵由于下渣 电压
信号
,
通过 大 分析使用,
渣
钢
电、电一
到电磁
大, 因 用
,
信号 到
3 对于
钢
的电 信号 进
,
作
的
,高钢水对中 的
期及 、
4期
,
渣
及 报警 报
率、不报率<3%。
(二)下渣延时报警技术
钢种的不同用途及特性决定了对钢水洁净度
的要求 ,女口管钢、汽车用钢、帘 钢等钢
文总结控制钢包
措施及方法
(-)优化改进下渣检测系统
柳钢转炉炼钢厂一区有5台连铸机,钢包
下渣
用国内某公司开发的
电流感应的控制 ,其主要运行原理是
钢包底部上水口位置 部安装一个环形的
传感器,钢包注未期,携带钢渣的钢水
30
柳钢科技
2019年第1期
进入水口,由于钢渣的导电率仅为钢水的
1/1 000,因此水口中含钢渣的钢柱将引起电磁场 电流的变化,进而影响磁场输出电压的变化,通
水, 且
下渣
, 此时
关闭钢包水口
低钢水
率。因此,研
究钢包
高度控制方法 高钢水质量
率具有重要意义?为抑制 的产生,
降低反应器(钢包)的
临高度,人们
进行了大量研究工, 出了许多技术性
,如李德军等人 出的上躲、下藏、抑制
等方法:上躲法即钢包在滑块关闭 ,£
降低
高 , 以 于钢渣 水口 流
实际生产过程中,
发现由于出钢时
高 钢水的
侵蚀, 钢 部出现
大小不一的凹坑,比如按500 mm X 300 mm x 200
mm
,则
200 kg钢水无法流入中
,如果出现
量增加
、大的
,则
期钢 残留钢水会
因
1 及时 发现、 复钢 部的 ,
钢 部的平 对于
余 重大 2
时 期 量钢
钢 的 控 及对
夹杂物控 即
2019年第1期
工作实践
31
等要求也不一样,因此精炼顶渣改质与否及造
渣具体工艺也大不相同。所以板坯二次精炼采
取不同顶渣渣系的造渣工艺,不同渣系的熔渣
物化性质,直接影响着钢渣分离的难易程度。
2015年~ 2016年,在生产板坯低碳低硅控铝钢 种等时,钢包翻渣余钢量突然增加,倒包时能