非晶材料的退火处理
非晶软磁材料的退火处理

非晶软磁材料的退火处理Amorphous soft magnetic materials are widely used in various applications such as transformers, inductors, and magnetic shielding due to their excellent magnetic properties. 非晶软磁材料因其优秀的磁性能,在变压器、电感器和磁屏蔽等各种应用中被广泛使用。
However, the properties of these materials can be enhanced through annealing processes. 但是,通过退火处理,这些材料的性能可以得到提升。
Annealing involves heating the material to a specific temperature and then allowing it to cool slowly in order to relieve internal stresses and soften the material. 退火涉及将材料加热到特定温度,然后让它慢慢冷却,以释放内部应力并软化材料。
One of the key benefits of annealing amorphous soft magnetic materials is the reduction of power loss. 通过退火非晶软磁材料的一个关键好处是减少功率损耗。
During the annealing process, the magnetic domains in the material become more aligned, leading to a reduction in eddy current losses and hysteresis losses. 在退火过程中,材料中的磁畴更加排列整齐,从而减少涡流损耗和磁滞损耗。
材料非晶晶化方法
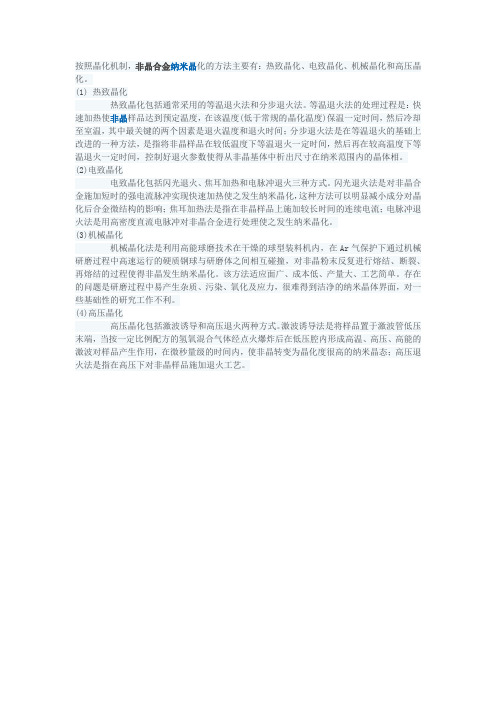
按照晶化机制,非晶合金纳米晶化的方法主要有:热致晶化、电致晶化、机械晶化和高压晶化。
(1) 热致晶化
热致晶化包括通常采用的等温退火法和分步退火法。
等温退火法的处理过程是:快速加热使非晶样品达到预定温度,在该温度(低于常规的晶化温度)保温一定时间,然后冷却至室温,其中最关键的两个因素是退火温度和退火时间;分步退火法是在等温退火的基础上改进的一种方法,是指将非晶样品在较低温度下等温退火一定时间,然后再在较高温度下等温退火一定时间,控制好退火参数使得从非晶基体中析出尺寸在纳米范围内的晶体相。
(2)电致晶化
电致晶化包括闪光退火、焦耳加热和电脉冲退火三种方式。
闪光退火法是对非晶合金施加短时的强电流脉冲实现快速加热使之发生纳米晶化,这种方法可以明显减小成分对晶化后合金微结构的影响;焦耳加热法是指在非晶样品上施加较长时间的连续电流;电脉冲退火法是用高密度直流电脉冲对非晶合金进行处理使之发生纳米晶化。
(3)机械晶化
机械晶化法是利用高能球磨技术在干燥的球型装料机内,在Ar气保护下通过机械研磨过程中高速运行的硬质钢球与研磨体之间相互碰撞,对非晶粉末反复进行熔结、断裂、再熔结的过程使得非晶发生纳米晶化。
该方法适应面广、成本低、产量大、工艺简单。
存在的问题是研磨过程中易产生杂质、污染、氧化及应力,很难得到洁净的纳米晶体界面,对一些基础性的研究工作不利。
(4)高压晶化
高压晶化包括激波诱导和高压退火两种方式。
激波诱导法是将样品置于激波管低压末端,当按一定比例配方的氢氧混合气体经点火爆炸后在低压腔内形成高温、高压、高能的激波对样品产生作用,在微秒量级的时间内,使非晶转变为晶化度很高的纳米晶态;高压退火法是指在高压下对非晶样品施加退火工艺。
非晶硅低温退火固相晶化的研究
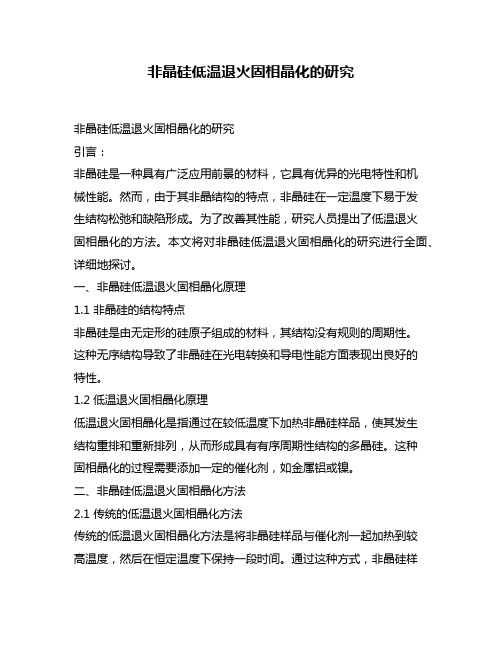
非晶硅低温退火固相晶化的研究非晶硅低温退火固相晶化的研究引言:非晶硅是一种具有广泛应用前景的材料,它具有优异的光电特性和机械性能。
然而,由于其非晶结构的特点,非晶硅在一定温度下易于发生结构松弛和缺陷形成。
为了改善其性能,研究人员提出了低温退火固相晶化的方法。
本文将对非晶硅低温退火固相晶化的研究进行全面、详细地探讨。
一、非晶硅低温退火固相晶化原理1.1 非晶硅的结构特点非晶硅是由无定形的硅原子组成的材料,其结构没有规则的周期性。
这种无序结构导致了非晶硅在光电转换和导电性能方面表现出良好的特性。
1.2 低温退火固相晶化原理低温退火固相晶化是指通过在较低温度下加热非晶硅样品,使其发生结构重排和重新排列,从而形成具有有序周期性结构的多晶硅。
这种固相晶化的过程需要添加一定的催化剂,如金属铝或镍。
二、非晶硅低温退火固相晶化方法2.1 传统的低温退火固相晶化方法传统的低温退火固相晶化方法是将非晶硅样品与催化剂一起加热到较高温度,然后在恒定温度下保持一段时间。
通过这种方式,非晶硅样品中的结构重排和重新排列可以得到有效控制,从而形成有序周期性结构的多晶硅。
2.2 新型的低温退火固相晶化方法近年来,研究人员提出了一些新型的低温退火固相晶化方法。
利用激光或电子束辐照非晶硅样品,可以在较低温度下实现快速结构转变和固相晶化。
还有人尝试使用等离子体处理非晶硅样品,以促进其结构重排和重新排列。
三、非晶硅低温退火固相晶化条件优化3.1 温度优化在进行非晶硅低温退火固相晶化时,选择合适的退火温度是非常重要的。
过高的温度可能导致非晶硅样品过度结晶,而过低的温度则无法实现有效的结构转变。
需要通过实验确定最佳的退火温度。
3.2 时间优化除了温度外,退火时间也是影响非晶硅低温退火固相晶化效果的关键因素。
合理控制退火时间可以使非晶硅样品在较短时间内实现结构重排和重新排列,从而提高固相晶化效率。
四、非晶硅低温退火固相晶化后性能改善4.1 光电特性改善通过非晶硅低温退火固相晶化,可以显著改善其光电特性。
非晶合金的热处理和性质研究

非晶合金的热处理和性质研究一、引言非晶合金又称为非晶态金属、非晶质合金、非晶态合金等,是一种不具有规则晶体结构的固态金属材料。
与传统晶体金属不同,非晶合金具有极佳的塑性、热稳定性、硬度、强度和耐腐蚀性能,在磁性、电学及光学方面也有独特性质。
而研究非晶合金的热处理和性质,具有重要的工业应用和学术意义。
二、非晶合金热处理方法1. 熔化法熔化法是将合金材料加热至液态,然后急速冷却到室温。
熔化法分为单一熔炼和多元系统熔炼,单一熔炼适用于制备有单一主要元素的非晶合金,多元系统熔炼则适用于复杂合金体系的制备。
2. 溅射法溅射法是将高纯金属靶材放在真空室内,然后通过加热和高能离子轰击使靶材发生溅射,形成非晶合金薄膜。
该方法薄膜制备速度快、成本低,而且可以制备大面积的非晶合金薄膜。
3. 退火法退火是指将高温制得的非晶合金材料在一定的时间内,在高温下保温,让其体系发生晶化,实现由非晶态向晶体的转变。
退火条件和参数对晶化微观结构有很大影响,通过控制不同的退火温度和时间可以制得具有不同微观结构的非晶合金材料。
三、非晶合金性质研究1. 磁性非晶合金具有极好的磁性,在储存、传输、保护信息等方面具有广泛的应用。
研究表明,非晶合金的磁性能与制备工艺和微观结构密切相关。
制备方法中,熔化法制备的非晶合金磁性能优于溅射法制备的;微观结构方面,非晶合金晶粒尺寸越小、分布越均匀、固溶体含量越高,磁性能越好。
2. 电学性质非晶合金的电学性质,在传感器、防磁屏蔽等领域有广泛的应用。
非晶合金的电学性质受化学成分、制备工艺和组织结构影响。
比如,铁基非晶合金中添加Co元素可以提高其电阻率、抗磁性能和疲劳寿命;晶化后的非晶合金电阻率明显提高,代表了其内部电子结构的改变。
3. 机械性能非晶合金具有强度高、塑性好、硬度高和弹性模量变化小等优点,常用于制作高强度、高韧性的结构材料。
然而,非晶合金的机械性能与制备工艺、化学成分和微观结构有密切关系。
以Zr、Nb和Cu为原料的非晶合金中,Cu的含量越多,抗拉强度越高、伸长率越低;而组织中纳米晶粒的尺寸、分布和方向对非晶合金的力学性能也有显著影响。
二氧化硅退火
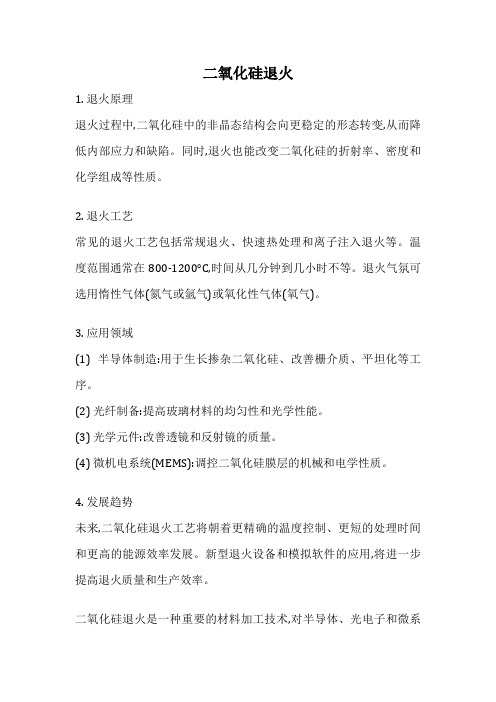
二氧化硅退火
1. 退火原理
退火过程中,二氧化硅中的非晶态结构会向更稳定的形态转变,从而降低内部应力和缺陷。
同时,退火也能改变二氧化硅的折射率、密度和化学组成等性质。
2. 退火工艺
常见的退火工艺包括常规退火、快速热处理和离子注入退火等。
温度范围通常在800-1200°C,时间从几分钟到几小时不等。
退火气氛可选用惰性气体(氮气或氩气)或氧化性气体(氧气)。
3. 应用领域
(1) 半导体制造:用于生长掺杂二氧化硅、改善栅介质、平坦化等工序。
(2) 光纤制备:提高玻璃材料的均匀性和光学性能。
(3) 光学元件:改善透镜和反射镜的质量。
(4) 微机电系统(MEMS):调控二氧化硅膜层的机械和电学性质。
4. 发展趋势
未来,二氧化硅退火工艺将朝着更精确的温度控制、更短的处理时间和更高的能源效率发展。
新型退火设备和模拟软件的应用,将进一步提高退火质量和生产效率。
二氧化硅退火是一种重要的材料加工技术,对半导体、光电子和微系
统等领域的发展具有重要意义。
退火处理对非晶态Ni—P合金超细粉结构及磁性能的影响

用 Na P H 0z为 还 原 剂 , 备 出 了 NiP合 金 超 细 粉 体 制 —
法 。笔 者用 Na P 作 为还 原 剂 , NiO H O 在 S 溶 液 中
还 原制 备 出 Ni ~ 晶合金 超 细粉体 材料 , 分析 比较 P非 并
了不 同退 火工 艺 处理 对 超 细 Ni — P合 金 粉 体磁 性 能 的
材料 。将 Ni — P合 金 粉 在 2 0 5 ℃ 下 退 火 处 理 , 0 ~4 0 并
通 过 X 射 线 衍 射 ( R 、 射 电镜 ( M ) 场 发 射 扫 X D) 透 TE 和 描 电 镜 ( E E ) 退 火 前 后 Ni 合 金 粉 的 结 构 、 F SM 对 — P 形
能方 面 , 晶态合 金 的电 阻率 比一 般 的软磁 材 料大 , 非 磁
P合 金粉 置于长 5m、 c 直径 0 8m 的石 英管 内 , 真空 .c 抽
致伸 缩特性 好 , 高频 感 应 器 、 型变 压 器 、 感 器 等 在 微 传 领域 具有广 阔 的用 途 。因此 , 晶 态 合金 的制 备 方 法 非 及磁 性能研 究成 为材料 科学 和 电子信息 领域 中的重 要
MXP 1 2 VAHF型 X射 线衍射 仪分 析 Ni — 金粉 的相 P合
组成 和 结 构 , u C Ka射 线 源 为 辐 射 源 , 射 线 波 长 X
作 用 , 冷 而成 的非 晶态 薄带 脱 离 辊 轮表 面而 甩 出 。 急
课 题 ~ 。引。
后 封装 。封装 好 的试样 在箱 式 电阻炉 中快速 升 温至所
需 温度 , 温 2 mi 保 0 n后空 冷 。
铁基非晶合金材料的热处理工艺优化

铁基非晶合金材料的热处理工艺优化铁基非晶合金材料是一种具有独特性质和广泛应用前景的金属材料。
在现代工业中,铁基非晶合金已经成为许多领域的理想选择,包括电子、汽车、航空航天等。
热处理工艺是铁基非晶合金材料制备过程中不可或缺的环节,通过对热处理工艺进行优化,可以改善材料的性能和工艺可控性。
热处理工艺主要包括退火、固溶处理、时效处理等步骤。
其中,退火是铁基非晶合金材料热处理过程中的关键步骤之一。
退火过程中,材料的内部结构发生重组,从而改变材料的硬度、导电性、磁导率等性质。
优化退火工艺可以控制材料的晶化行为和晶粒尺寸,进而影响材料的力学性能和导电性能。
一种常见的优化方法是调节退火温度和退火时间。
退火温度过高或退火时间过长会导致晶粒长大,从而降低材料的硬度和导电性。
然而,退火温度过低或退火时间过短则可能无法完全消除材料中的内部应力和组织缺陷,从而影响材料的力学性能和热稳定性。
因此,在实际应用中,需要通过试验和实验分析来确定最佳的退火参数。
除了温度和时间的调节之外,加入适量的合金元素也是优化热处理工艺的重要因素。
合金元素的选择和添加可以改变材料的组织结构和相变行为,进而影响材料的力学性能和导电性能。
例如,添加少量的钼、铌等元素可以有效提高铁基非晶合金的硬度和韧性。
而硼、氮等元素的加入则可以改善材料的热稳定性和抗腐蚀性能。
因此,选择合适的合金元素并控制其添加量,可以优化材料的热处理工艺并改善材料的性能。
此外,热处理过程中还需要控制材料的冷却速率。
快速冷却可以有效抑制铁基非晶合金的晶化行为,从而保持材料的非晶态结构。
而过慢的冷却速率则可能导致材料中的非晶态区域发生晶化,影响材料的性能。
因此,在热处理工艺中,合理控制冷却速率并选择适合的冷却介质非常重要。
综上所述,铁基非晶合金材料的热处理工艺优化对于提高材料的性能和工艺可控性具有重要意义。
通过调节退火温度和时间、添加合适的合金元素、控制冷却速率等方法,可以优化铁基非晶合金材料的热处理工艺并改善材料的力学性能、导电性能和热稳定性。
非晶合金热处理及其性能研究与应用
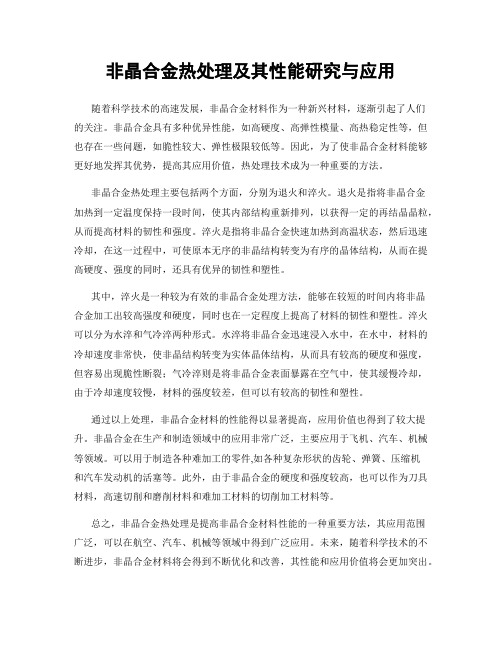
非晶合金热处理及其性能研究与应用随着科学技术的高速发展,非晶合金材料作为一种新兴材料,逐渐引起了人们的关注。
非晶合金具有多种优异性能,如高硬度、高弹性模量、高热稳定性等,但也存在一些问题,如脆性较大、弹性极限较低等。
因此,为了使非晶合金材料能够更好地发挥其优势,提高其应用价值,热处理技术成为一种重要的方法。
非晶合金热处理主要包括两个方面,分别为退火和淬火。
退火是指将非晶合金加热到一定温度保持一段时间,使其内部结构重新排列,以获得一定的再结晶晶粒,从而提高材料的韧性和强度。
淬火是指将非晶合金快速加热到高温状态,然后迅速冷却,在这一过程中,可使原本无序的非晶结构转变为有序的晶体结构,从而在提高硬度、强度的同时,还具有优异的韧性和塑性。
其中,淬火是一种较为有效的非晶合金处理方法,能够在较短的时间内将非晶合金加工出较高强度和硬度,同时也在一定程度上提高了材料的韧性和塑性。
淬火可以分为水淬和气冷淬两种形式。
水淬将非晶合金迅速浸入水中,在水中,材料的冷却速度非常快,使非晶结构转变为实体晶体结构,从而具有较高的硬度和强度,但容易出现脆性断裂;气冷淬则是将非晶合金表面暴露在空气中,使其缓慢冷却,由于冷却速度较慢,材料的强度较差,但可以有较高的韧性和塑性。
通过以上处理,非晶合金材料的性能得以显著提高,应用价值也得到了较大提升。
非晶合金在生产和制造领域中的应用非常广泛,主要应用于飞机、汽车、机械等领域。
可以用于制造各种难加工的零件,如各种复杂形状的齿轮、弹簧、压缩机和汽车发动机的活塞等。
此外,由于非晶合金的硬度和强度较高,也可以作为刀具材料,高速切削和磨削材料和难加工材料的切削加工材料等。
总之,非晶合金热处理是提高非晶合金材料性能的一种重要方法,其应用范围广泛,可以在航空、汽车、机械等领域中得到广泛应用。
未来,随着科学技术的不断进步,非晶合金材料将会得到不断优化和改善,其性能和应用价值将会更加突出。
非晶合金退火后硬度变化的实证分析
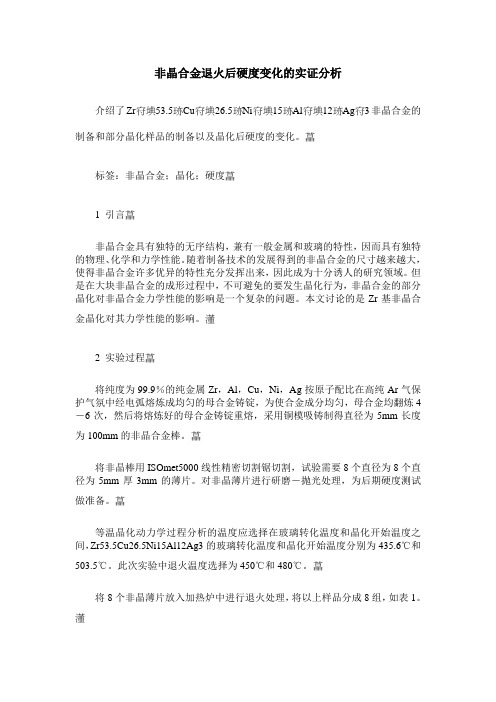
非晶合金退火后硬度变化的实证分析介绍了Zr53.5Cu26.5Ni15Al12Ag3非晶合金的制备和部分晶化样品的制备以及晶化后硬度的变化。
标签:非晶合金;晶化;硬度1 引言非晶合金具有独特的无序结构,兼有一般金属和玻璃的特性,因而具有独特的物理、化学和力学性能。
随着制备技术的发展得到的非晶合金的尺寸越来越大,使得非晶合金许多优异的特性充分发挥出来,因此成为十分诱人的研究领域。
但是在大块非晶合金的成形过程中,不可避免的要发生晶化行为,非晶合金的部分晶化对非晶合金力学性能的影响是一个复杂的问题。
本文讨论的是Zr基非晶合金晶化对其力学性能的影响。
2 实验过程将纯度为99.9%的纯金属Zr,Al,Cu,Ni,Ag按原子配比在高纯Ar气保护气氛中经电弧熔炼成均匀的母合金铸锭,为使合金成分均匀,母合金均翻炼4-6次,然后将熔炼好的母合金铸锭重熔,采用铜模吸铸制得直径为5mm长度为100mm的非晶合金棒。
将非晶棒用ISOmet5000线性精密切割锯切割,试验需要8个直径为8个直径为5mm厚3mm的薄片。
对非晶薄片进行研磨-抛光处理,为后期硬度测试做准备。
等温晶化动力学过程分析的温度应选择在玻璃转化温度和晶化开始温度之间,Zr53.5Cu26.5Ni15Al12Ag3的玻璃转化温度和晶化开始温度分别为435.6℃和503.5℃。
此次实验中退火温度选择为450℃和480℃。
将8个非晶薄片放入加热炉中进行退火处理,将以上样品分成8组,如表1。
2.1 硬度测试硬度测试是使用AMH43全自动显微测试仪,可测试材料的洛氏和维氏显微硬度。
测试要求样品的表面粗糙度为12,加载载荷50g,加载时间为10s,得到的数据如下:2.2 DSC测试采用STA449C型DSC分析仪,对退火前后的样品进行测试,采用的升温速率为20K/min,测试淬态样品及部分退火后样品的特征温度(玻璃转变温度Tg、晶化温度Tx),通过对这些样品的DSC曲线分析,考察样品的晶化行为。
非晶铁芯退火工艺
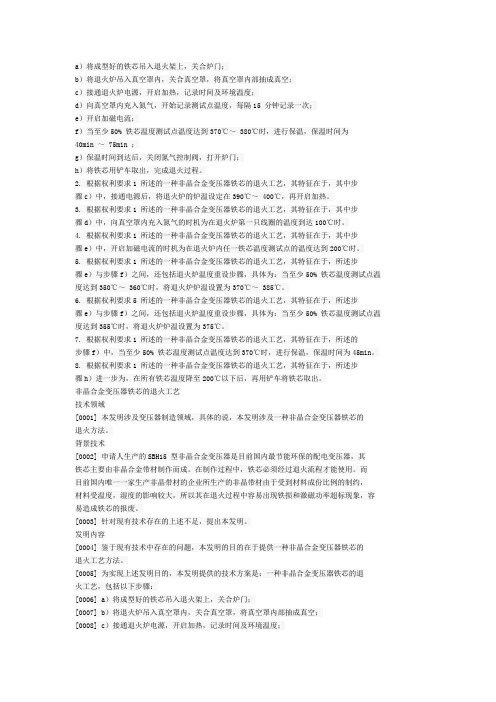
a)将成型好的铁芯吊入退火架上,关合炉门;b)将退火炉吊入真空罩内,关合真空罩,将真空罩内部抽成真空;c)接通退火炉电源,开启加热,记录时间及环境温度;d)向真空罩内充入氮气,开始记录测试点温度,每隔15 分钟记录一次;e)开启加磁电流;f)当至少50% 铁芯温度测试点温度达到370℃~ 380℃时,进行保温,保温时间为40min ~ 75min ;g)保温时间到达后,关闭氮气控制阀,打开炉门;h)将铁芯用铲车取出,完成退火过程。
2. 根据权利要求1 所述的一种非晶合金变压器铁芯的退火工艺,其特征在于,其中步骤c)中,接通电源后,将退火炉的炉温设定在390℃~ 400℃,再开启加热。
3. 根据权利要求1 所述的一种非晶合金变压器铁芯的退火工艺,其特征在于,其中步骤d)中,向真空罩内充入氮气的时机为在退火炉第一只线圈的温度到达100℃时。
4. 根据权利要求1 所述的一种非晶合金变压器铁芯的退火工艺,其特征在于,其中步骤e)中,开启加磁电流的时机为在退火炉内任一铁芯温度测试点的温度达到200℃时。
5. 根据权利要求1 所述的一种非晶合金变压器铁芯的退火工艺,其特征在于,所述步骤e)与步骤f)之间,还包括退火炉温度重设步骤,具体为:当至少50% 铁芯温度测试点温度达到350℃~ 360℃时,将退火炉炉温设置为370℃~ 385℃。
6. 根据权利要求5 所述的一种非晶合金变压器铁芯的退火工艺,其特征在于,所述步骤e)与步骤f)之间,还包括退火炉温度重设步骤,具体为:当至少50% 铁芯温度测试点温度达到355℃时,将退火炉炉温设置为375℃。
7. 根据权利要求1 所述的一种非晶合金变压器铁芯的退火工艺,其特征在于,所述的步骤f)中,当至少50% 铁芯温度测试点温度达到370℃时,进行保温,保温时间为45min。
8. 根据权利要求1 所述的一种非晶合金变压器铁芯的退火工艺,其特征在于,所述步骤h)进一步为,在所有铁芯温度降至200℃以下后,再用铲车将铁芯取出。
非晶磁芯热处理

非晶磁芯热处理
非晶磁芯是一种新型的磁性材料,具有低损耗、高磁导率、低噪声等优点。
然而,非晶磁芯的制备难度较大,热稳定性差,易受到热处理的影响。
为了解决这一问题,需要对非晶磁芯进行热处理。
非晶磁芯热处理是针对非晶态材料的一种加工工艺。
其主要目的是在非晶态材料与晶态材料之间进行转变,从而改善材料的性能。
非晶磁芯热处理的过程通常包括两个步骤:退火和磁化。
在退火阶段,非晶磁芯材料被加热到一定温度,以使其达到一定的温度与时间条件,从而促使其发生晶化。
晶化的过程可以通过传统的热处理方式进行,比如说加热、保温、冷却等。
狭义上的退火是一种简单的热处理工艺,可以利用较简单的工装和加热装置,没有任何特别的要求。
在磁化阶段,非晶磁芯材料被磁场作用下进行磁化,使其获得磁导率或磁饱和度等优良的磁性能。
此时需要注意磁场的大小和方向,会影响材料的磁性能。
因此磁化时需要进行施加适当大小和方向的磁场。
而磁化过程过程必须在非晶态材料的转变成晶态材料之前进行。
非晶磁芯热处理主要的作用是将非晶态材料转变为一定程度的晶态材料,从而改变其结构和性能。
首先,热处理可以消除材料中的应力,并使其结构均匀化,从而有助于提高材料的力学性能和稳定性。
其次,也可以通过热处理来调整材料的磁性能,比如说磁饱和度、矫顽力等,以满足不同应用场合的需要。
总之,非晶磁芯热处理是制备非晶磁芯的重要工艺。
通过合理的热处理方法,可以提高材料的性能和稳定性,进而拓展非晶磁芯在电力电子、通信等领域的应用。
- 1、下载文档前请自行甄别文档内容的完整性,平台不提供额外的编辑、内容补充、找答案等附加服务。
- 2、"仅部分预览"的文档,不可在线预览部分如存在完整性等问题,可反馈申请退款(可完整预览的文档不适用该条件!)。
- 3、如文档侵犯您的权益,请联系客服反馈,我们会尽快为您处理(人工客服工作时间:9:00-18:30)。
非晶材料的退火处理
非晶合金材料具有高饱和磁感应强度、矫顽力小、损耗低的优点,运用于电力变压器中,其高效、节能、环保的效果已经被电力行业所认可。
但在2009年前,我国整个行业市场上非晶合金变压器用的非晶合金带材,几乎全部是日本的日立金属公司所生产。
2010年,我国安泰科技公司具有自主知识产权的万吨级非晶合金带材生产线建设投产,成为世界上第2家具有万吨级非晶合金带材生产能力的制造企业,彻底打破了非晶原材料依赖进口的被动局面,加快了我国电力行业低碳经济、绿色经济的发展和建设。
热处理退火工艺是非晶合金铁心整个制作过程中最关键也是最难控制的工序,涉及的工艺要素也最多,包括退火温度点、升温速度、降温速度、保温时间、气氛保护、直流磁场大小、退火炉的炉况要求等。
此种磁性材料是很特殊的,是变压器铁心的一种材料,大家都知道变压器的铁心目前是以取向硅钢为主,我们知道取向硅钢为晶体材料的。
非晶合金带材的特点是:带材非常薄,硬度大,机械加工控制难度大,且相关材料特性的离散性大。
非晶合金铁心的片间结构设计、使用条件设计、质量计算,都跟非晶合金带材的厚度、叠片系数、平整度、硼含量有着密切的关系。
铁心的结构设计合理与否,不仅影响到生产制造技术,而且也影响到批量生产的效率、铁心的质量稳定性等问题。
因此,合理、优化的结构设计,是开发和推广国产化非晶合金带材铁心的重要前提
(1)热处理退火温度
日立金属公司非晶合金带材2605SA1的硼元素含量在2.4%以下,铁心最佳的最高常规热处理退火温度控制范围在340~355℃,甚至可以更宽些。
国产非晶合金带材1K101一A1的硼含量在2.4%~2.5%,1K10卜A2的硼含量在2.5%~2.6%,因此,铁心的热处理退火温度适宜在370~380℃之间。
由于非晶合金带材经热处理退火后呈脆性,退火温度越高,材料脆性越强,因此,热处理后的铁心,在搬运、吊装、储存、运输,以及变压器装配过程中容易形成碎片。
如碎片控制不合理,这对变压器运行是非常危险的。
因此,适宜的铁心退火温度,不仅要保证消除铁心的内在应力,恢复其磁特性,而且要能够尽量降低非晶合金带材的脆性,减少在铁心后续操作中形成碎片的风险。
试验表明:国产非晶合金带材铁心最终的退火温度控制在375~380℃为最佳。
①保温时间
铁心到达最佳退火温度后,必要的保温时间,对于调整铁心磁性能,尤其是降低铁心的激磁功率起关键作用。
非晶合金铁心的热处理退火温度、退火保温时间和铁心最终性能(单位空载损耗和单位激磁功率水平)的关系如图1所示。
单位空载损耗和单位激磁功率是铁心的2个主要性能指标。
单位空载损耗大小,决定着非晶变压器最终的空载损耗是否能符合变压器的空载损耗标准;而单位激磁功率的大小,会影响非晶合金变压器运行时的噪声水
平。
以目前对非晶合金铁心热处理退火工艺的研究,在整个退火过程中,经过最佳退火温度后,铁心的单位空载损耗随着退火温度的提高和退火时间的延长而增大,但单位激磁功率仍随着退火温度的提高和退火时间的延长而降低。
而且,铁心带材的脆性,也是随着退火时间的增加、退火温度的提高而增大。
因此,铁心制造者必须根据用户对铁心性能的要求,选择最佳的退火温度和最适宜的保温时间。
②气氛保护
非晶合金带材是铁基的合金材料,铁的成分占了90%以上,因此,铁心在高温热处理退火时很容易受温度和湿度的影响而被氧化。
铁心表面被氧化后,除了表面有锈迹,更主要的是表面氧化层会导致铁心的空载损耗明显增大。
因此,铁心在整个热处理退火过程中必须采用气氛保护,减少和防止铁心表面被氧化。
与日立金属公司的非晶合金带材相比,根据现有的试验数据,国产非晶合金带材被氧化的程度更明显。
因此,国产非晶合金带材铁心在热处理时更需加强气氛保护。
目前常用的工艺保护气体为氮气或氩气,保护气的纯度可根据当地气候环境、湿度情况等选择。
③升温和降温速度
非晶合金铁心的升温速度和降温速度,对铁心性能也有着重要影响。
由于铁心在批量生产时都是多个装载、批次性热处理,所以,合理的升温和降温速度,不仅影响非晶合金铁心的性能结果,而且也影响到生产效率和生产成本。
升温速度的快慢,会影响同炉次非晶合金铁心的温度离散性,也会影响到铁心性能的离散性,升温速度越快,离散性越大。
对比国产和进口非晶合金带材铁心在升温过程中的情况,进口非晶合金带材铁心在低温段的温度离散性较小,但到达高温区时会增大;而国产非晶合金带材铁心在到达高温区并接近最佳退火温度点时的温度离散性更小,几乎可以控制在3℃之内。
因此,在升温阶段,国产非晶合金带材铁心可以直接进行快速升温,而进口非晶合金带材铁心需要采用消除温差的工艺。
降温速度的快慢,也直接影响铁心的内在性能。
试验证明:降温速度快,对于降低铁心的空载损耗是有益的,但同时会增大铁心的激磁功率。
因此,国产非晶合金带材铁心的最佳降温速度,需根据热处理设备的特点、铁心最终所要达到的性能指标来选择,这需要一定的经验数据来支持,对于不同的铁心制造者来说,这不会是唯一的。
④直流磁场
成型后的非晶合金铁心,在退火时需附加直流磁场来改善其磁特性。
其原理是:将非晶合金铁心沿带材长度方向放在磁场中,引起非晶合金带材单轴各向异性的磁畴排列,以此获得良好的磁畴取向。
场强的大小,是改善非晶合金铁心磁特性的关键。
当采用的场强大于非晶合金铁心材料磁性能的最小饱和值时,该磁场不会对铁心最终的磁特性产生有益或有害影响。
因此,铁心退火时常用的场强与非晶合金材料磁性能的饱和值保持一致或略大即可。
由于成分、电磁特性等不同,国产与进口非晶合金带材铁心退火时的场强有明显差
异。
试验表明:进口非晶合金带材铁心退火时的场强为800A/m,或磁场电流大小在500~800A,可保证退火时铁心材料饱和;而国产非晶合金带材铁心退火时的场强需2000A/m 左右,或磁场电流大小在1400A时可保证退火时铁心材料饱和,才能达到最佳的退火效果。