【通用】胀管施工工艺.doc
胀管工艺方案
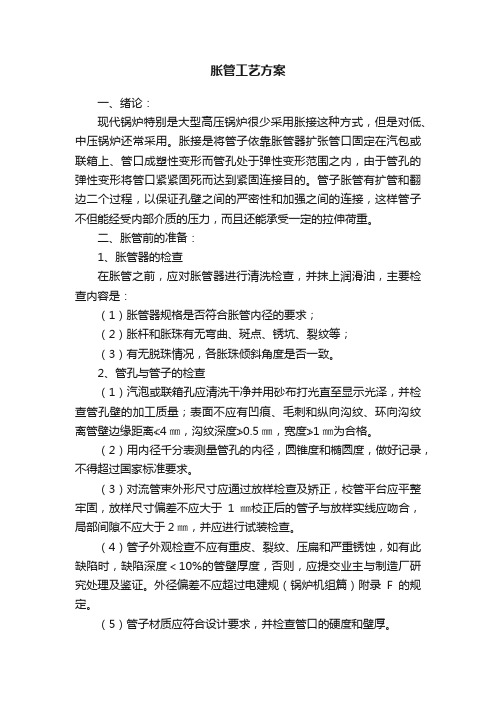
胀管工艺方案一、绪论:现代锅炉特别是大型高压锅炉很少采用胀接这种方式,但是对低、中压锅炉还常采用。
胀接是将管子依靠胀管器扩张管口固定在汽包或联箱上、管口成塑性变形而管孔处于弹性变形范围之内,由于管孔的弹性变形将管口紧紧固死而达到紧固连接目的。
管子胀管有扩管和翻边二个过程,以保证孔壁之间的严密性和加强之间的连接,这样管子不但能经受内部介质的压力,而且还能承受一定的拉伸荷重。
二、胀管前的准备:1、胀管器的检查在胀管之前,应对胀管器进行清洗检查,并抹上润滑油,主要检查内容是:(1)胀管器规格是否符合胀管内径的要求;(2)胀杆和胀珠有无弯曲、斑点、锈坑、裂纹等;(3)有无脱珠情况,各胀珠倾斜角度是否一致。
2、管孔与管子的检查(1)汽泡或联箱孔应清洗干净并用砂布打光直至显示光泽,并检查管孔壁的加工质量;表面不应有凹痕、毛刺和纵向沟纹、环向沟纹离管壁边缘距离≮4㎜,沟纹深度≯0.5㎜,宽度≯1㎜为合格。
(2)用内径千分表测量管孔的内径,圆锥度和椭圆度,做好记录,不得超过国家标准要求。
(3)对流管束外形尺寸应通过放样检查及矫正,校管平台应平整牢固,放样尺寸偏差不应大于1㎜校正后的管子与放样实线应吻合,局部间隙不应大于2㎜,并应进行试装检查。
(4)管子外观检查不应有重皮、裂纹、压扁和严重锈蚀,如有此缺陷时,缺陷深度<10%的管壁厚度,否则,应提交业主与制造厂研究处理及鉴证。
外径偏差不应超过电建规(锅炉机组篇)附录F的规定。
(5)管子材质应符合设计要求,并检查管口的硬度和壁厚。
(6)管口端面应与管中心垂直,偏斜值不应大于2%的管外径。
3、管子通球试验与管口处理(1)管子端口硬度超过HB170,同时高于管孔壁的硬度时应对管端进行退火。
退火方法采用铅溶法,退火长度不少于100㎜,加热温度控制在600~650℃。
保温采用干石灰粉进行。
(2)退火后的管端内外壁100㎜范围内应进行打磨,直致显示出金属光泽。
并测量出打磨后的管外径尺寸,与管孔直径选配编号,管外径应比孔径小 0.5㎜左右为宜。
胀管施工方案
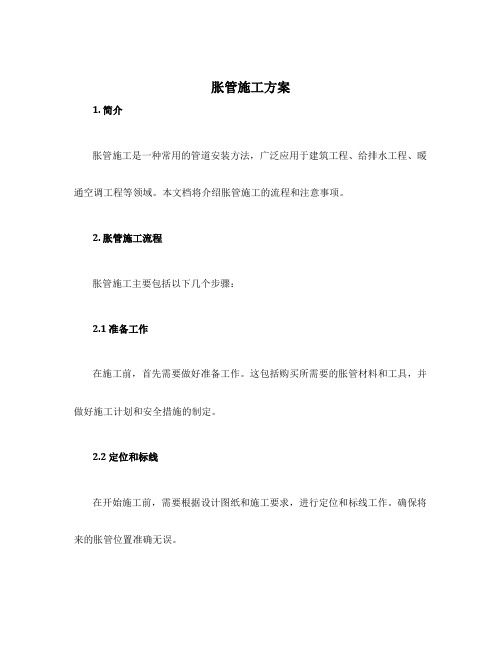
胀管施工方案1. 简介胀管施工是一种常用的管道安装方法,广泛应用于建筑工程、给排水工程、暖通空调工程等领域。
本文档将介绍胀管施工的流程和注意事项。
2. 胀管施工流程胀管施工主要包括以下几个步骤:2.1 准备工作在施工前,首先需要做好准备工作。
这包括购买所需要的胀管材料和工具,并做好施工计划和安全措施的制定。
2.2 定位和标线在开始施工前,需要根据设计图纸和施工要求,进行定位和标线工作。
确保将来的胀管位置准确无误。
2.3 凿洞根据标线,在需要胀管的位置进行凿洞工作。
洞的大小和形状应与胀管的要求相匹配。
2.4 安装胀管将胀管插入凿洞处,确保胀管与凿洞之间有足够的空隙,以便胀管能够膨胀至设计要求。
2.5 固定和密封在胀管安装完毕后,需要进行固定和密封工作。
确保胀管稳定固定,并使用密封材料将胀管与凿洞之间的间隙填充密封,防止漏水。
2.6 检查和测试在胀管施工完成后,需要进行检查和测试工作。
检查胀管的安装质量和密封性能,并进行相应的试验。
3. 胀管施工注意事项在进行胀管施工时,需要注意以下几个事项:3.1 工具和材料选择选择适合的工具和材料对于胀管施工的质量和效率至关重要。
确保所使用的胀管和固定材料具有良好的质量和合适的规格。
3.2 胀管位置确定胀管的位置应根据实际施工情况和设计要求进行确定。
在进行凿洞之前,必须对胀管位置进行仔细测量和标记。
3.3 胀管与凿洞间隙胀管与凿洞之间应保留一定的间隙,以确保胀管能够膨胀至设计要求。
过大的间隙会导致胀管固定不牢,过小的间隙会妨碍胀管的膨胀。
3.4 胀管固定和密封胀管安装完毕后,必须进行固定和密封工作。
固定材料应使用符合要求的胀管固定夹或支架,密封材料应具有良好的密封性能。
3.5 检查和测试施工完成后,必须进行胀管的检查和测试工作。
检查胀管的安装质量和密封性能,并进行相应的试验,确保施工符合要求。
4. 结论通过本文档,我们了解了胀管施工的流程和注意事项。
在进行胀管施工时,必须做好准备工作,按照流程进行施工,并注意选择合适的工具和材料。
锅炉胀管施工工艺11

锅炉胀管施工工法1、前言目前,锅炉设备日益广泛地应用于现代工业的各个部门,其中大型的散装锅炉具有功率大,效率高的特点,成为工业及采暖不可缺少的热源。
大型散装锅炉的安装中,锅炉管安装是最重要的分项工程之一。
2、工法特点锅炉胀管具有不易损坏管孔、更换管子方便的特点。
3、适用范围3.1 适用于工作介质压力小于或等于2.5Mpa,壁温不超过400℃的新装工业锅炉.3。
2 胀接管子的锅筒和管板的厚度不应小于12mm。
胀接管孔间的距离不应小于19mm。
外径大于102mm的管子不宜采用账接。
4、工艺原理锅炉壁是一种弹性变形材料,相对的说退火后的管端是塑性变形材料,胀接时,锅筒板孔内壁和管子外壁间就产生一对作用力.在该作用下,使板孔内壁与管外壁紧密啮全合达到密封作用的目的。
5、施工工艺流程及工艺要点5.1、工艺流程炉管检查、校正和被胀管端处理→锅炉管孔清洗、检查、处理、编号→管孔与炉管的选配→试胀试验→穿管→胀接→水压试验5。
1。
1、安装对流管和水冷壁管程序如图:5。
1.2、胀管工艺程序及质量控制如图:5.2、施工工艺要点5.2.1、管端退火处理当管子硬度值HB>170时或管子硬度>板孔壁处的硬度时,管端均需作退火处理温度控制在600~650℃,恒温10—15分钟. 管端退火处理方法一般有反射法,铅溶法及电加热法等.我们采用的是铅溶法管端退火法:(1)配备温度监测仪器,退火过程对退火温度进行适时监控. (2)布置加热铅浴箱、缓冷石棉灰保温棚和搭设退火管架。
(3) 将适量铅块置于退火铅浴箱内,并对铅浴箱进行加热。
(4)铅块完全溶解(温度约为350~400 ℃)后,将适量退火管子一端插入铅液中进行加热,控制插入深度不少于100 mm。
(5) 加热铅浴箱,使铅液温度升温至600 ℃后,控制铅液温度不超过650 ℃,持续时间不少于15 min;而后取出退火管子,清除挂铅插入干燥石棉灰中缓冷保温8 h以上。
(6)抽查退火后的管端硬度5。
主要污水管线胀管更换施工工艺概述:
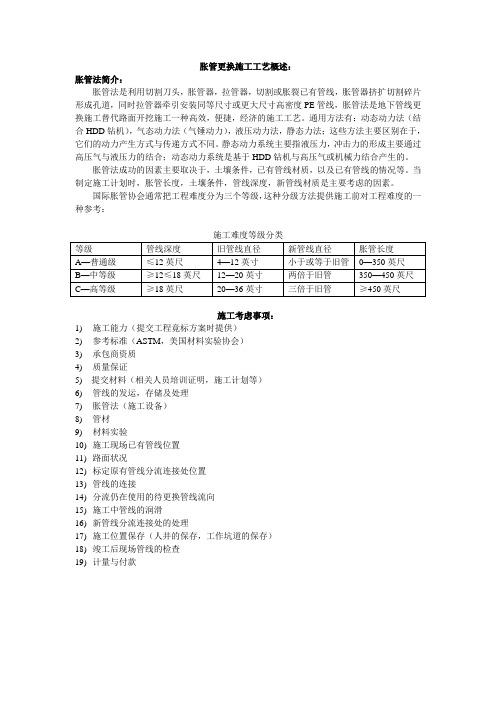
胀管更换施工工艺概述:
胀管法简介:
胀管法是利用切割刀头,胀管器,拉管器,切割或胀裂已有管线,胀管器挤扩切割碎片形成孔道,同时拉管器牵引安装同等尺寸或更大尺寸高密度PE管线,胀管法是地下管线更换施工替代路面开挖施工一种高效,便捷,经济的施工工艺。
通用方法有:动态动力法(结合HDD钻机),气态动力法(气锤动力),液压动力法,静态力法;这些方法主要区别在于,它们的动力产生方式与传递方式不同。
静态动力系统主要指液压力,冲击力的形成主要通过高压气与液压力的结合;动态动力系统是基于HDD钻机与高压气或机械力结合产生的。
胀管法成功的因素主要取决于,土壤条件,已有管线材质,以及已有管线的情况等。
当制定施工计划时,胀管长度,土壤条件,管线深度,新管线材质是主要考虑的因素。
国际胀管协会通常把工程难度分为三个等级,这种分级方法提供施工前对工程难度的一种参考:
施工难度等级分类
施工考虑事项:
1)施工能力(提交工程竟标方案时提供)
2)参考标准(ASTM,美国材料实验协会)
3)承包商资质
4)质量保证
5)提交材料(相关人员培训证明,施工计划等)
6)管线的发运,存储及处理
7)胀管法(施工设备)
8)管材
9)材料实验
10)施工现场已有管线位置
11)路面状况
12)标定原有管线分流连接处位置
13)管线的连接
14)分流仍在使用的待更换管线流向
15)施工中管线的润滑
16)新管线分流连接处的处理
17)施工位置保存(人井的保存,工作坑道的保存)
18)竣工后现场管线的检查
19)计量与付款。
胀管技术

• IP 2 - New 200mm PE pipe insertion pit (2 way), 4m Long x 1m Wide. Reconnect existing branch service main to new 200mm PE water main.
土质条件
好
▪ 回填土
▪ 可挤压黏土
难度系数
▪ 疏松鹅卵石
▪ 沙滩 &流沙
▪ 高密度的黏土
差
▪ 沙石层
胀管法受力分析(胀管设备的选择)
• 四个独立的受力组成
– 胀破力 – 摩擦力 – 土壤挤压力 – 管线重力 – 其他力
受力分析图
dor dir
Fscp
Fbp Fsc Fscn
Ff
Fb
Fbn
CL
Replacement Pipe
准备与工作人井的开挖
• 清洗现有旧管线与CCTV勘察 • 周围管线的勘探 • 通知用户 – 临时管线的停止使用 • 临时供水管线的安装 • 管线的热熔(HDPE) • 人井的开挖 • 交通改道&施工现场的安全 • 胀管 & 新管线的安装
• 设计 • 施工
场地考察与预设计
• 排土量的计算 • 增加尺寸考虑 • 现有旧管线的类型(材质) • 土质条件 • 新管线材质 • 周围管线的定位
胀管法施工中的排土量的计算
• 在胀管过程中管道碎片与土壤的体积排量将要变化 • 确切的估算将有多少土壤被排出 • 这些土壤都去了那里?
胀管技术
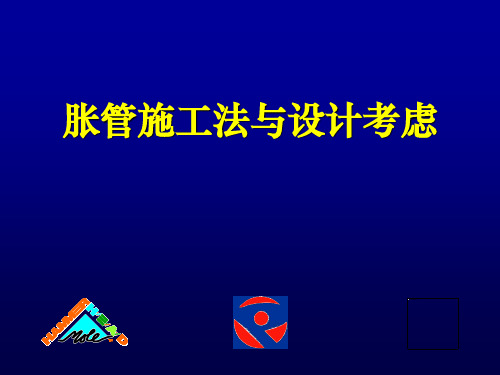
10
.5 d Right 1 d Right 1.5 d right
5
2.5 d Right 3.5 d Right 4.5 d Right
0
6 d Right
-5 90 110 130
Elapsed Time (min.)
150
170
Measurement logged during an actual 14’ to 28” major up-sizing replacement project, the depth-ofcover is approx. 10 feet and initial up-heave recorded = 7mm (0.276”) and settled at neg. 5mm (neg. 0.25”) after 2 ½ hours.
• MP 1 & MP 3 - HB5058 machine pit, 2.4m Long x 1m Wide; • MP 2 – HB5058 machine pit, 2.4m Long x 1m Wide. Also location for new service valve and new 100mm supply main tee off to apartment building; • IP 1 – New 200mm PE pipe insertion pit (2 way), 4m Long x 1m Wide. Also location for new valve chamber if required; • IP 2 - New 200mm PE pipe insertion pit (2 way), 4m Long x 1m Wide. Reconnect existing branch service main to new 200mm PE water main.
胀管施工方案

胀管施工方案1. 胀管施工概述胀管施工是一种用于增强地下工程土体稳定性的施工工艺。
通过在地下土体中注入高压水泥浆,形成密集的胀管体系,以增加土体的承载力和抗冲刷能力。
本文档将介绍胀管施工的具体步骤和注意事项。
2. 胀管施工步骤2.1 前期准备在进行胀管施工之前,需要进行一系列的前期准备工作,包括土体勘察、方案设计、设备准备等。
具体步骤如下:1.进行土体勘察,了解施工地的地质情况、土体特性等。
2.根据勘察结果,设计合理的胀管施工方案,包括胀管的数量、位置、深度等参数。
3.确定施工所需的设备和材料,包括胀管机、水泥浆、输送管道等。
2.2 施工操作胀管施工主要包括以下几个操作步骤:1.预先准备工作:搭建施工平台、清理施工现场等。
2.打孔准备:根据方案设计要求,在施工地点进行孔洞的打开。
3.胀管注浆:将水泥浆注入孔洞,通过高压注入设备实现胀管。
注浆时要确保注入的水泥浆充分混合均匀。
4.胀管养护:完成注浆后,需要对胀管进行养护,使其固化和强化。
3. 胀管施工注意事项在进行胀管施工时,需要注意以下几点:1.施工地点的选择应避免存在地下水、沉积物和较软的土体等不利因素。
2.在胀管施工过程中,需严格按照方案设计要求操作,并确保注浆设备的正常运行。
3.胀管注浆过程中,需要随时监测注浆的压力和流量,确保注入量和注入速度的控制。
4.在胀管养护期间,应加强施工现场的监测和巡视,及时处理可能出现的问题。
5.胀管施工完成后,需进行验收和检测,确保施工质量符合要求。
4. 安全措施胀管施工是一项复杂的地下工程施工操作,为确保施工过程中的安全,需要采取以下措施:1.严格遵守相关施工安全操作规程和标准,保证施工人员的安全福利。
2.在施工现场设置明显的警示标志,确保周围人员能够明确识别施工区域。
3.定期进行设备检查和维护,确保施工设备的正常运行。
4.建立完善的施工监测和应急预案,应对可能出现的突发状况。
5.提供相关的安全培训和教育,提高施工人员的安全意识和应急处理能力。
胀管施工工艺

引言:胀管施工工艺是一种常用的管道连接方法,具有施工简单、连接牢固等优点。
本文将从材料准备、工具器具、施工步骤、注意事项和效果评估五个方面详细介绍胀管施工工艺的具体内容。
概述:胀管施工工艺是一种利用压力将金属管道扩张,将连接管道或配件插入其中并实现连接的技术方法。
它广泛应用于建筑、石化、供水、暖通等领域。
本文将分别从材料准备、工具器具、施工步骤、注意事项和效果评估五个方面介绍胀管施工工艺。
正文内容:一、材料准备1.胀管工具:包括手持胀管器、电动胀管器等,根据实际需要选择合适的工具。
2.管道和配件:选择合适的材质和规格的管道和配件,确保其质量合格。
3.胀管药剂:根据材料的要求选用适当的药剂,常见的有胀管凝固剂和防腐剂。
二、工具器具1.手持胀管器:手持胀管器是一种常用的胀管工具,适用于小口径管道的胀管作业。
使用时需要掌握合适的力度和速度,避免过分用力导致管道变形。
2.电动胀管器:电动胀管器是一种高效的胀管工具,适用于大口径管道的胀管作业。
使用时需要注意电源稳定和转速控制,避免对管道造成损坏。
三、施工步骤1.准备工作:清洁管道和配件表面,确保无油、无尘和无杂质。
2.胀管操作:将胀管工具插入管道一段长度,以适当的力度和速度推进,直至达到胀管要求的直径。
3.连接管道:将需要连接的管道或配件插入胀管管道中,确保插入深度合适。
4.固定管道:使用合适的固定装置固定管道,确保连接牢固。
5.检查验收:对胀管连接进行检查,确保胀管质量符合要求。
四、注意事项1.安全注意:在使用胀管工具时要注意安全,避免因操作不当造成人身伤害。
2.材料选用:根据工程要求选择合适的材料,确保其质量和可靠性。
3.施工环境:确保施工环境干燥、清洁,避免灰尘和杂质对管道连接造成影响。
4.施工操作:掌握合适的力度和速度,避免过度胀管或胀管不足导致连接不牢固。
5.质量检查:在施工完成后进行质量检查,确保连接的牢固性和密封性。
五、效果评估胀管施工工艺连接的管道具有牢固、密封性好的特点,能够满足工程的要求。
胀管工艺
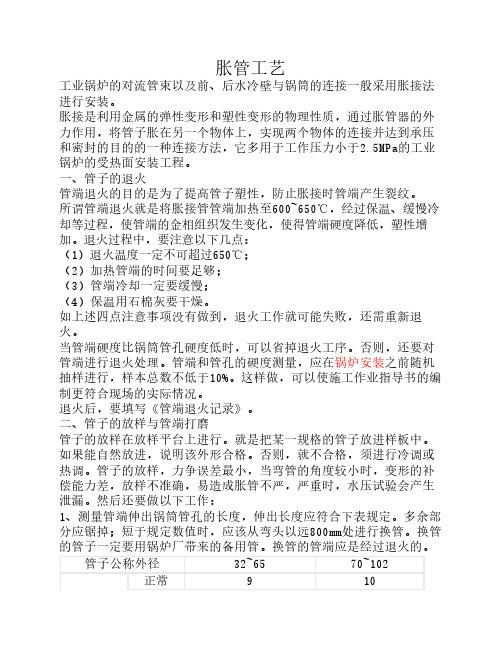
胀管工艺工业锅炉的对流管束以及前、后水冷壁与锅筒的连接一般采用胀接法进行安装。
胀接是利用金属的弹性变形和塑性变形的物理性质,通过胀管器的外力作用,将管子胀在另一个物体上,实现两个物体的连接并达到承压和密封的目的的一种连接方法,它多用于工作压力小于2.5MPa的工业锅炉的受热面安装工程。
一、管子的退火管端退火的目的是为了提高管子塑性,防止胀接时管端产生裂纹。
所谓管端退火就是将胀接管管端加热至600~650℃,经过保温、缓慢冷却等过程,使管端的金相组织发生变化,使得管端硬度降低,塑性增加。
退火过程中,要注意以下几点:(1)退火温度一定不可超过650℃;(2)加热管端的时间要足够;(3)管端冷却一定要缓慢;(4)保温用石棉灰要干燥。
如上述四点注意事项没有做到,退火工作就可能失败,还需重新退火。
当管端硬度比锅筒管孔硬度低时,可以省掉退火工序。
否则,还要对管端进行退火处理。
管端和管孔的硬度测量,应在锅炉安装之前随机抽样进行,样本总数不低于10%。
这样做,可以使施工作业指导书的编制更符合现场的实际情况。
退火后,要填写《管端退火记录》。
二、管子的放样与管端打磨管子的放样在放样平台上进行。
就是把某一规格的管子放进样板中。
如果能自然放进,说明该外形合格。
否则,就不合格,须进行冷调或热调。
管子的放样,力争误差最小,当弯管的角度较小时,变形的补偿能力差,放样不准确,易造成胀管不严,严重时,水压试验会产生泄漏。
然后还要做以下工作:1、测量管端伸出锅筒管孔的长度,伸出长度应符合下表规定。
多余部分应锯掉;短于规定数值时,应该从弯头以远800mm处进行换管。
换管的管子一定要用锅炉厂带来的备用管。
换管的管端应是经过退火的。
管子公称外径32~6570~102正常910伸出长度最大1112最小78管端伸出管孔的长度2、仔细检查每根管子裂纹、重皮、锈蚀凹坑等缺陷。
当缺陷严重时,应进行有缺陷管段的换管工作。
3、因胀接管端有氧化皮、锈蚀斑点、刻痕等污物和缺陷,胀接之前要将其彻底清除,以保证胀接质量。
胀管技术施工工法(2)
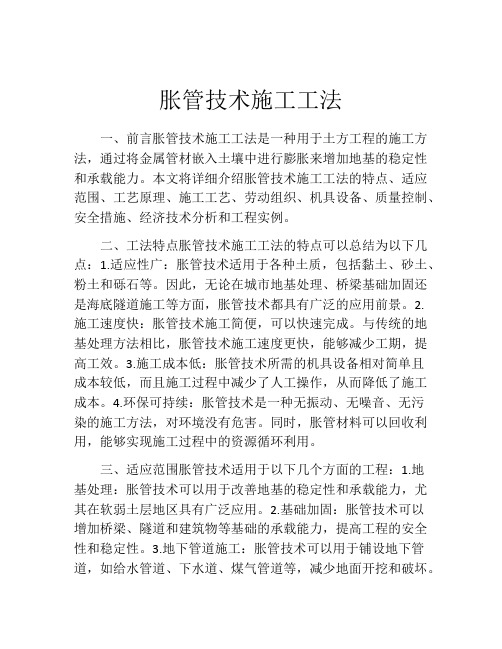
胀管技术施工工法一、前言胀管技术施工工法是一种用于土方工程的施工方法,通过将金属管材嵌入土壤中进行膨胀来增加地基的稳定性和承载能力。
本文将详细介绍胀管技术施工工法的特点、适应范围、工艺原理、施工工艺、劳动组织、机具设备、质量控制、安全措施、经济技术分析和工程实例。
二、工法特点胀管技术施工工法的特点可以总结为以下几点:1.适应性广:胀管技术适用于各种土质,包括黏土、砂土、粉土和砾石等。
因此,无论在城市地基处理、桥梁基础加固还是海底隧道施工等方面,胀管技术都具有广泛的应用前景。
2.施工速度快:胀管技术施工简便,可以快速完成。
与传统的地基处理方法相比,胀管技术施工速度更快,能够减少工期,提高工效。
3.施工成本低:胀管技术所需的机具设备相对简单且成本较低,而且施工过程中减少了人工操作,从而降低了施工成本。
4.环保可持续:胀管技术是一种无振动、无噪音、无污染的施工方法,对环境没有危害。
同时,胀管材料可以回收利用,能够实现施工过程中的资源循环利用。
三、适应范围胀管技术适用于以下几个方面的工程:1.地基处理:胀管技术可以用于改善地基的稳定性和承载能力,尤其在软弱土层地区具有广泛应用。
2.基础加固:胀管技术可以增加桥梁、隧道和建筑物等基础的承载能力,提高工程的安全性和稳定性。
3.地下管道施工:胀管技术可以用于铺设地下管道,如给水管道、下水道、煤气管道等,减少地面开挖和破坏。
4.海底隧道施工:胀管技术可以用于海底隧道的施工,通过在海底土层中嵌入胀管来增加隧道的稳定性和承载能力。
四、工艺原理胀管技术施工工法的工艺原理是通过胀管材料的膨胀力来增加地基的稳定性和承载能力。
具体来说,胀管施工工法在施工前需要先进行钻孔,将金属管材嵌入土体中,并填注压浆材料以提高管材与土体的粘结力。
然后,在管材内注入高压液体,使管材膨胀,并与土壤发生挤压作用,从而提高地基的稳定性和承载能力。
五、施工工艺胀管技术的施工工艺可以分为以下几个阶段:1.现场准备:确定施工地点和孔径,清理施工地面,搭建施工平台和围护结构。
胀管工艺

GB151-1999标准中规定,强度胀接适用于设计压力≤4MPa、设计温度≤300℃、无剧烈振动、无过大温度变化及无应力腐蚀的场合;强度焊接适用于振动较小和无间隙腐蚀的场合;胀、焊并用适用于密封性能较高、承受振动或疲劳载荷、有间隙腐蚀、采用复合管板的场合。
由此可见,单纯胀接或强度焊接的连接方式使用条件是有限制的。
胀、焊并用结构由于能有效地阻尼管束振动对焊口的损伤,避免间隙腐蚀,并且有比单纯胀接或强度焊具有更高的强度和密封性,因而得到广泛采用。
目前对常规的换热管通常采用“贴胀+强度焊”的模式;而重要的或使用条件苛刻的换热器则要求采用“强度胀+密封焊”的模式。
胀、焊并用结构按胀接与焊接在工序中的先后次序可分为先胀后焊和先焊后胀两种。
1 先胀后焊管子与管板胀接后,在管端应留有15mm长的未胀管腔,以避免胀接应力与焊接应力的迭加,减少焊接应力对胀接的影响,15mm的未胀管段与管板孔之间存在一个间隙(见图1)。
在焊接时,由于高温熔化金属的影响,间隙内气体被加热而急剧膨胀。
据国外资料介绍,间隙腔内压力在焊接收口时可达到200~300MPa 的超高压状态。
间隙腔的高温高压气体在外泄时对强度胀的密封性能造成致命的损伤,且焊缝收口处亦将留下肉眼难以觉察的针孔。
目前通常采用的机械胀接,由于对焊接裂纹、气孔等敏感性很强的润滑油渗透进入了这些间隙,焊接时产生缺陷的现象就更加严重。
这些渗透进入间隙的油污很难清除干净,所以采用先胀后焊工艺,不宜采用机械胀的方式。
由于贴胀是不耐压的,但可以消除管子与管板管孔的间隙,所以能有效的阻尼管束振动到管口的焊接部位。
但是采用常规手工或机械控制的机械胀接无法达到均匀的贴胀要求,而采用由电脑控制胀接压力的液袋式胀管机胀接时可方便、均匀地实现贴胀要求。
采用液袋式胀管机胀接时,为了使胀接结果达到理想效果,胀接前管子与管板孔的尺寸配合在设计制造上必须符合较为严格的要求。
只有这样对于常规设计的“贴胀+强度焊”可采用先胀后焊的方式,而对特殊设计的“强度胀+强度焊”则可采用先贴胀,再强度焊,最后强度胀的方法。
胀管工艺

胀管工艺规程一、胀接管子的技术要求1、胀接管子外表面不得有重皮、压扁、裂纹等表面缺陷,胀接管端不得有纵向刻痕。
如有横向刻横、麻点等缺陷时,缺陷深度不超过管子公称壁厚的10%。
2、胀接管子的端面倾斜度应不大于管子公称外径的1.5%,且最大不超过1mm 。
3、管板材料的硬度高于换热管材料硬度即可,当换热管硬度大于管板硬度时,应进行退火处理,一般管端退火长度应不小于100mm,且比管板厚度多至少15~30mm。
4、胀管前应对管端进行清理A、碳钢管端外表面进行除锈磨光,磨光长度不小于50mm.除锈磨光后的表面不得有起皮,凹痕,裂纹和纵向沟槽等缺陷,磨光后的最小外径符合表1规定。
管端内表面应无严重腐蚀和铁屑等杂物并清除毛刺。
不锈钢管端应清除毛刺。
B、碳钢磨光后的管子应及时胀接,如不能则应妥善保管,防止再次生锈。
如生锈应重新打磨,磨光后的最小外径符合表1规定。
二、胀接管孔的技术要求1、用汽油等溶剂清洗管孔壁上的油污,再用细纱布打磨残留锈蚀,并去除管孔边缘毛刺,打磨后管孔壁的最大粗糙度不大于6.3。
2、清理后的管孔壁不得有纵向刻痕,个别管孔允许有一条螺旋形或环形刻槽,刻槽深度不超过0.5mm,宽度不得超过1mm,刻痕距管孔端部的距离不小于4mm。
3、管孔尺寸按GB151-1999 5.6.4规定。
见表2、表3。
4、如管孔直径超差,超差数值不得超过标准偏差值的50%。
当管孔不大于500时,超差孔数不得超过总数的2%,且不超过5个。
当管孔大于500时,超差孔数不得超过总数的1%,且不超过10个。
对于超差管孔,在管板上作出明显标记。
5、管孔加工后,宜采用机械式挤光器挤光管孔,以提高管孔内壁表面硬度和减少粗糙度,以利于胀接。
Ⅱ级管束表2三、胀管设备电动式机械胀管机和相应胀管器具液压胀管机和相应胀管器具四、穿管1、按照每个胀接面总数的10%,且不多于30根,不少于5根,随机测量管孔直径D,管端壁厚t,计算出D和t的算术平均值,并做好记录。
胀接通用工艺

胀接通用工艺1. 总则:本通用工艺适用于管壳式换热器管板与管子的胀接。
2 胀管前准备2.1 管端及管板必须清理干净,不得有油渍污物、毛刺、铁屑、锈蚀等杂物;管孔表面不得有影响紧密性的缺陷,如贯通的纵向或螺旋状刻痕等。
2.2 测量管板厚度,检查所领的胀管器是否符合要求。
2.3 准备润滑油及冷却用油。
3 胀管长度3.1 胀接连接时,其胀接长度不得伸出管板背面(壳程侧),换热管的胀接部分与非胀接部分应圆滑过渡,不得有急剧的棱角。
4 胀管率ρ对于钢管和钢管板,ρ=12~18%为强度胀接;ρ=7~10%为紧密胀接;ρ=3~7%为贴合胀接,不能保证联接强度和严密度。
过大的ρ会使管壁加工硬化严重,甚至发生裂纹,胀接强度也会降低。
如果管子直径较大,管子的金属材料较软,且管板的金属材料较硬时,则选取较大的胀管率。
其值可按下式计算:ρ=(d K-d N-e)/Do×100%式中:d K——管子胀接后的内径d N——管子胀接前的内径e—胀接前管子与管板的间隙(即管子胀前外径)Do—胀接前管板孔径5 胀接过程5.1 为减少管板胀后变形,推荐按梅花状的顺序定位胀。
5.2 对大直径,(D N>1000)特别是薄管板,为避免胀后变形,在定位胀前,将两管板保持与管子垂直,测量四点,其中两管板间距之差不得超过:D N<1000时2mm;D N≥1000时3mm。
两管板按上述要求调好后,靠近中心处临时用拉杆若干根将两管板拉紧,再按上述步骤胀接。
5.3 胀接过程中允许施用润滑油,但一定要防止润滑油带入管板孔内。
5.4 胀管时,一旦过胀,发现管子胀裂,需更换管子,管子抽出后,修磨管板孔。
管孔最大直径应不大于Do+1㎜。
5.5 管子全部胀完后,应逐根检查管口是否有漏胀。
如果管头超差应用钻头锪到允许范围,见下表6 胀管质量要求:6.1 胀口内壁光滑平整,无凹陷擦伤、重皮、起毛。
6.2 胀口扩大部分的过渡区应无明显棱角,不准出现裂纹。
胀管工艺

换热管的允许偏差 表 1-1
材料
标准
碳 GB8163-87
钢
外径×厚度
(mm)
3
57×3.5
Ⅰ级换热器 外径偏差 壁厚偏差 (mm) (mm)
±0.2 ±0.3
+12% -10%
Ⅱ级换热器 外径偏差 壁厚偏差 (mm) (mm)
±0.4 ±0.45
19.40
+0.20 0
25.40
+0.2 0
32.50
+0.30 0
38.50
+0.30 0
45.50
+0.40 0
57.70
+0.40 0
2、对工艺评定的要求 实施本工艺时,必须按照正确方法完成下列工艺评定: (1)换热器与管板接头焊接工艺评定。 (2)换热器与管板接头贴胀工艺评定。 3、对管子与管板结合部位的清理
级
换 热 管板
器
管孔直径 (mm) 允许偏差 (mm)
19.25
+0.15 0
25.25
+0.15 0
32.35
+0.2 0
38.40
+0.20 0
45.40
+0.20 0
57.55
+0.25 0
Ⅱ 换热器 级 换 热 管板 器
允许偏差 (mm) 管孔直径 (mm) 允许偏差 (mm)
±0.40 ±0.40 ±0.45 ±0.45 ±0.45 ±0.57
8
6
(一)主要质量控制流程(见表 1-3) (二)主要的质量标准 1.外观检查 (1)换热管的胀接部位和非胀接部位手感检查应过渡圆滑,不得有 棱角。 (2)胀接长度应符合图纸要求。 (3)用 10 倍放大镜检查焊缝外观,应符合下列要求: a、焊缝尺寸应符合图纸及规范要求。 b、表面不允许有裂纹、气孔、弧坑、夹渣等缺陷,并不得保留有熔渣 和飞溅物。 c、在图纸对咬边缺陷无特殊规定时咬边深度不大于 0.5 ㎜ ,咬边总长度 不大于焊缝总长的 10%。 d、焊缝应向母材圆滑过渡。如设计需要打磨焊缝时,不得损伤管板母 材,且打磨处不得凹陷,局部凹陷不允许超过管板厚度的负偏差。 e、管板的最终不平度应符合设计要求。 2、无损探伤 1)完成焊接 24h 后,用 PT(MT)探伤进行检查,无裂纹为合格。 2)贴胀完成后应进行 PT 或 MT 探伤,合格要求同焊后探伤。 3)如有必要,可以在水压试验完成后再进行一次抽查性 PT 或 MT 探伤, 标准同前。抽查部位由设计部门指定,无裂纹为合格。若发现裂纹,应 全部进行 PT 或 MT 探伤。
胀管施工工艺2013

胀管施工工艺江苏溧阳锅炉设备安装工程集团公司第八公司胀接施工工艺总则本工艺编制依据:《蒸汽锅炉安全技术监察规程》1996年276号;《工业锅炉胀接技术条件》ZJB980001-87;《低压水管锅炉胀接施工规程》。
本工艺适用于工业锅炉管子与锅筒、管板胀接。
胀管前的工量准备为了保证胀管质量,在胀管前必须做好工具、量具、操作人员确定工作。
胀管器胀管器选取必须符合ZJB980001-87规定,胀管器的胀珠、胀杆表面应光滑,不应有沟纹、撞伤、斑痕等现象;检查前清洗零件,同时查看各零件配合是否正确,胀杆不能弯曲,圆锥度一般为1:25,胀珠圆锥度为胀杆圆锥度的一半。
胀杆与胀珠装配时,其轴线有1.5~2°的夹角,胀杆与胀珠基本上能保持线接触,以保证胀接质量。
自行制作管子夹具及靠模、排管、角铁靠样,能牢固稳定管子即可。
选用自行制作的“车床式”管子接头打磨机械,一端用龙门钳固定管头,露出长度200mm,实际打磨100~200mm,打磨靠装在滑动块上的电机带动三块活动砂轮块,根据向心旋转力打磨表面,依据滑块掌握打磨光度。
管子内径用半圆锥清理干净。
管孔打磨用内圆磨包细砂纸进行。
其他工具有小木锤、线锤、内径百分表、游标卡尺、不带丝化纤布、或汽油。
CCL4管孔和管子汽包上管孔的检查10. 汽包的内部装置应拆除,以便清洗和检查汽包管孔。
检查时应先清洗掉管孔壁上的防护涂料,检查管孔壁的加工质量,不得有砂眼、凹痕、边缘毛刺和纵向刻痕;纵向或螺旋形刻痕的深度不得大于0.5mm,宽度不得大于1mm,刻痕到孔边的距离不得小于孔壁厚度的1/3,并且不得小于4mm。
管孔壁如有锈蚀,应用细砂布等不致使孔壁产生明显刻痕的工具,将孔壁处理至发出金属光泽。
当距离胀管时间较长时,应涂好防锈油。
11. 用内径千分表测量每个管孔的直径、圆锥度和椭圆度,记在展开图或记录表上,其偏差不得超过表1的规定。
当偏差超过本规定时,应与锅炉使用单位协商处理。
胀接工艺规程

胀接工艺胀接工艺1胀接前的准备工作1.1受热面管子安装前的检查,应符合下列要求1.1.1管子表面不应有重皮、裂纹、压扁和严重锈蚀等缺陷。
当管子表面有刻痕、麻点等其他缺陷时,其深度不应超过管子公称壁厚的10%。
1.1.3对流管束应作外形检查及矫正,校管平台应平整牢固,放样尺寸误差不应大于1mm,矫正后的管子和放样实线应吻合,局部间隙不应大于2mm,并应进行试装检查。
1.1.4受热面管排列应整齐,局部管段和设计安装位置偏差不宜大于5mm。
1.1.5胀接管口的端面倾斜度不应大于管子公称外径的1.5%,且不大于1mm。
1.1.6受热面管子应作通球检查,通球后的管子应有可靠的封闭措施,通球直径应符合表4-1的规定。
表4-1通球直径(mm)弯管半径<2.5Dw ≥2.5Dw,且<3.5 Dw ≥3.5 Dw通球直径0.70Dn 0.80Dn0.85Dn注:1、Dw—管子公称外径;Dn—管子公称内径;2、试验用球一般采用不易产生塑性变形的材料制造。
试验用球一般使用钢材或木材制成,不宜用铝等易产生塑性变形材料,通球所用的球要逐个编号,严格管理,防止球遗忘于管内,对完成通球检查的管子临时封堵。
做好通球记录。
1.2管子的硬度测定,每根管子的两端均应测试硬度,常用的硬度测定方法有布氏硬度(HB)和洛氏硬度(HRC)等。
1.3管子端头退火1.3.1胀接管子的锅筒(锅壳)和管板的厚度应不小于12mm。
胀接管孔间的距离不应小于19 mm。
外径大于102 mm的管子不宜采用胀接。
1.3.2胀接管子材料宜选用低于管板硬度的材料。
若管端硬度大于管板硬度时,应进行退火处理。
管端退火不得用煤炭作燃料直接加热,管端退火长度不应小于100 mm。
1.3.3管子胀端退火时,受热应均匀,退火温度应控制在600~650℃之间,并应保持10~15min,退火时间应为100~150min,退火后的管端应有缓慢冷却的保温措施。
1.4胀接管孔的质量应符合下列要求1.4.1胀管管孔的表面粗糙度Ra不应大于12.5μm,且不应有凹痕,边缘毛刺和纵向裂痕,少量管孔的环向或螺旋形刻痕深度不应大于0.5mm,宽度不应大于1mm,刻痕至管孔边缘的距离不应小于4mm。
胀管技术施工工法
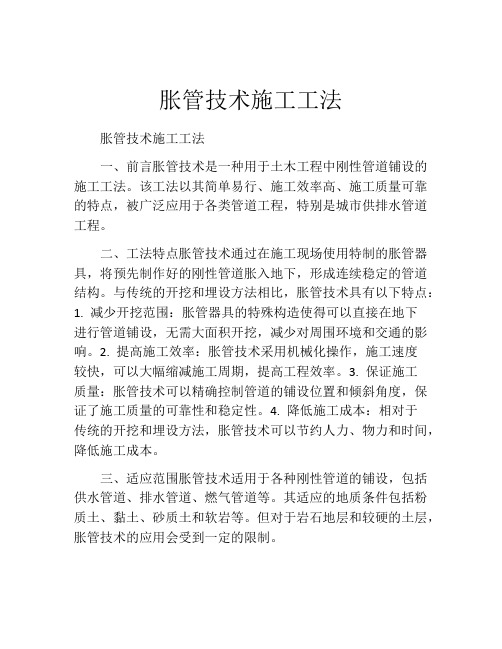
胀管技术施工工法胀管技术施工工法一、前言胀管技术是一种用于土木工程中刚性管道铺设的施工工法。
该工法以其简单易行、施工效率高、施工质量可靠的特点,被广泛应用于各类管道工程,特别是城市供排水管道工程。
二、工法特点胀管技术通过在施工现场使用特制的胀管器具,将预先制作好的刚性管道胀入地下,形成连续稳定的管道结构。
与传统的开挖和埋设方法相比,胀管技术具有以下特点:1. 减少开挖范围:胀管器具的特殊构造使得可以直接在地下进行管道铺设,无需大面积开挖,减少对周围环境和交通的影响。
2. 提高施工效率:胀管技术采用机械化操作,施工速度较快,可以大幅缩减施工周期,提高工程效率。
3. 保证施工质量:胀管技术可以精确控制管道的铺设位置和倾斜角度,保证了施工质量的可靠性和稳定性。
4. 降低施工成本:相对于传统的开挖和埋设方法,胀管技术可以节约人力、物力和时间,降低施工成本。
三、适应范围胀管技术适用于各种刚性管道的铺设,包括供水管道、排水管道、燃气管道等。
其适应的地质条件包括粉质土、黏土、砂质土和软岩等。
但对于岩石地层和较硬的土层,胀管技术的应用会受到一定的限制。
四、工艺原理胀管技术的工艺原理主要是通过运用强大的推力和旋转力,将胀管器具沿预设的管道轨迹向地下推进,同时在推进过程中及时回转管道,以确保管道的正确位置和角度。
五、施工工艺胀管技术的施工过程一般包括以下几个阶段:1. 预处理:根据设计要求,对施工区域进行勘测、测量和地质探查,确定施工的具体方案和施工参数。
2. 地面准备工作:清理施工区域,确保施工现场的安全和整洁。
3. 胀管器具安装:安装胀管器具,包括推进台车、胀管头和胀管杆等,对设备进行检查和调试。
4. 推进施工:根据管道轨迹和设计要求,通过推车控制器操控推进操作,进行胀管推进。
同时,根据需要进行调整或旋转管道,以保证其位置和角度的准确性。
5.胀管后处理:在完成推进后,进行管道连接、消除管间隙以及填补周围填土等后处理工作,以确保管道的连续性和稳定性。
胀管施工工艺
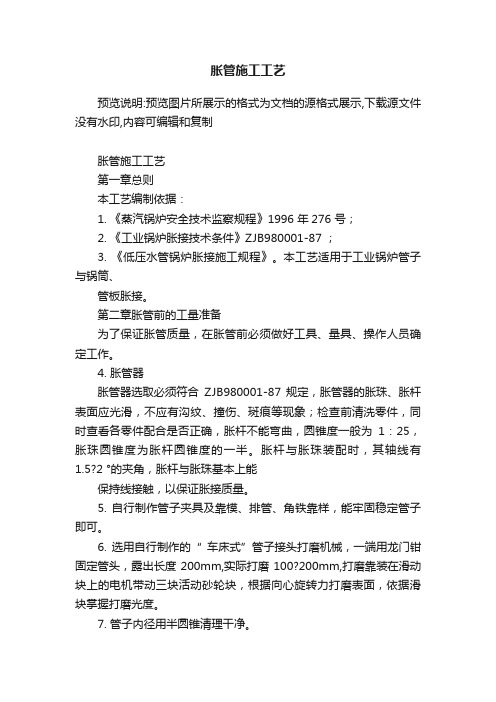
胀管施工工艺预览说明:预览图片所展示的格式为文档的源格式展示,下载源文件没有水印,内容可编辑和复制胀管施工工艺第一章总则本工艺编制依据:1. 《蒸汽锅炉安全技术监察规程》1996 年276 号;2. 《工业锅炉胀接技术条件》ZJB980001-87 ;3. 《低压水管锅炉胀接施工规程》。
本工艺适用于工业锅炉管子与锅筒、管板胀接。
第二章胀管前的工量准备为了保证胀管质量,在胀管前必须做好工具、量具、操作人员确定工作。
4. 胀管器胀管器选取必须符合ZJB980001-87 规定,胀管器的胀珠、胀杆表面应光滑,不应有沟纹、撞伤、斑痕等现象;检查前清洗零件,同时查看各零件配合是否正确,胀杆不能弯曲,圆锥度一般为1:25,胀珠圆锥度为胀杆圆锥度的一半。
胀杆与胀珠装配时,其轴线有1.5?2 °的夹角,胀杆与胀珠基本上能保持线接触,以保证胀接质量。
5. 自行制作管子夹具及靠模、排管、角铁靠样,能牢固稳定管子即可。
6. 选用自行制作的“ 车床式”管子接头打磨机械,一端用龙门钳固定管头,露出长度200mm,实际打磨100?200mm,打磨靠装在滑动块上的电机带动三块活动砂轮块,根据向心旋转力打磨表面,依据滑块掌握打磨光度。
7. 管子内径用半圆锥清理干净。
8. 管孔打磨用内圆磨包细砂纸进行。
9. 其他工具有小木锤、线锤、内径百分表、游标卡尺、不带丝化纤布、CCL4或汽油。
第三章管孔和管子第一节汽包上管孔的检查10. 汽包的内部装置应拆除,以便清洗和检查汽包管孔。
检查时应先清洗掉管孔壁上的防护涂料,检查管孔壁的加工质量,不得有砂眼、凹痕、边缘毛刺和纵向刻痕;纵向或螺旋形刻痕的深度不得大于0.5mm ,宽度不得大于1mm,刻痕到孔边的距离不得小于孔壁厚度的1/3 ,并且不得小于4mm管孔壁如有锈蚀,应用细砂布等不致使孔壁产生明显刻痕的工具,将孔壁处理至发出金属光泽。
当距离胀管时间较长时,应涂好防锈油。
11. 用内径千分表测量每个管孔的直径、圆锥度和椭圆度,记在展幵图或记录表上,其偏差不得超过表1的规定。
04-胀管作业指导书

04-胀管作业指导书引言概述:胀管作业是一项重要的工作,它在建筑、石油、化工等行业中得到广泛应用。
胀管作业的目的是通过胀管技术将管道连接紧密,确保其密封性和安全性。
本文将从胀管作业的准备工作、操作步骤、注意事项、常见问题及解决方法以及作业后的清理工作等五个大点进行详细阐述。
正文内容:1. 准备工作1.1 确定胀管的类型和规格1.2 检查胀管工具的完好性1.3 清理工作区域,确保安全1.4 准备所需的材料和工具1.5 组织作业人员,分工合作2. 操作步骤2.1 安装胀管工具2.2 调整胀管工具的参数2.3 将管道插入胀管工具2.4 开始胀管操作2.5 检查胀管效果3. 注意事项3.1 操作人员必须穿戴个人防护装备3.2 注意胀管工具的稳定性3.3 控制胀管力度,避免过度胀管3.4 注意胀管过程中的温度和压力变化3.5 遵守相关安全操作规程4. 常见问题及解决方法4.1 胀管效果不理想4.1.1 胀管工具参数调整不当4.1.2 管道材质不适合胀管4.2 胀管工具损坏4.2.1 胀管工具使用寿命过长4.2.2 胀管工具操作不当4.3 胀管过程中发生泄漏4.3.1 胀管力度不够4.3.2 管道表面不光滑5. 作业后的清理工作5.1 清理胀管工具5.2 清理作业区域5.3 对胀管效果进行检查和记录总结:通过本文的阐述,我们了解了胀管作业的准备工作、操作步骤、注意事项、常见问题及解决方法以及作业后的清理工作等方面的内容。
在进行胀管作业时,我们应该做好准备工作,严格按照操作步骤进行操作,并注意安全事项。
同时,对于常见问题的解决方法和作业后的清理工作也要进行妥善处理。
只有这样,我们才能确保胀管作业的质量和安全性。
胀管通用工艺

XG/T22-2011胀管通用工艺1.范围本守则适用工业锅炉胀接设备、胀前准备、胀接及检查等,适用额定工作压力不大于2.5MPa以水为介质的固定式锅炉。
-2.规范性引用文件下列标准的条文通过本守则引用而成为本守则的条文。
在本守则制定时,所示版本均为有效。
所有标准都会被修订,使用本守则的各方应探讨使用下列标准最新版本的可能性。
JB/T 9619 工业锅炉胀接技术条件JB/T 1625 中低压锅炉焊接管孔尺寸3.胀前准备3.1 胀接管子在装配之前应进行逐根复查,并符合下列条件:3.1.1 管子外表不得有重皮、裂纹、压扁等缺陷,胀接管端不得有纵向刻痕,如有横向刻痕、麻点等缺陷时,缺陷深度不得超过管子工程壁厚的10%。
3.1.2 胀接管端的外径和壁厚偏差应符合GB 3087的规定。
3.1.3 胀接管子的制造偏差应符合JB/T 1611的规定。
3.2 胀接管端的端面倾斜度△f(图1)应不大于管子公称外径的1.5%,且最大不得超过1mm。
图13.3胀接管子材料宜选用低于管板硬度的材料,若管端硬度大于管板硬度时,应进行退火处理。
3.4胀接管端退火时,应符合下列要求。
3.4.1管端的退火应缓慢升温,退火温度应控制在600~650℃之间,保温10~15min。
3.4.2管端退火不得用煤炭作燃料直接加热,退火长度不应小于100mm。
3.4.3退火后的管端应有缓慢冷却的保温措施。
3.4.4退火温度应有仪表显示或监测。
3.5 胀接管端的清理应符合下列要求。
3.5.1胀接管端的表面应均匀地打磨至显出金属光泽,打磨长度不得小于50mm,打磨后的管子表面不得有起皮、凹痕、裂纹和纵向沟槽等缺陷。
3.5.2胀接管端的毛刺、污垢和铁锈应清理干净;。
管端内表面应无铁屑等杂物。
3.6 胀接管孔的质量应符合下列要求。
3.6.1胀接管孔的表面粗糙度不得大于。
3.6.2管孔上不允许有纵向刻痕,个别管孔上允许有一条螺旋行或环向刻痕,刻痕深度不得超过0.5mm,宽度不得超过1mm,刻痕至管孔边缘的距离不得小于4mm。
- 1、下载文档前请自行甄别文档内容的完整性,平台不提供额外的编辑、内容补充、找答案等附加服务。
- 2、"仅部分预览"的文档,不可在线预览部分如存在完整性等问题,可反馈申请退款(可完整预览的文档不适用该条件!)。
- 3、如文档侵犯您的权益,请联系客服反馈,我们会尽快为您处理(人工客服工作时间:9:00-18:30)。
胀管施工工艺江苏溧阳锅炉设备安装工程集团公司第八公司胀接施工工艺第一章总则本工艺编制依据:1.《蒸汽锅炉安全技术监察规程》1996年276号;2.《工业锅炉胀接技术条件》ZJB980001-87;3.《低压水管锅炉胀接施工规程》。
本工艺适用于工业锅炉管子与锅筒、管板胀接。
第二章胀管前的工量准备为了保证胀管质量,在胀管前必须做好工具、量具、操作人员确定工作。
4.胀管器胀管器选取必须符合ZJB980001-87规定,胀管器的胀珠、胀杆表面应光滑,不应有沟纹、撞伤、斑痕等现象;检查前清洗零件,同时查看各零件配合是否正确,胀杆不能弯曲,圆锥度一般为1:25,胀珠圆锥度为胀杆圆锥度的一半。
胀杆与胀珠装配时,其轴线有1.5~2°的夹角,胀杆与胀珠基本上能保持线接触,以保证胀接质量。
5.自行制作管子夹具及靠模、排管、角铁靠样,能牢固稳定管子即可。
6.选用自行制作的“车床式”管子接头打磨机械,一端用龙门钳固定管头,露出长度200mm,实际打磨100~200mm,打磨靠装在滑动块上的电机带动三块活动砂轮块,根据向心旋转力打磨表面,依据滑块掌握打磨光度。
7.管子内径用半圆锥清理干净。
8.管孔打磨用内圆磨包细砂纸进行。
9.其他工具有小木锤、线锤、内径百分表、游标卡尺、不带丝化纤布、CCL4或汽油。
第三章管孔和管子第一节汽包上管孔的检查10. 汽包的内部装置应拆除,以便清洗和检查汽包管孔。
检查时应先清洗掉管孔壁上的防护涂料,检查管孔壁的加工质量,不得有砂眼、凹痕、边缘毛刺和纵向刻痕;纵向或螺旋形刻痕的深度不得大于0.5mm,宽度不得大于1mm,刻痕到孔边的距离不得小于孔壁厚度的1/3,并且不得小于4mm。
管孔壁如有锈蚀,应用细砂布等不致使孔壁产生明显刻痕的工具,将孔壁处理至发出金属光泽。
当距离胀管时间较长时,应涂好防锈油。
11. 用内径千分表测量每个管孔的直径、圆锥度和椭圆度,记在展开图或记录表上,其偏差不得超过表1的规定。
当偏差超过本规定时,应与锅炉使用单位协商处理。
12. 有缺陷的管孔在缺陷未消除前不得胀管,消除较小的缺陷一般可用刮刀修刮。
用刮刀或其他修整工具后的管孔壁,其加工质量、椭圆度和圆锥度,应符合第10条和第11条的规定。
13.为防止管孔壁表面金属再次氧化,应尽量缩短从管孔清理完到胀管的时间。
管孔的允许偏差(毫米)表1注:1. 椭圆度是指管孔同一断面处最大和最小直径之差。
圆锥度是指沿管孔深度方向最大和最小直径之差。
2.括号内数值适用于按1961年锅炉专业标准制造的锅炉。
第二节 管子的检查14. 管子必须具有出厂合格证明书,其钢号应与设计要求相符,如无出厂证明书或对材质有所怀疑,应作化学分析和机械性能试验,不符合要求时不得使用。
15. 擦去管子表面上的污物,检查管子的表面。
外表面不得有斑疤、小眼、裂纹和重皮,管端胀接部分不得有纵向沟纹,如果有横向沟纹,其深度不得超过管壁厚度的1/10,内外表面均不得有严重锈蚀。
16. 管子的外形应在放样平台上进行检查,其偏差如超过下列规定时应予校正(校正时应往锅炉上试装一下,以作核对):1) 直管的弯曲度不得超过每米1mm ,全长弯曲度不得超过3mm ,长度偏差不得超过±3mm 。
2) 弯曲管外形偏差不得超过图2的规定。
3) 弯曲管平面的不平度(图3)不得超过表2的规定。
弯曲管不平度的允许偏差(mm )4) 管子最后校正完毕,应作通球试验,以能全部通过为合格,图2 弯曲管外形的允许偏差(mm )图3 弯曲管的不平度对过热器蛇形管和弯曲半径不大于 3.5倍管子外径的弯曲管子,所用圆球直径为管子公称内径的80%,对其它管子所用圆球直径为管子公称内径的85%,圆球一般应用钢材或木材制成,不得用铅等易产生塑性变形的材料。
17.检查每根管子胀接端的外径,其偏差不得超过表3的规定。
检查数量一般为管子根数的25%,有问题时全部检查。
管子外径的允许偏差(mm)表318.检查每个管子胀接端的壁厚,其偏差不得超过表4的规定(当管子表面有缺陷时,缺陷深度不得使管壁厚度小于允许最小壁厚)。
管口壁厚的允许偏差(mm)表4当偏差超过本规定时,应与锅炉使用单位协商处理。
19.管口断面不得有毛刺,并应与管子中心线相垂直,用角尺检查时,角尺与管口边缘之间的间隙(图4)g不得大于管子外径的2%。
图4 用角尺检查管口断面、第四章胀管准备第一节技工鉴定及试胀工作20.胀管工作人员必须掌握本规程的规定,需经口试和实际操作试验,合格后方可进行胀管操作。
21.胀管的实际操作试验,其试件的钢号、尺寸、加工精度、管子与管孔的配合等要求应与设备相符,胀闭后应通过下列检验:1)按本规程第六章规定进行外观检查和水压试验;2)确定合适的胀管率和操作中控制胀管的方法;3)割下管头,检查胀口印痕、管壁减薄、管孔变形等情况。
22.如果是熟练的胀管技工,又是连续施工型号规格相同的锅炉,所用的胀管器并未更换,经施工单位主管部门技术负责人的批准,可不经过试验。
第二节管端退火23.未经退火的管子胀接端应进行退火,如果胀接端外表的硬度低于HB170,同时低于管孔壁处的硬度时,也可不进行退火。
测硬度时去掉金属表面的氧化皮。
24.管端退火长度应为150~200mm,退火时应先将管子另一端堵住(以防空气在管内流动),在将退火端均匀地加热至600~650℃,在此温度下保持10~15分钟,不得将管端加热到700℃以上。
25.管子的冷却应埋在干燥的保温材料(如石灰、砂、白灰等)内进行,如果保温材料降低到接近环境湿度后方得取出。
不得在风、雪、雨的露天场地上进行冷却。
26.退火一般采用“铅浴法”间接加热:1)铅锅规格应根据具体要求决定。
2)铅材内不得含有能腐蚀管子的杂质,熔化后除掉夹渣,铅液表面应铺洒厚约10mm的煤灰渣等粉末状材料。
3)为了测量正确,防止超出或不到规定温度范围,应用热电偶等高温计测量,温度计的量程最好在0~1000℃范围内,不得目测估计。
4)热电偶的瓷管外应套有相应规格的一端堵死的钢管,作为保护,热电偶的毫伏计应调整准确,其冷端应装有补偿导线或补偿器。
5)铅液易飞溅和氧化,氧化铅有毒,操作地点应宽敞和通风,并有防止铅中毒和铅液溅伤的安全措施。
6)退火的管子应根据管排分批堆放,预热烤干。
管头应干燥,无其它杂物,待铅液加热至600℃左右时,将管子逐根逐批插入铅锅。
7)管子插入铅锅后,加热应缓慢,平均温升不得超过15℃/分钟。
27.退火方法亦可采用锯末、木炭、焦碳(含硫、磷量各在0.03%以下)或电能直接加热。
第三节胀接面的清理28.管子胀接端的外表面应挫磨至全面出现金属光泽,挫磨长度应比管孔壁厚长50mm。
挫磨时应尽量使管子外表面维持圆形()不要成多边形),挫磨掉的厚度一般不宜超过0.2mm。
挫磨后不得有起皮、凹痕、夹层、裂纹、麻点和纵向沟纹等缺陷。
距管口100mm内管子内壁的锈皮,应予除掉。
29.挫磨后的管端不得碰撞和沾污,如因某种情况当时不能立即胀管,应妥善保护,防止生锈。
第五章胀接面的清理第一节装管30.管子经挫磨后,在装管前应用外径千分尺或游标卡尺测量其胀接段的外径,一般应测量几处,取得平均值后作好记录。
31.装管前应核对汽包和联箱的相对位置是否正确,并检查它们固定得是否牢稳,方得进行胀接工作。
32.装管前应将管孔和管子上已错磨的胀接面清洗干净,如有浮锈,需用砂布擦去。
清洗剂一般不使用含乙铅得汽油或四氯化碳,洗净后应用干净的棉布擦干,再进行装管。
33.装管前对外形相同的管子,应按照已量得的管孔直径和管子胀接段的外径进行选配,尽量使管子与管孔间的间隙不超过表5中的正常值。
当间隙超过表5的最大值时,应与锅炉使用单位和当地锅炉监察部门协商处理。
34.管子的两个胀接端装入管孔时,应能自由伸入。
管子必须装正,不得歪斜;当发现有卡住、偏斜等现象时,不得使劲硬插,应把管子取出检查校正后再插入。
装管时为节省人力,可使用管卡子(图5),将管子重量通过管卡子支持在下汽包上。
管子与管孔间的允许间隙(mm)表535.管端伸出管孔的长度(图6)h,应符合表6的规定。
在同一个汽包内,应尽量作到伸出长度一致,如果伸出长度超过规定,切除后应按第22条进行检查。
图5 管卡子示意图图6 管端伸出管孔的长度管端伸出管孔的长度(mm)表6第三节胀管一般规定36.管子安装后应随即进行胀管。
在锅炉的许多管子中,应先胀汽包两端的管排,作为基准管排(图7),然后一般宜自从中间分向两边胀接,同一根管子应先焊焊接端,后胀胀接端。
37.各管排的排列应整齐,以免影响挂砖;应按照基准管排为基准,用拉线法和卡板进行找正。
38.各管子胀接的次序易采用反节式,以防胀管时使其它管子的胀接松弛。
39.胀管工作在环境温度为0℃以上时进行。
40.胀管过程中应严防油、水和灰尘等渗入胀接面间。
41.胀接完的管端,其管口应翻边,斜度为15度,并应在伸入管孔1~2mm处开始倾斜(图8),即b-a=1~2mm。
图7 基准管排示意图图8 胀完的管端(沿汽包纵向截面)42.管子的胀管率应在1~2.1%的范围内,每台锅炉的预定胀管率应根据试胀情况确定,预定胀管率不宜选择太高,应留有余地,使在必要的补胀后最终胀管率不超过2.1%。
胀管率应按下列公式计算:H=[(d1+2t)/d-1]×100%式中:H —胀管率(mm)d1 —管子胀完后的最终内径(mm)t —未胀时管子实测壁厚(mm)d —胀管前管孔的实际直径(mm )43. 胀管前,管端内部以及胀管器的胀珠和胀杆上,均应涂上润滑脂,必须注意不使油脂渗入胀接面间。
一般情况下,每胀过15~20个胀口,应将胀管器拆开放在煤油中洗净,仔细检查是否损坏或过度磨损。
44. 胀管器放入管内时应保持胀杆正对管孔中心,操作时始终应保持正确的相对位置;胀杆转动应平稳而均匀,不得忽快忽慢,或对胀杆施加冲击力。
45. 胀口内壁应平滑,无凹痕、擦伤、重皮和起皮等现象,否则应找出原因(例如胀管时润滑是否不良,管内的铁锈和铁渣是否未除洁净,或胀珠是否已磨损不平等),清除缺陷。
46. 施工人员在锅炉上胀最初几根管子时应注意检查,观察胀管方法和所选用的胀管率是否恰当,必要时可对单根管子进行水压试验(图9)。
在胀管过程中,当对某个胀接端的严密度有怀疑时,可对该管子作单根水压试验。
47. 胀管时应指定专人,认真记录每个管孔和管端的测量数据,作为质量鉴定和交工验收时计算胀管率的依据;测量计算胀管率所需的各数据时,测外径应使用内径千分尺,测内径应使用内径千分表。
求实际胀管率不一定对每个管头都进行计算,可选择其中若干典型者,一般计算数不得少于总数的10%。
48. 胀管的操作方法,可采用一次胀管法,也可采用二次胀管法。
基准管排一般采用二次胀管法。